U.S. patent application number 16/758307 was filed with the patent office on 2020-10-15 for lubricant supply passage for compressor.
The applicant listed for this patent is Carrier Corporation. Invention is credited to Masao Akei.
Application Number | 20200325899 16/758307 |
Document ID | / |
Family ID | 1000004959145 |
Filed Date | 2020-10-15 |

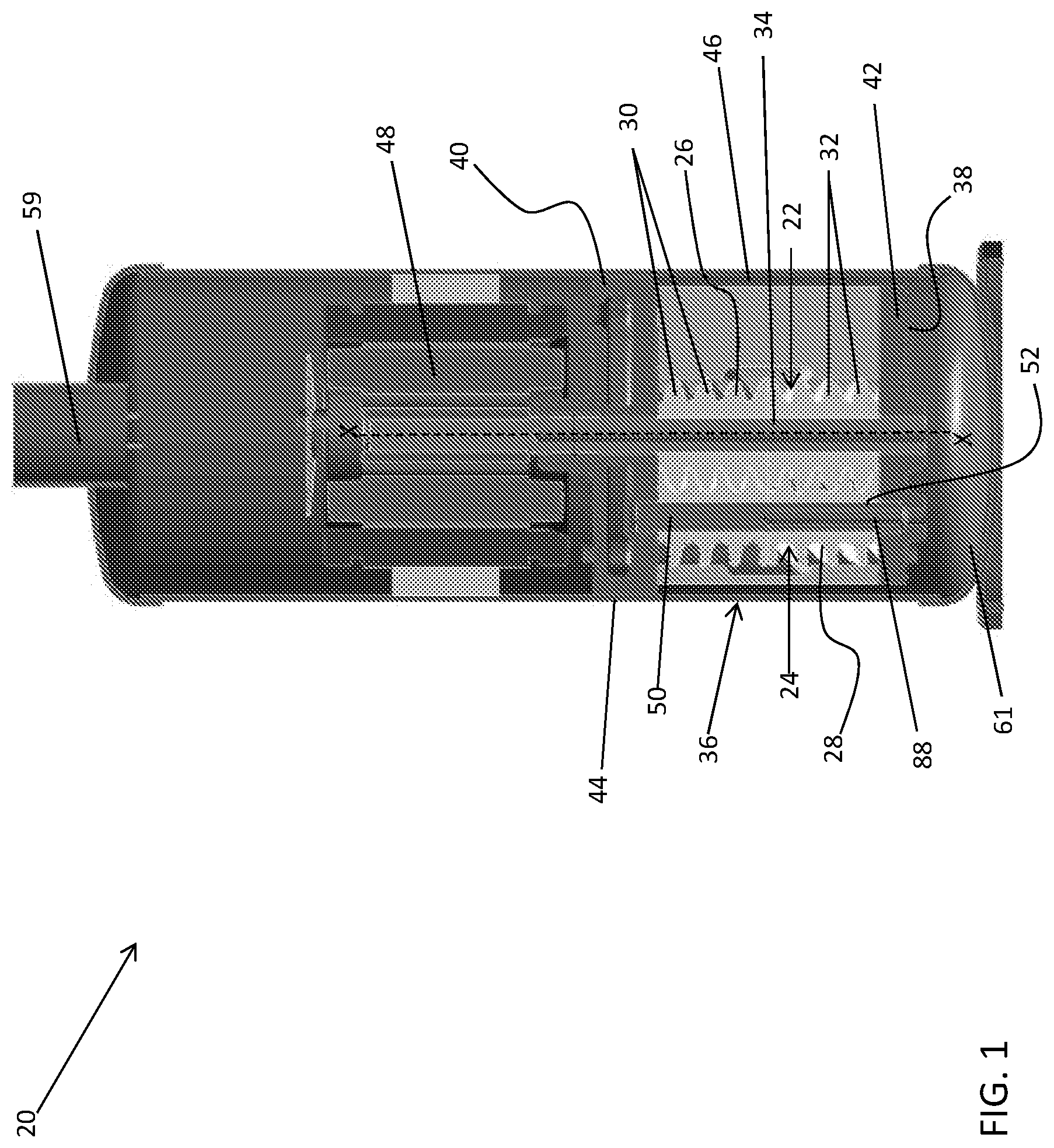
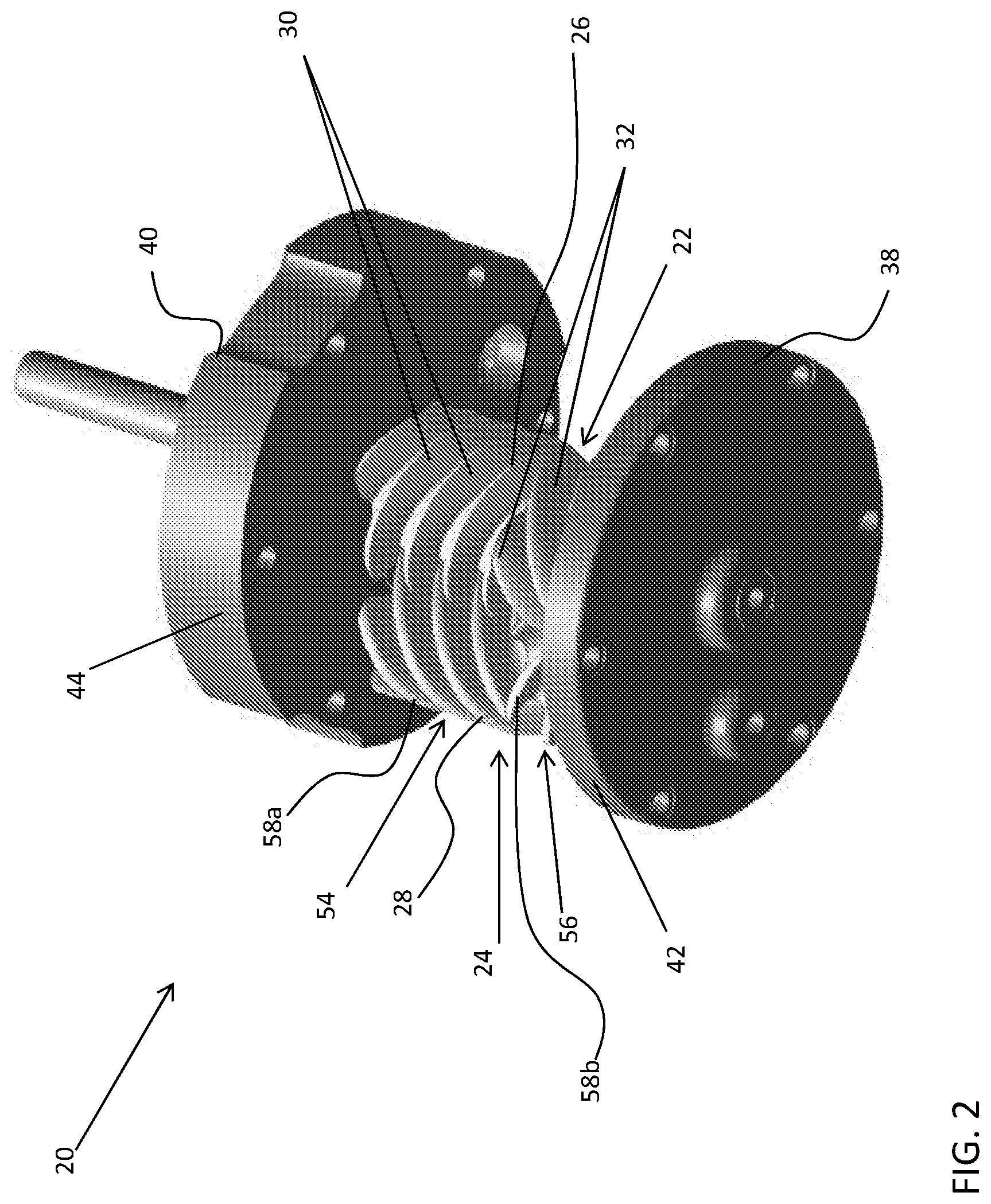

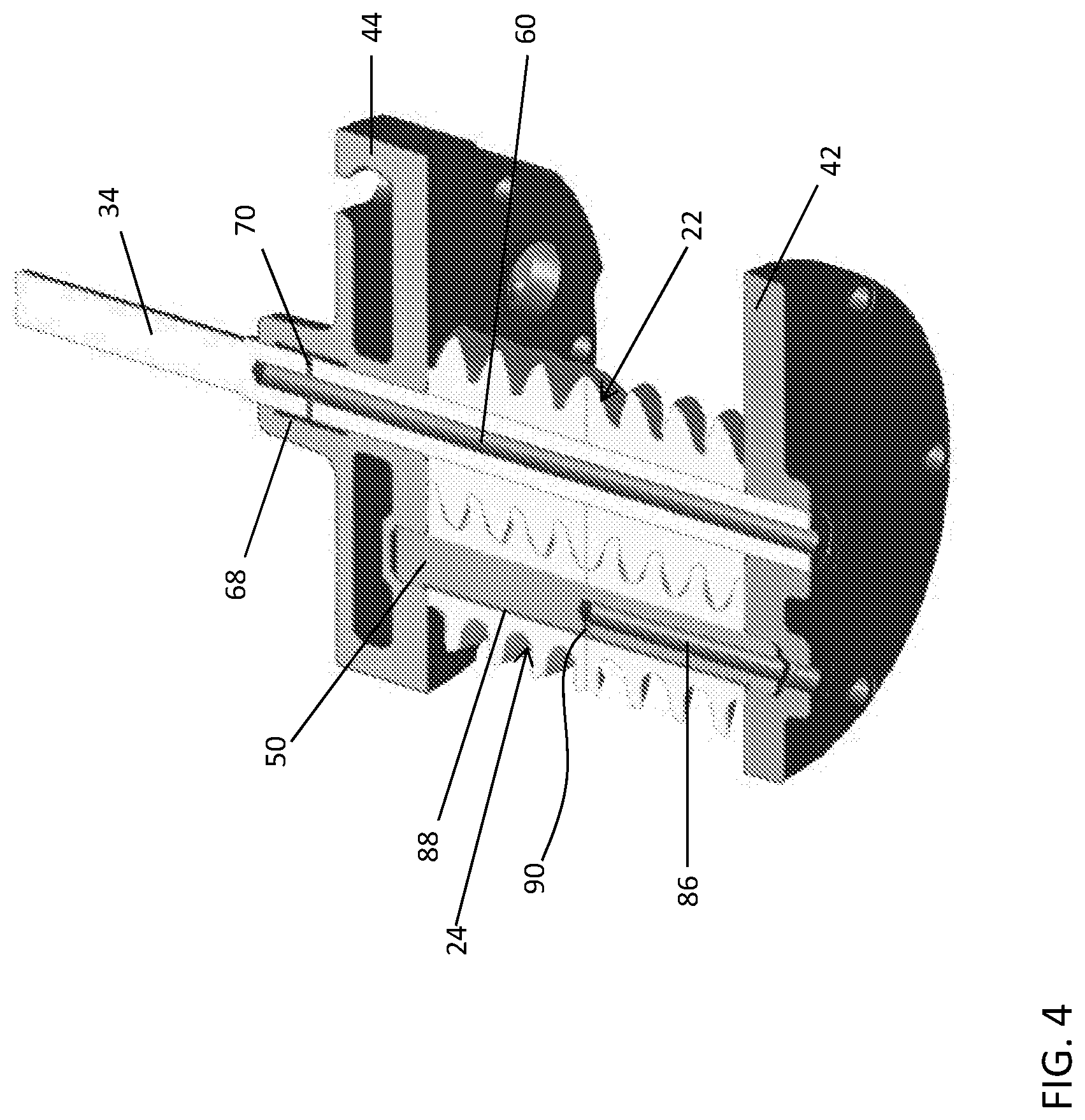



United States Patent
Application |
20200325899 |
Kind Code |
A1 |
Akei; Masao |
October 15, 2020 |
LUBRICANT SUPPLY PASSAGE FOR COMPRESSOR
Abstract
A fluid machine includes a first rotor rotatable about a first
axis, a second rotor rotatable about a second axis, a casing for
supporting said first rotor and said second rotor, a sump having a
volume of lubricant contained therein, a first lubricant passage
for supplying lubricant from the sump to a dynamic interface
associated with the first rotor, and a second lubricant passage for
supplying lubricant from the sump to a dynamic interface associated
with the second rotor. A pressure differential created within the
fluid machine supplies the lubricant from the sump to the first
lubricant passage and the second lubricant passage.
Inventors: |
Akei; Masao; (Cicero,
NY) |
|
Applicant: |
Name |
City |
State |
Country |
Type |
Carrier Corporation |
Palm Beach Gardens |
FL |
US |
|
|
Family ID: |
1000004959145 |
Appl. No.: |
16/758307 |
Filed: |
October 16, 2018 |
PCT Filed: |
October 16, 2018 |
PCT NO: |
PCT/US2018/056101 |
371 Date: |
April 22, 2020 |
Related U.S. Patent Documents
|
|
|
|
|
|
Application
Number |
Filing Date |
Patent Number |
|
|
62576430 |
Oct 24, 2017 |
|
|
|
Current U.S.
Class: |
1/1 |
Current CPC
Class: |
F04C 18/16 20130101;
F04C 29/025 20130101 |
International
Class: |
F04C 29/02 20060101
F04C029/02; F04C 18/16 20060101 F04C018/16 |
Claims
1. A fluid machine comprising: a first rotor rotatable about a
first axis; a second rotor rotatable about a second axis; a casing
for supporting said first rotor and said second rotor; a sump
having a volume of lubricant contained therein; a first lubricant
passage for supplying lubricant from the sump to a dynamic
interface associated with the first rotor; and a second lubricant
passage for supplying lubricant from the sump to a dynamic
interface associated with the second rotor, wherein a pressure
differential created within the fluid machine supplies the
lubricant from the sump to the first lubricant passage and the
second lubricant passage.
2. The fluid machine of claim 1, wherein during operation of the
fluid machine, the pressure differential is formed between a high
pressure adjacent at least one end of the casing and low pressure
at a central location of the first rotor and the second rotor.
3. The fluid machine of claim 1, wherein said lubricant is supplied
from said sump to said first lubricant passage and said second
lubricant passage simultaneously.
4. The fluid machine of claim 1, wherein said first rotor is
rotatably mounted to the casing without roller element
bearings.
5. The fluid machine of claim 1, wherein the first rotor includes a
first shaft rotatably mounted to the casing, wherein at least one
surface of the casing and the first shaft define the dynamic
interface associated with the first rotor.
6. The fluid machine of claim 5, wherein the at least one surface
of the casing arranged in direct contact with the first shaft
functions as a bearing.
7. The fluid machine of claim 6, wherein the at least one surface
of the casing arranged in direct contact with the first shaft
includes a first surface arranged in direct contact with a portion
the first shaft adjacent a first end, and a second surface arranged
in direct contact with a portion the first shaft adjacent a second
end.
8. The fluid machine of claim 7, wherein the first lubricant
passage includes a first portion for supplying lubricant to the
first surface and a second portion, distinct from the first
portion, for supplying lubricant to the second surface, wherein
lubricant is supplied to both the first portion and the second
portion simultaneously.
9. The fluid machine of claim 5, wherein the first lubricant
passage further comprises: a cavity formed in a portion of the
casing adjacent the first shaft; a passage extending axially
through at least a portion of the first shaft; at least one radial
hole coupling the cavity and the passage; and a groove extending
from the cavity to an interior of a compression pocket formed
between the first rotor and the second rotor and the casing.
10. The fluid machine of claim 9, wherein the first lubricant
passage further comprises: a counter bore formed at the interface
between the casing and the compression pocket.
11. The fluid machine of claim 5, wherein the first lubricant
passage comprises: a groove extending from the sump to an interior
of a compression pocket formed between the first rotor and the
second rotor and the casing.
12. The fluid machine of claim 5, wherein the second rotor further
comprises: a second shaft supported by the casing; and a working
portion rotatable relative to the second shaft, wherein the second
shaft and the working portion define the dynamic interface
associated with the second rotor.
13. The fluid machine of claim 12, wherein the second lubricant
passage further comprises: a first passage extending axially
through at least a portion of the second shaft; a second passage
formed in an outer periphery of the second shaft; and at least one
radial hole coupling the first passage and the second passage.
14. The fluid machine of claim 13, wherein the second passage
extends axially such that a first end of the second passage is
fluidly coupled to a first portion of the casing and a second,
opposite end of the second passage is fluidly coupled to a second
portion of the casing.
15. The fluid machine of claim 1, wherein a counter bore is formed
in the casing where at least one of the first lubricant passage and
the second lubricant passage enters a compression pocket formed
between the first rotor and the second rotor.
16. The fluid machine of claim 15, further comprising a recess is
formed in the casing in fluid communication with the counter bore,
the recess being arranged at an angle towards an interface between
the first rotor and the second rotor.
17. The fluid machine of claim 16, wherein at least one of an
angle, length, width, and depth of the recess is optimized to
control a flow of lubricant to the compression pocket.
18. A method of lubricating one or more dynamic interfaces of a
fluid machine comprising: supplying lubricant from a sump to a
dynamic interface associated with a first rotor of the fluid
machine via a first lubricant passage; and supplying lubricant from
a sump to a dynamic interface associated with a second rotor of the
fluid machine via a second lubricant passage, the second lubricant
passage being distinct from the first lubricant passage; wherein
supplying lubricant to the dynamic interface associated with the
first rotor and the dynamic interface associated with the second
rotor occurs automatically in response to a pressure differential
created within the fluid machine during operation of the fluid
machine.
19. The method of claim 18, wherein supplying lubricant from a sump
to a dynamic interface associated with a first rotor and supplying
lubricant from a sump to a dynamic interface associated with a
second rotor occurs simultaneously.
20. The method of claim 18, wherein supplying lubricant from a sump
to a dynamic interface associated with a first rotor and supplying
lubricant from a sump to a dynamic interface associated with a
second rotor occurs without a pump or control valve.
21. The method of claim 18, wherein supplying lubricant from a sump
to a dynamic interface associated with a first rotor further
comprises: supplying lubricant via a first passage to a first
bearing surface, the first passage extending through an opening
formed in a first shaft of the first rotor; and supplying lubricant
via a second passage to a second bearing surface.
22. The method of claim 18, further comprising supplying lubricant
from the dynamic interface associated with a first rotor and the
dynamic interface associated with a second rotor to a compression
pocket formed between the first rotor and the second rotor.
Description
BACKGROUND
[0001] The subject matter disclosed herein relates generally to
fluid machines, and more specifically, to fluid machines, such as
compressors, having helically lobed rotors.
[0002] It has been determined that commonly used refrigerants, such
as R-410A in one non-limiting example, have unacceptable global
warming potential (GWP) such that their use will cease for many
HVAC&R applications. Non-flammable, low GWP refrigerants are
replacing existing refrigerants in many applications, but have
lower density and do not possess the same cooling capacity as
existing refrigerants. Replacement refrigerants require a
compressor capable of providing a significantly greater
displacement, such as a screw compressor.
[0003] Existing screw compressor typically utilized roller, ball,
or other rolling element bearings to precisely position the rotors
and minimize friction during high speed operation. However, for
typical HVAC&R applications, existing screw compressors with
roller element bearings result in an unacceptable large and costly
fluid machine.
[0004] Therefore, there exists a need in the art for an
appropriately sized and cost effective fluid machine that minimizes
friction while allowing precise positioning and alignment of the
rotors.
BRIEF DESCRIPTION
[0005] According to one embodiment, a fluid machine includes a
first rotor rotatable about a first axis, a second rotor rotatable
about a second axis, a casing for supporting said first rotor and
said second rotor, a sump having a volume of lubricant contained
therein, a first lubricant passage for supplying lubricant from the
sump to a dynamic interface associated with the first rotor, and a
second lubricant passage for supplying lubricant from the sump to a
dynamic interface associated with the second rotor. A pressure
differential created within the fluid machine supplies the
lubricant from the sump to the first lubricant passage and the
second lubricant passage.
[0006] In addition to one or more of the features described above,
or as an alternative, in further embodiments during operation of
the fluid machine, the pressure differential is formed between a
high pressure adjacent at least one end of the casing and low
pressure at a central location of the first rotor and the second
rotor.
[0007] In addition to one or more of the features described above,
or as an alternative, in further embodiments said lubricant is
supplied from said sump to said first lubricant passage and said
second lubricant passage simultaneously.
[0008] In addition to one or more of the features described above,
or as an alternative, in further embodiments said first rotor is
rotatably mounted to the casing without roller element
bearings.
[0009] In addition to one or more of the features described above,
or as an alternative, in further embodiments the first rotor
includes a first shaft rotatably mounted to the casing, wherein at
least one surface of the casing and the first shaft define the
dynamic interface associated with the first rotor.
[0010] In addition to one or more of the features described above,
or as an alternative, in further embodiments the at least one
surface of the casing arranged in direct contact with the first
shaft functions as a bearing.
[0011] In addition to one or more of the features described above,
or as an alternative, in further embodiments the at least one
surface of the casing arranged in direct contact with the first
shaft includes a first surface arranged in direct contact with a
portion the first shaft adjacent a first end, and a second surface
arranged in direct contact with a portion the first shaft adjacent
a second end.
[0012] In addition to one or more of the features described above,
or as an alternative, in further embodiments the first lubricant
passage includes a first portion for supplying lubricant to the
first surface and a second portion, distinct from the first
portion, for supplying lubricant to the second surface, wherein
lubricant is supplied to both the first portion and the second
portion simultaneously.
[0013] In addition to one or more of the features described above,
or as an alternative, in further embodiments the first lubricant
passage further comprises: a cavity formed in a portion of the
casing adjacent the first shaft, a passage extending axially
through at least a portion of the first shaft, at least one radial
hole coupling the cavity and the passage, and a groove extending
from the cavity to an interior of a compression pocket formed
between the first rotor and the second rotor and the casing.
[0014] In addition to one or more of the features described above,
or as an alternative, in further embodiments the first lubricant
passage further comprises: a counter bore formed at the interface
between the casing and the compression pocket.
[0015] In addition to one or more of the features described above,
or as an alternative, in further embodiments the first lubricant
passage comprises: a groove extending from the sump to an interior
of a compression pocket formed between the first rotor and the
second rotor and the casing.
[0016] In addition to one or more of the features described above,
or as an alternative, in further embodiments the second rotor
further comprises: a second shaft supported by the casing, and a
working portion rotatable relative to the second shaft. The second
shaft and the working portion define the dynamic interface
associated with the second rotor.
[0017] In addition to one or more of the features described above,
or as an alternative, in further embodiments the second lubricant
passage further comprises: a first passage extending axially
through at least a portion of the second shaft, a second passage
formed in an outer periphery of the second shaft, and at least one
radial hole coupling the first passage and the second passage.
[0018] In addition to one or more of the features described above,
or as an alternative, in further embodiments the second passage
extends axially such that a first end of the second passage is
fluidly coupled to a first portion of the casing and a second,
opposite end of the second passage is fluidly coupled to a second
portion of the casing.
[0019] In addition to one or more of the features described above,
or as an alternative, in further embodiments a counter bore is
formed in the casing where at least one of the first lubricant
passage and the second lubricant passage enters a compression
pocket formed between the first rotor and the second rotor.
[0020] In addition to one or more of the features described above,
or as an alternative, in further embodiments comprising a recess is
formed in the casing in fluid communication with the counter bore,
the recess being arranged at an angle towards an interface between
the first rotor and the second rotor.
[0021] In addition to one or more of the features described above,
or as an alternative, in further embodiments at least one of an
angle, length, width, and depth of the recess is optimized to
control a flow of lubricant to the compression pocket.
[0022] According to another embodiment, a method of lubricating one
or more dynamic interfaces of a fluid machine includes supplying
lubricant from a sump to a dynamic interface associated with a
first rotor of the fluid machine via a first lubricant passage, and
supplying lubricant from a sump to a dynamic interface associated
with a second rotor of the fluid machine via a second lubricant
passage. The second lubricant passage is distinct from the first
lubricant passage. Supplying lubricant to the dynamic interface
associated with the first rotor and the dynamic interface
associated with the second rotor occurs automatically in response
to a pressure differential created within the fluid machine during
operation of the fluid machine.
[0023] In addition to one or more of the features described above,
or as an alternative, in further embodiments supplying lubricant
from a sump to a dynamic interface associated with a first rotor
and supplying lubricant from a sump to a dynamic interface
associated with a second rotor occurs simultaneously.
[0024] In addition to one or more of the features described above,
or as an alternative, in further embodiments supplying lubricant
from a sump to a dynamic interface associated with a first rotor
and supplying lubricant from a sump to a dynamic interface
associated with a second rotor occurs without a pump or control
valve.
[0025] In addition to one or more of the features described above,
or as an alternative, in further embodiments supplying lubricant
from a sump to a dynamic interface associated with a first rotor
further comprises: supplying lubricant via a first passage to a
first bearing surface, the first passage extending through an
opening formed in a first shaft of the first rotor, and supplying
lubricant via a second passage to a second bearing surface.
[0026] In addition to one or more of the features described above,
or as an alternative, in further embodiments comprising supplying
lubricant from the dynamic interface associated with a first rotor
and the dynamic interface associated with a second rotor to a
compression pocket formed between the first rotor and the second
rotor.
BRIEF DESCRIPTION OF THE DRAWINGS
[0027] The subject matter, which is regarded as the disclosure, is
particularly pointed out and distinctly claimed in the claims at
the conclusion of the specification. The foregoing and other
features, and advantages of the disclosure are apparent from the
following detailed description taken in conjunction with the
accompanying drawings in which:
[0028] FIG. 1 is cross-sectional view of a fluid machine according
to an embodiment;
[0029] FIG. 2 is a perspective view of a working portion of a fluid
machine according to an embodiment;
[0030] FIG. 3 is cross-sectional view of a fluid machine including
a lubricant supply passage according to an embodiment;
[0031] FIG. 4 is a cross-sectional view of a working portion of a
fluid machine according to an embodiment;
[0032] FIG. 5 is a perspective cross-sectional view of a casing of
a fluid machine according to an embodiment;
[0033] FIG. 6 is a perspective view of a second shaft of a fluid
machine according to an embodiment; and
[0034] FIG. 7 is a front view of a surface of a bearing housing
facing towards a compression pocket of the fluid machine according
to an embodiment.
[0035] The detailed description explains embodiments of the
disclosure, together with advantages and features, by way of
example with reference to the drawings.
DETAILED DESCRIPTION
[0036] Referring now to the FIGS. 1 and 2, a fluid machine 20 is
illustrated. In the illustrated, non-limiting embodiment, the fluid
machine 20 is an opposed screw compressor. However, other suitable
embodiments of a fluid machine, such as a pump, fluid motor, or
engine for example, are also within the scope of the disclosure.
The fluid machine 20 includes a first rotor 22 intermeshed with a
second rotor 24. In an embodiment, the first rotor 22 is a male
rotor having a male-lobed working portion 26 and the second rotor
24 is a female rotor including a female-lobed portion 28.
Alternatively, the first rotor 22 may be a female rotor and the
second rotor 24 may be a male rotor. The working portion 26 of the
first rotor 22 includes at least one first helical lobe 30 and at
least one second helical lobe 32. In the illustrated, non-limiting
embodiment, the first rotor 22 includes two separate portions
defining the first helical lobes 30 and the second helical lobes
32. In another embodiment, the first rotor 22, including the first
and second helical lobes 30, 32, may be formed as a single integral
piece.
[0037] The fluid machine 20 includes a first shaft 34 fixed for
rotation with the first rotor 22. The fluid machine 20 further
include a casing 36 rotatably supporting the first shaft 34 and at
least partially enclosing the first rotor 22 and the second rotor
24. A first end 38 and a second end 40 of the casing 36 are
configured to rotatably support the first shaft 34. In the
illustrated, non-limiting embodiment, the first, lower end 38 of
the casing 36 is formed by a lower bearing housing 42 and the
second, upper end 40 of the casing 36 is formed by a distinct upper
bearing housing 44. A rotor case 46 may extend between and couple
the lower and upper bearing housings 42, 44. However, embodiments
where the lower bearing housing 42 and/or the upper bearing housing
44 is integrally formed with the rotor case 46 are also
contemplated herein.
[0038] The first shaft 34 of the illustrated embodiments is
directly coupled to an electric motor 48 operable to drive rotation
of the first shaft 34 about an axis X. Any suitable type of
electric motor 48 is contemplated herein, including but not limited
to an induction motor, permanent magnet (PM) motor, and switch
reluctance motor for example. In an embodiment, the first rotor 22
is fixed to the first shaft 34 by a fastener, coupling, integral
formation, interference fit, and/or any additional structures or
methods known to a person having ordinary skill in the art (not
shown), such that the first rotor 22 and the first shaft 34 rotate
about axis X in unison.
[0039] The fluid machine 20 additionally includes a second shaft 50
operable to rotationally support the second rotor 24. The second
rotor 24 includes an axially extending bore 52 within which the
second shaft 50 is received. In an embodiment, the second shaft 50
is stationary or fixed relative to the casing 36 and the second
rotor 24 is configured to rotate about the second shaft 50.
However, embodiments where the second shaft 50 is also rotatable
relative to the casing 36 are also contemplated herein.
[0040] With specific reference to FIG. 2, the first rotor 22 is
shown as including four first helical lobes 30 and at least four
second helical lobes 32. The illustrated, non-limiting embodiment,
is intended as an example only, and it should be understood by a
person of ordinary skill in the art that any suitable number of
first helical lobes 30 and second helical lobes 32 are within the
scope of the disclosure. As shown, the first helical lobes 30 and
the second helical lobes 32 have opposite helical configurations.
In the illustrated, non-limited embodiment, the first helical lobes
30 are left-handed and the second helical lobes 32 are
right-handed. Alternatively, the first helical lobes 30 may be
right-handed and the second helical lobes 32 may be
left-handed.
[0041] By including lobes 30, 32 with having opposite helical
configurations, opposing axial flows are created between the first
and second helical lobes 30, 32. Due to the symmetry of the axial
flows, thrust forces resulting from the helical lobes 30, 32 are
generally equal and opposite, such that the thrust forces
substantially cancel one another. As a result, this configuration
of the opposing helical lobes 30, 32 provides a design advantage
since the need for thrust bearings in the fluid machine can be
reduced or eliminated.
[0042] The second rotor 24 has a first portion 54 configured to
mesh with the first helical lobes 30 and a second portion 56
configured to mesh with the second helical lobes 32. To achieve
proper intermeshing engagement between the first rotor 22 and the
second rotor 24, each portion 54, 56 of the second rotor 24
includes one or more lobes 58 having an opposite configuration to
the corresponding helical lobes 30, 32 of the first rotor 22. In
the illustrated, non-limiting embodiment, the first portion 54 of
the second rotor 24 has at least one right-handed lobe 58a, and the
second portion 56 of the second rotor 24 includes at least one
left-handed lobe 58b.
[0043] In an embodiment, the first portion 54 of the second rotor
24 is configured to rotate independently from the second portion 56
of the second rotor 24. However, embodiments where the first and
second portions 54, 56 are rotationally coupled are also
contemplated herein. Each portion 54, 56 of the second rotor 24 may
include any number of lobes 58. In an embodiment, the total number
of lobes 58 formed in each portion 54, 56 of the second rotor 24 is
generally larger than a corresponding portion of the first rotor
24. For example, if the first rotor 22 includes four first helical
lobes 30, the first portion 54 of the second rotor 24 configured to
intermesh with the first helical lobes 30 may include five helical
lobes 58a. However, embodiments where the total number of lobes 58
in a portion 54, 56 of the second rotor 24 is equal to a
corresponding group of helical lobes (i.e. the first helical lobes
30 or the second helical lobes 32) of the first rotor 22 are also
within the scope of the disclosure.
[0044] Returning to FIG. 1, during operation of the fluid machine
20 of one embodiment, a gas or other fluid, such as a low GWP
refrigerant for example, is drawn to a central location by a
suction process generated by the fluid machine 20. Rotation of the
first rotor 22 and the second rotor 24 compresses the refrigerant
and forces the refrigerant toward the outer ends 38, 40 of the
casing 36 due to the structure and function of the opposing helical
rotors 22, 24. The compressed refrigerant is routed by an internal
gas passage within the casing 36 and discharged through the upper
end 40 of the casing 36. The discharged refrigerant passes through
the electric motor 48 and out of the discharge outlet 59.
[0045] With reference now to FIGS. 3-7, the fluid machine 20
includes one or more lubricant supply passages for providing a
lubricant from a sump 61 to the dynamic interfaces of the machine
20. In an embodiment, the sump 61 containing a volume of lubricant,
such as oil for example, is located adjacent and in communication
with the lower bearing housing 42. A first shaft passage 60 extends
axially through at least a portion of the first shaft 34. In the
illustrated, non-limiting embodiment, the first shaft passage 60
extends from adjacent the lower end 38 of the casing 36 to adjacent
the upper end 40 of the casing 36.
[0046] As best shown in FIGS. 4 and 5, in an embodiment, a cavity
68 formed in the upper bearing housing 64 is configured to surround
a periphery of part of the first shaft 34. At least one radial hole
70 extends between the first shaft passage 60 to the outer surface
of the shaft 34 to deliver lubricant to the cavity 68. In the
illustrated, non-limiting embodiment, two radial holes 70 extending
in opposite directions relative to one another from the first shaft
passage 60 to the outer surface of the shaft 34. In addition, one
or more surfaces of the bore formed in the upper bearing portion 44
and configured to contact the first shaft 34 may function as a
bearing. For example, with reference for FIG. 5, a first surface 72
disposed adjacent a first side of the cavity 68 is operable as a
main bearing and a second surface 74, disposed adjacent a second,
opposite side of the cavity 68, is operable as a sub-bearing.
Similarly, the bore formed in a lower bearing portion 62 for
receiving a portion of the first shaft 34 includes a surface 76
operable as a bearing.
[0047] In an embodiment, a groove 80 extends over the axial length
of the surface 72. This groove 80 is arranged in fluid
communication with the cavity 68 and is configured to distribute
lubricant from the cavity 68 over the axial length of the first
surface 72. Alternatively, or in addition, a groove 84 extends over
the axial length of the surface 76. The groove 84 is configured to
distribute lubricant from the sump 61 located adjacent the lower
bearing housing 42.
[0048] A second shaft passage 86 extends axially through the lower
bearing housing 42 and at least a portion of the second shaft 50.
In the illustrated, non-limiting embodiment, the second shaft
passage 86 extends over about half of the axial length of the
second shaft 50. However, a shaft passage 86 of any length is
contemplated herein. With reference now to FIG. 6, an axially
extending passage 88 is formed in an outer periphery of the second
shaft 50 and at least one radial hole 90 fluidly couples the shaft
passage 86 and the axial passage 88. In an embodiment, the radial
hole is arranged generally centrally relative to the axial passage
such that a portion of the lubricant is distributed in two
directions relative to the radial hole 90. However, embodiments
where the radial hole 90 is arranged adjacent an end of the passage
88 or at another location are also contemplated herein. The axial
passage 88 is configured to distribute lubricant at the interface
formed between the second shaft 50 and the bore 52 formed in the
second rotor 24. In an embodiment, the axial passage 88 extends
between the upper and lower bearing housings 44, 42.
[0049] During operation of the fluid machine 20, the relatively
high pressure discharge at outer ends 38, 40 of the casing 36, and
the relatively low pressure suction at a central location of the
first rotor 22 and the second rotor 24, urges or draws lubricant
from the sump 61 through the lubricant supply passages associated
with the first and second rotors 22, 24. More specifically,
lubricant will flow from the sump 61 through the first shaft
passage 60, the axial groove 84 formed in surface 76 of the lower
bearing housing 42, and through the second shaft passage 86
simultaneously. The lubricant supply passages are intended to
lubricate the surfaces 72, 74, and 76 of the upper and lower
bearing housings 42, 44 that function as bearings for the first
shaft 34, and the interface between the second shaft 50 and the
second rotor 24 to reduce friction there between.
[0050] A counter bore 78, 82, 92, 94 may be formed in the surfaces
of the lower bearing housing 42 and the upper bearing housing 44
facing the first and second rotors 22, 24, respectively. The
counterbore 78 may be arranged in fluid communication with the
groove 80. The counterbore 82 may be arranged in fluid
communication with the groove 84. As a result, lubricant will flow
to each of the counter bores 78, 82 after lubricating the
respective surfaces 72, 74, and 76. Also, the counterbore 92, 94
may be arranged in fluid communication with the axial passage 88.
As a result, lubricant will flow to the counter bores 92, 94 after
lubricating the interface between the second shaft 50 and the
second rotor 24. In an embodiment, a recess 96 may extend from one
or more of the counter bores 78, 82, 92, 94 at an angle towards the
interface between the first rotor 22 and the second rotor 24.
Although the fluid machine illustrated and described herein
includes a recess formed at each of the counter bores, embodiments
where none or only some of the counter bores includes a recess are
also within the scope of the disclosure.
[0051] The configuration of each recess 96, such as the angle,
length, width, and depth for example, may be optimized to control
the amount of lubricant flow to the compression pocket. In an
embodiment, the recess 96 has a linear contour and is aligned with
the interface between the lobes 30, 32 of the first rotor 22 and
the corresponding lobes 58a, 58b of the second rotor 24.
Accordingly, as shown FIG. 6, the angle of the recess 96 relative
to the axis extending through the origin of both the first and
second shafts 34, 50 is between 0 degrees and 60 degrees.
[0052] By positioning the recess 96 in alignment with the
intermeshing engagement of the rotors 22, 24, the recess
communicates with both the high pressure and low pressure areas
adjacent the first rotor 22 and second rotor 24. As a result,
lubricant may flow from the recess 96 into the compression pocket
formed between the first and second rotors 22, 24. In an
embodiment, the length of the recess 96, measured radially from the
origin of the bore for receiving a corresponding shaft 34 or 50 is
greater than a root radius of the rotor 22 or 24. Further, the
length of the recess 96 may be greater than the root radius, but
less than the tip radius of the rotor 22 or 24 associated
therewith. In an embodiment, a width of the recess 96, measured
perpendicular to the length, is between 1 mm and 10 mm, and a depth
of the recess 96 extending into the lower or upper bearing housing
42, 44 is between 1-5 times the axial length of the clearance
between the rotor 22 or 24 and the adjacent surface of the lower or
upper bearing housing 42, 44. It should be understood that in
embodiments including a plurality of recesses, the configuration of
recesses may be the same, or alternatively, may be different.
[0053] The fluid machine 20 illustrated and described herein
provides a simple and low cost configuration for a lubricant supply
system. Because the pressure of the machine 20 is used to draw the
fluid to the respective interfaces, costly devices, such as a pump
or control valve for example, are not required. Further, because
the lubricant is driven by the pressure differential created during
operation of the machine 20, a stable supply of lubricant is
provided over a wide range of shaft speeds.
[0054] While the disclosure has been described in detail in
connection with only a limited number of embodiments, it should be
readily understood that the disclosure is not limited to such
disclosed embodiments. Rather, the disclosure can be modified to
incorporate any number of variations, alterations, substitutions or
equivalent arrangements not heretofore described, but which are
commensurate with the spirit and scope of the disclosure.
Additionally, while various embodiments of the disclosure have been
described, it is to be understood that aspects of the disclosure
may include only some of the described embodiments. Accordingly,
the disclosure is not to be seen as limited by the foregoing
description, but is only limited by the scope of the appended
claims.
* * * * *