U.S. patent application number 16/807853 was filed with the patent office on 2020-09-10 for method for manufacturing light-emitting element.
This patent application is currently assigned to NICHIA CORPORATION. The applicant listed for this patent is NICHIA CORPORATION. Invention is credited to Naoto INOUE.
Application Number | 20200287074 16/807853 |
Document ID | / |
Family ID | 1000004691352 |
Filed Date | 2020-09-10 |


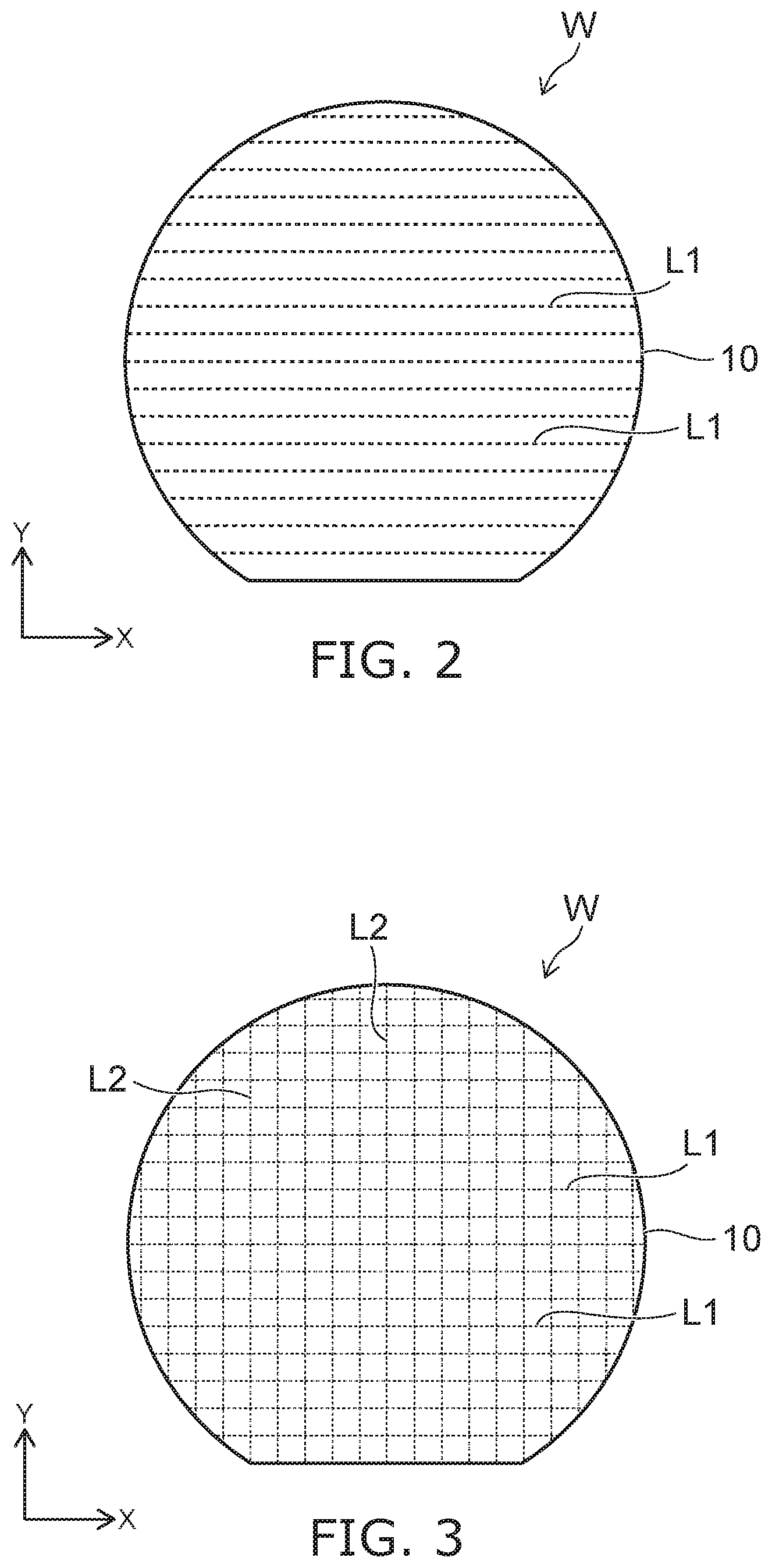


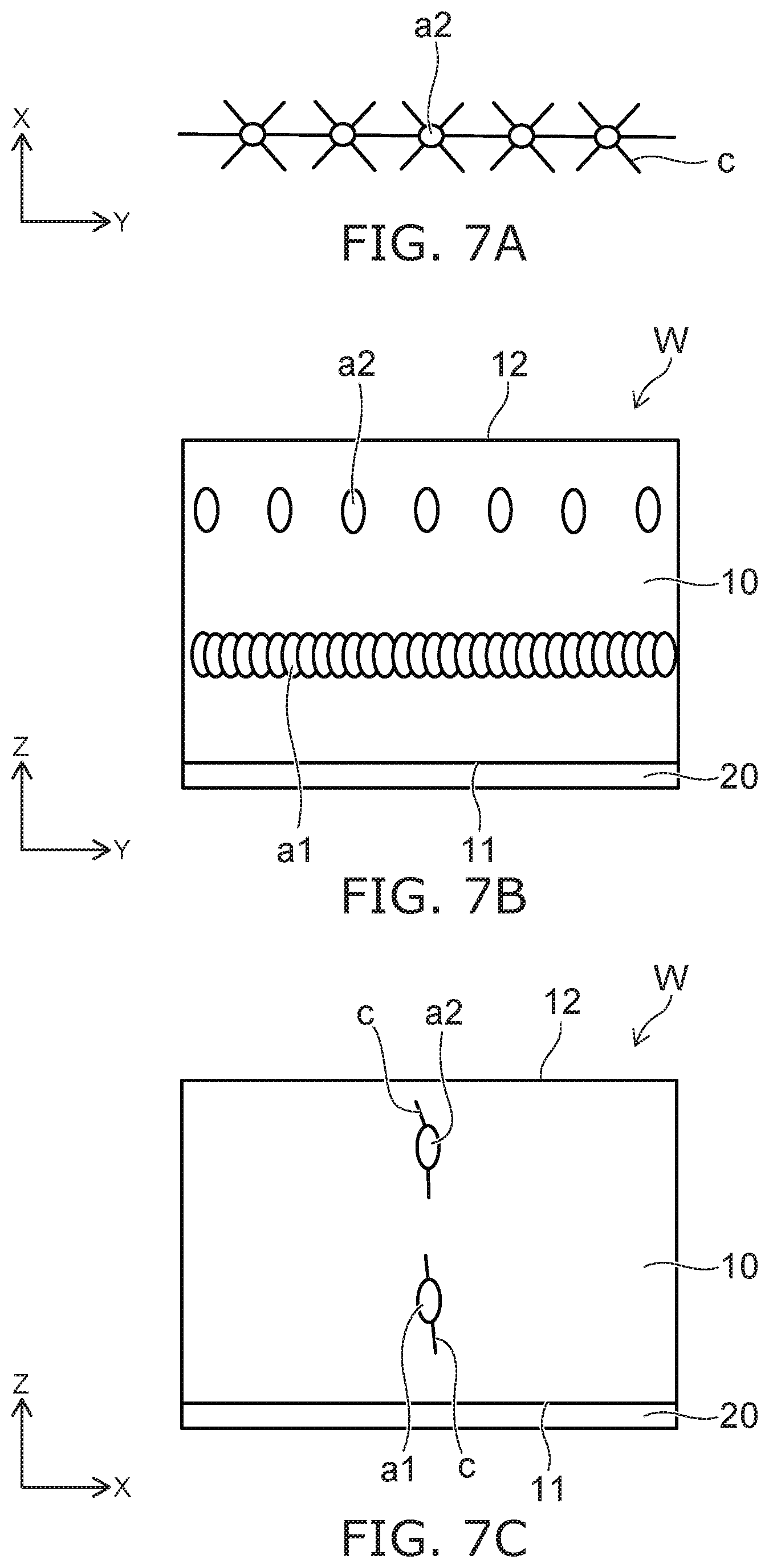


United States Patent
Application |
20200287074 |
Kind Code |
A1 |
INOUE; Naoto |
September 10, 2020 |
METHOD FOR MANUFACTURING LIGHT-EMITTING ELEMENT
Abstract
A method for manufacturing a light-emitting element includes:
providing a wafer comprising: a substrate having a first surface
and a second surface, and a semiconductor structure provided at the
first surface; irradiating a laser beam into an interior of the
substrate from a second surface side of the substrate, which
comprises: forming a plurality of first modified regions, a
plurality of second modified regions, and a plurality of third
modified regions in the interior of the substrate; and
subsequently, separating the wafer into a plurality of
light-emitting elements.
Inventors: |
INOUE; Naoto; (Anan-shi,
JP) |
|
Applicant: |
Name |
City |
State |
Country |
Type |
NICHIA CORPORATION |
Anan-shi |
|
JP |
|
|
Assignee: |
NICHIA CORPORATION
Anan-shi
JP
|
Family ID: |
1000004691352 |
Appl. No.: |
16/807853 |
Filed: |
March 3, 2020 |
Current U.S.
Class: |
1/1 |
Current CPC
Class: |
H01L 33/0095
20130101 |
International
Class: |
H01L 33/00 20060101
H01L033/00 |
Foreign Application Data
Date |
Code |
Application Number |
Mar 8, 2019 |
JP |
2019-043118 |
Claims
1. A method for manufacturing a light-emitting element, the method
comprising: providing a wafer comprising: a substrate having a
first surface and a second surface, and a semiconductor structure
provided at the first surface; irradiating a laser beam into an
interior of the substrate from a second surface side of the
substrate, which comprises: forming a plurality of first modified
regions in the interior of the substrate by scanning the laser beam
at a first irradiation pitch along a first direction parallel to
the second surface, subsequently, forming a plurality of second
modified regions in the interior of the substrate between the
second surface and the first modified regions by scanning the laser
beam at a second irradiation pitch along the first direction, the
second irradiation pitch being wider than the first irradiation
pitch, and subsequently, forming a plurality of third modified
regions in the interior of the substrate at a depth within a range
of the second modified regions by scanning the laser beam at a
third irradiation pitch along the first direction, an output of the
laser beam in the step of forming the plurality of third modified
regions being higher than an output of the laser beam in the step
of forming the plurality of second modified regions, the third
irradiation pitch being narrower than the second irradiation pitch;
and subsequently, separating the wafer into a plurality of
light-emitting elements.
2. The method according to claim 1, wherein: the first irradiation
pitch is 2.5 .mu.m or less.
3. The method according to claim 1, wherein: the third irradiation
pitch is wider than the first irradiation pitch.
4. The method according to claim 2, wherein: the third irradiation
pitch is wider than the first irradiation pitch.
5. The method according to claim 1, wherein: an output of the laser
beam in the step of forming the plurality of first modified regions
is 0.2 W or less.
6. The method according to claim 2, wherein: an output of the laser
beam in the step of forming the plurality of first modified regions
is 0.2 W or less.
7. The method according to claim 3, wherein: an output of the laser
beam in the step of forming the plurality of first modified regions
is 0.2 W or less.
8. The method according to claim 4, wherein: an output of the laser
beam in the step of forming the plurality of first modified regions
is 0.2 W or less.
9. The method according to claim 1, wherein: in the step of forming
the plurality of second modified regions, the laser beam is scanned
in a region closer to the second surface than a crack extending
from the first modified region toward the second surface.
10. The method according to claim 2, wherein: in the step of
forming the plurality of second modified regions, the laser beam is
scanned in a region closer to the second surface than crack
extending from the first modified region toward the second
surface.
11. The method according to claim 3, wherein: in the step of
forming the plurality of second modified regions, the laser beam is
scanned in a region closer to the second surface than crack
extending from the first modified region toward the second
surface.
12. The method according to claim 4, wherein: in the step of
forming the plurality of second modified regions, the laser beam is
scanned in a region closer to the second surface than crack
extending from the first modified region toward the second
surface.
13. The method according to claim 5, wherein: in the step of
forming the plurality of second modified regions, the laser beam is
scanned in a region closer to the second surface than crack
extending from the first modified region toward the second
surface.
14. The method according to claim 1, wherein: the step of
irradiating the laser beam into the interior of the substrate
further comprises: forming a plurality of fourth modified regions
in the interior of the substrate by scanning the laser beam at a
fourth irradiation pitch along a second direction parallel to the
second surface and crossing the first direction, subsequently,
forming a plurality of fifth modified regions in the interior of
the substrate between the second surface and the first modified
regions by scanning the laser beam at a fifth irradiation pitch
along the second direction, the fifth irradiation pitch being wider
than the fourth irradiation pitch, and subsequently, forming a
plurality of sixth modified regions in the interior of the
substrate at a depth within a range of the fifth modified regions
by scanning the laser beam at a sixth irradiation pitch along the
second direction, an output of the laser beam in the step of
forming the plurality of sixth modified regions being higher than
an output of the laser beam in the step of forming the plurality of
fifth modified regions, the sixth irradiation pitch being narrower
than the fifth irradiation pitch.
15. The method according to claim 2, wherein: the step of
irradiating the laser beam into the interior of the substrate
further comprises: forming a plurality of fourth modified regions
in the interior of the substrate by scanning the laser beam at a
fourth irradiation pitch along a second direction parallel to the
second surface and crossing the first direction, subsequently,
forming a plurality of fifth modified regions in the interior of
the substrate between the second surface and the first modified
regions by scanning the laser beam at a fifth irradiation pitch
along the second direction, the fifth irradiation pitch being wider
than the fourth irradiation pitch, and subsequently, forming a
plurality of sixth modified regions in the interior of the
substrate at a depth within a range of the fifth modified regions
by scanning the laser beam at a sixth irradiation pitch along the
second direction, an output of the laser beam in the step of
forming the plurality of sixth modified regions being higher than
an output of the laser beam in the step of forming the plurality of
fifth modified regions, the sixth irradiation pitch being narrower
than the fifth irradiation pitch.
16. The method according to claim 3, wherein: the step of
irradiating the laser beam into the interior of the substrate
further comprises: forming a plurality of fourth modified regions
in the interior of the substrate by scanning the laser beam at a
fourth irradiation pitch along a second direction parallel to the
second surface and crossing the first direction, subsequently,
forming a plurality of fifth modified regions in the interior of
the substrate between the second surface and the first modified
regions by scanning the laser beam at a fifth irradiation pitch
along the second direction, the fifth irradiation pitch being wider
than the fourth irradiation pitch, and subsequently, forming a
plurality of sixth modified regions in the interior of the
substrate at a depth within a range of the fifth modified regions
by scanning the laser beam at a sixth irradiation pitch along the
second direction, an output of the laser beam in the step of
forming the plurality of sixth modified regions being higher than
an output of the laser beam in the step of forming the plurality of
fifth modified regions, the sixth irradiation pitch being narrower
than the fifth irradiation pitch.
17. The method according to claim 4, wherein: the step of
irradiating the laser beam into the interior of the substrate
further comprises: forming a plurality of fourth modified regions
in the interior of the substrate by scanning the laser beam at a
fourth irradiation pitch along a second direction parallel to the
second surface and crossing the first direction, subsequently,
forming a plurality of fifth modified regions in the interior of
the substrate between the second surface and the first modified
regions by scanning the laser beam at a fifth irradiation pitch
along the second direction, the fifth irradiation pitch being wider
than the fourth irradiation pitch, and subsequently, forming a
plurality of sixth modified regions in the interior of the
substrate at a depth within a range of the fifth modified regions
by scanning the laser beam at a sixth irradiation pitch along the
second direction, an output of the laser beam in the step of
forming the plurality of sixth modified regions being higher than
an output of the laser beam in the step of forming the plurality of
fifth modified regions, the sixth irradiation pitch being narrower
than the fifth irradiation pitch.
18. The method according to claim 5, wherein: the step of
irradiating the laser beam into the interior of the substrate
further comprises: forming a plurality of fourth modified regions
in the interior of the substrate by scanning the laser beam at a
fourth irradiation pitch along a second direction parallel to the
second surface and crossing the first direction, subsequently,
forming a plurality of fifth modified regions in the interior of
the substrate between the second surface and the first modified
regions by scanning the laser beam at a fifth irradiation pitch
along the second direction, the fifth irradiation pitch being wider
than the fourth irradiation pitch, and subsequently, forming a
plurality of sixth modified regions in the interior of the
substrate at a depth within a range of the fifth modified regions
by scanning the laser beam at a sixth irradiation pitch along the
second direction, an output of the laser beam in the step of
forming the plurality of sixth modified regions being higher than
an output of the laser beam in the step of forming the plurality of
fifth modified regions, the sixth irradiation pitch being narrower
than the fifth irradiation pitch.
19. The method according to claim 6, wherein: the step of
irradiating a laser beam into the interior of the substrate further
comprises: forming a plurality of fourth modified regions in the
interior of the substrate by scanning the laser beam at a fourth
irradiation pitch along a second direction parallel to the second
surface and crossing the first direction, subsequently, forming a
plurality of fifth modified regions in the interior of the
substrate between the second surface and the first modified regions
by scanning the laser beam at a fifth irradiation pitch along the
second direction, the fifth irradiation pitch being wider than the
fourth irradiation pitch, and subsequently, forming a plurality of
sixth modified regions in the interior of the substrate at a depth
within a range of the fifth modified regions by scanning the laser
beam at a sixth irradiation pitch along the second direction, an
output of the laser beam in the step of forming the plurality of
sixth modified regions being higher than an output of the laser
beam in the step of forming the plurality of fifth modified
regions, the sixth irradiation pitch being narrower than the fifth
irradiation pitch.
20. The method according to claim 9, wherein: the step of
irradiating a laser beam into the interior of the substrate further
comprises: forming a plurality of fourth modified regions in the
interior of the substrate by scanning the laser beam at a fourth
irradiation pitch along a second direction parallel to the second
surface and crossing the first direction, subsequently, forming a
plurality of fifth modified regions in the interior of the
substrate between the second surface and the first modified regions
by scanning the laser beam at a fifth irradiation pitch along the
second direction, the fifth irradiation pitch being wider than the
fourth irradiation pitch, and subsequently, forming a plurality of
sixth modified regions in the interior of the substrate at a depth
within a range of the fifth modified regions by scanning the laser
beam at a sixth irradiation pitch along the second direction, an
output of the laser beam in the step of forming the plurality of
sixth modified regions being higher than an output of the laser
beam in the step of forming the plurality of fifth modified
regions, the sixth irradiation pitch being narrower than the fifth
irradiation pitch.
Description
CROSS-REFERENCE TO RELATED APPLICATION
[0001] This application claims priority to Japanese Patent
Application No. 2019-043118, filed on Mar. 8, 2019, the disclosure
of which is hereby incorporated by reference in its entirety.
BACKGROUND
[0002] The disclosure relates to a method for manufacturing a
light-emitting element.
[0003] Generally, a semiconductor light-emitting element is
obtained by, for example, dicing a wafer in which a compound
semiconductor layer is epitaxially grown on a sapphire substrate.
Laser stealth dicing is known as a wafer dicing technique in which
modified regions are formed by concentrating a laser beam in a
substrate interior and by singulating the wafer by using cracks
extending from the modified regions as starting points.
SUMMARY
[0004] The present disclosure is directed to a method for
manufacturing a light-emitting element in which the meandering of
cracks can be suppressed while maintaining a high fracture strength
in a laser beam irradiation process before singulation.
[0005] In one embodiment of the present disclosure, a method for
manufacturing a light-emitting element, the method comprising:
[0006] providing a wafer comprising: [0007] a substrate having a
first surface and a second surface, and [0008] a semiconductor
structure provided at the first surface;
[0009] irradiating a laser beam into an interior of the substrate
from a second surface side of the substrate, which comprises:
[0010] forming a plurality of first modified regions in the
interior of the substrate by scanning the laser beam at a first
irradiation pitch along a first direction parallel to the second
surface, [0011] subsequently, forming a plurality of second
modified regions in the interior of the substrate between the
second surface and the first modified regions by scanning the laser
beam at a second irradiation pitch along the first direction, the
second irradiation pitch being wider than the first irradiation
pitch, and [0012] subsequently, forming a plurality of third
modified regions in the interior of the substrate at a depth within
a range of the second modified regions by scanning the laser beam
at a third irradiation pitch along the first direction, an output
of the laser beam in the step of forming the plurality of third
modified regions being higher than an output of the laser beam in
the step of forming the plurality of second modified regions, the
third irradiation pitch being narrower than the second irradiation
pitch; and
[0013] subsequently, separating the wafer into a plurality of
light-emitting elements.
[0014] According to a method for manufacturing a light-emitting
element in the disclosure, the meandering of cracks can be
suppressed while maintaining a high fracture strength in a laser
beam irradiation process before singulation.
BRIEF DESCRIPTION OF THE DRAWINGS
[0015] FIG. 1 is a schematic cross-sectional view of a wafer on
which a method for manufacturing a light-emitting element of an
embodiment of the invention is used;
[0016] FIG. 2 to FIG. 5 are schematic plan views showing a method
for manufacturing a light-emitting element of an embodiment of the
invention;
[0017] FIG. 6A is a schematic plan view of a laser beam irradiation
portion of a first scanning process of the embodiment of the
invention;
[0018] FIG. 6B is a schematic cross-sectional view of the laser
beam irradiation portion of the first scanning process of the
embodiment of the invention;
[0019] FIG. 6C is a schematic cross-sectional view of the laser
beam irradiation portion of the first scanning process of the
embodiment of the invention;
[0020] FIG. 7A is a schematic plan view of a laser beam irradiation
portion of a second scanning process of the embodiment of the
invention;
[0021] FIG. 7B is a schematic cross-sectional view of the laser
beam irradiation portion of the second scanning process of the
embodiment of the invention;
[0022] FIG. 7C is a schematic cross-sectional view of the laser
beam irradiation portion of the second scanning process of the
embodiment of the invention;
[0023] FIG. 8A is a schematic plan view of a laser beam irradiation
portion of a third scanning process of the embodiment of the
invention;
[0024] FIG. 8B is a schematic cross-sectional view of the laser
beam irradiation portion of the third scanning process of the
embodiment of the invention;
[0025] FIG. 8C is a schematic cross-sectional view of the laser
beam irradiation portion of the third scanning process of the
embodiment of the invention; and
[0026] FIG. 9 is a graph illustrating the verification results on
the method for manufacturing the light-emitting element of the
embodiment of the invention.
DETAILED DESCRIPTION OF EMBODIMENTS
[0027] Embodiments will now be described with reference to the
drawings. The same components in the drawings are marked with the
same reference numerals.
[0028] FIG. 1 is a schematic cross-sectional view of a wafer W on
which a method for manufacturing a light-emitting element of the
one embodiment of the invention is used.
[0029] The wafer W includes a substrate 10 and a semiconductor
structure 20. The substrate 10 has a first surface 11, and a second
surface 12 on the side opposite to the first surface 11. The
semiconductor structure 20 is provided at the first surface 11.
[0030] The substrate 10 may be, for example, a sapphire substrate.
The first surface 11 may be, for example, the c-plane of the
sapphire. The first surface 11 may be oblique to the c-plane within
a range in which the semiconductor structure 20 can be formed to
have good crystallinity.
[0031] The semiconductor structure 20 may include, for example, a
nitride semiconductor represented by In.sub.xAl.sub.yGa.sub.1-x-yN
(0.ltoreq.x, 0.ltoreq.y, and x+y<1). The semiconductor structure
20 includes an active layer, and the peak wavelength of the light
emitted by the active layer may be, for example, not less than 360
nm and not more than 650 nm.
[0032] The method for manufacturing the light-emitting element of
the embodiment includes a process of irradiating a laser beam into
the interior of the substrate 10, and a process of separating the
wafer W into multiple light-emitting elements after the laser beam
irradiation process.
[0033] FIG. 2 and FIG. 3 are schematic plan views of the wafer W
showing the laser beam irradiation process.
[0034] An X-direction and a Y-direction are two directions
orthogonal to each other in a plane parallel to the first surface
11 and the second surface 12 of the substrate 10 shown in FIG.
1.
[0035] The laser beam irradiation process includes a process of
forming multiple dicing lines L1 along the X-direction by scanning
the laser beam multiple times along the X-direction (FIG. 2), and a
process of forming multiple dicing lines L2 along the Y-direction
by scanning the laser beam multiple times along the Y-direction
before or after forming the dicing lines L1 (FIG. 3). For example,
the X-direction may be aligned with the m-axis direction of the
sapphire, and the Y-direction is aligned with the a-axis direction
of the sapphire.
[0036] The dicing lines L1 and L2 correspond to columns of multiple
modified regions described below that are formed in the interior of
the substrate 10 by laser beam irradiation.
[0037] The irradiated laser beam is concentrated at a position
having a designated depth in the interior of the substrate 10, and
the energy of the laser beam concentrates at the position. Modified
regions that are more embrittled than portions not subjected to the
laser beam irradiation are formed at the irradiation portion (the
concentration portion) of the laser beam.
[0038] For example, the laser beam may be emitted in pulse form.
For example, a Nd:YAG laser, a titanium sapphire laser, a
Nd:YVO.sub.4 laser, a Nd:YLF laser, or the like may be used as the
laser light source. The wavelength of the laser beam is a
wavelength of light that passes through the substrate 10. For
example, the laser beam may have a peak wavelength not less than
800 nm and not more than 1200 nm.
[0039] FIG. 4 and FIG. 5 are schematic plan views of the wafer W
that show the separation process.
[0040] For example, after the laser beam irradiation process,
first, a singulation process may be performed along the dicing
lines L1. As shown in FIG. 4, the wafer W is separated into
multiple bars 30. Subsequently, a singulation process is performed
along the dicing lines L2, and the wafer W is separated into
multiple light-emitting elements 50 as shown in FIG. 5.
[0041] Details of the laser beam irradiation process will now be
described.
[0042] The laser beam irradiation process in the embodiment
includes a first scanning process, a second scanning process, and a
third scanning process. For example, first, the dicing lines L1
described above may be formed by the first scanning process, the
second scanning process, and the third scanning process along the
X-direction. Subsequently, the dicing lines L2 described above may
be formed by the first scanning process, the second scanning
process, and the third scanning process along the Y-direction.
Although the laser beam irradiation process that includes the first
scanning process, the second scanning process, and the third
scanning process is performed in the two directions of the
X-direction and the Y-direction in the embodiment, the effects
described above are provided even when the laser beam irradiation
process is performed only in one direction of the X-direction or
the Y-direction.
[0043] Although the first scanning process, the second scanning
process, and the third scanning process along the Y-direction are
described in the following example, the first scanning process, the
second scanning process, and the third scanning process along the
X-direction are performed similarly.
[0044] FIG. 6A is a drawing of the laser beam irradiation portion
of the first scanning process when viewed from a Z-direction. FIG.
6B is a schematic cross-sectional view of the laser beam
irradiation portion of the first scanning process.
[0045] In FIG. 6B and FIG. 6C, the Z-direction is aligned with the
thickness direction of the wafer W and is orthogonal to the
X-direction and the Y-direction. FIG. 6B illustrates a cross
section along the Y-direction, which is the scanning direction of
the laser beam, and FIG. 6C illustrates a cross section along the
X-direction orthogonal to the scanning direction of the laser
beam.
[0046] In the first scanning process, the laser beam is irradiated
through the second surface 12 side and scanned discretely along the
Y-direction at a first irradiation pitch in the interior of the
substrate 10. By scanning at the first irradiation pitch, multiple
first modified regions a1 are formed densely to overlap each other
along the Y-direction.
[0047] In the first scanning process, it is favorable for the
output of the laser beam to be not less than 0.05 W and not more
than 0.2 W, e.g., 0.14 W. It is favorable for the first irradiation
pitch to be 2.5 .mu.m or less, e.g., 1.5 .mu.m.
[0048] The thickness of the substrate 10 is about 150 .mu.m. For
example, a position at a depth of 20 to 50 .mu.m from the second
surface 12 is an example of the setting value of the focus position
of the laser beam in the first scanning process.
[0049] In the first modified regions a1 formed by the irradiation
of the laser beam, stress is generated, and cracks c occur due to
the stress. When viewed from the c-plane side of the sapphire,
which is a hexagonal crystal, the a-axis directions are three
directions at 60.degree.-spacing, and the cracks c are formed
easily along the three directions of the a-axes as shown in FIG.
6A.
[0050] According to verifications described below, it was found
that the fracture strength of the wafer W is strongly dependent on
the irradiation pitch of the laser beam, and a high fracture
strength is obtained by reducing the irradiation pitch of the laser
beam. The modified regions that are formed by the irradiation of
the laser beam are formed more densely as the irradiation pitch of
the laser beam decreases. It is considered that by densely forming
the modified regions, voids do not exist easily in the modified
regions, and a high fracture strength is obtained.
[0051] In the first scanning process of the embodiment, the
fracture strength of the wafer W can be high because the multiple
first modified regions a1 are densely formed to overlap each other
along the Y-direction. Unintended breakage of the wafer W in the
laser irradiation process before the separation process can be
suppressed thereby.
[0052] Verification results relating to the conditions of the first
irradiation pitch in the first scanning process will now be
described.
[0053] In the verification, a sapphire substrate having a thickness
of 200 .mu.m was used as the substrate 10. The planar configuration
of each of the samples was a square having 10.2 mm sides. A laser
beam was irradiated into the central portion of the sample with
varying irradiation conditions. The laser beam was irradiated along
the m-axis of the sapphire substrate. After the irradiation of the
laser beam, the fracture strength of the sample was measured. The
pressing speed of the head applied to the sample in the measurement
of the fracture strength was 0.05 mm/sec.
[0054] For a sample SP11, the output of the laser beam was 0.35 W,
and the irradiation pitch of the laser beam was 1.5 .mu.m. For the
sample SP11, the pulse width of the laser beam was 5.0 ps.
[0055] For a sample SP12, the output of the laser beam was 0.35 W,
and the irradiation pitch of the laser beam was 2.0 .mu.m. For the
sample SP12, the pulse width of the laser beam was 5.0 ps.
[0056] For a sample SP13, the output of the laser beam was 0.35 W,
and the irradiation pitch of the laser beam was 2.5 .mu.m. For the
sample SP13, the pulse width of the laser beam was 5.0 ps.
[0057] For a sample SP14, the output of the laser beam was 0.35 W,
and the irradiation pitch of the laser beam was 3.0 .mu.m. For the
sample SP14, the pulse width of the laser beam was 5.0 ps.
[0058] Thus, among the irradiation conditions of the laser beam for
the samples SP11 to SP14, the value of the output was the same, and
the value of the pulse width was the same, but the value of the
irradiation pitch was modified.
[0059] FIG. 9 is a graph illustrating the verification results.
[0060] The vertical axis of FIG. 9 is the fracture strength
(newtons: N). The fracture strengths of the samples SP11 to SP14
recited above are shown in FIG. 9. The fracture strengths of the
samples SP11 to SP14 shown in FIG. 9 each are average values of the
values obtained by measuring the samples SP11 to SP14 five times
each.
[0061] The fracture strength of the sample SP11 (having an
irradiation pitch of 1.5 .mu.m) was 3.8 N.
[0062] The fracture strength of the sample SP12 (having an
irradiation pitch of 2.0 .mu.m) was 2.3 N.
[0063] The fracture strength of the sample SP13 (having an
irradiation pitch of 2.5 .mu.m) was 1.6 N.
[0064] The fracture strength of the sample SP14 (having an
irradiation pitch of 3.0 .mu.m) was 0.6 N.
[0065] It can be seen from FIG. 9 that the fracture strength is
strongly dependent on the irradiation pitch of the laser beam. A
high fracture strength is obtained by reducing the irradiation
pitch. The fracture strength when the irradiation pitch is 2.5
.mu.m is not less than 2 times the fracture strength when the
irradiation pitch is 3.0 .mu.m, and the fracture strength increases
further as the irradiation pitch decreases to 2.0 .mu.m and 1.5
.mu.m. According to the experiment results, it is desirable for the
first irradiation pitch to be 2.5 .mu.m or less in the first
scanning process that is directed to provide a high fracture
strength.
[0066] In the experiment described above, the laser beam was
irradiated along the m-axis of the sapphire substrate. It is
considered that results similar to those of FIG. 9 are obtained
also when the laser beam is irradiated along the a-axis of the
sapphire substrate.
[0067] The second scanning process is performed after the first
scanning process. FIG. 7A is a schematic plan view of the laser
beam irradiation portion of the second scanning process, and FIG.
7B and FIG. 7C are schematic cross-sectional views of the laser
beam irradiation portion of the second scanning process. FIG. 7B
illustrates a cross section along the Y-direction, which is the
scanning direction of the laser beam, and FIG. 7C illustrates a
cross section along the X-direction orthogonal to the scanning
direction of the laser beam.
[0068] In the second scanning process, the laser beam is irradiated
through the second surface 12 side and scanned discretely along the
Y-direction at a second irradiation pitch in a region of the
interior of the substrate 10 between the second surface 12 and the
first modified regions a1. By scanning at the second irradiation
pitch, multiple second modified regions a2 are formed discretely in
the Y-direction.
[0069] In the second scanning process, the output of the laser beam
is not less than 0.05 W and not more than 0.2 W, e.g., 0.10 W. The
second irradiation pitch is wider than the first irradiation pitch
of the first scanning process, is not less than 3 .mu.m and not
more than 5 .mu.m, e.g., 3.5 .mu.m when scanning in the m-axis
direction, and is not less than 5 .mu.m and not more than 10 .mu.m,
e.g., 6.5 .mu.m when scanning in the a-axis direction. The setting
value of the focus position of the laser beam in the second
scanning process is shallower than the setting value of the focus
position of the laser beam in the first scanning process and may
be, for example, a position at a depth of 10 to 35 .mu.m from the
second surface 12.
[0070] For example, when the modified regions are densely arranged
to overlap as in the first modified regions a1, among the cracks
that extend in the three directions recited above, the cracks that
extend in directions other than the scanning direction (in the
example, the Y-direction) connect easily, and the cracks meander
easily.
[0071] On the other hand, in the second scanning process, the laser
beam is irradiated at the second irradiation pitch, which is wider
than the first irradiation pitch of the first scanning process;
thereby, the second modified regions a2 are formed at a wider pitch
than the first modified regions a1. Thereby, as shown in FIG. 7A,
the cracks c can be caused to extend while suppressing the
meandering along the scanning direction by mutually connecting the
cracks c extending in the scanning direction while suppressing the
connection of the cracks c extending in the directions other than
the scanning direction.
[0072] The third scanning process is performed after the second
scanning process. FIG. 8A is a drawing of the laser beam
irradiation portion of the third scanning process when viewed from
the Z-direction, and FIG. 8B and FIG. 8C are schematic
cross-sectional views of the laser beam irradiation portion of the
third scanning process. FIG. 8B shows a cross section along the
Y-direction, which is the scanning direction of the laser beam. In
FIG. 8B, the second modified regions a2 are shown by broken lines.
FIG. 8C shows a cross section along the X-direction orthogonal to
the scanning direction of the laser beam.
[0073] In the third scanning process, the laser beam is irradiated
through the second surface 12 side and scanned discretely along the
Y-direction at a third irradiation pitch at a depth in the interior
of the substrate 10 within the range of the second modified regions
a2. By the third scanning process, multiple third modified regions
a3 are formed more densely than the second modified regions a2
along the Y-direction at a depth within the range of the second
modified regions a2.
[0074] The output of the laser beam in the third scanning process
is higher than the output of the laser beam in the second scanning
process and is not less than 0.1 W and not more than 0.5 W, e.g.,
0.14 W. The third irradiation pitch is wider than the first
irradiation pitch of the first scanning process and narrower than
the second irradiation pitch of the second scanning process, and is
not less than 2 .mu.m and not more than 4 .mu.m, e.g., 2 .mu.m. The
setting value of the focus position of the laser beam in the third
scanning process is the same as that of the second scanning process
and may be, for example, a position at a depth of 10 to 35 .mu.m
from the second surface 12.
[0075] Although the cracks c are caused to extend easily in the
thickness direction of the wafer W by increasing the output of the
laser beam in the laser beam irradiation process, the meandering of
the cracks c also occurs easily. In the second scanning process
described above, the cracks are formed such that the meandering
along the scanning direction is suppressed by using a laser beam
output lower than that of the third scanning process. Then, in the
third scanning process, by scanning with a higher laser beam output
and at a narrower pitch than the second scanning process, the
cracks c that are formed in the second scanning process easily can
be caused to extend in the thickness direction of the wafer W while
still suppressing the meandering.
[0076] Here, the occurrence of the cracks is due to the stress
generated when forming the modified regions being released by the
occurrence of the cracks. If the irradiation pitch is set to be too
narrow, the modified regions are formed proximate to the modified
regions of which the stress has been released by the cracks.
Accordingly, the stress is not generated easily and cracks do not
occur easily for the modified regions proximate to such modified
regions including cracks. Accordingly, in the third scanning
process, the cracks that were formed in the second scanning process
can be caused to extend easily by scanning at the third irradiation
pitch, which is wider than the first irradiation pitch of the first
scanning process.
[0077] By performing the first scanning process, the second
scanning process, and the third scanning process such as those
described above, the meandering of the cracks can be suppressed
while maintaining a high fracture strength in the laser beam
irradiation process before singulation. As a result, unintended
breaking in the laser beam irradiation process and chipping of the
light-emitting element after singulation can be suppressed, and the
productivity can be increased.
[0078] Compared to the second scanning process and the third
scanning process, the laser beam irradiation of the first scanning
process is irradiated into a region proximate to the semiconductor
structure 20; therefore, the damage of the semiconductor structure
20 can be suppressed by setting the output of the laser beam to be,
for example, 0.2 W or less.
[0079] If the cracks c shown in FIG. 6C that are formed by the
first scanning process reach the region where the second modified
regions a2 and the third modified regions a3 are formed, the cracks
that are formed in the second scanning process easily meander due
to the effects of the cracks c formed in the first scanning
process. Even if such meandering cracks are caused to extend in the
third scanning process, the extension occurs while undesirably
meandering.
[0080] Therefore, in the second scanning process, the laser beam is
scanned in a region closer to the second surface 12 than the cracks
c extending from the first modified region a1 toward the second
surface 12. Thus, by performing the second scanning process, the
meandering is suppressed when causing the cracks to extend in the
third scanning process. Also, by setting the output of the laser
beam in the first scanning process to be, for example, 0.2 W or
less, the cracks c that extend in the direction from the first
modified region a1 toward the second surface 12 do not lengthen too
much. Accordingly, by setting the output of the laser beam to 0.2 W
or less, the cracks c can be prevented from reaching the regions
where the second modified regions a2 and the third modified regions
a3 are formed.
[0081] Although the first scanning process, the second scanning
process, and the third scanning process described above in the
laser irradiation of the embodiment are performed first along the
X-direction, the first scanning process, the second scanning
process, and the third scanning process may be performed first
along the Y-direction.
[0082] After the laser beam irradiation process, for example,
first, as shown in FIG. 4, the wafer W may be separated into the
multiple bars 30 along the dicing lines L1. Subsequently, as shown
in FIG. 5, the wafer W is separated into the multiple
light-emitting elements 50 along the dicing lines L2. For example,
the separating into the bars 30 and the separating into the
light-emitting elements 50 may be performed by applying a force to
the wafer W by using a pressing member.
[0083] At the side surfaces of the separated light-emitting
elements 50, the modified regions a1 to a3 described above are
exposed as regions having higher surface roughness than the
portions without the modified regions a1 to a3.
[0084] Certain embodiments of the present invention have been
described as examples. However, the present invention is not
limited to these examples. Based on the above-described embodiments
of the present invention, all embodiments that can be implemented
with appropriately design modification by one skilled in the art
are also within the scope of the present invention as long as the
gist of the present invention is included. Further, within the
scope of the spirit of the present invention, one skilled in the
art can conceive various modifications, and the modifications fall
within the scope of the present invention.
* * * * *