U.S. patent application number 15/712151 was filed with the patent office on 2019-02-28 for buried word line of a dynamic random access memory and method for fabricating the same.
The applicant listed for this patent is Fujian Jinhua Integrated Circuit Co., Ltd., UNITED MICROELECTRONICS CORP.. Invention is credited to Kai-Jiun Chang, Pin-Hong Chen, Tzu-Chieh Chen, Yi-Wei Chen, Tsun-Min Cheng, Yi-An Huang, Chih-Chieh Tsai, Chia-Chen Wu.
Application Number | 20190067296 15/712151 |
Document ID | / |
Family ID | 65437576 |
Filed Date | 2019-02-28 |


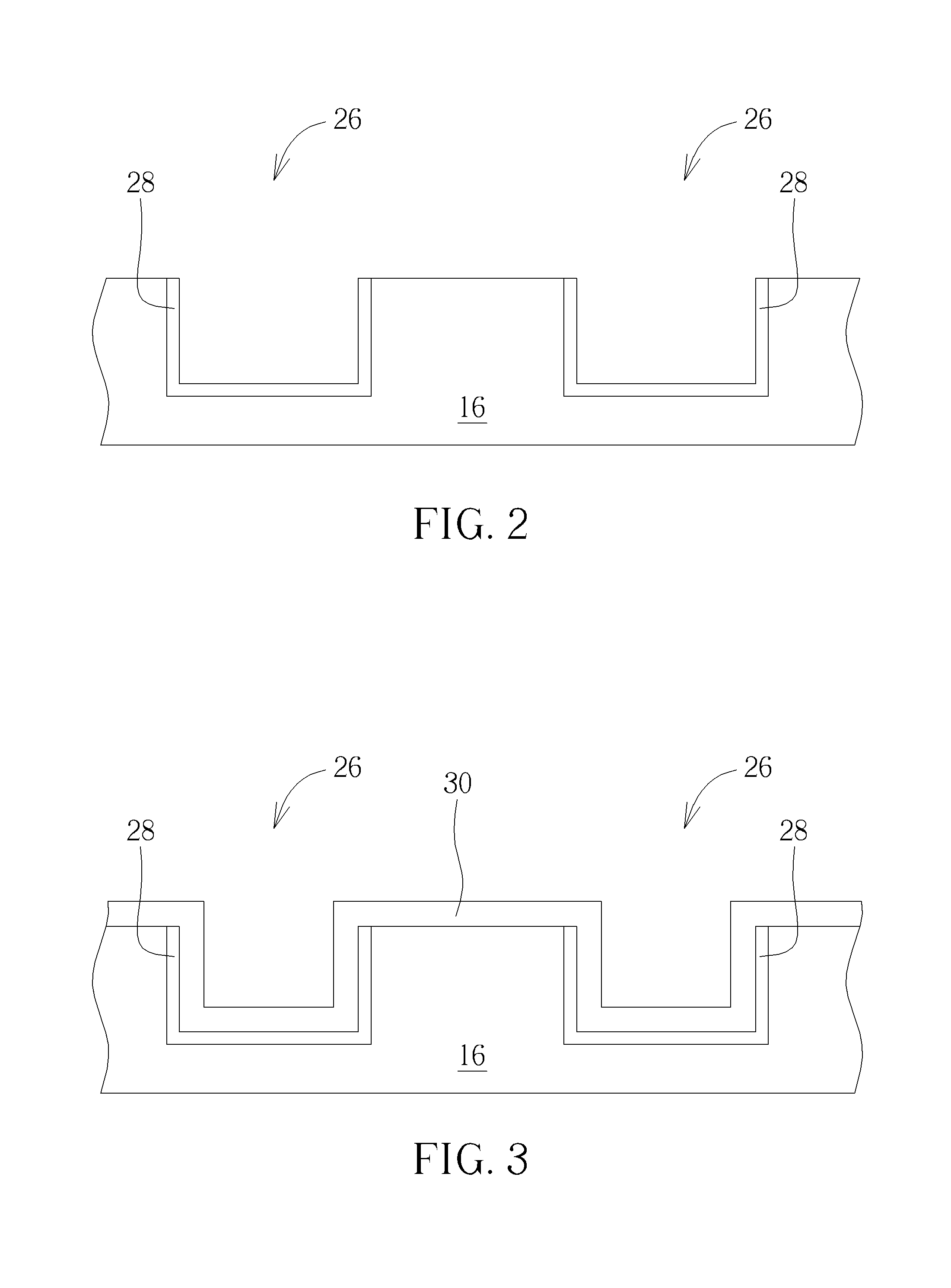



United States Patent
Application |
20190067296 |
Kind Code |
A1 |
Chen; Pin-Hong ; et
al. |
February 28, 2019 |
BURIED WORD LINE OF A DYNAMIC RANDOM ACCESS MEMORY AND METHOD FOR
FABRICATING THE SAME
Abstract
A method for fabricating buried word line of a dynamic random
access memory (DRAM) includes the steps of: forming a trench in a
substrate; forming a first conductive layer in the trench; forming
a second conductive layer on the first conductive layer, in which
the second conductive layer above the substrate and the second
conductive layer below the substrate comprise different thickness;
and forming a third conductive layer on the second conductive layer
to fill the trench.
Inventors: |
Chen; Pin-Hong; (Tainan
City, TW) ; Chen; Yi-Wei; (Taichung City, TW)
; Chen; Tzu-Chieh; (Pingtung County, TW) ; Tsai;
Chih-Chieh; (Kaohsiung City, TW) ; Wu; Chia-Chen;
(Nantou County, TW) ; Chang; Kai-Jiun; (Taoyuan
City, TW) ; Huang; Yi-An; (New Taipei City, TW)
; Cheng; Tsun-Min; (Changhua County, TW) |
|
Applicant: |
Name |
City |
State |
Country |
Type |
UNITED MICROELECTRONICS CORP.
Fujian Jinhua Integrated Circuit Co., Ltd. |
Hsin-Chu City
Quanzhou City |
|
TW
CN |
|
|
Family ID: |
65437576 |
Appl. No.: |
15/712151 |
Filed: |
September 22, 2017 |
Current U.S.
Class: |
1/1 |
Current CPC
Class: |
H01L 27/10891 20130101;
H01L 27/10823 20130101 |
International
Class: |
H01L 27/108 20060101
H01L027/108 |
Foreign Application Data
Date |
Code |
Application Number |
Aug 24, 2017 |
CN |
201710733801.2 |
Claims
1. A method for fabricating buried word line of a dynamic random
access memory (DRAM), comprising: forming a trench in a substrate;
forming a first conductive layer in the trench; forming a second
conductive layer on the first conductive layer, wherein the second
conductive layer above the substrate and the second conductive
layer below the substrate comprise different thickness; and forming
a third conductive layer on the second conductive layer to fill the
trench.
2. The method of claim 1, further comprising: performing a thermal
anneal process after forming the third conductive layer; and
performing a planarizing process to remove part of the third
conductive layer, part of the second conductive layer, and part of
the first conductive layer to form a gate structure.
3. The method of claim 1, further comprising performing a physical
vapor deposition (PVD) process to form the second conductive
layer.
4. The method of claim 1, wherein the second conductive layer above
a top surface of the substrate comprises a first thickness and the
second conductive layer on a top surface of the first conductive
layer within the trench comprises a second thickness.
5. The method of claim 4, wherein the first thickness and the
second thickness are different.
6. The method of claim 4, wherein the second thickness is less than
the first thickness.
7. The method of claim 4, wherein the second conductive layer on a
sidewall of the first conductive layer within the trench comprises
a third thickness.
8. The method of claim 7, wherein the third thickness is less than
the second thickness.
9. The method of claim 1, wherein the first conductive layer
comprises titanium nitride (TiN).
10. The method of claim 1, wherein the second conductive layer
comprises Ti.
11. The method of claim 1, wherein the third conductive layer
comprises cobalt (Co).
12. A buried word line of a dynamic random access memory (DRAM),
comprising: a gate structure in a substrate, wherein the gate
structure comprises: a first conductive layer on the substrate; a
second conductive layer on the first conductive layer, wherein the
second conductive layer comprises a horizontal portion and two
vertical portions and the horizontal portion and one of the two
vertical portions comprise different thickness; and a third
conductive layer on the second conductive layer.
13. The buried word line of a DRAM of claim 12, wherein the first
conductive layer is U-shaped.
14. The buried word line of a DRAM of claim 12, wherein the first
conductive layer comprises titanium nitride (TiN).
15. The buried word line of a DRAM of claim 12, wherein the second
conductive layer comprises Ti.
16. The buried word line of a DRAM of claim 12, wherein the third
conductive layer comprises cobalt (Co).
17. A buried word line of a dynamic random access memory (DRAM),
comprising: a gate structure in a substrate, wherein the gate
structure comprises: a first conductive layer in the substrate; a
second conductive layer on the first conductive layer, wherein the
second conductive layer is I-shaped; and a third conductive layer
on the second conductive layer.
18. The buried word line of a DRAM of claim 17, wherein the first
conductive layer is U-shaped.
19. The buried word line of a DRAM of claim 17, wherein the first
conductive layer comprises titanium nitride (TiN) and the second
conductive layer comprises Ti.
20. The buried word line of a DRAM of claim 17, wherein the third
conductive layer comprises cobalt (Co).
Description
BACKGROUND OF THE INVENTION
1. Field of the Invention
[0001] The invention relates to a method for fabricating
semiconductor device, and more particularly to a method for
fabricating a dynamic random access memory (DRAM) device.
2. Description of the Prior Art
[0002] As electronic products develop toward the direction of
miniaturization, the design of dynamic random access memory (DRAM)
units also moves toward the direction of higher integration and
higher density. Since the nature of a DRAM unit with buried gate
structures has the advantage of possessing longer carrier channel
length within a semiconductor substrate thereby reducing capacitor
leakage, it has been gradually used to replace conventional DRAM
unit with planar gate structures.
[0003] Typically, a DRAM unit with buried gate structure includes a
transistor device and a charge storage element to receive
electrical signals from bit lines and word lines. Nevertheless,
current DRAM units with buried gate structures still pose numerous
problems due to limited fabrication capability. Hence, how to
effectively improve the performance and reliability of current DRAM
device has become an important task in this field.
SUMMARY OF THE INVENTION
[0004] According to an embodiment of the present invention, a
method for fabricating buried word line of a dynamic random access
memory (DRAM) includes the steps of: forming a trench in a
substrate; forming a first conductive layer in the trench; forming
a second conductive layer on the first conductive layer, in which
the second conductive layer above the substrate and the second
conductive layer below the substrate comprise different thickness;
and forming a third conductive layer on the second conductive layer
to fill the trench.
[0005] According to another aspect of the present invention, a
buried word line of a dynamic random access memory (DRAM) includes
a gate structure in a substrate. Preferably, the gate structure
further includes: a first conductive layer on the substrate; a
second conductive layer on the first conductive layer, wherein the
second conductive layer comprises a horizontal portion and two
vertical portions and the horizontal portion and one of the two
vertical portions comprise different thickness; and a third
conductive layer on the second conductive layer.
[0006] According to yet another aspect of the present invention, a
buried word line of a dynamic random access memory (DRAM) includes
a gate structure in a substrate. Preferably, the gate structure
includes: a first conductive layer in the substrate; a second
conductive layer on the first conductive layer, wherein the second
conductive layer is I-shaped; and a third conductive layer on the
second conductive layer.
[0007] These and other objectives of the present invention will no
doubt become obvious to those of ordinary skill in the art after
reading the following detailed description of the preferred
embodiment that is illustrated in the various figures and
drawings.
BRIEF DESCRIPTION OF THE DRAWINGS
[0008] FIGS. 1-7 illustrate a method for fabricating a DRAM device
according to an embodiment of the present invention.
[0009] FIG. 8 illustrates a structural view of a buried word line
of a DRAM according to an embodiment of the present invention.
DETAILED DESCRIPTION
[0010] Referring to FIGS. 1-7, FIGS. 1-7 illustrate a method for
fabricating a DRAM device according to an embodiment of the present
invention, in which FIG. 1 illustrates a top-view diagram of a DRAM
device, FIG. 2 illustrates a cross-sectional view of FIG. 1 along
the sectional line AA', and FIGS. 3-7 illustrate cross-sectional
views following the fabrication of FIG. 2. Preferably, the present
embodiment pertains to fabricate a memory device, and more
particularly a DRAM device 10, in which the DRAM device 10 includes
at least a transistor device (not shown) and at least a capacitor
structure (not shown) that will be serving as a smallest
constituent unit within the DRAM array and also used to receive
electrical signals from bit lines 12 and word lines 14.
[0011] As shown in FIG. 1, the DRAM device 10 includes a substrate
16 such as a semiconductor substrate or wafer made of silicon, a
shallow trench isolation (STI) 24 formed in the substrate 16, and a
plurality of active areas (AA) 18 defined on the substrate 16. A
memory region 20 and a periphery region (not shown) are also
defined on the substrate 16, in which multiple word lines 14 and
multiple bit lines 12 are preferably formed on the memory region 20
while other active devices (not shown) could be formed on the
periphery region. For simplicity purpose, only devices or elements
on the memory region 20 are shown in FIG. 1 while elements on the
periphery region are omitted.
[0012] In this embodiment, the active regions 18 are disposed
parallel to each other and extending along a first direction, the
word lines 14 or multiple gates 22 are disposed within the
substrate 16 and passing through the active regions 18 and STI 24.
Preferably, the gates 22 are disposed extending along a second
direction, in which the second direction crosses the first
direction at an angle less than 90 degrees.
[0013] The bit lines 12 on the other hand are disposed on the
substrate 16 parallel to each other and extending along a third
direction while crossing the active regions 18 and STI 24, in which
the third direction is different from the first direction and
orthogonal to the second direction. In other words, the first
direction, second direction, and third direction are all different
from each other while the first direction is not orthogonal to both
the second direction and the third direction. Preferably, contact
plugs such as bit line contacts (BLC) (not shown) are formed in the
active regions 18 adjacent to two sides of the word lines 14 to
electrically connect to source/drain region (not shown) of each
transistor element and storage node contacts (not shown) are formed
to electrically connect to a capacitor.
[0014] The fabrication of word lines 14 (or also referred to as
buried word lines) is explained below. As shown in FIG. 2, at least
a trench or trenches 26 are formed in the substrate 16, and an
in-situ steam generation (ISSG) process is conducted to form a gate
dielectric layer 28 in the trenches 26.
[0015] In this embodiment, the gate dielectric layer 28 preferably
includes silicon oxide or high-k dielectric layer depending on the
demand of the product, in which the high-k dielectric layer is
preferably selected from dielectric materials having dielectric
constant (k value) larger than 4. For instance, the high-k
dielectric layer may be selected from hafnium oxide (HfO.sub.2),
hafnium silicon oxide (HfSiO.sub.4), hafnium silicon oxynitride
(HfSiON), aluminum oxide (Al.sub.2O.sub.3), lanthanum oxide
(La.sub.2O.sub.3), tantalum oxide (Ta.sub.2O.sub.5), yttrium oxide
(Y.sub.2O.sub.3), zirconium oxide (ZrO.sub.2), strontium titanate
oxide (SrTiO.sub.3), zirconium silicon oxide (ZrSiO.sub.4), hafnium
zirconium oxide (HfZrO.sub.4), strontium bismuth tantalate
(SrBi.sub.2Ta.sub.2O.sub.9, SBT), lead zirconate titanate
(PbZr.sub.xTi.sub.1-xO.sub.3, PZT), barium strontium titanate
(Ba.sub.xSr.sub.1-xTiO.sub.3, BST) or a combination thereof.
[0016] Next, as shown in FIG. 3, a first conductive layer 30 is
formed in the trenches 26. In this embodiment, the first conductive
layer 30 preferably includes TiN, but not limited thereto.
Specifically, the first conductive layer 30 preferably includes a
work function metal layer which could be a n-type work function
metal layer or p-type work function metal layer depending on the
demand of the process or product. In this embodiment, n-type work
function metal layer could include work function metal layer having
a work function ranging between 3.9 eV and 4.3 eV such as but not
limited to for example titanium aluminide (TiAl), zirconium
aluminide (ZrAl), tungsten aluminide (WAl), tantalum aluminide
(TaAl), hafnium aluminide (HfAl), or titanium aluminum carbide
(TiAlC), but it is not limited thereto. P-type work function metal
layer on the other hand could include work function metal layer
having a work function ranging between 4.8 eV and 5.2 eV such as
but not limited to for example titanium nitride (TiN), tantalum
nitride (TaN), or tantalum carbide (TaC), but not limited
thereto.
[0017] Preferably, the first conductive layer 30 covers the surface
of the substrate 16 and the sidewalls and top surface of the gate
dielectric layer 28 evenly, in which the first conductive layer 30
within the trenches 26 and outside the trenches 26 preferably has
even thickness. Specifically, the thickness of the first conductive
layer 30 on the top surface of the substrate 16 is equal to the
thickness of the first conductive layer 30 on the sidewalls of the
gate dielectric layer 28 and the thickness of the first conductive
layer on a top surface of the gate dielectric layer 28 in the
trench 26. Preferably, the thickness of the first conductive layer
30 is between 20-30 Angstroms and most preferably 20 Angstroms.
[0018] Next, as shown in FIG. 4, a second conductive layer 32 is
formed on the first conductive layer 30. Preferably, the second
conductive layer 32 is deposited on the first conductive layer 32
through a physical vapor deposition (PVD) process so that the
second conductive layer 32 on the substrate 16 and the second
conductive layer 32 below the substrate 16 preferably have
different thickness. Specifically, the second conductive layer 32
deposited by PVD process could be formed on the top surface of the
first conductive layer 30 outside the trenches 26 and the top
surface of the first conductive layer 30 within the trenches 26
without forming on the sidewalls of the first conductive layer 30
as shown in FIG. 4, or could be formed not only on the top surface
of first conductive layer 30 outside and within the trenches 26 but
also on the sidewalls of the first conductive layer 30 as shown in
FIG. 5.
[0019] According to an embodiment of the present invention, the
thickness of the second conductive layer 32 disposed on the top
surface of the substrate 16 (or outside the trenches 26) is
different from the thickness of the second conductive layer 32
disposed in the trenches 26. Specifically, the thickness of the
second conductive layer 32 disposed on the top surface of the
substrate 16 is greater than the thickness of the second conductive
layer 32 disposed on the top surface of first conductive layer 30
within the trenches 26.
[0020] As shown in FIG. 4, the second conductive layer 32 disposed
on the top surface of the substrate 16 outside the trenches 26
preferably includes a first thickness A, the second conductive
layer 32 disposed on the top surface of the first conductive layer
30 within the trenches 26 includes a second thickness B, and as
shown in FIG. 5, if the second conductive layer 32 were also formed
on the sidewalls of the first conductive layer 30 the second
conductive layer 32 would further include a third thickness C. In
this embodiment, the first thickness A is greater than the second
thickness B and the third thickness C and the second thickness B is
also greater than the third thickness C, in which the first
thickness A is preferably between 90-110 Angstroms or most
preferably 100 Angstroms, the second thickness B is preferably
between 20-30 Angstroms, and the third thickness C is preferably
less than 5 Angstroms. Preferably, the second conductive layer 32
and the first conductive layer 30 are made of different material.
For instance, the first conductive layer 30 preferably includes TiN
while the second conductive layer 32 includes Ti, but not limited
thereto.
[0021] Next, as shown in FIG. 6, an atomic layer deposition (ALD)
process is conducted to form a third conductive layer 34 on the
second conductive layer 32 and fill the trenches 26 completely, and
a thermal treatment process is conducted to lower the resistance of
the conductive layers during deposition process. In this
embodiment, the third conductive layer 34 preferably includes
cobalt (Co) and the temperature of the thermal treatment process is
preferably between 250.degree. C. to 500.degree. C., but not
limited thereto.
[0022] Next, as shown in FIG. 7, a planarizing process such as
chemical mechanical polishing (CMP) process is conducted to remove
part of the third conductive layer 34, part of the second
conductive layer 32, and part of the first conductive layer 30 to
form gate structures 36 in the trenches 26, in which the gate
structures 36 then become the word lines 14 shown in FIG. 1. Next,
an ion implantation process could be conducted depending on the
demand of the process to forma doped region (not shown) such as
lightly doped drain or source/drain region in the substrate 16
adjacent to two sides of the gate structures 36. Next, a contact
plug process could be conducted to form bit line contacts adjacent
to two sides of the gate structures 36 electrically connecting the
source/drain region and bit lines formed thereafter and storage
node contacts electrically connecting the source/drain region and
capacitors fabricated in the later process.
[0023] Referring again to FIG. 7, FIG. 7 further illustrates a
structural view of a buried word line of a DRAM according to an
embodiment of the present invention. As shown in FIG. 7, the buried
word line preferably includes at least a gate structure 36 embedded
within the substrate 16, in which the gate structure 36 preferably
includes a first conductive layer 30 disposed in the substrate 16,
a gate dielectric layer 28 disposed between the first conductive
layer 30 and the substrate 16, a second conductive layer 32
disposed on the first conductive layer 30, and a third conductive
layer 34 disposed on the second conductive layer 32. Specifically,
each of the gate dielectric layer 28 and first conductive layer 30
is U-shaped while the second conductive layer 32 is I-shaped, in
which the thickness of the I-shaped second conductive layer is
preferably between 20-30 Angstroms. The first conductive layer 30,
the second conductive layer 32, and the third conductive layer 34
are preferably made of different material, in which the first
conductive layer 30 preferably includes TiN, the second conductive
layer 32 preferably includes Ti, and the third conductive layer 34
preferably includes Co.
[0024] Referring to FIG. 8, FIG. 8 illustrates a structural view of
a buried word line of a DRAM according to an embodiment of the
present invention. According to an embodiment of the present
invention, if the second conductive layer were deposited not only
on the top surface of first conductive layer 30 outside and within
the trenches 26 but also on the sidewalls of the first conductive
layer 30, it would be desirable to follow similar processes as
disclosed in FIGS. 6-7 to form a third conductive layer 34 on the
second conductive layer 32, perform a thermal treatment process,
and conducting a planarizing process to remove part of the third
conductive layer 34, part of the second conductive layer 32, and
part of the first conductive layer 30 to obtain the structure as
shown in FIG. 8.
[0025] As shown in FIG. 8, the buried word line also includes at
least a gate structure 36 embedded in the substrate 16, in which
the gate structure 36 includes a first conductive layer 30 in the
substrate 16, a gate dielectric layer 28 between the first
conductive layer 30 and the substrate 16, a second conductive layer
32 on the first conductive layer 30, and a third conductive layer
34 on the second conductive layer 32.
[0026] Specifically, the gate dielectric layer 28, the first
conductive layer 30, and the second conductive layer 32 in this
embodiment are all U-shaped. Preferably, the second conductive
layer 32 in particular includes a horizontal portion 38 and two
vertical portions 40, in which the horizontal portion 38 and one of
the two vertical portions 40 have different thicknesses. For
instance, the thickness of the horizontal portion 38 is preferably
between 20-30 Angstroms while the thickness of each of the vertical
portions 40 is less than 5 Angstroms.
[0027] Overall, the present invention first forms at least a trench
in the substrate, deposits a first conductive layer preferably made
of TiN into the trench, and then forms a second conductive layer
preferably made of Ti on the first conductive layer through PVD
process, in which the thickness of the second conductive layer
within the trench preferably less than the thickness of the second
conductive layer outside the trench or on the top surface of the
substrate. Thereafter, a third conductive layer made of cobalt is
deposited through ALD process to fill the trench and a thermal
treatment process is conducted to repair gaps between lattice
structures. This provides a buried word line structure with defect
free and enhanced smooth surface as well as a device with better
resistance under small critical dimension environment.
[0028] Those skilled in the art will readily observe that numerous
modifications and alterations of the device and method may be made
while retaining the teachings of the invention. Accordingly, the
above disclosure should be construed as limited only by the metes
and bounds of the appended claims.
* * * * *