U.S. patent application number 16/596102 was filed with the patent office on 2020-11-12 for austenitic light weight steel.
The applicant listed for this patent is Hyundai Motor Company, Kia Motors Corporation. Invention is credited to Joong Kil Choe, Bong Lae Jo, Dong Hwi Kim.
Application Number | 20200354805 16/596102 |
Document ID | / |
Family ID | 1000004397800 |
Filed Date | 2020-11-12 |


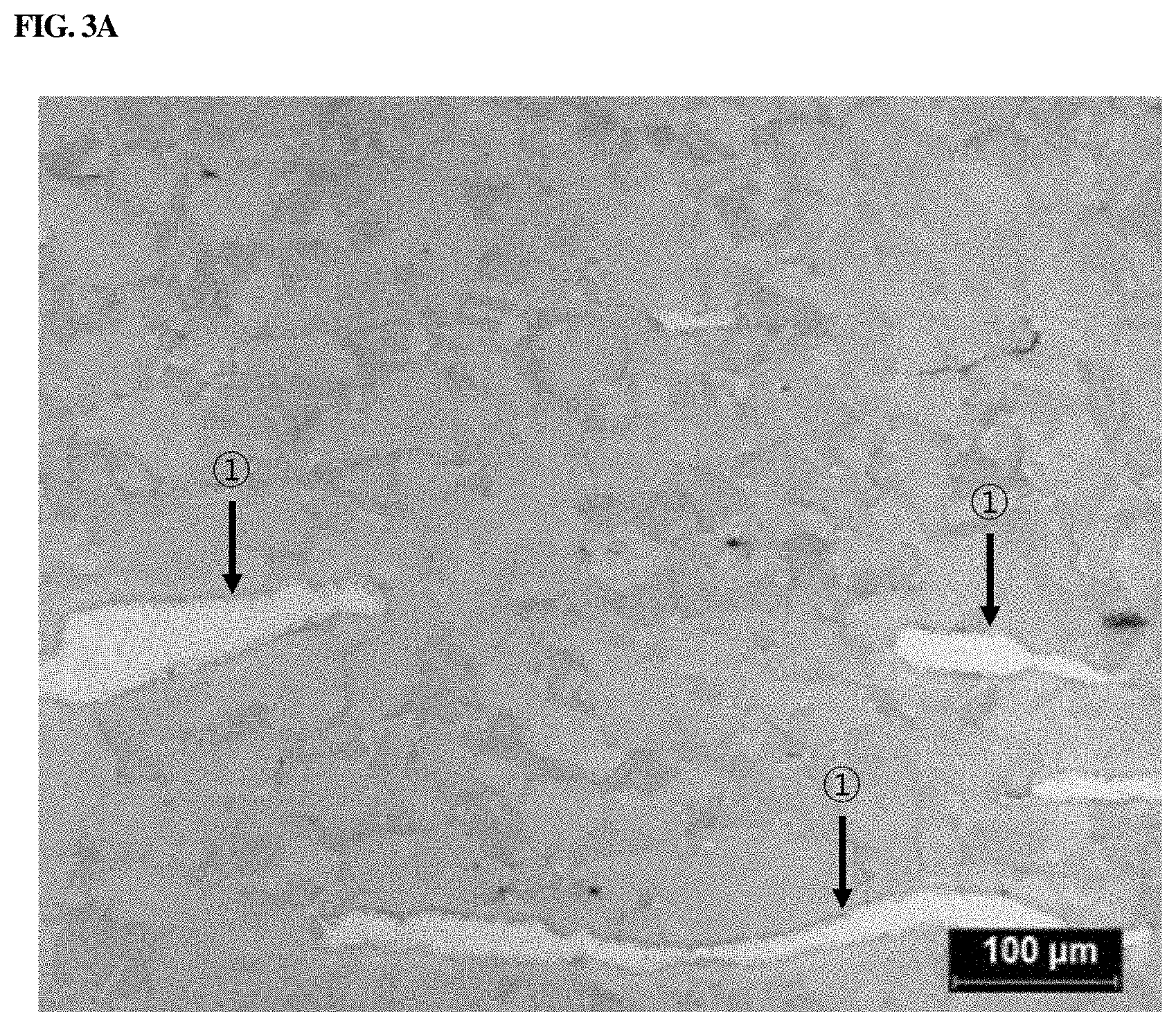


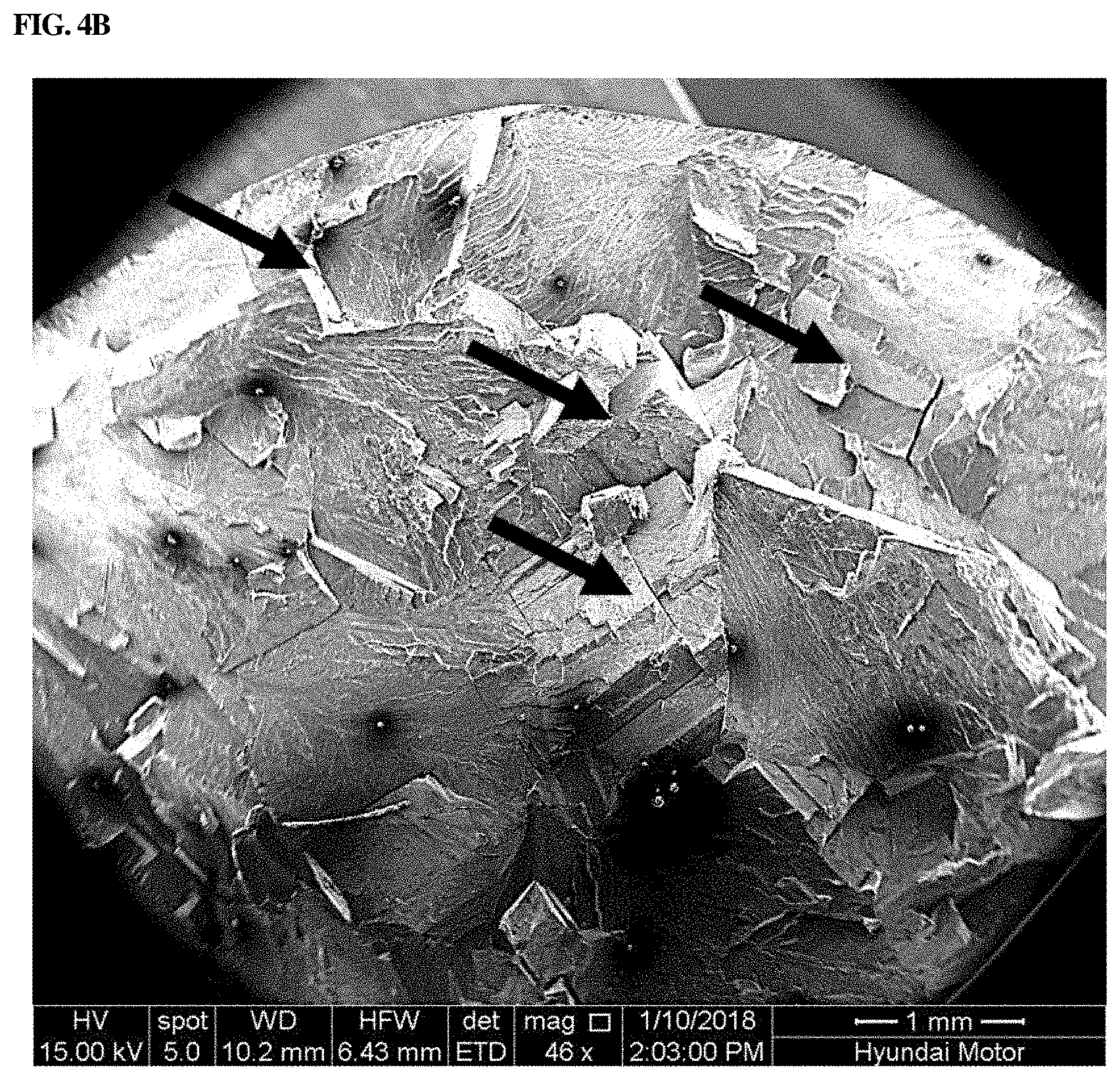

United States Patent
Application |
20200354805 |
Kind Code |
A1 |
Kim; Dong Hwi ; et
al. |
November 12, 2020 |
AUSTENITIC LIGHT WEIGHT STEEL
Abstract
Disclosed is an austenitic light weight steel which may have
decreased specific gravity while maintaining excellent strength and
ductility. The austenitic light weight steel may include carbon (C)
in an amount of about 0.8 to 1.3 weight %, aluminum (Al) in an
amount of about 9.0 to 15.0 weight %, manganese (Mn) in an amount
of about 10.0 to 20.0 weight %, nickel (Ni) in an amount of about
0.25 weight % or less (excluding 0 weight %), chromium (Cr) in an
amount of about 0.5 weight % or less (excluding 0 weight %),
silicon (Si) in an amount of about 0.5 weight % or less (excluding
0 weight %), a sum of titanium (Ti) and vanadium (V) in an amount
of about 1.0 weight % or less (excluding 0 weight %), other
unavoidable impurities, and iron (Fe) constituting the remaining
balance, based on the total weight of the light weight steel.
Inventors: |
Kim; Dong Hwi; (Yongin,
KR) ; Jo; Bong Lae; (Yongin, KR) ; Choe; Joong
Kil; (Suwon, KR) |
|
Applicant: |
Name |
City |
State |
Country |
Type |
Hyundai Motor Company
Kia Motors Corporation |
Seoul
Seoul |
|
KR
KR |
|
|
Family ID: |
1000004397800 |
Appl. No.: |
16/596102 |
Filed: |
October 8, 2019 |
Current U.S.
Class: |
1/1 |
Current CPC
Class: |
C21D 6/005 20130101;
C22C 38/46 20130101; C21D 2211/004 20130101; C22C 38/06 20130101;
C21D 6/008 20130101; C21D 2211/005 20130101; C22C 38/58 20130101;
C21D 9/46 20130101; C22C 38/50 20130101; C21D 6/004 20130101; C22C
38/02 20130101; C21D 2211/001 20130101; C21D 8/0205 20130101 |
International
Class: |
C21D 9/46 20060101
C21D009/46; C22C 38/58 20060101 C22C038/58; C22C 38/50 20060101
C22C038/50; C22C 38/46 20060101 C22C038/46; C22C 38/06 20060101
C22C038/06; C22C 38/02 20060101 C22C038/02; C21D 8/02 20060101
C21D008/02; C21D 6/00 20060101 C21D006/00 |
Foreign Application Data
Date |
Code |
Application Number |
May 7, 2019 |
KR |
10-2019-0052788 |
Claims
1. An austenitic light weight steel comprising: carbon (C) in an
amount of about 0.8 to 1.3 weight %, aluminum (Al) in an amount of
about 9.0 to 15.0 weight %, manganese (Mn) in an amount of about
10.0 to 20.0 weight %, nickel (Ni) in an amount of about 0.25
weight % or less (excluding 0 weight %), chromium (Cr) in an amount
of about 0.5 weight % or less (excluding 0 weight %), silicon (Si)
in an amount of about 0.5 weight % or less (excluding 0 weight %),
a sum of titanium (Ti) and vanadium (V) in an amount of about 1.0
weight % or less (excluding 0 weight %), other unavoidable
impurities, and iron (Fe) constituting the remaining balance, all
the weight % based on the total weight of the light weight
steel.
2. The austenitic light weight steel of claim 1, further
comprising: niobium (Nb) in an amount of about 0.03 weight % or
less, phosphorus (P) in an amount of about 0.1 weight % or less,
sulfur (S) in an amount of about 0.05 weight % or less, nitrogen
(N) in an amount of about 0.01 weight % or less, or a combination
thereof, based on the total weight of the light weight steel.
3. The austenitic light weight steel of claim 1, wherein the
austenitic light weight steel has a yield strength of about 600 MPa
or greater.
4. The austenitic light weight steel of claim 1, wherein the
austenitic light weight steel has a tensile strength of about 1000
MPa or greater.
5. The austenitic light weight steel of claim 1, wherein the
austenitic light weight steel has an elongation of about 20% or
greater.
6. The austenitic light weight steel of claim 1, wherein the
austenitic light weight steel has a density of about 6.85
g/cm.sup.3 or less.
7. The austenitic light weight steel of claim 1, wherein in the
austenitic light weight steel, a matrix is an austenite, and a
ferrite is formed at a fraction of about 15% or less.
8. The austenitic light weight steel of claim 7, wherein in the
austenitic light weight steel, a .kappa.-carbide is formed at a
fraction of about 10% or less.
9. The austenitic light weight steel of claim 7, wherein in the
austenitic light weight steel, a Fe--Al intermetallic compound is
formed at a fraction of about 2% or less.
10. The austenitic light weight steel of claim 1, wherein a grain
of the austenitic light weight steel is formed to have a length of
about 40 .mu.m or less in a rolling direction.
11. The austenitic light weight steel of claim 1, wherein in the
austenitic light weight steel, .beta.-Mn is not formed.
12. The austenitic light weight steel of claim 1, consisting
essentially of: carbon (C) in an amount of about 0.8 to 1.3 weight
%, aluminum (Al) in an amount of about 9.0 to 15.0 weight %,
manganese (Mn) in an amount of about 10.0 to 20.0 weight %, nickel
(Ni) in an amount of about 0.25 weight % or less (excluding 0
weight %), chromium (Cr) in an amount of about 0.5 weight % or less
(excluding 0 weight %), silicon (Si) in an amount of about 0.5
weight % or less (excluding 0 weight %), a sum of titanium (Ti) and
vanadium (V) in an amount of about 1.0 weight % or less (excluding
0 weight %), other unavoidable impurities, and iron (Fe)
constituting the remaining balance, all the weight % based on the
total weight of the light weight steel.
13. The austenitic light weight steel of claim 1, consisting
essentially of: carbon (C) in an amount of about 0.8 to 1.3 weight
%, aluminum (Al) in an amount of about 9.0 to 15.0 weight %,
manganese (Mn) in an amount of about 10.0 to 20.0 weight %, nickel
(Ni) in an amount of about 0.25 weight % or less (excluding 0
weight %), chromium (Cr) in an amount of about 0.5 weight % or less
(excluding 0 weight %), silicon (Si) in an amount of about 0.5
weight % or less (excluding 0 weight %), a sum of titanium (Ti) and
vanadium (V) in an amount of about 1.0 weight % or less (excluding
0 weight %), one or more selected from the group consisting of
niobium (Nb) in an amount of about 0.03 weight % or less,
phosphorus (P) in an amount of about 0.1 weight % or less, sulfur
(S) in an amount of about 0.05 weight % or less, nitrogen (N) in an
amount of about 0.01 weight % or less, other unavoidable
impurities, and iron (Fe) constituting the remaining balance, all
the weight % based on the total weight of the light weight
steel.
14. A vehicle part comprising an austenitic light weight steel of
claim 1.
15. A vehicle comprising an austenitic light weight steel of claim
1.
Description
CROSS REFERENCE TO RELATED APPLICATION
[0001] The present application claims priority to Korean Patent
Application No. 10-2019-0052788, filed May 7, 2019, the entire
contents of which is incorporated herein for all purposes by this
reference.
TECHNICAL FIELD
[0002] The present invention relates to an austenitic light weight
steel, which may have decreased specific gravity while maintaining
excellent strength and ductility by adjusting an alloy component
and the content thereof.
BACKGROUND
[0003] In order to improve fuel efficiency of an automobile,
research on weight reduction of materials has been continuously
conducted. In particular, research on weight reduction of parts
made of steel materials which constitute most of vehicle parts has
been continuously conducted.
[0004] A light weight steel proposed for weight reduction of steel
materials includes, for example, a ferritic lightweight steel, an
austenitic light weight steel, and a light weight steel having dual
phase structure (duplex) of ferrite-austenite. These light weight
steels have high specific strength due to a large amount of Al in
steel materials, and thus has been prominent as high-tech
structural materials such as automobile parts.
[0005] Meanwhile, an austenitic light weight steel has excellent
mechanical properties such as strength and ductility, and weight
reduction effect. However, an austenitic light weight steel had a
problem in that a rupture phenomenon easily occurs at an edge
portion during molding such as rolling and forging, and thus it was
difficult to be applied in mass production.
[0006] The contents described as the related art have been provided
only for assisting in the understanding for the background of the
present invention and should not be considered as corresponding to
the related art known to those skilled in the art.
SUMMARY
[0007] In preferred aspects, provided is an austenitic light weight
steel, which may have reduced specific gravity as maintaining
excellent strength and ductility by adjusting an alloy component
and the content thereof. Preferably, the austenitic light weight
steel may be used in vehicle parts to which various molding methods
are applied.
[0008] In one aspect, provided is an austenitic light weight steel
that may include: carbon (C) in an amount of about 0.8 to 1.3
weight %, aluminum (Al) in an amount of about 9.0 to 15.0 weight %,
manganese (Mn) in an amount of about 10.0 to 20.0 weight %, nickel
(Ni) in an amount of about 0.25 weight % or less (excluding 0
weight %), chromium (Cr) in an amount of about 0.5 weight % or less
(excluding 0 weight %), silicon (Si) in an amount of about 0.5
weight % or less (excluding 0 weight %), a sum of titanium (Ti) and
vanadium (V) in an amount of about 1.0 weight % or less (excluding
0 weight %), other unavoidable impurities, and iron (Fe)
constituting the remaining balance. All the weight % are based on
the total weight of the light weight steel.
[0009] The austenitic light weight steel may further include
niobium (Nb) in an amount of about 0.03 weight % or less,
phosphorus (P) in an amount of about 0.1 weight % or less, sulfur
(S) in an amount of about 0.05 weight % or less, nitrogen (N) in an
amount of about 0.01 weight % or less, or a combination thereof,
based on the total weight of the light weight steel.
[0010] Further provided is the austenitic light weight steel
consisting of, consisting essentially of, or essentially consisting
of the components as described above. For instance, the austenitic
light weight steel may consist of, consist essentially of, or
essentially consist of: carbon (C) in an amount of about 0.8 to 1.3
weight %, aluminum (Al) in an amount of about 9.0 to 15.0 weight %,
manganese (Mn) in an amount of about 10.0 to 20.0 weight %, nickel
(Ni) in an amount of about 0.25 weight % or less (excluding 0
weight %), chromium (Cr) in an amount of about 0.5 weight % or less
(excluding 0 weight %), silicon (Si) in an amount of about 0.5
weight % or less (excluding 0 weight %), a sum of titanium (Ti) and
vanadium (V) in an amount of about 1.0 weight % or less (excluding
0 weight %), other unavoidable impurities, and iron (Fe)
constituting the remaining balance. In addition, the austenitic
light weight steel may consist of, consist essentially of, or
essentially consist of: carbon (C) in an amount of about 0.8 to 1.3
weight %, aluminum (Al) in an amount of about 9.0 to 15.0 weight %,
manganese (Mn) in an amount of about 10.0 to 20.0 weight %, nickel
(Ni) in an amount of about 0.25 weight % or less (excluding 0
weight %), chromium (Cr) in an amount of about 0.5 weight % or less
(excluding 0 weight %), silicon (Si) in an amount of about 0.5
weight % or less (excluding 0 weight %), a sum of titanium (Ti) and
vanadium (V) in an amount of about 1.0 weight % or less (excluding
0 weight %), other unavoidable impurities, and one or more selected
from the group consisting of niobium (Nb) in an amount of about
0.03 weight % or less, phosphorus (P) in an amount of about 0.1
weight % or less, sulfur (S) in an amount of about 0.05 weight % or
less, nitrogen (N) in an amount of about 0.01 weight % or less, and
iron (Fe) constituting the remaining balance.
[0011] The austenitic light weight steel may suitably have a yield
strength of about 600 MPa or greater.
[0012] The austenitic light weight steel may suitably have a
tensile strength of about 1000 MPa or greater.
[0013] The austenitic light weight steel may suitably have an
elongation of about 20% or greater.
[0014] The austenitic light weight steel may suitably have a
density of about 6.85g/cm.sup.3 or less.
[0015] In the austenitic light weight steel, a matrix may be
austenite, and a ferrite may suitably be formed at a fraction of
about 15% or less.
[0016] In the austenitic light weight steel, a .kappa.-carbide may
suitably be formed at a fraction of about 10% or less.
[0017] In the austenitic light weight steel, a Fe--Al intermetallic
compound may be formed at a fraction of about 2% or less.
[0018] A grain of the austenitic light weight steel may be formed
to suitably have a length of about 40 .mu.m of less in a rolling
direction.
[0019] In the austenitic light weight steel, .beta.-Mn may not be
formed. In other words, the austenitic light weight steel does not
include .beta.-Mn.
[0020] In another aspect, provided is a vehicle part including the
austenitic light weight steel as described herein. Also provided is
a vehicle including a vehicle part as described herein.
[0021] Other aspects of the invention are discussed infra.
BRIEF DESCRIPTION OF THE DRAWINGS
[0022] FIG. 1 is a table illustrating components of Example and
Comparative Example.
[0023] FIG. 2 is a table illustrating physical properties and
performances of Example and Comparative Example.
[0024] FIGS. 3A and 3B are photographs of a microstructure of an
austenitic light weight steel in Example according to an exemplary
embodiments of the present invention.
[0025] FIGS. 4A and 4B are enlarged photographs of an austenitic
light weight steel according to Example and Comparative
Example.
[0026] FIG. 5 is a graph for explaining the relationship of
stress-elongation for the specimens according to Example and
Comparative Example.
DETAILED DESCRIPTION OF THE EMBODIMENTS
[0027] Hereinafter, an austenitic light weight steel according to
embodiments of the present invention is described with reference to
the accompanying drawings.
[0028] The terminology used herein is for the purpose of describing
particular exemplary embodiments only and is not intended to be
limiting of the invention. As used herein, the singular forms "a",
"an" and "the" are intended to include the plural forms as well,
unless the context clearly indicates otherwise. It will be further
understood that the terms "comprises" and/or "comprising," when
used in this specification, specify the presence of stated
features, integers, steps, operations, elements, and/or components,
but do not preclude the presence or addition of one or more other
features, integers, steps, operations, elements, components, and/or
groups thereof. As used herein, the term "and/or" includes any and
all combinations of one or more of the associated listed items.
[0029] Unless specifically stated or obvious from context, as used
herein, the term "about" is understood as within a range of normal
tolerance in the art, for example within 2 standard deviations of
the mean. "About" can be understood as within 10%, 9%, 8%, 7%, 6%,
5%, 4%, 3%, 2%, 1%, 0.5%, 0.1%, 0.05%, or 0.01% of the stated
value. Unless otherwise clear from the context, all numerical
values provided herein are modified by the term "about."
[0030] It is understood that the term "vehicle" or "vehicular" or
other similar term as used herein is inclusive of motor vehicles in
general such as passenger automobiles including sports utility
vehicles (SUV), buses, trucks, various commercial vehicles,
watercraft including a variety of boats and ships, aircraft, and
the like, and includes hybrid vehicles, electric vehicles, plug-in
hybrid electric vehicles, hydrogen-powered vehicles and other
alternative fuel vehicles (e.g. fuels derived from resources other
than petroleum). As referred to herein, a hybrid vehicle is a
vehicle that has two or more sources of power, for example both
gasoline-powered and electric-powered vehicles.
[0031] FIG. 1 is a table illustrating the components of Example and
Comparative Example and FIG. 2 is a table illustrating physical
properties and performances of Example and Comparative Example.
[0032] The austenitic light weight steel according to an embodiment
of the present invention may be is obtained by controlling the
proportion of a ferrite structure. In particular, the amount of
a.kappa.-carbide and a Fe--Al intermetallic compound may be formed
in an austenitic matrix by optimizing the content of the main alloy
component. The austenitic light weight steel may suitably include
carbon (C) in an amount of about 0.8 to 1.3 weight %, aluminum (Al)
in an amount of about 9.0 to 15.0 weight %, manganese (Mn) in an
amount of about 10.0 to 20.0 weight %, nickel (Ni) in an amount of
about 0.25 weight % or less (excluding 0 weight %), chromium (Cr)
in an amount of about 0.5 weight % or less (excluding 0 weight %),
silicon (Si) in an amount of about 0.5 weight % or less (excluding
0 weight %), a sum of titanium (Ti) and vanadium (V) in an amount
of about 1.0 weight % or less (excluding 0 weight %), other
unavoidable impurities, and iron (Fe) constituting the remaining
balance. All the weight % are based on the total weight of the
light weight steel.
[0033] In the present invention, the reasons for limiting the alloy
components and the composition ranges thereof are as follows.
Hereinafter, weight %, wt %, or % by weight expressed as units of
composition range means by weight and a fraction means a volume
fraction, unless otherwise stated.
[0034] It is preferable that the austenitic light weight steel may
include an amount of about 0.8 to 1.3 weight % of carbon (C) based
on the total weight of the steel. Carbon (C) as used herein may be
an element effective for stabilizing austenite as a matrix, and for
improving strength. Depending on the content of carbon (C), the
fraction and strength of the constituent composition may be varied.
However, it is preferable to add 0.8 weight % or greater of carbon
(C) in order to stably maintain an austenite fraction of 85% or
more regardless of the contents of Mn and Al. However, when carbon
(C) is added in an amount is greater than about 1.3 weight %, a
.kappa.-carbide is formed at a fraction greater than about 10% in
the range of annealing temperature of about 900 to 1250.degree. C.,
and thus the brittleness of the material may be increased and the
effect of controlling the physical properties by aging may be
deteriorated.
[0035] It is preferable that the austenitic light weight steel may
include an amount of about 9.0 to 15.0 weight % of aluminum (Al)
based on the total weight of the steel. Aluminum (Al) as used
herein may be a ferrite-stabilizing element and is an element which
may effectively reduce the specific gravity of materials during
alloying. It is preferable to add 9 weight % or greater of aluminum
(Al) in order to stably form the ferrite of up to a fraction of
about 15% in the temperature range of about 900 to 1250.degree. C.,
which is a general annealing temperature range, while obtaining a
weight reduction effect. However, when the content of aluminum (Al)
is greater than about 15 weight %, a large amount of the ferrite, a
Fe--Al intermetallic compound and a .kappa.-carbide may be formed
in the annealing temperature range of about 900 to 1250.degree. C.
regardless of the contents of C and Mn. Thus, the target structure
and physical properties of the present invention are not
implemented.
[0036] The austenitic light weight steel may include an amount of
about 10.0 to 20.0 weight % of manganese (Mn) based on the total
weight of the steel. Manganese (Mn) as used herein may be an
austenite-stabilizing element. When the content of manganese (Mn)
is less than about 10 weight %, it is difficult to stably obtain
austenite in a fraction of about 85% or greater in the temperature
range of about 900 to 1250.degree. C., which is general annealing
temperature range. In addition, when the content of manganese (Mn)
is greater than about 20 weight %, .beta.-Mn may be partially
formed depending on a cooling condition, thereby increasing
brittleness of the materials. Thus, the maximum content of
manganese (Mn) may be preferably limited to prevent .beta.-Mn from
being formed.
[0037] The austenitic light weight steel may include nickel (Ni) in
an amount of about 0.25 weight % or less (excluding 0 weight %)
based on the total weight of the steel. Nickel (Ni) as used herein
may be an austenite-stabilizing element, and an excessive Fe--Al
intermetallic compound may be formed when nickel is added in large
amounts, thereby deteriorating the aging effect, such that the
maximum content thereof may be preferably limited to about 0.25
weight %.
[0038] The austenitic light weight steel may include an amount of
about 0.5 weight % or less (excluding 0 weight %) of chromium (Cr)
and silicon (Si), based on the total weight of the steel,
respectively. Chromium (Cr) and silicon (Si) as used herein may be
ferrite-stabilizing elements, respectively, but they may cause
brittleness when they are added in large amounts, such that the
maximum contents of chromium (Cr) and silicon (Si) may be
preferably limited to about 0.5 weight %, respectively.
[0039] The austenitic light weight steel may include the sum of the
contents of titanium (Ti) and vanadium (V) in an amount of about
1.0 weight % or less (excluding 0 weight %) based on the total
weight of the steel. Titanium (Ti) and vanadium (V) as used herein
may be elements which preferentially form the fine carbide at a
high temperature by a single addition or a combined addition to
improve the strength. However, when titanium (Ti) and vanadium (V)
are added greater than the predetermined amount (e.g., 1.0 weight
%), a carbide may be formed at a high temperature to inhibit a
formation of the .kappa.-carbide. It is preferable that a maximum
value for the sum of the contents of titanium (Ti) and vanadium (V)
may be limited to 1 weight %.
[0040] Meanwhile, the austenitic light weight steel may further
include niobium (Nb) in an amount of about 0.03 weight % or less,
phosphorus (P) in an amount of about 0.1 weight % or less, sulfur
(S) in an amount of about 0.05 weight % or less, nitrogen (N) in an
amount of about 0.01 weight % or less, or a combination thereof,
based on the total weight of the steel.
[0041] The content of niobium (Nb) may suitably be limited to about
0.03 weight % in order to maximize the effect of Ti and V.
[0042] The contents of phosphorus (P) and sulfur (S) may suitably
be controlled as low as possible because they may be impurities.
Considering the removal process of phosphorus (P) and sulfur (S),
the content of phosphorus (P) may be limited to an amount of about
0.1 weight % and the content of sulfur (S) may be limited to about
0.05 weight %, based on the total weight of the steel.
[0043] The content of nitrogen (N) may suitably be controlled as
low as possible in order to inhibit nitride formation with nitrogen
and Ti, V, Al, or the like. Considering the removal process, the
content of nitrogen (N) may be limited to an amount of about 0.01
weight % based on the total weight of the steel.
[0044] Meanwhile, the balance other than components as described
above is Fe and unavoidable impurities.
EXAMPLE
[0045] Hereinafter, the present invention will be described with
reference to Examples and Comparative Examples.
[0046] Experiments were conducted to produce a steel bar according
to the Examples and the Comparative Examples depending on
production conditions of commercially produced steel bar. A bloom
was sequentially subjected to rough hot rolling, primary hot
rolling, primary annealing, secondary hot rolling, secondary
annealing, and cold rolling to produce a steel bar, wherein the
bloom was produced through the steel bar produced by changing the
content of each component as shown in FIG. 1. Here, the Examples
and the Comparative Examples are not limited to those produced in
the form of a steel bar, and may also be applied to coiled or
square steel products. In addition, Nb, P, S and N, which are alloy
elements not described in FIG. 1, were adjusted so that their
contents are minimized. The upper limit was adjusted so as not to
exceed the upper limit defined in the present invention.
[0047] A bloom was reheated in a temperature range of 900 to
1250.degree. C. at a ratio of 2 minutes/1 mm thickness for rough
hot rolling. The bloom may be subjected to primary annealing by
reheating performed at this time. The temperature range of
reheating at which the primary annealing is performed was set to
900 to 1250.degree. C. to prevent the occurrence of defects such as
rupture by inhibiting the precipitation of the .kappa.-carbide and
the Fe--Al intermetallic compound and securing workability in the
subsequent hot rolling process.
[0048] The reheated bloom was manufactured into a billet by rolling
to a pressure ratio of 3.5 or greater at a temperature of
900.degree. C. or greater.
[0049] The rolled billet was manufactured into a form of a steel
bar by primary hot rolling at a temperature range of 900 to
1200.degree. C. Subsequently, the primary hot rolled steel bar was
subjected to water-cooling or oil-cooling in order to inhibit the
formation of the .kappa.-carbide. Here, the primary hot rolled
steel bar may be subjected to primary intermediate annealing at a
temperature range of 500 to 850.degree. C. for precipitation of the
.kappa.-carbide. The primary intermediate annealed steel bar was
subjected to water-cooling or oil-cooling in order to inhibit
further formation of the .kappa.-carbide.
[0050] The cooled steel bar was manufactured into a form of a steel
bar by secondary hot rolling at a temperature range of 800 to
1200.degree. C. Subsequently, the secondary hot rolled steel bar
was subjected to water-cooling or oil-cooling in order to inhibit
the formation of the .kappa.-carbide. The secondary hot rolled
steel bar may be subjected to secondary intermediate annealing at a
temperature range of 650 to 850.degree. C. for precipitation of the
.kappa.-carbide. The secondary intermediate annealed steel bar was
subjected to water-cooling or oil-cooling in order to inhibit
further formation of the .kappa.-carbide.
[0051] The cooled steel bar may be subjected to cool rolling for
final size correction. In addition, the cool rolled materials may
be subjected to a normalizing treatment or a quenching and
tempering treatment for final control of carbides.
[0052] Next, test methods for identifying physical properties of
the steel bar according to the Examples and Comparative Examples
manufactured as described above will be described.
[0053] The tests were performed to measure yield strength, tensile
strength, elongation, fraction of ferrite, fraction of the
.kappa.-carbide, fraction of Fe--Al intermetallic compound, and
density of the specimens according to the respective Examples and
Comparative Examples. The results are shown in FIG. 2.
[0054] Here, the specimens according to the respective Examples and
Comparative Examples were processed in accordance with the steel
bar standard specimen specification of ASTM E 8 at the 1/2R
position of the steel bar rolled with .phi.35.
[0055] In addition, the specimens were evaluated in accordance with
the test method of ASTM E 8 in a uniaxial tension tester at a
temperature of 25.degree. C., a humidity of 65%, and a maximum load
of 250 kN to measure yield strength, tensile strength, and
elongation.
[0056] In addition, the density of the specimens was measured in
accordance with ASTM D 792 method A.
[0057] Meanwhile, the fraction of the ferrite, the fraction of the
.kappa.-carbide, and the fraction of the Fe--Al intermetallic
compound of the specimens were determined by primarily measuring
weakly etched specimens after mirror polish according to ASTM E 45,
and then verifying the consistency with image analysis results
after Lepera color etching.
[0058] As shown in FIG. 2, in the Examples according to the present
invention yield strength, tensile strength, elongation, density,
and the fraction of the .kappa.-carbide all satisfied the
requirement of the present invention.
[0059] For example, in Examples 1 to 7 according to exemplary
embodiments of the present invention, the yield strength is 600 MPa
was greater and the tensile strength was 1000 MPa or greater.
[0060] In addition, in Examples 1 to 7 according to exemplary
embodiments of the present invention, the elongation was 20% or
greater and the density was 6.85 g/cm.sup.3 or less.
[0061] In addition, in Examples 1 to 7 according to exemplary
embodiments of the present invention, the matrix was formed by
austenite, the ferrite was formed at the fraction of 15% or less,
the .kappa.-carbide was formed at the fraction of 10% or less, and
the Fe--Al intermetallic compound was formed at the fraction of 2%
or less.
[0062] On the other hand, in Comparative Example 1, as the content
of C was less than the range suggested by the present invention,
the ferrite was excessively formed, and thus the yield strength and
the tensile strength did not satisfy the requirements of the
present invention. The density also did not satisfy the
requirements of the present invention.
[0063] In Comparative Example 2, as the contents of C and Mn were
added in excess of the range suggested by the present invention,
the .kappa.-carbide was excessively formed, and thus the elongation
did not satisfy the requirements of the present invention.
Accordingly, it was confirmed that forging cracks occurred during
molding.
[0064] In Comparative Example 3, as the content of Mn was added in
excess of the range suggested by the present invention, the
.kappa.-carbide was excessively formed and the .beta.-Mn was
formed, and thus the elongation did not satisfy the requirements of
the present invention. Accordingly, it was confirmed that forging
cracks occurred during molding.
[0065] In Comparative Example 4, as the content of Al was added in
excess of the range suggested by the present invention, the
ferrite, the .kappa.-carbide and the Fe--Al intermetallic compound
were excessively formed, and thus the elongation did not satisfy
the requirements of the present invention. Accordingly, it was
confirmed that forging cracks occurred during molding.
[0066] In Comparative Example 5, as the content of Al was added to
the range lower than that suggested by the present invention, the
.kappa.-carbide was excessively formed, and thus the elongation did
not satisfy the requirements of the present invention. Accordingly,
it was confirmed that forging cracks occurred during molding. The
density also did not satisfy the requirements of the present
invention.
[0067] Meanwhile, FIGS. 3A and 3B are photographs of a
microstructure of the austenitic light weight steel according to
Inventive Examples, and are photographs of the microstructure of
the austenitic light weight steel according to Example 1 of FIG.
1.
[0068] As shown from FIGS. 3A and 3B, in Example 1, a trace amount
of ferrite structure, the .kappa.-carbide and the Fe--Al
intermetallic compound were observed in the austenitic matrix.
[0069] In FIG. 3A, portions indicated by an arrow {circle around
(1)} are the ferrite structure and the remainder is the austenite
structure. From this, it can be confirmed that a trace amount of
ferrite structure is formed in the austenite structure as the
matrix in Example 1.
[0070] In FIG. 3B, portions indicated by an arrow {circle around
(2)} are the .kappa.-carbide and a portion indicated by an arrow
{circle around (3)} is the Fe--Al intermetallic compound.
Accordingly, it can be confirmed that a trace amount of the
.kappa.-carbide and the Fe--Al intermetallic compound were formed
in the austenite structure as the matrix.
[0071] In addition, most of the .kappa.-carbide was mostly observed
in the form of needles at the ferrite-austenite grain boundary, but
some was distributed in austenite-austenite grain boundary. In
addition, most of the Fe--Al intermetallic compound was found in
the form of stripes at the austenite-austenite grain boundary.
[0072] The relationship between the grain size and the elongation
of the specimens according to Examples and Comparative Examples was
examined. The results are shown in FIGS. 4A, 4B, and 5.
[0073] FIG. 4A is an enlarged photograph of the austenitic light
weight steel according to Example, FIG. 4B is an enlarged
photograph of the austenitic light weight steel according to the
Comparative Example, and FIG. 5 is a graph for explaining the
relationship of stress-elongation for the specimens according to
Example and Comparative Example.
[0074] Particularly, FIG. 4A is the enlarged photograph of the
austenitic light weight steel according to Example 3 of FIG. 1 and
FIG. 4B is the enlarged photograph of the austenitic light weight
steel according to Comparative Example 5 of FIG. 1.
[0075] As shown in FIG. 4A, it was confirmed that the size of a
grain is formed in the range of 25 to 38 pm in Example 3.
[0076] In addition, as shown in FIG. 4B, it was confirmed that the
size of the grain was formed in the range of 50 to 100 .mu.m in
Comparative Example 5.
[0077] When the size of the grain exceeds 40 .mu.m, even if the
same thermal treatment is performed, crack surfaces of a specific
direction (arrows in FIG. 4B) develop in the coarse grain, which
lead to premature failure, such that it is impossible to secure
sufficient elongation and rolling properties.
[0078] Therefore, the grain of the light weight steel according to
an embodiment of the present invention may be formed to have a
length of about 40 .mu.m or less in a rolling direction.
[0079] In addition, as shown in FIG. 5, in Comparative Example 5,
the elongation was about 15%, and in Example 3, the elongation was
about 27%. As shown in FIG. 5, according to an exemplary embodiment
of the present invention, it was confirmed that the elongation may
be secured to have 20% or more.
[0080] According to various exemplary embodiments of the present
invention, the proportion of the ferrite structure, and the amount
of the .kappa.-carbide and the Fe--Al intermetallic compound which
are formed in an austenitic matrix may be suitably controlled by
adjusting the content of the main alloy component, thereby
obtaining an austenitic light weight steel capable of securing an
elongation of about 20% or greater and reducing specific gravity,
while maintaining an excellent yield strength and tensile
strength.
[0081] In addition, according to various exemplary embodiments of
the present invention, an excellent elongation may be ensured,
thereby improving hot workability and cold workability.
[0082] Although the present invention has been shown and described
with respect to specific embodiments, it will be apparent to those
having ordinary skill in the art that the present invention may be
variously modified and altered without departing from the spirit
and scope of the present invention as defined by the following
claims.
* * * * *