U.S. patent application number 16/657291 was filed with the patent office on 2021-04-22 for waveguide bends with mode confinement.
The applicant listed for this patent is GLOBALFOUNDRIES U.S.Inc.. Invention is credited to Yusheng Bian, Ajey Poovannummoottil Jacob.
Application Number | 20210116638 16/657291 |
Document ID | / |
Family ID | 1000004438602 |
Filed Date | 2021-04-22 |

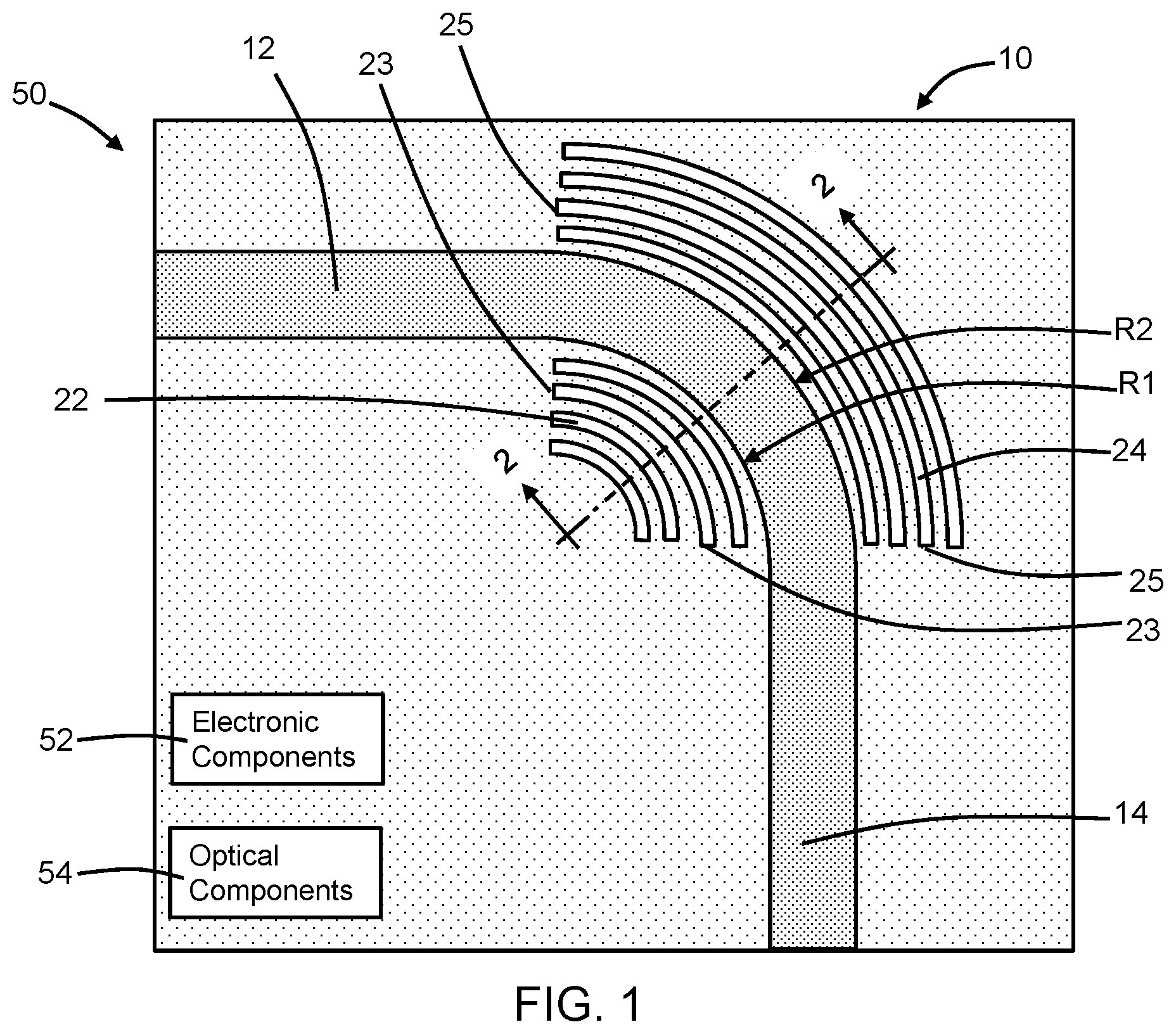

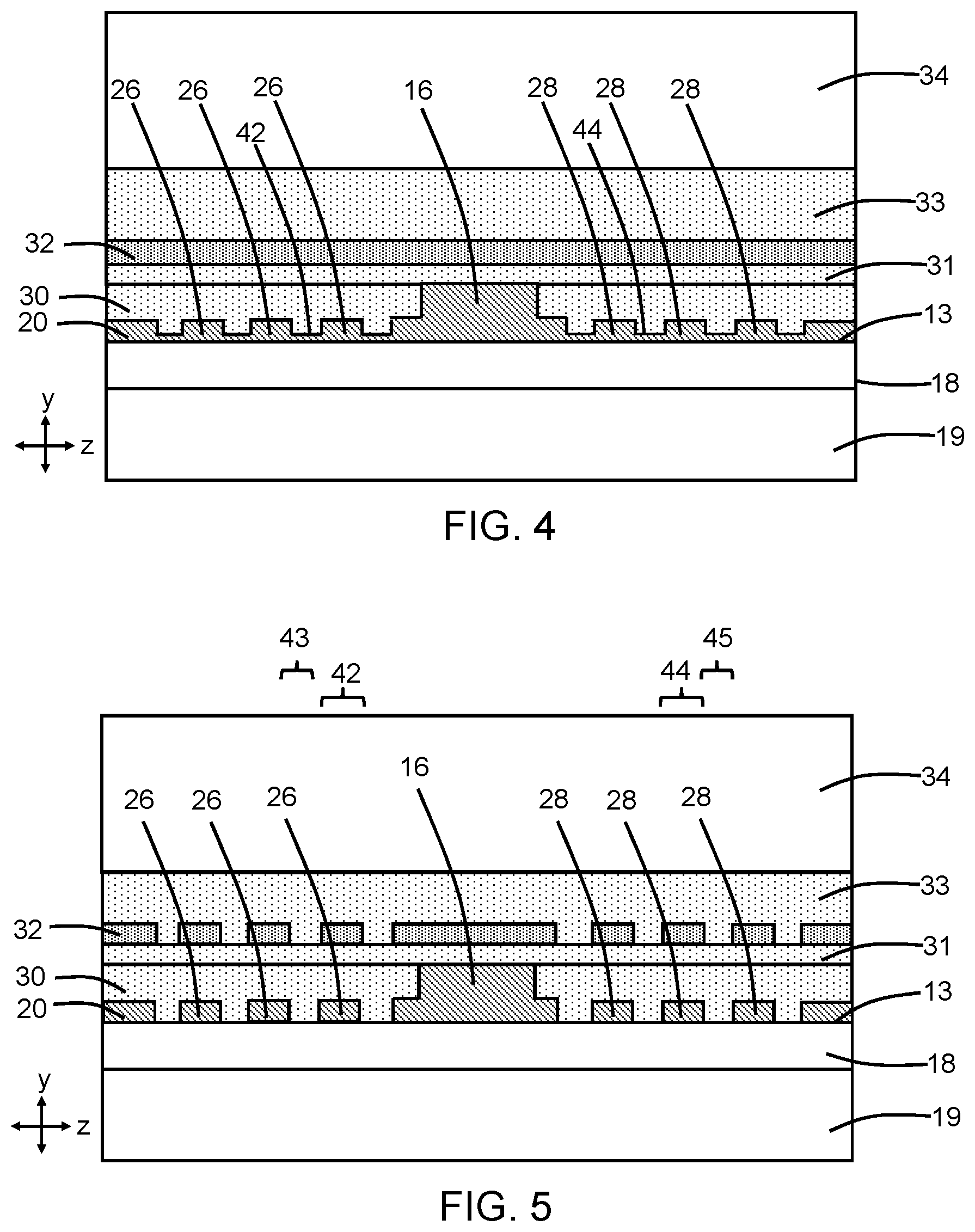

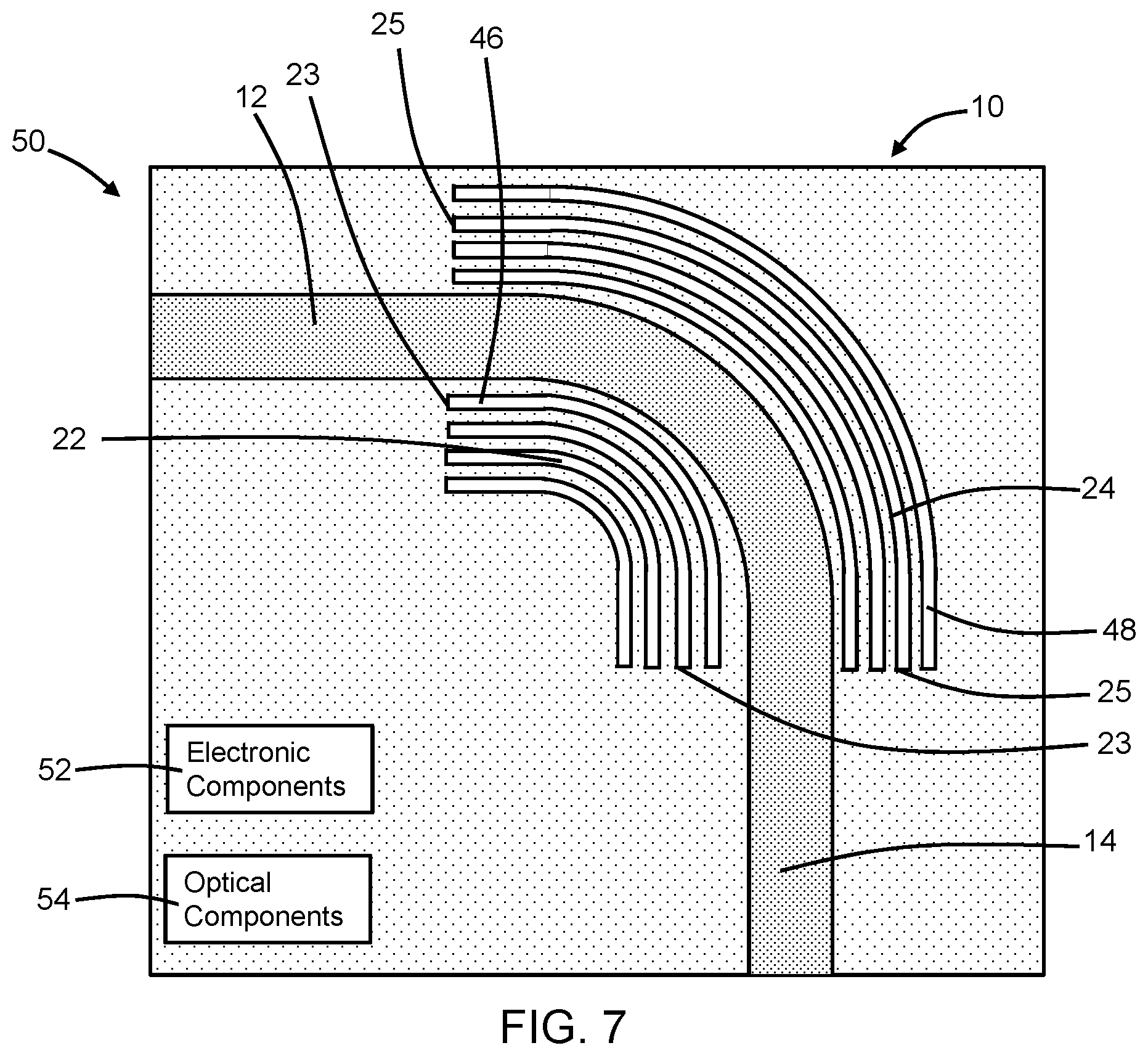
United States Patent
Application |
20210116638 |
Kind Code |
A1 |
Bian; Yusheng ; et
al. |
April 22, 2021 |
WAVEGUIDE BENDS WITH MODE CONFINEMENT
Abstract
Structures for a waveguide bend and methods of fabricating a
structure for a waveguide bend. A waveguide bend is connected to a
waveguide core. A slab layer, which is thinner than the waveguide
bend, is coupled to the waveguide core and the waveguide bend. The
slab layer includes a first curved opening and a second curved
opening that is positioned between the first curved opening and a
side surface of the waveguide bend. A section of the slab layer is
positioned between the first and second curved openings. The first
curved opening has a first radius, and the second curved opening
has a second radius that is greater than or less than the first
radius of the first curved opening.
Inventors: |
Bian; Yusheng; (Ballston
Lake, NY) ; Jacob; Ajey Poovannummoottil;
(Watervliet, NY) |
|
Applicant: |
Name |
City |
State |
Country |
Type |
GLOBALFOUNDRIES U.S.Inc. |
Santa Clara |
CA |
US |
|
|
Family ID: |
1000004438602 |
Appl. No.: |
16/657291 |
Filed: |
October 18, 2019 |
Current U.S.
Class: |
1/1 |
Current CPC
Class: |
G02B 6/125 20130101;
G02B 2006/12035 20130101; G02B 6/13 20130101; G02B 6/12004
20130101; G02B 2006/12147 20130101 |
International
Class: |
G02B 6/125 20060101
G02B006/125; G02B 6/12 20060101 G02B006/12; G02B 6/13 20060101
G02B006/13 |
Claims
1. A structure comprising: a first dielectric layer; a waveguide
core positioned on the first dielectric layer; a waveguide bend
positioned on the first dielectric layer, the waveguide bend
connected to the waveguide core, and the waveguide bend having a
first side surface; and a slab layer positioned on the first
dielectric layer, the slab layer directly connected to a lowermost
portion of the waveguide core and a lowermost portion of the
waveguide bend, the slab layer being thinner than the waveguide
bend, the slab layer including a first curved opening, a second
curved opening positioned between the first curved opening and the
first side surface of the waveguide bend, and a first section
positioned between the first curved opening and the second curved
opening, the first curved opening having a first radius, and the
second curved opening having a second radius that is greater than
or less than the first radius of the first curved opening.
2. The structure of claim 1 wherein the waveguide core, the
waveguide bend, and the slab layer are comprised of single-crystal
silicon.
3. The structure of claim 1 wherein the first side surface is
located at an inner convex side of the waveguide bend, and the
second radius of the second curved opening is greater than the
first radius of the first curved opening.
4. The structure of claim 1 wherein the first side surface is
located at an outer concave side of the waveguide bend, and the
second radius of the second curved opening is less than the first
radius of the first curved opening.
5. The structure of claim 1 wherein the waveguide bend includes a
second side surface, the slab layer includes a third curved
opening, a fourth curved opening positioned between the third
curved opening and the second side surface of the waveguide bend,
and a second section positioned between the third curved opening
and the fourth curved opening, the third curved opening has a third
radius, and the fourth curved opening has a fourth radius that
differs from the third radius of the third curved opening.
6. The structure of claim 5 wherein the third radius of the third
curved opening is greater than the fourth radius of the fourth
curved opening, and the second radius of the second curved opening
is less than the first radius of the first curved opening.
7. The structure of claim 6 wherein the third curved opening and
the fourth curved opening are concentric, and the first curved
opening and the second curved opening are concentric.
8. The structure of claim 1 wherein the first curved opening and
the second curved opening are concentric.
9. The structure of claim 1 wherein the first curved opening and
the second curved opening extend fully through the slab layer.
10. The structure of claim 1 wherein the first curved opening and
the second curved opening extend fully through the slab layer to
the first dielectric layer.
11. The structure of claim 1 wherein the first curved opening and
the second curved opening extend partially through the slab
layer.
12. The structure of claim 1 further comprising: a second
dielectric layer over the waveguide bend, wherein the second
dielectric layer includes a first curved opening and a second
curved opening over the slab layer, and the first curved opening
and the second curved opening in the second dielectric layer are
laterally spaced from the first side surface of the waveguide
bend.
13. The structure of claim 12 wherein the first curved opening in
the second dielectric layer is positioned directly over the first
curved opening in the slab layer, and the second curved opening in
the second dielectric layer is positioned directly over the second
curved opening in the slab layer.
14. The structure of claim 1 wherein the first curved opening and
the second curved opening are filled by dielectric material.
15. The structure of claim 1 wherein the first curved opening and
the second curved opening include air gaps.
16. The structure of claim 1 wherein the slab layer includes a
first extension opening that is appended to the first curved
opening and a second extension opening that is appended to the
second curved opening, and the first extension opening and the
second extension opening each extend substantially parallel to the
waveguide core.
17. A method comprising: forming a waveguide core, a waveguide bend
connected to the waveguide core, and a slab layer directly
connected to a lowermost portion of the waveguide core and a
lowermost portion of the waveguide bend; and forming a first curved
opening in the slab layer and a second curved opening in the slab
layer that is positioned between the first curved opening and a
first side surface of the waveguide bend, wherein the waveguide
core, the waveguide bend, and the slab layer are positioned on a
dielectric layer, the slab layer is thinner than the waveguide
bend, a first section of the slab layer is positioned between the
first curved opening and the second curved opening, and the second
curved opening has a second radius that is greater than or less
than a first radius of the first curved opening.
18. The method of claim 17 wherein the second radius of the second
curved opening is less than the first radius of the first curved
opening.
19. The method of claim 17 wherein the second radius of the second
curved opening is greater than the first radius of the first curved
opening.
20. The method of claim 17 wherein the waveguide bend includes a
second side surface, the slab layer includes a third curved
opening, a fourth curved opening positioned between the third
curved opening and the second side surface of the waveguide bend,
and a second section positioned between the third curved opening
and the fourth curved opening, the third curved opening has a third
radius, and the fourth curved opening has a fourth radius that
differs from the third radius of the third curved opening.
Description
BACKGROUND
[0001] The present invention relates to photonics chips and, more
specifically, to structures for a waveguide bend and methods of
fabricating a structure for a waveguide bend.
[0002] Photonics chips are used in many applications and systems
such as data communication systems and data computation systems. A
photonics chip integrates optical components, such as waveguides,
optical switches, directional couplers, and waveguide bends, and
electronic components, such as field-effect transistors, into a
unified platform. Among other factors, layout area, cost, and
operational overhead may be reduced by the fabrication of both
types of components on a shared chip.
[0003] On-chip communication and sensing may rely on guiding
optical signals through waveguides on the photonics chip to other
optical components. Optical signals may propagate as
electromagnetic waves within waveguides using several different
modes that are characterized by distinct properties. Transverse
electric (TE) modes are dependent upon transverse electric waves in
which the electric field vector is oriented perpendicular to the
direction of propagation. Transverse magnetic (TM) modes are
dependent upon transverse magnetic waves in which the magnetic
field vector is oriented perpendicular to the direction of
propagation.
[0004] Optical signals guided by a waveguide bend may experience
bending loss. Bending loss may be reduced by increasing the bending
radius during the design phase. However, increasing the bending
radius increases the form factor of the waveguide bend. A waveguide
bend with a core fabricated from single-crystal silicon may include
a slab layer of partially-etched single-crystal silicon coupled to
the base of the core. Bending loss may be exacerbated due to mode
leakage into the slab layer.
[0005] Improved waveguide bends and methods of fabricating
waveguide bends are needed.
SUMMARY
[0006] In an embodiment of the invention, a structure includes a
waveguide core and a waveguide bend that is connected to the
waveguide core. A slab layer, which is thinner than the waveguide
bend, is coupled to the waveguide core and the waveguide bend. The
slab layer includes a first curved opening and a second curved
opening positioned between the first curved opening and a side
surface of the waveguide bend. A section of the slab layer is
positioned between the first and second curved openings in the slab
layer. The first curved opening has a first radius, and the second
curved opening has a second radius that is greater than or less
than the first radius of the first curved opening.
[0007] In an embodiment of the invention, a method includes forming
a waveguide core, a waveguide bend that is connected to the
waveguide core, and a slab layer coupled to the waveguide core and
the waveguide bend. The method further includes forming a first
curved opening in the slab layer and a second curved opening in the
slab layer that is positioned between the first curved opening and
a side surface of the waveguide bend. The slab layer is thinner
than the waveguide bend. A section of the slab layer is positioned
between the first and second curved openings in the slab layer. The
second curved opening has a second radius that is greater than or
less than a first radius of the first curved opening.
BRIEF DESCRIPTION OF THE DRAWINGS
[0008] The accompanying drawings, which are incorporated in and
constitute a part of this specification, illustrate various
embodiments of the invention and, together with a general
description of the invention given above and the detailed
description of the embodiments given below, serve to explain the
embodiments of the invention.
[0009] FIG. 1 is a top view of a structure at a fabrication stage
of a processing method in accordance with embodiments of the
invention.
[0010] FIG. 2 is a cross-sectional view of the structure taken
generally along line 2-2 in FIG. 1.
[0011] FIG. 3 is a cross-sectional view of the structure at a
fabrication stage of the processing method subsequent to FIG.
2.
[0012] FIGS. 4-6 are cross-sectional views similar to FIG. 3 of
structures in accordance with alternative embodiments of the
invention.
[0013] FIG. 7 is a top view similar to FIG. 1 of a structure in
accordance with alternative embodiments of the invention.
DETAILED DESCRIPTION
[0014] With reference to FIGS. 1, 2 and in accordance with
embodiments of the invention, a structure 10 includes a waveguide
core 12, a waveguide core 14, and a waveguide bend 16 that are
positioned over a top surface 13 of a dielectric layer 18. The
dielectric layer 18 may be composed of an electrical insulator,
such as silicon dioxide. In an embodiment, the dielectric layer 18
may be the buried dielectric layer of a silicon-on-insulator (SOI)
wafer. The waveguide core 12, waveguide core 14, and waveguide bend
16 may be composed of a single-crystal semiconductor material, such
as single-crystal silicon. In an embodiment, the single-crystal
semiconductor material may be single-crystal silicon from the
device layer of the silicon-on-insulator wafer that is patterned to
form the waveguide core 12, waveguide core 14, and the waveguide
bend 16. The SOI wafer may further include a semiconductor
substrate 19 on which the dielectric layer 18 is arranged.
[0015] A slab layer 20 surrounds the waveguide core 12, waveguide
core 14, and waveguide bend 16. The slab layer 20 is directly
connected to the lowermost portions of the waveguide core 12,
waveguide core 14, and waveguide bend 16, and is located on both
sides of the waveguide core 12, waveguide core 14, and waveguide
bend 16. The slab layer 20 may be composed of single-crystal
semiconductor material (e.g., single-crystal silicon) and is
positioned over the dielectric layer 18. The slab layer 20 has a
thickness in the vertical direction (i.e., y-direction) that is
less than the thickness of the waveguide core 12, waveguide core
14, and waveguide bend 16. The waveguide core 12, waveguide core
14, waveguide bend 16, and slab layer 20 may directly contact the
dielectric layer 18.
[0016] The waveguide bend 16 has one end connected to the waveguide
core 12, and the waveguide bend 16 has an opposite end connected to
the waveguide core 14 such that the waveguide bend 16 directly
connects the waveguide core 12 with the waveguide core 14. The ends
of the waveguide bend 16 may be defined as the locations at which
the curvature ceases. The waveguide bend 16 functions to change the
direction of guided optical signals from an initial direction
within waveguide core 12 to a different direction within waveguide
core 14. The waveguide bend 16 may have a curved inner side surface
15 with an inner radius, R1, and a curved outer side surface 17
with an outer radius, R2, that is greater than the inner radius,
R1. The waveguide bend 16 may curve in an arc having a central
angle equal to 90.degree., although other central angles (e.g.,
45.degree. or 180.degree.) are contemplated. The curved inner side
surface 15 is located on an inner concave side of the waveguide
bend 16, and the curved outer side surface 17 is located on an
outer convex side of the waveguide bend 16.
[0017] The structure 10 further includes a series of curved
openings 22 that are laterally positioned in the section of the
slab layer 20 interior of the curved inner side surface 15 of the
waveguide bend 16 and a series of curved openings 24 that are
laterally positioned in the section of the slab layer 20 exterior
of the curved outer side surface 17 of the waveguide bend 16. In
the representative embodiment, each of the curved openings 22
extends through the full thickness of the slab layer 20, and each
of the curved openings 24 extends through the full thickness of the
slab layer 20. The waveguide core 12, waveguide core 14, and
waveguide bend 16 are free of openings similar to curved openings
22, 24.
[0018] The curved openings 22 have different respective radii, and
the curved openings 24 also have different respective radii. A
curved section 26 of the slab layer 20 is arranged as a strip
between each adjacent pair of the curved openings 22 and between
the waveguide bend 16 and the curved opening 22 nearest to the
curved inner side surface 15. A curved section 28 of the slab layer
20 is also arranged as a strip between each adjacent pair of the
curved openings 24 and between the waveguide bend 16 and the curved
opening 24 nearest to the curved outer side surface 17.
[0019] Each of the curved openings 22 has a radius that is less
than the radius of the curved inner side surface 15, and the radii
of the curved openings 22 progressively decrease with increasing
distance from the curved inner side surface 15. Each of the curved
openings 24 has a radius that is greater than the radius of the
curved outer side surface 17, and the radii of the curved openings
24 progressively increase with increasing distance from the curved
outer side surface 17. In an embodiment, the curved openings 22 may
be concentric. In an embodiment, the curved openings 24 may be
concentric. In an embodiment, the curved openings 22 may be
concentric with each other and may also be concentric with the
curved inner side surface 15 of the waveguide bend 16. In an
embodiment, the curved openings 24 may be concentric. In an
embodiment, the curved openings 24 may be concentric with each
other and may also be concentric with the curved outer side surface
17 of the waveguide bend 16. The radii of the curved openings 24
are greater than the radii of the curved openings 22 such that the
waveguide bend 16 is laterally positioned in the space between the
curved openings 22 and the curved openings 24.
[0020] Each of the curved openings 22 has opposite terminating ends
23. In an embodiment, the curved openings 22 may each terminate at
the end 23 that is proximate to the end of the waveguide bend 16
that is connected to the waveguide core 12. Each of the curved
openings 24 has opposite terminating ends 25. In an embodiment, the
curved openings 24 may each terminate at the end 23 that is
proximate to the end of the waveguide bend 16 that is connected to
the waveguide core 14. In an embodiment, the curved openings 24 may
each terminate at the end 25 that is proximate to the end of the
waveguide bend 16 that is connected to the waveguide core 12. In an
embodiment, the curved openings 24 may each terminate at the end 25
that is proximate to the end of the waveguide bend 16 that is
connected to the waveguide core 14.
[0021] The curved sections 26 of the slab layer 20 and the curved
openings 22 provide a grating structure that has a given
periodicity or pitch in a direction transverse to the waveguide
bend 16. The curved sections 28 of the slab layer 20 and the curved
openings 24 provide another grating structure that also has a given
periodicity or pitch in the direction transverse to the waveguide
bend 16. The pitches of these different grating structures may be
either equal or unequal.
[0022] The curved sections 26 and/or the curved sections 28 of the
slab layer 20 may have a uniform width in a direction transverse to
the waveguide bend 16. In an alternative embodiment, the curved
sections 26 and/or the curved sections 28 of the slab layer 20 may
have a width that varies non-linearly with position in a direction
transverse to the waveguide bend 16. The non-linear widths may be
selected based on a non-linear function, such as a quadratic,
parabolic, or exponential function, in order to provide the
variation with position relative to the waveguide bend 16.
[0023] The curved sections 26 and/or the curved sections 28 of the
slab layer 20 may have constant radii over their respective arc
lengths. In an alternative embodiment, the curved sections 26
and/or the curved sections 28 of the slab layer 20 may have radii
that vary with position relative to the waveguide bend 16. For
example, the radius of each of the curved openings 22 may vary such
that the radius is smallest near the ends 23 of the curved openings
22 proximate to the end of the waveguide bend 16 that is connected
to the waveguide core 12 and the radius is greatest near the ends
23 of the curved openings 22 proximate to the end of the waveguide
bend 16 that is connected to the waveguide core 14. The waveguide
bend 16 has an inner radius at the curved inner side surface 15
that is greater than the radii of all of the curved openings 22.
The waveguide bend 16 has an outer radius at the curved outer side
surface 17 that is less than the radii of all of the curved
openings 24.
[0024] The proximity of the curved openings 22, 24 to the waveguide
bend 16 may function to push the mode field of guided optical
signals back into the waveguide bend 16. The improved confinement
may reduce bending loss by mitigating mode leakage into the slab
layer 20.
[0025] In an alternative embodiment, all of the curved openings 24
may be omitted such that only the curved openings 22 are present in
the slab layer 20 on one side of the waveguide bend 16. In an
alternative embodiment, all of the curved openings 22 may be
omitted such that only the curved openings 24 are present in the
slab layer 20 on one side of the waveguide bend 16.
[0026] The waveguide core 12, waveguide core 14, and waveguide bend
16 may be patterned from a layer of single-crystal semiconductor
material with lithography and etching processes. The etching
process is controlled and halted before penetrating through the
full thickness of the semiconductor layer such that the slab layer
20 is formed. In an embodiment, the waveguide core 12, waveguide
core 14, and waveguide bend 16 all have the same thickness in the
vertical direction (i.e., y-direction), and the slab layer 20 has a
smaller thickness. The curved openings 22, 24 may be patterned in
the slab layer 20 with lithography and etching processes. In the
representative embodiment, the curved openings 22, 24 may extend
through the full thickness of the slab layer 20 to the top surface
of the dielectric layer 18. In alternative embodiments, the
waveguide core 12, waveguide core 14, waveguide bend 16, and slab
layer 20 may be composed of a different material, such as silicon
nitride, than single-crystal semiconductor material.
[0027] With reference to FIG. 3 in which like reference numerals
refer to like features in FIG. 2 and at a subsequent fabrication
stage of the processing method, dielectric layers 30, 31, 32, 33
composed of respective dielectric materials are sequentially formed
over the waveguide core 12, waveguide core 14, waveguide bend 16,
and slab layer 20. The waveguide core 12, waveguide core 14,
waveguide bend 16, and slab layer 20 are embedded or buried in the
dielectric material of the dielectric layer 30. Portions of the
dielectric layer 30 may fully fill the curved openings 22 and the
curved openings 24 in the slab layer 20.
[0028] The dielectric layer 31 is positioned over the dielectric
layer 30, the dielectric layer 32 is positioned over the dielectric
layer 31, and the dielectric layer 33 is positioned over the
dielectric layer 31. The dielectric layer 30 may be composed of a
dielectric material, such as silicon dioxide, deposited by chemical
vapor deposition and planarized with, for example, chemical
mechanical polishing to remove topography. The dielectric layer 31
may be composed of dielectric material, such as silicon dioxide,
deposited by chemical vapor deposition or atomic layer deposition
over the dielectric layer 30. The dielectric layer 32 may be
composed of dielectric material, such as silicon nitride, deposited
by chemical vapor deposition or atomic layer deposition over the
dielectric layer 31. The dielectric layer 33 may be composed of
dielectric material, such as silicon dioxide, deposited by chemical
vapor deposition or atomic layer deposition over the dielectric
layer 32. In an embodiment, the dielectric layer 33 may be composed
of a dielectric material, such as silicon dioxide, deposited by
chemical vapor deposition using ozone and tetraethylorthosilicate
(TEOS) as reactants.
[0029] A back-end-of-line stack, generally indicated by reference
numeral 34, may be formed over the dielectric layer 33. The
back-end-of-line stack 34 may include one or more dielectric layers
composed of a dielectric material, such as silicon dioxide or a
low-k dielectric material, and metallization composed of a metal,
such as copper or cobalt, that is arranged as wiring in the one or
more dielectric layers.
[0030] The structure 10, in any of its embodiments described
herein, may be integrated into a photonics chip 50 (FIG. 1) that
includes electronic components 52 and optical components 54. For
example, the photonics chip 50 may integrate one or more
photodetectors representing optical components 54 that receive
optical signals carried by the structure 10 and convert those
optical signals into electrical signals that may be processed by
the electronic components 52. The electronic components 52 may
include field-effect transistors that are fabricated by CMOS
front-end-of-line processes using the device layer of the SOI
wafer.
[0031] With reference to FIG. 4 in which like reference numerals
refer to like features in FIG. 3 and in accordance with alternative
embodiments of the invention, the curved openings 22, 24 may only
extend partially through the slab layer 20. In this instance, the
etching process forming the curved openings 22, 24 is halted before
penetrating fully through the slab layer 20. Portions 36 of the
slab layer 20, which are thinner than the curved sections 26 of the
slab layer 20, remain intact inside the curved openings 22 and are
located adjacent to the dielectric layer 18. Similarly, portions 38
of the slab layer 20, which are thinner than the curved sections 28
of the slab layer 20, remain intact inside the curved openings 24
and are located adjacent to the dielectric layer 18.
[0032] With reference to FIG. 5 in which like reference numerals
refer to like features in FIG. 3 and in accordance with alternative
embodiments of the invention, the dielectric layer 32 may be
patterned with lithography and etching processes to provide curved
sections 42 and curved openings 43 between adjacent curved sections
42 that are displaced in a vertical direction and in a lateral
direction from the waveguide bend 16 offset inward from the curved
inner side surface 15 of the waveguide bend 16. The dielectric
layer 32 may also be patterned with lithography and etching
processes to provide curved sections 44 and curved openings 45
between adjacent curved sections 44 that are displaced in a
vertical direction and in a lateral direction from the waveguide
bend 16 outward from the curved outer side surface 17 of the
waveguide bend 16. The curved openings 43 forming the curved
sections 42 and the curved openings 43 and the curved sections 44
may extend through the full thickness of the dielectric layer 32
such that respective curved gratings are defined in the dielectric
layer 32. In an embodiment, the curved sections 42 and associated
curved openings 43 may be respectively positioned directly over the
curved sections 26 and the associated curved openings 22, and the
curved sections 44 and associated curved openings 45 may be
positioned directly over the curved sections 28 and the associated
curved openings 24.
[0033] With reference to FIG. 6 in which like reference numerals
refer to like features in FIG. 3 and in accordance with alternative
embodiments of the invention, the dielectric layer 30 may be
deposited such that the curved openings 22 and the curved openings
24 in the slab layer 20 are only partially filled with solid
dielectric material. The partial filling of the curved openings 22
may encapsulate air gaps 40 in the spaces provided between the
curved sections 26 of the slab layer 20. The partial filling of the
curved openings 24 may encapsulate air gaps 40 in the spaces
provided between the curved sections 28 of the slab layer 20. The
air gaps 40 may be surrounded by dielectric material from the
dielectric layer 03.
[0034] With reference to FIG. 7 in which like reference numerals
refer to like features in FIG. 1 and in accordance with alternative
embodiments of the invention, extension openings 46 may be formed
in the slab layer 20 and appended to the curved openings 22 to
relocate one or both of the ends 23, and extension openings 48 may
be formed in the slab layer 20 and appended to the curved openings
24 to relocate one or both of the ends 25. The extension openings
46 may be straight or substantially straight sections that extend
parallel or substantially parallel to the waveguide core 12, and
the extension openings 48 may be straight or substantially straight
sections that extend parallel or substantially parallel to the
waveguide core 14. The extension openings 46, 48 may be formed when
the curved openings 22, 24 are patterned.
[0035] The methods as described above are used in the fabrication
of integrated circuit chips. The resulting integrated circuit chips
can be distributed by the fabricator in raw wafer form (e.g., as a
single wafer that has multiple unpackaged chips), as a bare die, or
in a packaged form. The chip may be integrated with other chips,
discrete circuit elements, and/or other signal processing devices
as part of either an intermediate product or an end product. The
end product can be any product that includes integrated circuit
chips, such as computer products having a central processor or
smartphones.
[0036] References herein to terms modified by language of
approximation, such as "about", "approximately", and
"substantially", are not to be limited to the precise value
specified. The language of approximation may correspond to the
precision of an instrument used to measure the value and, unless
otherwise dependent on the precision of the instrument, may
indicate +/-10% of the stated value(s).
[0037] References herein to terms such as "vertical", "horizontal",
etc. are made by way of example, and not by way of limitation, to
establish a frame of reference. The term "horizontal" as used
herein is defined as a plane parallel to a conventional plane of a
semiconductor substrate, regardless of its actual three-dimensional
spatial orientation. The terms "vertical" and "normal" refer to a
direction perpendicular to the horizontal, as just defined. The
term "lateral" refers to a direction within the horizontal
plane.
[0038] A feature "connected" or "coupled" to or with another
feature may be directly connected or coupled to or with the other
feature or, instead, one or more intervening features may be
present. A feature may be "directly connected" or "directly
coupled" to or with another feature if intervening features are
absent. A feature may be "indirectly connected" or "indirectly
coupled" to or with another feature if at least one intervening
feature is present. A feature "on" or "contacting" another feature
may be directly on or in direct contact with the other feature or,
instead, one or more intervening features may be present. A feature
may be "directly on" or in "direct contact" with another feature if
intervening features are absent. A feature may be "indirectly on"
or in "indirect contact" with another feature if at least one
intervening feature is present.
[0039] The descriptions of the various embodiments of the present
invention have been presented for purposes of illustration but are
not intended to be exhaustive or limited to the embodiments
disclosed. Many modifications and variations will be apparent to
those of ordinary skill in the art without departing from the scope
and spirit of the described embodiments. The terminology used
herein was chosen to best explain the principles of the
embodiments, the practical application or technical improvement
over technologies found in the marketplace, or to enable others of
ordinary skill in the art to understand the embodiments disclosed
herein.
* * * * *