U.S. patent application number 16/697962 was filed with the patent office on 2020-06-04 for heat recovery system.
This patent application is currently assigned to Borgwarner Emissions Systems Spain, S.L.U.. The applicant listed for this patent is Borgwarner Emissions Systems Spain, S.L.U.. Invention is credited to Xoan Xose Hermida Dominguez, Marta Laguela Lopez, Manuel Lorenzo Gonzalez, Jorge Teniente Molinos, Ignacio Vidal Garcia.
Application Number | 20200173323 16/697962 |
Document ID | / |
Family ID | 65408853 |
Filed Date | 2020-06-04 |

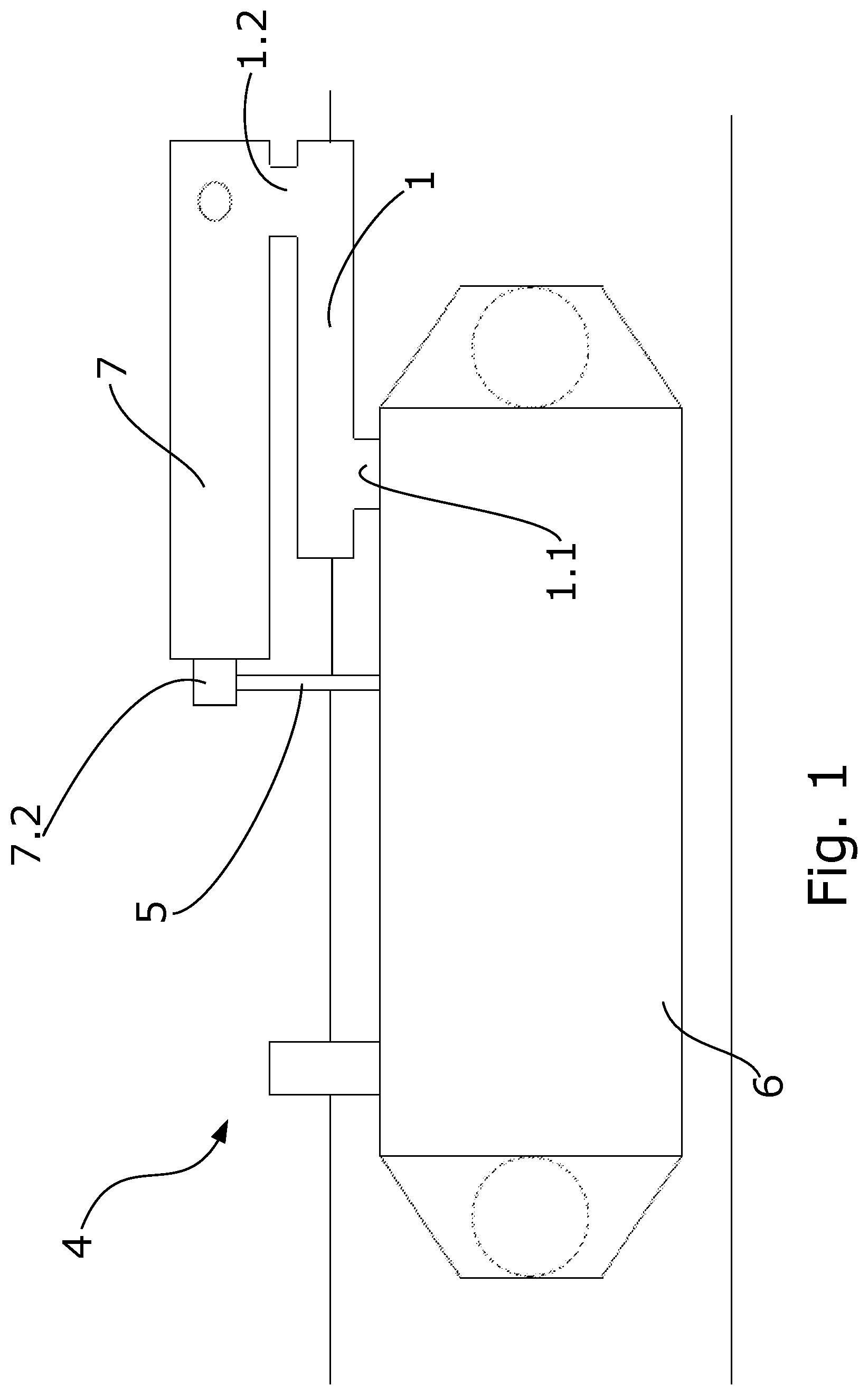

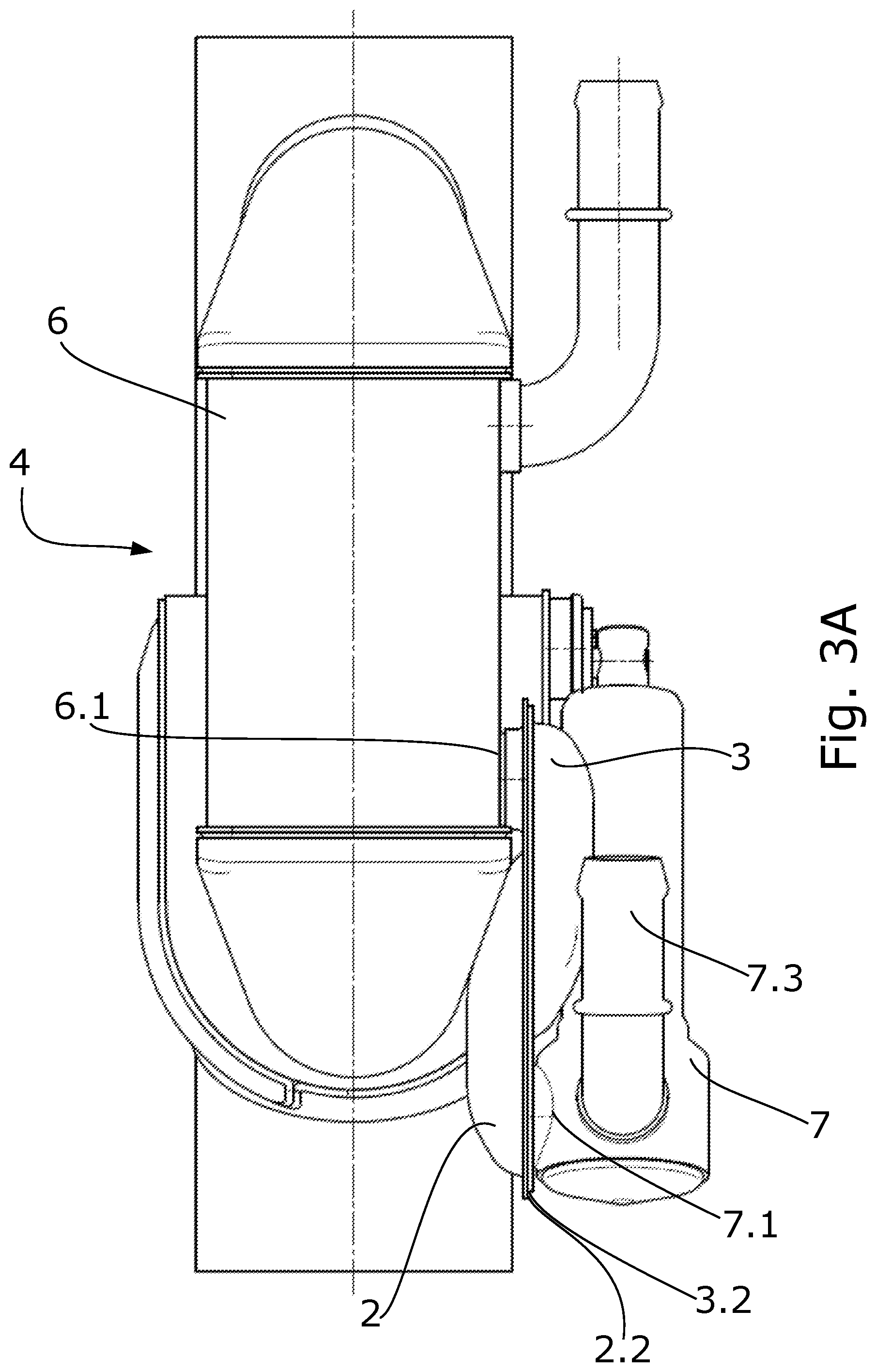
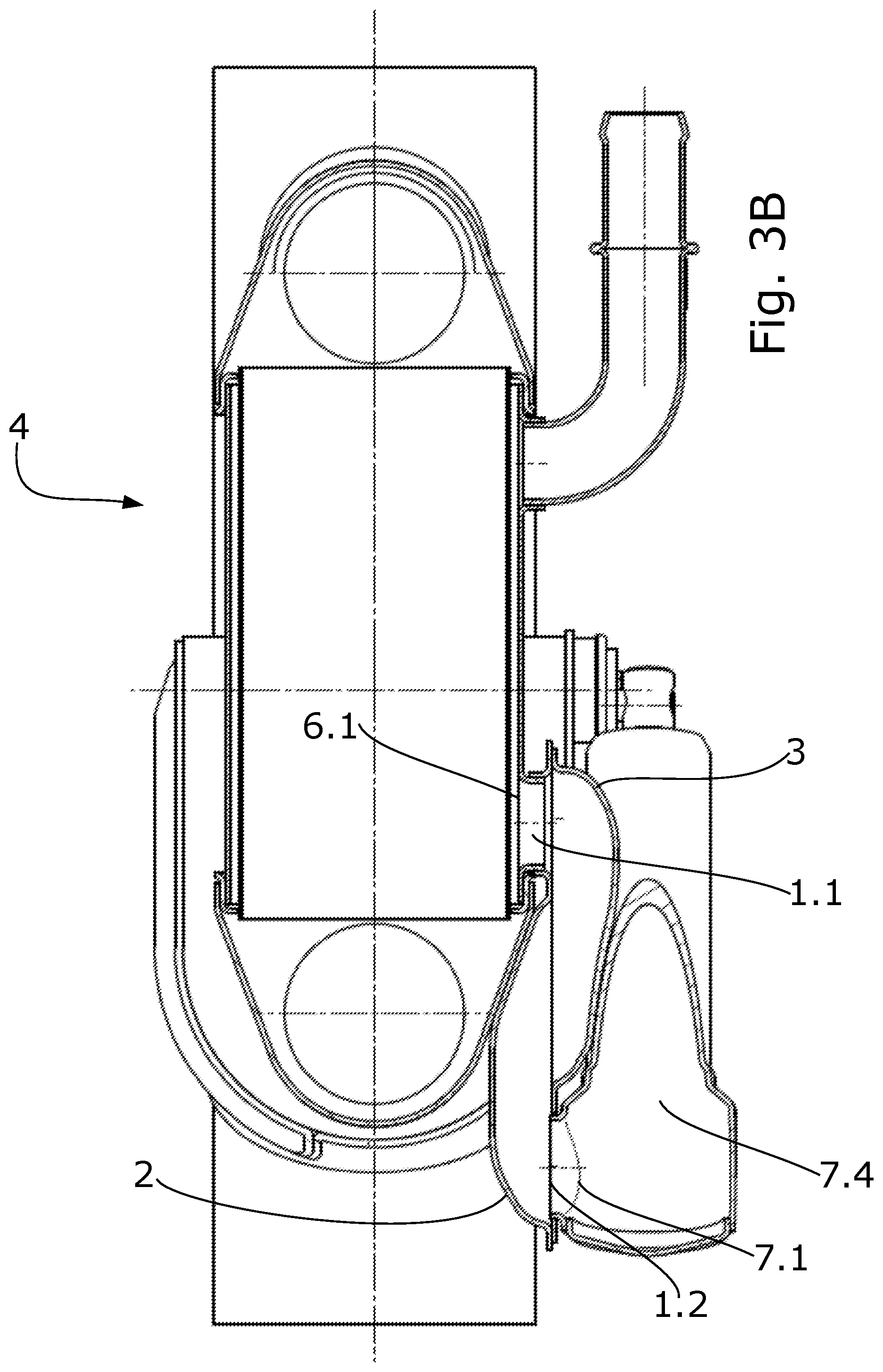
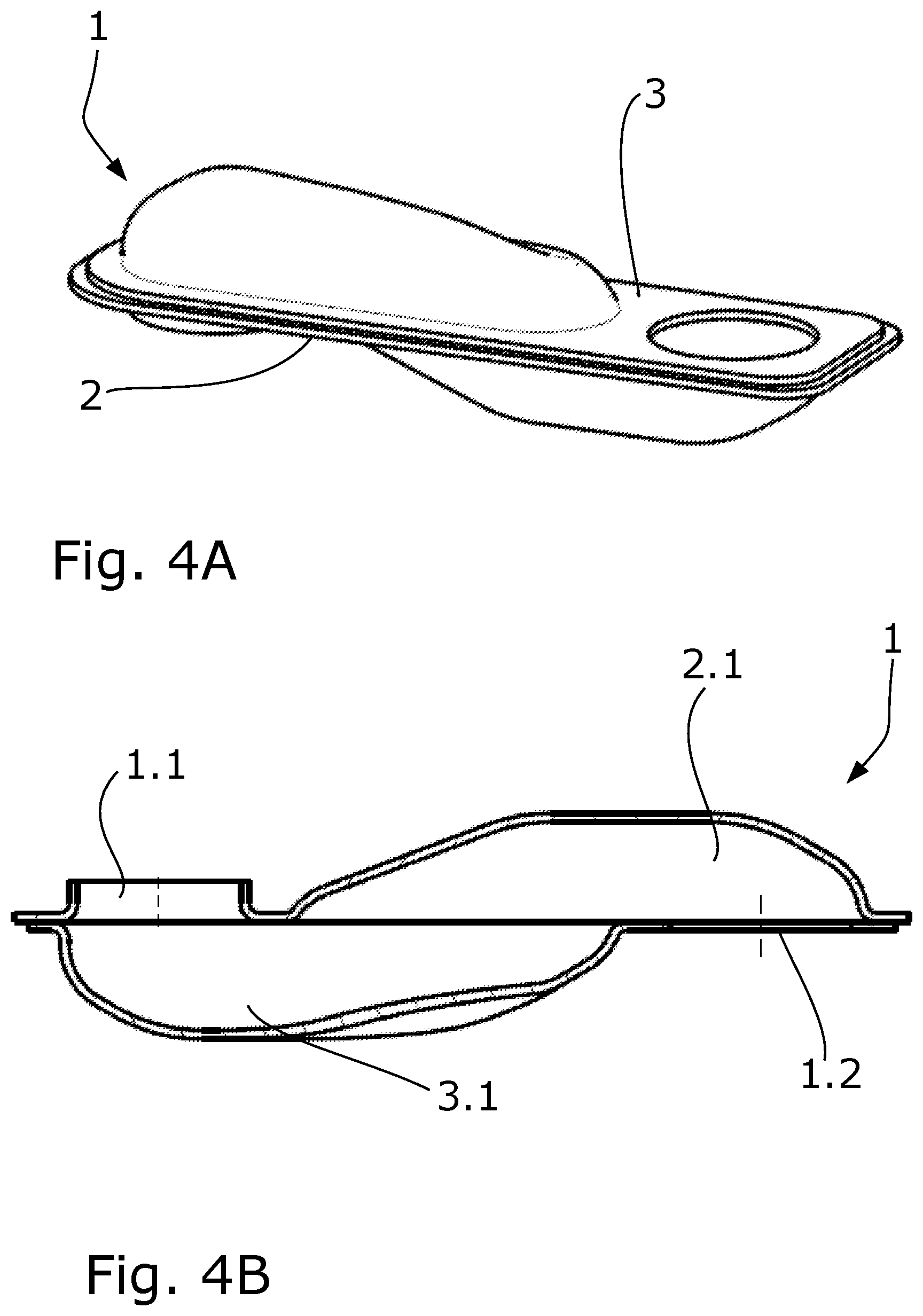

United States Patent
Application |
20200173323 |
Kind Code |
A1 |
Hermida Dominguez; Xoan Xose ;
et al. |
June 4, 2020 |
Heat Recovery System
Abstract
The present invention relates to a heat recovery system
comprising a device which allows the connection between the
elements of said system, such as a heat exchanger and an actuator
controlling a valve of the present system. Said actuator is in turn
configured such that its operation depends on the behavior of a
substance due to the action of the temperature of a fluid, for
example the liquid coolant used in the heat exchanger of the
system, which is arranged in an exhaust duct of an internal
combustion engine. Additionally, the invention also relates to a
method of assembly of a system having these features.
Inventors: |
Hermida Dominguez; Xoan Xose;
(Vigo, ES) ; Laguela Lopez; Marta; (Vigo, ES)
; Lorenzo Gonzalez; Manuel; (Vigo, ES) ; Vidal
Garcia; Ignacio; (Vigo, ES) ; Teniente Molinos;
Jorge; (Vigo, ES) |
|
Applicant: |
Name |
City |
State |
Country |
Type |
Borgwarner Emissions Systems Spain, S.L.U. |
Vigo |
|
ES |
|
|
Assignee: |
Borgwarner Emissions Systems Spain,
S.L.U.
Vigo
ES
|
Family ID: |
65408853 |
Appl. No.: |
16/697962 |
Filed: |
November 27, 2019 |
Current U.S.
Class: |
1/1 |
Current CPC
Class: |
F01N 2240/02 20130101;
F01N 13/18 20130101; F01N 2410/00 20130101; F01N 5/02 20130101;
F01N 13/1838 20130101; F01N 3/0205 20130101; F01N 13/08 20130101;
F01N 2390/00 20130101 |
International
Class: |
F01N 3/02 20060101
F01N003/02; F01N 13/08 20060101 F01N013/08; F01N 13/18 20060101
F01N013/18 |
Foreign Application Data
Date |
Code |
Application Number |
Nov 30, 2018 |
EP |
18382877.1 |
Claims
1. A system (4) comprising: an exhaust duct (8), a heat exchanger
(6) for the exchange of heat between a hot gas coming from the
exhaust duct (8) and a liquid coolant, comprising at least one
fluid connection (6.1) for entry/exit of the liquid coolant, a
valve actuated through a shaft (5) for opening or closing the
passage of hot gas through the heat exchanger (6), an actuator (7)
comprising a drive rod (7.2) actuated by a substance the specific
volume of which changes in the event of changes in temperature, the
actuator (7) further comprising: an inlet/outlet port (7.1) for the
entry/exit of a fluid; an internal chamber (7.4) in fluid
communication with the inlet/outlet port (7.1) and in thermal
communication with the substance such that in operating mode, the
substance is in thermal communication with the fluid entering the
internal chamber (7.4) through the inlet/outlet port (7.1); a metal
fluid coupling device (1), attached at a first fluid inlet/outlet
(1.1) by means of welding to the at least one fluid connection
(6.1) of the heat exchanger (6) and at a second fluid outlet/inlet
(1.2) to the inlet/outlet port (7.1) of the actuator (7) such that
a fluid connection is established between the inlet/outlet port
(7.1) of the actuator (7) and the fluid connection (6.1) of the
heat exchanger (6) through the fluid coupling device (1), and
wherein the drive rod (7.2) of the actuator (7) is connected with
the shaft (5) of the valve for the actuation thereof according to
the temperature of the liquid coolant.
2. The system (4) according to claim 1, wherein the metallic fluid
coupling device (1) is made of stamped metal sheet.
3. The system (4) according to claim 1, wherein the metallic fluid
coupling device (1) is a structural element which supports the
actuator (7).
4. The system (4) according to claim 1, wherein the metallic fluid
coupling device (1) comprises a plurality of parts.
5. The system (4) according to claim 4, wherein the metallic fluid
coupling device (1) comprises: a first part (2) comprising: a first
support region (2.2); a first inner space (2.1) with a first
opening (2.1.1) wherein the first opening (2.1.1) is peripherally
demarcated by the first support region (2.2); the first fluid
inlet/outlet (1.1) of the metallic fluid coupling device (1); a
second part (3) comprising: a second support region (3.2); a second
inner space (3.1) with a second opening (3.1.1) wherein the second
opening (3.1.1) is peripherally demarcated by the second support
region (3.2); the second fluid outlet/inlet (1.2) of the metallic
fluid coupling device (1); wherein: the first support region (2.2)
and second support region (3.2) are attached, the first fluid
inlet/outlet (1.1) is in fluid communication with the second inner
space (3.1), the second fluid outlet/inlet (1.2) is in fluid
communication with the first inner space (2.1), and the first inner
space (2.1) and second inner space (3.1) are in fluid communication
through the first opening (2.1.1) and second opening (3.1.1).
6. The system (4) according to claim 5, wherein the attachment of
the first support region (2.2) and second support region (3.2) is
configured as follows: before the attachment, the first support
region (2.2) and second support region (3.2) establish a sliding
support with one support region (2.2) on top of the other support
region (3.2), such that the first inner space (2.1) is in fluid
communication with the second inner space (3.1); and after the
attachment between the first support region (2.2) and second
support region (3.2), the attachment establishes the leak-tight
closure of the space generated by the attachment of the first inner
space (2.1) and second inner space (2.1) and the fluid
communication between the first fluid inlet/outlet (1.1) and second
fluid outlet/inlet (1.2).
7. The system (4) according to claim 5, wherein the first support
region (2.2) and second support region (3.2) of the metallic
coupling device (1) are flat.
8. The system (4) according to claim 5, wherein the first inner
space (2.1) of the first part (2) is concave, the second inner
space (3.2) of the second part (3) is concave, and after the
attachment of the first support region (2.2) and second support
region (3.2) of the metallic fluid coupling device (1), the
concavity of the first inner space (2.1) is opposite the concavity
of the second inner space (3.2).
9. The system (4) according to claim 5, wherein the attachment
between the first part (2) and second part (3) of the metallic
fluid coupling device (1) is made by welding.
10. The system (4) according to claim 5, wherein the space
generated by the attachment of the first inner space (2.1) and
second inner space (3.1) for fluid communication between the first
fluid inlet/outlet (1.1) and second fluid outlet/inlet (1.2) of the
metallic fluid coupling device (1) is configured according to a
zigzag-type conduit.
11. The system (4) according to claim 5, wherein the inlet/outlet
port (7.1) of the actuator (7) is fluidically connected with the
second fluid outlet/inlet (1.2) of the second part (3) of the
metallic fluid coupling device (1), and wherein the first fluid
inlet/outlet (1.1) of the first part (2) of the metallic fluid
coupling device (1) is furthermore fluidically connected with the
fluid connection (6.1) of the heat exchanger (6).
12. A method of assembly of a system (4) according to claim 1,
which method comprises carrying out the following steps a) to d) in
any order: a) building the heat exchanger (6) with the fluid
connection (6.1) for the liquid coolant, the exhaust duct (8), and
the valve actuated through a shaft (5) for opening or closing the
passage of hot gas; b) building the actuator (7) with the drive rod
(7.2) and the inlet/outlet port (7.1); c) attaching the fluid
connection (6.1) of the heat exchanger (6) with the metallic fluid
coupling device (1) by means of welding; d) attaching the
inlet/outlet port (7.1) of the actuator (7) with the fluid coupling
device (1) by means of welding.
13. The method of assembly according to claim 12, wherein step c)
comprises attaching the fluid connection (6.1) of the heat
exchanger (6) with the second part (3) of the metallic coupling
device (1) by means of welding, and step d) comprises attaching the
inlet/outlet port (7.1) of the actuator (7) with the first part (2)
of the metallic coupling device (1) by means of welding, and
wherein the following steps are carried out sequentially after step
d): e) placing the assembly formed by the heat exchanger (6) and
the second part (3) with respect to the second assembly formed by
the actuator (7) and the first part (2) such that the first support
region (2.2) of the first part (2) and the second support region
(3.2) of the second part (3) are in sliding contact, f) attaching
the first part (2) of the metallic fluid coupling device (1) and
the second part (3) of the device.
14. The method of assembly according to claim 12, wherein the
attachments are established by means of brazing.
Description
OBJECT OF THE INVENTION
[0001] The present invention relates to a heat recovery system
comprising a device which allows the connection between the
elements of said system, such as a heat exchanger and an actuator
controlling a valve of the present system. Said actuator is in turn
configured such that its operation depends on the behavior of a
substance due to the action of the temperature of a fluid, for
example the liquid coolant used in the heat exchanger of the
system, wherein said heat exchanger is arranged in an exhaust duct
of an internal combustion engine.
[0002] Additionally, the invention also relates to a method of
assembly of a system having these features.
BACKGROUND OF THE INVENTION
[0003] One of the fields of the art that has been subjected to the
most intensive development is the field of heat recovery systems in
vehicles with an internal combustion engine.
[0004] In particular, said heat recovery systems are configured
with the attachment of different elements, such as a heat
exchanger, an exhaust duct, and a valve, allowing the heat recovery
device, depending on the position of said valve, to heat the
coolant of the internal combustion engine, or not, by the action of
the exhaust gas. An actuator, also comprised in the heat recovery
system, allows control over the valve.
[0005] The attachments between different elements of the system,
particularly between the heat exchanger and the actuator, are
established today by means of connections involving additional
parts, for example flexible tubing, metal tubing, or independent
manifolds, which do allow the fluid attachment between elements but
in turn entail complex connections.
[0006] These complex attachments entail various drawbacks, such as
the presence of additional parts occupying a larger space, the
possibility of leakage in the connections between parts, and the
risk of requiring higher assembly tolerances that do not allow
suitable fitting between parts.
[0007] The present invention solves these problems by proposing a
system provided with a coupling device which allows a more compact
and robust attachment of the elements of said heat recovery system,
thereby preventing possible fluid leakage and providing better
assembly tolerances.
[0008] Additionally, the method of assembly also object of the
present invention allows obtaining a heat recovery system having
these features.
DESCRIPTION OF THE INVENTION
[0009] A first aspect of the invention relates to a heat recovery
system, comprising: [0010] an exhaust duct, [0011] a heat exchanger
for the exchange of heat between a hot gas coming from the exhaust
duct and a liquid coolant, comprising at least one fluid connection
for the entry/exit of the liquid coolant, [0012] a valve actuated
through a shaft for opening or closing the passage of hot gas
through the heat exchanger, [0013] an actuator comprising a drive
rod actuated by a substance the specific volume of which changes in
the event of changes in temperature, the actuator further
comprising: [0014] an inlet/outlet port for the entry/exit of a
fluid; [0015] an internal chamber in fluid communication with the
inlet/outlet port and in thermal communication with the substance
such that in operating mode, the substance is in thermal
communication with the fluid entering the internal chamber through
the inlet/outlet port;
[0016] One of the main elements of the present heat recovery system
is a heat exchanger, whereby the exhaust gas is cooled upon the
exchange of heat with the fluid coolant, said coolant in turn
therefore being heated, as well as an exhaust duct through which
all of the exhaust gas from the internal combustion engine flows in
the event that it is not cooled. The hot gas comes from the engine
and flows through the exhaust duct, the additional passage thereof
through the inside of the heat exchanger being possible for cooling
thereof.
[0017] The heat recovery system in turn comprises a valve, wherein
the flap controlled by the shaft of said valve allows, or not,
depending on its arrangement, the passage of the exhaust gas
through the heat exchanger, which allows the cooling, or not, of
said exhaust gas, and therefore the corresponding heating of the
coolant.
[0018] This valve is controlled by the actuator which, in this
case, is operated based on the behavior with respect to the
temperature of a substance contained in said actuator.
[0019] The specific volume of said substance changes as a response
to the temperature of a fluid with which it is in contact, said
fluid being the liquid coolant circulating through the heat
exchanger.
[0020] The liquid coolant can, interchangeably, exchange heat first
with the substance in the internal chamber located inside the
actuator, and then with the exhaust gas inside the heat exchanger,
or vice versa.
[0021] The system according to the first aspect of the invention
additionally comprises: [0022] a metallic fluid coupling device,
attached at a first fluid inlet/outlet by means of welding to the
at least one fluid connection of the heat exchanger and at a second
fluid outlet/inlet to the inlet/outlet port of the actuator such
that a fluid connection is established between the inlet/outlet
port of the actuator and the fluid connection of the heat exchanger
through the fluid coupling device, and wherein the drive rod of the
actuator is connected with the shaft of the valve for the actuation
thereof according to the temperature of the liquid coolant.
[0023] The present metallic fluid coupling device is attached to
both the heat exchanger and the actuator, such that the liquid
coolant is capable of flowing through said metallic fluid coupling
device from the heat exchanger to the actuator or vice versa.
[0024] Advantageously, the attachment of the heat exchanger and the
actuator through the metallic fluid coupling device allows said
actuator to fix its position with respect to the exchanger.
[0025] In a particular embodiment, the metallic fluid coupling
device acts like a structural element and allows supporting the
actuator such that the need to incorporate additional parts, for
example brackets, which hold the actuator in its position with
respect to the heat exchanger, is prevented.
[0026] An attachment by means of the metallic fluid coupling device
thereby allows reducing the parts that were previously required,
thereby resulting in a more lightweight and more compact
system.
[0027] Additionally, since the fluid coupling device is a metallic
device, it allows preventing any risk of deterioration due to the
action of high temperatures and heat, unlike the fluid coupling
devices of the state of the art, which usually consist of flexible
rubber tubing.
[0028] In a particular embodiment, the metallic fluid coupling
device is manufactured from stamped metal sheet, preferably punched
and stamped metal sheet.
[0029] In a particular embodiment, said metallic fluid coupling
device is configured by a plurality of parts, which allows the
fitting between said parts, as well as with the actuator and the
heat exchanger, to be even more precise.
[0030] In a particular embodiment, wherein the metallic fluid
coupling device is configured by a plurality of parts, specifically
a configuration of two different parts, this device comprises:
[0031] a first part comprising: [0032] a first support region;
[0033] a first inner space with a first opening wherein the first
opening is peripherally demarcated by the first support region;
[0034] the first fluid inlet/outlet of the metallic fluid coupling
device; [0035] a second part comprising: [0036] a second support
region; [0037] a second inner space with a second opening wherein
the second opening is peripherally demarcated by the second support
region; [0038] the second fluid outlet/inlet of the metallic fluid
coupling device; wherein: [0039] the first support region and
second support region are attached [0040] the first fluid
inlet/outlet is in fluid communication with the second inner space,
[0041] the second fluid outlet/inlet is in fluid communication with
the first inner space, and [0042] the first inner space and second
inner space are in fluid communication through the first and second
openings.
[0043] This particular embodiment alone constitutes a second aspect
of the invention which is described in the embodiments as a
specific solution applied to the first inventive aspect.
[0044] The present configuration allows a direct connection of the
exchanger and actuator, and therefore a closed circuit for the
coolant, through the attachment of the first part and second part
by means of their support regions and the overlapping of the first
opening and second opening.
[0045] These first and second support regions are, preferably, flat
regions which allow their attachment to occur through a common
plane defining a contact surface. In turn, the first opening and
second opening are areas limiting the first inner space and second
inner space, respectively. Said limitation occurs on the plane of
each of the support regions, since each of the openings is defined
and limited on the plane of each corresponding support region.
[0046] Additionally, in a particular example of the second
inventive aspect, the attachment of the first support region and
second support region is configured as follows: [0047] before the
attachment, the first support region and second support region
establish a sliding support with one support region on top of the
other support region, such that the first inner space is in fluid
communication with the second inner space; and [0048] after the
attachment between the first support region and second support
region, the attachment establishes the leak-tight closure of the
space generated by the attachment of the first inner space and
second inner space and the fluid communication between the first
fluid inlet/outlet and second fluid outlet/inlet.
[0049] Said sliding support allows the absorption of the necessary
tolerances relating to the manufacture and assembly of the present
system. After the attachment of said regions, the support generated
between both support regions is fixed, the closure being leak-tight
and therefore preventing any type of coolant leakage as it passes
through the metallic fluid coupling device between the actuator and
heat exchanger.
[0050] Preferably, the metallic fluid coupling device comprises,
between the first support region and second support region, a
closed perimeter contact area with an internal passage through
which the first inner space communicates with the second inner
space.
[0051] Said perimeter contact area is contained on the common plane
generated from the attachment of both support regions, whereas the
internal passage is defined by the overlap existing between the
first opening and second opening contained in each of the support
regions and peripherally limited by same.
[0052] Preferably, the attachment between the first part and second
part of the metallic fluid coupling device through the first and
second support regions is established by welding.
[0053] In a particular example, the first inner space of the first
part is concave, the second inner space of the second part is
concave, and after the attachment of the first support region and
second support region of the metallic fluid coupling device, the
concavity of the first inner space is opposite to the concavity of
the second inner space.
[0054] Said concave inner spaces allow defining a path for the
fluid coolant upon the passage thereof through the metallic fluid
coupling device, said device thereby being more compact.
[0055] Preferably, the space generated by the attachment of the
first inner space and second inner space for fluid communication
between the openings which allow the entry and exit of the coolant
in the metallic fluid coupling device is configured according to a
zigzag-type conduit, preferably a tubular zigzag-type conduit,
which allows reducing the dimensions of the metallic fluid coupling
device.
[0056] In a particular embodiment, the inlet/outlet port of the
actuator is fluidically connected with the second fluid
outlet/inlet of the second part of the metallic fluid coupling
device, and wherein the first fluid inlet/outlet of the first part
of the metallic fluid coupling device is furthermore fluidically
connected with the fluid connection of the heat exchanger.
[0057] Additionally, the actuator has a second outlet/inlet port
connected to the cooling circuit of the internal combustion
engine.
[0058] Each of the plates forming the metallic fluid coupling
devices is thereby connected with one of the elements of the
system, thus forming the circuit through which the coolant
circulates.
[0059] Therefore, the second part of the device allows supporting
the actuator, with the weight being transmitted through the first
part of the device, connected with the heat exchanger, which is
what supports the remaining parts of the system.
[0060] Preferably, the mentioned connections are established by
means of welding, more preferably by brazing.
[0061] In a particular embodiment, the thermal substance of the
actuator is wax, and the rod is in a first position when the
temperature of the fluid accessing its interior through its inlet
port is at a temperature below a pre-established value, and extends
to a second position when the temperature of the fluid accessing
its interior through its inlet port exceeds said pre-established
value.
[0062] A third inventive aspect relates to a method of assembly of
a system according to the first inventive aspect, which method
comprises carrying out the following steps a) to d) in any order:
[0063] a) building the heat exchanger with the fluid connection for
the liquid coolant, the exhaust duct, and the valve actuated
through a shaft for opening or closing the passage of hot gas;
[0064] b) building the actuator with the drive rod and the
inlet/outlet port; [0065] c) attaching the fluid connection of the
heat exchanger with the metallic fluid coupling device by means of
welding; [0066] d) attaching the inlet/outlet port of the actuator
with the fluid coupling device by means of welding.
[0067] Advantageously, the present method of assembly allows
obtaining a compact system, wherein a lower number of parts is
needed to form said heat recovery system, which allows said
recovery device to occupy less space.
[0068] For the particular embodiment in which the metallic fluid
coupling device is configured from a first part and second part,
the method of assembly is modified as follows: [0069] step c)
comprises attaching the fluid connection of the heat exchanger with
the second part of the metallic coupling device by means of
welding, and [0070] step d) comprises attaching the inlet/outlet
port of the actuator with the first part of the metallic coupling
device by means of welding, and [0071] wherein the following steps
are carried out sequentially after step d): [0072] e) placing the
assembly formed by the heat exchanger and the second part with
respect to the second assembly formed by the actuator and the first
part such that the first support region of the first part and the
second support region of the second part are in sliding contact,
and [0073] f) attaching the first part of the metallic fluid
coupling device and the second part of the device.
[0074] Particularly, the movement between the first position of the
rod and the second position of the rod of the actuator establishes
the opening/closing of the valve.
[0075] This advantageously enables the additional attachment
between both parts of the metallic fluid coupling device to
maintain the leak-tightness of said device, while at the same time
it enables greater flexibility for absorbing tolerances in the
assembly of the system.
[0076] Preferably, each of the mentioned attachments is established
by means of brazing.
DESCRIPTION OF THE DRAWINGS
[0077] The foregoing and other features and advantages of the
invention will become more apparent based on the following detailed
description of a preferred embodiment given only by way of
illustrative and non-limiting example in reference to the attached
drawings.
[0078] FIG. 1 shows a diagram of a particular embodiment of the
system according to the first inventive aspect.
[0079] FIG. 2 shows a perspective view of a system according to the
second inventive aspect, according to a particular embodiment
thereof.
[0080] FIGS. 3A/3B show a front view and section view,
respectively, of a system according to the same particular
embodiment as FIG. 2.
[0081] FIGS. 4A-4B show a perspective view as well as a section
view of a particular example of a metallic fluid coupling
device.
[0082] FIGS. 4C-4D show a perspective view of each part of the
metallic fluid coupling device of FIGS. 4A and 4B.
DETAILED DESCRIPTION OF THE INVENTION
[0083] FIG. 1 shows a diagram in which a particular example of a
system (4) like the one of the first inventive aspect of the
present application is defined.
[0084] Said system (4) is formed by a tube heat exchanger (6)
through which tubes there circulates an exhaust gas coming from the
exhaust duct (8), and therefore from the internal combustion engine
of the vehicle, as well as an actuator (7) which, by means of a rod
(7.2), allows the operation of the shaft (5) of a valve not shown
in the present figure. This operation involves the change in
position of the flap of the valve, allowing passage of the exhaust
gas through the heat exchanger (6) in a first position, such that
this may heat up the coolant circulating outside the tubes (while
at the same time it is cooled by said coolant), or allowing passage
of all of the exhaust gas through the exhaust duct or bypass duct
(8) in a second position, thereby preventing the heating of the
coolant by said exhaust gas as the latter is expelled directly into
the atmosphere.
[0085] The attachment between the actuator (7) and the heat
exchanger (6) is established through an intermediate element, a
metallic fluid coupling device (1), which allows supporting said
actuator (7) on the exchanger (6).
[0086] In particular, a first fluid inlet/outlet (1.1) of the
metallic fluid coupling device (1) is attached to the fluid
connection through which the coolant enters/exit the heat exchanger
(6), whereas a second fluid outlet/inlet (1.2) of the metallic
fluid coupling device (1) is attached to the inlet/outlet port
(7.1) through which said coolant enters/exits the actuator (7).
[0087] A closed circuit is thereby formed for the liquid coolant
circuit which, in this case, goes from the actuator (7), where it
causes the operation of the rod (7.2) by the action of its
temperature on the substance of the actuator (7), through the
metallic fluid coupling device (1), to the heat exchanger (6), in
order to thereby cool the exhaust gas going through the tubes of
said exchanger (6).
[0088] In an additional particular example, this circuit could be
configured in the opposite manner, the liquid coolant thereby
flowing from the heat exchanger (6) to the actuator (7).
[0089] FIG. 4A shows a perspective view of a particular example of
a metallic fluid coupling device (1), particularly formed by a
first part (2) and a second part (3) which are attached to one
another through a flat surface of each of the two parts (2, 3),
thereby forming an internal path by means of concave cavities in
each of these parts (2, 3) which allow the liquid coolant to pass
therethrough.
[0090] FIG. 4B shows a section of this same metallic fluid coupling
device (1), wherein the parts (2, 3) comprise a first inner space
(2.1, 3.1), respectively, or internal cavity through which the
coolant circulates as it passes through the device (1).
[0091] The liquid coolant accesses the metallic fluid coupling
device (1) through the second fluid inlet (1.2) of the device (1)
from the actuator (7), and it exits said device (1) towards the
exchanger (6) through the first fluid outlet (1.1). In other words,
access of the coolant to the device (1) occurs through the second
fluid inlet (1.2) located in the second part (3), in fluid
connection with the actuator (7), and its access from the device
(1) to the exchanger (6) occurs through the first fluid outlet
(1.1) located in the first part (2) forming the device (1).
[0092] As shown in FIGS. 4C and 4D, which show a perspective view
of each of the parts (2, 3) forming the device (1), each part (2,
3) has a flat support region (2.2, 3.2), respectively. Said
attachment of parts (2, 3) is shown in FIGS. 4A and 4B, being
welded to one another by means of brazing to achieve closure of the
device (1), thereby preventing leakage of the coolant as it passes
through said device (1).
[0093] Additionally, FIG. 4C shows the first inner space (2.1) of
the first part (2), which is demarcated by the first opening
(2.1.1).
[0094] The first fluid inlet/outlet (1.1) is, in turn, a punched
opening on the first part (2).
[0095] The first support region (2.2) peripherally demarcates both
the first fluid inlet/outlet (1.1) and the first opening
(2.1.1).
[0096] Similarly, FIG. 4D shows the second inner space (3.1) of the
second part (3), which is demarcated by the second opening
(3.1.1).
[0097] The second fluid outlet/inlet (1.2) is, in turn, a punched
opening on the second part (3).
[0098] The second support region (3.2) peripherally demarcates both
the second fluid outlet/inlet (1.2) and the second opening
(3.1.1).
[0099] FIGS. 2, 3A, and 3B show perspective, front, and section
views, respectively, of an already assembled complete heat recovery
system (4).
[0100] In that sense, a tube heat exchanger (6) as well as the
adjacent exhaust duct (8) through which the exhaust gas circulates,
following the path demarcated by the valve comprised in the system
(4), can be seen in said drawings.
[0101] An actuator (7) is arranged on the exchanger (6), such that
it allows controlling the shaft (5) of the valve which offers
access of the exhaust gas to the exchanger (6) itself at all
times.
[0102] In this particular example, the actuator (7) is a wax
actuator, this wax being a substance contained in the internal
chamber (7.4) of the actuator (7) which, by means of reacting to
the temperature upon contact with the coolant, operates the rod
(7.2) on the shaft (5) of the valve.
[0103] The fluid connection which allows the passage of the coolant
from the exchanger (6) to the actuator (7) is established through
the metallic fluid coupling device (1) configured from two parts
(2, 3) attached by respective support regions (2.2, 3.2), as can be
seen in FIG. 3A.
[0104] As shown in FIG. 3B, the heat exchanger (6) has a fluid
connection (6.1) which allows the passage of the fluid coolant, in
this case coming from the actuator (7). In order to allow access of
said fluid coolant, the actuator (7) has an outlet port (7.1), in
connection with the metallic fluid coupling device (1), and in
particular with the second part (3) of said device (1), which
allows the fluid coolant to flow from the actuator (7) to the
device (1), and from the latter to the exchanger (6) through the
fluid connection (6.1).
[0105] As can be seen in FIG. 3B, the outlet port (7.1) is
therefore in fluid connection with the second fluid inlet/outlet
(1.2) of the device (1), whereas the fluid connection (6.1) is
fluidically connected with the first fluid inlet/outlet (1.1) of
the device (1).
[0106] FIG. 3A shows a spigot (7.3) as part of the actuator (7)
from which the liquid coolant comes, said spigot (7.3) being
fluidically connected with the cooling circuit of the engine (not
shown).
* * * * *