U.S. patent application number 16/305603 was filed with the patent office on 2020-10-15 for precipitation-hardening hot rolled steel sheet having excellent material uniformity and hole expandability, and manufacturing method therefor.
The applicant listed for this patent is POSCO. Invention is credited to Sung-Il KIM, Hyun-Taek NA, Seok-Jong SEO, Hwan-Goo SEONG.
Application Number | 20200325563 16/305603 |
Document ID | / |
Family ID | 1000004971846 |
Filed Date | 2020-10-15 |

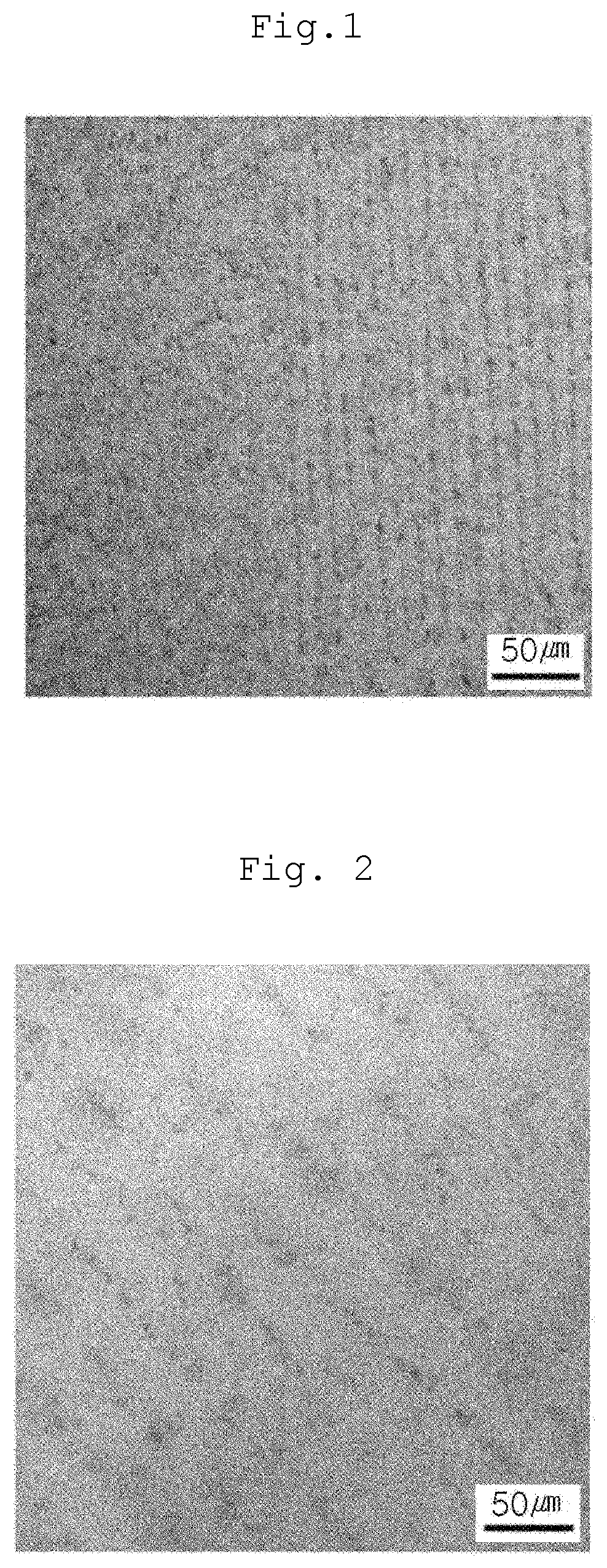
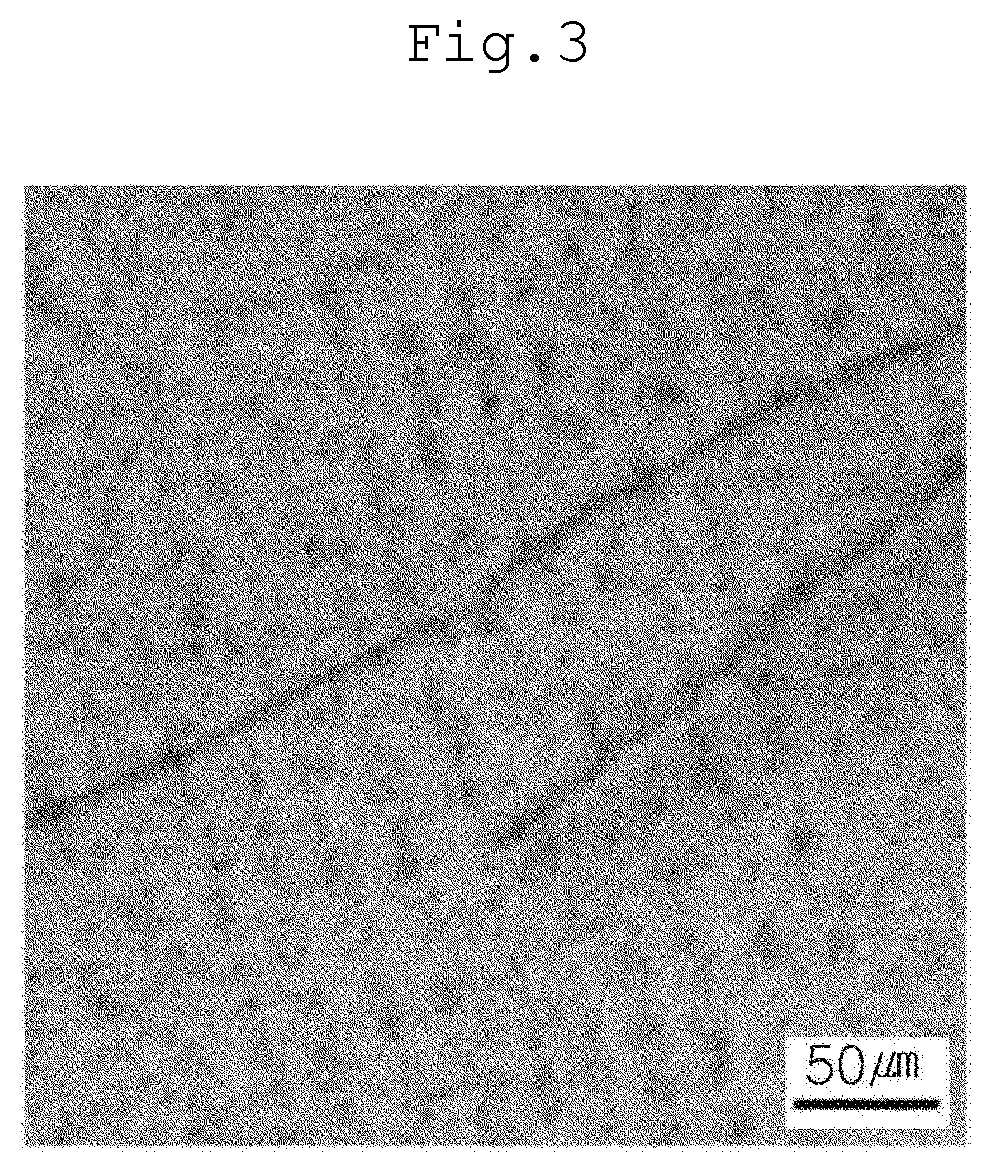


United States Patent
Application |
20200325563 |
Kind Code |
A1 |
NA; Hyun-Taek ; et
al. |
October 15, 2020 |
PRECIPITATION-HARDENING HOT ROLLED STEEL SHEET HAVING EXCELLENT
MATERIAL UNIFORMITY AND HOLE EXPANDABILITY, AND MANUFACTURING
METHOD THEREFOR
Abstract
Provided is a precipitation-hardening hot rolled steel sheet,
having excellent material uniformity and hole expandability,
comprising, by weight, 0.02% to 0.05% of C, 0.01% to 0.3% of Si,
1.0% to 1.6% of Mn, 0.04% to 0.1% of Ti, 0.01% to 0.05% of Nb,
0.008% or less of N, and a remainder of Fe and inevitable
impurities, satisfying Relationship 1, wherein a microstructure of
the precipitation-hardening hot rolled steel sheet comprises 95
area % or more of ferrite and (Ti, Nb)C complex precipitates, the
number of (Ti, Nb)C complex precipitates having a diameter of 10 nm
or less is five or more times the number of (Ti, Nb)C complex
precipitates having a diameter greater than 10 nm. Relationship 1:
0.35.ltoreq.(Ti+Nb+V+Mo)/(C+N) 0.70.
Inventors: |
NA; Hyun-Taek;
(Gwangyang-si, KR) ; SEONG; Hwan-Goo;
(Gwangyang-si, KR) ; SEO; Seok-Jong;
(Gwangyang-si, KR) ; KIM; Sung-Il; (Gwangyang-si,
KR) |
|
Applicant: |
Name |
City |
State |
Country |
Type |
POSCO |
Pohang-si |
|
KR |
|
|
Family ID: |
1000004971846 |
Appl. No.: |
16/305603 |
Filed: |
June 23, 2017 |
PCT Filed: |
June 23, 2017 |
PCT NO: |
PCT/KR2017/006668 |
371 Date: |
November 29, 2018 |
Current U.S.
Class: |
1/1 |
Current CPC
Class: |
C22C 38/001 20130101;
C21D 9/46 20130101; C21D 8/0205 20130101; C22C 38/14 20130101; C22C
38/02 20130101; C22C 38/12 20130101; C21D 8/0226 20130101; C22C
38/04 20130101 |
International
Class: |
C22C 38/14 20060101
C22C038/14; C22C 38/12 20060101 C22C038/12; C22C 38/04 20060101
C22C038/04; C22C 38/02 20060101 C22C038/02; C22C 38/00 20060101
C22C038/00; C21D 8/02 20060101 C21D008/02; C21D 9/46 20060101
C21D009/46 |
Foreign Application Data
Date |
Code |
Application Number |
Jun 23, 2016 |
KR |
10-2016-0078573 |
Claims
1. A precipitation-hardening hot rolled steel sheet, having
excellent material uniformity and hole expandability, comprising,
by weight, 0.02% to 0.05% of C, 0.01% to 0.3% of Si, 1.0% to 1.6%
of Mn, 0.04% to 0.1% of Ti, 0.01% to 0.05% of Nb, 0.008% or less of
N, and a remainder of Fe and inevitable impurities, satisfying
Relationship 1, wherein a microstructure of the
precipitation-hardening hot rolled steel sheet comprises 95 area %
or more of ferrite and (Ti, Nb)C complex precipitates, the number
of (Ti, Nb)C complex precipitates having a diameter of 10 nm or
less is five or more times the number of (Ti, Nb)C complex
precipitates having a diameter greater than 10 nm,
0.35.ltoreq.(Ti+Nb+V+Mo)/(C+N).ltoreq.0.70 Relationship 1: (In
Relationship 1, each element symbol refers to at. % of each
element, and an element not included in the steel sheet is
calculated as zero).
2. The precipitation-hardening hot rolled steel sheet according to
claim 1, wherein the hot rolled steel sheet satisfies Relationship
2: 0.04.ltoreq.(Ti+Nb+V+Mo)/(C+Mn+Si+Cr) Relationship 2: (In
Relationship 2, each element symbol refers to at. % of each
element, and an element not included in the steel sheet is
calculated as zero).
3. The precipitation-hardening hot rolled steel sheet according to
claim 1, wherein a distance between the (Ti, Nb)C complex
precipitates is 30 nm or less.
4. The precipitation-hardening hot rolled steel sheet according to
claim 1, wherein the (Ti, Nb)C complex precipitate is present in a
frequency of 15,000/.mu.m.sup.2 or more.
5. The precipitation-hardening hot rolled steel sheet according to
claim 1, wherein the hot rolled steel sheet has a tensile strength
of 590 MPa or more and material deviation in a width/length
direction within .+-.5% with respect to an average value.
6. A production method for a precipitation-hardening hot rolled
steel sheet, having excellent material uniformity and hole
expandability, comprising: continuous casting ingot steel
comprising, by weight, 0.02% to 0.05% of C, 0.01% to 0.3% of Si,
1.0% to 1.6% of Mn, 0.04% to 0.1% of Ti, 0.01% to 0.05% of Nb,
0.008% or less of N, and a remainder of Fe and inevitable
impurities, satisfying Relationship 1, to produce a thin slab;
rough rolling the thin slab to obtain a bar; heating or
concurrently heating the bar; finish rolling the heated bar to
obtain a hot rolled steel sheet; cooling and air cooling the hot
rolled steel sheet at a cooling rate of 30.degree. C./s or higher
to a temperature within a range of 600.degree. C. to 700.degree. C.
in a run-out table; and coiling the cooled hot rolled steel sheet
at a temperature within a range of 450.degree. C. to 600.degree.
C., 0.35.ltoreq.(Ti+Nb+V+Mo)/(C+N).ltoreq.0.70 Relationship 1: (In
Relationship 1, each element symbol refers to at. % of each
element, and an element not included in the steel sheet is
calculated as zero).
7. The production method according to claim 6, wherein the hot
rolled steel sheet satisfies Relationship 2:
0.04.ltoreq.(Ti+Nb+V+Mo)/(C+Mn+Si+Cr), Relationship 2: (In
Relationship 2, each element symbol refers to at. % of each
element, and an element not included in the steel sheet is
calculated as zero).
8. The production method according to claim 6, wherein a thickness
of the thin slab is 30 mm to 150 mm.
9. The production method according to claim 6, wherein a mass-flow
velocity of the hot rolled steel sheet in the run-out table is 100
mpm to 200 mpm, and a difference in velocity is 10% or less.
10. The production method according to claim 6, further comprising
coiling the heated bar between the heating operation and the finish
rolling operation.
11. The production method according to claim 6, wherein the rough
rolling operation is performed in a temperature within a range of
850.degree. C. to 1,150.degree. C.
12. The production method according to claim 6, wherein heating or
concurrently heating the bar in a temperature within a range of
850.degree. C. to 1,150.degree. C. in the heating operation.
13. The production method according to claim 6, wherein the finish
rolling operation is performed in a temperature within a range of
770.degree. C. to 1,000.degree. C.
Description
TECHNICAL FIELD
[0001] The present disclosure relates to a precipitation-hardening
hot rolled steel sheet, having excellent material uniformity and
hole expandability, and a manufacturing method therefor.
BACKGROUND ART
[0002] As known in the related art, in order to improve hole
expandability, it is necessary to suppress the occurrence of fine
cracks during a machining operation. In addition, when a difference
in hardness between a hard phase and a soft phase is relatively
high, deformation may be concentrated on, and fine cracks may occur
at, grain boundaries of two phases.
[0003] Patent Document 1 discloses a transformation-strengthening
steel in which a relatively large amount of bainite is formed to
prevent the occurrence of fine cracks, and to ensure hole
expandability.
[0004] Further, research has been carried out on the development of
precipitation-hardening steel materials capable of securing high
strength by precipitation-hardening effects using Ti, Nb, Mo, V, C,
and the like, on a ferrite main phase, to maximize hole
expandability and to secure high strength at the same time.
[0005] Patent Document 2 discloses a technique for securing
strength by realizing a ferrite-based soft main phase matrix
structure to prevent the occurrence of fine cracks due to a
difference in hardness between a soft phase and a hard phase in
advance, and by inducing a fine precipitation phenomenon in a
crystal grain during transformation from austenite to ferrite,
under conditions matching an Ar.sub.3 nose and a precipitation nose
after a strip mill rolling operation.
[0006] In the case of the precipitation-hardening steel material of
Patent Document 2, it can be confirmed that burring properties were
further improved while ensuring similar levels of strength in
materials, as compared to the transformation-strengthening steel
material. However, Patent Document 2 relates to a conventional
mill-process-based manufacturing method comprising: cooling a slab
to room temperature; and then reheating and rolling the cooled slab
again, but has a problem in which deviation in a material is
present in view of strength, elongation, hole expandability, or the
like, due to heterogeneity of the precipitation behavior by
deviation in a temperature in width and length directions after a
rolling operation, and conditions of a heating furnace.
[0007] Meanwhile, a Continuous Endless Mill (CEM) method, a new
process for milling steel that has gained attention recently and
which produces steel sheets by a so-called high-speed continuous
casting process and an endless rolling process, is known as a
process for obtaining a steel material having good deviation in a
material, because it has small deviation in a temperature in width
and longitudinal directions of the strip due to a characteristic
features of process.
[0008] As disclosed in Patent Documents 3 and 4, most of research
and development focuses on transformation-strengthening hot rolled
steel sheets such as DP steel and TRIP steel. However, the
above-described transformation-strengthening hot rolled steel
sheets may have a problem in ensuring excellent burring properties,
because a combination of a soft phase and a hard phase in steel is
inevitable.
[0009] Further, in the case of the solid solution strengthening hot
rolled steel sheet, the steel sheet may have a problem of
increasing manufacturing costs, because a large amount of solid
solution strengthening elements such as Si, Mn and Cr should be
added during the manufacturing operation of high strength steel
having a tensile strength of 590 MPa or more.
[0010] Meanwhile, there may be advantages, in that
precipitation-hardening steel materials have low manufacturing
costs and excellent burring properties. However, when
precipitation-hardening steel materials are manufactured by
applying a CEM method using a high-speed continuous casting process
and an endless rolling process, problems such as the occurrence of
casting cracks, the occurrence of edge cracks due to precipitation
elements such as Ti, Nb, N, or the like, and relatively low strip
mill rolling temperatures, deterioration of a passing ability due
to change in a deformation resistant behavior of the material by
Nb, or the like, may occur.
[0011] Accordingly, there is a need for development of a
precipitation-hardening hot rolled steel sheet which may address
the above-described problems to be applicable to the CEM method and
has excellent material uniformity and hole expandability, and a
manufacturing method therefor.
PRIOR ART DOCUMENT
[0012] Patent Document 1: Japanese Laid-Open Patent Publication No.
1994-200351
[0013] Patent Document 2: Japanese Laid-Open Patent Publication No.
2003-321739
[0014] Patent Document 3: Korean Patent Publication No.
2012-0049993
[0015] Patent Document 4: Korean Patent Publication No.
2012-0052022
DISCLOSURE
Technical Problem
[0016] An aspect of the present disclosure is to provide a
precipitation-hardening hot rolled steel sheet, having excellent
material uniformity and hole expandability, and a manufacturing
method therefor.
[0017] Meanwhile, the object of the present disclosure is not
limited to the above description. It will be understood by those of
ordinary skill in the art that there would be no difficulty in
understanding the additional problems of the present
disclosure.
Technical Solution
[0018] According to an aspect of the present disclosure, a
precipitation-hardening hot rolled steel sheet, having excellent
material uniformity and hole expandability, includes, by weight,
0.02% to 0.05% of C, 0.01% to 0.3% of Si, 1.0% to 1.6% of Mn, 0.04%
to 0.1% of Ti, 0.01% to 0.05% of Nb, 0.008% or less of N, and a
remainder of Fe and inevitable impurities, satisfying Relationship
1,
[0019] wherein a microstructure of the precipitation-hardening hot
rolled steel sheet comprises 95 area % or more of ferrite and (Ti,
Nb)C complex precipitates,
[0020] the number of (Ti, Nb)C complex precipitates having a
diameter of 10 nm or less is five or more times the number of (Ti,
Nb)C complex precipitates having a diameter greater than 10 nm.
0.35.ltoreq.(Ti+Nb+V+Mo)/(C+N).ltoreq.0.70 Relationship 1:
[0021] (In Relationship 1, each element symbol refers to at. % of
each element, and an element not included in the steel sheet is
calculated as zero.)
[0022] According to another aspect of the present disclosure, a
production method for a precipitation-hardening hot rolled steel
sheet, having excellent material uniformity and hole expandability,
includes:
[0023] continuous casting ingot steel satisfying the
above-described alloy composition to produce a thin slab;
[0024] rough rolling the thin slab to obtain a bar;
[0025] heating or concurrently heating the bar;
[0026] finish rolling the heated bar to obtain a hot rolled steel
sheet;
[0027] cooling and air cooling the hot rolled steel sheet at a
cooling rate of 30.degree. C./s or higher to a temperature within a
range of 600.degree. C. to 700.degree. C. in a run-out table; and
coiling the cooled hot rolled steel sheet at a temperature within a
range of 450.degree. C. to 600.degree. C.
Advantageous Effects
[0028] According to an aspect of the present disclosure, a
precipitation-hardening hot rolled steel sheet and a production
method therefor, having a tensile strength of 590 MPa or more and
material deviation in a width/length direction within .+-.5% with
respect to an average value, and having excellent material
uniformity and hole expandability, may be provided.
DESCRIPTION OF DRAWINGS
[0029] FIG. 1 is an image of a microstructure of Inventive Example
1 captured by a scanning electron microscope;
[0030] FIG. 2 is an image of a microstructure of Comparative
Example 1 captured by a scanning electron microscope; and
[0031] FIG. 3 is an image of a microstructure of Comparative
Example 7 captured by a scanning electron microscope.
BEST MODE FOR INVENTION
[0032] Hereinafter, preferred embodiments of the present disclosure
will be described. However, the embodiments of the present
disclosure can be modified into various other forms, and the scope
of the present disclosure is not limited to the embodiments
described below. Further, the embodiments of the present disclosure
are provided to more fully explain the present disclosure to those
skilled in the art.
[0033] The present inventors have recognized that when
precipitation-hardening steel materials are manufactured by
applying the CEM method using a high-speed continuous casting
process and an endless rolling process, problems such as the
occurrence of casting cracks, the occurrence of edge cracks due to
precipitation elements such as Ti, Nb, N, or the like, and
relatively low strip mill rolling temperature, deterioration of a
passing ability due to change in a deformation resistant behavior
of the material by Nb, or the like, may occur, and have conducted a
deep investigation into solving these problems.
[0034] As a result, it has been confirmed that a
precipitation-hardening hot rolled steel sheet, applying the CEM
method using a high-speed continuous casting process and an endless
rolling process to have excellent material uniformity and hole
expandability, may be provided by precisely controlling the alloy
composition and manufacturing method, thereby completing the
present disclosure.
[0035] Hereinafter, a precipitation-hardening hot rolled steel
sheet, having excellent material uniformity and hole expandability,
according to an aspect of the present disclosure will be described
in detail.
[0036] The precipitation-hardening hot rolled steel sheet, having
excellent material uniformity and hole expandability, according to
an aspect of the present disclosure, includes, by weight, 0.02% to
0.05% of C, 0.01% to 0.3% of Si, 1.0% to 1.6% of Mn, 0.04% to 0.1%
of Ti, 0.01% to 0.05% of Nb, 0.008% or less of N, and a remainder
of Fe and inevitable impurities, satisfying Relationship 1, wherein
a microstructure of the precipitation-hardening hot rolled steel
sheet comprises 95 area % or more of ferrite and (Ti, Nb)C complex
precipitates, the number of (Ti, Nb)C complex precipitates having a
diameter of 10 nm or less is five or more times the number of (Ti,
Nb)C complex precipitates having a diameter greater than 10 nm.
0.35.ltoreq.(Ti+Nb+V+Mo)/(C+N).ltoreq.0.70 Relationship 1:
[0037] (In Relationship 1, each element symbol refers to at. % of
each element, and an element not included in the steel sheet is
calculated as zero.)
[0038] First, an alloy composition of the precipitation-hardening
hot rolled steel sheet, having excellent material uniformity and
hole expandability, according to an aspect of the present
disclosure will be described in detail.
[0039] Hereinafter, the unit of each element content is % by
weight.
[0040] C: 0.02% to 0.05%
[0041] C may be the most economical and effective element to
strengthen steel. Meanwhile, C may cause a volume shrinkage
phenomenon during transformation of liquid+ferrite.fwdarw.austenite
in a solidification operation of a high-speed casting process, and
may promote occurrence of surface cracks, when the content thereof
is present in the hypoperitectic composition.
[0042] When the content of C exceeds 0.05%, surface cracks may
occur during a high-speed continuous casting process. Meanwhile,
when the content of C is lower than 0.02%, strength and weldability
may significantly deteriorate.
[0043] Si: 0.01% to 0.3%
[0044] Si may be an element stabilizing ferrite by removing oxygen
from ingot steel. Si may promote ferrite transformation during a
cooling operation after a hot rolling operation. Therefore, Si may
help to form a uniform ferrite structure, and to secure high
strength material by a solid solution strengthening effect.
[0045] When the content of Si is lower than 0.01%, the
above-mentioned effects may be insufficient. Meanwhile, when the
content of Si is higher than 0.3%, the solid solution strengthening
effect may be greater than the precipitation hardening effect. In
addition, a red color scale due to Si may be formed on a surface of
the steel sheet during a hot rolling operation. Therefore, a more
preferable upper limit of the Si content is 0.2%, and a still more
preferable upper limit of the Si content is 0.1%.
[0046] Mn: 1.0% to 1.6%
[0047] Mn, in a similar manner as Si, may be an effective element
for solid solution strengthening steel.
[0048] When the content of Mn is lower than 1.0%, sufficient
strength of the welded portion may be difficult to be secured by a
scheme adding the above-mentioned low content of C. Meanwhile, when
the content of Mn exceeds 1.6%, the ferrite transformation may be
delayed excessively, a sufficient precipitation effect may not be
realized, and carbide or pearlite may be formed in the structure to
lower the burring property. Therefore, the content of Mn according
to the present disclosure is preferably limited to be 1.0% to
1.6%.
[0049] Ti: 0.04% to 0.1%
[0050] Ti may be an element capable of maximizing an increase in
strength due to a fine precipitation effect at an interphase (Ti,
Nb)C upon transformation from austenite to ferrite.
[0051] When the content of Ti is lower than 0.04%, a sufficient
fine precipitation effect may be not easy to be secured due to N
that is inevitably included in the steelmaking process. Meanwhile,
when the content of Ti exceeds 0.1%, a fine precipitation effect
may be saturated, and surplus Ti may be present after the formation
of fine precipitates, which is economically undesirable.
[0052] Nb: 0.01% to 0.05%
[0053] Nb may be an important element for the formation of (Ti,
Nb)C fine precipitates together with Ti, and may be an element
useful for forming a fine ferrite grain size.
[0054] When the content of Nb is lower than 0.01%, the
above-described effect may be difficult to be realized. Meanwhile,
when the content of Nb exceeds 0.05%, a temperature of the
non-recrystallized zone of the material may rise, which may cause a
load problem during a rolling operation.
[0055] N: 0.008% or Less
[0056] N may have a great effect on mechanical properties of steel
even in an extremely small amount. N may increase tensile strength
and yield strength. N may be a main factor of strain aging, which
lowers an elongation rate, causes blue brittleness, deteriorates
the impact characteristics of the material, and particularly
wrinkles on a surface during a thin sheet processing. Further,
since nitrogen, together with other alloying elements, forms a
nitride, the (Ti, Nb)C fine precipitation effect which is important
in the present disclosure may be reduced.
[0057] Therefore, in the present disclosure, N may be considered as
an impurity, and the content thereof is preferable to be strictly
controlled to be 0.008% or less.
[0058] The remainder of the present disclosure may be iron (Fe). In
the ordinary manufacturing process, impurities that are not
intended from the raw material or the surrounding environment may
be inevitably incorporated. Therefore, the impurities may not be
excluded. The impurities are not specifically mentioned in this
specification, as are known to any person skilled in the art of
steel manufacturing. For example, P, S, Cu, V, Ni, Al, Cr, and the
like, may be inevitably incorporated.
[0059] In the present disclosure, not only the above-described
content of each element should be satisfied, but also, Relationship
1 should be satisfied.
0.35.ltoreq.(Ti+Nb+V+Mo)/(C+N).ltoreq.0.70 Relationship 1:
[0060] (In Relationship 1, each element symbol refers to at. % of
each element, and an element not included in the steel sheet is
calculated as zero.)
[0061] The metallurgical significance of Relationship 1 is to take
into account the optimum atomic ratio in consideration of loss of
Ti, Nb, V, and Mo due to initial coarse precipitation by C and N,
to maximize the fine precipitation behavior. Considering this
equivalence ratio in advance, steels having excellent burring
property with relatively low alloying iron costs may be
manufactured by minimizing the content of elements such as Si, Cr,
and the like.
[0062] When the value of Relationship 1 is lower than 0.35,
sufficient (Ti, Nb)C precipitates may be difficult to secure in the
ferrite, and strength of the material may be insufficient.
Meanwhile, when the value of Relationship 1 is higher than 0.70,
the effect of the surplus Ti, Nb, V, Mo remaining after the
formation of the complex precipitate by chemical bonding with C on
the basis of the equivalence ratio may be relatively small, and may
have a negative impact on securing economic efficiency.
[0063] In addition, not only the content of each of the above
elements and the value of Relationship 1 should be satisfied, but
also the value of Relationship 2 should be satisfied.
0.04.ltoreq.(Ti+Nb+V+Mo)/(C+Mn+Si+Cr) Relationship 2:
[0064] (In Relationship 2, each element symbol refers to at. % of
each element, and an element not included in the steel sheet is
calculated as zero.)
[0065] Relationship 2 is based on the atomic ratio of precipitation
elements (Ti, Nb, Mo, and V) and solid solution elements (C, Si,
Mn, and Cr), and is to secure a desired tensile strength by the
precipitation hardening.
[0066] When the value of Relationship 2 is lower than 0.04, an
effect of solid solution strengthening is greater than an effect of
precipitation hardening. To satisfy tensile strength of 590 MPa or
more, a large amount of solid solution strengthening elements such
as Si, Mn, Cr, and the like, should be added. Therefore, there is a
problem in that the manufacturing costs thereof may be
increased.
[0067] A microstructure of the precipitation-hardening hot rolled
steel sheet, having excellent material uniformity and hole
expandability, according to an aspect of the present disclosure may
include 95 area % or more of ferrite and (Ti, Nb)C complex
precipitates. In addition, the number of (Ti, Nb)C complex
precipitates having a diameter of 10 nm or less may be formed to be
five or more times the number of (Ti, Nb)C complex precipitates
having a diameter greater than 10 nm. In the present disclosure,
the (Ti, Nb)C complex precipitate may be a concept including TiC,
NbC, and (Ti, Nb)C complex carbide, and the diameter refers to a
circle equivalent diameter.
[0068] When the content of ferrite is lower than 95 area %, a
relatively large amount of a structure having a relatively large
difference between the phases in hardness may be present, as
compared to pearlite and ferrite such as low-temperature
transformation phase.
[0069] When the number of (Ti, Nb)C complex precipitates having a
diameter of 10 nm or less is lower than five times the number of
(Ti, Nb)C complex precipitates having a diameter greater than 10
nm, the precipitation hardening effect may be insufficient and the
tensile strength may be deteriorated.
[0070] The fact that the number of (Ti, Nb)C complex precipitates
having a diameter of 10 nm or less is formed at five or more times
the number of (Ti, Nb)C complex precipitates having a diameter
greater than 10 nm means that the value of Relationship 3:
.PHI. = d = 0 1 0 P N .times. ( d = 1 0 2 0 P N + d = 2 O 50 P N +
d = 5 0 1 0 0 P N ) - 1 ##EQU00001##
[0071] Relationship 3:
[0072] In Relationship 3, PN is the number of (Ti, Nb)C complex
precipitates in a structure of the hot rolled steel sheet, and d is
a diameter of the complex precipitate captured by a transmission
microscope (TEM), and the unit thereof is nm.
[0073] .SIGMA..sub.d=0.sup.10PN, .SIGMA..sub.d=10.sup.20PN,
.SIGMA..sub.d=20.sup.50PN, .SIGMA..sub.d=50.sup.100PN refer to the
number of precipitates having diameters of greater than 0 nm to 10
nm, greater than 10 nm to 20 nm, greater than 20 nm to 50 nm, and
greater than 50 nm to 100 nm, respectively. In addition,
precipitates exceeding 100 nm are almost not present, and may thus
be excluded.
[0074] At this time, a distance between the (Ti, Nb)C complex
precipitates may be 30 nm or less.
[0075] More specifically, the distance refers to a line-spacing
(LS) of interphase precipitation, present in a curved or straight
form in series, when observed by Transmission Electron Microscopy
(TEM) analysis based on [001] or [110] zone axis, may be 30 nm or
less.
[0076] When a distance between the (Ti, Nb)C complex precipitates
is greater than 30 nm, a problem in which the effect of fine
precipitation on strength is remarkably reduced, may occur. The
lower limit thereof is not particularly limited, but may be 5 nm or
more.
[0077] In addition, the (Ti, Nb)C complex precipitate may be
present in a frequency of 15,000/.mu.m.sup.2 or more.
[0078] Even in the case that a distance between the (Ti, Nb)C
complex precipitates is 30 nm or less, when the (Ti, Nb)C complex
precipitate is lower than 15,000/.mu.m.sup.2, distribution of
uniform and fine precipitates may be not realized over the entire
area within the crystal grain, and the burring workabilities may
not be easy to be secured.
[0079] Meanwhile, the hot rolled steel sheet according to the
present disclosure may have a tensile strength of 590 MPa or more
and material deviation in a width/length direction within .+-.5%
with respect to an average value. Not only material deviation in
view of strength and elongation, but also material deviation in
view of hole expandability, may be secured in a good level.
[0080] Hereinafter, a production method for a
precipitation-hardening hot rolled steel sheet, having excellent
material uniformity and hole expandability, which is another aspect
of the present disclosure, will be described in detail.
[0081] The precipitation-hardening hot rolled steel sheet, having
excellent material uniformity and hole expandability, which is
another aspect of the present disclosure, includes:
[0082] continuous casting ingot steel satisfying the
above-described alloy composition to produce a thin slab;
[0083] rough rolling the thin slab to obtain a bar;
[0084] heating or concurrently heating the bar;
[0085] finish rolling the heated bar to obtain a hot rolled steel
sheet;
[0086] cooling and air cooling the hot rolled steel sheet at a
cooling rate of 30.degree. C./s or higher to a temperature within a
range of 600.degree. C. to 700.degree. C. in a run-out table;
and
[0087] coiling the cooled hot rolled steel sheet at a temperature
within a range of 450.degree. C. to 600.degree. C.
[0088] Continuous Casting Operation
[0089] A thin slab may be prepared by continuously casting ingot
steel satisfying the above-described alloy composition.
[0090] At this time, a thickness of the thin slab may be 30 mm to
150 mm. The thin slab may be compared to slabs of 200 mm or more
produced from continuous casting machines of conventional mills.
Since the slabs of 200 mm or more produced in the prior art are
completely cooled in a yard, etc., it is necessary to sufficiently
reheat the steel sheet to a surface temperature of 1100.degree. C.
or more in a reheating furnace before performing a hot rolling
operation. Meanwhile, since the thin slab may be transported
directly to a rough rolling mill without going through the
reheating furnace, heat in the continuous casting operation may be
used as it is. Therefore, energy may be saved, and productivity may
be greatly improved.
[0091] Rough Rolling Operation
[0092] The thin slab may be rough rolled to obtain a bar. At this
time, the rough rolling operation may be performed at a temperature
within a range of 850.degree. C. to 1,150.degree. C. When the rough
rolling temperature is lower than 850.degree. C., cracks may easily
occur at an edge portion. When the rough rolling temperature is
higher than 1,150.degree. C., cracks may easily occur on a surface
of the thin slab during a rolling operation.
[0093] Heating Operation
[0094] The bar may be heated or concurrently heated. At this time,
the heating or concurrent heating may be a temperature within a
range of 850.degree. C. to 1,150.degree. C. When the temperature is
lower than 850.degree. C., a rolling load may be considerably
increased during a finish rolling operation. When the temperature
exceeds 1,150.degree. C., energy costs for temperature rise may
increase, and the tendency of surface scale defects occurring may
increase.
[0095] At this time, an operation of coiling the heated bar after
the above heating operation and before the subsequent finish
rolling operation may be further included.
[0096] Finish Rolling Operation
[0097] The heated bar may be subjected to a finish rolling
operation to obtain a hot rolled steel sheet. At this time, the
finish rolling operation may be performed in a temperature within a
range of 770.degree. C. to 1,000.degree. C. When the finish rolling
temperature is lower than 770.degree. C., the effect of the rolling
operation in a two-phase region may be strengthened, and the
desired material due to a severe anisotropy of the structure may be
difficult to secure.
[0098] Meanwhile, it is necessary to heat the steel sheet at a high
temperature of 1,150.degree. C. or more in the heating operation,
to control the finish rolling temperature to exceed 1,000.degree.
C. Therefore, surface scale defects may result, and high costs may
be required economically.
[0099] Cooling Operation
[0100] The hot rolled steel sheet may be cooled and air cooled in a
run-out table to a temperature within a range of 600.degree. C. to
700.degree. C. at a cooling rate of 30.degree. C./s or higher. When
the cooling end temperature is out of the temperature range of
600.degree. C. to 700.degree. C., the fine precipitation behavior
which occurs upon ferrite transformation in the austenite may not
be sufficiently realized. When the cooling rate is lower than
30.degree. C./s, even if the cooling end temperature is satisfied,
the ferrite transformation of a substantial fraction prior to the
air cooling operation may be carried out, a fraction of ferrite to
secure micro precipitates may be remarkably reduced, and, thus, a
material having a desired strength may be not secured.
[0101] At this time, a mass-flow velocity of the hot rolled steel
sheet in the run-out table may be 100 mpm to 200 mpm, and a
difference in velocity may be 10% or less.
[0102] Coiling Operation
[0103] The cooled hot rolled steel sheet may be coiled at a
temperature within a range of 450.degree. C. to 600.degree. C. When
the cooled hot rolled steel sheet is coiled at a temperature of
less than 450.degree. C., it may be very difficult to control the
temperature uniformly by entering a boiling transition zone.
Therefore, incorporation of a hard phase such as martensite and
bainite may be caused, and burring properties may be remarkably
reduced. Meanwhile, when the cooled hot rolled steel sheet is
coiled at a temperature of higher than 600.degree. C., another hard
phase such as cementite may be formed, and burring property may be
reduced.
MODE FOR INVENTION
[0104] Hereinafter, the present disclosure will be described more
specifically by way of examples. It should be noted, however, that
the following examples are intended to illustrate the present
disclosure in more detail, and not to limit the scope of the
present disclosure. The scope of the present disclosure is
determined by the matters described in the claims and the matters
reasonably deduced therefrom.
[0105] Ingot steel having a component composition shown in Table 1
below was prepared.
[0106] Except for Comparative Examples 5, 6 and 7, a thin slab of
90 mm in thickness was prepared through a high-speed casting
operation by applying a CEM process. The thin slab was rough rolled
at a temperature of 1,000.degree. C., without cooling to room
temperature. The rough rolled thin slab was subjected to a finish
rolling operation at the finish rolling temperature (FDT) shown in
Table 2 below, cooled and air cooled to a temperature of
650.degree. C. at the cooling rate and the mass-flow velocity shown
in Table 2 below, and then coiled at the coiling temperature (CT)
shown in Table 2 below, to prepare a hot rolled steel sheet.
[0107] In the case of Comparative Examples 5, 6 and 7, slabs having
a thickness of 220 mm were manufactured by applying a conventional
milling method. The slabs were cooled to room temperature, and then
subjected to a reheating operation (1250.degree. C.) and a rough
rolling operation (1,000.degree. C.) (FDT). The rough rolled slab
was subjected to a finish rolling operation at the finish rolling
temperature (FDT) shown in Table 2 below, cooled and air cooled to
a temperature of 650.degree. C. at the cooling rate and the
mass-flow velocity shown in Table 2 below, and then coiled at the
coiling temperature (CT) shown in Table 2 below, to prepare a hot
rolled steel sheet.
[0108] The number of precipitates, the value of Relationship 3, the
material uniformity, the hole expandability, the tensile strength
(TS), the fracture elongation (El), and the ferrite fraction were
measured or evaluated, depending on the sizes of the hot rolled
steel sheet, as shown in Table 3.
[0109] The tensile test was carried out on specimens taken in
accordance with JIS-5 standard in a 90.degree. direction, with
respect to a rolling direction of the rolled plate. For the ferrite
phase fraction, specimens of the rolled plate were etched with
Nital etchant solution and LePera etchant solution, respectively,
observed by an optical microscope at a magnification of 500 times,
and analyzed and compared using an image analyzer.
[0110] Evaluation of hole extensibility was carried out by
preparing a square specimen, 120 mm square, punching a hole having
a diameter of 10 mm at the center of the specimen through a
punching operation, and pushing a cone upwardly while placing the
burrs in an upward direction, and was expressed as a value obtained
by calculating a diameter of the hole expanded until just before
occurring cracks in the circumference portion as a percentage of
the initial hole diameter (10 mm).
[0111] In order to confirm whether not only material deviation of
strength, elongation, and the like, but also material deviation of
hole expandability, may be secured, the material deviation of hole
expandability in a width/length direction was measured. When
material deviation of hole expandability in a width/length
direction is within .+-.5% with respect to an average value, it is
indicated as good. Meanwhile, when material deviation of hole
expandability in a width/length direction exceeds .+-.5%, it is
indicated as bad.
[0112] Precipitates were observed and analyzed in the area of about
1,400,000 nm.sup.2 in the hot rolled steel sheet using a TEM, based
on zone [100] axis. Interphase precipitation in a curved or
straight form was observed along the face (331).
.PHI. = d = 0 1 0 P N .times. ( d = 1 0 2 0 P N + d = 2 O 50 P N +
d = 5 0 1 0 0 P N ) - 1 ##EQU00002##
[0113] Relationship 3:
[0114] In Relationship 3, PN is the number of (Ti, Nb)C complex
precipitates in a structure of the hot rolled steel sheet, and d is
a diameter of the complex precipitate captured by a transmission
microscope (TEM), and the unit thereof is nm.
[0115] .SIGMA..sub.d=0.sup.10PN, .SIGMA..sub.d=10.sup.20PN,
.SIGMA..sub.d=20.sup.50PN, .SIGMA..sub.d=50.sup.100PN refer to the
number of precipitates having diameters of greater than 0 nm to 10
nm, greater than 10 nm to 20 nm, greater than 20 nm to 50 nm, and
greater than 50 nm to 100 nm, respectively, and these were
expressed in Table 3 below as PN10, PN20, PN50, and PN100,
respectively.
TABLE-US-00001 TABLE 1 C Si Mn Nb Ti N
.sup..star-solid..star-solid..star-solid.RE1 RE2
.sup..star-solid..star-solid.CE1 0.038 0.060 1.435 0.014 0.045
0.008 0.292 0.039 CE2 0.044 0.064 1.447 0.014 0.049 0.008 0.277
0.041 CE3 0.050 0.059 1.403 0.003 0.067 0.008 0.302 0.052 CE4 0.040
0.088 1.429 0.005 0.055 0.007 0.314 0.041 CE5 0.030 0.050 1.400
0.010 0.070 0.004 0.564 0.058 CE6 0.045 0.060 1.400 0.011 0.075
0.006 0.404 0.061 CE7 0.050 0.065 1.500 0.010 0.100 0.006 0.455
0.071 CE8 0.030 0.050 1.400 0.010 0.070 0.004 0.564 0.058
.sup..star-solid.IE1 0.049 0.069 1.427 0.014 0.076 0.007 0.360
0.061 IE2 0.046 0.067 1.418 0.014 0.066 0.007 0.391 0.054 IE3 0.049
0.077 1.416 0.011 0.077 0.007 0.377 0.061 IE4 0.043 0.080 1.553
0.013 0.081 0.006 0.457 0.059 IE5 0.030 0.050 1.400 0.010 0.070
0.004 0.564 0.058 IE6 0.044 0.061 1.472 0.011 0.075 0.006 0.412
0.058 IE7 0.030 0.050 1.400 0.010 0.085 0.006 0.644 0.069
.sup..star-solid.IE: Inventive Example,
.sup..star-solid..star-solid.CE: Comparative Example,
.sup..star-solid..star-solid..star-solid.RE: Relationship
[0116] In Table 1, the unit of each element content was % by
weight, and Relationships 1 and 2 were as follows:
0.35.ltoreq.(Ti+Nb+V+Mo)/(C+N).ltoreq.0.70 Relationship 1:
0.04.ltoreq.(Ti+Nb+V+Mo)/(C+Mn+Si+Cr) Relationship 2:
[0117] (In Relationships 1 and 2, each element symbol refers to at.
% of each element, and an element not included in the steel sheet
is calculated as zero.)
TABLE-US-00002 TABLE 2 Cooling Mass-Flow FDT Rate CT Velocity
Process (.degree. C.) (.degree. C./s) (.degree. C.) (mpm) **CE1 CEM
808 23 622 190 CE2 CEM 778 22 596 190 CE3 CEM 769 32 506 190 CE4
CEM 764 24 566 190 CE5 ***Conv. Mill 880 28 601 410 CE6 Conv. Mill
859 26 599 410 CE7 Conv. Mill 877 27 610 410 CE8 CEM 778 24 581 190
*IE1 CEM 770 35 481 190 IE2 CEM 771 33 501 190 IE3 CEM 774 36 477
190 IE4 CEM 769 30 523 190 IE5 CEM 771 33 499 190 IE6 CEM 770 31
514 190 IE7 CEM 779 32 514 190 *IE: Inventive Example, **CE:
Comparative Example, ***Conv. Mill: Conventional Mill
TABLE-US-00003 TABLE 3 TS E1
.sup..star-solid..star-solid..star-solid.HE
.sup..star-solid..star-solid..star-solid..star-solid.MU Ferrite
PN10 PN20 PN50 PN100 RE(3) (MPa) (%) (%) (%) (area %)
.sup..star-solid..star-solid.CE1 14520 5720 4230 30 1.45 543 28 130
4 97 CE2 11250 2230 1940 0 2.70 511 31 140 3 98 CE3 18010 4010 2110
0 2.94 551 27 121 5 98 CE4 20940 4240 710 0 4.23 505 24 134 4 98
CE5 11790 19470 670 0 0.59 699 21 93 20 98 CE6 13920 16550 1140 0
0.79 674 21 89 16 97 CE7 19540 14760 2120 0 1.16 601 23 91 21 97
CE8 7643 3710 1430 0 1.48 537 25 119 6 96 .sup..star-solid.IE1
29830 1810 260 0 14.41 644 23 101 4 97 IE2 41750 3320 220 0 11.79
598 24 99 3 97 IE3 24510 330 70 0 61.28 609 22 97 2 96 IE4 17270
2910 170 0 5.61 640 21 105 4 98 IE5 35880 1180 220 0 25.63 599 24
92 3 97 IE6 21190 1910 190 0 10.09 617 25 109 4 96 IE7 33490 2140
240 0 14.07 607 25 120 2 96 .sup..star-solid.IE.: Inventive
Example, .sup..star-solid..star-solid.CE.: Comparative Example, RE:
Relationship, .sup..star-solid..star-solid..star-solid.HE: hole
expandability,
.sup..star-solid..star-solid..star-solid..star-solid.MU: material
uniformity
[0118] In Inventive Examples 1 to 7 satisfying all of the
requirements of the present disclosure, it can be confirmed that
both material uniformity and the hole expandability were excellent,
and the tensile strength of 590 MPa or more was also secured.
[0119] Meanwhile, the content of each element in Comparative
Examples 1 and 2 was in the effective range proposed by the present
disclosure, but did not satisfy Relationship 1. In addition, the
content of each element in Comparative Examples 3 and 4 did not
satisfy the Nb content and Relationship 1. It can be confirmed that
hole expandability thereof is excellent, but since a sufficient
precipitation-hardening effect may not be realized, tensile
strength thereof is low.
[0120] In the case of Comparative Examples 5, 6 and 7, the case of
applying the conventional milling method, it can be confirmed that
tensile strength thereof was excellent, but material uniformity was
deteriorated.
[0121] In the case of Comparative Examples 5 and 8 and Inventive
Example 5, the compositions thereof were the same as each other,
but the manufacturing conditions thereof were different to each
other. In the case of Comparative Example 5, it can be confirmed
that material uniformity thereof was poor due to the conventional
milling process. In the case of Comparative Example 8, it can be
confirmed that material uniformity and tensile strength thereof are
both excellent.
[0122] FIGS. 1, 2, and 3 are images of microstructure of Inventive
Example 1, Comparative Example 1, and Comparative Example 7,
respectively, captured by a scanning electron microscope. Compared
with FIGS. 2 and 3, it can be seen from FIG. 1 that fine and
uniform (Ti, Nb)C complex precipitates were formed in Inventive
Example 1.
[0123] While exemplary embodiments have been shown and described
above, it will be apparent to those skilled in the art that
modifications and variations could be made without departing from
the scope of the present disclosure as defined by the appended
claims.
* * * * *