U.S. patent application number 16/977367 was filed with the patent office on 2021-02-18 for thermal barrier coating.
This patent application is currently assigned to JAPAN FINE CERAMICS CENTER. The applicant listed for this patent is JAPAN FINE CERAMICS CENTER, TOCALO CO.,LTD.. Invention is credited to Yoichiro HABU, Yoshiyasu ITO, Naoki KAWASHIMA, Satoshi KITAOKA, Tsuneaki MATSUDAIRA, Mikako NAGAO, Kazuo NODA, Yuhei OHIDE, Kaito TAKAGI, Makoto TANAKA, Daisaku YOKOE.
Application Number | 20210047968 16/977367 |
Document ID | / |
Family ID | 1000005236586 |
Filed Date | 2021-02-18 |

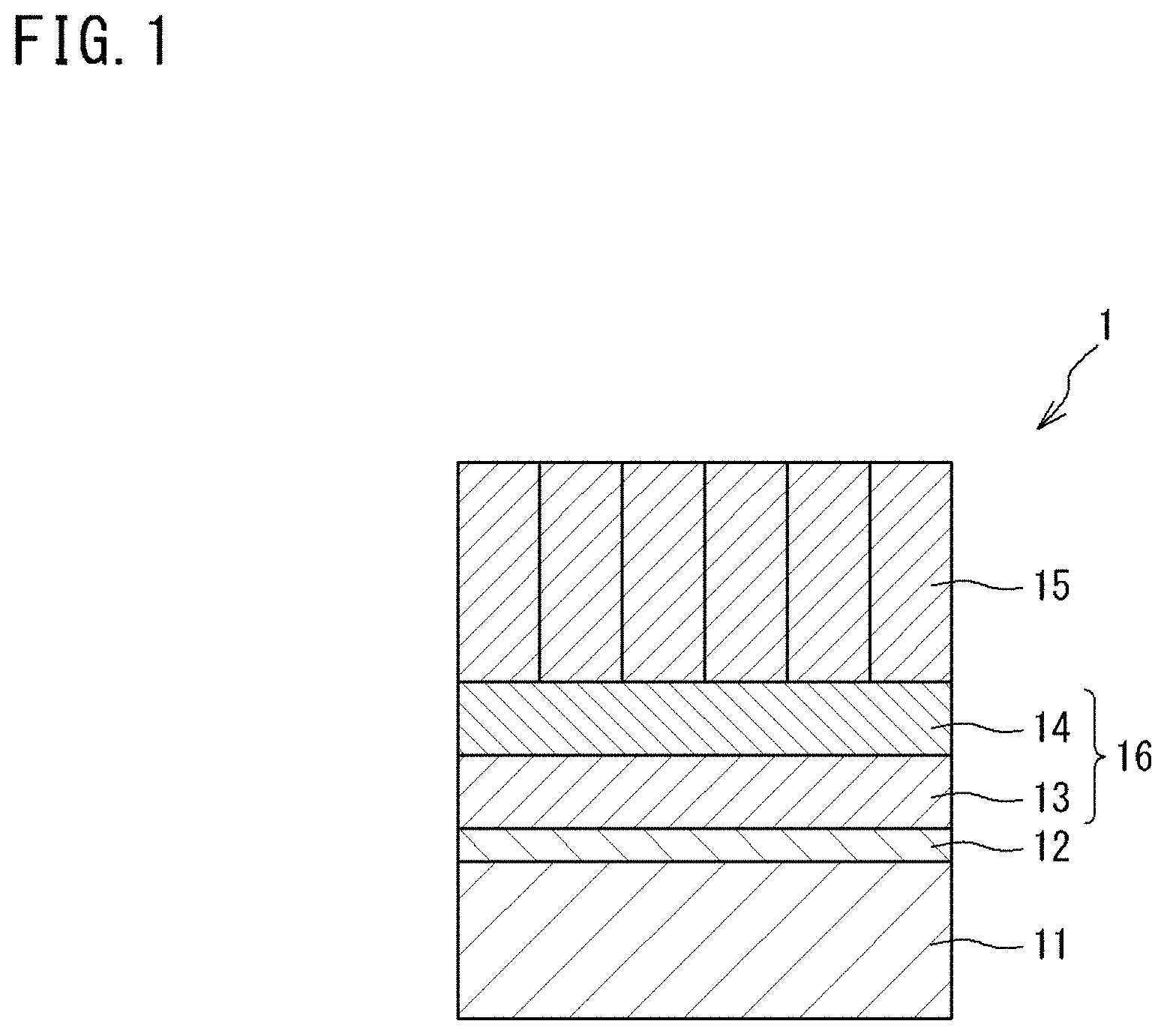
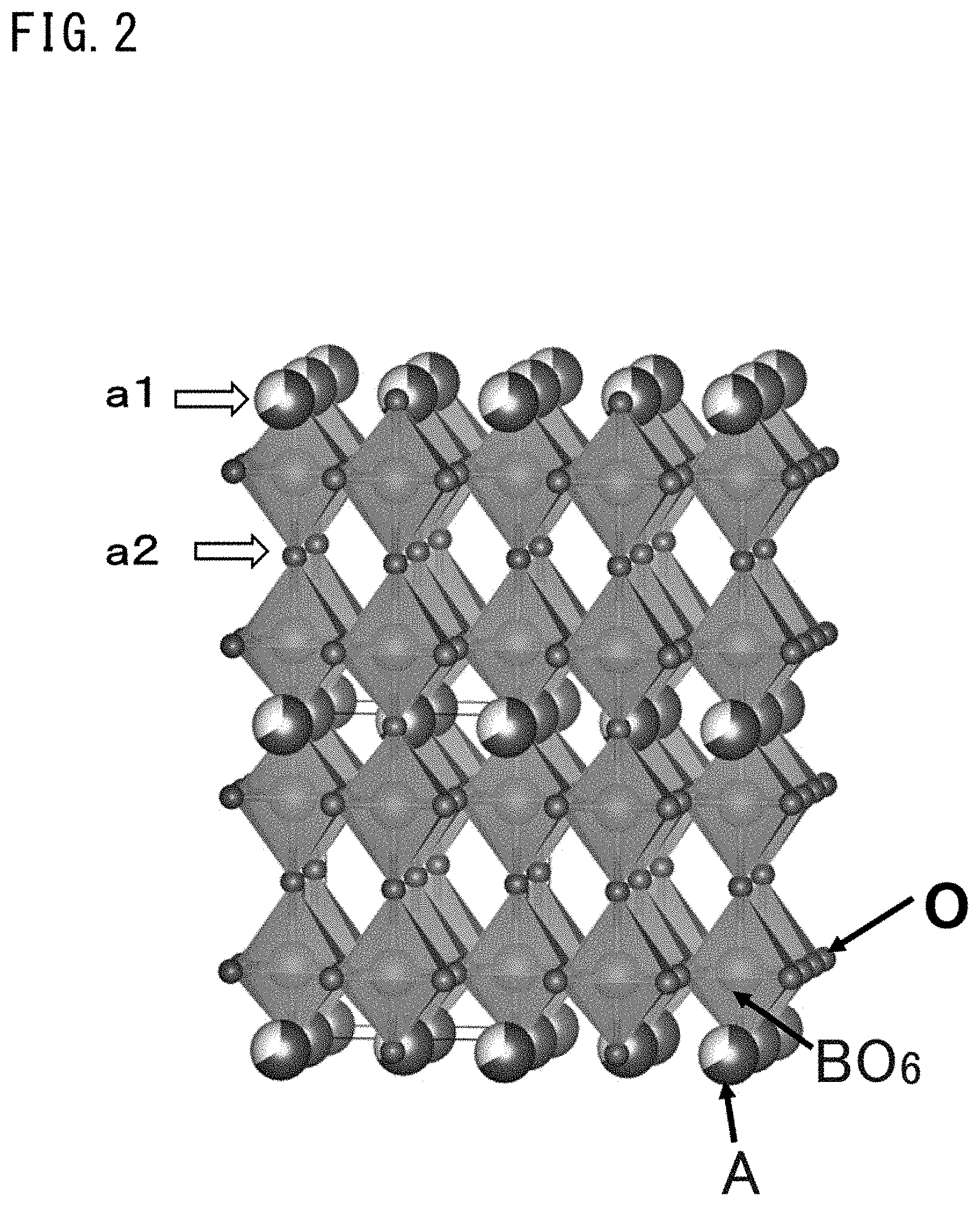


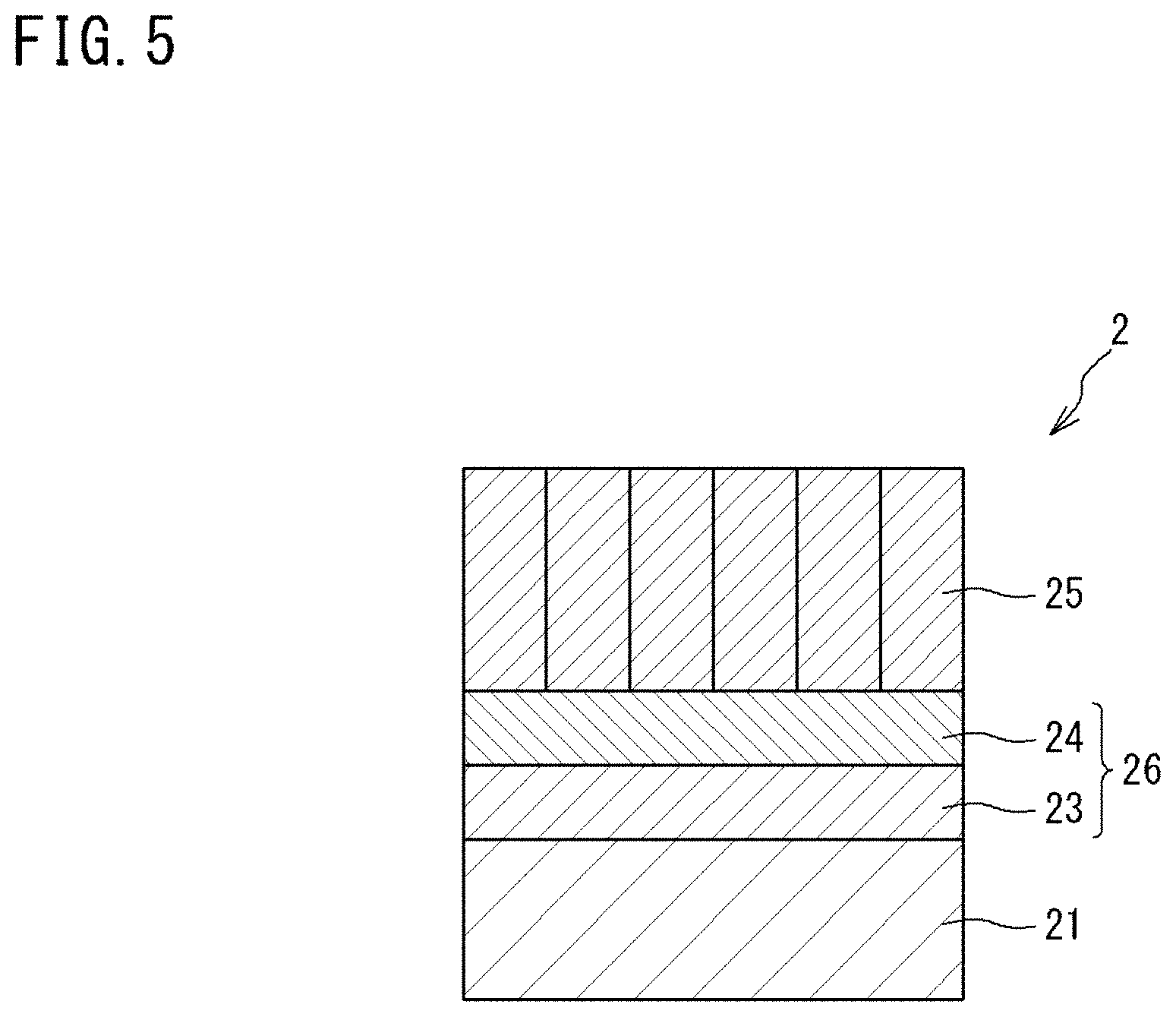

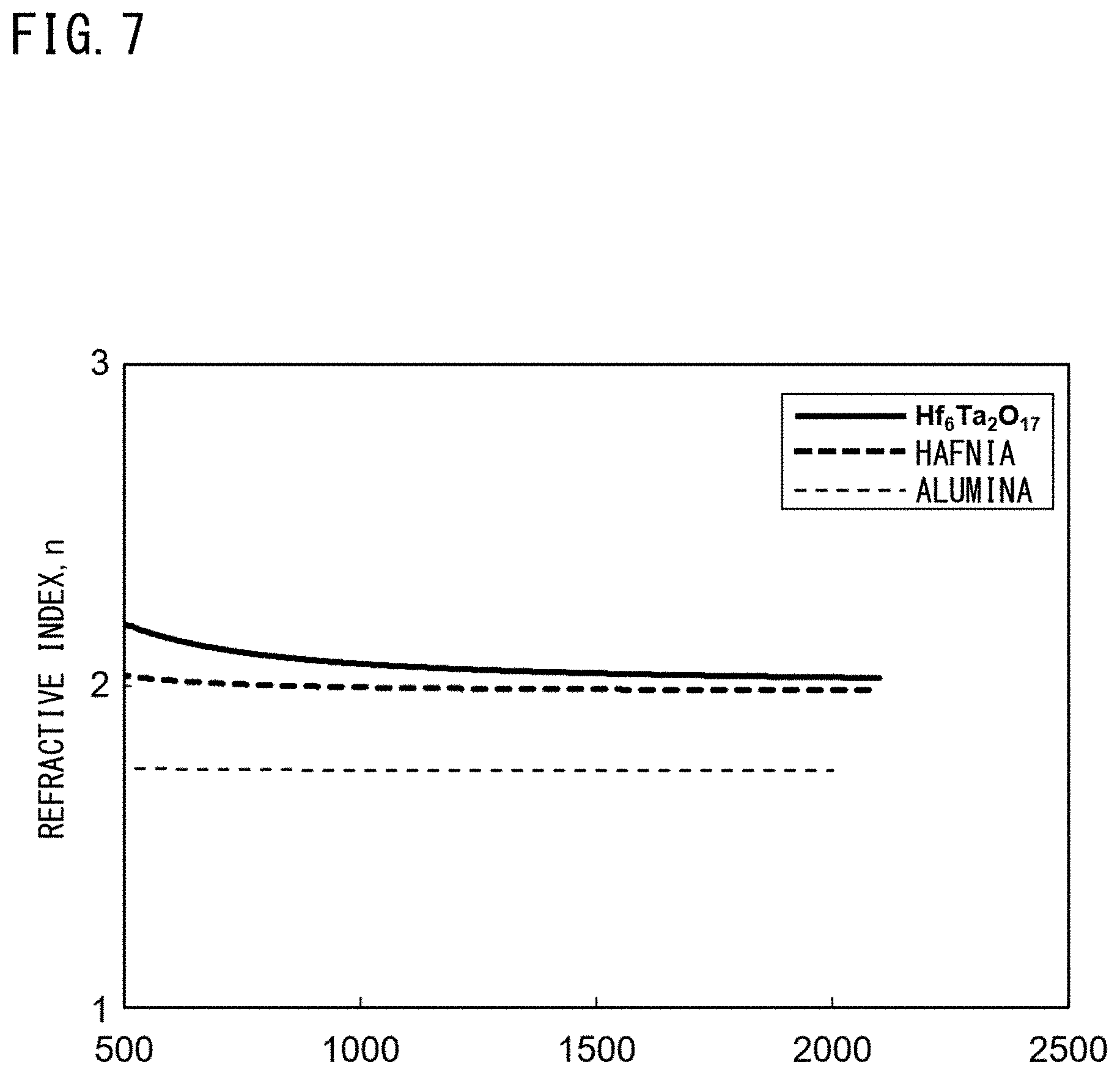



View All Diagrams
United States Patent
Application |
20210047968 |
Kind Code |
A1 |
MATSUDAIRA; Tsuneaki ; et
al. |
February 18, 2021 |
THERMAL BARRIER COATING
Abstract
A thermal barrier coating includes: a metal bonding layer made
of an alloy containing Al; a thermal barrier layer; and an
intermediate layer provided between the metal bonding layer and the
thermal barrier layer. The thermal barrier layer contains a
compound represented by the following general formula (1),
Ln.sub.xTa.sub.yHf.sub.zO.sub.(3x+5y+4z)/2 (1) (wherein Ln is an
atom of one element selected from among rare earth elements, x is 0
to 1.0, y is 0.8 to 3.0, and z is 0 to 7.0). The intermediate layer
contains at least one layer selected from among the following (A)
to (C): (A) a layer containing hafnium oxide (HfO.sub.2) as a main
component; (B) a layer containing, as a main component, a compound
consisting of tantalum (Ta), hafnium (Hf), and oxygen (O); and (C)
a layer containing, as a main component, a compound consisting of a
rare earth element, tantalum (Ta), hafnium (Hf), and oxygen
(O).
Inventors: |
MATSUDAIRA; Tsuneaki;
(Aichi, JP) ; KITAOKA; Satoshi; (Aichi, JP)
; KAWASHIMA; Naoki; (Aichi, JP) ; YOKOE;
Daisaku; (Aichi, JP) ; TANAKA; Makoto; (Aichi,
JP) ; HABU; Yoichiro; (Hyogo, JP) ; NAGAO;
Mikako; (Miyagi, JP) ; NODA; Kazuo; (Miyagi,
JP) ; ITO; Yoshiyasu; (Hyogo, JP) ; OHIDE;
Yuhei; (Hyogo, JP) ; TAKAGI; Kaito; (Hyogo,
JP) |
|
Applicant: |
Name |
City |
State |
Country |
Type |
JAPAN FINE CERAMICS CENTER
TOCALO CO.,LTD. |
Aichi
Hyogo |
|
JP
JP |
|
|
Assignee: |
JAPAN FINE CERAMICS CENTER
Aichi
JP
TOCALO CO.,LTD.
Hyogo
JP
|
Family ID: |
1000005236586 |
Appl. No.: |
16/977367 |
Filed: |
March 1, 2019 |
PCT Filed: |
March 1, 2019 |
PCT NO: |
PCT/JP2019/008178 |
371 Date: |
September 1, 2020 |
Current U.S.
Class: |
1/1 |
Current CPC
Class: |
F01D 5/28 20130101; C23C
28/042 20130101; C23C 4/073 20160101; F01D 25/145 20130101; C23C
4/11 20160101; C23C 4/134 20160101; F02C 7/24 20130101; F05D
2260/231 20130101 |
International
Class: |
F02C 7/24 20060101
F02C007/24; F01D 5/28 20060101 F01D005/28; F01D 25/14 20060101
F01D025/14; C23C 4/073 20060101 C23C004/073; C23C 4/11 20060101
C23C004/11; C23C 28/04 20060101 C23C028/04 |
Foreign Application Data
Date |
Code |
Application Number |
Mar 2, 2018 |
JP |
2018-038011 |
Claims
1. A thermal barrier coating comprising: a metal bonding layer made
of an alloy containing Al; a thermal barrier layer; and an
intermediate layer provided between the metal bonding layer and the
thermal barrier layer, wherein the thermal barrier layer contains a
compound represented by the following general formula (1),
Ln.sub.xTa.sub.yHf.sub.zO.sub.(3x+5y+4z)/2 (1) (wherein Ln is an
atom of one element selected from among rare earth elements, x is 0
to 1.0, y is 0.8 to 3.0, and z is 0 to 7.0), and the intermediate
layer contains at least one layer selected from among the following
(A) to (C), (A) a layer containing hafnium oxide (HfO.sub.2) as a
main component, (B) a layer containing, as a main component, a
compound consisting of tantalum (Ta), hafnium (Hf), and oxygen (O),
and (C) a layer containing, as a main component, a compound
consisting of a rare earth element, tantalum (Ta), hafnium (Hf),
and oxygen (O).
2. The thermal barrier coating according to claim 1, wherein the
compound represented by the general formula (1) is a complex oxide
represented by the following general formula (2), LnTa.sub.3O.sub.9
(2) (wherein Ln is an atom of one element selected from among rare
earth elements).
3. The thermal barrier coating according to claim 1, further
comprising a layer provided between the metal bonding layer and the
intermediate layer and containing aluminum oxide
(Al.sub.2O.sub.3).
4. The thermal barrier coating according to claim 1, wherein the
thermal barrier layer has a segment structure including a plurality
of columnar structures.
5. The thermal barrier coating according to claim 1, wherein the
intermediate layer includes a layer having a porosity of 5% by
volume or less.
6. The thermal barrier coating according to claim 1, wherein the
intermediate layer includes the layer (A) and the layer (B), and
the layer (A) is provided at the metal bonding layer side.
7. The thermal barrier coating according to claim 1, wherein the
intermediate layer includes the layer (B), and the layer (B) is a
layer containing a compound represented by the following general
formula (3) as a main component, Ta.sub.yHf.sub.zO.sub.(5y+4z)/2
(y=2.0, 5.0.ltoreq.z.ltoreq.7.0) (3).
8. The thermal barrier coating according to claim 1, wherein the
intermediate layer includes the layer (A) and the layer (C), the
layer (A) is provided at the metal bonding layer side, and the
layer (C) is a layer containing, as a main component, a compound
consisting of a rare earth element that is the same as Ln in the
general formula (1), tantalum (Ta), hafnium (Hf), and oxygen
(O).
9. The thermal barrier coating according to claim 3, wherein the
intermediate layer includes the layer (A) and the layer (B), and
the layer (A) is provided at the metal bonding layer side.
10. The thermal barrier coating according to claim 3, wherein the
intermediate layer includes the layer (B), and the layer (B) is a
layer containing a compound represented by the following general
formula (3) as a main component, Ta.sub.yHf.sub.zO.sub.(5y+4z)/2
(y=2.0, 5.0.ltoreq.z.ltoreq.7.0) (3).
11. The thermal barrier coating according to claim 3, wherein the
intermediate layer includes the layer (A) and the layer (C), the
layer (A) is provided at the metal bonding layer side, and the
layer (C) is a layer containing, as a main component, a compound
consisting of a rare earth element that is the same as Ln in the
general formula (1), tantalum (Ta), hafnium (Hf), and oxygen
(O).
12. The thermal barrier coating according to claim 6, wherein the
intermediate layer includes the layer (B), and the layer (B) is a
layer containing a compound represented by the following general
formula (3) as a main component, Ta.sub.yHf.sub.zO.sub.(5y+4z)/2
(y=2.0, 5.0.ltoreq.z.ltoreq.7.0) (3).
Description
TECHNICAL FIELD
[0001] The present invention relates to a thermal barrier
coating.
BACKGROUND ART
[0002] In a gas turbine for power generation, a jet engine for an
aircraft, or the like, the temperature of the combustion gas
thereof is, for example, as high as 1600.degree. C. Therefore, as a
high-temperature part such as a rotor blade, a stator blade, and a
combustor, there is a known part that includes, as a thermal
barrier coating (TBC) on the surface of a heat-resistant substrate
made of a superalloy containing Ni, Co, or Fe as a main component,
a metal bonding layer made of an MCrAlY alloy (M is at least one of
Ni, Co, and Fe) having excellent corrosion resistance and oxidation
resistance or platinum aluminide having excellent corrosion
resistance and oxidation resistance, and a thermal barrier layer
provided on the metal bonding layer and containing a ceramic
material such as yttria-stabilized zirconia (YSZ) as a main
component.
[0003] In addition, development and study of a material for a
thermal barrier coating, which has better heat resistance than
yttria-stabilized zirconia (YSZ), is also in progress.
[0004] For example, PATENT LITERATURE 1 proposes a material for a
thermal barrier coating, containing a compound represented by the
following general formula (6) such as YTa.sub.3O.sub.9.
M.sup.1M.sup.2.sub.3O.sub.9 (6)
(wherein M.sup.1 is one atom of one element selected from among
rare earth elements, and M.sup.2 is a tantalum atom or a niobium
atom.)
CITATION LIST
Patent Literature
[0005] PATENT LITERATURE 1: Japanese Laid-Open Patent Publication
No. 2014-125656
SUMMARY OF INVENTION
Technical Problem
[0006] The compound represented by the general formula (6)
described in PATENT LITERATURE 1 is suitable as a material for a
thermal barrier coating since the compound has a lower thermal
conductivity than YSZ.
[0007] On the other hand, when a thermal barrier layer made of the
compound represented by the general formula (6) (for example,
YTa.sub.3O.sub.9) is laminated on a metal bonding layer made of,
for example, an MCrAlY alloy (M is the same as above) or platinum
aluminide, the following problem may occur.
[0008] Specifically, it is known that, during use under a
high-temperature environment, a layer containing aluminum oxide
(Al.sub.2O.sub.3) as a main component (hereinafter, also referred
to as an alumina layer) is formed at the interface between the
metal bonding layer made of an MCrAlY alloy (M is the same as
above) or platinum aluminide and the thermal barrier layer made of
YTa.sub.3O.sub.9. When the alumina layer and the layer made of
YTa.sub.3O.sub.9 are in contact with each other, a chemical
reaction proceeds between Al.sub.2O.sub.3 and YTa.sub.3O.sub.9
under a high-temperature environment, and each of Al.sub.2O.sub.3
and YTa.sub.3O.sub.9 is altered, whereby oxidation resistance and
thermal barrier properties deteriorate. That is, the metal bonding
layer loses its ability to generate Al.sub.2O.sub.3, and the
thermal barrier layer loses its function as a thermal barrier
coating due to deterioration of thermal barrier performance, which
may cause peeling or damage to the substrate.
Solution to Problem
[0009] The present inventors have conducted an intensive study to
solve such a problem. As a result, the present inventors have found
that the above problem can be solved by providing a predetermined
intermediate layer between the metal bonding layer and the thermal
barrier layer, and completed the present invention.
[0010] (1) A thermal barrier coating according to the present
invention includes:
[0011] a metal bonding layer made of an alloy containing Al;
[0012] a thermal barrier layer; and
[0013] an intermediate layer provided between the metal bonding
layer and the thermal barrier layer, wherein
[0014] the thermal barrier layer contains a compound represented by
the following general formula (1),
Ln.sub.xTa.sub.yHf.sub.zO.sub.(3x+5y+4z)/2 (1)
(wherein Ln is an atom of one element selected from among rare
earth elements, x is 0 to 1.0, y is 0.8 to 3.0, and z is 0 to 7.0),
and
[0015] the intermediate layer contains at least one layer selected
from among the following (A) to (C),
[0016] (A) a layer containing hafnium oxide (HfO.sub.2) as a main
component,
[0017] (B) a layer containing, as a main component, a compound
consisting of tantalum (Ta), hafnium (Hf), and oxygen (O), and
[0018] (C) a layer containing, as a main component, a compound
consisting of a rare earth element, tantalum (Ta), hafnium (Hf),
and oxygen (O).
[0019] The thermal barrier coating is a laminate including a
plurality of layers, and includes a thermal barrier layer
containing the compound represented by the general formula (1). The
thermal barrier layer has low heat conductivity as compared to a
thermal barrier layer made of YSZ, and the thermal barrier coating
has excellent thermal barrier performance.
[0020] Moreover, in the thermal barrier coating, the intermediate
layer is provided between the metal bonding layer made of an alloy
containing Al and the thermal barrier layer containing the compound
represented by the general formula (1). The intermediate layer
contains at least one layer selected from among the layers (A) to
(C). Therefore, even if an alumina layer is formed on the metal
bonding layer due to use under a high-temperature environment,
Al.sub.2O.sub.3 in the alumina layer and the compound represented
by the general formula (1) can be prevented from reacting with each
other. Furthermore, since Al.sub.2O.sub.3 in the alumina layer is
not solid-dissolved in the intermediate layer, disappearance of the
alumina layer can be prevented, and the Al component contained in
the metal bonding layer can also be prevented from moving and
diffusing to the thermal barrier layer side.
[0021] As a result, deterioration of the metal bonding layer due to
a reduction in Al of the metal bonding layer can be prevented.
Therefore, the thermal barrier coating also has excellent long-term
reliability.
[0022] In the present specification, the "main component" refers to
a component having the highest content ratio among all components
and having a content ratio of 40 mol % or greater among all
components. The content ratio of the main component among all
components is preferably 80 mol % or greater and more preferably 98
mol % or greater.
[0023] (2) In the thermal barrier coating, the compound represented
by the general formula (1) is preferably a complex oxide
represented by the following general formula (2).
LnTa.sub.3O.sub.9 (2)
(wherein Ln is an atom of one element selected from among rare
earth elements)
[0024] The thermal barrier layer containing the complex oxide
represented by the general formula (2) has particularly excellent
thermal barrier performance
[0025] (3) The thermal barrier coating preferably further includes
a layer provided between the metal bonding layer and the
intermediate layer and containing aluminum oxide
(Al.sub.2O.sub.3).
[0026] The thermal barrier coating has one technical feature of
preventing solid dissolution of Al.sub.2O.sub.3 in the intermediate
layer by providing the intermediate layer. Thus, the thermal
barrier coating including the layer containing aluminum oxide is
suitable as a thermal barrier coating that achieves the
advantageous effects of the present invention.
[0027] Moreover, by providing the layer containing aluminum oxide,
stability under a high-temperature environment and oxygen
permeation prevention of the thermal barrier coating can be
ensured.
[0028] (4) In the thermal barrier coating, the thermal barrier
layer preferably has a segment structure including a plurality of
columnar structures.
[0029] In this case, the thermal barrier layer is suitable for
avoiding stress concentration at the thermal barrier layer due to
expansion/contraction of each layer when the thermal barrier
coating is used under heat cycle conditions. Therefore, damage due
to peeling, or the like, is particularly less likely to occur in
the thermal barrier layer having the above segment structure.
[0030] (5) In the thermal barrier coating, the intermediate layer
preferably includes a layer having a porosity of 5% by volume or
less.
[0031] In this case, there are almost no pores penetrating the
intermediate layer, and rapid solid dissolution of Al.sub.2O.sub.3
through pores and entry and permeation of corrosive substances from
the thermal barrier layer side can be prevented. Therefore, the
intermediate layer is more suitable for ensuring stability of the
intermediate layer and the alumina layer under a high-temperature
environment.
[0032] (6) In the thermal barrier coating, preferably, the
intermediate layer includes the layer (A) and the layer (B),
and
[0033] the layer (A) is provided at the metal bonding layer
side.
[0034] In this case, as compared to the case where the intermediate
layer is composed of only the layer (A), the adhesion between the
intermediate layer and the thermal barrier layer is significantly
improved, and thermal stress is relieved. Therefore, during use of
the thermal barrier coating, peeling between the intermediate layer
and the thermal barrier layer is less likely to occur.
[0035] (7) In the thermal barrier coating, preferably, the
intermediate layer includes the layer (B), and
[0036] the layer (B) is a layer containing a compound represented
by the following general formula (3) as a main component.
Ta.sub.yHf.sub.zO.sub.(5y+4z)/2
(y=2.0, 5.0.ltoreq.z.ltoreq.7.0) (3)
[0037] The layer containing the compound represented by the general
formula (3) as a main component has excellent adhesion to the
thermal barrier layer and the layer (A), and peeling of the thermal
barrier layer becomes more unlikely to occur by providing the layer
containing the compound represented by the general formula (3) as a
main component.
[0038] (8) In the thermal barrier coating, preferably, the
intermediate layer includes the layer (A) and the layer (C),
[0039] the layer (A) is provided at the metal bonding layer side,
and
[0040] the layer (C) is a layer containing, as a main component, a
compound consisting of a rare earth element that is the same as Ln
in the general formula (1), tantalum (Ta), hafnium (HD, and oxygen
(O).
[0041] In this case, as compared to the case where the intermediate
layer is composed of only the layer (A), the adhesion between the
intermediate layer and the thermal barrier layer is significantly
improved, and thermal stress is relieved. Therefore, during use of
the thermal barrier coating, peeling between the intermediate layer
and the thermal barrier layer is less likely to occur.
Advantageous Effects of Invention
[0042] In the thermal barrier coating according to the present
invention, the thermal barrier layer contains the compound
represented by the general formula (1) and thus is excellent in low
thermal conductivity, and the thermal barrier coating is less
likely to be thermally deteriorated since the thermal barrier
coating includes the intermediate layer. Thus, the thermal barrier
coating can be used over a long period of time under high
temperature (for example, 1100 to 1800.degree. C.) conditions.
[0043] Therefore, the thermal barrier coating according to the
present invention is suitable for use for high-temperature parts in
gas turbines for power generation, jet engines for an aircraft,
etc.
BRIEF DESCRIPTION OF DRAWINGS
[0044] FIG. 1 is a schematic cross-sectional view showing an
example of a thermal barrier coating according to a first
embodiment.
[0045] FIG. 2 is a schematic diagram showing the structure of a
complex oxide represented by general formula (2).
[0046] FIG. 3 is an enlarged cross-sectional view schematically
showing a thermal barrier layer included in the thermal barrier
coating shown in FIG. 1.
[0047] FIG. 4 is an enlarged cross-sectional view showing an
example of a second intermediate layer included in the thermal
barrier coating shown in FIG. 1.
[0048] FIG. 5 is a schematic cross-sectional view showing an
example of a thermal barrier coating according to a second
embodiment.
[0049] FIG. 6 is a graph showing the results of Evaluation Test
1.
[0050] FIG. 7 is a graph showing the results of Evaluation Test
2.
[0051] FIG. 8 is an X-ray diffraction pattern obtained in
Evaluation Test 3.
[0052] FIG. 9 is an X-ray diffraction pattern obtained in
Evaluation Test 4.
[0053] FIG. 10 is an X-ray diffraction pattern obtained in
Evaluation Test 5.
[0054] FIG. 11 is an X-ray diffraction pattern obtained in
Evaluation Test 6.
[0055] FIG. 12 is an observation photograph of a cross section of a
thermal barrier coating produced in Example 1 with a scanning
electron microscope.
DESCRIPTION OF EMBODIMENTS
[0056] Hereinafter, embodiments of the present invention will be
described with reference to the drawings.
First Embodiment
[0057] FIG. 1 is a schematic cross-sectional view showing an
example of a thermal barrier coating according to the present
embodiment. FIG. 2 is a schematic diagram showing the structure of
a complex oxide represented by general formula (2). FIG. 3 is an
enlarged cross-sectional view schematically showing a thermal
barrier layer included in the thermal barrier coating shown in FIG.
1. FIG. 4 is an enlarged cross-sectional view showing an example of
a second intermediate layer included in the thermal barrier coating
shown in FIG. 1.
[0058] The thermal barrier coating 1 according to the present
embodiment is a laminate that includes: a metal bonding layer 11;
an alumina layer 12 formed on the surface of the metal bonding
layer 11 and containing aluminum oxide (Al.sub.2O.sub.3) as a main
component; a first intermediate layer 13 laminated on the alumina
layer 12; a second intermediate layer 14 laminated on the first
intermediate layer 13; and a thermal barrier layer 15 laminated on
the second intermediate layer 14. The respective layers included in
the thermal barrier coating 1 are in close contact with each other.
The thermal barrier coating 1 has the first intermediate layer 13
and the second intermediate layer 14 as an intermediate layer
16.
Metal Bonding Layer
[0059] The metal bonding layer 11 is a layer made of an alloy
containing Al and preferably has a melting point of 1300.degree. C.
or higher.
[0060] For the metal bonding layer 11, for example, a Fe-based
alloy, a Ni-based alloy, a Co-based alloy, an aluminide-type
intermetallic compound, etc., can be used. Specific examples
thereof include an MCrAlY alloy (M is at least one of Ni, Co, and
Fe), platinum aluminide, and nickel-platinum-aluminide
[0061] The metal bonding layer 11 may be laminated on another
heat-resistant substrate (not shown).
[0062] An example of the other heat-resistant substrate is at least
one metal, or an alloy made of at least two metals, selected from
among Ni, Co, Fe, Nb, Ta, Mo, W, Pt, Ir, Cr, Al, and the like. As
the other heat-resistant substrate, a bulk material made of a
superalloy containing Ni, Co, or Fe as a main component or the like
is preferable.
Alumina Layer
[0063] The crystal phase of the aluminum oxide contained in the
alumina layer may be any of .alpha.-alumina, (.beta.-alumina,
.gamma.-alumina, .sigma.-alumina, .chi.-alumina, .eta.-alumina,
.theta.-alumina, and .kappa.-alumina, or may be a combination of
two or more of these aluminas.
[0064] The alumina layer 12 is preferably a layer made of
.alpha.-alumina from the viewpoints of stability at high
temperature, oxygen permeation prevention, and the like.
[0065] The alumina layer 12 is preferably made of only aluminum
oxide (Al.sub.2O.sub.3), but may contain another compound composed
of NiAl.sub.2O.sub.4, (Co, Ni)(Al, Cr).sub.2O.sub.4, or the like as
long as the advantageous effects of the present invention are
obtained.
[0066] It is known that, when the thermal barrier coating 1 having
the metal bonding layer 11 made of an MCrAlY alloy (M is the same
as above), platinum aluminide, or the like and containing Al is
used in a high-temperature environment, an alumina layer is formed
on the surface of the metal bonding layer 11 as described
above.
[0067] Therefore, the alumina layer 12 included in the thermal
barrier coating 1 may be a layer that is inevitably formed on the
surface of the metal bonding layer 11 containing Al during use. In
this case, although described in a second embodiment described
later, it is only necessary to produce a thermal barrier coating 1
having no alumina layer 12 at the time of production. In such a
thermal barrier coating 1, an alumina layer is formed during use in
a high-temperature environment.
[0068] On the other hand, the alumina layer 12 included in the
thermal barrier coating 1 may be a layer that is intentionally
provided on the surface of the metal bonding layer 11 before the
intermediate layer 16 is laminated on the metal bonding layer 11 in
the production process of the thermal barrier coating 1.
[0069] In this case, the thermal barrier coating 1 includes the
alumina layer 12 at a time point after production and before
use.
[0070] As a method for intentionally forming the alumina layer 12
on the surface of the metal bonding layer 11, there is, for
example, a method of forcibly oxidizing the surface of the metal
bonding layer 11 by heating at a high temperature in an
oxygen-containing atmosphere, and the method is preferably a method
of forcibly oxidizing the surface of the metal bonding layer 11 by
heating at a high temperature in an oxygen-containing atmosphere
after the surface of the metal bonding layer 11 is subjected to Al
diffusion treatment or the like to increase the Al content of the
metal bonding layer 11. Meanwhile, the same effect can also be
obtained by forming an alumina layer directly on the surface of the
metal bonding layer 11 by physical vapor deposition (PVD) or
chemical vapor deposition (CVD).
[0071] The thickness of the alumina layer 12 is not particularly
limited, but, in the case of forming the alumina layer 12 on the
surface of the metal bonding layer 11 during production of the
thermal barrier coating 1, the thickness of the alumina layer 12 is
preferably 0.5 to 10 .mu.m, more preferably 0.5 to 5 .mu.m, and
further preferably 0.5 to 2 .mu.m from the viewpoint of durability,
etc., under heat cycle conditions.
[0072] Meanwhile, the thickness of the alumina layer 12 that is
inevitably formed on the surface of the metal bonding layer 11
during use of the thermal barrier coating 1 cannot be generally
stated since the thickness also depends on usage conditions, etc.,
but the thickness is preferably 0.5 to 10 .mu.m, more preferably
0.5 to 5 .mu.m, and further preferably 0.5 to 2 .mu.m.
Intermediate Layer
[0073] The intermediate layer 16 included in the thermal barrier
coating 1 according to the present embodiment includes the first
intermediate layer 13 and the second intermediate layer 14
laminated on the first intermediate layer 13.
First Intermediate Layer
[0074] The first intermediate layer 13 is a layer containing
hafnium oxide (HfO.sub.2) as a main component (hereinafter, also
referred to as a hafnia layer).
[0075] Even if the hafnia layer and the alumina layer are exposed
to an atmosphere of 1600.degree. C. in a state where both layers
are in contact with each other, Al.sub.2O.sub.3 is not
solid-dissolved in HfO.sub.2, and thus the alumina layer does not
disappear. In addition, the Al component in the metal bonding layer
11 does not diffuse toward the thermal barrier layer 15. Therefore,
it is possible to avoid problems (degradation of the metal bonding
layer, peeling between each layer, damage to the substrate, etc.)
caused by Al in the metal bonding layer 11 moving to another layer
to be depleted, as described above.
[0076] The first intermediate layer 13 is preferably made of only
hafnium oxide (HfO.sub.2), but may contain another compound as long
as the advantageous effects of the present invention are
obtained.
[0077] The first intermediate layer 13 preferably has a porosity of
5% by volume or less. When the porosity of the first intermediate
layer 13 is set to 5% by volume or less, there are no pores
penetrating the first intermediate layer 13, and rapid solid
dissolution of Al.sub.2O.sub.3 through such pores and entry and
permeation of corrosive substances from the thermal barrier layer
side can be prevented. In this case, the first intermediate layer
13 is suitable for ensuring the stability of the alumina layer and
the first intermediate layer under a high-temperature environment.
The porosity is more preferably 3% by volume or less. In this case,
the first intermediate layer 13 has more excellent environmental
resistance.
[0078] The porosity of the first intermediate layer 13 is a value
obtained by observing a cross-section of a coating with a scanning
electron microscope (SEM) and calculating the area of pores in the
entire coating.
[0079] The thickness of the first intermediate layer 13 is not
particularly limited, but is preferably 10 to 50 .mu.m.
[0080] If the thickness of the first intermediate layer 13 is less
than 10 .mu.m, movement and diffusion of Al cannot be sufficiently
suppressed in some cases. On the other hand, even if the thickness
of the first intermediate layer 13 is greater than 50 .mu.m, the
effect of suppressing movement and diffusion of Al is not
necessarily improved significantly.
[0081] The thickness of the first intermediate layer 13 is more
preferably 10 to 20 .mu.m.
Second Intermediate Layer
[0082] The second intermediate layer 14 is a layer containing, as a
main component, a compound consisting of tantalum (Ta), hafnium
(Hf), and oxygen (O) or a compound containing, in addition to these
components, a rare earth element that is the same as Ln in the
general formula (1).
[0083] The compound consisting of tantalum (Ta), hafnium (Hf), and
oxygen (O) is represented by the following general formula (3).
Ta.sub.yHf.sub.zO.sub.(5y+4z)/2
(y=2.0, 5.0.ltoreq.z.ltoreq.7.0) (3)
[0084] A specific example of the compound represented by the
general formula (3) is Hf.sub.6Ta.sub.2O.sub.17.
[0085] The compound consisting of the rare earth element that is
the same as Ln in the general formula (1), tantalum (Ta), hafnium
(Hf), and oxygen (O) is represented by the following general
formula (4) or the following general formula (5).
Ln.sub.xTa.sub.yHf.sub.zO.sub.(3x+5y+4z)/2
(0<x.ltoreq.0.25, 0<y.ltoreq.0.25, 0.5.ltoreq.z.ltoreq.1.0)
(4)
Ln.sub.xTa.sub.yHf.sub.zO.sub.(3x+5y+4z)/2
(0.5.ltoreq.x.ltoreq.1.0, 0.5.ltoreq.y.ltoreq.1.0,
0<z.ltoreq.1.0) (5)
[0086] The second intermediate layer 14 is a layer having good
adhesion to one or both of the first intermediate layer (hafnia
layer) 13 and the thermal barrier layer 15. In the thermal barrier
coating 1, since the second intermediate layer 14 is provided,
peeling of the thermal barrier layer 15 is less likely to
occur.
[0087] The compound represented by the general formula (4) is a
compound in which Ln and Ta are solid-dissolved in HfO.sub.2, and a
layer containing this compound as a main component has particularly
excellent adhesion to the hafnia layer 13. In addition, the
compound represented by the general formula (4) itself has
excellent heat barrier properties.
[0088] The compound represented by the general formula (5) is a
compound in which Hf is solid-dissolved in LnTaO.sub.4, and a layer
containing this compound as a main component has particularly
excellent adhesion to the thermal barrier layer 15. In addition,
the compound represented by the general formula (5) itself has
excellent heat barrier properties.
[0089] The second intermediate layer 14 may be composed of two
layers, an inner second intermediate layer 14b and an outer second
intermediate layer 14a as shown in FIG. 4. In this case,
preferably, the inner second intermediate layer 14b is a layer
containing the compound represented by the general formula (4) as a
main component, and the outer second intermediate layer 14a is a
layer containing the compound represented by the general formula
(5) as a main component.
[0090] Moreover, in the case where the inner second intermediate
layer 14b is a layer containing the compound represented by the
general formula (4) as a main component, and the outer second
intermediate layer 14a is a layer containing the compound
represented by the general formula (5) as a main component, the
inner second intermediate layer 14b has good adhesion to the hafnia
layer 13, the outer second intermediate layer 14a has good adhesion
to the complex oxide contained in the thermal barrier layer 15 and
represented by the general formula (1), and the adhesion between
the compound represented by the general formula (4) and the
compound represented by the general formula (5) is also good. Thus,
the second intermediate layer 14 has very good adhesion to each of
the first intermediate layer (hafnia layer) 13 and the thermal
barrier layer 15.
[0091] The thickness of the second intermediate layer 14 is not
particularly limited, but is preferably 0.2 to 30 .mu.m.
[0092] If the thickness of the second intermediate layer 14 is less
than 0.2 .mu.m, it is difficult for the second intermediate layer
14 to uniformly cover the entirety of the first intermediate layer
(hafnia layer) 13, and sufficient adhesion cannot be obtained in
some cases. On the other hand, if the thickness is greater than 30
.mu.m, the second intermediate layer 14 may cause generation of new
thermal stress.
[0093] In addition, in the case where the second intermediate layer
14 is composed of two layers, the outer second intermediate layer
14a and the inner second intermediate layer 14b, each of the
thicknesses of the outer second intermediate layer 14a and the
inner second intermediate layer 14b is preferably 0.1 to 15
.mu.m.
[0094] The compound forming the second intermediate layer 14 may be
a compound in which x=0 and/or y=0 in the general formula (4), or
may be a compound in which z=0 in the general formula (5).
Thermal Barrier Layer
[0095] The thermal barrier layer 15 is a layer containing a
compound represented by the following general formula (1) as a main
component.
Ln.sub.xTa.sub.yHf.sub.zO.sub.(3x+5y+4z)/2 (1)
(wherein Ln is an atom of one element selected from among rare
earth elements, x is 0 to 1.0, y is 0.8 to 3.0, and z is 0 to
7.0)
[0096] Examples of the rare earth element that represents the atom
Ln in the general formula (1) include scandium (Sc), yttrium (Y),
lanthanum (La), cerium (Ce), praseodymium (Pr), neodymium (Nd),
promethium (Pm), samarium (Sm), europium (Eu), gadolinium (Gd),
terbium (Tb), dysprosium (Dy), holmium (Ho), erbium (Er), thulium
(Tm), ytterbium (Yb), and lutetium (Lu).
[0097] Among them, Yb is preferable. This is because a compound
represented by the general formula (1) in which Ln is Yb has a
particularly low thermal conductivity among them, and causes no
phase transformation accompanying a rise and fall in temperature,
and the thermal conductivity has negative temperature dependency in
that the thermal conductivity gradually decreases with a rise in
temperature.
[0098] The thermal barrier layer 15 is preferably made of only the
compound represented by the general formula (1), but may contain
another compound as long as the advantageous effects of the present
invention are obtained.
[0099] In the case where the compound represented by the general
formula (1) is a compound represented by the following general
formula (2), the compound is a cation-deficient-type defective
perovskite complex oxide (hereinafter, also referred to merely as
"complex oxide") and has a structure shown in FIG. 2.
LnTa.sub.3O.sub.9 (2)
(wherein Ln is an atom of one element selected from among rare
earth elements)
[0100] This structure is a structure in which 1/3 of the A ions in
the a1 plane and all the A ions in the a2 plane are deficient in a
perovskite structure represented by A.sub.3B.sub.3O.sub.9, and 2/3
of the A ions are deficient in the entire crystal lattice.
[0101] When the thermal barrier layer 15 contains the complex oxide
represented by the general formula (2), the thermal barrier layer
15 becomes more excellent in low thermal conductivity, and can
impart excellent thermal barrier performance to the thermal barrier
coating 1.
[0102] In addition, when the thermal barrier layer 15 containing
the above complex oxide is included, excellent corrosion
resistance, oxidation resistance, and heat resistance can also be
imparted to the thermal barrier coating 1.
[0103] The melting point of the complex oxide represented by the
general formula (2) is normally 1700.degree. C. or higher, and the
thermal conductivity, of the complex oxide, measured according to
JIS R 1611 by the laser flash method (measurement temperature:
20.degree. C. to 1400.degree. C.) is normally less than 3.0 W/(mK)
at the material stage (sintered body).
[0104] The number of compounds represented by the general formula
(1) and contained in the thermal barrier layer 15 may be one, or
may be two or more. In the case where the thermal barrier layer 15
contains two or more compounds represented by the general formula
(1), the thermal barrier layer 15 preferably contains the complex
oxide represented by the general formula (2) as at least one of the
compounds, and the complex oxide represented by the general formula
(2) is more preferably a main component. In addition, in the case
where the thermal barrier layer 15 contains two or more complex
oxides represented by the general formula (2), at least one of the
complex oxides is preferably YbTa.sub.3O.sub.9. In this case, the
main component of the thermal barrier layer 15 is preferably
YbTa.sub.3O.sub.9.
[0105] Moreover, the thermal barrier layer 15 is preferably made of
only the complex oxide(s) represented by the general formula
(2).
[0106] The thermal barrier layer 15 preferably has a segment
structure including a plurality of columnar structures (15a to 15h)
erected so as to extend from the second intermediate layer 14 side
to the outermost layer side (upper side in the drawing) as shown in
a schematic observation image in FIG. 3.
[0107] In the case where the thermal barrier layer 15 has the above
segment structure, a minute gap is present between adjacent
columnar structures. Thus, when the thermal barrier coating 1 is
used under heat cycle conditions, even if expansion/contraction
corresponding to temperature change occurs in each layer, stress
concentration due to the expansion/contraction of each layer is
less likely to occur at the thermal barrier layer 15. Therefore,
the thermal barrier layer 15 having the segment structure is
particularly less likely to be damaged under heat cycle
conditions.
[0108] In the case where the thermal barrier layer 15 has the
segment structure, the porosity of the thermal barrier layer 15 is
preferably 3 to 25% by volume. If the porosity of the thermal
barrier layer 15 is less than 3% by volume, a sufficient reduction
in thermal conductivity due to the presence of pores cannot be
exhibited, and the required thermal barrier properties cannot be
obtained in some cases. On the other hand, if the porosity is
greater than 25% by volume, a sufficient reduction in thermal
conductivity due to the presence of pores is exhibited and
excellent thermal barrier properties are obtained, but resistance
to erosion due to particulate matter and the like contained in
combustion gas and the like cannot be obtained in some cases. The
porosity is more preferably 5 to 20% by volume.
[0109] The porosity of the thermal barrier layer 15 is a value
obtained by observing a cross-section of a coating with a scanning
electron microscope (SEM) and calculating the area of pores in the
entire coating.
[0110] In the case where the thermal barrier layer 15 has the
segment structure, the number of columnar structures included in
the segment structure (segment number) is preferably 5 to 30
structures/mm as a segment number per unit length.
[0111] If the segment number per unit length is less than 5
structures/mm, a sufficient effect of avoiding damage under heat
cycle conditions cannot be achieved in some cases. On the other
hand, if the segment number is greater than 30 structures/mm,
deterioration of the underlayer may occur due to entry of
combustion gas.
[0112] The segment number per unit length (structures/mm) is a
value calculated by the following method.
[0113] First, an image of a cross section of the thermal barrier
layer 15 along the thickness direction (see FIG. 3) is acquired,
and a virtual reference line (alternate long and short dash line in
FIG. 3) BL that is parallel to the surface of the layer (second
intermediate layer 14 in FIG. 3) immediately below the thermal
barrier layer 15 is drawn at a position corresponding to 1/2 of the
thickness of the thermal barrier layer 15 in the acquired image.
Then, the number of columnar structures crossed by the virtual
reference line BL is counted, and the number of columnar structures
crossed by a virtual reference line BL having a length of 1 mm is
calculated as a segment number per unit length (structures/mm).
[0114] At this time, the segment number per unit length
(structures/mm) is calculated using at least a virtual reference
line having a length of 10 mm in total.
[0115] In the example of FIG. 3, eight columnar structures 15a to
15h (see .diamond-solid. marks in the drawing) are present.
[0116] The thickness of the thermal barrier layer 15 is not
particularly limited, but is preferably 100 to 2000 .mu.m from the
viewpoint of properties such as low thermal conductivity and
durability as well as corrosion resistance, oxidation resistance,
heat resistance, and an effect of protecting the metal bonding
layer.
[0117] The thickness of the thermal barrier layer 15 is more
preferably 200 to 500 .mu.m.
[0118] The thermal barrier coating 1 according to the present
embodiment can be produced by sequentially laminating each layer
from the metal bonding layer 11 side.
[0119] For example, a coating of each layer may be sequentially
laminated on the surface of a heat-resistant substrate made of a
Ni-based superalloy, a Co-based superalloy, a Fe-based superalloy,
or the like.
[0120] In the formation of the above coating, the metal bonding
layer 11, the first intermediate layer 13, and the second
intermediate layer 14 may be produced, for example, by a method
such as electron beam physical vapor deposition (EB-PVD),
atmospheric plasma spraying, low pressure plasma spraying,
suspension thermal spraying (suspension plasma spraying, suspension
high velocity flame spraying, etc.), high velocity flame spraying,
and sintering.
[0121] A more specific method is as follows.
[0122] The metal bonding layer 11 is preferably formed by
atmospheric plasma spraying, low pressure plasma spraying, high
velocity flame spraying, or EB-PVD.
[0123] The first intermediate layer 13 is preferably formed by
suspension thermal spraying, atmospheric plasma spraying, low
pressure plasma spraying, or EB-PVD.
[0124] The second intermediate layer 14 is preferably formed by
suspension thermal spraying, atmospheric plasma spraying, low
pressure plasma spraying, or EB-PVD.
[0125] In addition, as described above, the alumina layer 12 may be
intentionally formed on the surface of the metal bonding layer 11,
or may be inevitably formed during use.
[0126] The thermal barrier layer 15 may be formed by a method such
as electron beam physical vapor deposition (EB-PVD), atmospheric
plasma spraying, low pressure plasma spraying, suspension thermal
spraying, and sintering, using the compound represented by the
general formula (1).
[0127] A method for producing the complex oxide represented by the
general formula (2) is generally a method in which a compound
containing the rare earth element forming the atom Ln in the
general formula (2) (hereinafter, referred to as a "compound (m1)")
and a compound containing Ta (hereinafter, referred to as a
"compound (m2)") are blended such that the molar ratio of the atom
Ln and Ta is a predetermined ratio, and the mixture is
heat-treated.
[0128] Furthermore, in order to obtain a more uniform complex
oxide, for example, a method of obtaining a mixture containing urea
and then heat-treating the mixture may be adopted.
[0129] As the compound (m1) and the compound (m2), oxides,
hydroxides, sulfates, carbonates, nitrates, phosphates, halides,
etc., can be used. Among them, in the case of obtaining a complex
oxide having a more uniform composition, water-soluble compounds
are preferable, but water-insoluble compounds can also be used.
[0130] A preferable method for producing the complex oxide is as
follows. First, an aqueous solution or aqueous dispersion
(suspension) containing urea and the compound (m1) and the compound
(m2) that are blended such that the molar ratio of the atom Ln and
Ta is 1:3, is prepared. The concentration of the compound (m1) is
preferably 0.02 to 0.1 mol/l and more preferably 0.02 to 0.05
mol/l. The concentration of the compound (m2) is preferably 0.02 to
0.1 mol/l and more preferably 0.02 to 0.05 mol/l. The concentration
of urea is preferably 2 to 10 mol/l and more preferably 2 to 5
mol/l.
[0131] Next, the mixture liquid is heated under reflux cooling at a
temperature of 80.degree. C. to 95.degree. C. to carry out a urea
hydrolysis reaction. The reaction time is normally 10 to 20
hours.
[0132] Thereafter, depending on the form of the reaction product
contained in the reaction system, centrifugation or the like is
performed as necessary, and the reaction product is collected.
Then, the reaction product is washed with water, alcohol, or the
like, dried, and ground as necessary, to obtain powder composed of
a first precursor compound.
[0133] Next, the powder composed of the first precursor compound is
sized, and subjected to press molding or the like as necessary, to
produce a molded product having a plate shape, a lump shape, or the
like. Then, the molded product is heat-treated (calcined) for about
1 to 3 hours at a temperature of 1200.degree. C. to 1500.degree. C.
in an atmosphere containing oxygen gas to obtain a calcined
product. Then, the obtained calcined product is ground and sized as
necessary. Then, the product is subjected to press molding or the
like as necessary to produce a molded product having a plate shape,
a lump shape, or the like, and the molded product is heat-treated
for about 1 to 3 hours at a temperature of 1400.degree. C. to
1700.degree. C. in an atmosphere containing oxygen gas to obtain
the complex oxide represented by the general formula (2).
[0134] The method for forming the thermal barrier layer 15 is
preferably a method of performing suspension thermal spraying using
a material containing the compound represented by the general
formula (1) and having an average particle diameter of 0.05 to 5
.mu.m, or the compound represented by the general formula (2) and
having an average particle diameter of 0.05 to 5 .mu.m. This method
is suitable as a method for forming the thermal barrier layer 15
having the segment structure.
[0135] In the case of forming the thermal barrier layer 15 having
the segment structure by suspension thermal spraying, the porosity
in the segment structure and the segment number per unit length can
be controlled by changing a heat input amount, a spraying distance,
a traverse speed, and a pitch that are spraying conditions.
Second Embodiment
[0136] FIG. 5 is a schematic cross-sectional view showing an
example of a thermal barrier coating according to the present
embodiment.
[0137] The thermal barrier coating according to the present
embodiment is a thermal barrier coating produced without providing
an alumina layer, and is a thermal barrier coating 2 that includes
a metal bonding layer 21, an intermediate layer 26 (a first
intermediate layer 23 and a second intermediate layer 24) laminated
on the surface of the metal bonding layer 21, and a thermal barrier
layer 25 laminated on the second intermediate layer 24 as shown in
FIG. 5.
[0138] The configuration of the metal bonding layer 21, the first
intermediate layer 23, the second intermediate layer 24, and the
thermal barrier layer 25 in the thermal barrier coating 2 is the
same as that in the thermal barrier coating 1 according to the
first embodiment.
[0139] The thermal barrier coating 2 having such a layer
configuration is an unused thermal barrier coating 2. When the
thermal barrier coating 2 is used, an alumina layer is gradually
formed at the first intermediate layer 23 side of the metal bonding
layer 21 with a lapse of use time, and the layer configuration
becomes the same as that of the thermal barrier coating 1 according
to the first embodiment.
[0140] Such a thermal barrier coating, in which there is no alumina
layer when the thermal barrier coating is unused and in which an
alumina layer is formed with a lapse of use time, is also one of
embodiments of the present invention.
Third Embodiment
[0141] In a thermal barrier coating according to an embodiment of
the present invention, only a layer containing hafnium oxide
(HfO.sub.2) as a main component may be provided as an intermediate
layer.
[0142] In this case, the layer containing hafnium oxide (HfO.sub.2)
as a main component is formed directly on a metal bonding layer (or
alumina layer), and a thermal barrier layer is further formed
directly on the hafnia layer.
Fourth Embodiment
[0143] In a thermal barrier coating according to an embodiment of
the present invention, only a layer containing, as a main
component, a compound consisting of tantalum (Ta), hafnium (Hf),
and oxygen (O) may be provided as an intermediate layer.
[0144] In this case, the layer containing, as a main component, a
compound consisting of tantalum (Ta), hafnium (Hf), and oxygen (O)
is formed directly on a metal bonding layer (or alumina layer), and
a thermal barrier layer is further formed directly on the
intermediate layer.
[0145] Here, a specific example of the compound consisting of
tantalum (Ta), hafnium (Hf), and oxygen (O) is the compound
represented by the general formula (3).
Fifth Embodiment
[0146] In a thermal barrier coating according to an embodiment of
the present invention, only a layer containing, as a main
component, a compound consisting of a rare earth element, tantalum
(Ta), hafnium (Hf), and oxygen (O) may be provided as an
intermediate layer.
[0147] In this case, the layer containing, as a main component, a
compound consisting of a rare earth element, tantalum (Ta), hafnium
(Hf), and oxygen (O) is formed directly on a metal bonding layer
(or alumina layer), and a thermal barrier layer is further formed
directly on the intermediate layer.
[0148] Here, the rare earth element is preferably the same rare
earth element as Ln in the general formula (1). In addition,
specific examples of the compound consisting of the rare earth
element, tantalum (Ta), hafnium (Hf), and oxygen (O) include the
compound represented by the general formula (4) and the compound
represented by the general formula (5).
Other Embodiments
[0149] In the first embodiment and the second embodiment, the
intermediate layer included in the thermal barrier coating may
include a first intermediate layer containing, as a main component,
a compound consisting of tantalum (Ta), hafnium (Hf), and oxygen
(O), and a second intermediate layer containing, as a main
component, a compound containing a rare earth element that is the
same as Ln in the general formula (1) in addition to tantalum (Ta),
hafnium (Hf), and oxygen (O).
[0150] In the first embodiment and the second embodiment, the
compound contained in the second intermediate layer and consisting
of tantalum (Ta), hafnium (Hf), and oxygen (O), and the compound
containing the rare earth element that is the same as Ln in general
formula (1) in addition to these components, may each have a
composition ratio that gradually changes from the first
intermediate layer side toward the thermal barrier layer side.
[0151] The compounds represented by the general formula (4) and the
general formula (5) themselves have excellent heat barrier
properties, and thus can also be used for a thermal barrier layer.
In this case, the thermal barrier layer may contain, as a main
component, the compound represented by the general formula (4) or
the compound represented by the general formula (5), or may be made
of only the compound represented by the general formula (4) or the
compound represented by the general formula (5).
[0152] The thermal barrier coatings according to the embodiments of
the present invention are suitable for use for, for example,
high-temperature parts such as rotor blades in jet engines for an
aircraft and gas turbines for power generation, high-temperature
parts in various plants and various engines of automobiles and the
like, etc.
[0153] When the thermal barrier coatings are used for
high-temperature parts such as combustors in jet engines for an
aircraft, the operating temperature can be increased to improve
fuel efficiency.
[0154] Moreover, when the thermal barrier coatings are used for
high-temperature parts such as rotor blades in gas turbines for
power generation, the operating temperature can be increased to
improve power generation efficiency.
Evaluation Tests
[0155] The following evaluation tests were conducted in order to
confirm the performance of the thermal barrier coatings according
to the embodiments of the present invention.
Evaluation Test 1
[0156] Hf.sub.6Ta.sub.2O.sub.17, which is one of the compounds
forming the intermediate layers in the thermal barrier coatings
according to the embodiments of the present invention, was
evaluated for heat conduction performance
(1) Production of Evaluation Sample (Hf.sub.6Ta.sub.2O.sub.17)
[0157] 25 g (0.078 mol) of HfCl.sub.4 powder (Wako Pure Chemical
Corporation) having a purity of 99.9% or higher was put into 773 g
of distilled water contained in a reactor made of a fluorine resin,
and the mixture was stirred at room temperature (25.degree. C.) for
1 hour to obtain a colorless transparent aqueous solution. Next,
586 g (9.8 mol) of urea was added to this aqueous solution, and the
mixture was stirred at room temperature (25.degree. C.) for 1 hour.
Then, 6 g (0.014 mol) of Ta.sub.2O.sub.5 powder (manufactured by
RARE METALLIC Co., Ltd.) having a purity of 99.9% or higher was
added to the obtained colorless transparent aqueous solution, and
the mixture was stirred at room temperature (25.degree. C.) for 7
hours to obtain a suspension.
[0158] Next, the suspension was heated to 95.degree. C. and reacted
(urea hydrolysis reaction) with stirring under reflux cooling
(reaction time: 14 hours). Then, the obtained reaction solution was
centrifuged at 25.degree. C. and 4800 rpm for 30 minutes, and the
gel in the lower layer was collected. This gel was put into a large
amount of distilled water, and the mixture was sufficiently
stirred. Then, the mixture was centrifuged under the same
conditions as above, and the gel in the lower layer was
collected.
[0159] Then, the precipitate was heated in an air atmosphere at
1700.degree. C. for 1 hour, ground in an alumina mortar, and sieved
(100 mesh) to collect fine powder.
[0160] This fine powder was subjected to press molding (pressure:
25 MPa). Then, this molded body was heat-treated at 1600.degree. C.
for 2 hours by hot pressing (40 MPa, Ar atmosphere). The obtained
fired body was dry-ground in a mortar at room temperature
(25.degree. C.), and X-ray diffraction measurement was performed on
the ground product to confirm that the ground product had an
orthorhombic crystal system composed of Hf.sub.6Ta.sub.2O.sub.17.
The density .rho. was 10.4 g/cm.sup.3.
(2) Production of Comparative Sample (7 wt %
Y.sub.2O.sub.3--ZrO.sub.2)
[0161] 7 wt % Y.sub.2O.sub.3--ZrO.sub.2 powder (Tosoh Corporation,
TZ-4YS) was subjected to press molding (pressure: 25 MPa). Then,
this molded body was heat-treated in an air atmosphere at
1500.degree. C. for 5 hours. The density .rho. was 9.91
g/cm.sup.3.
(3) Measurement of Thermal Conductivity
[0162] Each of the evaluation sample (Hf.sub.6Ta.sub.2O.sub.17) and
the comparative sample (7 wt % Y.sub.2O.sub.3--ZrO.sub.2) was
subjected to a laser flash method (according to JIS R 1611) to
measure thermal conductivities at 25.degree. C., 100.degree. C.,
200.degree. C., 300.degree. C., 400.degree. C., 500.degree. C.,
600.degree. C., 700.degree. C., 800.degree. C., 900.degree. C., and
1000.degree. C.
[0163] Since the thermal conductivity of a solid is affected by
pores, and becomes a low value when the solid includes pores,
correction was performed using a correction equation shown in the
following formula (7) (reference literature: C. Wan, et al., Acta
Mater., 58, 6166-6172 (2010)).
k'/k=1-4/3.phi. (7)
(wherein k' is the thermal conductivity of the specimen, k is the
thermal conductivity as a dense substance, and .phi. is the
porosity.)
[0164] Here, the measured value of thermal conductivity was
corrected using the above equation (7), and the corrected thermal
conductivity was used as an evaluation value.
[0165] FIG. 6 is a graph showing the results of Evaluation Test 1
and shows the temperature dependence of thermal conductivity.
[0166] As shown in FIG. 6, it was clarified that the thermal
conductivity of Hf.sub.6Ta.sub.2O.sub.17 consistently exhibited a
lower value than that of YSZ from room temperature to a high
temperature of 1300.degree. C.
Evaluation Test 2
[0167] The refractive indexes of Hf.sub.6Ta.sub.2O.sub.17 and
HfO.sub.2 (hafnia), which are the compounds that can form the
intermediate layers in the thermal barrier coatings according to
the embodiments of the present invention, were measured. In
addition, the refractive index of Al.sub.2O.sub.3 (alumina) as a
comparative sample was measured.
(1) Production of Evaluation Sample
(1-1) Sintered Body of Hf.sub.6Ta.sub.2O.sub.17
[0168] An evaluation sample was produced in the same manner as
Evaluation Test 1.
(1-2) Sintered Body of HfO.sub.2
[0169] HfO.sub.2 powder (99.99% or higher, EM Japan Co., Ltd.) was
subjected to press molding (pressure: 25 MPa). Then, this molded
body was heat-treated in an air atmosphere at 1600.degree. C. for 5
hours to produce a sintered body. The density .rho. was 9.91
g/cm.sup.3.
(2) Production of Comparative Sample
Sintered Body of Al.sub.2O.sub.3
[0170] Al.sub.2O.sub.3 powder (99.9999% or higher, TAIMEI CHEMICALS
CO., LTD.) was subjected to press molding (pressure: 25 MPa). Then,
this molded body was heat-treated in an air atmosphere at
1500.degree. C. for 5 hours to produce a sintered body. The density
.rho. was 3.97 g/cm.sup.3.
(3) Measurement of Refractive Index
[0171] The refractive index of each sample was measured in the
wavelength range of 500 to 2000 nm using a spectroscopic
ellipsometer (manufactured by Horiba, Ltd., trade name:
UVISEL).
[0172] FIG. 7 is a graph showing the results of this evaluation
test and shows the wavelength dependence of refractive index.
[0173] As shown in FIG. 7, it was clarified that the refractive
indexes of Hf.sub.6Ta.sub.2O.sub.17 and HfO.sub.2 consistently
exhibited higher values than that of Al.sub.2O.sub.3 in the
wavelength range of 500 to 2000 nm.
[0174] From this, it was considered that, when a HfO.sub.2 layer or
a Hf.sub.6Ta.sub.2O.sub.17 layer is provided on an Al.sub.2O.sub.3
layer, a great refractive index difference is formed between the
Al.sub.2O.sub.3 layer and the HfO.sub.2 layer or the
Hf.sub.6Ta.sub.2O.sub.17 layer, and thermal energy incident from
the outside can be effectively reflected.
Evaluation Test 3
[0175] Evaluation Test 3 was conducted in order to predict the
interface stability between a HfO.sub.2 layer and a
Hf.sub.6Ta.sub.2O.sub.17 layer.
[0176] HfO.sub.2 powder and Hf.sub.6Ta.sub.2O.sub.17 powder were
blended in a composition of 49.2 wt % and 50.8 wt %, respectively,
such that the volume fractions thereof were equal, and these
powders were mixed using a mortar.
[0177] The HfO.sub.2 powder and the Hf.sub.6Ta.sub.2O.sub.17 powder
used in Evaluation Test 3 were the same as the sintering powders
used in Evaluation Test 2 described above.
[0178] This mixed powder was press-molded (pressure: 25 MPa) and
then heat-treated in an air atmosphere at 1400.degree. C. for 20
hours.
[0179] X-ray diffraction was performed on the mixed powder before
heat treatment and the sintered body after heat treatment. The
results are shown in FIG. 8.
[0180] FIG. 8 is an X-ray diffraction pattern obtained in this
evaluation test.
[0181] As shown in FIG. 8, only diffraction lines of HfO.sub.2 and
Hf.sub.6Ta.sub.2O.sub.17 were detected for both the mixed powder
before heat treatment and the sintered body after heat treatment,
and it was confirmed that no reaction proceeded between HfO.sub.2
and Hf.sub.6Ta.sub.2O.sub.17.
Evaluation Test 4
[0182] Evaluation Test 4 was conducted in order to predict the
interface stability between an Al.sub.2O.sub.3 layer and a
Hf.sub.6Ta.sub.2O.sub.17 layer.
[0183] Al.sub.2O.sub.3 powder and Hf.sub.6Ta.sub.2O.sub.17 powder
were blended in a composition of 27.7 wt % and 72.3 wt %,
respectively, such that the volume fractions thereof were equal,
and these powders were mixed using a mortar.
[0184] The Al.sub.2O.sub.3 powder and the Hf.sub.6Ta.sub.2O.sub.17
powder used in Evaluation Test 4 were the same as the sintering
powders used in Evaluation Test 2 described above.
[0185] This mixed powder was press-molded (pressure: 25 MPa) and
then heat-treated in an air atmosphere at 1400.degree. C. for 20
hours.
[0186] X-ray diffraction was performed on the mixed powder before
heat treatment and the sintered body after heat treatment. The
results are shown in FIG. 9.
[0187] FIG. 9 is an X-ray diffraction pattern obtained in this
evaluation test.
[0188] As shown in FIG. 9, only diffraction lines of
Al.sub.2O.sub.3 and Hf.sub.6Ta.sub.2O.sub.17 were detected for both
the mixed powder before heat treatment and the sintered body after
heat treatment, and it was confirmed that no reaction proceeded
between Al.sub.2O.sub.3 and Hf.sub.6Ta.sub.2O.sub.17.
Evaluation Test 5
[0189] Evaluation Test 5 was conducted in order to predict the
interface stability between a Hf.sub.6Ta.sub.2O.sub.17 layer and a
YTa.sub.3O.sub.9 layer.
[0190] Hf.sub.6Ta.sub.2O.sub.17 powder and YTa.sub.3O.sub.9 powder
were blended in a composition of 58.0 wt % and 42.0 wt %,
respectively, such that the volume fractions thereof were equal,
and these powders were mixed using a mortar.
[0191] This mixed powder was press-molded (pressure: 25 MPa) and
then heat-treated in an air atmosphere at 1400.degree. C. for 20
hours.
[0192] The Hf.sub.6Ta.sub.2O.sub.17 powder used in Evaluation Test
5 was the same as the sintering powder used in Evaluation Test 1
described above.
[0193] Meanwhile, the YTa.sub.3O.sub.9 powder was produced by the
following procedure.
[0194] 28 g (0.072 mol) of Y(NO.sub.3).sub.3.6H.sub.2O powder
(manufactured by KANTO CHEMICAL CO., INC.) having a purity of
99.99% or higher was put into 713 g of distilled water contained in
a reactor made of a fluorine resin, and the mixture was stirred at
room temperature (25.degree. C.) for 1 hour to obtain a colorless
transparent aqueous solution.
[0195] Next, 540 g (9 mol) of urea was added to this aqueous
solution, and the mixture was stirred at room temperature
(25.degree. C.) for 1 hour. Then, 50 g (0.113 mol) of
Ta.sub.2O.sub.5 powder (manufactured by RARE METALLIC Co., Ltd.)
having a purity of 99.9% or higher was added to the obtained
colorless transparent aqueous solution, and the mixture was stirred
at room temperature (25.degree. C.) for 7 hours to obtain a
suspension.
[0196] Next, the suspension was heated to 95.degree. C. and reacted
(urea hydrolysis reaction) with stirring under reflux cooling
(reaction time: 14 hours). Then, the obtained reaction solution was
centrifuged at 25.degree. C. and 4800 rpm for 30 minutes, and the
gel in the lower layer was collected. This gel was put into a large
amount of distilled water, and the mixture was sufficiently
stirred. Then, the mixture was centrifuged under the same
conditions as above, and the gel in the lower layer was
collected.
[0197] Then, the precipitate was heated in an air atmosphere at
120.degree. C. for 14 hours to obtain dried powder. Next, the dried
powder was sieved (100 mesh) to collect fine powder. This fine
powder was subjected to press molding (pressure: 25 MPa) and then
heat-treated in an air atmosphere at 1700.degree. C. for 1 hour.
The obtained sample was dry-ground in a mortar at room temperature
to obtain fine powder. X-ray diffraction measurement was performed
on the fine powder to confirm that the fine powder had an
orthorhombic crystal system composed of YTa.sub.3O.sub.9.
[0198] X-ray diffraction was performed on the mixed powder before
heat treatment and the sintered body after heat treatment. The
results are shown in FIG. 10.
[0199] FIG. 10 is an X-ray diffraction pattern obtained in this
evaluation test.
[0200] As shown in FIG. 10, generation of hetero phase due to the
heat treatment was very little, and it was confirmed that the
reaction between Hf.sub.6Ta.sub.2O.sub.17 and YTa.sub.3O.sub.9 was
slight.
Evaluation Test 6
[0201] Evaluation Test 6 was conducted in order to predict the
interface stability between an Al.sub.2O.sub.3 layer and a
YTa.sub.3O.sub.9 layer.
[0202] Al.sub.2O.sub.3 powder and YTa.sub.3O.sub.9 powder were
blended in a composition of 34.5 wt % and 65.5 wt %, respectively,
such that the volume fractions thereof were equal, and these
powders were mixed using a mortar.
[0203] The Al.sub.2O.sub.3 powder used in Evaluation Test 6 was the
same as the sintering powder used in Evaluation Test 2 described
above, and the YTa.sub.3O.sub.9 powder used in Evaluation Test 6
was the same as the sintering powder used in Evaluation Test 5
described above.
[0204] This mixed powder was press-molded (pressure: 25 MPa) and
then heat-treated in an air atmosphere at 1400.degree. C. for 20
hours.
[0205] X-ray diffraction was performed on the mixed powder before
heat treatment and the sintered body after heat treatment. The
results are shown in FIG. 11.
[0206] FIG. 11 is an X-ray diffraction pattern obtained in this
evaluation test.
[0207] As shown in FIG. 11, strong diffraction lines of
AlTaO.sub.4, etc., were detected due to the heat treatment, and it
was confirmed that reaction proceeded between Al.sub.2O.sub.3 and
YTa.sub.3O.sub.9.
EXAMPLE 1
[0208] A thermal barrier coating was produced by the following
method.
[0209] As a substrate for forming the thermal barrier coating, a
plate made of SUS430 stainless steel and having a length of 50 mm,
a width of 75 mm, and a thickness of 2 mm was prepared, and a
thermally sprayed coating having a thickness of 120 .mu.m was
formed on the substrate by high velocity flame spraying using
CoNiCrAlY powder (particle size: 16 to 45 .mu.m) as a spraying
material.
[0210] Subsequently, a thermally sprayed coating having a thickness
of 20 .mu.m was formed on the thermally sprayed coating formed
immediately before, by suspension plasma spraying using a HfO.sub.2
slurry (solid content: 20 wt %, solvent: water, particle size: 0.8
to 13.2 .mu.m) as a spraying material.
[0211] Subsequently, a thermally sprayed coating having a thickness
of 250 .mu.m was formed on the thermally sprayed coating formed
immediately before, by suspension plasma spraying using a
YbTa.sub.3O.sub.9 slurry (solid content: 25 wt %, solvent: ethanol,
particle size: 0.2 to 1.3 .mu.m) as a spraying material.
[0212] Through these steps, a thermal barrier coating in which a
CoNiCrAlY layer, a HfO.sub.2 layer, and a YbTa.sub.3O.sub.9 layer
were laminated in this order on the plate made of SUS430 stainless
steel was produced.
[0213] FIG. 12 is a photograph obtained when the sample (thermal
barrier coating) produced as described above was cut and the
cross-section of the sample was observed with a scanning electron
microscope (SEM).
[0214] The thermal barrier coating formed on the substrate has a
structure in which a metal bonding layer (CoNiCrAlY), an
intermediate layer (HfO.sub.2), and a thermal barrier layer
(YbTa.sub.3O.sub.9) are laminated in this order from the substrate
(SUS430) side as shown in FIG. 12.
[0215] The thermal barrier layer, which is the outermost layer, has
a segment structure including a plurality of columnar structures
erected so as to extend from the substrate side to the outermost
layer side. The number of columnar structures included in the
segment structure (segment number) was 9 (structures/mm) per unit
length. Since a minute gap is present between adjacent columnar
structures in the structure and thus residual stress is less likely
to occur, even if the substrate and each layer formed thereon
thermally expands or thermally contracts under heat cycle
conditions, damage is less likely to occur.
REFERENCE SIGNS LIST
[0216] 1, 2 thermal barrier coating
[0217] 11, 21 metal bonding layer
[0218] 12 alumina layer
[0219] 13, 23 first intermediate layer
[0220] 14, 24 second intermediate layer
[0221] 14a outer second intermediate layer
[0222] 14b inner second intermediate layer
[0223] 15, 25 thermal barrier layer
[0224] 15a to 15h columnar structure
[0225] 16, 26 intermediate layer
* * * * *