U.S. patent application number 17/570987 was filed with the patent office on 2022-04-28 for steel reinforced joint, steel reinforced assembly, and precast steel reinforced concrete body.
The applicant listed for this patent is Akira Fukuda. Invention is credited to Akira Fukuda, Keiji Hirai, Kozo Wakiyama.
Application Number | 20220127838 17/570987 |
Document ID | / |
Family ID | 1000006134942 |
Filed Date | 2022-04-28 |
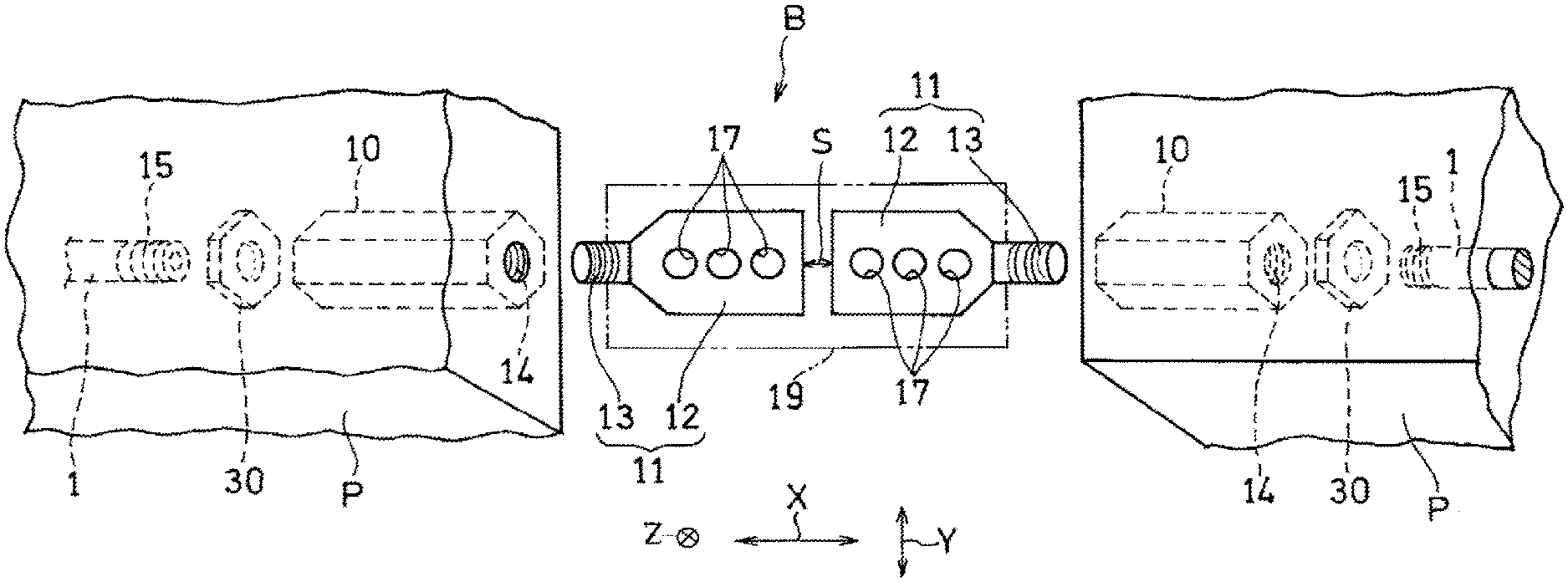

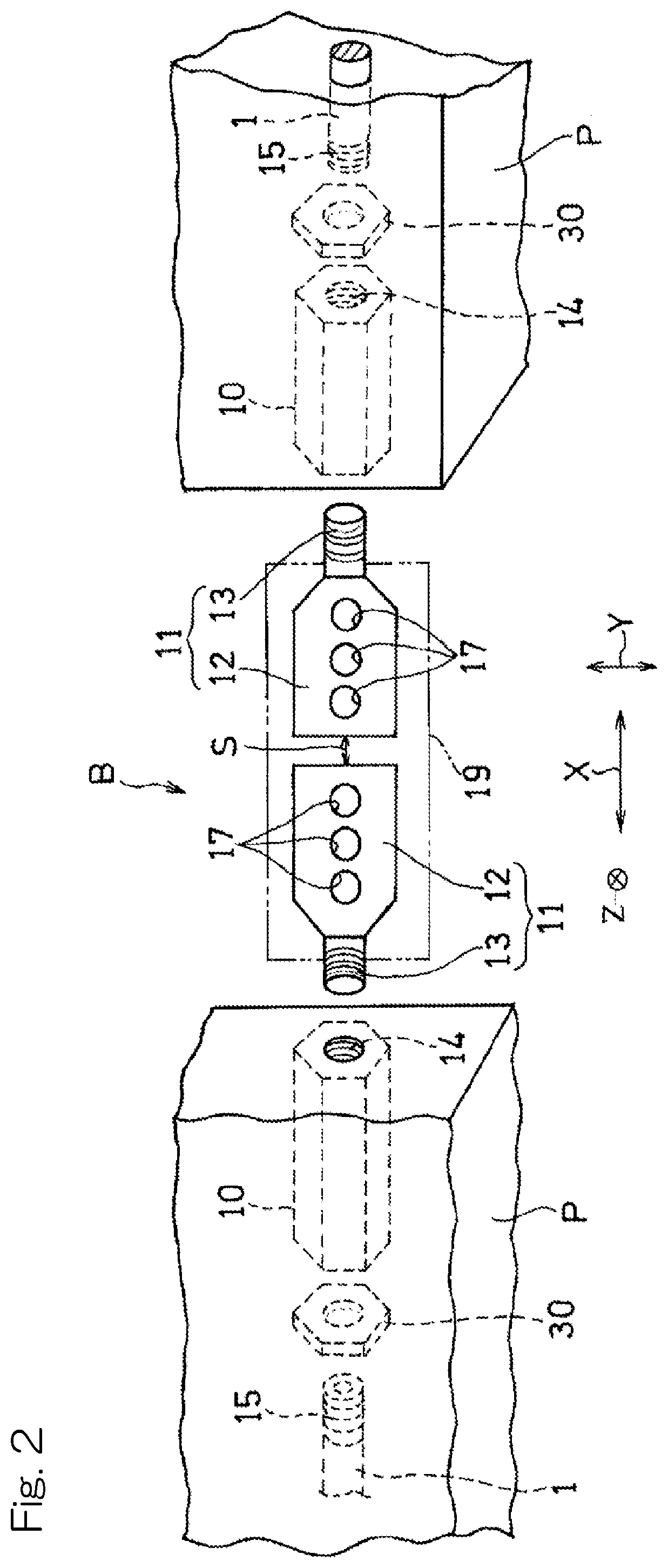

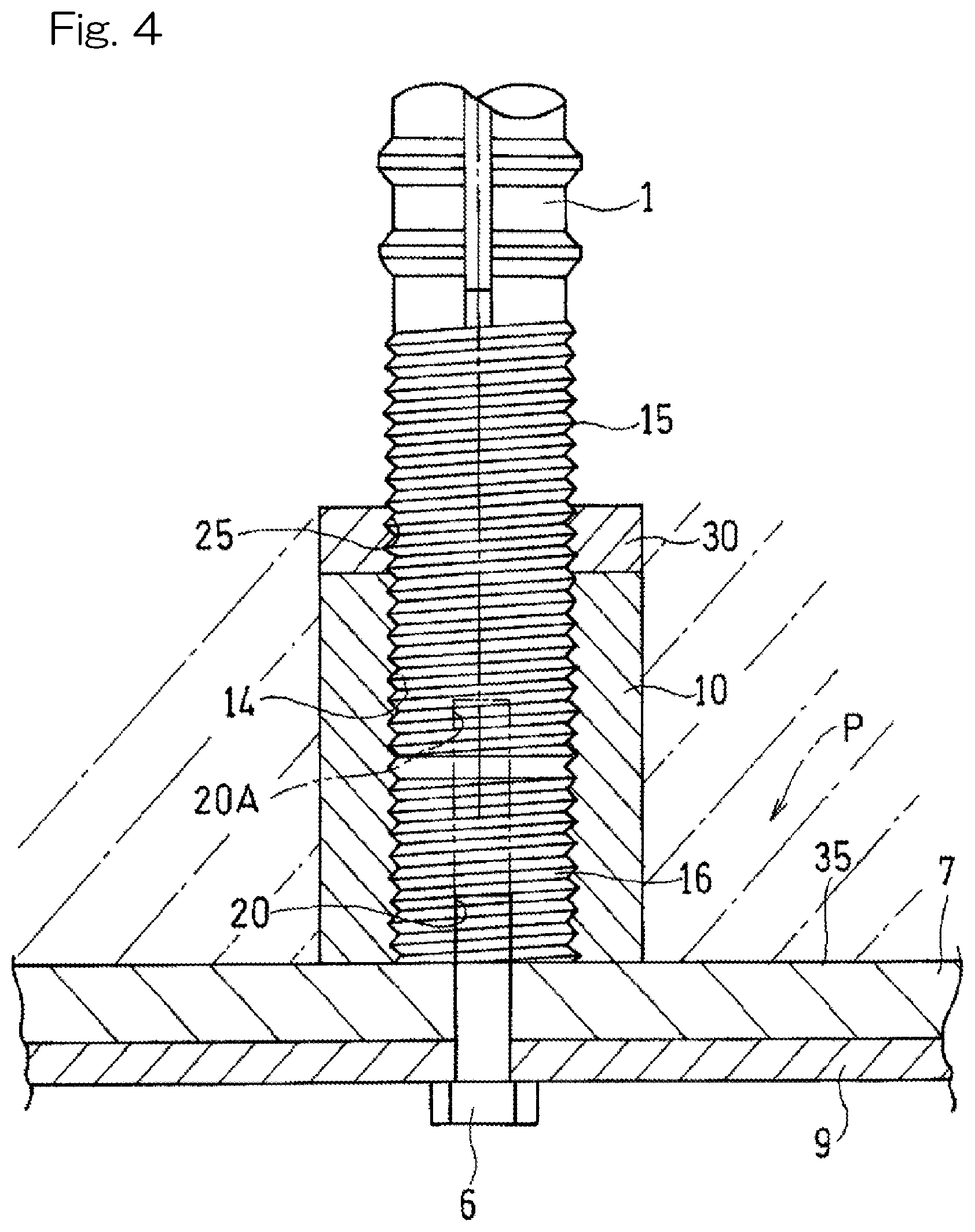




United States Patent
Application |
20220127838 |
Kind Code |
A1 |
Fukuda; Akira ; et
al. |
April 28, 2022 |
STEEL REINFORCED JOINT, STEEL REINFORCED ASSEMBLY, AND PRECAST
STEEL REINFORCED CONCRETE BODY
Abstract
A reinforcing bar joint includes: cylindrical bodies each
including an inner surface including a female thread part; joint
members each including one end portion including a joint male
thread part; and a connecting member configured to connect a pair
of the joint members which face each other, such that the pair of
the joint members are allowed to move in the longitudinal direction
and in an orthogonal direction to the longitudinal direction. Each
of the cylindrical bodies includes one end portion configured to
threadedly engage with a reinforcing bar male thread part at an end
portion of one of reinforcing bars, and the other end portion
configured to threadedly engage with the joint male thread part at
the one end portion of a corresponding one of the joint
members.
Inventors: |
Fukuda; Akira; (Osaka,
JP) ; Wakiyama; Kozo; (Osaka, JP) ; Hirai;
Keiji; (Miyako-gun, JP) |
|
Applicant: |
Name |
City |
State |
Country |
Type |
Fukuda; Akira |
Osaka |
|
JP |
|
|
Family ID: |
1000006134942 |
Appl. No.: |
17/570987 |
Filed: |
January 7, 2022 |
Related U.S. Patent Documents
|
|
|
|
|
|
Application
Number |
Filing Date |
Patent Number |
|
|
PCT/JP2019/029052 |
Jul 24, 2019 |
|
|
|
17570987 |
|
|
|
|
Current U.S.
Class: |
1/1 |
Current CPC
Class: |
E04B 1/61 20130101; E04B
1/04 20130101; E04C 5/18 20130101 |
International
Class: |
E04B 1/04 20060101
E04B001/04; E04B 1/61 20060101 E04B001/61; E04C 5/18 20060101
E04C005/18 |
Claims
1. A reinforcing bar joint configured to connect end portions of a
pair of reinforcing bars to each other, the reinforcing bars facing
to each other in a longitudinal direction of the reinforcing bars,
the reinforcing bar joint comprising: cylindrical bodies each
including an inner surface including a female thread part; joint
members each including one end portion including a joint male
thread part; and a connecting member configured to connect a pair
of the joint members which face each other, such that the pair of
the joint members are allowed to move in the longitudinal direction
and in an orthogonal direction to the longitudinal direction,
wherein each of the cylindrical bodies includes one end portion
configured to threadedly engage with a reinforcing bar male thread
part at an end portion of one of the reinforcing bars, and the
other end portion configured to threadedly engage with the joint
male thread part at the one end portion of a corresponding one of
the joint members.
2. The reinforcing bar joint as claimed in claim 1, wherein each of
the joint members includes a body part and the joint male thread
part, and the connecting member and the joint members are removably
coupled to each other by a fastener, with body parts of the pair of
the joint members facing each other in the longitudinal
direction.
3. The reinforcing bar joint as claimed in claim 2, wherein the
body parts of the joint members are interposed between a pair of
connecting members.
4. A reinforcing bar assembly comprising: a plurality of
reinforcing bars arranged parallel to each other; stirrups binding
the plurality of reinforcing bars; and cylindrical bodies each
including an inner surface having a female thread part, wherein the
cylindrical bodies are threadedly engaged with reinforcing bar male
thread parts at end portions of the reinforcing bars, with the
reinforcing bar male thread parts inserted into axially inner
portions of female thread parts of the cylindrical bodies, and
axially outer portions of the female thread parts exposed to
outside of the reinforcing bar assembly.
5. A precast reinforcing bar concrete body comprising the
reinforcing bar joint as claimed in claim 1, wherein the
cylindrical bodies of the reinforcing bar joint and the reinforcing
bars are buried in concrete, and female thread parts at outer end
faces of the cylindrical bodies are exposed at an end face of the
concrete.
Description
CROSS REFERENCE TO THE RELATED APPLICATION
[0001] This application is a continuation application, under 35
U.S.C. .sctn. 111(a) of international patent application No.
PCT/JP2019/029052, filed Jul. 24, 2019.
BACKGROUND OF THE INVENTION
Field of the Invention
[0002] The present invention relates to a reinforcing bar joint and
a reinforcing bar assembly, as well as a precast reinforcing bar
concrete body which are best suited for the precast construction
method for building a reinforcing bar concrete structure such as a
beam and a pillar.
Description of Related Art
[0003] As is well known, reinforcing bar joints for reinforcing bar
concrete structures such as a beam and a pillar are generally
categorized into the following four types namely, lap joints, gas
pressure welding joints, welding joints, and mechanical joints. In
particular, a construction method with mechanical joints is known
to include placing couplers over end portions of reinforcing bars
to join the reinforcing bars by engagement between nodes of the
reinforcing bars and the couplers or by fixing with screws.
Mechanical joints are advantageous in that the reinforcing bars do
not become shorter upon installation, that they allow fully aligned
joint arrangement at ends of bar members, that operators do not
need to have a special license, and that this operation is not
affected by weather or the like.
[0004] Besides the four types of reinforcing bar joints, an
expensive grout material (such as mortar, cement milk, synthetic
resin) may also be used to join reinforcing bars (for example,
Patent Document 1).
RELATED DOCUMENT
Patent Document
[0005] [Patent Document 1] JP Laid-open Patent Publication No.
2008-63730
[0006] In a case of the grout joint, however, it is difficult to
secure positional accuracy of reinforcing bars as a group, and it
takes a considerable time after a grout material is poured until
the grout material is cured to reach a predetermined strength.
Therefore, the process cannot proceed to a next step until the
grout material is cured, which has a substantial influence on the
costs and construction period.
SUMMARY OF THE INVENTION
[0007] An object of the present invention is to provide a
reinforcing bar joint and a reinforcing bar assembly, as well as a
precast reinforcing bar concrete body which can effectively be used
for the precast construction method for building a reinforcing bar
concrete structure such as a beam and a pillar, without increasing
costs or causing delay in a construction period. In order to
achieve the above object, the present invention provides a
reinforcing bar joint configured to connect end portions of a pair
of reinforcing bars to each other, the reinforcing bars facing to
each other in a longitudinal direction of the reinforcing bars, the
reinforcing bar joint including:
[0008] cylindrical bodies each including an inner surface including
a female thread part;
[0009] joint members each including one end portion including a
joint male thread part; and
[0010] a connecting member configured to connect a pair of the
joint members which face each other, such that the pair of the
joint members are allowed to move in the longitudinal direction and
in an orthogonal direction to the longitudinal direction,
[0011] wherein each of the cylindrical bodies includes one end
portion configured to threadedly engage with a reinforcing bar male
thread part at an end portion of one of the reinforcing bars, and
the other end portion configured to threadedly engage with the
joint male thread part at the one end portion of a corresponding
one of the joint members.
[0012] According to this constitution, the pair of reinforcing bar
joints can be joined within the cylindrical bodies only through
thread engagement, without using a grout material such as mortar
which is expensive and takes a few days to cure, so that it is
possible to reduce construction costs and shorten a construction
period. The connecting member which connects the pair of joint
members facing each other can connect the pair of joint members in
a movable manner in the longitudinal direction and the orthogonal
direction to the longitudinal direction. Therefore, even where
there is some misalignment between the pair of joint members, i.e.,
some misalignment or positional shift in the longitudinal direction
between a pair of reinforcing bars, the connecting member can
accommodate the misalignment to connect the pair of joint members
to each other or the pair of reinforcing bars to each other, so
that it is easy to secure the positional accuracy of the
reinforcing bars as a group. Thus, the construction period can also
be shortened thanks to the fact that the pair of reinforcing bars
can be connected within a certain allowable range.
[0013] In the present invention, each of the joint members may
include a body part and the joint male thread part, and the
connecting member and the joint members may be removably coupled to
each other by a fastener, with body parts of the pair of the joint
members facing each other in the longitudinal direction. This
constitution can expedite and facilitate not only assemblage of
reinforcing bars in a plant, but also assemblage of reinforcing
bars at a construction site.
[0014] In the present invention, the body parts of the joint
members may be interposed between a pair of connecting members.
According to this constitution, the pair of connecting members can
rigidly hold the body parts of the joint members with a sandwich
structure, which also improves the reliability of the connection
between the pair of reinforcing bars.
[0015] A reinforcing bar assembly according to the present
invention includes: a plurality of reinforcing bars arranged
parallel to each other; stirrups or stirrup reinforcement binding
the plurality of reinforcing bars; and cylindrical bodies each
including an inner surface having a female thread part, wherein the
cylindrical bodies are threadedly engaged with reinforcing bar male
thread parts on the reinforcing bars, with the reinforcing bar male
thread parts inserted into axially inner portions of female thread
parts of the cylindrical bodies, and axially outer portions of the
female thread parts exposed to outside of the reinforcing bar
assembly. According to this constitution, since the female thread
parts of the cylindrical bodies are exposed at end portions of the
respective reinforcing bars, the joint members can be easily
coupled to the reinforcing bars by bringing the joint members into
thread engagement with the exposed female thread parts. This makes
it more efficient to couple the reinforcing bars with the
reinforcing bar joints.
[0016] A precast reinforcing bar concrete body according to the
present invention includes the reinforcing bar joint, wherein the
cylindrical bodies and the reinforcing bars are buried in concrete,
and the female thread parts of the cylindrical bodies are exposed
at an end face of the concrete. According to this constitution, in
a case where precast reinforcing bar concrete bodies to be used for
e.g. a beam and a pillar in a reinforcing bar concrete structure
are produced in a plant and are joined together at a construction
site, the female thread parts at outer end faces of cylindrical
bodies, which are exposed from the end face of the concrete, can be
used so that the adjacent precast reinforcing bar concrete bodies
can be easily connected to each other by reinforcing bar joints.
This remarkably improves workability at construction sites.
[0017] The present invention encompasses any combination of at
least two features disclosed in the claims and/or the specification
and/or the drawings. In particular, any combination of two or more
of the appended claims should be equally construed as included
within the scope of the present invention.
BRIEF DESCRIPTION OF THE DRAWINGS
[0018] The present invention will be more clearly understood from
the following description of preferred embodiments thereof, when
taken in conjunction with the accompanying drawings. However, the
embodiments and the drawings are given only for the purpose of
illustration and explanation, and are not to be taken as limiting
the scope of the present invention in any way whatsoever, which
scope is to be determined by the appended claims. In the
accompanying drawings, like reference numerals are used to denote
like or corresponding parts throughout the several views:
[0019] FIG. 1 is a front view showing reinforcing bar joints and
reinforcing bar assemblies according to a first embodiment of the
present invention;
[0020] FIG. 2 is an exploded perspective view of a reinforcing bar
joint according to the same embodiment to be threadedly engaged
with reinforcing bar male thread parts at end portions of
reinforcing bars;
[0021] FIG. 3 is an enlarged perspective view of a joint member of
the reinforcing bar joint;
[0022] FIG. 4 is an enlarged cross-sectional view illustrating a
different attachment structure between a formwork and an end face
of a male thread part of a reinforcing bar;
[0023] FIG. 5 is a side view of the reinforcing bar joint;
[0024] FIG. 6 is a front view of the reinforcing bar joint;
[0025] FIG. 7 is a front view illustrating a case of connecting
misaligned reinforcing bars with the reinforcing bar joint, with a
connecting member not illustrated in the figure; and
[0026] FIG. 8 is a side view of a reinforcing bar joint according
to a second embodiment.
DESCRIPTION OF THE EMBODIMENTS
[0027] Hereinafter, a preferable embodiment of the present
invention will be described with reference to the drawings. FIG. 1
is a front view showing reinforcing bar assemblies according to a
first embodiment of the present invention which are attached to
formworks.
[0028] Structure of Reinforcing Bar Assembly
[0029] FIG. 1 shows one reinforcing bar assembly A located on the
right side and another reinforcing bar assembly A located on the
left side. These reinforcing bar assemblies may be constructed into
a beam or a pillar. This example is described for a case where the
reinforcing bar assemblies A are constructed into a beam. The left
and right reinforcing bar assemblies A, A are identical, each of
which includes a same number of main bars (reinforcing bars) or
main reinforcement 1 and a same or different number of stirrups or
stirrup reinforcement 2.
[0030] In FIG. 1, each reinforcing bar assembly A includes a
plurality of reinforcing bars 1 that serve as the main bars and are
arranged with spacing therebetween in a vertical direction and in a
depth direction of a plane of FIG. 1 to extend parallel to each
other in a left-to-right direction (in this example, a horizontal
direction). A plurality of stirrups 2 that serve as shear
enforcement bars are wound around these reinforcing bars 1. Each of
the reinforcing bars 1 is a deformed bar which includes, on an
outer periphery thereof, projections including a rib extending in a
longitudinal direction and node portions extending in a
circumferential direction at certain intervals. Alternatively, each
of the reinforcing bars may be a general round bar.
[0031] Each reinforcing bar 1 has end portions each including a
male thread part 15 formed by e.g. rolling. The male thread part 15
may be formed as a separate member from the reinforcing bar 1 and
be welded to an end face of the reinforcing bar 1. A cylindrical
body 10 including an inner surface including a female thread part
is screwed onto the male thread part 15. Attachment thread bodies 6
as described later are inserted from outside the formwork 7 and are
screwed into the cylindrical bodies 10 to attach the reinforcing
bar assembly A to the formwork 7. The reinforcing bar assembly A on
the left side has the same structure.
[0032] Each reinforcing bar assembly A is attached with the
formwork 7 in a plant, and fresh concrete is poured into the
formwork 7 to produce a precast reinforcing bar concrete body P
(hereinafter, simply referred to as "PC concrete body P") for e.g.
a beam and a pillar. Alternatively, each reinforcing bar assembly A
attached with the formwork 7 may be transferred to a construction
site, and fresh concrete may then be poured into the formwork 7 at
the site. Alternatively, the reinforcing bars 1, the stirrups 2,
the cylindrical bodies 10, and the formworks 7 may be separately
transferred to a construction site to obtain the reinforcing bar
assemblies A attached with the formworks 7 at the site, and fresh
concrete may then be poured into the formworks 7.
[0033] The thread bodies 6 are removed to detach the formwork 7,
and the reinforcing bars 1, 1 of the left and right PC concrete
bodies P are connected by the reinforcing bar joint B. This example
is described for a case where the PC concrete body P is used for a
beam. In a case where the PC concrete body P is used for a pillar,
the reinforcing bar joint connects reinforcing bars 1, 1 of a pair
of upper and lower PC concrete bodies P.
[0034] Structure of Reinforcing Bar Joint
[0035] The reinforcing bar joint B will be described with reference
to FIG. 2.
[0036] As illustrated in the exploded perspective view in FIG. 2,
the reinforcing bar joint B includes: the above-described
cylindrical bodies 10 or couplers each including an inner surface
including a female thread part 14; joint members 11 each including
one end portion including a joint male thread part 13; and a
connecting member 19 connecting a pair of the joint members 11, 11
which face each other.
[0037] The connecting member 19 holds the pair of upper and lower
joint members 11 with a sandwich structure such that the joint
members 11 are movable in a longitudinal direction (axial
direction) X and in an orthogonal direction Y to the longitudinal
direction. The longitudinal direction X is common to the joint
members 11 and the reinforcing bars 1. The direction Y extends
perpendicular to the longitudinal direction X and parallel to a
main face of a body part 12 of each joint member 11, i.e.,
perpendicular to a through hole 17. A direction Z extends
perpendicular to both the directions X, Y. The cylindrical bodies
10 are buried into the concrete body P as described above.
[0038] Each cylindrical body 10 has an outer shape having a
hexagonal cross-section and includes, on the inner surface thereof,
the female thread part 14 configured to be threadedly engaged with
a reinforcing bar male thread part 15 which is exposed at an end
portion of a reinforcing bar 1. Each cylindrical body 10 may have
an outer shape having a round or polygonal cross-section. The
reinforcing bar male thread part 15 only comes into thread
engagement with an axially inner portion which is a portion of the
female thread part 14 of the cylindrical body 10. Each joint member
11 includes, as shown in FIG. 3, a body part 12 having a flat shape
and a joint male thread part 13 at a tip of the body part, the
joint male thread part being configured to be threadedly engaged
with a female thread part 14 of a cylindrical body 10.
[0039] The body part 12 includes three through holes 17 at
predetermined intervals (for example, 60 mm) This example includes
three through holes 17. Alternatively, there may be two through
holes, or four or more through holes. Each of the through holes 17
is a loosely fitting hole (oversized hole) having an inner diameter
larger by a few millimeters than an outer diameter of a
high-strength bolt or an ultrahigh-strength bolt (hereinafter,
sometimes simply referred to as "bolt") 25 which will be described
later. Each through hole 17 is provided with friction adjusting
parts 17a which are circular projections or chamfers at edge
portions on opposite ends of the through hole 17. Thus, when the
bolt 25 is fastened with a large force, the projections are crushed
or a part of the connecting member 19 enters recesses of the
chamfers to provide a greater friction force, so that force
transmission action is enhanced.
[0040] As shown in FIG. 2, the identical cylindrical bodies 10 and
the identical joint members 11 are arranged in an opposite manner
in the longitudinal direction (here, in the horizontal direction
because this example is described for a case of beam reinforcing
bars), and the joint male thread parts 13 of the respective joint
members 11 are threadedly engaged with the corresponding female
thread parts 14 of the cylindrical bodies 10. In a case where the
engagement may interfere with coupling between the PC concrete
bodies P, P, the joint members 11 may be attached to the
cylindrical bodies 10 of the PC concrete bodies P at a later point.
There is a small gap S (of approximately 70 mm) between the joint
members 11, 11. The joint member(s) 11 may be turned to increase or
decrease an engaging amount with the cylindrical body (or bodies)
10 and change the size of the gap S, so that a difference in
separation distance between the reinforcing bars 1, 1 can be
accommodated.
[0041] FIG. 4 illustrates a structure for attaching a reinforcing
bar 1 to a formwork 7 of FIG. 1 in an enlarged manner. As shown in
FIG. 4, a formwork male thread body 16 includes a predefined
threaded hole 20 in an outer end face thereof. The formwork male
thread body 16 is attached to the formwork 7 by an attachment
thread body 6. The formwork male thread body 16 is brought into
thread engagement with a cylindrical body 10, and the female thread
part 14 on the inner surface of that cylindrical body 10 is brought
into thread engagement with a reinforcing bar male thread part 15
of a reinforcing bar 1. As needed, a lock nut 30 may be fastened
thereto.
[0042] In this state, as described above, fresh concrete is poured
into the formwork 7 to a filling surface 35, and then the formwork
7 is removed to obtain a PC concrete body P. When connecting the
reinforcing bars 1, 1, the formwork male thread body 16 is removed
using a tool, so that the female thread part 14 on the inner
surface of the cylindrical body 10 is exposed to outside from an
end face of the PC concrete body P. The exposed female thread part
14 is brought into thread engagement with a joint male thread part
13 of a joint member 11 as shown in FIG. 2. On an outer side of the
formwork 7, an iron frame 9 for positioning the reinforcing bar(s)
is removably attached by the attachment thread body 6.
[0043] As a variant of attachment of the reinforcing bar 1 to the
formwork 7, it is possible to omit the formwork thread body 16 and
provide a longer attachment thread body 6 as illustrated with a
two-dot chain line to be threadedly engaged with a threaded hole
20A at the end face of the reinforcing bar 1, so that the
reinforcing bar 1 engaged with the cylindrical body 10 can be
attached to the formwork 7. In this variant, it is only necessary
to remove the formwork 7 to expose the female thread part 14 of the
cylindrical body 10 to the outside from the end face of the PC
concrete body P.
[0044] The body parts 12, 12 of these joint members 11, 11 are
abutted with a pair of connecting members 19, 19 on front and rear
sides of the body parts 12 so as to be held with the sandwich
structure, as shown in FIG. 5. Each connecting member 19 has a form
of a flat plate and includes six coupling holes 27 at positions
corresponding to those of the through holes 17 of the joint members
11. Bolts 25, which are an example of fasteners, are inserted from
the coupling holes 27 of one of the connecting members 19. The
bolts 25 pass through the through holes 17 of the joint member 11,
and tip end portions of the bolts 25 project from corresponding
coupling holes 27 of the connecting member 19 on the opposite side.
Nuts 30 are fastened to the tip end portions of the fasteners
(bolts) 25. Accordingly, in this example, the fasteners include the
bolts 25 and the nuts 30.
[0045] Each coupling hole 27 is also an oversized hole having an
inner diameter larger by a few millimeters than an outer diameter
of the fastener 25. According to the Guidebook on Design and
Fabrication of Bolted Connections, as for a bolt having a diameter
of 24 mm, an oversized hole may have a larger inner diameter by up
to +6 mm, and as for a bolt having a diameter of 27 mm, an
oversized hole may have a larger inner diameter by up to +8 mm
Thus, there are larger gaps between the oversized holes 17, 27 and
the bolts 25 than that in case of typical thread engagement, so
that these gaps allow the joint members 11, 11 connected by the
connecting members 19 to move in the longitudinal direction X and
in the orthogonal direction Y to the longitudinal direction. In
this way, as shown in FIG. 6, the adjacent PC concrete bodies P, P
are coupled to each other by the reinforcing bar joint B.
[0046] Coupling Operation with Reinforcing Bar Joint
[0047] When two reinforcing bars 1, 1 which serve for reinforcement
in e.g. a beam or a pillar are coupled to each other by the
reinforcing bar joint B, first of all, the joint male thread parts
13 of the joint members 11 are brought into thread engagement with
the female thread parts 14 of the cylindrical bodies 10 of FIG. 2.
If necessary, lock nuts 31 and washers 32 as shown in FIG. 5 may be
attached to the axial outer ends of the cylindrical bodies 10.
Thus, with the reinforcing bar male thread parts 15 inserted into
the axially inner portions of the female thread parts 14 of the
cylindrical bodies 10, the joint male thread parts 13 are
threadedly engaged with the axially outer portions which are
different parts of the female thread parts.
[0048] In this state, as described above, the joint members 11, 11
are held in a sandwiched manner by the plate-like connecting
members 19, 19 on opposite sides. Further, six bolts 25 are
inserted through the coupling holes 27 of the connecting members 19
and the coupling holes 17 of the joint members 11, and nuts 30 are
threadedly engaged with and fastened to tip end portions of the
bolts, if necessary, with washers 32 interposed therebetween. The
gap between the PC concrete bodies P, P which are thus coupled to
each other is filled by pouring concrete at a site. Therefore, the
reinforcing bar joint B is buried in concrete, so that the joint is
not exposed to the outside.
[0049] Effects and Advantages
[0050] The reinforcing bar joint B according to the present
invention which has the above configuration only involves thread
engagement, without using a grout material such as mortar which is
expensive and takes a few days to cure, so that it is possible to
reduce construction costs and shorten a construction period. Each
of the pair of joint members 11 facing each other as shown in FIG.
2 includes the body part 12 and the joint male thread part 13, and
the connecting members 19 and the joint members 11 are removably
coupled to one another by the fasteners 25, 30 with the body parts
12, 12 of the pair of joint members 11 facing each other in the
longitudinal direction. Thus, the coupling structure is simplified.
This can expedite and facilitate not only assemblage of reinforcing
bars in a plant, but also assemblage of reinforcing bars at a
construction site.
[0051] In FIG. 6, the joint members 11, 11 are concentric. As shown
in FIG. 7, there may be a misalignment C1 between a longitudinal
axis X1 of one of the joint members 11 and a longitudinal axis X2
of the other of the joint members 11, or there may be a positional
shift in the axial direction, i.e., a variation in the size of the
gap S. Even in such cases, since the through holes 17 of the joint
members 11 and the coupling holes 27 of the connecting members 19
are oversized holes, the excess in size can accommodate the
misalignment or shift of the reinforcing bars 1, 1, so that the
reinforcing bars can be smoothly connected.
[0052] To smoothly fasten the bolts 25, the body parts 12 of the
joint members 11 may be turned to an orientation in which the bolts
can be easily fastened. In such a case, a misalignment may occur in
the Z direction as shown in FIG. 5 to generate a gap between a body
part 12 and a connecting member 19. A filler plate may be inserted
into this gap. Alternatively, without using a filler plate, since
there is the gap S between the joint members 11, 11 in the
longitudinal direction X, the bolts 25 may be fastened tightly such
that the joint member 11 and the connecting member 19 are deformed
to incline so as to eliminate the gap between them in the Z
direction.
[0053] Thanks to the structure in which the body parts 12 of the
joint members 11 are interposed between the pair of connecting
members 19, 19 as shown in FIG. 5, the body parts 12 of the joint
members 11 are rigidly held with the sandwich structure by the pair
of connecting members 19, 19, so that the reliability of the
connection between the pair of reinforcing bars 1, 1 is also
improved.
[0054] Further, a reinforcing bar assembly A according to the
present embodiment includes a plurality of reinforcing bars 1
arranged parallel to each other and stirrups 2 binding the
reinforcing bars. In such a reinforcing bar assembly A, the
cylindrical bodies 10 each including the inner surface including
the female thread part 14 are threadedly engaged with the
reinforcing bar male thread parts 15 on the reinforcing bars 1,
with the reinforcing bar male thread parts 15 inserted into the
axially inner portions of the female thread parts 14, and the
axially outer portions of the female thread parts 14 exposed to the
outside of the reinforcing bar assembly A. Therefore, the joint
members 11 can be easily coupled to the reinforcing bars 1 by
bringing the joint male thread parts 13 of the joint members 11
into thread engagement with the exposed female thread parts 14. As
a result, this makes it more efficient to couple the reinforcing
bars 1, 1 with the reinforcing bar joint B. Thus, the operation
efficiency is improved for both cases where the reinforcing bar
concrete structures such as beams and pillars are mass-produced in
a plant as well as where concrete is cast at a construction
site.
[0055] A reinforcing bar joint according to a second embodiment
will be described with reference to FIG. 8. The second embodiment
has a same basic configuration as that of the first embodiment as
shown in FIG. 5 and only differs from the first embodiment in that
the cylindrical bodies 10 of the reinforcing bar joint B are not
buried into the PC concrete body P. The male thread parts 15 at the
end portions of the reinforcing bars 1 protrude from the PC
concrete body P, and the cylindrical bodies 10 are brought into
thread engagement with the protruding male thread parts 15 at a
construction site. The connection structure of the joint members 11
to the cylindrical bodies 10 and the coupling structure between the
joint members 11 and the connecting members 19 are the same as
those of the first embodiment.
[0056] Although the present invention has been described in terms
of the preferred embodiments thereof with reference to the
drawings, various additions, modifications, or deletions may be
made without departing from the scope of the invention.
Accordingly, such variants are included within the scope of the
present invention.
REFERENCE NUMERALS
[0057] A . . . reinforcing bar assembly
[0058] B . . . reinforcing bar joint
[0059] P . . . PC concrete body for e.g. a beam and a pillar
[0060] 1 . . . reinforcing bar
[0061] 2 . . . stirrup
[0062] 6 . . . bolt (fastener)
[0063] 7 . . . formwork
[0064] 10 . . . cylindrical body
[0065] 11 . . . joint member
[0066] 12 . . . body part
[0067] 13 . . . joint male thread part
[0068] 14 . . . female thread part
[0069] 15 . . . reinforcing bar male thread part
[0070] 17 . . . through hole
[0071] 17a . . . friction adjusting part
[0072] 19 . . . connecting member
[0073] 20 . . . threaded hole
[0074] 27 . . . coupling hole
[0075] 30 . . . nut (fastener)
* * * * *