U.S. patent application number 17/426930 was filed with the patent office on 2022-03-31 for method for manufacturing single sheet-type green sheet, method for manufacturing silicon nitride sintered body, single sheet-type green sheet, and silicon nitride sintered body.
This patent application is currently assigned to DENKA COMPANY LIMITED. The applicant listed for this patent is DENKA COMPANY LIMITED. Invention is credited to Yoshiyuki ESHIMA, Seiji KOBASHI, Koji NISHIMURA, Ryuhei WATANABE, Akimasa YUASA.
Application Number | 20220098121 17/426930 |
Document ID | / |
Family ID | |
Filed Date | 2022-03-31 |








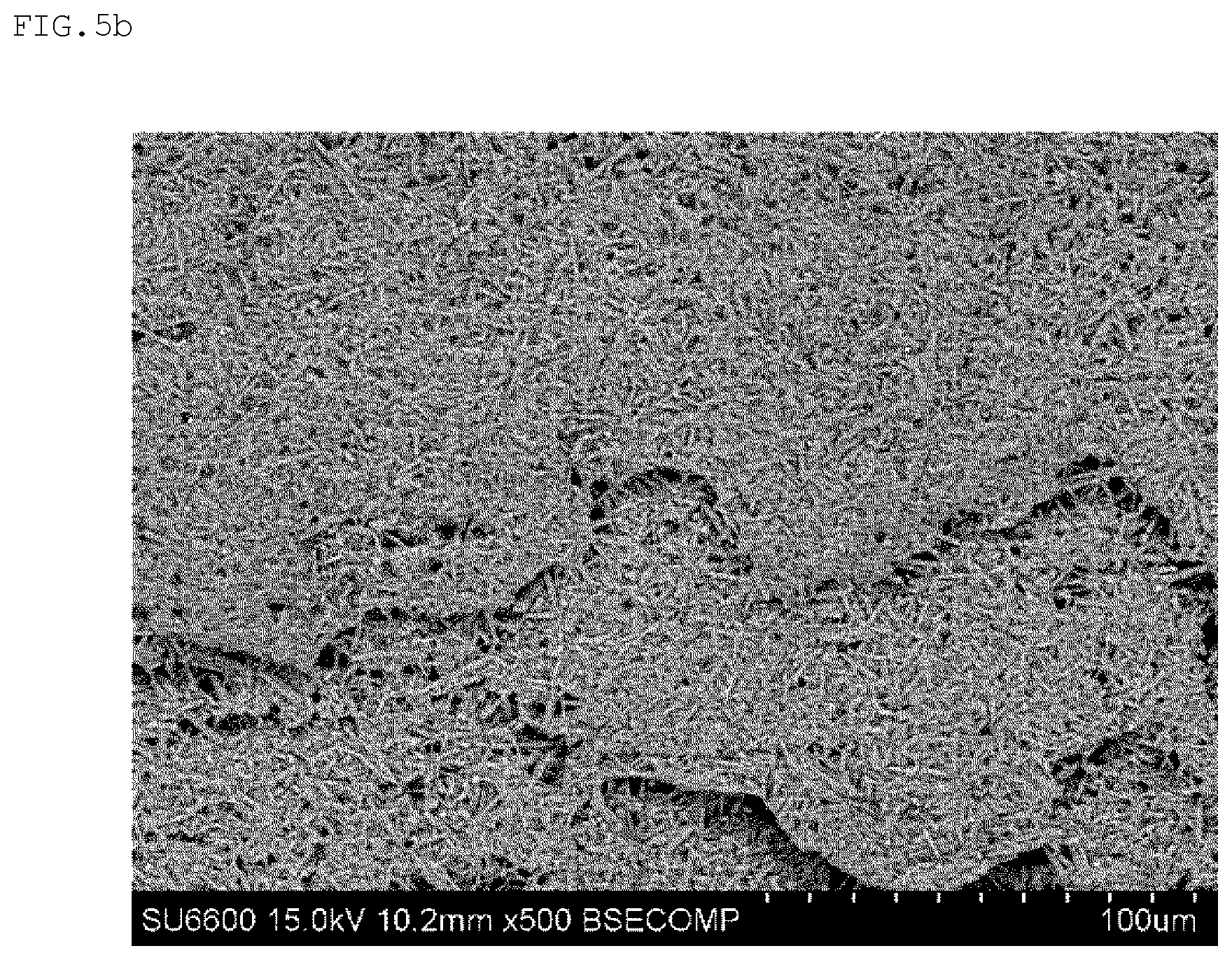


View All Diagrams
United States Patent
Application |
20220098121 |
Kind Code |
A1 |
YUASA; Akimasa ; et
al. |
March 31, 2022 |
METHOD FOR MANUFACTURING SINGLE SHEET-TYPE GREEN SHEET, METHOD FOR
MANUFACTURING SILICON NITRIDE SINTERED BODY, SINGLE SHEET-TYPE
GREEN SHEET, AND SILICON NITRIDE SINTERED BODY
Abstract
A method for manufacturing a single sheet-type green sheet
includes a transporting step of transporting a strip-shaped green
sheet that contains ceramic along a longitudinal direction thereof,
and an irradiation step of irradiating the transported strip-shaped
green sheet with a laser beam to cut the strip-shaped green sheet,
thereby obtaining a single sheet-type green sheet.
Inventors: |
YUASA; Akimasa; (Omuta-shi,
JP) ; ESHIMA; Yoshiyuki; (Omuta-shi, JP) ;
WATANABE; Ryuhei; (Omuta-shi, JP) ; KOBASHI;
Seiji; (Omuta-shi, JP) ; NISHIMURA; Koji;
(Omuta-shi, JP) |
|
Applicant: |
Name |
City |
State |
Country |
Type |
DENKA COMPANY LIMITED |
Tokyo |
|
JP |
|
|
Assignee: |
DENKA COMPANY LIMITED
Tokyo
JP
|
Appl. No.: |
17/426930 |
Filed: |
January 30, 2020 |
PCT Filed: |
January 30, 2020 |
PCT NO: |
PCT/JP2020/003329 |
371 Date: |
July 29, 2021 |
International
Class: |
C04B 41/00 20060101
C04B041/00; C04B 35/584 20060101 C04B035/584; B28B 11/14 20060101
B28B011/14; B28B 11/24 20060101 B28B011/24 |
Foreign Application Data
Date |
Code |
Application Number |
Jan 30, 2019 |
JP |
2019-013761 |
Claims
1. A method for manufacturing a single sheet-type green sheet
comprising an irradiation step of irradiating a strip-shaped green
sheet that contains ceramic with a laser beam to cut the
strip-shaped green sheet to obtain a single sheet-type green
sheet.
2. The method for manufacturing a single sheet-type green sheet
according to claim 1, wherein the laser beam with which the
strip-shaped green sheet is irradiated in the irradiation step is
emitted from an irradiation portion that emits a carbon dioxide
laser beam.
3. The method for manufacturing a single sheet-type green sheet
according to claim 1, further comprising a transporting step of
transporting the strip-shaped green sheet to the irradiation step
along a longitudinal direction of the strip-shaped green sheet.
4. The method for manufacturing a single sheet-type green sheet
according to claim 3, further comprising a step of performing
doctor blade molding or extrusion molding on a slurry containing
ceramic powder to have a strip shape to obtain the strip-shaped
green sheet, the step being performed before the transporting
step.
5. The method for manufacturing a single sheet-type green sheet
according to claim 4, wherein the ceramic powder includes silicon
nitride powder or aluminum nitride powder.
6. A method for manufacturing a silicon nitride sintered body
comprising heating and sintering the single sheet-type green sheet
that is manufactured by the method for manufacturing a single
sheet-type green sheet according to claim 1 to obtain a silicon
nitride sintered body.
7. A single sheet-type green sheet having a laser cut surface on at
least one side surface.
8. The single sheet-type green sheet according to claim 7, wherein
the laser cut surface has a surface roughness Ra of equal to or
greater than 0.5 .mu.m and equal to or smaller than 2.0 .mu.m, and
the laser cut surface has a surface roughness Rz of equal to or
greater than 5.0 .mu.m and equal to or smaller than 12.0 .mu.m.
9. A silicon nitride sintered body formed in a sheet shape
comprising an end surface, wherein the end surface has a surface
roughness Ra of equal to or greater than 0.5 .mu.m and equal to or
smaller than 2.0 .mu.m, and the end surface has a surface roughness
Rz of equal to or greater than 5.0 82 m and equal to or smaller
than 12.0 .mu.m.
Description
TECHNICAL FIELD
[0001] The present invention relates to a method for manufacturing
a single sheet-type green sheet, a method for manufacturing a
silicon nitride sintered body, a single sheet-type green sheet, and
a silicon nitride sintered body.
BACKGROUND ART
[0002] It has been known that a ceramic board is used as a base
material of a circuit board for a power module. Such a ceramic
board is manufactured such that a strip-shaped green sheet made of
ceramic is cut to obtain single sheet-type green sheets, the
obtained single sheet-type green sheets are laminated to obtain a
laminate, and the laminate obtained by the single sheet-type green
sheets being laminated is sintered.
[0003] Here, in Patent Document 1, a method for manufacturing a
ceramic laminate including a cutting step of cutting a ceramic
strip-shaped green sheet to obtain a plurality of single sheet-type
green sheets, a laminating step of laminating the plurality of
single sheet-type green sheets obtained by the cutting, and a
sintering step of sintering the plurality of single sheet-type
green sheets obtained by the laminating is disclosed. In the
above-mentioned cutting step, the plurality of single sheet-type
green sheets are obtained by cutting the strip-shaped green sheet
using a plate-shaped cutting blade.
RELATED DOCUMENT
Patent Document
[0004] [Patent Document 1] Japanese Unexamined Patent Publication
No. 2017-065059
SUMMARY OF THE INVENTION
Technical Problem
[0005] As described above, in the manufacturing method disclosed in
Patent Document 1, the strip-shaped green sheet is cut using the
cutting blade in the cutting step. Thus, this manufacturing method
has the following problems. That is, chips may be generated from
the cut surfaces of the single sheet-type green sheets by a cutting
operation using the cutting blade, and the cutting blade maybe worn
by the repeated cutting operation, so that metal powder may be
generated. In addition, in a case where the laminating step is
performed with the generated chips and metal powder adhering to the
surfaces of the single sheet-type green sheets, unevenness defects
occur in the single sheet-type green sheets. Furthermore, during
the cutting of the strip-shaped green sheet using the cutting
blade, the cutting blade moves while pressurizing the strip-shaped
green sheet with a blade edge. Therefore, the cut surfaces of the
single sheet-type green sheets, which are formed by the cutting
with the cutting blade, are formed while the strip-shaped green
sheet is pulled by the blade edge. As a result, cracks may be
generated near the cut surfaces of the single sheet-type green
sheets.
[0006] As described above, the generation of unevenness defects and
cracks results in a problem of a decrease in the yield of the
ceramic board.
[0007] An object of the present invention is to provide a method
for manufacturing a single sheet-type green sheet in which chips
from a cut surface and cracks near the cut surface are hardly
generated, and metal powder due to a cutting blade is not generated
in a case where the strip-shaped green sheet is cut to obtain the
single sheet-type green sheets.
Solution to Problem
[0008] A method for manufacturing a single sheet-type green sheet
of a first aspect of the present invention includes a transporting
step of transporting a strip-shaped green sheet that contains
ceramic along a longitudinal direction thereof, and an irradiation
step of irradiating the transported strip-shaped green sheet with a
laser beam to cut the strip-shaped green sheet to obtain a single
sheet-type green sheet.
[0009] According to the manufacturing method of a second aspect of
the present invention, in the method for manufacturing a single
sheet-type green sheet of the first aspect, the laser beam with
which the strip-shaped green sheet is irradiated in the irradiation
step is emitted from an irradiation portion that emits a carbon
dioxide laser beam.
[0010] According to the manufacturing method of a third aspect of
the present invention, in the method for manufacturing a single
sheet-type green sheet of the first or second aspect, a step of
performing doctor blade molding or extrusion molding on a slurry
containing ceramic powder to have a strip shape to obtain the
strip-shaped green sheet, is the step being performed before the
transporting step, is further included.
[0011] According to the manufacturing method of a fourth aspect of
the present invention, in the method for manufacturing a single
sheet-type green sheet of the third aspect, the ceramic powder
includes silicon nitride powder or aluminum nitride powder.
[0012] According to a method for manufacturing a silicon nitride
sintered body of the present invention, the single sheet-type green
sheet that is manufactured by the method for manufacturing a single
sheet-type green sheet according to any one aspect of the first to
fourth aspects is heated and sintered to obtain a silicon nitride
sintered body.
[0013] The single sheet-type green sheet according to the first
aspect of the present invention has a laser cut surface on at least
one side surface.
[0014] According to the single sheet-type green sheet of the second
aspect of the present invention, in the single sheet-type green
sheet of the first aspect, the laser cut surface has a surface
roughness Ra of equal to or greater than 0.5 .mu.m and equal to or
smaller than 2.0 .mu.m, and the laser cut surface has a surface
roughness Rz of equal to or greater than 5.0 .mu.m and equal to or
smaller than 12.0 .mu.m.
[0015] A silicon nitride sintered body of the present invention is
formed in a sheet shape and includes an end surface, in which the
end surface has a surface roughness Ra of equal to or greater than
0.5 .mu.m and equal to or smaller than 2.0 .mu.m, and the end
surface has a surface roughness Rz of equal to or greater than 5.0
.mu.m and equal to or smaller than 12.0 .mu.m.
Advantageous Effects of Invention
[0016] According to the method for manufacturing a single
sheet-type green sheet of the present invention, chips from the cut
surface and cracks near the cut surface are hardly generated, and
metal powder due to the cutting blade is not generated in a case
where the strip-shaped green sheet is cut to obtain the single
sheet-type green sheets.
BRIEF DESCRIPTION OF THE DRAWINGS
[0017] The above and other objects, advantages and features of the
present invention will be more apparent from the following
description of certain preferred embodiments taken in conjunction
with the accompanying drawings.
[0018] FIG. 1 is a flow chart illustrating a manufacturing process
of a ceramic board of the present embodiment.
[0019] FIG. 2A is a diagram for explaining a molding step of the
present embodiment, and is a schematic view for explaining a state
in which a strip-shaped green sheet is produced from a slurry using
a doctor blade molding device.
[0020] FIG. 2B is a diagram for explaining a cutting step of the
present embodiment, and is a schematic view (side view) for
explaining a state in which the strip-shaped green sheet is cut
using a cutting device to produce a single sheet-type green
sheet.
[0021] FIG. 2C is a schematic view of FIG. 2B when seen from the
front.
[0022] FIG. 2D is a schematic view of a laminate of the present
embodiment.
[0023] FIG. 3 is an SEM image of a cut surface of the single
sheet-type green sheet of the present embodiment.
[0024] FIG. 4 is a table summarizing conditions and observation
results of a first test.
[0025] FIG. 5A is an enlarged photograph of the vicinity of a cut
surface of a single sheet-type green sheet of a first comparative
example, in which the photograph is seen from an upper surface side
in a thickness direction.
[0026] FIG. 5B is an SEM image of the cut surface of the single
sheet-type green sheet of the first comparative example.
[0027] FIG. 6 is an enlarged photograph of the vicinity of a cut
surface of a single sheet-type green sheet of a second comparative
example, in which the photograph is seen from an upper surface side
in a thickness direction.
[0028] FIG. 7 is an enlarged photograph of the vicinity of a cut
surface of a single sheet-type green sheet of a third comparative
example, in which the photograph is seen from an upper surface side
in a thickness direction.
[0029] FIG. 8 is an enlarged photograph of the vicinity of a cut
surface of a single sheet-type green sheet of a fourth comparative
example, in which the photograph is seen from an upper surface side
in a thickness direction.
[0030] FIG. 9 is an enlarged photograph of the vicinity of the cut
surface of the single sheet-type green sheet of the present
embodiment, in which the photograph is seen from an upper surface
side in a thickness direction.
[0031] FIG. 10 is a table summarizing conditions and measurement
results of a third test.
DESCRIPTION OF EMBODIMENTS
Summary
[0032] First, a method for manufacturing a silicon nitride sintered
body 40 (see FIG. 2D) of the present embodiment will be described
with reference to the drawings. Next, Example of the present
embodiment will be described with reference to the drawings. In all
the drawings referenced in the following description, the same
components are denoted by the same reference numerals, and the
description thereof will not be repeated as appropriate.
[0033] Here, the silicon nitride sintered body 40 is, for example,
a ceramic board for a power module mounted on an electric vehicle,
a railroad vehicle, or other industrial equipment. The silicon
nitride sintered body 40 is obtained such that single sheet-type
green sheets 30 (see FIGS. 2B and 2C) described later are sintered
in a laminated state, for example. Each of the single sheet-type
green sheets 30 is obtained such that a strip-shaped green sheet 20
is cut (see FIGS. 2A and 2B). That is, a relationship between the
silicon nitride sintered body 40 and the single sheet-type green
sheet 30 is a relationship between a finished product and an
intermediate product (a product manufactured in a step before the
finished product is obtained) or a relationship between a first
intermediate product and a second intermediate product (a product
manufactured in a step before the first intermediate product is
obtained). Therefore, the single sheet-type green sheet 30 of the
present embodiment is manufactured through steps at an intermediate
stage of the method for manufacturing the silicon nitride sintered
body 40 of the present embodiment, which will be described later.
Therefore, the method for manufacturing the single sheet-type green
sheet 30 of the present embodiment will be described in the
description of the method for manufacturing the silicon nitride
sintered body 40 of the present embodiment.
Method for Manufacturing Silicon Nitride Sintered Body of Present
Embodiment
[0034] Hereinafter, the method for manufacturing the silicon
nitride sintered body 40 of the present embodiment will be
described with reference to FIG. 1, FIG. 2A, FIG. 2B, and FIG.
2C.
[0035] As illustrated in a flow chart of FIG. 1, the method for
manufacturing the silicon nitride sintered body 40 of the present
embodiment includes a slurry producing step, a molding step, a
cutting step, a depositing step, a degreasing step, and a sintering
step, and these steps are carried out in the described order.
[0036] In the flow chart of FIG. 1, the method for manufacturing
the silicon nitride sintered body 40 is denoted by reference
numeral S10, and the slurry producing step, the molding step, the
cutting step, the depositing step, the degreasing step, and the
sintering step are denoted by reference numerals S11, S12, S13,
S14, S15, and S16, respectively.
Slurry Producing Step
[0037] First, a slurry producing step S11 will be described. This
step is a step of mixing raw material powder with an organic
solvent described later to produce a slurry 10. The slurry 10
produced in this step (see FIG. 2A) is molded into the strip-shaped
green sheet 20 in the next step (molding step).
[0038] The raw material powder of the slurry 10 is a powder
containing a main component and a sintering aid, which will be
described later. The main component is, for example, silicon
nitride (Si.sub.3N.sub.4) of 80% by weight to 98.3% by mass, and
the sintering aid is, for example, at least one rare earth element
of 1% by weight to 10% by mass (expressed in terms of oxide) and
magnesium (Mg) of 0.7% by weight to 10% by mass (expressed in terms
of oxide). A ratio at which silicon nitride powder is of an
.alpha.-phase is preferably 20% to 100% in consideration of the
density, bending strength, and thermal conductivity of the silicon
nitride sintered body 40. Here, to give further details about the
meaning of "to" used in the present specification, for example,
"20% to 100%" means "equal to or more than 20% and equal to or less
than 100%". In addition, "to" used in this specification means
equal to or more than the description before "to" and equal to or
less than the description after "to".
[0039] The reason why a ratio of silicon nitride (Si.sub.3N.sub.4)
in the raw material powder is 80% by weight to 98.3% by mass as an
example is that the bending strength and thermal conductivity of
the obtained silicon nitride sintered body 40 are not too low, a
denseness of the silicon nitride sintered body 40 due to lack of
the sintering aid is ensured, and the like.
[0040] The reason why the ratio of at least one rare earth element
in the raw material powder is 1% by weight to 10% by mass
(expressed in terms of oxide) is that in a case where a ratio
thereof is less than the ratio of 1% by weight to 10% by mass, the
bond between the silicon nitride particles is weakened and cracks
easily extend at grain boundaries, and in a case where a ratio is
more than the ratio of 1% by weight to 10% by mass, the bending
strength decreases and a ratio of grain boundary phases increases
and the thermal conductivity decreases. The reason why the ratio of
magnesium (Mg) in the raw material powder is 0.7% by weight to 10%
by mass (expressed in terms of oxide) is that in a case where a
ratio thereof is less than the ratio of 0.7% by weight to 10% by
mass, a liquid phase produced at a low temperature is insufficient,
and in a case where a ratio thereof is more than the ratio of 0.7%
by weight to 10% by mass, the volatilization amount of Mg increases
and holes are likely to be formed in the silicon nitride sintered
body 40.
[0041] Here, a content of Mg is preferably 0.7% by weight to 7% by
mass (expressed in terms of oxide), and more preferably 1% by
weight to 5% by mass. In addition, a content of at least one rare
earth element is preferably 2% by weight to 10% by mass (expressed
in terms of oxide). Therefore, a content of Si.sub.3N.sub.4 is
preferably 83% by weight to 97.3% by mass, and more preferably 90%
by weight to 97% by mass. As the rare earth element, Y, La, Ce, Nd,
Pm, Sm, Eu, Gd, Dy, Ho, Er, Tm, Yb, Lu, and the like can be used,
but Y is preferably used from the viewpoint of an increase in the
density of the silicon nitride sintered body 40. It is preferable
to use each of Mg and at least one rare earth element in the form
of oxide powder.
[0042] Therefore, the sintering aid is preferably a combination of
MgO powder and Y.sub.2O.sub.3 powder.
[0043] Hereinafter, for the simplification of the description, the
raw material powder of silicon nitride is referred to as
Si.sub.3N.sub.4 powder (also known as an example of silicon nitride
powder or ceramic powder), the raw material powder of Mg is
referred to as MgO powder, and the raw material powder of the rare
earth element is referred to as Y.sub.2O.sub.3 powder. However, as
described above, the raw material powder of silicon nitride and the
raw material powder of the sintering aid may not be Si.sub.3N.sub.4
powder, and MgO powder and Y.sub.2O.sub.3 powder, respectively.
[0044] The Si.sub.3N.sub.4 powder, MgO powder, and Y.sub.2O.sub.3
powder blended as described above are mixed with a plasticizer, an
organic binder, and an organic solvent to produce the slurry 10.
Therefore, the slurry 10 produced in this step contains ceramic
powder. Here, examples of the plasticizer include a phthalic
acid-based plasticizer such as di-n-butylphthalate, a dibasic
acid-based plasticizer such as di2-ethylhexyl sebacate, and the
like. Examples of the organic binder include ethyl cellulose,
polyvinyl butyral, an acrylic-based binder, and the like. Examples
of the organic solvent include ethyl alcohol, toluene, acetone,
MEK, and the like. A solid content concentration of the slurry 10
produced in this step is preferably 30% by weight to 70% by mass
from the viewpoint of ease of molding in the next step (molding
step).
[0045] The above is the description of the slurry producing
step.
Molding Step
[0046] Next, a molding step S12 will be described. This step is a
step of producing the strip-shaped green sheet 20 from the slurry
10 as illustrated in FIG. 2A.
[0047] This step is carried out using a doctor blade molding device
100 illustrated in FIG. 2A. Here, the doctor blade molding device
100 is provided with a belt transporting mechanism 110, a molding
unit 120, and a heating unit 130. The belt transporting mechanism
110 includes a roller 112A on an upstream, a roller 112B on a
downstream, and a belt 114, and movement of the belt 114 from the
roller 112 on the upstream to the roller 112 on the downstream
(along an X direction) is made by the drive of the roller 112 on
the downstream. The molding unit 120 is disposed on an upper side
of the belt 114 (on a Z direction side of the belt 114) and faces
the belt 114. The molding unit 120 is provided with an
accommodating portion 122 accommodating the slurry 10 and a doctor
blade 124.
[0048] In addition, as illustrated in FIG. 2A, the molding unit 120
forms the sheet-shaped slurry 10 having a film thickness, which is
obtained such that the slurry 10 is brought out from the
accommodating portion 122 due to its own weight and an adhesive
force between the slurry 10 and the moving belt 114, and is
regulated and defined by the doctor blade 124. The heating unit 130
blows warm air WC onto the slurry 10 having the defined film
thickness on the belt 114 to form the slurry 10 into a sheet (the
organic solvent is vaporized). As a result, in the molding step,
the strip-shaped green sheet 20 having a width defined from the
slurry 10 (a Y direction in the drawing corresponds to a width
direction) is produced. That is, in the molding step, the slurry 10
is formed into a strip shape by the doctor blade molding to obtain
the strip-shaped green sheet 20 containing Si.sub.3N.sub.4
(ceramic) as an example.
[0049] As an example, this step is carried out after defoaming the
slurry 10 that is produced in the slurry producing step S11 and
thickening the slurry 10. In addition, the film thickness of the
strip-shaped green sheet 20 produced in this step is set in
consideration of a film thickness of the silicon nitride sintered
body 40 to be finally produced. Along with this, regulation
conditions (a distance from the belt 114, and the like) of the
doctor blade 124 for regulating the slurry 10 to have the defined
film thickness are also set in consideration of the film thickness
of the silicon nitride sintered body 40 to be finally produced.
Here, the film thickness of the strip-shaped green sheet 20 to be
set is set to, for example, 0.25 mm to 1 mm depending on the film
thickness of the silicon nitride sintered body 40 to be finally
produced, but 0.25 mm to 0.9 mm is preferable, and 0.25 to 0.8 mm
is more preferable.
[0050] The above is the description of the molding step.
Cutting Step
[0051] Next, a cutting step S13 will be described. This step is a
step of cutting the strip-shaped green sheet 20 to produce the
single sheet-type green sheet 30 as illustrated in FIG. 2B.
[0052] This step is performed using a cutting device 200
illustrated in FIG. 2B. Here, the cutting device 200 is provided
with a sheet transporting mechanism 210 and a cutting portion
220.
[0053] The sheet transporting mechanism 210 includes a supporting
portion 212, a first transporting portion 214, and a second
transporting portion 216. The supporting portion 212 rotatably
supports the roller 112B (see FIGS. 2A and 2B) with the
strip-shaped green sheet 20 produced in the molding step being
wound around an outer peripheral surface thereof. The first
transporting portion 214 adjusts the posture of the strip-shaped
green sheet 20 transported from the supporting portion 212 and
transports the strip-shaped green sheet 20 to the cutting portion
220 along the X direction (along the longitudinal direction of the
strip-shaped green sheet 20). The second transporting portion 216
transports the single sheet-type green sheet 30 produced by the
strip-shaped green sheet 20 being cut at the cutting portion 220 to
further downstream (to the X direction).
[0054] The cutting portion 220 includes a housing 222, an
irradiation portion 224, and a moving mechanism 226. The
irradiation portion 224 emits a carbon dioxide laser beam LB (an
example of a laser beam) as an example. The moving mechanism 226
causes the irradiation portion 224 to scan the strip-shaped green
sheet 20 from one end to the other end thereof in the lateral
direction (the Y direction in the drawing). The irradiation portion
224 and the moving mechanism 226 are mounted in the housing
222.
[0055] Then, in the cutting device 200 of the present embodiment,
the sheet transporting mechanism 210 allows the strip-shaped green
sheet 20 to be transported by the length of the single sheet-type
green sheet 30 and to stop the transportation of the strip-shaped
green sheet 20, and the strip-shaped green sheet 20 is cut by the
cutting portion 220. In this case, the cutting portion 220 causes
the irradiation portion 224 to emit the carbon dioxide laser beam
LB while causing the moving mechanism 226 to move the irradiation
portion 224 from one end side to the other end side of the
strip-shaped green sheet 20 in the lateral direction along the Y
direction. In addition, the irradiation portion 224 that performs
the scanning through the moving mechanism 226 intermittently emits
the carbon dioxide laser beam LB. Here, "intermittently" means to
repeat irradiation for a certain time period and non-irradiation
for a certain time period. Therefore, the moving mechanism 226
causes the irradiation portion 224 to move and stop repeatedly so
as to cause the irradiation portion 224 to perform the
scanning.
[0056] As described above, in this step, the strip-shaped green
sheet 20 is irradiated with the carbon dioxide laser beam LB to cut
the strip-shaped green sheet 20, so that the single sheet-type
green sheet 30 is obtained. In addition, this step also includes a
step of transporting the strip-shaped green sheet 20 by the sheet
transporting mechanism 210 (transporting step), and a step of
cutting the strip-shaped green sheet 20 by the cutting portion 220
to obtain the single sheet-type green sheet 30 (irradiation
step).
[0057] In the explanation of this step, an example of a laser beam
LB is the carbon dioxide laser beam LB. However, a laser beam
having a wavelength different from the wavelength of the carbon
dioxide laser beam LB may be used as long as the light beam emitted
from the irradiation portion 224 is a laser beam. For example, an
infrared laser beam LB (IR laser beam LB), an ultraviolet laser
beam LB (UV laser beam LB), and the like may be used. However, as
in this step, the laser beam LB emitted from the irradiation
portion 224 is preferably a carbon dioxide laser beam LB. The
reason for this will be described in the description of Example
described later. FIG. 3 is an SEM image of a cut surface 32 (an
example of a laser cut surface) of the single sheet-type green
sheet 30 produced by the cutting step of the present embodiment,
and details of this SEM image will also be described later in the
description of Example described later.
[0058] The above is the description of the cutting step.
Depositing Step
[0059] Next, a depositing step S14 will be described. This step is
a step of laminating a plurality of the strip-shaped green sheet 20
in the film thickness direction as illustrated in FIG. 2D. This
step is a step performed for efficiently sintering the single
sheet-type green sheet 30 in the subsequent step (sintering step
S16).
[0060] In this step, as illustrated in FIG. 2D, the plurality of
the single sheet-type green sheets 30 are deposited by interposing
a non-reactive powder layer (not illustrated) therebetween, which
will be described later. Here, in a case where the number of the
single sheet-type green sheets 30 to be laminated is small, the
number of sheets that can be processed in a sintering furnace (not
illustrated) at one time in the subsequent sintering step S16 is
small (the production efficiency decreases). On the other hand, in
a case where the number of the single sheet-type green sheets 30 to
be laminated is large, binders contained in the single sheet-type
green sheets 30 are unlikely to be decomposed in the next step
(degreasing step S15). According to the above reasons, the number
of the single sheet-type green sheets 30 to be laminated in this
step is 8 to 100, and preferably 30 to 70.
[0061] The non-reactive powder layer of the present embodiment is,
for example, a boron nitride powder layer (BN powder layer) having
a film thickness of about 1 .mu.m to 20 .mu.m. The BN powder layer
has a function of easily separating the silicon nitride sintered
body 40 after the subsequent step (sintering step S16). The BN
powder layer is applied as a slurry of BN powder on one surface of
each single sheet-type green sheet 30 by, for example, spraying,
brush coating, roll coater, screen printing, or the like. The BN
powder has a purity of 85% or more, and preferably has an average
particle diameter of 1 .mu.m to 20 .mu.m.
[0062] The above is the description of the depositing step.
Degreasing Step
[0063] Next, a degreasing step S15 will be described. This step is
a step of degreasing a binder and a plasticizer contained in the
single sheet-type green sheet 30 before the next step (sintering
step S16).
[0064] In this step, as an example, a plurality of the single
sheet-type green sheets 30 (see FIG. 2D) laminated in the
depositing step S14 are held in a temperature environment of
450.degree. C. to 750.degree. C. for 0.5 hours to 20 hours. As a
result, the binders and the plasticizers contained in the plurality
of the single sheet-type green sheets 30 are degreased.
[0065] The above is the description of the degreasing step.
Sintering Step
[0066] Next, a sintering step S16 will be described. This step is a
step of sintering the plurality of the single sheet-type green
sheets 30 laminated in the depositing step S14 (hereinafter,
referred to as the plurality of single sheet-type green sheets 30
in FIG. 2D) using a sintering device (not illustrated).
[0067] The sintering device is provided with a sintering furnace
and a control device that controls a temperature of the sintering
furnace. The sintering furnace includes a heater and a thermometer.
Then, in this step, the plurality of single sheet-type green sheets
30 illustrated in FIG. 2D are accommodated in the sintering
furnace, and the heater as an example is controlled by the control
device according to a temperature control program described
later.
[0068] Here, the temperature control program is a program that is
stored in a storage device (for example, ROM or the like) included
in the control device, and that controls the temperature of the
heater while referring to a temperature profile based on
temperature information of the thermometer included in the
sintering furnace (for example, PID control or the like).
Specifically, the temperature control program is a program setting
the temperature profile in the sintering furnace as a profile that
is formed with a temperature increasing region with a gradually
heating region, a temperature maintaining region, and a cooling
region, which proceed in the described order. Hereinafter, the
technical significance of the gradually heating region, the
temperature maintaining region, and the cooling region will be
described.
Temperature Maintaining Region
[0069] The temperature maintaining region is a temperature region
where rearrangement of silicon nitride particles, production of
.beta.-type silicon nitride crystals, and grain growth of silicon
nitride crystals are enhanced from the liquid phase produced in the
gradually heating region to further densify the sintered body.
[0070] The temperature in the temperature maintaining region is
preferably set to a temperature within the range of 1600.degree. C.
to 2000.degree. C. and the maintaining time is preferably 1 hour to
30 hours in consideration of a size and an aspect ratio (a ratio of
the major axis to the minor axis) of .beta.-type silicon nitride
particles, formation of holes due to volatilization of the
sintering aid, and the like. In a case where the temperature in the
temperature maintaining region is lower than 1600.degree. C., the
silicon nitride sintered body 40 is difficult to be densified. On
the other hand, in a case where the temperature higher than
2000.degree. C., the sintering aid volatilizes and the silicon
nitride decomposes violently, which makes the silicon nitride
sintered body 40 difficult to be densified. In a case where the
temperature in the temperature maintaining region is the
temperature within the range of 1600.degree. C. to 2000.degree. C.,
a heating temperature in the temperature maintaining region may be
set to change with time (for example, the temperature is gradually
increased).
[0071] Here, the temperature in the temperature maintaining region
is more preferably a temperature in the range of 1750.degree. C. to
1950.degree. C., and even more preferably a temperature in the
range of 1790.degree. C. to 1890.degree. C. Furthermore, the
temperature in the temperature maintaining region is preferably
equal to or 50.degree. C. higher than the upper limit of a
temperature in the gradually heating region, and more preferably
equal to or 100.degree. C. to 300.degree. C. higher than the upper
limit thereof. The maintaining time of the temperature maintaining
region is more preferably 2 hours to 20 hours, and even more
preferably 3 hours to 10 hours.
[0072] The above is the description of the sintering step. In
addition, the above is the description of the method for
manufacturing the silicon nitride sintered body 40 of the present
embodiment.
Example
[0073] Next, Example of the present embodiment (tests for deriving
the preferable form of the present embodiment) will be described
with reference to the drawings. Here, the tests for which the
preferable form of the present embodiment has been derived are a
first test, a second test, and a third test described below. The
effects of the present embodiment described above will be described
inconsideration of a result of each test described later.
First Test
[0074] Hereinafter, a first test will be described.
Method of First Test
[0075] In this test, a test of observing a photograph of a cut
section of the single sheet-type green sheet 30 produced in the
cutting step S13 of the present embodiment and photographs of cut
sections of single sheet-type green sheets produced in cutting
steps of comparative examples (a first to fourth comparative
examples) described below was performed. Specifically, cut sections
(cut surfaces and peripheral portions thereof) of a sample of the
single sheet-type green sheet 30 of the present embodiment and
samples of the single sheet-type green sheets of the first to
fourth comparative examples each were photographed from the lower
surface side, and observed. Then, the enlarged photograph of each
sample was observed to confirm the presence or absence of cutting
chips and burrs on the cut surface. As a result, the sample with at
least one of cutting chips or burrs was regarded as unacceptable,
and the sample without both was regarded as acceptable.
[0076] Here, the single sheet-type green sheet (see FIGS. 5A and
5B) of the first comparative example was produced such that the
strip-shaped green sheet 20 was cut by an extrusion blade (not
illustrated). The single sheet-type green sheet (see FIG. 6) of the
second comparative example was produced such that the strip-shaped
green sheet 20 was cut by a Thomson blade (not illustrated). The
single sheet-type green sheet (see FIG. 7) of the third comparative
example was produced such that the strip-shaped green sheet 20 was
cut by shirring (not illustrated). The single sheet-type green
sheet (see FIG. 8) of the fourth comparative example was produced
such that the strip-shaped green sheet 20 was cut by an ultrasonic
cutter (not illustrated). The single sheet-type green sheet 30 of
the present embodiment was produced by using an infrared laser (IR
laser) provided with the irradiation portion 224 (see FIGS. 2B and
2C).
Result and Discussion of First Test
[0077] FIG. 4 is a table summarizing conditions and observation
results of each sample of this test.
[0078] The first to fourth comparative examples were all
unacceptable. Here, in the first comparative example (extrusion
blade), cutting chips were observed (see FIGS. 4, 5A, and 5B). In
the second comparative example (Thomson blade), burrs were observed
(see FIGS. 4 and 6). In the third comparative example (shirring),
cutting chips were observed (see FIGS. 4 and 7). In the fourth
comparative example (ultrasonic cutter), cutting chips were
observed (see FIGS. 4 and 8).
[0079] The present embodiment (laser) was acceptable (see FIGS. 3,
4, and 9).
[0080] It is presumed that fracture surfaces were generated during
the cutting since all of the first to fourth comparative examples
were produced by a contact-type cutting unit. On the other hand, it
is presumed that a fracture surface was not generated (or hardly
generated) during the cutting as in the case of the first to fourth
comparative examples since the present embodiment is produced by a
non-contact-type cutting unit.
[0081] As described above, according to the method for
manufacturing the single sheet-type green sheet 30 of the present
embodiment, chips from the cut surface are not generated (or hardly
generated) in a case where the strip-shaped green sheet 20 is cut
to obtain the single sheet-type green sheet 30. In addition,
according to the method for manufacturing the single sheet-type
green sheet 30 of the present embodiment, the fracture surface is
not generated (or hardly generated) and cracks near the cut surface
also are not generated (or hardly generated) during the cutting. In
the method for manufacturing the single sheet-type green sheet 30
of the present embodiment, metal powder from the cutting blade is
not generated since the cutting blade is not used during the
cutting. Along with these, according to the method for
manufacturing the silicon nitride sintered body 40 of the present
embodiment, the yield is higher than that in the case where the
contact-type cutting unit is used in the cutting step.
[0082] The above is the description of the first test.
Second Test
[0083] Next, the second test will be described.
Method of Second Test
[0084] In this test, the single sheet-type green sheet 30 was
produced using a carbon dioxide laser, an infrared laser (IR
laser), and an ultraviolet laser (IJV laser) as the irradiation
portion 224 (see FIGS. 2B and 2C), the cut surface 32 (see FIG. 2B
and FIG. 3) was observed, and time periods required for cutting
operations (processing time) were compared to each other.
[0085] Here, center wavelengths of a laser beam LB of the carbon
dioxide laser were 9360 nm and 10600 nm, a center wavelength of a
laser beam LB of the infrared laser was 1064 nm, and a center
wavelength of the laser beam LB of the ultraviolet laser was 355
nm.
Result and Discussion of Second Test
[0086] Cutting chips and burrs were not observed on the cut surface
32 (laser cut surfaces) in any cases (a result is the same result
as in the first test illustrated in Table of FIG. 4). In addition,
the processing time at the same output was shorter in the order of
carbon dioxide laser, infrared laser, and ultraviolet laser (a
graph of the test result or the like is not described).
[0087] Therefore, in the cutting step S13 of the present
embodiment, chips and burrs from the cut surface 32 are not
generated (or hardly generated) even using any lasers as the
irradiation portion 224. However, from the viewpoint of shortening
the processing time, it can be said that the carbon dioxide laser,
the infrared laser, and the ultraviolet laser are preferably used
in this order.
[0088] Regarding the infrared laser and the ultraviolet laser, the
former has a shorter processing speed than that of the latter, and
the reason is presumed to be as follows. That is, it is presumed
that thermal processing with respect to the cutting of the
strip-shaped green sheet 20 is preferentially performed before
optical processing, and the laser beam LB from the infrared laser
is more easily converted due to heat than the laser beam LB from
the ultraviolet laser. Here, a bandgap of the strip-shaped green
sheet 20 is about 5.0 eV, whereas a bandgap of the ultraviolet
laser is 3.5 eV corresponding to the center wavelength of 355 nm.
Therefore, it is presumed that the laser beam LB from the
ultraviolet laser is difficult to sufficiently photoexcite the
strip-shaped green sheet 20.
[0089] The above is the description of the second test.
Third Test
[0090] Next, the third test will be described.
Method of Third Test
[0091] In this test, samples each of which was obtained such that
three single sheet-type green sheets 30 that have been cut in the
cutting step S13 of the present embodiment were sintered in the
sintering step S16, and samples each of which was obtained such
that three single sheet-type green sheets that have been cut using
press processing (extrusion blade) in the cutting step were
sintered in the sintering step S16 were produced. Subsequently,
surface roughnesses Ra, Ry, and Rz of these samples were measured
based on JIS B 0601-1994.
[0092] Here, each of the carbon dioxide laser, the infrared laser,
and the ultraviolet laser was used for cutting each sample of the
present embodiment in the cutting step S13.
Result and Discussion of Third Test
[0093] Table in FIG. 10 summarizes conditions and measurement
results of the third test. This test is not a test for identifying
the quality of each sample from the measurement results of the
surface roughnesses Ra, Ry, and Rz of each sample. However, from
the result of the first test, it can be said that the silicon
nitride sintered body 40 manufactured in the steps including the
cutting step S13 of the present embodiment satisfies the
measurement result in each sample using the carbon dioxide laser,
the infrared laser, and the ultraviolet laser in Table of FIG.
10.
[0094] Therefore, it can be said that in the silicon nitride
sintered body 40 of the present embodiment, the surface roughness
Ra of the end surface 42 (see FIG. 2D, in other words, the laser
cut surface after sintering or the sintered surface of the laser
cut surface) is equal to or greater than 0.5 .mu.m and equal to or
smaller than 2.0 .mu.m, and the surface roughness Rz of the end
surface 42 is preferably equal to or greater than 5.0 .mu.m and
equal to or smaller than 12.0 .mu.m. Along with this, it can be
said that in the single sheet-type green sheet 30 of the present
embodiment, the surface roughness Ra of the cut surface 32 (see
FIGS. 2B and 3) is equal to or greater than 0.5 .mu.m and equal to
or smaller than 2.0 .mu.m, and the surface roughness Rz of the cut
surface 32 is preferably equal to or greater than 5.0 .mu.m and
equal to or smaller than 12.0 .mu.m.
[0095] The above is the description of Example of the present
embodiment.
[0096] As described above, the present embodiment has been
described as an example of the present invention, but the present
invention is not limited to the present embodiment. The technical
scope of the present invention also includes, for example, the
following forms (modifications).
[0097] For example, in the description of the present embodiment,
an example of the ceramic powder has been described as silicon
nitride. However, an example of the ceramic powder may be another
ceramic powder. For example, aluminum nitride may be used.
[0098] In the description of the molding step S12 of the present
embodiment, it is assumed that the molding step S12 is performed by
doctor blade molding. However, as long as the slurry 10 can be
molded into the strip-shaped green sheet 20, another method may be
adopted as the molding method. For example, extrusion molding may
be used.
[0099] In the description of the cutting step S13 of the present
embodiment, the strip-shaped green sheet 20 is cut while the
irradiation portion 224 moves from one end side to the other end
side of the strip-shaped green sheet 20 in the lateral direction.
However, as long as the single sheet-type green sheet 30 can be
obtained by cutting the strip-shaped green sheet 20 as a result, a
cut portion of the strip-shaped green sheet 20 may not be a linear
portion crossing over from one end side to the other end side of
the strip-shaped green sheet 20 in the lateral direction as in the
case of the present embodiment. For example, the strip-shaped green
sheet 20 may be cut such that a hole that has a shape of the single
sheet-type green sheet 30 is made in the strip-shaped green sheet
20 to separate (or hollow out) the single sheet-type green sheet 30
from the strip-shaped green sheet 20. That is, the single
sheet-type green sheet 30 obtained by cutting the strip-shaped
green sheet 20 may have at least a part of all end surfaces thereof
as a cut surface.
[0100] Priority is claimed on Japanese Patent Application No.
2019-013761, filed Jan. 30, 2019, the disclosure of which is
incorporated herein its entirety by reference.
* * * * *