U.S. patent application number 16/938543 was filed with the patent office on 2021-01-28 for gas furnace.
The applicant listed for this patent is LG ELECTRONICS INC.. Invention is credited to Doyong Ha, Yongki Jeong, Jusu KIM, Hansaem Park, Janghee Park.
Application Number | 20210025621 16/938543 |
Document ID | / |
Family ID | 1000004989159 |
Filed Date | 2021-01-28 |




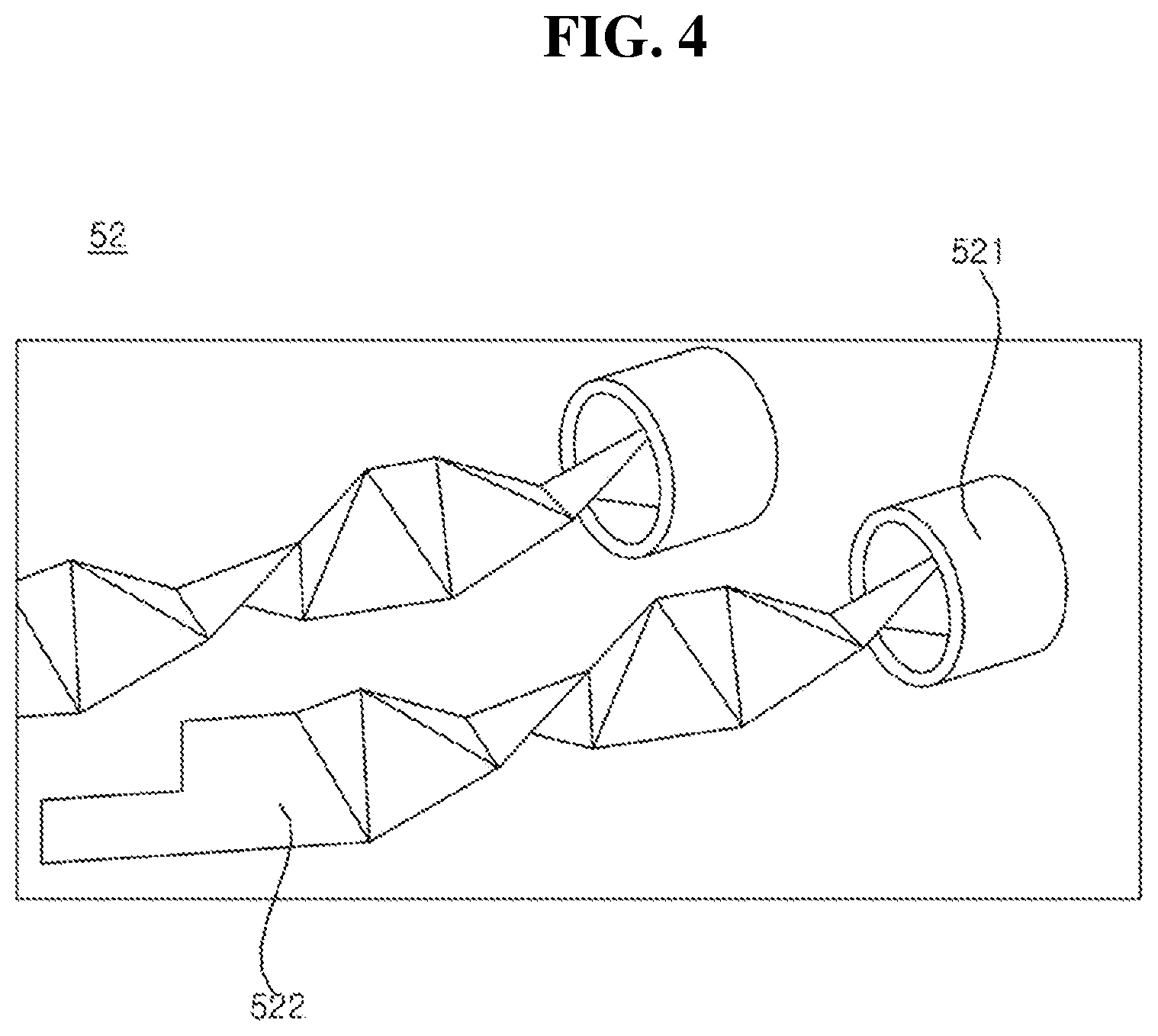






View All Diagrams
United States Patent
Application |
20210025621 |
Kind Code |
A1 |
KIM; Jusu ; et al. |
January 28, 2021 |
GAS FURNACE
Abstract
Provided is a gas furnace. The gas furnace includes: a manifold
with an exhaust port for discharging fuel gas; a nozzle attached to
the exhaust port; a burner for burning a mixture of air and fuel
gas ejected from the nozzle; a primary heat exchanger that provides
a first flow path and allows a combustion gas produced by the
combustion of the mixture to move through the first flow path; and
a secondary heat exchanger located adjacent to the primary heat
exchanger, that provides a second flow path and allows the
combustion gas discharged from the primary heat exchanger to move
through the second flow path, wherein the secondary heat exchanger
includes: at least one tube forming the second flow path; and a
baffle inserted into the at least one tube, the baffle including: a
plate longitudinally extending in a lengthwise direction and
twisted in the shape of a screw; and a plurality of holes formed to
penetrate the plate.
Inventors: |
KIM; Jusu; (Seoul, KR)
; Ha; Doyong; (Seoul, KR) ; Jeong; Yongki;
(Seoul, KR) ; Park; Janghee; (Seoul, KR) ;
Park; Hansaem; (Seoul, KR) |
|
Applicant: |
Name |
City |
State |
Country |
Type |
LG ELECTRONICS INC. |
Seoul |
|
KR |
|
|
Family ID: |
1000004989159 |
Appl. No.: |
16/938543 |
Filed: |
July 24, 2020 |
Current U.S.
Class: |
1/1 |
Current CPC
Class: |
F23D 14/22 20130101;
F24H 9/0063 20130101; F24H 3/025 20130101; F23D 14/48 20130101 |
International
Class: |
F24H 3/02 20060101
F24H003/02; F23D 14/22 20060101 F23D014/22; F23D 14/48 20060101
F23D014/48; F24H 9/00 20060101 F24H009/00 |
Foreign Application Data
Date |
Code |
Application Number |
Jul 26, 2019 |
KR |
10-2019-0090923 |
Claims
1. A gas furnace comprising: a manifold with an exhaust port for
discharging fuel gas; a nozzle attached to the exhaust port; a
burner for burning a mixture of air and fuel gas ejected from the
nozzle; a primary heat exchanger that provides a first flow path
and allows a combustion gas produced by the combustion of the
mixture to move through the first flow path; and a secondary heat
exchanger located adjacent to the primary heat exchanger, that
provides a second flow path and allows the combustion gas
discharged from the primary heat exchanger to move through the
second flow path, wherein the secondary heat exchanger comprises:
at least one tube forming the second flow path; and a baffle
inserted into the at least one tube, wherein the baffle comprises:
a plate extending long in a lengthwise direction of the tube and
twisted in the shape of a screw; and a plurality of holes formed to
penetrate the plate.
2. The gas furnace of claim 1, wherein the plate comprises a
plurality of segments, and the plurality of holes are formed in the
plurality of segments, respectively.
3. The gas furnace of claim 1, wherein the plate comprises a
plurality of segments, and the plurality of holes are formed in
each of the plurality of segments.
4. The gas furnace of claim 1, wherein the plurality of holes are
formed for each pitch of a screw pattern on the plate, and are
sequentially arranged along the central axis of the tube.
5. The gas furnace of claim 1, wherein the plurality of holes are
formed for each pitch of a screw pattern on the plate and arranged
in an alternating fashion along the central axis of the tube.
6. The gas furnace of claim 1, wherein the plurality of holes
comprises: a plurality of holes in a first row formed along the
central axis of the tube; a plurality of holes in a second row
formed along the central axis of the tube, spaced apart from the
central axis of the tube; a plurality of holes in a third row
formed along the central axis of the tube, spaced apart from the
central axis of the tube, and facing the plurality of holes in the
second row with respect to the central axis of the tube.
7. The gas furnace of claim 1, wherein the plurality of holes form
cutouts on at least one edge of the plate in a width direction, and
the cutouts have an overall triangular shape.
8. The gas furnace of claim 7, wherein the cutouts have an overall
rectangular shape.
Description
CROSS-REFERENCE TO RELATED APPLICATION
[0001] This application claims the priority from Korean Patent
Application No. 10-2019-0090923, filed on Jul. 26, 2019, in the
Korean Intellectual Property Office, the disclosure of which is
incorporated herein by reference in its entirety.
FIELD OF THE DISCLOSURE
[0002] The present disclosure relates to a gas furnace. More
particularly, the present disclosure relates to a gas furnace with
a baffle that can facilitate heat transfer and/or condensate water
formation.
RELATED ART
[0003] Generally, a gas furnace is an apparatus that heats up a
room by supplying air heated through heat exchange with a flame and
high-temperature combustion gas produced by the combustion of a
fuel gas.
[0004] The gas furnace may have a primary heat exchanger and a
secondary heat exchanger. The secondary heat exchanger is generally
a finned tube heat exchanger.
[0005] US 2006/0213499 A1 discloses a baffle that is inserted into
a tube to enhance the heat transfer efficiency of the secondary
heat exchanger.
[0006] However, the above-mentioned US 2006/0213499 A1 may have the
problem of a pressure drop in the tube and a flow stagnation at the
center of the tube, since the baffle is inserted into the tube.
Another problem is that the power consumption of a fan increases
with increasing resistance to gas flow in the tube with the baffle
inserted in it. Other problems include condensate water standing in
the tube into which the baffle is inserted.
SUMMARY OF THE DISCLOSURE
[0007] A first problem to be solved by the present disclosure is to
provide a gas furnace that can alleviate the pressure drop in the
tube.
[0008] A second problem to be solved by the present disclosure is
to provide a gas furnace that can alleviate the stagnation of flow
in the tube.
[0009] A third problem to be solved by the present disclosure is to
provide a gas furnace that can reduce the power consumption of the
fan by decreasing the resistance to gas flow in a heat
exchanger.
[0010] A fourth problem to be solved by the present disclosure is
to provide a gas furnace that can alleviate condensate water
standing in the tube into which the baffle is inserted.
[0011] Technical problems to be solved by the present disclosure
are not limited to the above-mentioned technical problems, and
other technical problems not mentioned herein may be clearly
understood by those skilled in the art from description below.
[0012] To solve the above-mentioned problems, there is provided a
gas furnace according to an aspect of the present disclosure,
including: a manifold with an exhaust port for discharging fuel
gas; a nozzle attached to the exhaust port; a burner for burning a
mixture of air and fuel gas ejected from the nozzle; a primary heat
exchanger that provides a first flow path and allows a combustion
gas produced by the combustion of the mixture to move through the
first flow path; and a secondary heat exchanger located adjacent to
the primary heat exchanger, that provides a second flow path and
allows the combustion gas discharged from the primary heat
exchanger to move through the second flow path, wherein the
secondary heat exchanger includes: at least one tube forming the
second flow path; and a baffle inserted into the at least one tube,
wherein the baffle includes: a plate extending long in a lengthwise
direction of the tube and twisted in the shape of a screw; and a
plurality of holes formed to penetrate the plate.
[0013] According to another aspect of the present disclosure, the
plate may include a plurality of segments, and the plurality of
holes may be formed in the plurality of segments, respectively.
[0014] According to another aspect of the present disclosure, the
plate may include a plurality of segments, and the plurality of
holes may be formed in each of the plurality of segments.
[0015] According to another aspect of the present disclosure, the
plurality of holes may be formed for each pitch of a screw pattern
on the plate, and are sequentially arranged along the central axis
of the tube.
[0016] According to another aspect of the present disclosure, the
plurality of holes may be formed for each pitch of a screw pattern
on the plate and arranged in an alternating fashion along the
central axis of the tube.
[0017] According to another aspect of the present disclosure, the
plurality of holes may include: a plurality of holes in a first row
formed along the central axis of the tube; a plurality of holes in
a second row formed along the central axis of the tube, spaced
apart from the central axis of the tube; a plurality of holes in a
third row formed along the central axis of the tube, spaced apart
from the central axis of the tube, and facing the plurality of
holes in the second row with respect to the central axis of the
tube.
[0018] According to another aspect of the present disclosure, the
plurality of holes may form cutouts on at least one edge of the
plate in a width direction, and the cutouts may have an overall
triangular shape.
[0019] According to another aspect of the present disclosure, the
cutouts may have an overall rectangular shape.
[0020] Means for solving other problems not mentioned above will be
easily deduced from the descriptions of embodiments of the present
disclosure.
BRIEF DESCRIPTION OF THE DRAWINGS
[0021] FIG. 1 is a view illustrating an example of a gas furnace
according to an exemplary embodiment of the present disclosure.
[0022] FIG. 2 is a view illustrating a part of the construction of
the gas furnace according to the exemplary embodiment of the
present disclosure.
[0023] FIG. 3 is a view illustrating another part of the
construction of the gas furnace according to the exemplary
embodiment of the present disclosure.
[0024] FIGS. 4 and 5 are views illustrating a construction in which
a baffle is inserted into a heat exchanger tube according to the
exemplary embodiment of the present disclosure.
[0025] FIGS. 6 to 13 are views illustrating various examples of the
baffle according to the exemplary embodiment of the present
disclosure.
DESCRIPTION OF EXEMPLARY EMBODIMENTS
[0026] Advantages and features of the present disclosure and
methods for achieving them will be made clear from embodiments
described below in detail with reference to the accompanying
drawings. The present disclosure may, however, be embodied in many
different forms and should not be construed as being limited to the
embodiments set forth herein. Rather, these embodiments are
provided so that this disclosure will be thorough and complete, and
will fully convey the scope of the disclosure to those skilled in
the art. The present disclosure is merely defined by the scope of
the claims. Like reference numerals refer to like elements
throughout the specification.
[0027] The present disclosure will be described with respect to a
spatial orthogonal coordinate system illustrated in FIG. 2 and
other figures where X, Y, and Z axes are orthogonal to each other.
In this specification, the X axis, Y axis, and Z axis are defined
assuming that the up-down direction is along the Z axis and the
front-back direction is along the X axis. Each axis direction
(X-axis direction, Y-axis direction, and Z-axis direction) refers
to two directions in which each axis runs. Each axis direction with
a `+` sign in front of it (+X-axis direction, +Y-axis direction,
and +Z-axis direction) refers to a positive direction which is one
of the two directions in which each axis runs. Each axis direction
with a `-` sign in front of it (-X-axis direction, -Y-axis
direction, and -Z-axis direction) refers to a negative direction
which is the other of the two directions in which each axis
runs.
[0028] Referring to FIGS. 1 and 2, the gas furnace 10 is an
apparatus that heats up a room by supplying air heated through heat
exchange with a flame and high-temperature combustion gas P
produced by the combustion of a fuel gas R.
[0029] The gas furnace 10 according to the exemplary embodiment of
the present disclosure includes a gas valve 20 that supplies a fuel
gas R to a manifold 30, a burner 40 in which the fuel gas R
released from the manifold 30 is mixed with air and flows in an
air-fuel mixture, and a heat exchanger 50 through which a
combustion gas P produced by the combustion of the air-fuel mixture
in the burner 40 flows.
[0030] Furthermore, the gas furnace 10 include an inducer 70 for
inducing a flow of combustion gas P to an exhaust pipe 80 through
the heat exchanger 50, a blower 60 for blowing air around the heat
exchanger 50 so that the air is supplied to a room, and a
condensate water trap 90 for collecting condensate water produced
in the heat exchanger 50 and/or the exhaust pipe 80 and discharging
it.
[0031] The fuel gas R supplied through the gas valve 20 may
include, for example, liquefied natural gas (LNG), which is natural
gas that has been cooled down to liquid form, or liquefied
petroleum gas (LPG), which is prepared by pressurizing gaseous
by-products of petroleum refining into liquid form.
[0032] As the gas valve 20 opens or closes, the fuel gas R may be
supplied to the manifold 30 or its supply may be cut off. Also, the
amount of fuel gas R supplied to the manifold 30 may be regulated
by adjusting the opening degree of the gas valve 20. As such, the
gas valve 20 may regulate the heating power of the gas furnace 10.
To this end, the gas furnace 10 may further include a control part
for adjusting the opening or closing of the gas valve 20 or its
opening degree.
[0033] The manifold 30 may guide the fuel gas R to the burner 40,
and the fuel gas R, once introduced into the burner 40, may flow in
a mixture with air.
[0034] The air-fuel mixture flowing through the burner 40 may be
burnt due to flame ignition by an igniter. In this case, the
combustion of the air-fuel mixture may produce a flame and a
high-temperature combustion gas P.
[0035] The heat exchanger 50 may have a flow path through which the
combustion gas P can flow.
[0036] Referring to FIGS. 2 and 3, the heat exchanger 50 may
include a primary heat exchanger 51 and/or a secondary heat
exchanger 52.
[0037] The primary heat exchanger 51 may be placed with one end
being adjacent to the burner 40. The other end of the primary heat
exchanger 51 opposite the one end may be attached to a coupling box
14. The combustion gas P flowing from one end of the primary heat
exchanger 51 to the other end may be conveyed to the secondary heat
exchanger 52 via the coupling box 14.
[0038] One end of the secondary heat exchanger 52 may be connected
to the coupling box 14. The combustion gas P, once passed through
the primary heat exchanger 51, may be introduced into one end of
the secondary heat exchanger 52 and pass through the secondary heat
exchanger 52.
[0039] The secondary heat exchanger 52 may allow the combustion gas
P passed through the primary heat exchanger 51 to exchange heat
with the air passing around the secondary heat exchanger 52.
[0040] That is, the thermal energy of the combustion gas P passed
through the primary heat exchanger 51 through the secondary heat
exchanger 52 may be additionally used, thereby improving the
efficiency of the gas furnace 10.
[0041] The combustion gas P passed through the secondary heat
exchanger 52 may condense through heat transfer to the air passing
around the secondary heat exchanger 52, thereby producing a
condensate. In other words, the vapor contained in the combustion
gas P may condense and turn into condensate.
[0042] Due to this reason, the gas furnace 10 equipped with the
primary heat exchanger 51 and secondary heat exchanger 52 is also
called a condensing gas furnace.
[0043] Referring to FIGS. 1 to 3, the combustion gas P passed
through the other end of the secondary heat exchanger 52 may be
discharged out of the gas furnace 10 through the exhaust pipe 80 by
means of the inducer 70.
[0044] The condensate produced in the secondary heat exchanger 52
may be released to the condensate water trap 90 and then discharged
out of the gas furnace 10 through an outlet.
[0045] The inducer 70 may induce a flow of combustion gas P that
passes through the primary heat exchanger 51, coupling box 14, and
secondary heat exchanger 52 and is discharged to the exhaust pipe
80. In this regard, the inducer 70 may be understood as an induced
draft motor (IDM).
[0046] The blower 60 for the gas furnace may be located at the
bottom of the gas furnace 10. Air supplied to the room may move
upward from the bottom of the gas furnace 10 by the blower 60. In
this regard, the blower 60 may be understood as an indoor blower
motor (IBM).
[0047] The blower 60 may allow air to pass around the heat
exchanger 50.
[0048] The air passing around the heat exchanger 50, blown by the
blower 60, may have a temperature rise by receiving thermal energy
from the high-temperature combustion gas P via the heat exchanger
50. The room may be heated as the higher-temperature air is
supplied to the room.
[0049] A room air duct D1 through which air (hereinafter, "room
air") RA coming from a room passes may be installed adjacent to the
inducer 60.
[0050] A supply air duct D2 through which air (hereinafter, "supply
air") SA supplied to the room passes may be installed adjacent to
the heat exchanger 50.
[0051] That is, when the blower 60 operates, the room air RA coming
from the room through the room air duct D1 has a temperature rise
as it passes through the heat exchanger 50, and may be supplied
into the room through the supply air duct D2 and used as the supply
air SA, thereby heating the room.
[0052] Referring to FIGS. 4 and 5, the secondary heat exchanger 52
may have a tube 521. A plurality of tubes 521 may be provided. A
baffle 522 may be inserted into the tube 521. A plurality of
baffles 522 may be provided, and the baffles 522 may be inserted
into the tubes 521, respectively. For example, the baffle 522 may
be a longitudinally-extending plate and twisted in the shape of a
screw.
[0053] The combustion gas P flowing in the tube 521 with the baffle
522 inserted in it may be directed by the baffle 522 in such a way
as to form a swirl or vortex. This prevents displacement or
deflection of the flow of combustion gas P in the tube 521.
Therefore, the heat transfer efficiency of the tube 521 and the
combustion gas P flowing in the tube 521 may be enhanced.
[0054] Referring to FIG. 6, the baffle 522 may have a plurality of
holes 522h. The holes 522h may be formed to penetrate both sides of
the baffle 522. The baffle 522 may have a plurality of segments
522S. For example, the segments 522S may be formed in a triangular
shape such that the baffle 522 has a screw pattern. The plurality
of holes 522h may be formed in the plurality of segments 522S,
respectively. For example, one hole 522h may be formed in one
segment 522S of the baffle 522. Thus, the area of contact between
the combustion gas P (see FIG. 5) and the baffle 522 may be
decreased, thus alleviating the pressure loss in the tube 521 (see
FIG. 5) and, at the same time, a new flow of combustion gas P may
be generated at the center of the tube 521, thus alleviating the
stagnation of flow of combustion gas P in the tube 521.
[0055] Referring to FIG. 7, the baffle 522 may have a plurality of
holes 522h. The holes 522h may be formed to penetrate both sides of
the baffle 522. The baffle 522 may have a plurality of segments
522S. For example, the segments 522S may be formed in a triangular
shape such that the baffle 522 has a screw pattern. The plurality
of holes 522h may be formed in each of the segments 522S. For
example, three holes 522h may be formed in one segment 522S of the
baffle 522. Thus, the area of contact between the combustion gas P
(see FIG. 5) and the baffle 522 may be decreased, thus alleviating
the pressure loss in the tube 521 (see FIG. 5) and, at the same
time, a new flow of combustion gas P may be generated at the center
of the tube 521, thus alleviating the stagnation of flow of
combustion gas P in the tube 521.
[0056] Referring to FIG. 8, the baffle 522 may have a plurality of
holes 522h. The holes 522h may be sequentially arranged in series
along the flow direction P of combustion gas. The baffle 522 may be
twisted in the shape of a screw. Two holes 522h may be formed for
each twist pitch PT of the baffle 522. Thus, the area of contact
between the combustion gas P (see FIG. 5) and the baffle 522 may be
decreased, thus alleviating the pressure loss in the tube 521 (see
FIG. 5) and, at the same time, a new flow of combustion gas P may
be generated at the center of the tube 521, thus alleviating the
stagnation of flow of combustion gas P in the tube 521.
[0057] Referring to FIG. 9, the baffle 522 may have a plurality of
holes 522h. The holes 522h may be sequentially arranged, in an
alternating fashion along the central axis of the tube 521 formed
along the flow direction P of combustion gas. The baffle 522 may be
twisted in the shape of a screw. Four holes 522h may be formed for
each twist pitch PT of the baffle 522. Thus, the path of the flow
of combustion gas P may be extended, and the area of contact
between the combustion gas P (see FIG. 5) and the baffle 522 may be
decreased, thus alleviating the pressure loss in the tube 521 (see
FIG. 5) and, at the same time, a new flow of combustion gas P may
be generated at the center of the tube 521, thus alleviating the
stagnation of flow of combustion gas P in the tube 521.
[0058] Referring to FIG. 10, the baffle 522 may have a plurality of
holes 522h. The holes 522h may be sequentially arranged in series
along the flow direction P of combustion gas. The baffle 522 may be
twisted in the shape of a screw. A plurality of holes 522h may be
formed in succession for each twist pitch PT of the baffle 522.
Thus, the area of contact between the combustion gas P (see FIG. 5)
and the baffle 522 may be decreased, thus alleviating the pressure
loss in the tube 521 (see FIG. 5) and, at the same time, a new flow
of combustion gas P may be generated in large quantities at the
center of the tube 521, thus alleviating the stagnation of flow of
combustion gas P in the tube 521.
[0059] Referring to FIG. 11, the baffle 522 may have a plurality of
holes 522h. The holes 522h may be sequentially arranged in series
along the flow direction P of combustion gas. The baffle 522 may be
twisted in the shape of a screw. A plurality of holes 522h may be
formed in succession for each twist pitch PT of the baffle 522.
[0060] A plurality of holes 522h1 in a first row may be formed
along the central axis of the tube 521. A plurality of holes 522h2
in a second row may be formed along the central axis of the tube
521, spaced apart from the central axis of the tube 521. A
plurality of holes 522h3 in a third row may be formed along the
central axis of the tube 521, spaced apart from the central axis of
the tube 521, and may face the plurality of holes in the second row
or be symmetrical to them with respect to the central axis of the
tube 521.
[0061] Thus, the area of contact between the combustion gas P (see
FIG. 5) and the baffle 522 may be decreased, thus alleviating the
pressure loss in the tube 521 (see FIG. 5) and, at the same time, a
new flow of combustion gas P may be generated in large quantities
at the center of the tube 521, thus alleviating the stagnation of
flow of combustion gas P in the tube 521. The stagnation of flow of
combustion gas P in the tube 521.
[0062] Referring to FIGS. 12 and 13, the baffle 522 may have a
plurality of cutouts 522C. The cutouts 522C may be formed on both
edges of the baffle 522. The baffle 522 may have a plurality of
segments 522S. For example, the segments 522S may be formed in a
triangular shape such that the baffle 522 has a screw pattern. The
plurality of cutouts 522C may be formed in the plurality of
segments 522S, respectively. For example, one cutout 522C may be
formed in one segment 522S of the baffle 522. For example, the
cutouts 522C (see FIG. 12) may be triangular. In another example,
the cutouts 522C (see FIG. 13) may be rectangular.
[0063] This may alleviate the narrowing of the flow path in the
tube 521 (see FIG. 5) due to condensate water and therefore reduce
the pressure loss, and also may generate a turbulence at the
cutouts 522C, which enhances heat transfer efficiency.
[0064] Thus, the area of contact between the combustion gas P (see
FIG. 5) and the baffle 522 may be decreased, thus alleviating the
pressure loss in the tube 521 (see FIG. 5) and, at the same time, a
new flow of combustion gas P may be generated at the center of the
tube 521, thus alleviating the stagnation of flow of combustion gas
Pin the tube 521.
[0065] In the above, a gas furnace according to an exemplary
embodiment of the present disclosure has been described with
reference to the accompanying drawings. However, the present
disclosure is not limited to the above embodiments, and it will be
apparent to those skilled in the art that various modifications or
implementations within the equivalent scopes can be made without
departing from the subject matter of the present disclosure.
[0066] The present disclosure provides one or more of the following
advantages.
[0067] Firstly, a gas furnace may be provided that can alleviate
the pressure drop in the tube.
[0068] Secondly, a gas furnace may be provided that can alleviate
the stagnation of flow in the tube.
[0069] Thirdly, a gas furnace may be provided that can reduce the
power consumption of the fan by decreasing the resistance to gas
flow in a heat exchanger.
[0070] Fourthly, a gas furnace may be provided that can alleviate
condensate water standing in the tube into which the baffle is
inserted.
* * * * *