U.S. patent application number 16/963545 was filed with the patent office on 2021-02-18 for reactor and process for the hydrogenation of carbon dioxide.
The applicant listed for this patent is Nederlandse Organisatie voor toegepast-natuurwetenschappelijk onderzoek TNO. Invention is credited to Rajat Bhardwaj, Juliana Garcia Moretz-Sohn Monteiro, Earl Lawrence Vincent Goetheer, Marco Johannes Gerardus Linders.
Application Number | 20210046442 16/963545 |
Document ID | / |
Family ID | 1000005222605 |
Filed Date | 2021-02-18 |
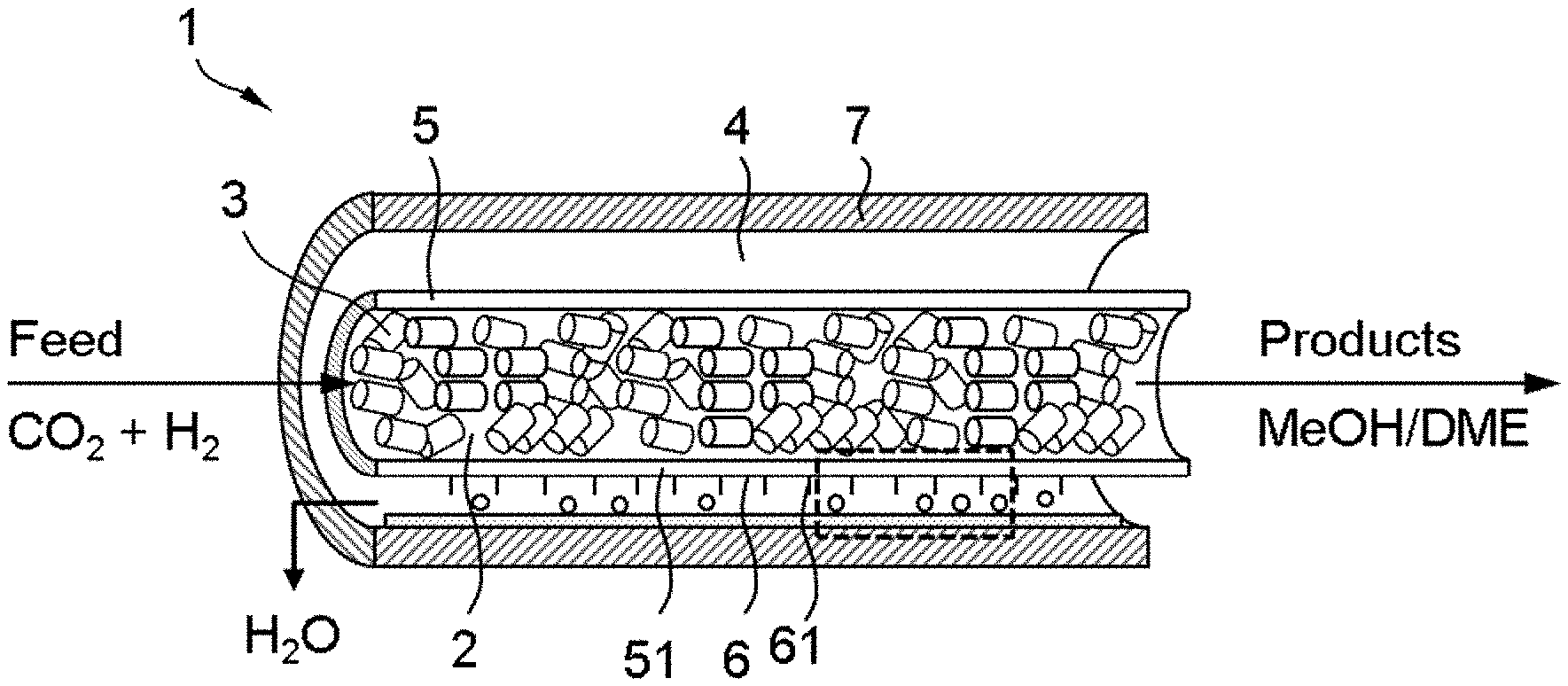










United States Patent
Application |
20210046442 |
Kind Code |
A1 |
Goetheer; Earl Lawrence Vincent ;
et al. |
February 18, 2021 |
Reactor and Process for the Hydrogenation of Carbon Dioxide
Abstract
The present invention is directed to a membrane reactor for the
hydrogenation of carbon dioxide, said membrane reactor comprising a
reaction compartment (2) comprising a catalyst bed, a permeate
compartment (4) and a membrane separating the reaction compartment
and the permeate compartment, wherein said permeate compartment
comprises a condensing surface.
Inventors: |
Goetheer; Earl Lawrence
Vincent; (Mol, BE) ; Linders; Marco Johannes
Gerardus; (Delfgauw, NL) ; Garcia Moretz-Sohn
Monteiro; Juliana; (Alphen aan den Rijn, NL) ;
Bhardwaj; Rajat; (Delft, NL) |
|
Applicant: |
Name |
City |
State |
Country |
Type |
Nederlandse Organisatie voor toegepast-natuurwetenschappelijk
onderzoek TNO |
's-Gravenhage |
|
NL |
|
|
Family ID: |
1000005222605 |
Appl. No.: |
16/963545 |
Filed: |
January 28, 2019 |
PCT Filed: |
January 28, 2019 |
PCT NO: |
PCT/NL2019/050046 |
371 Date: |
July 21, 2020 |
Current U.S.
Class: |
1/1 |
Current CPC
Class: |
B01J 8/009 20130101;
B01J 8/067 20130101; B01J 8/065 20130101; B01J 2208/00168 20130101;
C07C 29/152 20130101; B01J 2208/00115 20130101; C07C 41/01
20130101 |
International
Class: |
B01J 8/00 20060101
B01J008/00; B01J 8/06 20060101 B01J008/06; C07C 29/152 20060101
C07C029/152; C07C 41/01 20060101 C07C041/01 |
Foreign Application Data
Date |
Code |
Application Number |
Jan 26, 2018 |
EP |
18153753.1 |
Claims
1. A membrane reactor for the hydrogenation of carbon dioxide, said
membrane reactor comprising a reaction compartment comprising a
catalyst bed, a permeate compartment and a water-permeable membrane
separating the reaction compartment and the permeate compartment,
wherein said permeate compartment comprises a condensing surface
and a means for cooling that is connected to said condensing
surface such that during operation of the reactor, water can
condense on the condensing surface.
2. The membrane reactor in accordance with claim 1, wherein the
means for cooling comprises an active-cooling device.
3. The membrane reactor in accordance with claim 1, wherein said
reactor comprises an inner wall bounding an inner space that
defines the reaction compartment; an outer wall that is arranged
around said inner wall, wherein said outer wall and inner wall
bound an outer space that defines the permeate compartment; wherein
said inner wall comprises the water-permeable membrane, and wherein
said condensing surface is connected to the outer wall.
4. The membrane reactor in accordance with claim 1, wherein said
reactor comprises an inner wall bounding an inner space that
defines the permeate compartment; an outer wall that is arranged
around said inner wall, wherein said outer wall and inner wall
bound an outer space that defines the reaction compartment; wherein
said inner wall comprises the water-permeable membrane, and wherein
the condensing surface is located away from the inner wall.
5. The membrane reactor in accordance with claim 1, wherein said
permeate compartment and means for cooling comprise an
active-cooling device which active-cooling device is disconnected
from the inner wall.
6. The membrane reactor in accordance with claim 3, wherein said
inner wall and outer wall are tubular and the outer wall is at
least partially co-axially arranged around said inner wall.
7. The membrane reactor in accordance with claim 1, wherein the
condensing surface comprises protruding surface elements.
8. The membrane reactor in accordance with claim 1, wherein said
water-permeable membrane comprises a hydrophilic membrane.
9. The membrane reactor in accordance with claim 1, wherein said
catalyst bed comprises copper, zinc oxide, zirconia, palladium,
cerium(IV) oxide or combinations thereof.
10. The process for the hydrogenation of carbon dioxide, wherein
said process comprises reacting carbon dioxide with hydrogen to
form methanol and/or dimethyl ether, and water as a side product,
and wherein said process further comprises removing said water from
the process by a combination of permeation of said water through a
water-permeable membrane and condensation of the water.
11. The process for the hydrogenation of carbon dioxide carried out
in a membrane reactor in accordance with claim 1, wherein the
condensing surface has a temperature of less than 150.degree.
C.
12. The process in accordance with claim 11, wherein reacting
carbon dioxide with hydrogen is carried out at a temperature in the
range of 150-400.degree. C. and/or at a pressure in the range of
1-10 MPa.
13. The process in accordance with claim 10, wherein said carbon
dioxide and/or said hydrogen originate from biogas.
14. The membrane reactor of claim 1 wherein the means for cooling
comprises a passage through which a cooling fluid can flow.
15. The membrane reactor of claim 1 wherein said water-permeable
membrane comprises a zeolite membrane, an amorphous membrane or a
polymer membrane.
16. The process of claim 11 wherein the condensing surface has a
temperature of less than 50.degree. C.
17. The process of claim 11 wherein the condensing surface has a
temperature of less than 10.degree. C.
18. The process of claim 12 wherein reacting carbon dioxide with
hydrogen is carried out at a temperature in the range of
200-300.degree. C. and/or at a pressure in the range of 2-8
MPa.
19. The process of claim 12 wherein reacting carbon dioxide with
hydrogen is carried out at a temperature of about 250.degree. C.
and/or at a pressure of about 5 MPa.
Description
[0001] The invention is in the field of chemical reactors and
chemical processes. In particular, the invention is directed to a
reactor and a process for the hydrogenation of carbon dioxide into
methanol and/or dimethyl ether.
[0002] The process of hydrogenating carbon dioxide into methanol
and/or dimethyl ether (also referred to as DME) can i.a. be used to
lower CO.sub.2 concentration in the atmosphere. In addition, the
process can also be used to further valorize biogas and to provide
a broader applicability of said biogas. For instance, by separating
biogas into CO.sub.2 and methane, the methane can be reformed into
hydrogen (H.sub.2) and the obtained hydrogen can be allowed to
react with the CO.sub.2 to form methanol and/or DME. This concept
is not limited to biogas since in principle any CO.sub.2-containing
gas can be valorized and provided with a broader applicability by
hydrogenating the CO.sub.2 therein.
[0003] The hydrogenation of CO.sub.2 is believed to involve the
following reactions:
CO.sub.2+3H.sub.2CH.sub.3OH+H.sub.2O (I)
CO.sub.2+H.sub.2CO+H.sub.2O (II)
CO+2H.sub.2CH.sub.3OH (III)
2CH.sub.3OH CH.sub.3OCH.sub.3+H.sub.2O (IV)
[0004] The reaction CO.sub.2 to MeOH can proceed directly (equation
I), or via the intermediate CO (equation II and III). Depending on
the process parameters, the obtained MeOH can react further into
DME (equation IV). As is apparent from equations I-IV, water is
produced as a side product concomitantly with MeOH and/or DME. In
addition, since these reactions (I-IV) are in equilibrium under the
process conditions, full conversion to the products can in
principle not be obtained under thermodynamic equilibrium
conditions. Therefore, in order to maximize the conversion into
methanol and/or DME, it is preferred that at least one of the
reaction products which is formed in the reaction (i.e. water,
methanol and/or DME) is removed from the reaction medium.
[0005] Examples of conventional methods for the removal of the
reaction products include condensation in a recycle configuration,
reactive adsorption of water, and in-situ water-consuming reaction.
US 2004/064002 discloses water vapor permeation through a membrane
to remove the water from a reaction of MeOH to DME. In
WO2015/030578, a reactor and a process are described comprising two
stages including a zone or stage wherein a liquid condensate of
methanol and water is condensed. However, all these methods are
associated with several drawbacks.
[0006] For instance, a recycle configuration results in a bulky
process design with installation of separate equipment, piping and
control, while the use of solid system for the adsorption or
reactive-consumption of water pose challenging regeneration and
handling, also making the overall process bulky and expensive.
Furthermore, a solid adsorption system involves regeneration which
leads to a discontinuous type of operation and higher temperatures
are needed for regeneration. Although the use of water vapor
permeation through a membrane is elegant, this conventional method
is associated with concomitant removal of H.sub.2 from the reaction
and decrease of the overall conversion. The combined condensation
of methanol and water as disclosed in WO2015/0305578 requires a
subsequent separation of the water and methanol in order to obtain
dry methanol and results in a liquid methanol product, whereas it
may be preferred to maintain a gaseous methanol product if is going
to sequentially be converted into products in a gaseous phase
reaction. This process is therefore relative high in energy
consumption.
[0007] It is an object of the present invention to provide a
process and reactor, in particular for the hydrogenation of carbon
dioxide, that addresses at least one of these drawbacks.
[0008] A further object of the present invention is to provide an
improved hydrogenation of carbon dioxide, by enhancing reaction
rates towards the production of methanol and/or DME, improving
catalyst lifetime, improving reactor design and intensification of
process of production of methanol and/or DME from several steps to
single reaction-separation-removal unit, and/or by providing a
conversion beyond equilibrium constraints due to selective removal
of at least one reaction product from the reaction mixture.
[0009] The present inventors found that these objects can at least
partially be met by a combination of permeation of the formed water
through a membrane and condensation of said water after permeation.
This provides a method to selectively remove the water from the
process, without the requirement of bulky process design with
installation of separate equipment. The permeation and condensation
are carried out in the same reactor, which reactor is another
aspect of the present invention (vide infra). In particular, this
method enables the in-situ removal of condensed water from the
reaction within the same reactor in which the hydrogenation
reaction is carried out.
[0010] Accordingly, the present invention is directed to a process
for the hydrogenation of carbon dioxide, wherein said process
comprises reacting carbon dioxide with hydrogen to form methanol
and/or dimethyl ether, and water as a side product, and wherein
said process further comprises removing said water from the process
by a combination of permeation of said water through a membrane and
condensation of the water.
[0011] In another aspect, the present invention is directed to a
membrane reactor for the hydrogenation of carbon dioxide, said
membrane reactor comprising a reaction compartment comprising a
catalyst bed, a permeate compartment, and a water-permeable
membrane that separates the reaction compartment and the permeate
compartment. Said permeate compartment comprises a condensing
surface such that the reactor is particularly suitable for carrying
out the method of the present invention. The condensing surface in
the permeate compartment is configured and is connected to a means
for cooling (herein also referred to as cooling means) such that
during operation of the reactor, the water can condense on the
surface.
[0012] The means for cooling may be such to effect active and/or
passive cooling. Examples of passive cooling include heat sinks and
heat conductive materials that can be passively cooled by
conductive cooling due to a temperature difference. Active cooling
however is typically more effective and therefore preferred. Active
cooling can be obtained by providing the means for cooling with an
active-cooling device, for instance a passage such as a tube
through which a cooling fluid can flow and/or a fan directing air.
Suitable cooling fluids include gases (e.g. air) and liquids (e.g.
water). A combination of active and passive cooling, e.g. by
providing both fluid cooling through a tube or by a fan and a heat
sink can also be used.
[0013] The water-permeable membrane is typically not exclusively
permeable for water. For instance, hydrogen molecules, which are
also present in the reaction compartment, are smaller than water
molecules and may also (albeit undesirably) permeate the membrane.
In fact, due to this permeation of hydrogen, substantial amounts of
hydrogen removal from the reaction mixture have been observed in
the aforementioned conventional methods. It is believed that the
requirement of a sweeping gas stream to remove the vapor, also
removes the permeated hydrogen. Advantageously, the presence of the
condensing surface mitigates the requirement of the sweeping gas
stream and the condensing surface selectively condensates water
while hydrogen remains gaseous under the condensation and reaction
conditions. With this method, separation of water from the reaction
mixture and from 112, may be carried out in one step, limiting the
need of additional equipment for individual steps of separation and
purification.
[0014] Typical reaction conditions include elevated temperatures
and pressures. In particular, reacting carbon dioxide with hydrogen
may be carried out at a temperature in the range of 150-400.degree.
C., preferably in the range of 200 to 300.degree. C., more
preferably about 250.degree. C. and/or at a pressure in the range
of 1-10 MPa, preferably in the range of 2-8 MPa, more preferably
about 5 MPa.
[0015] The water-permeable membrane (herein also referred to as the
membrane) can accordingly suitably function at these reaction
conditions. Therefore, the water-permeable membrane is preferably a
hydrophilic membrane, which preferably comprises a zeolite
membrane, an amorphous membrane or a polymer membrane. Particularly
suitable zeolite membranes comprise mordenite (MOR), ZSM-5,
chabazite (CHA), silicalite-1 (SIL-1), Z4A, faujasite (FAU), Si/Al
variant MFI, and the like. Suitable amorphous membranes may
comprise Al.sub.2O.sub.3/SiO.sub.2. The polymer membranes may
comprise ceramic-supported polymers (CSP), as these are
particularly suitable for functioning at elevated temperatures.
Membranes that are used for the water removal in Fischer-Tropsch
processes may also be suitably used for the present invention (see
e.g. Rohde et al. Microporous and Mesoporous Materials 115 (2008)
123-136).
[0016] The catalyst bed may comprise any known catalyst that
suitably catalyzes the hydrogenation of carbon dioxide (see e.g.
Gallucci et al. Chemical Engineering and Processing 43 (2004)
1029-1036 and references therein, which are incorporated herein in
their entirety). Particularly suitable catalysts comprise copper,
zinc oxide, zirconia, palladium, cerium(IV) oxide or combinations
thereof. The catalyst may be supported on suitable supports such as
alumina or silica. Advantageously, the present invention can
increase the lifetime of the catalyst due to an increased removal
of the water. As such, less water may condense in the catalyst
particles, which can increase both performance and lifetime.
[0017] In FIG. 1, a particular embodiment of the reactor in
accordance with the present invention is illustrated. The reactor
comprises: [0018] an inner wall (5) bounding an inner space that
defines the reaction compartment (2); [0019] an outer wall (7) that
is arranged around said inner wall, wherein said outer wall (7) and
inner wall (5) bound an outer space that defines the permeate
compartment (4); wherein said inner wall (5) comprises the
water-permeable membrane (51). Preferably, as illustrated in FIG.
1, the inner wall and outer wall are tubular and the outer wall is
co-axially arranged around said inner wall.
[0020] In a preferred embodiment, the condensing surface is part of
a protruding surface elements (62) that are connected to or part of
the cooling means. In a particular embodiment, the protruding
surface elements are connected to said inner wall (5) and
protruding into the permeate compartment. An example of this
embodiment is illustrated in FIG. 2. In an alternative, embodiment,
the protruding surface is connected to outer wall (7) and
protruding into the permeate compartment (not shown). This may be
preferred as condensation of water in the membrane is preferably
prevented because condensed water in the membrane can block the
membrane' pores. The protruding surface elements and thus the
surface can have various shapes. For instance, the surface may be
undulating or jagged to increase the total surface area. Suitable
shapes may result from protruding elements such as rods, bars,
blades and the like. Such protruding elements may comprise at least
part of the active-cooling device such a tubing.
[0021] In particular embodiments, the condensing surface is
situated in the reactor in the vicinity of the membrane. As such,
the permeated water can travel a relatively short path before it
condenses. The inventors found however, that in certain
embodiments, it may actually be preferred that the cooling means
and the condensing surface is situated in the reactor away from the
membrane. For the hydrogenation reaction, typical reaction
temperatures are around 250.degree. C. due to which the membrane
may have a temperature of about 200.degree. C., while it is
preferred that the condensing surface is kept at a much lower
temperature (vide infra). Accordingly, such a temperature
difference can more easily and efficiently be maintained when the
cooling means and condensing surface are situated away from the
membrane, or at least by situating the cooling means and condensing
surface disconnected from the membrane and the inner wall. In
addition, it can preferred condensed water in the membrane's pores.
Away from the inner wall and in the vicinity of the outer wall
herein means that the cooling means are closes to the outer wall
than to the inner wall.
[0022] In FIG. 3, an embodiment of the reactor is shown, wherein
the configuration is similar to that as illustrated in FIG. 1, but
the means for cooling (6) in this embodiment is situated away from
the inner wall (5) and more in the vicinity of the outer wall
(7).
[0023] In FIG. 4, yet another configuration of the membrane reactor
is illustrated. In this particular embodiment, which is preferred,
the membrane reactor (1) comprises [0024] an inner wall (5)
bounding an inner space that defines the permeate compartment (4);
[0025] an outer wall (7) that is arranged around said inner wall,
wherein said outer wall (7) and inner wall (5) bound an outer space
that defines the reaction compartment (2);
[0026] wherein said inner wall (5) comprises the water-permeable
membrane (51). Thus, the embodiment wherein the permeate
compartment is at least partially enclosed by reaction compartment,
is an inverse configuration of the reactor illustrated in FIGS. 1
and 3 wherein the reactor compartment is at least partially
enclosed by the permeate compartment. As further illustrated in
FIG. 4, preferably the cooling means (6) and the condensing surface
(61) are located away from the inner wall. For instance, in an
co-axial, tubular configuration of the reactor, the cooling means
can be placed in the (longitudinal) axis of the reactor, as
illustrated in FIG. 4 as well. The cooling means however, can have
various shapes, and are not confined to a straight configuration as
illustrated in FIG. 4. For instance, the cooling means can be a
U-shaped, helical shaped, jagged and/or undulated tube, a various
thereof. The cooling means can also comprise the protruding
elements such as rods, bars, blades and the like.
[0027] The condensing surface is generally preferably actively
cooled, meaning that it is maintained at a temperature by which
water can condensate under the, generally elevated, reaction
pressures. The condensing surface can be cooled actively by
providing a cooling fluid stream, for instance air or (relatively)
cool water, within tubing or a space near the condensing surface.
It is to be understood that the cooling fluid should preferably be
prevented from contacting the reactants in the reactor, such a
hydrogen. The cooling fluid therefore is typically separated from
the reaction compartment and the permeate compartment by a wall.
For effective condensation under the reaction conditions, the
condensing surface is preferably maintained at a temperature in the
range of 50 to 150.degree. C. The inventors however found that
water can particularly effectively be condensed at less than
100.degree. C., preferably less than 50.degree. C.
[0028] Surprisingly, the inventors found that in case the
condensing surface is 10.degree. C. or less, condensation of the
water occurs in such an effective manner, that a water mass flux
across the membrane can be achieved (see FIG. 10). The water mass
flux across the membrane results in even better DME yields. For
this reason, it is preferred that the cooling means of the reactor
described herein, are adapted to be able to cool, preferably
actively cool, the condensing surface to a temperature of less then
100.degree. C., preferably less than 50.degree. C., most preferably
less than 10.degree. C., during operation of the reactor wherein a
reaction is carried out at a temperature in the range of
150-400.degree. C., preferably in the range of 200 to 300.degree.
C., more preferably about 250.degree. C.
[0029] The condensed water can be collected and let out the
permeate compartment.
[0030] For the purpose of clarity and a concise description
features are described herein as part of the same or separate
embodiments, however, it will be appreciated that the scope of the
invention may include embodiments having combinations of all or
some of the features described. The invention can be illustrated by
the following non-limiting examples.
EXAMPLE 1--EFFECT OF WATER REMOVAL ON DME PRODUCTION
[0031] The following reaction and reactor is analysed in silico. In
a membrane reactor as illustrated in FIG. 5, at the feed side (i.e.
in the reaction compartment) a carbon dioxide hydrogenation
reaction takes place to produce methanol and subsequent conversion
to dimethyl ether, at 250.degree. C. and 50 bar, according to the
reactions 1-4. Reaction 3 is the combination of reaction 1 and 2.
By removing water from reaction 4, the reaction can be shifted to
the right-hand side to produce more dimethyl ether. Therefore,
in-situ removal of water from the mixture of H.sub.2, H.sub.2O, CO,
CH.sub.3OH, CH.sub.3OCH.sub.3 will drive the reactions towards more
DME production. To show the effect of water removal, two models
were created.
CO+2H.sub.2CH.sub.3OH (1)
CO.sub.2+H.sub.2CO+H.sub.2O (2)
CO.sub.2+3H.sub.2CH.sub.3OH+H.sub.2O (3)
2CH.sub.3OH CH.sub.3OCH.sub.3+H.sub.2O (4)
[0032] In the first model kinetic equations and equilibrium
constants for reaction 1-3 were used from Portha et al., Erena et
al. and Alharbi et al., to show the establishment of chemical
equilibrium in DME production. (see also Portha et al., Ind. Eng.
Chem. Res., 56 (2017) 13133-13145, Erena et al., Chem. Eng. J. 174
(2011) 660-667 and Alharbi et al. ACS Catal 5 (2015) 7186-7193.
This equilibrium limits the amount of DME produced. By modelling
the chemical equilibrium with and without water removal, it is
shown that in-situ water removal with membrane reactor leads to an
increase in DME production. Table 1 contains the starting
conditions and pressures for the equilibrium model.
TABLE-US-00001 TABLE 1 Input values for equilibrium model Input
values: T [.degree. C.] 250 P [bar] 50 Start pressure CO.sub.2
[bar] 7.5 Start pressure CO [bar] 7.5 Start pressure H.sub.2 [bar]
35
[0033] A second model calculates the steady state water removal by
the membrane reactor, driven by the pressure difference between
feed and permeate side. The calculated water removal from the feed
side is used as an input for the first model in the graph, to show
the increase in DME production. Additionally, variations in air gap
and temperature of the cooling element show the effect of different
parameter on the membrane reactor's performance
[0034] For modelling a steady state in-situ water removal during
conversion from CO.sub.2 to dimethyl ether (DME), theory was used
that is commonly applied for air gap membrane distillation
processes used in water treatment. FIG. 6 shows the temperature and
pressure profiles for the membrane reactor from FIG. 5. Water
removal through the membrane is driven by a pressure difference
between the water gas pressure on the feed side P.sub.F and the
water pressure just above the liquid film on the condenser surface
P.sub.C.
[0035] The water gas pressure on the feed side is calculated by
multiplying its calculated vapor fraction with the total pressure
on the feed side of the reaction.
P.sub.F=y.sub.i*P.sub.total (5)
[0036] On the other side of the membrane, the vapor pressure just
above the liquid film on the condenser surface is described by the
Antoine equation (see equation 6).
P C = 10 4.6543 - 1435.264 T cool - 64.848 ( 1.0 E + 5 ) ( 6 )
##EQU00001##
[0037] The dominant mechanism for the water vapor mass flux is
indicated by the Knudsen number. Equation 7 is used to calculate
the Knudsen number, with k.sub.B,T,r, d.sub.H2O and P as Boltzmann
constant, temperature, membrane thickness, diameter water molecule
and pressure.
K n = k B T 2 L .pi. d H 2 O 2 P 2 ( 7 ) ##EQU00002##
[0038] A membrane thickness of 1 mm gives a Knudsen number smaller
than 0.01 indicating that molecular diffusion through the air gap
will be the mass transfer limiting step at 250.degree. C. and 50
bar. Molecular diffusion through the air gap is usually the
limitation in mass transfer in air gap membrane distillation.
[0039] Equation 8 gives the water flux for transition flow. Based
on membrane properties in Table 2, a flux of 0.097 kg/m.sup.2/s was
calculated.
J = PDM .DELTA. p ( .tau..delta. + b ) RT ( P a ) ( 8 )
##EQU00003##
TABLE-US-00002 TABLE 2 properties used in flux calculations
Properties Values used in calculation Temperature condenser surface
[.degree. C.] 8 Radius condenser element [mm] 1 Air gap [mm] 2
Vapor fraction H.sub.2O in feed gases yi 2.94E-4 Length membrane
[m] 0.1 Membrane thickness [mm] 1 Membrane pore radius r [.mu.m] 1
Porosity .epsilon. 0.56 Tortuosity .tau. 2 Diffusion coefficient
water-air [m.sup.2/s] 2.8E-5 Flow rate H.sub.2O feed side [l/s]
3
[0040] Equation 8 represents the one-dimensional flux, whereas the
experimental setup is cylindrical. As a simplification, the surface
of the cylindrical membrane area was multiplied with the
one-dimensional flux to get the total flux to be deposited on the
inner cylindrical cooling element.
[0041] The result of the in silico reaction are illustrated in
FIGS. 7 to 9.
[0042] FIG. 7 shows the model for establishing chemical equilibrium
for reactions 1-4. This represents the chemical reactions that
occur on the feed side of the membrane reactor, without water
removal, starting from the pressures in Table 1. This can be
compared to the situation where the cooling element at the permeate
side of the membrane reactor is at the same temperature as the feed
side and there is no in-situ water removal. Water is produced in
reaction 3, but consumed in the water gas shift reaction (reaction
2 to the left hand side). Overall, without water removal, the end
concentration of DME is 6.21 vol %.
[0043] FIG. 8 shows the same chemical equilibrium model with a
constant water removal where 33% of the created water is removed.
This amount of water removal matches with the water flux calculated
in the model of the in-situ water removal membrane reactor with the
standard parameters in Table 2. An equilibrium model with an added
constant water removal corresponds to the situation where the
reactions 2 and 3 shift more to the right-hand side of the
equations due to the water removal, giving a higher DME yield. With
water removal matching to the flux of water removal calculated in
the membrane reactor model, the yield of DME rises with 51 vol %.
FIG. 9 shows the 51 vol % increase in DME yield due to water
removal.
EXAMPLE 2--EFFECT OF CONDENSING SURFACE TEMPERATURE ON THE FLUX OF
WATER ACROSS THE MEMBRANE
[0044] Based on the models described in Example 1, the water mass
flux over the membrane can be calculated, depending on the
temperature of the condensing surface. The results are depicted in
FIG. 10, from which it can be deduced that at condensing surface
temperatures of >50.degree. C., essentially no water flux is
expected. The operating temperatures of membrane is close to
200.degree. C. at which the condensation on/inside the membranes is
not taking place. The results further show that active cooling with
condensing temperature of <10.degree. C. results in positive
flux for water flux across the membrane.
* * * * *