U.S. patent application number 16/052294 was filed with the patent office on 2019-06-27 for wafer polishing pad and method of wafer polishing using the same.
The applicant listed for this patent is SAMSUNG ELECTRONICS CO., LTD.. Invention is credited to Seok Ryul Kim, Sunghyup Kim, Sanghoon Lee.
Application Number | 20190193238 16/052294 |
Document ID | / |
Family ID | 66949235 |
Filed Date | 2019-06-27 |
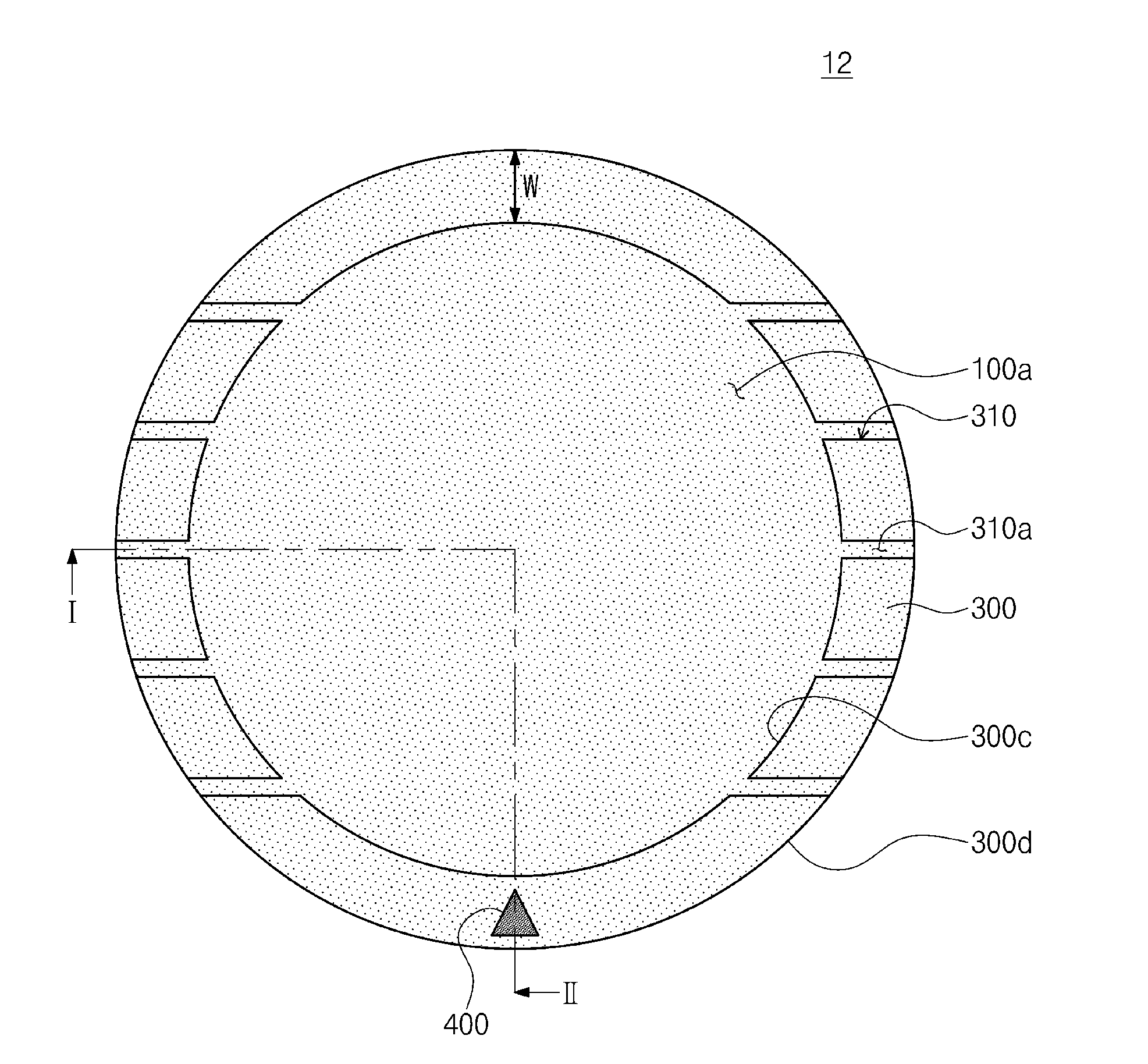


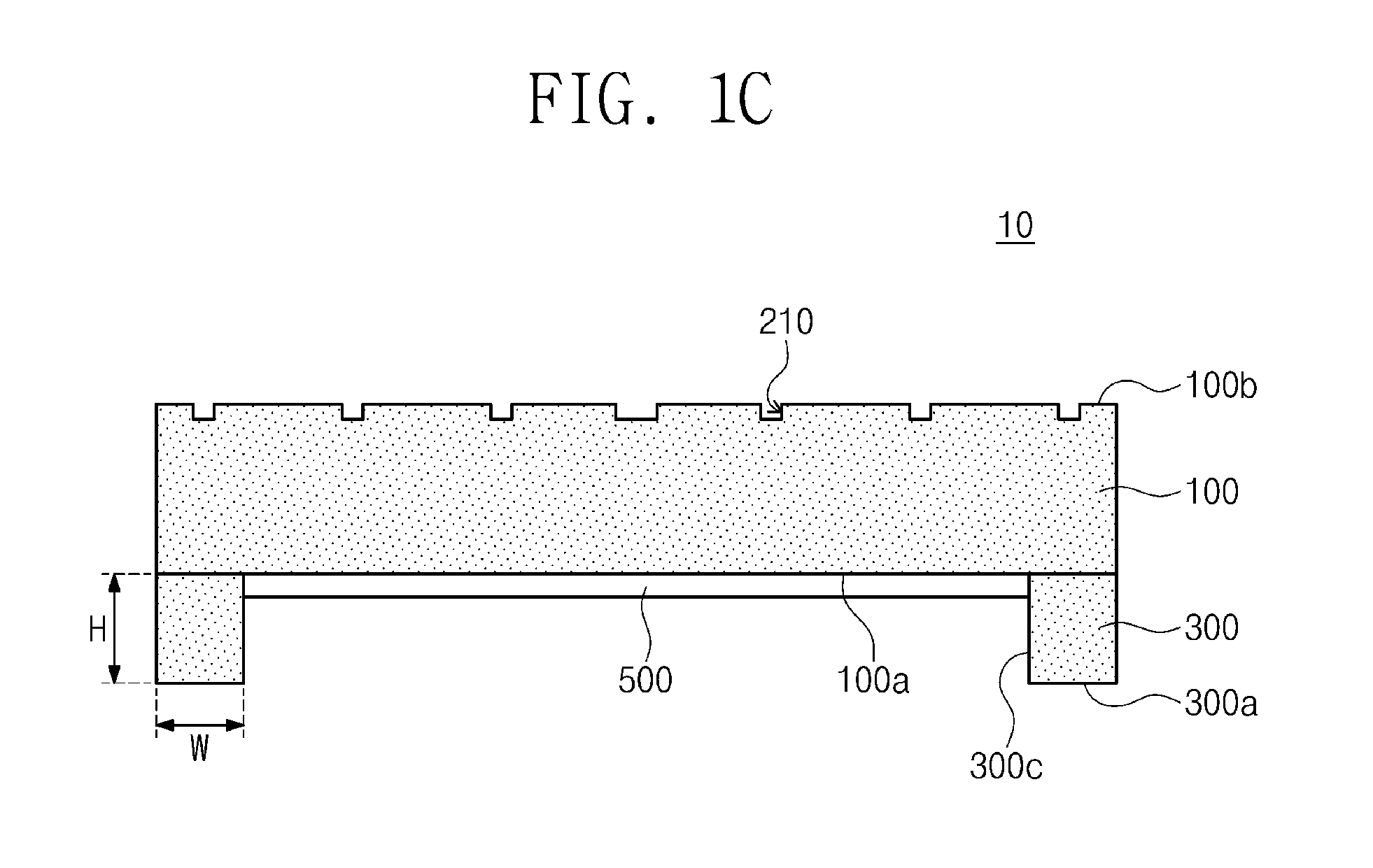

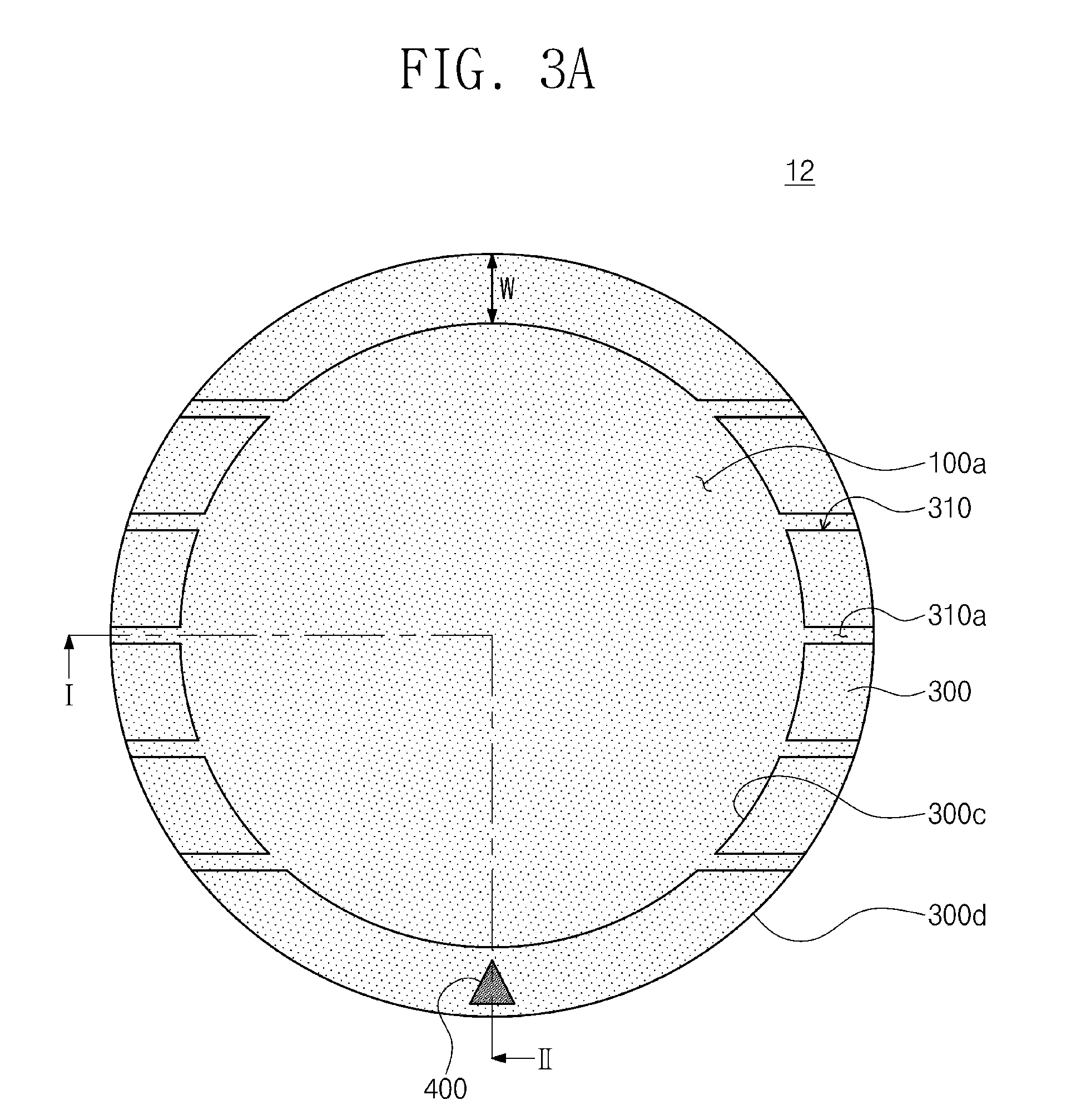

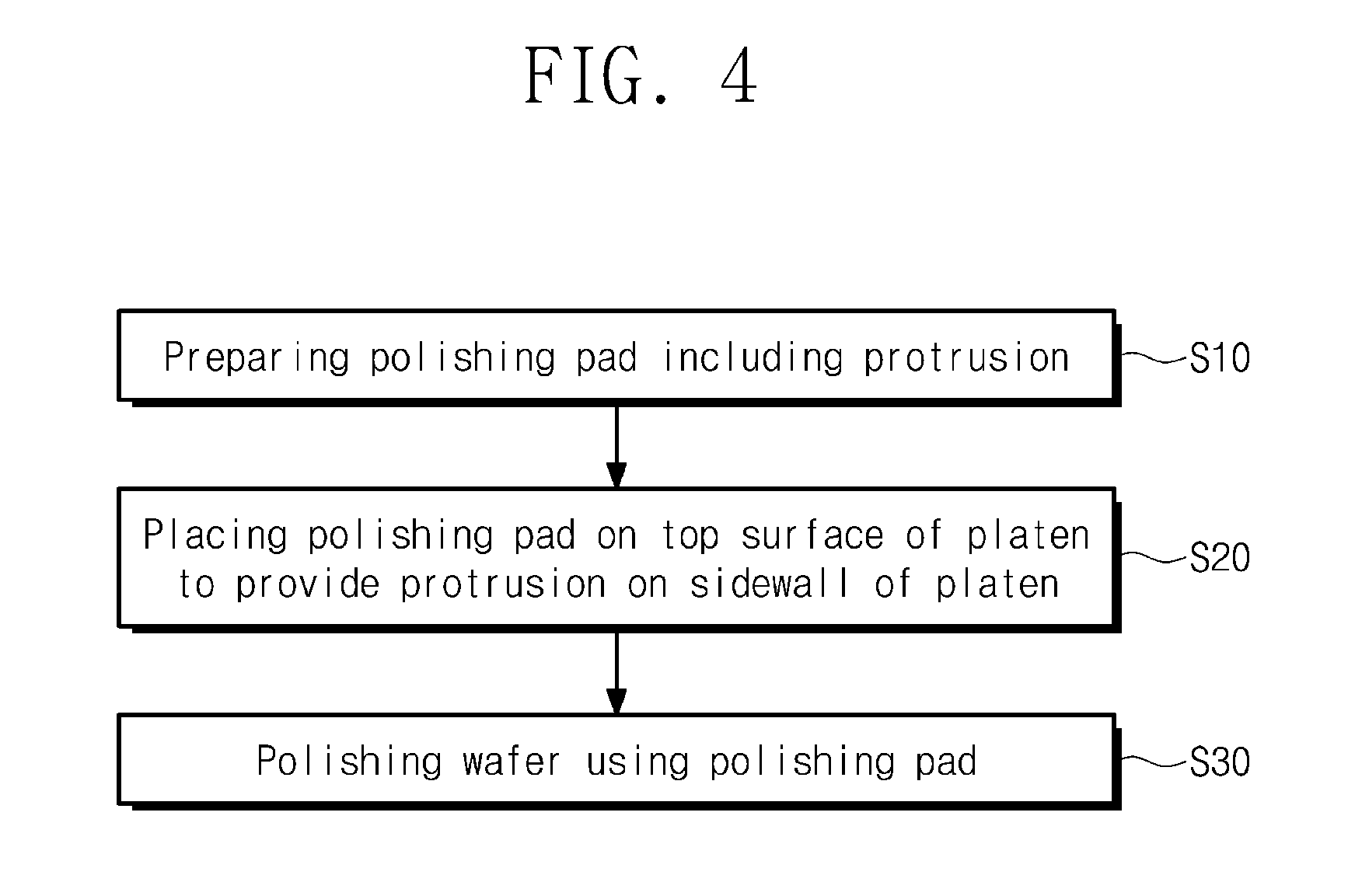


United States Patent
Application |
20190193238 |
Kind Code |
A1 |
Kim; Seok Ryul ; et
al. |
June 27, 2019 |
WAFER POLISHING PAD AND METHOD OF WAFER POLISHING USING THE
SAME
Abstract
A wafer polishing pad includes a first pad having a first
surface configured to receive a platen. A protrusion is disposed on
the first surface of the first pad. The protrusion is disposed on
an edge region of the first pad in a plan view such that a side
surface of the protrusion makes contact with a side surface of the
platen when the first pad is disposed on the platen.
Inventors: |
Kim; Seok Ryul;
(Hwaseong-si, KR) ; Kim; Sunghyup; (Hwaseong-si,
KR) ; Lee; Sanghoon; (Seoul, KR) |
|
Applicant: |
Name |
City |
State |
Country |
Type |
SAMSUNG ELECTRONICS CO., LTD. |
Suwon-si |
|
KR |
|
|
Family ID: |
66949235 |
Appl. No.: |
16/052294 |
Filed: |
August 1, 2018 |
Current U.S.
Class: |
1/1 |
Current CPC
Class: |
B24B 37/26 20130101;
B24B 37/22 20130101 |
International
Class: |
B24B 37/26 20060101
B24B037/26; B24B 37/22 20060101 B24B037/22 |
Foreign Application Data
Date |
Code |
Application Number |
Dec 27, 2017 |
KR |
10-2017-0180750 |
Claims
1. A wafer polishing pad, comprising: a first pad having a first
surface configured to receive a platen; and a protrusion disposed
on the first surface of the first pad, wherein the protrusion is
disposed on an edge region of the first pad in a plan view such
that a side surface of the protrusion makes contact with a side
surface of the platen when the first pad is disposed on the
platen.
2. The wafer polishing pad of claim 1, wherein the protrusion
exposes a central region of the first surface of the first pad, and
when viewed in the plan view, the protrusion circumscribes the
central region of the first pad.
3. The wafer polishing pad of claim 1, wherein the protrusion
comprises a vent groove disposed within a bottom surface of the
protrusion.
4. The wafer polishing pad of claim 3, wherein a floor surface of
the vent groove is located at substantially a same level as that of
the first surface of the first pad.
5. The wafer polishing pad of claim 3, further comprising a mark
disposed on the bottom surface of the protrusion.
6. The wafer polishing pad of claim 3, further comprising an
adhesive layer covering a portion of the first surface of the first
pad, wherein the portion of the first surface of the first pad is
exposed by the protrusion.
7. The wafer polishing pad of claim 1, wherein a groove is disposed
on a second surface of the first pad, wherein the second surface of
the first pad is opposite to the first surface.
8. The wafer polishing pad of claim 1, further comprising: a second
pad disposed on the first pad; and an adhesive layer disposed
between the first pad and the second pad.
9. The wafer polishing pad of claim 8, wherein a groove is disposed
on a second surface of the second pad, wherein the second surface
of the second pad faces away from the first pad.
10. The wafer polishing pad of claim 1, wherein a topmost portion
of an edge region of a second surface of the first pad is located
at substantially the same level as that of a topmost portion of a
central region of the second surface of the first pad, wherein the
second surface of the first pad is opposite to the first surface of
the first pad.
11. A wafer polishing pad, comprising: a top surface including a
groove; a first bottom surface opposite to the top surface and
corresponding to a central region of the polishing pad; and a
second bottom surface opposite to the top surface and corresponding
to an edge region of the polishing pad, wherein the second bottom
surface is located at a lower level than that of the first bottom
surface.
12. The wafer polishing pad of claim 11, wherein the second bottom
surface has a closed loop shape.
13. The wafer polishing pad of claim 11, further comprising a vent
groove disposed within the second bottom surface, wherein a floor
surface of the vent groove is connected to the first bottom
surface.
14. The wafer polishing pad of claim 13, further comprising an
adhesive layer disposed on the first bottom surface.
15-20. (canceled)
21. A wafer polishing pad, comprising: a polishing surface
configured to mechanically polish a wafer; a receiving surface,
opposite to the polishing surface, configured to make contact with
a top surface of a platen; and a ring disposed on the receiving
surface and configured to make contact with a side surface of the
platen.
22. The wafer polishing pad of claim 21, wherein the ring of the
polishing wafer is configured to buttress a portion of the
polishing surface that extends beyond the platen.
23. The wafer polishing pad of claim 21, wherein the wafer
polishing pad comprises a first pad and a second pad that are
joined together by an adhesive layer, the first pad including the
polishing surface and the second pad including the receiving
surface.
Description
CROSS-REFERENCE TO RELATED APPLICATIONS
[0001] This U.S. nonprovisional application claims priority under
35 U.S.C .sctn. 119 to Korean Patent Application No.
10-2017-0180750 filed on Dec. 27, 2017, in the Korean Intellectual
Property Office, the entire contents of which are hereby
incorporated by reference.
TECHNICAL FIELD
[0002] The present disclosure relate to a polishing pad, and more
particularly, to a wafer polishing pad and a method of wafer
processing using the wafer polishing pad.
DISCUSSION OF THE RELATED ART
[0003] An integrated circuit is generally formed by successively
disposing conductors, semiconductors, and/or insulators on a wafer.
After each layer is disposed, the layer is etched to define the
circuit. As layers are successively disposed and etched, the wafer
gradually becomes rough on its exposed surface. To correct for this
roughness, the wafer may be periodically planarized to flatten the
exposed surface of the wafer. A chemical mechanical polishing
process may be employed in planarizing the wafer. The chemical
mechanical polishing process may use a polishing pad to polish the
wafer.
SUMMARY
[0004] A wafer polishing pad includes a first pad having a first
surface configured to receive a platen. A protrusion is disposed on
the first surface of the first pad. The protrusion is disposed on
an edge region of the first pad in a plan view such that a side
surface of the protrusion makes contact with a side surface of the
platen when the first pad is disposed on the platen.
[0005] A wafer polishing pad includes a top surface including a
groove. A first bottom surface opposite to the top surface
corresponds to a central region of the polishing pad. A second
bottom surface opposite to the top surface corresponds to an edge
region of the polishing pad. The second bottom surface is located
at a lower level than that of the first bottom surface.
[0006] A wafer polishing method includes preparing a polishing pad
comprising a first pad and a protrusion. The protrusion is disposed
on an edge region of a first surface of the first pad. The
polishing pad is placed on a platen such that the first surface of
the first pad faces the platen. A wafer is polished using the
polishing pad. Placing the polishing pad on the platen includes
causing the protrusion of the polishing pad to make contact with a
sidewall of the platen.
[0007] A wafer polishing pad includes a polishing surface
configured to mechanically polish a wafer. A receiving surface,
opposite to the polishing surface, is configured to make contact
with a top surface of a platen. A ring is disposed on the receiving
surface and the ring is configured to make contact with a side
surface of the platen.
BRIEF DESCRIPTION OF THE DRAWINGS
[0008] A more complete appreciation of the present disclosure and
many of the attendant aspects thereof will be readily obtained as
the same becomes better understood by reference to the following
detailed description when considered in connection with the
accompanying drawings, wherein:
[0009] FIG. 1A is a plan view illustrating a polishing pad
according to exemplary embodiments of the present disclosure;
[0010] FIG. 1B is a plan view illustrating grooves of a polishing
pad according to exemplary embodiments of the present
disclosure;
[0011] FIG. 1C is a cross-sectional view taken along line I-II of
FIG. 1A;
[0012] FIG. 2 is a cross-sectional view illustrating a polishing
pad according to exemplary embodiments of the present
disclosure;
[0013] FIG. 3A is a plan view illustrating a polishing pad
according to exemplary embodiments of the present disclosure;
[0014] FIG. 3B is a cross-sectional view taken along line I-II of
FIG. 3A;
[0015] FIG. 3C is a cross-sectional view illustrating an adhesive
layer attaching method according to exemplary embodiments of the
present disclosure;
[0016] FIG. 4 is a flow chart illustrating a wafer polishing method
according to exemplary embodiments of the present disclosure;
[0017] FIG. 5 is a perspective view illustrating a wafer polishing
method according to exemplary embodiments of the present
disclosure; and
[0018] FIG. 6 is a cross-sectional view illustrating a polishing
pad associated with a platen in accordance with exemplary
embodiments of the present disclosure.
DETAILED DESCRIPTION OF EMBODIMENTS
[0019] In describing exemplary embodiments of the present
disclosure illustrated in the drawings, specific terminology is
employed for sake of clarity. However, the present disclosure is
not intended to be limited to the specific terminology so selected,
and it is to be understood that each specific element includes all
technical equivalents which operate in a similar manner. In the
specification and the various figures, like reference numerals may
indicate like components.
[0020] Exemplary embodiments of the present invention may utilize a
wafer polishing pad and a wafer polishing method using the
same.
[0021] FIG. 1A is a plan view illustrating a polishing pad
according to exemplary embodiments of the present disclosure. FIG.
1B is a plan view illustrating grooves disposed on a polishing pad,
according to exemplary embodiments of the present disclosure,
showing a top surface of the polishing pad. FIG. 1C is a
cross-sectional view taken along line I-II of FIG. 1A.
[0022] Referring to FIGS. 1A to 1C, a polishing pad 10 may include
a first pad 100 and a protrusion 300. The first pad 100 may have a
plurality of pores at least partially penetrating the first pad
100. The first pad 100 may include, for example, a polymer such as
polyurethane. The pores of the first pad 100 may receive slurry.
The slurry may be used for chemically and mechanically polishing a
polishing target, using the first pad 100. The polishing target may
be a wafer.
[0023] The first pad 100 may have a first surface 100a and a second
surface 100b opposite to the first surface 100a. The second surface
100b of the first pad 100 may correspond to a top surface of the
polishing pad 10 while the first surface 100a of the first pad 100
may correspond to a bottom surface of the polishing pad. The second
surface 100b of the first pad 100 may serve as a polishing surface.
For example, the second surface 100b of the first pad 100 may make
contact with and polish the polishing target. The second surface
100b of the first pad 100 may be relatively rough, for example, the
second surface 100b may be rougher than the first surface 100a. The
first pad 100 may have a uniform thickness. For example, central
and edge regions of the first pad 100 may have the same or similar
maximum thickness. The second surface 100b of the first pad 100 may
be straight and unbent. For example, the second surface 100b of the
first pad 100 may have central and edge regions whose respective
topmost portions are located at substantially the same level. The
edge region of the second surface 100b of the first pad 100 may
indicate a zone overlapped with the protrusion 300.
[0024] A plurality of grooves 210 may be disposed on the second
surface 100b of the first pad 100. As illustrated in FIG. 1B, one
or more of the plurality of grooves 210 may extend radially from a
center of the polishing pad 10 toward an edge of the polishing pad
10. Others of the plurality of grooves 210 may be arranged in
concentric circles. However, the present invention does not
necessarily have this particular geometric configuration of grooves
210. For example, the grooves 210 may have spiral shapes. The
planar shape of the grooves 210 may be arranged in various ways,
all within the scope of the present disclosure. When a polishing
process is performed, the grooves 210 may act as slurry paths
through which the slurry may travel.
[0025] The protrusion 300 may be disposed on the first surface 100a
of the first pad 100. The first surface 100a of the first pad 100
may be relatively flat. When viewed in plan as illustrated in FIG.
1A, the protrusion 300 may overlap with and extend up from an edge
region of the first surface 100a of the first pad 100. The
protrusion 300 may have a closed loop shape such as a ring shape.
The protrusion 300 may expose a central region of the first surface
100a of the first pad 100. The protrusion 300 may have a height H
equal to or greater than about 1 mm, for example, ranging from
about 1 mm to about 100 mm, as may be seen in FIG. 1C. The
protrusion 300 may have a bottom surface 300a at a different level
from that of the first surface 100a of the first pad 100. For
example, the bottom surface 300a of the protrusion 300 may be
disposed at a lower level than that of the first surface 100a of
the first pad 100. The protrusion 300 may have a width W ranging
from about 2 mm to about 5 mm.
[0026] For example, the protrusion 300 and the first pad 100 may be
integrally formed so as to constitute a single unitary body. The
protrusion 300 and the first pad 100 may be connected to each other
without a boundary, and may include the same material. The
protrusion 300 may alternatively be formed by attaching a separate
structure (e.g., a preliminary protrusion) onto the first surface
100a of the first pad 100. In this case, the protrusion 300 and the
first pad 100 may include the same or different materials, and an
adhesion may be used to attach the first pad 100 and the protrusion
300. The protrusion 300 may include a polymer, but the protrusion
300 may be formed of another material.
[0027] An adhesive layer 500 may further be disposed on the first
surface 100a of the first pad 100. The first pad 100 may thus have
the adhesive layer 500 attached onto an area of the first surface
100a that is not covered with the protrusion 300. The adhesive
layer 500 may have a thickness that is less than the height H of
the protrusion 300. The bottom surface 300a of the protrusion 300
may be located at a lower level than that of a bottom surface of
the adhesive layer 500. The adhesive layer 500 may further extend
along an inside surface 300c (e.g. inside facing sidewall) of the
protrusion 300. The adhesive layer 500 may include a polymer.
[0028] FIG. 2 is a cross-sectional view taken along line I-II of
FIG. 1A, showing a polishing pad according to exemplary embodiments
of the present invention. It may be assumed that elements that are
not described in detail below are at least similar to corresponding
elements described above.
[0029] Referring to FIG. 2, a polishing pad 11 may include a
protrusion 300, a first pad 100, and a second pad 200. The first
pad 100 and the protrusion 300 may be at least similar to
corresponding elements discussed above with reference to FIGS. 1A
and 1B. The polishing pad 11 may have a first bottom surface and a
second bottom surface respectively corresponding to a central
region and an edge region in a plan view. The first bottom surface
may correspond to the first surface 100a of the first pad 100, and
the second bottom surface may correspond to the bottom surface 300a
of the protrusion 300. The second bottom surface may be located at
a lower level than that of the first bottom surface. The first pad
100 may be covered with the adhesive layer 500 on its first surface
100a (e.g., the first bottom surface) exposed by (e.g. not covered
by) the protrusion 300. The second surface 100b of the first pad
100 may have central and edge regions whose respective topmost
portions are located at the same or similar level. Differently from
that shown FIGS. 1B and 1C, the second surface 100b of the first
pad 100 might not serve as a polishing surface, and no grooves 210
are disposed in the first pad 100.
[0030] The second pad 200 may be disposed on the first pad 100. The
second pad 200 may have a plurality of pores at least partially
penetrating the second pad 200. The second pad 200 may include, for
example, a polymer such as polyurethane. The second pad 200 may
have a first surface facing the first pad 100 and a second surface
200b opposite to the first surface. The second surface 200b of the
second pad 200 may correspond to a top surface of the polishing pad
11. The second surface 200b of the second pad 200 may serve as a
polishing surface. A plurality of grooves 210 may be disposed on
the second surface 200b of the second pad 200. The grooves 210 may
have planar shapes and may be at least similar to the grooves 210
discussed above with reference to FIGS. 1B and 1C. Central and edge
regions of the second pad 200 may have substantially the same
maximum thickness as each other. The second surface 200b of the
second pad 200 may have central and edge regions whose respective
topmost portions are located at substantially the same level.
[0031] An adhesive pattern 150 may be interposed between the first
pad 100 and the second pad 200. The second pad 200 may be attached
through the adhesive pattern 150 to the first pad 100. The adhesive
pattern 150 may include an insulating polymer. Central and edge
regions of the adhesive pattern 150 may have substantially the same
maximum thickness as each other.
[0032] FIG. 3A is a plan view illustrating a polishing pad
according to exemplary embodiments of the present disclosure. FIG.
3B is a cross-sectional view taken along line I-II of FIG. 3A. It
may be assumed that elements that are not described in detail below
are at least similar to corresponding elements described above.
[0033] Referring to FIGS. 3A and 3B, a polishing pad 12 may include
a first pad 100, a second pad 200, and a protrusion 300 disposed on
the first pad 100. The first pad 100, the second pad 200, and the
protrusion 300 may each be substantially the same as corresponding
elements discussed above with reference to FIGS. 1A to 1C and 2. It
is to be understood, however, that the adhesive pattern 150 and the
second pad 200 are optional elements and may be omitted without
departing from the scope of the present disclosure. As illustrated
in FIGS. 1B and 1C, the grooves 210 may be disposed in the first
pad 100. The protrusion 300 may have an inside surface 300c and an
outside surface 300d opposite to each other. The inside and outside
surfaces 300c and 300d of the protrusion 300 may extend in a
direction intersecting the first surface 100a of the first pad
100.
[0034] A plurality of vent grooves 310 may be disposed in the
protrusion 300. The vent grooves 310 may be disposed on and may
penetrate the bottom surface 300a of the protrusion 300. As
illustrated in FIG. 3B, the vent grooves 310 may have floor
surfaces 310a at substantially the same level as that of the first
surface 100a of the first pad 100. The floor surfaces 310a of the
vent grooves 310 may be connected to the first surface 100a of the
first pad 100. When viewed in plan, as illustrated in FIG. 3A, the
vent grooves 310 may extend from the inside surface 300c of the
protrusion 300 toward the outside surface 300d of the protrusion
300. For example, the vent grooves 310 may penetrate the inside and
outside surfaces 300c and 300d of the protrusion 300.
Alternatively, the vent grooves 310 may penetrate the inside
surface 300c of the protrusion 300, but not the outside surface
300d of the protrusion 300. The number and planar shapes of the
vent grooves 310 is not limited to the arrangements shown, and
various different arrangements may be used, within the scope of the
present disclosure.
[0035] The protrusion 300 may be formed on the first pad 100, and
then the protrusion 300 may be partially removed to form the vent
grooves 310. According to an exemplary embodiment of the present
disclosure, the formation of the vent grooves 310 may include
preparing a plurality of preliminary protrusions and attaching the
preliminary protrusions onto the first surface 100a of the first
pad 100 so as to be spaced apart from each other. In this case, the
protrusion 300 may include a plurality of sub-protrusions spaced
apart from each other, and the vent grooves 310 may be disposed
between each of the plurality of sub-protrusions.
[0036] A mark 400 may further be disposed on the bottom surface
300a of the protrusion 300. The mark 400 may be a character or
figure displayed on the bottom surface 300a of the protrusion 300.
For example, the mark 400 may be formed by attaching a pattern onto
the bottom surface 300a of the protrusion 300. Alternatively, the
mark 400 may be a recession formed within the bottom surface 300a
of the protrusion 300. A planar arrangement of the mark 400 is not
limited to that shown, and various different arrangements are
within the scope of the present disclosure.
[0037] The first pad 100 may include an adhesive layer 500 on its
first surface 100a exposed by (e.g. not covered by) the protrusion
300. The adhesive layer 500 may further cover the inside surface
300c of the protrusion 300. An attaching process of the adhesive
layer 500 and functions of the vent grooves 310 are described in
greater detail below.
[0038] FIG. 3C is a cross-sectional view taken along line I-II of
FIG. 3A, showing a method for attaching an adhesive layer according
to exemplary embodiments of the present disclosure. It may be
assumed that elements that are not described in detail below are at
least similar to corresponding elements described above.
[0039] Referring to FIGS. 3A and 3C, the adhesive layer 500 may be
disposed onto the first surface 100a of the first pad 100. In the
process of attaching the adhesive layer 500, as indicated by an
arrow in FIG. 3C, air may flow into the vent grooves 310 from
between the adhesive layer 500 and the first pad 100. Air bubbles
may then be reduced or prevented from being formed between the
adhesive layer 500 and the first pad 100. The adhesive layer 500
may be sufficiently attached to the first pad 100. The mark 400 may
signify an attachment direction in the process of attaching the
adhesive layer 500. The attachment direction of the adhesive layer
500 may intersect the directions of extension of the vent grooves
310. Therefore, in the process of attaching the adhesive layer 500,
air may be easily discharged through the vent grooves 310 to the
outside.
[0040] A wafer polishing method according to exemplary embodiments
of the present disclosure is described in detail below.
[0041] FIG. 4 is a flow chart illustrating a wafer polishing method
according to exemplary embodiments of the present disclosure. FIG.
5 is a perspective view illustrating a wafer polishing method
according to exemplary embodiments of the present disclosure. FIG.
6 is a cross-sectional view illustrating a polishing pad associated
with a platen. It may be assumed that elements that are not
described in detail below are at least similar to corresponding
elements described above.
[0042] Referring to FIG. 4, one of the polishing pads 10, 11, and
12 including the protrusion 300 may be prepared (S10). For example,
the polishing pad 10 discussed with reference to FIGS. 1A to 1C,
the polishing pad 11 discussed with reference to FIG. 2, or the
polishing pad 12 discussed with reference to FIGS. 3A and 3B may be
prepared. The first pad 100 may include the adhesive layer 500
attached onto its first surface 100a exposed by (e.g. not covered
by) the protrusion 300. For example, the attachment of the adhesive
layer 500 may be performed at least similarly to that discussed
above with reference to FIG. 3C. For convenience of description, a
wafer polishing method using the polishing pad 11 of FIG. 2 will be
described. According to exemplary embodiments of the present
disclosure, a top surface of the polishing pad 11 may denote the
second surface 200b of the second pad 200. When the polishing pad
10 of FIGS. 1A to 1C is used, the top surface of the polishing pad
11 may denote the second surface 100b of the first pad 100.
[0043] Referring to FIG. 5, a polishing apparatus may be prepared.
The polishing apparatus may include a platen 1000, a wafer carrier
2000, a slurry supply 3000, and a pad conditioner 4000. The platen
1000 may have, for example, a cylindrical shape. The platen 1000
may receive power from a motor and the platen 1000 may be caused to
rotate around its rotational axis. The rotational axis may be
perpendicular to a top surface of the platen 1000.
[0044] Referring to FIGS. 4, 5, and 6, the polishing pad 11 may be
placed on the top surface of the platen 1000 so as to cause the
first surface 100a of the first pad 100 to face the top surface of
the platen 1000 (S20). The polishing pad 11 may be attached through
the adhesive layer 500 to the platen 1000. As illustrated in FIG.
6, the polishing pad 11 may have a diameter A1 greater than a
diameter A2 of the platen 1000. The first pad 100 may have a
diameter on its first surface 100a (e.g., the first bottom surface)
exposed by (e.g. not covered by) the protrusion 300, and the
diameter of the first surface 100a may be the same as or greater
than the diameter A2 of the platen 1000. The protrusion 300 may be
disposed on a sidewall 1000d of the platen 1000. The polishing pad
11 may then be precisely aligned with the platen 1000. For example,
in a plan view, a central point of the polishing pad 11 may be
aligned with a central point of the platen 1000. In addition, the
polishing pad 11 and the platen 1000 may be aligned with each other
at high speed to reduce process time. The protrusion 300 may more
rigidly fix the polishing pad 11 to the platen 1000.
[0045] The polishing pad 11 may be used to polish a wafer WF (S30).
In some exemplary embodiments of the present disclosure, the wafer
WF may be prepared. The wafer carrier 2000 may use vacuum pressure
to hold the wafer WF so as to cause a polishing target surface of
the wafer WF to face the polishing pad 11. The wafer carrier 2000
may be driven to move up and down by an elevation unit. The wafer
carrier 2000 may move downward to contact with the polishing pad 11
when a polishing process is performed. The wafer carrier 2000 may
rotationally move to rotate the wafer WF during the polishing
process.
[0046] The slurry supply 3000 may provide slurry onto the top
surface of the polishing pad 11. A material of the slurry may be
determined based on a kind and material of the polishing target
surface of the wafer WF. The slurry may chemically polish the
polishing target surface of the wafer WF, while contacting the
polishing target surface of the wafer WF. For example, the
polishing target surface of the wafer WF may change into an easily
removable state due to reaction with the slurry.
[0047] The polishing pad 11 may be supported by and may rotate
together with the platen 1000 during the polishing process. As
discussed above, the pores of the first pad 100 or of the second
pad 200 may receive the slurry. The polishing target surface of the
wafer WF and the top surface of the polishing pad 11 may abrade
against each other to mechanically polish the polishing target
surface of the wafer WF. The grooves 210 may serve as paths for the
slurry and polishing residues. When the central point of the
polishing pad 11 is misaligned with the central point of the platen
1000, the slurry in the grooves 210 may move unintentionally. In
some exemplary embodiments of the present disclosure, since the
polishing pad 11 and the platen 1000 are accurately aligned with
each other due to the protrusion 300, when the platen 1000 moves in
rotary motion, the slurry may be evenly distributed in the grooves
210 and slurry residues may be satisfactorily discharged/removed
from the grooves 210. As a result, the wafer WF may be evenly
polished on its polishing target surface.
[0048] The pad conditioner 4000 may be installed adjacent to the
platen 1000. The pad conditioner 4000 may move rotationally and
reciprocally. The pad conditioner 4000 may contact the top surface
of the polishing pad 11 and maintain an even surface roughness of
the top surface of the polishing pad 11. Therefore, even though the
polishing process is performed for a long time, the wafer WF may be
satisfactorily polished on its polishing target surface.
[0049] When the diameter A1 of the polishing pad 11 is the same as
or less than the diameter A2 of the platen 1000, the pad
conditioner 4000 may come into contact with the platen 1000 (e.g.,
with an edge portion of the platen 1000) during the operation of
the pad conditioner 4000. In this case, the pad conditioner 4000
and/or the platen 1000 may suffer from damage. In some exemplary
embodiments of the present disclosure, the diameter A1 of the
polishing pad 11 may be greater than the diameter A2 of the platen
1000. For example, the diameter A1 of the polishing pad 11 may be
approximately 5 to 10 mm larger than the diameter A2 of the platen
1000. The pad conditioner 4000 and the platen 1000 may accordingly
be prevented from colliding against each other.
[0050] When the diameter A1 of the polishing pad 11 is greater than
the diameter A2 of the platen 1000, an edge portion of the
polishing pad 11 might not be supported by the platen 1000. When no
protrusion 300 is provided, edge portions of the first and second
pads 100 and 200 may bend down lower than central portions of the
first and second pads 100 and 200. For example, the edge portions
not being supported by the platen 1000 may tend to bend inwardly
toward the platen 1000. The top surface of the polishing pad 11 may
thus be bent. The bending portion of the top surface of the
polishing pad 11 may be excessively abraded by the pad conditioner
4000, with the result that the polishing pad 11 may decrease in
life span. In some exemplary embodiments of the present disclosure,
the polishing pad 11 may include the protrusion 300. The protrusion
300 may be disposed on the edge portion of the first pad 100.
Hence, the edge portion of polishing pad 11 may be supported and
this support may prohibit the first pad 100 from bending down. When
the height H of the protrusion 300 is less than 1 mm, it may be
unlikely that the protrusion 300 sufficiently prevents the bending
of the polishing pad 11. In some exemplary embodiments of the
present disclosure, the height H of the protrusion 300 may fall
within a range equal to or greater than 1 mm, and thus the
polishing pad 11 may be sufficiently prevented from bending. The
polishing pad 11 may accordingly be prevented from being
excessively abraded on its top surface. Thus, the polishing pad 11
may increase in life span.
[0051] According to exemplary embodiments of the present
disclosure, a polishing pad may include a protrusion. The polishing
pad may be disposed on the top surface of a platen. The protrusion
may be disposed on the sidewall of the platen. The protrusion may
accurately and quickly align the polishing pad with the platen. The
process time may then decrease. The protrusion may rigidly fix the
polishing pad to the platen.
[0052] The protrusion may prevent the polishing pad from bending
down on the platen. The protrusion may suppress excessive abrasion
of the polishing pad, and as a result, the polishing pad may
increase in life span.
[0053] Exemplary embodiments described herein are illustrative, and
many variations can be introduced without departing from the spirit
of the disclosure or from the scope of the appended claims. For
example, elements and/or features of different exemplary
embodiments may be combined with each other and/or substituted for
each other within the scope of this disclosure and appended
claims.
* * * * *