U.S. patent application number 16/617559 was filed with the patent office on 2020-09-03 for 700mpa class steel bar having excellent yield ratio and uniform elongation property, and method for manufacturing the same.
This patent application is currently assigned to KOREA UNIVERSITY RESEARCH AND BUSINESS FOUNDATION. The applicant listed for this patent is FOUNDATION FOR RESEARCH AND BUSINESS, SEOUL NATIONAL UNIVERSITY OF SCIENCE AND TECHNOLOGY, KOREA UNIVERSITY RESEARCH AND BUSINESS FOUNDATION. Invention is credited to Taeun HONG, Byoungchul HWANG, Joonho LEE, Sangin LEE, Sangchul SHIM.
Application Number | 20200277681 16/617559 |
Document ID | / |
Family ID | 1000004854843 |
Filed Date | 2020-09-03 |
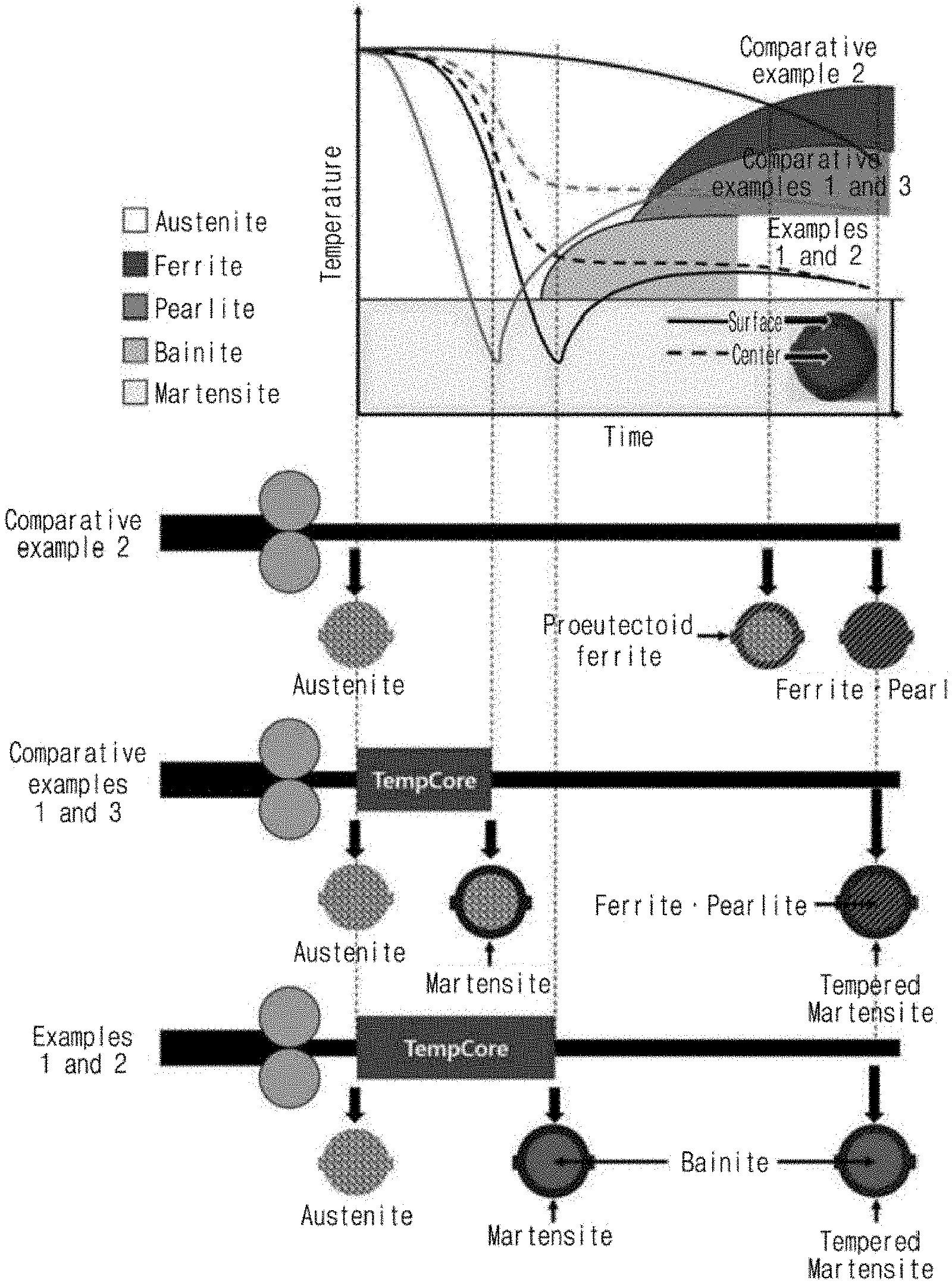
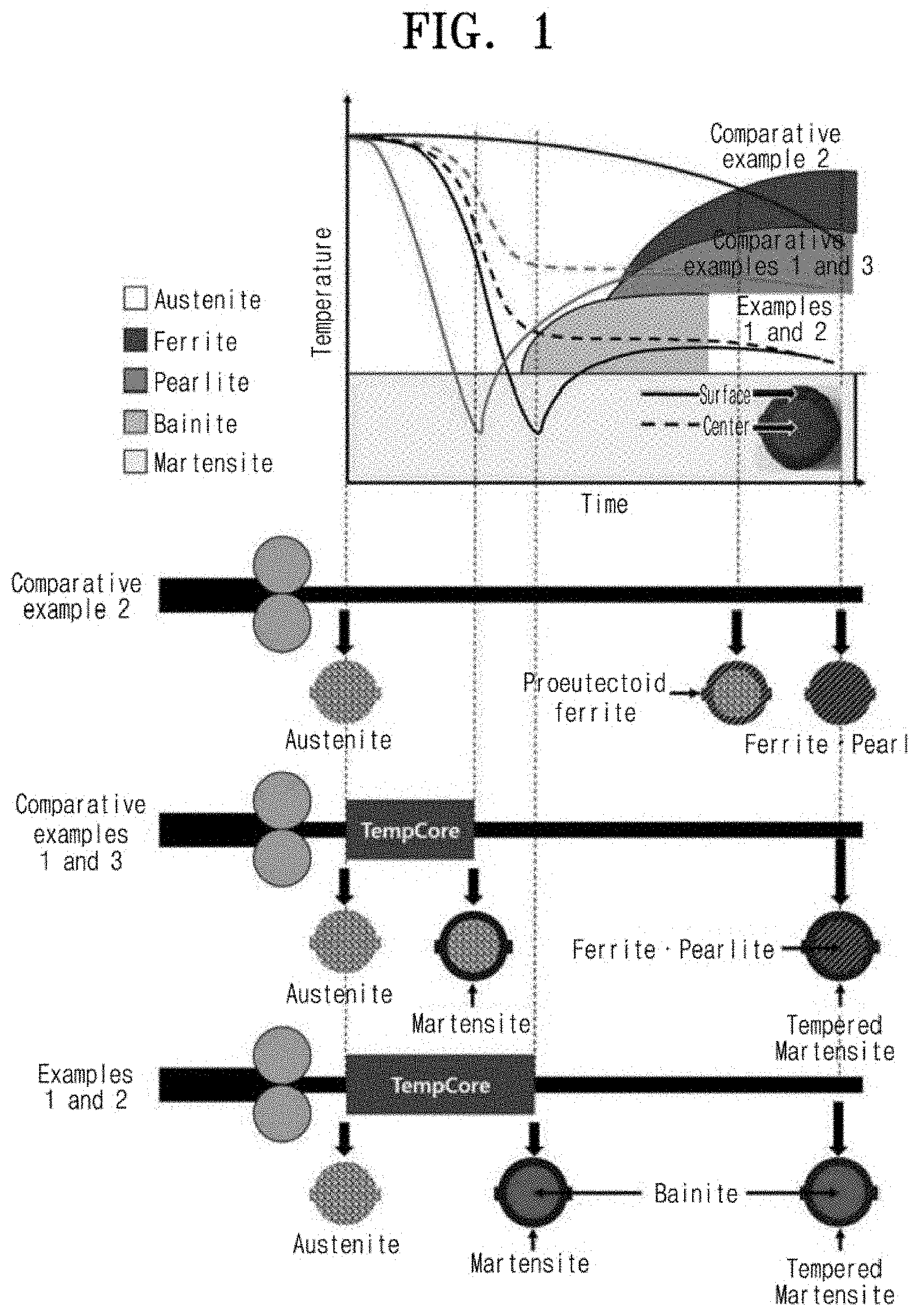
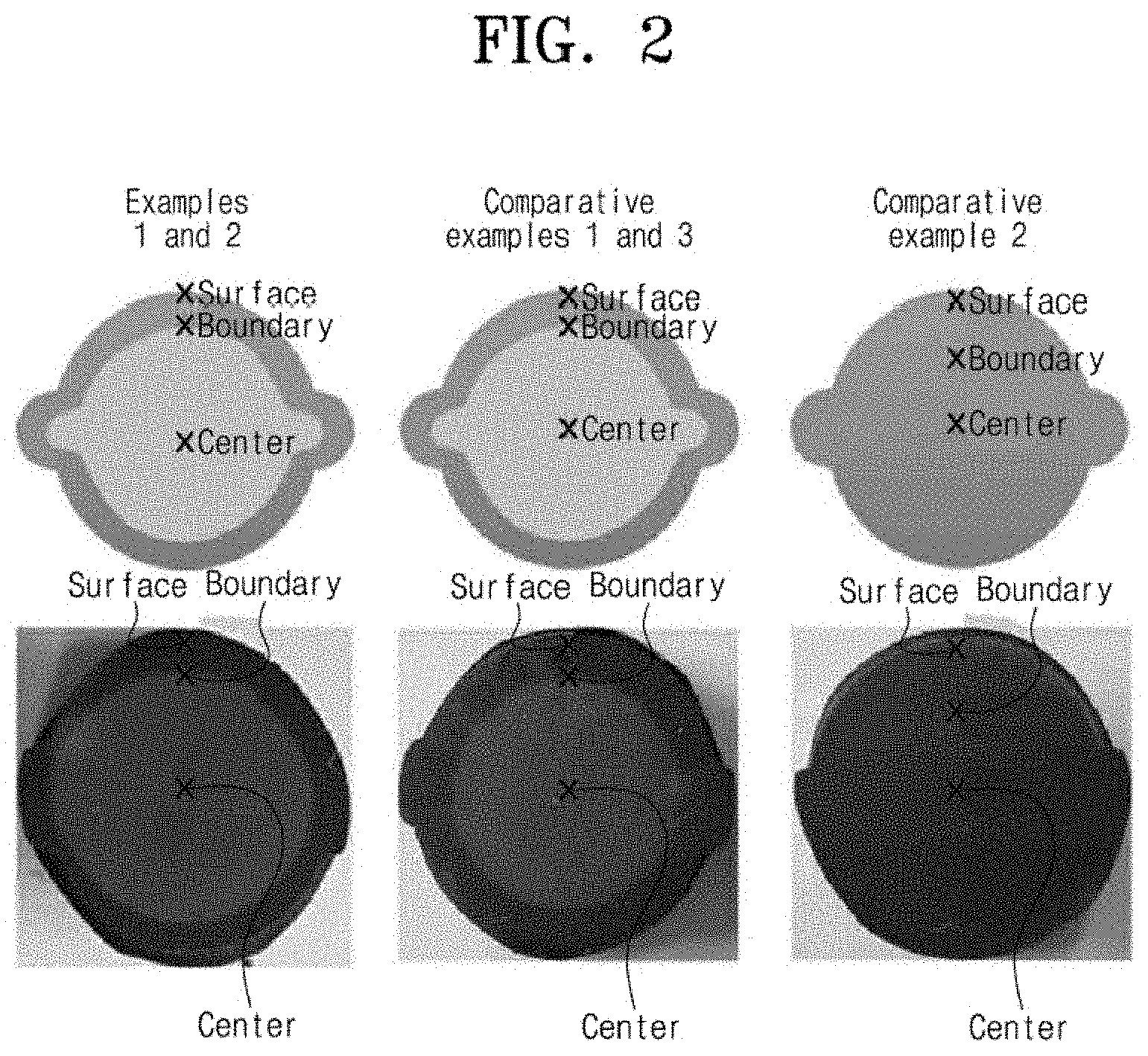
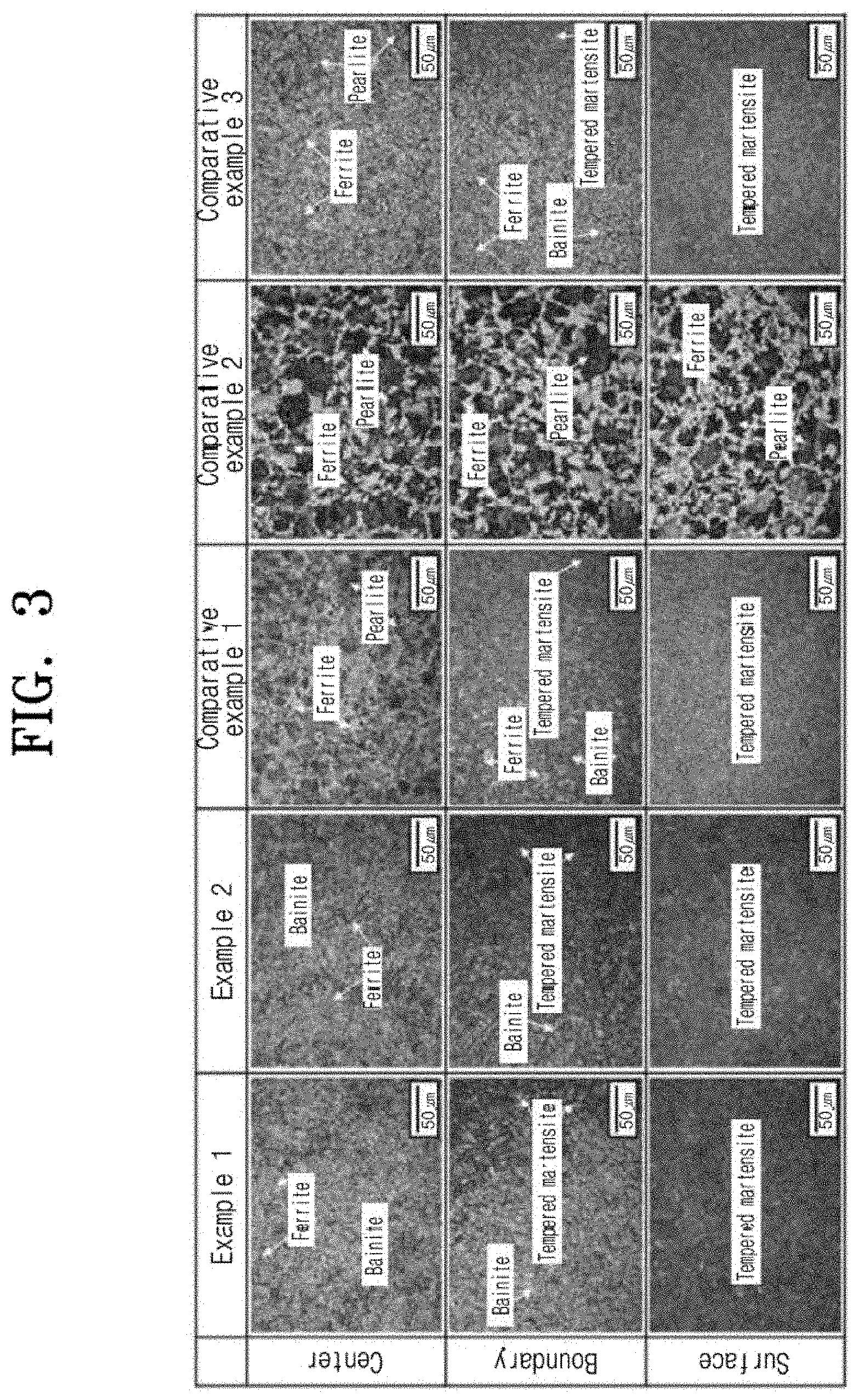
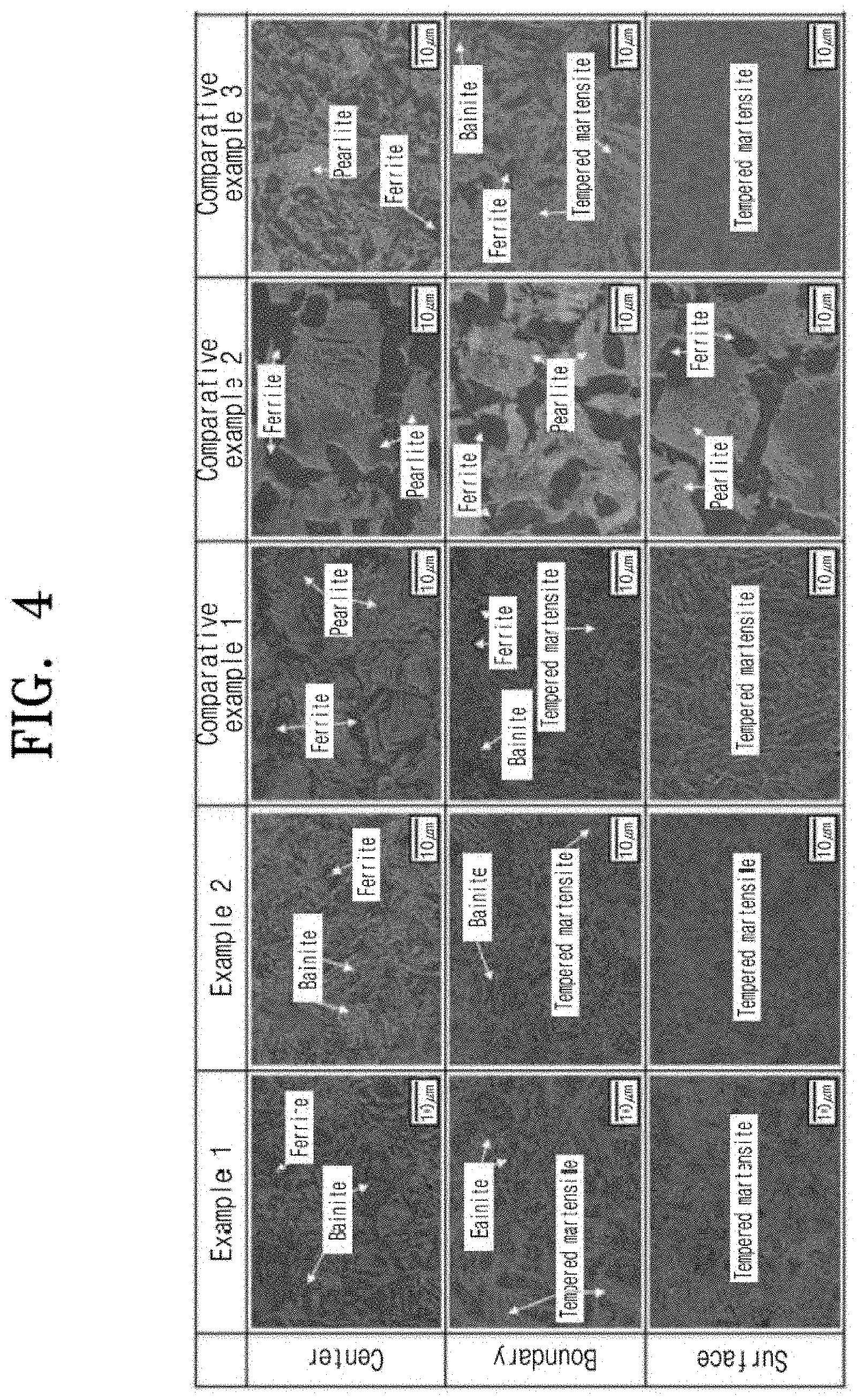
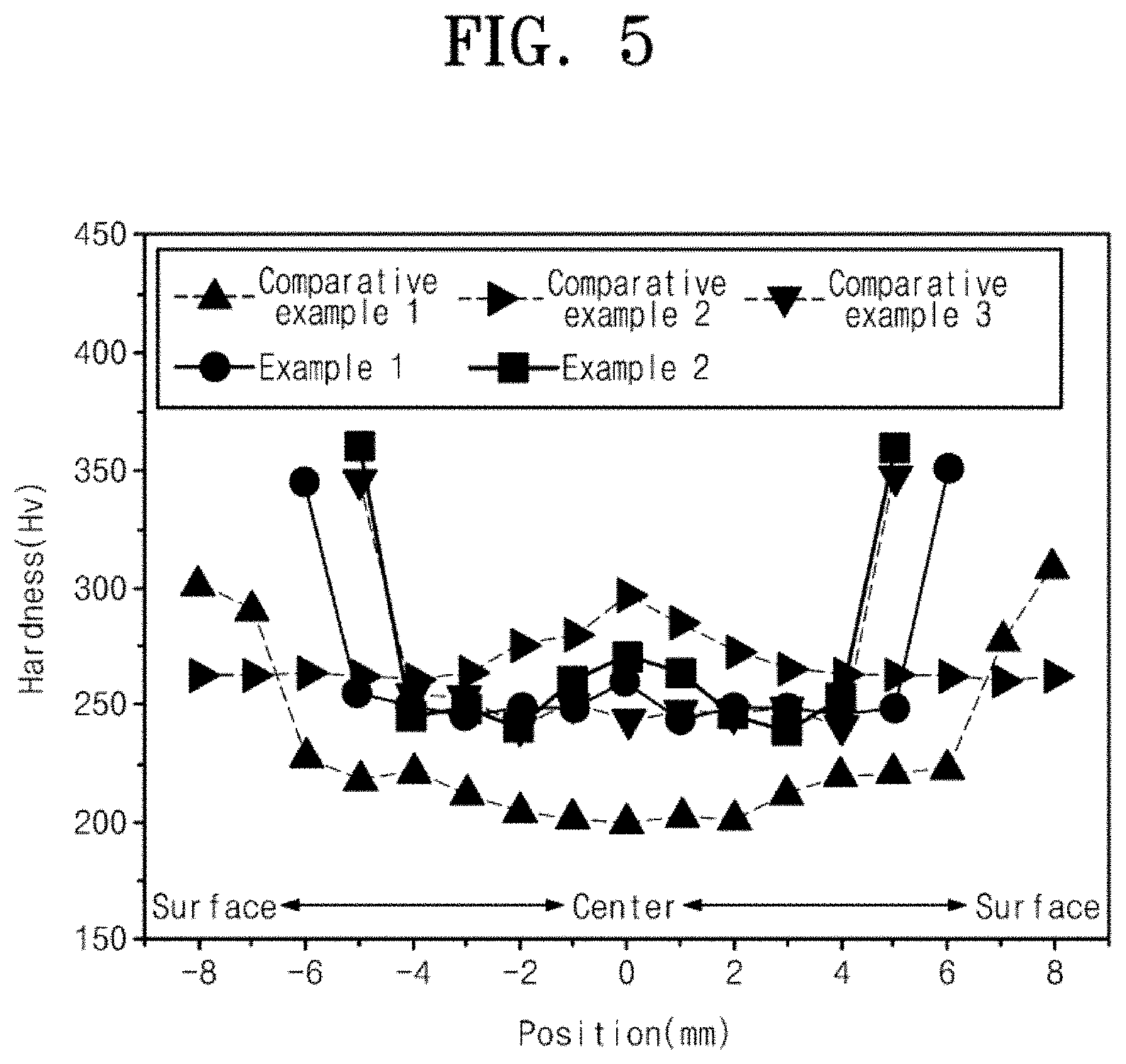
United States Patent
Application |
20200277681 |
Kind Code |
A1 |
LEE; Joonho ; et
al. |
September 3, 2020 |
700MPa CLASS STEEL BAR HAVING EXCELLENT YIELD RATIO AND UNIFORM
ELONGATION PROPERTY, AND METHOD FOR MANUFACTURING THE SAME
Abstract
A steel bar having yield strength of 700 MPa class, excellent
yield ratio, and excellent uniform elongation property is provided.
The steel bar includes bainite and ferrite included in a center of
the steel bar and bainite accounts for 20 to 80% by volume.
Inventors: |
LEE; Joonho; (Seongnam-si,
KR) ; SHIM; Sangchul; (Busan, KR) ; HWANG;
Byoungchul; (Seoul, KR) ; HONG; Taeun; (Seoul,
KR) ; LEE; Sangin; (Seoul, KR) |
|
Applicant: |
Name |
City |
State |
Country |
Type |
KOREA UNIVERSITY RESEARCH AND BUSINESS FOUNDATION
FOUNDATION FOR RESEARCH AND BUSINESS, SEOUL NATIONAL UNIVERSITY OF
SCIENCE AND TECHNOLOGY |
Seoul
Seoul |
|
KR
KR |
|
|
Assignee: |
KOREA UNIVERSITY RESEARCH AND
BUSINESS FOUNDATION
Seoul
KR
FOUNDATION FOR RESEARCH AND BUSINESS, SEOUL NATIONAL UNIVERSITY
OF SCIENCE AND TECHNOLOGY
Seoul
KR
|
Family ID: |
1000004854843 |
Appl. No.: |
16/617559 |
Filed: |
November 23, 2018 |
PCT Filed: |
November 23, 2018 |
PCT NO: |
PCT/KR2018/014517 |
371 Date: |
November 27, 2019 |
Current U.S.
Class: |
1/1 |
Current CPC
Class: |
C22C 38/02 20130101;
C21D 8/065 20130101; C21D 6/005 20130101; C21D 2211/002 20130101;
C22C 38/04 20130101; C22C 38/12 20130101; C21D 6/008 20130101; C21D
2211/005 20130101; C21D 9/0075 20130101 |
International
Class: |
C21D 9/00 20060101
C21D009/00; C21D 8/06 20060101 C21D008/06; C21D 6/00 20060101
C21D006/00; C22C 38/12 20060101 C22C038/12; C22C 38/04 20060101
C22C038/04; C22C 38/02 20060101 C22C038/02 |
Foreign Application Data
Date |
Code |
Application Number |
Nov 16, 2018 |
KR |
10-2018-0141344 |
Claims
1. A steel bar having yield strength of 700 MPa class, excellent
yield ratio, and excellent uniform elongation property, the steel
bar comprising: bainite and ferrite included in a center of the
steel bar, wherein the bainite accounts for 20 to 80% by
volume.
2. The steel bar of claim 1, wherein the steel bar has the yield
strength of 700 to 900 MPa and the yield ratio of 1.25 to 1.50.
3. The steel bar of claim 1, wherein, when manufacturing the steel
bar, a bainite structure is formed in the center of the steel bar
by a rapid cooling through a Tempcore cooling process.
4. The steel bar of claim 3, wherein the Tempcore cooling process
is performed at a speed of the steel bar of 5 to 20 m/sec, a
pressure of cool water of 10 to 30 bar, and an amount of water of
100 to 300 m.sup.3/hr.
5. A method of manufacturing a steel bar having yield strength of
700 MPa class, excellent yield ratio, and excellent uniform
elongation property, the method comprising: heating a billet for
the steel bar; hot-rolling the heated billet to be formed in a
steel bar shape; cooling a rolled body having the steel bar shape
at a Tempcore; and performing reheating and additional cooling,
wherein the cooling at the Tempcore is performed at a speed of the
steel bar of 5 to 20 m/sec, a pressure of cool water of 10 to 30
bar, and an amount of water of 100 to 300 m.sup.3/hr.
6. The method of claim 5, wherein, in the heating of the billet for
the steel bar, the billet for the steel bar includes carbon (C) of
0.18 to 0.30 wt %, manganese (Mn) of 0.65 to 2.00 wt %, silicon
(Si) of 0.13 to 0.40 wt %, vanadium (V) of 0 to 0.10 wt %, the
remaining Fe, and other unavoidable impurity components.
7. The method of claim 5, wherein, in the reheating, a temperature
of the center of the steel bar is maintained at 500 to 600.degree.
C.
8. The method of claim 5, wherein, after the reheating, a structure
of the center of the steel bar includes bainite and ferrite.
9. The method of claim 5, wherein, after the reheating and the
additional cooling, the steel bar has the yield strength of 700 to
900 MPa and the yield ratio of 1.25 to 1.50.
Description
CROSS-REFERENCE TO RELATED APPLICATIONS
[0001] A claim for priority under 35 U.S.C. .sctn. 119 is made to
Korean Patent Application No. 10-2018-0141344 filed on Nov. 16,
2018 and PCT International Application No. PCT/KR2018/014517 filed
on Nov. 23, 2018, the entire contents of which are hereby
incorporated by reference.
BACKGROUND
[0002] Embodiments of the inventive concept described herein relate
to an ultra-high strength steel bar having excellent yield ratio
(tensile-to-yield strength, TS/YS) and uniform elongation property
and a method of manufacturing the same, more particularly, relate
to a steel bar having yield strength of a 700 MPa class having a
yield ratio and an excellent uniform elongation property which are
suitable for a seismic resistant steel bar, in which a cooling
process is improved to increase the yield strength of the steel bar
and to increase the yield ratio of the steel bar, and a method of
the same.
[0003] In recent years, as a building heightens, a cross-section of
a vertical member has increased and a seismic resistant design of
the building has attracted attention due to earthquakes occurring
around the world. Therefore, importance of development and
production technology of a high strength seismic resistant steel
bar mainly used as a structural material of the building has
increased. The high strength seismic resistant steel bar is
designed to have higher yield strength and yield ratio than a
general steel bar, thereby withstanding loads in small amounts and
improving seismic resistant performance of the building by securing
a margin from a start of plastic deformation after elastic
deformation to final fracture, and thus damage of human life is
minimized.
[0004] In general, the seismic resistant performance of the steel
bar is related to a deformation capacity of the material and the
deformation capacity is determined by yield ratio or uniform
elongation property. Therefore, specification related to the
deformation capacity will be important in specification of the
ultra-high strength seismic resistant steel bar having the yield
strength of 700 MPa class or more. Thus, systematic studies on the
high yield strength, the yield ratio, and the uniform elongation
property are required to develop the high strength seismic
resistant steel bar having the yield strength of 700 MPa class or
more.
[0005] In recent, the steel bar is manufactured through various
methods and an addition of alloying elements to improve the
strength and seismic resistant performance of the steel bar. In
particular, a solid solution strengthening and a precipitation
strengthening by the addition of the alloying elements have been
mainly utilized to secure the strength and seismic resistant
performance in a limited manufacturing process. However, excessive
addition of alloying elements causes some problems in welding and
material cost increase during manufacturing, thereby limiting a
carbon equivalent (Ceq) to a specific value or less.
[0006] However, the ultra-high strength seismic resistant steel bar
having the yield strength of 700 MPa class or more has not been
developed so far.
[0007] Therefore, development of the ultra-high strength seismic
resistant steel bar having the yield strength of 700 MPa class or
more which is excellent in the yield strength, the yield ratio, and
the uniform elongation property has been required.
SUMMARY
[0008] Embodiments of the inventive concept provide an ultra-high
strength seismic resistant steel bar having yield strength of 700
MPa class or more.
[0009] Embodiments of the inventive concept provide a seismic
resistant steel bar having yield strength of 700 MPa or more, yield
ratio of 1.25 or more, and excellent uniform elongation
property.
[0010] According to an exemplary embodiment, a steel bar having
yield strength of 700 MPa class, excellent yield ratio, and
excellent uniform elongation property includes bainite and ferrite
included in a center of the steel bar, wherein bainite accounts for
20 or more by volume.
[0011] In addition, according to the inventive concept, the steel
bar has the yield strength of 700 to 900 MPa and the yield ratio of
1.25 to 1.50.
[0012] In addition, according to the inventive concept, when
manufacturing the steel bar, a bainite structure is formed in the
center of the steel bar by a rapid cooling through a Tempcore
cooling process.
[0013] In addition, according to the inventive concept, the
Tempcore cooling process is performed at a speed of the steel bar
of 5 to 20 m/sec, a pressure of cool water of 10 to 30 bar, and an
amount of water of 100 to 300 m.sup.3/hr.
[0014] According to an exemplary embodiment, a method of
manufacturing a steel bar having yield strength of 700 MPa class,
excellent yield ratio, and excellent uniform elongation property
includes heating a billet for the steel bar, hot-rolling the heated
billet to be formed in a steel bar shape, cooling the rolled body
having the steel bar shape at a Tempcore; and performing reheating
and additional cooling, wherein the cooling at the Tempcore is
performed at a speed of the steel bar of 5 to 20 m/sec, a pressure
of cool water of 10 to 30 bar, and an amount of water of 100 to 300
m.sup.3/hr.
[0015] In addition, according to the inventive concept, in the
heating of the billet for the steel bar, the billet for the steel
bar includes carbon (C) of 0.18 to 0.30 wt %, manganese (Mn) of
0.65 to 2.00 wt %, silicon (Si) of 0.13 to 0.40 wt %, vanadium (V)
of 0 to 0.10 wt %, the remaining Fe, and other unavoidable impurity
components.
[0016] In addition, according to the inventive concept, in the
reheating, a temperature of the center of the steel bar is
maintained at 500 to 600.degree. C.
[0017] In addition, according to the inventive concept, after the
reheating, a structure of the center of the steel bar includes
bainite and ferrite.
[0018] In addition, according to the inventive concept, after the
reheating and the additional cooling, the steel bar has the yield
strength of 700 to 900 MPa and the yield ratio of 1.25 to 1.50.
BRIEF DESCRIPTION OF THE FIGURES
[0019] The above and other objects and features will become
apparent from the following description with reference to the
following figures, wherein like reference numerals refer to like
parts throughout the various figures unless otherwise specified,
and wherein:
[0020] FIG. 1 shows temperature change of steel bars and structure
change by location depending on processes of Examples and
Comparative Examples;
[0021] FIG. 2 shows cross-sectional views of steel bars of Examples
according to the inventive concept and Comparative Examples;
[0022] FIG. 3 shows optical micrographs of Examples according to
the inventive concept and Comparative Examples;
[0023] FIG. 4 shows scanning electron micrographs of Examples
according to the inventive concept and Comparative Examples;
and
[0024] FIG. 5 shows a graph showing positional hardness of Examples
according to the inventive concept and Comparative Examples.
DETAILED DESCRIPTION
[0025] Hereinafter, embodiments of the inventive concept will be
described in detail with reference to the accompanying drawings.
The embodiment of the inventive concept may be modified in various
forms, and the scope of the inventive concept should not be
construed as being limited to the following embodiments. These
embodiments are provided to more fully describe the inventive
concept to those skilled in the art. Thus, shapes of elements of
the drawings have been exaggerated to emphasize a clearer
description.
[0026] The inventive concept provides a method of a steel bar
having yield strength of 700 MPa class, which is excellent in yield
ratio and uniform elongation property, including heating a billet
for a steel bar; hot-rolling the heated billet to be formed in a
steel bar shape; cooling the rolled billet having the steel bar
shape at a Tempcore; and performing reheating and additional
cooling.
[0027] According to the inventive concept, the billet for the steel
bar may include carbon (C) of 0.18 to 0.30 wt %, manganese (Mn) of
0.65 to 2.00 wt %, silicon (Si) of 0.13 to 0.40 wt %, vanadium (V)
of 0 to 0.10 wt %, the remaining Fe, and other unavoidable impurity
components.
[0028] Carbon (C) is an effective element for increasing strength.
When an amount of carbon (C) is low, desired high strength is not
obtained and when the amount of carbon (C) is high, the strength is
increased but deterioration of toughness and ductility shows a
remarkable increase. Therefore, carbon (C) is preferably 0.18 to
0.30 wt % to obtain the high strength.
[0029] Manganese (Mn) has an effect of increasing the strength
during a heat treatment. Manganese (Mn) is an essential element for
strength compensation because the amount of C added is limited.
When the amount of manganese (Mn) is low, the effect of improving
hardenability is almost absent. When manganese (Mn) exceeds a
specific range, weldability is lowered and risk of cracking is
increased. Therefore, the amount of manganese (Mn) is preferably
0.65 to 2.00 wt %.
[0030] Silicon (Si) is an element essential for deoxidation of a
steel and for improving the strength. When an amount of silicon
(Si) is 0.10 wt % or less, the desired high strength is hardly
obtained. When the amount of silicon (Si) exceeds a specific range,
the toughness and the ductility decrease. Accordingly, the amount
of silicon (Si) is preferably 0.13 to 0.40 wt %.
[0031] Vanadium (V) is added to ensure the strength by solid
solution strengthening and precipitation strengthening. Vanadium
plays roles of preventing movement at an austenite grain boundary
during the heating and the hot-rolling to make austenite grains
fine, of suppressing nucleation at the austenite grain boundary to
increases the hardenability of the steel bar, and of being combined
with carbon or nitrogen and forming a precipitate to improve the
strength of the steel bar. However, when vanadium (V) is
excessively added, cracking may occur during the rolling.
Therefore, vanadium (V) is preferably more than 0 and 0.01 wt % or
less.
[0032] In the heating of the billet for the steel bar, all carbides
and carbonitrides, which are added substances, are completely
dissolved, and a heating temperature is 900 to 1100.degree. C.
[0033] After the heating of the billet for the steel bar, the
heated billet is subjected to the hot-rolling.
[0034] In the hot-rolling after the heating of the billet for the
steel bar, the heated billet may be formed in the steel bar shape
through a roughing mill, an intermediate mill, and a finishing
mill. The hot-rolling process is a method of manufacturing a
general steel bar, and a hot-rolling technology is not particularly
limited.
[0035] The cooling at the Tempcore is performed after the
hot-rolling.
[0036] In the inventive concept, a cooling condition is important
in the cooling at the Tempcore. In a case of a rapid cooling, a
condition where bainite is sufficiently formed in the center may be
satisfied, and thus a bainite structure may be formed.
[0037] That is, in the reheating after the rapid cooling, a section
in which bainite is formed in the center is maintained for a long
time to form the bainite structure of 20% by volume or more
[0038] Preferably, the bainite structure may be formed 20 to 80% by
volume.
[0039] The cooling at the Tempcore may be performed by water
cooling. In a cooling line of the Tempcore, a rolled body of the
steel bar, a position of a cooling equipment, and an amount of
cooling water are determined. To this end, the amount of cooling
water and the speed are adjusted to convert austenite to martensite
at a surface of the steel bar, and thus a cooling rate may be
determined after the rolled body of the steel bar is reheated above
a start temperature of bainite formation at the center upon a final
reheating.
[0040] The bainite formation temperature may be 500 to 600.degree.
C. At an end of the cooling process at the Tempcore, the center
maintains the temperature of 500 to 600.degree. C. In the
reheating, the center maintains the temperature of 500 to
600.degree. C.
[0041] To this end, the speed of the steel bar, pressure of water,
and the amount of water may be adjusted in the cooling at the
Tempcore. The speed of the steel bar may be 5 to 20 m/sec, the
pressure of water may be 10 bar or more, preferably 10 to 20 bar,
and the amount of water may be 100 m.sup.3/hr or more, preferably
100 to 300 m.sup.3/hr.
[0042] The speed of the steel bar, the pressure of water, and the
amount of water may be adjusted in the cooling at the Tempcore to
form a tempered martensite structure in the surface and a
low-temperature metamorphic structure such as tempered martensite
and bainite in a boundary, from the first austenite through the
cooling process. In addition, bainite is mainly formed in the
center and ferrite is formed in the rest
[0043] In the center, bainite accounts for 20% by volume or more,
and the rest is occupied by ferrite. Preferably bainite may account
for 20% to 80% by volume. This is possible because the cooling at
the Tempcore rapidly lowers to a temperature at which bainite is
formed and then the bainite formation temperature is maintained in
the reheating.
[0044] The inventive concept is characterized by maintaining the
section, in which bainite is formed in the center of the steel bar,
for a long time through the reheating process after the cooling.
Therefore, a specific amount or more of bainite is formed and thus
the yield strength is improved.
[0045] The reheating is performed after the cooling at the
Tempcore. The reheating may be performed through
self-tempering.
[0046] In the reheating, it may be important to change the
temperature of the center of the steel bar at a constant
temperature and the bainite structure may be formed in the center.
To this end, in the inventive concept, in the reheating, the
temperature of the center may be maintained to be 500 to
600.degree. C., which is a section in which bainite may be
formed.
[0047] That is, it is important to create a condition in which
bainite is formed in the center of the steel bar by slow moving
speed and the rapid cooling through high water pressure in the
Tempcore process and to maintain the condition a long time in the
reheating.
[0048] The reheating process takes about 0.3 to 1 second after the
cooling at the Tempcore.
[0049] After the reheating, the additional cooling through air
cooling is provided. The additional cooling is performed at a
cooling rate of 10.about.20.degree. C./sec to be cooled to
200.degree. C. or less. In the air cooling, a flow in the air
occurs for quick cooling to be cooled.
[0050] Hereinafter, Examples of the inventive concept will be
described in detail.
Example 1
[0051] Example 1 included carbon (C) of 0.34 wt %, manganese (Mn)
of 1.07 wt %, silicon (Si) of 0.15 wt %, vanadium (V) of 0.04 wt %,
the remaining Fe, and other unavoidable impurity components, which
were heated at about 1000.degree. C. (heating a billet for a steel
bar)
[0052] After the heating the billet for the steel bar, hot-rolling
was performed to be formed in a steel bar shape through a roughing
mill, an intermediate mill, and a finishing mill.
[0053] After the hot-rolling, cooling at a Tempcore was performed
at a speed of the steel bar of 10 m/sec, a pressure of cool water
of 10 bar, and an amount of water of 150 m.sup.3/hr.
[0054] After the cooling at the Tempcore, reheating and additional
cooling were performed. The additional cooling was carried out by
an air cooling manner to complete the steel bar.
Example 2
[0055] The same as Example 1, but
[0056] Example 2 included carbon (C) of 0.33 wt %, manganese (Mn)
of 1.12 wt %, silicon (Si) of 0.15 wt %, vanadium (V) of 0.04 wt %,
the remaining Fe, and other unavoidable impurity components.
[0057] In addition, after the heating, the cooling at the Tempcore
was carried out at the speed of the steel bar of 5 m/sec, the
pressure of cool water of 15 bar, and the amount of water of 150
m.sup.3/hr.
Comparative Example 1
[0058] The same process as in Example 1, but
[0059] Comparative Example 1 included carbon (C) of 0.29 wt %,
manganese (Mn) of 0.52 wt %, silicon (Si) of 0.14 wt %, the
remaining Fe, and other unavoidable impurity components.
[0060] The cooling at the Tempcore was carried out at the speed of
the steel bar of 30 m/sec through the air cooling.
Comparative Example 2
[0061] The same process as Example 1, but
[0062] Comparative Example 2 included carbon (C) of 0.30 wt %,
manganese (Mn) of 1.15 wt %, silicon (Si) of 0.16 wt %, vanadium
(V) of 0.11 wt %, the remaining Fe, and other unavoidable impurity
components.
[0063] In addition, only cooling by air cooling was performed, not
cooling at the Tempcore.
Comparative Example 3
[0064] The same process as Example 2, but
[0065] Comparative Example 3 included carbon (C) of 0.32 wt %,
manganese (Mn) of 1.08 wt %, silicon (Si) of 0.15 wt %, vanadium
(V) of 0.04 wt %, the remaining Fe, and other unavoidable impurity
components.
[0066] The cooling at the Tempcore was carried out at the speed of
the steel bar of 30 m/sec through the air cooling.
[0067] The properties of the steel bars prepared by Examples 1, 2
and Comparative Examples 1 to 3 summarized in Table 1 below.
TABLE-US-00001 TABLE 1 Yield Ratio (Tensile Yield Tensile Strength/
Uniform Total Strength Strength Yield Elongation Elongation (Mpa)
(Mpa) Strength) property (%) property (%) Example 1 705 886 1.26
7.4 11.1 Example 2 711 908 1.28 6.7 8.8 Comparative 667 777 1.16
11.2 16.8 Example 1 Comparative 643 883 1.37 10.1 13.6 Example 2
Comparative 611 816 1.34 8.3 11.0 Example 3
[0068] The steel bars of Comparative Examples have a conventional
steel bar performance having yield strength of 600 MPa class. The
steel bars of Examples 1 and 2 of the inventive concept show yield
ratio property of 1.25 or more and high uniform elongation property
of 5.0% or more, although having a very high strength of 700 MPa or
more.
[0069] That is, the steel bar according to the inventive concept
having the yield strength of 700 MPa or more, which is excellent in
the yield ratio and uniform elongation property, may be confirmed
that the yield and tensile strength is increased in comparison with
the conventional steel bar. This is believed that the center is
formed of the bainite structure of 20% or more and the surface is
formed of tempered martensite. Details of an internal structure and
hardness characteristics of the steel bars will be described with
reference to the drawings.
[0070] FIG. 1 shows temperature change of steel bars and structure
change by location depending on processes of Examples and
Comparative Examples.
[0071] Referring to FIG. 1, in the case of Example 1 and Example 2,
after the hot-rolling, in the cooling at the Tempcore, the slow
moving speed, rapid quenching degree `H` due to high water
pressure, and the reheating cause bainite of 20% by volume or more
to be formed in the center and tempered martensite to be formed in
the surface
[0072] The Tempcore process (the rapid cooling through the slow
moving speed and the high pressure of water) creates the condition
for bainite to be formed in the center of the steel bar and then
the condition is maintained for a long time during the reheating,
and thus lots of bainite structures are formed in the center.
[0073] As shown in FIG. 1, the centers of Examples 1 and 2 are
adjusted by the section where bainite is formed due to the rapid
cooling. The section is maintained to form lots of bainite
structures.
[0074] On the contrary, in the case of Comparative Example 1 and
Comparative Example 3, after the cooling at the Tempcore, the air
cooling is carried out through the reheating process. In the case
of the steel bar performing the cooling at the Tempcore, martensite
is formed in the surface of the steel bar by the Tempcore. Then in
the air cooling, martensite is self-tempered by reheating to form
tempered martensite, and ferrite and pearlite are formed from
retained austenite. Eventually, tempered martensite is shown in the
surface and microstructure property of ferrite-pearlite is shown in
the center.
[0075] In the case of Comparative Example 2, the microstructure
property of ferrite-pearlite is shown in both the surface and the
center due to the air cooling process.
[0076] In the case of Comparative Examples 1 to 3, since the
cooling is not performed until bainite is formed in the center, the
bainite is hardly formed.
[0077] FIG. 2 shows cross-sectional views of steel bars of Examples
according to the inventive concept and Comparative Examples.
[0078] Referring to FIG. 2, the steel bars of Example 1 and Example
2 may be confirmed that the boundary is formed between the surface
and the center and is defined by a different structure from
tempered martensite formed in the surface and bainite and ferrite
formed in the center.
[0079] In Comparative Examples 1 and 3, it may be confirmed that
the boundary is formed between the surface and the center and is
defined between tempered martensite, and ferrite and pearlite of
the center.
[0080] In the case of Comparative Example 2, the boundary is not
distinguished because both the surface and the center have a
structure of ferrite and pearlite.
[0081] FIGS. 3 and 4 show optical micrographs and scanning electron
micrographs of Examples according to the inventive concept and
Comparative Examples.
[0082] Referring to FIGS. 3 and 4, in the case of Examples 1 and 2,
not only tempered martensite is formed in the surface but also
bainite having a large ratio is formed in the center due to the
slow speed and the high water pressure during the cooling at the
Tempcore, and thus the yield strength may be 700 MPa or more and
the yield ratio may be 1.25.
[0083] On the contrary, in Comparative Examples 1 and 3, bainite
and tempered martensite are partially formed at the boundary due to
the cooling at the Tempcore, and tempered martensite is formed in
the surface, but soft ferrite and pearlite structure is formed in
the center, and thus the yield strength is less than 700 MPa.
[0084] In the case of Comparative Example 2, the surface, the
boundary, and the center are formed the soft ferrite, pearlite
structure, and thus the yield strength is less than 700 MPa.
[0085] FIG. 5 shows a graph showing positional hardness of Examples
according to the inventive concept and Comparative Examples.
[0086] Referring to FIG. 5, it may be seen that the steel bars of
Example 1 and Example 2 have similar or higher hardness in all
positions in comparison with the steel bars of Comparative Example
1 and Comparative Example 3 manufactured through the Tempcore.
[0087] Particularly, in the case of the hardness of the center, it
may be seen that the hardness characteristics of steels bars of
Examples 1 and 2 were superior to those of the steel bars of
Comparative Examples 1 and 3 because the bainite structure of 20%
by volume or more is formed in the steel bars of Examples 1 and
2.
[0088] However, in the case of Comparative Example 2 subjected to
the air cooling after hot-rolling, the highest hardness at the
center is showed. In the case of Comparative Example 2, a large
amount of vanadium (V) is added to compensate for the low strength
of the ferrite-pearlite structure, thereby performing precipitation
strengthening. Therefore, in the case of Comparative Example 2, it
may be seen that the hardness of the center is the largest by a
large amount of vanadium carbide.
[0089] In conclusion, it may be confirmed that the steel bar
according to the inventive concept is the steel bar having the
yield strength of 700 MPa or more, the yield strength of 1.25 or
more, and the excellent uniform elongation property because the
bainite structure of 20% by volume or more is formed in the center
and the tempered martensite is formed in the surface.
[0090] According to one embodiment of the inventive concept,
bainite accounts for 20% by volume or more in the center of the
steel bar and thus the steel bar has the yield strength of 700 MPa
or more and the yield ratio of 1.25 or more, which is suitable for
the seismic resistant steel bar.
[0091] The steel bar having the yield strength of 700 MPa class,
which is excellent in the yield ratio and the uniform elongation
property, according to the inventive concept is provided as the
seismic resistant steel bar having the yield strength of 700 MPa or
more, the high yield ratio, and the high uniform elongation
property of 5% or more.
[0092] In the inventive concept, after the rolling process, the
condition of the cooling of the steel bar is changed to form the
bainite structure in the center of the steel bar at the specific
ratio or more, to increase the uniform elongation property of the
steel bar, and to increase the yield ratio of 1.25 or more, thereby
greatly improving the quality of the seismic resistant steel
bar.
[0093] While the inventive concept has been described with
reference to exemplary embodiments, it will be apparent to those
skilled in the art that various changes and modifications may be
made without departing from the spirit and scope of the inventive
concept. Therefore, it should be understood that the above
embodiments are not limiting, but illustrative.
* * * * *