U.S. patent application number 17/296259 was filed with the patent office on 2022-04-28 for multiphase ceramic material with giant dielectric constant, and preparation method thereof.
The applicant listed for this patent is GUANGDONG FENGHUA ADVANCED TECHNOLOGY HOLDING CO., LTD.. Invention is credited to Xiuhua Cao, Dehong Chen, Terry James Frankcombe, Zhenxiao Fu, Jianmei Liu, Yun Liu, Haidong Ren, Shiwo Ta.
Application Number | 20220127197 17/296259 |
Document ID | / |
Family ID | 1000006107645 |
Filed Date | 2022-04-28 |



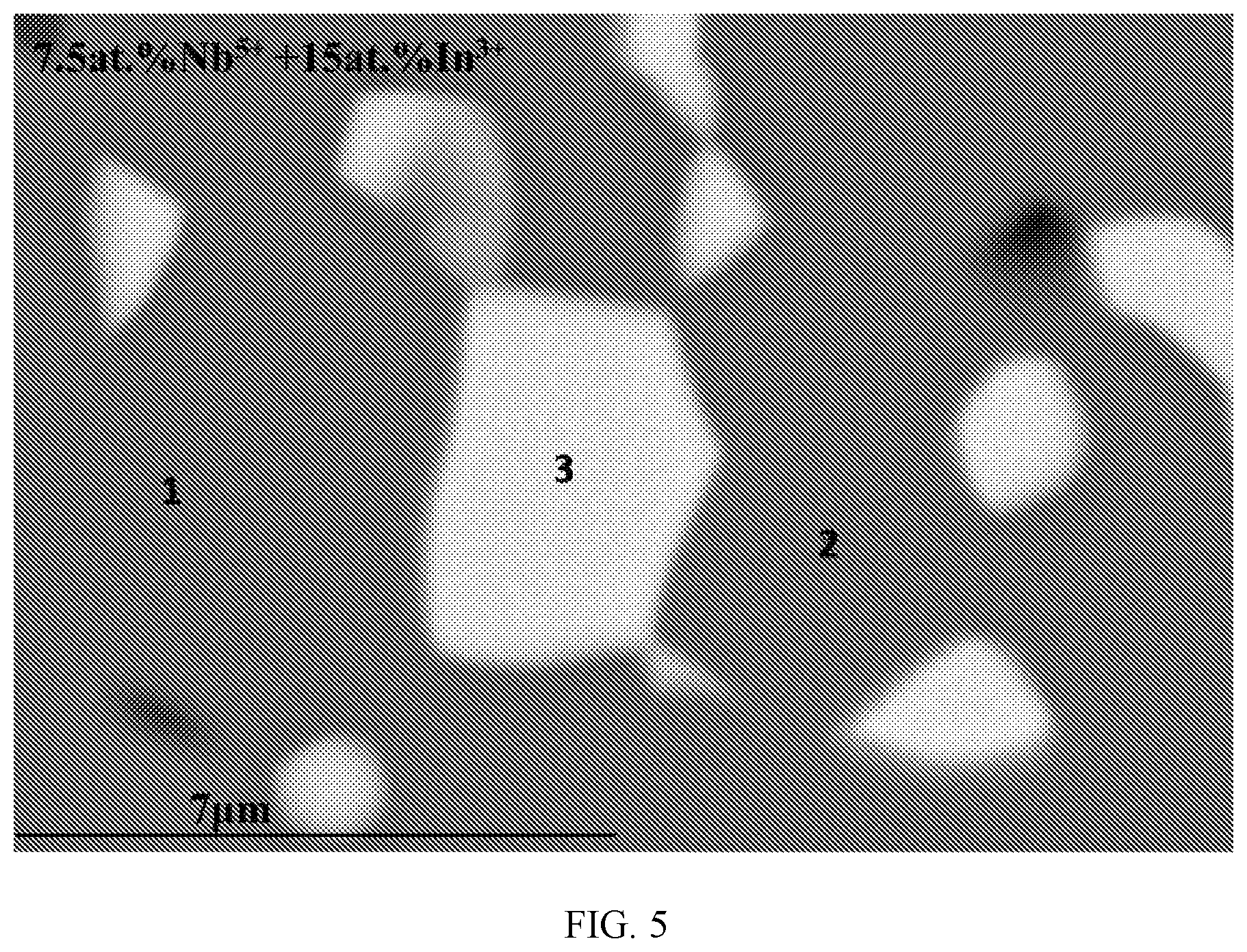
United States Patent
Application |
20220127197 |
Kind Code |
A1 |
Cao; Xiuhua ; et
al. |
April 28, 2022 |
MULTIPHASE CERAMIC MATERIAL WITH GIANT DIELECTRIC CONSTANT, AND
PREPARATION METHOD THEREOF
Abstract
The present invention discloses a multiphase ceramic material
with a giant dielectric constant, wherein the multiphase ceramic
material has a general formula of
A.sub.xB.sub.nxTi.sub.1-(n+1)xO.sub.2; wherein A is at least one
selected from the group consisting of Nb, Ta, V, Mo, and Sb, B is
at least one selected from the group consisting of In, Ga, Al, Co,
Cr, Sc, Fe (III), and a trivalent rare-earth cation; n is a molar
ratio of B to A, 1<n.ltoreq.5 , 0<x.ltoreq.0.1. The
multiphase ceramic material possesses outstanding properties
including a giant dielectric constant, a low dielectric loss, and
excellent frequency- and temperature-stability. In particular, it
exhibits a high insulation resistivity of higher than 10.sup.11
.OMEGA.cm and a high breakdown voltage, which implies it can be
applied in high-energy storage devices and supercapacitors. This
invention also provides a method to synthesize the multiphase
ceramic material.
Inventors: |
Cao; Xiuhua; (Zhaoqing,
Guangdong, CN) ; Liu; Jianmei; (Canberra, Australian
Capital Territory, AU) ; Chen; Dehong; (Canberra,
Australian Capital Territory, AU) ; Ren; Haidong;
(Zhaoqing, Guangdong, CN) ; Liu; Yun; (Canberra,
Australian Capital Territory, AU) ; Frankcombe; Terry
James; (Canberra, Australian Capital Territory, AU) ;
Fu; Zhenxiao; (Zhaoqing, Guangdong, CN) ; Ta;
Shiwo; (Zhaoqing, Guangdong, CN) |
|
Applicant: |
Name |
City |
State |
Country |
Type |
GUANGDONG FENGHUA ADVANCED TECHNOLOGY HOLDING CO., LTD. |
Zhaoqing, Guangdong |
|
CN |
|
|
Family ID: |
1000006107645 |
Appl. No.: |
17/296259 |
Filed: |
March 29, 2020 |
PCT Filed: |
March 29, 2020 |
PCT NO: |
PCT/CN2020/081953 |
371 Date: |
May 24, 2021 |
Current U.S.
Class: |
1/1 |
Current CPC
Class: |
C04B 35/6261 20130101;
C04B 35/64 20130101; C04B 2235/3234 20130101; C04B 2235/612
20130101; C04B 2235/606 20130101; C04B 2235/662 20130101; C04B
2235/762 20130101; C04B 35/62695 20130101; C04B 2235/6562 20130101;
H01B 3/12 20130101; C04B 35/62655 20130101; C04B 2235/6021
20130101; C04B 35/462 20130101; C04B 2235/6567 20130101; C04B
2235/604 20130101; C04B 35/6264 20130101 |
International
Class: |
C04B 35/462 20060101
C04B035/462; C04B 35/626 20060101 C04B035/626; C04B 35/64 20060101
C04B035/64; H01B 3/12 20060101 H01B003/12 |
Foreign Application Data
Date |
Code |
Application Number |
Mar 20, 2020 |
CN |
202010205096.0 |
Claims
1. A multiphase ceramic material with a giant dielectric constant,
wherein the multiphase ceramic material has a general formula of
A.sub.xB.sub.nxTi.sub.1-(n+1)xO.sub.2; wherein A is at least one
selected from the group consisting of Nb, Ta, V, Mo, and Sb, B is
at least one selected from the group consisting of In, Ga, Al, Co,
Cr, Sc, Fe (III), and a trivalent rare-earth cation; n is a molar
ratio of B to A, 1<n.ltoreq.5, 0<x.ltoreq.0.1.
2. The multiphase ceramic material of claim 1, wherein a primary
phase of the ceramic material is A5+ and B3+ co-doped rutile TiO2,
a secondary phase of the ceramic material is B2TiO5; the secondary
phase is evenly dispersed in the primary phase.
3. The multiphase ceramic material of claim 2, wherein the
secondary phase is B.sub.2TiOs with an orthogonal structure.
4. The multiphase ceramic material of claim 1, wherein the
multiphase ceramic material has a resistivity of higher than
10.sup.11 .OMEGA.cm.
5. The multiphase ceramic material of claim 1, wherein the
multiphase ceramic material has a dielectric constant of higher
than 10,000 at a frequency of 20 Hz to 2.times.10.sup.6 Hz; the
multiphase ceramic material has a dielectric loss of less than 0.05
before 2.times.10.sup.5 Hz.
6. The multiphase ceramic material of claim 1, wherein the
multiphase ceramic material has a dielectric constant of higher
than 10,000 from -160.degree. C. to 170.degree. C.; the multiphase
ceramic material has a dielectric loss of less than 0.05 from
-50.degree. C. to 150.degree. C.
7. A method of preparing the multiphase ceramic material with a
giant dielectric constant of claim 1, wherein the method comprises
steps of: (1) weighing reactants, which comprise a titanium source,
an A source, and a B source, according to a general formula of the
multiphase ceramic material, A.sub.xB.sub.nxTi.sub.1-(n+1)xO.sub.2;
(2) ball-milling in a ball-milling tank and drying to obtain a
homogeneous mixture powder; (3) transferring the mixture powder
into a mortar; pure water is added, and the weight of the pure
water is 5%-10% of the weight of the mixture powder; mixing
thoroughly; transferring the mixture powder into a die, pressing at
a pressure of at least 400 MPa to obtain a green pellet; placing
the green pellet in a mortar; pulverizing and grinding the green
pellet to obtain a preliminary powder; (4) transferring the
preliminary powder into a die; pressing at a pressure of at least 2
MPa, followed by sintering; sintering parameters comprise heating
rate: 1.5.degree. C./min-15.degree. C./min, temperature:
1200.degree. C.-1500.degree. C., holding time: 1 h-24 h; after
sintering, the product obtained is naturally cooled down to room
temperature to obtain a dense ceramic pellet; (5) polishing a
surface of the dense ceramic sheet, followed by annealing;
annealing parameters comprise heating rate: 1.5.degree.
C./min-15.degree. C./min, temperature: 1000.degree. C.-1200.degree.
C., holding time: 1 h-24 h; after annealing, the product obtained
is naturally cooled down to room temperature to obtain the
multiphase ceramic material with a giant dielectric constant.
8. The method of claim 7, wherein in step 1, the titanium source is
TiO.sub.2, the A source is A.sub.2O.sub.5, the B source is at least
one selected from the group consisting of B.sub.2O.sub.3,
B.sub.2(C.sub.2O.sub.4).sub.3, B.sub.2(C.sub.2O.sub.4).sub.3
hydrate, B(NO.sub.3).sub.3, B(NO.sub.3).sub.3 hydrate,
B.sub.2(SO.sub.4).sub.3, B.sub.2(SO.sub.4).sub.3 hydrate,
B.sub.2(CO.sub.3).sub.3, B.sub.2(CO.sub.3).sub.3 hydrate,
B(C.sub.2H.sub.3O.sub.2).sub.3, B(C.sub.2H.sub.3O.sub.2).sub.3
hydrate.
9. The method of claim 7, wherein the ball-milling in step (2)
comprises using ethanol or acetone as a dispersant, and using
yttrium-stabilized zirconia balls as a ball-milling medium;
ball-milling is performed for more than 12 hours; in steps (4) and
(5), an atmosphere for the sintering and the annealing is air.
10. The method of claim 7, wherein the polishing of the surface in
step (5) comprises rough polishing the surface by a 240-grit
sandpaper, followed by finely polishing the surface by a 1200-grit
sandpaper.
11. The multiphase ceramic material of claim 2, wherein the
multiphase ceramic material has a dielectric constant of higher
than 10,000 at a frequency of 20 Hz to 2.times.10.sup.6 Hz; the
multiphase ceramic material has a dielectric loss of less than 0.05
before 2.times.10.sup.5 Hz.
12. The multiphase ceramic material of claim 3, wherein the
multiphase ceramic material has a dielectric constant of higher
than 10,000 at a frequency of 20 Hz to 2.times.10.sup.6 Hz; the
multiphase ceramic material has a dielectric loss of less than 0.05
before 2.times.10.sup.5 Hz.
13. The multiphase ceramic material of claim 2, wherein the
multiphase ceramic material has a dielectric constant of higher
than 10,000 from -160.degree. C. to 170.degree. C.; the multiphase
ceramic material has a dielectric loss of less than 0.05 from
-50.degree. C. to 150.degree. C.
14. The multiphase ceramic material of claim 3, wherein the
multiphase ceramic material has a dielectric constant of higher
than 10,000 from -160.degree. C. to 170.degree. C.; the multiphase
ceramic material has a dielectric loss of less than 0.05 from
-50.degree. C. to 150.degree. C.
15. A method of preparing the multiphase ceramic material with a
giant dielectric constant of claim 2, wherein the method comprises
steps of: (1) weighing reactants, which comprise a titanium source,
an A source, and a B source, according to a general formula of the
multiphase ceramic material, A.sub.xB.sub.nxTi.sub.1-(n+1)xO.sub.2;
(2) ball-milling in a ball-milling tank and drying to obtain a
homogeneous mixture powder; (3) transferring the mixture powder
into a mortar; pure water is added, and the weight of the pure
water is 5%-10% of the weight of the mixture powder; mixing
thoroughly; transferring the mixture powder into a die, pressing at
a pressure of at least 400 MPa to obtain a green pellet; placing
the green pellet in a mortar; pulverizing and grinding the green
pellet to obtain a preliminary powder; (4) transferring the
preliminary powder into a die; pressing at a pressure of at least 2
MPa, followed by sintering; sintering parameters comprise heating
rate: 1.5.degree. C./min-15.degree. C./min, temperature:
1200.degree. C.-1500.degree. C., holding time: 1 h-24 h; after
sintering, the product obtained is naturally cooled down to room
temperature to obtain a dense ceramic pellet; (5) polishing a
surface of the dense ceramic sheet, followed by annealing;
annealing parameters comprise heating rate: 1.5.degree.
C./min-15.degree. C./min, temperature: 1000.degree. C.-1200.degree.
C., holding time: 1 h-24 h; after annealing, the product obtained
is naturally cooled down to room temperature to obtain the
multiphase ceramic material with a giant dielectric constant.
Description
FIELD OF THE INVENTION
[0001] This invention relates to a multiphase ceramic material with
a giant dielectric constant and its preparation method.
BACKGROUND OF THE INVENTION
[0002] Researches on the miniaturization of high-energy storage
devices, supercapacitors and other equipment have shown that as an
indispensable part of these devices and equipment, the dielectric
material needs to simultaneously possess a giant dielectric
constant, a low dielectric loss, and good frequency- and
temperature-stability, and the high breakdown strength. The
capacity of the energy storage device/equipment is proportional to
the square of the working voltage of the dielectric material,
suggesting that it is necessary to study the breakdown strength of
dielectric ceramic materials.
[0003] Numerous studies have shown that ferroelectric materials,
such as BaTiO.sub.3, have a high dielectric constant. However,
their dielectric constant is highly dependent on temperature. For
other non-ferroelectric materials, such as CaCuTi.sub.3O.sub.12
(CCTO), doped NiO and La.sub.2xSr.sub.xNiO.sub.4 (x=1/3, 1/8),
etc., although their dielectric constant can reach 10.sup.5 or more
within a wide temperature range, their dielectric loss is very high
(>0.1).
[0004] Therefore, there is a need to prepare a dielectric ceramic
material with a high dielectric constant, a low dielectric loss,
good temperature- and frequency-stability, and high breakdown
strength.
SUMMARY OF THE INVENTION
[0005] The objective of the present invention is to provide a
multiphase ceramic material with a giant dielectric constant to
overcome the deficiencies of the prior art.
[0006] The technical solution of the present invention is a
multiphase ceramic material with a giant dielectric constant,
wherein the multiphase ceramic material has a general formula of
A.sub.xB.sub.nxTi.sub.1-(n+1)xO.sub.2, wherein A is at least one
selected from the group consisting of Nb, Ta, V, Mo, and Sb, B is
at least one selected from the group consisting of In, Ga, Al, Co,
Cr, Sc, Fe (III), and a trivalent rare-earth cation; n is a molar
ratio of B to A, 1<n.ltoreq.5, 0<x.ltoreq.0.1.
[0007] The multiphase ceramic material of the present application
possesses outstanding dielectric properties including a giant
dielectric constant, a low dielectric loss, and good frequency- and
temperature-stability. In particular, it exhibits a high insulation
resistivity and a high breakdown voltage. The ceramic material has
an insulation resistivity of higher than 10.sup.11 .PSI.cm; it can
be applied in high-energy storage devices and supercapacitors.
[0008] Preferably, a primary phase of the ceramic material is
A.sup.5+ and B.sup.3+ co-doped rutile TiO.sub.2, a secondary phase
of the ceramic material is B.sub.2TiO.sub.5; the secondary phase is
evenly dispersed in the primary phase. The primary phase provides
the multiphase ceramic material with the giant dielectric property,
while the secondary phase exhibits excellent electrical insulation
properties. The secondary phase is discontinuously and uniformly
distributed around the grain boundary of the primary phase.
Therefore, it can effectively block the transfer of weakly bounded
charges, which contributes to increasing the working voltage and
breakdown voltage of the material. Meanwhile, the existence of the
secondary phase does not cause the deterioration of the giant
dielectric property of the material.
[0009] More preferably, the secondary phase is B.sub.2TiO.sub.5
with an orthogonal structure. During a one-step synthesis process,
the secondary phase has a lower synthesis temperature comparing to
that of the primary phase, helping to separate two phases.
[0010] Preferably, the multiphase ceramic material has a
resistivity of higher than 10.sup.11 .OMEGA.cm.
[0011] Preferably, the multiphase ceramic material has a dielectric
constant of higher than 10,000 at a frequency of 20 Hz to
2.times.10.sup.6 Hz; the multiphase ceramic material has a
dielectric loss of less than 0.05 before 2.times.10.sup.5 Hz.
[0012] Preferably, the multiphase ceramic material has a dielectric
constant of higher than 10,000 from -160.degree. C. to 170.degree.
C.; the multiphase ceramic material has a dielectric loss of less
than 0.05 from -50.degree. C. to 150.degree. C.
[0013] The present invention also provides a method of preparing
the multiphase ceramic material with a giant dielectric constant,
the method comprises steps of:
[0014] (1) weighing reactants, which comprise a titanium source, an
A source, and a B source, according to a general formula of the
multiphase ceramic material,
A.sub.xB.sub.nxTi.sub.1-(n+1)xO.sub.2;
[0015] (2) ball-milling in a ball-milling tank and drying to obtain
a homogeneous mixture powder;
[0016] (3) transferring the mixture powder into a mortar; pure
water is added, and the weight of the pure water is 5%-10% of the
weight of the mixture powder; mixing thoroughly; transferring the
mixture powder into a die, pressing at a pressure of at least 400
MPa to obtain a green pellet; placing the green pellet in a mortar;
pulverizing and grinding the green pellet to obtain a preliminary
powder;
[0017] (4) transferring the preliminary powder into a die; pressing
at a pressure of at least 2 MPa, followed by sintering; sintering
parameters comprise heating rate: 1.5.degree. C./min-15.degree.
C./min, temperature: 1200.degree. C.-1500.degree. C., holding time:
1 h -24 h; after sintering, the product obtained is naturally
cooled down to room temperature to obtain a dense ceramic
pellet;
[0018] (5) polishing a surface of the dense ceramic sheet, followed
by annealing; annealing parameters comprise heating rate:
1.5.degree. C./min-15.degree. C./min, temperature: 1000.degree.
C.-1200.degree. C., holding time: 1 h-24 h; after annealing, the
product obtained is naturally cooled down to room temperature to
obtain the multiphase ceramic material with a giant dielectric
constant.
[0019] Preferably, in step 1, the titanium source is TiO.sub.2, the
A source is A.sub.2O.sub.5, the B source is at least one selected
from the group consisting of B.sub.2O.sub.3,
B.sub.2(C.sub.2O.sub.4).sub.3, B.sub.2(C.sub.2O.sub.4).sub.3
hydrate, B(NO.sub.3).sub.3, B(NO.sub.3).sub.3 hydrate,
B.sub.2(SO.sub.4).sub.3, B.sub.2(SO.sub.4).sub.3 hydrate,
B.sub.2(CO.sub.3).sub.3, B.sub.2(CO.sub.3).sub.3 hydrate,
B(C.sub.2H.sub.3O.sub.2).sub.3, B(C.sub.2H.sub.3O.sub.2).sub.3
hydrate.
[0020] The non-oxide B source can reduce the synthesis temperature
of the secondary phase and reduce its mobility around the grain
boundary, helping to form a discontinuously and uniformly
distributed B phase.
[0021] Preferably, the ball-milling in step (2) comprises using
ethanol or acetone as a dispersant, and using yttrium-stabilized
zirconia balls as a ball-milling medium; ball-milling is performed
for more than 12 hours; in steps (4) and (5), an atmosphere for the
sintering and the annealing is air.
[0022] Preferably, the polishing of the surface in step (5)
comprises rough polishing the surface by a 240-grit sandpaper,
followed by finely polishing the surface by a 1200-grit
sandpaper
[0023] Compared with the prior art, the advantages of the present
invention are discussed below.
[0024] In the present invention, rutile titanium dioxide is
chemically modified by co-doping A.sup.5+ and B.sup.3+ metal ions
to obtain a multiphase material, in which the primary phase is
A.sup.5+ and B.sup.3+ co-doped rutile TiO.sub.2 and the secondary
phase (B.sub.2TiO.sub.5) is evenly dispersed in the primary phase.
The multiphase ceramic material of the present application has
outstanding properties including a giant dielectric constant, a low
dielectric loss, and good frequency- and temperature-stability. In
particular, it has a high insulation resistivity and a high
breakdown voltage. The ceramic material can be used in high-energy
storage devices and supercapacitors. Its detailed advantages
are:
[0025] (1) The primary phase of the multiphase ceramic material
with a giant dielectric constant is A.sup.5+and B.sup.3+co-doped
rutile TiO.sub.2, and the secondary phase of the ceramic material
is B.sub.2TiO.sub.5. The secondary phase is evenly dispersed in the
primary phase.
[0026] (2) The multiphase ceramic material has a high insulation
resistivity and a high breakdown voltage. The ceramic material has
an insulation resistivity of higher than 10.sup.11 .OMEGA.cm.
[0027] (3) At the frequency range of 20 Hz to 2.times.10.sup.6 Hz
and at the temperature range of -160.degree. C. to 170.degree. C.,
the dielectric constant (>10.sup.4) of the multiphase ceramic
material shows very little frequency- and temperature-dependency.
The dielectric loss of the ceramic material is less than 0.05
before 2.times.10.sup.5 Hz from -50.degree. C. to 150.degree.
C.
BRIEF DESCRIPTION OF DRAWINGS
[0028] FIG. 1 shows the XRD spectra of the multiphase ceramic
material of embodiment 1 and embodiment 2.
[0029] FIG. 2 shows the backscattered electron (BSE) images and the
secondary electron (SE) images of the multiphase ceramic material
of embodiment 1 and embodiment 2.
[0030] FIG. 3 illustrates the frequency-dependent dielectric
properties of the multiphase ceramic material of embodiment 1,
which is measured at room temperature.
[0031] FIG. 4 illustrates the temperature-dependent dielectric
properties of the multiphase ceramic material of embodiment 1 with
four selected frequencies (100 Hz, 1 kHz, 10 kHz and 100 kHz)
embodiment.
[0032] FIG. 5 is a backscattered electron (BSE) image of the
multiphase ceramic material of embodiment 2.
DETAILED DESCRIPTION OF EMBODIMENTS
[0033] The objectives, technical solutions, and beneficial effects
of the present invention will be described below with reference to
the accompanying drawings and embodiments.
Embodiment 1
[0034] Embodiment 1 is one of the embodiments in the present
invention. The multiphase ceramic material of this embodiment has a
general formula of A.sub.xB.sub.nxTi.sub.1-(n+1)xO.sub.2, where A
is Nb, B is In, x=0.0125, and n=2.
[0035] The detailed method to synthesize this embodiment comprised
the following steps:
[0036] (1) 0.2492 g Nb.sub.2O.sub.5, 0.5206 g In.sub.2O.sub.3, and
11.5312 g TiO.sub.2 were weighed;
[0037] (2) The aforementioned reactants were placed in a
ball-milling tank with the grinding medium of yttrium-stabilized
zirconia balls and the dispersant of ethanol or acetone;
ball-milling was carried out for more than 12 h until the reactants
were thoroughly mixed; the mixture was dried to obtain a
homogeneous mixture powder;
[0038] (3) The mixture powder was granulated in a mortar, and the
detailed condition was: the pure water was added as the additive,
and the weight ratio of pure water to the powder was 5%; mixed
thoroughly; transferred the granulated powder into a 32 mm die,
pressed at 416 MPa to obtain a green pellet; the green pellet was
pulverized and ground in a mortar to obtain preliminary powder;
[0039] (4) The preliminary powder was transferred into a 1.2 mm
die, pressed at a pressure of 2 MPa, followed by sintering in the
air; sintering parameters included heating rate: 15.degree. C./min,
temperature: 1420.degree. C., holding time: 3 h; after sintering,
the product was naturally cooled down to room temperature to obtain
a dense ceramic pellet;
[0040] (5) The surface of the dense ceramic pellet obtained in step
(4), was polished by a 240-grit sandpaper and a 1200-grit
sandpaper; annealed in the air; annealing parameters include
heating rate: 15.degree. C./min, temperature: 1200.degree. C.,
holding time: 1 h; after annealing, the product obtained was
naturally cooled down to room temperature to obtain the multiphase
ceramic material.
Embodiment 2
[0041] Embodiment 2 is one of the embodiments in the present
invention. The multiphase ceramic material of this embodiment has a
general formula of A.sub.xB.sub.nxTi.sub.1-(n+1)xO.sub.2, wherein A
is Nb, B is In, x=0.075, and n=2.
[0042] The detailed method to synthesize this embodiment comprised
the following steps:
[0043] (1) 1.4952 g Nb.sub.2O.sub.5, 3.1233 g In.sub.2O.sub.3, and
9.2849 g TiO.sub.2 were weighed;
[0044] (2) The aforementioned reactants were placed in a
ball-milling tank with the grinding medium of yttrium-stabilized
zirconia balls and the dispersant of ethanol or acetone;
ball-milling was carried out for more than 12 h until the reactants
were thoroughly mixed; the mixture was dried to obtain a
homogeneous mixture powder;
[0045] (3) The mixture powder was granulated in a mortar, and the
detailed condition was: the pure water was added as the additive,
and the weight ratio of pure water to the powder was 10%; mixed
thoroughly; transferred the granulated powder into a 32 mm die,
pressed at 416 MPa to obtain a green pellet; the green pellet was
pulverized and ground in a mortar to obtain preliminary powder;
[0046] (4) The preliminary powder was transferred into a 1.2 mm
die, pressed at a pressure of 2 MPa, followed by sintering in the
air; sintering parameters included heating rate: 3.8.degree.
C./min, temperature: 1200.degree. C., holding time: 3 h; after
sintering, the product was naturally cooled down to room
temperature to obtain a dense ceramic pellet;
[0047] (5) The surface of the dense ceramic pellet obtained in step
(4) was polished with a 240-grit sandpaper and a 1200-grit
sandpaper; annealed in the air; annealing parameters include
heating rate: 5.degree. C./min, temperature: 1000.degree. C.,
holding time: 24 h; after annealing, the product obtained was
naturally cooled down to room temperature to obtain the multiphase
ceramic material.
Embodiment 3
[0048] Embodiment 3 is one of the embodiments in the present
invention. The multiphase ceramic material of this embodiment has a
general formula of A.sub.xB.sub.nxT.sub.1-(n+1)xO.sub.2, wherein A
is Nb, B is In, x=0.0125, and n=3.
[0049] The detailed method to synthesize this embodiment comprised
the following steps:
[0050] (1) 0.2492 g Nb.sub.2O.sub.5, 0.7809 g In.sub.2O.sub.3, and
11.3809 g TiO.sub.2 were weighed;
[0051] (2) The aforementioned reactants were placed in a
ball-milling tank with the grinding medium of yttrium-stabilized
zirconia balls and the dispersant of ethanol or acetone;
ball-milling was carried out for more than 12 h until the reactants
were thoroughly mixed; the mixture was dried to obtain a
homogeneous mixture powder;
[0052] (3) The mixture powder was granulated in a mortar, and the
detailed condition was: the pure water was added as the additive,
and the weight ratio of pure water to the powder was 5%; mixed
thoroughly; transferred the granulated powder into a 32 mm die,
pressed at 416 MPa to obtain a green pellet; the green pellet was
pulverized and ground in a mortar to obtain preliminary powder;
[0053] (4) The preliminary powder was transferred into a 1.2 mm
die, pressed at a pressure of 2 MPa, followed by sintering in the
air; sintering parameters included heating rate: 3.8.degree.
C./min, temperature: 1420.degree. C., holding time: 3 h; after
sintering, the product was naturally cooled down to room
temperature to obtain a dense ceramic pellet;
[0054] (5) The surface of the dense ceramic pellet obtained in step
(4) was polished with a 240-grit sandpaper and a 1200-grit
sandpaper; annealed in the air; annealing parameters include
heating rate: 5.degree. C./min, temperature: 1200.degree. C.,
holding time: 1 h; after annealing, the product obtained was
naturally cooled down to room temperature to obtain the multiphase
ceramic material with a giant dielectric constant.
Embodiment 4
[0055] Embodiment 4 is one of the embodiments in the present
invention. The multiphase ceramic material of this embodiment has a
general formula of A.sub.xB.sub.nxTi.sub.1-(n+1)xO.sub.2, wherein A
is Nb, B is In, x=0.0125, and n=4.
[0056] The detailed method to synthesize this embodiment comprised
the following steps:
[0057] (1) 0.2492 g Nb.sub.2O.sub.5, 1.0412 g In.sub.2O.sub.3, and
11.2312 g TiO.sub.2 were weighed;
[0058] (2) The aforementioned reactants were placed in a
ball-milling tank with the grinding medium of yttrium-stabilized
zirconia balls and the dispersant of ethanol or acetone;
ball-milling was carried out for more than 12 h until the reactants
were thoroughly mixed; the mixture was dried to obtain a
homogeneous mixture powder;
[0059] (3) The mixture powder obtained was granulated in a mortar,
and the detailed condition was: the pure water was added as the
additive, and the weight ratio of pure water to the powder was 5%;
mixed thoroughly; transferred the mixture powder into a 32 mm die,
pressed at 416 MPa to obtain a green pellet; the green pellet was
pulverized and ground in a mortar to obtain preliminary powder;
[0060] (4) The preliminary powder was transferred into a 1.2 mm
die; pressed at a pressure of 2 MPa, followed by sintering in the
air; sintering parameters included heating rate: 3.8.degree.
C./min, temperature: 1420.degree. C., holding time: 3 h; after
sintering, the product obtained was naturally cooled down to room
temperature to obtain a dense ceramic pellet;
[0061] (5) The surface of the dense ceramic pellet obtained in step
(4) was polished with a 240-grit sandpaper and a 1200-grit
sandpaper, followed by annealing in the air; annealing parameters
include heating rate: 5.degree. C./min, temperature: 1200.degree.
C., holding time: 1 h; after annealing, the product obtained was
naturally cooled down to room temperature to obtain the multiphase
ceramic material with a giant dielectric constant.
[0062] FIG. 1 shows the XRD spectra of the multiphase ceramic
material with a giant dielectric constant of embodiment 1 (1.25 at.
% Nb.sup.5++2.5 at. % In.sup.3+) and embodiment 2 (7.5 at. %
Nb.sup.5++15 at. % In.sup.3+). FIG. 1 illustrates that the
materials prepared in embodiment 1 and embodiment 2 have two
structures, that is, rutile titanium dioxide and orthogonal
In.sub.2TiO.sub.5.
[0063] FIG. 2 shows the backscattered electron (BSE) images and the
secondary electron (SE) images of the multiphase ceramic material
with a giant dielectric constant of embodiment 1 (1.25 at. %
Nb.sup.5++2.5 at. % In.sup.3+) and embodiment 2 (7.5 at. %
Nb.sup.5++15 at. % In.sup.3+). FIG. 2 further demonstrates that the
materials prepared in embodiment 1 and embodiment 2 have two
phases, and the secondary phase is evenly dispersed in the primary
phase.
[0064] FIG. 3 shows frequency-dependent dielectric properties of
embodiment 1 (1.25 at. % Nb.sup.5++2.5 at. % In.sup.3+) at room
temperature. FIG. 3 demonstrates that at the frequency range of 20
Hz to 2.times.10.sup.6 Hz, the dielectric constant of the ceramic
material prepared in embodiment 1 (1.25 at. % Nb.sup.5++2.5 at. %
In.sup.3+) is higher than 10,000 and it depends very little on
frequency. When the frequency is lower than 2.times.10.sup.5 Hz,
the dielectric loss is less than 0.05.
[0065] FIG. 4 shows temperature-dependent dielectric properties of
embodiment 1 (1.25 at. % Nb.sup.5++2.5 at. % In.sup.3+) and 4
frequencies (100 Hz, 1 kHz, 10 kHz and 100 kHz) were selected. FIG.
4 shows that the dielectric constant of embodiment 1 (1.25 at. %
Nb.sup.5++2.5 at. % In.sup.3+) is higher than 10,000 from
-160.degree. C. to 170.degree. C. and it is almost
temperature-independent. The dielectric loss is less than 0.05 from
-50.degree. C. to 150.degree. C.
[0066] FIG. 5 is the backscattered electron (BSE) image of
embodiment 2 (7.5 at. % Nb.sup.5++15 at. % In.sup.3+). Table 1 is
the atomic ratio of elements of spots labelled out in FIG. 5, which
was measured by the energy-dispersive spectroscopy (EDS).
TABLE-US-00001 TABLE 1 The atomic ratio of elements of spots
labelled out in FIG. 5 EDS # Ti at. % Nb at. % In at. % 1 83.30
8.25 8.46 2 82.92 8.38 8.69 3 32.93 0.98 66.09
[0067] FIG. 1, FIG. 5, and table 1 show that the primary phase of
the multiphase ceramic materials with a giant dielectric constant
is Nb.sup.5+ and In.sup.3 + co-doped rutile TiO.sub.2, while the
secondary phase is B.sub.2TiO.sub.5.
[0068] Table 2 summarizes the resistivity, the dielectric constant
and the dielectric loss of the ceramic materials prepared in
embodiments 1, 3, and 4 and a reference material:
TABLE-US-00002 TABLE 2 Resistivity, dielectric constant and
dielectric loss of the materials of embodiments 1, 3, and 4 and a
reference material Resistivity Dielectric constant Dielectric loss
n General formula (.OMEGA. cm) (frequency f = 1 kHz) (frequency f =
1 kHz) 1 Nb.sub.1.25%In.sub.1.25%Ti.sub.97.5%O.sub.2 9.88 .times.
10.sup.10 57000 0.0031 (Reference material) 2
Nb.sub.1.25%In.sub.2.5%Ti.sub.96.25%O.sub.2 3.26 .times. 10.sup.11
12000 0.0048 3 Nb.sub.1.25%In.sub.3.75%Ti.sub.95%O.sub.2 2.53
.times. 10.sup.11 11000 0.0058 4
Nb.sub.1.25%In.sub.5%Ti.sub.93.75%O.sub.2 5.26 .times. 10.sup.11
10000 0.016
[0069] Compared with the reference material (1.25 at %
Nb.sup.5+1.25 at % In.sup.3+), the materials of embodiments 1, 3
and 4 have higher resistivity, as well as a high dielectric
constant (>10,000) and low dielectric loss (<0.05). This
suggests that because the secondary phase is discontinuously and
uniformly distributed at the grain boundary of the primary phase,
it effectively blocks the movement of weakly bounded charges,
contributing to high working voltage and breakdown voltage of the
material. Meanwhile, the existence of the secondary phase does not
cause the deterioration of the giant dielectric property of the
material.
[0070] At last, it should be noted that the aforementioned
embodiments are only used to illustrate the technical solutions of
the present invention that does not limit the protection scope of
the present invention. Although the present invention has been
described in detail with reference to the preferred embodiments,
those of ordinary skill in the art should understand that the
technical solution of the present invention can be modified without
deviating from the essence and scope of the technical solution of
the present invention.
* * * * *