U.S. patent application number 16/615296 was filed with the patent office on 2020-05-21 for improved system for additive manufacturing.
The applicant listed for this patent is STRUCTO PTE LTD. Invention is credited to Kah Fai Chin, Siu Hon Lam, Devansh Sharma, Boyle Suwono, Hubertus Theodorus Petrus Van Esbroek.
Application Number | 20200156317 16/615296 |
Document ID | / |
Family ID | 59220736 |
Filed Date | 2020-05-21 |
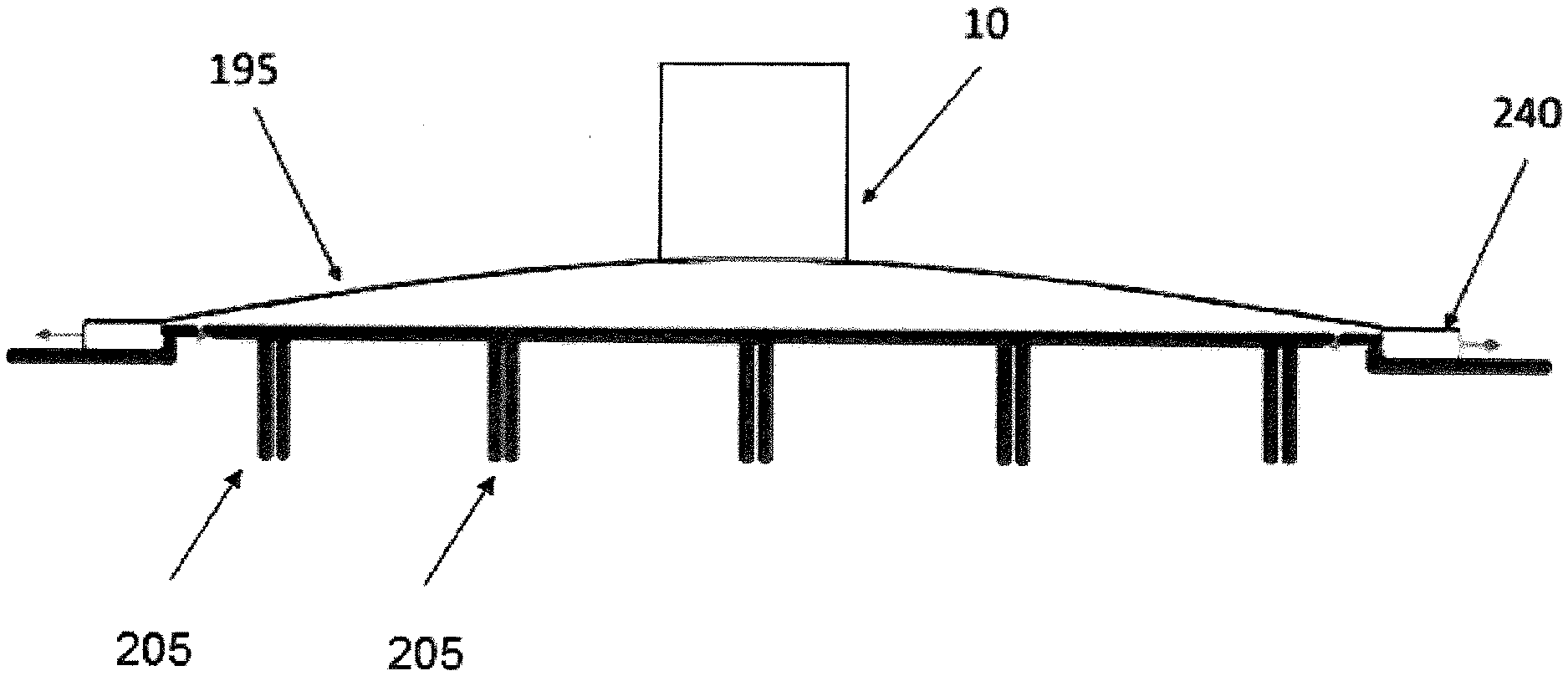
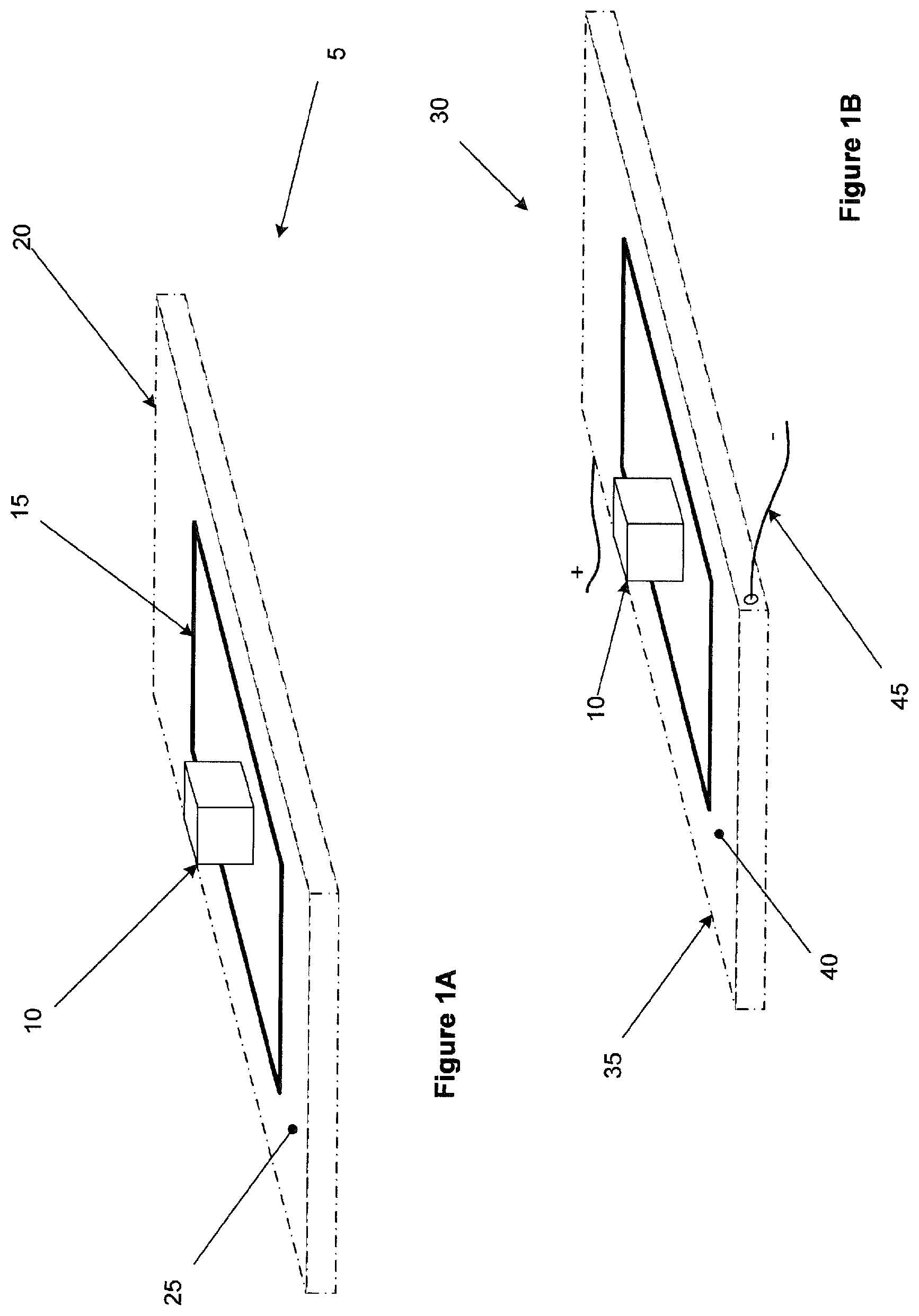



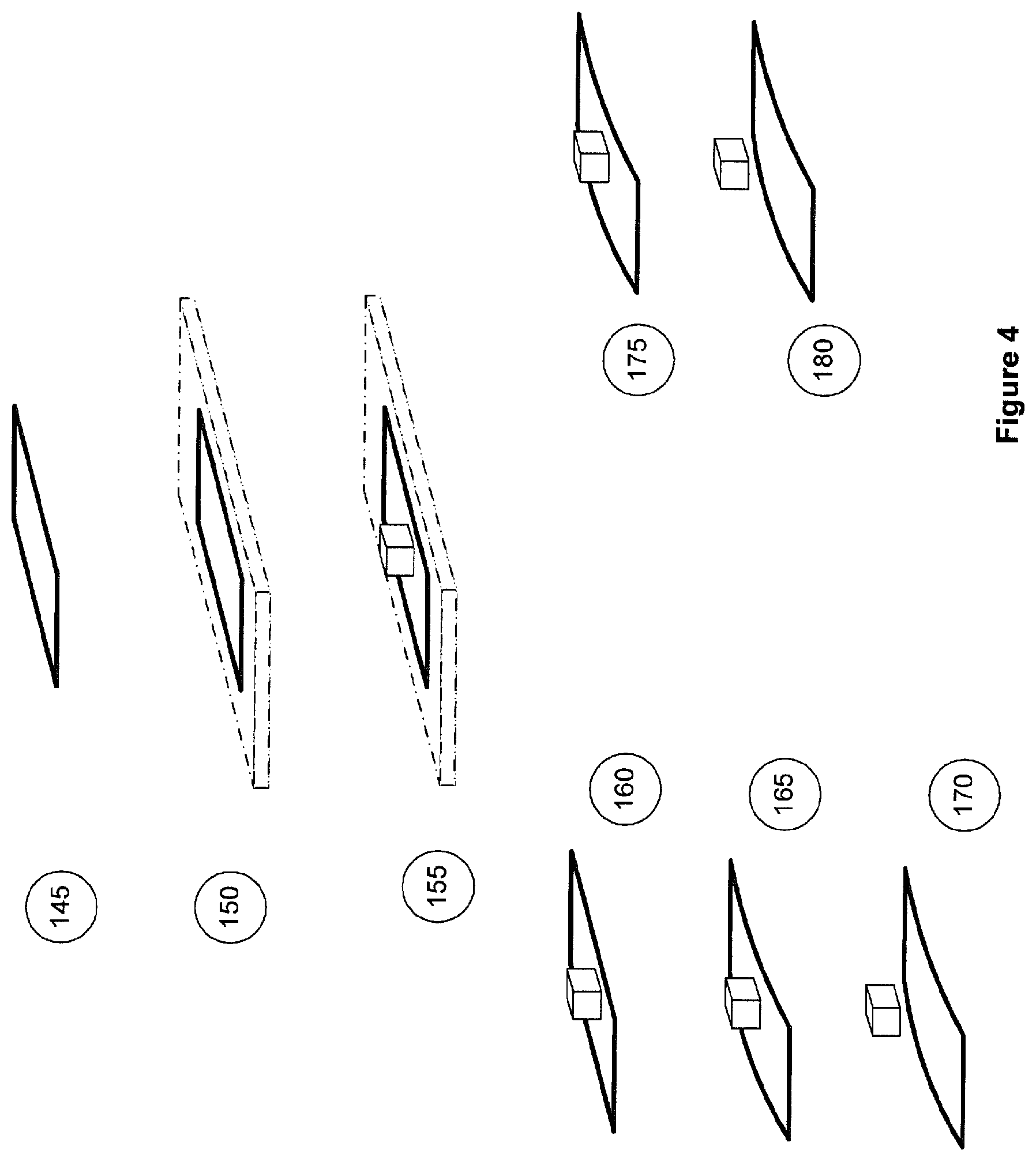

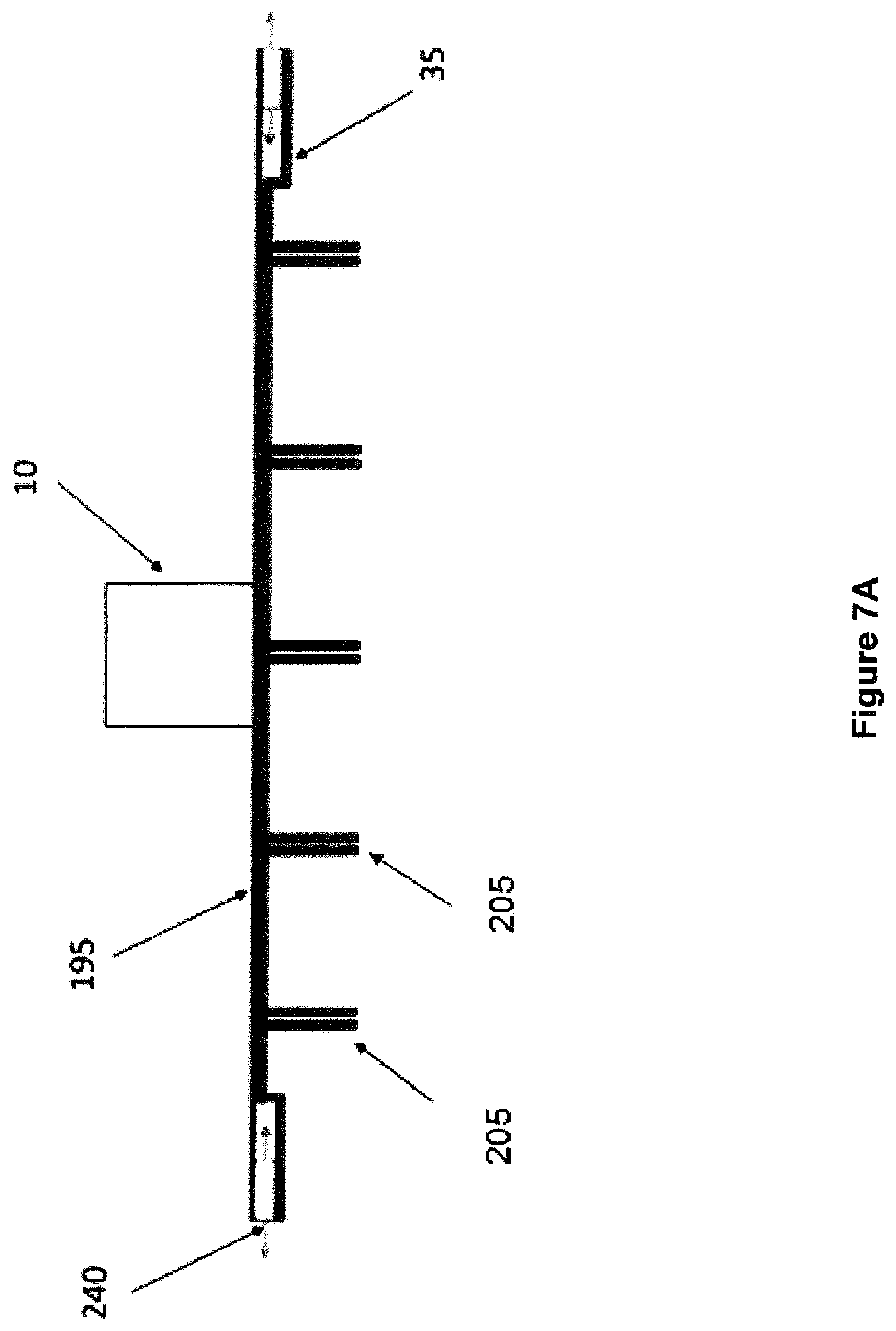
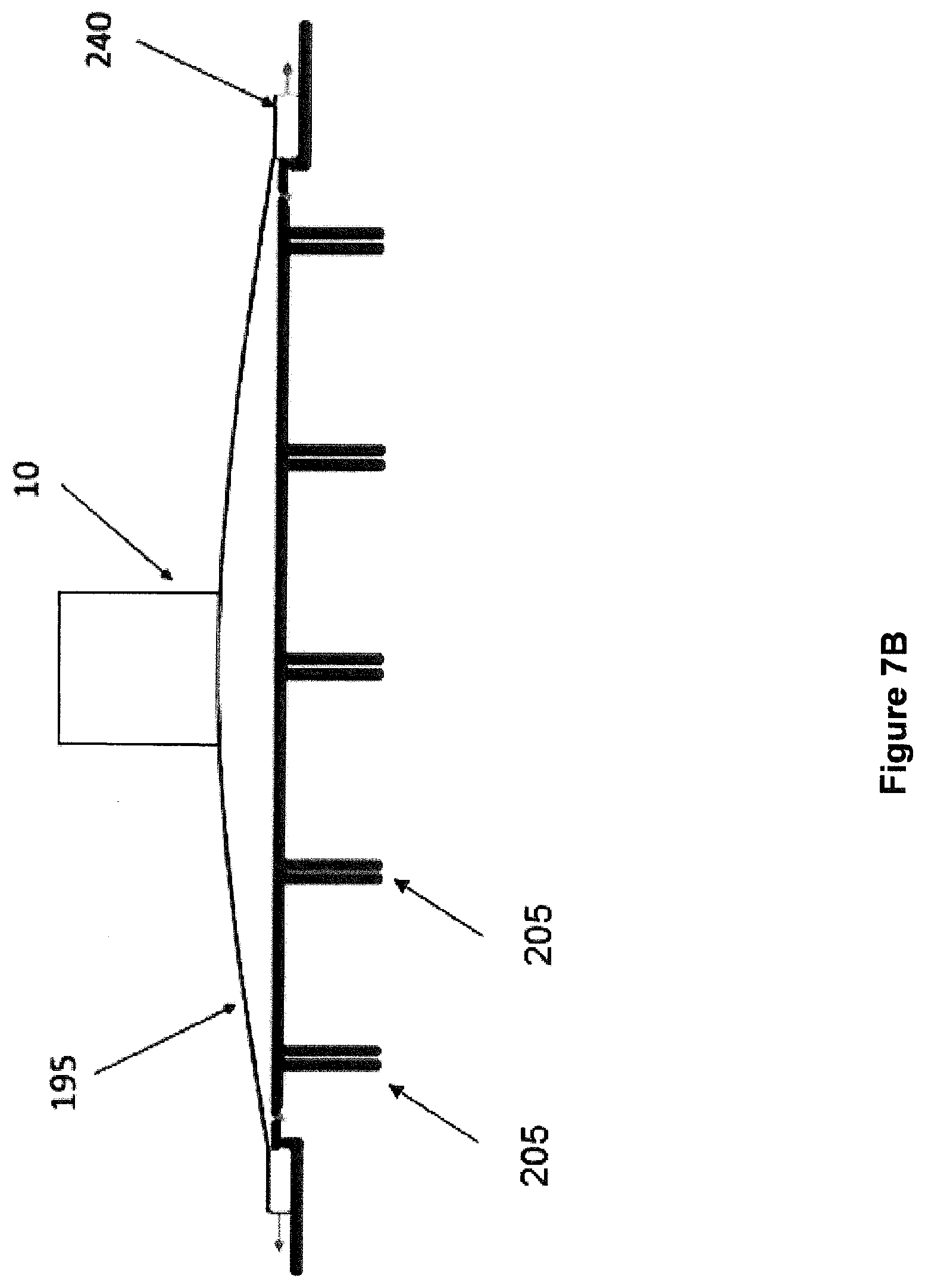
United States Patent
Application |
20200156317 |
Kind Code |
A1 |
Van Esbroek; Hubertus Theodorus
Petrus ; et al. |
May 21, 2020 |
Improved System for Additive Manufacturing
Abstract
An additive manufacturing device arranged to produce a part,
comprising: a printer bed; a platform engaged to said printer bed,
said platform arranged to receive the part on a surface of said
platform; wherein said platform is arranged to at least partially
disengage from said printer bed.
Inventors: |
Van Esbroek; Hubertus Theodorus
Petrus; (Singapore, SG) ; Suwono; Boyle;
(Singapore, SG) ; Chin; Kah Fai; (Singapore,
SG) ; Sharma; Devansh; (Singapore, SG) ; Lam;
Siu Hon; (Singapore, SG) |
|
Applicant: |
Name |
City |
State |
Country |
Type |
STRUCTO PTE LTD |
Singapore |
|
SG |
|
|
Family ID: |
59220736 |
Appl. No.: |
16/615296 |
Filed: |
May 22, 2018 |
PCT Filed: |
May 22, 2018 |
PCT NO: |
PCT/SG2018/050246 |
371 Date: |
November 20, 2019 |
Current U.S.
Class: |
1/1 |
Current CPC
Class: |
B29C 64/245 20170801;
B33Y 30/00 20141201 |
International
Class: |
B29C 64/245 20060101
B29C064/245; B33Y 30/00 20060101 B33Y030/00 |
Foreign Application Data
Date |
Code |
Application Number |
May 22, 2017 |
GB |
1708188.6 |
Claims
1. An additive manufacturing device arranged to produce a part,
comprising a printer bed; a platform engaged to said printer bed,
said platform arranged to receive the part on a surface of said
platform; wherein said platform is arranged to at least partially
disengage from said printer bed.
2. The additive manufacturing device according to claim 1, wherein
the platform is arranged to selectively separate from said printer
bed.
3. The additive manufacturing device according to claim 1, wherein
the platform is magnetically engaged with the printer bed.
4. The additive manufacturing device according to claim 3, wherein
the printer bed includes a surface having at least one permanent
magnet and said platform includes a ferromagnetic material.
5. The additive manufacturing device according to claim 3, wherein
the printer bed includes a surface having at least one selectively
operable electro-magnet and said platform includes a ferromagnetic
material.
6. The additive manufacturing device according to claim 1, wherein
the platform is adhesively engaged with the printer bed.
7. The additive manufacturing device according to claim 6, wherein
the printer bed includes a surface with at least a portion
including an adhesive.
8. The additive manufacturing device according to claim 1, wherein
the platform is mechanically engaged with the printer bed.
9. The additive manufacturing device according to claim 8, wherein
the printer bed includes elements arranged to selectively engage
the platform.
10. The additive manufacturing device according to claim 9, wherein
the elements include clips or latches arrangement to move from a
first position to a second position, whereby the second position
corresponds to engagement with the platform.
11. The additive manufacturing device according to claim 9, wherein
the elements include studs on the surface of the printer bed, said
studs corresponding to engagable apertures in both the platform
and/or printer bed.
12. The additive manufacturing device according to claim 1, wherein
the platform is pneumatically engaged with the printer bed.
13. The additive manufacturing device according to claim 12,
wherein the surface of the printer bed includes an array of vacuum
apertures in fluid communication with a vacuum source.
14. The additive manufacturing device according to claim 1, wherein
the platform further comprises at least one biasing member, the
biasing member arranged to allow the platform to retain flexibility
and/or shape after repeated cycles of bending and/or
stretching.
15. The additive manufacturing device according to claim 6, wherein
the engagement is through discrete adhesive points.
16. The additive manufacturing device according to claim 7, wherein
adhesive has deterioration or melting temperatures fractionally
above ambient room temperature.
17. The additive manufacturing device according to claim 7, wherein
the adhesive comprises a binding agent with a considerably higher
rate of thermal expansion or contraction than the platform.
18. The additive manufacturing device according to claim 12,
wherein the platform is engaged with the printer bed by sliding
joints.
19. The additive manufacturing device according to claim 18,
wherein the sliding joints are actuable sideways to flex the
platform.
20. The additive manufacturing device according to claim 1, wherein
the printer bed comprises an array of ejector pins arranged to
actuate against the platform and consequently apply a curvature to
the platform.
Description
FIELD OF THE INVENTION
[0001] The invention relates to an additive manufacturing device
and, in particular, a printer bed, arranged to receive a
manufactured part created by such a device.
BACKGROUND
[0002] Existing additive manufacturing devices, such as a
stereolithographic additive manufacturing device as disclosed in WO
2015/072921, the contents of which are incorporated herein by
reference, allow large objects to be printed at high speeds using
additive manufacturing processes. In many additive manufacturing
processes including, but not limited to, Stereo-lithography (SLA)
and Masked Stereolithography (MSLA) processes, the manufactured
part is deposited to a platform of a printer bed. After the
additive process is completed, it is necessary to remove the part
from the platform, before it can be processed further or
immediately used. The removal process of part(s) from the platform
is often difficult and labour intensive because of the considerable
adhesion forces bonding the part to the platform. Depending on the
geometry of the printed parts, the removal process may even damage
the parts, for instance, thin member parts cracking or big parts
permanently deformed and remain out of shape.
SUMMARY OF THE INVENTION
[0003] In a first aspect, the invention provides an additive
manufacturing device arranged to produce a part, comprising: a
printer bed; a platform engaged to said printer bed, said platform
arranged to receive the part on a surface of said platform; wherein
said platform is arranged to at least partially disengage from said
printer bed.
[0004] Accordingly, by having a platform that is at least partially
separable and then providing a means of delaminating the part from
the platform, the stress concentration established by the
delamination allows the part to be readily removed without causing
damage to the part through an excessive application of shear force
to the part.
[0005] In one embodiment, the means of delamination may include
deforming the platform to promote the stress concentration. In an
alternative embodiment, the platform may be a single use item. In a
further embodiment, the single use platform may be frangible so as
to permit the platform to be fractured so as to break the platform
away from the part. In a different embodiment, the printer bed may
be of a highly differing coefficient of thermal expansion such that
it expands/contract much more than the printed part, thus removing
the part easily.
BRIEF DESCRIPTION OF DRAWINGS
[0006] It will be convenient to further describe the present
invention with respect to the accompanying drawings that illustrate
possible arrangements of the invention. Other arrangements of the
invention are possible and consequently, the particularity of the
accompanying drawings is not to be understood as superseding the
generality of the preceding description of the invention.
[0007] FIGS. 1A, 1B and 1C are isometric views of a platform having
a magnetic attachment to a printer bed according to one embodiment
of the present invention;
[0008] FIGS. 2A and 2B are isometric views of a platform having
mechanical engagement to a printer bed according to a further
embodiment of the present invention;
[0009] FIGS. 3A and 3B are isometric views of a platform engaged to
the printer bed through adhesion according to a further embodiment
of the present invention;
[0010] FIG. 4 includes sequential steps of the engagement of the
platform to the bed and subsequent removal of the part according to
a further embodiment of the present invention;
[0011] FIG. 5 is an isometric view of a platform in vacuum
engagement with the printer bed according to a further embodiment
of the present invention;
[0012] FIG. 6 includes sequential step of a part being removed from
a platform using an ejector pin according to one embodiment of the
present invention;
[0013] FIG. 7A shows the platform secured to the pneumatically
engaged arrangement by sliding joints before removal of the
part.
[0014] FIG. 7B shows the flexing of the platform during removal of
part.
DETAILED DESCRIPTION
[0015] As mentioned, the invention seeks to solve the problem of a
manufactured part(s) adhering to a platform(s) upon which the
part(s) is/are produced. By having the platform(s) at least
partially separable from the printer bed different techniques may
be used to separate the part(s) from the platform(s), which may not
be readily available as compared to the platform(s) being a unitary
surface of the printer bed.
[0016] As mentioned, in one embodiment, the platform(s) may be
delaminated from the part permitting the operator to secure the
separated part without having to apply a shear force to the part in
order to achieve separation.
[0017] FIGS. 4 and 6 show processes by which this separation is
achieved with the remaining figures providing embodiments of
mounting the platform to the printer bed and so achieve the
selective removal identified in FIGS. 4 and 6.
[0018] To outline the underlying method of the invention, the
reader's attention is drawn to FIG. 4 showing sequential steps of
the platform firstly being secured 145 to the printer bed 150. The
additive manufacturing process creates a part on the platform at
step 155 with the platform then being removed 160 from the printer
bed. In a first alternative process, the platform, which may be
naturally planar, and is subjected to a curvature 165 which leads
to delamination between the effectively rigid part and flexible
platform to achieve separation 170. The nature of the engagement
between the platform and printer bed is the subject of the
alternative embodiments to be discussed below.
[0019] The alternative process, once the platform is removed from
the printer bed, depends upon the nature of the platform itself. At
step 160 the platform may be naturally planar, however for the
process of 175 the platform includes a camber. On release from the
printer bed, the platform adopts its natural curvature, immediately
leading to the development of a stress concentration between the
part and the platform. The stress concentration then assists in the
delamination of the part from the platform. For the planar
platform, applying the curvature to the platform may be achieved in
several ways including applying axial loads to the platform so as
to buckle the platform. Alternatively, a curvature may be applied
to the platform such as placing the platform on a curved template,
and hold the platform in place as the part is delaminated. A
further alternative shown in FIG. 6 as follows.
[0020] FIG. 6 shows a platform 210 which is only partially
separable from the printer bed 215. In FIG. 6, the part 10 has been
created on the platform 210 and is now ready for separation from
the platform.
[0021] In this embodiment, the printer bed includes an ejector pin
225 which pushes the partially separable platform 210 upwards. It
will be appreciated that the method shown in FIG. 6 may apply to
both partially and fully separable platforms. For a fully separable
platform, the edges of the platform may need to be restrained by
any of the engagement methods described herein, with the embodiment
of FIG. 6 using selectively removable blocks 220 such that the
ejector pin applies a curvature to the platform 210. The curvature,
as discussed, leads to a delamination 230 and subsequent separation
235 of the part from the platform.
[0022] With reference to the various methods of engaging a fully
separable platform with the printer bed and its subsequent removal,
we turn to FIGS. 1A, 1B and 1C showing a magnetically engaged
platform.
[0023] In FIG. 1A, an arrangement 5 includes the part 10 engaged
with a platform 15 which in turn is engaged with a surface 25 of a
printer bed 20. In this case the printer bed includes permanent
magnets either embedded within the printer bed or as a layer
forming the surface 25. The number, or extent, of the permanent
magnets will depend upon the degree of adhesion required between
the platform and printer bed. As the permanent magnets cannot be
switched off, a tab 23 (shown in FIG. 1C) may be provided in the
platform to aid in initiating separation of the platform from the
surface 25.
[0024] It will be appreciated that initiation of the separation
could be achieved in a number of different ways including a ridge
or projection in the platform or the printer bed 20 preventing
complete engagement between the platform and printer bed, and so
providing an available point to initiate the separation. For
instance, the tabs may be replaced by projections or other
convenient means to grip the platform.
[0025] FIG. 1B shows an alternative arrangement 30 whereby the
printer bed 35 includes in the surface 40, either as a layer or as
an array of discrete points, electro-magnets powered by an
electrical supply 45. This has the advantage of being able to
selectively turn off the electro-magnets and thus assist in
separating the platform from the printer bed 35.
[0026] The nature of the platform for the embodiments of FIGS. 1A,
1B and 1C clearly require the platform to include a ferromagnetic
material to be engaged by the magnetic surface. In an alternate
embodiment, the platform may be a spring steel or the like, that
will retain its flexibility and shape after many cycles or rounds
of bending and/or stretching. In subsequent embodiments, the
platform, however, could be made from a series of different
materials and not necessarily limited to a metallic material,
including polymers such as, but not limited to, Polypropylene, PET,
PE etc.
[0027] FIGS. 2A and 2B show mechanical means by which the platform
is engaged with the printer bed. For FIG. 2A, the platform 65 is
fixed through clips 70 on the surface 60 of the printer bed 55,
which are arranged to move from a first, unengaged position to a
second engaged position. Thus, to remove the platform it merely
needs to be unclipped for easy removal. The clips may be
electronically actuated or simply spring loaded. The clips may, not
only restrain the platform, but bias it against the printer bed to
maintain planarity. The terms clips and latches may be used
interchangeably.
[0028] FIG. 2B shows an alternative mechanical arrangement 75
whereby the surface 85 of the printer bed 80 includes studs 90
which engage with apertures 95 in the platform 100. The studs may
engage with the apertures as a screw threaded nut or press fit into
the apertures or any of a number of means by which the platform can
be selectively fixed to the surface 85 of the printer bed 80.
Alternatively, the platform may include studs which fit into
apertures within the printer bed.
[0029] FIGS. 3A and 3B show an alternative arrangement of the
platform adhesively engaged with the printer bed. The first
arrangement 105 in FIG. 3A shows the platform 115 fixed using a
reusable adhesive surface applied to the printer bed. The adhesive
should be strong enough that it sufficiently resists separation of
the platform from the printer bed. Yet it should also be removable
given a correct force that is applied from a feature like tab 23 to
initiate such separation.
[0030] For FIG. 3B rather than the entire surface having the
adhesive, a replaceable layer 135 may be used. As mentioned the
adhesive may be a reusable adhesive. Alternatively, the adhesive,
either at the surface or a dedicated layer, may be a consumable
that requires replacing for the manufacture of each part. The
adhesive layer can be a membrane that sticks to the platform with
enough adherence force such that during the printing process, the
membrane adheres completely to the platform and can be peeled from
the edge, allowing the printed parts to be easily removed from the
membrane.
[0031] In a further alternative, the adhesive surface or layer may
be subject to deterioration through heat or other means such as UV
light, water solubility or other solvent (such as organic solvent
but may also include different types of solvents made widely
available). Preferably, the material of the part will be unreactive
with the selected solvent. To this end, immersing the printer bed
in hot water or applying a hot air jet or steam may be sufficient
to break down the adhesive layer for removal of the platform. It
follows that any application of heat, either as a hot bath, hot air
or steam, must be balanced against preventing any damage to the
part itself. It will be appreciated that several adhesives may be
used for the embodiment that have deterioration or melting
temperatures fractionally above ambient room temperature.
[0032] A quasi-adhesive/mechanical engagement may also be used,
such as in the form of a hook-and-loop mechanism (such as
Velcro.TM.) could also be used as a reusable "adhesive".
[0033] It will be appreciated that any of the embodiments directed
to adhesive engagement may adopt either a surface application or a
discrete layer on the surface. However, discrete adhesive points
may also be useful, particularly around the periphery of the
platform to aid in removal as compared to having to peel the
platform directly from a more widely distributed layer.
[0034] A further alternative to the temperature dependent
deterioration of the adhesive is the use of a binding agent such as
hot melt or other means of bonding the platform to the printer bed.
In this embodiment, the bonding agent may have a considerably
higher rate of thermal expansion than the platform, and so
delamination through differential expansion for relatively small
changes in temperature may be sufficient to delaminate the part
from the platform. Alternatively, it is also possible that the
platform is able to expand and contract considerably more than the
printed parts which stick to the platform. After the printing
process is completed, the platform(s) is exposed to high
temperature (for example, a hot water bath). The significant
difference in the thermal expansion/contraction causes the printed
parts to get removed from the platform. The opposite can also be
applied, where the platform(s) is exposed to a low temperature,
resulting in a similar outcome.
[0035] FIG. 5 shows a pneumatically engaged arrangement, whereby
the platform 195 is engaged with the surface 200 of a printer bed
190 through a vacuum seal. The surface 200 may include an array of
vacuum apertures 205 in communication with a vacuum source to
selectively engage the platform 195. In order to release the
platform the vacuum source merely needs to be switched off for easy
removal. Though FIG. 5 shows the vacuum apertures 205 extending
beyond the platform, this is for illustration purposes only. For
the most efficient use of the vacuum engagement the platform may be
designed to cover all of the available vacuum apertures so as not
to undermine the efficiency of the vacuum seal.
[0036] Before removal of the part 10 as shown in FIG. 7A, the
platform 195 is secured to the pneumatically engaged arrangement by
sliding joints 240, allowing the platform to bend but remaining
attached to the mechanism. During removal as shown in FIG. 7B, the
suction force can then be stopped, and the platform is pushed in
the middle by pneumatic actuation or other means, thereby flexing
it. The part 10 will then be dropped or released from the
platform.
[0037] Another embodiment of this method is to have the sliding
joints similar as described above, and having it actuated sideways
by pneumatic actuation or other means. When printing process is
done and suction force is stopped, the sliding joints can be
actuated, creating a flex to the platform. The parts will then drop
from the platform.
[0038] Although particular embodiments have been described and
illustrated herein, it will be appreciated by those of ordinary
skill in the art that various modifications and combinations of
features of the above embodiments are possible such as the removal
of part(s) using the combination of pneumatic and magnetic methods.
There is also a possibility that the platform can encompass the
following characteristics such as shape variation, e.g. outlines
(rectangular, square, circular, etc.), perforated vs.
non-perforated, flat vs. naturally bent, etc, and/or having
thickness variation, e.g. thin (such as 1 mm [0.04 in] or even
less), or thick. The material of the platform(s) can also vary,
e.g., hard and/or sturdy material such as spring steel or the like,
flexible, stretchy, etc. The platform may also retain its
flexibility and shape after many cycles or rounds of bending and/or
stretching. The platform can feature various designs to achieve
certain desired characteristic, e.g. unidirectional bending,
uniform directional bending, etc.
* * * * *