U.S. patent application number 17/009896 was filed with the patent office on 2020-12-24 for melt-anisotropic aromatic polyester multifilament.
This patent application is currently assigned to KURARAY CO., LTD.. The applicant listed for this patent is KURARAY CO., LTD.. Invention is credited to Takuji NAKAMURA, Yuji OGINO, Kota TOGII.
Application Number | 20200399788 17/009896 |
Document ID | / |
Family ID | 1000005118519 |
Filed Date | 2020-12-24 |







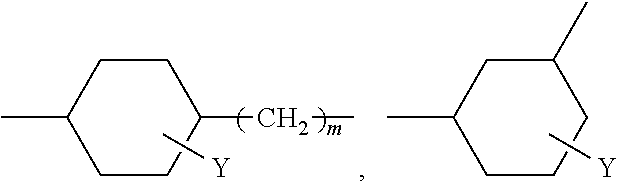



View All Diagrams
United States Patent
Application |
20200399788 |
Kind Code |
A1 |
OGINO; Yuji ; et
al. |
December 24, 2020 |
MELT-ANISOTROPIC AROMATIC POLYESTER MULTIFILAMENT
Abstract
Provided is a melt-anisotropic aromatic polyester multifilament
having excellent abrasion resistance. The melt-anisotropic aromatic
polyester multifilament has a single fiber fineness from 10 to 80
dtex and comprises 3 to 10 wt % of a dimethylsilicone-series
finishing agent applied on a fiber surface of the multifilament,
based on the multifilament, the finishing agent containing a
dimethylsilicone-series compound having a weight average molecular
weight from 15000 to 40000.
Inventors: |
OGINO; Yuji; (Saijo-shi,
JP) ; NAKAMURA; Takuji; (Osaka-shi, JP) ;
TOGII; Kota; (Saijo-shi, JP) |
|
Applicant: |
Name |
City |
State |
Country |
Type |
KURARAY CO., LTD. |
Kurashiki-shi |
|
JP |
|
|
Assignee: |
KURARAY CO., LTD.
Kurashiki-shi
JP
|
Family ID: |
1000005118519 |
Appl. No.: |
17/009896 |
Filed: |
September 2, 2020 |
Related U.S. Patent Documents
|
|
|
|
|
|
Application
Number |
Filing Date |
Patent Number |
|
|
PCT/JP2019/008039 |
Mar 1, 2019 |
|
|
|
17009896 |
|
|
|
|
Current U.S.
Class: |
1/1 |
Current CPC
Class: |
D06M 15/643 20130101;
D01F 8/14 20130101; D01F 6/62 20130101 |
International
Class: |
D01F 8/14 20060101
D01F008/14; D01F 6/62 20060101 D01F006/62; D06M 15/643 20060101
D06M015/643 |
Foreign Application Data
Date |
Code |
Application Number |
Mar 7, 2018 |
JP |
2018-040771 |
Claims
1. A melt-anisotropic aromatic polyester multifilament having a
single fiber fineness from 10 to 80 dtex, the melt-anisotropic
aromatic polyester multifilament comprising 3 to 10 wt % of a
dimethylsilicone-series finishing agent applied on a fiber surface
of the multifilament, based on the multifilament, the finishing
agent containing a dimethylsilicone-series compound having a weight
average molecular weight from 15000 to 40000.
2. The melt-anisotropic aromatic polyester multifilament according
to claim 1, wherein the melt-anisotropic aromatic polyester
multifilament has a tenacity of 20 cN/dtex or higher.
3. The melt-anisotropic aromatic polyester multifilament according
to claim 1, wherein the melt-anisotropic aromatic polyester
multifilament includes single fibers having an average fiber
diameter from 30 to 85 .mu.m.
4. The melt-anisotropic aromatic polyester multifilament according
to claim 1, wherein the dimethylsilicone-series finishing agent has
a viscosity from 300 to 3000 mm.sup.2/s.
5. The melt-anisotropic aromatic polyester multifilament according
to claim 1, wherein the melt-anisotropic aromatic polyester
multifilament has an interfiber dynamic friction coefficient from
0.080 to 0.150.
6. The melt-anisotropic aromatic polyester multifilament according
to claim 1, wherein the melt-anisotropic aromatic polyester
multifilament has a single fiber fineness from 15 to 60 dtex.
7. The melt-anisotropic aromatic polyester multifilament according
to claim 1, wherein the finishing agent contains a
dimethylsilicone-series compound having a weight average molecular
weight from 20000 to 40000.
8. The melt-anisotropic aromatic polyester multifilament according
to claim 1, wherein the melt-anisotropic aromatic polyester
multifilament comprises 3 to 8 wt % of the dimethylsilicone-series
finishing agent based on the multi filament.
9. The melt-anisotropic aromatic polyester multifilament according
to claim 1, wherein the melt-anisotropic aromatic polyester
multifilament includes single fibers having an average fiber
diameter from 35 to 80 urn.
10. The melt-anisotropic aromatic polyester multifilament according
to claim 1, wherein the melt-anisotropic aromatic polyester
multifilament has an interfiber dynamic friction coefficient from
0.085 to 0.140.
11. A fiber structure comprising a melt-anisotropic aromatic
polyester multifilament as recited in claim 1 in at least a part of
the fiber structure.
Description
CROSS REFERENCE TO THE RELATED APPLICATION
[0001] This application is a continuation application, under 35
U.S.C .sctn. 111(a) of international application No.
PCT/JP2019/008039, filed Mar. 1, 2019, which claims priority to
Japanese patent application No. 2018-040771, filed Mar. 7, 2018,
the entire disclosures of all of which are herein incorporated by
reference as a part of this application.
BACKGROUND OF THE INVENTION
Field of Invention
[0002] The present invention relates to a melt-anisotropic aromatic
polyester multifilament having excellent abrasion resistance.
Description of Related Art
[0003] Melt-anisotropic aromatic polyester has been known as a
polymer having a rigid molecular chain that is melt-spinnable to
obtain fibers capable of exhibiting the highest tenacity and
elastic modulus among melt-spinnable fibers because melt spinning
makes the melt-anisotropic aromatic polyester have highly oriented
molecular chains in a fiber axial direction and heat treatment
attains solid-phase polymerization. It is also known that
solid-phase polymerization increases the molecular weight and the
melting point of the melt-anisotropic aromatic polyester fibers so
as to enhance heat resistance and dimensional stability of the
fibers. Thus, the melt-anisotropic aromatic polyester fibers
subjected to solid-phase polymerization can exhibit high tenacity,
high elastic modulus, excellent heat resistance, and dimensional
stability.
[0004] In addition to the above properties, the melt-anisotropic
aromatic polyester fibers have high chemical resistance and low
hygroscopicity. Thus, the melt-anisotropic aromatic polyester
fibers are used in applications including control cables, tension
members (such as optical fibers, electric wires, head corns), cord
reinforcing members for various electrical appliances, core yarns
of heater wires, sailcloth, ropes, protective gloves, and
reinforcing members for plastics. Because of its particularly
excellent abrasion resistance, the melt-anisotropic aromatic
polyester fibers are also used in applications including climbing
ropes, land nets (such as safety nets, nets used in golf practice
ranges), lifelines, fishing lines, fishing nets, longlines, and
slings.
[0005] Patent Document 1 (JP Laid-open Patent Publication No.
2013-133576) describes that melt spinning of a melt-anisotropic
aromatic polyester containing a certain amount of a metallic soap
can produce multifilaments which have reduced unevenness between
single fibers of the multifilaments, high tenacity, high elastic
modulus, excellent heat resistance and dimensional stability, less
fluff, and excellent fiber application processability, and can
produce fibers that can be suitably used in applications such as
ropes, fishing nets, and slings.
SUMMARY OF THE INVENTION
Problems to be Solved by the Invention
[0006] In Patent Document 1, however, the production method may
lead to generation of fluff in a rewinding process after a
solid-phase polymerization process because the method involves
application of an oiling agent before the solid-phase
polymerization process, which may result in decomposition of the
oiling agent during the solid-phase polymerization process
depending on the type of the oiling agent. Also, even where such an
oiling agent is not decomposed, the oiling agent may be transferred
or removed due to evaporation of an oiling-agent-containing
component or heat convection caused by heat applied during the
solid-phase polymerization process, so that uneven distribution of
the oiling agent may be caused after the solid-phase polymerization
process. Therefore, thus-obtained melt-anisotropic aromatic
polyester multifilaments have insufficient abrasion resistance.
[0007] The present invention presents a solution to such problems
of the conventional techniques and provides a melt-anisotropic
aromatic polyester multifilament having excellent abrasion
resistance.
Means for Solving the Problems
[0008] In order to improve abrasion resistance of a
melt-anisotropic aromatic polyester multifilament, the inventors of
the present invention have made extensive study and have found that
where a specific amount of a dimethylsilicone-series finishing
agent containing a dimethylsilicone-series compound having a
specific molecular weight is applied to surfaces of a
melt-anisotropic aromatic polyester multifilament each having a
specific large single fiber fineness, surprisingly, such a
melt-anisotropic aromatic polyester multifilament can exhibit
markedly improved abrasion resistance while maintaining its
tenacity, compared to that of a conventional multifilament of
single fibers having small fineness. The inventors thus achieved
the present invention.
[0009] That is, the present invention may include the following
aspects.
[0010] Aspect 1
[0011] A melt-anisotropic aromatic polyester multifilament having a
single fiber fineness from 10 to 80 dtex (preferably from 10 to 60
dtex, and more preferably from 15 to 50 dtex), the melt-anisotropic
aromatic polyester multifilament comprising 3 to 10 wt %
(preferably 3 to 8 wt %, and more preferably 4 to 6 wt %) of a
dimethylsilicone-series finishing agent applied on a fiber surface
of the multifilament, based on the multifilament, the finishing
agent containing a dimethylsilicone-series compound having a weight
average molecular weight from 15000 to 40000 (preferably from 18000
to 35000, and more preferably from 20000 to 30000).
[0012] Aspect 2
[0013] The melt-anisotropic aromatic polyester multifilament
according to aspect 1, wherein the melt-anisotropic aromatic
polyester multifilament has a tenacity of 20 cN/dtex or higher
(preferably 21 cN/dtex or higher, and more preferably 23 cN/dtex or
higher).
[0014] Aspect 3
[0015] The melt-anisotropic aromatic polyester multifilament
according to aspect 1 or 2, wherein the melt-anisotropic aromatic
polyester multifilament includes single fibers having an average
fiber diameter from 30 to 85 .mu.m (preferably from 33 to 80 .mu.m,
and more preferably from 35 to 70 .mu.m).
[0016] Aspect 4
[0017] The melt-anisotropic aromatic polyester multifilament
according to any one of aspects 1 to 3, wherein the
dimethylsilicone-series finishing agent has a viscosity from 300 to
3000 mm.sup.2/s (preferably from 300 to 2000 mm.sup.2/s, and more
preferably from 300 to 1500 mm.sup.2/s).
[0018] Aspect 5
[0019] The melt-anisotropic aromatic polyester multifilament
according to any one of aspects 1 to 4, wherein the
melt-anisotropic aromatic polyester multifilament has an interfiber
dynamic friction coefficient from 0.080 to 0.150 (preferably from
0.085 to 0.140, and more preferably from 0.090 to 0.130).
[0020] Aspect 6
[0021] A fiber structure comprising a melt-anisotropic aromatic
polyester multifilament as recited in any one of aspects 1 to 5 in
at least a part of the fiber structure.
[0022] As used herein, the term "melt-anisotropic aromatic
polyester multifilament" refers to a melt-anisotropic aromatic
polyester multifilament on which a dimethylsilicone-series
finishing agent is applied. Therefore, for the sake of convenience,
the plain term "multifilament (plain multifilament)" is used to
refer to a multifilament alone not including a
dimethylsilicone-series finishing agent, whereas the term
"melt-anisotropic aromatic polyester multifilament" is used to
refer to a multifilament including a dimethylsilicone-series
finishing agent.
[0023] Any combination of at least two constructions, disclosed in
the appended claims and/or the specification should be construed as
included within the scope of the present invention. In particular,
any combination of two or more of the appended claims should be
equally construed as included within the scope of the present
invention.
Effect of the Invention
[0024] The present invention can provide a melt-anisotropic
aromatic polyester multifilament having excellent abrasion
resistance. The melt-anisotropic aromatic polyester multifilament
of the present invention may to be suitably used for fiber
structure applications such as ropes, cords, and particularly
slings.
DESCRIPTION OF THE EMBODIMENTS
[0025] Hereinafter, the present invention will be described in
detail.
[0026] Melt-Anisotropic Aromatic Polyester
[0027] A multifilament made of a melt-anisotropic aromatic
polyester may be obtained by melt-spinning of the melt-anisotropic
aromatic polyester. The melt-anisotropic aromatic polyester may
comprise repeating structural units originating from, for example,
aromatic diols, aromatic dicarboxylic acids, aromatic
hydroxycarboxylic acids, etc. As long as the effect of the present
invention is not spoiled, the repeating structural units
originating from aromatic diols, aromatic dicarboxy lie acids, and
aromatic hydroxycarboxylic acids are not limited to a specific
chemical composition. The melt-anisotropic aromatic polyester may
include the structural units originating from aromatic diamines,
aromatic hydroxy amines, or aromatic aminocarboxylic acids in the
range which does not spoil the effect of the present invention. For
example, preferable structural units may include units shown in
Table 1.
TABLE-US-00001 TABLE 1 ##STR00001## ##STR00002## In the formula, X
is selected from the following structures. ##STR00003##
##STR00004## ##STR00005## ##STR00006## ##STR00007## ##STR00008## m
is an integer from 0 to 2, Y is a substituent selected from
hydrogen atom, halogen atoms, alkyl groups, aryl groups, aralkyl
groups, alkoxy groups, aryloxy groups, aralkyloxy groups.
[0028] In the structural units in Table 1, m is an integer from 0
to 2, and Y in the formula independently represents, as from one
substituent to the number of substituents in the range of the
replaceable maximum number of aromatic ring, a hydrogen atom, a
halogen atom (for example, fluorine atom, chlorine atom, bromine
atom and iodine atom), an alkyl group (for example, an alkyl group
having 1 to 4 carbon atoms such as methyl group, ethyl group,
isopropyl group and t-butyl group), an alkoxy group (for example,
methoxy group, ethoxy group, isopropoxy group, n-butoxy group,
etc.), an aryl group (for example, phenyl group, naphthyl group,
etc.), an aralkyl group (for example, benzyl group (phenylmethyl
group), phenethyl group (phenylethyl group), etc.), an aryloxy
group (for example, phenoxy group etc.), an aralkyloxy group (for
example, benzyloxy group etc.), and others.
[0029] As more preferable structural units, there may be mentioned
structural units as described in Examples (1) to (18) shown in the
following Tables 2, 3, and 4. It should be noted that where the
structural unit in the formula is a structural unit which can show
a plurality of structures, combination of two or more units may be
used as structural units for a polymer.
TABLE-US-00002 TABLE 2 (1) ##STR00009## ##STR00010## (2)
##STR00011## ##STR00012## ##STR00013## (3) ##STR00014##
##STR00015## ##STR00016## (4) ##STR00017## ##STR00018##
##STR00019## ##STR00020## (5) ##STR00021## ##STR00022##
##STR00023## ##STR00024## (6) ##STR00025## ##STR00026##
##STR00027## ##STR00028## (7) ##STR00029## ##STR00030##
##STR00031## ##STR00032## (8) ##STR00033## ##STR00034##
##STR00035## ##STR00036## ##STR00037##
TABLE-US-00003 TABLE 3 (9) ##STR00038## ##STR00039## (10)
##STR00040## ##STR00041## ##STR00042## (11) ##STR00043##
##STR00044## ##STR00045## ##STR00046## (12) ##STR00047##
##STR00048## ##STR00049## (13) ##STR00050## ##STR00051##
##STR00052## ##STR00053## (14) ##STR00054## ##STR00055##
##STR00056## (15) ##STR00057## ##STR00058## ##STR00059##
##STR00060## ##STR00061##
TABLE-US-00004 TABLE 4 (16) ##STR00062## ##STR00063## ##STR00064##
##STR00065## (17) ##STR00066## ##STR00067## ##STR00068##
##STR00069## (18) ##STR00070## ##STR00071## ##STR00072##
[0030] In the structural units shown in Tables 2, 3, and 4, n is an
integer of 1 or 2, among each of the structural units, n=1 and n=2
may independently exist, or may exist in combination; each of the
Y.sub.1 and Y.sub.2 independently represents, a hydrogen atom, a
halogen atom, (for example, fluorine atom, chlorine atom, bromine
atom, iodine atom, etc.), an alkyl group (for example, an alkyl
group having 1 to 4 carbon atoms such as methyl group, ethyl group,
isopropyl group, and t-butyl group, etc.), an alkoxy group (for
example, methoxy group, ethoxy group, and isopropoxy group,
n-butoxy group, etc.), an aryl group (for example, phenyl group,
naphthyl group, etc.), an aralkyl group (for example, benzyl group
(phenylmethyl group), phenethyl group (phenylethyl group), etc.),
an aryloxy group (for example, phenoxy group etc.), an aralkyloxy
group (for example, benzyloxy group etc.), and others. Among these,
the preferable Y may include a hydrogen atom, a chlorine atom, a
bromine atom, and a methyl group.
[0031] Z may include substitutional groups denoted by following
formulae.
##STR00073##
[0032] Preferable melt-anisotropic aromatic polyesters may comprise
a combination of a structural unit having a naphthalene skeleton.
Especially preferable one may include both the structural unit (A)
derived from hydroxybenzoic acid and the structural unit (B)
derived from hydroxy naphthoic acid. For example, the structural
unit (A) may have a following formula (A), and the structural unit
(B) may have a following formula (B). In order to improve
melt-formability, the ratio of the structural unit (A) and the
structural unit (B) may preferably be in a range of former/latter
of 9/1 to 1/1, more preferably from 7/1 to 1/1, and still
preferably from 5/1 to 1/1.
##STR00074##
[0033] The total proportion of the structural units of (A) and (B)
may be, based on all the structural units, for example, 65 mol % or
higher, more preferably 70 mol % or higher, and further preferably
80 mol % or higher. A melt-anisotropic aromatic polyester having
the structural unit (B) at a proportion of 4 to 45 mol % is
especially preferred among polymers.
[0034] The melt-anisotropic aromatic polyester suitably used in the
present invention preferably has a melting point (hereinafter,
sometimes referred to as Mp) in the range from 250 to 360.degree.
C., and more preferably from 260 to 320.degree. C. As used herein,
the melting point refers to a main absorption peak temperature
determined and observed in accordance with JIS K 7121 test method,
using a differential scanning calorimeter (DSC; "TA3000"
manufactured by Mettler-Toledo International Inc.). Specifically, a
melting point is determined as the position of an endothermic peak
that occurs when a sample (10 to 20 mg) introduced to an aluminum
pan in the DSC device is subjected to temperature increase at a
rate of 20.degree. C./min, with nitrogen as a carrier gas flowing
at 100 cc/min. Depending on the type of the polymer, where a clear
peak does not appear during the 1st run of the DSC measurement, the
temperature is increased at a temperature increase rate of
50.degree. C./min to a temperature higher than an expected flowing
temperature by 50.degree. C., retained at that temperature for 3
minutes to completely melt the polymer, and then decreased to
50.degree. C. at a temperature decrease rate of 80.degree. C./min.
Thereafter, an endothermic peak is measured at a temperature
increase rate of 20.degree. C./min.
[0035] The above melt-anisotropic aromatic polyester may be added
with thermoplastic polymers, such as a polyethylene terephthalate,
a modified-polyethylene terephthalate, a polyolefin, a
polycarbonate, a polyamide, a polyphenylene sulfide, a polyether
ether ketone, a fluoro-resin, and others, as long as they do not
spoil the effect of the present invention. Additives may also be
added, including inorganic substances such as titanium oxide,
kaolin, silica, and barium oxide; carbon black; a colorant such as
dyes and paints; an antioxidant; an ultraviolet-ray absorbent; and
a light stabilizer.
[0036] Melt-Anisotropic Aromatic Polyester Multifilament
[0037] It is important that a melt-anisotropic aromatic polyester
multifilament of the present invention have a single fiber fineness
from 10 to 80 dtex in order to have high tenacity and improved
abrasion resistance. In the present invention, it has been found
that unexpectedly, abrasion resistance of the melt-anisotropic
aromatic polyester multifilament can be markedly improved by using
fibers each having a single fiber fineness in a specific range.
Where a same finishing agent is applied to melt-anisotropic
aromatic polyester multifilaments with different single fiber
fineness from each other, it has been found that abrasion
resistance of the melt-anisotropic aromatic polyester multifilament
with a single fiber fineness of 10 dtex or higher is markedly
improved. Although abrasion resistance is improved as the single
fiber fineness increases over this value, the melt-anisotropic
aromatic polyester multifilament with too large single fiber
fineness tends to have reduced abrasion resistance. The reason is
not clear why abrasion resistance is improved where the single
fiber fineness is 10 dtex or higher. On the other hand, as the
single fiber fineness increases, tensile strength tends to
decrease. Too large single fiber fineness of melt-anisotropic
aromatic polyester multifilaments tends to deteriorate abrasion
resistance presumably because the effect of improving abrasion
resistance is cancelled out due to the decrease in tensile
strength. Further, the multifilament with a single fiber fineness
exceeding 80 dtex has difficulty in bundling, and thus, for
example, the multifilament wound into a square end shape tends to
easily collapse at its end face in a spinning step or a rewinding
step. The single fiber fineness may more preferably be from 10 to
60 dtex, and further preferably from 15 to 50 dtex.
[0038] The melt-anisotropic aromatic polyester multifilament of the
present invention may have an average single fiber diameter from 30
to 85 .mu.m in order to have high tenacity and improved abrasion
resistance. The average single fiber diameter may preferably be
from 33 to 80 .mu.m, and more preferably from 35 to 70 .mu.m. It
should be noted that an average single fiber diameter is determined
in accordance with the method described later in Examples and is a
value calculated from single fiber finenesses, assuming that the
cross section of each fiber is a perfect circle. A specific gravity
used in the calculation may be determined by a known method.
[0039] The melt-anisotropic aromatic polyester multifilament of the
present invention may include 5 to 5000 filaments. Where the number
of filaments in the melt-anisotropic aromatic polyester
multifilament is too small, the multifilament may not be able to
withstand a winding tension and be broken therefor. Where the
number of filaments is too large, the multifilament may be
difficult to normally wind using a winding machine because the
multifilament is too thick.
[0040] Further, the multifilament may preferably have a total
fineness from 50 to 400000 dtex. Where the total fineness is too
small, the multifilament may not be able to withstand a tension
during processing and be broken therefor. Where the total fineness
is too large, the multifilament may be difficult to normally wind
using a winding machine because the multifilament is too thick.
[0041] It is important that the melt-anisotropic aromatic polyester
multifilament of the present invention include 3 to 10 wt % of a
specific dimethylsilicone-series finishing agent applied to a fiber
surface based on the multifilament. More preferably 3 to 8 wt % and
further preferably 4 to 6 wt % of the finishing agent may be
applied to the multifilament. It may be difficult to coat the
entire fiber surface with the finishing agent in a proportion of
less than 3 wt %, so that the finishing agent is unevenly applied,
resulting in insufficient abrasion resistance. On the other hand,
where the amount of the finishing agent exceeds 10 wt %, the
finishing agent accumulated on surfaces of guides, rollers and the
like causes deterioration in process passableness or a handling
property of a product cheese, so that productivity may be
lowered.
[0042] Although it is not clear why application of a specific
dimethylsilicone-series finishing agent can remarkably improve
abrasion resistance of the melt-anisotropic aromatic polyester
multifilament of the present invention, it is presumed that one of
the reasons is that the dimethylsilicone-series finishing agent is
applied so as to form a coating on the outer surface of the
multifilament and is distributed so as to converge the filaments
together by covering the respective filaments of the multifilament.
In such a case, the dimethylsilicone-series finishing agent
permeates into the converged filaments so as to coat the respective
filaments and suppresses abrasion between the filaments, improving
abrasion resistance.
[0043] The melt-anisotropic aromatic polyester multifilament of the
present invention may have a tenacity of 20 cN/dtex or higher. The
melt-anisotropic aromatic polyester multifilament with too low
tenacity may require large fineness and/or an increased number of
filaments in order to obtain a desired strength for, e.g., sling
belt applications because low tenacity of the melt-anisotropic
aromatic polyester multifilament may lead to a thick and heavy
sling belt. Where the tenacity is 20 cN/dtex or higher, however, it
is possible to obtain a multifilament that meets a required
strength for, e.g., sling belt applications, even if the
multifilament has a small fineness and a small number of filaments.
Thus, it is possible to make a sling belt thin and lightweight. The
tenacity may more preferably be 21 cN/dtex or higher, and further
preferably 23 cN/dtex or higher. Although there is no specific
upper limit, the tenacity may preferably be 40 cN/dtex or lower,
and more preferably 35 cN/dtex or lower. It should be noted that
the tenacity refers to a tensile strength and may be determined in
accordance with the method described later in Examples.
[0044] In order to improve abrasion resistance, the
melt-anisotropic aromatic polyester multifilament of the present
invention may preferably have an interfiber dynamic friction
coefficient from 0.080 to 0.150, more preferably from 0.085 to
0.140, and further preferably from 0.090 to 0.130 in a state where
the finishing agent is applied thereto, when measured in accordance
with the measurement method as described later.
[0045] Dimethylsilicone-Series Finishing Agent
[0046] It is important that a dimethylsilicone-series finishing
agent be used as a finishing agent for the melt-anisotropic
aromatic polyester multifilament of the present invention in order
to improve abrasion resistance. As long as the
dimethylsilicone-series finishing agent contains a
dimethylsilicone-series compound as a main component, and the
dimethylsilicone-series compound has a dimethyl polysiloxane
structure in its chemical structure, the dimethylsilicone-series
finishing agent is not particularly limited and may have a part of
a side chain or a terminal that is modified with a functional group
different from a methyl group. The dimethylsilicone-series
finishing agent may also contain various additives such as
surfactants, penetrants, antistatic agents, and antibacterial
agents, in addition to the dimethylsilicone-series compound. It is
important that the dimethylsilicone-series compound have a weight
average molecular weight from 15000 to 40000, more preferably from
18000 to 35000, and further preferably from 20000 to 30000. Where
the weight average molecular weight is lower than 15000, sufficient
coating strength may not be obtained on the fiber surface,
resulting in insufficient abrasion resistance. Where the weight
average molecular weight exceeds 40000, the viscosity of the
finishing agent may become too high, making it difficult to
uniformly apply the finishing agent over the fiber surface. It
should be noted that the weight average molecular weight of the
dimethylsilicone-series compound may be determined as a weight
average molecular weight based on polystyrene in gel permeation
chromatography (GPC).
[0047] Further, the dimethylsilicone-series finishing agent may
preferably have a viscosity from 300 to 3000 mm.sup.2/s. Where the
viscosity is too low, such a viscosity would lower the interfiber
dynamic friction coefficient and make it easy to apply the
finishing agent over the fiber surface, whereas the finishing agent
may be easily fall off from the fiber surface due to friction
between the fibers, resulting in poor abrasion resistance. Where
the viscosity is too high, the finishing agent may not be able to
accommodate the frictional movement of fibers and thus to reduce
abrasion of the single fibers because of an increased dynamic
friction coefficient, resulting in poor abrasion resistance. The
viscosity may more preferably be from 300 to 2000 mm.sup.2/s, and
further preferably from 300 to 1500 mm.sup.2/s. As used herein, the
viscosity refers to a kinematic viscosity and may be determined in
accordance with JIS Z 8803 using, for example, an Ubbelohde
viscometer.
[0048] A method of producing a melt-anisotropic aromatic polyester
multifilament of the present invention may at least comprise:
producing as-spun filaments of a melt-anisotropic aromatic
polyester; heat-treating the as-spun filaments; and applying a
specific dimethylsilicone-series finishing agent to the
heat-treated multifilament in a proportion of 3 to 10 wt % of based
on the multi filament.
[0049] The as-spun filaments of the melt-anisotropic aromatic
polyester are not particularly limited in terms of the method of
fiberizing and may usually be fibers obtained by melt spinning.
Melt spinning may be performed by a known or conventional method.
For example, fibers may be obtained by melting a fiber-formable
resin for liquid crystal polyester fibers in an extruder and
discharging the melt from a nozzle at a predetermined spinning
temperature.
[0050] Tenacity as well as elastic modulus of the melt-anisotropic
aromatic polyester fibers of the present invention can further be
enhanced by subjecting the as-spun filaments to heat treatment.
Heat treatment may preferably be performed at a temperature in a
range from (Mp-80) to (Mp).degree. C. The heat treatment
temperature may be, for example, more preferably from (Mp-50) to
(Mp).degree. C., and further preferably from (Mp-30) to
(Mp-1).degree. C. Since the melting point of the melt-anisotropic
aromatic polyester fibers of the present invention increases along
with as the heat treatment temperature increase, a preferable heat
treatment process may involve performing heat treatment at
stepwisely increased temperatures. As a heat treatment atmosphere,
an inert gas such as nitrogen and argon, or an active gas such as
air, or a combination thereof may suitably be used. Heat treatment
may be performed under a reduced pressure.
[0051] Heat treatment may be performed to the multifilament wound
on a metal bobbin in the form of a package or the multifilament in
the form of a skein (hank) or a tow, or may be continuously
performed to the multifilament between rollers. In order to
simplify equipment and improve productivity, it is preferable to
perform heat treatment to the multifilament wound in the form of a
package.
[0052] A process of applying 3 to 10 wt % of the
dimethylsilicone-series finishing agent to the heat-treated
multifilament based on the weight of the multifilament is not
particularly limited as long as a specific amount of the
dimethylsilicone-series finishing agent can be applied to the
multifilament. For example, any known application method may be
used including impregnation treatment, discharge treatment, coating
treatment, and impregnation and squeezing treatment. In order to
adjust the application amount, discharge (spray) treatment, coating
treatment, and impregnation and squeezing treatment are preferably
carried out in such a way that the finishing agent is applied to
the traveling filaments during rewinding of the heat-treated
multifilament. Since the application of the dimethylsilicone-series
finishing agent to the heat-treated multifilament can suppress
decomposition or transfer of the dimethylsilicone-series finishing
agent due to heat treatment, it is possible to apply the finishing
agent so as to form a coating on the surface of the
multifilament.
[0053] As long as a specific amount of the dimethylsilicone-series
finishing agent can be applied to the multifilament, the
dimethylsilicone-series finishing agent may take any form when the
finishing agent is applied. The dimethylsilicone-series compound
may be applied in the form of a stock solution or a diluted
solution (for example, emulsion). It should be noted that the
application amount of the dimethylsilicone-series finishing agent
based on the weight of the multifilament does not include an amount
of a solvent used for dilution.
[0054] The melt-anisotropic aromatic polyester multifilament of the
present invention may be suitably used for various fiber
structures. As used herein, the fiber structure includes ropes,
nets, fishing nets, sling belts, tension members and the like which
are composed of fibers of the present invention. The fiber
structure may be made only of the melt-anisotropic aromatic
polyester multifilaments or include other constituting components
in the range which does not spoil the effect of the present
invention. Preferably, the fiber structure may be suitably used for
ropes and sling belts that require particularly high abrasion
resistance because high load is applied due to the nature of the
intended use.
EXAMPLES
[0055] Hereinafter, the present invention will be described more
specifically in conjunction with Examples, which are not intended
to limit the present invention in any way whatsoever.
[0056] Single Fiber Fineness, Total Fineness, Average Single Fiber
Diameter, Tenacity, Strength
[0057] A single fiber fineness and a total fineness of a
multifilament were measured in accordance with JIS L 1013. An
average single fiber diameter was calculated from the measured
single fiber fineness and a specific gravity (1.41 g/cm.sup.3) of a
melt-anisotropic aromatic polyester used in Examples and
Comparative Examples.
[0058] Measurement of a tenacity and a strength of the
melt-anisotropic aromatic polyester multifilament was performed in
accordance with JIS L 1013 under the conditions of a length of 20
cm, an initial load of 0.098 cN/dtex, and a tensile speed of 10
cm/min to determine a breaking strength (tensile strength). An
average was taken from measurements at 5 or more locations.
[0059] Amount of Finishing Agent Applied
[0060] An amount of a finishing agent applied was determined by the
following method. A 10-m sample of a multifilament after being
subjected to heat treatment and before applying the finishing agent
was prepared using a wrap reel. A weight of the sample at this
stage was measured and denoted as "a" (g). Next, a 10-m sample of a
melt-anisotropic aromatic polyester multifilament after applying
the finishing agent during rewinding was prepared in the same
manner. A weight of the sample at this stage was measured and
denoted as "b" (g). The amount of the finishing agent applied was
calculated by the following formula (1).
Amount of finishing agent applied (wt %)=(b-a)/a.times.100 (1)
[0061] Interfiber Dynamic Friction Coefficient
[0062] An interfiber dynamic friction coefficient was determined by
the following method using a radar friction coefficient tester. Two
cylindrical test pieces were prepared as duplicates in each of
which a melt-anisotropic aromatic polyester multifilament was wound
around a cylinder having an outer diameter of 8 mm under an initial
load of 0.098 cN/dtex. Next, a test sample having a length of about
150 mm was obtained from the same melt-anisotropic aromatic
polyester multifilament. While attaching a weight of 500 mg to each
end of the sample, the test sample was hung on one of the
cylindrical test pieces, and then one end of the test sample was
connected to a hook of a torsion balance. Measurement of the
dynamic friction coefficient (A) was performed by rotating the
cylindrical test piece at a speed of 120 rpm (a peripheral speed of
697.2 cm/min in a state where the melt-anisotropic aromatic
polyester multifilament was wound) and determining a weight at
which the opposite ends of the test sample were balanced using the
torsion balance. A single strand of the test sample was used to be
hung at a central part of the cylindrical test piece and measured.
Then, the cylindrical test piece was moved in a horizontal
direction to perform another measurement on a new friction surface
using a new test sample in the same manner. The measurement was
repeated 5 times for each cylindrical test piece. An average was
calculated from the total 10 measurements for the two cylindrical
test pieces.
[0063] Evaluation of Abrasion Resistance
[0064] Abrasion resistance was determined by the following method.
A melt-anisotropic aromatic polyester multifilament having a total
fineness of 1670 dtex and the number of twists of 80 turns/m was
prepared. The melt-anisotropic aromatic polyester multifilament was
hung in a loop shape over two pulleys each having a diameter of 50
mm and was fixed so that the pulleys and the melt-anisotropic
aromatic polyester multifilament did not slip. The distance between
the pulleys was adjusted to 500 mm. The hung melt-anisotropic
aromatic polyester multifilament had three twisting portions
between the pulleys, and a load of 3 kg was applied to one pulley.
Then, the pulley was reciprocated at an angle of 180.degree. in a
cycle of 105 times/min so that the melt-anisotropic aromatic
polyester multifilament was abraded at the twisting portions so as
to count the number of reciprocations of the pulley before the
melt-anisotropic aromatic polyester multifilament broke. Evaluation
was performed based on the following criteria.
[0065] A: 10000 times or more
[0066] B: 5000 times or more and less than 10000 times
[0067] C: less than 5000 times
Example 1
[0068] A melt-anisotropic aromatic polyester (Mp: 281.degree. C.)
having the above structural units (A) and (B) in a proportion of
(A)/(B)=73/27 (molar ratio) was used as a melt-anisotropic aromatic
polyester. The melt-anisotropic aromatic polyester was spun using a
single-screw extruder and a nozzle having a hole diameter .phi. of
0.18 mm and the number of holes of 100H to produce a multifilament
of 1670 dtex/100 f (single fiber fineness of 16.7 dtex). The
obtained as-spun filaments were rewound on a metal bobbin with many
perforations to form a package having a winding density of 0.6
g/cm.sup.3 and then were heat-treated for 20 hours under a dry
nitrogen atmosphere at 260.degree. C. Thereafter, the obtained
package was further rewound with applying a 5.0 wt % of a
dimethylsilicone having a weight average molecular weight of 25000
and a viscosity of 1000 mm.sup.2/s as a finishing agent to the
fibers in the yarn. The fibers were then wound on a paper tube. The
tenacity of the obtained melt-anisotropic aromatic polyester
multifilament was 25.3 cN/dtex. The interfiber dynamic friction
coefficient was 0.109. Further, in the evaluation of abrasion
resistance, the pulley was reciprocatingly rotated 17981 times
before fiber breakage.
Example 2
[0069] As-spun filaments of a multifilament of 1670 dtex/50 f
(single fiber fineness of 33.4 dtex) were obtained in the same
manner as that of Example 1 except that a nozzle having a hole
diameter y of 0.25 mm and the number of holes of 501-1 was used in
spinning. The obtained as-spun filaments were subjected to heat
treatment under the same conditions as those of Example 1 and were
rewound with applying the finishing agent in the same manner. The
tenacity of the obtained melt-anisotropic aromatic polyester
multifilament was 23.6 cN/dtex. The interfiber dynamic friction
coefficient was 0.096. Further, in the evaluation of abrasion
resistance, the pulley was reciprocatingly rotated 40941 times
before fiber breakage.
Example 3
[0070] A melt-anisotropic aromatic multifilament of 1670 dtex/100 f
(single fiber fineness of 16.7 dtex) was obtained in the same
manner as that of Example 1 except that a dimethylsilicone having a
weight average molecular weight of 15000 and a viscosity of 300
mm.sup.2/s was used as a finishing agent. The tenacity of the
obtained melt-anisotropic aromatic polyester multifilament was 25.5
cN/dtex. The interfiber dynamic friction coefficient was 0.144.
Further, in the evaluation of abrasion resistance, the pulley was
reciprocatingly rotated 13164 times before fiber breakage.
Example 4
[0071] As-spun filaments of a multifilament of 1670 dtex/36 f
(single fiber fineness of 46.4 dtex) were obtained in the same
manner as that of Example 1 except that a nozzle having a hole
diameter .phi. of 0.25 mm and the number of holes of 36H was used
in spinning. The obtained as-spun filaments were subjected to heat
treatment under the same conditions as those of Example 1 and were
rewound with applying the finishing agent in the same manner. The
tenacity of the obtained melt-anisotropic aromatic polyester
multifilament was 21.1 cN/dtex. The interfiber dynamic friction
coefficient was 0.089. Further, in the evaluation of abrasion
resistance, the pulley was reciprocatingly rotated 64316 times
before fiber breakage.
Comparative Example 1
[0072] As-spun filaments of a multifilament of 1670 dtex/300 f
(single fiber to fineness of 5.6 dtex) were obtained in the same
manner as that of Example 1 except that a nozzle having a hole
diameter .phi. of 0.10 mm and the number of holes of 300H was used
in spinning. The obtained as-spun filaments were subjected to heat
treatment under the same conditions as those of Example 1 and were
rewound with applying the finishing agent in the same manner. The
tenacity of the obtained melt-anisotropic aromatic polyester
multifilament was 26.1 cN/dtex. The interfiber dynamic friction
coefficient was 0.158. Further, in the evaluation of abrasion
resistance, the pulley was reciprocatingly rotated 1470 times
before fiber breakage.
Comparative Example 2
[0073] As-spun filaments of a multifilament of 1670 dtex/20 f
(single fiber fineness of 83.5 dtex) were obtained in the same
manner as that of Example 1 except that a nozzle having a hole
diameter .phi. of 0.40 mm and the number of holes of 20H was used
in spinning. The obtained as-spun filaments were subjected to heat
treatment under the same conditions as those of Example 1 and were
rewound with applying the finishing agent in the same manner. The
tenacity of the obtained melt-anisotropic aromatic polyester
multifilament was 18.2 cN/dtex. The interfiber dynamic friction
coefficient was 0.072. Further, in the evaluation of abrasion
resistance, the pulley was reciprocatingly rotated 8948 times
before fiber breakage.
Comparative Example 3
[0074] A melt-anisotropic aromatic multifilament of 1670 dtex/100 f
(single fiber fineness of 16.7 dtex) was obtained in the same
manner as that of Example except that the finishing agent was
applied at 2.0 wt %. The tenacity of the obtained melt-anisotropic
aromatic polyester multifilament was 25.1 cN/dtex. The interfiber
dynamic friction coefficient was 0.182. Further, in the evaluation
of abrasion resistance, the pulley was reciprocatingly rotated 1360
times before fiber breakage.
Comparative Example 4
[0075] A melt-anisotropic aromatic multifilament of 1670 dtex/50 f
(single fiber fineness of 33.4 dtex) was obtained in the same
manner as that of Example 2 except that the finishing agent was
applied at 2.0 wt %. The tenacity of the obtained melt-anisotropic
aromatic polyester multifilament was 23.2 cN/dtex. The interfiber
dynamic friction coefficient was 0.167. Further, in the evaluation
of abrasion resistance, the pulley was reciprocatingly rotated 3745
times before fiber breakage.
Comparative Example 5
[0076] A melt-anisotropic aromatic multifilament of 1670 dtex/100 f
(single fiber fineness of 16.7 dtex) was obtained in the same
manner as that of Example 1 except that a dimethylsilicone having a
weight average molecular weight of 6000 and a viscosity of 110
mm.sup.2/s was used as a finishing agent. The tenacity of the
obtained melt-anisotropic aromatic polyester multifilament was 25.7
cN/dtex. The interfiber dynamic friction coefficient was 0.069.
Further, in the evaluation of abrasion resistance, the pulley was
reciprocatingly rotated 4598 times before fiber breakage.
Comparative Example 6
[0077] A melt-anisotropic aromatic multifilament of 1670 dtex/100 f
(single fiber fineness of 16.7 dtex) was obtained in the same
manner as that of Example 1 except that a dimethylsilicone having a
weight average molecular weight of 100000 and a viscosity of 9500
mm.sup.2/s was used as a finishing agent. The tenacity of the
obtained melt-anisotropic aromatic polyester multifilament was 24.9
cN/dtex. The interfiber dynamic friction coefficient was 0.289.
Further, in the evaluation of abrasion resistance, the pulley was
reciprocatingly rotated 2299 times before fiber breakage.
Comparative Example 7
[0078] As-spun filaments of a multifilament of 1670 dtex/600 f
(single fiber fineness of 2.8 dtex) were obtained in the same
manner as that of Example 1 except that a nozzle having a hole
diameter .phi. of 0.08 mm and the number of holes of 600H was used
in spinning. The obtained as-spun filaments were subjected to heat
treatment under the same conditions as those of Example 1 and were
rewound with applying the finishing agent in the same manlier. The
tenacity of the obtained melt-anisotropic aromatic polyester
multifilament was 26.3 cN/dtex. The interfiber dynamic friction
coefficient was 0.196. Further, in the evaluation of abrasion
resistance, the pulley was reciprocatingly rotated 761 times before
fiber breakage.
Comparative Example 8
[0079] A melt-anisotropic aromatic multifilament of 1670 dtex/100 f
(single fiber fineness of 16.7 dtex) was obtained in the same
manner as that of Example 1 except that a step of applying 5.0 wt %
of a dimethylsilicone having a weight average molecular weight of
25000 and a viscosity of 1000 mm.sup.2/s to the multifilament was
performed to as-spun filaments before heat treatment, instead of
applying it as a finishing agent after heat treatment. The amount
of the dimethylsilicone applied was a proportion of the weight of
the dimethylsilicone applied to the as-spun filaments based on the
weight of the as-spun filaments of the multifilament and was a
value measured before heat treatment. The tenacity of the obtained
melt-anisotropic aromatic polyester multifilament was 21.2 cN/dtex.
The interfiber dynamic friction coefficient was 0.264. Further, in
the evaluation of abrasion resistance, the pulley was
reciprocatingly rotated 5380 times before fiber breakage.
TABLE-US-00005 TABLE 5 Dimethylsilicone-series Melt-anisotropic
aromatic polyester multifilament finishing agent Evaluation Single
Single fiber Amount of Interfiber Weight Abrasion fiber average
fiber Total finishing dynamic average resistance (number fineness
diameter fineness agent applied Tenacity friction molecular
Viscosity Strength of replications (dtex) (.mu.m) (dtex) (wt %)
(cN/dtex) coefficient weight (mm.sup.2/s) (N) before breaking) Ex.
1 16.7 38.8 1670 5 25.3 0.109 25000 1000 473 17981 A Ex. 2 33.4
54.9 1670 5 23.6 0.096 25000 1000 394 40941 A Ex. 3 16.7 38.8 1670
5 25.5 0.144 15000 300 426 13164 A Ex. 4 46.4 64.7 1670 5 21.1
0.089 25000 1000 352 64316 A Com. Ex. 1 5.6 22.5 1670 5 26.1 0.158
25000 1000 436 1470 C Com. Ex. 2 83.5 86.8 1670 5 18.2 0.072 25000
1000 304 8948 B Com. Ex. 3 16.7 38.8 1670 2 25.1 0.182 25000 1000
419 1360 C Com. Ex. 4 33.4 54.9 1670 2 23.2 0.167 25000 1000 387
3745 C Com. Ex. 5 16.7 38.8 1670 5 25.7 0.069 6000 110 429 4598 C
Com. Ex. 6 16.7 38.8 1670 5 24.9 0.289 100000 9500 416 2299 C Com.
Ex. 7 2.8 15.9 1670 5 26.3 0.196 25000 1000 439 761 C Com. Ex. 8
16.7 38.8 1670 --* 21.2 0.264 --* --* 354 5380 B *A
dimethylsilicone having a weight average molecular weight of 25000
and a viscosity of 1000 mm.sup.2/s was applied at 5 wt % to as-spun
filaments before heat treatment.
[0080] Table 5 shows the evaluation results. As demonstrated by
Examples 1 to 4, the melt-anisotropic aromatic polyester
multifilaments each having a single fiber fineness from 10 to 80
dtex and comprising 3 to 10 wt % of a dimethylsilicone having a
weight average molecular weight from 15000 to 40000 applied as a
finishing agent to the fiber surface of the multifilament show
excellent abrasion resistance. The melt-anisotropic aromatic
polyester multifilaments of Examples 1 to 4 have a tenacity of 20
cN/dtex or higher.
[0081] In contrast, since each of Comparative Examples 1 and 7 has
a single fiber fineness less than 10 dtex, Comparative Examples 1
and 7 are broken early because the single fibers are abraded due to
interfiber friction in the melt-anisotropic aromatic polyester
multifilament. Comparative Example 2 has poor abrasion resistance
in comparison with those of Examples 1, 2 and 4 because Comparative
Example 2 has a single fiber fineness exceeding 80 dtex. In
Comparative Examples 3 and 4, the finishing agent is applied by
small amounts, resulting in a higher dynamic friction coefficient.
Thus, Comparative Examples 3 and 4 are not able to reduce abrasion
of the single fibers and are broken early. In Comparative Example
5, the finishing agent is prone to falling off from the fiber
surface due to interfiber friction because the dimethylsilicone has
a low weight average molecular weight and the finishing agent has a
low viscosity. Thus, Comparative Example 5 is not able to reduce
abrasion of the single fibers and is broken early. In Comparative
Example 6, the finishing agent is not able to accommodate
interfiber friction because the dimethylsilicone has a high weight
average molecular weight and the finishing agent has a high
viscosity, resulting in a higher dynamic friction coefficient.
Thus, Comparative Example 6 is not able to reduce abrasion of the
single fibers and is broken early. Comparative Example 8 has poor
abrasion resistance in comparison with that of Example 1 because
the dimethylsilicone is applied before heat treatment, instead of
being applied as a finishing agent after heat treatment.
INDUSTRIAL APPLICABILITY
[0082] Melt-anisotropic aromatic polyester fibers having excellent
abrasion resistance which can be obtained by the present invention
may be suitably used for fiber structure applications such as
ropes, cords, and particularly slings.
[0083] Although the preferred examples of the present invention
have been described, those skilled in the art who read the present
specification would arrive at various changes and modifications
without departing from the scope of the invention.
[0084] Accordingly, such changes and modifications are included
within the scope of the present invention defined by the appended
claims.
* * * * *