U.S. patent application number 16/610307 was filed with the patent office on 2020-07-30 for heat exchanger tube and corresponding heat exchanger.
This patent application is currently assigned to Valeo Systemes Thermiques. The applicant listed for this patent is Valeo Systemes Thermiques. Invention is credited to Xavier Marchadier, Christian Riondet.
Application Number | 20200240714 16/610307 |
Document ID | 20200240714 / US20200240714 |
Family ID | 1000004786192 |
Filed Date | 2020-07-30 |
Patent Application | download [pdf] |
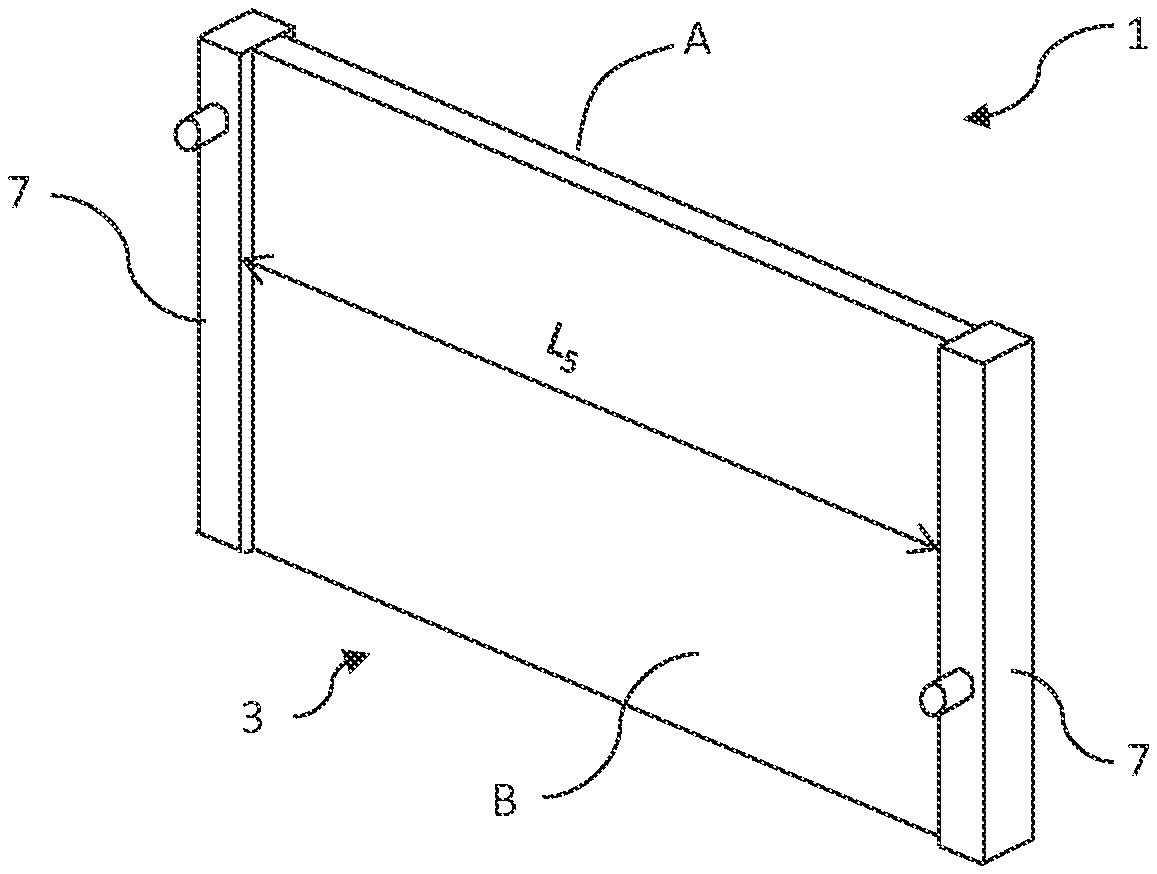
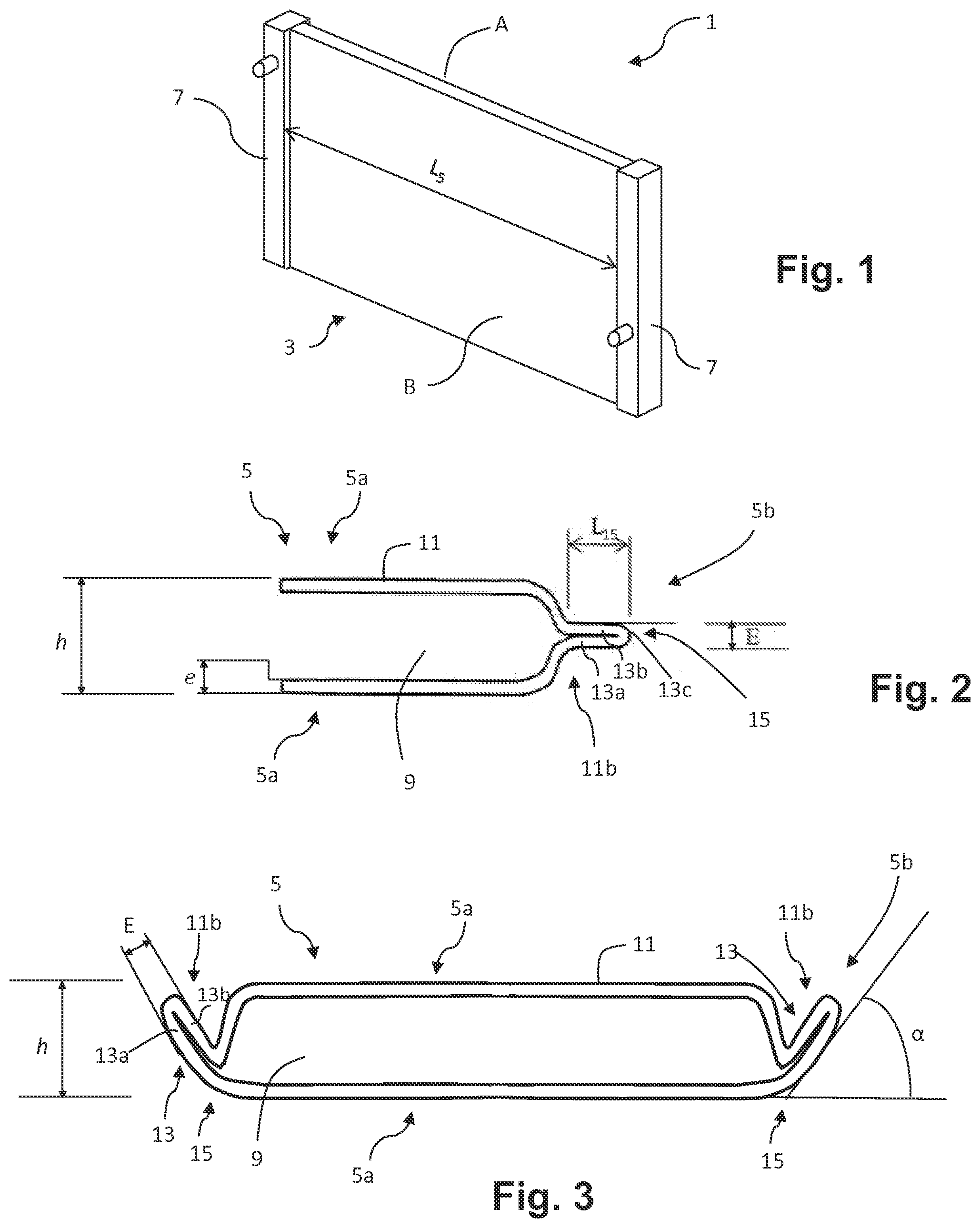
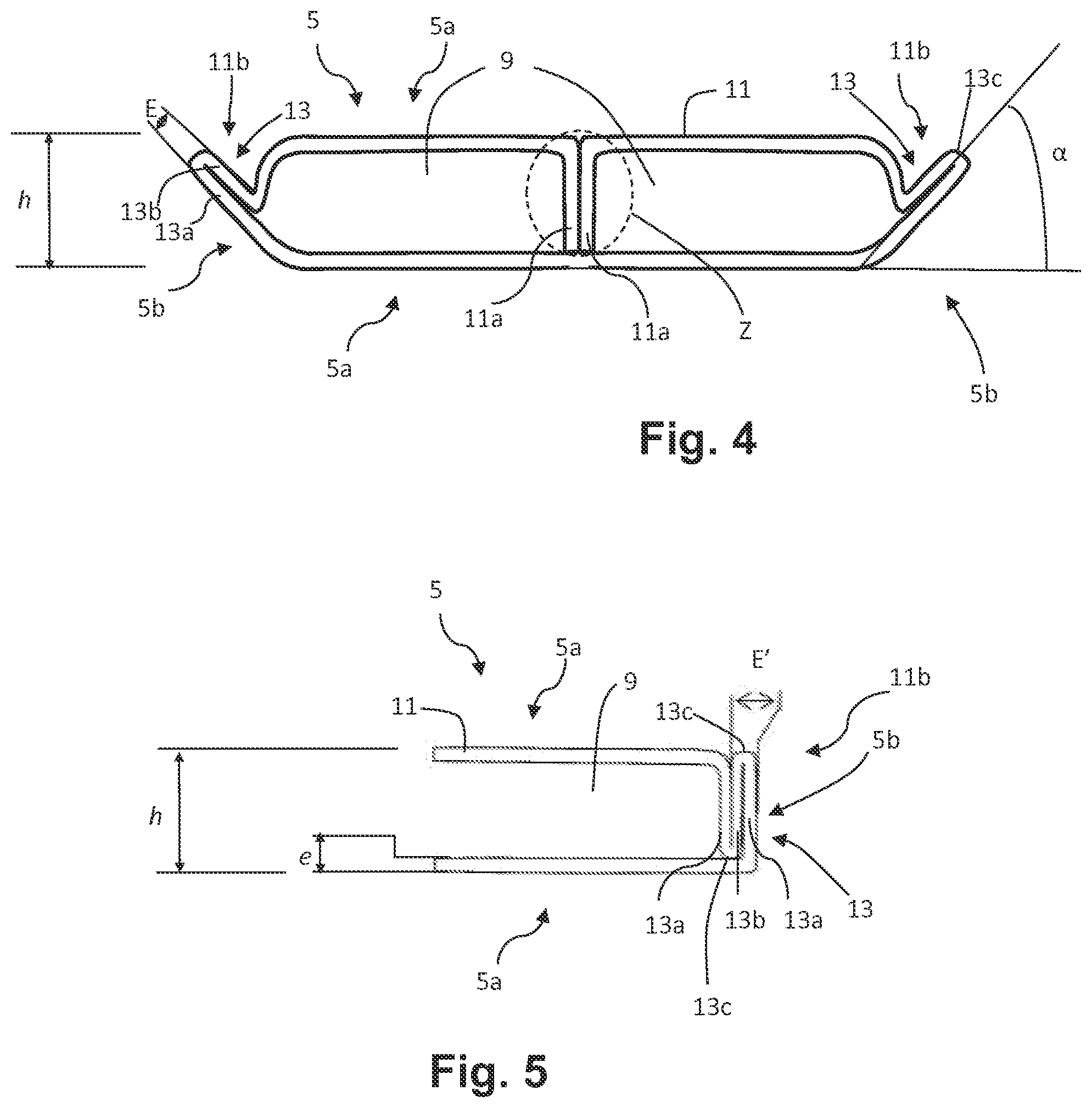
United States Patent
Application |
20200240714 |
Kind Code |
A1 |
Marchadier; Xavier ; et
al. |
July 30, 2020 |
HEAT EXCHANGER TUBE AND CORRESPONDING HEAT EXCHANGER
Abstract
The tube (5) of a heat exchanger (1) is produced from a strip of
material (11), the strip of material (11) having two end parts
joined such as to form the tube (5). The strip of material (11)
forming the tube (5) is folded on itself such as to define at least
one fold (13) formed by two strip portions (13a, 13b) with
continuity of material. At least one strip portion (13a, 13b) of
the fold (13) is a strip portion (13a, 13b) for protecting the tube
(5) in the event of an impact from an element outside the tube (5)
and is formed in an intermediate part (11 b) of the strip of
material (11).
Inventors: |
Marchadier; Xavier; (Le
Mesnil Saint-Denis, FR) ; Riondet; Christian; (Reims,
FR) |
|
Applicant: |
Name |
City |
State |
Country |
Type |
Valeo Systemes Thermiques |
Le Mesnil-Saint-Denis Cedex |
|
FR |
|
|
Assignee: |
Valeo Systemes Thermiques
Le Mesnil-Saint-Denis Cedex
FR
|
Family ID: |
1000004786192 |
Appl. No.: |
16/610307 |
Filed: |
May 2, 2018 |
PCT Filed: |
May 2, 2018 |
PCT NO: |
PCT/FR2018/051093 |
371 Date: |
January 9, 2020 |
Current U.S.
Class: |
1/1 |
Current CPC
Class: |
F28F 1/022 20130101;
F28F 2225/04 20130101; F28D 1/0391 20130101 |
International
Class: |
F28D 1/03 20060101
F28D001/03; F28F 1/02 20060101 F28F001/02 |
Foreign Application Data
Date |
Code |
Application Number |
May 2, 2017 |
FR |
1753851 |
Claims
1. A tube for a heat exchanger made from a strip of material, the
strip of material having two end parts joined such as to form the
tube, the strip of material forming the tube is folded on itself
such as to define at least one fold formed by two strip portions
with continuity of material such that at least one strip portion of
the fold: is a strip portion for protecting the tube in the event
of an impact from an element outside the tube, and is formed in an
intermediate part of the strip of material.
2. The tube as claimed in claim 1, wherein the intermediate part
lacks a join zone between the two end parts to close the tube in a
sealed manner.
3. The tube as claimed in claim 1, wherein said at least one fold
is formed along at least one lateral side of the tube.
4. The tube as claimed in claim 1, wherein the strip of material is
folded such as to form a protuberance extending from the tube
toward the exterior of the tube.
5. The tube as claimed in claim 4, wherein the protuberance has a
thickness at least equal to twice the material thickness of the
strip of material.
6. The tube as claimed claim 4, wherein the protuberance forms,
with the general plane of extension of the tube, a non-zero angle
of the order of 30.degree..
7. The tube as claimed in claim 4, in which the protuberance
extends over a width equal to at least twice and to at most ten
times the material thickness of the strip of material.
8. The tube as claimed in claim 1, wherein the strip of material is
folded in the direction of the height of the tube, such as to form
an excess thickness of material.
9. The tube as claimed in claim 8, wherein the height of the strip
portions of said at least one fold is of the order of the height of
the tube.
10. A heat exchanger for a motor vehicle, comprising: a bundle of
tubes, each tube of the bundle of tubes being made from a strip of
material, the strip of material having two end parts joined such as
to form each tube, wherein the strip of material forming each tube
is folded on itself such as to define at least one fold formed by
two strip portions with continuity of material such that at least
one strip portion of the fold: is a strip portion for protecting
each tube in the event of an impact from an element outside each
tube, and is formed in an intermediate part of the strip of
material.
11. A tube for a heat exchanger made from a strip of material, the
strip of material comprising two end parts joined such as to form
the tube, the tube comprising two lateral ends and an intermediate
part; wherein the strip of material forming the tube is folded on
itself such as to define at least one fold formed by two strip
portions with continuity of material such that at least one strip
portion of the fold: is a strip portion for protecting the tube in
the event of an impact from an element outside the tube, and is
formed in the intermediate part of the strip of material, wherein
the intermediate part is the portion of the tube that does not
include the lateral ends of the tube and is a longitudinal
extension corresponding to the longitudinal extension of the tube.
Description
[0001] The invention relates to a heat exchanger tube, notably for
motor vehicles. The invention also relates to a heat exchanger
comprising a bundle of such tubes.
[0002] The invention pertains to the field of heat exchangers,
notably for motor vehicles.
[0003] The present invention relates in particular to heat
exchangers designed to be placed at the front end of a motor
vehicle. A front end, also called a front end assembly, is a
structural element that is able to incorporate a variety of
equipment of the vehicle, such as headlamps, flashers, audible
warning device, heat exchangers, engine fans or cooling module.
[0004] The heat exchanger is, for example, used to cool the engine
or, again, to air-condition the car interior.
[0005] Generally, heat exchangers conventionally comprise a bundle
of tubes and collector boxes into which the ends of the tubes of
the bundle open out such as to allow the circulation of a fluid,
notably a cooling fluid, in the tubes of the bundle.
[0006] The tubes of such exchangers may be produced, for example,
by extrusion. This type of manufacture gives rise to a significant
cost, however, notably owing to the need for specific dies for each
type of tube.
[0007] In a variant, tubes are produced from a strip of material,
for example, by folding the strip of material.
[0008] However, the tubes of heat exchangers may be subject to
numerous stresses, such as a high-speed impact with an object (for
example, a piece of gravel) originating from the exterior
environment. The tubes of heat exchangers are thus subject to
exterior stresses. The fluid must not escape from the tubes of heat
exchangers as this is likely to compromise the way in which these
heat exchangers function, so it is necessary to preserve the
exterior/fluid leaktightness of the tubes.
[0009] With a view to protecting these heat exchangers, a grille,
generally one made from plastics, may be incorporated at the front
end in order to stop pieces of gravel. Nevertheless, the
integration of such a grille at the front end engenders a certain
cost.
[0010] It has proven to be useful to guarantee that the material
used for the tube is sufficiently strong in order to prevent any
risk of fluid escaping from the heat exchanger, for example in the
event of an impact with a piece of gravel on the road.
[0011] A known solution is to enable the tube to withstand such an
impact by locally increasing the thickness of the wall of the tube
in the case of an extruded tube. However, such tubes are expensive
to manufacture. Moreover, it has been observed that such tubes are
less corrosion-resistant than tubes made from a strip of material,
notably by folding.
[0012] In a first known tube produced from a strip of material, the
end parts of the tube are folded and secured together by brazing,
on a side or at the tube nose. Such folds that are brazed at the
end parts require a complex manufacturing process.
[0013] Furthermore, such tubes may not be sufficiently able to
withstand impact from pieces of gravel.
[0014] Thus, an object of the invention is to propose a solution
for a tube produced from a strip of material, conferring, on the
tube, in a simple manner, improved resistance to exterior stresses
while still resolving the above-mentioned prior-art drawbacks at
least in part.
[0015] To that end, a subject of the invention is a tube for a heat
exchanger made from a strip of material, the strip of material
having two end parts joined such as to form the tube. According to
the invention, the strip of material forming the tube is folded on
itself such as to define at least one fold formed by two strip
portions with continuity of material such that at least one strip
portion of the fold: [0016] is a strip portion for protecting the
tube in the event of an impact from an element outside the tube,
and [0017] is formed in an intermediate part of the strip of
material.
[0018] The two strip portions of said at least one fold may be
formed in the intermediate part of the strip of material.
[0019] In other words, the intermediate part of the strip of
material is by definition distinct from, i.e. does not include, the
lateral ends of the strip of material.
[0020] The end parts of the strip of material each include a
lateral end of the strip of material.
[0021] It is possible, for example, to define the intermediate part
of the strip of material as the central part corresponding to 80%
of the width of the strip of material, the end parts corresponding,
for example, to the parts having a width of 10% on either side of
the intermediate part.
[0022] However, this value of 80% is purely indicative. The
important thing is for the intermediate part not to include the
lateral ends of the strip of material.
[0023] Furthermore, the intermediate part has a longitudinal
extension corresponding to the longitudinal extension of the
tube.
[0024] Thus, advantageously in locations where there are high
levels of stress, notably stresses from outside the tube, this fold
or these folds are used to create one or more zones of
reinforcement of the tube that make it possible to absorb energy in
the event of an impact from an element originating from the
exterior environment, such as a piece of gravel.
[0025] The one or more folds are not produced in a zone where walls
of the strip of material that need to be leaktight join or overlap,
but the wall is folded on itself with continuity of material. Thus,
even were the folds to deform or to unfold, the leaktightness of
the tube, furthermore achieved, for example, by brazing or
electrowelding, would remain guaranteed.
[0026] The invention thus offers the advantage of protection for
the join between the end parts of the strip of material and thus
the leaktightness of the tube.
[0027] Said tube may, furthermore, comprise one or more of the
following features, taken separately or in combination.
[0028] Preferably, the intermediate part does not include a join
zone between the two end parts in order to close the tube in a
sealed manner. In other words, the intermediate part lacks such a
join zone.
[0029] According to one aspect of the invention, said at least one
fold is formed along at least one lateral side of the tube. This
side is configured such as to be arranged on the front side of a
heat exchanger facing an inlet for a flow of external air at the
front end of a motor vehicle.
[0030] According to one example, the tube has two major sides
connected by two lateral minor sides. Said at least one fold is
formed on a lateral minor side.
[0031] According to another aspect of the invention, the strip
portions of said at least one fold are brazed together such as to
increase the mechanical strength of the tube.
[0032] The strip portions of said at least one fold may or may not
lie against one another.
[0033] According to a first embodiment, the strip of material is
folded such as to form a protuberance extending from the tube
toward the exterior of the tube.
[0034] Such a protuberance is the first surface of the tube with
which a piece of gravel, for example, enters into contact in the
event of impact. The protuberance may fold and/or deform through
the effect of the impact and thus absorb the energy of the piece of
gravel.
[0035] Lastly, such a tube may be produced in a simple manner
without requiring a plurality of manufacturing steps.
[0036] The protuberance may have a thickness at least equal to
twice the material thickness of the strip of material.
[0037] For example, the protuberance forms, with the horizontal, a
non-zero angle notably less than or of the order of 45.degree.,
preferably of the order of 30.degree..
[0038] The protuberance may extend over a width equal to at least
twice and to at most ten times the material thickness of the strip
of material.
[0039] According to a second embodiment, the strip of material is
folded in the direction of the height of the tube, such as to form
an excess thickness of material.
[0040] A sufficient excess thickness, advantageously provided at
the nose of the tube, is obtained with a view to guaranteeing
mechanical strength and thereby protecting the tube in the event of
impacts originating from the exterior environment, without the risk
of a leak of fluid.
[0041] The height of the strip portions of said at least one fold
is, for example, of the order of the height of the tube.
[0042] According to either embodiment, the tube is a folded tube.
The tube may have a cross section substantially in the form of a
"B", defining two parallel fluid-circulation channels delimited by
a separation.
[0043] The tube may be an electrowelded tube.
[0044] The invention further relates to a heat exchanger, notably
for a motor vehicle, characterized in that it comprises a bundle of
tubes as defined above.
[0045] Further features and advantages of the invention will become
more clearly apparent upon reading the following description, given
by way of illustrative, non-limiting example, and the appended
drawings, in which:
[0046] FIG. 1 shows, in part and schematically, a heat
exchanger,
[0047] FIG. 2 is a cross-sectional view showing, in part, a first
example of a tube of the exchanger of FIG. 1,
[0048] FIG. 3 is a cross-sectional view of a second example of a
tube of the exchanger of FIG. 1,
[0049] FIG. 4 is a cross-sectional view of a third example of a
tube of the exchanger of FIG. 1, and
[0050] FIG. 5 is a cross-sectional view of a fourth example of a
tube of the exchanger of FIG. 1.
[0051] In these figures, identical elements bear the same
references.
[0052] The following embodiments are examples. Although the
description relates to one or more embodiments this does not mean
necessarily that each reference relates to the same embodiment or
that the features apply to only one embodiment. Simple features
from different embodiments may likewise be combined or interchanged
in order to provide further embodiments.
[0053] In the description, certain elements may include an index
mark such as, for example, first element or second element. In this
event, this is simple indexing to differentiate and to name similar
but not identical elements. This indexing does not imply that any
element takes priority over any other element, and such
designations may easily be interchanged without departing from the
scope of the present description. This indexing does not, likewise,
imply an order in terms of time.
[0054] FIG. 1 schematically shows an example of a heat exchanger 1
according to the invention. This is, in particular, a heat
exchanger 1 designed to be placed at the front end of a motor
vehicle.
[0055] An example that may be cited is that of radiators for
cooling the engine or, again, "low-temperature" radiators, for
example for auxiliary cooling circuits in the motor vehicle. It may
also be, for example, a condenser of an air-conditioning
circuit.
[0056] The heat exchanger 1, such as a cooling radiator, placed at
the front end of the vehicle may be accessed by a first fluid, such
as a flow of external air, originating from outside the vehicle. A
second fluid, such as a cooling fluid, circulates inside the heat
exchanger 1 such as to exchange heat with this flow of external
air.
[0057] The heat exchanger 1 has a front side A, i.e. designed to be
arranged on the side of the grille of the motor vehicle or,
alternatively, facing an inlet for the flow of external air
designed to traverse the heat exchanger 1. The heat exchanger 1
also has a rear side B, or engine side, which is opposite the front
side A.
[0058] In the present description, the terms front/rear are
designed to refer to the direction of progress, in a forward gear,
of the motor vehicle intended to be equipped with a heat exchanger
1 as described. Similarly, the terms vertical/horizontal are
designed to refer to the arrangement of the elements in FIGS. 2 to
5, which corresponds to the arrangement of the elements in the
assembled state in the motor vehicle.
[0059] As illustrated in part in FIG. 1, the heat exchanger 1
conventionally comprises a bundle 3 (shown very schematically in
FIG. 1) of tubes 5.
[0060] Examples of tubes 5 are in part shown in FIGS. 2 to 5. These
tubes 5 are mounted between two distribution housings or collector
boxes 7, also called water boxes, (referring, likewise, to FIG. 1)
for the second fluid.
[0061] In the assembled state in the motor vehicle, the heat
exchanger 1 may be arranged such as to allow, for example, a
transverse circulation of fluid in the tubes 5 that extend
transversely to the motor vehicle. There are, however,
configurations in which circulation takes place vertically in
vertical tubes 5.
[0062] Advantageously, the heat exchanger 1 is a "brazed"
exchanger. In this case, the various component parts of the body of
such a heat exchanger 1 are made from metal and may be assembled
and then brazed by passing through a brazing furnace with a view to
securing together all the component parts. It should be noted that
other elements made from plastics, in particular, are typically
attached on top after brazing, such as, for example, water
boxes.
[0063] The tubes 5 (FIGS. 2 to 5) may extend longitudinally along a
length L.sub.5 shown schematically in FIG. 1. The ends of these
tubes 5 open out into the collector boxes 7, for example by means
of collector plates (not shown), which may be arranged transversely
relative to the tubes 5.
[0064] Each tube 5 delimits one or more circulation channels 9 (see
FIGS. 2 to 5) for the second fluid.
[0065] The tubes 5 may be separated from one another by inserts
(not shown), for example corrugated inserts, traversed by the first
fluid, such as the flow of external air, for the purposes of a
thermal exchange with the second fluid, such as the cooling fluid
circulating in the tubes 5.
[0066] According to a variant embodiment (not shown), an internal
insert, for example a corrugated insert, may be inserted in the or
each circulation channel 9. This internal insert has, for example,
a thickness of the order of 80 .mu.m to 140 .mu.m.
[0067] The invention relates more precisely to a tube 5 for such a
heat exchanger 1, examples of which are shown schematically in
FIGS. 2 to 5.
[0068] The tube 5 is produced from a strip of material 11. This is,
in particular, a metallic strip 11. The metallic strip is
preferably made of aluminum or aluminum alloy. The strip of
material 11 is, for example, of rectangular general shape.
[0069] This strip of material 11 has a thickness e, which, below,
is also called material thickness. This material thickness e is
constant. By way of example, the material thickness e may be of the
order of 180 .mu.m to 270 .mu.m, in particular of the order of 200
.mu.m to 270 .mu.m.
[0070] Notably, the tube 5 may be obtained from a reel of metallic
foil that, after being unwound as a strip, is progressively formed
to the required cross section using specific tools, for example
folding or similar tools, and is then cut to the desired length, in
sections corresponding to a plurality of final tubes 5.
[0071] In particular, the strip of material 11 has end parts 11a,
which may be seen in the example of FIG. 4, which are joined such
as to form the tube 5, notably to close the tube 5 in a leaktight
manner. These end parts 11a comprise the lateral ends or lateral
borders of the strip of material 11.
[0072] Leaktightness may be assured by brazing at the join of the
end parts 11a. In a variant, this may be an electrowelded tube
5.
[0073] The strip of material 11 also has an intermediate part 11b.
This intermediate part 11b does not include the lateral ends of the
strip of material 11. The intermediate part 11b is distinct from
the end parts 11a.
[0074] By way of non-limiting example, the end parts 11a of the
strip of material 11 may extend on each side of the strip of
material 11, each over a width of the order of 10% of the total
width of the strip of material 11.
[0075] The intermediate part 11b, meanwhile, forms a central part
extending, for example, over a width of the order of 80% of the
total width of the strip of material 11.
[0076] Furthermore, the end parts 11a and the intermediate part 11b
each have a longitudinal extension corresponding to the
longitudinal extension of the tube 5.
[0077] The tube 5 may be folded or formed such as to define a
single channel 9 for circulation of fluid (FIG. 3). By way of
non-limiting example, the tube 5 may have a cross section of oblong
general shape. The strip of material 11 then forms an envelope of
this circulation channel 9.
[0078] In a variant, the tube 5 may be folded or formed such as to
define at least two circulation channels 9 (FIG. 4). The tube 5 may
have a cross section of "B" form.
[0079] The cross section of "B" form of the illustrated tube 5 has
two juxtaposed parallel channels 9 for circulation of fluid which
are separated by a separation forming a spacer. To that end, the
metallic strip is folded such as to form the envelope of these
juxtaposed parallel circulation channels 9. The separation is
produced jointly by the folded opposite end parts 11a of the strip
of material 11. In this example, the intermediate part 11b of the
strip of material 11 does not include the join zone Z, which is
encircled in a broken line in FIG. 4, of the two end parts 11a to
form the separation.
[0080] A description has been given here of a folded tube of "B"
form. Naturally, provision may be made for any other type of
folding.
[0081] The end parts 11a of the strip of material 11, visible only
in the example of FIG. 4, may be placed against or superposed on
one another. In particular, in the example of FIG. 4, the end parts
11a may be folded up, for example substantially at a right angle,
and placed against one another.
[0082] According to any of the variants shown in FIGS. 2 to 5, the
tube 5 has two major sides 5a, notably with a planar surface,
connected by two lateral minor sides 5b of height h, which defines
the height h of the tube 5. These minor sides 5b may be rounded and
are likewise called radii of the tube 5.
[0083] The height h of the tube 5 also corresponds to the overall
thickness of the tube 5. This height h of a tube 5 is, for example,
of the order of 1.2 mm to 3 mm.
[0084] Moreover, during the method for manufacturing the tube 5,
the strip of material 11 forming the tube 5 is folded on itself
such as to define, with continuity of material, at least one fold
13.
[0085] This strip of material 11 is folded on itself at least at
one side of the tube 5, also called the nose of the tube 5. This is
a lateral minor side 5b of the tube 5 intended to be arranged on
the front side A of the heat exchanger 1. The side 5b of the tube 5
having one or more folds 13 is configured such as to extend along a
transverse axis, in the direction of the width, of a motor vehicle
equipped with a heat exchanger 1 comprising such a tube 5.
[0086] Furthermore, the or each fold 13 is formed by two strip
portions 13a, 13b, with continuity of material, via a return 13c.
"With continuity of material" is understood to mean the fact that
the fold 13 is not formed by two distinct walls secured
together.
[0087] Each fold 13 thus forms a double thickness of strip. Only
one fold 13 is shown in the examples of FIGS. 2 to 4. In the
example of FIG. 5, two folds 13 are shown and share a common strip
portion 13b. Naturally, the invention is not limited to one or two
folds 13.
[0088] Moreover, at least one of the strip portions 13a or 13b of
the fold 13 is a protective strip portion, i.e. it protects the
tube 5 particularly in the event of impact between an element from
the exterior environment and the tube 5.
[0089] At least the protective strip portion 13a and/or 13b of the
fold 13 is formed along the nose or side 5b of the tube 5.
[0090] At least the protective strip portion 13a and/or 13b is
produced in an intermediate part 11b of the strip of material 11.
The two strip portions 13a and 13b forming a fold 13 may be
produced in this intermediate part 11b of the strip of material 11.
As stated previously, the intermediate part 11b of the strip of
material 11 does not include the lateral ends of the strip of
material 11 and likewise does not include a join zone Z of the end
parts 11a (see FIG. 4) for joining the strip of material 11. The
protective fold 13 is thus not produced at the end parts 11a or,
more precisely, at the lateral ends.
[0091] The strip portions 13a, 13b of each fold 13 may optionally
be placed against one another.
[0092] Provision may be made for these strip portions 13a, 13b to
be brazed together at each fold 13 such as to increase the
mechanical strength of the tube 5. The fold or folds 13 being
formed with continuity of material, such a brazing step does not
have the effect of making the tube 5 leaktight.
[0093] First Solution
[0094] According to a first solution, different examples of which
are illustrated schematically in FIGS. 2 to 4, the strip of
material 11 is folded such as to form a protuberance 15 or spur.
This protuberance 15 extends from the tube 5, more precisely from
the side or nose of the tube 5, toward the exterior of the tube 5.
In other words, this protuberance 15 extends away from the channel
9 for circulation of coolant fluid delimited by the tube 5.
[0095] In other words, the protuberance 15 is formed by the strip
portions 13a, 13b of the one or more folds 13. In this case, the
strip portions 13a, 13b of each fold 13 may be placed against one
another and are advantageously brazed together. Naturally,
provision may be made for more than one fold 13.
[0096] This protuberance 15 formed from at least two strip portions
13a, 13b of a fold 13 thus has a thickness E equal to at least
twice the material thickness e of the strip of material 11 forming
the tube 5.
[0097] Moreover, the protuberance 15 may extend over a width
L.sub.15 (referenced in FIG. 2), which is advantageously between
twice and ten times the material thickness e of the strip of
material 11 forming the tube 5.
[0098] Furthermore, the orientation of the one or more folds 13
forming the protuberance 15 may be adapted in accordance with
requirements, as illustrated in the examples of FIGS. 2 to 4.
[0099] Reference is now made to FIG. 2, which shows a sectional
view of such a tube 5 according to a first example. In this first
example, the fold 13 is formed horizontally in the figure. In this
case, the protuberance 15, and thus the strip portions 13a, 13b
forming it, extend parallel to the major sides 5a of the tube 5.
This protuberance 15 extends in the transverse direction of the
tube 5.
[0100] The strip of material 11 forming the tube 5 is thus folded
over one or more times on itself horizontally (in the figure) at
least at the lateral minor side 5b or nose of the tube 5, thereby
increasing the dimension of the tube 5 in the direction of the
width or the transverse direction of the tube 5.
[0101] In this first example, the two strip portions 13a and 13b of
the fold 13 forming the protuberance 15 carry out the function of
providing protection in the event of impact by an exterior element,
such as a piece of gravel.
[0102] In the first example of FIG. 2, the tube 5 is shown only in
part, and of course the cross section of this tube 5 may be oblong
or, for example, of "B" form, as described previously.
[0103] In an alternative, the protuberance 15 may, with the general
plane of extension of the tube 5, corresponding in the figures to a
horizontal plane, form a non-zero angle .alpha.. Such an
alternative is illustrated in a second example of a tube 5 in FIG.
3 and in a third example of a tube 5 in FIG. 4. In other words, the
protuberance 15 may form a non-zero angle .alpha. with the major
faces 5a of the tube 5.
[0104] In particular, the angle .alpha. may be of the order of or
less than 45.degree.. According to a particular example, the angle
.alpha. is of the order of 30.degree..
[0105] The third example, of FIG. 4, differs from the second
example, of FIG. 3, in terms of the cross section of the tube 5 of
"B" form instead of the oblong cross section.
[0106] In these examples, at least the first strip portion 13a
forming the fold 13, which is the outermost relative to the tube 5,
is designed to be the first surface in contact with an exterior
element in an impact on the tube 5 and performs at least the
function of protection.
[0107] Second Solution
[0108] According to a second solution, illustrated schematically in
FIG. 5, the strip of material 11 is folded in the direction of the
height h of the tube 5. Only differences from the examples of the
first solution are described below.
[0109] According to this second solution, the tube 5 thus has one
or more vertical folds 13 that form an excess thickness E' of
material at least at the nose of the tube 5 or lateral minor side
5b. The vertical folds 13 of the second solution are akin to the
folds 13 according to the second and third examples of the first
solution, forming a protuberance 15 inclined at an angle of the
order of 90.degree. to the horizontal.
[0110] The tube 5 thus formed therefore has a variable thickness.
In other words, the tube 5 has one or more reinforced zones, i.e.
zones with a greater thickness which are obtained by folding the
strip of material 11 on itself. These reinforced zones correspond
to the zones of the tube 5 that are the most stressed, particularly
the nose of the tube 5.
[0111] In a manner similar to the first solution, at least one of
the strip portions 13a, 13b of the folds 13 forming the excess
thickness E' performs the function of protecting the tube 5 in the
event of impact by an exterior element such as a piece of gravel.
Indeed, this excess thickness E' also makes it possible to absorb
the energy of the piece of gravel in the event of impact.
[0112] In the example illustrated in FIG. 5, only two folds 13 with
a common strip portion 13b are shown. Naturally, there is no
limitation on the number of folds 13. Provision may be made for a
plurality of folds 13, in particular with an odd total number of
strip portions 13a, 13b.
[0113] Furthermore, the folds 13 are produced over the entire
height h of the tube 5. At the very least, the strip portions 13a,
13b of the folds 13 must extend over a height corresponding to the
height of the circulation channel 9, i.e. the height h of a tube 5
minus twice the material thickness e.
[0114] Thus, in the course of the method for obtaining such a tube
5, the strip of material 11 may be folded at at least an
intermediate part 11b, as described according to any of the
variants with reference to FIGS. 2 to 5, such as to form, with
continuity of material, at least one fold 13 formed by two strip
portions 13a, 13b, at least one strip portion 13a and/or 13b of
which forms the protection for the tube 5.
[0115] This folding-over at at least an intermediate part 11b of
the strip of material 11 may take place prior to the folding of the
strip of material 11 with a view to obtaining a folded tube with a
cross section that is oblong or of "B" form or, again, of any other
form. It is then possible to secure the assembly in the course of
brazing the heat exchanger 1.
[0116] In a variant, the folding-over of the strip of material 11
at at least an intermediate part 11b to form one or more folds 13
may take place prior to or after electrowelding to form the tube
5.
[0117] It will thus be understood that with the one or more fold(s)
13 formed at least at the nose of the tube 5 according to any of
the embodiments described previously sufficient material is
guaranteed at strategic locations in such a manner as to withstand
stresses, notably exterior stresses, stressing the tube 5.
[0118] Naturally, other arrangements of the tube 5 that make it
possible to withstand interior stresses, notably from the fluid,
may be combined with these different embodiments described
previously.
[0119] Such tubes 5 may be provided in any type of heat exchanger
1, notably a brazed heat exchanger, such as an engine-cooling
radiator or, again, a low-temperature radiator or a condenser in an
air-conditioning circuit.
[0120] The invention may likewise be applied to a front face or
front face module incorporating one or more heat exchangers
comprising such tubes 5.
* * * * *