U.S. patent application number 16/440498 was filed with the patent office on 2020-12-17 for machine to backfill pipelines with improved lifting device.
The applicant listed for this patent is SCAIP S.P.A.. Invention is credited to Gian Paolo DONDI.
Application Number | 20200392697 16/440498 |
Document ID | / |
Family ID | 1000004348959 |
Filed Date | 2020-12-17 |
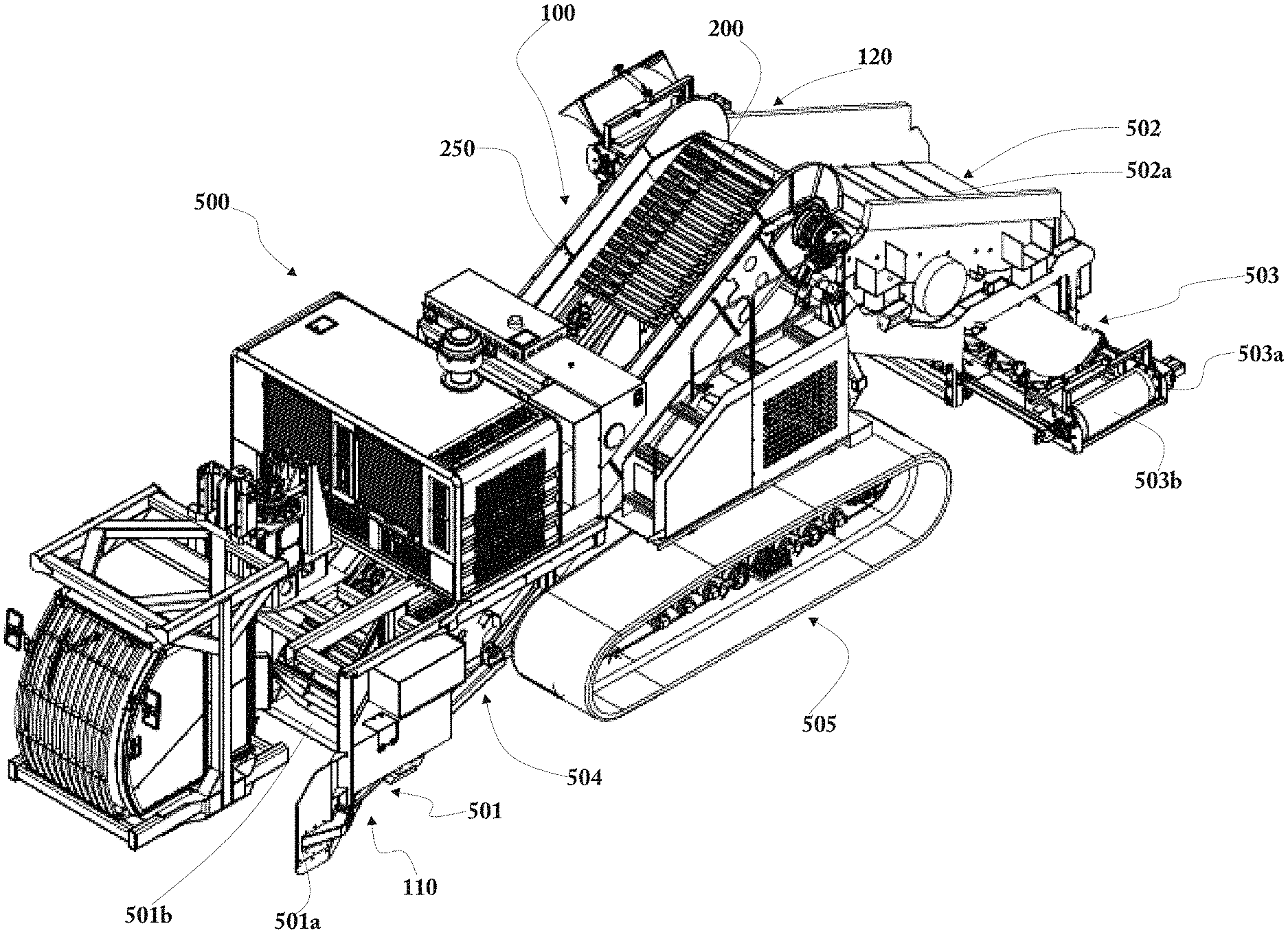
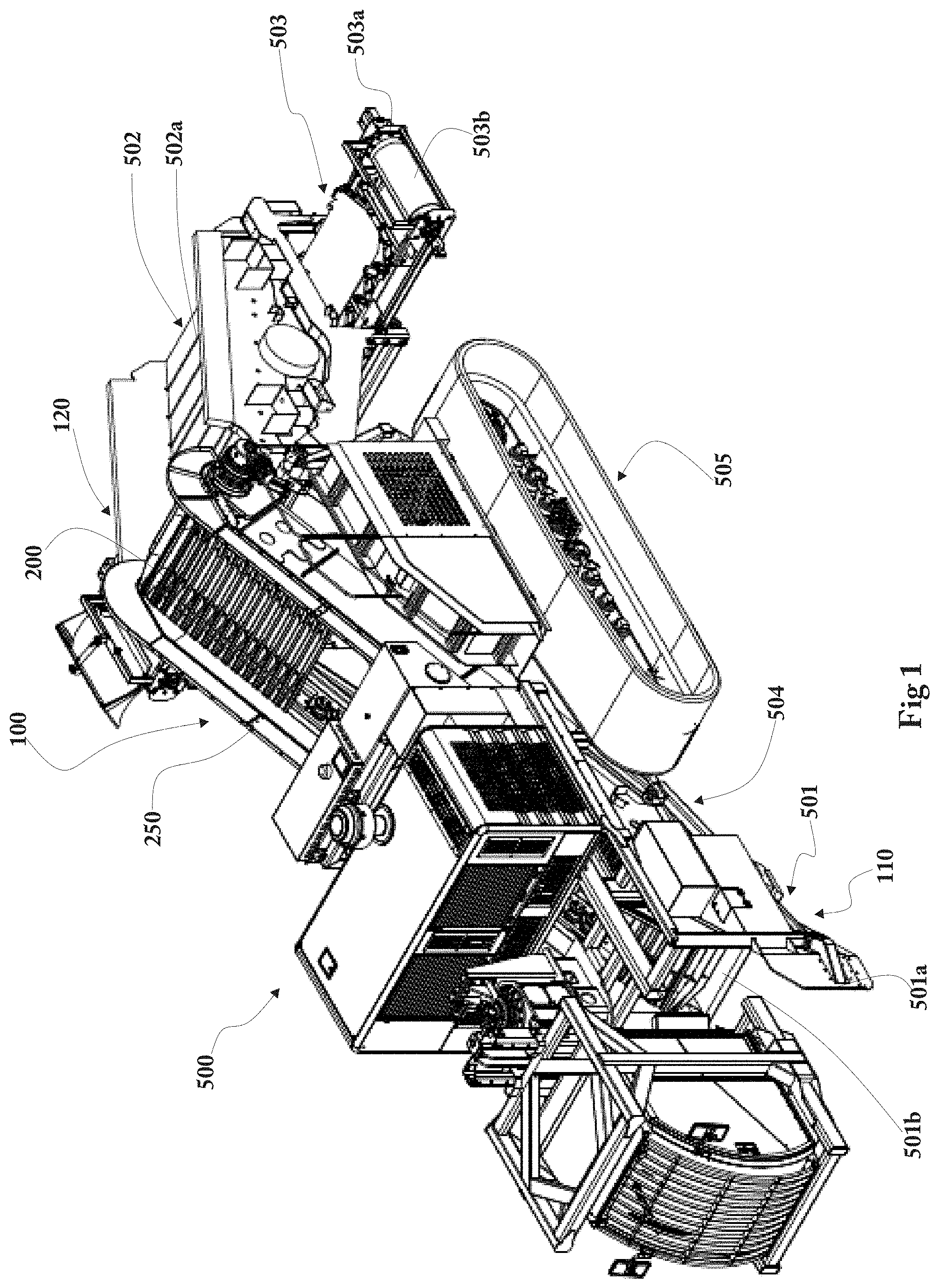

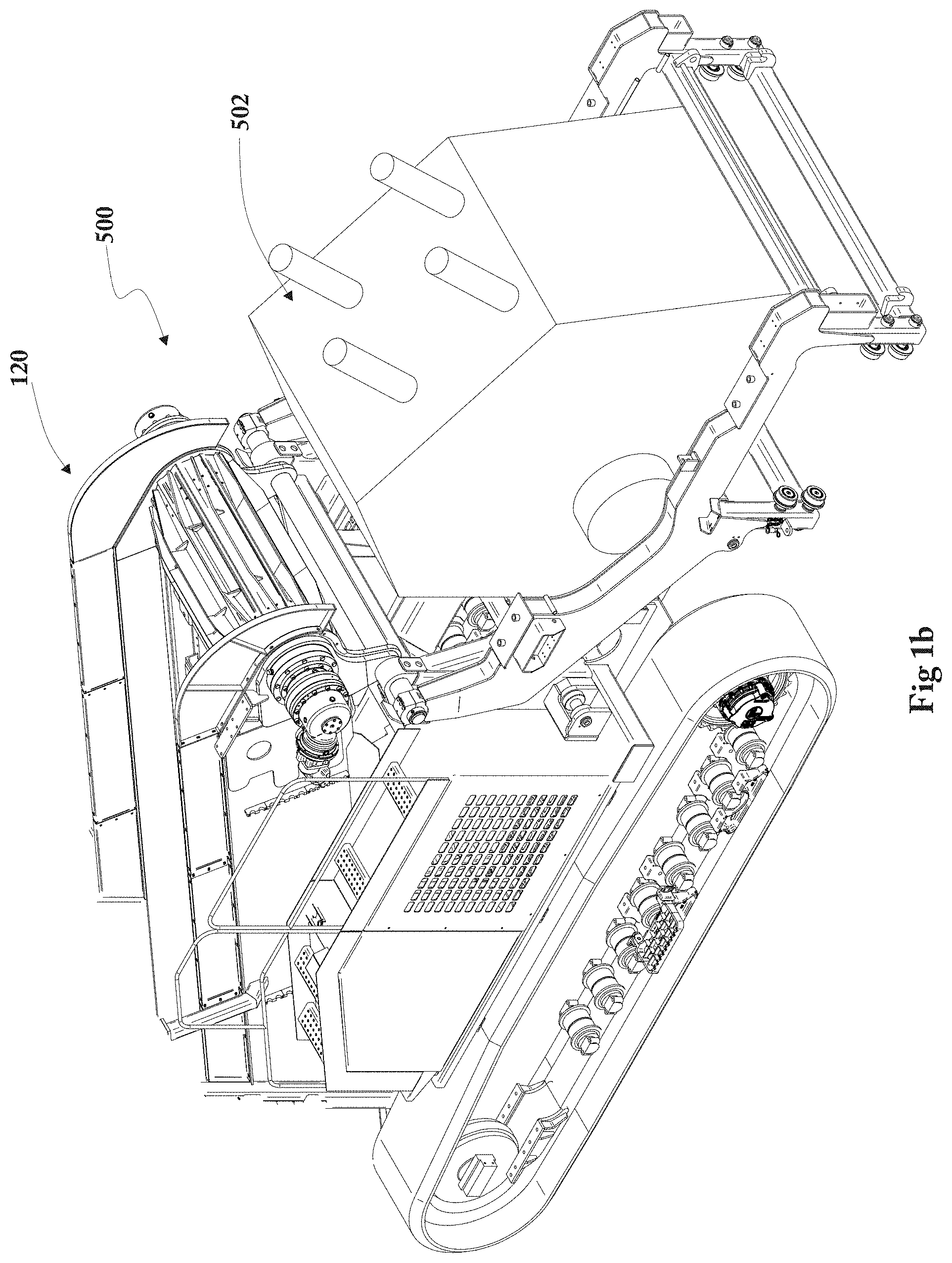



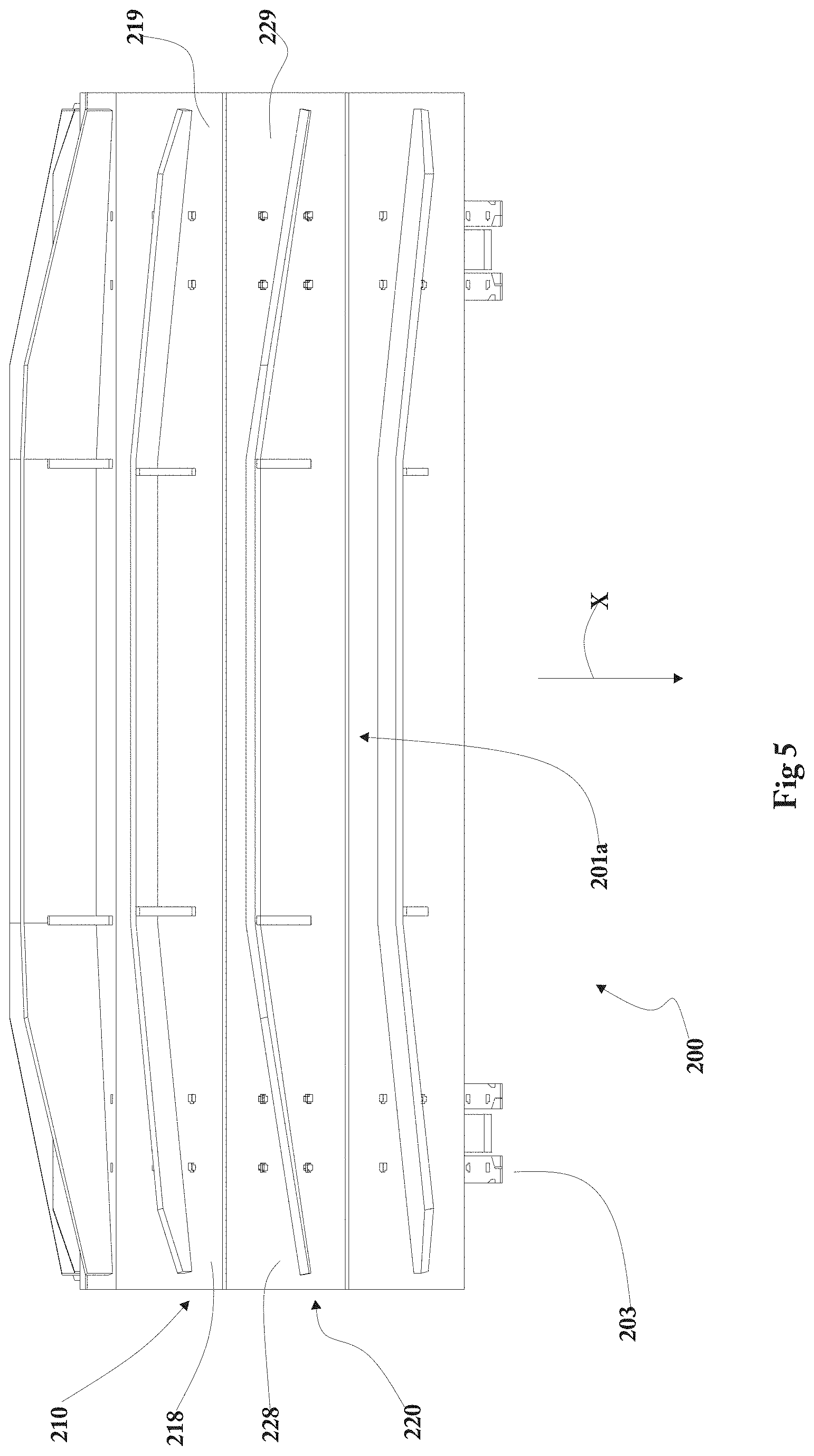
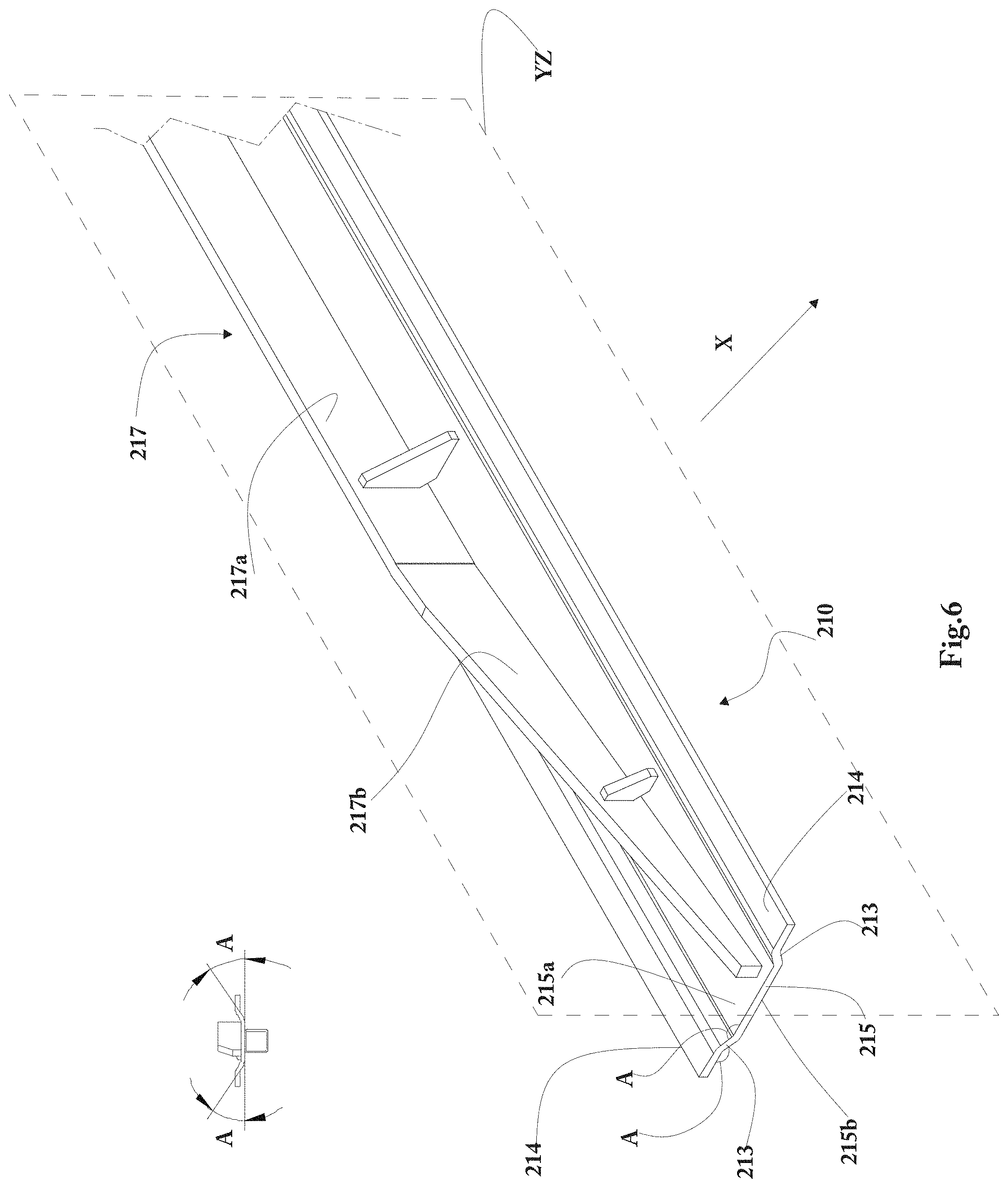

United States Patent
Application |
20200392697 |
Kind Code |
A1 |
DONDI; Gian Paolo |
December 17, 2020 |
MACHINE TO BACKFILL PIPELINES WITH IMPROVED LIFTING DEVICE
Abstract
Machine for the definition of a material for the burying of
pipes, especially a padding machine and/or crusher, in particular
adapted to cover said pipe with the corresponding material,
preferably consisting of the waste material of the excavation for
laying the pipes, comprising a lifting device configured to
transfer the material from a collection area to a storage area, by
means of a conveyor belt comprising a plurality of sections
mechanically associated to towing means, for the movement thereof,
in which said sections alternate in such a way that an overlying
section is continuously in an overlapping relationship with the
adjacent underlying section which precedes it and which follows
it.
Inventors: |
DONDI; Gian Paolo; (Parma
(PR), IT) |
|
Applicant: |
Name |
City |
State |
Country |
Type |
SCAIP S.P.A. |
Parma (PR) |
|
IT |
|
|
Family ID: |
1000004348959 |
Appl. No.: |
16/440498 |
Filed: |
June 13, 2019 |
Current U.S.
Class: |
1/1 |
Current CPC
Class: |
B07B 1/005 20130101;
B07B 13/16 20130101; E02F 5/226 20130101; B07B 1/10 20130101 |
International
Class: |
E02F 5/22 20060101
E02F005/22; B07B 1/10 20060101 B07B001/10; B07B 1/00 20060101
B07B001/00; B07B 13/16 20060101 B07B013/16 |
Foreign Application Data
Date |
Code |
Application Number |
Jun 13, 2019 |
IT |
102019000008805 |
Claims
1. A machine for definition of a material for burying pipe,
comprising: a lifting device configured to transfer the material
from a collection area to a storage area, the lifting device
including: a conveyor belt comprising: a towing chain, a plurality
of sections connected to the towing chain for moving the plurality
of sections, the plurality of sections including overlying sections
alternating with underlying sections in such a way that one of the
overlying sections is continuously in an outwardly overlapping
relationship with both an adjacent one of the underlying sections
that precedes the one of the overlying sections ;n an advancement
direction of the conveyor belt and an adjacent one of the
underlying sections that follows the one of the overlying sections
in the advancement direction.
2. The machine according to claim 1, wherein each of the underlying
and overlying sections comprises respectively a front end and a
rear end, with respect to the advancement direction of the conveyor
belt, in which the front end and the rear end of the one of the
overlying sections overlaps respectively at the rear end of the
adjacent one of the underlying sections that precedes the one of
the overlying sections and at the front end of the adjacent one of
the underlying sections that follows the one of the overlying
sections.
3. The machine according to claim 1, wherein the towing chain
comprises a plurality of links hinged to one another.
4. The machine according to claim 3, wherein each of the plurality
of sections is mechanically connected to one of the plurality of
links, respectively.
5. The machine according to claim 1. wherein each of the plurality
of sections comprises respectively a front end, a rear end and flat
central body, which extends between the front end and the rear
end.
6. The machine according to claim 5, wherein the flat central body,
and the front end and the rear end are symmetrical with respect to
a symmetry plane orthogonal to the advancement direction.
7. The machine according to claim 5, wherein the flat central body
is mechanically connected to a link of the towing chain and
arranged parallel to an axis connecting two fulcrums of rotation of
the link.
8. The machine according to claim 2, wherein the front end and the
rear end of the one of the overlying sections comprise a flat
element parallel to the central body and connected to the central
body by a connecting element forming an angle with the central
body, the connecting element extending away from the towing
chain.
9. The machine according to claim 8, wherein the front end and the
rear end of each of the underlying sections comprise an angled
element connected to the central body and forming an angle with
said central body, the angled element extending toward the towing
chain.
10. The machine according to claim 9, wherein the conveyor belt
further includes a transmission element and a return element for
moving the towing chain and wherein the angle between the
connecting element and the central body and the angle between the
angled element and the central body are configured to allow a
maximum curvature of the towing chain on at least one chosen from
the transmission element and the return element.
11. The machine according to claim 9, wherein the angle between the
connecting element and the central body and the angle between the
angled element and the central body are simular and the connecting
element and the angled element are positioned so that at least in a
rectilinear length of the conveyor belt, the connecting element and
the angled element are overlapping, or facing each other.
12. The machine according to claim 5, wherein each of the plurality
of sections further comprises at the flat central body a
reinforcement element positioned on an inner face toward the towing
chain.
13. The machine according to claim 12, wherein each of the
plurality of sections further comprises a deflector element for
collecting and transferring the material, the deflector element
being positioned at the flat central body.
14. The machine according to claim 13, wherein the deflector
element comprises a plate arranged parallel to a plane of symmetry
and positioned in in the central area of the each of the plurality
of section.
15. The machine according to claim 14, wherein the plate extends
from the central area towards respective side edges and defines
folded wings having an inclination from the central area toward the
respective side edges in the advancement direction.
16. The machine according to claim 13, wherein the deflector
element of the overlying section has a lower height than the
deflector element of the underlying section.
17. The machine according to claim 13, wherein the deflector
element of the underlying section is positioned at an outer face of
the central body, in a rearward position relative to the
advancement direction adjacent the front end of an adjacent
overlying section which follows the underlying section.
18. A lifting device for a machine for burying pipe, the lifting
device configured to transfer material from a collection area to a
storage area, the lifting device comprising: a conveyor belt
comprising: a towing chain, a plurality of sections connected to
the towing chain for moving the plurality of sections, the
plurality of sections including overlying sections alternating with
underlying sections in such a way that one of the overlying
sections is continuously in an outwardly overlapping relationship
with both an adjacent one of the underlying sections that precedes
the one of the overlying sections in an advancement direction of
the conveyor belt and an adjacent one of the underlying sections
that follows the one of the overlying sections in the advancement
direction.
19. The machine according to claim 1, wherein the machine is at
least one chosen from a padding machine and a crusher, and is
adapted to cover the pipe with the material, the material being
waste material from excavation for laying the pipe.
Description
FIELD OF APPLICATION OF THE INVENTION
[0001] The present finding relates to a machine for the burying of
pipes, in particular arranged in a respective excavation of the
ground, such as gas pipelines, oil pipelines, aqueducts or others,
and in particular adapted to cover said pipe with a corresponding
material.
[0002] In particular, it relates to padding machines or crushers,
the lifting devices of which are adapted to transfer the covering
material, or waste material of the excavation, from a collection
area to a storage area for the subsequent screening or
crushing.
STATE OF THE ART
[0003] When constructing pipelines, the ground is generally dug to
create a ditch into which the tubes constituting said pipelines are
positioned.
[0004] Generally, part of the material, which is excavated from the
ground to obtain the ditch, is subsequently re-used to cover the
tubes.
[0005] Preferably said material is a treated, i.e., screened
material, or suitably crushed, such as not to damage the pipe or
such as not to create empty zones about the same pipe, and
preferably consists of the waste material of the excavation for
laying the pipes.
[0006] By means of a screening or crushing system, the larger
components, such as rocks or boulders, which could damage the pipes
themselves, or not allow a proper compaction of the ground above
the tube, are eliminated.
[0007] Machines, or padding machines, are known from the prior art,
for the burying of pipes, in particular arranged in a respective
excavation of the ground, such as gas pipelines, oil pipelines,
aqueducts, or others, and in particular adapted to cover said pipe
with a corresponding material, in particular a treated
material.
[0008] Said machines comprise a main support framework of the
apparatus, and generally comprise lifting devices adapted to
transfer the waste material from the collection area to the storage
area, for example, the screening area.
[0009] Said lifting devices are typically obtained from conveyor
belts in which the waste material is loaded and transferred to the
screen or a crushing device.
[0010] Conveyor belts are known from the prior art, which comprise
a plurality of sections, on which the waste material rests, which
are so shaped that there is a partial overlapping between a section
and the one which precedes or follows it. This configuration is
important in order to avoid that the transported waste material may
fall in any cracks that are present between a section and the nest
one, thereby being lost.
[0011] The known solutions, such as that described in document
EP2076632, provide for an overlapping of the rear end of a section
to the front end of the adjacent one, where front and rear are
meant with reference to the advancement direction of the sections
of the conveyor belt.
[0012] This involves considerable costs for the implementation said
sections, since, in order to achieve the above-described
overlapping, in which each rear end of a section is overlapped to
the adjacent one, each section has the initial and final ends
differently shaped from one another.
[0013] Said configurations requires that the processing operations
are carried out with different equipment and configurations, for
example, the bends, by different bending tools.
[0014] Consequently, this involves long and expensive production
times.
DISCLOSURE AND ADVANTAGES OF THE FINDING
[0015] The technical problem underlying the present invention is to
provide a machine for the burying of pipes, especially a padding
machine, wherein a lifting device of the waste material is
structurally and functionally devised to overcome one or more of
the limitations set forth above with reference to the cited prior
art.
[0016] Within the scope of the above-mentioned problem, main object
of the invention is to develop a machine for the burying of pipes
with a lifting device which allows obtaining a rational solution,
which allows a reduction of the manufacturing costs for the
manufacturing thereof.
[0017] A further object of the invention is also to provide to the
art a machine for the burying of pipes with a lifting device, in
view of a solution which allows achieving the maximum transport
efficiency of waste material, reducing losses during the lifting
thereof.
[0018] Such and other objects are achieved by virtue of the
characteristics of the invention set forth in the independent
claims. The dependent claims outline preferred and/or particularly
advantageous aspects of the invention.
[0019] In particular, the present invention provides a machine for
the burying of pipes, especially a padding machine, in particular
adapted to cover said pipe with a corresponding material,
preferably consisting of the waste material of the excavation for
laying the pipes. Said machine comprises a lifting device
configured to transfer the material from a collection area to a
storage area, by means of a movable conveyor belt comprising a
plurality of sections mechanically associated to towing means for
the movement thereof, in which said sections alternate in such a
way that an overlying section is continuously in an overlapping
relationship with the adjacent underlying section which precedes it
and which follows it.
[0020] By virtue of this configuration, the efficiency of the
conveyor belt is improved, since excessive amounts of the material
are prevented from falling through said sections.
[0021] A preferred embodiment provides that each section comprises,
respectively, a front end and a rear end with respect to the
advancement direction of the conveyor belt, in which both the front
end and the rear end of the overlying section overlap respectively
at the rear end and at the front end of the adjacent underlying
sections.
[0022] In fact, the sections comprise a substantially flat central
body, which extends between the front end and the rear end.
Preferably said central body and the front ends and the rear end of
the sections are symmetrical with respect to a symmetry plane
orthogonal to the advancement direction of the same sections.
[0023] By virtue of this solution, the manufacturing of the
sections is simplified at the production level.
[0024] In fact, the front and rear ends are equal and symmetrical
for each section, therefore they need the same processing, without
changing tools or configurations.
[0025] Said objects and advantages are all achieved by the machine
for the burying of pipes with lifting device that is the subject
matter of the present finding, which is characterized by what has
been provided in the claims set forth herein below.
BRIEF DESCRIPTION OF THE FIGURES
[0026] This and other characteristics will be more clearly
understood from the following description of some embodiments,
which are illustrated by way of non-limiting example in the
attached drawing tables.
[0027] FIG. 1: illustrates a perspective, schematic view of a
preferred implementation of machine or padding machine according to
the present finding;
[0028] FIG. 1a: illustrates a perspective, schematic view of a
preferred implementation of machine of the star screen type
according to the present finding;
[0029] FIG. 1b: illustrates a perspective, schematic view of a
preferred implementation of machine of the crusher screen type
according to the present finding;
[0030] FIG. 2: illustrates a schematic axonometric view of a
preferred implementation of a lifting device according to the
present finding;
[0031] FIG. 3: illustrates a schematic side view of a preferred
implementation of a lifting device according to the present
finding;
[0032] FIG. 4: illustrates a schematic magnification of a preferred
implementation of the conveyor belt according to the present
finding;
[0033] FIG. 5: illustrates a top view of a preferred implementation
of a sequence of sections of the conveyor belt according to the
present finding;
[0034] FIG. 6: illustrates an axonometric view of a preferred
implementation of an overlying section of the conveyor belt
according to the present finding;
[0035] FIG. 7: illustrates an axonometric view of a preferred
implementation of an underlying section of the conveyor belt
according to the present finding.
DESCRIPTION OF THE FINDING
[0036] With particular reference to FIGS. 1, 1a, and 1b, a machine
500 for the definition of a material for the burying of pipes
according to the present invention is illustrated, in particular a
preferred implementation of said machine for the burying of pipes,
especially a padding machine or crushers.
[0037] By the term definition of a material is meant that the
machine may provide both a selection of a predetermined dimension
of material, when the machine is of the padding machine type, and
provide an intervention on the material itself in order to obtain a
predetermined dimension of said material, when the machine is of
the crusher type.
[0038] Said pipes are in particular located in a respective
excavation of the ground, for example gas pipelines, oil pipelines,
aqueducts, or others.
[0039] The machine 500 provides for covering said pipe with a
corresponding material, especially a treated, i.e., screened,
material, as represented in FIG. 1, 1a, or a crushed material, as
represented in FIG. 1b, such as not to damage the pipe or such as
not to create empty zones about the same pipe, and preferably
consisting of the waste material of the excavation for laying the
pipes.
[0040] Especially, FIG. 1 illustrates a padding machine, FIG. 1a
illustrates a screen of the star type in which the rotors are
arranged under protection and pre-selection bars, both configured
to select a predetermined dimension of material, while FIG. 1b
illustrates a screen crusher providing for an intervention on the
material itself in order to obtain a predetermined dimension of
said material.
[0041] In particular, the machine 500 comprises a main support
framework 504 of the apparatus, which extends according to a
respective longitudinal axis of the same machine 500.
[0042] In particular, as it is inferred from FIG. 1, in the machine
500, means 505 for the advancement of the machine 500 with respect
to the ground, in particular in the form of rotatable means are
provided, which engage the ground and support said main support
framework 504, and preferably a first and a second side tracks for
the advancement and support of the machine 500 on the ground.
[0043] The machine 500 preferably includes a collection assembly
501 of the waste material collected from the ground.
[0044] Typically, said material can be the same material which has
been previously excavated to obtain the excavation in which the
pipes have to be arranged.
[0045] In particular, as it is inferred from FIG. 1, the collection
assembly 501 of the pipe covering material, in particular for the
collection of said material from the ground, preferably comprises
an element 501b for the separation of said material, in particular
in the form of a horizontal cutting element.
[0046] In particular, as it is inferred from the figure, the
machine has means, or apparatus 503 for discharging the material,
in particular the treated material, above said pipes, and
especially into the housing excavation of the same pipe, in
particular said means, or apparatus 503 for discharging the
material are adapted to laterally extend, beyond the respective
side of said machine 500, in particular at both sides of the same
machine 500, and preferably are in the form of a respective
conveyor belt having a support frame 503a supported by said main
support framework 504 of said machine 500 and an endless belt 182
rotatable on said support frame.
[0047] In particular, as it can be inferred from FIG. 1, in the
machine 500, means, or apparatus 502 are provided, for the
treatment of said material, in particular in the form of means, or
apparatus, for screening said material, in particular including a
perforated plate 502a, preferably extending from the top down,
according to the rear direction with respect to the machine 500, on
which plate 502a said material is dropped, which material falls,
passing through the screen on the upstream end of said means, or
apparatus 503 for discharging the material, while that portion of
the material that does not pass through the screen is preferably
discharged at the rear of the same machine 500.
[0048] However, it shall be understood that said perforated plate
502a could also be substituted by a convenient net suitable to the
purpose.
[0049] Furthermore, as represented in FIGS. 1a and 1b, the machine
500 could comprise means 502 for the treatment of the material,
which can be in the form of the screen cited above, or they can
also be defined by corresponding bars or rotors adapted to perform
the same function represented in FIG. 1a, or in the form of a
corresponding crusher, adapted to crush the boulders or hard
material of said material, in order to reduce the dimensions
thereof, represented in FIG. 1b.
[0050] In particular, as it is inferred from the figures, in the
machine 500, a lifting device 100 configured to transfer the
excavated waste material from a collection area 110 to a storage
area 120 is provided.
[0051] Said collection area 110 and storage area 120 are, for
example, the collection assembly 501 and the treatment apparatus
502.
[0052] Said lifting device 100 is preferably in the form of a
respective ascending conveyor belt 200, extending between the
collection area 110 and the storage area 120.
[0053] Said collection area 110 is preferably arranged at a lowered
end upstream, with respect to the advancement direction of the
machine 500, substantially at the level of the ground, which
receives the material through the collection assembly 501 of the
tube covering material.
[0054] As illustrated, said lifting device 100 is preferably
preceded by the collection assembly 501 of the material, which has
opposite side small edges 501a for holding the material, which
small edges extend, diverging from each other, anteriorly to said
conveyor belt 200, with respective ends, which are arranged at the
same ground and provide for centrally conveying the material on
said conveyor belt 200.
[0055] Said storage area 120 is preferably arranged at a lifted end
downstream, with respect to the advancement direction of the
machine 500, which lets the material fall on said means, or
apparatus 502 for the treatment of said material.
[0056] Said lifting device 100 preferably comprises a support frame
250, which is supported by said main support framework 504 of said
machine 500, and an endless conveyor belt 200 rotatable on said
support frame 250.
[0057] The waste material rests on and is transferred to the
conveyor belt 200.
[0058] For the movement of the conveyor belt 200, the lifting
device 100 further comprises towing means 203 configured to be
operatively connected to a transmission element 202.
[0059] As represented in the figure, the towing means 203 are for
example a chain 203a preferably comprising a plurality of links 204
hinged to one another.
[0060] Consequently, in the case where the towing means 203 are of
the chain type 203a, they can be operatively connected to a
transmission element 202, for example, they can mesh with a pinion
or a crown, or alternatively, any transmission elements that those
skilled in the art find as suitable.
[0061] Said transmission element 202 is preferably integral to a
pin 202a, actuated so as to rotate by means of actuation devices,
such as electrical, hydraulic motors, etc.
[0062] According to an embodiment, the conveyor belt 200, on which
the waste material rests, is therefore movable and comprises a
plurality of sections 210, 220 each mechanically associated to the
towing means 203, for the movement thereof.
[0063] A preferred embodiment provides that said sections 210, 220
are mechanically associated to two or more towing means 203 for
example two chains 203a arranged in the proximity of the side edges
218, 219 and 228, 229, of the sections 210, 220; by side edges 218,
219 and 228, 229 the end areas of the length of each section 210,
220 are meant, where by length is meant the extension of the
section 210, 220 in an orthogonal direction with respect to an
advancement direction X of the conveyor belt 200.
[0064] In the lifting devices 100 having larger dimensions, said
sections 210, 220 can be mechanically associated, for example, to
three towing means 203, for example three chains 203a arranged,
besides in the proximity of the side edges 218, 219 and 228, 229,
also centrally.
[0065] As represented in FIG. 3, the lifting device 100 further
comprises a return element 205 about which the towing means 203
wind, and therefore about which the conveyor belt 200 rotates.
[0066] In this manner, said conveyor belt 200 is shaped as a closed
ring, hence being endlessly rotatable.
[0067] In the case that the towing means 203 are of the chain type
203a, the return element 205, can be for example a rotatable pinion
or crown, or wheel, or, alternatively, a fixed pad or any return
element that those skilled in the art find as suitable.
[0068] A preferred embodiment provides that, since said conveyor
belt 200 is shaped as a closed ring, it comprises an upper portion
201a, on which the waste material rests for the lifting thereof,
and a lower portion 201b facing the ground.
[0069] Said upper portion 201a, and lower portion 201b are
preferably rectilinear and preferably arranged inclined with
respect to the ground.
[0070] The upper portion 201a, and the lower portion 201b are
joined by a first curvilinear portion 201c, of the conveyor belt
200, arranged at the top of the lifting device 100 and by a second
curvilinear portion 201d, of the conveyor belt 200, arranged at the
bottom of the lifting device 100.
[0071] Said first curvilinear portion 201c is located at the
storage area 120, while the second curvilinear portion 201d is
located at the collection area 110.
[0072] In particular, as represented in FIG. 3, the first
curvilinear portion 201c winds about the transmission element 202,
while the second curvilinear portion 201d winds about the return
element 205.
[0073] Said solution is preferred, since it optimizes the movement
of the towing means 203, which operate by towing in the loaded
part, i.e., at the upper portion 201a on which the material is
present.
[0074] Nevertheless, on the contrary, the first curvilinear portion
201c winds about the return element 205, while the second
curvilinear portion 201d winds about the transmission element 202,
even if said configuration involves that the towing means 203 have
to operate by a thrust in the loaded part, i.e., at the upper
portion 201a on which the material is present.
[0075] As represented in FIGS. 3 and 4, the conveyor belt provides
that the sections 210, 220 are installed on the towing means 203,
and in particular on the chain 203a.
[0076] Preferably, each section 210, 220 is integral and/or
mechanically connected, to the respective link 204 of said chain
203a.
[0077] According to a preferred embodiment, the sections 210 and
220 have at least two different configurations, and in particular
the invention defines one section, which will be referred to as
overlying section 210, and one section, which will be referred to
as underlying section 220.
[0078] Said sections 210, 220 are preferably arranged so that an
overlying section 210 is followed by an underlying section 220, and
so on.
[0079] According to an aspect of the finding, the overlying section
210 is continuously in an overlapping relationship with the
adjacent underlying section 220 which precedes it and which follows
it with respect to the advancement direction X of the conveyor belt
200.
[0080] Said continuous overlapping prevents excessive amounts of
the material from falling through said sections 210, 220, thereby
compromising the efficiency of the conveyor belt.
[0081] In accordance with an aspect of the invention, each section
210, 220 comprises respectively a front end 211, 221 and a rear end
212, 222, with respect to the advancement direction X of the
conveyor belt 200.
[0082] In particular, as represented in FIGS. 3 and 4, both said
front end 211 and said rear end 212 of the overlying section 210
overlap respectively at the rear end 222 and at the front end 221
of the adjacent underlying sections 220.
[0083] That is, said front end 211 of the overlying section 210
overlaps the rear end 222 of the adjacent underlying section 220
which precedes it, while the rear end 212 of the overlying section
210 overlaps the front end 221 of the adjacent underlying section
220 which follows it.
[0084] A possible embodiment provides that both the front end 211
and the rear end 212 of the overlying section 210 overlap
respectively at the rear end 222 and at the front end 221 of the
adjacent sections 220, leaving a variable spacing H during the
winding of the conveyor belt 200 about the transmission element 202
on which the towing means 203 mesh, and/or about the return element
205 on which the towing means 203 wind.
[0085] Said sections 210, 220 comprise preferably a substantially
flat central body 215, 225, which extends between the front end
211, 221 and the rear end 212, 222.
[0086] An embodiment provides that the central body 215, 225 is
mechanically connected to the towing means 203; in particular in
the case where said means are a chain 203a, the central body 215,
225 is preferably arranged parallel to the axis connecting the two
fulcrums of rotation of each link 204 of the chain 203a.
[0087] Preferably the central body 215, 225 and the front ends 211,
221 and the rear end 212, 222 of the sections 210, 220 are
symmetrical with respect to a symmetry plane YZ orthogonal to the
advancement direction X of the section 210, 220. In particular said
plane of symmetry YZ, as represented in FIGS. 7, 8, passes through
the center of the central body 215, 225.
[0088] By virtue of said configuration, the section 210, 220 can be
obtained in a simple, rapid manner. In fact, by virtue of the
symmetry, as it will be more fully described herein below, the
processing operations, for example, the bends, to be carried out do
not require changes of tools, such as, for example, bending
knives.
[0089] In accordance with possible embodiments, as represented in
FIG. 6, the front end 211 and the rear end 212 of the overlying
sections 210 comprise a flat element 214 substantially parallel to
the central body 215 connected thereto, by means of a connecting
element 213 facing away from the towing means 203, for example
moving away from the link 204 of the chain 203a.
[0090] In particular the connecting element 213 forms an angle A
with the central body 215.
[0091] The angle A is preferably the same as the angle formed
between the connecting element 213 and the flat element 214.
[0092] In particular, the angle A, between the connecting element
213 and the central body 215, is configured to allow the maximum
curvature of the towing means 203, for example of the chain 203a,
on the transmission element 202 and/or on the return element
205.
[0093] As regards the underlying sections 220, an embodiment
represented in FIG. 7 provides that the front end 221 and the rear
end 222 comprise an angled element 223 connected to the central
body 225 and facing the towing means 203, i.e., the link 204 of the
chain 203a. The angled element 223 forms an angle A' with the
central body 225, for example by means of a sharp edge connection,
or a junction having a curvature radius that is suitable to the
link 204 of the chain on which the section 220 is installed.
[0094] In this case also, the angle A' between the angled element
223 and the central body 225 is preferably configured to allow the
maximum curvature of the towing means 203, for example of the chain
203a, on the transmission element 202 and/or on the return element
205.
[0095] A preferred embodiment provides that the angles A and A' are
substantially simular.
[0096] Except for tolerances that are known to those skilled in the
art, said angles A and A' are further preferably equal.
[0097] For example, a preferred embodiment provides that A can be
equal to 35.degree., and A' can be equal to 33.degree., when, for
example, the maximum curvature of the towing means 203 is about
35.degree..
[0098] This improves the overlapping and simplifies the processing
required for the production of the sections 210 and 220, since it
is possible to always use the same knives to obtain the bends,
without needing to change the equipment.
[0099] Furthermore, the connecting element 213 and the angled
element 223 are positioned preferably so that, in the rectilinear
length of the belt 200, for example in the upper 201a and lower
201b portions, they are perfectly overlapping, or facing each
other, as represented in FIG. 4.
[0100] The sections 210 and 220, according to the constructive form
described above, can be made by bending a plate or metal sheet.
[0101] The advantage of the constructive form of the sections 210
and 210 is that their manufacturing is simplified at a productive
level.
[0102] In fact, the front 211, 221 and rear 212, 222 ends are equal
and symmetric for each section 210, 220, therefore they need the
same processing, without changing tools or configurations.
[0103] In particular the underlying section 220 is especially quick
to be produced, and with low production costs.
[0104] For example, for the implementation of the underlying
section 220, the blink, i.e., for example, the laid metal sheet, is
inserted into the bending machine to obtain the first bend, for
example at the front end 221, thus obtaining the first angled
element 223; the thus-obtained working piece is taken and
positioned again into the bending machine rotated by 180.degree.,
and then the second bend is created, at the rear end 222, to obtain
the second angled element 223.
[0105] The implementation of the overlying section 210 is also
easy.
[0106] In fact, the characteristic that the central body 215 and
the flat element 214 are parallel makes so that the bending angle
(A) of the two bends to be obtained is the same.
[0107] Also for the implementation of the overlying section 210,
the laid metal sheet is inserted into the bending machine and the
first bend is obtained, for example on the front end 211, between
the central body 215 and the first connecting element 213; the
thus-obtained working piece is taken and positioned again into the
bending machine, while being arranged upside-down and then the
second bend is created between the first connecting element 213 and
the flat element 214; the thus-obtained working piece is taken and
positioned again into the bending machine, while being rotated by
180.degree., and the bends on the rear end 212 are created in the
same manner described above.
[0108] A characteristic of the finding provides that each section
210, 220 comprises, at the central body 215, 225, a reinforcement
element 216, 226, in particular installed on an inner face thereof
215b, 225b facing the towing means 203, for example, the chain
203a.
[0109] As represented in the figure, said reinforcement element
216, 226 can be, for example, a tubular piece.
[0110] Main object of the reinforcement element 216, 226 is to
increase the resistant section of each section 210, 220, so that it
may oppose the flexure that is due to the load of material present
in the upper portion 201a, and also oppose the torsion due to the
fact that each section 210, 220 is mechanically connected, for
example, to two chains 203a which could not even be exactly
phased.
[0111] Said reinforcement element 216, 226 can be for example
directly welded on the inner face 215b, 225b of the sections 210,
220, or be removably connected by means of screws or simular
securing elements.
[0112] A further aspect of the invention, as represented in the
figure, provides that the section 210, 220 comprises a deflector
element 217, 227 for collecting and transferring the waste
material.
[0113] Said deflector element 217, 227 is installed preferably at
the central body 215, 225 and in particular an outer face 215a,
225a thereof opposite the inner face 215b, 225b.
[0114] The deflector element is shaped so as to pick up the
material from the collection area 110, conveyed by the collection
assembly 501 of the tube covering material.
[0115] The material is centrally conveyed on the conveyor belt 200,
by the opposite holding small edge 501a, which extend, diverging
from each other, anteriorly to said conveyor belt 200, with
respective ends arranged at the same ground.
[0116] Furthermore, the deflector element 217, 227 is shaped so as
to hold the collected material to lift it along the upper portion
201a and to allow the discharge thereof into the storage area
120.
[0117] In particular as represented in FIGS. 3 and 4, the deflector
element 217 associated to the overlying section 210 preferably has
a lower height than the deflector element 227 associated to the
underlying section 220.
[0118] This configuration is due to the fact that the underlying
section 220 is the one having a single bend at the front 221 and
rear 222 ends, and therefore it is the one having a lesser section
that is resistant to flexural and torsional stresses.
[0119] The fact that a higher deflector element 227 is associated
thereto, increases the flexural strength and torsion thereof.
[0120] On the contrary, the overlying section 210, with two bends
at the front and rear ends 211 and 212, is the one having a larger
section that is resistant to flexural and torsional stresses.
Therefore, in such a case, the association therewith of a high
deflector element 217 can be omitted, which would excessively
increase the weight of the conveyor belt to be moved, resulting in
consequences on the larger size of the mechanical components and
the actuation devices, such as electrical, hydraulic motors,
etc.
[0121] Preferably, the overlying section 210 will have a deflector
element 217 which is lower than the deflector element 227
mechanically associated thereto, having a height sufficient for
receiving, holding, lifting, and depositing the material.
[0122] The fact that the overlying section 210 preferably provides
a deflector element 217 which is lower than the deflector element
227 provided on the underlying section 220 facilitates the
assembling, since it provides always a high deflector element 227
alternated with a low deflector element 217. Therefore, the
possibility of errors by the operator in charge for the assembling
of the conveyor belt 200 will be reduced.
[0123] As represented in FIGS. 6 and 7, said deflector element 217,
227 can be, for example, directly welded on the outer face 215a,
225a of the sections 210, 220 or be removably connected by means of
screws or simular securing elements.
[0124] An example of a specific form of the deflector element 217,
227 is the one represented in FIGS. 6 and 7, in which it comprises
for example a plate 217a, 227a arranged parallel to the plane of
symmetry YZ and preferably placed in the central area of the
section 210, 220.
[0125] Said plate 217a, 227a extends from the central area towards
the side edges 218, 219 and 228, 229, defining folded wings 217b,
227b whose inclination is in accordance with the advancement
direction X.
[0126] Furthermore, reinforcements such as ribs supporting the
plate 217a, 227a and/or the folded wings 217b, 227b and which
discharge their load on the section 210, 220 can be present.
[0127] Said configuration of the deflector element 217, 227 is
merely an example, which does not limit the protection scope of the
finding. Therefore, any alternative solution that those skilled in
the art find as suitable to the same functions falls within the
protection scope.
[0128] A preferred implementation form provides that the deflector
element 227 associated to the underlying section 220 is installed
at the outer face 225a of the central body 225, in a rearward
position, that is, moved in the opposite direction to the
advancement direction X with respect to the plane of symmetry YZ of
the underlying section 220. Preferably, the deflector element 227
is arranged in the proximity of the front end 211 of the adjacent
overlying section 210 which follows it.
[0129] Therefore, once the belt 200 has been mounted, the plate
227a of the underlying section 220 will be located, for example, at
a distance of some mm from the front end 211 of the adjacent
overlying section 210 which flows it with respect to the
advancement direction X of the conveyor belt 200.
[0130] By virtue of this solution, the possibility that the
material may insert between the front end 211 of the overlying
section 210 and the rear end 222 of the underlying section 220, as
it would tend to spontaneously do, above all in the ascending upper
portion 201a, is greatly reduced.
[0131] Therefore, by virtue of this solution, the loss of material
is reduced, to the advantage of the efficiency of the lifting
device 100.
[0132] In particular, this effect is pointed out in the upper
portion 201a, on which the waste material rests during the lifting
thereof.
[0133] Considering that the upper portion 201a is the longest
length of the conveyor belt 200 on which the material is present,
it is clear that the advantageous effect is considerable.
[0134] Object of the finding is also a lifting device 100 that can
be installed on a machine 500 for the burying of pipes, especially
a padding machine, in particular adapted to cover said pipe with a
corresponding material, preferably consisting of the waste material
of the excavation for laying the pipes. Said lifting device 100 is
configured to transfer the material from a collection area 110 to a
storage area 120, being obtained according to at least one of the
characteristics described above.
[0135] However, it is intended that what has been described above
is of a non-limiting, exemplary value; therefore, any detail
variations that would be necessary due to technical and/or
functional reasons are as of now considered to fall within the same
protecting scope defined by the claims set forth herein below.
* * * * *