U.S. patent application number 16/955481 was filed with the patent office on 2020-11-26 for magnesium alloy sheet and method for producing same.
The applicant listed for this patent is POSCO. Invention is credited to Young-Wook CHAE, Jae Joong KIM, Oh-Duck KWON, Jun Ho PARK.
Application Number | 20200370157 16/955481 |
Document ID | / |
Family ID | 1000005021348 |
Filed Date | 2020-11-26 |
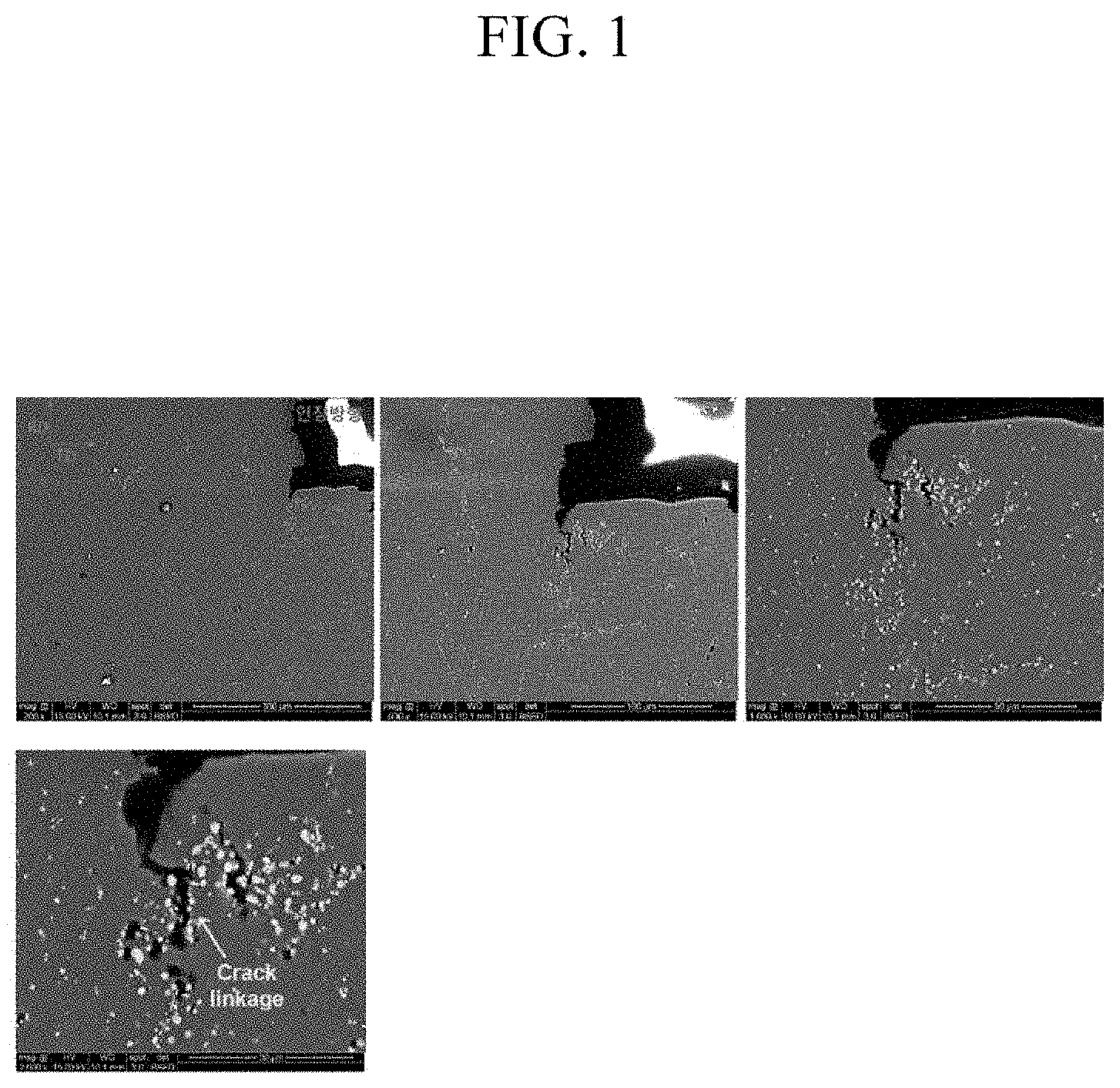
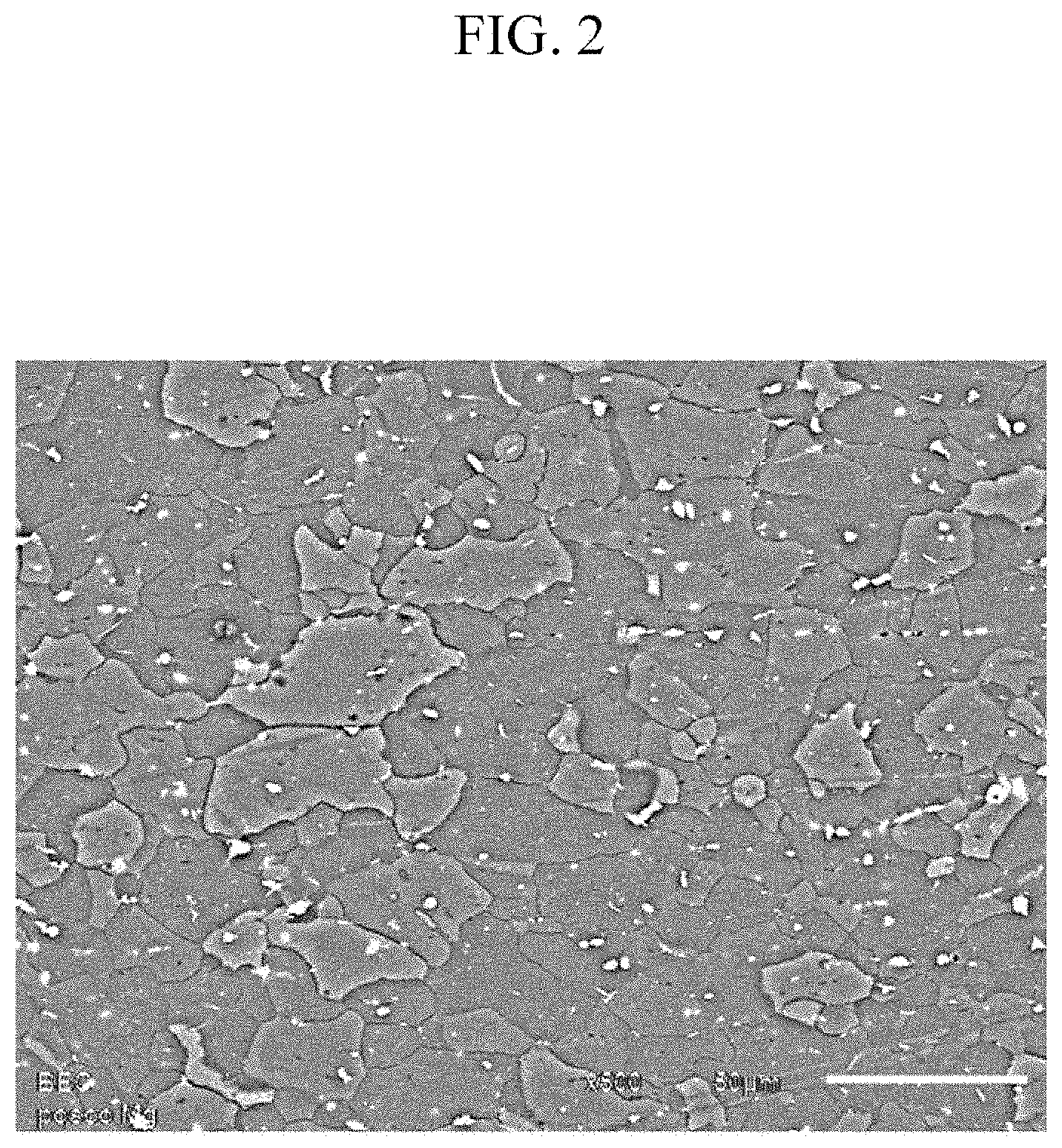
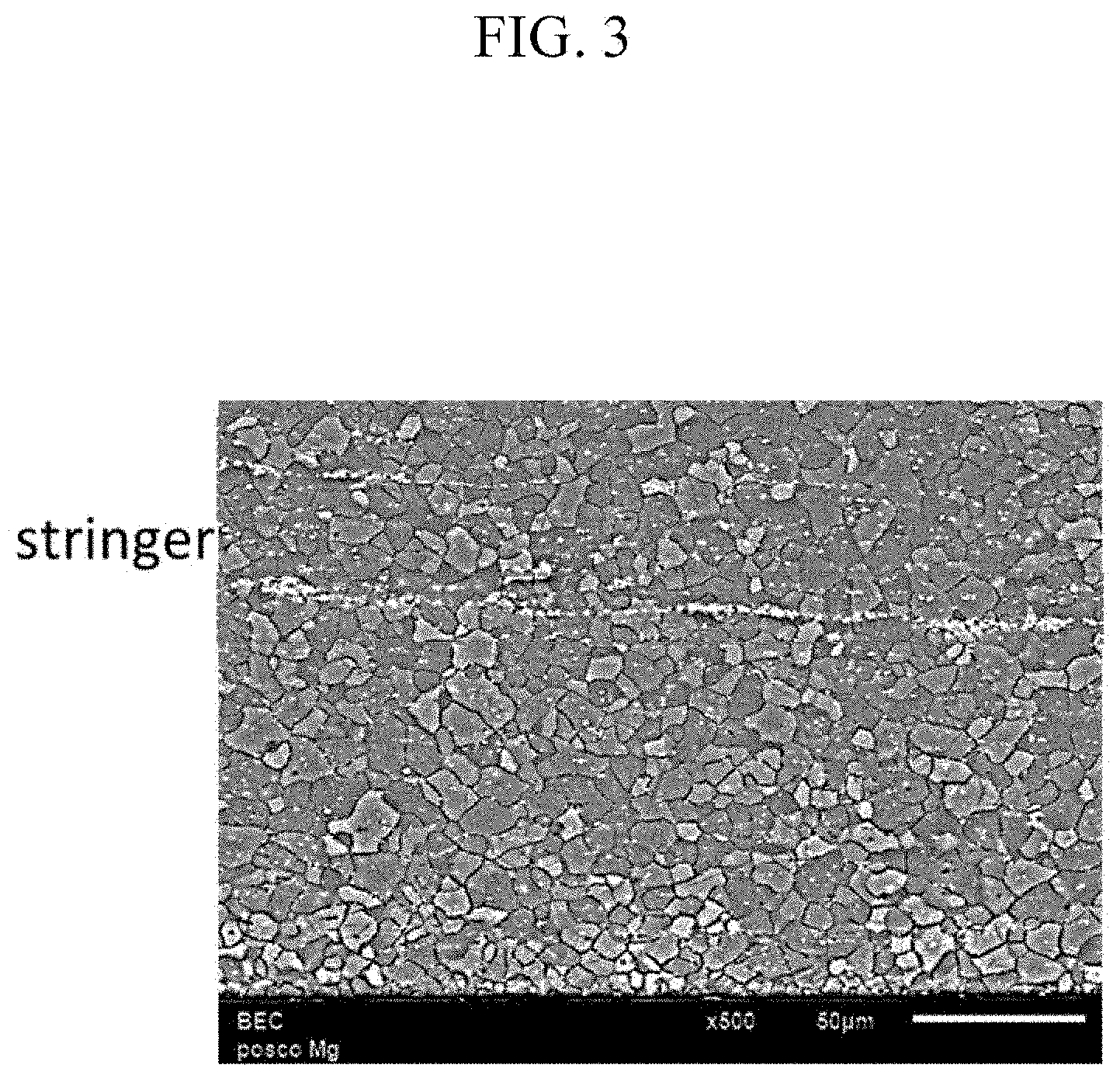
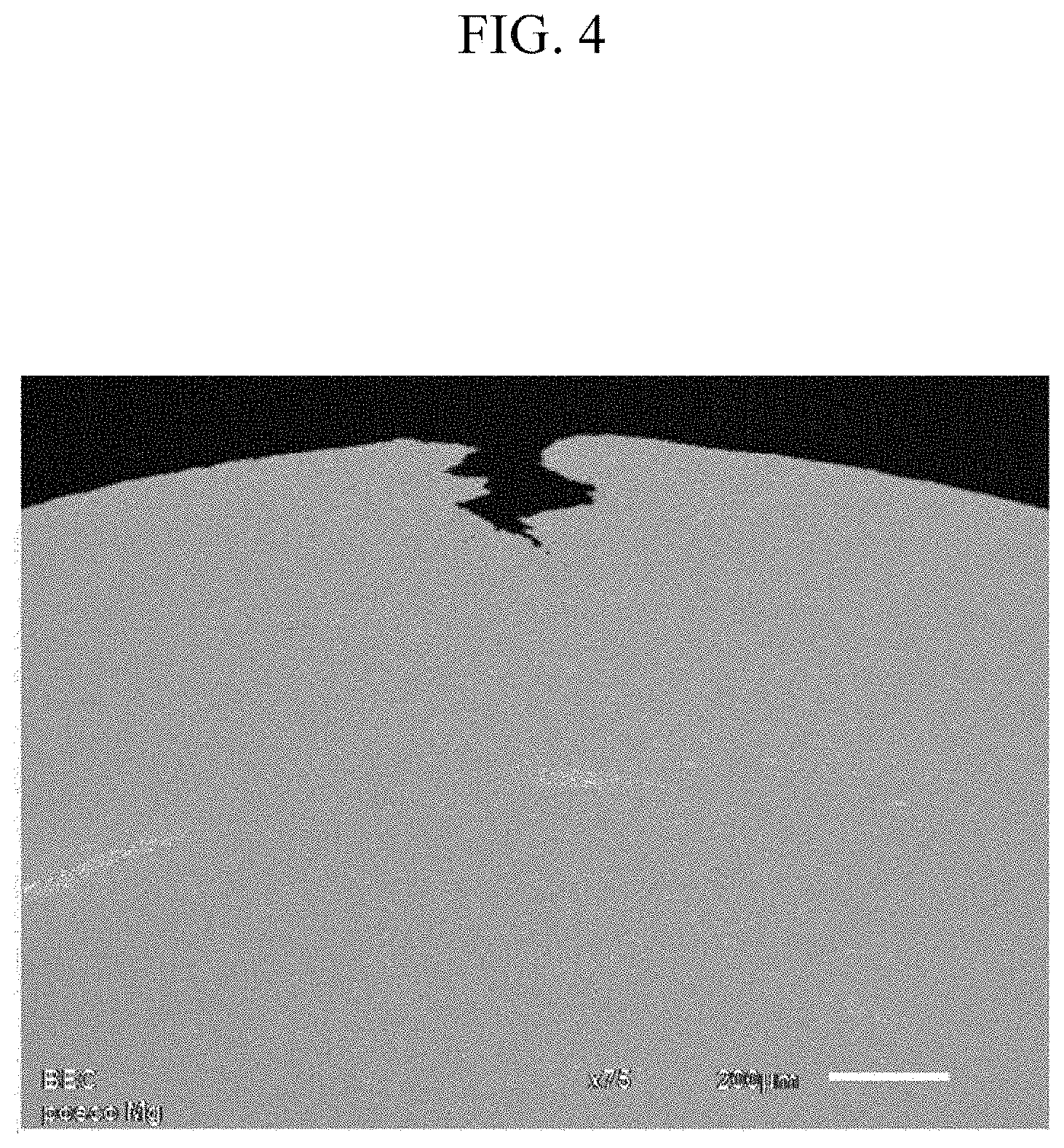
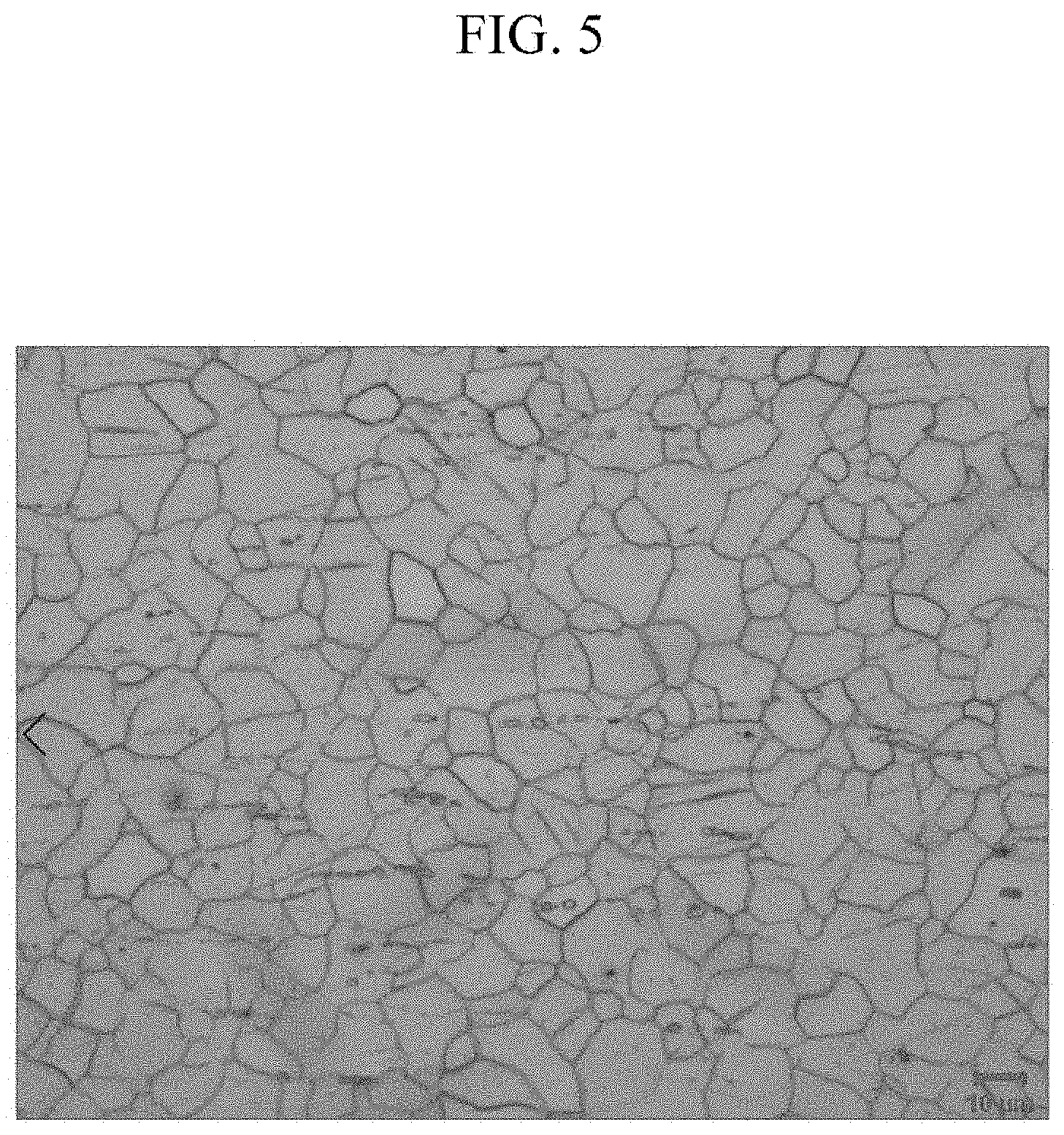
United States Patent
Application |
20200370157 |
Kind Code |
A1 |
PARK; Jun Ho ; et
al. |
November 26, 2020 |
MAGNESIUM ALLOY SHEET AND METHOD FOR PRODUCING SAME
Abstract
The present invention relates to a magnesium alloy sheet and a
manufacturing method thereof. An embodiment of the present
invention provides a magnesium alloy sheet including 0.5 to 1.5 wt
% of Al, 0.5 to 1.5 wt % of Zn, 0.1 to 1.0 wt % of Ca, 0.01 to 1.0
wt % of Mn, a remainder of Mg, and other inevitable impurities with
respect to the entire 100 wt % of the magnesium alloy sheet.
Inventors: |
PARK; Jun Ho; (Pohang-si,
Gyeongsangbuk-do, KR) ; KWON; Oh-Duck; (Pohang-si,
Gyeongsangbuk-do, KR) ; CHAE; Young-Wook; (Pohang-si,
Gyeongsangbuk-do, KR) ; KIM; Jae Joong; (Pohang-si,
Gyeongsangbuk-do, KR) |
|
Applicant: |
Name |
City |
State |
Country |
Type |
POSCO |
Pohang-si, Gyeongsangbuk-do |
|
KR |
|
|
Family ID: |
1000005021348 |
Appl. No.: |
16/955481 |
Filed: |
December 21, 2018 |
PCT Filed: |
December 21, 2018 |
PCT NO: |
PCT/KR2018/016510 |
371 Date: |
June 18, 2020 |
Current U.S.
Class: |
1/1 |
Current CPC
Class: |
C22C 1/02 20130101; C22F
1/06 20130101; B21B 3/00 20130101; C22C 23/02 20130101 |
International
Class: |
C22F 1/06 20060101
C22F001/06; C22C 23/02 20060101 C22C023/02; C22C 1/02 20060101
C22C001/02; B21B 3/00 20060101 B21B003/00 |
Foreign Application Data
Date |
Code |
Application Number |
Dec 26, 2017 |
KR |
10-2017-0180090 |
Claims
1. A magnesium alloy sheet comprising: 0.5 to 1.5 wt % of Al, 0.1
to 0.7 wt % of Zn, 0.1 to 0.5 wt % of Ca, 0.01 to 0.3 wt % of Mn, a
remainder of Mg, and other inevitable impurities with respect to
the entire 100 wt % of the magnesium alloy sheet.
2. The magnesium alloy sheet of claim 1, wherein the Al is 0.5 to
1.3 wt % for the entire 100 wt % of the magnesium alloy sheet.
3. The magnesium alloy sheet of claim 2, wherein the magnesium
alloy sheet includes a secondary phase, and an area fraction of a
secondary phase is equal to or less than 5% for the entire area of
100% of the magnesium alloy sheet.
4. The magnesium alloy sheet of claim 3, wherein the secondary
phase is Al.sub.2Ca, Al.sub.8Mn.sub.5, or a combination
thereof.
5. The magnesium alloy sheet of claim 4, wherein the magnesium
alloy sheet includes a stringer, and a length of the stringer is
equal to or less than 50 .mu.m at a maximum.
6. The magnesium alloy sheet of claim 5, wherein a limited bending
radius (LBR) value in a rolling direction (RD) is 0 to 0.5 R/t when
the magnesium alloy sheet is at equal to or greater than
150.degree. C.
7. The magnesium alloy sheet of claim 6, wherein the limited
bending radius (LBR) value in a transverse direction (TD) is 0 to
0.5 R/t when the magnesium alloy sheet is at equal to or greater
than 150.degree. C.
8. The magnesium alloy sheet of claim 7, wherein a ratio of the
limited bending radius (LBR) value in a transverse direction (TD)
against the rolling direction (RD) is 0.8 to 1.2 when the magnesium
alloy sheet is at equal to or greater than 150.degree. C.
9. The magnesium alloy sheet of claim 8, wherein a limited dome
height (LDH) of the magnesium alloy sheet is equal to or greater
than 8 mm.
10. A method for manufacturing a magnesium alloy sheet, comprising:
preparing an alloy molten metal including 0.5 to 1.5 wt % of Al 0.5
to 1.5 wt % of Zn, 0.1 to 1.0 wt % of Ca, 0.01 to 1.0 wt % of Mn, a
remainder of Mg, and other inevitable impurities with respect to
the entire 100 wt %; preparing a casting material by casting the
molten metal; preparing a rolled material by rolling the casting
material; and finally annealing the rolled material.
11. The method of claim 10, wherein regarding the preparing of an
alloy molten metal, Al is 0.5 to 1.3 wt % for the entire 100 wt %
of the alloy molten metal.
12. The method of claim 10, wherein the preparing of a rolled
material by rolling a casting material includes performing rolling
with a reduction ratio that is equal to or less than 50% (excluding
0%) for each rolling.
13. The method of claim 12, wherein the preparing of a rolled
material by rolling a casting material includes rolling the casting
material once or at least twice.
14. The method of claim 13, wherein the preparing of a rolled
material by rolling a casting material includes performing rolling
at a temperature of 100 to 350.degree. C.
15. The method of claim 10, wherein the preparing of a rolled
material by rolling a casting material further includes
intermediately annealing the rolled material.
16. The method of claim 15, wherein the intermediately annealing of
the rolled material is performed at a temperature of 300 to
500.degree. C.
17. The method of claim 16, wherein the intermediately annealing of
the rolled material is performed for 30 minutes to 6 hours.
18. The method of claim 10, wherein the finally annealing of the
rolled material is performed at equal to or greater than
250.degree. C.
19. The method of claim 18, wherein the finally annealing of the
rolled material is performed for 30 minutes to 6 hours.
20. The method of claim 10, wherein the preparing of a casting
material by casting the molten metal includes performing casting by
a strip casting method.
Description
CROSS-REFERENCE TO RELATED APPLICATION
[0001] This application claims priority to and the benefit of
Korean Patent Application No. 10-2017-0180090 filed in the Korean
Intellectual Property Office on Dec. 26, 2017, the entire contents
of which are incorporated herein by reference.
BACKGROUND OF THE INVENTION
(a) Field of the Invention
[0002] An embodiment of the present invention relates to a
magnesium alloy sheet and a manufacturing method thereof.
(b) Description of the Related Art
[0003] Recently, interests in materials of which weight may be
reduced as structural materials have increased and active
researches thereon are in progress. Accordingly, there are many
interests in magnesium sheets with excellent specific strength
(strength against density).
[0004] The magnesium has density of 1.74 g/cm.sup.3, so is the
lightest metal among the structural metals including aluminum and
steel, and it is a metal that is attracting attention in mobile and
IT fields because of its excellent vibration absorbing ability and
electromagnetic wave shielding ability.
[0005] In addition, in the field of automobiles, researches are
being actively carried out in advanced countries including Europe
to reduce the weight of the vehicle body due to fuel economy and
performance regulations. Hence, magnesium is being considered to be
one of substitute metals.
[0006] However, the magnesium sheet has an HCP structure, and its
deformation mechanism at room temperature is limited, so it is
impossible to be formed at room temperature. Therefore, there are
some limits in applying it to the automobile industry. Many
researches have been performed so as to overcome them.
[0007] For example, there are differentiated speed rolling for
providing different speeds to an upper roller and a lower roller,
an ECAP process, and a high temperature rolling method for
performing rolling at around a eutectic temperature of the
magnesium sheet. However, the above-noted processes are far from
being commercially available.
[0008] For another example, there may be a method of improvement
through an alloy as given by a prior patent (Publication No.
2012-0055304). In detail, a magnesium sheet containing 1 to 10 wt %
of Zn and 0.1 to 5 wt % of Ca may be used. However, the sheet may
not be applied to a strip casting process. Therefore, mass
production is unacceptable, and it is difficult to perform a
long-tern casting because of a fusion phenomenon between a casting
material and a roll.
[0009] Meanwhile, a preceding patent (Korean Application No.
2015-0185017) provides a method for obtaining a high mold with a
limited dome height of equal to or greater than 7 mm by improving
the conventional process of the alloy with 3 wt % of Al, 1 wt % of
Zn, and 1 wt % of Ca. However, the method requires at least one
intermediate annealing and warm forming in the rolling step.
Because of this, a large processing expense is needed, and a large
amount of investment costs such as for a mold or a heating device
is generated. Hence, productivity is deteriorated, and a processing
cost of the magnesium alloy is expensive compared to competing
materials.
[0010] In addition, anisotropy exists when a part is formed in the
case of a high-forming E-form alloy (AZX311) sheet currently
developed by the applicant's company. Accordingly, a magnesium
alloy sheet for solving the above-described problems will be
provided.
[0011] The above information disclosed in this Background section
is only for enhancement of understanding of the background of the
invention, and therefore it may contain information that does not
form the prior art that is already known in this country to a
person of ordinary skill in the art.
SUMMARY OF THE INVENTION
[0012] The present invention has been made in an effort to provide
a magnesium alloy sheet with excellent moldability at room
temperature and less anisotropy of a physical property, and a
manufacturing method thereof.
[0013] In detail, a fraction of a secondary phase containing less
aluminum may be reduced. Hence, a boundary segregating effect
increases to improve moldability at room temperature.
[0014] Further, a secondary phase stringer may be reduced as the
fraction of the secondary phase is reduced. Therefore, a magnesium
alloy sheet, when stretched in a transverse direction (TD), that
does not have a large physical property difference from the case
when stretched in a rolling direction (RD), will be provided.
[0015] An exemplary embodiment of the present invention provides a
magnesium alloy sheet including: 0.5 to 1.5 wt % of Al, 0.1 to 0.7
wt % of Zn, 0.1 to 0.5 wt % of Ca, 0.01 to 0.3 wt % of Mn, a
remainder of Mg, and other inevitable impurities, for the entire
100 wt %.
[0016] The Al may be 0.5 to 1.3 wt % for the entire 100 wt % of the
magnesium alloy sheet.
[0017] The magnesium alloy sheet may include a secondary phase, and
an area fraction of a secondary phase may be equal to or less than
5% for the entire area of 100% of the magnesium alloy sheet.
[0018] The secondary phase may be Al.sub.2Ca, Al.sub.8Mn.sub.5, or
a combination thereof.
[0019] The magnesium alloy sheet may include a stringer, and a
length of the stringer may be equal to or less than 50 .mu.m at a
maximum.
[0020] A limited bending radius (LBR) value in a rolling direction
(RD) may be 0 to 0.5 R/t when the magnesium alloy sheet is at equal
to or greater than 150.degree. C.
[0021] The limited bending radius (LBR) value in a transverse
direction (TD) may be 0 to 0.5 R/t when the magnesium alloy sheet
is at equal to or greater than 150.degree. C.
[0022] A ratio of the limited bending radius (LBR) value in a
transverse direction (TD) against the rolling direction (RD) may be
0.8 to 1.2 when the magnesium alloy sheet is at equal to or greater
than 150.degree. C.
[0023] A limited dome height (LDH) of the magnesium alloy sheet may
be equal to or greater than 8 mm.
[0024] Another embodiment of the present invention provides a
method for manufacturing a magnesium alloy sheet, including:
preparing an alloy molten metal including 0.5 to 1.5 wt % of Al,
0.5 to 1.5 wt % of Zn, 0.1 to 1.0 wt % of Ca, 0.01 to 1.0 wt % of
Mn, a remainder of Mg, and other inevitable impurities with respect
to the entire 100 wt %; preparing a casting material by casting the
molten metal; preparing a rolled material by rolling the casting
material; and finally annealing the rolled material.
[0025] Regarding the preparing of an alloy molten metal, Al may be
0.5 to 1.3 wt % for the entire 100 wt % of the alloy molten
metal.
[0026] The preparing of a casting material by casting the molten
metal may include performing casting by a strip casting method.
[0027] The preparing of a rolled material by rolling a casting
material may include performing rolling with a reduction ratio that
is equal to or less than 50% (excluding 0%) for each rolling.
[0028] In detail, the casting material may be rolled once or at
least twice.
[0029] In further detail, the rolling may be performed at a
temperature of 100 to 350.degree. C.
[0030] The preparing of a rolled material by rolling a casting
material may further include intermediately annealing the rolled
material.
[0031] The intermediately annealing of the rolled material may be
performed at a temperature of 300 to 500.degree. C.
[0032] In detail, the intermediately annealing of the rolled
material may be performed for 30 minutes to 6 hours.
[0033] The finally annealing of the rolled material may be
performed at equal to or greater than 250.degree. C. In detail, the
finally annealing of the rolled material may be performed for 30
minutes to 6 hours.
[0034] According to the embodiment of the present invention, a
magnesium alloy sheet with less anisotropy may be manufactured,
when a bending test is performed in the rolling direction (RD) and
the transverse direction (TD), by controlling the fraction of the
secondary phase and the stringer of the secondary phase according
to the content of aluminum.
[0035] Further, a magnesium alloy sheet with excellent moldability
at room temperature may be simultaneously provided.
BRIEF DESCRIPTION OF THE DRAWINGS
[0036] FIG. 1 sequentially shows a crack forming mechanism
according to a secondary phase stringer during a tension test in a
transverse direction (TD).
[0037] FIG. 2 shows an observation of a cross-section of Example 1
with a SEM.
[0038] FIG. 3 shows an observation of a cross-section of
Comparative Example 1 with a SEM.
[0039] FIG. 4 shows an observation of a cross-section where a crack
is generated during a bending test of Comparative Example 1 with a
SEM.
[0040] FIG. 5 shows an observation of a cross-section of Example 2
with an optical microscope.
DETAILED DESCRIPTION OF THE EMBODIMENTS
[0041] The advantages and features of the present invention and the
manner of achieving them will become apparent with reference to the
embodiments described in detail below with reference to the
accompanying drawings. The present invention may, however, be
embodied in many different forms and should not be construed as
limited to the embodiments set forth herein. Rather, these
embodiments are provided so that this disclosure will be thorough
and complete, and will fully convey the scope of the invention to
those skilled in the art, and the present invention is defined by
the scope of the claims. Like reference numerals designate like
elements throughout the specification.
[0042] Thus, in some embodiments, well-known techniques are not
specifically described to avoid an undesirable interpretation of
the present invention. Unless defined otherwise, all terms
(including technical and scientific terms) used herein may be used
in a sense commonly understood by one of ordinary skill in the art
to which this invention belongs. Unless explicitly described to the
contrary, the word "comprise" and variations such as "comprises" or
"comprising" will be understood to imply the inclusion of stated
elements but not the exclusion of any other elements. Also,
singular forms include plural forms unless the context clearly
dictates otherwise.
[0043] The magnesium alloy sheet according to an embodiment of the
present invention may include 0.5 to 1.5 wt % of Al, 0.1 to 0.7 wt
% of Zn, 0.1 to 0.5 wt % of Ca, 0.01 to 0.3 wt % of Mn, a remainder
of Mg, and other inevitable impurities, for the entire 100 wt
%.
[0044] In detail, the Al may be 0.5 to 1.3 wt % for the entire 100
wt % of the magnesium alloy sheet.
[0045] A reason for limiting a component and a composition of the
magnesium alloy sheet will now be described.
[0046] Al may be included at 0.5 to 1.5 wt %. In detail, it may be
contained at 0.5 to 1.3 wt %. In further detail, aluminum functions
to improve moldability at room temperature, so it may be cast by a
strip casting method when it is contained at the above-noted
content.
[0047] In detail, regarding a method for manufacturing a magnesium
alloy sheet to be described below, a texture is changed to a strong
basal texture when performing rolling in a rolling step. In this
instance, a solute dragging effect is provided as a mechanism for
suppressing the change to the basal texture. The solute dragging
mechanism may reduce boundary mobility, when heated or deformed, as
an element such as Ca having a bigger atom radius than Mg is
segregated in a crystal boundary. Accordingly, formation of basal
texture by dynamic recrystallization or rolling deformation during
a rolling process may be suppressed.
[0048] Therefore, when more than 1.5 wt % of aluminum is added, an
amount of the secondary phase of Al.sub.2Ca also steeply increases,
so the amount of Ca segregated to the boundary may be reduced.
Accordingly, a solute dragging effect may be reduced. In addition,
as the fraction occupied by the secondary phase is reduced, the
stringer may also be reduced. The stringer will be described below
in detail.
[0049] On the contrary, when less than 0.5 wt % of aluminum is
added, casting by the strip casting method may be impossible. The
aluminum functions to improve fluidity of a molten metal, so it may
prevent a roll sticking phenomenon during casting. It is impossible
to cast a Mg--Zn-based magnesium alloy to which no aluminum is
added by using the strip casting method because of an actual roll
sticking phenomenon.
[0050] 0.1 to 0.7 wt % of Zn may be contained.
[0051] In further detail, when zinc is added together with calcium,
it activates a base slip through a non-basal softening phenomenon,
thereby functioning to improve moldability of the sheet. However,
when more than 0.7 wt % of zinc is added, it is combined to
magnesium to generate an intermetallic compound, which may exercise
an adverse effect upon the moldability.
[0052] 0.1 to 0.5 wt % of Ca may be contained.
[0053] When the calcium is included with zinc, a non-basal
softening phenomenon is generated to activate a non-basal slip,
thereby functioning to improve moldability of the sheet.
[0054] In detail, texture has the characteristic of changing to a
strong base texture during rolling in the method for manufacturing
a magnesium alloy sheet. The solute dragging effect is provided as
a mechanism for suppressing the characteristic. In detail, it may
reduce boundary mobility, when heated or deformed, as an element
having a bigger atom radius than Mg is segregated in a crystal
boundary. In this instance, Ca may be used as an element with the
bigger atom radius than Mg. In this case, formation of basal
texture by dynamic recrystallization or rolling deformation during
a rolling process may be suppressed.
[0055] However, when more than 0.5 wt % thereof is added, adhesion
with a casting roll during a casting process with strip casting
occurs, so the sticking phenomenon may increase. Therefore, the
casting property is lowered by reducing fluidity of the molten
metal, so productivity may be reduced.
[0056] 0.01 to 0.3 wt % of Mn may be contained.
[0057] The manganese forms an Fe--Mn-based compound to thus
function to reduce the content of the component of Fe in the sheet.
Therefore, when the manganese is contained, an Fe--Mn compound in a
form of dross or sludge may be formed in an alloyed molten metal
state before performing a casting process. A sheet with a less
content of the component of Fe may be produced during a casting
process. The manganese may form a secondary phase of
Al.sub.8Mn.sub.5 with aluminum. Accordingly, it functions to
increase the amount of calcium that may be segregated to the
crystal boundary by suppressing the used amount of calcium. Hence,
when manganese is added, the solute dragging effect may be further
improved.
[0058] Regarding the magnesium alloy sheet, calcium elements may be
segregated to the crystal boundary. In this instance, the calcium
elements may be segregated to the crystal boundary not in an
intermetallic compound form but in a solute form.
[0059] In detail, as the calcium does not form a secondary phase
with an element such as aluminum but is melted and segregated in a
solute form to the boundary, mobility of the boundary is reduced
and the basal texture is suppressed. Accordingly, the magnesium
alloy sheet with excellent moldability at room temperature may be
provided.
[0060] Therefore, the above-described magnesium alloy sheet
contains Al.sub.2Ca, Al.sub.8Mn.sub.5, or a secondary phase that is
a combination thereof, and an area fraction of the secondary phase
may be equal to or less than 5% of the entire area (100%) of the
magnesium alloy sheet. In detail, it may be equal to or less than
3%. In further detail, it may be equal to or less than 1%.
[0061] This is a significantly low numerical value compared to the
conventional other magnesium alloy sheets containing more than 1.5
wt % of Al against the entire weight of the magnesium alloy
sheet.
[0062] By controlling the fraction of the secondary phase to the
minimum such as the range, boundary segregation may be improved and
moldability at room temperature may be improved. In addition, the
stringer of the secondary phase generated as the fraction of the
secondary phase increases may be reduced.
[0063] In the present specification, the stringer signifies that
the secondary phases gather together to form a band in the rolling
direction (RD).
[0064] In detail, the magnesium alloy sheet may include a stringer,
and a length of the stringer may be 50 .mu.m as a maximum or less
than the same. When the length range of the stringer is 50 .mu.m as
a maximum or less than the same, this may signify that the stringer
is hardly included.
[0065] In another way, when the secondary phases gather together so
that a stringer in a band shape that is greater than the maximum
value of 50 .mu.m in the rolling direction (RD) exists, anisotropy
that is the physical property of the magnesium alloy sheet may be
large. In detail, when the magnesium alloy sheet includes a
stringer that is greater than the maximum length of 50 .mu.m in the
rolling direction thereof and the same is bent or extended in the
transverse direction (TD), the secondary phase is broken along the
stringer formed in the rolling direction (RD), and a crack may be
easily spread.
[0066] Particularly, when the above-noted secondary phase stringer
exists near a surface of the magnesium alloy sheet, the crack may
be further easily generated when a bending test is performed in the
transverse direction that is perpendicular to the rolling
direction.
[0067] The crack forming mechanism according to the stringer of the
secondary phase may be confirmed through FIG. 1.
[0068] FIG. 1 sequentially shows a crack forming mechanism
according to a secondary phase stringer during a tension test in
the transverse direction (TD).
[0069] As shown in FIG. 1, it is found that, when the sheet is
extended in the transverse direction (TD), the crack is generated
along the secondary phase stringer (white dot) formed in the
rolling direction (RD). That is, the stringer of the secondary
phase is parallel to the generated direction of the crack, so the
trend for the crack to continue along the secondary phase stringer
exists.
[0070] Therefore, when the magnesium alloy sheet including a
secondary phase stringer is extended in the transverse direction
(TD), anisotropy may be inferior to the case of being extended in
the rolling direction (RD). Therefrom, a difference of physical
properties between the case of extending (or bending) in the
rolling direction (RD) and the case of extending (or bending) in
the transverse direction (TD) may be large.
[0071] That is, in the present specification, a reference of the
secondary phase stringer giving a bad influence to bending
anisotropy is defined to be a stringer of which the maximum length
is greater than 50 .mu.m.
[0072] The transverse direction (TD) represents a direction that is
perpendicular to the rolling direction (RD).
[0073] The anisotropy signifies that the physical property in the
rolling direction (RD) is different from the physical property in
the transverse direction (TD). As will be described in a later
portion of the present specification, the anisotropy is measured by
performing a bending test in the rolling direction (RD) and the
transverse direction (TD) through a V-bending test. A limited
bending radius (LBR) value through the bending test is indicated as
an index of anisotropy.
[0074] When it is described that anisotropy is excellent, it
signifies that there is a small difference of the physical
properties in the rolling direction (RD) and the transverse
direction (TD).
[0075] Therefore, the limited bending radius (LBR) value in the
rolling direction (RD) of the magnesium alloy sheet at a
temperature that is equal to or greater than 150.degree. C. may be
0 to 0.5 R/t.
[0076] The limited bending radius (LBR) value in the transverse
direction (TD) of the magnesium alloy sheet at the temperature that
is equal to or greater than 150.degree. C. may be 0 to 0.5 R/t
[0077] The limited bending radius (LBR) signifies the ratio of a
thickness (t) of the sheet vs. an internal curvature radius (R) of
the sheet after the V-bending test. In detail, it may be the
internal curvature radius (R) of the sheet/the thickness (t) of the
sheet.
[0078] In detail, the ratio of the limited bending radius (LBR) of
the transverse direction (TD) against the rolling direction (RD) of
the magnesium alloy sheet may be 0.8 to 1.2.
[0079] The range signifies that the difference of the physical
properties between the rolling direction (RD) and the transverse
direction (TD) is not large.
[0080] The limited dome height (LDH) of the magnesium alloy sheet
may be equal to or greater than 8 mm.
[0081] The limited dome height (LDH) represents a value drawn
through an Erichsen Cupping Test at room temperature. The
moldability of the sheet may be compared from the above-noted
value.
[0082] In detail, an Erichsen value indicates a height of the
deformed sheet until a break is generated thereto when the sheet is
deformed into a cup shape. Therefore, as the deformed height of the
magnesium alloy sheet is great, the Erichsen value may be large.
Accordingly, moldability may be excellent.
[0083] Therefrom, the limited dome height of the magnesium alloy
sheet according to an exemplary embodiment of the present invention
may have a great value compared to the conventional magnesium alloy
material.
[0084] A method for manufacturing a magnesium alloy sheet according
to another exemplary embodiment of the present invention may
include: preparing an alloy molten metal including 0.5 to 1.5 wt %
of Al, 0.5 to 1.5 wt % of Zn, 0.1 to 1.0 wt % of Ca, 0.01 to 1.0 wt
% of Mn, a remainder of Mg, and other inevitable impurities for the
entire 100 wt % (S100); casting the molten metal and preparing a
casting material (S200); rolling the casting material and preparing
a rolled material (S300); and finally annealing the rolled material
(S400).
[0085] In detail, in the step S100, Al may be 0.5 to 1.0 wt % for
the entire 100 wt % of the alloy molten metal.
[0086] The reason for limiting the component and the composition of
the molten metal corresponds to the above-described reason for
limiting the component and the composition of the magnesium alloy
sheet, so it will not be described.
[0087] In the step S200, the casting method for preparing a casting
material may be die-casting, direct chill casting, billet casting,
centrifugal casting, tilt casting, die gravity casting, sand
casting, strip casting, or a combination thereof. However, the
method is not limited thereto.
[0088] In detail, the strip casting method may be used for
performing casting. The casting by the strip casting method may be
possible by the alloy molten metal of the above-described
composition.
[0089] In detail, the molten metal may be cast at a rate of 0.5 to
10 mpm.
[0090] A thickness of the produced casting material may be 3 to 13
mm, and it is not limited thereto.
[0091] In the step S300, rolling may be performed with a reduction
ratio that is equal to or less than 50% (excluding 0%) for each
rolling. In detail, a crack may be generated during rolling when
the reduction ratio is greater than 50% for each rolling.
[0092] The reduction ratio represents an operation of dividing a
difference between a thickness of a material before passing through
a rolling roll during rolling and a thickness of the material after
passing through the rolling roll by the thickness of the material
before passing through the rolling roll, and then multiplying a
resultant value by 100.
[0093] In detail, the casting material may be rolled once or at
least twice. In further detail, when the casting material is thick,
it may be rolled at least twice.
[0094] In further detail, it may be rolled at a temperature of 100
to 350.degree. C. In further detail, when the rolling temperature
is less than 100.degree. C., cracks may be generated during
rolling. When the roll temperature is greater than 350.degree. C.,
segregation of Ca may be deteriorated, which may be
disadvantageous.
[0095] The step S300 may further include intermediately annealing a
rolled material (S310).
[0096] In detail, when the rolling is performed at least twice,
intermediate annealing may be performed in the middle of the
rolling step. The step S310 may be performed at a temperature of
300 to 500.degree. C. In detail, it may be performed for 30 minutes
to 6 hours.
[0097] In detail, when the intermediate annealing is performed
under the condition, a stress generated during the rolling may be
sufficiently settled. In further detail, the stress may be settled
through recrystallization in a range not exceeding the fusion
temperature of the rolled material. In addition, formation of
grains with a non-basal crystallographic orientation may be induced
through the recrystallization.
[0098] Finally, a step S400 for finally annealing the rolled
material may be performed at equal to or greater than 250.degree.
C. In detail, it may be performed at the temperature of 250 to
450.degree. C.
[0099] In further detail, it may be performed for 30 minutes to 6
hours.
[0100] The recrystallization may be easily formed by the final
annealing under the above-noted condition.
[0101] An example will be provided for detailed description. The
example given below exemplifies the present invention, and the
present invention is not limited to the example.
PREPARATION EXAMPLE
[0102] A magnesium alloy sheet is produced according to an
exemplary embodiment and a comparative example with a component and
a composition expressed in Table 1 below.
[0103] In detail, an alloy molten metal including the component and
the composition disclosed in Table 1 is prepared. The molten metal
is cast by the strip casting method to prepare a casting material.
The casting material is rolled 7 to 10 times with a reduction ratio
of 25% for each rolling at 200.degree. C.
[0104] Intermediate annealing is performed in the middle of the
rolling. In detail, it is performed for 3 hours at 400.degree.
C.
[0105] Finally, the rolled sheet is annealed at 300.degree. C.
[0106] Estimation on the above-produced tensile strength (YS),
elongation (El), limited dome height (LDH), and limited bending
radius (LBR) according to an exemplary embodiment and a comparative
example is shown in Table 1.
[0107] In this instance, a method for estimating physical
properties is as follows.
[Tensile Strength Measuring Method]
[0108] The tensile strength signifies a value found by dividing a
maximum tensile load until a test piece is broken by a
cross-section of a test piece before a test is performed. In
detail, it is measured by using a uniaxial tensile tester at room
temperature, and a strain rate is given as 10.sup.-3s.
[Elongation Measuring Method]
[0109] The elongation represents a ratio for a material to increase
during a tensile test, and it signifies a value shown by a
percentage of a changed length of a test piece against a length of
the test piece before a test is performed. In detail, it is
equivalent to a tensile strength measuring condition, and an
increased length against an initial length of a gauge part.
[Erichsen Value Measuring Method]
[0110] A magnesium alloy sheet with a horizontal length and a
vertical length of respectively 50 to 60 mm is used, and a
lubricant is used on an exterior side of the sheet so as to reduce
friction between the sheet and a spherical punch.
[0111] In this instance, when the test is performed, the die and
the spherical punch are at room temperature.
[0112] In detail, the magnesium alloy sheet is inserted between an
upper die and a lower die, an exterior circumference portion of the
sheet is fixed with a force of 10 kN, and the sheet is deformed at
a speed of 5 mm/min by using a spherical punch with the diameter of
20 mm. The punch is inserted until the sheet is broken, and when it
is broken, a deformed height of the sheet is measured.
[0113] The above-noted deformed height of the sheet is referred to
as an Erichsen value or a limited dome height (LDH).
[Limited Bending Radium (V-Bending) Measuring Method]
[0114] A result according to a V-bending test is referred to as a
limited bending radius (LBR).
[0115] In detail, regarding the test, the temperature is controlled
until it reaches a target temperature by installing a hot wire so
as to heat the device including a die and a punch. The die and the
punch may respectively have an angle of 90.degree.. Regarding the
types of the punch, curvature radii are 0R to 9R.
[0116] After the sheet is bent by using the device, R of the punch
that is bent without cracks is determined. In this instance, the
bending speed of the punch is measured to be 30 to 60 mm per
second.
[0117] A mechanical 60 ton servo press is used for the device, and
a V-bending mold including a punch and a die is installed in the
press and is then used.
TABLE-US-00001 TABLE 1 YS El. LDH (MPa) (%) (mm) Limited bending
radius (R/t) Al Zn Mn Ca Room RT (room Classify wt % temperature
temperature) 150.degree. C. 200.degree. C. 250.degree. C. Example 1
1 0.85 0.2 0.67 RD 147 22.5 8.6 2.9 0.4 0.4 0.0 TD 92 18.7 2.9 0.4
0.4 0.0 Example 2 1.03 0.45 0.12 0.19 RD 157 26.0 8.2 2.1 0.3 0.0
0.0 TD 126 26.1 2.1 0.3 0.0 0.0 Comparative 2 0.92 0.3 0.63 RD 169
25.0 8.6 2.3 1.2 0.4 0 Example 1 TD 142 21.0 3.1 2.8 1.5 0.9
Comparative 3 0.8 0.3 0.62 RD 151 27.3 8.0 2.1 1.4 0.7 0.4 Example
2 TD 144 15.4 4.3 3.2 2.9 2.9 Comparative 3 0.74 0.3 -- RD 177 28.5
3.8 8 2.3 1.8 1.4 Example 3 TD 209 24.3 8 3.6 2.3 1.8 Comparative
ZEK100 1.0 RD 223 20.4 8.1 4.1 1.5 0.9 Example 4 TD 140 25.6 4.1
1.5 0.9
[0118] As expressed in Table 1, it is found that the limited dome
height (LDH) value with 2 wt % of an aluminum content according to
a comparative example 1 is excellent, but the limited bending
radius (LBR) value is bad.
[0119] Particularly, regarding Comparative Example 1, the ratio of
the limited bending radius (LBR) value in the transverse direction
(TD) against the limited bending radius (LBR) value in the rolling
direction (RD) is 3.75 at 200.degree. C., so it is found that
anisotropy is large when respectively extended in the rolling
direction and the transverse direction.
[0120] Further, it is found that anisotropy according to
Comparative Example 4 is excellent compared to Comparative Examples
1 to 3, but the limited bending radius (LBR) value is bad compared
to Examples 1 and 2.
[0121] This may be found according to the drawings of the present
invention.
[0122] FIG. 2 shows an observation of a cross-section of Example 1
with a SEM.
[0123] As shown in FIG. 2, it is found from the user's eye that
Example 1 includes no secondary phase stringer. Accordingly, it may
be determined from Example 1 that the difference of the physical
properties is not large when extended in the rolling direction (RD)
and in the transverse direction (TD).
[0124] FIG. 3 shows an observation of a cross-section of
Comparative Example 1 with a SEM.
[0125] As shown in FIG. 3, it is found that Comparative Example 1
includes a band-shaped stringer in the rolling direction formed
when the secondary phase is gathered together on the surface of the
sheet and a portion below the surface. The length of the stringer
is found to be equal to or greater than at least 100 .mu.m.
[0126] Therefore, the reason that the anisotropy in the transverse
direction and in the rolling direction according to a comparative
example 1 is large may be determined.
[0127] In detail, the generation of a crack during the bending test
according to Comparative Example 1 may be found from FIG. 4.
[0128] FIG. 4 shows an observation of a cross-section where a crack
is generated during a bending test of Comparative Example 1 with a
SEM. In detail, as shown in FIG. 4, the stringer is found on the
surface and the portion below the surface in Comparative Example 1.
As a result, it is found that cracks are easily generated in the
surface.
[0129] FIG. 5 shows an observation of a cross-section of Example 2
with an optical microscope.
[0130] As shown in FIG. 5, it is found that Example 2 includes a
secondary phase (black dots). However, it is found from the user's
eye that the fraction of the secondary phase against the magnesium
alloy sheet is very small.
[0131] Therefrom, the magnesium alloy sheet that does not have
large anisotropy when a bending test is performed in the rolling
direction (RD) and the transverse direction (TD) may be produced by
controlling the fraction of the secondary phase and the secondary
phase stringer according to the content of aluminum according to
the example of the present invention.
[0132] In addition, the magnesium alloy sheet with excellent
moldability at room temperature may be simultaneously provided.
[0133] While this invention has been described in connection with
what is presently considered to be practical exemplary embodiments,
it is to be understood that the invention is not limited to the
disclosed embodiments, but, on the contrary, is intended to cover
various modifications and equivalent arrangements included within
the spirit and scope of the appended claims.
[0134] The range of the present invention is provided in the claims
to be described rather than the above-described detailed
description, and all modifications or modified forms drawn from the
meanings, range, and equivalent concepts of the claims of the
patent are to be interpreted to be included in the range of the
present invention.
* * * * *