U.S. patent application number 17/421086 was filed with the patent office on 2022-04-21 for construction machine control system and construction machine control method.
This patent application is currently assigned to Komatsu Ltd.. The applicant listed for this patent is Komatsu Ltd.. Invention is credited to Toru Matsuyama.
Application Number | 20220120059 17/421086 |
Document ID | / |
Family ID | |
Filed Date | 2022-04-21 |
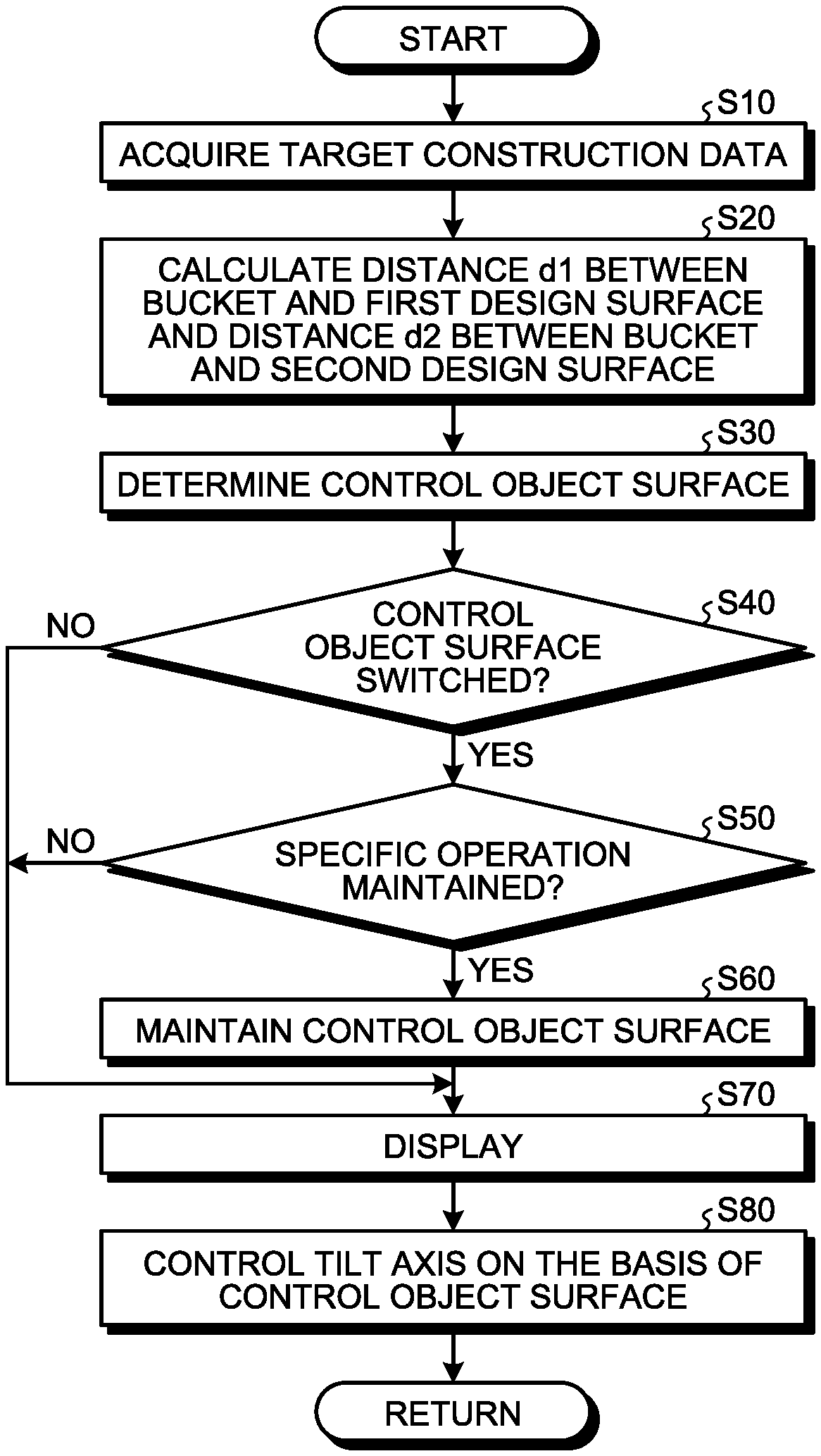










View All Diagrams
United States Patent
Application |
20220120059 |
Kind Code |
A1 |
Matsuyama; Toru |
April 21, 2022 |
CONSTRUCTION MACHINE CONTROL SYSTEM AND CONSTRUCTION MACHINE
CONTROL METHOD
Abstract
A control system of a construction machine comprises: a
determination unit that determines a control object surface from a
first design surface and a second design surface adjacent to the
first design surface on the basis of a distance between a tilt
bucket and the first design surface and a distance between the tilt
bucket and the second design surface; a working equipment control
unit that controls a tilt axis of the tilt bucket on the basis of
the control object surface determined by the determination unit;
and a display control unit that causes a display device to use
different display modes to display the control object surface and a
surface other than the control object surface.
Inventors: |
Matsuyama; Toru; (Tokyo,
JP) |
|
Applicant: |
Name |
City |
State |
Country |
Type |
Komatsu Ltd. |
Tokyo |
|
JP |
|
|
Assignee: |
Komatsu Ltd.
Tokyo
JP
|
Appl. No.: |
17/421086 |
Filed: |
January 9, 2020 |
PCT Filed: |
January 9, 2020 |
PCT NO: |
PCT/JP2020/000524 |
371 Date: |
July 7, 2021 |
International
Class: |
E02F 9/26 20060101
E02F009/26; E02F 3/43 20060101 E02F003/43 |
Foreign Application Data
Date |
Code |
Application Number |
Jan 31, 2019 |
JP |
2019-016477 |
Claims
1. A control system of a construction machine provided with working
equipment which includes an arm and a tilt bucket, the control
system comprising: a determination unit that determines a control
object surface from a first design surface and a second design
surface adjacent to the first design surface on the basis of a
distance between the tilt bucket and the first design surface and a
distance between the tilt bucket and the second design surface; a
working equipment control unit that controls a tilt axis of the
tilt bucket on the basis of the control object surface determined
by the determination unit; and a display control unit that causes a
display device to use different display modes to display the
control object surface and a surface other than the control object
surface.
2. The control system of the construction machine according to
claim 1, the control system comprising: an input data acquisition
unit that acquires input data generated through an operation of an
input device, wherein the determination unit determines the control
object surface from the first design surface and the second design
surface on the basis of the input data.
3. The control system of the construction machine according to
claim 1, the control system comprising: an operating data
acquisition unit that acquires operating data generated through an
operation of an operating device that operates at least part of the
construction machine, wherein the working equipment control unit
determines, on the basis of the operating data, whether or not a
specific operation is maintained and, during a period in which the
specific operation is maintained, controls the tilt axis in a state
where the control object surface is maintained.
4. The control system of the construction machine according to
claim 3, wherein the specific operation includes an operation to
drive the arm.
5. The control system of the construction machine according to
claim 4, wherein the specific operation includes an operation to
drive a traveling body of the construction machine.
6. The control system of the construction machine according to
claim 3, wherein the determination unit determines, as the control
object surface, one of the first design surface and the second
design surface, which has a shorter distance from the tilt bucket,
and wherein, in a case where the control object surface is
determined as being the first design surface, the working equipment
control unit controls the tilt axis in a state of maintaining the
control object surface as the first design surface during the
period in which the specific operation is maintained, even when the
one which is the shorter distance from the tilt bucket changes from
the first design surface to the second design surface.
7. A control method of a construction machine provided with working
equipment which includes an arm and a tilt bucket, the control
method comprising: determining a control object surface from a
first design surface and a second design surface adjacent to the
first design surface on the basis of a distance between the tilt
bucket and the first design surface and a distance between the tilt
bucket and the second design surface; controlling a tilt axis of
the tilt bucket on the basis of the determined control object
surface; and causing a display device to use different display
modes to display the control object surface and a surface other
than the control object surface.
8. A control method of a construction machine provided with working
equipment which includes an arm and a tilt bucket, the control
method comprising: acquiring input data generated through an
operation of an input device; determining a control object surface
from a first design surface and a second design surface adjacent to
the first design surface on the basis of the input data; and
controlling a tilt axis of the tilt bucket on the basis of the
determined control object surface.
Description
FIELD
[0001] The present invention relates to a construction machine
control system and a construction machine control method.
BACKGROUND
[0002] In technological fields pertaining to construction machines,
construction machine control systems like that disclosed in Patent
Literature 1, which control a tilt bucket on the basis of a target
construction data representing a target shape for a construction
object, are known.
CITATION LIST
Patent Literature
[0003] Patent Literature 1: Japanese Patent Publication No.
6046320
SUMMARY
Technical Problem
[0004] The target construction data sometimes include a first
design surface and a second design surface adjacent to the first
design surface. When the tilt bucket is controlled so as to track
the first design surface, the driver of the construction machine
must operate an operating device for driving working equipment to
bring the tilt bucket close to the first design surface. When it
takes time to bring the tilt bucket close to the first design
surface, work efficiency may be reduced.
[0005] An object of an aspect of the present invention is to
suppress a reduction in the work efficiency of a construction
machine having a tilt bucket.
Solution to Problem
[0006] According to an aspect of the present invention, a control
system of a construction machine provided with working equipment
which includes an arm and a tilt bucket, the control system
comprises: a determination unit that determines a control object
surface from a first design surface and a second design surface
adjacent to the first design surface on the basis of a distance
between the tilt bucket and the first design surface and a distance
between the tilt bucket and the second design surface; a working
equipment control unit that controls a tilt axis of the tilt bucket
on the basis of the control object surface determined by the
determination unit; and a display control unit that causes a
display device to use different display modes to display the
control object surface and a surface other than the control object
surface.
Advantageous Effects of Invention
[0007] According to an embodiment of the present invention, a
reduction in the work efficiency of a construction machine having a
tilt bucket can be suppressed.
BRIEF DESCRIPTION OF DRAWINGS
[0008] FIG. 1 is a perspective view of an example of a construction
machine according to a first embodiment.
[0009] FIG. 2 is a block diagram illustrating an example of a
construction machine control system according to the first
embodiment.
[0010] FIG. 3 is a diagram schematically illustrating a
construction machine according to the first embodiment.
[0011] FIG. 4 is a diagram schematically illustrating a bucket
according to the first embodiment.
[0012] FIG. 5 is a function block diagram illustrating an example
of a control device according to the first embodiment.
[0013] FIG. 6 is a schematic diagram to illustrate an example of
processing by a determination unit according to the first
embodiment.
[0014] FIG. 7 is a flowchart illustrating an example of a
construction machine control method according to the first
embodiment.
[0015] FIG. 8 is a plan view to illustrate an example of the
operation of the construction machine according to the first
embodiment.
[0016] FIG. 9 is a perspective view to illustrate an example of the
operation of the construction machine according to the first
embodiment.
[0017] FIG. 10 is a schematic diagram to illustrate an example of
the operation of the construction machine according to the first
embodiment.
[0018] FIG. 11 is a schematic diagram illustrating an example of
the display of a display device according to the first
embodiment.
[0019] FIG. 12 is a flowchart illustrating an example of a
construction machine control method according to a second
embodiment.
[0020] FIG. 13 is a block diagram illustrating an example of a
computer system according to the embodiment.
DESCRIPTION OF EMBODIMENTS
[0021] Although embodiments of the present invention are described
hereinbelow with reference to the drawings, the present invention
is not limited to or by such embodiments. Constituent elements of
the embodiments described hereinbelow can be suitably combined.
Moreover, some of the constituent elements may also not be
used.
[0022] In the description hereinbelow, the positional relationships
between the parts are described by defining a three-dimensional
vehicle-body coordinate system (X, Y, Z). The vehicle-body
coordinate system refers to a coordinate system based on an origin
which is fixed to the construction machine. The vehicle-body
coordinate system is defined by an X axis that extends in a defined
direction with reference to an origin which is set to the
construction machine, a Y axis which orthogonally intersects the X
axis, and a Z axis which orthogonally intersects the X axis and the
Y axis, respectively. A direction parallel to the X axis is taken
to be an X-axis direction. A direction parallel to the Y axis is
taken to be a Y-axis direction. A direction parallel to the Z axis
is taken to be a Z-axis direction. A direction of rotation or
inclination about the X axis is taken to be a .theta.X direction. A
direction of rotation or inclination about the Y axis is taken to
be a .theta.Y direction. A direction of rotation or inclination
about the Z axis is taken to be a .theta.Z direction.
First Embodiment
[0023] FIG. 1 is a perspective view of an example of a construction
machine 100 according to this embodiment. In this embodiment, an
example in which the construction machine 100 is an excavator is
described. In the description hereinbelow, the construction machine
100 is, where appropriate, referred to as the excavator 100.
[0024] As illustrated in FIG. 1, the excavator 100 is provided with
working equipment 1 that is hydraulically operated; a swing body 2
that supports the working equipment 1; and a traveling body 3 that
supports the swing body 2. The swing body 2 has a driver cabin 4 in
which a driver rides. A seat 4S on which the driver sits is
disposed in the driver cabin 4. The swing body 2 is capable of
swinging about a swing axis RX so as to be supported by the
traveling body 3.
[0025] The traveling body 3 has a pair of crawler tracks 3C. The
excavator 100 travels due to the rotation of the crawler tracks 3C.
Note that the traveling body 3 may also have tires.
[0026] The working equipment 1 is supported on the swing body 2.
The working equipment 1 has a boom 6 connected to the swing body 2,
an arm 7 connected to the distal end of the boom 6, and a bucket 8
connected to the distal end of the arm 7. The bucket 8 has a blade
edge 9. In this embodiment, the blade edge 9 of the bucket 8 is the
distal end of a straight-shaped blade. Note that the blade edge 9
of the bucket 8 may also be the distal end of a convex-shaped blade
provided to the bucket 8.
[0027] The boom 6 is rotatable with respect to the swing body 2
about a boom axis AX1. The arm 7 is rotatable with respect to the
boom 6 about an arm axis AX2. In this embodiment, the bucket 8 is a
tilt bucket. The bucket 8 is rotatable with respect to the arm 7
about a bucket axis AX3 and a tilt axis AX4, respectively. The boom
axis AX1, the arm axis AX2, and the bucket axis AX3 run parallel to
the Y axis. The tilt axis AX4 orthogonally intersects the bucket
axis AX3. The swing axis RX runs parallel to the Z axis. The X-axis
direction is a front-back direction of the swing body 2. The Y-axis
direction is a vehicle-width direction of the swing body 2. The
Z-axis direction is an up-down direction of the swing body 2. The
direction in which the working equipment 1 exists is a forward
direction with reference to the driver sitting on the seat 4S.
Control System
[0028] FIG. 2 is a block diagram illustrating an example of a
control system 200 of an excavator 100 according to this
embodiment. FIG. 3 is a diagram schematically illustrating the
excavator 100 according to this embodiment. FIG. 4 is a diagram
schematically illustrating the bucket 8 according to this
embodiment.
[0029] As illustrated in FIG. 2, the control system 200 of the
excavator 100 is provided with: an engine 5; a plurality of
hydraulic cylinders 10 that drive the working equipment 1; a swing
motor 16 that drives the swing body 2; a travel motor 15 that
drives the traveling body 3; a hydraulic pump 17 that discharges
hydraulic fluid; a valve device 18 that distributes the hydraulic
fluid discharged from the hydraulic pump 17 to the plurality of
hydraulic cylinders 10, the travel motor 15, and the swing motor
16, respectively; a vehicle-body position calculation device 20
that calculates position data of the swing body 2; an angle
detection device 30 that detects an angle .theta. of the working
equipment 1; an operating device 40 that operates at least part of
the excavator 100; a control device 50; a display device 80; and an
input device 90.
[0030] The working equipment 1 operates due to the motive power
generated by the hydraulic cylinders 10. The hydraulic cylinders 10
perform driving on the basis of the hydraulic fluid supplied from
the hydraulic pump 17. The hydraulic cylinders 10 include a boom
cylinder 11 that causes the boom 6 to operate, an arm cylinder 12
that causes the arm 7 to operate, and a bucket cylinder 13 and a
tilt cylinder 14 that cause the bucket 8 to operate. The boom
cylinder 11 generates motive power that causes the boom 6 to rotate
about the boom axis AX1. The arm cylinder 12 generates motive power
that causes the arm 7 to rotate about the arm axis AX2. The bucket
cylinder 13 generates motive power that causes the bucket 8 to
rotate about the bucket axis AX3. The tilt cylinder 14 generates
motive power that causes the bucket 8 to rotate about the tilt axis
AX4.
[0031] In the description hereinbelow, the rotation of the bucket 8
about the bucket axis AX3 is suitably called bucket rotation, and
the rotation of the bucket 8 about the tilt axis AX4 is suitably
called tilt rotation.
[0032] The swing body 2 swings due to the motive power generated by
the swing motor 16. The swing motor 16 is a hydraulic motor and
performs driving on the basis of the hydraulic fluid supplied from
the hydraulic pump 17. The swing motor 16 generates motive power
that causes the swing body 2 to swing about the swing axis RX.
[0033] The traveling body 3 travels due to the motive power
generated by the travel motor 15. The travel motor 15 is a
hydraulic motor and performs driving on the basis of the hydraulic
fluid supplied from the hydraulic pump 17. The travel motor 15
generates motive power that causes the traveling body 3 to advance
and retreat.
[0034] The engine 5 is mounted in the swing body 2. The engine 5
generates motive power for driving the hydraulic pump 17.
[0035] The hydraulic pump 17 discharges hydraulic fluid for driving
the hydraulic cylinders 10, the swing motor 16, and the travel
motor 15.
[0036] The valve device 18 has a plurality of valves that
distribute the hydraulic fluid supplied from the hydraulic pump 17
to the plurality of hydraulic cylinders 10, the swing motor 16, and
the travel motor 15. The valve device 18 adjusts the flow rate of
the hydraulic fluid supplied to each of the plurality of hydraulic
cylinders 10. The operating speed of the working equipment 1 is
adjusted by adjusting the flow rate of the hydraulic fluid supplied
to the hydraulic cylinders 10. The valve device 18 adjusts the flow
rate of the hydraulic fluid supplied to the swing motor 16. The
swing speed of the swing body 2 is adjusted by adjusting the flow
rate of the hydraulic fluid supplied to the swing motor 16. The
valve device 18 adjusts the flow rate of the hydraulic fluid
supplied to the travel motor 15. The travel speed of the traveling
body 3 is adjusted by adjusting the flow rate of the hydraulic
fluid supplied to the travel motor 15.
[0037] The vehicle-body position calculation device 20 calculates
position data of the swing body 2. The position data of the swing
body 2 includes the position of the swing body 2, the attitude of
the swing body 2, and the orientation of the swing body 2. The
vehicle-body position calculation device 20 has a position
calculator 21 that calculates the position of the swing body 2, an
attitude calculator 22 that calculates the attitude of the swing
body 2, and an orientation calculator 23 that calculates the
orientation of the swing body 2.
[0038] The position calculator 21 calculates, as the position of
the swing body 2, the position of the swing body 2 in a global
coordinate system. The position calculator 21 is disposed on the
swing body 2. The global coordinate system denotes a coordinate
system with reference to an origin which is fixed to the earth. The
global coordinate system is a coordinate system defined by a global
navigation satellite system (GNSS). GNSS refers to a global
navigation satellite system. An example of a global navigation
satellite system is a global positioning system (GPS). A GNSS has a
plurality of positioning satellites. A GNSS detects positions
defined by latitude, longitude, and altitude coordinate data. A GPS
antenna is provided to the swing body 2. The GPS antenna receives
radio waves from GPS satellites and outputs, to the position
calculator 21, a signal generated on the basis of the received
radio waves. The position calculator 21 calculates the position of
the swing body 2 in the global coordinate system on the basis of
the signal supplied from the GPS antenna. The position calculator
21 calculates the position of a representative point O of the swing
body 2 as illustrated in FIG. 3, for example. In the example
illustrated in FIG. 3, the representative point O of the swing body
2 is set on the swing axis RX. Note that the representative point O
may also be set on the boom axis AX1.
[0039] The attitude calculator 22 calculates, as the attitude of
the swing body 2, angles of inclination of the swing body 2
relative to the horizontal plane in the global coordinate system.
The attitude calculator 22 is disposed on the swing body 2. The
attitude calculator 22 includes an inertial measurement unit (IMU).
The angles of inclination of the swing body 2 relative to the
horizontal plane include a roll angle .alpha. representing the
angle of inclination of the swing body 2 in the vehicle-width
direction, and a pitch angle .beta. representing the angle of
inclination of the swing body 2 in the front-back direction.
[0040] The orientation calculator 23 calculates, as the orientation
of the swing body 2, the orientation of the swing body 2 relative
to a reference orientation in the global coordinate system. The
reference orientation is north, for example. The orientation
calculator 23 is disposed on the swing body 2. The orientation
calculator 23 includes a gyro sensor. Note that the orientation
calculator 23 may also calculate the orientation on the basis of
the signal supplied from the GPS antenna. The orientation of the
swing body 2 relative to the reference orientation includes a yaw
angle .gamma. representing the angle formed between the orientation
of the swing body 2 and the reference orientation.
[0041] The angle detection device 30 detects the angle .theta. of
the working equipment 1. The angle detection device 30 is disposed
on the working equipment 1. As illustrated in FIGS. 3 and 4, the
angle .theta. of the working equipment 1 includes a boom angle
.theta.1 representing the angle of the boom 6 relative to the Z
axis, an arm angle .theta.2 representing the angle of the arm 7
relative to the boom 6, a bucket angle .theta.3 representing the
angle of the bucket 8 in the bucket rotation direction relative to
the arm 7, and a tilt angle .theta.4 representing the angle of the
bucket 8 in the tilt-rotation direction relative to a plane XY.
[0042] The angle detection device 30 has a boom angle detector 31
that detects the boom angle .theta.1, an arm angle detector 32 that
detects the arm angle .theta.2, a bucket angle detector 33 that
detects the bucket angle .theta.3, and a tilt angle detector 34
that detects the tilt angle .theta.4. The angle detection device 30
may include a stroke sensor that detects the strokes of the
hydraulic cylinders 10 or may include an angle sensor that detects
the angle .theta. of the working equipment 1 such as a rotary
encoder. When the angle detection device 30 includes a stroke
sensor, the angle detection device 30 calculates the angle .theta.
of the working equipment 1 on the basis of detection data of the
stroke sensor.
[0043] The operating device 40 is operated by the driver in order
to drive the hydraulic cylinders 10, the swing motor 16, and the
travel motor 15. The operating device 40 is disposed in the driver
cabin 4. The working equipment 1 is operated due to the driver
operating the operating device 40. The operating device 40 includes
levers which are operated by the driver of the excavator 100. The
levers of the operating device 40 include a right-operation lever
41, a left-operation lever 42, and a tilt-operation lever 43.
[0044] When the right-operation lever 41, which is in a neutral
position, is maneuvered forward, the boom 6 is lowered, and when
maneuvered backward, the boom 6 is raised. When the right-operation
lever 41, which is in a neutral position, is maneuvered rightward,
the bucket 8 performs a dumping operation, and when maneuvered
leftward, the bucket 8 performs an excavation operation.
[0045] When the left-operation lever 42, which is in a neutral
position, is maneuvered forward, the arm 7 performs a dumping
operation, and when maneuvered backward, the arm 7 performs an
excavation operation. When the left-operation lever 42, which is in
a neutral position, is maneuvered rightward, the swing body 2
swings rightward, and when maneuvered leftward, the swing body 2
swings leftward.
[0046] When the tilt-operation lever 43 is operated, the bucket 8
undergoes tilt rotation.
[0047] The operating device 40 also includes a travel lever (not
illustrated). Operating the travel lever causes the traveling body
3 to switch between advancing and retreating. The travel speed of
the traveling body 3 is adjusted by operating the travel lever.
[0048] The display device 80 displays display data. The display
device 80 is disposed in the driver cabin 4. Examples of the
display device 80 include a flat-panel display such as a liquid
crystal display (LCD) or an organic EL (electroluminescence)
display (OLED).
[0049] The input device 90 is operated by the driver to input input
data to the control device 50. The input device 90 is disposed in
the driver cabin 4. Examples of the input device 90 are
contact-type input devices which are operated manually by the
driver such as a computer keyboard, a mouse, a touch panel, an
operating switch, and an operating button. Note that the input
device 90 may also be a speech input device which is operated via
the speech of an administrator.
Control Device
[0050] FIG. 5 is a function block diagram illustrating an example
of the control device 50 according to this embodiment. The control
device 50 has a vehicle-body position data acquisition unit 51, an
angle data acquisition unit 52, an operating data acquisition unit
53, an input data acquisition unit 54, a target construction data
acquisition unit 55, a bucket position data calculation unit 56, a
determination unit 57, a storage unit 60, a working equipment
control unit 61, and a display control unit 62.
[0051] The vehicle-body position data acquisition unit 51 acquires
position data of the swing body 2 from the vehicle-body position
calculation device 20. The position data of the swing body 2
includes the position of the swing body 2, the attitude of the
swing body 2, and the orientation of the swing body 2.
[0052] The angle data acquisition unit 52 acquires angle data
representing the angle .theta. of the working equipment 1 from the
angle detection device 30. The angle data of the working equipment
1 includes the boom angle .theta.1, the arm angle .theta.2, the
bucket angle .theta.3, and the tilt angle .theta.4.
[0053] The operating data acquisition unit 53 acquires operating
data which is generated through the operation of the operating
device 40. The operating data of the operating device 40 includes
the amount the operating device 40 is operated. An operation amount
sensor for detecting the amount the levers are operated is provided
to the operating device 40. The operating data acquisition unit 53
acquires the operating data of the operating device 40 from the
operation amount sensor of the operating device 40. The operating
data includes operating data generated in order to cause the
working equipment 1 to operate, operating data generated in order
to cause the swing body 2 to swing, and operating data generated in
order to cause the traveling body 3 to travel.
[0054] The input data acquisition unit 54 acquires input data which
is generated through the operation of the input device 90.
[0055] The target construction data acquisition unit 55 acquires
target construction data CS representing a target shape of a
construction object. The target construction data CS represents a
three-dimensional target shape after construction by the excavator
100. In this embodiment, the target construction data CS is defined
in a vehicle-body coordinate system. Note that the target
construction data CS may also be defined in a global coordinate
system. In this embodiment, the target construction data CS is
generated by a target construction data supply device 70. The
target construction data acquisition unit 55 acquires the target
construction data from the target construction data supply device
70. The target construction data supply device 70 may also be
provided in a remote location of the excavator 100. The target
construction data CS generated by the target construction data
supply device 70 may also be transmitted to the control device 50
via a communications system. Note that the target construction data
generated by the target construction data supply device 70 may also
be stored in the storage unit 60. The target construction data
acquisition unit 55 may also acquire the target construction data
CS from the storage unit 60. The target construction data CS is
defined in a vehicle-body coordinate system.
[0056] The bucket position data calculation unit 56 calculates
position data of a regulation point RP set in the bucket 8. The
bucket position data calculation unit 56 calculates the position
data of the regulation point RP set in the bucket 8 on the basis of
the position data of the swing body 2 acquired by the vehicle-body
position data acquisition unit 51, the angle data of the working
equipment 1 acquired by the angle data acquisition unit 52, and the
working equipment data stored in the storage unit 60.
[0057] As illustrated in FIGS. 3 and 4, the working equipment data
includes a boom length L1, an arm length L2, a bucket length L3, a
tilt length L4, and a bucket width L5. The boom length L1 is the
distance between the boom axis AX1 and the arm axis AX2. The arm
length L2 is the distance between the arm axis AX2 and the bucket
axis AX3. The bucket length L3 is the distance between the bucket
axis AX3 and the blade edge 9 of the bucket 8. The tilt length L4
is the distance between the bucket axis AX3 and the tilt axis AX4.
The bucket width L5 is the dimension of the bucket 8 in the width
direction thereof. The working equipment data includes bucket
outline data representing the shape and dimensions of the bucket 8.
The bucket outline data includes outline data of the bucket 8 which
includes the outer surface contour of the bucket 8. The bucket
outline data includes coordinate data of a plurality of regulation
points RP of the bucket 8 with reference to a predetermined part of
the bucket 8.
[0058] The bucket position data calculation unit 56 calculates the
respective relative positions of the plurality of regulation points
RP with respect to the representative point O of the swing body 2.
Furthermore, the bucket position data calculation unit 56
calculates the respective absolute positions of the plurality of
regulation points RP.
[0059] The bucket position data calculation unit 56 is capable of
calculating the respective relative positions of the plurality of
regulation points RP with respect to the representative point O on
the basis of: working equipment data including the boom length L1,
the arm length L2, the bucket length L3, the tilt length L4, and
the bucket outline data; and working equipment angle data including
the boom angle .theta.1, the arm angle .theta.2, the bucket angle
.theta.3, and the tilt angle .theta.4. As illustrated in FIG. 3,
the representative point O is set as the swing axis RX of the swing
body 2. Note that the representative point O may also be set on the
boom axis AX1.
[0060] The bucket position data calculation unit 56 is capable of
calculating the absolute position of the bucket 8 on the basis of
the absolute position of the swing body 2 calculated by the
vehicle-body position calculation device 20 and the relative
positions of the representative point O and the bucket 8. The
absolute position of the swing body 2 and the relative position
with respect to the representative point O are existing data
derived from various data of the excavator 100. The bucket position
data calculation unit 56 is capable of calculating the respective
absolute positions of the plurality of regulation points RP of the
bucket 8 on the basis of the position data including the absolute
position of the swing body 2, the relative positions of the
representative point O and the bucket 8, the working equipment
data, and the working equipment angle data.
[0061] The determination unit 57 determines a control object
surface Fc, which is to be used to control the bucket 8, from the
target construction data CS acquired by the target construction
data acquisition unit 55 and the position data of the regulation
points RP acquired by the bucket position data calculation unit
56.
[0062] FIG. 6 is a schematic diagram to illustrate an example of
processing by the determination unit 57 according to this
embodiment. As illustrated in FIG. 6, the target construction data
CS includes a plurality of design surfaces F. The design surfaces F
represent the target shape of the construction object.
[0063] The determination unit 57 determines the control object
surface Fc used to control the bucket 8 from the plurality of
design surfaces F of the target construction data CS. Furthermore,
the determination unit 57 determines a non-control object surface
Fn which is not used to control the bucket 8 from the plurality of
design surfaces F of the target construction data CS. In this
embodiment, control of the bucket 8 includes at least control of
the tilt axis AX4 of the bucket 8. Control of the tilt axis AX4 of
the bucket 8 includes control of at least one of the tilt angle
.theta.4 representing the angle (position) of the bucket 8 in the
tilt-rotation direction, the rotation speed of the bucket 8 in the
tilt-rotation direction, and the rotation acceleration of the
bucket 8 in the tilt-rotation direction.
[0064] Note that control of the bucket 8 may also include control
of the bucket axis AX3 of the bucket 8. The control of the bucket
axis AX3 of the bucket 8 includes control of at least one of the
bucket angle .theta.3 representing the angle (position) of the
bucket 8 in the bucket rotation direction, the rotation speed of
the bucket 8 in the bucket rotation direction, and the rotation
acceleration of the bucket 8 in the bucket rotation direction.
[0065] For the bucket 8, the tilt axis AX4 is controlled on the
basis of the control object surface Fc. The determination unit 57
determines the control object surface Fc used to control the tilt
axis AX4 of the bucket 8 from the plurality of design surfaces F of
the target construction data. Furthermore, the determination unit
57 determines the non-control object surface Fn, which is not used
to control the tilt axis of the bucket 8, from the plurality of
design surfaces F of the target construction data. Among the
plurality of design surfaces F of the target construction data CS,
the control object surface Fc which is used to control the tilt
axis AX4 of the bucket 8 is determined to be the design surface F
which is the shortest distance from the bucket 8. In this
embodiment, the target construction data CS including the plurality
of design surfaces F is defined in a vehicle-body coordinate
system. The position data of the bucket 8 (the regulation points
RP) is also defined in the vehicle-body coordinate system. The
determination unit 57 determines a point AP, among the target
construction data CS, which is the shortest distance (vertical
distance) from the bucket 8 calculated by the bucket position data
calculation unit 56. The determination unit 57 determines the
design surface F which contains point AP to be the control object
surface Fc which is the shortest distance from the bucket 8.
[0066] The non-control object surface Fn which is not used to
control the tilt axis AX4 of the bucket 8 is arranged at least
partially around the control object surface Fc. The control object
surface Fc and non-control object surface Fn are adjacent to one
another. The distance between the control object surface Fc and the
bucket 8 is shorter than the distance between the non-control
object surface Fn and the bucket 8.
[0067] Furthermore, the determination unit 57 determines a
working-equipment operation plane WP which passes through point AP
and the bucket 8 and which orthogonally intersects the bucket axis
AX3. The working-equipment operation plane WP is an operation plane
in which the bucket 8 moves due to the operation of at least one of
the boom cylinder 11, the arm cylinder 12, and the bucket cylinder
13, and is parallel to a plane XZ in the vehicle-body coordinate
system.
[0068] The determination unit 57 also determines a line LX which
represents an intersection between the working-equipment operation
plane WP and the target construction data CS. Furthermore, the
determination unit 57 determines a line LY which passes through
point AP and intersects line LX in the target construction data
CS.
[0069] The determination unit 57 determines whether or not the
control object surface Fc, which has been determined on the basis
of the target construction data CS acquired by the target
construction data acquisition unit 55 and the position data of the
regulation points RP acquired by the bucket position data
calculation unit 56, has switched from a previous control object
surface Fb. When the control object surface Fc is the same as the
previous control object surface Fb, the control object surface Fc
is maintained as the previous control object surface Fb.
[0070] When the control object surface Fc has switched from the
previous control object surface Fb, the determination unit 57
determines whether or not a specific operation of the working
equipment 1 is maintained on the basis of operating data acquired
by the operating data acquisition unit 53. When the specific
operation of the working equipment 1 is maintained, the control
object surface Fc is maintained as the previous control object
surface Fb. When the specific operation is not maintained, the
control object surface Fc is maintained on the basis of the target
construction data CS and the position data of the regulation points
RP.
[0071] The working equipment control unit 61 controls the tilt axis
AX4 of the bucket 8 such that the bucket 8 does not dig into the
design surfaces F, on the basis of the control object surface Fc
determined by the determination unit 57. Furthermore, the working
equipment control unit 61 controls the bucket axis AX3 of the
bucket 8 such that the bucket 8 does not dig into the design
surfaces F, on the basis of the control object surface Fc
determined by the determination unit 57. The working equipment
control unit 61 also controls the boom 6 such that the bucket 8
does not dig into the design surfaces F. In other words, the
working equipment control unit 61 executes control of the working
equipment 1 including at least control of the tilt axis AX4 such
that the bucket 8 tracks the control object surface Fc.
[0072] The working equipment control unit 61 causes the boom 6 and
the arm 7 to move along line LX and subjects the bucket 8 to bucket
rotation. The working equipment control unit 61 also subjects the
bucket 8 to tilt rotation along line LY. The working equipment
control unit 61 controls the tilt axis AX4 of the bucket 8 so as to
maintain the relative angle in the tilt-rotation direction between
the bucket 8 and line LY of the control object surface Fc.
[0073] The display control unit 62 causes the display device 80 to
display display data. The display control unit 62 causes the
display device 80 to generate a display such that the mode in which
the control object surface Fc determined by the determination unit
57 is displayed differs from that of surfaces other than the
control object surface Fc. The display control unit 62 causes the
display device 80 to generate a display such that the mode in which
the control object surface Fc determined by the determination unit
57 is displayed differs from that of the non-control object surface
Fn.
Control Method
[0074] FIG. 7 is a flowchart illustrating an example of a control
method of the excavator 100 according to this embodiment.
[0075] The target construction data acquisition unit 55 acquires
the target construction data CS (step S10).
[0076] The vehicle-body position data acquisition unit 51 acquires
position data of the swing body 2 from the vehicle-body position
calculation device 20. The angle data acquisition unit 52 acquires
angle data of the working equipment 1 from the angle detection
device 30. The bucket position data calculation unit 56 calculates
the position of the bucket 8 (the regulation points RP) on the
basis of the position data of the swing body 2, the angle data of
the working equipment 1, and the working equipment data stored in
the storage unit 60.
[0077] The target construction data CS includes the first design
surface F1 and the second design surface F2 adjacent to the first
design surface F1. The gradient of the first design surface F1 and
the gradient of the second design surface F2 differ from one
another. The determination unit 57 calculates a distance d1 between
the bucket 8 and the first design surface F1 and a distance d2
between the bucket 8 and the second design surface F2 on the basis
of the position data of the bucket 8 and the target construction
data CS (step S20).
[0078] In this embodiment, the distance d1 and distance d2 are
defined in a vehicle-body coordinate system. Note that the distance
d1 and distance d2 may also be defined in a global coordinate
system.
[0079] The determination unit 57 determines the control object
surface Fc from among the first design surface F1 and the second
design surface F2 on the basis of the distance d1 between the
bucket 8 and the first design surface F1 and the distance d2
between the bucket 8 and the second design surface F2 (step
S30).
[0080] In the description hereinbelow, by way of an example,
distance d1 is shorter than distance d2, the first design surface
F1 is determined as being control object surface Fc, and the second
design surface F2 adjacent to the first design surface F1 is
determined as being the non-control object surface Fn.
[0081] FIG. 8 is a plan view to illustrate an example of the
operation of the excavator 100 according to this embodiment. FIG. 9
is a perspective view to illustrate an example of the operation of
the excavator 100 according to this embodiment. As illustrated in
FIGS. 8 and 9, the driver operates the operating device 40 such
that the bucket 8 of which the tilt axis AX4 is controlled moves
from a first position P1 on the first design surface F1 to a third
position P3 via a second position P2. The first position P1 is a
position on the first design surface F1 far from the swing body 2.
The second position P2 is a position on the first design surface F1
which is closer to the swing body 2 than the first position P1. The
third position P3 is a position on the first design surface F1
which is closer to the swing body 2 than the second position
P2.
[0082] The first design surface F1 is an inclined surface which is
inclined with respect to plane XY. The driver is able to form an
inclined surface for the construction object by operating the
operating device 40 to drive at least the arm 7 such that the
bucket 8 of which the tilt axis AX4 is controlled approaches the
swing body 2.
[0083] Note that, as illustrated in FIGS. 8 and 9, when the
position of the center of the swing body 2 in the vehicle-width
direction and the position of the center of the first design
surface F1 are different, the driver may operate the operating
device 40 so as to cause the swing body 2 to swing while the
working equipment 1 is operated, such that the bucket 8 does not
dig into the first design surface F1.
[0084] The determination unit 57 determines whether or not the
control object surface Fc has been switched. In other words, the
determination unit 57 determines whether or not the control object
surface Fc has been switched from the first design surface F1 to
the second design surface F2 on the basis of distance d1 between
the bucket 8 and the first design surface F1 and distance d2
between the bucket 8 and the second design surface F2 (step
S40).
[0085] When it is determined in step S40 that the control object
surface Fc has been switched from the first design surface F1 to
the second design surface F2 (step S40: Yes), the processing
advances to step S50.
[0086] When it is determined in step S40 that the control object
surface Fc has not been switched from the first design surface F1
to the second design surface F2 (step S40: No), that is, when the
control object surface Fc has been maintained as the first design
surface F1, the processing advances to step S70.
[0087] The operating data of the operating device 40 is acquired by
the operating data acquisition unit 53. The determination unit 57
determines whether or not a specific operation has been maintained,
on the basis of the operating data acquired by the operating data
acquisition unit 53 (step S50).
[0088] In this embodiment, the specific operation is an operation
to drive the arm 7 such that the bucket 8 moves from the first
position P1 to the third position P3. The determination unit 57
determines whether or not the operation of the operating device 40
(the left-operation lever 42) for driving the arm 7 is
continuing.
[0089] When it is determined in step S50 that the specific
operation is maintained (step S50: Yes), during the period in which
the specific operation is maintained, the determination unit 57
maintains the control object surface Fc as the first design surface
F1 without switching the control object surface Fc to the second
design surface F2 (step S60).
[0090] When it is determined in step S50 that the specific
operation is not maintained (step S50: No), the determination unit
57 determines that the design surface F, among the first design
surface F1 and the second design surface F2, which is the shortest
distance from the bucket 8 is the control object surface Fc and the
processing advances to step S70.
[0091] For example, when the bucket 8 is moving from the first
position P1 toward the third position P3, the driver quits the
operation using the operating device 40 (left-operation lever 42)
to operate the arm 7, and in a case where the design surface F,
among the first design surface F1 and second design surface F2,
which is the shortest distance from the bucket 8 at the moment the
driver quits the operation of the arm 7 is the first design surface
F1, the working equipment control unit 61 controls the tilt axis
AX4 of the bucket 8 such that the blade edge 9 of the bucket 8 is
parallel to the first design surface F1. On the other hand, in a
case where the design surface F, among the first design surface F1
and second design surface F2, which is the shortest distance from
the bucket 8 at the moment the driver quits the operation of the
arm 7 is the second design surface F2, the working equipment
control unit 61 controls the tilt axis AX4 of the bucket 8 such
that the blade edge 9 of the bucket 8 is parallel to the second
design surface F2.
[0092] The display control unit 62 causes the display device 80 to
generate a display such that the mode in which the control object
surface Fc determined by the determination unit 57 is displayed
differs from that of surfaces other than the control object surface
Fc (step S70).
[0093] The working equipment control unit 61 controls the tilt axis
AX4 of the bucket 8 such that the blade edge 9 of the bucket 8 and
the first design surface F1 are parallel to each other, on the
basis of the first design surface F1 which is the control object
surface Fc determined by the determination unit 57 (step S80).
[0094] FIG. 10 is a schematic diagram to illustrate an example of
the operation of the excavator 100 according to this embodiment.
FIG. 10 illustrates the relative angle between the blade edge 9 of
the bucket 8 and the first design surface F1 when the bucket 8 has
moved to the first position P1, second position P2, and third
position P3, respectively.
[0095] As illustrated in FIG. 10, in the first position P1 and
second position P2 respectively, the design surface F, among the
first design surface F1 and second design surface F2, which is the
shortest distance from the bucket 8 is the first design surface F1.
Therefore, the determination unit 57 determines the first design
surface F1 which, among the first design surface F1 and second
design surface F2, is the shortest distance from the bucket 8 as
the control object surface Fc.
[0096] As illustrated in FIG. 10, in the third position P3, for
example, the design surface F which is the shortest distance from
the bucket 8 sometimes changes from the first design surface F1 to
the second design surface F2. In this embodiment, in a case where
the control object surface Fc is determined as being the first
design surface F1, the determination unit 57 maintains the control
object surface Fc as the first design surface F1 in the period in
which the specific operation (the operation of driving the arm 7)
is maintained, even when the design surface F which is the shortest
distance from the bucket 8 changes from the first design surface F1
to the second design surface F2, and the working equipment control
unit 61 controls the tilt axis AX4 of the bucket 8 on the basis of
the control object surface Fc. In other words, in a case where the
control object surface Fc is determined as being the first design
surface F1, the working equipment control unit 61 controls the tilt
axis AX4 of the bucket 8 such that, in the period in which the
specific operation (the operation of driving the arm 7) is
maintained, the relative angle between the bucket 8 in the
tilt-rotation direction and the control object surface Fc (the
first design surface F1) is maintained, even when the design
surface which is the shortest distance from the bucket 8 changes
from the first design surface F1 to the second design surface
F2.
[0097] FIG. 11 is a schematic diagram illustrating an example of
the display of the display device 80 according to this embodiment.
As illustrated in FIG. 11, the display control unit 62 causes the
display device 80 to display the first design surface F1 and the
second design surface F2 adjacent to the first design surface F1 on
the basis of the target construction data CS. In this embodiment,
the gradient of the first design surface F1 and the gradient of the
second design surface F2 differ from one another. As illustrated in
FIG. 11, a groove (valley) is formed by the first design surface F1
and the second design surface F2. The first design surface F1 and
second design surface F2 are each flat. A letter "V" shaped groove
is formed by the first design surface F1 and second design surface
F2.
[0098] The display control unit 62 causes the display device 80 to
use different display modes to display the control object surface
Fc and the non-control object surface Fn. When the first design
surface F1 is determined as being the control object surface Fc and
the second design surface F2 is determined as being the non-control
object surface Fn, the display control unit 62 causes the display
device 80 to use different display modes to display the first
design surface F1 and the second design surface F2. In the example
illustrated in FIG. 11, the display control unit 62 causes graphic
data 81 pointing to the first design surface F1 which is the
control object surface Fc to be displayed in the vicinity of the
first design surface F1. The graphic data 81 is not displayed in
the vicinity of the second design surface F2 which is the
non-control object surface Fn. By viewing the display device 80,
the driver is able to visually recognize which of the first design
surface F1 and second design surface F2 is the control object
surface Fc.
[0099] The driver views the display device 80 while operating the
operating device 40 such that the bucket 8 approaches the first
design surface F1 which is the control object surface Fc, that is,
such that the bucket 8 faces (directly opposes) the first design
surface F1. The driver is able to operate the operating device 40
to drive the working equipment 1 and is able to bring the bucket 8
close to the first design surface F1 which is the control object
surface Fc by causing the swing body 2 to swing. Because the first
design surface F1 which is the control object surface Fc is
displayed using a different display mode from that of the second
design surface F2, the driver is able to view the display device 80
while smoothly bringing the bucket 8 close to the first design
surface F1 in a short time.
[0100] Note that the control object surface Fc and the non-control
object surface Fn may be displayed on the display device 80 using
different display modes. For example, the control object surface Fc
may be displayed using a first color (red, for example), and the
non-control object surface Fn may be displayed using a second color
different from the first color (yellow, for example). For example,
the control object surface Fc may be displayed so as to light up
intermittently (blink), and the non-control object surface Fn may
be displayed so as to be continuously lit.
[0101] The operator drives at least the arm 7 by operating the
operating device 40 such that the bucket 8 moves along the second
design surface F2. Note that the operator may operate the operating
device 40 to drive the boom 6 or to drive both the arm 7 and the
boom 6.
[0102] In other words, when the second design surface F2 is
determined as being the control object surface Fc and the first
design surface F1 is determined as being the non-control object
surface Fn, the display control unit 62 displays the graphic data
81 pointing to the second design surface F2 which is the control
object surface Fc, close to the second design surface F2, for
example.
Advantageous Effects
[0103] As described hereinabove, according to this embodiment, the
control object surface Fc is determined from among the first design
surface F1 and the second design surface F2 on the basis of
distance d1 between the bucket 8 and the first design surface F1
and distance d2 between the bucket 8 and the second design surface
F2. The display control unit 62 causes the display device 80 to use
different display modes to display the control object surface Fc
and surfaces other than the control object surface Fc. Accordingly,
the driver is able to visually recognize which of the first design
surface F1 and second design surface F2 is the control object
surface Fc. Thus, the driver is able to view the display device 80
while operating the operating device 40 such that the bucket 8
approaches the first design surface F1 which is the control object
surface Fc, that is, such that the bucket 8 faces (directly
opposes) the first design surface F1. The driver is able to view
the display device 80 while smoothly bringing the bucket 8 close to
the first design surface F1 in a short time. Because the time
required to bring the bucket 8 close to the first design surface F1
is shortened, a reduction in the work efficiency of the excavator
100 is suppressed.
[0104] In this embodiment, it is determined whether or not a
specific operation is maintained on the basis of operating data of
the operating device 40, and during a period in which the specific
operation is maintained, the tilt axis AX4 is controlled in a state
where the control object surface Fc is maintained. For example,
when the control object surface Fc is determined as being the first
design surface F1, the control object surface Fc is maintained as
the first design surface F1 during a period in which the specific
operation is maintained even when the design surface which is the
shortest distance from the bucket 8 has changed from the first
design surface F1 to the second design surface F2. Contrary to the
driver's wishes, tilt rotation of the bucket 8 is accordingly
suppressed. That is, when the driver intends to try to construct a
construction object on the basis of the first design surface F1,
even though the arm 7 is being operated to move the bucket 8 of
which the tilt axis AX4 is controlled on the basis of the first
design surface F1 from the first position P1 to the third position
P3, when the bucket 8 changes from a state where the tilt axis AX4
thereof is controlled on the basis of the first design surface F1
to a state where the tilt axis AX4 of the bucket 8 is controlled on
the basis of the second design surface F2, the bucket 8 will likely
dig into the design surface F significantly. In this embodiment,
during a period in which the operating device 40 (the
left-operation lever 42) is being operated, the working equipment
control unit 61 recognizes that the driver intends to try to
construct a construction object on the basis of the first design
surface F1. In a case where it is recognized that the driver
intends to try to construct a construction object on the basis of
the first design surface F1, the working equipment control unit 61
controls the tilt axis AX4 of the bucket 8 on the basis of the
first design surface F1 even when distance d2 between the bucket 8
and the second design surface F2 is shorter than distance d1
between the bucket 8 and the first design surface F1. The driver's
wishes are accordingly respected, and the bucket 8 is prevented
from digging into the design surface F.
[0105] Note that, in this embodiment, the specific operation is
assumed to be an operation to drive the arm 7. The specific
operation may also be an operation to drive the traveling body 3 of
the excavator 100. For example, in a case where the bucket 8 of
which the tilt axis AX4 is controlled is moved from the first
position P1 to the third position P3, the traveling body 3 is
sometimes made to retreat without driving the arm 7. The working
equipment control unit 61 may also determine whether or not the
specific operation is maintained, on the basis of the operating
data of the operating device 40 (the travel lever) that operates
the traveling body 3.
Second Embodiment
[0106] A second embodiment will be described next. In the
description hereinbelow, the same reference signs are assigned to
constituent elements which are the same as or similar to those of
the foregoing embodiment, and descriptions of such elements are
simplified or omitted.
[0107] In this embodiment, an example in which the control object
surface Fc and the non-control object surface Fn are determined on
the basis of the input data of the input device 90 will be
described.
[0108] FIG. 12 is a flowchart illustrating an example of a
construction machine control method according to the second
embodiment.
[0109] The target construction data acquisition unit 55 acquires
the target construction data CS which includes the first design
surface F1 and second design surface F2 (step S10).
[0110] The display control unit 62 causes the display device 80 to
display the target construction data CS which includes the first
design surface F1 and second design surface F2 (step S15).
[0111] The driver views the display device 80 while operating the
input device 90 to select the control object surface Fc from among
the first design surface F1 and second design surface F2 which are
displayed on the display device 80. The input data acquisition unit
54 acquires the input data which is generated through the operation
of the input device 90 (step S25).
[0112] The display control unit 62 may cause the display device 80
to display a first line representing a cross-section of the first
design surface F1 and a second line representing a cross-section of
the second design surface F2, for example. The display control unit
62 may also display the first line and the second line at different
angles on the display screen of the display device 80. The driver
is thus able to distinguish between the image data representing the
first design surface F1 and the image data representing the second
design surface F2.
[0113] The determination unit 57 determines the control object
surface Fc from among the first design surface F1 and the second
design surface F2 on the basis of the input data acquired by the
input data acquisition unit 54 (step S30).
[0114] The display control unit 62 causes the display device 80 to
use different display modes to display the first design surface F1
and the second design surface F2 (step S35).
[0115] The working equipment control unit 61 controls the tilt axis
AX4 of the bucket 8 such that the blade edge 9 of the bucket 8 and
the first design surface F1 are parallel to each other, on the
basis of the first design surface F1 which is the control object
surface Fc determined by the determination unit 57 (step S80).
[0116] Note that the first design surface F1 and the second design
surface F2 may be displayed using display modes which the driver is
able to visually distinguish between. For example, image data
representing the first design surface F1 may be displayed using a
first color (red, for example), and image data representing the
second design surface F2 may be displayed using a second color
different from the first color (yellow, for example). The image
data representing the first design surface F1 may be displayed so
as to light up intermittently (blink), and the image data
representing the second design surface F2 may be displayed so as to
be continuously lit. Furthermore, text data representing the first
design surface F1 and second design surface F2 may also be
displayed on the display device 80.
[0117] In the description hereinbelow, by way of an example, the
first design surface F1 is selected by the driver as the control
object surface Fc, and the first design surface F1 is determined as
being the control object surface Fc by a determination unit 87
which determines the second design surface F2 adjacent to the first
design surface F1 as being the non-control object surface Fn.
[0118] The vehicle-body position data acquisition unit 51 acquires
position data of the swing body 2 from the vehicle-body position
calculation device 20. The angle data acquisition unit 52 acquires
angle data of the working equipment 1 from the angle detection
device 30. The bucket position data calculation unit 56 calculates
the position of the bucket 8 (the regulation points RP) on the
basis of the position data of the swing body 2, the angle data of
the working equipment 1, and the working equipment data stored in
the storage unit 60.
[0119] Furthermore, the operator drives at least the arm 7 by
operating the operating device 40 such that the bucket 8 moves
along the first design surface F1. Note that the operator may
operate the operating device 40 to drive the boom 6 or to drive
both the arm 7 and the boom 6.
[0120] The driver operates the operating device 40 such that the
bucket 8 of which the tilt axis AX4 is controlled moves from the
first position P1 to the third position P3.
Advantageous Effects
[0121] As described hereinabove, according to this embodiment, the
control object surface Fc is determined from among the first design
surface F1 and the second design surface F2 on the basis of the
input data generated through the operation of the input device 90.
In other words, the driver is able to determine by themselves which
of the first design surface F1 and second design surface F2 is to
be the control object surface Fc. Thus, the driver is able to
operate the operating device 40 such that the bucket 8 approaches
the first design surface F1 which is the control object surface Fc,
that is, such that the bucket 8 faces (directly opposes) the first
design surface F1. Because the control object surface Fc desired by
the driver is selected, even when the bucket 8 approaches the
non-control object surface Fn, the bucket is prevented from digging
into the design surface F when the control object surface Fc is
switched. The excavator 100 can thus carry out the work smoothly.
Moreover, because the time required to bring the bucket 8 close to
the first design surface F1 is shortened, a reduction in the work
efficiency of the excavator 100 is suppressed.
Computer System
[0122] FIG. 13 is a block diagram illustrating an example of a
computer system 1000 according to the embodiment. The foregoing
control device 50 includes the computer system 1000. The computer
system 1000 has a processor 1001 such as a central processing unit
(CPU), a main memory 1002 that includes a nonvolatile memory such
as a read-only memory (ROM) and a volatile memory such as a
random-access memory (RAM), a storage 1003, and an interface 1004
that includes I/O circuitry. The functions of the foregoing control
device 50 are stored in the storage 1003 as a program. The
processor 1001 reads the program from the storage 1003,
decompresses same in the main memory 1002, and executes the
foregoing processing according to the program. Note that the
program may also be distributed to the computer system 1000 via a
network.
[0123] The computer system 1000 is capable, according to the
foregoing embodiment, of executing: acquiring target construction
data representing the target shape of a construction object
including the first design surface F1 and the second design surface
F2 adjacent to the first design surface F1; of determining the
control object surface Fc from among the first design surface F1
and the second design surface F2 on the basis of the distance d1
between the bucket 8 and the first design surface F1 and the
distance d2 between the bucket 8 and the second design surface F2;
of controlling the tilt axis AX4 of the bucket 8 on the basis of
the control object surface Fc thus determined; and of causing the
display device 80 to use different display modes to display the
control object surface Fc and surfaces other than the control
object surface Fc.
[0124] In addition, the computer system 1000 is capable, according
to the foregoing embodiment, of executing: acquiring target
construction data representing the target shape of a construction
object including the first design surface F1 and the second design
surface F2 adjacent to the first design surface F1; of acquiring
input data generated through the operation of the input device 90;
of determining the control object surface Fc from among the first
design surface F1 and the second design surface F2 on the basis of
the input data; and of controlling the tilt axis AX4 of the bucket
8 on the basis of the control object surface Fc thus
determined.
Other Embodiments
[0125] Note that, in the foregoing embodiments, the construction
machine 100 is an excavator. The constituent elements described in
the foregoing embodiments are also applicable to a construction
machine, which has working equipment, other than an excavator.
[0126] Note that, in the foregoing embodiments, the swing motor 16
that causes the swing body 2 to swing need not be a hydraulic
motor. The swing motor 16 may also be an electric motor that
performs driving by being supplied with electrical power. Moreover,
the working equipment 1 may be operated independently of the
hydraulic cylinders 10 by using the motive power generated by an
electric actuator such as an electric motor, for example.
REFERENCE SIGNS LIST
[0127] 1 WORKING EQUIPMENT
[0128] 2 SWING BODY
[0129] 3 TRAVELING BODY
[0130] 3C CRAWLER TRACK
[0131] 4 DRIVER CAB
[0132] 4S SEAT
[0133] 5 ENGINE
[0134] 6 BOOM
[0135] 7 ARM
[0136] 8 BUCKET
[0137] 9 BLADE EDGE
[0138] 10 HYDRAULIC CYLINDER
[0139] 11 BOOM CYLINDER
[0140] 12 ARM CYLINDER
[0141] 13 BUCKET CYLINDER
[0142] 14 TILT CYLINDER
[0143] 15 TRAVEL MOTOR
[0144] 16 SWING MOTOR
[0145] 17 HYDRAULIC PUMP
[0146] 18 VALVE DEVICE
[0147] 20 VEHICLE-BODY POSITION CALCULATION DEVICE
[0148] 21 POSITION CALCULATOR
[0149] 22 ATTITUDE CALCULATOR
[0150] 23 ORIENTATION CALCULATOR
[0151] 30 ANGLE DETECTION DEVICE
[0152] 31 BOOM ANGLE DETECTOR
[0153] 32 ARM ANGLE DETECTOR
[0154] 33 BUCKET ANGLE DETECTOR
[0155] 34 TILT ANGLE DETECTOR
[0156] 40 OPERATING DEVICE
[0157] 41 RIGHT-OPERATION LEVER
[0158] 42 LEFT-OPERATION LEVER
[0159] 43 TILT-OPERATION LEVER
[0160] 50 CONTROL DEVICE
[0161] 51 VEHICLE-BODY POSITION DATA ACQUISITION UNIT
[0162] 52 ANGLE DATA ACQUISITION UNIT
[0163] 53 OPERATING DATA ACQUISITION UNIT
[0164] 54 INPUT DATA ACQUISITION UNIT
[0165] 55 TARGET CONSTRUCTION DATA ACQUISITION UNIT
[0166] 56 BUCKET POSITION DATA CALCULATION UNIT
[0167] 57 DETERMINATION UNIT
[0168] 60 STORAGE UNIT
[0169] 61 WORKING EQUIPMENT CONTROL UNIT
[0170] 62 DISPLAY CONTROL UNIT
[0171] 70 TARGET CONSTRUCTION DATA SUPPLY DEVICE
[0172] 80 DISPLAY DEVICE
[0173] 90 INPUT DEVICE
[0174] 100 CONSTRUCTION MACHINE
[0175] 200 CONTROL SYSTEM
[0176] AX1 BOOM AXIS
[0177] AX2 ARM AXIS
[0178] AX3 BUCKET AXIS
[0179] AX4 TILT AXIS
[0180] F1 FIRST DESIGN SURFACE
[0181] F2 SECOND DESIGN SURFACE
[0182] Fc CONTROL OBJECT SURFACE
[0183] Fn NON-CONTROL OBJECT SURFACE
* * * * *