U.S. patent application number 17/210326 was filed with the patent office on 2022-04-21 for sample collection apparatus for scent detection.
This patent application is currently assigned to The Government of the United States of America, as represented by the Secretary of Homeland Security. The applicant listed for this patent is The Government of the United States of America, as represented by the Secretary of Homeland Security, The Government of the United States of America, as represented by the Secretary of Homeland Security. Invention is credited to Mark Fry.
Application Number | 20220120645 17/210326 |
Document ID | / |
Family ID | 1000005697784 |
Filed Date | 2022-04-21 |

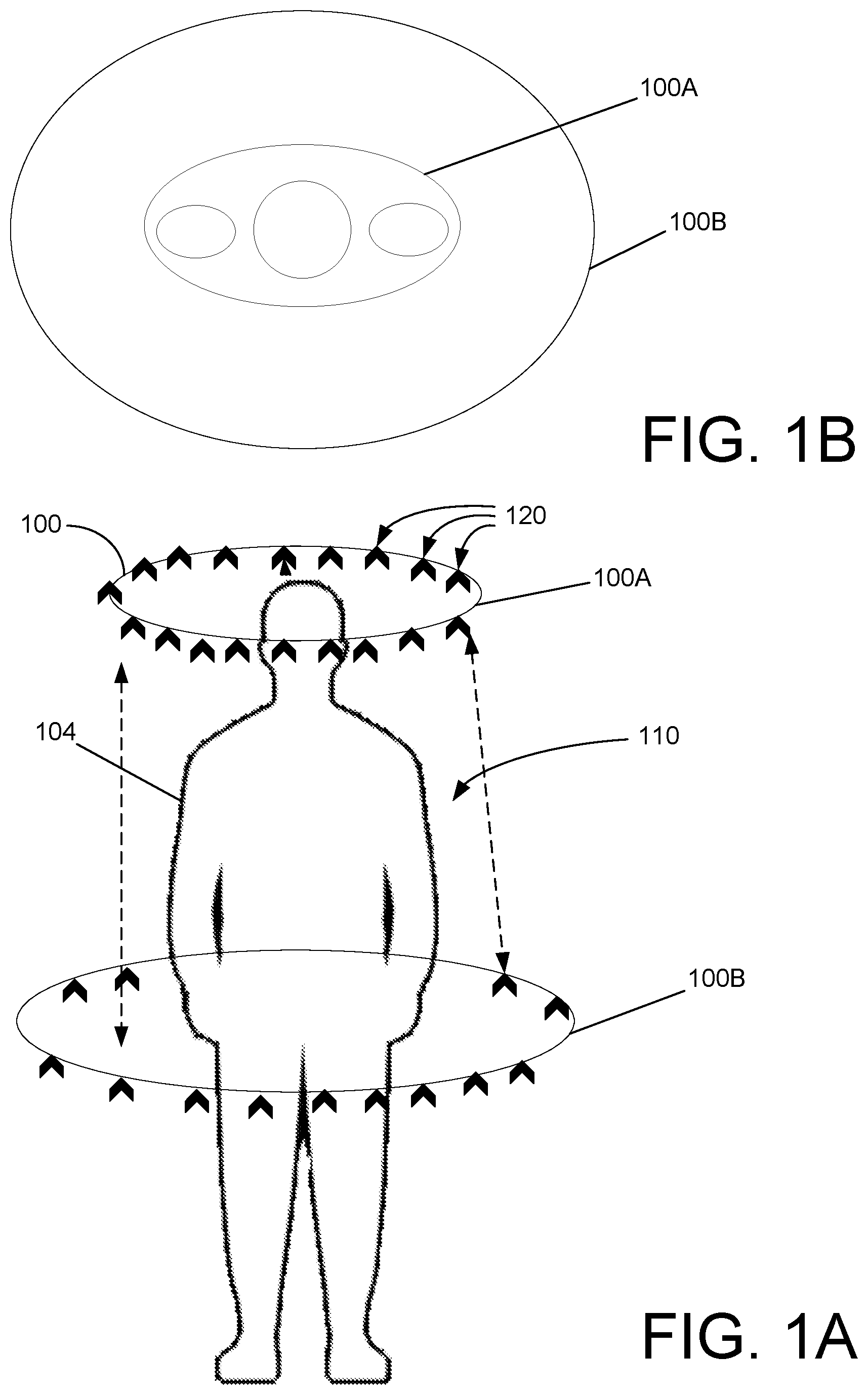

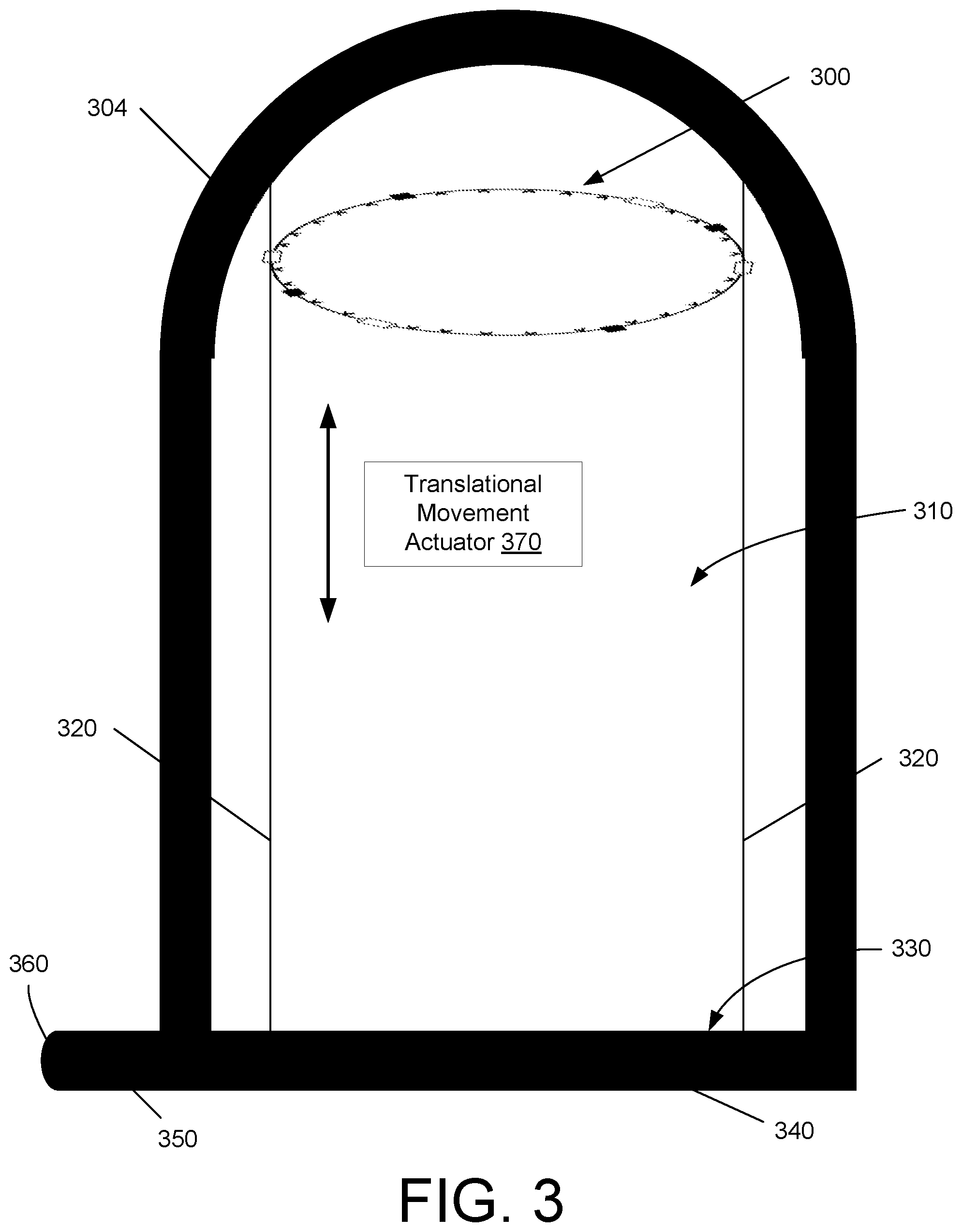




United States Patent
Application |
20220120645 |
Kind Code |
A1 |
Fry; Mark |
April 21, 2022 |
SAMPLE COLLECTION APPARATUS FOR SCENT DETECTION
Abstract
In an example, a sample collection apparatus to collect sample
from a detection subject includes a circumferential ring tubing
surrounding an interior and configured to be moved between bottom
ring tubing position and top ring tubing position. The
circumferential ring tubing includes air nozzles along a
circumferential length of the ring tubing to direct air flow toward
the interior as the ring tubing is moved from the top ring tubing
position to the bottom ring tubing position, to blow air toward the
detection subject in a sample collection zone in the interior and
to push a sample of the detection subject via an air flow toward a
platform on which the detection subject is positioned. The sample
includes particles and/or vapor of the detection subject. A
receptacle is disposed below the platform to collect the sample
carried by the air flow through collection openings of the platform
to the receptacle.
Inventors: |
Fry; Mark; (Marco Island,
FL) |
|
Applicant: |
Name |
City |
State |
Country |
Type |
The Government of the United States of America, as represented by
the Secretary of Homeland Security |
Washington |
DC |
US |
|
|
Assignee: |
The Government of the United States
of America, as represented by the Secretary of Homeland
Security
Washington
DC
|
Family ID: |
1000005697784 |
Appl. No.: |
17/210326 |
Filed: |
March 23, 2021 |
Related U.S. Patent Documents
|
|
|
|
|
|
Application
Number |
Filing Date |
Patent Number |
|
|
63092903 |
Oct 16, 2020 |
|
|
|
Current U.S.
Class: |
1/1 |
Current CPC
Class: |
G01N 1/2211 20130101;
G01N 1/2247 20130101; G01N 2001/024 20130101; G01N 2001/2223
20130101; G01N 1/28 20130101 |
International
Class: |
G01N 1/22 20060101
G01N001/22; G01N 1/28 20060101 G01N001/28 |
Claims
1. A sample collection apparatus to collect sample from a detection
subject comprising: a platform to support a detection subject on
which a bottom of the detection subject is positioned; a
circumferential ring tubing surrounding an interior and configured
to be moved generally vertically between a bottom ring tubing
position and a top ring tubing position, the circumferential ring
tubing including a plurality of air nozzles along a circumferential
length of the circumferential ring tubing to direct air flow toward
the interior as the circumferential ring tubing is moved from the
top ring tubing position to the bottom ring tubing position, to
blow air toward the detection subject in a sample collection zone
in the interior of the circumferential ring tubing as the
circumferential ring tubing is moved from the top ring tubing
position to the bottom ring tubing position, and to push a sample
of the detection subject via an air flow forward toward the
platform below the detection subject on which the bottom of the
detection subject is positioned, the sample including at least one
of particles and vapor of the detection subject; a receptacle
disposed below the platform to collect the sample of the detection
subject carried by the air flow through a plurality of collection
openings of the platform to the receptacle; and, a plurality of
circumferential length adjusting telescoping actuators disposed on
the circumferential ring tubing to adjust a circumferential length
of the circumferential ring tubing to contract the circumferential
ring tubing by decreasing the circumferential length and to expand
the circumferential ring tubing by increasing the circumferential
length.
2. The sample collection apparatus of claim 1, wherein the air
nozzles are oriented between an angle of about 0.degree.
horizontally inward toward the interior of the circumferential ring
tubing and an angle of less in magnitude than about -90.degree.
vertically downward.
3. The sample collection apparatus of claim 2, wherein the air
nozzles are oriented between an angle of about 5.degree. inward
toward the interior of the circumferential ring tubing and an angle
of about -15.degree. partially inward and partially downward.
4. The sample collection apparatus of claim 1, wherein the
circumferential ring tubing includes a plurality of linear tubes
connected together; and, wherein the plurality of circumferential
length adjusting telescoping actuators are coupled with the
plurality of linear tubes of the circumferential ring tubing to
adjust a circumferential length of the circumferential ring tubing
to contract the circumferential ring tubing by decreasing the
circumferential length and to expand the circumferential ring
tubing by increasing the circumferential length.
5. The sample collection apparatus of claim 1, further comprising:
a plurality of sensors disposed on the circumferential ring tubing
to detect shape and size of the detection subject to produce
detection data; and a controller to control the circumferential
length adjusting telescoping actuators to adjust the
circumferential length of the circumferential ring tubing based on
the detection data.
6. The sample collection apparatus of claim 5, wherein the
controller is configured to control the circumferential length
adjusting telescoping actuators to adjust the circumferential
length of the circumferential ring tubing to keep a distance
between the circumferential ring tubing and the detection subject
to within a preset distance range.
7. The sample collection apparatus of claim 1, further comprising:
a plurality of translational stanchions to which the
circumferential ring tubing is slidably attached to travel
translationally between the top ring tubing position and the bottom
ring tubing position.
8. A sample collection method to collect sample from a detection
subject, the method comprising: placing a circumferential ring
tubing at a ring tubing initiation position at or near an
initiation end of the detection subject, the circumferential ring
tubing surrounding an interior; moving the circumferential ring
tubing translationally from the ring tubing initiation position to
a ring tubing collection position at or near a platform to which
the detection subject is connected, blowing air through a plurality
of air nozzles along a circumferential length of the
circumferential ring tubing to direct air flow toward the interior
as the circumferential ring tubing is moved from the ring tubing
initiation position to the ring tubing collection position to blow
air toward the detection subject in a sample collection zone in the
interior of the circumferential ring tubing as the circumferential
ring tubing is moved from the ring tubing initiation position to
the ring tubing collection position, and to push a sample of the
detection subject via an air flow forward toward the platform to
which the detection subject is connected, the sample including at
least one of particles and vapor of the detection subject;
collecting the sample of the detection subject carried by the air
flow through a plurality of collection openings of the platform to
an opposite side of the platform from the detection subject to a
receptacle; and, adjusting a circumferential length of the
circumferential ring tubing, using a plurality of circumferential
length adjusting telescoping actuators disposed on the
circumferential ring tubing, to contract the circumferential ring
tubing by decreasing the circumferential length and to expand the
circumferential ring tubing by increasing the circumferential
length.
9. The sample collection method of claim 8, further comprising:
orienting the air nozzles for blowing air toward the detection
subject between an angle of about 0.degree. horizontally inward
toward the interior of the circumferential ring tubing and an angle
of less in magnitude than about -90.degree. vertically
downward.
10. The sample collection method of claim 9, wherein the air
nozzles are oriented between an angle of about 5.degree.
horizontally inward toward the interior of the circumferential ring
tubing and an angle of about -15.degree. partially inward and
partially downward.
11. The sample collection method of claim 8, wherein the
circumferential ring tubing includes a plurality of linear tubes
connected together; and wherein the plurality of circumferential
length adjusting telescoping actuators are coupled with the
plurality of linear tubes of the circumferential ring tubing to
adjust a circumferential length of the circumferential ring tubing
to contract the circumferential ring tubing by decreasing the
circumferential length and to expand the circumferential ring
tubing by increasing the circumferential length.
12. The sample collection method of claim 8, further comprising:
detecting shape and size of the detection subject, using a
plurality of sensors disposed on the circumferential ring tubing,
to produce detection data; and controlling the circumferential
length adjusting telescoping actuators to adjust the
circumferential length of the circumferential ring tubing based on
the detection data.
13. The sample collection method of claim 12, wherein the
circumferential length adjusting telescoping actuators are
controlled to adjust the circumferential length of the
circumferential ring tubing to keep a distance between the
circumferential ring tubing and the detection subject to within a
preset distance range based on the detection data.
14. The sample collection method of claim 8, further comprising:
adjusting the circumferential length of the circumferential ring
tubing, by controlling the circumferential length adjusting
telescoping actuators, to keep a distance between the
circumferential ring tubing and the detection subject to within a
preset distance range.
15. The sample collection method of claim 8, further comprising:
slidably attaching the circumferential ring tubing to a plurality
of translational stanchions to travel translationally between the
ring tubing initiation position and the ring tubing collection
position; and moving the circumferential ring tubing
translationally from the ring tubing initiation position to a ring
tubing collection position at or near the platform to which the
detection subject is connected.
16. A sample collection apparatus to collect sample from a
detection subject comprising: a platform to support a detection
subject, the platform having a plurality of collection openings; a
sample receptacle; and a circumferential ring tubing surrounding an
interior and configured to be moved between an ring tubing
initiation position and a ring tubing collection position, the
circumferential ring tubing including a plurality of air nozzles
along a circumferential length of the circumferential ring tubing
to direct air flow toward the interior as the circumferential ring
tubing is moved from the ring tubing initiation position forward to
the ring tubing collection position, to blow air toward the
detection subject in a sample collection zone in the interior of
the circumferential ring tubing as the circumferential ring tubing
is moved from the ring tubing initiation position to the ring
tubing collection position, and to push a sample of the detection
subject via an air flow forward through the plurality of collection
openings of the platform to an opposite side of the platform from
the detection subject toward the sample receptacle, the sample
including at least one of particles and vapor of the detection
subject; and, a plurality of circumferential length adjusting
telescoping actuators to adjust a circumferential length of the
circumferential ring tubing to contract the circumferential ring
tubing by decreasing the circumferential length and to expand the
circumferential ring tubing by increasing the circumferential
length.
17. The sample collection apparatus of claim 16, wherein the air
nozzles are oriented between an angle of about 0.degree.
horizontally inward toward the interior of the circumferential ring
tubing and an angle of about -30.degree. partially inward and
partially forward.
18. The sample collection apparatus of claim 16, wherein the
circumferential ring tubing includes a plurality of linear tubes
connected together; and, wherein the plurality of circumferential
length adjusting telescoping actuators are coupled with the
plurality of linear tubes of the circumferential ring tubing to
adjust a circumferential length of the circumferential ring tubing
to contract the circumferential ring tubing by decreasing the
circumferential length and to expand the circumferential ring
tubing by increasing the circumferential length.
19. The sample collection apparatus of claim 16, further
comprising: means for mapping an outer surface of the detection
subject to produce mapping data; and a controller to control the
circumferential length adjusting telescoping actuators to adjust
the circumferential length of the circumferential ring tubing,
based on the mapping data, to keep a distance between the
circumferential ring tubing and the outer surface of the detection
subject to within a preset distance range.
20. The sample collection apparatus of claim 16, further
comprising: means for guiding forward movement of the
circumferential ring tubing between the ring tubing initiation
position and the ring tubing collection position.
Description
CROSS-REFERENCE TO RELATED APPLICATIONS
[0001] The application claims the benefit of priority from U.S.
Provisional Patent Application No. 63/092,903, filed on Oct. 16,
2020, entitled CANINE TESTING AND DETECTION AIDE, the disclosure of
which is incorporated by reference in its entirety.
SUMMARY STATEMENT OF GOVERNMENT INTEREST
[0002] The present invention was made by employees of the United
States Department of Homeland Security in the performance of their
official duties. The U.S. Government has certain rights in this
invention.
FIELD
[0003] The discussion below relates generally to systems and
methods of facilitating detection and testing of illicit substances
utilizing canine or the like.
BACKGROUND
[0004] U.S. Pat. No. 10,123,509 discloses enhancing air flow with
fans in vapor wake detection for detecting explosives and other
illicit substances. With vapor wake detection, a handler positions
a canine in a desired location and the canine detects scents in the
air that come to the canine. When the canine detects a trained
scent such as a bomb scent, the canine follows behind the carrier
of the item with the scent and leads the handler to the
carrier.
SUMMARY
[0005] Embodiments of the present invention are directed to
apparatuses and methods for directing not only vapor but also
particles from a detection subject or carrier to a detection area
for detecting explosives or other illicit substances, for instance,
by a canine trained in scent detection.
[0006] In some embodiments, a canine testing and detection aide is
more focused and separates the dog from the detection subjects. The
sample collection apparatus may be configured to collect particles
as well as vapor of the detection subject for detection and thus
greatly increases the sample size.
[0007] In accordance with an aspect, a sample collection apparatus
to collect sample from a detection subject comprises: a
circumferential ring tubing surrounding an interior and configured
to be moved generally vertically between a bottom ring tubing
position and a top ring tubing position, the circumferential ring
tubing including a plurality of air nozzles along a circumferential
length of the circumferential ring tubing to direct air flow toward
the interior as the circumferential ring tubing is moved from the
top ring tubing position to the bottom ring tubing position, to
blow air toward the detection subject in a sample collection zone
in the interior of the circumferential ring tubing as the
circumferential ring tubing is moved from the top ring tubing
position to the bottom ring tubing position, and to push a sample
of the detection subject via an air flow forward toward a platform
on which the detection subject is positioned, the sample including
at least one of particles and vapor of the detection subject; and a
receptacle disposed below the platform to collect the sample of the
detection subject carried by the air flow through a plurality of
collection openings of the platform to the receptacle.
[0008] Another aspect is directed to a sample collection method to
collect sample from a detection subject. The method comprises:
placing a circumferential ring tubing at a ring tubing initiation
position at or near an initiation end of the detection subject, the
circumferential ring tubing surrounding an interior; moving the
circumferential ring tubing translationally from the ring tubing
initiation position to a ring tubing collection position at or near
a platform to which the detection subject is connected, blowing air
through a plurality of air nozzles along a circumferential length
of the circumferential ring tubing to direct air flow toward the
interior as the circumferential ring tubing is moved from the ring
tubing initiation position to the ring tubing collection position
to blow air toward the detection subject in a sample collection
zone in the interior of the circumferential ring tubing as the
circumferential ring tubing is moved from the ring tubing
initiation position to the ring tubing collection position, and to
push a sample of the detection subject via an air flow forward
toward the platform to which the detection subject is connected,
the sample including at least one of particles and vapor of the
detection subject; and collecting the sample of the detection
subject carried by the air flow in a receptacle disposed adjacent
the platform through a plurality of collection openings of the
platform to the receptacle.
[0009] In accordance with another aspect, a sample collection
apparatus to collect sample from a detection subject comprises: a
sample receptacle; and a circumferential ring tubing surrounding an
interior and configured to be moved between an ring tubing
initiation position and a ring tubing collection position, the
circumferential ring tubing including a plurality of air nozzles
along a circumferential length of the circumferential ring tubing
to direct air flow toward the interior as the circumferential ring
tubing is moved from the ring tubing initiation position forward to
the ring tubing collection position, to blow air toward the
detection subject in a sample collection zone in the interior of
the circumferential ring tubing as the circumferential ring tubing
is moved from the ring tubing initiation position to the ring
tubing collection position, and to push a sample of the detection
subject via an air flow forward toward the sample receptacle, the
sample including at least one of particles and vapor of the
detection subject.
[0010] Other features and aspects of various examples and
embodiments will become apparent to those of ordinary skill in the
art from the following detailed description which discloses, in
conjunction with the accompanying drawings, examples that explain
features in accordance with embodiments. This summary is not
intended to identify key or essential features, nor is it intended
to limit the scope of the invention, which is defined solely by the
claims.
BRIEF DESCRIPTION OF THE DRAWINGS
[0011] The attached drawings help explain the embodiments described
below.
[0012] FIG. 1A is a front view of an example of a sample collection
apparatus for collecting a sample for scent detection according to
an embodiment.
[0013] FIG. 1B is a simplified top view of the apparatus of FIG.
1A.
[0014] FIG. 2 is a front view of an example of an open screening
portal which includes a sample collection apparatus for collecting
a sample for scent detection according to another embodiment.
[0015] FIG. 3 is a front view of an example of an enclosed
screening portal which includes a sample collection apparatus for
collecting a sample for scent detection according to another
embodiment.
[0016] FIG. 4 is a simplified top view of an air ring in the sample
collection apparatus of FIG. 3.
[0017] FIG. 5 is a block diagram of an example of a control system
of the sample collection apparatus according to an embodiment.
[0018] FIG. 6 is a flow diagram illustrating an example of a sample
collection process.
[0019] FIG. 7 illustrates a computing system including logic
according to an embodiment.
DETAILED DESCRIPTION
[0020] A number of examples or embodiments of the present invention
are described, and it should be appreciated that the present
invention provides many applicable inventive concepts that can be
embodied in a variety of ways. The embodiments discussed herein are
merely illustrative of ways to make and use the invention and are
not intended to limit the scope of the invention. Rather, as will
be appreciated by one of skill in the art, the teachings and
disclosures herein can be combined or rearranged with other
portions of this disclosure along with the knowledge of one of
ordinary skill in the art.
[0021] FIG. 1A is a front view of an example of a sample collection
apparatus for collecting a sample for scent detection according to
an embodiment. FIG. 1B is a simplified top view of the apparatus of
FIG. 1A.
[0022] An air ring 100 is disposed at a top ring position 100A
above the detection subject 104 typically standing in a sample
collection zone 110 such as a passenger portal at a passenger
screening area or checkpoint. The air ring 100 may be a
circumferential ring tubing 100 formed of one continuous tubing or
a plurality of linear and/or curvilinear tubes connected together.
It includes a plurality of air nozzles 120 that are distributed
along a circumferential length of the air ring 100 and pointed
inwardly toward an interior (e.g., center or central axis) of the
sample collection zone 110 and downwardly toward the bottom of the
sample collection zone 110. The range of possible nozzle angles may
be between about 0.degree. (horizontally inward) and less in
magnitude than about -90.degree. (vertically downward), or between
0.degree. and about -60.degree. (partially inward and partially
downward), or between 0.degree. and about -30.degree. , or between
about 5.degree. and about -15.degree.. The air ring 100 may be
controlled to move or slide downwardly from the top ring position
110A to a lower position 110B, for instance, down to a bottom ring
position at or near a bottom of the detection subject such as a
platform on which the detection subject 104 stands. The air flow
forms a sheet of air acting as a boundary layer that pushes
particles and vapor as a sample of the detection subject 104
downward, for instance, toward a sample receptacle.
[0023] The plurality of air nozzles 120 along the circumferential
length of the circumferential ring tubing 100 direct air flow
toward the interior as the circumferential ring tubing 100 is moved
from the top ring tubing position 100A to the bottom ring tubing
position to blow air toward the detection subject 104 in the sample
collection zone 110 in the interior, to push a sample of the
detection subject 104 via an air flow downward toward the platform
on which the detection subject 104 is positioned. The sample
includes particles and/or vapor of the detection subject 104.
[0024] The nozzle angles of the air nozzles 120 may be fixed or
adjustable. In one embodiment, the nozzle angle may be fixed during
movement of the air ring 100 from the top ring position 100A to the
bottom ring position. In another embodiment, the nozzle angle may
be adjusted during movement of the air ring 100 from the top ring
position 100A to the bottom ring position; this may improve sample
collection. The air ring tubing 100 may have a circular
cross-section and the nozzles 120 may be configured to be rotatable
around the circular cross-section of the air ring tubing 100 to
adjust the nozzle angle. A nozzle controller may be provided to
rotate the nozzles 120 during movement of the air ring 100 from the
top ring position 100A to the bottom ring position. The nozzle
angle may be adjusted as a function of the vertical or
translational position of the air ring 100. For instance, the
nozzle angle may gradually change to an increasingly downward
orientation as the air ring 100 moves closer to the bottom ring
position to push the sample toward the collection receptacle more
effectively.
[0025] As seen in FIGS. 1A and 1B, the air ring 100 has an oval or
elliptical shape with a major diameter and a minor diameter. In
another embodiment, the air ring 100 may be a circle. Still other
embodiments may provide other linear and/or curvilinear shapes for
the air ring 100. The ring 100 of nozzles 120 may have an
adjustable lateral position (e.g., varying major and minor
diameters) to keep the nozzles in close proximity of the detection
subject 104 (i.e., moving inwardly to form a smaller ring around
the head, moving outwardly to form a larger ring around the
shoulder and the core and the hip, and moving inwardly to form a
smaller ring around the lower legs).
[0026] FIG. 2 is a front view of an example of an open screening
portal which includes a sample collection apparatus for collecting
a sample for scent detection according to another embodiment. An
air ring 200 slides from a top ring position 200A above the
detection subject typically standing in a sample collection zone
210. It includes a plurality of air nozzles 220 that are pointed
inwardly toward the interior of the sample collection zone 210 and
downwardly toward the bottom of the sample collection zone 210. At
the bottom is a platform 230 on which the detection subject may
stand or to which the detection subject is connected. The air ring
200 is controlled to move or slide downwardly from the top ring
position 200A to a bottom ring position at or near the platform
230. A sample receptacle 240 may be disposed below the platform 230
which includes a plurality of collection receptors 244 such as
perforations or openings through the platform 230, to collect the
sample of the detection subject carried by the air flow through the
plurality of collection receptors 244 of the platform 230 to the
receptacle 240.
[0027] The air flow from the air ring 200 of nozzles 220 forms a
sheet of air acting as a boundary layer that pushes particles and
vapor of the detection subject downward toward the collection
receptors 244. This action causes the air flow to drive particles
and vapor of the detection subject through the collection receptors
244 to the sample receptacle 240. A vacuum or negative pressure 270
may be provided to help draw the air flow into the sample
receptacle 240. A receptor tunnel or receptor channel 250 may be
connected to the sample receptacle 240 to direct the air flow of
particles and vapor collected at the sample receptacle 240 toward
an outlet 260 where a dog is located to perform scent detection of
the sample. One benefit is the dog can be separated from the
detection subject and does not interact with the detection subject,
unlike the approach disclosed in U.S. Pat. No. 10,123,509.
[0028] FIG. 3 is a front view of an example of an enclosed
screening portal which includes a sample collection apparatus for
collecting a sample for scent detection according to another
embodiment. An air ring 300 is disposed inside the enclosed
screening portal or enclosure 304 which may be open or closed. An
open enclosure 304 may have an enclosure opening for the detection
subject to enter and exit the enclosure 304. In another example,
there may be an entrance enclosure opening and an exit enclosure
opening for the detection subject to walk into the enclosure, get
tested, and walk through and out of the enclosure 304. The
enclosure opening(s) may include door(s) that can be closed to
provide a more controlled environment of a closed enclosure in
which to drive the sample using the ring 300 of air nozzles and
collect the sample.
[0029] The air ring 300 may be a pneumatic ring employing a
plurality of sensors for detecting the shape and size of the
detection subject to produce detection data, which may then be used
to control adjustment of the circumferential length of the
circumferential ring tubing 300. The air ring 300 may include a
plurality of air blowers or nozzles for blowing air inwardly toward
the interior of a sample collection zone 310 and downwardly toward
the bottom of the sample collection zone 310. To guide up and down
movements of the pneumatic ring 300, stanchions or lines 320 may be
used. The stanchions 320 may be fixed and may be attached to the
base or platform 330 and/or the top of the enclosure 304. The
stanchions 320 may be rigid or flexible laterally. The pneumatic
ring 300 is slidably attached to the translational stanchions 320
to travel translationally between a top ring position and a bottom
ring position. In one example, the stanchions are vertical
stanchions 320. The bottom ring position may be at the platform 330
or a short distance (e.g., several inches) above the platform
330.
[0030] A sample receptacle 340 may be disposed below or adjacent
the platform 330 which includes a plurality of collection receptors
such as perforations or openings through the platform 330. The air
flow from the air ring 300 of nozzles forms a sheet of air acting
as a boundary layer that pushes a sample of particles and vapor of
the detection subject downward toward the collection receptors
through the platform 330, driving the sample through the collection
receptors to the sample receptacle 340. A vacuum or negative
pressure may be provided to help draw the air flow into the sample
receptacle 340. A receptor tunnel or receptor channel 350 may be
connected to the sample receptacle 340 to direct the air flow of
particles and vapor collected at the sample receptacle 340 through
an outlet 360 to a sample analysis location where the collected
sample is analyzed.
[0031] One or more translational movement actuators 370 may be used
to control translational movement of the air ring 300 along the
stanchions 320. In one example, the actuators are vertical movement
actuators 370. In other examples, the translational movement is not
vertical but any forward and backward movement, including inclined
movement and even horizontal movement. Furthermore, the vertical
movement actuators 370 may move the air ring 300 upward from the
bottom ring tubing position to the top ring tubing position for
collecting the sample, instead of downward. In general, the air
ring 300 starts from a ring tubing initiation position at or near
an initiation end of the detection subject (top air ring position
at or above the top of the detection subject in the examples of
FIGS. 2 and 3) and is driven forward (downward in the examples of
FIGS. 2 and 3) by the translational movement actuators 370 to a
ring tubing collection position at or near a collection end of the
detection subject (bottom air ring position at or near the bottom
of the detection subject in the examples of FIGS. 2 and 3) for
sample collection. The "forward" direction is downward in FIGS. 2
and 3, but may be an upward direction in another embodiment and may
be any other nonvertical direction in other embodiments. The
translational movement actuators 370 may be disposed on the air
ring 300 or the stanchions 320, or connected thereto from a remote
location, and these actuators 370 may be mechanical, pneumatic,
electrical, or the like. This is one example mechanism or means for
guiding forward movement of the circumferential ring tubing 300
between the ring tubing initiation position and the ring tubing
collection position. Other mechanisms, which may be mechanical or
of some other type, can be used in other embodiments.
[0032] FIG. 4 is a simplified top view of an example of an air ring
in the sample collection apparatus of FIG. 3. The air ring is a
circular pneumatic air ring 400. In other embodiments, the air ring
400 may be oval or elliptical or some other linear and/or
curvilinear shape.
[0033] The pneumatic air ring 400 may include a plurality of
pneumatic devices 410 for driving air through the air nozzles 430
toward the sample collection zone 450 (310 in FIG. 3). The
pneumatic devices 410 may be controlled locally or remotely by an
operator and/or a computer. The pneumatic devices 410 may be
activated only when the air ring 400 is moved from the top ring
position or top ring tubing position to the bottom ring position or
bottom ring tubing position.
[0034] The air ring 400 may include a plurality of circumferential
length adjusting devices or actuators 440 for adjusting the size of
the air ring 400. The air ring 400 shrinks or contracts in size
when the circumferential length is decreased and expands in size
when the circumferential length is increased. The circumferential
length of the air ring tubing 400 may be changed in a telescoping
manner utilizing a telescoping construction of overlapping
circumferential tubes for forming the air ring tubing 400. The
circumferential length adjusting devices 440 may be controlled
locally or remotely by an operator and/or a computer, based on
operator input and/or sensor input. This is one example mechanism
or means for adjusting a circumferential length of the
circumferential ring tubing to contract the circumferential ring
tubing by decreasing the circumferential length and to expand the
circumferential ring tubing by increasing the circumferential
length. Other mechanisms, which may be mechanical or of some other
type, can be used in other embodiments.
[0035] In one embodiment, the circumferential length adjusting
devices 440 adjust the size of the air ring 400 based at least in
part on sensors 420 that detect the shape and size of the detection
subject. The sensors 420 may be disposed on the air ring 400. One
example is a Lidar sensor. Lidar is an acronym for "light detection
and ranging" and is sometimes called "laser scanning" or "3D
scanning." The technology uses eye-safe laser beams to create a 3D
representation of the surveyed environment. In this example, the
Lidar sensor detects or maps the outline or outer surface (shape
and size) of the body of the detection subject. This is one example
mechanism or means for mapping an outer surface of the detection
subject to produce mapping data. The detection information can be
used to adjust the size of the air ring 400. For example, the
detection information may be used to keep a consistent distance
between the air ring 400 and the body while traveling from head to
toe. A computerized process may be used to link the detection
result of the sensors 420 via computer control to the
circumferential length adjusting devices 440 to change the size of
the air ring 400 to keep the distance between the air ring 400 and
the body consistent (e.g., within a preset distance range of
several inches or the like). This is one example mechanism or means
for adjusting the circumferential length of the circumferential
ring tubing, based on the mapping data, to keep a distance between
the circumferential ring tubing and the outer surface of the
detection subject to within a preset distance range. Other
mechanisms, which may be mechanical or of some other type, can be
used in other embodiments.
[0036] FIG. 4 shows four pneumatic devices 410, four sensors 420,
and four circumferential length adjusting devices 440, which may be
distributed evenly along the circumferential length of the air ring
400. More or fewer pneumatic devices 410, sensors 420, and
circumferential length adjusting devices 440 may be used. The
number of sensors 420 and the number of circumferential length
adjusting devices 440 may be different from one another in some
embodiments.
[0037] A plurality of air blowers or nozzles 430 are distributed
along the circumferential length of the air ring 400 for blowing
air inwardly toward the interior of the sample collection zone 450
and downwardly toward the bottom of the sample collection zone 450
such as the platform 330. To guide up and down movements of the
pneumatic ring 400, the stanchions 320 of FIG. 3 may be provided
between the base or platform 330 and the top of the enclosure 404.
The stanchions 320 may be fixed at the top and/or the bottom but
have sufficient lateral flexibility or compliance to accommodate
the shrinking and expansion of the air ring 400 as it slides up and
down the sample collection zone 450.
[0038] FIG. 5 is a block diagram of an example of a control system
of the sample collection apparatus according to an embodiment.
These may include control of the translational movement of the air
ring tubing 400 using the translational movement actuators 370,
control of the circumferential length adjustment of the air ring
tubing 400 using the circumferential length adjusting devices 440,
control of the nozzle angle of the nozzles 430 by rotating the
nozzles 430, and control of the air flow through the air nozzles
430 on the air ring tubing 400 using the pneumatic devices 410.
[0039] The translational movement actuators 370 may be controlled
by one or more translational movement controllers 570, which may be
disposed on the air ring 400 or the stanchions 320, or connected to
the translational movement actuators 370 from a remote location.
The controllers 570 may be separate from or integrally constructed
with the translational movement actuators 370, to control
translational movement of the air ring 400 along the stanchions
320. The control may involve moving the air ring 400 to an initial
position at the top ring position for a current sample collection
cycle, controlling the speed of descent from the top ring position,
moving the air ring 400 to a final position at the bottom ring
position, and returning the air ring 400 to the top ring position
for the next sample collection cycle. The control may be manually
set by the operator or automatically set by a computer, or a
combination of both.
[0040] The circumferential length adjusting devices 440 may be
controlled by one or more circumferential length adjusting
controllers 540, which may be disposed on the air ring 400 or
connected to the circumferential length adjusting devices 440 from
a remote location. The controllers 540 may be separate from or
integrally constructed with the circumferential length adjusting
devices 440, to control circumferential length adjustment of the
air ring 400 to change the circumferential size of the air ring
400, for example, to maintain the distance between the air ring 400
and the body of the detection subject to within a preset distance
range. The controllers 540 may control the circumferential length
adjusting devices 440 to change the circumferential size of the air
ring 400, locally or remotely by an operator and/or a computer,
based on operator input and/or sensor input of the sensors 420. The
control may be manually set by the operator or automatically set by
a computer, or a combination of both.
[0041] The nozzle angles of the nozzles 430 may be controlled by
one or more nozzle controllers 530 to orient the nozzles 430 at
specified angles toward the detection subject. The nozzle
controllers 530 may be disposed on the air ring 400 or connected to
the nozzles 430 from a remote location, to control the nozzle
angles locally or remotely by an operator and/or a computer, based
on operator input and/or vertical or translational position of the
air ring 400 (e.g., in coordination with the translational movement
controllers 570).
[0042] The pneumatic devices 410 may be controlled by one or more
pneumatic controllers 510 for blowing air through the air nozzles
430 toward the sample collection zone 450. The pneumatic
controllers 510 may be disposed on the air ring 400 or connected to
the pneumatic devices 410 from a remote location. The controllers
510 may be separate from or integrally constructed with the
pneumatic devices 410, to control the air flow through the air
nozzles 430, locally or remotely by an operator and/or a computer.
The pneumatic devices 410 may be activated only when the air ring
400 is moved from the top ring position or top ring tubing position
to the bottom ring position or bottom ring tubing position.
[0043] The pneumatic controllers 510, circumferential length
adjusting controllers 540, nozzle angle controllers 530, and
translational movement controllers 570 can operate independently or
they may be under a single master controller 590 to coordinate the
controls. The master controller 590 may include a computer
processor programmed to provide computer control with or without
operator input via a user interface and with or without sensor
input from position sensors, pneumatic sensors, mapping sensors,
and the like.
[0044] FIG. 6 is a flow diagram illustrating an example of a sample
collection process 600. Step 610 involves placing a circumferential
ring tubing 400 at or near an initiation end of the detection
subject (e.g., at or above a top of the detection subject), the
circumferential ring tubing surrounding a sample collection zone in
an interior. Step 620 involves moving the circumferential ring
tubing 400 translationally from a ring tubing initiation position
to a ring tubing collection position (e.g., vertically from a top
ring tubing position to a bottom ring tubing position in the
examples of FIGS. 2 and 3) around the detection subject in the
sample collection zone.
[0045] Steps 630 to 660 may be performed during step 620 of moving
the circumferential ring tubing 400 from top to bottom. In step
630, air is blown through air nozzles 430 along a circumferential
length of the circumferential ring tubing 400 to direct air flow
toward the detection subject as the circumferential ring tubing 400
is moved from the ring tubing initiation position to the ring
tubing collection position, to push a sample of the detection
subject via an air flow forward toward a platform 330. In step 640,
the air nozzles are oriented for blowing air inwardly toward the
detection subject and forward toward the platform 330. Step 650
involves detecting the shape and size of the detection subject,
using sensors 420 disposed on the ring tubing 400, to produce
detection data. In step 660, the circumferential length of the
circumferential ring tubing 400 is adjusted based on the detection
data to change the size of the circumferential ring tubing 400, for
example, to maintain the distance between the ring tubing 400 and
the body of the detection subject to within a preset distance
range.
[0046] Step 670 involves collecting the sample of the detection
subject carried by the air flow in a receptacle 340 disposed beyond
or adjacent the platform 330 through collection openings. In step
680, the air flow of the sample is directed from the receptacle 340
through a channel 350 connected to the receptacle through an outlet
360 to a sample analysis location.
[0047] The sample collection apparatus benefits screening because
it collects particles as well as vapor. The design is based on
large molecular weights of explosives with respect to air (e.g., up
to an order of magnitude larger or more) and the deficit of
available sample. Features such as the number of nozzles, air flow
rates, and design of the collection receptors and sample receptacle
at the bottom may be determined or selected for optimization.
Additional features include compressed air connections, doors, and
slides. The sample collection zone or passenger portal may be open,
partially enclosed, or completely enclosed.
[0048] The detection subject is a stationary target. The directed
air flow drives the vapor and/or particles of the subject from the
stationary target to an outlet where the canine is positioned which
is generally a stationary position. It is relatively easy to
achieve appropriate positioning of the canine in the stationary
system to maximize the air flow and scents that the canine is able
to analyze. The canine does not need to move around in an open
space to follow the subject being detected and choke points and
crowds are of no concern.
[0049] Unlike the nonstationary or mobile environment in which fans
are used to generate air currents which assist the canine in
detecting explosive odor, the stationary environment (especially if
the subject is enclosed) provides better and more reliable control
of the air flow by eliminating variables of fan placement, crowd
interference, other crowd or mobile effects, and the like. It also
eliminates the need for special training of canine to perform vapor
wake screening such as that described in U.S. Pat. No.
10,213,509.
[0050] In one example, the ring of nozzles maintains a constant
lateral position (e.g., constant diameter of a circle) as it moves
from the top ring position to the bottom ring position. In another
embodiment, the ring of nozzles has an adjustable lateral position
(e.g., varying diameter) to keep the nozzles in close proximity
within a preset distance range of the detection subject (i.e.,
moving inwardly to form a smaller ring around the head, moving
outwardly to form a larger ring around the shoulder and the core
and the hip, and moving inwardly to form a smaller ring around the
legs).
[0051] In one embodiment, the detection is performed by a dog which
is used as a sniffing or scent detection mechanism. In another
embodiment, the detection is performed by another kind of animal
with a superior sense of smell such as rodents and other mammals
for scent detection.
[0052] FIG. 7 illustrates a computing system 700 including logic
according to an embodiment. The computing system 700 includes a
processing system 710 having a hardware processor 725 configured to
perform a predefined set of basic operations 730 by loading
corresponding ones of a predefined native instruction set of codes
735 as stored in the memory 715. The computing system 700 further
includes input/output 720 having user interface 750, display unit
755, communication unit 760, and storage 765. The computing system
700 can be used to implement some or all of the processes or
operations of the controllers (510, 530, 540, and 570) in FIG.
5.
[0053] The memory 715 is accessible to the processing system 710
via the bus 770. The memory 715 includes the predefined native
instruction set of codes 735, which constitute a set of
instructions 740 selectable for execution by the hardware processor
725. In an embodiment, the set of instructions 740 include logic
745 representing various processor logic and/or modules. An example
of such logic 745 is set forth in greater detail with respect to
the flow diagram illustrated in FIG. 1. Each of the above-mentioned
algorithms (e.g., MMWI, neutron imaging, and other detection
algorithms and other imaging algorithms) can be a separate system
or a module in an overall computer system 700. The various logic
745 is stored in the memory 715 and comprises instructions 740
selected from the predefined native instruction set of codes 735 of
the hardware processor 725, adapted to operate with the processing
system 710 to implement the process or processes of the
corresponding logic 745.
[0054] A hardware processor may be thought of as a complex
electrical circuit that is configured to perform a predefined set
of basic operations in response to receiving a corresponding basic
instruction selected from a predefined native instruction set of
codes. The predefined native instruction set of codes is specific
to the hardware processor; the design of the processor defines the
collection of basic instructions to which the processor will
respond, and this collection forms the predefined native
instruction set of codes. A basic instruction may be represented
numerically as a series of binary values, in which case it may be
referred to as a machine code. The series of binary values may be
represented electrically, as inputs to the hardware processor, via
electrical connections, using voltages that represent either a
binary zero or a binary one. These voltages are interpreted as such
by the hardware processor. Executable program code may therefore be
understood to be a set of machine codes selected from the
predefined native instruction set of codes. A given set of machine
codes may be understood, generally, to constitute a module. A set
of one or more modules may be understood to constitute an
application program or "app." An app may interact with the hardware
processor directly or indirectly via an operating system. An app
may be part of an operating system.
[0055] A computer program product is an article of manufacture that
has a computer-readable medium with executable program code that is
adapted to enable a processing system to perform various operations
and actions. Non-transitory computer-readable media may be
understood as a storage for the executable program code. Whereas a
transitory computer-readable medium holds executable program code
on the move, a non-transitory computer-readable medium is meant to
hold executable program code at rest. Non-transitory
computer-readable media may hold the software in its entirety, and
for longer duration, compared to transitory computer-readable media
that holds only a portion of the software and for a relatively
short time. The term, "non-transitory computer-readable medium,"
specifically excludes communication signals such as radio frequency
signals in transit. The following forms of storage exemplify
non-transitory computer-readable media: removable storage such as a
USB disk, a USB stick, a flash disk, a flash drive, a thumb drive,
an external SSD, a compact flash card, an SD card, a diskette, a
tape, a compact disc, an optical disc; secondary storage such as an
internal hard drive, an internal SSD, internal flash memory,
internal non-volatile memory, internal DRAM, ROM, RAM, and the
like; and the primary storage of a computer system.
[0056] Different terms may be used to express the relationship
between executable program code and non-transitory
computer-readable media. Executable program code may be written on
a disc, embodied in an application-specific integrated circuit,
stored in a memory chip, or loaded in a cache memory, for example.
Herein, the executable program code may be said, generally, to be
"in" or "on" a computer-readable media. Conversely, the
computer-readable media may be said to store, to include, to hold,
or to have the executable program code.
[0057] The inventive concepts taught by way of the examples
discussed above are amenable to modification, rearrangement, and
embodiment in several ways. For example, this invention may be
applicable for collecting samples from inanimate objects as well as
live detection subjects. Moreover, the sample analysis may involve
types of analysis other than scent detection using animals. For
example, a piece of illicit material detection equipment such as an
explosive trace detector (ETD) may be used to analyze the collected
sample in the sample analysis area or location. Accordingly,
although the present disclosure has been described with reference
to specific embodiments and examples, persons skilled in the art
will recognize that changes may be made in form and detail without
departing from the spirit and scope of the disclosure.
[0058] Certain attributes, functions, steps of methods, or
sub-steps of methods described herein may be associated with
physical structures or components, such as a module of a physical
device that, in implementations in accordance with this disclosure,
make use of instructions (e.g., computer executable instructions)
that are embodied in hardware, such as an application specific
integrated circuit, or that may cause a computer (e.g., a
general-purpose computer) executing the instructions to have
defined characteristics. There may be a combination of hardware and
software such as processor implementing firmware, software, and so
forth so as to function as a special purpose computer with the
ascribed characteristics. For example, in embodiments a module may
comprise a functional hardware unit (such as a self-contained
hardware or software or a combination thereof) designed to
interface the other components of a system such as through use of
an API. In embodiments, a module is structured to perform a
function or set of functions, such as in accordance with a
described algorithm. This disclosure may use nomenclature that
associates a component or module with a function, purpose, step, or
sub-step to identify the corresponding structure which, in
instances, includes hardware and/or software that function for a
specific purpose. For any computer-implemented embodiment, "means
plus function" elements will use the term "means;" the terms
"logic" and "module" and the like have the meaning ascribed to them
above, if any, and are not to be construed as means.
[0059] The claims define the invention and form part of the
specification. Limitations from the written description are not to
be read into the claims.
[0060] An interpretation under 35 U.S.C. .sctn. 112(f) is desired
only where this description and/or the claims use specific
terminology historically recognized to invoke the benefit of
interpretation, such as "means," and the structure corresponding to
a recited function, to include the equivalents thereof, as
permitted to the fullest extent of the law and this written
description, may include the disclosure, the accompanying claims,
and the drawings, as they would be understood by one of skill in
the art.
[0061] To the extent the subject matter has been described in
language specific to structural features and/or methodological
steps, it is to be understood that the subject matter defined in
the appended claims is not necessarily limited to the specific
features or steps described. Rather, the specific features and
steps are disclosed as example forms of implementing the claimed
subject matter. To the extent headings are used, they are provided
for the convenience of the reader and are not be taken as limiting
or restricting the systems, techniques, approaches, methods,
devices to those appearing in any section. Rather, the teachings
and disclosures herein can be combined, rearranged, with other
portions of this disclosure and the knowledge of one of ordinary
skill in the art. It is the intention of this disclosure to
encompass and include such variation. The indication of any
elements or steps as "optional" does not indicate that all other or
any other elements or steps are mandatory.
* * * * *