U.S. patent application number 16/978001 was filed with the patent office on 2021-02-11 for bumper with viewing window for autonomous cleaner.
The applicant listed for this patent is David KHALIL, Joseph SEXTON, TECHTRONIC FLOOR CARE TECHNOLOGY LIMITED. Invention is credited to David Khalil, Joseph Sexton.
Application Number | 20210038033 16/978001 |
Document ID | / |
Family ID | 1000005209384 |
Filed Date | 2021-02-11 |



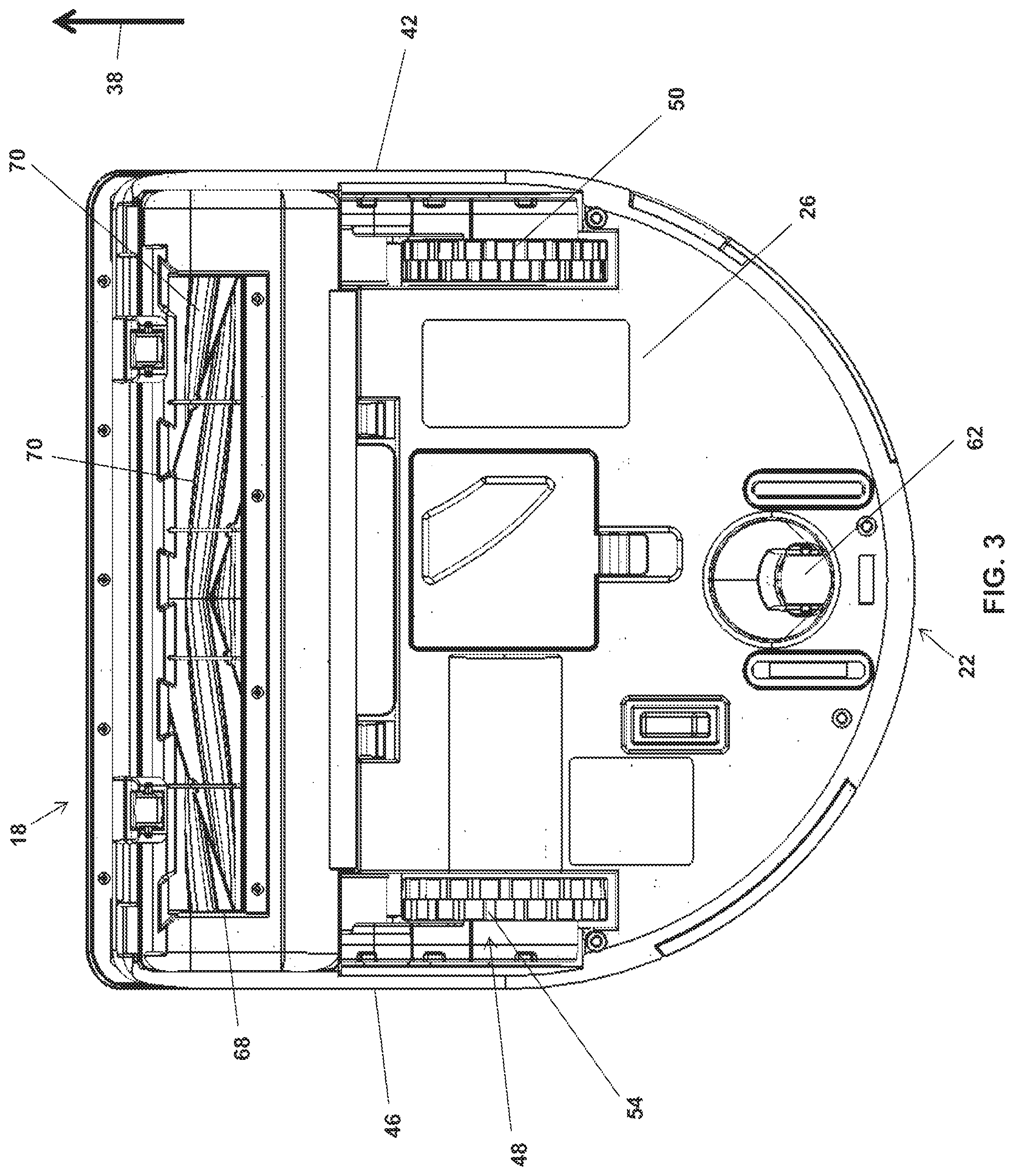


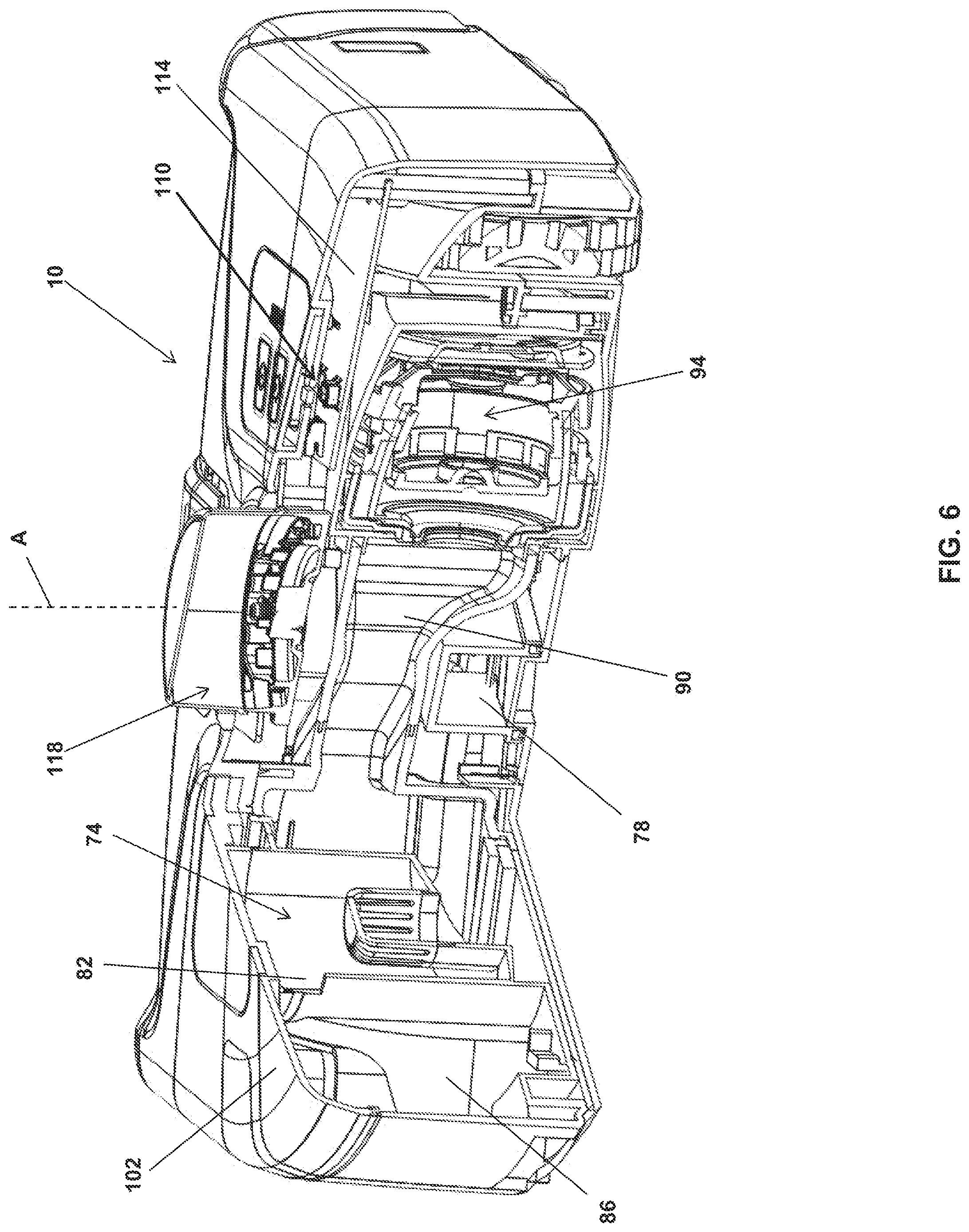
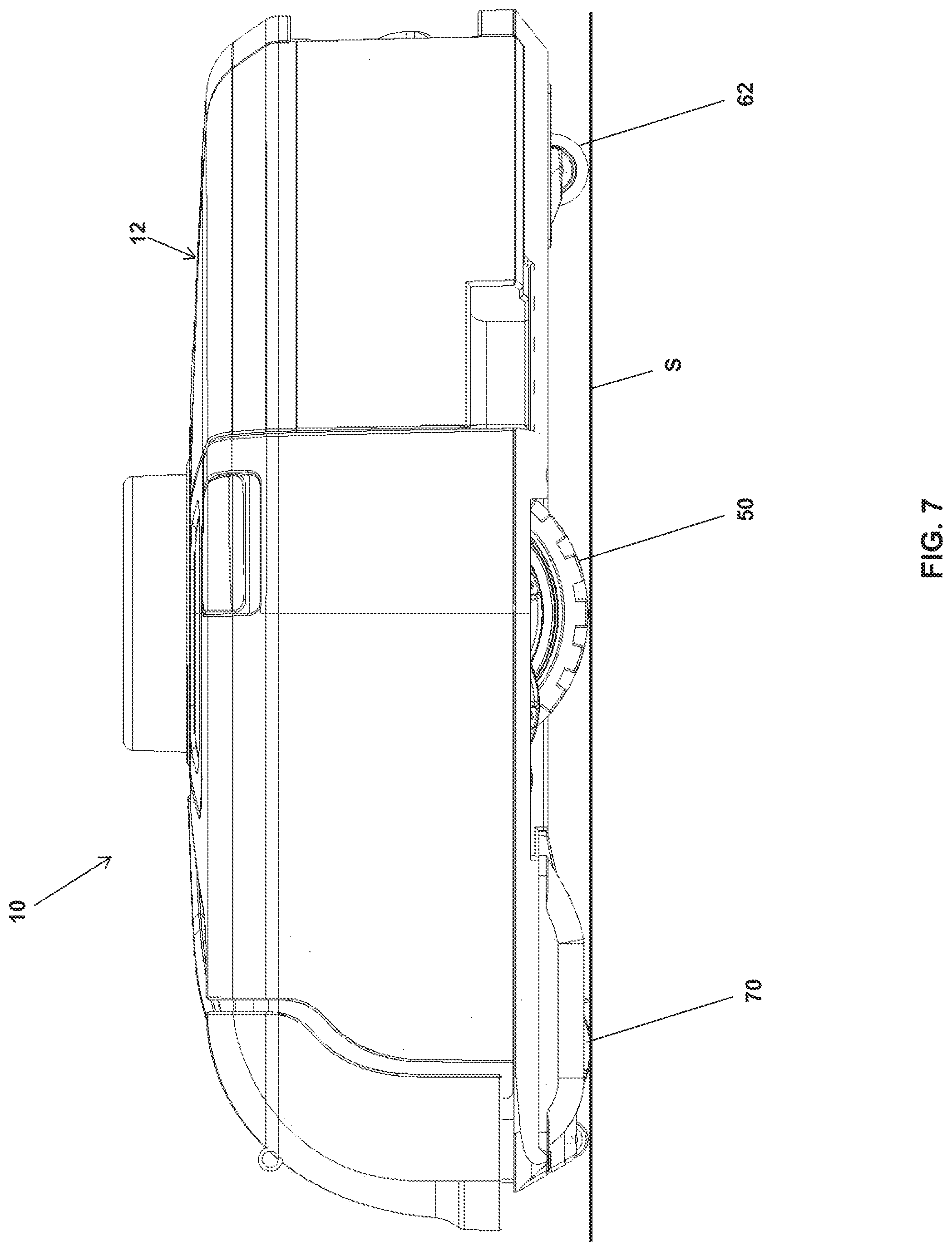
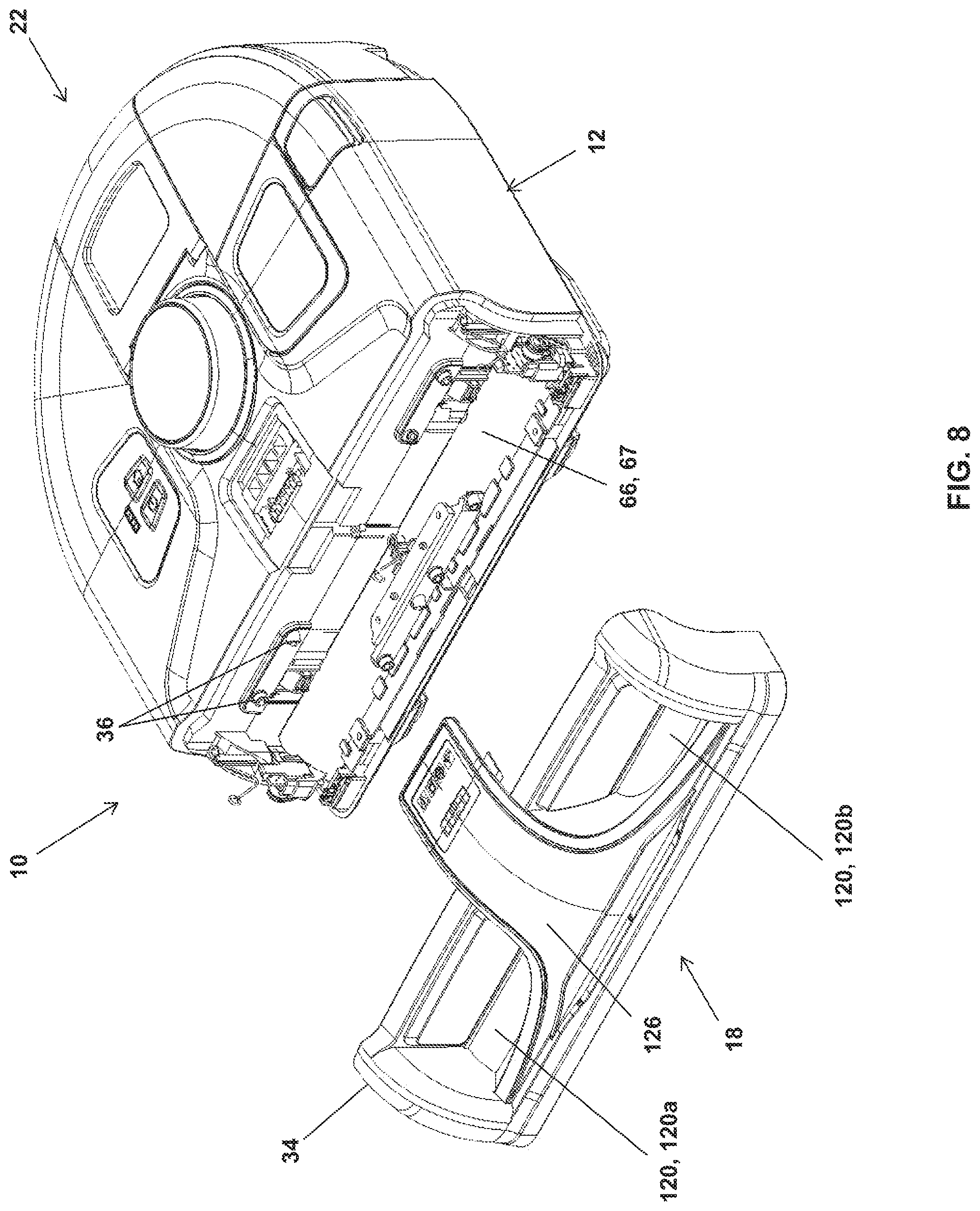


View All Diagrams
United States Patent
Application |
20210038033 |
Kind Code |
A1 |
Sexton; Joseph ; et
al. |
February 11, 2021 |
BUMPER WITH VIEWING WINDOW FOR AUTONOMOUS CLEANER
Abstract
An autonomous cleaner includes a body, a dust collection
assembly including a dust inlet disposed interior of a perimeter of
the body, a brush roll mounted adjacent the dust inlet and
proximate a transparent or translucent portion of the dust inlet, a
drive unit configured to move the body along a cleaning surface, a
controller configured to control an autonomous operation of the
drive unit, and a bumper operable to sense an impact mounted to and
at least partially along the perimeter of the body. The bumper has
at least one viewing window configured to allow a user to view the
brush roll through the at least one viewing window and the
transparent or translucent portion of the dust inlet.
Inventors: |
Sexton; Joseph;
(Huntersville, NC) ; Khalil; David; (College Park,
MD) |
|
Applicant: |
Name |
City |
State |
Country |
Type |
SEXTON; Joseph
KHALIL; David
TECHTRONIC FLOOR CARE TECHNOLOGY LIMITED |
Charlotte
College Park
Tortola |
NC
MD |
US
US
VG |
|
|
Family ID: |
1000005209384 |
Appl. No.: |
16/978001 |
Filed: |
March 5, 2019 |
PCT Filed: |
March 5, 2019 |
PCT NO: |
PCT/US2019/020801 |
371 Date: |
September 3, 2020 |
Related U.S. Patent Documents
|
|
|
|
|
|
Application
Number |
Filing Date |
Patent Number |
|
|
62639387 |
Mar 6, 2018 |
|
|
|
Current U.S.
Class: |
1/1 |
Current CPC
Class: |
A47L 2201/04 20130101;
A47L 9/2889 20130101; A47L 9/009 20130101; A47L 2201/022 20130101;
A47L 9/2826 20130101; A47L 9/0477 20130101 |
International
Class: |
A47L 9/04 20060101
A47L009/04; A47L 9/28 20060101 A47L009/28; A47L 9/00 20060101
A47L009/00 |
Claims
1. An autonomous cleaner comprising: a body having a perimeter; a
dust collection assembly including a dust inlet disposed interior
of the perimeter and a brush roll mounted adjacent the dust inlet
and proximate a transparent or translucent portion of the dust
inlet; a drive unit configured to move the body along a cleaning
surface; a controller configured to control an autonomous operation
of the drive unit; and a bumper operable to sense an impact mounted
to and at least partially along the perimeter of the body, the
bumper having at least one viewing window configured to allow a
user to view the brush roll through the at least one viewing window
and the transparent or translucent portion of the dust inlet.
2. The autonomous cleaner of claim 1, wherein the at least one
viewing window defines an aperture that extends through the
bumper.
3. The autonomous cleaner of claim 1, wherein the at least one
viewing window is formed from a transparent or translucent
material.
4. The autonomous cleaner of claim 1, further comprising a suction
motor configured for generating an air flow through the dust
inlet.
5. The autonomous cleaner of claim 4, the dust collection assembly
further comprising a dust collection chamber in communication with
the dust inlet and the suction motor.
6. The autonomous cleaner of claim 1, the dust collection assembly
further comprising a dust collection chamber proximate the dust
inlet and brush roll configured for receiving dust swept by the
brush roll.
7. The autonomous cleaner of claim 1, wherein the bumper defines a
chamber configured to receive the transparent or translucent
portion of the dust inlet therein.
8. The autonomous cleaner of claim 1, wherein the body further
comprises a chassis configured to support the dust collection
assembly at a front end of the autonomous cleaner, wherein the
bumper is mounted to the body at the front end and the at least one
viewing window is disposed adjacent the transparent or translucent
portion of the dust collection assembly relative to the cleaning
surface.
9. The autonomous cleaner of claim 1, wherein the bumper includes
an opaque central portion and the at least one viewing window
includes a pair of viewing windows that are formed on opposite
sides of the opaque central portion.
10. The autonomous cleaner of claim 9, wherein the bumper includes
a frame member having opposing first and second side walls, a neck
body located between the first and second side walls, a first rear
wall extending from the neck body toward the first side wall, a
second rear wall extending from the neck body toward the second
side wall, a first arcuate arm extending forwardly relative to the
first rear wall and outwardly from the neck body to the first side
wall and a second arcuate arm extending forwardly relative to the
second rear wall and outwardly from the neck body to the second
side wall, and wherein the at least one viewing window includes a
first viewing window formed between the first arcuate arm and the
first rear wall and a second viewing window formed between the
second arcuate arm and the second rear wall.
11. The autonomous cleaner of claim 1, wherein the bumper includes
a frame member having opposing first and second side walls and a
rear wall extending from the first side wall extending toward the
second side wall, and wherein the at least one viewing window
includes a first viewing window provided in the frame member
forwardly of the rear wall.
12. The autonomous cleaner of claim 11 further comprising a sensor
operable in combination with the controller to sense a surrounding
environment, the sensor being mounted to the body at the front end
of the autonomous cleaner, wherein the rear wall of the bumper
defines a pass-through opening that extends through the rear wall
and is aligned with the sensor.
13. The autonomous cleaner of claim 1, wherein the dust inlet is
proximate a forward portion of the perimeter of the body.
Description
CROSS-REFERENCE TO RELATED APPLICATIONS
[0001] This application claims priority to U.S. Provisional Patent
Application No. 62/639,387 filed Mar. 6, 2018, the entire contents
of which are hereby incorporated by reference herein.
BACKGROUND
[0002] The present disclosure relates to a bumper with a viewing
window associated with an autonomous cleaner
[0003] Vacuum cleaners and sweepers generally use mechanical action
and/or air flow to draw dust, dirt, or other debris from a surface.
A vacuum cleaner typically draws a combination of air and dust,
dirt, or other debris into the cleaner through a floor nozzle. This
"dirty air" typically enters a dust separator in the vacuum that
separates the dust, dirt, or debris from the air. A bin or bag
collects the separated dust, dirt, or debris separated from the air
for later disposal. The resulting "clean air" exits the dust
separator where it is exhausted from the vacuum cleaner. A sweeper
typically uses mechanical action to sweep dust, dirt, or other
debris from a floor into the sweeper through a dirt inlet into a
bin for later disposal. An autonomous cleaner may be a vacuum
cleaner or sweeper that is configured to traverse and clean an area
without requiring a user to operate.
SUMMARY
[0004] In some embodiments, the present disclosure relates to an
autonomous cleaner. The autonomous cleaner comprises a body having
a perimeter, a dust collection assembly including a dust inlet
disposed interior of the perimeter and a brush roll mounted
adjacent the dust inlet and proximate a transparent or translucent
portion of the dust inlet, a drive unit configured to move the body
along a cleaning surface, a controller configured to control an
autonomous operation of the drive unit, and a bumper operable to
sense an impact mounted to and at least partially along the
perimeter of the body. The bumper has at least one viewing window
configured to allow a user to view the brush roll through the at
least one viewing window and the transparent or translucent portion
of the dust inlet.
[0005] Other features and advantages of the present disclosure will
become apparent by consideration of the following description and
the appended claims when taken in connection with the accompanying
drawings.
BRIEF DESCRIPTION OF THE DRAWINGS
[0006] FIG. 1 is a perspective view of an autonomous cleaner
engaged with a charging base in accordance with an embodiment of
the present disclosure.
[0007] FIG. 2 is a perspective view of the autonomous cleaner of
FIG. 1.
[0008] FIG. 3 is a plan view of the bottom of the autonomous
cleaner of FIG. 2.
[0009] FIG. 4 is a front perspective view of the autonomous cleaner
of FIG. 2 with a portion of an outer housing removed to illustrate
a nozzle, a conduit, and a portion of a separator assembly.
[0010] FIG. 5 is a perspective view of the rear of the autonomous
cleaner of FIG. 2.
[0011] FIG. 6 is a perspective view of the autonomous cleaner of
FIG. 5 with a portion of the outer housing removed to illustrate a
portion of the separator assembly, a dust cup, and a suction motor
assembly.
[0012] FIG. 7 is a right side elevational view of the autonomous
cleaner of FIG. 2.
[0013] FIG. 8 is a partially exploded perspective view of the
autonomous cleaner of FIG. 2.
[0014] FIG. 9 is a front perspective view of the bumper of the
autonomous of FIG. 2.
[0015] FIG. 10 is a partially exploded perspective view of the
bumper of FIG. 9.
[0016] FIG. 11 is a rear bottom perspective view of the bumper of
FIG. 9.
DETAILED DESCRIPTION
[0017] Before any embodiments are explained in detail, it is to be
understood that the present disclosure is not limited in its
application to the details of construction and the arrangement of
components set forth in the following description or illustrated in
the following drawings. The present disclosure is capable of other
embodiments and of being practiced or of being carried out in
various ways. It should be understood that the description of
specific embodiments is not intended to limit the disclosure from
covering all modifications, equivalents and alternatives falling
within the spirit and scope of the disclosure as defined in the
appended claims. Also, it is to be understood that the phraseology
and terminology used herein is for the purpose of description and
should not be regarded as limiting.
[0018] Referring now to the figures, FIG. 1 illustrates an
embodiment of an autonomous cleaner 10 having a bumper with a
viewing window (as described below). The autonomous cleaner 10 can
selectively engage a charging base 14. The charging base 14 (or
base station 14 or charging station 14) can be coupled to a source
of electricity (e.g., to a wall outlet by a cord, etc.). In
response to the autonomous cleaner 10 engaging the charging base
14, the charging base 14 can supply electricity to the autonomous
cleaner 10, and more specifically can supply electricity to
recharge one or more batteries (not shown) that power the
autonomous cleaner 10.
[0019] Referring to FIGS. 2-3, the autonomous cleaner 10 is shown
disengaged from the charging base 14. The autonomous cleaner 10
includes a body 12 having a perimeter P and a front end 18 that is
opposite a back end 22. The autonomous cleaner 10 also includes a
chassis 26 (or an undercarriage 26 or a frame 26) (shown in FIG.
3). An outer housing 30 (or outer shell 30) cooperates with the
chassis 26 to encase one or more components of the autonomous
cleaner 10. The chassis 26 and the outer housing 30 may cooperate
to define the body 12.
[0020] With specific reference to FIG. 2, a front bump sensor 34
(or bumper 34) is positioned at the front end 18 of the autonomous
cleaner 10 and is mounted to and at least partially along the
perimeter P of the body 12. The front bump sensor 34 is provided at
a leading edge of the autonomous cleaner 10 in a direction of
forward travel 38. The direction of forward travel 38 generally
extends from the back end 22 towards the front end 18. The
autonomous cleaner 10 is also configured to operate in a direction
opposite the direction of forward travel 38, or in reverse.
[0021] Referring now to FIG. 3, the autonomous cleaner 10 includes
a drive assembly 48. The drive assembly 48 includes a pair of
motorized drive wheels 50, 54. A first drive wheel 50 is positioned
proximate a first side 42, while a second drive wheel 54 is
positioned proximate a second side 46 of the autonomous cleaner 10.
The drive wheels 50, 54 can operate (or rotate) independently of
each other. As such, the drive wheels 50, 54 can rotate at the same
speed, resulting in the direction of forward travel 38 being
generally straight, or can rotate at different speeds to facilitate
a turning movement of the autonomous cleaner 10. The autonomous
cleaner 10 can also include one or more third wheels 62, which can
be driven or non-driven (e.g., a caster wheel 62).
[0022] The drive assembly 48 is operably connected to a controller
110 (shown in FIG. 6) of the autonomous cleaner 10. The controller
110 can be provided in association with a printed circuit board
114. The controller 110 may be configured to map the area to be
cleaned and to operate the plurality of drive wheels 50, 54 to move
the autonomous cleaner 10 (or the associated chassis 26) along a
cleaning surface S (shown in FIG. 7) within the area to be
cleaned.
[0023] For example, the controller 110 may be in communication with
an area sensing unit that is configured to map the area to be
cleaned. In the embodiment illustrated in FIGS. 4 and 6, the area
sensing unit can be a laser distance sensor 118. The laser distance
sensor 118 includes a laser emitter (not shown) and a light sensor
(not shown). The laser emitter emits a beam (or a light beam or
emitted light), and the light sensor detects light from the beam
that is reflected by an obstacle (or reflected light). The light
sensor outputs a signal to the controller 110 corresponding to a
distance to the obstacle. In one example, the laser distance sensor
118 and the controller 110 are configured to calculate a distance
to the obstacle by triangulation using the angle of reflected light
and the distance between the laser emitter and the light sensor. In
other embodiments, other laser rangefinders may be used. The laser
distance sensor 118 measures a distance to objects at points around
the autonomous cleaner 10 as the cleaner operates such that the
controller 110 can determine the bounds of the map of the area to
be cleaned as the autonomous cleaner 10 moves about the area.
[0024] In addition, the autonomous cleaner 10 can include one or
more odometry encoders (not shown) operably connected to the drive
wheels 50, 54, and configured to determine a distance and an
estimated direction the autonomous cleaner 10 travels based on
rotation of one or both of the drive wheels 50, 54. The odometry
data from the encoders can be combined with the laser distance
sensor data from the laser distance sensor 118 by the controller
110 using Simultaneous Localization and Mapping (SLAM) algorithms,
or other mapping techniques, to develop the map of the area to be
cleaned (or mapped area). The controller 110 can also control the
autonomous cleaner 10 within the mapped area based on where the
autonomous cleaner 10 travels.
[0025] In addition, the controller 110 may receive signals from one
or more obstacle detection sensors to identify objects (or
obstacles) in the area to be cleaned (e.g., a chair, a sofa, an
ottoman, etc.). Obstacle detection sensors may include proximity
sensors (e.g., infrared sensors, ultrasonic sensors, and tactile
sensors), cliff sensors, bump sensors, or any other sensor that is
configured to sense or detect an object as the autonomous cleaner
travels. The controller 110 can then incorporate those objects into
the map of the area to be cleaned. In the illustrated embodiment,
the controller 110 may receive signals, for example, from the front
bump sensor 34 to identify objects (or obstacles) in the area to be
cleaned.
[0026] Referring back to FIGS. 2-4, the autonomous cleaner 10
includes a dust collection assembly 64 having a dust inlet 66. In
the illustrated embodiment, the autonomous cleaner 10 is a vacuum
cleaner and the dust inlet is a nozzle 66 (shown in FIG. 2).
Optionally, the dust collection assembly 64 includes a brush roll
70 (shown in FIGS. 3-4) mounted adjacent the dust inlet or nozzle
66 that is configured to rotate at least partially within the dust
inlet or nozzle 66 for engaging a portion of the cleaning surface S
to facilitate dust collection. The nozzle 66 may be disposed
interior of the perimeter P of the body 12 proximate a forward
portion of the perimeter P of the body 12 and may be carried by the
chassis 26. The brush roll 70 may extend through an air inlet 68,
for example, an air inlet slot, of the nozzle 66 such that
engagement of the brush roll 70 to a portion of the cleaning
surface S cooperates with air flow into the air inlet slot 68 to
facilitate dust collection. In an alternative embodiment, the
autonomous cleaner may be a sweeper where the brush roll 70 extends
through the dust inlet 66 such that engagement of the brush roll 70
to a portion of the cleaning surface S sweeps dust, dirt, or other
debris into the dirt inlet to facilitate dust collection. To
facilitate rotation, the brush roll 70 may be operably connected to
a brush roll motor (not shown) by a belt (e.g., a geared belt,
etc.) (not shown) and may be carried by the chassis 26. With
specific reference to FIG. 4, the nozzle 66 is fluidly connected to
a dust separator assembly 74 by a conduit 78 for transporting dirty
air (i.e., air containing dust) drawn into the nozzle 66 at the air
inlet 68 to the separator assembly 74. In the illustrated vacuum
cleaner embodiment, the separator assembly 74 is a cyclonic
separator. In other embodiments, the separator assembly 74 can be
any suitable separator assembly (e.g., a bag unit, a filter unit,
any suitable non-cyclone separator, etc.).
[0027] With continued reference to FIG. 4, dust that exits the
separator assembly 74 through a dust outlet 82 collects in a dust
cup 86 (or a dust collection chamber 86 or a dirt cup 86 or a
collection bin 86) (shown in FIG. 6). In an alternative embodiment,
the autonomous cleaner is a sweeper where the dust collection
chamber 86 is proximate the dust inlet 66 and brush roll 70 and is
configured for receiving dust swept by the brush roll. A portion of
the outer housing 30 may form a removable cover (not shown)
configured to cover the separator assembly 74 (or portion thereof)
and the dust cup 86 (or portion thereof). With reference to FIG. 6,
cleaned air exits through the separator assembly 74 by a clean air
outlet 90, and travels to a suction motor assembly 94 and then is
discharged through a vent 98 (shown in FIG. 5). More specifically,
the suction motor assembly 94, which is in fluid communication with
the nozzle 66 via the separator assembly 74, includes a suction
motor 96 that rotates a fan or impeller to generate a suction
airflow at the air inlet 68 for drawing dirty air through the
suction nozzle 66 and into the separator assembly 74. The nozzle 66
has a transparent or translucent portion 67 that is formed
proximate the brush roll 70. For example, the transparent or
translucent portion 67 may be formed above the brush roll 70
(relative to the cleaning surface S) and may extend along a portion
or the entire length of the nozzle 66.
[0028] Referring to FIGS. 5 and 8-9, an energy storage system 106
(or a battery pack 106) is positioned in the autonomous cleaner 10
to store and provide electricity to operate the autonomous cleaner
10, including various components and associated electronic circuits
thereof, such as the drive assembly 48, the suction motor 96, the
controller 110 and the laser distance sensor 118. The energy
storage system 106 can include a plurality of cells or battery
cells (not shown). The illustrated energy storage system 106 can be
recharged (e.g., in a remote charging station, at the charging base
14, etc.).
[0029] With reference to FIGS. 8-11, the bumper 34 may include one
or more viewing windows 120 for viewing the brush roll 70 (shown in
FIGS. 3-4) mounted at the air inlet 68 (shown in FIGS. 3-4) of the
nozzle 66. In the illustrated embodiment, the bumper 34 includes an
opaque central portion 126 and a pair of viewing windows 120a and
120b formed in the bumper 34 on opposite sides of the opaque
central portion 126. More specifically, the bumper 34 may include a
frame member 124 having opposing first and second side walls 130
and 132, a neck body 134 located between the first and second side
walls 130 and 132, a first rear wall 136 extending from the neck
body 134 toward the first side wall 130, and a second rear wall 138
extending from the neck body 134 toward the second side wall 132.
Alternatively, the frame member includes a rear wall extending
between the opposing first and second side walls 130, 132.
Optionally, a first arcuate arm 140 extends forwardly relative to
the first rear wall 136 and outwardly from the neck body 134 to the
first side wall 130. Similarly, a second arcuate arm 142 extends
forwardly relative to the second rear wall 138 and outwardly from
the neck body 134 to the second side wall 132. The first viewing
window 120a may be provided in the frame member 124 forwardly of
the first rear wall 136 and the second viewing window 120b is
provided in the frame member 124 forwardly of the second rear wall
138. In the illustrated embodiment, the first viewing window 120a
is formed as a first aperture or window between the first arcuate
arm 140 and the first rear wall 136 and the second viewing window
120b is formed as a second aperture or window between the second
arcuate arm 142 and the second rear wall 138, the apertures or
windows corresponding to the transparent or translucent portion
67.
[0030] The frame member 124 may be an assembly of components, as
shown in the illustrated embodiment, or may be a single piece,
including for example an injection molded or other unitary,
one-piece, integral construction. Also, in other embodiments, the
viewing windows 120 of the bumper 34 may be formed from a
transparent or translucent material, thereby allowing at least some
visible light to pass through the material so that the nozzle 66
behind the bumper 34 (and the brush roll 70, as described below) is
visible. In addition, although the illustrated embodiment
illustrates a pair of viewing windows 120, it should be appreciated
that other embodiments may include a bumper having a single viewing
window, for example, a single viewing window that extends
uninterrupted along the entire length of the bumper, or a bumper
having three or more viewing windows, which may, for example, be
formed between a plurality of opaque portions of the bumper.
[0031] With reference again to FIGS. 8-11, the transparent or
translucent portion 67 of the dust inlet or nozzle 66 is received
in a chamber 144 defined by the bumper 34. The viewing windows 120
of the bumper 34 are disposed adjacent the transparent or
translucent portion 67 of the nozzle 66 such that a user can view
the brush roll 70 through the viewing windows 120 and the
transparent portion 67 of the nozzle 66. In the illustrated
embodiment, for example, the viewing windows 120 are disposed above
the transparent or translucent portion 67 of the nozzle 66
(relative to the cleaning surface S). The viewing windows 120 of
the bumper 34 advantageously permit a user to visually detect
whether an object is lodged in the nozzle 66 or the brush roll 70
fails to rotate properly during operation of the autonomous cleaner
10.
[0032] In addition, the first rear wall 136 of the bumper 34 may
define one or more pass-through openings 146 that extend through
the first rear wall 136. Each pass-through opening 146 may be
aligned with an obstacle detection sensor 36, such as an infrared
sensor or an ultrasonic sensor, that is mounted to the body 12 at
the front end 18 of the autonomous cleaner 10 and is operable in
combination with the controller 110 to remotely sense a surrounding
environment, for example to identify objects (or obstacles) in the
area to be cleaned. The pass-through openings 146 may be covered by
sensor covers 148 to protect the obstacle detection sensors 36 from
dust or dirt buildup or other damage without interfering with the
operation of the sensors.
[0033] Thus, the present disclosure provides, among other things, a
bumper with a viewing window for use with an autonomous cleaner.
Various features and advantages of the present disclosure are set
forth in the following claims.
* * * * *