U.S. patent number 10,322,808 [Application Number 15/505,765] was granted by the patent office on 2019-06-18 for expandable seat leg attachment fixture.
This patent grant is currently assigned to Safran Seats USA LLC. The grantee listed for this patent is Safran Seats USA LLC. Invention is credited to Farhan Alamgir, Robert Trimble.







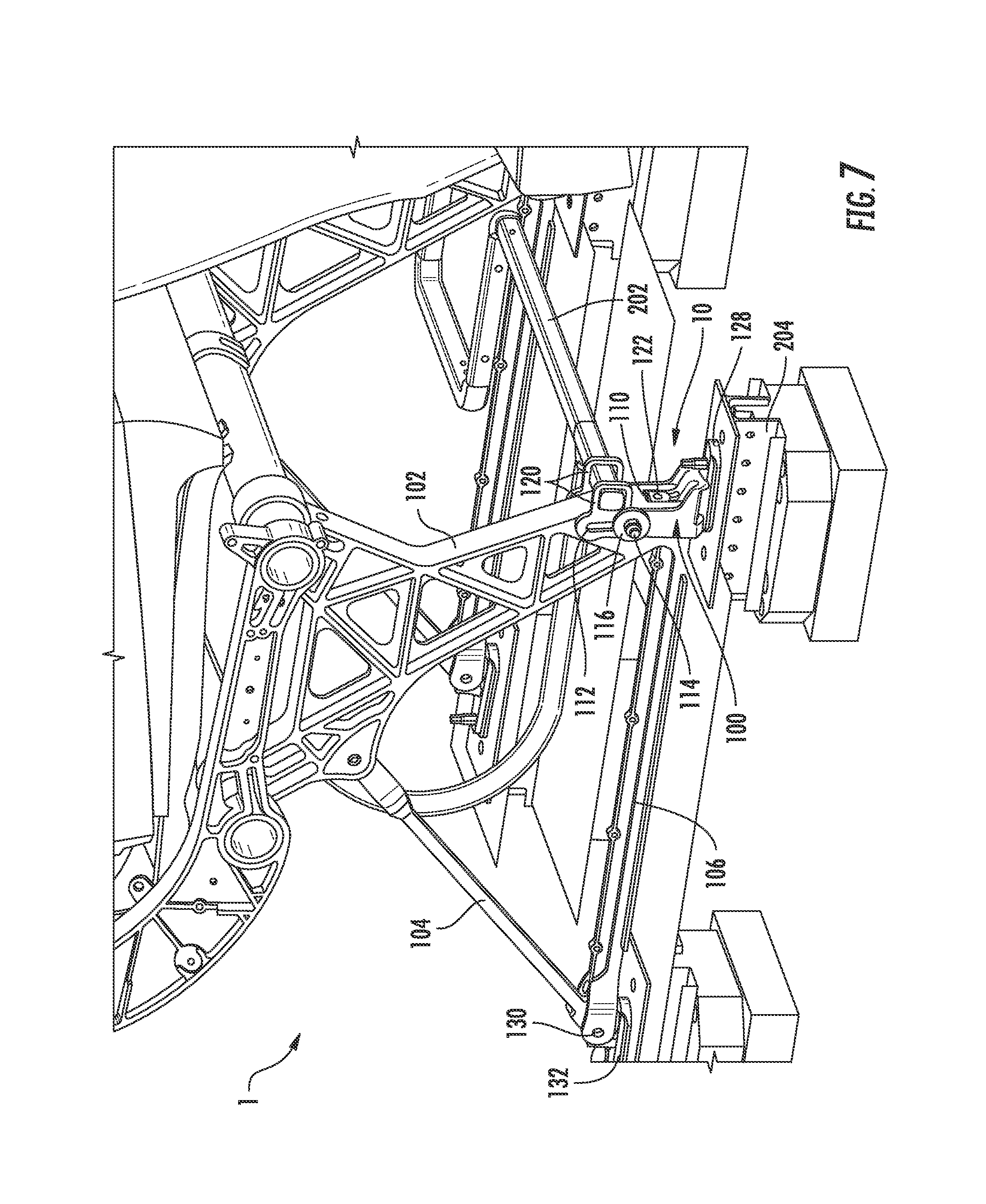
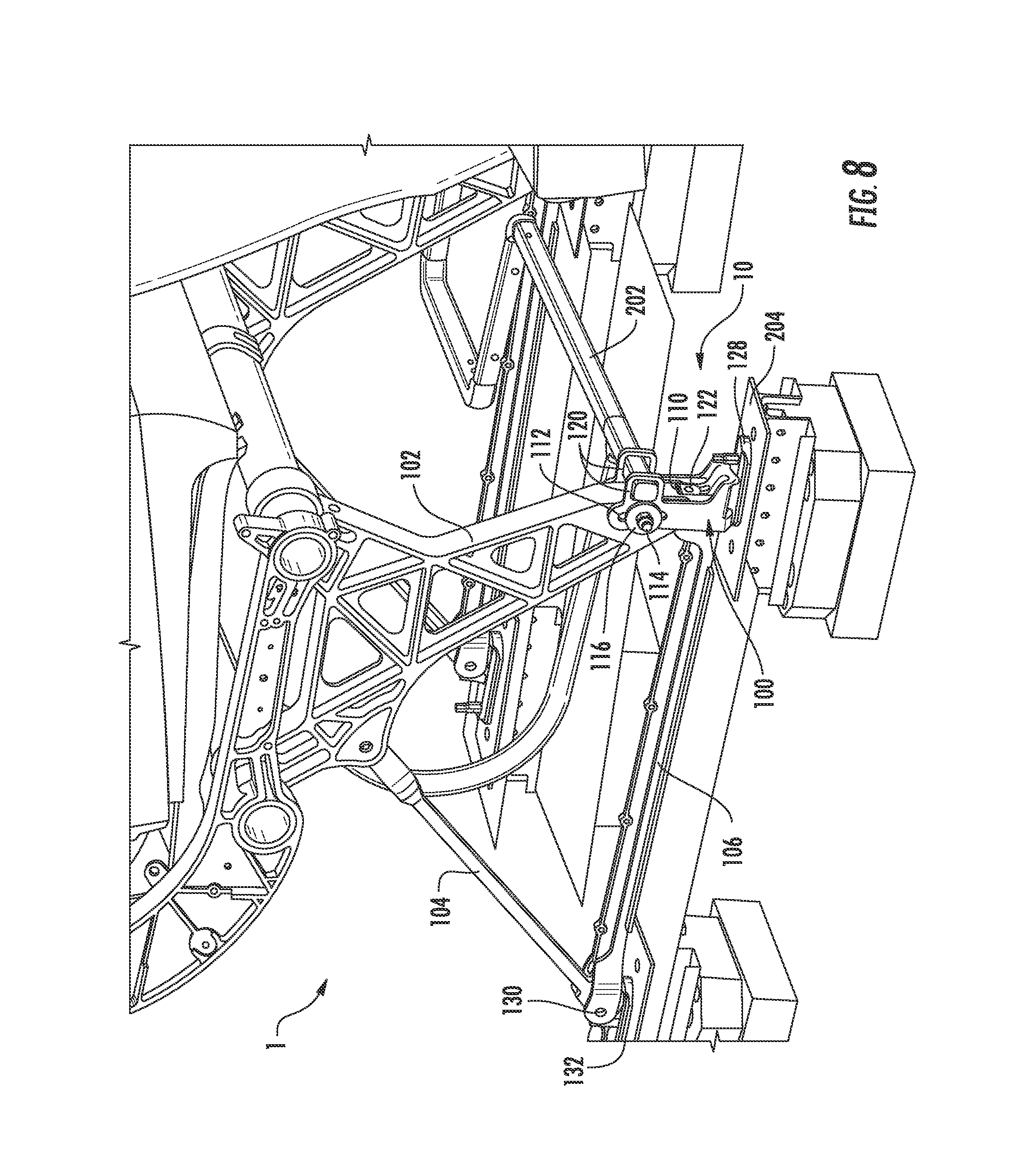


View All Diagrams
United States Patent |
10,322,808 |
Alamgir , et al. |
June 18, 2019 |
Expandable seat leg attachment fixture
Abstract
Described is an extendable joint (10,100) for attaching a
passenger seat to a cabin floor or support structure. The
extendable joint (10,100) exhibits behavior of a rigid mounting
during normal usage, such as when carrying or securing passengers
or luggage. However, if a force threshold is exceeded, such as with
an emergency situation, the extendable joint (10,100) may lengthen
to absorb energy applied from the cabin floor through the passenger
seat and vice versa. Additional force damping mechanisms may also
be incorporated into the joint to further absorb, distribute, or
reduce loadings that may otherwise separate the passenger seat from
the floor or support structure.
Inventors: |
Alamgir; Farhan (Denton,
TX), Trimble; Robert (Gainesville, TX) |
Applicant: |
Name |
City |
State |
Country |
Type |
Safran Seats USA LLC |
Gainesville |
TX |
US |
|
|
Assignee: |
Safran Seats USA LLC
(Gainesville, TX)
|
Family
ID: |
54147317 |
Appl.
No.: |
15/505,765 |
Filed: |
September 4, 2015 |
PCT
Filed: |
September 04, 2015 |
PCT No.: |
PCT/US2015/048563 |
371(c)(1),(2),(4) Date: |
February 22, 2017 |
PCT
Pub. No.: |
WO2016/037069 |
PCT
Pub. Date: |
March 10, 2016 |
Prior Publication Data
|
|
|
|
Document
Identifier |
Publication Date |
|
US 20170274999 A1 |
Sep 28, 2017 |
|
Related U.S. Patent Documents
|
|
|
|
|
|
|
Application
Number |
Filing Date |
Patent Number |
Issue Date |
|
|
62045597 |
Sep 4, 2014 |
|
|
|
|
Current U.S.
Class: |
1/1 |
Current CPC
Class: |
B60N
2/005 (20130101); B64D 11/0619 (20141201); B64D
11/06 (20130101); B64D 25/04 (20130101); B64D
11/0696 (20130101); B60N 2/42736 (20130101) |
Current International
Class: |
B64D
11/06 (20060101); B64D 25/04 (20060101); B60N
2/42 (20060101); B60N 2/005 (20060101); B60N
2/427 (20060101) |
References Cited
[Referenced By]
U.S. Patent Documents
Foreign Patent Documents
|
|
|
|
|
|
|
1190944 |
|
Mar 2002 |
|
EP |
|
1997028983 |
|
Aug 1997 |
|
WO |
|
2013076255 |
|
May 2013 |
|
WO |
|
Other References
International Patent Application No. PCT/US2015/048563, Search
Report and Written Opinion, dated Nov. 24, 2015. cited by
applicant.
|
Primary Examiner: Walraed-Sullivan; Kyle J.
Attorney, Agent or Firm: Kilpatrick Townsend & Stockton
LLP Russell; Dean W. Lucas; Davidson G.
Parent Case Text
CROSS REFERENCE TO RELATED APPLICATIONS
This patent application is the U.S. national stage of
PCT/US2015/048563 ("the '563 application"), filed on Sep. 4, 2015,
which application is related to and claims priority benefits from
U.S. Provisional Application Ser. No. 62/045,597 ("the '597
application"), filed on Sep. 4, 2014, entitled "Pitch Reducing
Fixture". The '563 and '597 applications are hereby incorporated in
their entireties by this reference.
Claims
That which is claimed is:
1. An extendable joint configured for a passenger seat, the
extendable joint comprising: a first joint portion comprising a
first slot; a second joint portion comprising a second slot; and a
preload mechanism, wherein: the preload mechanism stabilizes the
extendable joint up to a threshold force and allows a relative
motion between the first joint portion and the second joint portion
beyond the threshold force; after exceeding the threshold force, a
portion of the preload mechanism moves through at least a portion
of the first slot and through at least a portion of the second
slot; and in at least one position based on the relative motion
between the first joint portion and the second joint portion, the
first slot and the second slot are non-parallel with one
another.
2. The extendable joint of claim 1, further comprising: a third
joint portion; and a rotation joint; wherein the second joint
portion and the third joint portion may rotate with respect to one
another about the rotation joint.
3. The extendable joint of claim 1, further comprising: an
un-lengthened position wherein the portion of the preload mechanism
is disposed at an uppermost end of the first slot in the first
joint portion and the portion of the preload mechanism is disposed
at a lowermost end of the second slot in the second joint portion;
and a fully lengthened position wherein the portion of the preload
mechanism is disposed at a lowermost end of the first slot in the
first joint portion and the portion of the preload mechanism is
disposed at an uppermost end of the second slot in the second joint
portion.
4. The extendable joint of claim 1, wherein the first slot and the
second slot comprise a curve matching an arc of motion of the
extendable joint.
5. The extendable joint of claim 1, wherein the first joint portion
is configured to telescope relative to the second joint
portion.
6. The extendable joint of claim 1, wherein the first joint portion
and the second joint portion form a double-lap joint.
7. The extendable joint of claim 1, wherein the preload mechanism
comprises at least one of a bolt, a friction washer, a shear
fastener, a rip-through material, a crush material, a corrugated
metal, a honeycomb, or a collapsible tube.
8. The extendable joint of claim 1, further comprising a rebound
damping mechanism.
9. The extendable joint of claim 8, wherein the rebound damping
mechanism comprises at least one of a spring, a damper, a crushable
component, a shear pin, friction, binding of the extendable joint,
galling of the first joint portion, galling of the second joint
portion, or a friction washer.
10. The extendable joint of claim 1, wherein: the first joint
portion comprises a front seat leg with a first clearance recess;
the second joint portion comprises an extension fixture with a
second clearance recess; the portion of the preload mechanism
comprises a bolt passing through the first slot and the second
slot; and the bolt is torqued to a preload to prevent the relative
motion of the front seat leg and the extension fixture up to the
threshold force, the first clearance recess accommodates a portion
of the extension fixture, and the second clearance recess
accommodates a portion of the front seat leg.
11. The extendable joint of claim 1, wherein the second joint
portion comprises at least one clearance recess, wherein the at
least one clearance recess comprises an area adjacent to a raised
side wall of the second joint portion such that the at least one
clearance recess accommodates and provides clearance for a portion
of the first joint portion.
12. The extendable joint of claim 1, wherein the first joint
portion and the second joint portion rotate relative to one another
about the preload mechanism.
13. The extendable joint of claim 1, wherein the first slot and the
second slot each comprise a constant cross-section along an entire
length of each of the first slot and the second slot.
14. A passenger seat comprising: a front seat leg comprising a
first slot and a first clearance recess; a rear seat leg; a base
member; a rear leg joint; an extension fixture comprising a second
slot and a second clearance recess; and a preload mechanism;
wherein the front seat leg and the extension fixture are coupled
such that the first slot and the second slot are overlapping, the
first clearance recess accepts a portion of the extension fixture,
the second clearance recess accepts a portion of the front seat leg
to form an extendable joint, wherein: the preload mechanism
prevents relative motion of the front seat leg and the extension
fixture below a threshold force; and after exceeding the threshold
force, a portion of the preload mechanism moves through at least a
portion of the first slot and through at least a portion of the
second slot; and the relative motion of the front seat leg and the
extension fixture after exceeding the threshold force causes the
front seat leg to rotate about the rear leg joint.
15. The passenger seat of claim 14, wherein the base member is
rotatably coupled to the extension fixture to allow rotation of the
base member with respect to the extension fixture and the front
seat leg.
16. The passenger seat of claim 14, further comprising a baggage
loop configured to receive a baggage bar.
17. The passenger seat of claim 14, wherein the front seat leg
telescopes with respect to the extension fixture.
18. The passenger seat of claim 14, wherein the preload mechanism
comprises at least one of a bolt, a friction washer, a shear
fastener, a rip-through material, a crush material, a corrugated
metal, a honeycomb, or a collapsible tube.
19. The passenger seat of claim 14, further comprising a rebound
damping mechanism.
20. The passenger seat of claim 19, wherein the rebound damping
mechanism comprises at least one of a spring, a damper, a crushable
component, a shear pin, friction, binding of the extendable joint,
galling of the front seat leg, galling of the extension fixture, or
a friction washer.
21. A method for preventing separation of a passenger seat from a
cabin floor, the method comprising: providing a joint between a
front seat leg and a fixture; preloading the joint to prevent
relative motion of the of the front seat leg and the cabin floor
under normal conditions; and lengthening the joint such that the
cabin floor and the front seat leg may partially separate in
response to a force exceeding a threshold determined by the
preloading of the joint, wherein: the front seat leg comprises a
first slot and the fixture comprises a second slot; after exceeding
the threshold, a portion of the joint moves through at least a
portion of the first slot and through at least a portion of the
second slot; and during lengthening of the joint, in at least one
position of the joint, the first slot and the second slot are
non-parallel with one another.
22. The method of claim 21, further comprising damping a rebound
motion of the joint.
23. The method of claim 21, further comprising providing a rotation
joint between a base member and the cabin floor; and rotating the
base member relative to the cabin floor to prevent separation of
the passenger seat from the cabin floor.
Description
FIELD OF THE INVENTION
The field of the invention relates to passenger seats or the like,
and more particularly to safety components for passenger seats.
BACKGROUND
There has been continuous movement in carrier industries,
particularly with respect to air carriers, to improve and enhance
passenger safety, particularly in the area of regulatory
compliance. Passenger seats must pass through a number of
regulatory tests and certifications before they may be installed in
commercial vehicles. As a result, there is a push for new
technologies to improve passenger safety in survivable crashes and
maintain regulatory compliance by passing all applicable safety
testing.
Passenger seats have traditionally been rigidly mounted to a cabin
floor or other support structure within the vehicle. Rigid mounting
of seats improves passenger confidence and comfort. However, during
an emergency such as a survivable crash, deformation of the cabin
floor or support structures can lead to excessive loading and
separation of the passenger seat attachment points from the cabin
floor or support structures. Separation of the passenger seats from
the cabin floor or support structures not only results in reduced
survivability for passengers, but fails to meet certain regulatory
requirements. In particular, Federal Aviation Administration
guidelines contained within 14 C.F.R. 25.562, sometimes referred to
as the 16G Pitch and Roll Test, mandate that a seat mounting may
not separate from a cabin floor in the event of a distortion of the
cabin floor equivalent to a ten degree pitch and ten degree
roll.
In certain cases, it may be desirable to provide a passenger seat
with an extendable joint between the passenger seat frame and the
cabin floor or support structure. The extendable joint, which is
preloaded or otherwise restricted to prevent motion in normal
circumstances, allows the passenger seat legs or frame to extend
and move with the cabin floor or support structure when it deforms.
The extension of the passenger seat frame or leg absorbs and
distributes the forces applied to the passenger seat over a longer
period of time and a greater range of motion. The result is
decreased loading of the seat to floor attachment points and seat
frame resulting in a reduced likelihood of separation between the
passenger seat and the cabin floor, or failure of other parts of
the passenger seat frame. The extendable joint also provides
opportunities for additional components, such as crushable inserts
or springs, that may be used to further absorb forces resulting
from a crash or emergency situation.
SUMMARY
The terms "invention," "the invention," "this invention" and "the
present invention" used in this patent are intended to refer
broadly to all of the subject matter of this patent and the patent
claims below. Statements containing these terms should be
understood not to limit the subject matter described herein or to
limit the meaning or scope of the patent claims below. Embodiments
of the invention covered by this patent are defined by the claims
below, not this summary. This summary is a high-level overview of
various aspects of the invention and introduces some of the
concepts that are further described in the Detailed Description
section below. This summary is not intended to identify key or
essential features of the claimed subject matter, nor is it
intended to be used in isolation to determine the scope of the
claimed subject matter. The subject matter should be understood by
reference to appropriate portions of the entire specification of
this patent, any or all drawings and each claim.
According to certain embodiments of the present invention, an
extendable joint may comprise a first joint portion, a second joint
portion, and a preload mechanism. The preload mechanism may
stabilize the extendable joint up to a threshold force and allow
relative motion between the first joint portion and the second
joint portion beyond the threshold force.
In some embodiments, the extendable joint may further comprise a
third joint portion and a rotation joint. The second joint portion
and the third joint portion may then rotate with respect to one
another about the rotation joint.
In certain embodiments, the extendable joint may further comprise a
first slot in the first joint portion and a second slot in the
second joint portion. The first slot and the second slot may
comprise a curve matching an arc of motion of the extendable
joint.
In some embodiments, the first joint portion may be configured to
telescope relative to the second joint portion.
In certain embodiments, the first joint portion and the second
joint may form a double-lap joint.
In some embodiments, the preload mechanism may be selected from the
group consisting of a bolt, a friction washer, a shear fastener, a
rip-through material, a crush material, a corrugated metal, a
honeycomb, and a collapsible tube.
In certain embodiments, the extendable joint may further comprise a
rebound damping mechanism. The damping mechanism may be selected
from the group consisting of a spring, a damper, a crushable
component, a shear pin, friction, binding of the extendable joint,
galling of the first joint portion, galling of the second joint
portion, and a friction washer.
In some embodiments, the first joint portion may comprise a front
seat leg with a first slot and a first clearance recess, the second
joint portion may comprise an extension fixture with a second slot
and a second clearance recess, and the preload mechanism may
comprise a bolt passing through the first slot and the second slot.
The bolt may be torqued to a preload to prevent the relative motion
of the front seat leg and the extension fixture up to the threshold
force. The first clearance recess may accommodate a portion of the
extension fixture, and the second clearance recess may accommodate
a portion of the front seat leg.
According to certain embodiments of the present invention, a
passenger seat may comprise a front seat leg, which may comprise a
first slot and a first clearance recess, a rear seat leg, a base
member, a rear leg joint, an extension fixture, which may comprise
a second slot and a second clearance recess, and a preload
mechanism. The front seat leg and the extension fixture may be
coupled such that the first slot and the second slot are
overlapping. The first clearance recess may accept a portion of the
extension fixture, and the second clearance recess may accept a
portion of the front seat leg to form an extendable joint. The
preload mechanism may prevent relative motion of the front seat leg
and the extension fixture below a threshold force.
In some embodiments, the base member may be rotatably coupled to
the extension fixture to allow rotation of the base member with
respect to the extension fixture and the front seat leg.
In certain embodiments, the passenger seat may further comprise a
baggage loop configured to receive a baggage bar.
In some embodiments, the front seat leg may telescope with respect
to the extension fixture.
In certain embodiments, the preload mechanism may be selected from
the group consisting of a bolt, a friction washer, a shear
fastener, a rip-through material, a crush material, a corrugated
metal, a honeycomb, and a collapsible tube.
In some embodiments, the passenger seat may further comprise a
rebound damping mechanism. The rebound damping mechanism may be
selected from the group consisting of a spring, a damper, a
crushable component, a shear pin, friction, binding of the
extendable joint, galling of the front seat leg, galling of the
extension fixture, and a friction washer.
According to certain embodiments of the present invention, a method
for preventing separation of a passenger seat from a cabin floor
may comprise providing a joint between a front seat leg and the
cabin floor, preloading the joint to prevent relative motion of the
front seat leg and the cabin floor under normal conditions, and
lengthening the joint such that the cabin floor and the front seat
leg may partially separate in response to a force exceeding a
threshold determined by the preloading of the joint.
In some embodiments, the method for preventing separation of a
passenger seat from the cabin floor may further comprise damping a
rebound motion of the joint.
In certain embodiments, the method for preventing separation of a
passenger seat from the cabin floor may further comprise providing
a rotation joint between a base member and the cabin floor and
rotating the base member relative to the cabin floor to prevent
separation of the passenger seat from the cabin floor.
BRIEF DESCRIPTION OF THE DRAWINGS
FIG. 1 is a perspective view of an extension joint according to
certain embodiments of the present invention.
FIG. 2 is a front elevation view of the extension joint of FIG.
1.
FIG. 3 is a side elevation view of the extension joint of FIG.
1.
FIG. 4 is a perspective view of an extension joint according to
certain embodiments of the present invention.
FIG. 5 is a sectional view of the extension joint of FIG. 4.
FIG. 6 is a perspective view of an extension fixture according to
certain embodiments of the present invention.
FIG. 7 is a perspective view of an extension joint in an initial
position according to certain embodiments of the present
invention.
FIG. 8 is a perspective view of the extension joint of FIG. 7 in a
partially extended position.
FIG. 9 is a perspective view of the extension joint of FIG. 7 in a
fully extended position.
FIG. 10 is a perspective view of the extension joint of FIG. 7 in a
partially collapsed position.
FIG. 11 is a perspective view of the extension joint of FIG. 7 in a
fully collapsed position.
FIG. 12 is a sectional view of an extension joint in an initial
position according to certain embodiments of the present
invention.
FIG. 13 is a sectional view of the extension joint of FIG. 12 in a
partially extended position.
FIG. 14 is a sectional view of the extension joint of FIG. 12 in a
fully extended position.
FIG. 15 is a sectional view of the extension joint of FIG. 12 in a
partially collapsed position.
FIG. 16 is a sectional view of the extension joint of FIG. 12 in a
fully collapsed position.
DETAILED DESCRIPTION
The subject matter of embodiments of the present invention is
described here with specificity to meet statutory requirements, but
this description is not necessarily intended to limit the scope of
the claims. The claimed subject matter may be embodied in other
ways, may include different elements or steps, and may be used in
conjunction with other existing or future technologies. This
description should not be interpreted as implying any particular
order or arrangement among or between various steps or elements
except when the order of individual steps or arrangement of
elements is explicitly described.
The described embodiments of the invention provide for an
extendable attachment joint for securing the front leg of a
passenger seat to a floor or other structural support. While the
extendable joints are discussed for use with airline passenger
seats, they are by no means so limited. Rather, embodiments of the
extendable joint may be used in any passenger seat including, but
not limited to, automotive, marine, bus, train, or other commercial
passenger seats.
In some embodiments of the present invention, as shown in FIGS.
1-3, an extension joint 10 comprises an extension fixture 100
coupled to a front seat leg 102 and optionally a base member 106. A
rear seat leg 104 may also be coupled to the front seat leg 102 and
the base member 106 and connected to the cabin floor or other
support structure at the rear leg joint 130. The front seat leg
102, rear seat leg 104, and base member 106 may be affixed or
otherwise attached to one another to form a basic passenger seat
leg assembly, which carries the load from a passenger and
associated seat hardware and transfers that load into the cabin
floor or other support structures (not shown). In certain
embodiments, the rear leg joint 130 may allow the rear seat leg 104
and/or base member 106 to rotate, freely or with some level of
resistance, about the rear leg joint 130 and/or the rear floor
mount 132. The front seat leg 102 and base member 106 may be joined
together at the extension fixture 100, which may be attached to the
cabin floor or other support structures through the front floor
mount 128.
The front seat leg 102 and base member 106 are attached to the
front floor mount 128 through the extension fixture 100. The
extension fixture 100 may comprise one or more uprights 101 with
apertures such as fixture slots 112. In certain embodiments, the
fixture slots 112 may be straight, or they may be curved or
otherwise contoured such that the fixture slots 112 follow the arc
of rotation defined by the distance of the fixture slot from the
rear leg joint 130. A curved or otherwise contoured fixture slot
112 may then allow the base member 106 to rotate about the rear leg
joint 130 through the range of motion of the extension joint 10
without binding. The front seat leg 102 is affixed or otherwise
attached to the extension fixture 100 through the use of a bolt 114
that passes through the fixture slots 112 and is secured with a nut
118. In some embodiments, washers 116 may be used to distribute the
forces from the bolt 114 and nut 118 and/or to modify or alter the
preloading and fixture properties of the bolt 114 and nut 118 as
they pass through the fixture slots 112 and front seat leg 102. The
base member 106 may be attached to the extension fixture 100 with a
bolt 124. In certain embodiments, the base member 106 is affixed or
attached to the extension fixture 100 through a rotation joint 122
(FIG. 4) that allows for the extension fixture 100 to rotate about
the axis of the bolt 124 relative to the base member 106. The
extension fixture 100 may then be affixed or otherwise attached to
the cabin floor or other support structure directly or through the
front floor mount 128.
In some embodiments, the front seat leg 102 may be modified or
otherwise optimized for use with the extension fixture 100. For
example, the front seat leg 102 may include a clearance recess 110
and a leg slot 111 (FIG. 5). The clearance recess 110 and/or leg
slot 111 may allow for greater overlap of the front seat leg 102
with the extension fixture 100. For example, the leg slot 111 may
be co-planar, co-linear, or otherwise aligned with the fixture
slots 112 such that the bolt 114 may pass through the leg slot 111
and fixture slots 112 to secure the extension fixture 100 to the
front seat leg 102. The bolt 114 may be positioned at the bottom of
the fixture slots 112 and at the top of the leg slot 111 so that
during extension, the extension joint 10 may expand by the combined
length of the fixture slots 112 and the leg slot 111. In some
embodiments, the leg slot 111 may be curved or otherwise contoured
as described with reference to fixture slots 112 above. Greater
overlap of the front seat leg 102 and extension fixture 100 allows
for greater lengthening of the extension joint 10 during an
extension event. Similarly, the extension fixture 100 may include
fixture clearance recesses 108 to allow for greater overlap of the
front seat leg 102 and extension fixture 100. In certain
embodiments, the extension fixture 100 may include one or more
loops 120 to receive a baggage bar (not shown) or other structural
components of the passenger seat not described above.
Certain embodiments of the extension joint 10 may include
additional or alternative features to those shown in FIGS. 1-3. For
example, in some embodiments, the front seat leg 102 and extension
fixture 100 may be tubular structures, wherein one tubular
structure is of a smaller diameter and may telescope into or out of
the other structure. In certain other embodiments, the front seat
leg 102 and extension fixture 100 may be configured to such that
the extension joint 10 is a lap joint, or a double lap joint as
shown in FIGS. 1-3.
Still referring to FIGS. 1-3, the extension joint 10 and the
structure of the extension fixture 100 in combination with a
standard or modified front seat leg 102 allows the cabin floor or
other structural support to move relative to the front seat leg 102
in an emergency situation. Under normal operating conditions, such
as supporting a passenger and/or luggage loads, the extension joint
10 will function in a manner similar to a standard seat leg
attachment. That is, the front seat leg 102 will behave as though
it were rigidly attached to the cabin floor or support structure
without any relative motion between the front seat leg 102 and the
extension fixture 100. However, in an emergency situation, once a
threshold level of force is applied between the cabin floor or
support structures and the passenger seat, the front seat leg 102
and extension fixture 100 will move relative to one another and
lengthen the extension joint 10. By allowing the extension joint 10
to lengthen, forces applied between the cabin floor or support
structure and the passenger seat are decreased and/or spread out
over a long period of time and/or a greater displacement of the
extension joint 10. By lengthening the extension joint 10, the
forces applied between the cabin floor or support structure and
passenger seat, and thus the front seat leg 102 and extension
fixture 100, are reduced. The reduction of forces may prevent or
reduce the likelihood of separation of the front floor mount 128
from the cabin floor or support structure.
In order to allow for the extension joint 10 to function as a rigid
mounting under normal conditions but allow for relative motion of
the front seat leg 102 and extension fixture 100 under emergency
conditions, the extension joint must be preloaded or otherwise
secured such that it will not lengthen unless a certain threshold
level of force is applied to the extension joint 10. The extension
fixture 100 must also be affixed or otherwise attached to the front
seat leg 102 in a manner that allows relative motion between the
two parts, but that will not allow for complete separation of the
front seat leg 102 and extension fixture 100 in emergency
circumstances when the extension joint 10 is fully lengthened and
has reached the end of its range of motion. In certain embodiments,
the extension joint 10 may be held together through the use of the
bolt 114 that passes through the fixture slots 112, and through the
front seat leg 102 and/or the optional leg slot 111. In some
embodiments, the extension joint may be held together with pins,
rivets, or other fasteners. The bolt 114, pin, rivet, or other
fastener should be chosen such that it will not shear and allow
complete separation of the extension joint 10. Rather, the bolt 114
or other fastener may act as a stop to prevent the extension joint
10 from failing and allowing complete separation of the front seat
leg 102 and extension fixture 100.
The extension joint 10 may be preloaded or otherwise tuned to
resist forces below a threshold through any number of mechanical or
structural mechanisms or components. For example, the extension
fixture 100 may be attached or otherwise affixed to the front seat
leg 102 with the bolt 114 passing through the fixture slots 112 and
the front seat leg 102 and/or leg slot 111. The bolt 114 may be
secured with the use of a nut 118. The bolt 114 and nut 118 may be
torqued down sufficiently such that the friction between the head
of the bolt 114, nut 118, and extension fixture 100 is sufficient
to prevent relative movement between the extension fixture 100 and
front seat leg 102 under normal conditions. However, the amount of
torque applied to the bolt 114, and the subsequent frictional force
between the bolt 114 and the extension fixture 100 may be tuned so
that in an emergency situation, the clamping force of the bolt 114
and nut 118 will allow the extension joint 10 to lengthen in
response to the increased loading in an emergency situation. In
certain embodiments, washers 116 may be used to alter or modify the
frictional properties between the bolt 114 and the extension
fixture 100 and/or between the nut 118 and the extension fixture
100. The amount of preload and subsequent threshold force necessary
to cause lengthening of the extension joint 10 may be increased by
using a washer 116 that is embedded with or otherwise includes
diamond powder, carbides, locking structures, or other abrasives or
friction enhancing features. The extension joint 10 may also
include a number of other mechanisms or components to adjust or
tune the amount of joint preload and subsequent threshold force
required to allow for lengthening of the extension joint 10. For
example, shear fasteners, a crush material, corrugated metal, a
honeycomb, or a collapsible tube may be incorporated into the
extension joint 10 such that the material must be sheared or
otherwise deformed to allow the extension joint 10 to lengthen.
Similarly, the fixture slots 112 and/or leg slot 111 may comprise a
groove or thinner section of material than the body of the
extension fixture 100 or the front seat leg 102. The bolt 114 or
other fastener may then tear through this thinner section of
material or groove once the forces applied to the extension joint
10 have exceeded a threshold value. In some embodiments, the above
mentioned preloading or threshold force mechanisms may also provide
resistance to continued lengthening of the extension joint 10
throughout its range of motion. The continued resistance may serve
to absorb additional energy throughout an extension event. For
example, the frictional force of the torqued bolt 114, or the
continued shear, material deformation, or material yielding of
other force limiting components, will provide a drag or resistance
on the lengthening of the extension joint 10 and absorb energy as
it continues through its range of motion.
In certain embodiments, the extension joint 10 may also include
additional mechanisms to absorb forces both on extension and on
rebound or collapse of the extension joint after it has lengthened.
For example, the extension joint 10 may include springs, dampers,
crushable components, and/or shear components that dampen or absorb
energy during lengthening of the extension joint 10 or during the
rebound and collapse of the extension joint 10 in an emergency
situation. In some embodiments, the friction of the bolt 114 and/or
optional washers 116 may continue to resist relative motion of the
extension fixture 100 and the front seat leg 102 during collapse or
rebound of the extension joint 10. The kinematics and motion of the
extension joint 10 itself may also provide some resistance to
motion or energy absorption. For instance, depending on the amount
of clearance between the extension fixture 100 and front seat leg
102 and the forces applied to the extension joint 10, the extension
fixture 100 and front seat leg 102 may become misaligned and bind
or otherwise interfere with one another, thereby causing additional
friction and/or energy absorption. Also, the bolt 114 and/or nut
118 may cut into, gall, or otherwise deform the extension fixture
100 and/or front seat leg 102 and absorb the energy of lengthening
or collapse of the extension joint 10.
FIG. 4 is a perspective view of an extension joint 10 attached to a
floor support 204 and integrated into a passenger seat. The
extension fixture 100 is affixed or otherwise attached to the floor
support 204 through a front floor mount 128. The base member 106 is
attached to the extension fixture 100 at the rotation joint 122.
The front seat leg 102 is positioned between the uprights 101 and a
bolt 114 passing through the fixture slots 112 and the front seat
leg 102 is secured by nut 118 and washer 116. The extension fixture
100 includes loops 120 that are configured to receive baggage bar
202. In certain embodiments, the front seat leg 102 may include a
clearance recess 110 configured to allow for a greater overlap
between the front seat leg 102 and the extension fixture 100 and
provide clearance with the rotation joint 122. Similarly, the
extension fixture 100 may include fixture clearance recesses 108 to
allow for additional overlap and clearance between the extension
fixture 100 and any protuberances or extensions of the front seat
leg 102.
FIG. 5 is a sectional view of the extension joint 10 depicted in
FIG. 4. The extension fixture 100 is affixed or otherwise attached
to the base member 106 at the rotation joint 122. The rotation
joint allows for articulation of the extension fixture 100 about
the axis of the extension joint 122 with respect to the base member
106. This extra degree of freedom allows the extension joint 10 to
rotate in an emergency situation, preventing unwanted binding or
restriction of the extension joint 10 that my cause it to not
lengthen as intended. Furthermore, the addition of the rotation
joint 122 may allow for the extension fixture 100 to be directly
mounted to the cabin floor or structural supports without the need
a separate mounting fixture. The front seat leg 102 is positioned
between the uprights 101 of the extension fixture 100. A bolt 114
passes through fixture slot 112 and leg slot 111 to secure the
front seat leg 102 to the extension fixture 100. A washer 116 is
included with the bolt 114. The extension fixture includes loop 120
that is configured to receive other parts of the seat structure,
such as a baggage bar.
Still referring to FIG. 5, the front seat leg 102 includes a
clearance recess 110 configured to accommodate the rotation joint
122 and allow for increased overlap of the front seat leg 102 and
extension fixture 100. Similarly, the extension fixture 100
includes fixture clearance recess 108 to accommodate the lower
portions of the front seat leg 102. The extension fixture 100 is
secured to the cabin floor or support structure through front floor
mount 128.
The extension joint 10 is shown in an initial, or un-lengthened,
position. In this position, the maximum overlap between the
extension fixture 100 and front seat leg 102 may be desirable. To
allow for the greatest amount of overlap, and consequently the
largest amount of lengthening of the extension joint 10, the bolt
114 is positioned at the lower extremity of the fixture slot 112
and the upper extremity of the leg slot 111. When the extension
joint 10 lengthens, the bolt 114 may move through the entire length
of the fixture slot 112 and the entire length of the leg slot 111
to provide a longer range of motion than if only a single slot were
used. For example, as the front seat leg 102 and extension fixture
100 move away from one another to disengage, the bolt 114 will
translate from the bottom of the fixture slot 112 to the top of the
fixture slot 112. During this motion, the bolt 114 may also
translate through the leg slot 111 from its uppermost extremity to
its lower extremity. In order to facilitate the motion of the bolt
114 through both the fixture slot 112 and the leg slot 111, the
fixture slot 112 and leg slot 111 may be co-linear, co-planar, or
otherwise aligned such that the motion of the bolt 114 through the
fixture slot 112 is compatible with the motion of the bolt 114
through the leg slot 111 and vice versa. In certain embodiments,
the fixture slot 112 and/or leg slot 111 may be curved or otherwise
contoured to reflect the kinematics and motion of the front seat
leg 102 and/or extension fixture 100 during a lengthening
event.
FIG. 6 is a perspective view of saddle-type extension fixture 100.
The extension fixture 100 may comprise two uprights 101 that
include fixture slots 112 configured to allow a bolt or other
fastener to pass through the fixture slots 112. The extension
fixture 100 may also include a rotation joint 122 to allow the
extension fixture to pivot about a base member (not shown), loops
120 to receive additional seat structures or components, and/or
fixture clearance recesses 108 to accommodate or otherwise provide
space for a front seat leg (not shown) or other components. The
saddle-type extension fixture 100 is configured to cradle a seat
leg between the uprights 101 and pin or otherwise fasten the
extension fixture 100 to the seat leg by passing a fastener through
the fixture slots 112. The fixture slots 112 also provide the
motion path for the lengthening of the extension joint in an
emergency situation. As shown, the extension fixture 100 would
provide for a double-lap type joint between the extension fixture
100 and a seat leg. However, the extension fixture 100 may also be
configured to provide a telescoping joint, a single lap joint,
and/or such that the uprights 101 fit within the seat leg.
FIGS. 7-11 are perspective views of a passenger seat assembly 1
incorporating an extension joint 10 during various stages of an
emergency situation and/or testing simulation. The passenger seat
assembly 1 comprises a front seat leg 102, rear seat leg 104, and
base member 106. The rear seat leg 104 and base member 106 are
affixed or otherwise attached to one another at the rear leg joint
130, which is attached to the cabin floor or structural support
through rear floor mount 132. The base member 106 is affixed or
otherwise attached to the extension fixture 100 at the rotation
joint 122. Front seat leg 102, including leg slot 111 and clearance
recess 110, is positioned within the extension fixture 100. Bolt
114 passes through fixture slot 112 and leg slot 111 to connect the
front seat leg 102 to the extension fixture 100. Washer 116 may
provide additional friction modification to bolt 114. The extension
fixture 100 also includes loops 120, which are configured to
receive baggage bar 202. The front floor mount 128 rigidly connects
the floor support 204 to the extension fixture 100, and ties the
extension joint 10 and its associated components to the cabin floor
or support structure.
FIG. 7 shows the passenger seat assembly 1 and the extension joint
10 in an initial, un-lengthened position. In this position, the
front seat leg 102 and extension fixture 100 are fully engaged and
have the greatest amount of overlap between their components and
the fixture slots 112 and leg slot 111. In FIG. 8, the floor
support 204 has been moved downwards, moving the front floor mount
128 and the extension fixture 100 with it. Under these conditions,
the threshold force to overcome the preload of the extension joint
10 has been met, and the extension joint 10 has begun to lengthen.
As shown, as the extension fixture 100 moves downward with the
floor support 204, the extension fixture 100 and front seat leg 102
begin to disengage and separate. Bolt 114 is displaced from its
previous position in FIG. 7, and the baggage bar 202 has begun to
articulate downwards with the extension fixture 100. FIG. 9 shows
the extension joint 10 in a fully lengthened position. Here, the
floor support 204 has completed its downward motion and the front
seat leg 102 and extension fixture 100 are fully disengaged and
extended. The bolt 114 has been displaced from its original
position at the lower extremity of the fixture slot 112 and upper
extremity of the leg slot 111 to a new position at the lower
extremity of the leg slot and upper extremity of the fixture slot
112. In this position, the bolt 114 will prevent further
lengthening and separation of the extension joint 10. In this
position, the base member 106 and baggage bar 202 have also
articulated and/or rotated downwards in response to the lowering of
the floor support 204. The baggage bar 202, because of its
attachment to the extension fixture 100 through loops 120, has
followed the displacement of the floor (not shown) as the floor
support 204 has been lowered. As a result, the baggage bar 202 will
maintain its relationship to the floor and continue to restrain any
luggage or items that were stowed under the passenger seat assembly
1. Also, rotation joint 122 has allowed the extension fixture 100
to pivot about the base member 106 as it articulates through its
range of motion. By allowing the extension fixture 100 to rotate
about the base member, the extension fixture 100 and extension
joint 10 maintain proper alignment with the front seat leg 102
without excessive binding that would interfere with the lengthening
and proper function of the extension joint 10.
In FIG. 10, the extension joint 10 has begun to collapse because
the floor support 204 has reached the end of its motion, and the
passenger seat assembly 1 has begun to rebound and fall, causing
the extension joint 10 to return to an engaged, un-lengthened,
position. The front seat leg 102 and leg slot 111 are partially
engaged and overlapped with the extension fixture 100 and fixture
slots 112. The bolt 114 is also displaced within the slots 111, 112
such that it is not at an extremity of one or more of the slots
111, 112. FIG. 11 shows the extension joint 10 in a fully collapsed
position after the passenger seat assembly 1 has fully rebounded
into a rest position. The floor support 204 remains in a lowered
position, and the base member 106 and baggage bar 202 are rotated
or articulated from their original starting positions. Here, the
front seat leg 102 is fully engaged with the extension fixture 100.
The front seat leg 102 and leg slot 111 are fully overlapped with
the extension fixture 100 and fixture slots 112. Due to the motion
of the extension joint 10, the bolt 114 may not return to its
original position and may remain partially or fully displaced as
shown. By allowing the lengthening of the extension joint 10, the
force applied to the passenger seat assembly 1 and front floor
mount 128 has been greatly reduced because it has been extended
over a longer period of time and a longer range of motion. This
reduction in force results in a reduced likelihood of separation
between the front floor mount 128 and the floor support 204, and a
reduced likelihood of damage to other components in the passenger
seat assembly 1. Furthermore, the reduction in force and increased
flexibility of the extension joint 10 may help prevent damage to
other seat mounts or joints such as the rear floor mount 132 and
rear leg joint 130.
FIGS. 12-16 are sectional vies of the extension joint 10 as it
moves through its range of motion from an initial, un-lengthened,
position (FIG. 12), to a fully extended position (FIG. 14), and a
fully collapsed position (FIG. 16). The extension joint 10 may
comprise an front seat leg 102 including a leg slot 111 and
clearance recess 110. The front seat leg 102 is slidably coupled to
the extension fixture 100 by bolt 114, which passes through upright
101 via the fixture slot 112 and leg slot 111. Washer 116 may
provide improved frictional properties or force distribution from
the torqued bolt 114. The base member 106 is affixed or otherwise
attached to the extension fixture 100 through rotation joint 122.
The extension fixture 100 also includes loop 120 to receive
additional seat structures or components, and fixture clearance
recess 108 to accommodate the lower portions of the front seat leg
102. The extension joint 10 is rigidly attached to the cabin floor
or support structure (not shown) through the front floor mount
128.
The extension joint 10 begins in an initial, un-lengthened position
(FIG. 12), wherein the front seat leg 102 is fully engaged within
the upright 101 of the extension fixture 100. In this position, the
bolt 114 is at the upper extremity of the leg slot 111 and the
lower extremity of the fixture slot 112. The clearance recess 110
and fixture clearance recess 108 facilitate greater overlap of the
front seat leg 102 and extension fixture 100. As the front floor
mount 128 is pulled downwards, as with a test procedure or in an
emergency, the extension joint 10 begins to lengthen and disengage
the front seat leg 102 from the extension fixture 100 (FIG. 13).
The bolt 114 is displaced within the fixture slot 112 and leg slot
111 as the extension joint 10 lengthens to absorb distribute forces
applied through the front floor mount 128. As the front floor mount
128 continues its relative downward motion, the extension joint 10
will eventually reach a fully lengthened position (FIG. 14). In
this position, the bolt 114 has reached the upper extremity of the
fixture slot 112 and the lower extremity of the leg slot 111. In
this position, the interference of the bolt 114 with the walls of
the fixture slot 112 and/or leg slot 111 will prevent further
extension and separation of the extension joint 10. As shown, to
allow for additional length of the leg slot 111, the leg slot may
extend below the clearance recess 110 into the lower extremities of
the front seat leg 102, which are received by the fixture clearance
recesses 108.
After the front floor mount 128 has reached its final position, the
extension joint 10 will begin to collapse and return to a fully
engaged, un-lengthened, position (FIG. 15). The front seat leg 102
will begin its downward motion to re-engage the extension fixture
100. As the front seat leg 102 rebounds, the leg slot 111 and
fixture slots 112 will begin to overlap, and the bolt 114 will be
displaced within the slots 111, 112. The front seat leg 102 will
continue its downward motion until it is fully engaged with the
extension fixture 100 (FIG. 16). In this position, the extension
joint 10 is in a collapsed position, and has returned to
substantially its original length. Due to the displacement of the
bolt 114 through the range of motion of the extension joint 10, the
bolt may remain displaced from its initial position. However,
because of the clamping force of the bolt, or any other applicable
force absorbing or dampening components or mechanisms, the
extension joint 10 may still retain all or a portion of its
preload. As a result, the extension joint 10 may endure multiple
loading cycles while maintaining its force absorption and movement
threshold properties.
Any of the above described components, parts, or embodiments may
take on a range of shapes, sizes, or materials as necessary for a
particular application of the described invention. The components,
parts, or mechanisms of the described invention may be made of any
materials selected for the suitability in use, cost, or ease of
manufacturing. Materials including, but not limited to aluminum,
stainless steel, fiber reinforced plastics, carbon fiber,
composites, polycarbonate, polypropylene, other metallic materials,
or other polymers may be used to form any of the above described
components.
Different arrangements of the components depicted in the drawings
or described above, as well as components and steps not shown or
described are possible. Similarly, some features and
sub-combinations are useful and may be employed without reference
to other features and sub-combinations. Embodiments of the
invention have been described for illustrative and not restrictive
purposes, and alternative embodiments will become apparent to
readers of this patent. Accordingly, the present invention is not
limited to the embodiments described above or depicted in the
drawings, and various embodiments and modifications may be made
without departing from the scope of the claims below.
* * * * *