U.S. patent application number 16/677952 was filed with the patent office on 2020-05-14 for sheet holding device, image forming apparatus, and image reading device.
This patent application is currently assigned to Ricoh Company, Ltd.. The applicant listed for this patent is Junichi Sugita. Invention is credited to Junichi Sugita.
Application Number | 20200148492 16/677952 |
Document ID | / |
Family ID | 70551800 |
Filed Date | 2020-05-14 |
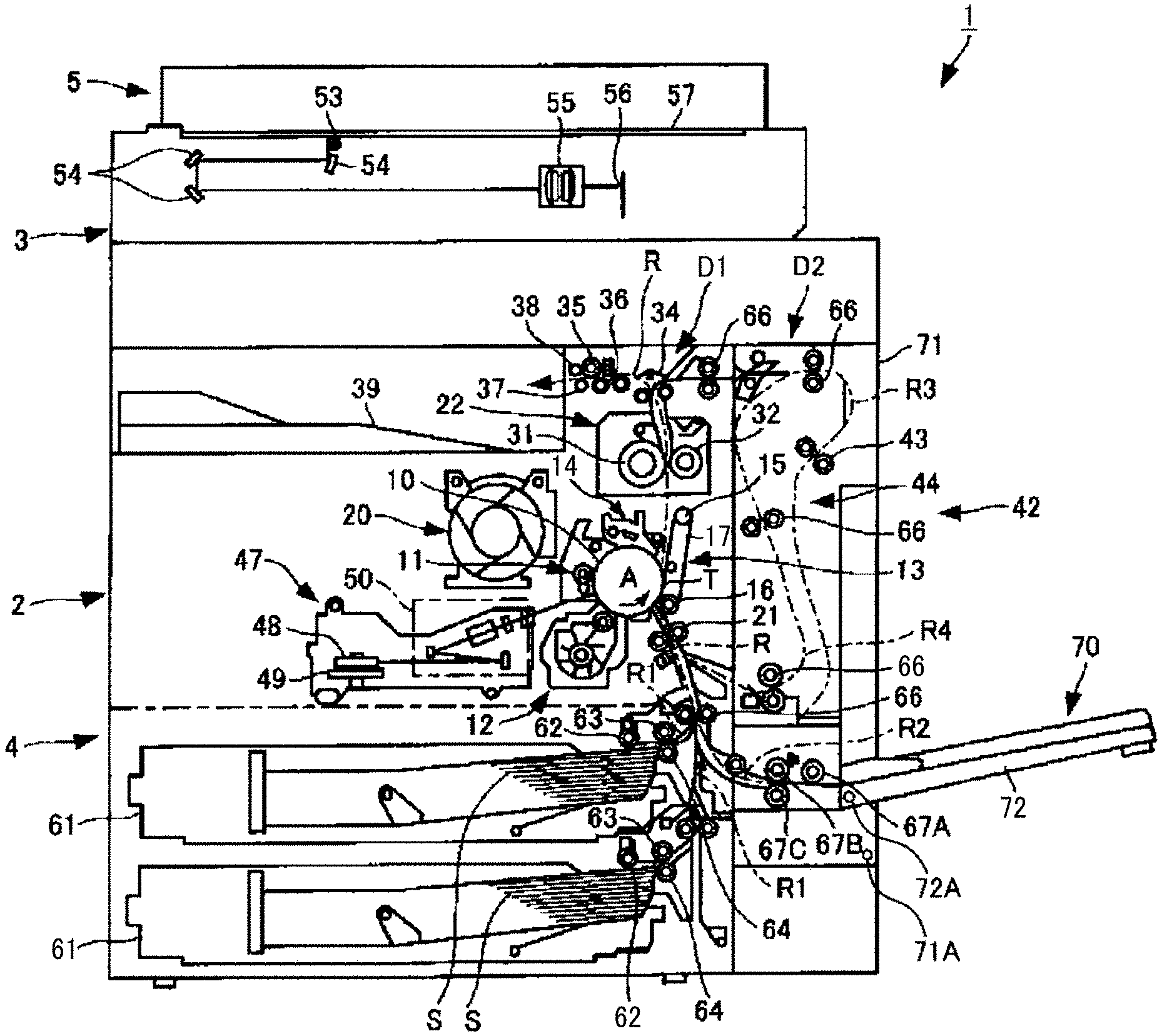
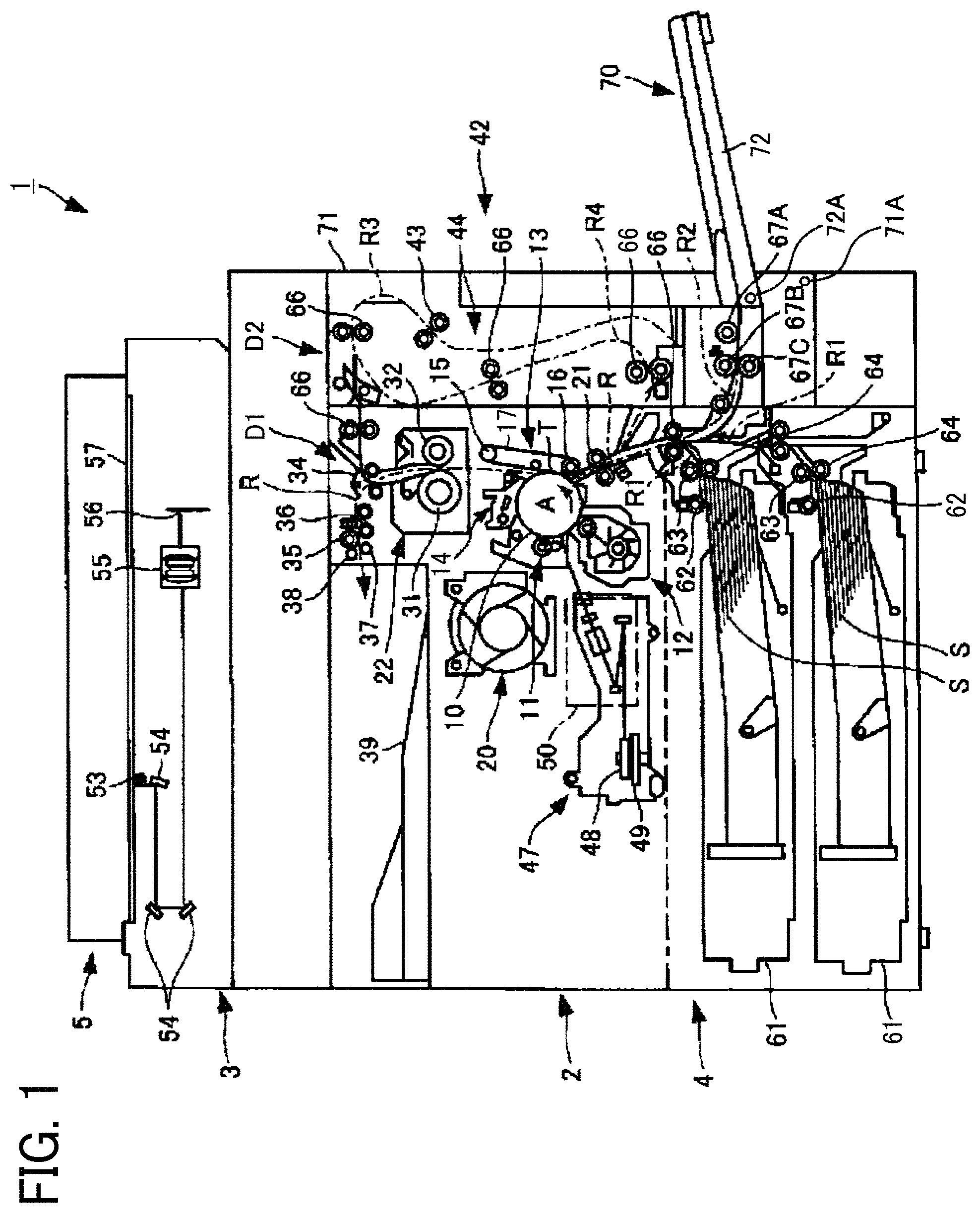
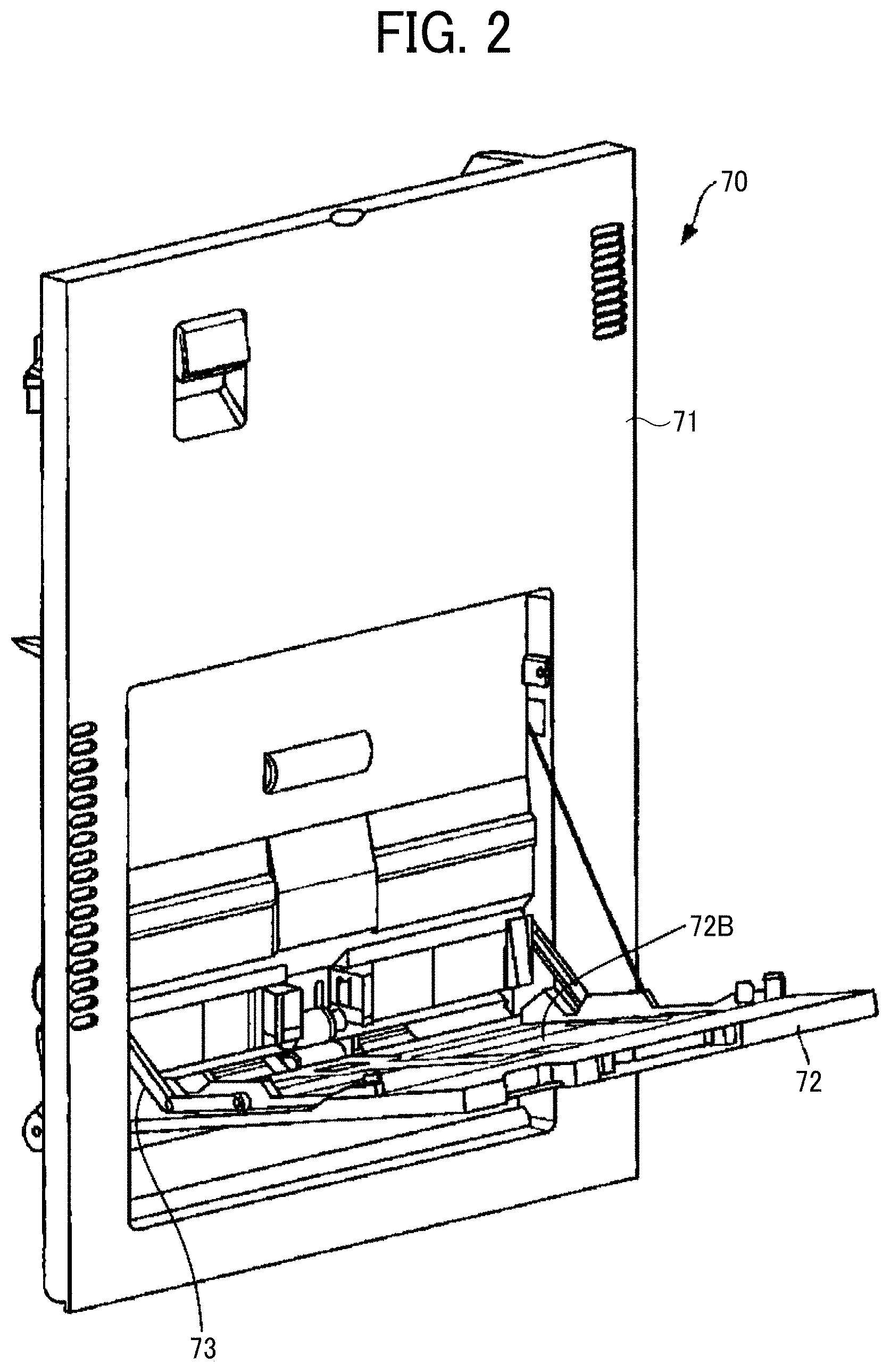
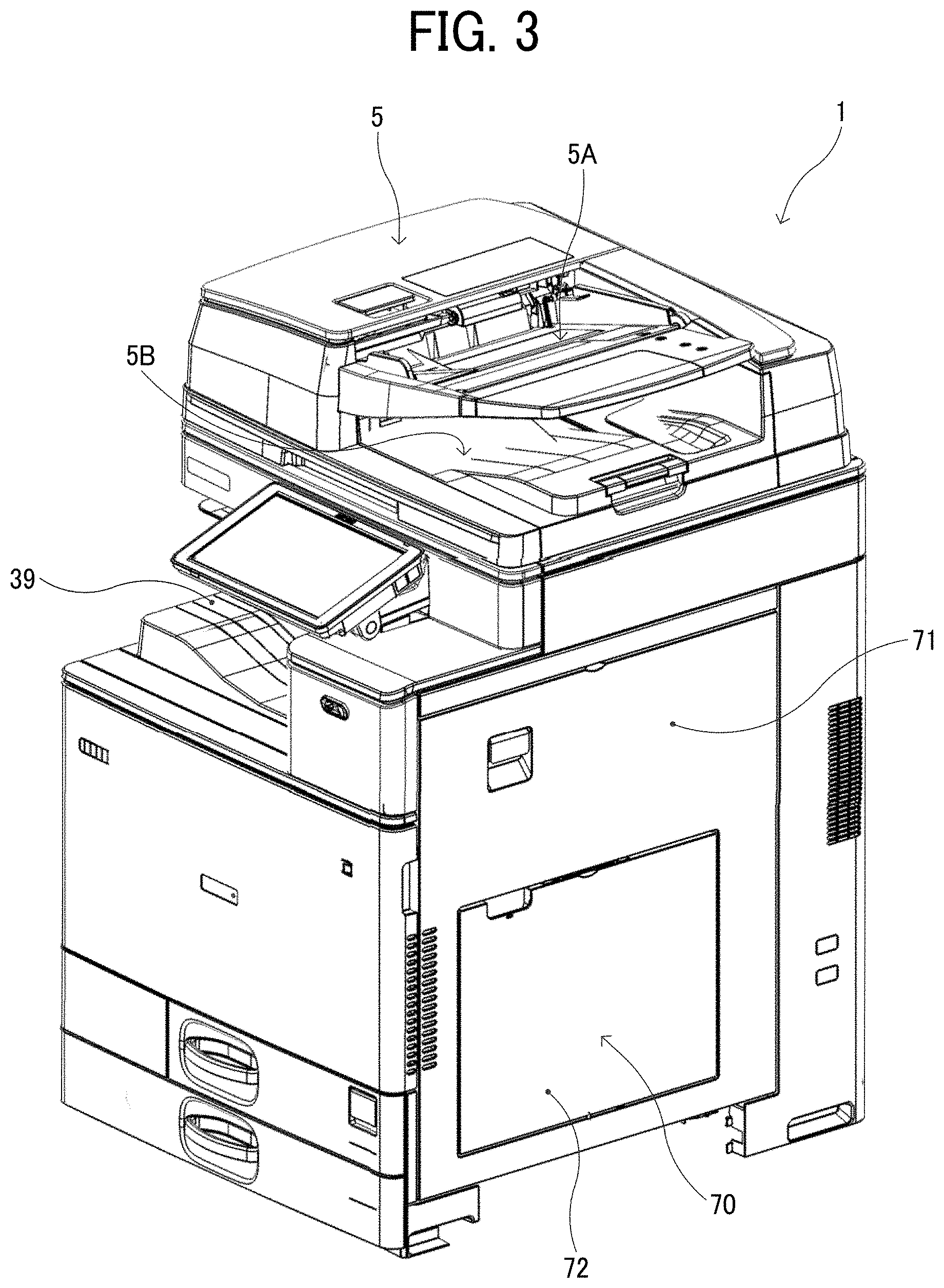

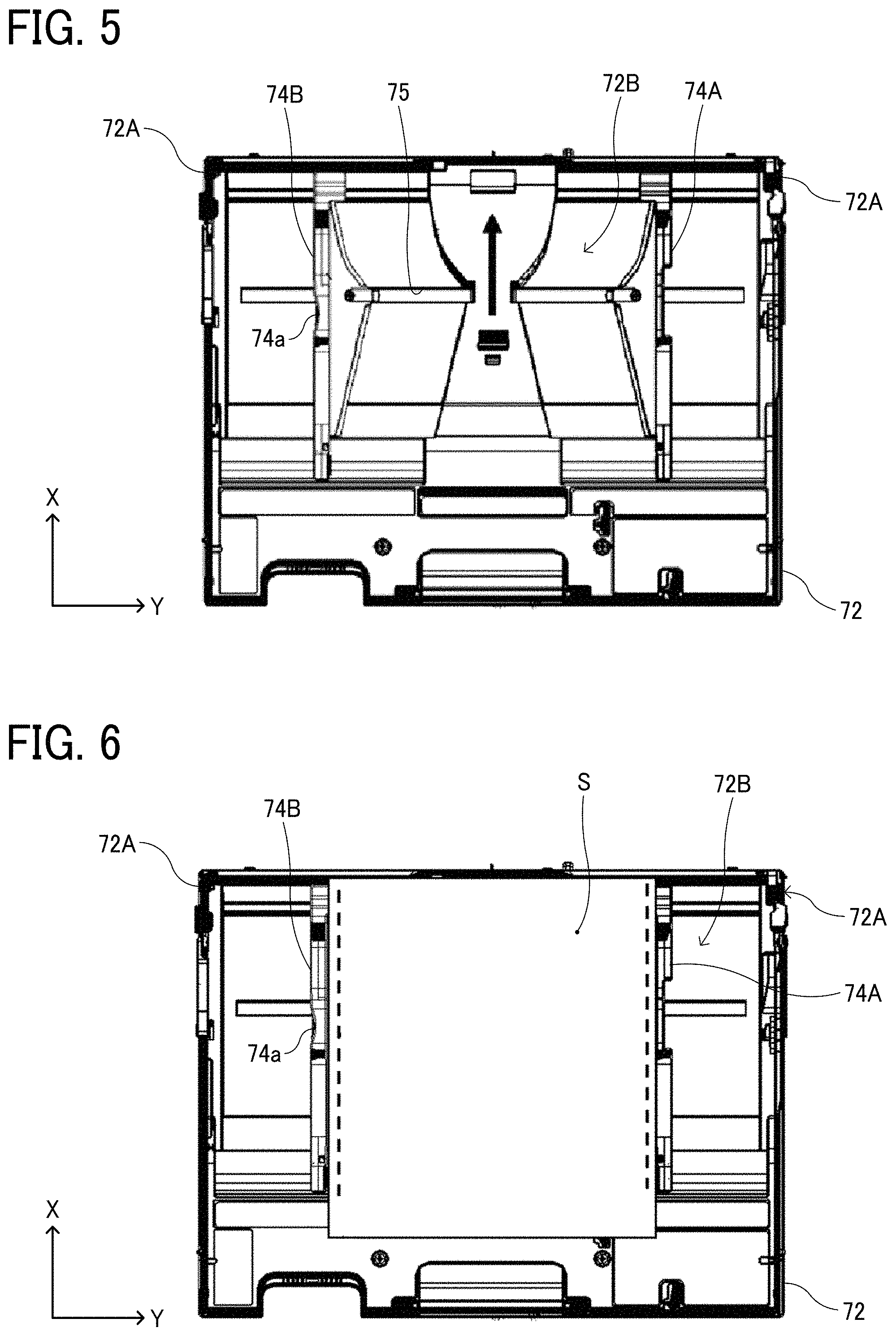
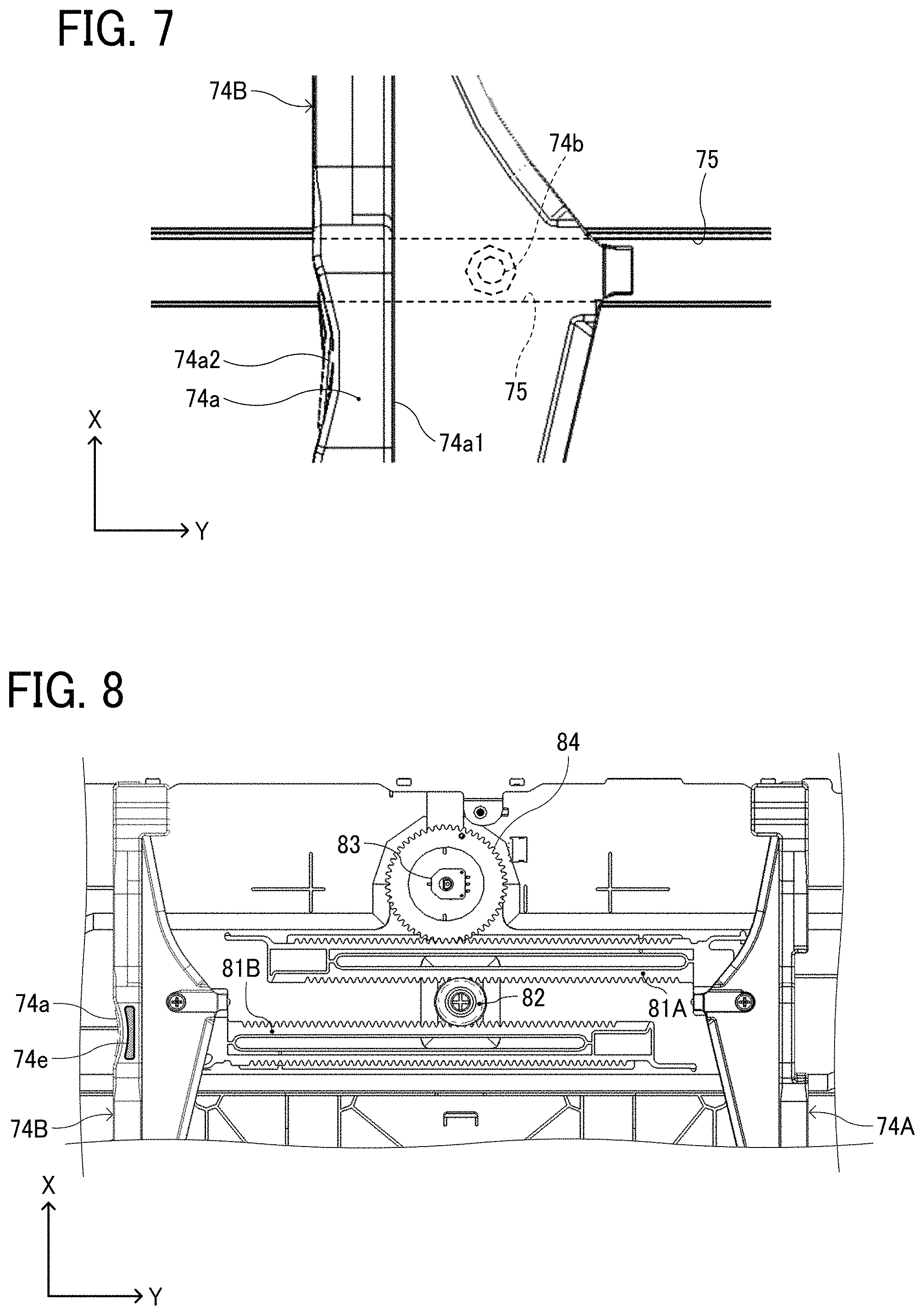
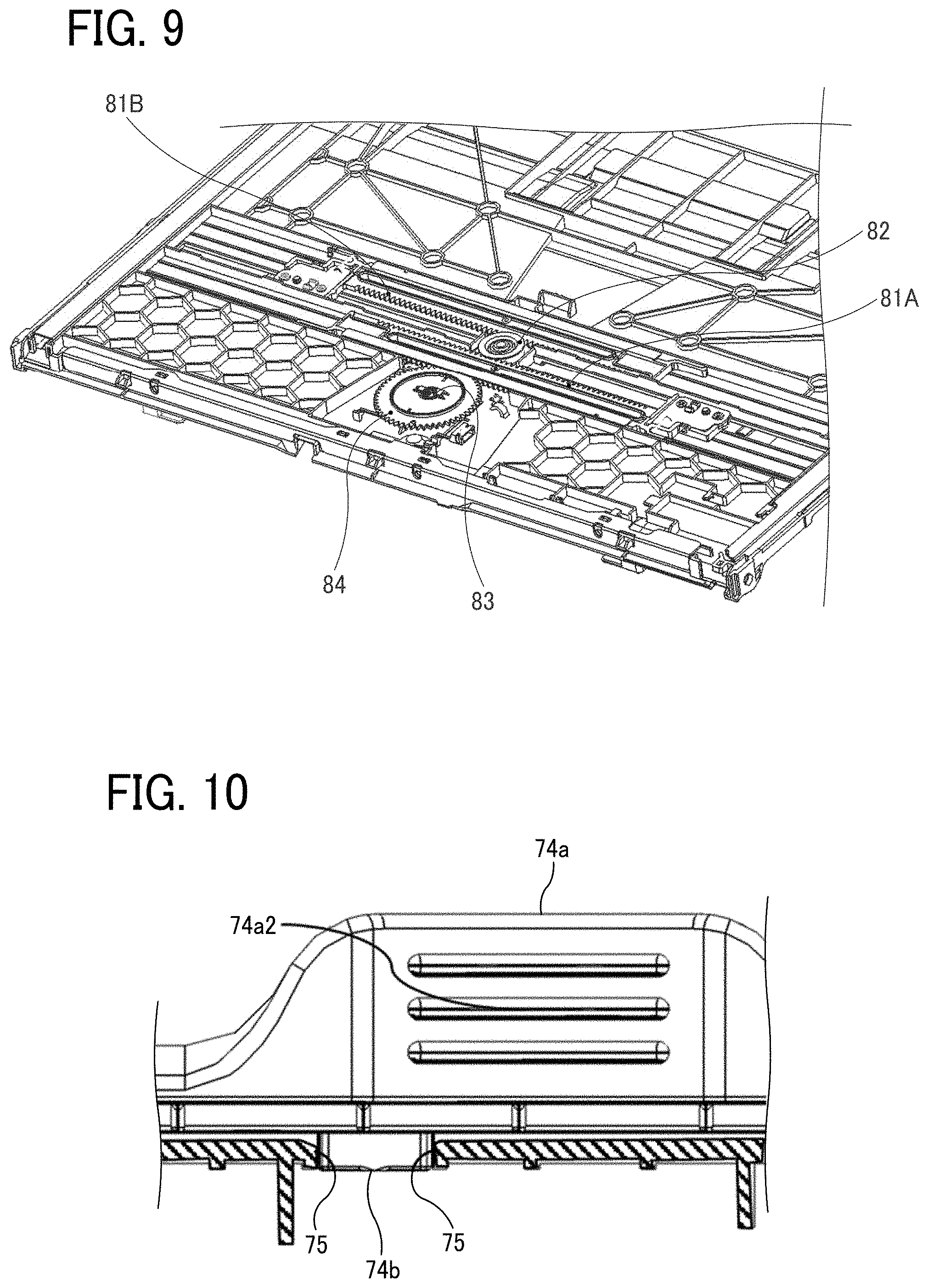

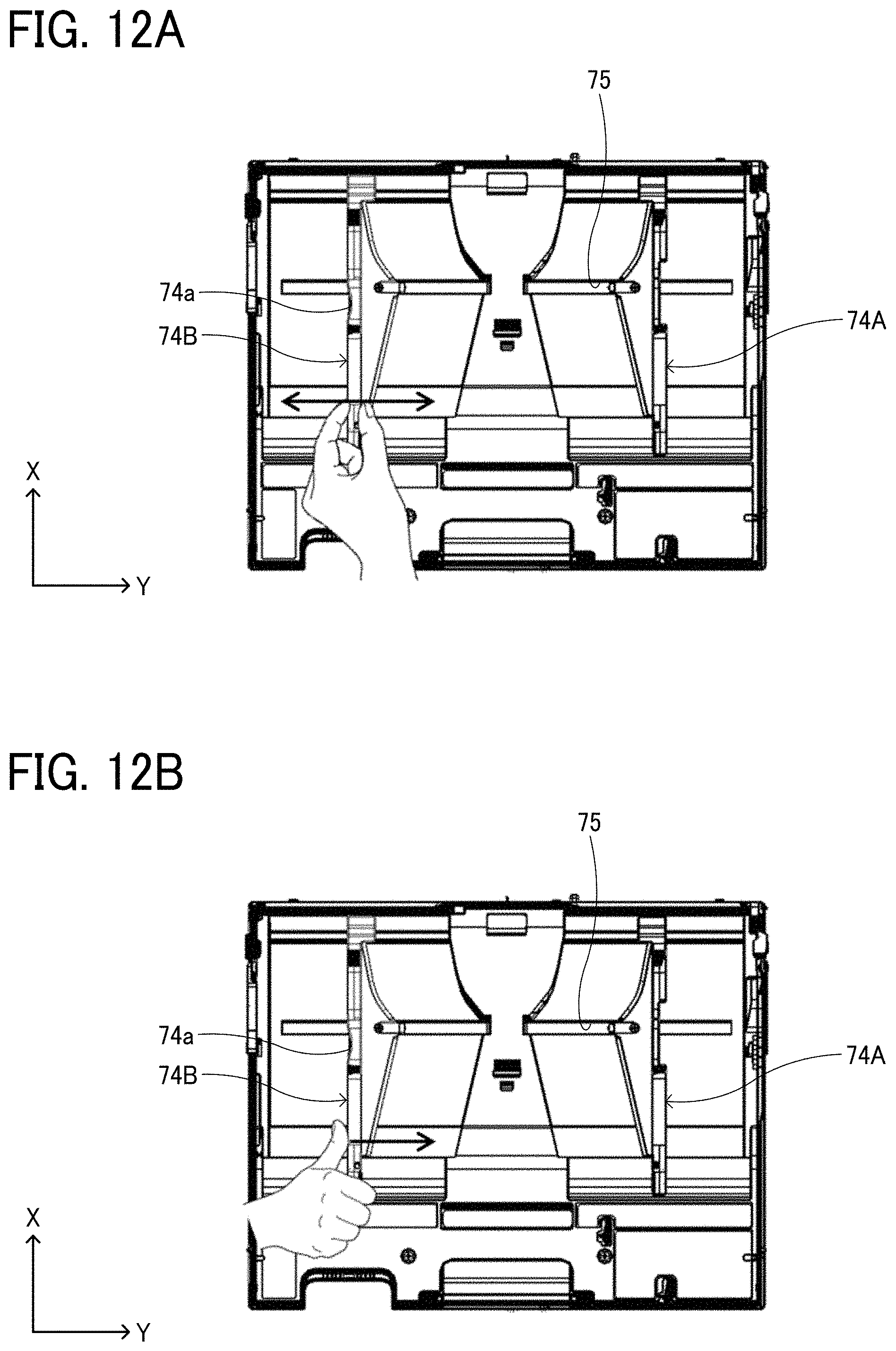

View All Diagrams
United States Patent
Application |
20200148492 |
Kind Code |
A1 |
Sugita; Junichi |
May 14, 2020 |
SHEET HOLDING DEVICE, IMAGE FORMING APPARATUS, AND IMAGE READING
DEVICE
Abstract
A sheet holding device includes a sheet placement surface and a
sheet regulating member. A sheet is to be placed on the sheet
placement surface. The sheet regulating member is movable in a
contacting direction to contact and a separating direction to
separate from an edge of the sheet placed on the sheet placement
surface. The sheet regulating member includes a grip portion and a
non-grip portion. The grip portion is configured to be gripped by a
user to move the sheet regulating member. The non-grip portion is
lower in height from the sheet placement surface than the grip
portion. The non-grip portion has, on at least one end face in the
contacting direction, a slope whose height from the sheet placement
surface increases toward a center of the non-grip portion in the
contacting direction or the separating direction.
Inventors: |
Sugita; Junichi; (Tokyo,
JP) |
|
Applicant: |
Name |
City |
State |
Country |
Type |
Sugita; Junichi |
Tokyo |
|
JP |
|
|
Assignee: |
Ricoh Company, Ltd.
Tokyo
JP
|
Family ID: |
70551800 |
Appl. No.: |
16/677952 |
Filed: |
November 8, 2019 |
Current U.S.
Class: |
1/1 |
Current CPC
Class: |
B65H 5/36 20130101; B65H
1/04 20130101; B65H 2511/20 20130101; B65H 2402/64 20130101; B65H
2701/1315 20130101; B65H 2511/12 20130101; B65H 2407/21 20130101;
B65H 3/06 20130101; B65H 2407/20 20130101; B65H 2511/12 20130101;
B65H 2220/01 20130101; B65H 2511/20 20130101; B65H 2220/02
20130101 |
International
Class: |
B65H 5/36 20060101
B65H005/36; B65H 3/06 20060101 B65H003/06 |
Foreign Application Data
Date |
Code |
Application Number |
Nov 13, 2018 |
JP |
2018-212701 |
Claims
1. A sheet holding device comprising: a sheet placement surface on
which a sheet is to be placed; and a sheet regulating member
movable in a contacting direction to contact and a separating
direction to separate from an edge of the sheet placed on the sheet
placement surface, the sheet regulating member including: a grip
portion configured to be gripped by a user to move the sheet
regulating member; and a non-grip portion lower in height from the
sheet placement surface than the grip portion, the non-grip portion
having, on at least one end face in the contacting direction, a
slope whose height from the sheet placement surface increases
toward a center of the non-grip portion in the contacting direction
or the separating direction.
2. The sheet holding device according to claim 1, wherein a whole
of the at least one end face of the non-grip portion is the
slope.
3. The sheet holding device according to claim 1, wherein the slope
is a curved surface whose angle between the sheet placement surface
and a tangent line to the slope decreases toward the center of the
non-grip portion in the contacting direction or the separating
direction.
4. The sheet holding device according to claim 1, wherein the
non-grip portion has slopes on both end faces in the contacting
direction.
5. The sheet holding device according to claim 4, wherein the
contacting direction and the separating direction of the sheet
regulating member are orthogonal to a sheet conveyance direction in
which the sheet is conveyed from the sheet placement surface,
wherein the sheet regulating member includes at least two of
non-grip portions, including the non-grip portion, across the grip
portion in the sheet conveyance direction, and wherein a non-grip
portion of the at least two non-grip portions upstream of the grip
portion in the sheet conveyance direction has the slopes on both
end faces in the contacting direction.
6. The sheet holding device according to claim 1, wherein the
non-grip portion has a sheet regulating surface extending in a
normal direction of the sheet placement surface on an end face on a
side to contact the edge of the sheet.
7. The sheet holding device according to claim 6, wherein the
contacting direction and the separating direction of the sheet
regulating member are orthogonal to a sheet conveyance direction in
which the sheet is conveyed from the sheet placement surface,
wherein the sheet regulating member includes at least two non-grip
portions, including the non-grip portion, across the grip portion
in the sheet conveyance direction, and wherein a non-grip portion
of the at least two non-grip portions downstream of the grip
portion in the sheet conveyance direction has the sheet regulating
surface.
8. The sheet holding device according to claim 1, further
comprising a single guide member extending in the contacting
direction and configured to guide and move the sheet regulating
member, and wherein the grip portion is disposed at a position
overlapping with the single guide member.
9. The sheet holding device according to claim 1, further
comprising: two sheet regulating members, including the sheet
regulating member, configured to regulate both edges of the sheet
placed on the sheet placement surface; and a moving mechanism
configured to move, in conjunction with movement of one of the two
sheet regulating members, another one of the sheet regulating
members.
10. The sheet holding device according to claim 1, wherein at least
one end face of the grip portion in the contacting direction has a
recessed shape as viewed in a normal direction of the sheet
placement surface.
11. The sheet holding device according to claim 1, wherein the
sheet holding device is a sheet feeding tray.
12. An image forming apparatus comprising the sheet holding device
according to claim 1.
13. An image reading device comprising the sheet holding device
according to claim 1.
Description
CROSS-REFERENCE TO RELATED APPLICATION
[0001] This patent application is based on and claims priority
pursuant to 35 U.S.C. .sctn. 119(a) to Japanese Patent Application
No. 2018-212701, filed on Nov. 13, 2018, in the Japan Patent
Office, the entire disclosure of which is incorporated by reference
herein.
BACKGROUND
Technical Field
[0002] Aspects of the present disclosure relate to a sheet holding
device, an image forming apparatus, and an image reading
device.
Discussion of the Background Art
[0003] There has been known a sheet holding device in which a grip
portion of a sheet regulating member movable in a
contacting/separating direction toward and away from an edge of a
sheet placed on a sheet placement surface is gripped by a user so
that the sheet regulating member is moved.
[0004] For example, for a manual sheet feeding tray (sheet holding
device), a user grips an operation section (grip portion) provided
on a side fence (sheet regulating member) and manually moves the
side fence.
SUMMARY
[0005] In an aspect of the present disclosure, there is provided a
sheet holding device that includes a sheet placement surface and a
sheet regulating member. A sheet is to be placed on the sheet
placement surface. The sheet regulating member is movable in a
contacting direction to contact and a separating direction to
separate from an edge of the sheet placed on the sheet placement
surface. The sheet regulating member includes a grip portion and a
non-grip portion. The grip portion is configured to be gripped by a
user to move the sheet regulating member. The non-grip portion is
lower in height from the sheet placement surface than the grip
portion. The non-grip portion has, on at least one end face in the
contacting direction, a slope whose height from the sheet placement
surface increases toward a center of the non-grip portion in the
contacting direction or the separating direction.
[0006] In another aspect of the present disclosure, there is
provided an image forming apparatus that includes the sheet holding
device.
[0007] In still another aspect of the present disclosure, there is
provided an image reading device that includes the sheet holding
device.
BRIEF DESCRIPTION OF THE DRAWINGS
[0008] The aforementioned and other aspects, features, and
advantages of the present disclosure would be better understood by
reference to the following detailed description when considered in
connection with the accompanying drawings, wherein:
[0009] FIG. 1 is a schematic view illustrating a copier according
to an embodiment;
[0010] FIG. 2 is an external perspective view illustrating a manual
sheet feeder of the copier;
[0011] FIG. 3 is an external perspective view of the copier when a
sheet feeding tray is in a closed state in an upright posture;
[0012] FIG. 4 is an external perspective view of the copier when
the sheet feeding tray is in an open state in an inclined
posture;
[0013] FIG. 5 is a plan view of the sheet feeding tray;
[0014] FIG. 6 is a plan view of the sheet feeding tray on which a
sheet is placed;
[0015] FIG. 7 is a partially enlarged view illustrating a guide pin
of a side fence fitted into a guide rail;
[0016] FIG. 8 is a plan view illustrating a moving mechanism of the
side fence in the sheet feeding tray;
[0017] FIG. 9 is a perspective view illustrating the moving
mechanism;
[0018] FIG. 10 is an enlarged view of a grip portion provided on
one side fence as viewed from the outside in the sheet width
direction;
[0019] FIGS. 11A and 11B are plan views illustrating how a user
holds the grip portion with his/her fingers and moves the side
fence along the sheet width direction;
[0020] FIGS. 12A and 12B are plan views illustrating how the user
holds a portion other than the grip portion on the side fence with
his/her fingers and moves the side fence along the sheet width
direction;
[0021] FIG. 13A is a perspective view of the side fence including
the grip portion as viewed from the outside in the sheet width
direction; FIG. 13B is a perspective view of the side fence as
viewed from the inside in the sheet width direction;
[0022] FIG. 14 is a cross-sectional view of the grip portion cut by
a plane orthogonal to the sheet feeding direction;
[0023] FIG. 15 is a cross-sectional view of a non-grip portion
adjacent to the downstream side of the grip portion in the sheet
feeding direction, which is cut by a plane orthogonal to the sheet
feeding direction;
[0024] FIG. 16 is a cross-sectional view of a non-grip portion
adjacent to the upstream side of the grip portion in the sheet
feeding direction, which is cut by a plane orthogonal to the sheet
feeding direction; and
[0025] FIG. 17 is a cross-sectional view illustrating a variation
in which the inner end face of the non-grip portion is also formed
so that the entire end face is a slope as well as the outer end
face.
[0026] The accompanying drawings are intended to depict embodiments
of the present disclosure and should not be interpreted to limit
the scope thereof. The accompanying drawings are not to be
considered as drawn to scale unless explicitly noted.
DETAILED DESCRIPTION
[0027] In describing embodiments illustrated in the drawings,
specific terminology is employed for the sake of clarity. However,
the disclosure of this patent specification is not intended to be
limited to the specific terminology so selected and it is to be
understood that each specific element includes all technical
equivalents that operate in a similar manner and achieve similar
results.
[0028] Although the embodiments are described with technical
limitations with reference to the attached drawings, such
description is not intended to limit the scope of the disclosure
and all of the components or elements described in the embodiments
of this disclosure are not necessarily indispensable.
[0029] Referring now to the drawings, embodiments of the present
disclosure are described below. In the drawings for explaining the
following embodiments, the same reference codes are allocated to
elements (members or components) having the same function or shape
and redundant descriptions thereof are omitted below.
[0030] Hereinafter, a sheet feeding tray of a copier as an image
forming apparatus will be described as a sheet holding device
according to an embodiment of the present disclosure.
[0031] FIG. 1 is a schematic view illustrating a copier 1 as the
image forming apparatus according to the present embodiment.
[0032] The copier 1 according to the present embodiment includes an
image forming apparatus main body 2, an image reading device 3
disposed on the image forming apparatus main body 2, a table-shaped
sheet feeder 4 disposed below the image forming apparatus main body
2, and an automatic document carrier 5 disposed on the image
reading device 3 to be openable and closable. The copier 1 further
includes a switchback device 42, and a manual sheet feeder 70.
[0033] The image forming apparatus main body 2 internally includes
a drum-shaped photoconductor 10 as an image bearer. A charging
device 11 is disposed on the left side in the drawing around the
photoconductor 10, and a developing device 12, a transfer device
13, and a cleaning device 14 are disposed along the rotational
direction (counterclockwise direction: arrow A in the drawing) of
the photoconductor 10. The transfer device 13 includes a transfer
belt 17 wound between upper and lower rollers 15 and 16, and the
transfer belt 17 is pressed against the circumferential surface of
the photoconductor 10 at a transfer position T.
[0034] A toner supply device 20 for supplying new toner to the
developing device 12 is disposed on the left side of the charging
device 11 and the cleaning device 14. Further, the image forming
apparatus main body 2 internally includes a sheet conveyer D1 that
feeds a sheet, such as a paper sheet and an overhead projector
(OHP) sheet, from a supply position to be described later and
conveys the sheet to a stack position through a transfer position
T. The sheet conveyer D1 includes a supply path R1, a manual supply
path R2, and a sheet conveying path R to be described later. The
sheet conveying path R has a substantially L shape extending upward
from the bottom of the drawing between the photoconductor 10 and
the transfer device 13 and then turning to the left.
[0035] The sheet conveying path R has a registration roller 21
disposed at an upstream position of the photoconductor 10 in the
sheet conveyance direction. Further, a fixing device 22 is disposed
at a downstream position of the photoconductor 10 in the sheet
conveyance direction. The fixing device 22 includes a pair of
fixing rollers (fixing rotating bodies) 31 and 32. One of the
fixing rollers 31 internally includes a fixing heater, and a
pressure spring and a pressure arm are disposed around the other
fixing roller 32. The pressure spring and the pressure arm cause
one of the fixing rollers 31 to be pressed by the other fixing
roller 32. One of the fixing rollers 31 further includes a
thermistor and a thermostat.
[0036] The fixing heater turns on or off the fixing heater using
the thermostat while measuring a temperature of the fixing roller
31 using the thermistor, thereby keeping one of the fixing rollers
31 at a predetermined temperature.
[0037] At further downstream of the fixing device 22 in the sheet
conveyance direction, there are disposed an ejection bifurcating
claw 34, an ejection roller 35, a first pressure roller 36, a
second pressure roller 37, and a stiffening roller 38, and further
ahead of those components, there is disposed an ejection stack
section (ejection position) 39 for stacking sheets having been
subject to image formation.
[0038] A laser writing device 47 is disposed on the left side of
the developing device 12 in the drawing. The laser writing device
47 includes a laser light source, a rotary polygon mirror 48 for
scanning, a polygon motor 49, a scanning optical system 50, such as
an fO lens, and the like.
[0039] The image reading device 3 includes a light source 53, a
plurality of mirrors 54, an imaging optical lens 55, an image
sensor 56, such as a charge-coupled device (CCD), and the like, and
a contact glass 57 is disposed on the upper surface.
[0040] One end of the automatic document carrier 5 is connected to
one end of the upper surface of the image reading device 3 by a
connector having a hinge structure. The automatic document carrier
5 is provided in such a manner that the lower surface is openable
and closable in a state where the inclination angle with the upper
surface of the contact glass 57 is, for example, 90 degrees at the
maximum from the horizontal state of pressing a document sheet
placed on the upper surface of the contact glass 57 from above. The
automatic document carrier 5 includes, in addition to a placing
table 5A at the document placing position and an ejection table 5B
at the ejecting position, a sheet conveyer including a document
conveying path for conveying a sheet, such as a document sheet,
from the placing table 5A to the ejection table 5B through the
reading position on the contact glass 57 of the image reading
device 3. The sheet conveyer includes a plurality of sheet
conveying rollers (sheet conveyance rotating body) for conveying a
sheet, such as a document sheet.
[0041] The sheet feeder 4 internally includes sheet separating
devices 61, which are supply positions of a sheet S, in multiple
stages. Each of the sheet separating devices 61 includes a
corresponding pickup roller (feeding roller) 62, a feed roller
(feeding roller) 63, and a reverse roller (separating roller) 64.
The supply path R1 communicating with the sheet conveying path R of
the image forming apparatus main body 2 is formed on the right side
of the sheet separating devices 61 disposed in multiple stages in
the drawing. The supply path R1 includes a number of sheet
conveying rollers (sheet conveyance rotating bodies) 66 for
conveying a sheet.
[0042] The switchback device 42 is disposed on the right side of
the image forming apparatus main body 2 in the drawing. The
switchback device 42 includes a sheet conveyer D2 that branches
from the position of the ejection bifurcating claw 34 of the sheet
conveying path R. The sheet conveyer D2 includes a reverse path R3
leading to a switchback position 44 at which a pair of switchback
rollers 43 is disposed, and a re-conveying path R4 leading to, from
the switchback position 44, the registration roller 21 of the sheet
conveying path R again. The sheet conveyer D2 further includes the
plurality of sheet conveying rollers (sheet conveyance rotating
bodies) 66 for conveying a sheet. In the present embodiment, the
switchback device 42 is attached to an opening and closing member
71 to be described later.
[0043] The manual sheet feeder 70 is disposed on the right side of
the image forming apparatus main body 2 in the drawing. The manual
sheet feeder 70 includes a pickup roller (feeding roller) 67A, a
feed roller (feeding roller) 67B, and a reverse roller (separating
roller) 67C, and supplies the sheet S stacked on the sheet feeding
tray 72 to the sheet conveying path R of the image forming
apparatus main body 2.
[0044] Next, operation of the copier 1 will be described.
[0045] First, to generate a copy using the copier 1, a main switch
is turned on and a document is set in the automatic document
carrier 5. Alternatively, the automatic document carrier 5 is
opened, a document is directly set on the contact glass 57 of the
image reading device 3, and then the automatic document carrier 5
is closed to press the document.
[0046] Then, when a start switch is pressed, in the case where the
document is set in the automatic document carrier 5, the document
is moved through the document conveying path onto the contact glass
57 by the sheet conveying roller, the image reading device 3 is
driven, the content of the document is read, and then the document
is ejected onto the ejection table. On the other hand, in the case
where the document is directly set on the contact glass 57, the
image reading device 3 is driven immediately.
[0047] When the image reading device 3 starts driving, the light
source 53 moves along the contact glass 57 while emitting light,
and irradiates the document surface on the contact glass 57 with
light. The plurality of mirrors 54 receives light reflected from
the document surface, and reflects the light toward the imaging
optical lens 55. The imaging optical lens 55 forms an image of the
reflected light on the image sensor 56. The image sensor 56 reads
the content of the document, accordingly.
[0048] At the same time, the photoconductor 10 is rotated by a
photoconductor drive motor, and along with this, the surface of the
photoconductor is uniformly charged by the charging device 11 using
a charging roller, and then the laser writing device 47 irradiates
the surface of the photoconductor with laser light according to the
content of the document read by the image reading device 3
described above so that writing is performed on the surface of the
photoconductor, thereby forming an electrostatic latent image on
the surface of the photoconductor 10. Subsequently, toner is
attracted to the surface of the photoconductor when the portion of
the electrostatic latent image formed on the surface of the
photoconductor faces the developing device 12, whereby the
electrostatic latent image is made into a visible image.
[0049] Further, when the start switch is pressed, among the
plurality of sheet separating devices 61 provided in multiple
stages in the sheet feeder 4, a corresponding sheet separating
device 61 is selected on the basis of sheet size selecting signals.
Then, a pickup roller 62 corresponding to the sheet separating
device 61 feeds one sheet S in the sheet separating device 61. The
reverse roller 64 separates the uppermost sheet S when attempting
to feed a plurality of sheets S, and blocks the conveyance of the
remaining sheets S. Subsequently, the feed roller 63 inserts the
sheet S into the supply path R1 while conveying the sheet S, the
sheet conveying roller 66 successively conveys the sheet S and
guides it to the sheet conveying path R, and the registration
roller 21 abuts on the sheet S to stop the conveyance of the sheet
S. Then, the registration roller 21 rotates in synchronization with
the rotation of the photoconductor 10 described above, and feeds
the sheet S to the right side of the photoconductor 10.
[0050] In the case of performing the manual sheet feeding, the
sheet feeding tray 72 of the manual sheet feeder 70 is sifted from
the closed state in the upright posture to the open state in the
inclined posture as illustrated in FIG. 1, and a sheet is set on a
sheet placement surface 72B of the sheet feeding tray 72. When the
start switch is pressed, the pickup roller 67A feeds one sheet, and
then the feed roller 67B successively feeds the sheet. The reverse
roller 67C separates the uppermost sheet when attempting to feed a
plurality of sheets, and blocks the conveyance of the remaining
sheets. The sheet conveying roller 66 continues to convey the sheet
supplied to the manual supply path R2, and guides it to the sheet
conveying path R. Thereafter, in a similar manner to the sheet
feeder 4 described above, the registration roller 21 feeds the
sheet to the right side of the photoconductor 10 in synchronization
with the rotation of the photoconductor 10.
[0051] Subsequently, the transfer device 13 transfers the toner
image on the photoconductor 10 onto the sheet S to form an image
when the sheet S fed to the right side of the photoconductor 10
comes to the transfer position T. The cleaning device 14 removes
and cleans the residual toner on the photoconductor 10 after the
image transfer, and then a static eliminator removes the residual
potential on the photoconductor 10 to prepare for the next image
formation starting from the charging device 11.
[0052] Next, the fixing device 22 conveys the sheet S bearing the
above-described transferred toner image with the transfer belt 17
through the space between the pair of fixing rollers 31 and 32, and
applies heat and pressure at the fixing position to fix the
transferred image. The sheet S having been subject to the fixing is
made into a flat surface and is stiffened in the process of passing
through the first pressure roller 36, the ejection roller 35, the
second pressure roller 37, and the stiffening roller 38, ejected
onto the ejection stack section 39, and is stacked.
[0053] Note that the ejection bifurcating claw 34 is switched in
the case of transferring the image onto both sides of the sheet S.
Then, the sheet S bearing the image transferred to its surface is
inserted from the sheet conveying path R to the reverse path R3,
conveyed by the sheet conveying roller 66 to be inserted to the
switchback position 44, and then switchback is carried out at the
switchback position 44. Thereafter, the sheet is put into the
re-conveying path R4 and is reversed, conveyed by the sheet
conveying roller 66, guided to the sheet conveying path R again,
and an image is transferred onto the back side of the sheet as well
in a similar manner to the descriptions above.
[0054] FIG. 2 is an external perspective view illustrating the
manual sheet feeder 70.
[0055] As illustrated in FIG. 1, the manual sheet feeder 70
according to the present embodiment includes the opening and
closing member 71 whose upper portion is opened and closed with a
pivot fulcrum 71A being held at a lower part with respect to the
image forming apparatus main body 2, and the sheet feeding tray 72
whose upper portion is opened and closed with a pivot fulcrum 72A
being held at a lower part with respect to the opening and closing
member 71. As illustrated in FIG. 2, the manual sheet feeder 70
further includes a link member 73 that connects the opening and
closing member 71 to the image forming apparatus main body 2 in an
openable/closable manner.
[0056] In order to easily remove paper jam sheets clogged in the
sheet conveying path R or the re-conveying path R4, perform
maintenance on the inside of the image forming apparatus main body
2, and the like, the opening and closing member 71 is made into the
open state in the inclined posture, and the sheet conveying path R
or the re-conveying path R4 is opened. That is, the manual sheet
feeder 70 shifts the opening and closing member 71 from the closed
state in the upright posture to the open state in the inclined
posture, and opens the sheet conveying path R or the re-conveying
path R4, whereby the removal of the paper jam sheets, the
maintenance, and the like can be easily performed.
[0057] Furthermore, the manual sheet feeder 70 shifts the sheet
feeding tray 72 from the closed state in the upright posture as
illustrated in FIG. 3 to the open state in the inclined posture as
illustrated in FIG. 4, and stacks sheets on the sheet placement
surface 72B of the sheet feeding tray 72, whereby sheets for manual
feeding can be supplied to the sheet conveying path R.
[0058] FIG. 5 is a plan view of the sheet feeding tray 72 according
to the present embodiment.
[0059] FIG. 6 is a plan view of the sheet feeding tray 72 on which
the sheet S is placed.
[0060] The sheet feeding tray 72, which is a sheet holding device,
includes side fences 74A and 74B, and a guide rail 75. Two side
fences 74A and 74B are installed in the sheet width direction (Y
direction) in the space above the sheet placement surface 72B
(loading space of the sheet S).
[0061] The sheet feeding tray 72 according to the present
embodiment includes the guide rail 75 as a guide member extending
in the sheet width direction (Y direction). As illustrated in FIG.
7, the pair of side fences 74A and 74B installed at both ends in
the sheet width direction to sandwich the sheet S includes a guide
pin 74b to be fitted in the guide rail 75. With the guide pin 74b
being guided to the guide rail 75, the side fences 74A and 74B can
be manually moved in the contacting/separating direction (sheet
width direction) contacting or separated from the edge of the sheet
S in the width direction along the guide rail 75, and are
positioned corresponding to the size of the sheet S in the width
direction. That is, the side fences 74A and 74B function as a sheet
regulating member that regulates the position of the sheet S in the
width direction.
[0062] In the sheet feeding tray according to the present
embodiment, there may be provided an end fence on the upstream side
in the sheet feeding direction (X direction) in the space above the
sheet placement surface 72B (loading space of the sheet S).
Specifically, the sheet feeding tray 72 includes a guide rail as a
guide member extending in the sheet feeding direction (X
direction), and an end fence is installed along the guide rail to
be movable in the sheet feeding direction, for example. The end
fence is positioned corresponding to the size of the sheet S placed
on the sheet placement surface 72B in the feeding direction. That
is, the end fence functions as a sheet regulating member that
regulates the position of the edge of sheet S in the feeding
direction.
[0063] In the present embodiment, the pair of side fences 74A and
74B interlocks to increase or decrease the interval in the width
direction. That is, when one of the side fences 74A and 74B is
manually moved in the +Y direction, in conjunction with that, the
other one of the side fences 74B and 74A moves in the -Y direction.
When one of the side fences 74A and 74B is manually moved in the -Y
direction, in conjunction with that, the other one of the side
fences 74B and 74A moves in the +Y direction.
[0064] Note that, although the feeding direction (sheet conveyance
direction) of the sheet S is X direction and the sheet feeding tray
72 can be inserted/removed in the Y direction in FIGS. 5 and 6,
embodiments of the present disclosure are not limited to those
directional relationships.
[0065] FIG. 8 is a plan view illustrating a moving mechanism of the
side fences 74A and 74B in the sheet feeding tray 72 according to
the present embodiment. FIG. 9 is a perspective view illustrating
the moving mechanism of the side fences 74A and 74B in the sheet
feeding tray 72 according to the present embodiment. Note that FIG.
9 illustrates a state in which the side fences 74A and 74B are
removed.
[0066] In the moving mechanism of the side fences 74A and 74B
according to the present embodiment, the pair of side fences 74A
and 74B moves in conjunction with each other so that the center of
the sheet S in the width direction matches the center of the sheet
placement surface 72B in the width direction even if the size of
the sheet S in the width direction changes. In the present
embodiment, a pinion rack mechanism is used as the moving mechanism
of the side fences 74A and 74B.
[0067] Specifically, as illustrated in FIG. 8, each of the side
fences 74A and 74B includes racks 81A and 81B. Each of the racks
81A and 81B is engaged with the pinion to sandwich the pinion 82
disposed at the approximate center in the sheet width direction
from both sides. Accordingly, when one of the side fences 74A and
74B moves in the sheet width direction, the racks 81A and 81B of
the side fences 74A and 74B interlock to move in the sheet width
direction, thereby rotating the pinion 82. The rotation of the
pinion 82 causes the other racks 81B and 81A to move in the passing
direction along the sheet width direction, and in conjunction with
that, the other one of the side fences 74B and 74A moves in the
sheet width direction.
[0068] In the present embodiment, one of the racks 81A is engaged
with a gear (rotating member) 84. The gear 84 has a rotation shaft
84a, which is fitted into an engagement hole 83b on a rotor
(detected member) 83a of a rotary sensor 83 and connected. For
example, when a user moves the side fence 74A in the sheet width
direction, the rack 81A of the side fence 74A interlocks to move in
the sheet width direction, thereby rotating the gear 84 engaged
with the rack 81A. As a result, the rotor 83a of the rotary sensor
83 connected to the gear 84 rotates integrally with the gear 84,
and the rotation amount of the rotor 83a is detected by the rotary
sensor 83. The detection result (rotation amount of the rotor 83a)
of the rotary sensor 83 is transmitted to a control unit of the
image forming apparatus, and is used to determine, for example, the
size of the sheet S set on the sheet feeding tray 72 in the width
direction.
[0069] FIG. 10 is an enlarged view of the grip portion 74a provided
on one of the side fences 74B as viewed from the outside in the
sheet width direction.
[0070] The sheet feeding tray 72 according to the present
embodiment is configured such that the user grips the grip portion
74a provided on one of the side fences 74B and moves the side
fences 74A and 74B along a sheet width direction Y. Specifically,
as illustrated in FIG. 11A, the user grips the grip portion 74a
provided on one of the side fences 74B with his/her fingers in the
sheet width direction Y, and moves the side fences 74A and 74B
along the sheet width direction Y, for example. Alternatively, as
illustrated in FIG. 11B, the user may push the outer surface of the
grip portion 74a in the sheet width direction with his/her finger,
thereby moving the side fences 74A and 74B in the sheet width
direction Y, for example.
[0071] The sheet feeding tray 72 according to the present
embodiment has a configuration in which the side fences 74A and 74B
are guided by a single guide rail 75, and as illustrated in FIG. 10
and the like, the grip portion 74a is disposed at a position
overlapping the guide rail 75. Accordingly, when the user grips the
grip portion 74a and moves one of the side fences 74B in the sheet
width direction Y, a rotational moment centered on a guide pin 74b
of one of the side fences 74B does not occur, or its magnitude is
small even if the rotational moment occurs. Therefore, the contact
pressure between the guide pin 74b provided on one of the side
fences 74B and the guide rail 75 is relatively small, and the
frictional force at the time of sliding of both components is
small. In addition, the rack 81B provided on one of the side fences
74B moves approximately straight along its longitudinal direction,
a proper engagement state between the rack 81B and the pinion 82 is
maintained, the pinion 82 can rotate smoothly, and the moving load
received from the pinion 82 is also small. Therefore, one of the
side fences 74B and the other one of the side fences 74A moving in
conjunction with the side fence 74B can move smoothly.
[0072] However, there may be a case where, as illustrated in FIG.
12A, the user grips a portion other than the grip portion 74a on
one of the side fences 74B, or as illustrated in FIG. 12B, the user
pushes a portion other than the grip portion 74a with his/her
finger to attempt to move the side fence 74B. In that case, the
portion gripped or pushed by the user with his/her fingers is
largely shifted in the sheet feeding direction from the guide pin
74b of one of the side fences 74B fitted into the guide rail 75,
whereby a large rotational moment centered on the guide pin 74b
occurs. Therefore, force to rotate around the guide pin 74b acts on
one of the side fences 74B, and the rack 81B of one of the side
fences 74B is pressed against the pinion 82 accordingly, whereby
the contact pressure between the guide pin 74b of one of the side
fences 74B and the guide rail 75 increases by receiving the
reaction force. As a result, the frictional force between the guide
pin 74b and the guide rail 75 increases, and one of the side fences
74B and the other one of the side fences 74A that moves in
conjunction with the side fence 74B cannot move smoothly.
[0073] Also in a case where the user grips or pushes a portion
where a rotational moment in the reverse direction occurs with
his/her fingers, the frictional force between the guide pin 74b and
the guide rail 75 increases similarly, whereby one of the side
fences 74B and the other one of the side fences 74A that moves in
conjunction with the side fence 74B cannot move smoothly. In
addition, one of the side fences 74B tends to rotate in the
direction in which the rack 81B is away from the pinion 82 so that
the engagement between the rack 81B and the pinion 82 may be
disengaged, and in such a case, the sheet S cannot match the center
of the sheet placement surface 72B in the width direction.
Furthermore, the size of the sheet S set on the sheet feeding tray
72 in the width direction cannot be properly determined from the
detection result of the rotary sensor 83.
[0074] In view of the above, in the present embodiment, the
configuration of the side fence 74B is devised in such a manner
that the user does not grips a portion other than the grip portion
74a of the side fence 74B to move the side fence 74B.
[0075] FIG. 13A is a perspective view of the side fence 74B
including the grip portion 74a as viewed from the outside in the
sheet width direction.
[0076] FIG. 13B is a perspective view of the side fence 74B
including the grip portion 74a as viewed from the inside in the
sheet width direction.
[0077] FIG. 14 is a cross-sectional view of the grip portion 74a
cut by a plane orthogonal to the sheet feeding direction.
[0078] The side fence 74B according to the present embodiment
includes the grip portion 74a near the center of a sheet feeding
direction X. As illustrated in FIG. 14, in the grip portion 74a, an
end face 74al (hereinafter referred to as an "inner end face") on
the side in contact with the edge of the sheet S is a sheet
regulating surface extending in the normal direction of the sheet
placement surface 72B, and the edge of the sheet stacked on the
sheet placement surface 72B abuts on the inner end face 74al of the
grip portion 74a, thereby regulating the position of a bundle of
the sheets S in the width direction.
[0079] On the other hand, an end face 74a2 (hereinafter referred to
as an "outer end face") opposite to the inner end face 74al of the
grip portion 74a is an uneven surface in which unevenness is
continuous in the vertical direction so that the user's finger does
not slip in the vertical direction. As illustrated in FIGS. 7, 13A,
and 13B, the outer end face 74a2 of the grip portion 74a is in a
recessed shape as viewed in the normal direction of the sheet
placement surface 72B. This makes it difficult for the user's
finger to slip in the horizontal direction as well. Moreover, with
such an uneven surface and a recessed shape, the user can easily
recognize that the grip portion 74a is a portion to be gripped, and
it is suppressed that the user grips a portion other than the grip
portion 74a of the side fence 74B and moves the side fence 74B. In
particular, as illustrated in FIG. 8, a mark 74e is silk-printed on
the upper surface of the grip portion 74a to highlight the position
of the grip portion, which serves as assistance for the user to
easily recognize the position of the grip portion 74a when the user
looks at the side fence 74B from above.
[0080] The grip portion 74a is formed to be higher in height from
the sheet placement surface 72B than non-grip portions 74c and 74d
adjacent to the upstream side and the downstream side in the sheet
feeding direction. Therefore, the grip portion 74a is easier to
grip with the user's finger than the non-grip portions 74c and 74d.
Conversely, since the non-grip portions 74c and 74d are lower in
height from the sheet placement surface 72B than the grip portion
74a, it is more difficult for the user to grip than the grip
portion 74a. Therefore, it is suppressed that the user grips the
non-grip portions 74c and 74d, which are other than the grip
portion 74a of the side fence 74B, and moves the side fence
74B.
[0081] Moreover, in the non-grip portions 74c and 74d according to
the present embodiment, at least one end face in the sheet width
direction Y has a slope where a height from the sheet placement
surface 72B increases as it goes inward from the outside in the
sheet width direction Y. Specifically, as illustrated in FIG. 15,
the non-grip portion 74c adjacent to the downstream side of the
grip portion 74a in the sheet feeding direction has a slope 74c2 on
the end face outside in the sheet width direction, and as
illustrated in FIG. 16, the non-grip portion 74d adjacent to the
upstream side of the grip portion 74a in the sheet feeding
direction has slopes 74d1 and 74d2 on both end faces in the sheet
width direction Y. As a result, the user's finger is less likely to
be caught on the end face than in the case where the slope is a
plane orthogonal to the sheet placement surface 72B.
[0082] In a case where the slopes 74c2, 74d1, and 74d2 are planes
orthogonal to the sheet placement surface 72B like an inner end
face (sheet regulating surface) 74c1 of the non-grip portion 74c in
the sheet width direction as illustrated in FIG. 15, the user can
push the planes straight in the normal direction with his/her
finger to move the side fence 74B. Accordingly, a situation in
which the user's finger slips on the planes is unlikely to occur,
whereby the user can easily grip the non-grip portions 74c and 74d
and move the side fence 74B.
[0083] Meanwhile, in the case of the slopes 74c2, 74d1, and 74d2 as
in the present embodiment, the direction pushed by the user's
finger (direction parallel to the sheet width direction) is
inclined relative to the normal direction of the slopes 74c2, 74d1,
and 74d2. In that case, force is generated in the direction in
which the user's finger slides on the slope, whereby the user's
finger is likely to slip on the slope. Accordingly, even if the
user attempts to grip the non-grip portions 74c and 74d, which are
portions other than the grip portion 74a of the side fence 74B, to
move the side fence 74B, the finger slips and cannot successfully
move the side fence 74B. As a result, it is suppressed that the
user grips the non-grip portions 74c and 74d and moves the side
fence 74B.
[0084] In particular, the entire outer end faces of the non-grip
portions 74c and 74d according to the present embodiment are the
slopes 74c2 and 74d2, whereby there is substantially no portion at
which the user's finger can push the end face straight in the
normal direction. Therefore, it is more reliably suppressed that
the user grips the non-grip portions 74c and 74d and moves the side
fence 74B.
[0085] As illustrated in FIG. 15, the slope 74c2 according to the
present embodiment is a curved surface in which the angle between
tangent lines L1 and L2 and the sheet placement surface 72B
decreases as it goes inward from the outside in the sheet width
direction Y. With such a curved surface, the contact area with the
user's finger is made small, and the finger is further slippery,
whereby it is suppressed that the user grips the non-grip portion
74c and moves the side fence 74B. The same applies to the slopes
74d1 and 74d2 of the non-grip portion 74d.
[0086] Meanwhile, as illustrated in FIGS. 15 and 16, the inner end
faces of the non-grip portions 74c and 74d according to the present
embodiment have sheet regulating surfaces 74c1 and 74d3 extending
in the normal direction of the sheet placement surface 72B.
Accordingly, the edge of the sheet S placed on the sheet placement
surface 72B abuts on the sheet regulating surfaces 74c1 and 74d3 on
the inner end faces of the non-grip portions 74c and 74d, whereby
the position of the bundle of the sheets S in the width direction
can be regulated.
[0087] In particular, in the present embodiment, the entire inner
end face of the non-grip portion 74c adjacent to the grip portion
74a on the downstream side in the sheet feeding direction is the
sheet regulating surface 74c1, and the inner end face has no slope,
as illustrated in FIG. 15. In that case, when the user grips the
non-grip portion 74c, the user can push the sheet regulating
surface 74c1 straight in the normal direction with his/her finger,
whereby the effect of suppressing the situation in which the user
grips the non-grip portion 74c and moves the side fence 74B is
reduced.
[0088] However, for the user, it is generally easier to operate at
a position far from the outer wall surface of the image forming
apparatus main body 2 with respect to the side fence 74B on the
sheet feeding tray 72 protruding from the outer wall surface of the
image forming apparatus main body 2. In view of the above, the
non-grip portion 74c adjacent to the grip portion 74a on the
downstream side in the sheet feeding direction is at a position
near the image forming apparatus main body 2 on the sheet feeding
tray 72, which is at a position difficult to be operated by the
user within the side fence 74B. Therefore, it can be said that,
even if the suppression effect is reduced, the non-grip portion 74c
has less influence on the overall suppression effect.
[0089] Meanwhile, when the position of the sheet S placed on the
sheet placement surface 72B of the sheet feeding tray 72 in the
width direction is regulated, from the viewpoint of preventing skew
of the sheet S, for example, positional regulation of the sheet S
on the downstream side in the feeding direction is of higher level
of importance than positional regulation on the upstream side.
Therefore, in the present embodiment, the non-grip portion 74c
adjacent to the grip portion 74a on the downstream side in the
sheet feeding direction prioritizes the positional regulation even
if the suppression effect is reduced, and the entire inner end face
of the non-grip portion 74c serves as the sheet regulating surface
74c1 and has no slope.
[0090] In addition, the non-grip portion 74d adjacent to the grip
portion 74a on the upstream side in the sheet feeding direction is
at a position far from the image forming apparatus main body 2 on
the sheet feeding tray 72, which is at a position easily operated
by the user. Therefore, the entire inner end face of the non-grip
portion 74d does not serve as the sheet regulating surface 74d3 so
that the suppression effect is not reduced, and has the slope 74d1.
In that case as well, in consideration of the effect of suppressing
the situation in which the user grips the non-grip portion 74d and
moves the side fence 74B, half or more of the inner end face of the
non-grip portion 74d in the height direction is preferably the
slope 74d1. Note that, as illustrated in FIG. 17, the inner end
face of the non-grip portion 74d may be formed so that the entire
end face is a slope in the same manner as the outer end face.
[0091] Note that, although the sheet feeding tray 72 has been
described in the present embodiment, the sheet holding device
according to an embodiment of the present disclosure is not limited
to the sheet feeding tray 72 but may be, for example, a sheet
container in the sheet separating device 61 of the sheet feeder 4,
a placing table of the automatic document carrier 5 in the image
reading device, or the like as long as sheets are held.
[0092] The descriptions above represent merely an example, and
specific effects can be exerted in the following aspects.
[0093] First Aspect According to a first aspect, there is provided
a sheet holding device (e.g., sheet feeding tray 72) in which the
user grips a grip portion (e.g., grip portion 74a) of a sheet
regulating member (e.g., side fences 74A and 74B) movable in a
contacting direction (e.g., sheet width direction Y) to contact and
a separating direction to separate from an edge of a sheet (e.g.,
sheet S) placed on a sheet placement surface (e.g., sheet placement
surface 72B) and moves the sheet regulating member, in which a
non-grip portion (e.g., non-grip portions 74c and 74d) of the sheet
regulating member lower in height from the sheet placement surface
than the grip portion has, on at least one end face in the
contacting direction, a slope (e.g., slopes 74c2, 74d1, and 74d2)
whose height from the sheet placement surface increases toward a
center of the non-grip portion in the contacting direction or the
separating direction.
[0094] In the present aspect, since the non-grip portion of the
sheet regulating member is lower in height from the sheet placement
surface than the grip portion, it is more difficult for the user to
grip than the grip portion. Accordingly, the situation in which the
user grips the non-grip portion, which is a portion other than the
grip portion of the sheet regulating member, and moves the sheet
regulating member is suppressed.
[0095] Furthermore, the non-grip portion has, on at least one end
face in the contacting/separating direction, a slope in which the
height from the sheet placement surface increases as it goes inward
from the outside in the contacting/separating direction, whereby
the user's finger is less likely to be caught than in the case
where the end face is a plane orthogonal to the sheet placement
surface.
[0096] If the slope is a plane orthogonal to the sheet placement
surface, the user can push the plane straight in the normal
direction with his/her finger and move the sheet regulating member.
Accordingly, a situation in which the user's finger slips on the
plane is unlikely to occur, whereby the user can easily grip the
non-grip portion and move the sheet regulating member. Meanwhile,
in the case where at least one end face in the
contacting/separating direction is a slope as in the present
aspect, the direction pushed by the user's finger (direction
parallel to the contacting/separating direction) is inclined
relative to the normal direction of the slope. In that case, force
is generated in the direction in which the user's finger slides on
the slope, whereby the user's finger is likely to slip on the
slope. Accordingly, even if the user attempts to grip the non-grip
portion, which is a portion other than the grip portion of the
sheet regulating member, to move the sheet regulating member, the
finger slips and cannot successfully move the sheet regulating
member. As a result, the situation in which the user grips the
non-grip portion and moves the sheet regulating member is
suppressed.
[0097] Second Aspect
[0098] According to a second aspect, the whole of the at least one
end face is the slope in the first aspect.
[0099] According to the present aspect, there is substantially no
portion at which the user's finger can push the end face of the
non-grip portion straight in the normal direction, whereby the
situation in which the user grips the non-grip portion and moves
the sheet regulating member can be more reliably suppressed.
[0100] Third Aspect
[0101] According to a third aspect, the slope is a curved surface
in which the angle between the tangent line and the sheet placement
surface decreases inward in the contacting/separating direction in
the first or second aspect.
[0102] According to the present aspect, the contact area between
the end face of the non-grip portion and the user's finger is
smaller than in the case of a flat surface so that the finger is
further slippery, whereby the situation in which the user grips the
non-grip portion and moves the sheet regulating member is
suppressed.
[0103] Fourth Aspect
[0104] According to a fourth aspect, the non-grip portion has
slopes on both end faces in the contacting/separating direction in
any one of the first to third aspects.
[0105] According to the present aspect, any finger of the user
gripping the non-grip portion from both sides is slippery, whereby
the situation in which the user grips the non-grip portion and
moves the sheet regulating member is suppressed.
[0106] Fifth Aspect
[0107] According to a fifth aspect, in the fourth aspect, the
contacting/separating direction of the sheet regulating member is a
direction (e.g., sheet width direction Y) orthogonal to the sheet
conveyance direction (e.g., sheet feeding direction X), at least
two of the non-grip portions exist to sandwich the grip portion in
the sheet conveyance direction, and the non-grip portion 74d
positioned on the upstream side of the grip portion in the sheet
conveyance direction has the slopes 74d1 and 74d2 on both of the
end faces.
[0108] In general, the non-grip portion adjacent to the grip
portion on the upstream side in the sheet conveyance direction is
easier for the user to operate than the non-grip portion adjacent
to the grip portion on the downstream side in the sheet conveyance
direction. According to the present aspect, the non-grip portion
has slopes on both of the end faces so that the non-grip portion,
which tends to be operated by the user, is less likely to be
gripped, whereby the situation in which the user grips the non-grip
portion and moves the sheet regulating member can be effectively
suppressed.
[0109] Sixth Aspect
[0110] According to a sixth aspect, in any one of the first to
fifth aspects, the non-grip portion has the sheet regulating
surfaces 74c1 and 74d3 extending in the normal direction of the
sheet placement surface on the end face on the side in contact with
the edge of the sheet.
[0111] With this arrangement, positional regulation of the sheet
edge is made possible even at the portion of the non-grip portion
on the sheet regulating member.
[0112] Seventh Aspect
[0113] According to a seventh aspect, in the sixth aspect, the
contacting/separating direction of the sheet regulating member is
the direction orthogonal to the sheet conveyance direction, at
least two of non-grip portions exist to sandwich the grip portion
in the sheet conveyance direction, and the non-grip portion 74c
positioned on the downstream side of the grip portion in the sheet
conveyance direction has the sheet regulating surface 74c1.
[0114] As described above, when the position of the sheet placed on
the sheet placement surface in the width direction is regulated,
from the viewpoint of preventing skew of the sheet, for example,
positional regulation on the downstream side in the sheet
conveyance direction is of higher level of importance than
positional regulation on the upstream side. According to the
present aspect, it is possible to perform the positional regulation
in the sheet width direction with the non-grip portion adjacent to
the grip portion on the downstream side in the sheet feeding
direction.
[0115] Eighth Aspect
[0116] According to an eight aspect, in any one of the first to
seventh aspects, the sheet regulating member moves while being
guided by a single guide member (e.g., guide rail 75) extending in
the contacting/separating direction, and the grip portion is
disposed at a position overlapping the single guide member.
[0117] According to the present aspect, as described above, when
the user grips the grip portion and moves the sheet regulating
member in the contacting/separating direction, no rotational moment
is generated centered on the portion (guide pin 74b) on the sheet
regulating member guided by the single guide member, or its
magnitude is small even if the rotational moment is generated.
Accordingly, the contact pressure between the sheet regulating
member and the guide member is relatively small, and frictional
force at the time of sliding between the two components can be made
small. Therefore, when the user grips the grip portion and moves
the sheet regulating member, the sheet regulating member can be
moved smoothly.
[0118] Ninth Aspect
[0119] According to a ninth aspect, in any one of the first to
eight aspects, two of the sheet regulating members are provided to
regulate both edges of the sheet placed on the sheet placement
surface, the sheet holding device including a moving mechanism
(e.g., pinion rack mechanism) for moving, in conjunction with
movement of one of the two sheet regulating members, the other one
of the sheet regulating members.
[0120] According to the present aspect, the user can move the other
one of the sheet regulating members together by moving one of the
sheet regulating members.
[0121] Tenth Aspect
[0122] According to a tenth aspect, in any one of the first to
ninth aspects, at least one end face of the grip portion in the
contacting/separating direction has a recessed shape as viewed in
the normal direction of the sheet placement surface.
[0123] With this arrangement, when the user grips the grip portion,
the user's finger is less likely to slip in the direction parallel
to the sheet placement surface. The user can easily see and
recognize that the grip portion is a portion to be gripped, whereby
the situation in which the user grips a portion other than the grip
portion of the sheet regulating member and moves the sheet
regulating member is suppressed.
[0124] Eleventh Aspect
[0125] According to an eleventh aspect, in any one of the first to
tenth aspects, the sheet holding device is a sheet feeding
tray.
[0126] In the sheet feeding tray, sheets of various sizes tend to
be placed in turn, and the frequency with which the user moves the
sheet regulating member is high, whereby the situation in which the
user grips a portion other than the grip portion of the sheet
regulating member and moves the sheet regulating member occurs
frequently. According to the present aspect, the situation in which
the user grips a portion other than the grip portion of the sheet
regulating member on such a sheet feeding tray and moves the sheet
regulating member can be suppressed.
[0127] Twelfth Aspect
[0128] According to a twelfth aspect, there is provided an image
forming apparatus (e.g., copier 1) including a sheet holding device
(e.g., sheet feeding tray 72) in which a sheet holding device in
any one of the first to eleventh aspects is used as the sheet
holding device.
[0129] According to the present aspect, it is possible to provide
an image forming apparatus in which the situation where the user
grips a portion other than the grip portion of the sheet regulating
member and moves the sheet regulating member is suppressed.
[0130] Thirteenth Aspect
[0131] According to a thirteenth aspect, there is provided an image
reading device 3 including a sheet holding device (e.g., placing
table 5A) in which a sheet holding device in any one of the first
to eleventh aspects is used as the sheet holding device.
[0132] According to the present aspect, it is possible to provide
an image reading device in which the situation where the user grips
a portion other than the grip portion of the sheet regulating
member and moves the sheet regulating member is suppressed.
[0133] Numerous additional modifications and variations are
possible in light of the above teachings. It is therefore to be
understood that, within the scope of the above teachings, the
present disclosure may be practiced otherwise than as specifically
described herein. With some embodiments having thus been described,
it will be obvious that the same may be varied in many ways. Such
variations are not to be regarded as a departure from the scope of
the present disclosure and appended claims, and all such
modifications are intended to be included within the scope of the
present disclosure and appended claims.
* * * * *