U.S. patent application number 16/662633 was filed with the patent office on 2020-07-09 for method for heat-treating uppermost surface of spheroidal graphite cast iron and spheroidal graphite cast iron heat-treated by th.
The applicant listed for this patent is Hyundai Motor Company Kia Motors Corporation. Invention is credited to Eun-Soo Kwon, Hyung-Gook Lee, Yong-Bo Sim.
Application Number | 20200216923 16/662633 |
Document ID | / |
Family ID | 71404956 |
Filed Date | 2020-07-09 |
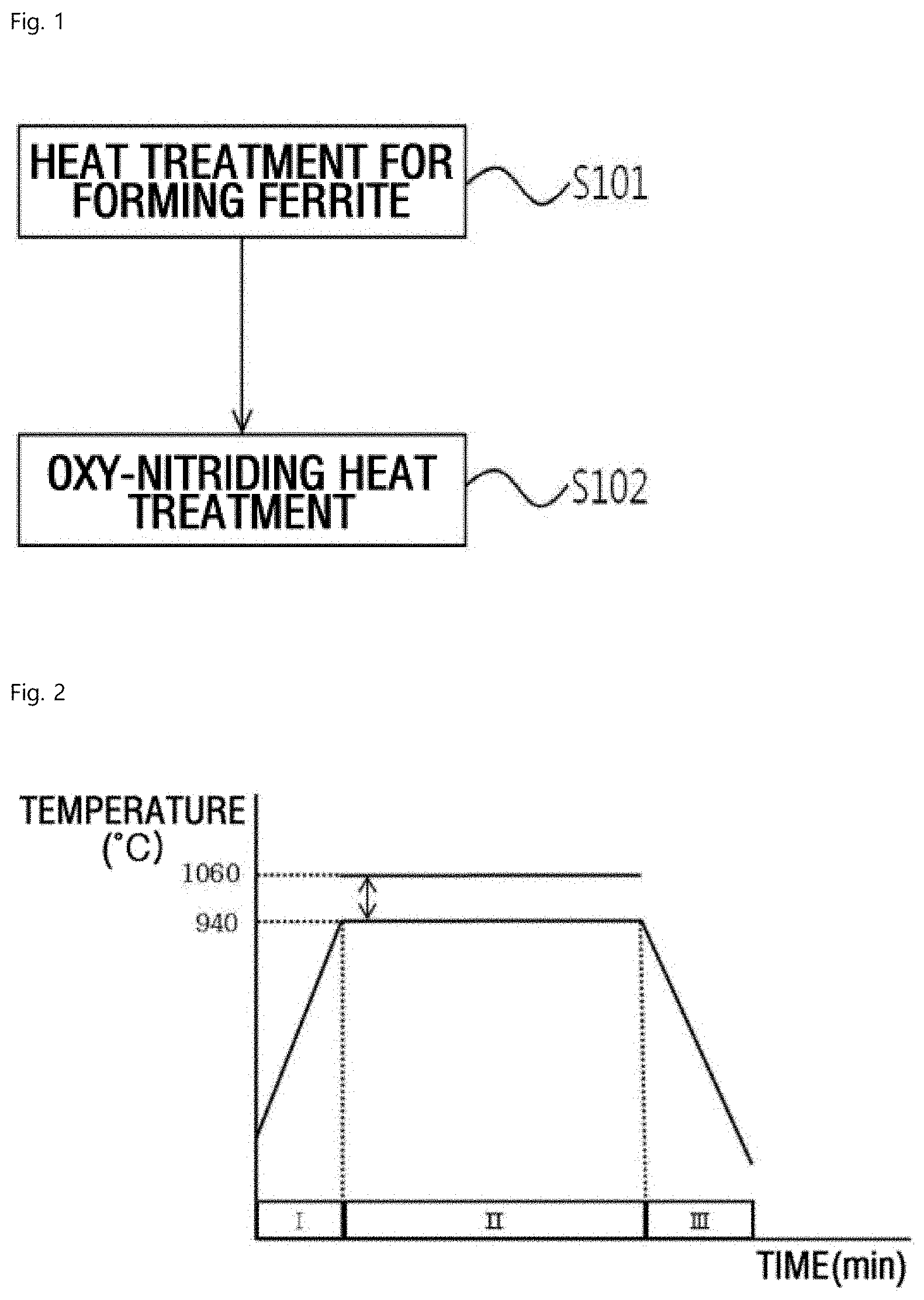
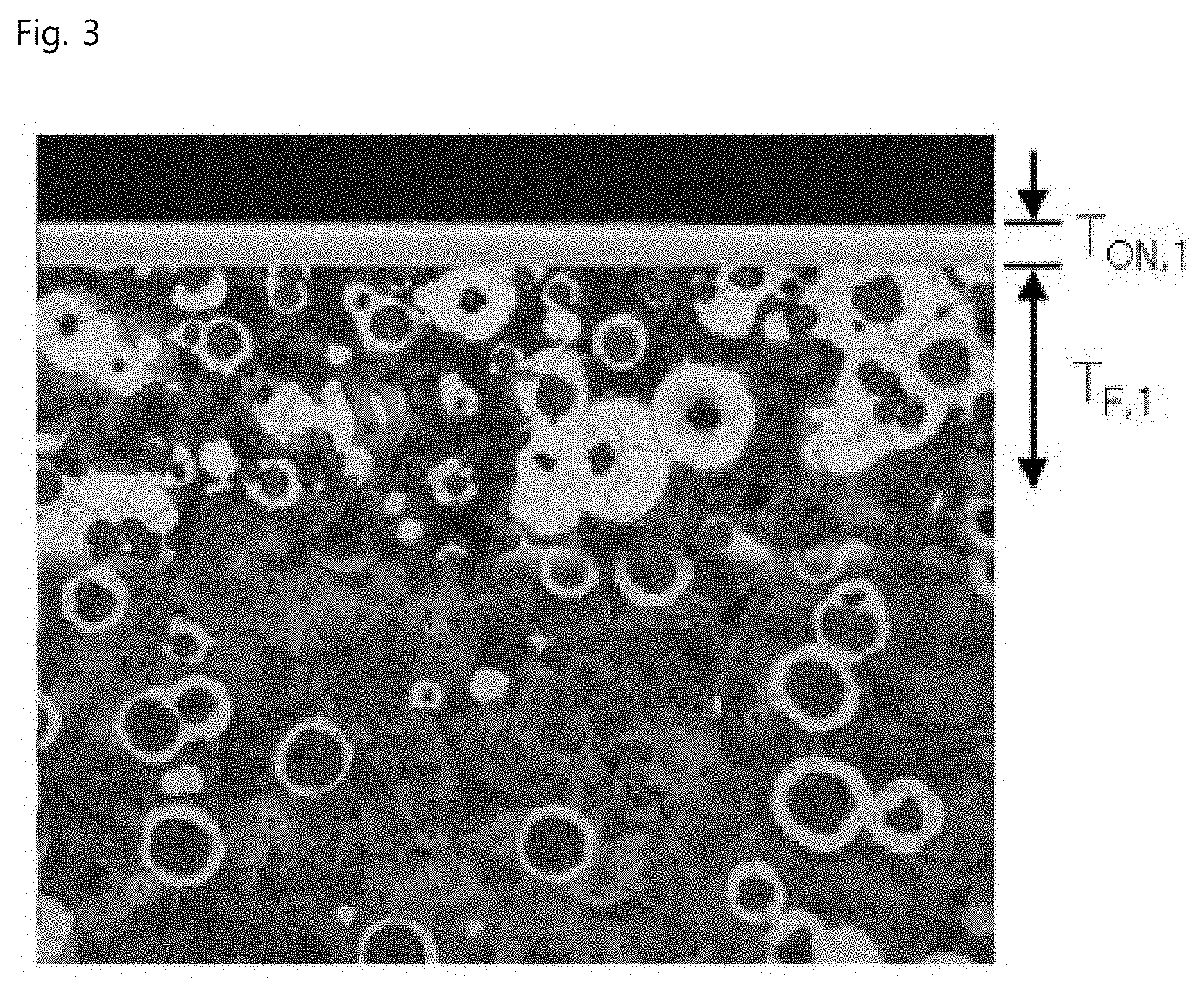
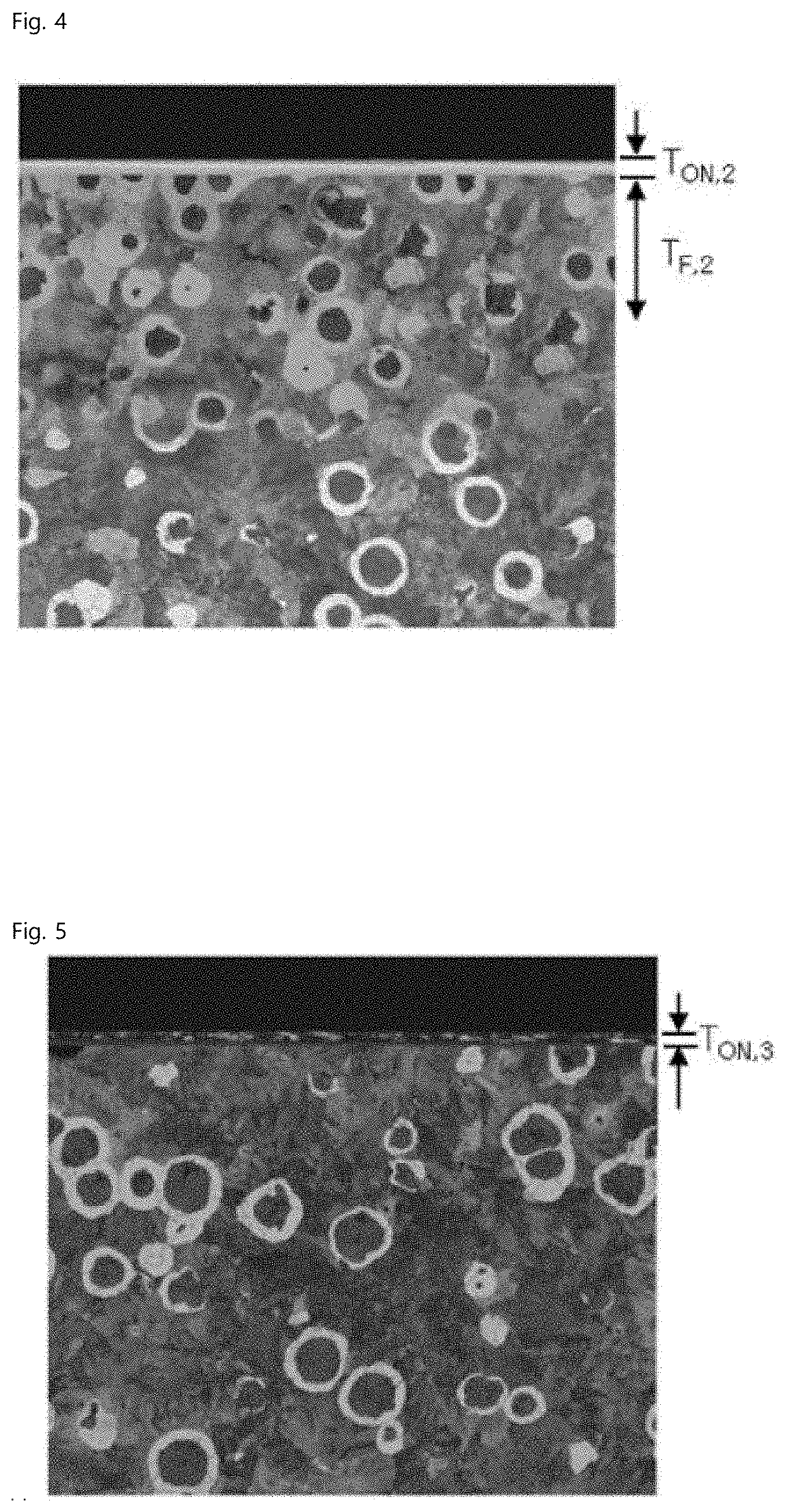
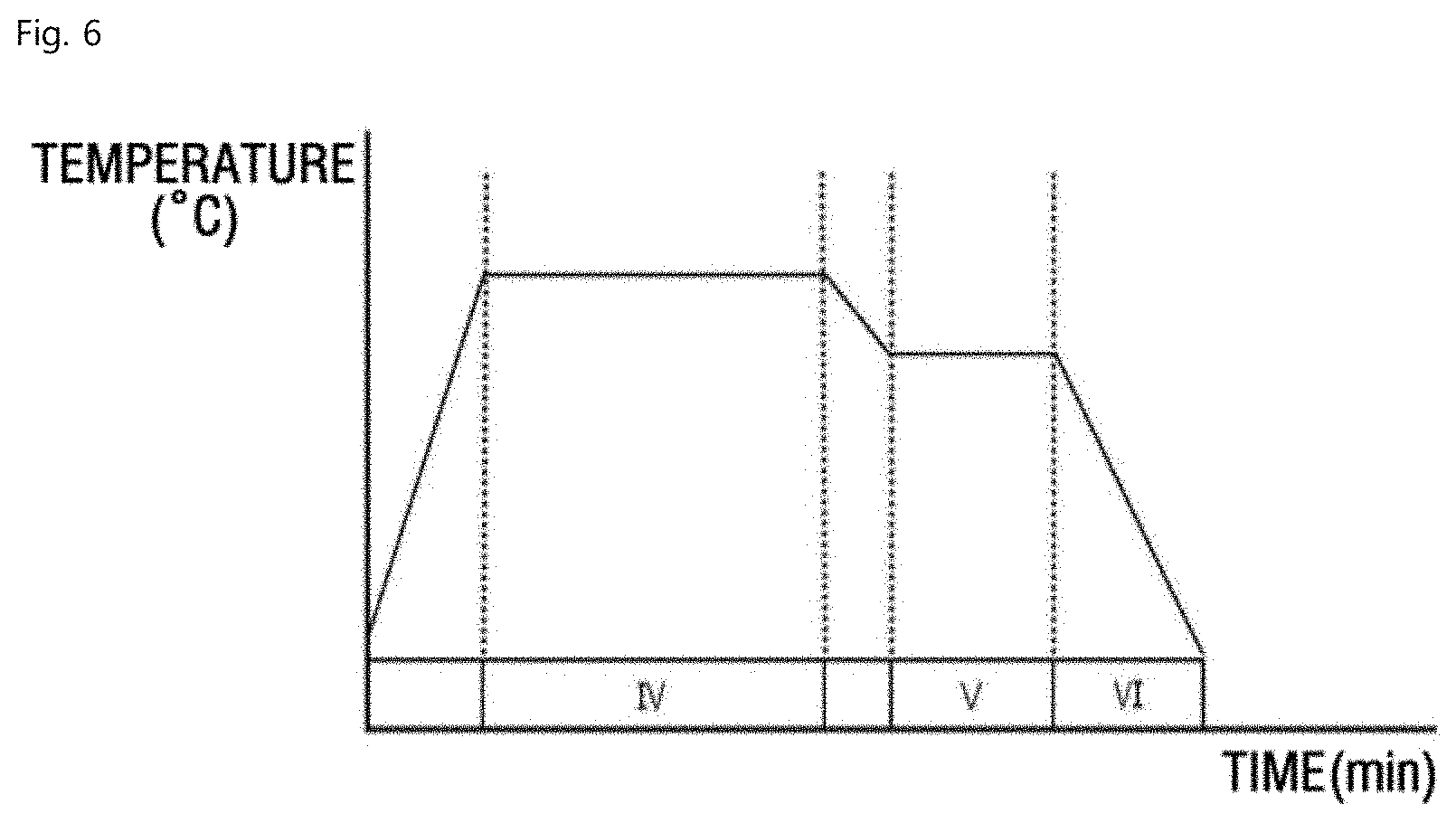
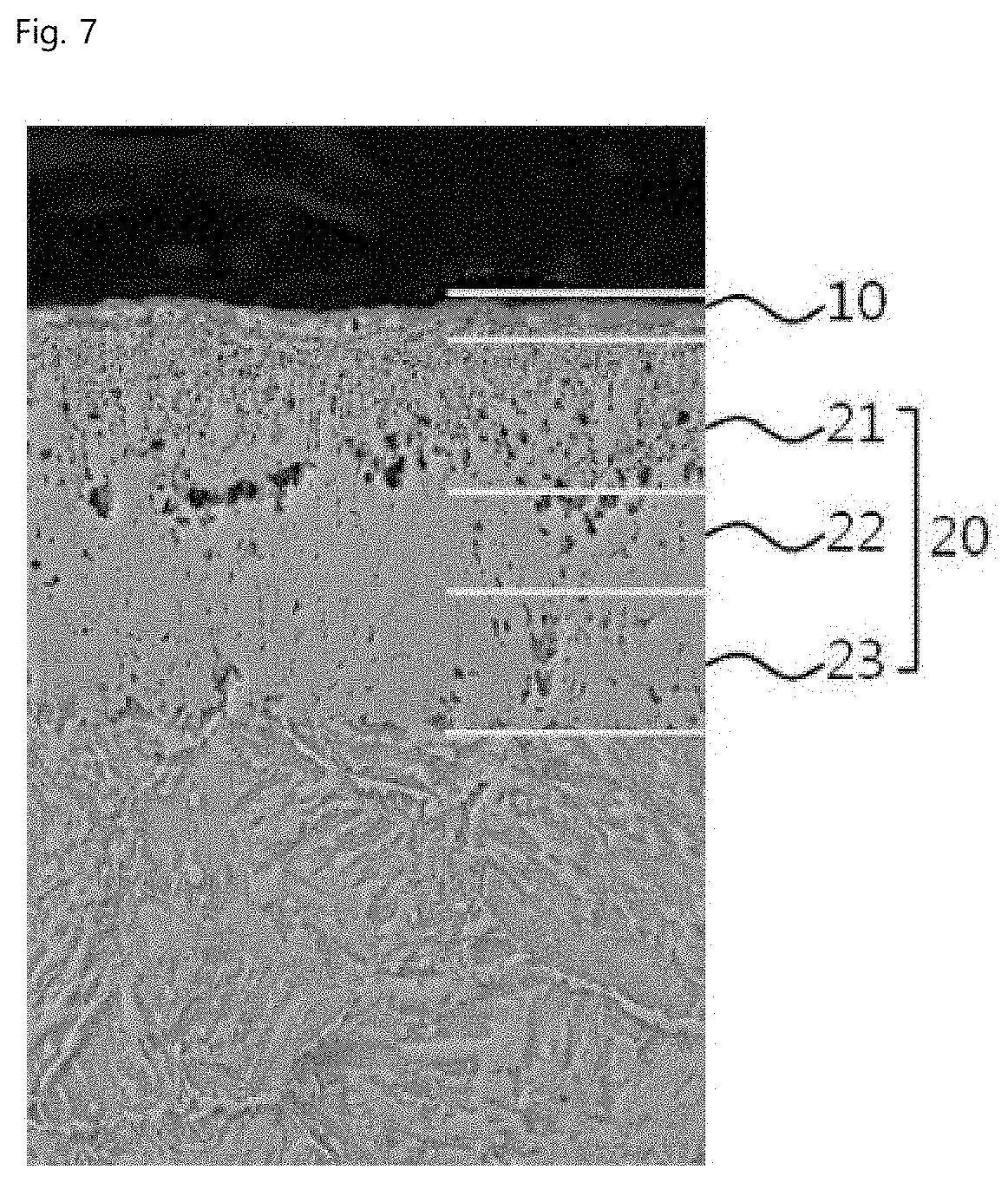
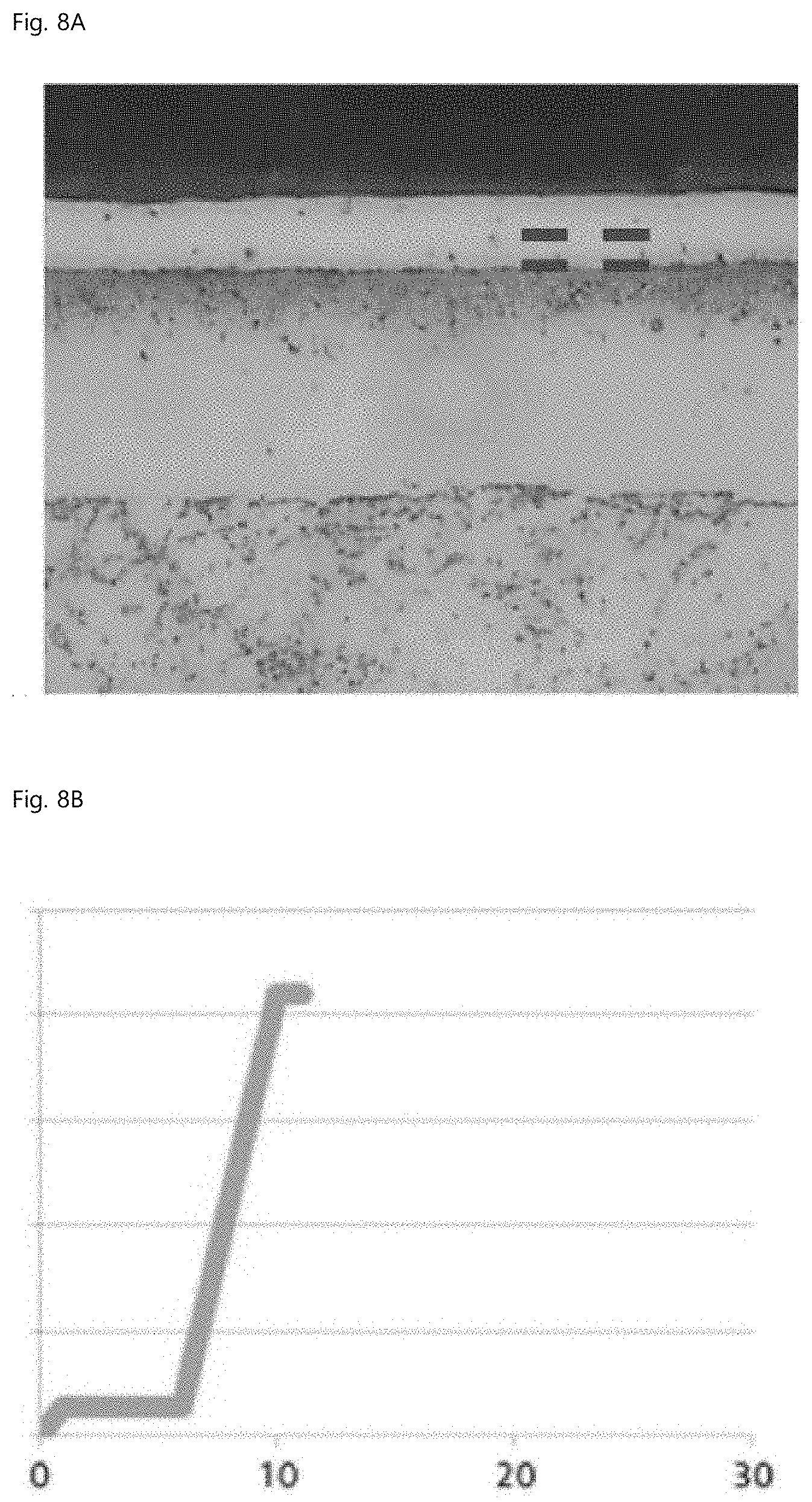
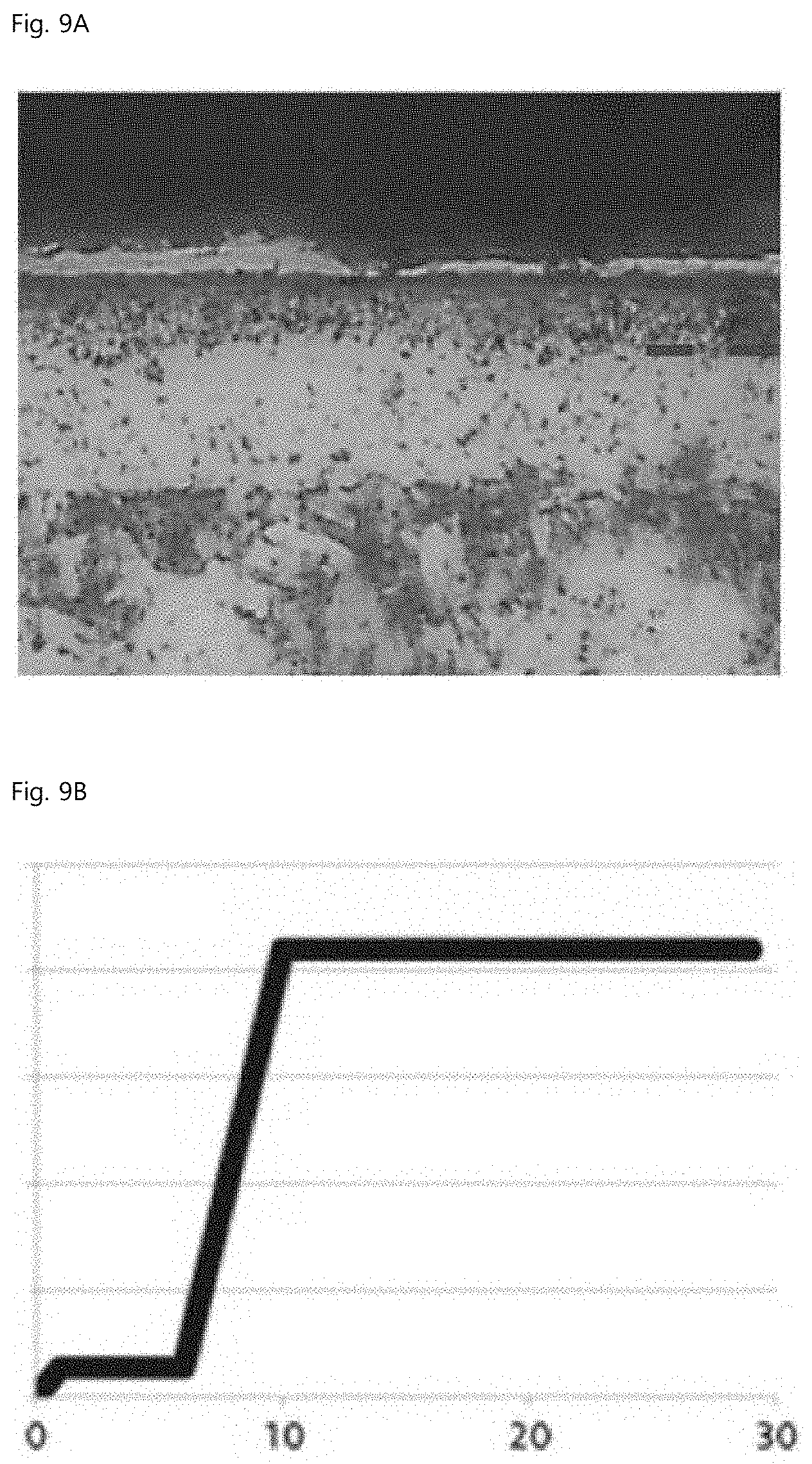
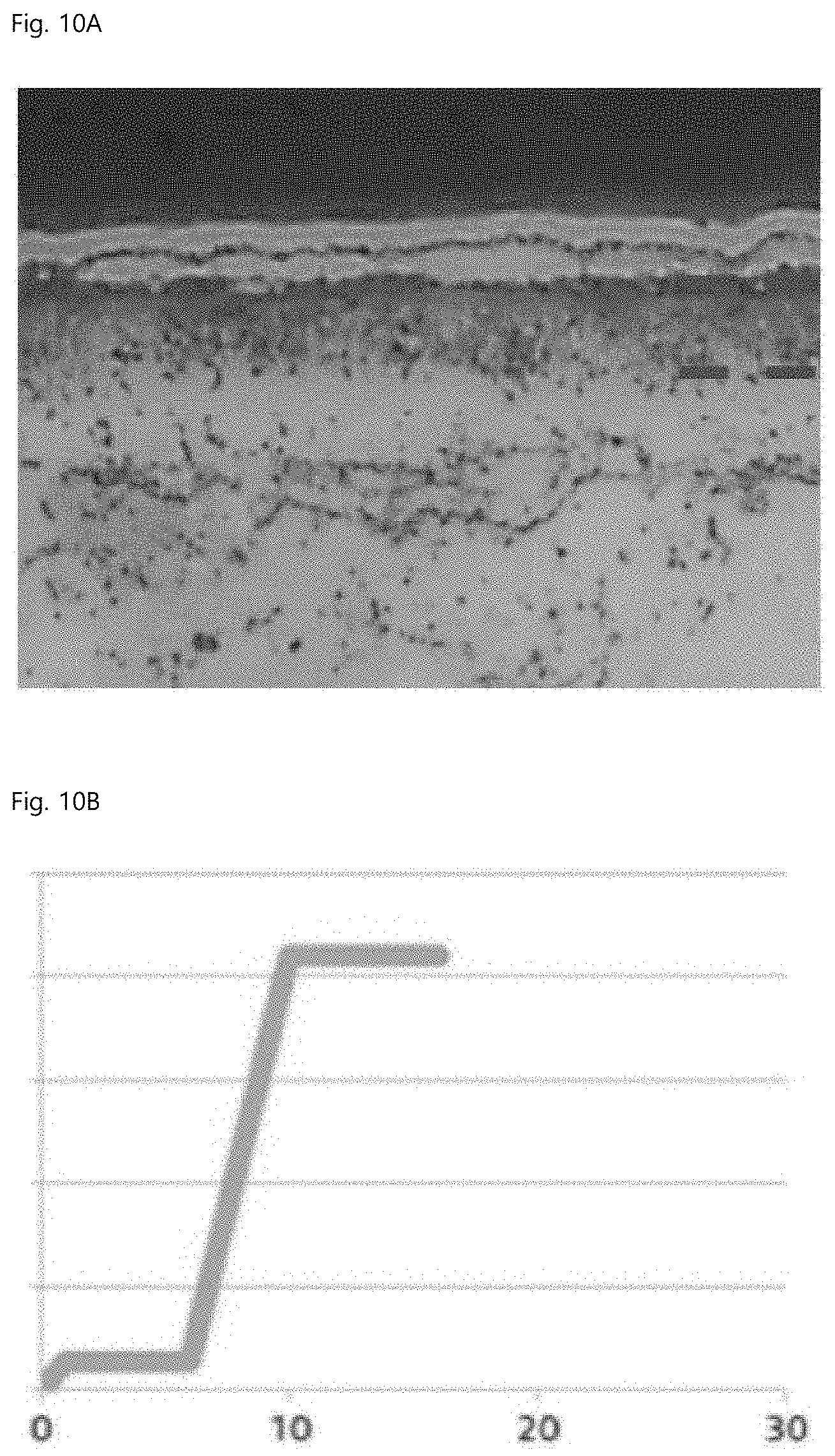
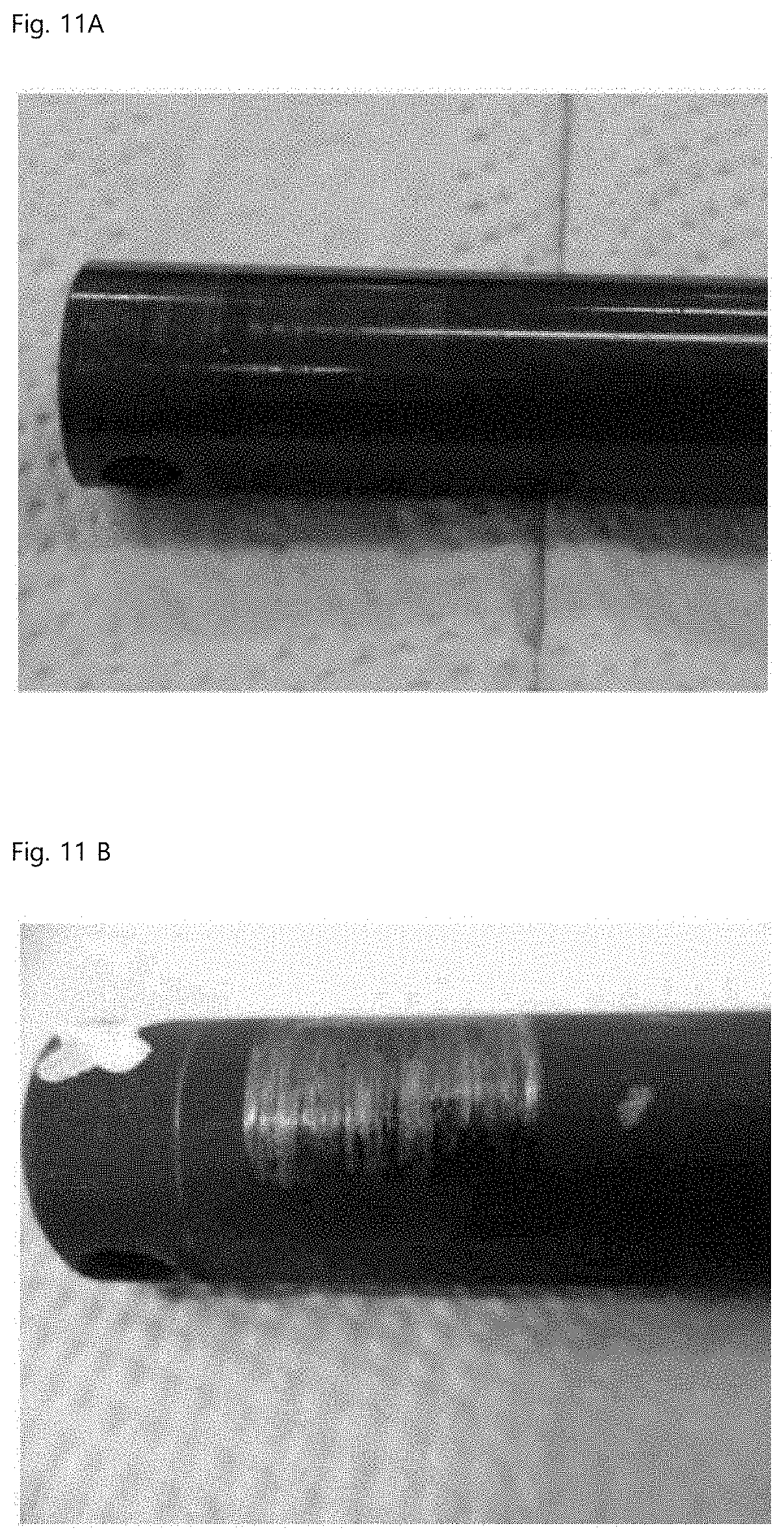

United States Patent
Application |
20200216923 |
Kind Code |
A1 |
Kwon; Eun-Soo ; et
al. |
July 9, 2020 |
METHOD FOR HEAT-TREATING UPPERMOST SURFACE OF SPHEROIDAL GRAPHITE
CAST IRON AND SPHEROIDAL GRAPHITE CAST IRON HEAT-TREATED BY THE
SAME
Abstract
Disclosed are a method for heat-treating a surface of a
spheroidal graphite cast iron, particularly, heat-treating an
uppermost surface of spheroidal graphite cast iron, and spheroidal
graphite cast iron heat-treated by the same. The method may include
first heat treating for forming ferrite and second heat treating
for oxy-nitriding. The spheroidal graphite cast iron heat-treated
includes an oxidation layer and a compound layer having a thickness
of about 15 to 30 .mu.m, which may be uniform. The method of the
heat-treating may decrease the pearlite fraction in the uppermost
surface of spheroidal graphite cast iron and increase the ferrite
fraction by forming ferrite, thereby forming a compound layer
having a thickness of about 15 to 30 .mu.m during an oxy-nitriding
heat treatment.
Inventors: |
Kwon; Eun-Soo; (Daegu,
KR) ; Lee; Hyung-Gook; (Iksan, KR) ; Sim;
Yong-Bo; (Seoul, KR) |
|
Applicant: |
Name |
City |
State |
Country |
Type |
Hyundai Motor Company
Kia Motors Corporation |
Seoul
Seoul |
|
KR
KR |
|
|
Family ID: |
71404956 |
Appl. No.: |
16/662633 |
Filed: |
October 24, 2019 |
Current U.S.
Class: |
1/1 |
Current CPC
Class: |
C23C 8/02 20130101; C21D
5/00 20130101; C23C 8/28 20130101; C23C 8/30 20130101; C23C 8/10
20130101; C23C 8/80 20130101 |
International
Class: |
C21D 5/00 20060101
C21D005/00; C23C 8/02 20060101 C23C008/02; C23C 8/10 20060101
C23C008/10; C23C 8/28 20060101 C23C008/28; C23C 8/80 20060101
C23C008/80 |
Foreign Application Data
Date |
Code |
Application Number |
Jan 7, 2019 |
KR |
10-2019-0001485 |
Claims
1. A method for heat-treating a surface of spheroidal graphite cast
iron, comprising: first heat treating the spheroidal graphite cast
iron for forming ferrite; and second heat treating for
oxy-nitriding the spheroidal graphite cast iron.
2. The method of claim 1, wherein the first heat treating
comprises: heating the spheroidal graphite cast iron to a first
heating temperature of about 940 to 1,060.degree. C.; and
maintaining the first heating temperature, wherein a total time for
the first heat treating time is about 80 to 100 minutes.
3. The method of claim 2, wherein the first heat treatment step
further comprises: air-cooling the spheroidal graphite cast iron
for about 110 to 130 minutes.
4. The method of claim 1, wherein the second heat treating
comprises: nitrocarburizing by introducing a gas; oxidizing the
spheroidal graphite cast iron; and cooling; wherein the
nitrocarburizing is performed at a second heat treating temperature
of about 550.degree. C. to 570.degree. C. for about 720 minutes to
1,200 minutes.
5. The method of claim 4, wherein the cooling is furnace
cooling.
6. A spheroidal graphite cast iron comprising: an oxidation layer;
and a compound layer, wherein the compound layer has a thickness of
about 15 to 30 .mu.m.
7. The spheroidal graphite cast iron of claim 6, wherein the
thickness of the compound layer is uniform.
8. The spheroidal graphite cast iron of claim 6, wherein an
uppermost surface of the spheroidal graphite cast iron comprises
ferrite fraction in about 60 to 80%.
9. The spheroidal graphite cast iron of claim 8, wherein the
compound layer comprises: a pore layer; and a nitride compound
layer comprising a gamma prime phase and an epsilon phase.
10. The spheroidal graphite cast iron of claim 9, wherein the
nitride compound layer consists of the gamma prime phase and the
epsilon phase.
11. The spheroidal graphite cast iron of claim 9, wherein the
nitride compound layer comprises the epsilon phase in about 80% or
greater.
12. The spheroidal graphite cast iron of claim 9, wherein the
compound layer has the hardness of about HV 600 to 1000.
13. The spheroidal graphite cast iron of claim 9, wherein the
compound layer comprises the pore layer in a fraction of about 25
to 35%.
14. The spheroidal graphite cast iron of claim 10, wherein the
compound layer comprises the pore layer in a fraction of about 25
to 35%.
15. The spheroidal graphite cast iron of claim 9, wherein the
compound layer comprises the oxidation layer, the pore layer, the
gamma prime phase and the epsilon phase from the uppermost surface
of the spheroidal graphite cast iron.
16. The spheroidal graphite cast iron of claim 6, the cast iron
comprises the oxidation layer and the compound layer from an
uppermost surface of the cast iron.
17. A vehicle part comprising a spheroidal graphite case iron of
claim 6.
18. A vehicle comprising a vehicle part of claim 17.
Description
CROSS-REFERENCE TO RELATED APPLICATIONS
[0001] This application claims priority under 35 U.S.C. .sctn. 119
to Korean Patent Application No. 10-2019-0001485, filed on Jan. 7,
2019, in the Korean Intellectual Property Office, the disclosure of
which is incorporated herein by reference in its entirety.
FIELD OF THE INVENTION
[0002] The present invention relates to a method for heat-treating
a surface of a spheroidal graphite cast iron, for example,
heat-treating an uppermost surface of the spheroidal graphite cast
iron and spheroidal graphite cast iron heat-treated by the same.
Particularly, the method may include an oxy-nitriding heat
treatment (second heat treating) of the uppermost surface of
spheroidal cast iron.
BACKGROUND OF THE INVENTION
[0003] Steel materials used as various parts of an automobile have
been subjected to various surface treatments such as high
frequency, oxy-nitration, and phosphate coating in order to secure
abrasion resistance and strength.
[0004] For instance, the oxy-nitriding heat treatment is a heat
treatment of increasing abrasion resistance and corrosion
resistance by introducing nitrogen [N] into a material in a high
temperature atmosphere to produce nitrides, and then spraying water
vapor to form an oxidation layer on the uppermost surface of a
compound layer.
[0005] The oxy-nitriding heat treatment has been frequently
performed on general carbon steel as a heat treatment for securing
durability and abrasion resistance, but the oxy-nitriding heat
treatment has not been applied well to spheroidal graphite cast
iron even though the oxy-nitriding heat treatment also needs to be
applied in order to secure abrasion resistance, and the like. This
is because spheroidal graphite cast iron not only includes a
greater amount of silicon (Si) than a conventional carbon steel,
but also has a pearlite fraction of 60% or greater. In particular,
even though the pearlite fraction is for having high toughness and
tensile strength, when an oxy-nitriding heat treatment is performed
on spheroidal graphite cast iron, a compound layer is
disadvantageously formed due to pearlite on the surface of
spheroidal graphite cast iron, so that the surface treatment effect
cannot be exhibited because the thickness of the compound layer is
formed at a level of 1/2 to 1/3 as compared to the conventional
carbon steel.
SUMMARY OF THE INVENTION
[0006] In preferred aspects, provided is a method of forming a
compound layer having a predetermined thickness or greater by
performing an oxy-nitriding heat treatment while reducing the
pearlite fraction on the uppermost surface of spheroidal graphite
cast iron.
[0007] The term "spheroidal graphite cast iron" as used herein
refers to a cast iron or a cast ferrous alloy including graphite
(e.g., nodular graphite, spheroid-like or spheroidal graphite) as
one of the carbon source. The term "spheroidal graphite cast iron"
may be used interchangeably with ductile cast iron so as to have
same grades and mechanical and chemical properties as ductile iron.
For instance, the spheroidal graphite cast iron may suitably
include carbon in an amount of about 3.2 to 3.60 wt % of the total
weight of the composition as well as other components such as
silicon, manganese, magnesium, phosphorus, sulfur, and/or copper
with remaining balance of iron.
[0008] The term "uppermost surface" as used herein refers to a
surface area and underneath thereof, which may include a space/area
from the surface to a predetermined depth, preferably a depth of up
about 50, 100 or 200 .mu.m from the exposed surface, more typically
a depth up to about 100 .mu.m from the exposed surface.
[0009] In an aspect, provided is a method for heat-treating a
surface of a spheroidal graphite cast iron, particularly an
uppermost surface of the spheroidal graphite cast iron. The method
may include first heat treating the spheroidal graphite cast iron
for forming ferrite, and second heat treating for oxy-nitriding the
spheroidal graphite cast iron.
[0010] As referred to herein, the term "spheroidal graphite cast
iron" is a type of iron that is also known as ductile iron or
ductile cast iron and may have graphite within that may appear like
spheres or nodules under high magnification (e.g. 100.times. or
magnification).
[0011] The term "oxy-nitriding" as used herein refers to a process
for nitriding and oxidation (oxidizing), which may be combined or
in separate sequential process. Preferably, the oxy-nitriding may
include sequential processes of respective nitriding and
oxidizing.
[0012] The term "nitriding" or "nitrocarburizing" as used herein
refers to a process for diffusing nitrogen on a surface of a metal
(e.g. metal alloy, steel or cast iron) by heat treating using gas,
salt or nitrogen media in plasma. Preferably, the nitriding process
may be performed by using nitrogen rich gas (e.g., NH.sub.3) so as
to form a nitride layer at high temperature, e.g., at a temperature
greater than about 500.degree. C., 600.degree. C., 700.degree. C.,
800.degree. C., 900.degree. C., or 1000.degree. C., or by applying
heat.
[0013] The term "oxidation" or "oxidizing" as used herein refers to
a process of inducing a reaction in which a metal and oxygen
combined to form an oxide, or oxidation layer or deposit thereof.
Exemplary oxidation process may include heat treating or high
temperature oxidation, e.g., at a temperature greater than about
500.degree. C., 600.degree. C., 700.degree. C., 800.degree. C.,
900.degree. C., or 1000.degree. C.
[0014] Preferably, the first heat treating for forming ferrite may
include heating the spheroidal graphite cast iron to a first
heating temperature of about 940 to 1,060.degree. C. and
maintaining the first heating temperature, and a total time for the
first heat treating may be about 80 to 100 minutes.
[0015] Preferably, the first heat treating for forming ferrite may
further include air-cooling the spheroidal graphite cast iron for
about 110 to 130 minutes.
[0016] Preferably, the second heat treating for oxy-nitriding may
include nitrocarburizing by introducing a gas, oxidizing the
spheroidal graphite cast iron, and cooling. The nitrocarburizing
may be performed at a second heat treating temperature of about
550.degree. C. to 570.degree. C. for about 720 minutes to 1,200
minutes.
[0017] In another aspect, provided is a spheroidal graphite cast
iron heat-treated by the heat treatment. In particular, an
uppermost surface of spheroidal graphite cast iron may be treated
by the method described herein. The spheroidal graphite cast iron
may include an oxidation layer and a compound layer, in which a
thickness of the compound layer is 15 to 30 .mu.m. Preferably, the
thickness of the compound layer may be uniform.
[0018] Preferably, an uppermost surface of the spheroidal graphite
cast iron may include a ferrite fraction in about 60 to 80%.
[0019] Preferably, the compound layer may include a pore layer and
a nitride compound layer. The nitride compound layer may include a
gamma prime phase and an epsilon phase. Alternatively, the nitride
compound layer may consist of the gamma prime phase and the epsilon
phase.
[0020] Preferably, the compound layer may include the pore layer
fraction in about 25 to 35%.
[0021] Preferably, the nitride compound layer may include the
epsilon phase in about 80% or greater.
[0022] Preferably, the compound layer may have a hardness of about
HV 600 to 1000.
[0023] According to various exemplary embodiments, the compound
layer having a thickness of 15 to 30 .mu.m, which may be formed
during oxy-nitriding heat treating (e.g., second heat treating) by
increasing the ferrite fraction, may be formed on the uppermost
surface of spheroidal graphite cast iron.
[0024] According to various exemplary embodiments, abrasion
resistance of the spheroidal graphite cast iron may be by
controlling the pore layer fraction to about 25 to 35%.
[0025] Preferably, the compound layer may include the oxidation
layer, the pore layer, the gamma prime phase and the epsilon phase
from the uppermost surface of the spheroidal graphite cast
iron.
[0026] The spheroidal graphite cast iron may include the oxidation
layer and the compound layer from an uppermost surface of the cast
iron.
[0027] Further provided is a vehicle part that may include the
spheroidal graphite cast iron as described herein.
[0028] Also provided is a vehicle that may include the vehicle part
as described herein.
[0029] Other aspects of the invention are provided infra.
BRIEF DESCRIPTION OF THE DRAWINGS
[0030] FIG. 1 shows an exemplary method for heat-treating an
exemplary cast iron including spheroidal graphite cast iron on its
uppermost surface according to an exemplary embodiment of the
present invention.
[0031] FIG. 2 shows an exemplary heat treatment step for forming
ferrite according to an exemplary embodiment of the present
invention.
[0032] FIG. 3 shows an images of an exemplary microstructure of
spheroidal graphite cast iron after the heat treatment step for
forming ferrite according to an exemplary embodiment of the present
invention.
[0033] FIG. 4 shows an images of an exemplary microstructure of an
exemplary spheroidal graphite cast iron heat-treated at a heating
temperature less than the heating temperature of the heat treatment
step for forming ferrite according to an exemplary embodiment of
the present invention.
[0034] FIG. 5 shows an exemplary microstructure of a conventional
spheroidal graphite cast iron.
[0035] FIG. 6 is a detailed configuration view of an oxy-nitriding
heat treatment step, according to an exemplary embodiment of the
present invention.
[0036] FIG. 7 illustrates a configuration of the uppermost surface
of spheroidal graphite cast iron after the oxy-nitriding heat
treatment step according to an exemplary embodiment of the present
invention.
[0037] FIG. 8A is a microstructure of Comparative Example 2, and
FIG. 8B is a result of evaluating seizure resistance of Comparative
Example 2.
[0038] FIG. 9A is a microstructure of Example 2, and FIG. 9B is a
result of evaluating seizure resistance of Example 2.
[0039] FIG. 10A is a microstructure of Comparative Example 3, and
FIG. 10B is a result of evaluating seizure resistance of
Comparative Example 3.
[0040] FIG. 11A is a photograph after evaluating seizure resistance
of Example 2, and FIG. 11B is a photograph after evaluating seizure
resistance of Comparative Example 3.
DETAILED DESCRIPTION OF THE EMBODIMENTS
[0041] Hereinafter, the present invention will be described in
detail. However, the present invention is not limited or restricted
by exemplary embodiments, objects and effects of the present
invention will be naturally understood or become apparent from the
following description, and the objects and effects of the present
invention are not limited by only the following description.
Further, in the description of the present invention, when it is
determined that the detailed description for the publicly-known
technology related to the present invention can unnecessarily
obscure the gist of the present invention, the detailed description
thereof will be omitted.
[0042] The terminology used herein is for the purpose of describing
particular embodiments only and is not intended to be limiting. As
used herein, the singular forms "a," "an" and "the" are intended to
include the plural forms as well, unless the context clearly
indicates otherwise. It will be further understood that the terms
"comprise", "include", "have", etc. when used in this
specification, specify the presence of stated features, regions,
integers, steps, operations, elements and/or components but do not
preclude the presence or addition of one or more other features,
regions, integers, steps, operations, elements, components, and/or
combinations thereof.
[0043] It is understood that the term "vehicle" or "vehicular" or
other similar term as used herein is inclusive of motor vehicles in
general such as passenger automobiles including sports utility
vehicles (SUV), buses, trucks, various commercial vehicles,
watercraft including a variety of boats and ships, aircraft, and
the like, and includes hybrid vehicles, electric vehicles, plug-in
hybrid electric vehicles, hydrogen-powered vehicles and other
alternative fuel vehicles (e.g. fuels derived from resources other
than petroleum). As referred to herein, a hybrid vehicle is a
vehicle that has two or more sources of power, for example both
gasoline-powered and electric-powered vehicles.
[0044] Further, unless specifically stated or obvious from context,
as used herein, the term "about" is understood as within a range of
normal tolerance in the art, for example within 2 standard
deviations of the mean. "About" can be understood as within 10%,
9%, 8%, 7%, 6%, 5%, 4%, 3%, 2%, 1%, 0.5%, 0.1%, 0.05%, or 0.01% of
the stated value. Unless otherwise clear from the context, all
numerical values provided herein are modified by the term
"about."
[0045] FIG. 1 shows an exemplary method for heat-treating the
uppermost surface of spheroidal graphite cast iron according to an
exemplary embodiment of the present invention. The method may
include a heat treatment step for forming ferrite (S101) and an
oxy-nitriding heat treatment step (S102).
[0046] Particularly, a proportion of pearlite which may be formed
or present on the uppermost surface of spheroidal graphite cast
iron may be decreased and a proportion of ferrite may be increased
by performing a first heat treatment step for forming ferrite
(S101) before performing a second heat treating step for
oxy-nitriding (S102). Accordingly, during the oxy-nitriding heat
treatment, a compound layer having a predetermined thickness or
greater may be formed, as such abrasion resistance characteristics
on the uppermost surface of spheroidal graphite cast iron may be
provided, and a dense and uniform compound layer may be formed.
Furthermore, a microstructure may be formed at the center of
pearlite in the deep portion of spheroidal graphite cast iron,
thereby having substantially improved toughness and strength.
[0047] The uppermost surface of spheroidal graphite cast iron as
used herein refers to an area from the surface of cast iron to a
depth of about 100 .mu.m. The compound layer having a predetermined
thickness or greater may have a thickness of about 15 .mu.m or
greater, or particularly have a thickness of about 15 to 30 .mu.m.
The dense and uniform compound layer refers to that compound layer
which is present while being distinguished from an oxide layer and
does not crack or break across the compound layer.
[0048] FIG. 2 shows an exemplary first heat treatment step for
forming ferrite according to an exemplary embodiment of the present
invention. The first heat treatment step for forming ferrite may
include heating spheroidal graphite cast iron to a first heat
treatment temperature of about 940 to 1,060.degree. C. (I),
maintaining the first heating treatment temperature (II), and
air-cooling the spheroidal graphite cast iron.
[0049] Preferably, a uniform austenitized state may be formed
through the heating step and the heating temperature maintaining
step. When the uppermost surface of cast iron is austenitized, and
then air-cooled, that residual stress may be removed due to
processing and the like and crystal grains may be micronized, and
ferrite may be formed on the uppermost surface, so that during the
oxy-nitriding heat treatment, production of a nitrogen compound
layer which is one configuration of the compound layer, for
example, an epsilon (.epsilon.) phase and a gamma prime phase
(.gamma.'), may be facilitated. In addition, the compound layer
which is more dense and has a uniform thickness may be formed on
the entire part surface.
[0050] The first heating treatment temperature of spheroidal
graphite cast iron may be about 940 to 1,060.degree. C. When
spheroidal graphite cast iron is heated at a temperature less than
about 940.degree. C., and then air-cooled, the ferrite fraction in
the uppermost surface of spheroidal graphite cast iron may be
reduced to less than 60%, so that a compound layer having a
predetermined thickness or more may not be secured. Accordingly, it
is preferred that the heating temperature of spheroidal graphite
cast iron may be 940.degree. C. or greater. Here, the unit "%",
which is a unit of the ferrite fraction, means an area occupied by
ferrite in spheroidal graphite cast iron. Meanwhile, when the
heating temperature is about 1,060.degree. C. or less, a uniform
austenite structure may be obtained because the austenite structure
does not change into a melt. Accordingly, it is preferred that the
maximum heating temperature is about 1,060.degree. C.
[0051] Preferably, the total time for performing the heating step
(I) and the heating temperature maintaining step (II) may be about
80 to 100 minutes in order to secure a ferrite fraction of 60% or
greater, and the time for performing the air-cooling step (III) may
be of about 110 to 130 minutes.
[0052] Ferrite present in a diffusion layer remaining after the
formation of the compound layer may improve elongation
characteristics of a part and increase toughness of the part.
Further, during the oxy-nitriding heat treatment, surface hardness
and compressive residual stress may occur due to the invasive
diffusion of carbon and nitrogen in the ferrite layer, and as a
result, fatigue strength may be improved.
[0053] As a deep portion is changed from a structure in a medium
pearlite state to a fine pearlite structure, the interlamellar
spacing of pearlite may be decreased, so that the stiffness of a
part may be improved because the sintering modification of the part
is blocked.
[0054] FIG. 3 illustrates an exemplary microstructure of an
exemplary spheroidal graphite cast iron heat-treated (hereinafter,
referred to as Example 1) by the first heat treatment step for
forming ferrite according to an exemplary embodiment of the present
invention, and FIG. 4 illustrates a microstructure of spheroidal
graphite cast iron heat-treated (hereinafter, referred to as
Comparative Example 1) at a heating temperature less than the
heating temperature of the heat treatment step for forming ferrite.
FIG. 5 illustrates an exemplary microstructure of a conventional
spheroidal graphite cast iron.
[0055] The following Table 1 summarizes the heating conditions and
cooling conditions of spheroidal graphite cast iron illustrated in
FIGS. 3 to 5. Table 2 summarizes the ferrite layer thicknesses,
ferrite fractions, and oxynitride layer thicknesses of spheroidal
graphite cast iron illustrated in FIGS. 3 to 5.
TABLE-US-00001 TABLE 1 Comparative Classification Example 1 Example
1 conventional Heating temperature 970.degree. C. 850.degree. C. X
Heating time 100 minutes 80 minutes X Cooling method Air cooling
Air cooling X Cooling time 120 minutes 120 minutes X
TABLE-US-00002 TABLE 2 Comparative Classification Example 1 Example
1 conventional Ferrite layer thickness 500 .mu.m 500 .mu.m --
(T.sub.F) Ferrite fraction 60~80% 30~50% 30% Oxynitride layer 20
.mu.m 6 .mu.m 4 .mu.m or less thickness (T.sub.ON)
[0056] As shown in Tables 1 and 2 and FIGS. 3 to 5, the ferrite
layer thickness (T.sub.F1) in Example 1 was 500 .mu.m and the
ferrite layer thickness (T.sub.F2) in Comparative Example 1 was
also 500 .mu.m and was the same as the ferrite layer thickness in
Example 1, but the ferrite fraction in Example 1 was 60 to 80%,
which is higher than the ferrite fraction in Comparative Example 1,
which was 30 to 50%, and accordingly, the thickness (T.sub.ON,1) of
the oxynitride layer in Example 1 was 20 .mu.m, which was formed to
be about 3.3 times larger than 6 .mu.m of the thickness
(T.sub.ON,2) of the oxynitride layer in Comparative Example 1.
[0057] In the related art, the conventional spheroidal graphite
cast iron which is not subjected to a heat treatment for forming
ferrite has a ferrite fraction of 30%, and the conventional
spheroidal graphite cast iron may not have a separate ferrite layer
capable of being distinguished from the other portions in the
spheroidal graphite cast iron. When as the ferrite layer is not
provided, the thickness (T.sub.ON,3) of the oxynitride layer in the
conventional cast iron may be also formed to be 4 .mu.m or less,
which is less than the thickness (T.sub.ON,2) of the oxynitride
layer in Comparative Example 1 and remarkably smaller than the
thickness (T.sub.ON,1) of the oxynitride layer in Example 1.
[0058] Accordingly, in order to secure an oxynitride layer
thickness of 15 .mu.m or greater, a ferrite fraction of 60 to 80%
needs to be secured by decreasing the pearlite fraction on the
surface of spheroidal graphite cast iron. Accordingly, a heat
treatment step for forming ferrite may be performed without fail
before the oxy-nitriding heat treatment, but the spheroidal
graphite cast iron may be heated at the temperature of about 940 to
1,060.degree. C. for about 80 to 100 minutes, and then may be
air-cooled for about 110 to 130 minutes.
[0059] FIG. 6 shows an exemplary second heat treating step for an
oxy-nitriding heat treatment according to an exemplary embodiment
of the present invention. The oxy-nitriding heat treatment step may
include a gas nitrocarburizing step (IV), an oxidation treatment
step (V), and a furnace cooling step (VI).
[0060] In order for a compound layer formed by the oxy-nitriding
heat treatment step to have abrasion resistance characteristics,
the fraction of a pore layer formed during the gas nitrocarburizing
step may be controlled. The pore layer fraction refers to the pore
layer thickness/the compound layer thickness, and the compound
layer refers to a layer including a pore layer and a nitride
compound layer consisting of a gamma prime phase (.gamma.') and an
epsilon phase (.epsilon.).
[0061] When the pore layer fraction is less than about 25%, the
oil-containing characteristics may be reduced, so that an effect of
lowering frictional force may significantly be decreased. When the
pore layer fraction is greater than 35%, the proportion of a soft
porous layer may be increased, so that the entire hardness of the
compound layer may be reduced, and as a result, abrasion resistance
may deteriorate. Accordingly, the compound layer may include the
pore layer fraction in about 25 to 35% in order to improve abrasion
resistance.
[0062] The pore layer fraction may be affected by temperature and
time during the nitrocarburizing treatment by introducing a gas,
e.g., gas nitrocarburizing. Preferably, the nitrocarburizing
treatment may be performed at an Ac1 temperature of about
723.degree. C. or less, or particularly, of about 550.degree. C. to
570.degree. C. for about 720 minutes to 1,200 minutes. When the
temperature is less than about 550.degree. C. and the treatment
time is greater than about 1,200 minutes, the pore layer fraction
may be decreased to less than about 25%. In addition, when the
temperature is greater than about 570.degree. C. and the treatment
time is less than about 720 minutes, the pore layer fraction may be
greater than about 35%. Preferably, the oxidation treatment step
may be performed at about 560.degree. C. for about 30 minutes, and
the furnace cooling step may be performed at about 60.degree. C.
for about 150 minutes.
[0063] FIG. 7 illustrates an image of an exemplary uppermost
surface of an exemplary spheroidal graphite cast iron after the
second heat treating, i.e. oxy-nitriding heat treatment step. The
uppermost surface of spheroidal graphite cast iron subjected to the
heat treatment for forming ferrite and the oxy-nitriding heat
treatment may include an oxidation layer 10 of Fe.sub.3O.sub.4 and
a compound layer 20, the compound layer may have a thickness of
about 15 .mu.m to 30 .mu.m, and the thickness may be uniform.
[0064] In order to improve the durability, the compound layer may
be formed to have a thickness of about 15 .mu.m to 30 .mu.m, which
may be uniform. When the thickness of the compound layer is formed
to less than about 15 .mu.m, hardness of the compound layer may be
reduced to less than about HV 600, so that when a part is operated,
the compound layer may be easily peeled off, and as a result, the
abrasion resistance function may be lost. Further, when the
thickness of the compound layer is formed to be more than 30 .mu.m,
the compound layer may have hardness enough for brittleness at a
level of HV 1200 to occur, so that when a part is operated, fatigue
failure occurs starting from the compound layer. Accordingly, it is
preferred that the thickness of the compound layer may be of about
15 .mu.m to 30 .mu.m in order to allow the compound layer to have a
hardness of HV 600 to 1000.
[0065] A pore layer 21 may be a porous layer of an oxynitride layer
present below an oxidation layer 10, and may be relatively soft in
the compound layer. The pore layer may contain a lubricating oil in
a transmission, an engine, and the like, so that when a part is
operated, frictional force may be reduced. Accordingly, when an
optimal pore layer fraction is secured, an influence in which
abrasion may occur by improving lubrication characteristics with
the opponent part may be minimized. Accordingly, it is preferred
that the pore layer fraction is about 25 to 35%.
[0066] Nitride compound layers 22 and 23 may include a gamma prime
(.gamma.') phase 22 and an epsilon (.epsilon.) phase 23. The
nitride compound layers 22 and 23 may be present below the pore
layer 21, the gamma prime phase 22 may be located under the pore
layer, and the epsilon phase 23 may be located below the gamma
prime phase 22. Moreover, it is preferred that the proportion of
the epsilon phase 23 in the nitride compound layers 22 and 23 may
be about 80% or greater. Meanwhile, the unit % means an area
occupied by the epsilon phase in the nitride compound layer.
[0067] During the gas nitrocarburizing treatment, the gamma prime
phase 22 of Fe.sub.4N may be produced while the uppermost surface
of spheroidal graphite cast iron begins to solid-solubilize
nitrogen. The gamma prime phase 22 may be generally produced when
the concentration of nitrogen is about 0.1% or greater, and from
the time when the concentration of nitrogen is about 6% or greater,
the epsilon phase 23 of Fe.sub.2,3N may be produced, and the
epsilon phase 23 may also be transformed into the gamma prime phase
22.
[0068] The gamma prime phase 22 may affect the strength of a
compound layer, and the epsilon phase 23 may affect the toughness.
In general, the higher the proportion of the epsilon phase 23 is,
the better corrosion resistance and abrasion resistance
characteristics of cast iron may be obtained. In addition, the
higher the proportion of the epsilon phase 23 is, the more nitrogen
may be solid solubilized. When the epsilon phase 23 is about 80% or
less, nitride may be relatively less solid solubilized on the
surface and may be disadvantageous in terms of seizure resistance
and abrasion resistance, so that the fraction of the epsilon phase
23 may be adjusted to about 80% or greater. Further, the fraction
of the epsilon phase 23 may be adjusted to about 80% or greater in
order to form a compound layer having a hardness of about HV 600 to
1000.
TABLE-US-00003 TABLE 3 Comparative Comparative Classification
Example 2 Example 2 Example 3 K.sub.N 1.5 2.0 3.0 Temperature
(.degree. C.) 540 570 590 Time (hr) 22 16 10 Pore layer fraction
10% 25% 40%
[0069] Table 3 summarizes the conditions of the gas
nitrocarburizing step and the pore layer fractions in Comparative
Example 2, Example 2, and Comparative Example 3. K.sub.N in Table 3
indicates a ratio of partial pressure of ammonia to partial
pressure of hydrogen in a furnace during the oxy-nitriding heat
treatment
( K N = P NH 3 P H 2 1 / 2 ) . ##EQU00001##
FIG. 8A is a microstructure of Comparative Example 2, and FIG. 8B
is a result of evaluating seizure resistance of Comparative Example
2. FIG. 9A is a microstructure of Example 2, and FIG. 9B is a
result of evaluating seizure resistance of Example 2. FIG. 10A is a
microstructure of Comparative Example 3, and FIG. 10B is a result
of evaluating seizure resistance of Comparative Example 3. The
x-axis and the y-axis in FIGS. 8B, 9B, and 10B are time (min) and
load (kg), respectively, and the interval of the load is 500
kg.
[0070] The evaluation of seizure resistance and abrasion resistance
is based on the FALEX PIN & VEE BLOCK test, based on ASTM
D3233A. A load is applied to the middle pin through right and left
V-BLOCKs, and when seizure occurs between a pin rotating at high
speed and a block, the test is terminated while the BRASS LOCKING
PIN is broken. By comparison of the time when breakage of the fixed
pin occurs, the seizure resistances of test specimens can be
compared. In other words, the times when the maximum load is
maintained are compared.
[0071] As shown in Table 3 and FIGS. 8 to 10, the fixed pin was
broken after a maximum load of 2,100 kg was maintained for 1 minute
in Comparative Example 2, whereas the same maximum load was
maintained for 20 minutes or more, but the fixed pin was not broken
in Example 2, and the fixed pin was broken after the same maximum
load was maintained for 6 minutes in Comparative Example 3.
Meanwhile, even though the case is not included in Table 3, when
K.sub.N=2.7 and the temperature and time of the gas
nitrocarburizing step were 570.degree. C. and 720 minutes,
respectively, the pore layer fraction was 35%, and a result was at
a level equivalent to Example 2 in Table 3.
[0072] FIG. 11A is a photograph after evaluating seizure resistance
of Example 2, and FIG. 11B is a photograph after evaluating seizure
resistance of Comparative Example 3. As shown in FIGS. 11A and 11B,
it can be seen that abrasion and seizure do not occur in Example 2,
whereas abrasion and seizure occur in Comparative Example 3.
[0073] As demonstrated in Comparative Example 2, Example 2, and
Comparative Example 3, in order to improve abrasion resistance of
cast iron, a pore layer fraction of about 25% or greater may be
secured, but a pore layer fraction of less than 40%, or
particularly of about 35% or less may be secured.
[0074] According to various exemplary embodiments of the present
invention, the cast iron may be applied to a control finger, but is
not limited thereto, and parts requiring high strength while
requiring the durability as compared to the conventional cast iron
may be subjected to a complex oxy-nitriding heat treatment. Since
cast iron is already used in various parts of an automobile, such
as a diff case or a control body, a compound layer having a
thickness of about 15 .mu.m or greater may be formed on the surface
layer by subjecting spheroidized graphite cast iron at the FCD450
to 700 level to the complex oxy-nitriding heat treatment such as
the invention.
[0075] The present invention has been described in detail through
representative Examples, but it is to be understood by a person
with ordinary skill in the art to which the present invention
pertains that various modifications are possible in the
above-described Examples within the range not departing from the
scope of the present invention. Therefore, the scope of the present
invention should not be limited to the above-described Examples but
should be determined by not only the claims to be described below
but also all the changes or modified forms derived from the claims
and the equivalent concept thereof.
* * * * *