U.S. patent application number 17/022952 was filed with the patent office on 2021-03-18 for rocker arm for an internal combustion engine.
The applicant listed for this patent is Koyo Bearings North America LLC. Invention is credited to Anthony Copper.
Application Number | 20210079815 17/022952 |
Document ID | / |
Family ID | 1000005102405 |
Filed Date | 2021-03-18 |

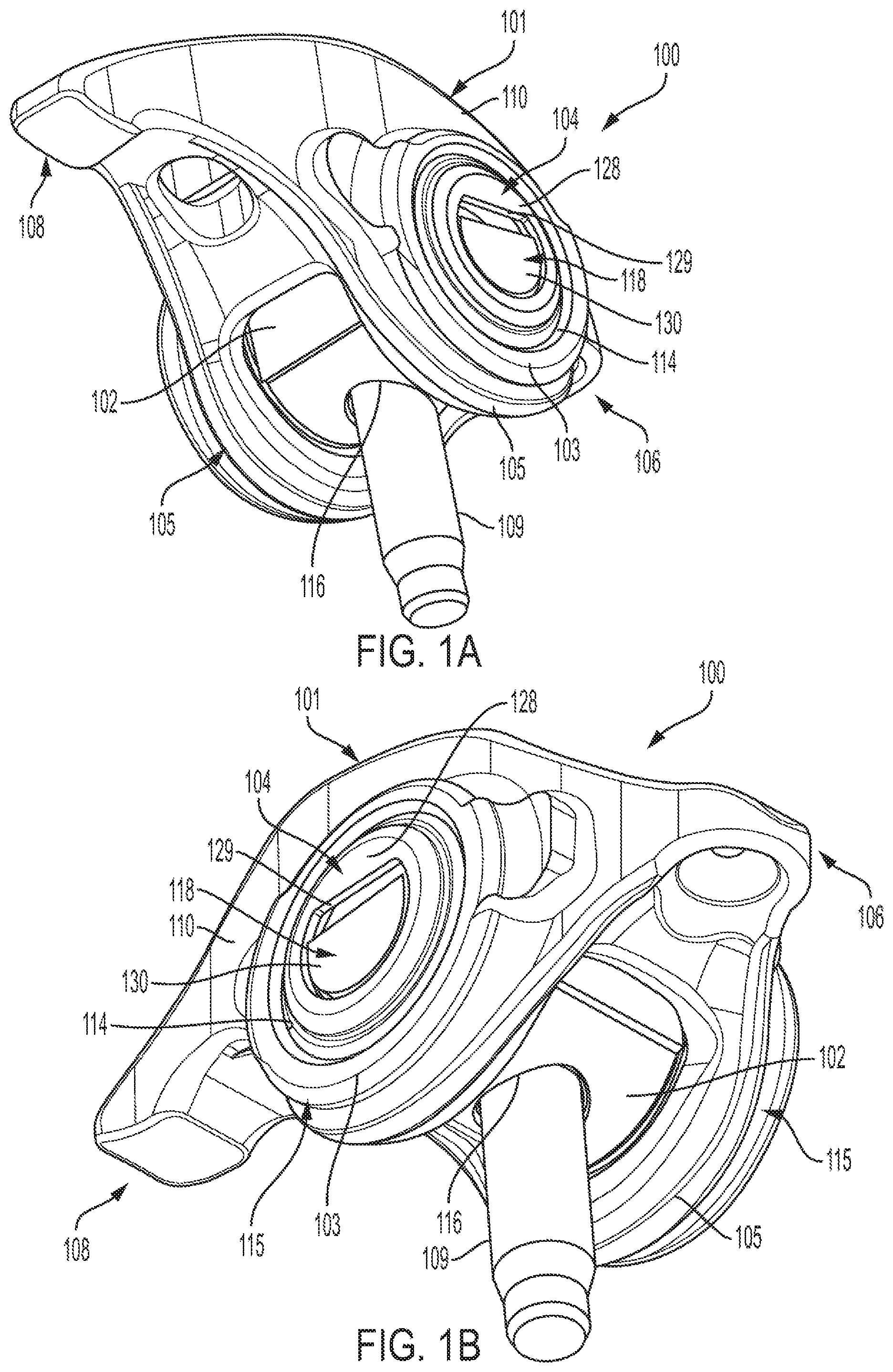
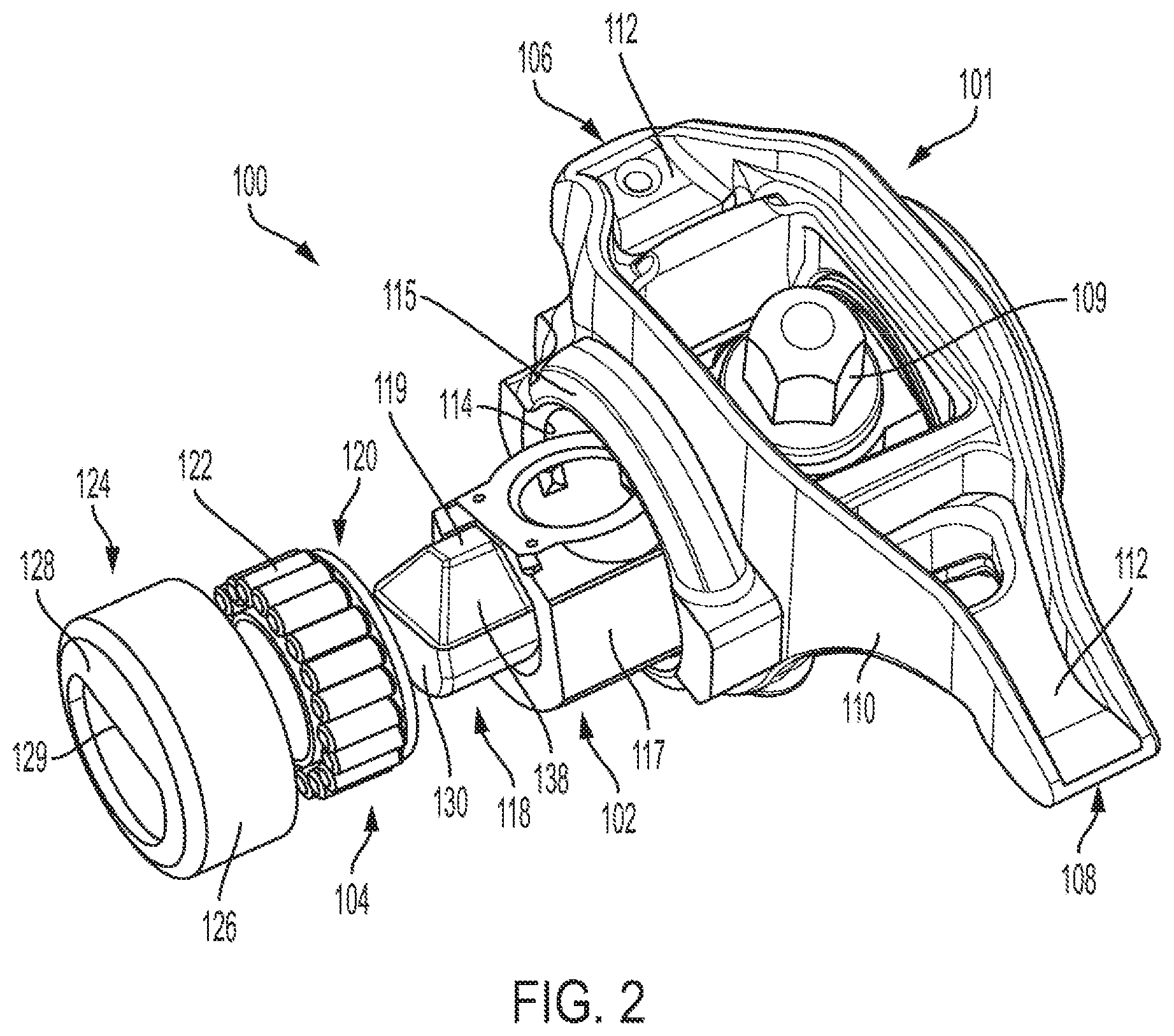


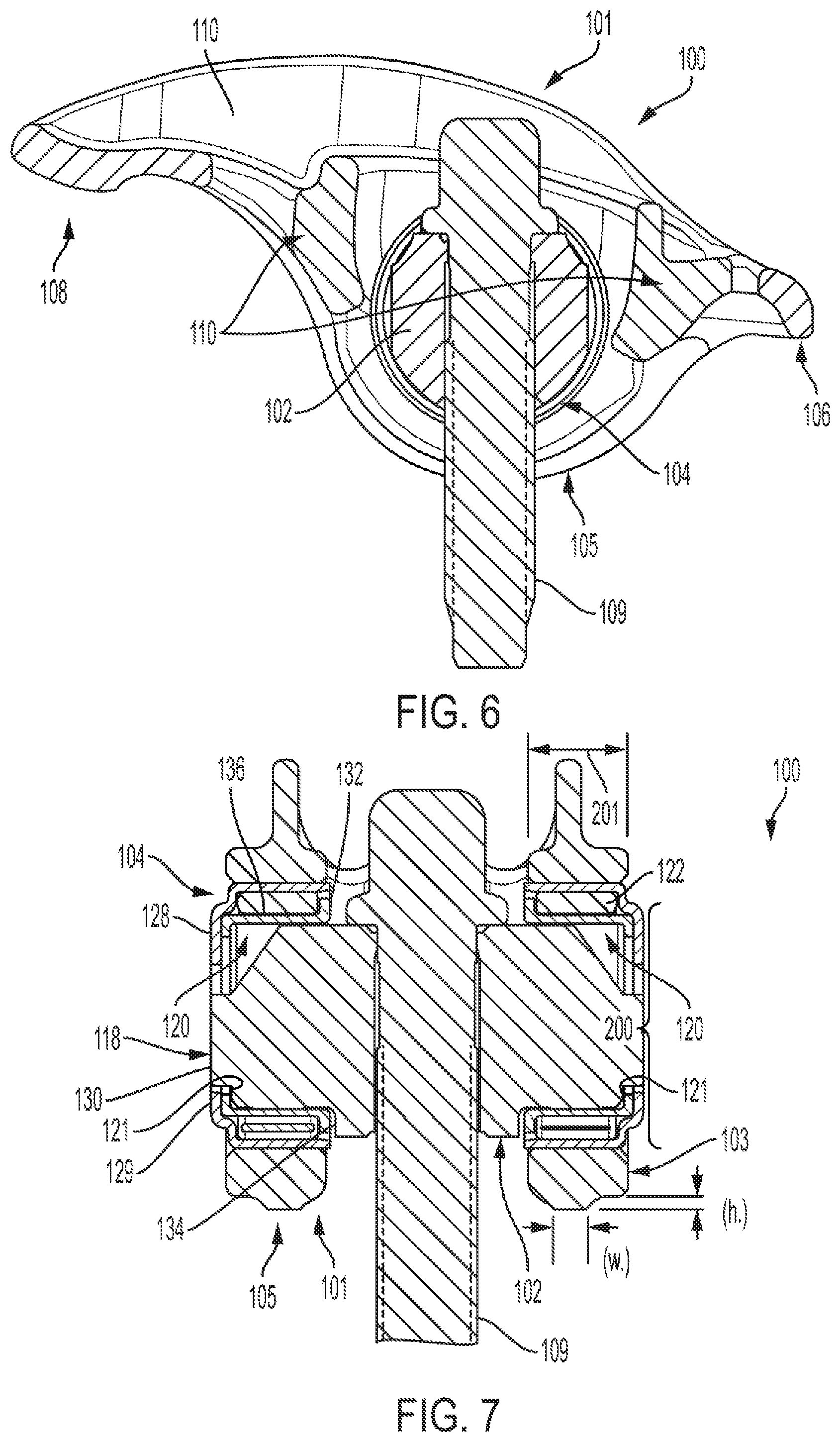
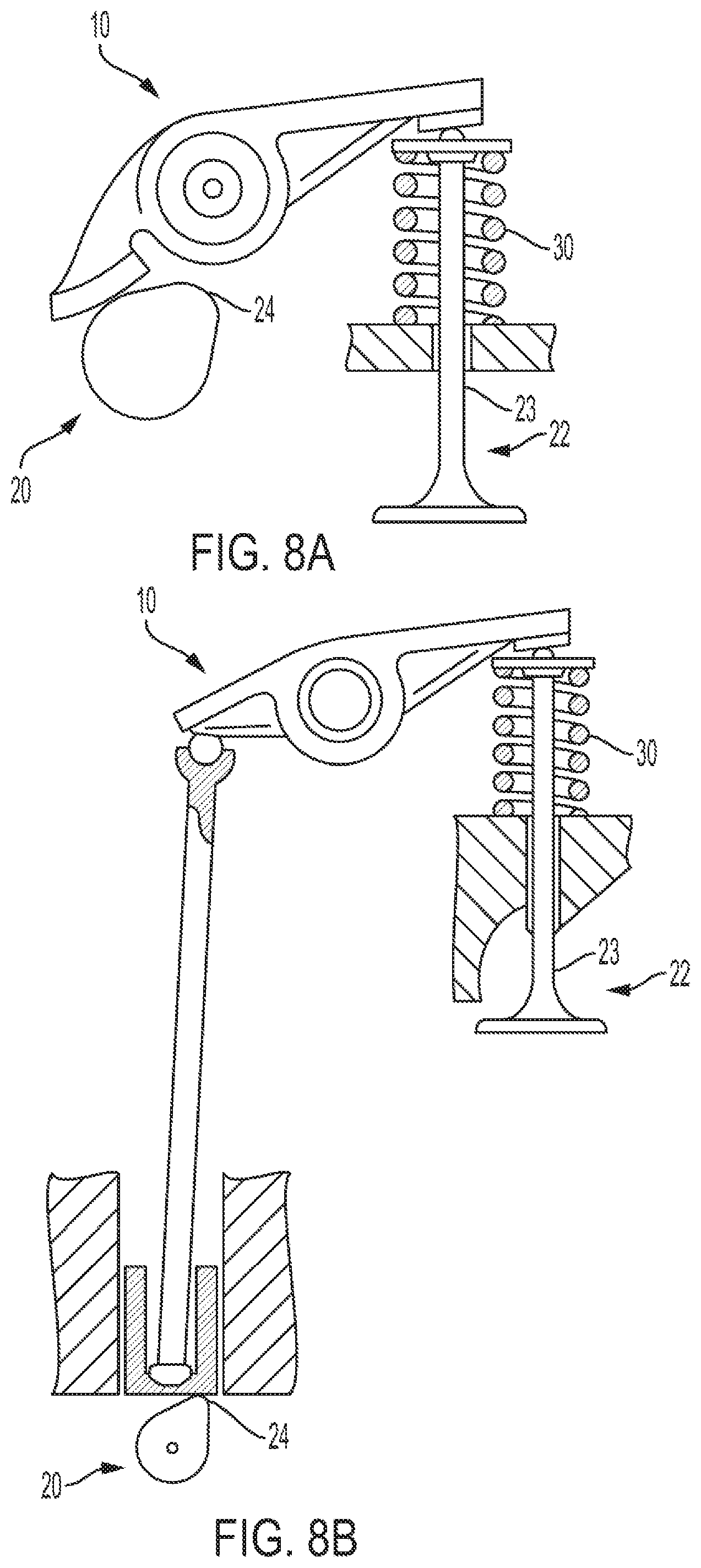
United States Patent
Application |
20210079815 |
Kind Code |
A1 |
Copper; Anthony |
March 18, 2021 |
ROCKER ARM FOR AN INTERNAL COMBUSTION ENGINE
Abstract
A rocker arm for use in a valvetrain of a vehicle, having a body
portion including two opposed side wall portions, each defining a
bearing aperture therein and including a bearing boss disposed
along a perimeter of the corresponding bearing aperture. A support
bearing has a pair of opposed ends, each opposed end being received
in a corresponding bearing aperture, and each bearing boss includes
a first portion having a first radial thickness and a second
portion having a second radial thicknesses, the first radial
thickness being greater than the second radial thickness.
Inventors: |
Copper; Anthony; (Fountain
Inn, SC) |
|
Applicant: |
Name |
City |
State |
Country |
Type |
Koyo Bearings North America LLC |
Greenville |
SC |
US |
|
|
Family ID: |
1000005102405 |
Appl. No.: |
17/022952 |
Filed: |
September 16, 2020 |
Related U.S. Patent Documents
|
|
|
|
|
|
Application
Number |
Filing Date |
Patent Number |
|
|
62901081 |
Sep 16, 2019 |
|
|
|
Current U.S.
Class: |
1/1 |
Current CPC
Class: |
F01L 1/047 20130101;
F01L 1/182 20130101 |
International
Class: |
F01L 1/18 20060101
F01L001/18 |
Claims
1. A rocker arm for use in a valvetrain of a vehicle, comprising: a
body portion including two opposed side wall portions, each side
wall portion defining a bearing aperture therein, each side wall
portion including a bearing boss disposed along a perimeter of the
corresponding bearing aperture and extending outwardly from the
corresponding side wall portion; and a support member having a pair
of opposed ends, each opposed end being received in a corresponding
bearing aperture, wherein each bearing boss includes a first
portion having a first radial thickness and a second portion having
a second radial thicknesses, the first radial thickness being
greater than the second radial thickness.
2. The rocker arm of claim 1, wherein each bearing boss is
asymmetric about the corresponding bearing aperture.
3. The rocker arm of claim 1, wherein the first portion of the
bearing boss is disposed below the second portion of the bearing
boss.
4. The rocker arm of claim 1, further comprising a pair of radial
roller bearings, each radial roller bearing being both disposed on
a corresponding one of the opposed ends of the support member and
disposed within a corresponding one of the bearing apertures.
5. The rocker arm of claim 1, further comprising a pair of
strengthening ribs, each strengthening rib extending outwardly from
the first portion of a corresponding bearing boss.
6. The rocker arm of claim 5, wherein each strengthening rib lies
in a plane that is transverse to the corresponding bearing
boss.
7. The rocker arm of claim 1, wherein the support member is affixed
to an upper end of a stud member.
8. A rocker arm for use in a valvetrain of a vehicle, comprising: a
body portion including two opposed side wall portions, each side
wall portion defining a circular bearing aperture therein, each
side wall portion including a bearing boss disposed along a
perimeter of the corresponding bearing aperture and extending
outwardly from the corresponding side wall portion, each bearing
boss having a circular outer perimeter; and a support member having
a pair of opposed ends, each opposed end being received in a
corresponding bearing aperture, wherein each bearing boss includes
a first portion having a first radial thickness and a second
portion having a second radial thicknesses, the first radial
thickness being greater than the second radial thickness.
9. The rocker arm of claim 8, wherein each bearing boss includes a
first portion having a first radial thickness and a second portion
having a second radial thicknesses, the first radial thickness
being greater than the second radial thickness.
10. The rocker arm of claim 8, wherein each bearing boss is
asymmetric about the corresponding bearing aperture.
11. The rocker arm of claim 8, wherein the first portion of the
bearing boss is disposed below the second portion of the bearing
boss.
12. The rocker arm of claim 8, further comprising a pair of radial
roller bearings, each radial roller bearing being both disposed on
a corresponding one of the opposed ends of the support member and
disposed within a corresponding one of the bearing apertures.
13. The rocker arm of claim 8, further comprising a pair of
strengthening ribs, each strengthening rib extending outwardly from
the first portion of a corresponding bearing boss.
14. The rocker arm of claim 13, wherein each strengthening rib lies
in a plane that is transverse to the corresponding bearing
boss.
15. The rocker arm of claim 8, wherein the support member is
affixed to an upper end of a stud member.
Description
CLAIM OF PRIORITY
[0001] This application claims priority to U.S. provisional patent
application No. 62/901,081 filed Sep. 16, 2019, the disclosure of
which is incorporated by reference herein.
FIELD OF THE INVENTION
[0002] The present invention relates generally to rocker arms used
with internal combustion engines. More particularly, the present
invention relates to rocker arms and methods of their manufacture,
particularly by investment casting processes.
BACKGROUND OF THE INVENTION
[0003] Referring to FIGS. 8A and 8B, rocker arms 10 are often used
in valve trains of an internal combustion engines to transmit
motion from a camshaft 20 of the engine to one or more intake or
exhaust valves 22. As camshaft 20 rotates, rocker arm 10 receives a
direct (FIG. 1A) or indirect (FIG. 1B) force from a corresponding
lobe 24 on the camshaft 20 via direct contact with the camshaft 20
(commonly referred to as "Type 3" rocker arm) or contact with a
pushrod and lifter (commonly referred to as "Type 5" rocker arm),
and transmits the force to valve 22 to open and/or close the valve.
The center of the rocker arm 10 is pivotably constrained to the
cylinder head so that the second end of the rocker arm 10 moves up
and down in a vertical plane. The second end of the rocker arm
engages an upper end of a valve stem 23 of the corresponding valve
22, thereby transmitting downward forces to the valve. A spring 30
constantly urges the second end of rocker arm 10 upward.
[0004] Preferably, engine components such as rocker arms exhibit
high strength for durability, yet are light weight so that low mass
moments of inertia facilitate rapid response of the components at
lower force levels, thereby improving the overall efficiency and
performance of the engine. As such, there remains a need for rocker
arms that exhibit high strength while exhibiting reduced mass
moments of inertia as compared to known rocker arms.
[0005] The present invention recognizes and addresses
considerations of prior art constructions and methods.
SUMMARY OF THE INVENTION
[0006] One embodiment of the present disclosure provides a rocker
arm for use in a valvetrain of a vehicle, having a body portion
including two opposed side wall portions, each side wall portion
defining a bearing aperture therein, each side wall portion
including a bearing boss disposed along a perimeter of the
corresponding bearing aperture and extending outwardly from the
corresponding side wall portion. A support member has a pair of
opposed ends, each opposed end being received in a corresponding
bearing aperture, and each bearing boss includes a first portion
having a first radial thickness and a second portion having a
second radial thicknesses, the first radial thickness being greater
than the second radial thickness.
[0007] Another embodiment of the present disclosure provides a
rocker arm for use in a valvetrain of a vehicle, having a body
portion including two opposed side wall portions, each side wall
portion defining a circular bearing aperture therein, each side
wall portion including a bearing boss disposed along a perimeter of
the corresponding bearing aperture and extending outwardly from the
corresponding side wall portion, each bearing boss having a
circular outer perimeter, and a support member having a pair of
opposed ends, each opposed end being received in a corresponding
bearing aperture, wherein each bearing boss includes a first
portion having a first radial thickness and a second portion having
a second radial thicknesses, the first radial thickness being
greater than the second radial thickness.
[0008] The accompanying drawings, which are incorporated in and
constitute a part of this specification, illustrate one or more
embodiments of the invention and, together with the description,
serve to explain the principles of the invention.
BRIEF DESCRIPTION OF THE DRAWINGS
[0009] A full and enabling disclosure of the present invention,
including the best mode thereof, directed to one of ordinary skill
in the art, is set forth in the specification, which makes
reference to the appended drawings, in which;
[0010] FIGS. 1A and 1B are perspective views of a rocker arm in
accordance with an embodiment of the present invention;
[0011] FIG. 2 is an exploded, perspective view of the rocker arm as
shown in FIGS. 1A and 1B;
[0012] FIGS. 3A and 3B are side views of the rocker arm shown in
FIGS. 1A and 1B;
[0013] FIG. 4 is a bottom view of the rocker arm shown in FIGS. 1A
and 1B;
[0014] FIG. 5 is a top perspective view of the rocker arm shown in
FIGS. 1A and 1B;
[0015] FIG. 6 is a cross-sectional view of the rocker arm shown in
FIG. 4, taken along line 6-6;
[0016] FIG. 7 is a cross-sectional view of the rocker arm as shown
in FIG. 3B, taken along line 7-7; and
[0017] FIGS. 8A and 8B are rocker arm assemblies in accordance with
the prior art as used in a valve train assembly of an internal
combustion engine.
[0018] Repeat use of reference characters in the present
specification and drawings is intended to represent same or
analogous features or elements of the invention according to the
disclosure.
DETAILED DESCRIPTION OF THE PREFERRED EMBODIMENTS
[0019] Reference will now be made in detail to presently preferred
embodiments of the invention, one or more examples of which are
illustrated in the accompanying drawings. Each example is provided
by way of explanation, not limitation, of the invention. In fact,
it will be apparent to those skilled in the art that modifications
and variations can be made in the present invention without
departing from the scope and spirit thereof. For instance, features
illustrated or described as part of one embodiment may be used on
another embodiment to yield a still further embodiment. Thus, it is
intended that the present invention covers such modifications and
variations as come within the scope of the appended claims and
their equivalents.
[0020] As used herein, terms referring to a direction or a position
relative to the orientation of the fuel-fired heating appliance,
such as but not limited to "vertical," "horizontal," "upper,"
"lower," "above," or "below," refer to directions and relative
positions with respect to the appliance's orientation in its normal
intended operation, as indicated in the Figures herein. Thus, for
instance, the terms "vertical" and "upper" refer to the vertical
direction and relative upper position in the perspectives of the
Figures and should be understood in that context, even with respect
to an appliance that may be disposed in a different
orientation.
[0021] Further, the term "or" as used in this disclosure and the
appended claims is intended to mean an inclusive "or" rather than
an exclusive "or." That is, unless specified otherwise, or clear
from the context, the phrase "X employs A or B" is intended to mean
any of the natural inclusive permutations. That is, the phrase "X
employs A or B" is satisfied by any of the following instances: X
employs A; X employs B; or X employs both A and B. In addition, the
articles "a" and "an" as used in this application and the appended
claims should generally be construed to mean "one or more" unless
specified otherwise or clear from the context to be directed to a
singular form. Throughout the specification and claims, the
following terms take at least the meanings explicitly associated
herein, unless the context dictates otherwise. The meanings
identified below do not necessarily limit the terms, but merely
provided illustrative examples for the terms. The meaning of "a,"
"an," and "the" may include plural references, and the meaning of
"in" may include "in" and "on." The phrase "in one embodiment," as
used herein does not necessarily refer to the same embodiment,
although it may.
[0022] Referring now to the figures, the present disclosure relates
to design elements for the manufacture of rocker arms for engine
valve trains utilizing an investment casting lost wax process. The
discussed features allow the rocker arm 100 to maintain high
performance with low mass and mass moment of inertia (MMOI), while
including desirable features for the manufacturability/cast-ability
of the rocker arm.
[0023] As shown in FIGS. 1A and 1B, an embodiment of a rocker arm
assembly 100 in accordance with the present disclosure includes a
rocker arm 101 supported on a rocker arm support member 102 by a
pair of radial roller bearings 104 (FIG. 2), as would be used in an
internal combustion engine. Rocker arm 101 has a first end 106 for
engagement with a hydraulic lash adjuster, not shown, and second
end 108 for engagement with a valve stem (23, FIG. 8A) of a poppet
valve (20, FIG. 8A). The rocker arm assembly 100 is mounted on the
engine by a stud 109, cap screw, or other stud means, not shown. As
shown, rocker arm 101 is of a cast configuration including a pair
of side walls 110 connected by a pair of end flanges 112, providing
added rigidity. Each side wall 110 includes a mounting aperture 114
for receiving a corresponding radial roller bearing 104 therein.
Note, however, the rocker arm assembly 100 of the present invention
may be employed with cast rocker arms of various
configurations.
[0024] Referring additionally to FIGS. 2 and 4, rocker arm support
member 102 has a substantially vertical bore 116 for receiving the
stud means 109 to mount the rocker arm 101 to the engine. Rocker
arm support member 102 has a body portion 117 and a pair of bearing
support arms 118 which extend in opposite directions along a common
axis perpendicular to the stud means. Radial roller bearings 104
are mounted along that axis over support arms 118 by inner bearing
sleeves 120 which provide inner raceways for roller members 122. As
shown, a top surface 119 of each bearing support arm 118 is flat
and side surfaces 138 are angled so that oil may flow between the
inner cylindrical surface of the corresponding inner sleeve 120 and
the bearing support arm 118. Roller bearings 104 may employ a full
complement of needle rollers 122, as illustrated, or may employ
other types of roller members, with or without retainers. Roller
members 122 are within an annulus formed between inner sleeves 120
and outer bearing cups 124. Outer bearing cups 124 have a common
axis and are rigidly mounted in the two spaced apart side walls 110
of rocker arm 101 by any of various fixing means. In the embodiment
shown, for example, mounting apertures 114 formed in the side walls
110 of rocker arm 101 provide an interference fit with bearing cups
124. Rocker arm support member 102 has a cross-section smaller than
the mounting apertures 114 in the side walls 110 of rocker arm 101,
thus allowing rocker arm support member 102 to be inserted through
one of the apertures during assembly, as best seen in FIG. 2.
[0025] As shown, outer bearing cups 124 are of the "open" type.
That is, each bearing cup has a cylindrical side wall 126, and a
top wall 128 that is perpendicular thereto and defines an aperture
129 therein. As best seen in FIG. 7, the inner surface of top wall
128 is engageable with ends of roller members 122 to limit outward
axial movement of the roller members, and the outer surface of the
side wall 126 is received in the corresponding mounting aperture
114 in an interference fit. Additionally, as best seen in FIG. 7,
an inwardly depending annular flange 121 on the outermost end of
each inner bearing sleeve 120 abuts an outer end of the
corresponding bearing support arm 118 so that each radial roller
bearing 104 is properly positioned within rocker arm 101. As well,
the outermost end of each bearing support arm 118 extends outwardly
through the aperture 129 of the top wall 128 of the corresponding
outer cup 124. In alternate embodiments, top wall 128 of outer cup
124 may be spaced from the end surface 130 of bearing support arm
118 to allow for enhanced flow of lubrication. Preferably, inner
sleeves 120 and outer cups 124 are formed by a drawing process.
[0026] Referring again to FIG. 7, inner bearing sleeves 120 are
formed with outwardly extending flanges 132 that are engageable
with the ends of roller members 122 to limit inward axial movement
of the rollers. As well, outwardly extending flanges 132 abut
planar surfaces 134 of rocker arm support member 102 to insure
proper axial location of inner bearing sleeves 120. A cylindrical
wall 136 of each inner bearing sleeve 120 provides an inner raceway
for roller members 122 and facilitates use of powder metal forming
of rocker arm support member 102 by allowing bearing support arms
118 to have a non-cylindrical configuration, as shown below. Note,
however, in alternate embodiments each bearing support arm may have
a circular cross-section.
[0027] As best seen in FIG. 2, rocker arm support member 102 may
include beveled surfaces 138 and flat side surfaces 140. The
beveled and flat surfaces facilitate manufacture of rocker arm
support member 102 by powder metal forming. Because roller members
122 ride on inner raceways provided by inner sleeves 120, and
because the greatest force from the rocker arm 101 is on the lower
portions of roller bearings 104, those beveled and flat surfaces on
the top and side portions of bearing support arms 118 of rocker arm
support member 102 do not affect operation of the rocker arm
assembly.
[0028] Referring to FIGS. 3A and 3B, a preferred embodiment of
rocker arm 100 includes a bearing boss 115 formed around each
mounting aperture 114, each of which is configured to receive a
corresponding bearing 104, wherein material used to form each
bearing boss 115 is concentrated toward the bottom portion 103 of
the bearing boss 115. Material is concentrated toward the bottom
portion 103 of each bearing boss 115 since the bottom portion is
the area where the load from the corresponding radial bearing 104,
about which the rocker arm 101 pivots, is concentrated on the
casting. Traditional rocker arm designs maintain the walls of this
feature axisymmetric about the bearing and bearing aperture, and
therefore waste mass and increases mass mount of inertia (MMOI)
with excess material where it is not required. As shown, although
the outer perimeter of the bearing boss 115 is circular, the
bearing boss is not concentric to the circular bearing aperture
114, i.e., the longitudinal center axis of the bearing aperture 114
is not collinear with the longitudinal center axis of the bearing
boss 115. As well, preferably, the width of the bearing boss 115 in
the radial direction is least at its top portion, and increases
gradually until reaching its maximum radial thickness at the bottom
portion 103 of the bearing boss 115. As best in FIGS. 5 and 6, the
top profile of the rocker arm 101 is scalloped on the camshaft
acting end 108 of the rocker arm 101 to lower MMOI and increase
performance in responsiveness. As well, as shown in FIGS. 1A, 1B,
and 4, strengthening ribs 105 added to the bottom of each side wall
100 of the rocker arm 101 improve the fatigue strength of the
rocker arm 101 while minimizing impact on MMOI or cast-ability.
[0029] Referring again to FIG. 7, preferably, the strengthening
ribs 105 extend the full length of the rocker arm from the cam
acting end 106 to the valve actuation end 108. The sizing of each
strengthening rib 105 is preferably optimized so that its width
(w.sub.1) is 25-50% of the width of the corresponding bearing hoop
201. The height (h.sub.1) of each rib 105 is preferably selected to
be 25-50% the rib width (w.sub.1) on the bottom of the bearing boss
section 103. The rib height (h.sub.2) increases to 40-60% of the
section height as it extends to the valve actuating end 108 of the
rocker arm 101. The rib height increases to 80-120% of section
thickness as it extends to the cam acting end of the rocker arm.
These proportions maximize the performance potential of the rocker
arm without compromising the manufacturability of the part for the
casting process. Note, however, other proportions are utilized in
alternate embodiments of the present invention.
[0030] Referring now to FIGS. 4 and 5, side view and a
cross-sectional view through the centerline of the rocker arm 101
shows gates 110 aligned with thick sections through the center of
the part to protect metal flow during casting, but hold the
sections tight to the center of rotation to minimize MMOI. FIGS. 6
and 7 provide views of the strengthening ribs and their placement
on the rocker arm 101.
[0031] While one or more preferred embodiments of the invention are
described above, it should be appreciated by those skilled in the
art that various modifications and variations can be made in the
present invention without departing from the scope and spirit
thereof. It is intended that the present invention cover such
modifications and variations as come within the scope and spirit of
the appended claims and their equivalents.
* * * * *