U.S. patent application number 16/569664 was filed with the patent office on 2020-09-17 for free-cut warp-knitted elastic fabric and method for production thereof.
The applicant listed for this patent is Pacific (Panyu) Textiles Ltd. Invention is credited to Baohong Hu, Yanfang Lai, Changsheng Peng, Lihong Qiu, Junbiao Wan, Xue Xiao, Xiangjiao Xie, Hualan Xu, Chun Wah Samuel Yeung, Gui Zhang, Shuying Zhang.
Application Number | 20200291556 16/569664 |
Document ID | / |
Family ID | 1000004348256 |
Filed Date | 2020-09-17 |
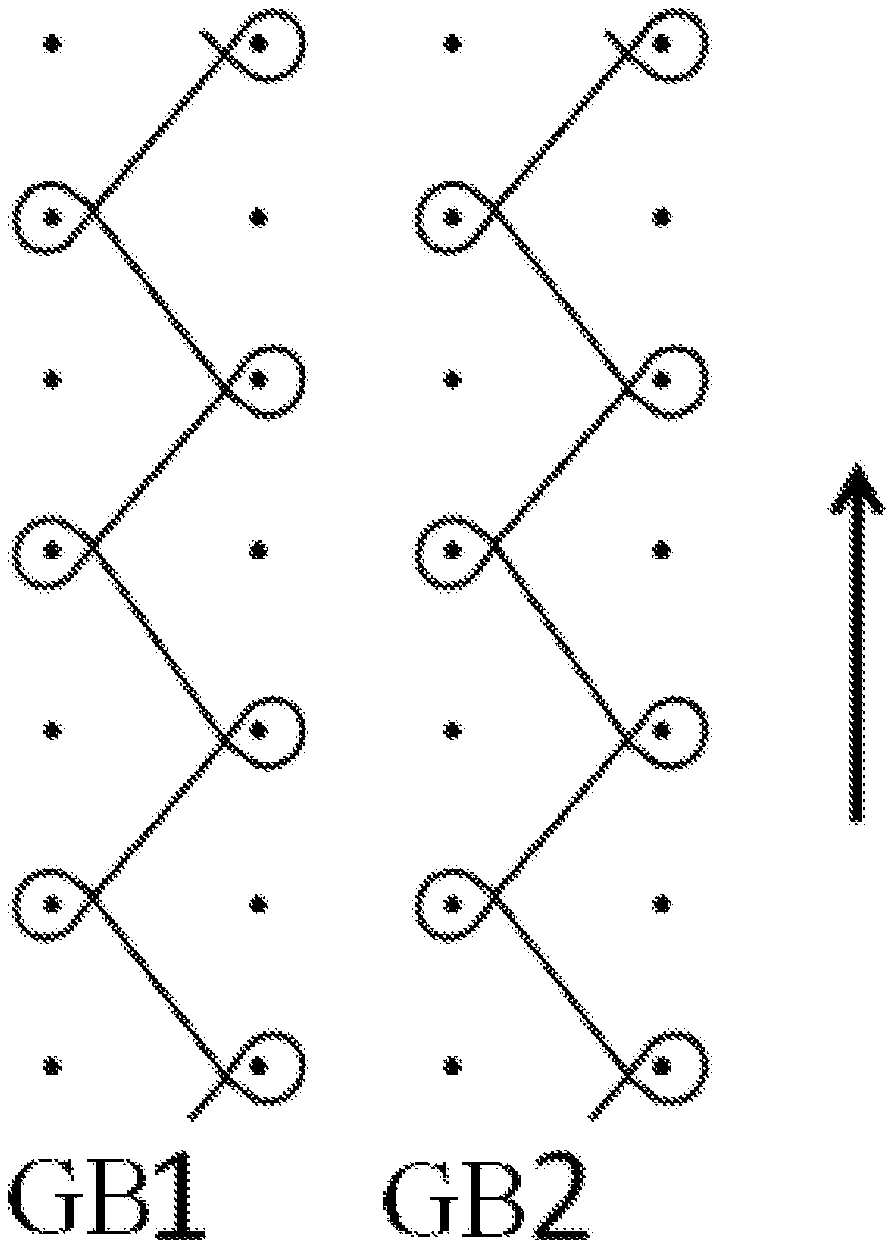
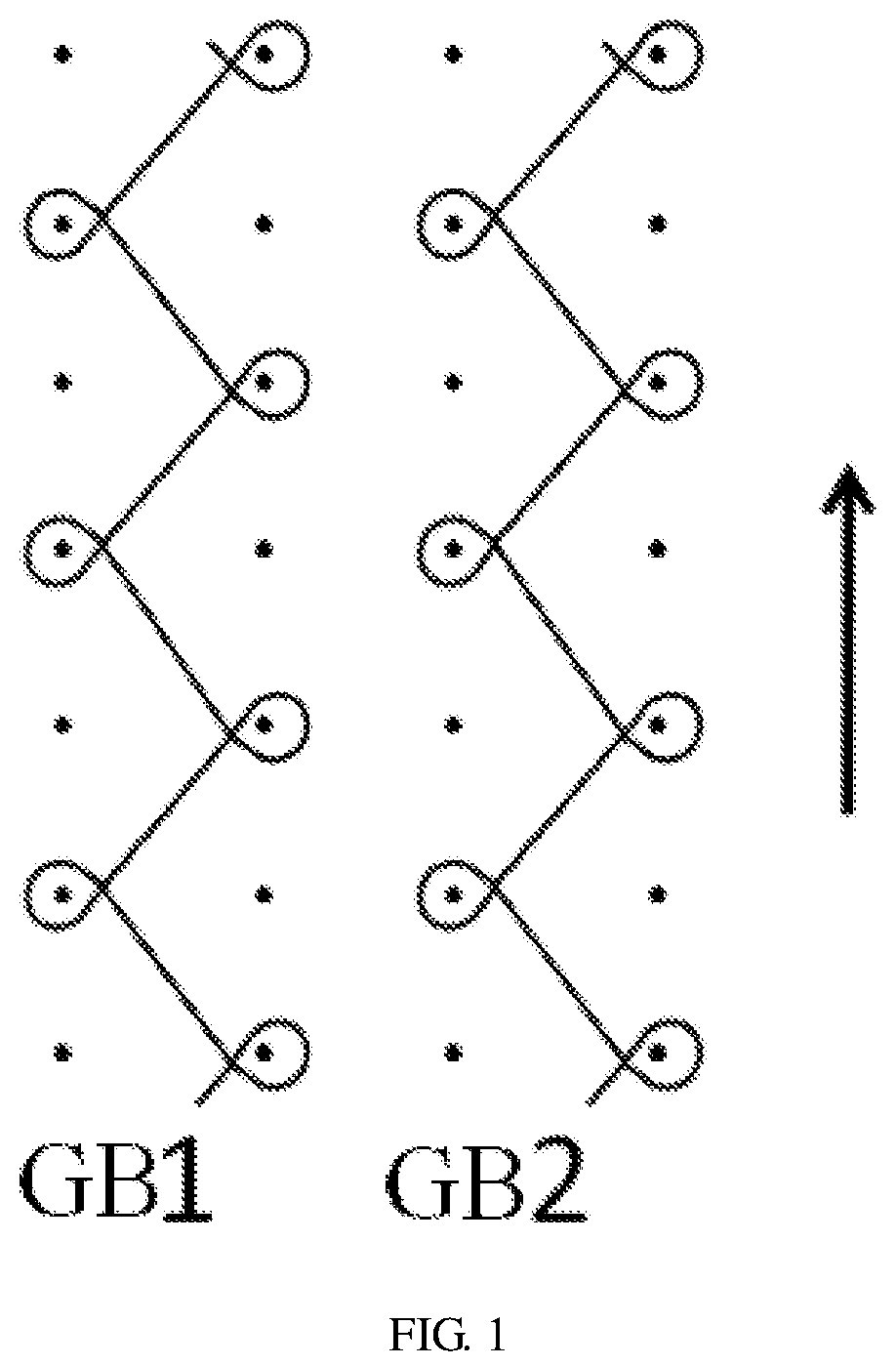
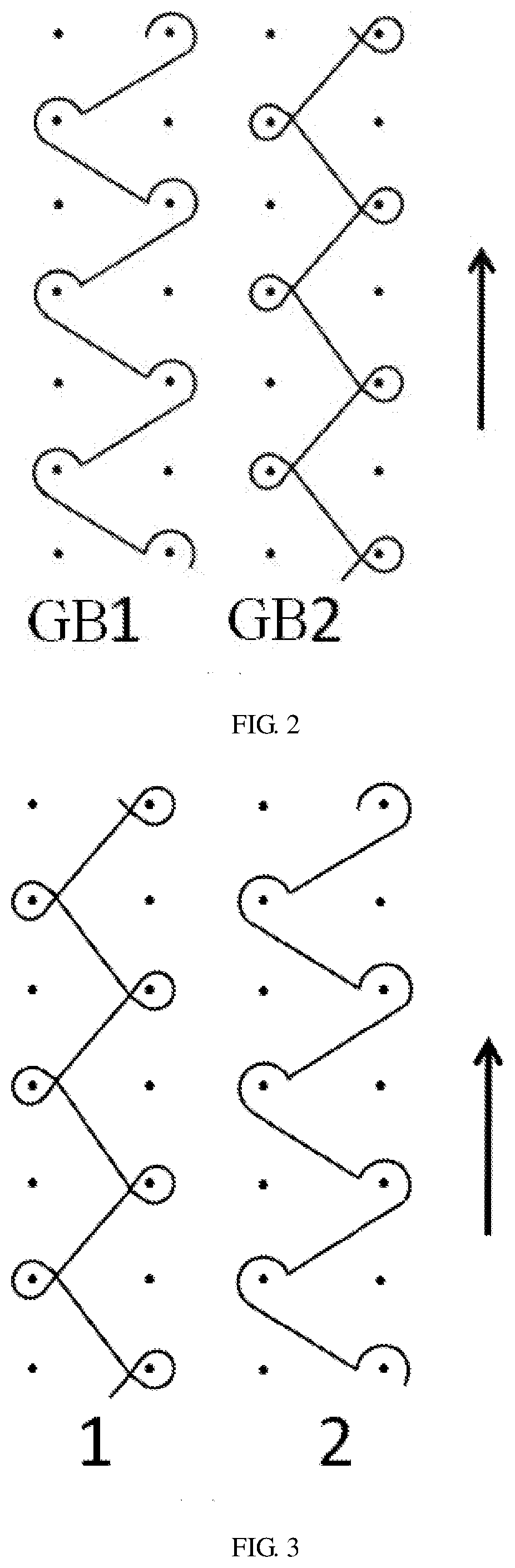
United States Patent
Application |
20200291556 |
Kind Code |
A1 |
Peng; Changsheng ; et
al. |
September 17, 2020 |
FREE-CUT WARP-KNITTED ELASTIC FABRIC AND METHOD FOR PRODUCTION
THEREOF
Abstract
The present invention provides a free-cut warp-knitted elastic
fabric and a method for production thereof. The method uses a first
guide bar and a second guide bar of a tricot warp knitting machine
for knitting, wherein a non-elastic yarn passes across a guide
needle of the first guide bar and forms the surface of the fabric
by knitting via two needles in a 1.times.1 warp plain stitch loop
mode, and an elastic yarn passes across a guide needle of the
second guide bar and forms the inside of the fabric by knitting
with the aforementioned non-elastic yarn in the same direction via
two needles in a 1.times.1 double warp plain stitch loop mode.
Finally the fabric which has good resilience, can be arbitrarily
cut, and has low raveling property, good elasticity and high
snagging level is obtained.
Inventors: |
Peng; Changsheng;
(Guangzhou, CN) ; Yeung; Chun Wah Samuel;
(Guangzhou, CN) ; Hu; Baohong; (Guangzhou, CN)
; Xie; Xiangjiao; (Guangzhou, CN) ; Qiu;
Lihong; (Guangzhou, CN) ; Zhang; Gui;
(Guangzhou, CN) ; Xiao; Xue; (Guangzhou, CN)
; Lai; Yanfang; (Guangzhou, CN) ; Zhang;
Shuying; (Guangzhou, CN) ; Xu; Hualan;
(Guangzhou, CN) ; Wan; Junbiao; (Guangzhou,
CN) |
|
Applicant: |
Name |
City |
State |
Country |
Type |
Pacific (Panyu) Textiles Ltd |
Guangzhou |
|
CN |
|
|
Family ID: |
1000004348256 |
Appl. No.: |
16/569664 |
Filed: |
September 12, 2019 |
Current U.S.
Class: |
1/1 |
Current CPC
Class: |
D04B 21/18 20130101;
D04B 21/20 20130101 |
International
Class: |
D04B 21/18 20060101
D04B021/18; D04B 21/20 20060101 D04B021/20 |
Foreign Application Data
Date |
Code |
Application Number |
Mar 12, 2019 |
CN |
201910185025.6 |
Claims
1. A method for producing a free-cut warp-knitted elastic fabric,
which uses a first guide bar and a second guide bar of a tricot
warp knitting machine for knitting, comprising: making a
non-elastic yarn pass across a guide needle of the first guide bar
and form the surface of the fabric by knitting via two needles in a
1.times.1 warp plain stitch loop mode, and making an elastic yarn
pass across a guide needle of the second guide bar and form the
inside of the fabric by knitting with the aforementioned
non-elastic yarn in the same direction via two needles in a
1.times.1 double warp plain stitch loop mode.
2. The method according to claim 1, wherein the non-elastic yarn
comprises a chemical fiber straight yarn and/or a draw textured
yarn; and preferably, the non-elastic yarn has a fineness of 11-77
dtex.
3. The method according to claim 1, wherein the elastic yarn has a
fineness of 22-88 dtex; and preferably, the elastic yarn comprises
spandex.
4. The method according to claim 1, wherein the temperature of a
knitting environment of the method is 20-30.degree. C., and the
humidity of the knitting environment of the method is 60-70 RH
%.
5. The method according to claim 1, wherein the 1.times.1 warp
plain stitch loop mode is a 1.times.1 closed warp plain stitch loop
mode for the first guide bar, and the 1.times.1 double warp plain
stitch loop mode is a 1.times.1 closed double warp plain stitch
loop mode for the second guide bar.
6. The method according to claim 1, wherein the 1.times.1 warp
plain stitch loop mode is a 1.times.1 open warp plain stitch loop
mode for the first guide bar, and the 1.times.1 double warp plain
stitch loop mode is a 1.times.1 closed double warp plain stitch
loop mode for the second guide bar.
7. The method according to claim 1, wherein the 1.times.1 warp
plain stitch loop mode is a 1.times.1 closed warp plain stitch loop
mode for the first guide bar, and the 1.times.1 double warp plain
stitch loop mode is a 1.times.1 open double warp plain stitch loop
mode for the second guide bar.
8. The method according to claim 1, wherein a dyeing and finishing
process of the method comprises: refining the knitted fabric, and
then dehydrating for the first time; after dehydration, executing a
presetting process, and then performing dyeing treatment; drying
the dyed fabric, and finally subjecting a finished product to
setting.
9. A fabric produced by using the method according to claim 1.
Description
CROSS-REFERENCE TO RELATED APPLICATION
[0001] This application claims priority to and benefits of Chinese
patent application No.
[0002] 201910185025.6 filed on Mar. 12, 2019, the entire content of
which is incorporated herein by reference.
TECHNICAL FIELD
[0003] The present invention belongs to the technical field of
textiles and relates to a free-cut warp-knitted elastic fabric and
a method for production thereof.
BACKGROUND
[0004] Free-cut fabrics are free-cut fabrics that have recently
received more attention from the market. The free-cut fabrics are
each usually a four-sided elastic fabric made of a chemical fiber
and spandex. The woven raw materials are generally nylon fiber and
low-temperature spandex. The made fabric has the advantages of no
curling, no raveling and not thread dropping, can be cut freely,
and has a softer and smoother hand feeling than a fabric cut
tracelessly.
[0005] At present, there are two types of free-cut warp-knitted
elastic fabrics in the market. One is a fabric where two guide bars
fully thread by using a two-needle open warp plain stitch
structure. This structure has a rough cloth cover, and there will
inevitably be a loss to make the structure flat and elastic. The
wearability of a finished product is limited. Moreover, once a coil
is broken, the fabric will be raveled easily. The other is a fabric
where a front guide bar uses cord stitch and where a back guide bar
uses double loop stitch. This fabric overcomes the shortcoming that
fabrics are raveled easily. However, the cloth cover is easily
subjected to looped pile reversal, and the fabric is rough and poor
in hand feeling and the elasticity is not excellent enough.
[0006] CN202043638U discloses a free-cut elastic underwear fabric,
including an ultra-fine soft first fiber line with a
moisture-absorbing effect and a flexible and elastic second fiber
line. The ultra-fine soft first fiber line with a
moisture-absorbing effect and the flexible and elastic second fiber
line form an extension line by alternate knitting. Due to the above
structure, by adjusting the feed ratio of the two fibers, the
free-cut elastic underwear fabric reduces the tension of the
extension line, and reduces the stress of the two fibers in the
fabric, so that the fabric is prevented from being curled and
raveled when cut open. However, the above-mentioned technical
features of the prior art are vague and cannot improve the hand
feeling and wearability of the fabric.
[0007] Therefore, it is necessary to develop an elastic fabric that
is not raveled easily, is not easily subjected to looped pile
reversal and is good in handfeeling and apply the elastic fabric to
underwear, corsets or sportswear, and the elastic fabric has a good
market prospect.
SUMMARY
[0008] Against the shortcomings in the prior art and according to
the actual demand, the present invention provides a free-cut
warp-knitted elastic fabric and a method for production thereof.
Through the selection of a yarn raw material, a warp plain stitch
structure combination is adopted to fully thread yarns, a knitting
process is optimized, production process parameters are adjusted,
steps and conditions synergistically interact and match each other
to finally obtain the fabric which has good resilience, can be
arbitrarily cut, has low raveling property, good elasticity and
high snagging level and is not curled, and the fabric has broad
application prospects and great market value.
[0009] In the preceding text, several terms are explained as
follows:
[0010] Warp plain stitch structure: The warp plain stitch structure
is one of the most basic warp-knitted structures, and is in such a
configuration that the coils formed by the same yarn are
alternately arranged in two adjacent coil wales. An extension line
of the warp plain stitch structure is shorter, so the elasticity is
relatively better.
[0011] Arbitrary cutting: When garments such as underwear are sewn,
a neckline, a lower hem and cuffs and the like do not need to bind
off, which improves the wearing comfort of the garments. The
present invention achieves this performance by utilizing a special
knitting structure.
[0012] Raveling property: The raveling property refers to the
phenomenon that coils are separated from each other when a yarn of
a knitted fabric breaks or loses an interlacing connection. Once a
loop breaks, the wales will be raveled from top to bottom, causing
the fabric to split into two parts. The present invention adopts
the double warp plain stitch structure, and the structure has the
raveling property. In order to overcome the structural defects,
with reference to the characteristics of the low-temperature
spandex, the spandex is micro-melted by a post-finishing process
and adheres to each other, and the goal that the spandex is not
raveled and can be freely cut is achieved.
[0013] Snagging: A fiber or a yarn in a knitted fabric is hooked by
an external object to form a yarn ring on the surface, which is a
snagging. Generally, the longer the extension line is, the worse
the snagging level will be, and the snagging level is also related
to a fabric stitch.
[0014] Curling property: A knitted fabric is subjected to fabric
edge roll wrapping in a free state, which results from that the
internal stress of a curved line segment in a loop tries to
straighten the line segment.
[0015] For this objective, the present invention adopts the
following technical solutions:
[0016] On the one hand, the present invention provides a method for
producing a free-cut warp-knitted elastic fabric, and the method
uses a first guide bar and a second guide bar of a tricot warp
knitting machine for knitting;
[0017] wherein a non-elastic yarn passes across a guide needle of
the first guide bar and forms the surface of the fabric by knitting
via two needles in a 1.times.1 warp plain stitch loop mode, and an
elastic yarn passes across a guide needle of the second guide bar
and forms the inside of the fabric by knitting with the
aforementioned non-elastic yarn in the same direction via two
needles in a 1.times.1 double warp plain stitch loop mode.
[0018] The inventor has obtained through a large amount of
experimental data in long-term production practice that the
finished fabric with a two-needle warp plain stitch structure has
better elasticity than other stitch structures such as a
three-needle stitch structure or a four-needle stitch structure,
and has a relative good snagging level; a large number of
experimental data proves that in the fabric developed using two
guide bars, the guide bar movements of a front guide bar and a back
guide bar are kept as swing in the same direction, and most of the
finished fabric has free cutting characteristics. Based on the
above two research findings, the present invention uses the two
guide bars for knitting through the selection of yarn raw
materials, and the front guide bar and the back guide bar select
the two-needle warp plain stitch and lay yarns in the same
direction, a knitting process is optimized by combination with
different combinations of an open structure and a closed structure,
production process parameters are adjusted, steps and conditions
synergistically interact and match each other, so that the fabric
which has good resilience, can be arbitrarily cut, has low raveling
property, good elasticity and high snagging level and is not curled
is obtained finally, and the fabric has broad application prospects
and great market value.
[0019] The two-needle warp plain stitch, is also referred to as
warp plain stitch, and is in such a configuration that the loop
formed by the same yarn are alternately arranged in two adjacent
loop wales, and the yarn laying digital of the stitch is 1-0/1-2//
or 1-2/1-0//.
[0020] The three-needle warp plain stitch structure, is also
referred to as cord stitch, and is in such a configuration that the
coils formed by the same yarn are alternately arranged in three
adjacent loop wales, and the yarn laying digital of the stitch is
1-0/2-3// or 2-3/1-0//.
[0021] The four-needle warp plain stitch, is also referred to as
satin stitch, and is in such a configuration that the loops formed
by the same yarn are alternately arranged in four adjacent coil
wales, and the yarn laying digital of the stitch is 1-0/3-4// or
3-4/1-0//.
[0022] Closed loop: A loop with two extension lines intersecting
and overlapping at a base of the loop is a closed loop.
[0023] Open loop: A loop with two extension lines not intersecting
and overlapping at a base of the loop is an open loop.
[0024] Preferably, the non-elastic yarn includes a chemical fiber
FDY yarn and/or a draw textured yarn;
[0025] where the FDY yarn is a chemical fiber filament which has a
draft during the spinning process, and the degree of orientation
and crystallinity are relatively high, and the knitted fabric is
relatively flat and smooth.
[0026] Draw textured yarn: The draw textured yarn is also referred
to a textured yarn, which is obtained by stretching and deformation
processing during the spinning process, and is fluffy and curly and
has certain elasticity. The woven fabric gives a relative cotton
feeling, the fabric texture is not clear, and the fabric is soft in
hand feeling.
[0027] Preferably, the non-elastic yarn has a fineness of 11-77
dtex, and may be, for example, 11 dtex, 22 dtex, 33 dtex, or 44
dtex.
[0028] Preferably, the elastic yarn has a fineness of 22-88 dtex,
and may be, for example, 22 dtex, 33 dtex, 44 dtex, or 55 dtex.
[0029] Preferably, the elastic yarn includes spandex.
[0030] Preferably, the temperature of a knitting environment of the
method is 20-30.degree. C., and may be, for example, 20.degree. C.,
23.degree. C., 25.degree. C., 27.degree. C., 29.degree. C. or
30.degree. C.
[0031] Preferably, the humidity of the knitting environment of the
method is 60-70%, and may be, for example, 60%, 62%, 64%, 66%, 68%
or 70%.
[0032] Preferably, the non-elastic yarn passes across a guide
needle of a first guide bar and is knitted via two needles in a
1.times.1 closed warp plain stitch loop mode, and the elastic yarn
passes across a guide needle of a second guide bar and is knitted
with the aforementioned non-elastic yarn in the same direction via
two needles in a 1.times.1 closed double warp plain stitch loop
mode.
[0033] Preferably, the non-elastic yarn passes across a guide
needle of a first guide bar and is knitted via two needles in a
1.times.1 open warp plain stitch loop mode, and the elastic yarn
passes across a guide needle of a second guide bar and is knitted
with the aforementioned non-elastic yarn in the same direction via
two needles in a 1.times.1 closed double warp plain stitch loop
mode.
[0034] Preferably, the non-elastic yarn passes across a guide
needle of a first guide bar and is knitted via two needles in a
1.times.1 closed warp plain stitch loop mode, and the elastic yarn
passes across a guide needle of a second guide bar and is knitted
with the aforementioned non-elastic yarn in the same direction via
two needles in a 1.times.1 open double warp plain stitch loop
mode.
[0035] Preferably, a threading mode of the method is full
threading; that is, modes for threading of the first guide bar and
the second guide bar are full-set threading.
[0036] Preferably, a dyeing and finishing process of the method
comprises: refining the knitted fabric, and then dehydrating for
the first time; after dehydration, executing a presetting process,
and then performing dyeing treatment; drying the dyed fabric, and
finally subjecting a finished product to setting, where the
objective of refining is to remove impurities on the fabric, make
the fabric white and soft and have good penetrating properties, and
prepare for post-dyeing. A refining device is generally a cooking
device, such as a cloth cooking pot. A first-time dehydration
device includes a rolling dehydrator, or a vacuum dehydrator, a
dryer, a centrifugal dehydrator, or the like; presetting and
setting devices adopt a tentering setting machine; a dyeing device
adopts a high temperature and high pressure dyeing machine, a skein
dyeing machine, a sizing and dyeing combination machine, a spray
dyeing device, a foam dyeing device, or the like; and a drying
device adopts a dryer.
[0037] In a second aspect, the present invention provides a fabric
produced by using the method as described in the first aspect.
[0038] Compared with the prior art, the present invention has the
following beneficial effects:
[0039] The two kinds of yarns of the fabric provided by the present
invention adopts the combination of the warp plain stitch
structure, and the finished fabric meets the requirements of free
cutting, and can meet the requirements on various occasions; the
setting of full threading of the elastic yarn by the second guide
bar makes the free-cut warp-knitted elastic fabric of the present
invention have excellent elasticity, and expands the range of
practical applications. Moreover, the combination of the warp plain
stitch structure makes the snagging level of the fabric better, and
the horizontal straight tension is moderate. The free-cut
warp-knitted elastic fabric does not curl, can be cut freely, has
good wearability, can be applied to underwear, corsets or
sportswear, and has a good market prospect.
BRIEF DESCRIPTION OF THE DRAWINGS
[0040] FIG. 1 shows a kintted structure of Embodiment 1 of the
present invention, in which a non-elastic yarn and an elastic yarn
form closed loops;
[0041] FIG. 2 shows a kintted structure of Embodiment 2 of the
present invention, in which a non-elastic yarn forms open loops and
an elastic yarn forms closed loops;
[0042] FIG. 3 shows a kintted structure of Embodiment 3 of the
present invention, in which a non-elastic yarn forms closed loops
and an elastic yarn forms open loops.
DETAILED DESCRIPTION OF THE EMBODIMENTS
[0043] In order to further explain the technical means adopted by
the present invention and effects thereof, the technical solutions
of the present invention will be further described with reference
to the accompanying drawings and specific embodiments, but the
present invention is not limited to the scope of the
embodiments.
[0044] The present invention uses a commercially available tricot
warp knitting machine, and the basic structure thereof includes a
let-off mechanism, a knitting mechanism, a guide bar traverse
movement mechanism, a pulling and curling mechanism, a transmission
mechanism, and the like. The knitting mechanism includes a needle
bed, a first guide bar, a second guide bar, and the like.
Embodiment 1
TABLE-US-00001 [0045] Knitting parameters Machine Karl Mayer HKS
2-3E type Tricot warp knitting machine Machine gauge E40 Guide bar
number 2 bars Temperature 25.degree. C. Humidity 65%
[0046] A threading method: modes for threading of a first guide bar
GB1 and a second guide bar GB2 are full-set threading.
[0047] Raw materials: The fabric uses two different types of yarns,
the non-elastic yarn is the chemical fiber FDY yarn, 22 dtex; and
the elastic yarn is spandex, 44 dtex.
[0048] A knitting process: a non-elastic yarn passes across a guide
needle of the first guide bar GB1 and is knitted via two needles in
a 1.times.1 closed warp plain stitch loop mode (a movement mode of
yarn laying digital is 1-0/1-2//), and an elastic yarn passes
across a guide needle of the second guide bar GB2 and is knitted
with the aforementioned non-elastic yarn in the same direction via
two needles in a 1.times.1 closed double warp plain stitch loop
mode (a movement mode of yarn laying digital is 1-0/1-2//), to form
a free-cut warp-knitted elastic gray fabric. The fabric structure
diagram is shown in FIG. 1.
[0049] A dyeing and finishing process:
[0050] A knitted fabric is refined in a cloth cooking pot to remove
impurities on the fabric, make the fabric white and soft and have
good penetrating properties, and prepare for post-dyeing, and then
dehydration is performed for the first time through a rolling
dehydrator; after the dehydration, the fabric enters a tentering
setting machine for presetting, and then dyeing treatment is
performed by using a spray dyeing device; the dyed fabric is placed
in a dryer for drying, and finally a finished product is subjected
to setting through the tentering setting machine.
Embodiment 2
TABLE-US-00002 [0051] Knitting parameters Machine Karl Mayer HKS
2-3E type Tricot warp knitting machine Machine gauge E40 Guide bar
number 2 bars Temperature 25.degree. C. Humidity 65%
[0052] A threading method: modes for threading of a first guide bar
GB1 and a second guide bar GB2 are full-set threading.
[0053] Raw materials: The fabric uses two different types of yarns,
the non-elastic yarn is the chemical fiber FDY yarn, 11 dtex; and
the elastic yarn is spandex, 22 dtex.
[0054] A knitting process: a non-elastic yarn passes across a guide
needle of the first guide bar GB1 and is knitted via two needles in
a 1.times.1 open warp plain stitch loop mode (a movement mode of
yarn laying digital is 0-1/2-1//), and an elastic yarn passes
across a guide needle of the second guide bar GB2 and is knitted
with the aforementioned non-elastic yarn in the same direction via
two needles in a 1.times.1 closed double warp plain stitch loop
mode (a movement mode of yarn laying digital is 1-0/1-2//), to form
a free-cut warp-knitted elastic gray fabric. The fabric structure
diagram is shown in FIG. 2.
[0055] A dyeing and finishing process:
[0056] A knitted fabric is refined in a cloth cooking pot to remove
impurities on the fabric, make the fabric white and soft and have
good penetrating properties, and prepare for post-dyeing, and then
dehydration is performed for the first time through a rolling
dehydrator; after the dehydration, the fabric enters a tentering
setting machine for presetting, and then dyeing treatment is
performed by using a spray dyeing device; the dyed fabric is placed
in a dryer for drying, and finally a finished product is subjected
to setting through the tentering setting machine.
Embodiment 3
TABLE-US-00003 [0057] Knitting parameters Machine Karl Mayer HKS
2-3E type Tricot warp knitting machine Machine gauge E40 Guide bar
number 2 bars Temperature 25.degree. C. Humidity 65%
[0058] A threading method: modes for threading of a first guide bar
GB1 and a second guide bar GB2 are full-set threading.
[0059] Raw materials: The fabric uses two different types of yarns,
the non-elastic yarn is the chemical fiber FDY yarn, 44 dtex; and
the elastic yarn is spandex, 55 dtex.
[0060] A knitting process: a non-elastic yarn passes across a guide
needle of the first guide bar GB1 and is knitted via two needles in
a 1.times.1 closed warp plain stitch loop mode (a movement mode of
yarn laying digital is 1-0/1-2//), and an elastic yarn passes
across a guide needle of the second guide bar GB2 and is knitted
with the aforementioned non-elastic yarn in the same direction via
two needles in a 1.times.1 open double warp plain stitch loop mode
(a movement mode of yarn laying digital is 0-1/2-1//), to form a
free-cut warp-knitted elastic fabric. The fabric structure diagram
is shown in FIG. 3.
[0061] A Dyeing and Finishing Process
[0062] A knitted fabric is refined in a cloth cooking pot to remove
impurities on the fabric, make the fabric white and soft and have
good penetrating properties, and prepare for post-dyeing, and then
dehydration is performed for the first time through a rolling
dehydrator; after the dehydration, the fabric enters a tentering
setting machine for presetting, and then dyeing treatment is
performed by using a spray dyeing device; the dyed fabric is placed
in a dryer for drying, and finally a finished product is subjected
to setting through the tentering setting machine.
Comparative Example 1
[0063] Other materials and processes are the same as embodiment 1
except that in the knitting process, "a non-elastic yarn passes
across a guide needle of a first guide bar GB1 and is knitted via
two needles in a 1.times.1 closed warp plain stitch loop mode (a
movement mode of yarn laying digital is 1-0/1-2//), and an elastic
yarn passes across a guide needle of the second guide bar GB2 and
is knitted with the aforementioned non-elastic yarn in opposite
directions via two needles in a 1.times.1 open warp plain stitch
loop mode (a movement mode of yarn laying digital is
0-1/2-1//)".
[0064] The formed fabric has a poor snagging and the curling
performance is not good.
Comparative Example 2
[0065] Other materials and processes are the same as embodiment 1
except that in the knitting process, "a non-elastic yarn passes
across a guide needle of a first guide bar GB1 and is knitted via
three needles in a 1.times.1.times.1 closed warp plain stitch loop
mode (a movement mode of yarn laying digital is 2-3/1-0//), and an
elastic yarn passes across a guide needle of a second guide bar GB2
and is knitted with the aforementioned non-elastic yarn in the same
direction via in a double open warp plain stitch loop mode (a
movement mode of yarn laying digital is 3-1/0-2//), to form a
free-cut warp-knitted elastic fabric".
[0066] The cloth cover of the formed fabric is easily subjected to
looped pile reversal, and the fabric surface is rough, which causes
a certain irritation to the skin in touch. The fabric is poor in
handfeel, and the elongation is not excellent enough.
[0067] The double loop open warp stitch structure: A warp-knitted
structure in which one yarn continuously forms two coils on one
course is called double loop stitch, and two extension lines of the
open double loop stitch coil do not intersect and overlap at the
base of the coil. The yarn laying digital is 0-2/3-1// or
3-1/0-2//.
[0068] Looped pile reversal: The coils in the knitted fabric are
formed on the surface of the fabric, and some fabrics are smooth in
hand feeling in the knitting direction, while in the reverse
direction of the knitting direction, the fabric gives a pricking
feeling in touch, and this phenomenon is called looped pile
reversal.
Comparative Example 3
[0069] Except that a knitting machine is a Raschel warp knitting
machine, others are the same as embodiment 1. The knitting process:
a non-elastic yarn passes across a guide needle of a first guide
bar GB1 and is knitted via two needles in a 1.times.1 closed warp
plain stitch loop mode (a movement mode of yarn laying digital is
1-0/1-2//), and an elastic yarn passes across a guide needle of a
second guide bar GB2 and is knitted with the aforementioned
non-elastic yarn in the same direction via two needles in a
1.times.1 closed double warp plain stitch loop mode (a movement
mode of yarn laying digital is 1-0/1-2//), to form a free-cut
warp-knitted elastic fabric. The formed fabric has a poor effect
and the cloth cover is rough and not flat enough.
[0070] In conclusion, the present invention provides a free-cut
warp-knitted elastic fabric and a method for production thereof.
Through the selection of a yarn raw material and a knitting
machine, a warp plain stitch structure combination is adopted to
fully thread yarns, a knitting process is optimized, production
process parameters are adjusted, steps and conditions
synergistically interact and match each other to finally obtain the
fabric which has good resilience, can be arbitrarily cut, has low
raveling property, good elongation and high snagging level, and the
fabric has broad application prospects and great market value.
[0071] Experimental Test
[0072] a. Stretch Property
[0073] Refer to the LTD-03 tension test method (Victoria's Secret
customer-specific test), this standard is for standard testing of
the elongation of the woven or knitted elastic fabric under the
agreed tension; and the test sample size is 9*3 inch. Fabrics of
embodiments and comparative examples are taken in the transverse
direction and the longitudinal direction. A tension instrument used
is Zwick/Roell's H01-LLJ-004 tensile machine, using a force of 7.5
lb, the intermediate clamping distance is 127 mm, the stretching
speed is 20 in/min, and the cyclic stretching is performed
twice.
[0074] b. Snagging Performance:
[0075] Refer to BS-8479 method for Measuring Textile Spinning
Tendency--Rotating Chamber Method. Under the James Heal Snagging
Tester instrument, the snagging testing of fabrics of the
embodiments and the comparative examples was carried out. The test
sample size was 140*140 mm, forward rotation for 50 revolutions and
reverse rotation for 50 revolutions were performed at a speed of at
60 r/min, the cycling was carried out 10 times, 1000 revolutions
were performed in total, then the samples were taken out for a
comparison with a standard rating picture, and the snag yarn levels
were given. The levels are 1-5, level 5 is the best, and level 1 is
the worst.
[0076] c. Handfeeling
[0077] Three textile industry technicians were chosen to make a
touch feeling on these three fabrics, and the fabric touch levels
were comprehensively evaluated. The levels are 1-5, and level 5 is
the best.
[0078] The elongation properties, snagging and handfeeling of the
finished fabrics obtained in Embodiments 1-3 and Comparative
Examples 1-3 were evaluated. The results are shown in
TABLE-US-00004 TABLE 1 Snagging/ Handfeeling/ Sample Elongation/%
level level Embodiment 1 Longitudinal 120 3.0 4 Transverse 200 3.5
Embodiment 2 Longitudinal 136 3.5 4.5 Transverse 180 3.0 Embodiment
3 Longitudinal 175 3.0 4.5 Transverse 240 3.5 Comparative
Longitudinal 135 1.5 5 example 1 Transverse 180 1.5 Comparative
Longitudinal 120 1.5 3.0 example 2 Transverse 81 2.0 Comparative
Longitudinal 110 2.5 2.5 example 3 Transverse 150 2.0
[0079] It can be obviously seen from the data in Table 1 that
fabrics knitted by the use of the TRICOT machine for knitting is
better than fabrics obtained by the RASCHEL machine for knitting in
terms of hand feeling and elasticity. With respect to the use of
reverse yarn laying movement, although the handfeeling is better,
the requirement of free cutting are not met, and the snag yarn is
relatively poor. The use of the three-needle warp plain stitch
structure in the same direction meets the requirements of free
cutting, but the elongation is not good, and the handfeeling is too
bad. In summary, the present invention is superior to the prior art
in both structure and properties of finished fabrics.
[0080] The applicant declares that detailed methods of the present
invention are described by the above-described embodiments, but the
present invention is not limited to the above detailed methods,
that is, it does not mean that the present invention must be
implemented by the above detailed methods. It should be apparent to
those skilled in the art that any modifications of the present
invention, equivalent substitutions of various materials of
products of the present invention, addition of auxiliary
components, selection of specific means, and the like are all
within the protection scope and disclosure scope of the present
invention.
* * * * *