U.S. patent application number 16/878965 was filed with the patent office on 2020-11-26 for heat pipe assembly and method.
The applicant listed for this patent is Thermal Corp.. Invention is credited to Nelson J. Gernert, Pablo Hidalgo, Mark T. North.
Application Number | 20200370838 16/878965 |
Document ID | / |
Family ID | 1000004859331 |
Filed Date | 2020-11-26 |




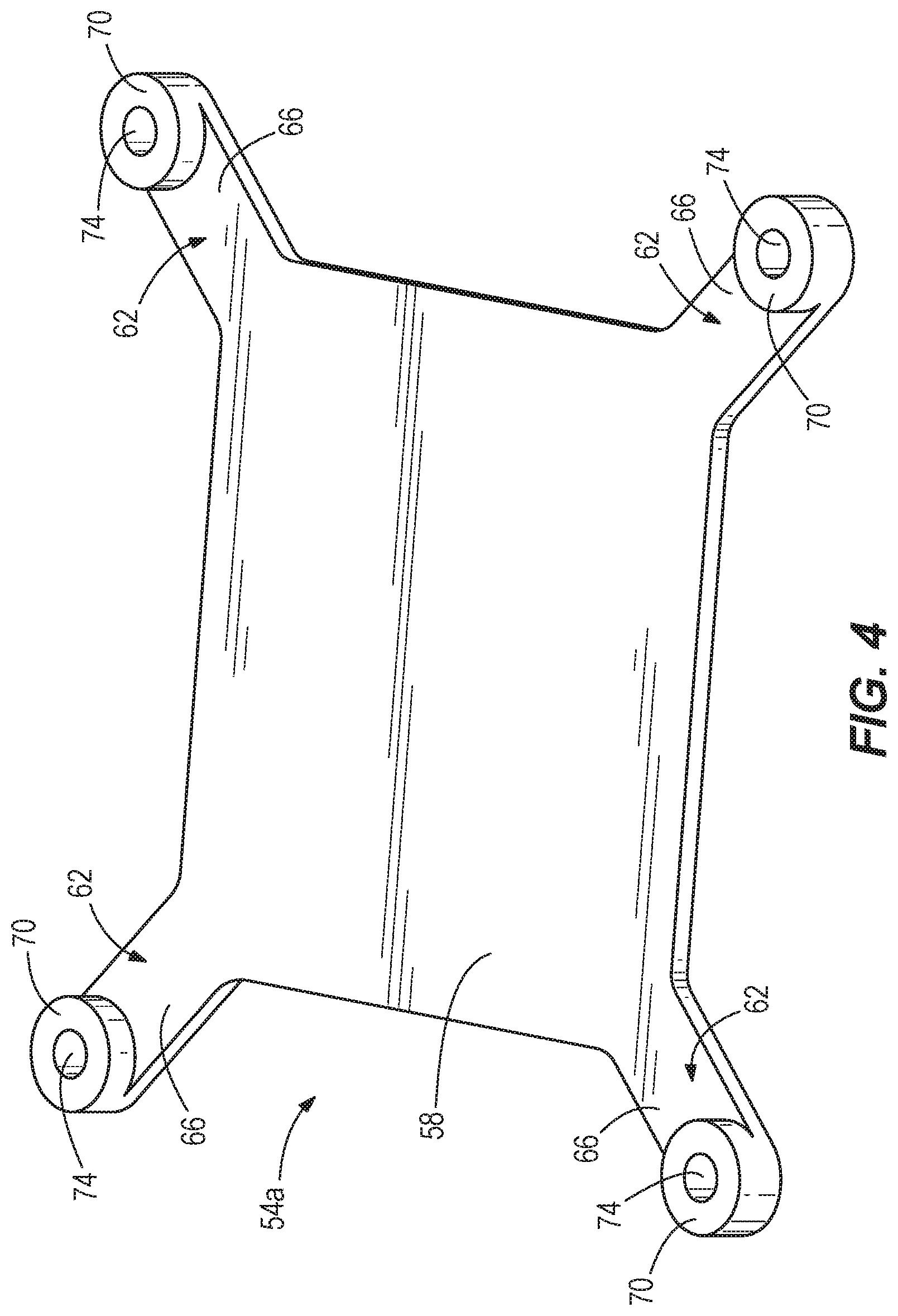
United States Patent
Application |
20200370838 |
Kind Code |
A1 |
North; Mark T. ; et
al. |
November 26, 2020 |
HEAT PIPE ASSEMBLY AND METHOD
Abstract
A heat transfer system includes a housing, an annealed heat pipe
coupled to the housing, and a heat source coupled to the housing.
The heat pipe exerts a biasing force in a direction toward the heat
source when the heat pipe is in thermal communication with the heat
source.
Inventors: |
North; Mark T.; (Lancaster,
PA) ; Hidalgo; Pablo; (Lancaster, PA) ;
Gernert; Nelson J.; (Elizabethtown, PA) |
|
Applicant: |
Name |
City |
State |
Country |
Type |
Thermal Corp. |
Willmington |
DE |
US |
|
|
Family ID: |
1000004859331 |
Appl. No.: |
16/878965 |
Filed: |
May 20, 2020 |
Related U.S. Patent Documents
|
|
|
|
|
|
Application
Number |
Filing Date |
Patent Number |
|
|
62850661 |
May 21, 2019 |
|
|
|
Current U.S.
Class: |
1/1 |
Current CPC
Class: |
F28D 2015/0216 20130101;
F28D 15/0275 20130101 |
International
Class: |
F28D 15/02 20060101
F28D015/02 |
Claims
1. A heat transfer system comprising: a housing; an annealed heat
pipe coupled to the housing; and a heat source coupled to the
housing, wherein the heat pipe is configured to exert a biasing
force in a direction toward the heat source when the heat pipe is
in thermal communication with the heat source.
2. The heat transfer system of claim 1, wherein the heat pipe has a
curved profile.
3. The heat transfer system of claim 2, wherein the heat pipe has a
J-shaped curved profile.
4. The heat transfer system of claim 1, wherein the heat pipe
includes a bellows.
5. The heat transfer system of claim 1, wherein at least a portion
of the heat pipe includes a flattened cross-sectional shape.
6. The heat transfer system of claim 1, wherein the heat pipe
includes a first end and a second, opposite end, wherein the second
end is fixed to the housing and the first end is movable to
different positions with respect to the second end.
7. The heat transfer system of claim 6, wherein the housing
includes a first mounting wall and a second, opposite mounting wall
spaced from the first mounting wall, wherein the first and second
mounting walls define an interior cavity therebetween in the
housing, wherein the second end of the heat pipe is fixed to the
second mounting wall.
8. The heat transfer system of claim 7, wherein the first end of
the heat pipe is disposed inside the interior cavity, and is spaced
from both the first and second mounting walls.
9. The heat transfer system of claim 7, wherein the heat source is
in direct contact with the first mounting wall.
10. The heat transfer system of claim 6, further comprising at
least one adjustable fastener configured to pull the first end of
the heat pipe toward the heat source.
11. The heat transfer system of claim 6, further comprising a heat
plate, wherein the first end of the heat pipe is coupled to the
heat plate, wherein the heat source is disposed between the heat
plate and the first mounting wall.
12. The heat transfer system of claim 11, further comprising at
least one fastener that is configured to both couple the heat plate
to the housing and to adjust pressure on the heat source.
13. The heat transfer system of claim 1, wherein at least one
portion of the heat pipe is out of plane with respect to a
different portion of the heat pipe when the heat pipe is in thermal
communication with the heat source.
14. The heat transfer system of claim 13, wherein the at least one
portion is out of plane with respect to the different portion in an
unstressed state of the heat pipe.
15. The heat transfer system of claim 1, wherein the heat pipe is a
first heat pipe, further comprising a second heat pipe, wherein the
first and second heat pipes each include an evaporator region that
is coupled to the heat source so as to receive heat from the heat
source and to move the heat away from the heat source.
16. The heat transfer system of claim 15, wherein the first and
second heat pipes each include a condenser region that is fixed to
the housing.
17. The heat transfer system of claim 15, wherein the first heat
pipe is configured to move heat away from the heat source in a
first direction, and the second heat pipe is configured to move
heat away from the heat source in a second, opposite direction.
18. The heat transfer system of claim 17, wherein the first heat
pipe and the second heat pipe each have a J-shaped profile.
19. The heat transfer system of claim 18, wherein the J-shaped
profiles face in opposite directions.
20. A heat transfer system comprising: a housing; a first annealed
heat pipe coupled to the housing, the first heat pipe having an
evaporator region and a condenser region; a second annealed heat
pipe coupled to the housing, the second heat pipe having an
evaporator region and a condenser region; a heat source coupled to
the housing; a heat plate, wherein the evaporator regions of the
first and second heat pipes are both coupled to the heat plate;
wherein the evaporator region of the first heat pipe is positioned
relative to the heat source so as to remove heat from the heat
source and to direct the heat in a first direction, and wherein the
evaporator region of the second heat pipe is positioned relative to
the heat source so as to remove heat from the heat source and to
direct the heat in a second direction different from the first
direction.
21. A heat transfer system comprising: a housing; a first annealed
heat pipe coupled to the housing, the first heat pipe having an
evaporator region and a condenser region, wherein the evaporator
region and the condenser region of the first heat pipe are out of
plane with respect to one another in an unstressed state of the
first heat pipe; a second annealed heat pipe coupled to the
housing, the second heat pipe having an evaporator region and a
condenser region, wherein the evaporator region and the condenser
region of the second heat pipe are out of plane with respect to one
another in an unstressed state of the second heat pipe; wherein the
evaporator regions of the first and second heat pipes extend
parallel to one another, and wherein the condenser regions of the
first and second heat pipes extend parallel to one another.
22. A heat transfer system comprising: a housing; a heat pipe
coupled to the housing; and a heat source coupled to the housing,
wherein the heat pipe is configured to exert a biasing force in a
direction away from the heat source when the heat pipe is in
thermal communication with the heat source.
Description
CROSS-REFERENCE TO RELATED APPLICATIONS
[0001] This patent application claims priority to U.S. patent
application Ser. No. 62/850,661, filed on May 21, 2019, the entire
contents of which are incorporated herein by reference.
BACKGROUND
[0002] Heat pipes are commonly used to remove heat from a heat
source, such as an electronic component. Heat pipes may be made,
for example, of a conductive material such as copper and contain a
phase-change working fluid. The phase changes of the working fluid
are used to dissipate heat from the heat source. Heat pipes
commonly include an evaporator region that is in thermal
communication with the heat source to receive heat from the heat
source, and a condenser region in thermal communication with the
evaporator region, where the heat is dissipated to the external
environment. Many heat pipes are hollow, and may include a wick
material disposed along an interior wall of the heat pipe to
generate a capillary action to facilitate return of working fluid
from the condenser region to the evaporator region.
[0003] In brief, the working fluid in the evaporator region of the
heat pipe absorbs heat generated by and transferred from the heat
source. The absorbed heat from the heat source vaporizes the
working fluid (i.e., changes the phase of the working fluid),
thereby transferring the heat away from the heat source. The heated
vapor then flows to the cooler condenser region of the heat pipe,
where the vaporized working fluid condenses and changes phase again
back to its fluid state. Condensation of the vaporized working
fluid dissipates the absorbed heat for removal from the condenser
region of the heat pipe to the external environment. The cooled
working fluid then returns to the evaporator region, often
facilitated by capillary action provided by a wick structure. Once
returned to the evaporator region of the heat pipe, the working
fluid again absorbs heat from the heat source. This heat
dissipation cycle can be continuously repeated as long as the heat
source generates heat.
SUMMARY
[0004] In accordance with one embodiment, a heat transfer system
includes a housing, a heat pipe coupled to the housing, and a heat
source coupled to the housing. The heat pipe exerts a biasing force
in a direction away from the heat source when the heat pipe is in
thermal communication with the heat source.
[0005] In accordance with another embodiment, a heat transfer
system includes a housing, an annealed heat pipe coupled to the
housing, a heat source coupled to the housing, and an adjustable
fastener that thermally couples the heat pipe to the heat
source.
[0006] In accordance with another embodiment, a heat transfer
system includes a housing, and an annealed heat pipe having a first
end and a second end, the second end coupled to the housing. The
heat transfer system further includes a heat source coupled to the
housing, and an adjustable fastener that thermally couples the
first end of the heat pipe to the heat source. The adjustable
fastener exerts adjustable pressure on the heat source.
[0007] In accordance with another embodiment, a heat transfer
system includes a housing, and a first annealed heat pipe coupled
to the housing, the first heat pipe having an evaporator region and
a condenser region. The heat transfer system further includes a
second annealed heat pipe coupled to the housing, the second heat
pipe having an evaporator region and a condenser region. The heat
transfer system further includes a heat source coupled to the
housing, as well as a heat plate. The evaporator regions of the
first and second heat pipes are both coupled to the heat plate. The
evaporator region of the first heat pipe is positioned relative to
the heat source so as to remove heat from the heat source and to
direct the heat in a first direction. The evaporator region of the
second heat pipe is positioned relative to the heat source so as to
remove heat from the heat source and to direct the heat in a second
direction different from the first direction.
[0008] In accordance with another embodiment, a heat transfer
system includes a housing, and a first annealed heat pipe coupled
to the housing. The first heat pipe has an evaporator region and a
condenser region separated by an intermediate region defining at
least one reversal of direction of the annealed heat pipe, the
evaporator and condenser regions of the first heat pipe both facing
in a first direction. The heat transfer system further includes a
second annealed heat pipe coupled to the housing, the second heat
pipe having an evaporator region and a condenser region separated
by an intermediate region defining at least one reversal of
direction of the first heat pipe, the evaporator and condenser
regions of the second heat pipe both facing in a second direction
that is opposite to the first direction.
[0009] In accordance with another embodiment, a heat transfer
system includes a housing and a first annealed heat pipe coupled to
the housing, the first heat pipe having an evaporator region and a
condenser region. The evaporator region and the condenser region of
the first heat pipe are out of plane with respect to one another in
an unstressed state of the first heat pipe. The heat transfer
system further includes a second annealed heat pipe coupled to the
housing, the second heat pipe having an evaporator region and a
condenser region. The evaporator region and the condenser region of
the second heat pipe are out of plane with respect to one another
in an unstressed state of the second heat pipe. The evaporator
regions of the first and second heat pipes extend parallel to one
another, and the condenser regions of the first and second heat
pipes extend parallel to one another.
[0010] In accordance with another embodiment, a heat transfer
system includes a housing, and a first heat pipe coupled to the
housing. The first heat pipe comprises a body of annealed metal and
has an evaporator region and a condenser region. The evaporator
region and the condenser region of the first heat pipe are out of
plane with respect to one another in at least one of a stressed
state and an unstressed state of the first heat pipe. The heat
transfer system further includes a second heat pipe coupled to the
housing, the second heat pipe comprises a body of annealed metal
and has an evaporator region and a condenser region. The evaporator
region and the condenser region of the second heat pipe are out of
plane with respect to one another in at least one of a stressed
state and an unstressed state of the second heat pipe. The
evaporator regions of the first and second heat pipes are spaced
from each other by a first distance, and the condenser regions of
the first and second heat pipes are spaced from each other by a
second distance. The second distance is greater than the first
distance.
[0011] Other embodiments and aspects of the various embodiments
will become apparent by consideration of the detailed description
and accompanying drawings.
BRIEF DESCRIPTION OF THE DRAWINGS
[0012] FIG. 1 is a perspective view of a spring heat pipe according
to one embodiment.
[0013] FIG. 2 is a perspective view of a spring heat pipe according
to another embodiment, with the inclusion of a flexible
bellows.
[0014] FIG. 3 is a perspective view of a heat transfer system
according to one embodiment that includes use of multiple spring
heat pipes and a heat plate.
[0015] FIG. 4 is a perspective view of a heat plate according to
another embodiment.
DETAILED DESCRIPTION
[0016] Before any embodiments are explained in detail, it is to be
understood that embodiments are not limited in their application to
the details of construction and the arrangement of components set
forth in the following description or illustrated in the following
drawings. Other embodiments are possible and embodiments described
and illustrated are capable of being practiced or of being carried
out in various ways.
[0017] FIG. 1 illustrates one exemplary embodiment of a heat pipe
10 having a first end 14, a second end 18, and an intermediate
region 22 disposed between the first and second ends 14, 18 along a
length of the heat pipe 10. As illustrated in FIG. 1, in some
embodiments the heat pipe 10 has a generally curved, shape or
profile (for example an "S" shape). In some embodiments, the first
end 14 and the second end 18 extend linearly and parallel to one
another, and at least a portion of the intermediate region 22 has a
bend that curves between the first end 14 and the second end 18.
Other embodiments include different shapes than those illustrated.
For example, in some embodiments the heat pipe 10 may have a
generally "J" shape, a "U" shape, an "S" shape, a "V" shape, an "L"
shape, or various other shapes having for example one, two, or more
bends therein.
[0018] The heat pipe 10 includes an evaporator region 26 and a
condenser region 30. In the illustrated embodiment, the evaporator
region 26 is located at the first end 14 and the condenser region
30 is located at the second end 18, although in other embodiments
the evaporator region 26 and/or the condenser region 30 may be
located at other areas of the heat pipe 10. For example, the
evaporator region 26 and/or the condenser region 30 may overlap
with or be located entirely within the intermediate region 22.
Alternatively, the evaporator region 26 may be located at the
second end 18, and the condenser region 30 may be located at the
first end 14.
[0019] The heat pipe 10 may be made of any of a number of suitable
materials, including copper, aluminum, stainless steel, titanium,
any alloy of these or other metals, or other materials. In some
embodiments, the heat pipe 10 includes a hollow, interior vapor
chamber sized to contain a working fluid. The working fluid may
include, for example, water, methanol, ammonia, or various other
types of suitable fluids. The materials selected for the heat pipe
10 and/or the fluids selected for the working fluid may depend, for
example, on the environment in which the heat pipe 10 will be used,
with some materials and working fluids being more suitable than
others, for example, in low-gravity and low-temperature
environments.
[0020] In some embodiments, the heat pipe 10 may additionally
include a capillary wick structure for moving the working fluid
within the heat pipe 10. The capillary wick structure may extend at
least partially within the heat pipe 10 from the condenser region
30 to the evaporator region 26, lining an interior surface of the
vapor chamber. In some embodiments, the wick structure is located
at the evaporator and condenser regions 26, 30, whereas in other
embodiments either or both of the evaporator and condenser regions
26, 30 do not include a wick structure. Also in some embodiments,
the wick structure extends without interruption along any part or
all of the distance between the evaporator and condenser regions
26, 30. The wick structure may be made, for example, from sintered
or brazed copper powder or other suitable materials, and/or may
include or be defined by axial grooves, one or more mesh objects,
or other capillary structures along the interior of the heat pipe
10 that facilitate a wicking action. The capillary wick structure
permits the heat pipe 10 to be used in low-gravity environments,
and in other applications in which force is needed to move the
working fluid in a desired direction (e.g., from the condenser
region 30 toward the evaporator region 26).
[0021] When heat is applied to the working fluid at the evaporator
region 26, the working fluid evaporates, changing phase into a
vapor state. The working fluid flows through the interior vapor
chamber in the vapor state from the evaporator region 26 to the
condenser region 30. The working fluid then discharges heat at the
condenser region 30 as the heat pipe discharges heat to another
object or area in thermal communication with the condenser region
30, and changes phase again back to a liquid state at the condenser
region 30. The condensed working fluid returns in the liquid state
to the evaporator region 26 through the wick structure (when
provided in some embodiments).
[0022] In some embodiments the heat pipe 10 has a generally
flattened, oval-shaped cross-section, extending along the entirety
of the heat pipe 10 from the first end 14 to the second end 18. An
example of such a flattened cross-sectional shape is shown in the
heat pipes illustrated in FIG. 2, which also applies to any other
heat pipes embodiments described and/or illustrated herein. In
other embodiments, the heat pipe 10 may have a more circular-shaped
cross-section or a cross-section with another shape (e.g.,
rectangular, etc.). Additionally, in some embodiments, one portion
of the heat pipe 10 may have a first cross-sectional shape with
another portion of the heat pipe 10 having a different
cross-sectional shape. For example, the first end 14 and the second
end 18 may each have a generally flattened, oval-shape, or a
rectangular cross-sectional shape having at least one generally
flat surface, whereas the intermediate region 22 may have a
circular-shaped cross-section (see again the heat pipes illustrated
in FIG. 2, which include heat pipe sections having generally
flattened, oval cross-sectional shapes, and other heat pipe
sections having circulate-shaped cross sections).
[0023] In some embodiments, at least a portion of the
cross-sectional shape of each heat pipe 10 has a major diameter and
a smaller minor diameter. In such embodiments, the heat pipe 10
flexes or bends with greater ease about the major diameter. With
reference to the embodiment of FIG. 3, for example (described in
greater detail below) in which the illustrated heat pipes have a
generally flattened cross-sectional shape along their lengths to
define flat top and bottom heat pipe surfaces, the flattened
cross-sectional shape better enables each heat pipe 10 to flex in
an upward and downward direction. This flexure changes the distance
(e.g., vertical distance) between the opposite ends 14, 18 of the
heat pipe 10. Stated in another way, this flexure changes the drop
or rise of one end 14 of the heat pipe 10 with respect to the other
end 18. Although the flattened oval cross-sectional shape of the
heat pipe 10 has this feature, it will be appreciated that other
heat pipe cross-sectional shapes, including others having a minor
axis and a larger major axis about which the heat pipe 10 can more
readily flex are possible, such as flattened rectangular
cross-sectional shapes, and irregular flattened shapes. In all such
embodiments, any portion or all of the length of each heat pipe 10
can be provided with such shapes to enable enhanced flexibility of
the heat pipe 10.
[0024] In some embodiments, the heat pipe 10 is shaped so that one
portion (e.g., the second end 18) of the heat pipe 10 is
manufactured or otherwise formed out of plane with respect to
another, different portion (e.g., the first end 14). In this
manner, the second end 18 of the heat pipe 10 is generally offset
relative to the first end 14 (i.e., has a drop or rise out of the
plane in which the first end 14, or second end 18 lie). In other
embodiments, when the heat pipe 10 is manufactured, the first and
second ends 14, 18 are in a common plane.
[0025] The manufactured heat pipe 10 can function as a curved
cantilever, such that when force is applied to deflect the first or
second ends 14, 18 of the heat pipe 10 relative to one another, a
stored tensile stress or spring-like biasing force is created in
the heat pipe 10 that seeks to return the heat pipe 10 to its
unstressed state or shape. Consequently, when the deflecting force
is removed, the heat pipe 10 returns to its original, unstressed
shape or state. In some embodiments, it is particularly
advantageous to provide a degree of control over the force exerted
by the heat pipe 10 against an object (e.g., computer chip) to be
cooled, and/or to enable a range of suitable forces to be applied
to such an object. Greater lengths of the heat pipe 10 enable a
longer cantilever, and therefore greater control over the amount of
force the heat pipe 10 exerts upon the object to be cooled--or
greater control over the amount of reaction force exerted by the
heat pipe 10 when deflected as described above. In some
applications, the ability to apply a specific force or range of
forces by the heat pipe 10 upon the object to be cooled is
important, such as for applications in which the object to be
cooled can be easily damaged. Therefore, the longer cantilevered
arm provided by the heat pipe 10 and the flattened cross-sectional
shape of the heat pipe 10 better enable the heat pipe 10 to flex,
and enable a greater degree of control over the force applied by
the heat pipe 10 when flexed.
[0026] Although relatively long heat pipes 10 can be straight in
order to provide the force control described above, such a shape
can greatly limit the package shape and/or size of devices in which
the heat pipe 10 is used. Therefore, some curved heat pipe 10
(e.g., U-shaped or J-shaped heat pipes) can provide a smaller
footprint or volume required for the heat pipe 10 in various
applications. Similarly, other curved heat pipe shapes (as
described herein) can be used to provide similar advantages. In
some embodiments for example, the heat pipe 10 may look like a
coiled spring, winding around multiple times in the same
direction.
[0027] With continued reference to FIG. 1, during manufacture of
the heat pipe 10, the heat pipe 10 may first be bent or otherwise
shaped (e.g., stamped, etc.) generally into its curved shape. The
heat pipe 10 can then be annealed (e.g., in an oven), thereby
exposing the heat pipe to an elevated temperature to soften the
metal of the heat pipe. The stiffness of the heat pipe 10 can
therefore be significantly reduced by being thus annealed, which
results in a heat pipe 10 that can be more easily flexed, and that
can flex in response to a range of forces under greater control.
The annealed feature of the heat pipes 10 can be used as yet
another design option (in addition to the longer cantilever of the
curved heat pipe 10 and the flattened cross-sectional shape of the
heat pipe 10 as discussed above) to better enable the heat pipe 10
to flex, and to enable a greater degree of control over the force
applied by the heat pipe 10 when flexed. In some embodiments, the
heat pipe 10 may be shaped (e.g., stamped, etc.) into shapes other
than that illustrated prior to being annealed.
[0028] In some embodiments, the heat pipe 10 can be further adapted
to better enable the heat pipe 10 to flex as desired (again, for a
greater degree of control over force applied by the heat pipe 10
when flexed). For example, FIG. 2 illustrates a modified heat pipe
10a that includes a bellows 114 located along the length of the
heat pipe 10a. The bellows 114 can be used to alter the spring
constant of the heat pipe 10a. While only a single bellows 114 is
illustrated, in other embodiments the heat pipe 10a may include a
plurality of bellows 114 or bellows regions. Additionally, the heat
pipe 10a may include one or more bellows 114 at locations other
than that illustrated.
[0029] In some embodiments the heat pipe 10 can be further adapted
to better enable the heat pipe 10 to flex as desired by reducing
the wall thickness of the heat pipe 10 at one or more locations
along the heat pipe 10 in comparison to other (thicker) wall
thicknesses at other locations along the heat pipe 10. For example,
in one or more regions of the heat pipe 10, the wall of the heat
pipe 10 is thinner than adjacent regions along the length of the
heat pipe 10 in order to enable the heat pipe 10 to flex in the
thinner regions. In each thinner-walled region, the entire
circumference of the heat pipe cross-sectional shape can be
thinner, or only selected areas of the cross-sectional shape are
thinner (e.g., thinner only along flattened sides of the heat pipe
10, thinner only along the major or wider sides of the heat pipe
10, thinner only along the minor or narrower sides of the heat pipe
10, and the like). All such thinned heat pipe regions enables the
design of the heat pipe 10 to be tailored to flex as desired for
any particular application and to exert a desired force or force
ranges upon the heat source 50.
[0030] When a deflecting force is applied to the heat pipe 10 as
described above to create a stored tensile stress or spring-like
biasing force, the heat pipe 10 will have a spring constant value
that depends at least in part upon the size and shape of the heat
pipe 10, the materials used to create the heat pipe 10, the amount
of deflecting force applied to the heat pipe, and the degree of
annealing that occurs during manufacturing of the heat pipe 10.
[0031] With reference now to FIG. 3, one or more of the spring-like
heat pipes 10 may be used in conjunction with a heat transfer
system 38 to both move heat away from a heat source 50 (e.g.,
circuit board, shown in phantom in FIG. 3), as well as to help
secure one or more of the components of the heat transfer system 38
in place. For example, as illustrated in the embodiment of FIG. 3,
the heat transfer system 38 includes a housing 42, which may have
any number of a variety of different shapes and sizes (e.g.,
rectangular-shaped, square-shaped, oval-shaped, irregularly-shaped,
etc.) within which are housed multiple heat pipes 10. In the
illustrated embodiment of FIG. 3, the housing 42 is a sealed
housing, and includes a cover 48 (shown in phantom in FIG. 3)
releasably and removably secured to the rest of the housing 42 via
screws or other suitable fasteners (not shown) received within
fastener holes 92, 96 of the housing 42 and its cover 48,
respectively. In the illustrated embodiment of FIG. 3, the fastener
holes 92 are located in the corners of the housing 42 and its cover
48, although such fastener holes 92 can be located in any other
positions of the housing 42 and its cover 48 as desired. With
continued reference to the illustrated embodiment of FIG. 3 by way
of example, all components of the heat transfer system 38 are
located inside the housing 42 and are sealed within the housing 42.
The interior chamber of the housing 42 can have a fluid-tight seal,
or in other more demanding environments and applications, the
housing 42 can be hermetically sealed, either of which protects the
heat source 50 from exposure to damaging environmental conditions
such as dust, dirt, and other debris, water, oil or other fluids,
and the like. In some embodiments, the housing 42 is a modular
assembly that can be installed and removed in a desired application
as one integral assembly. Also in some embodiments, other than one
or more electrical connectors on the housing 42 that can be
connected and disconnected preferably without tools, the entire
heat transfer system 38 can be installed in a desired location with
the use of one or more releasable fasteners, and can be removed by
release of such fastener(s). In this manner, the heat transfer
system 38, with its internal heat pipes 10 and heat source 50, can
be easily and readily removed and replaced as one integral
assembly, in some cases without disturbing the seal that seals the
internal components from the surrounding environment.
[0032] As illustrated in FIG. 3, the illustrated housing 42
includes a first mounting wall 48 (e.g., an upper wall including a
planar or other-shaped surface, such as defined by the cover 48 in
the illustrated embodiment of FIG. 3). The first mounting wall 48
can therefore define at least part of the housing 42. In some
cases, at least part of a housing seal (described above) is defined
or located between the first mounting wall 48 and the rest of the
housing 42. A heat source may be coupled to the first mounting wall
48 and located within the interior of the housing 42. The heat
source 50 may be a computer chip, circuit board, sensor, or other
electronic component that generates heat. In some embodiments, the
heat source 50 is fixed (e.g., via solder, adhesive, fasteners, or
other fastening elements or substances) directly to the first
mounting wall 48. In yet other embodiments, the heat source 50
merely sits or rests (e.g., loosely) on the first mounting wall 48,
without being directly fixed to the first mounting wall 48.
[0033] With continued reference to FIG. 3, the heat transfer system
38 may include multiple heat pipes 10, and may further include a
heat transfer plate 54. In some embodiments, fasteners 56 are used
to couple the heat transfer plate 54 to the first mounting wall 48.
For example, the fasteners 56 can be screws or other threaded
fasteners that are received within apertures in the heat transfer
plate 54 and that also extend into apertures 90 (e.g., threaded
apertures 90) in the cover 48 to couple the heat transfer plate 54
to the first mounting wall 48. The heat source 50 may be positioned
above the heat transfer plate 54 (e.g., sandwiched between the
first mounting wall 48 and the heat transfer plate 54 and held in
place frictionally or with fasteners between the first mounting
wall 48 and the heat transfer plate 54). In the illustrated
embodiment of FIG. 3, the first ends 14 of the heat pipes 10 are
coupled to (e.g., and restrained by) the heat transfer plate 54,
and the second ends 18 are spaced away from the first ends 14 in
opposite directions within the housing 42. The first ends 14 may be
restrained, for example, within channels of the heat transfer plate
54. As also illustrated in FIG. 3, the second end 18 of one of the
heat pipes 10 may be located at one end of the housing 42, whereas
the second end 18 of the other heat pipe 10 may be located at an
opposite end of the housing 42, with the first ends 14 generally
being located within a more central region of the housing 42.
Additionally, and as illustrated in FIG. 3, in some embodiments the
second ends 18 of the heat pipes 10 may be coupled to (e.g., and
restrained by) retention structures 44 (e.g., guides, rails,
brackets, etc.) within the housing 42. The heat pipes 10 may also
be shaped such that the first ends 14 are out of plane (e.g., lower
than, with reference to the orientation of FIG. 3) with respect to
the second ends 18, and such that the heat pipes 10 provide a
natural spring force in at least one direction when installed
within the housing 42. For example, the heat pipes 10 may be
positioned and shaped such that the first ends 14 exert a
reactionary force pulling the heat transfer plate 54 in a direction
away from the first mounting wall 48 when the fasteners 56 are
tightened to pull the heat plate 54 toward the heat source 50 and
the first mounting wall 48. Although in the illustrated embodiment
of FIG. 3 the second ends 18 of the heat pipes 10 are secured to
the housing 42 opposite the first mounting wall 48 in other
embodiments the second ends of the heat pipes 10 are instead
secured to the first mounting wall 48 and are shaped to exert the
same or similar reactionary force as described above when the
fasteners 56 are tightened to pull the heat plate 54 toward the
heat source 50 and the first mounting wall 48 Various other
embodiments include differently shaped housings, differently shaped
heat pipes, differently shaped heat transfer plates, and/or
different coupling locations for the ends of the heat pipes and the
heat transfer plates within the housing 42 than that
illustrated.
[0034] FIG. 4 illustrates a heat transfer plate 54a according to a
different embodiment. As illustrated in FIG. 4, in some embodiments
the heat transfer plate 54a may include an intermediate region 58
that is generally sized and shaped to fit over the heat source 50,
and to at least partially cover (e.g., substantially or entirely
cover) the heat source 50, thereby sandwiching the heat source 50
between the intermediate region 58 of the heat transfer plate 54a
and, for example, the first mounting wall 48. In the illustrated
embodiment of FIG. 4, the intermediate region 58 is a planar region
having a generally rectangular shape, although in other
embodiments, part or all of the intermediate region 58 may be
non-planar, and/or may have a different shape or size than that
illustrated. Additionally, one or more areas of the intermediate
region 58 may be flexible (e.g., made of thinner material than
other areas of the intermediate region 58), so as to facilitate
bending and/or shaping of the heat transfer plate 54a during use to
conform to and accommodate the shape and size of the heat source
50.
[0035] As also illustrated in FIG. 4, the heat transfer plate 54a
may further include at least one mounting region 62. In the
illustrated embodiment of FIG. 4, the heat transfer plate 54a
includes four mounting regions 62, each mounting region 62 being
disposed generally at a corner of the intermediate region 58. Other
embodiments may include different numbers and locations of mounting
regions 62 than that illustrated. With continued reference to FIG.
4, each mounting region 62 may include an arm 66 by which the heat
transfer plate 54a is connected for example to the first mounting
wall 48. The arms 66 can have any shape and size suitable for this
purpose, and can be relatively stiff or may flex when secured to
the first mounting wall 48. For example, the arms 66 in the
illustrated embodiment of FIG. 4 are integral with the heat
transfer plate 54a, and each include a thickened, distal end 70 at
which the heat transfer plate 54a may be connected, for example, to
the first mounting wall 48. The heat transfer plate 54a (and more
particularly, the arms 66 of the heat transfer plate 54 in the
illustrated embodiment of FIG. 4), can be provided with apertures
74 extending through the heat transfer plate 54 for attachment to
the first mounting wall 48. In the illustrated embodiment of FIG.
4, the apertures 74 extend through the distal end 70 of each arm
66, but can be located elsewhere in the heat transfer plate 54a in
other embodiments. Any number of apertures 74 can be used to secure
the heat transfer plate 54 to, for example, the first mounting wall
48, and in some embodiments can be internally threaded for mating
with fasteners.
[0036] In some embodiments, the heat transfer system 38 may further
include at least one fastener that is at least partially received
through each aperture 74 of the heat transfer plate 54a. For
example, the heat transfer system 38 may include four fasteners,
each of which is a threaded fastener for being threaded into a
respective one of the threaded apertures 74. Each fastener can have
a fastener head (not shown) disposed outside the housing 42 for
access and tightening or loosening by a user, and a fastener body
(also not shown) that extends through an aperture 90 (see FIG. 3)
in the first mounting wall 48 and into the threaded aperture 74. In
this manner, after the first mounting wall 48 (with the heat source
50 and any other components thereon) has been assembled to the rest
of the housing 42 (at which time access to the heat source 50, the
heat transfer plate 54, 54a, the heat pipes 10, and other
components within the housing 42 is limited or impossible), the
fasteners can still be adjusted from outside the housing 42 to
tighten or loosen the heat transfer plate 54, 54a against the heat
source 50. In some embodiments, the apertures 90 through which the
fasteners pass can each include a conventional seal (not shown) to
preserve the fluid-tight or hermetic seal of the housing 42
described above. Such adjustment can also therefore flex the heat
pipes 10 as described elsewhere herein without requiring user
access to the inside of the housing 42.
[0037] The heat transfer system 38 may further include at least one
biasing member (e.g., compression spring) disposed between the head
of the fastener 56 and the exterior of the first mounting wall 48.
The biasing members can exert a biasing force on the fasteners 56
in a direction away from the first mounting wall 48 and the heat
transfer plate 54, 54a, and can be used to prevent excessive force
exerted upon the heat transfer plate 54, 54a and the heat source 50
by overtightening the fasteners 56. The biasing members 56, in
combination with the threaded connection between the fasteners 56
and the mounting regions 62 (see FIG. 4, by way of example), may
thus exert a pulling force on the heat transfer plate 54, 54a
toward the first mounting wall 48, thereby pressing the plate's
intermediate region 58 (again, see FIG. 4 bay way of example)
against the heat source 50. This force creates a thermal bridge
between the heat source 50 and the heat transfer plate 54, 54a. In
some embodiments, this force can also be used to secure the heat
source 50 in place (e.g., frictionally) between the heat transfer
plate 54, 54a and the first mounting wall 48. In other embodiments,
the biasing members may be omitted, in which case the fasteners 56
may still be tightened to pull the heat transfer plate 54 against
the heat source 50 to secure the heat source 50 in place by
sandwiching the heat source 50 between the heat transfer plate 54,
54a and the first mounting wall 48.
[0038] In some embodiments, the evaporator region 26 of each heat
pipe 10 is coupled to or otherwise positioned on heat transfer
plate 54, 54a (e.g., the intermediate region 58 of the heat
transfer plate 54a in the illustrated embodiment of FIG. 4)
opposite the heat source 50. In these and other embodiments (and as
described above), the heat pipes 10 can take any shape desired. In
those embodiments in which the heat transfer system 38 includes two
or more heat pipes 10, significant space savings can be achieved
while still enjoying the benefits of a long cantilever arm for each
heat pipe by utilizing heat pipes that are curved, and that in some
embodiments have heat pipes shaped and positioned to be at least
partially nested or received within one another. For example, in
some embodiments the evaporator regions 26 of two "U"-shaped or
"J"-shaped heat pipes 10 are oriented adjacent one another such
that the first ends 14 extend generally parallel to and are spaced
apart from one another by a first distance, and such that the
second ends 18 (that include the condenser regions 30) extend
generally parallel to and are spaced apart from one another by a
second distance, the second distance being greater than the first
distance. In other embodiments, the distances between the heat
pipes 10 may vary as needed for any particular application or
environment. The ends of the heat pipes 10 also may face in
opposite directions, such that the evaporator ends 14 extend in
opposite directions with respect to one another to their respective
terminal ends, and the condenser ends 18 extend in opposite
directions with respect to one another to their respective terminal
ends. Portions of the heat pipes 10 may extend in an overlapping
configuration, where the first end 14 of one heat pipe 10 is
disposed in the space defined between the first end 14 and the
second end 18 of the other heat pipe 10, and vice versa. Such
arrangements can define an efficient use of space within the
housing 42, while also providing enhanced cooling of the heat
source 50 (i.e., by multiple heat pipes 10) in a relatively small
area.
[0039] In some embodiments, the first ends 14 are fixed (e.g., via
brazing, welding, soldering, etc.) to the heat transfer plate 54,
54a. In other embodiments, the first ends 14 are disposed inside or
beneath a portion of the heat transfer plate 54, 54a. For example,
the intermediate region 58 of the heat transfer plate 54a in FIG. 4
may include one or more areas (e.g., raised areas, recesses,
coverings, etc.) that define openings or chambers for receiving the
first ends 14 of the two heat pipes 10. The first ends 14 may slide
into these areas, and be retained therein frictionally, by brazing,
welding, soldering, adhesive, fasteners, or in any other suitable
manner. In some embodiments, surfaces of the first ends 14 of the
heat pipes 10 are flush with the surrounding portions of the heat
transfer plate 54, 54a, or are recessed within the heat transfer
plate 54, 54a. In such embodiments, the heat transfer plate 54, 54a
(and in some cases, the first ends of 14 of the heat pipes 10 as
well) present a collective surface that is relatively flat, and
that can therefore define a better thermal interface with the heat
source 50 to which the heat transfer plate 54, 54a faces. In this
regard, the first ends 14 of the heat pipes 10 and adjacent
portions of the heat transfer plate 54, 54a can be brought into
direct thermal contact with the heat source 50 in some embodiments,
including those in which the first ends 14 of the heat pipes 10 are
in or on the same side of the heat transfer plate 54, 54a that
faces the heat source 50.
[0040] In some embodiments, the second ends 18 of the two heat
pipes 10 are each coupled (e.g., fixed via brazing, welding,
soldering, etc.) to a second mounting wall 102 of the housing 42.
The first end 14 of each heat pipe 10 may be movable to different
positions with respect to the second end 18 of the heat pipe 10.
The second mounting wall 102 may be located opposite the first
mounting wall 48, although in other embodiments the second ends 18
of either or both heat pipes 10 are instead coupled to side walls
of the housing 42, or to other portions of the first mounting wall
48, depending at least in part upon the shape of the heat pipes 10.
The first mounting wall 48 and the second mounting wall 102, along
with side walls, may define a sealed interior cavity 110 of the
housing 42. The interior cavity 110 may be located between the
first mounting wall 48 and the second mounting wall 102. Other
embodiments may include different numbers of mounting walls and
side walls than that illustrated, as well as different shapes,
sizes, and dimensions of walls than that illustrated. In some
embodiments, the entirety of the first and second heat pipes 10,
the entirety of the heat transfer plate 54, 54a, and the entirety
of the heat source 50 may each be disposed within the sealed
interior cavity 110.
[0041] In some embodiments, the spring-like heat pipes 10 exert a
biasing force in a direction away from the first mounting wall 48
and heat source 50 when the heat pipes 10 are in thermal
communication with the heat source 50. For example, the heat pipes
10 may be placed in a stressed, tensile state when coupled to the
heat transfer plate 54, 54a (and for example to the second mounting
wall 102 with the first ends 14 of the heat pipes 10 out-of-plane
with respect to the second ends 18 of the heat pipes 10, and while
the heat pipes 10 are in conductive thermal communication with the
heat source 50. In such a state, the heat pipes 10 exert a
restorative force in a direction pulling the heat transfer plate
54, 54a away from the first mounting wall 48. In other words, in an
unstressed state, an offset distance of the first end 14 of each
heat pipe 10 with respect to the second end 18 would be less than
in the stressed state (the distance between the ends 14, 18 of the
heat pipe 10 may be zero if the first and second ends 14, 18 are in
a common plane in the unstressed state). Put another way, the
offset distance between the first and second ends 14, 18 of the
heat pipe 10 is greater in a stressed state than in an unstressed
state, thereby creating a stored spring-like biasing force in the
heat pipe 10. Thus, when stressed, the first ends 14 of the heat
pipes 10 exert a constant force on the heat transfer plate 54, 54a
in a direction away from the first mounting wall 48 (and for
example toward the opposite second mounting wall 102, while the
fasteners 56 and/or biasing members (if used) exert an opposite
force on the heat transfer plate 54, 54a toward the first mounting
wall 48. In this manner, the fasteners 56 can be adjusted with
significant precision to offset a desired amount of restorative
force of the heat pipes 10 urging the heat pipes 10 to return to
their unstressed state. This precision is in contrast to systems in
which the adjustment of force between the heat pipe(s) 10 and the
heat source 50 is either impossible, or is much more difficult to
perform.
[0042] In some embodiments, the heat pipes 10 may initially be in
an unstressed state when coupled to the heat transfer plate 54, 54a
(and for example to the second mounting wall 102). The heat pipes
10 in such a state can be offset as described and illustrated
herein, or in some embodiments can lie in the same plane. In some
embodiments, the fasteners 56 may then be tightened (e.g., to
varying degrees as desired), pulling the heat transfer plate 54,
54a toward the first mounting wall 48 and placing the heat pipes 10
in a stressed state by pulling the first ends 14 of the heat pipes
10 away from the fixed second ends 18 and toward the first mounting
wall 48. As a result, when so stressed, the first ends 14 of the
heat pipes 10 exert a constant spring-like biasing force on the
heat transfer plate 54, 54a in a direction away from the first
mounting wall 48 while the fasteners 56 and/or biasing members (if
used) exert an opposite force on the heat transfer plate 54, 54a
toward the first mounting wall 48.
[0043] In other embodiments, the heat pipes 10 exert a biasing
force in a direction toward the first mounting wall 48. In such
embodiments, in the unstressed state, the first end 14 of each heat
pipe 10 can be offset from the second end 18. In the stressed
assembled state, the first end 14 of each heat pipe 10 can be
positioned at an offset distance from the second end 18 of the heat
pipe 10 that is less than the initial offset distance (in the
unstressed state) so that the first end 14 seeks to return to its
initial position farther away from the first end 18 and closer
toward the first mounting wall 48. In such cases, the heat pipes 10
can exhibit a spring or biasing force on the heat transfer plate
54, 54a in a direction toward the first mounting wall 48.
[0044] In embodiments described above and illustrated in the
figures, the first and second ends 14, 18 of the heat pipes 10 are
offset in an unstressed state, and are either offset in the
stressed and assembled state or lie in the same plane in the
stressed and assembled state. In other embodiments, the heat pipes
10 lie in the same plane in the unstressed state, and are offset in
the stressed and assembled state. In still other embodiments, the
heat pipes 10 are offset in one direction in the unstressed state,
and are offset in the opposite direction in the stressed and
assembled state, wherein the first end 14 of each heat pipe flexes
from an unstressed and offset position with respect to the second
end 18, toward and past a co-planar state with the second end 18,
and on to a stressed an offset position with respect to the second
end 18.
[0045] The various embodiments of heat pipe 10 flexure (i.e.,
relative positions of the first and second ends 14, 18 when
unstressed and stressed) described herein can be selected as to
achieve a desired profile of force exerted upon the heat source 50
(e.g., when the fasteners 56 are tightened). For example, the range
of forces exerted by the heat pipes 10 as they are flexed toward a
co-planar position can be significantly different from the range of
forces exerted by the heat pipes 10 as they are flexed away from a
co-planar position. The force profile (change in force as a
function of changing heat pipe flexure) can be selected by the
designer of the heat transfer system 38 based upon the design
specifications/requirements and user preferences of the heat
transfer system 38.
[0046] With continued reference to FIGS. 1-4, during operation, the
heat source 50 generates heat that is conducted through the heat
transfer plate 54, 54a to the evaporator regions 26 of the heat
pipes 10 (the heat pipes 10 being in thermal communication with the
heat source 50). In some embodiments, the heat is transferred
directly from the heat source 50 to the heat pipes 10 (which can
include conductive heat transfer through braze, weld, solder, tape,
or other connecting material, and/or thermal grease, oil, paste, or
other thermal interface material). In other embodiments (dependent
at least in part upon the relative position of the heat pipes 10
with respect to the heat transfer plate 54, 54a), the heat is
transferred first into the heat transfer plate 54, 54a and then
into the heat pipes 10, or is transferred both directly into the
heat pipes 10 from the heat source 50 and indirectly into the heat
pipes 10 through the heat transfer plate 54, 54a.
[0047] The heat is then transferred to and absorbed by the working
fluid inside of the heat pipes 10 in the evaporator regions 26,
causing the working fluid to change phase and vaporize in the vapor
chamber. The vaporized working fluid then flows along the lengths
of the heat pipes 10 within the vapor chamber, through the
intermediate (e.g., curved) regions 22, and finally to the
condenser regions 30 where the working fluid then changes phase
again and condenses back into a liquid state. The heat released at
the condenser regions 30 when the vaporized working fluid changes
phase to condense into a liquid state may be dissipated, for
example, at least partially to the second mounting wall 102, to the
interior cavity 110 of the housing 42, and/or to one or more
additional heat transfer devices (not illustrated) that are
thermally coupled to the condenser regions 30. Once the heat has
been dissipated, the working fluid condensate flows back from the
condenser regions 30 of the heat pipes 10 (e.g., along the wick
structure) to the evaporator regions 26, where the working fluid
then again absorbs heat generated by the heat source 50, and the
heat transfer cycle repeats.
[0048] As described above, the heat pipes 10 may be oriented so
that their respective first ends 14 point in opposite directions to
one another, and/or their respective second ends 18 point in
opposite directions to one another. For example, heat pipes 10 with
J-shaped profiles may face in opposite directions. Thus, as
illustrated in FIG. 3, heat generated by the heat source 50
absorbed into one of the heat pipes 10 is conducted away toward one
side and/or corner of the housing 42, and heat generated by the
heat source 50 absorbed into the other heat pipe 10 is conducted
away toward an opposite side and/or corner of the housing 42. This
bi-directional heat conduction facilitates rapid heat dissipation
of heat away from the heat source 50. Additionally, because the
second ends 18 of the heat pipes 10 are offset from the respective
first ends 14 in some embodiments, heat generated by the heat
source 50 is conducted away from the heat source 50 both
vertically, as well as laterally, further facilitating a rapid
dissipation of heat away from the heat source 50.
[0049] In some embodiments, only a single heat pipe 10 is used
within the housing 42. The heat pipe 10 may have an "S" or "J"
shape, or may have any variety of different shapes as required by
the particular application or environment. In other embodiments,
more than two (e.g., three, four, etc.) heat pipes 10 may be used
within the housing 42, again each having an "S" or "J" shape or
other different shapes as required by the particular application or
environment. The shape of each heat pipe 10 may also be different
within the same housing 42. For example, one heat pipe 10 may have
a "J" shape, whereas another heat pipe 10 may have a "U" shape or
"S" shape, etc.
[0050] In some embodiments a heat transfer system includes a
housing, and annealed heat pipes coupled to the housing. Each of
the heat pipes has an evaporator region and a condenser region
separated by an intermediate region defining at least one reversal
of direction of the annealed heat pipe. The evaporator and
condenser regions of a first one of the heat pipes both face in a
first direction. The evaporator and condenser regions of a second
one of the heat pipes both face in a second direction that is
opposite to the first direction. The heat transfer system may
otherwise be similar or identical, for example, to the heat
transfer system 38 described above and illustrated in FIG. 3. For
example, in some embodiments first and second ends of the heat
pipes are offset in an unstressed state, and are either offset in
the stressed and assembled state or lie in the same plane in the
stressed and assembled state. In other embodiments, the heat pipes
lie the same plane in the unstressed state, and are offset in the
stressed and assembled state. In still other embodiments, the heat
pipes are offset in one direction in the unstressed state, and are
offset in the opposite direction in the stressed and assembled
state. The first end of each heat pipe may flex from an unstressed
and offset position with respect to the second end, toward and past
a co-planar state with the second end, and on to a stressed an
offset position with respect to the second end. Additionally, in
some embodiments the heat pipes are coupled to (e.g., restrained
by) a heat plate, similar to the heat plate 54 or 54a.
[0051] In some embodiments, the evaporator region and the condenser
region of a first heat pipe are out of plane with respect to one
another in an unstressed state of the first heat pipe. The
evaporator region and the condenser region of a second one of the
heat pipes may also be out of plane with respect to one another in
an unstressed state of the second heat pipe. The evaporator regions
of the first and second heat pipes may extend parallel to one
another, and the condenser regions of the first and second heat
pipes may extend parallel to one another.
[0052] In some embodiments, the evaporator regions of a first heat
pipe and second heat pipe are spaced from each other by a first
distance, and the condenser regions of the first and second heat
pipes are spaced from each other by a second distance. The second
distance is greater than the first distance. In other embodiments
the second distance is less than the first distance, or is equal to
the first distance.
[0053] Although various embodiments have been described in detail
with reference to certain examples illustrated in the drawings,
variations and modifications exist within the scope and spirit of
one or more independent aspects as described and illustrated.
* * * * *