U.S. patent application number 16/295459 was filed with the patent office on 2020-09-10 for device for attachment to a bridge support bracket.
The applicant listed for this patent is Eric Roberts. Invention is credited to Eric Roberts.
Application Number | 20200283971 16/295459 |
Document ID | / |
Family ID | 1000004007858 |
Filed Date | 2020-09-10 |




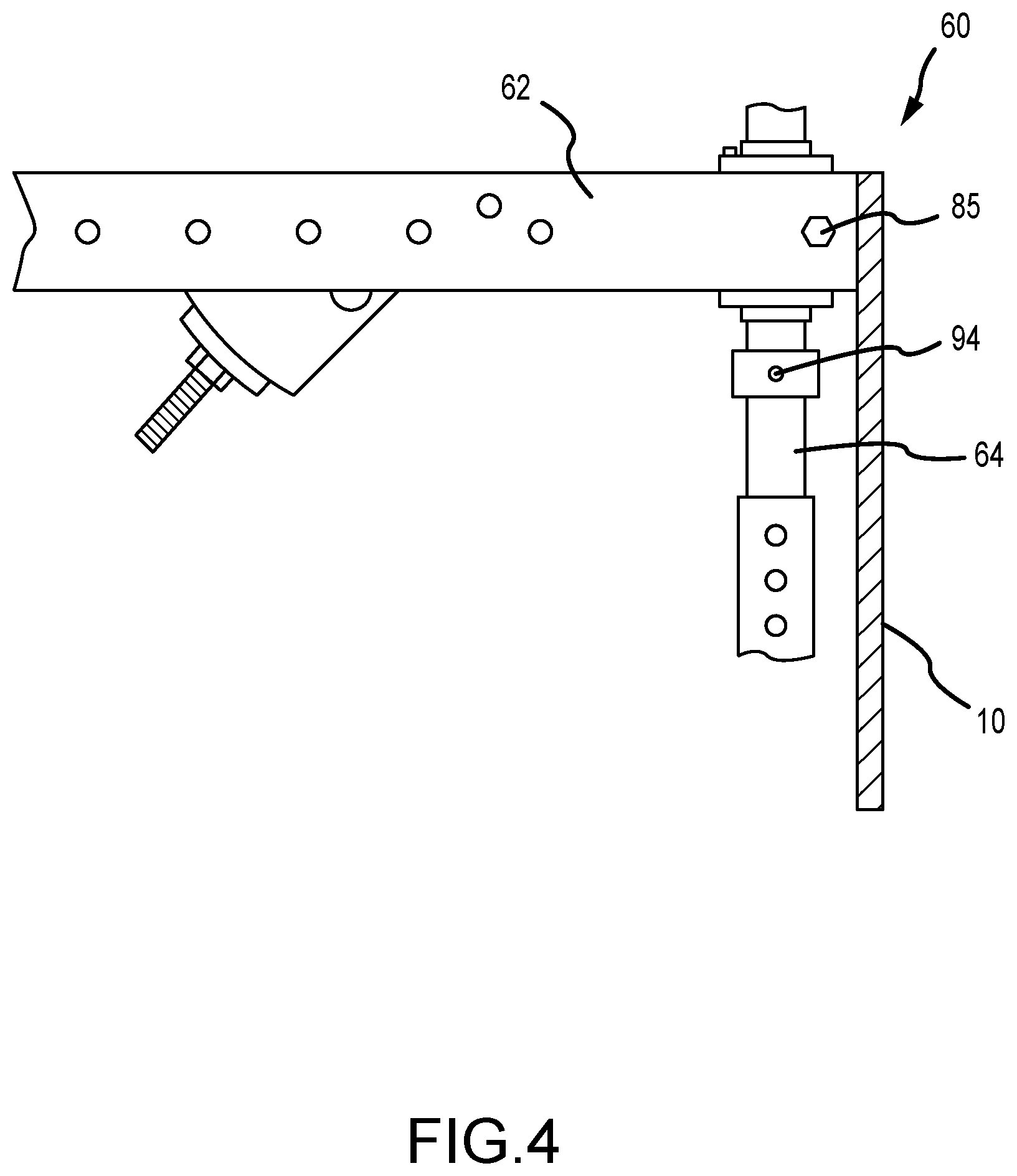






View All Diagrams
United States Patent
Application |
20200283971 |
Kind Code |
A1 |
Roberts; Eric |
September 10, 2020 |
DEVICE FOR ATTACHMENT TO A BRIDGE SUPPORT BRACKET
Abstract
A device for attachment to a bridge support bracket is adapted
to be connected to an end of a support bracket horizontal component
and to an end of a support bracket vertical component. The device
comprises a support adapted to be attached to the end of the
horizontal component, a sliding tube adapted to be attached to the
end of the vertical component, and a mounting tube attached to the
support for mounting the sliding for sliding movement relative to
the support. A slot is in the side of the mounting tube, and a nub
is attached to the sliding tube and extends through the slot. The
nub has a threaded opening therein, and a threaded rod extends
through and engages the threaded opening, the threaded rod being
mounted for rotation but not vertical movement relative to the
support, for moving the vertical piece vertically relative to the
support.
Inventors: |
Roberts; Eric; (Genoa City,
WI) |
|
Applicant: |
Name |
City |
State |
Country |
Type |
Roberts; Eric |
Genoa City |
WI |
US |
|
|
Family ID: |
1000004007858 |
Appl. No.: |
16/295459 |
Filed: |
March 7, 2019 |
Current U.S.
Class: |
1/1 |
Current CPC
Class: |
E01D 19/125 20130101;
E01D 19/10 20130101 |
International
Class: |
E01D 19/12 20060101
E01D019/12; E01D 19/10 20060101 E01D019/10 |
Claims
1. A device for attachment to a bridge support bracket, the support
bracket including a horizontal component, a vertical component, and
an angled component attached at one end to an end of the horizontal
component, and another end of the angled component is attached to
an end of the vertical component, the device being adapted to be
connected to the other end of the horizontal component and to the
other end of the vertical component, the device comprising: a
support adapted to be attached to the other end of the horizontal
component, a vertical piece adapted to be attached to the other end
of the vertical component, mounting means attached to the support
for mounting the vertical piece for sliding movement relative to
the support, and moving means attached to and between the support
and the vertical piece for moving the vertical piece vertically
relative to the support.
2. The device in accordance with claim 1 wherein the mounting means
is a mounting tube, and the vertical piece is a sliding tube
received in and slidable relative to the mounting tube.
3. The device in accordance with claim 2 wherein the moving means
comprises a slot in the side of the mounting tube, a nub attached
to the sliding tube and extending through the slot, the nub having
a nub threaded opening therein, and a threaded rod extending
through and engaging the nub threaded opening, the threaded rod
being mounted for rotation but not vertical movement relative to
the support, so that rotation of the threaded rod slides the nub
and sliding tube relative to the mounting tube and the support to
vary the combined length of the support bracket vertical component
and the vertical piece relative to the horizontal component to
change the angle of the horizontal component relative to the
vertical component.
4. The device in accordance with claim 1 wherein the support
comprises two spaced apart support plates, and wherein the threaded
rod is mounted for rotation relative to the support by the two
spaced apart support plates, each support plate being located on
opposite sides of the nub, with a threaded rod opening in each
support plate, the respective ends of the threaded rod each passing
through the respective plate threaded rod openings, and a threaded
rod nut fixed to each respective end of the threaded rod for
preventing sliding movement of the rod relative to the support,
with at least one nut being adapted to be rotated to in turn rotate
the threaded rod relative to the support.
5. The device in accordance with claim 1 wherein the vertical piece
is adapted to be attached to the other end of the support bracket
vertical component by having an attachment opening through one end
of the vertical piece, and a bolt that passes through the
attachment opening and through the other end of the vertical
component in order to secure the other end of the vertical
component to the end of the vertical piece.
6. A device for attachment to a bridge support bracket, the device
being adapted to be connected to an end of a support bracket
horizontal component and to an end of a support bracket vertical
component, the device comprising a support adapted to be attached
to the end of the horizontal component, a sliding tube adapted to
be attached to the end of the vertical component, and a mounting
tube attached to the support for mounting the sliding for sliding
movement relative to the support, the device having a slot is in
the side of the mounting tube, and the device further including a
nub attached to the sliding tube and extending through the slot,
the nub having a threaded opening therein, and a threaded rod
extending through and engaging the threaded opening, the threaded
rod being mounted for rotation but not vertical movement relative
to the support, for moving the vertical piece vertically relative
to the support.
Description
BACKGROUND
[0001] This application is directed to bridge building, and, more
particularly, to the use of bridge overhang support brackets used
in bridge construction.
[0002] As illustrated in FIG. 1, modern-day bridges use steel or
concrete I-beams 10 to support bridge loads. After placement of the
I-beams, concrete roadways 14 are formed on top of the I-beams.
Further, a portion 18 of the concrete roadway extends over the
outside edges of the I-beam. When constructing the bridge, concrete
forms 22 and the concrete 18 are supported by bridge overhang
support brackets 30 secured to the I-beam 10. Each support bracket
30 includes a horizontal component 32, a vertical component 34, and
an angled component 36 attached at one end 40 to an end 42 of the
horizontal component, and another end 46 attached to an end 48 of
the vertical component 34. Conventionally, the various ends are
attached to each other with nuts and bolts, with or without the use
of various adapters. The vertical component 34 is also attached at
one end 64 to an end 62 of the horizontal component. More
specifically, as illustrated in FIG. 2, the typical support bracket
vertical 34 and angled 36 components are telescoping tubes, and the
horizontal component 32 is made from spaced apart steel plates 49
and 51 (see FIG. 5). By varying the amount of telescoping of the
vertical and angled components, and the point of attachment of the
vertical and angled components to the horizontal component, various
support bracket dimensions can be accommodated in order to allow
the bridge overhang support bracket 30 to be used with different
bridge installations.
[0003] As shown in FIGS. 1 and 3, the connection of the support
bracket 30 to the I-beam 10 begins with the placement of a hanger
50 on the top of the I-beam 10. The hanger 50 is secured to the
I-beam 10 in a conventional fashion, such as by attaching the rear
of the hanger to the back side of the I-beam 10, as shown in FIG.
3, and a hanger end clip 52 is positioned just at the edge of the
I-beam where the support bracket 30 is to be positioned.
[0004] The next step in this process is to support the bridge
overhang support bracket 30 on the side of the I-beam 10 so a coil
rod 54 can be inserted through an opening (not shown) in the hangar
clip 52, and also inserted into a support bracket bolt holder 56 in
the support bracket 30. After being inserted through openings in
the hanger clip 52 and the bolt holder 56, the coil rod 54 is then
secured in place by coil nuts 58 on the ends of the coil rod
54.
[0005] Once in place, it is not uncommon for a bridge construction
worker to need to adjust the relative lengths of the support
bracket components, in order to adjust the relative angles between
the bracket sides. More specifically, the horizontal component 32
may not end up being horizontal, so, with other points of
attachment being fixed, by varying one point of attachment the
relative angle between the vertical component 34 and the horizontal
component 32 can changed to result in a truly level horizontal
component.
[0006] Two examples of how this is currently accomplished are as
follows. As shown in FIG. 2, it is common to have a threaded bolt
54 within the horizontal component 32, with a bolt head 57
accessible from outside the support bracket 30 for rotating the
threaded bolt 54. The bolt in turn is received in a clip 58 that
holds an end of the angled component 36 inside the horizontal
component 32. By rotating the threaded bolt 54, the point of
attachment of the angled component relative to the horizontal
component can be varied. In another bridge support bracket design,
as illustrated in U.S. Pat. No. 7,032,268, the vertical component
is a threaded rod, which can be turned in order to vary the
threaded rod points of attachment between the horizontal component
and the angled component, in order to change the relative angles
between the components.
SUMMARY
[0007] Disclosed is a device for attachment to a bridge support
bracket. The device is adapted to be connected to an end of a
support bracket horizontal component and to an end of a support
bracket vertical component. The device comprises a support adapted
to be attached to the end of the horizontal component, a sliding
tube adapted to be attached to the end of the vertical component,
and a mounting tube attached to the support for mounting the
sliding for sliding movement relative to the support. A slot is in
the side of the mounting tube, and a nub is attached to the sliding
tube and extends through the slot. The nub has a threaded opening
therein, and a threaded rod extends through and engages the
threaded opening, the threaded rod being mounted for rotation but
not vertical movement relative to the support, for moving the
vertical piece vertically relative to the support.
DRAWINGS
[0008] FIG. 1 is a side perspective view illustrating bridge
construction. An I-beam is show, with an attached bridge support
bracket, and forming for the concrete bridge.
[0009] FIG. 2 is a side perspective view illustrating further
details of the bridge support bracket.
[0010] FIG. 3 is a side view of a portion of an I-beam, a hanger,
and a coil rod passing through a hanger end clip and a bracket bolt
holder. A portion of a vertical component of the bridge support
bracket is shown attached to a bridge support bracket horizontal
component.
[0011] FIG. 4 is an enlarged side view of a portion of the support
bracket illustrated in FIG. 4, together with an adjustment device
according to this disclosure.
[0012] FIG. 5 is a top perspective view illustrating the adjustment
device of this disclosure being slid onto the end of the horizontal
component of the bridge support bracket.
[0013] FIG. 6 is a top perspective view of the adjustment device
attached to the end of the horizontal component of the bridge
support bracket.
[0014] FIG. 7 is a side perspective view of the adjustment device
according to this disclosure.
[0015] FIG. 8 is a side perspective view of another side of the
adjustment device shown in FIG. 7.
[0016] FIG. 9 is an enlarged side perspective view of the
adjustment device shown in FIG. 7.
[0017] FIG. 10 is an end view of the adjustment device shown in
FIG. 7.
[0018] FIG. 11 is a side perspective view of the adjustment device,
with a sliding tube shown in a first position relative to a holding
tube.
[0019] FIG. 12 is a side perspective view similar to FIG. 11, only
showing the sliding to the different second position relative to
the holding to.
[0020] Before one embodiment of the invention is explained in
detail, it is to be understood that the invention is not limited in
its application to the details of the construction and the
arrangements of components set forth in the following description
or illustrated in the drawings. The invention is capable of other
embodiments and of being practiced or being carried out in various
ways. Also, it is to be understood that the phraseology and
terminology used herein is for the purpose of description and
should not be regarded as limiting. Use of "including" and
"comprising" and variations thereof as used herein is meant to
encompass the items listed thereafter and equivalents thereof as
well as additional items. Use of "consisting of" and variations
thereof as used herein is meant to encompass only the items listed
thereafter and equivalents thereof. Further, it is to be understood
that such terms as "forward", "rearward", "left", "right", "upward"
and "downward", etc., are words of convenience in reference to the
drawings and are not to be construed as limiting terms.
DESCRIPTION OF A PREFERRED EMBODIMENT
[0021] Although the disclosure hereof is detailed and exact to
enable those skilled in the art to practice the invention, the
physical embodiments herein disclosed merely exemplify the
invention which may be embodied in other specific structures. While
the preferred embodiment has been described, the details may be
changed without departing from the invention, which is defined by
the claims.
[0022] Illustrated in the drawings is a metal device 60 for
attachment to a bridge overhang support bracket 30. The device 60
according to this disclosure is adapted, as shown in FIG. 4, to be
connected to the other end 62 of the horizontal component 32 and to
the other end 64 of the vertical component 34, so that the points
of attachment between the horizontal component and the angled
component can be varied in order to change the relative angles
between the components. Access to the device 60 is at the end of
the horizontal component by the I-beam, thus providing bridge
builders with a ready and convenient method of leveling the support
bracket horizontal component 32.
[0023] The device 60 according to this disclosure, as shown in FIG.
9, comprises a support 70 adapted to be attached to the other end
62 of the horizontal component 32, a vertical piece 72 adapted to
be attached to the other end 64 of the vertical component 34,
mounting means 74 attached to the support 70 for mounting the
vertical piece 72 for sliding movement relative to the support 70,
and moving means 76 attached to and between the support 70 and the
vertical piece 72 for moving the vertical piece 72 vertically
relative to the support 70.
[0024] More specifically, as shown in FIG. 7, the support is in the
form of two spaced apart rectangular plates 78 and 79. The spacing
of the support plates 78 and 79 is such that it allows the end
plates to snuggly slide along the top 80 and bottom 82 of the
horizontal component 32, as illustrated in FIGS. 6 and 7. The
spaced apart plates 49 and 51 at the end of the horizontal
component 32 provides room for the mounting of the vertical piece
72 and the mounting means 74, and the support plates 78 and 79 hold
the device 60 in place on the horizontal component 32.
[0025] In the illustrated embodiment, the mounting means is in the
form of a square mounting tube 74, and the vertical piece is a
sliding tube 72 received in and slidable relative to the mounting
tube 74. More specifically, the mounting tube 74 has a portion of
one side of the tube removed to provide a vertical piece access
slot 76, as shown in FIG. 9. The vertical piece 72 extends between
and through the spaced apart rectangular support plates 78 and 79,
and the vertical piece slot 76 is located between the spaced apart
support plates 78 and 79. An outward extension 83 (see FIG. 8) from
the mounting tube 74, opposite the vertical piece access slot 76,
has an opening 87 therethrough, adapted to receive therein a
mounting bolt 85 (see FIGS. 3 and 6) extending between the plates
49 and 51. This secures the device 60 in place and prevents further
horizontal sliding of the device 60 along the horizontal component
32 after the device 60 is positioned on the horizontal component
32.
[0026] The moving means, as shown in FIGS. 7 and 8, is in the form
of the slot 76 in the side of the mounting tube 74, and a nub 80
attached to the sliding tube 72 and extending through the slot 76,
the nub 80 having a nub threaded opening therein, and a threaded
rod 84 extending through and engaging the nub threaded opening, the
threaded rod 84 being mounted for rotation but not vertical
movement relative to the support plates 78 and 79, so that rotation
of the threaded rod 84 slides the nub 80 and sliding tube 72
relative to the mounting tube 74. This allows the device 60 to vary
the combined length of the support bracket vertical component 34
and sliding tube 72 relative to the horizontal component 32 so as
to change the angle of the horizontal component 32 relative to the
vertical component 34. The nub 80 also serves to keep the sliding
tube 72 within the mounting tube 74.
[0027] More particularly, the threaded rod 84 is mounted for
rotation relative to the support 70 by the support plates 78 and 79
located on opposite sides of the nub 80, with an opening in each
support plate, the respective ends of the threaded rod each passing
through the respective plate openings. Respective nuts 86 and 87
are each fixed such as by welding on each respective end of the
threaded rod 84. At least one nut 86 is adapted to be rotated to in
turn rotate the threaded rod 84 relative to the support 70, such as
by the use of a drill 90 (see FIGS. 11 and 12).
[0028] The sliding tube 72 is adapted to be attached to the other
end 64 of the support bracket vertical component 34 by having a
U-shaped attachment 91 (see FIG. 9) with an attachment opening 92
through one end of the sliding tube 72, and a bolt 94 (see FIG. 4)
that passes across the attachment and through the attachment's
spaced apart arms in order to secure the other end 64 of the
vertical component 34 to the end of the sliding tube 72. The bolt
94 passes through matching openings (not shown) in the other end 64
of the vertical component 34.
[0029] To use the device 60, a worker will slide the device 60 onto
the horizontal component 32. The sliding tube 72 is then attached
to the other end 64 of the vertical component 34, the vertical
component 34 being then adjusted, such as by telescoping, so as to
obtain the desired geometry of the bridge overhang support bracket
30. The bracket 30 is then positioned along the side of the I-beam
10 and secured to the I-beam 10. Then, in order to level or
otherwise adjust the angle of the horizontal component 32 relative
to the vertical component 34, the nut 86 on the end of the threaded
rod 84 can be rotated, so that the vertical position of the sliding
tube 72 relative to the horizontal component 32 can vary, as shown
in FIGS. 11 and 12.
[0030] Use of the device 60 thus eliminates the need to reach the
end 42 of the horizontal component 32, which involved the need to
either use a bucket truck to reach the end, or the need to climb
out to the end of the support bracket to reach the threaded bolt
head 57. Instead, a bridge builder can remain on top of the beam,
and with the use of a drill, adjust the level of the horizontal
component 32, using conventional bridge overhang support bracket
components.
[0031] The foregoing is considered as illustrative only of the
principles of the invention. Furthermore, since numerous
modifications and changes will readily occur to those skilled in
the art, it is not desired to limit the invention to the exact
construction and operation shown and described. While the preferred
embodiment has been described, the details may be changed without
departing from the invention, which is defined by the claims.
[0032] Various other features and advantages of the invention will
be apparent from the following claims.
* * * * *