U.S. patent number 10,303,840 [Application Number 15/498,804] was granted by the patent office on 2019-05-28 for integrated circuit manufacture using direct write lithography.
This patent grant is currently assigned to ARM Limited. The grantee listed for this patent is ARM Limited. Invention is credited to Gregory Munson Yeric.

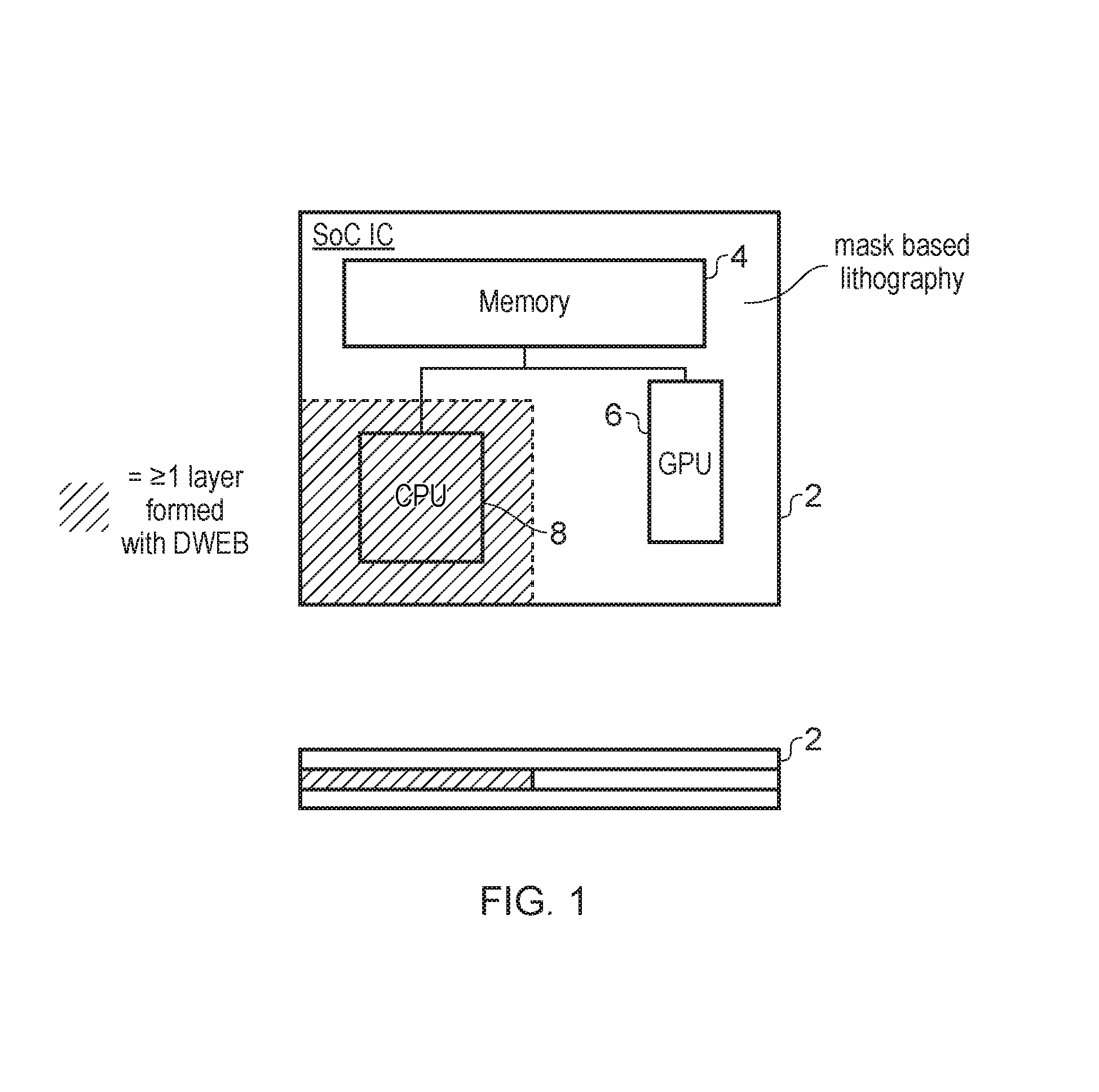
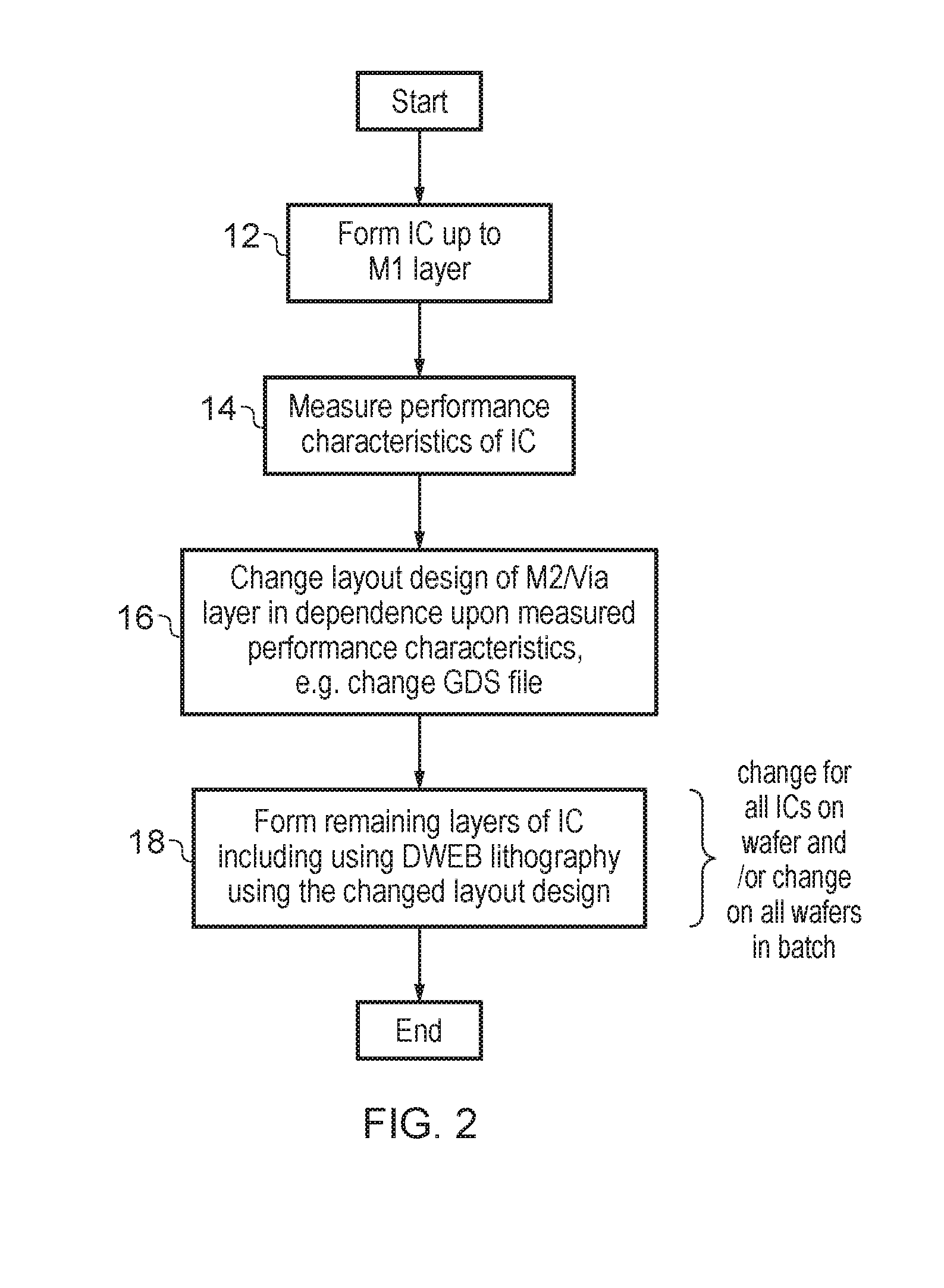



United States Patent |
10,303,840 |
Yeric |
May 28, 2019 |
Integrated circuit manufacture using direct write lithography
Abstract
Integrated circuits are manufactured using a direct write
lithography step to at least partially form at least one layer
within the integrated circuit. The performance characteristics of
an at least partially formed integrated circuit are measured and
then the layout design to be applied with a direct write
lithography step is varied in dependence upon those performance
characteristics. Accordingly, the performance of an individual
integrated circuit, wafer of integrated circuits or batch of wafers
may be altered.
Inventors: |
Yeric; Gregory Munson (Austin,
TX) |
Applicant: |
Name |
City |
State |
Country |
Type |
ARM Limited |
Cambridge |
N/A |
GB |
|
|
Assignee: |
ARM Limited (Cambridge,
GB)
|
Family
ID: |
50736119 |
Appl.
No.: |
15/498,804 |
Filed: |
April 27, 2017 |
Prior Publication Data
|
|
|
|
Document
Identifier |
Publication Date |
|
US 20170228493 A1 |
Aug 10, 2017 |
|
Related U.S. Patent Documents
|
|
|
|
|
|
|
Application
Number |
Filing Date |
Patent Number |
Issue Date |
|
|
13944129 |
Jul 17, 2013 |
9672316 |
|
|
|
Current U.S.
Class: |
1/1 |
Current CPC
Class: |
H01L
21/027 (20130101); H01L 22/14 (20130101); G03F
7/70383 (20130101); G03F 7/70433 (20130101); H01L
22/20 (20130101); G06F 30/398 (20200101); G06F
2119/18 (20200101) |
Current International
Class: |
G03F
7/20 (20060101); G06F 17/50 (20060101); H01L
21/66 (20060101); H01L 21/027 (20060101) |
Field of
Search: |
;716/112 |
References Cited
[Referenced By]
U.S. Patent Documents
Foreign Patent Documents
|
|
|
|
|
|
|
1425197 |
|
Jun 2003 |
|
CN |
|
101002141 |
|
Jul 2007 |
|
CN |
|
102 707 581 |
|
Oct 2012 |
|
CN |
|
2 203 529 |
|
Jul 2010 |
|
EP |
|
1 834 358 |
|
Jan 2012 |
|
EP |
|
63-274156 |
|
Nov 1988 |
|
JP |
|
H3-38862 |
|
Feb 1991 |
|
JP |
|
H06-69345 |
|
Mar 1994 |
|
JP |
|
H08-272480 |
|
Oct 1996 |
|
JP |
|
H10-112504 |
|
Apr 1998 |
|
JP |
|
2000-200812 |
|
Jul 2000 |
|
JP |
|
2003-520451 |
|
Jul 2003 |
|
JP |
|
2005-268774 |
|
Sep 2005 |
|
JP |
|
2007-59785 |
|
Mar 2007 |
|
JP |
|
2008-11323 |
|
Jan 2008 |
|
JP |
|
2010-238797 |
|
Oct 2010 |
|
JP |
|
2010-251468 |
|
Nov 2010 |
|
JP |
|
2011-77423 |
|
Apr 2011 |
|
JP |
|
2012-137986 |
|
Jul 2012 |
|
JP |
|
10-1101698 |
|
Dec 2011 |
|
KR |
|
200705229 |
|
Feb 2007 |
|
TW |
|
200935265 |
|
Aug 2009 |
|
TW |
|
WO 89/11659 |
|
Nov 1989 |
|
WO |
|
WO 97/45770 |
|
Dec 1997 |
|
WO |
|
WO 2009/052120 |
|
Apr 2009 |
|
WO |
|
Other References
Australian Examination Report dated Jun. 6, 2017 in AU 2014291840,
4 pages. cited by applicant .
Taiwanese Office Action dated Feb. 12, 2018 in TW Application No.
103116991 and English translation, 29 pages. cited by applicant
.
Singaporean Office Action dated Mar. 28, 2018 in SG Application No.
11201600093P, 7 pages. cited by applicant .
Japanese Office Action dated May 25, 2018 in JP Application No.
2016-526688 and English translation, 7 pages. cited by applicant
.
U.S. Appl. No. 13/944,129, filed Jul. 17, 2013, Inventor: Yeric.
cited by applicant .
Office Action dated Jan. 30, 2015 in co-pending U.S. Appl. No.
13/944,129 14 pages. cited by applicant .
Office Action dated May 18, 2016 in co-pending U.S. Appl. No.
13/944,129 15 pages. cited by applicant .
Black et al., "Supplemental multilevel interconnects by laser
direct writing: Application to GaAs digital integrated circuits",
Lincoln Lab, Massachusetts Institute of Technology, Feb. 1987, 3
pages. cited by applicant .
Ehrlich et al., "Emerging technology for in situ processing:
Patterning alternatives", Lincoln Lab, Massachusetts Institute of
Technology, Feb. 1988, 5 pages. cited by applicant .
International Search Report and Written Opinion of the
International Searching Authority dated Sep. 24, 2014 in
PCT/GB2014/051398, 10 pages. cited by applicant .
Chinese Office Action dated Jan. 25, 2017 in CN 201480038762.9 and
English translation, 12 pages. cited by applicant .
Chinese Second Office Action dated Aug. 1, 2017 in CN
201480038762.9 and English translation, 8 pages. cited by applicant
.
Japanese Office Action dated Sep. 22, 2017 in JP 2016-526688 and
English translation, 9 pages. cited by applicant .
Written Opinion dated Jan. 8, 2019 in SG Application 11201600093P,
6 pages. cited by applicant.
|
Primary Examiner: Alam; Mohammed
Attorney, Agent or Firm: Nixon & Vanderhye P.C.
Parent Case Text
This application is a divisional of U.S. patent application Ser.
No. 13/944,129 filed Jul. 17, 2013, the entire content of which is
hereby incorporated by reference in this application.
Claims
I claim:
1. A method of manufacturing integrated circuits having one or more
layers with a respective integrated circuit layout design at least
partially formed using a direct write lithography step, said method
comprising the steps of: changing said integrated circuit layout
design of at least one of said one or more layers to be formed
using said direct write lithography step to configure one or more
circuit elements within said integrated circuit to provide an
electrically-readable identifier for said integrated circuit; and
forming said at least one of said one or more layers using said
direct write lithography step in accordance with said changed
integrated circuit layout design.
2. An integrated circuit formed in accordance with a method as
claimed in claim 1.
3. A method of manufacturing system-on-chip integrated circuits
having a plurality of independently designed functional blocks and
one or more layers with a respective integrated circuit layout
design at least partially formed using a direct write lithography
step, said method comprising the steps of: changing said integrated
circuit layout design of at least one of said one or more layers to
be formed using said direct write lithography step to change a
design of one of said plurality of functional blocks while leaving
other of plurality of functional blocks unchanged; and forming said
at least one of said one or more layers using said direct write
lithography step in accordance with said changed integrated circuit
layout design.
4. An integrated circuit formed in accordance with a method as
claimed in claim 3.
5. A method of manufacturing integrated circuits having one or more
layers with a respective integrated circuit layout design at least
partially formed using a direct write lithography step, said method
comprising: measuring one or more performance characteristics of an
at least partially formed integrated circuit; changing said
integrated circuit layout design of at least one of said one or
more layers to be formed using said direct write lithography step
in dependence upon said one or more performance characteristics to
generate a changed layout design; and forming said at least one of
said one or more layers using said step of direct write lithography
in accordance with said changed integrated circuit layout design,
wherein said at least one of said one or more layers formed using
said changed integrated circuit layout design is formed partially
by direct-write lithography and partially by mask-based
lithography.
6. An integrated circuit formed in accordance with a method as
claimed in claim 5.
7. A method of manufacturing integrated circuits having one or more
layers with a respective integrated circuit layout design at least
partially formed using a direct write lithography step, said method
comprising: measuring one or more performance characteristics of an
at least partially formed integrated circuit; changing said
integrated circuit layout design of at least one of said one or
more layers to be formed using said direct write lithography step
in dependence upon said one or more performance characteristics to
generate a changed integrated circuit layout design; and forming
said at least one of said one or more layers using direct write
lithography in accordance with said changed integrated circuit
layout design, wherein said changing is an automatic feedback
process performed in accordance with a predetermined rule.
8. An integrated circuit formed in accordance with a method as
claimed in claim 7.
Description
BACKGROUND
This invention relates to the field of manufacturing integrated
circuits. More particularly, this invention relates to the use of
direct write lithography techniques as part of integrated circuit
manufacture.
It is known to manufacture integrated circuits using a sequence of
masks for forming different layers within the integrated circuit.
The manufacture of suitable masks is a time consuming and expensive
operation.
It is known to utilise direct write lithography during the
manufacture of integrated circuits. In particular, it is known to
use techniques such as direct write electron beam lithography to
correct manufacturing defects in individual integrated circuits
that have been manufactured. As an example, if an integrated
circuit has been manufactured with a short circuit between two
printed features, then direct write electron beam lithography may
be used to remove that short circuit and restore proper operation
to the integrated circuit. Such operations provide defect
correction within a fixed layout design.
Other direct write lithographic techniques are known. These include
inkjet circuit printing and aerosol jet circuit printing. These
techniques are becoming increasingly capable of producing circuits
of small size to the extent that they may be used to manufacture
integrated circuits.
A problem that is increasing as process size decreases in
integrated circuit manufacture is that of unwanted variability in
the size and positioning of circuit features. This can reduce the
yield of correctly operating integrated circuits and adversely
affect the performance characteristics of integrated circuits
taking them outside of a desired range.
SUMMARY
Viewed from one aspect the present invention provides a method of
manufacturing integrated circuits having one or more layers with a
respective layout design at least partially formed using a direct
write lithography step, said method comprising the steps of:
measuring one or more performance characteristics of an at least
partially formed integrated circuit; changing said layout design of
at least one of said one or more layers to be formed using said
direct write lithography step in dependence upon said one or more
performance characteristics to generate a changed layout design;
and forming said at least one of said one or more layers using said
step of direct write lithography in accordance with said changed
layout design.
The present technique uses direct write lithography in the
manufacture of at least part of at least one layer within the
integrated circuit. A performance characteristic of the integrated
circuit is measured and the layout design of one or more layers to
be formed using the direct write lithography is changed in
dependence upon the measured performance characteristic. Thus, the
layout design to which the integrated circuit is manufactured is
modified in dependence upon measured performance characteristics of
an at least partially formed integrated circuit. As direct write
lithography does not use fixed and expensive masks, it is practical
to modify the layer formed using direct write lithography in
response to measured performance characteristic feedback on an
individual integrated circuit basis, on the basis of individual
wafers of integrated circuits, or on the basis of batches of
wafers. The present techniques may be used to alter the design of a
partially manufactured integrated circuit. The present techniques
may also be used to alter the design of subsequently manufactured
integrated circuits, i.e. not the individual integrated circuit
that was subject to performance measurement.
The changing of the layout design may be performed as an automatic
feedback process in accordance with a predetermined rule. For
example, rules may be established whereby if a particular portion
of the integrated circuit is operating too slowly or too quickly,
then predetermined changes can be made which are known to alter the
speed of operation in the desired sense.
The layers which are formed by direct write lithography may be
partially formed by the direct write lithography and partially by
mask based lithography. Direct write lithography may be slower than
mask based lithography and accordingly direct write lithography may
be utilised on a restricted basis for those portions of a layer for
which it is desired to be able to dynamically change the layout
design.
As previously mentioned, the direct write lithography may take a
variety of different forms. For example, the direct write
lithography may be one of direct light electron beam lithography,
direct write inkjet circuit printing and direct write aerosol jet
circuit printing (gravure and intaglio printing technologies).
The layout design used by direct write lithographic techniques is
typically provided in the form of a computer file for controlling a
direct write lithography machine. A change to the layout design may
be conveniently and inexpensively made by changing the computer
file for driving such a machine (optionally using the predetermined
rules mentioned above).
The one or more performance characteristics which are measured can
take a variety of different forms. For example, minimum operating
voltage may be a measured parameter. However, a performance
characteristics well suited for adjustment using changes to the
design layout is that of the speed of operation of at least a
portion of the integrated circuit.
The step of measuring may be performed on a fully completed or
partially completed integrated circuit. It is convenient that the
measuring is performed after forming a first metal layer within an
integrated circuit and prior to completing manufacture of the
integrated circuit. After formation of the first metal layer,
useful information can be gathered regarding the performance
characteristics of the integrated circuit formed up to that point
and any adjustments to the layout design which may be made can take
effect in the subsequently formed layers to bring the measured
performance characteristics back to a desired level if
necessary.
The measuring of the performance characteristics may be performed
using one or more test circuit areas located within the integrated
circuit. Specific canary circuits may, for example, be included for
the purposes of measuring the speed of operation of an individual
integrated circuit to gather information that may be used to alter
the circuit layout.
The changes to the layout design may be made in a variety of
different ways. Convenient changes to layout design which can have
well controlled effects are changes to the second or higher metal
layer, a local interconnect layer or a via layer. Changing the
electrical connections within the integrated circuit design in this
way may be used to provide relatively deterministic changes to the
performance characteristics of the integrated circuit.
Examples of the changes to the layout design which may be made
include changing a number of gate fingers connected within a buffer
circuit thereby changing the drive strength of the buffer circuit.
Another design change which may be made within an integrated
circuit including a plurality of instances for circuit element is
to change the number of those instances of the circuit element
connected so as to be active during operation of the integrated
circuit. Thus, for example, a number of inverters used to drive a
node may be changed by changing the layout in a manner which brings
the drive strength of that node to a desired level.
Another change to the layout design which can alter the performance
characteristics in a desired manner is to change one or more
interconnect lines within the integrated circuit so as to alter the
resistance and/or capacitance of those interconnect lines.
When the interconnect lines comprise one or more parallel
interconnect lines, the configuration that may be changed is to
include or remove connections between those parallel interconnect
lines in a manner which changes their resistance and/or
capacitance. Another change which may be made to interconnect lines
is to change their transverse cross sectional area in a manner that
can change their resistance and/or capacitance.
The capacitance associated with an integrated line, and accordingly
its speed, may be changed by including shielding of the
interconnect line that changes in its effectiveness, e.g. providing
a shielding conductor which is changed from having a floating
potential to a grounded potential.
Viewed from another aspect the present invention provides a method
of manufacturing integrated circuits having one or more layers with
a respective layout design at least partially formed using a direct
write lithography step, said method comprising the steps of:
changing said layout design of at least one of said one or more
layers to be formed using said direct write lithography step to
configure one or more circuit elements within said integrated
circuit to generate an electrically readable identifier for said
integrated circuit; and forming said at least one of said one or
more layers using said direct write lithography step in accordance
with said changed layout design.
The direct write lithographic techniques applied during manufacture
to change the design of an integrated circuit layout may be used to
provide an electrically readable identifier for an integrated
circuit that is built in during manufacture by virtue of the layout
design used, e.g. integrated circuits could be signed and/or dated
using changes in the layout design permitted by the use of direct
write lithographic techniques. Such changes would not be cost
effective if masks needed to be changed as the time taken and cost
involved would be too high.
Viewed from a further aspect the present invention provides a
method of manufacturing system-on-chip integrated circuits having a
plurality of independently designed functional blocks and one or
more layers with a respective layout design at least partially
formed using a direct write lithography step, said method
comprising the steps of: changing said layout design of at least
one of said one or more layers to be formed using said direct write
lithography step to change a design of one of said plurality of
functional blocks while leaving other of plurality of functional
blocks unchanged; and forming said at least one of said one or more
layers using said direct write lithography step in accordance with
said changed layout design.
The present techniques may be used to update the layout design of a
portion of an integrated circuit while leaving other portions of
that integrated circuit unaltered. Thus, in a system-on-chip
integrated circuit comprising independently designed functional
blocks, some of those functional blocks could be formed using
direct light lithography in a manner which would permit their
design to be changed while other of the functional blocks are left
unaltered, e.g. are manufactured by mask based techniques.
Viewed from a further aspect the present invention provides a
method of manufacturing integrated circuits having one or more
layers with a respective layout design at least partially formed
using a direct write lithography step, said method comprising the
steps of: at least partially forming a plurality of instance of
said integrated circuit each having a different form of said layout
design; measuring one or more performance characteristics of said
plurality instances of said integrated circuit; selecting as a
selected layout design one of said different forms of said layout
design of at least one of said one or more layers to be formed
using said direct write lithography step in dependence upon said
one or more performance characteristics; and forming said at least
one of said one or more layers using said step of direct write
lithography in accordance with said selected layout design.
It is possible that a plurality of layout designs are formed and
tested in advance and then, in dependence upon a measured
performance characteristic, the layout design to be used in the
further manufacture of that integrated circuit is selected among
the plurality of pre-existing layout designs.
The above, and other objects, features and advantages of this
invention will be apparent from the following detailed description
of illustrative embodiments which is to be read in connection with
the accompanying drawings.
BRIEF DESCRIPTION OF THE DRAWINGS
FIG. 1 schematically illustrates a system-on-chip integrated
circuit in which one functional block includes a layer manufactured
by direct write electron beam lithography;
FIG. 2 is a flow diagram schematically illustrating the dynamic
alteration of a layout design during manufacture;
FIG. 3 is a diagram schematically illustrating an example change in
layout design that may be used to alter the number of gate fingers
that are active within a buffer circuit;
FIG. 4 schematically illustrates a number of instances of an
inverter with a change to the layout design formed by direct light
electron beam lithography being used to change the number of these
instances which are active;
FIGS. 5, 6, 7, 8 and 9 schematically illustrate tuning techniques
which may be applied to interconnect lines using connections
selectively formed in accordance with direct light electron beam
lithography.
DESCRIPTION OF EXAMPLE EMBODIMENTS
FIG. 1 schematically illustrates a system-on-chip integrated
circuit 2 including a plurality of functional blocks, such as a
memory 4, a graphics processing unit 6 and a general purpose
processor 8. At least one layer within the general purpose
processor 8 is formed using direct write electron beam lithography.
The portion of the system-on-chip integrated circuit which is
formed using this direct write lithographic technique is
illustrated as shaded in FIG. 1. FIG. 1 shows both a plan view and
a cross-sectional view of the integrated circuit 2.
FIG. 2 is a flow diagram schematically illustrating a manufacturing
process of an integrated circuit in which the layout design of one
or more layers may be altered. At step 12 the integrated circuit is
formed up to and including the Metal 1 layer. At step 14, one or
more performance characteristics of the partially manufactured
integrated circuit are measured. These performance characteristics
may be measured at predetermined test areas within the integrated
circuit, such as specifically provided ring oscillators or canary
circuits.
At step 16, the measured performance characteristics are compared
with desired performance characteristics and a change in the layout
design of the Metal 2 and/or via layer is made in dependence upon
those measured performance characteristics. This change in the
layout design may be conveniently made by changing an associated
GDS file defining the layout design. Direct write electron beam
lithography machines may be provided which read GDS files defining
circuit layout, fracture those designs and then drive the electron
beams to manufacture the appropriate circuit layout layer.
At step 18 the remaining layers of the integrated circuits are
manufactured including using the direct write electron beam
lithographic technique to form at least part of at least one of the
remaining layers that are formed (other techniques such as direct
write inkjet circuit printing, direct write aerosol circuit
printing and gravure and intaglio printing technologies may also be
used).
The changes to the layout design made at step 16 may be made for an
individual integrated circuit, all integrated circuits manufactured
on the same wafer and/or for all wafers in a given batch of
wafers.
FIG. 3 schematically illustrates the cross-section through a
portion of an integrated circuit including a substrate 20 on which
are formed a plurality of gate fingers 22. The gate fingers 22 are
part of a buffer circuit and the drive strength of that buffer
circuit may be altered by changing the number of gate fingers that
are active. Individual gate fingers 22 may be made active or
inactive by changing whether or not they are connected using the
via layer V1 to the Metal 2 layer M2. Thus, in accordance with the
present techniques, the layout design may be actively changed
following formation of the Metal 1 layer M1 by changing whether or
not individual via connections in the V1 layer are made to the
Metal 2 layer thereby either connecting or isolating the associated
gate finger 22.
FIG. 4 schematically illustrates a portion of the integrated
circuit in which a plurality of instances of an inverter 24 are
provided and which may act in parallel to drive a node 26. The node
26 may be a test area used to establish whether the speed of an
integrated circuit is nominal. If the speed is too low, then the
number of inverters driving that node may be increased. Conversely,
if the speed is too high, then the number of inverters driving that
node may be decreased. Metal connections between two of the
inverters 24 and the node 26 are formed using direct write electron
beam lithography and accordingly may be removed by an appropriate
change in the layout design so as to change the drive strength
applied to the node 26.
FIG. 5 schematically illustrates an interconnect line 28 which is
selectively coupled to a tuning line 30 via links 32. The links 32
are formed by direct write electron beam lithography and
accordingly the layout design may be dynamically changed to either
include or not include individual links 32. Thus, the capacitance
and/or resistance (and therefore speed) of the combination of the
main signal line 28 and the tuning line 30 may be altered.
FIG. 6 schematically illustrates a variation upon the arrangement
shown in FIG. 5. In this example, the tuning line 30 is replaced by
a plurality of tuning capacitances 34, 35 which may be connected or
not connected to the main signal line 36 using vias from above or
below the turning line 30. Connecting or not connecting a tuning
strap 34 alters the capacitance of the main signal line 36 and
accordingly the speed with which a signal change is propagated by
that main signal line.
FIG. 7 schematically illustrates another example change in the way
that an interconnect line is provided. In this example, the number
of connections between the different portions of the interconnect
line are altered thereby changing the resistance of the
interconnect line. The resistance of the interconnect line is
changed to change the speed of propagation of a signal along the
signal line and thereby adjust the performance parameters by a
change in the layout design (i.e. a number of links between
adjacent sections of the interconnect line).
FIG. 8 schematically illustrates another type of variation which
may be made to interconnect lines. In this example, the width of
the cross-section of the interconnect lines is varied to move their
edges closer to or further from shielding lines. Changing the space
in between the interconnect line and its shielding changes the
speed with which a signal may propagate along that interconnect
line. At least the portions of the width of the interconnect line
which are to be varied may be formed with direct write electron
beam lithography as illustrated and accordingly changed in
accordance with the measured performance characteristics of an
individual integrated circuit wafer or batch of wafers.
FIG. 9 illustrates a further example of the way in which the
performance characteristics of an interconnect circuit may be
tuned. In this example, an interconnect line is provided with
shielding lines and the layout design is changed by changing
whether or not those shielding lines are connected to ground or are
allowed to float. Connecting a shielding line to ground will tend
to slow down signal propagation along the interconnect line.
Accordingly, the fastest interconnect line illustrated in FIG. 9 is
the one in which both shielding conductors are floating. The
slowest interconnect line is the one in which both shielding
conductors are grounded and the nominal interconnect line is the
one in which one of the shielding conductors is floating and one of
the shielding conductors is grounded.
The layout design of a portion of the integrated circuit formed by
direct write lithography may be varied so as to provide a varying
electrically readable identifier for the integrated circuit. Thus,
any individual integrated circuit, wafer or batch of wafers may
have its layout changed to hardwire a particular value into a
register which may then be electrically read. In this way, an
individual integrated circuit could have a serial number attached
to it in a manner which it would not be possible to change without
destroying the integrated circuit.
The changes to the layout design of the portion of the integrated
circuit manufactured by direct write lithography may have been
determined in advance. For example, in the case of FIG. 4,
different layout designs may have been formed in advance which
respectively connect one, two or three of the inverters 24 to the
node 26. When the speed of the partially formed integrated circuit
has been determined, and it has been determined how many of the
inverters 24 should be connected to the node 26 to achieve the
desired performance level, then the appropriate one of these
preformed layout designs may be selected for use in the further
manufacture of the integrated circuits.
In some embodiments of the technique, integrated circuits
manufactured in accordance with a plurality of different layout
designs apply using direct beam lithography may be produced and
tested. In dependence upon those test results, a particular layout
design among those tested may be selected for further use in the
series production of the integrated circuit at a wafer or batch
level.
Although illustrative embodiments of the invention have been
described in detail herein with reference to the accompanying
drawings, it is to be understood that the invention is not limited
to those precise embodiments, and that various changes and
modifications can be effected therein by one skilled in the art
without departing from the scope and spirit of the invention as
defined by the appended claims.
* * * * *