U.S. patent application number 16/683257 was filed with the patent office on 2020-05-14 for pipeline exterior blasting system.
This patent application is currently assigned to ROBOTIC GRIT BLASTER, LLC. The applicant listed for this patent is JONATHAN STARKWEATHER PARTRIDGE. Invention is credited to JONATHAN PARTRIDGE, MICHAEL W. STARKWEATHER.
Application Number | 20200147757 16/683257 |
Document ID | / |
Family ID | 70551605 |
Filed Date | 2020-05-14 |
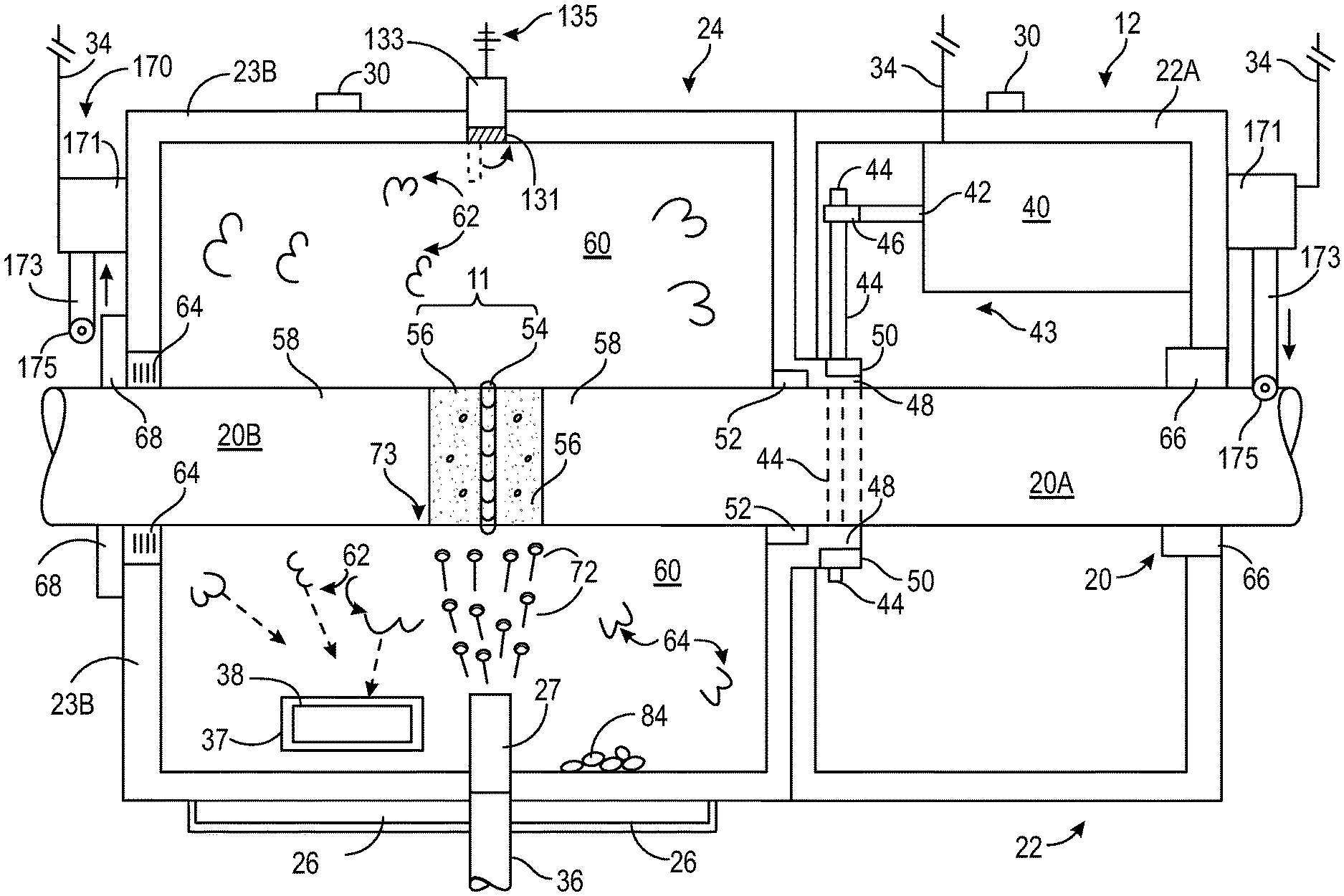



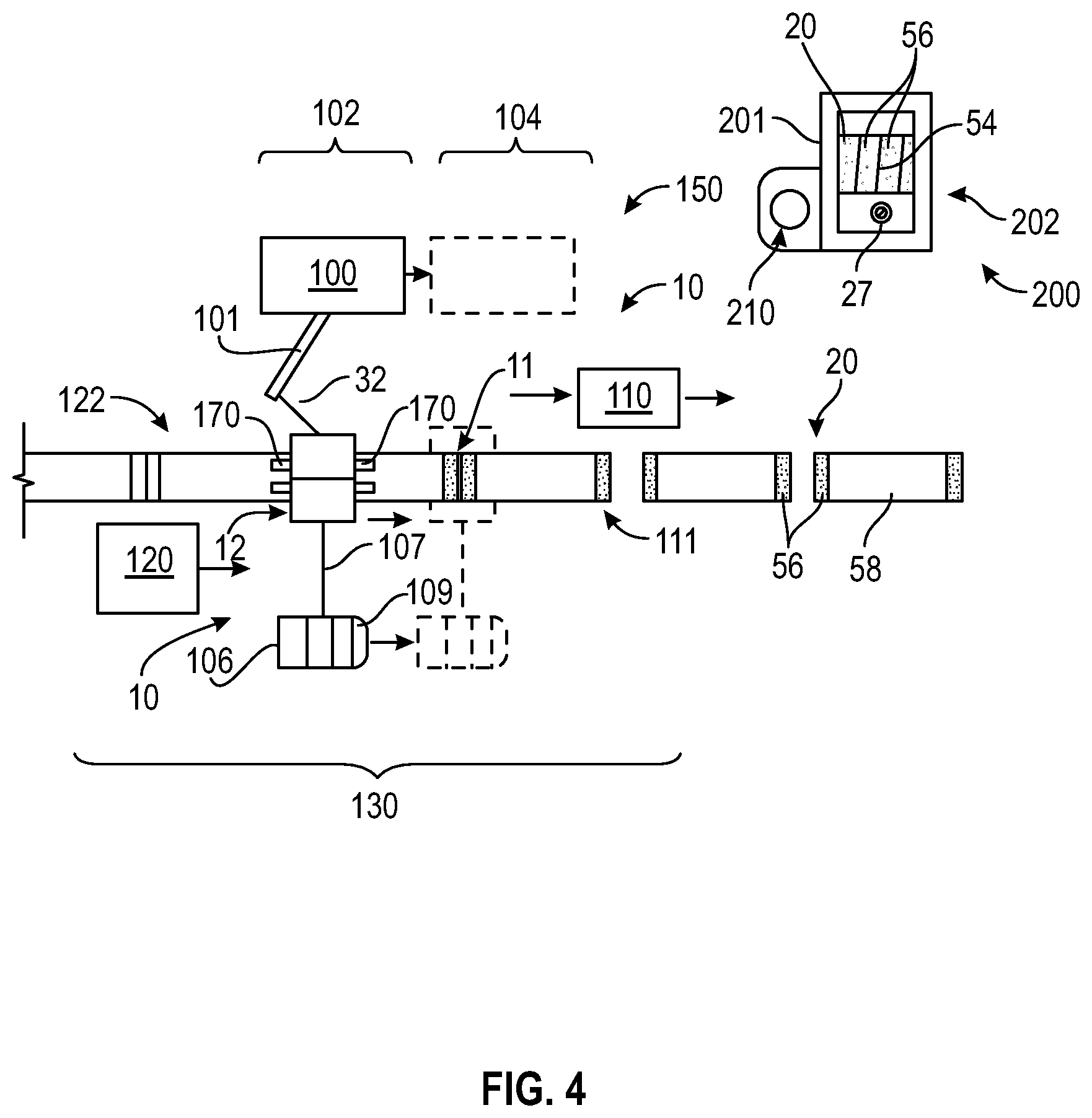
United States Patent
Application |
20200147757 |
Kind Code |
A1 |
PARTRIDGE; JONATHAN ; et
al. |
May 14, 2020 |
PIPELINE EXTERIOR BLASTING SYSTEM
Abstract
A pipeline exterior blasting system, movably mounted to a
pipeline, to blast only uncoated end sections of a first and second
pipe at a weld site where the first and second pipes were welded
together. Uniquely, there is a blasting containment device having:
a fixed portion 22; a rotating containment portion 24 rotatably
mounted to the fixed portion 22, and releasably and rotatively
coupled to the second pipe 20B; a support devices system 106,
coupled to the blasting containment device 12 via connections 107,
including: a blasting device 16, a vacuum device 18; and an
electrical power generator 14. Finally, there is a lateral movement
system, coupled to the blasting containment device 12, having: a
first position that holds the grit blasting containment device 12
in a fixed position as the grit blasting containment device blasts
particles circumferentially around the two pipes; a second position
that moving the grit blasting containment device off of the two
pipes; and a third position that provides movement of the grit
blasting containment device along the two pipes.
Inventors: |
PARTRIDGE; JONATHAN;
(SPANISH FORK, FL) ; STARKWEATHER; MICHAEL W.;
(TAMPA, FL) |
|
Applicant: |
Name |
City |
State |
Country |
Type |
PARTRIDGE; JONATHAN
STARKWEATHER; MICHAEL W. |
SPANISH FORK
TAMPA |
FL
FL |
US
US |
|
|
Assignee: |
ROBOTIC GRIT BLASTER, LLC
Tampa
FL
|
Family ID: |
70551605 |
Appl. No.: |
16/683257 |
Filed: |
November 13, 2019 |
Related U.S. Patent Documents
|
|
|
|
|
|
Application
Number |
Filing Date |
Patent Number |
|
|
62766993 |
Nov 14, 2018 |
|
|
|
Current U.S.
Class: |
1/1 |
Current CPC
Class: |
B24C 3/32 20130101; B24C
3/06 20130101; B24C 5/04 20130101; B24C 1/04 20130101 |
International
Class: |
B24C 3/32 20060101
B24C003/32; B24C 1/04 20060101 B24C001/04; B24C 3/06 20060101
B24C003/06 |
Claims
1. A pipeline exterior blasting system 10, movably mounted to a
pipeline 20, to blast only uncoated end sections of a first and
second pipe 20A and 20B at a weld site where the first and second
pipes were welded together, comprising: a) a blasting containment
device 12 having: i) a fixed portion 22, having: a. a releasable
holder 66 that releasably attaches to the first pipe 20A, to hold
the fixed portion 22 in position during blasting operation; b. a
motor 40, coupled to the fixed portion 22; c. a linkage system 42,
44, 46, 50, with one end coupled to the motor 40; ii) a rotating
containment portion 24 rotatably mounted to the fixed portion 22,
and releasably and rotatively coupled to the second pipe 20B;
having: a. a linkage engagement portion 48, coupled to a second end
of the linkage system 42, 44, 46, 50; b. a blasting nozzle 27,
directed at the weld site; c. a vacuum hose 38, oriented to suck
out airborne dust; d. a support device 68, abutting to the second
pipe 20B, positioned to rotatively move around the second pipe as
the rotating containment portion 24 circumferentially moves around
the second pipe; b) a support devices system 106, coupled to the
blasting containment device 12 via connections 107, including: i) a
blasting device 16, coupled to the blasting containment portion 22
via a blasting material delivery hose 36 and the material blasting
nozzle 27, to enable delivery of blasting material 72 to the
material blasting nozzle 27 at high air pressure and speed, and
thereby impacting the weld site 11 with the blasting material 72;
ii) a vacuum device 18, coupled to the blasting containment device
12, via a vacuum port 37, to enable resulting dust 62 to be
vacuumed out of the blasting containment device after impacting the
weld site 11 with the blasting material 72; and iii) an electrical
power generator 14, electrically coupled via electrical cord 34 to
the grit blasting containment device 12, the grit blasting device
16, and the grit vacuum device 18 to enable electrical power to be
provided thereto; and c) a lateral movement system, coupled to the
blasting containment device 12, having: iv) a first position that
holds the grit blasting containment device 12 in a fixed position
as the grit blasting containment device blasts particles
circumferentially around the two pipes; v) a second position that
moving the grit blasting containment device off of the two pipes;
and vi) a third position that provides movement of the grit
blasting containment device along the two pipes.
2. The system of claim 1, wherein the lateral movement system
includes: a) a first and second releasable holder devices 35,
mounted to the fixed portion 22 and rotating containment portion 24
respectively; b) a connector 33, inserted through the releasably
first and second holder devices 35; and c) a vehicle 100 with a
lifting device 101 that is releasably couplable to the connector
35.
3. The system of claim 1, wherein lateral movement device includes
a remote controlled vehicle 170, coupled to the grit blasting
containment device 12, and positioned on a top portion of the
pipeline 20 during movement thereof, having a carriage 175, movable
into a first position that moves the grit blasting containment
device 12 along the pipeline 20.
4. The system of claim 3, further includes: a) a camera 133,
mounted to the rotatable containment portion 24 oriented to send
real time images of the pipeline 20 relative positioning thereto,
and to enable proper alignment of the blasting nozzle 27 with the
welding site 11; and b) a remote viewing system 200, in controlling
communication with the remote controlled vehicle 170, sending
controlling signals to the remote controlled vehicle 170 to move
the grit blasting containment device 12 forward and backward along
the pipeline 20.
5. A method 150 of progressive welding, cleaning and coating a
pipeline, comprising the steps of: a) providing at least a first,
second, third, and forth pipe, each progressively lined up end to
end, wherein the site of the first and second abutting pipe ends
111 are not welded, the site of the second and third abutting pipe
ends 11 are welded, and the site of the third and forth abutting
pipe ends 122 are welded and cleaned; b) providing a welding system
110 at the site of the first and second abutting pipe ends 111; c)
providing a blasting containment device 12 at the site of the
second and third abutting pipe ends 11, that is removably coupled
around the second and third pipe ends 11; d) providing a pipe
protective coating application system 120 at the site of the third
and forth abutting pipe ends 122; d) providing a blasting
containment device moving system; e) welding the first and second
abutting pipe ends with the welding system 110; f) blasting the
second and third abutting pipe ends 11 with the blasting
containment device 12 without allowing dust from the blasting to
escape from the blasting containment device 12; g) coating the
third and forth abutting pipe ends 122 using the pipe protective
coating application system 120; and h) after completing the
welding, blasting and coating steps, performing the following
steps: i) releasing the blasting containment device 12 from being
coupled around the second and third pipe ends 11; ii) moving the
welding system 110 to a subsequent site where two subsequent pipe
ends are not welding together; iii) moving the blasting containment
device 12, via the blasting containment device moving system, to a
subsequent site where two subsequent pipe ends are welded together
but not coated by the pipe protective coating application system
120; and iv) moving the pipe protective coating application system
120 to a subsequent site where two subsequent pipe ends were
previously welded together and previously blasted by the blasting
containment device 12.
6. The method of claim 5, wherein the blasting containment device
moving system includes a vehicle with a boom arm coupled to a cable
attached to the blasting containment device 12.
7. The method of claim 5, wherein the blasting containment device
moving system includes a remote control vehicle mounted above the
pipeline 20 and coupled to the blasting containment device 12.
8. The method of claim 7, wherein the blasting containment device
12 is coupled to a support system 106 having: a power system 14, a
blasting material delivery system 16, and a vacuum system 18.
Description
CROSS REFERENCE TO RELATED APPLICATION
[0001] This application claims the benefit of copending U.S.
Provisional Application No. 62/766,993, having the at least one
inventor in common, filed Nov. 14, 2018, titled: "THE ROBOTIC GRIT
BLASTER."
BACKGROUND OF THE INVENTION
(1) Field of the Invention
[0002] This invention relates generally to the field of robotic
grit blasting tool, and more particularly to a system and device
for automatically blasting the welded site of a pipeline or two
pipes with blast material, to clean and prepare the surface prior
to coating that portion of the pipe with an environmental
protective coating layer, and blasting without contaminating the
surrounding work site with the grit material and unwanted dust, and
providing a safer work site for workers by eliminating the need to
wear full hazardous containment suits to perform such blasting
operations.
(2) Background of the Invention
[0003] The present invention relates generally to the field of
robotic grit blasting tool, and more particularly to a device for
automatically blasting the welded site of a pipe with grit material
to clean and prepare the surface prior to coating the pipe with a
environmental protective coating layer without contaminating the
work site with the grit material and providing a safer work site by
eliminating the workers need to wear full hazardous containment
suits.
[0004] It is well known that pipeline are often buried in the
ground for many years, which expose the iron based pipe to
environmental conditions that often will cause an eroding of the
pipe due to rusting and oxidation effects. Therefore, when
initially building a pipeline, the individual pipe sections are
typically coated with a protective coating prior to shipment to the
work site, where they are welded together to for the continuous
pipeline. By coating the pipe sections prior to the shipment, it is
possible to coat the majority of the pipe, often being 60 feet or
so. However, it is found that the coating material will interfere
with the welding process taking place at the ends of the pipes, so
those portions, from 2 to 24 inches at each end of the pipe, are
typically left exposed and not coated prior to shipment. As a
result, the now welded ends of the pipe must be coated to protect
the complete pipe from the deleterious effects from the
environmental oxidation, corrosion and rusting effects. However,
prior to applying the last coating of the pipe ends, the exposed
pipe sections must be cleaned after the welding process to remove
any oxidation and rusting and to rough up or pit the surface of the
pipe to increase the surface area and create holding spots for the
coating material to adhere to in an effective manner.
[0005] The common process for preparing the welded pipe ends is
currently complex and hazardous to the environment and toxic to the
workers. For example, and as a first step of the blasting process
of the welded pipe sections, the work site must be completely
sectioned off from the surrounding environment to prevent any of
the hazardous blasting material and dust from freely becoming
airborne and contaminating a large areas or exposing workers
respiratory air tracts to the hazardous aerosol and carcinogenic
contaminants. Wherein, erecting a tent around the selected welded
pipe sections typically is undertaken. This tent erection and
takedown step will take a great deal of employee time. It is noted
that to just complete on mile of pipeline, there may be 100 weld
sites or more. A typical pipeline may extend for hundreds or
thousands of miles, requiring tens of thousands of tent erection
and take down processes.
[0006] Next, the workers must be completely protected from coming
in contact to the hazardous materials, including skin contact and
respiratory airways. This step requires each worker to don a
complete head to toe hazardous material (haz-mat) protection suit.
These "haz-mat" suits make it difficult for the workers to do their
job in that they are cumbersome and create a very hot personal
space for the workers, especially during sunny days where the
ambient temperatures may reach 90 to 110 degrees Fahrenheit.
[0007] Now that the selected individual pipe weld site is contained
and the workers are properly protected, the blasting equipment must
be oriented, positioned and activated. Specifically, the typical
blasting equipment often includes a power source, a hopper for
holding the blasting material, a blasting air compressor pump, a
long hose with a nozzle, there may be other parts like individual
motors and hoppers, and electrical wiring and controllers which are
not detailed at this time.
[0008] Now that the blasting equipment, site contamination tent,
and worker protections are in place, the blasting process is now
ready to take place. This is assuming that the pipe weld section
has all along been elevated about the ground usually one to two
feet. Now the worker takes the blasting nozzle into the tent and
begins to blast the individual pipe weld section. This process
entails the worker directing the nozzle all around the complete
circumference of the pipe weld section. Given that the worker is in
a confined space, which is now being filled with a thick cloud of
blasting dust that is exiting the nozzle at 100 to 1600 lbs. of
pressure (psi), the worker is responsible to provide a completely
uniform circumferential cleaning of the pipe welded section. This
operation requires both visual inspect as the work advances, and to
specifically inspect not only the sides and top, but also the
bottom section of the pipe, which is only one to two feet above
ground, and requires the worker to get on their hands and knees
each time on each side of the pipe to inspect the cleaning quality
all while wearing a haz-mat suit that has restricted visual
capabilities or flexibility. In short, one can imagine that it is
very difficult to achieve a consistent high quality blast cleaning
product under these conditions in a single blasting of an
individual pipe weld section, let alone repeat this process
consistently for tens of thousands of operations.
[0009] One might imagine that the process is now complete, but they
would be mistaken; the cleanup process must now take place.
Ideally, the blast material is contained in the tent, but now the
hazardous blast material is now all over the ground under the tent.
So the tent must now be taken down, and the ground under the tent
must now be decontaminated by removing all the hazardous material
from the ground. This removal is typically done by workers, still
wearing haz-mat suits, taking shovels and digging up the ground and
placing the contaminated ground in a haz-mat disposal bag; whereby
the haz-mat bags are then loaded onto trucks and transported to
approved costly disposal sites.
[0010] Therefore, it s now clear and obvious that the current
methods and took used in cleaning the welded pipe sections is time
consuming, and adds great costs to the overall pipeline
construction project. Further, pipeline blasting is also fraught
with unsafe and hazardous working conditions. Additionally, the
overall goal of achieving consistent and uniform quality cleaning
and the pipeline coating preparation is completely out of quality
control by any process engineering guidelines.
[0011] As such, there has been demonstrated that there is a great
need for a new system and tool that is capable of eliminating the
afore described problems with the cleaning of the welded pipe
sections. Specifically, there is described hereinafter a new
inventive process and tool that would work without detrimentally
impacting the environment, without subjecting workers to unsafe and
hazardous working conditions, allowing the process to take less
overall time and expense, providing a consistent quality of
cleaning and surface preparation for thousands of applications, and
prevent environmental contamination and eliminate the ground
cleaning operations.
[0012] The following patents and applications are presented for
background purposes, and are herein incorporated by reference for
their supportive teachings to support the present invention, which
review hereof would easily assist and enable one skilled in the art
to more easily understand the potential operations of various
aspects of the presently described invention, in which:
[0013] U.S. Pat. No. 5,398,461, issued Mar. 21, 1995 to Rose,
entitled Apparatus and method for cleaning a pipeline, teaches of
an apparatus for cleaning the outer surface of a pipeline including
a self propelled carriage supported on the pipeline for
movement.
[0014] U.S. Pat. No. 5,458,683, issued Oct. 17, 1995 to Taylor et
al., entitled Device for surface cleaning, surface preparation and
coating applications, discloses a pipeline treating apparatus that
has a pair of pivotally mounted housing sections and a pair of
separately pivotal nozzle frames.
[0015] U.S. Pat. No. 9,415,426, issued Aug. 16, 2016 to Blake et
al. entitled Pipe cleaning apparatus, discloses a pipe cleaning
apparatus with a support frame having an elongated carriage frame
member, at least one pipe blasting assembly carried by the carriage
frome member of the apparatus support frame and including an
assembly carriage carried by the carriage frame member.
[0016] U.S. Pat. No. 1,815,573, issued Jul. 21, 1931 to McManis,
entitled Device for cleaning the outside of pipes, disclose an
apparatus for cleaning and removing rust, scale and other corrosion
and foreign matter adhering to the outside of pipes.
[0017] U.S. Pat. No. 2,460,989, issued Feb. 8, 1949 to Kramer,
entitled a Pipe cleaning machine, discloses a machine for cleaning
metal pipe where it is desired to remove mill scale, rust or
portions of previously applied coating material.
[0018] U.S. Pat. No. 4,603,516, issued Aug. 5, 1986, to Hoffman,
entitled Self propelled pipe blast cleaner capable of travel along
a pipeline supported over the ditch, teaches of a device that
continuously blast cleans the outside of the pipe in advance of
pipe coating or wrapping.
[0019] U.S. Pat. No. 5,199,226, issued Apr. 6, 1993 to Rose,
entitled a Method and apparatus for removing outer coatings from
pipe, discloses a coating removal machine for a pipe that has an
enclosed housing extending about front and rear tool carriers,
which rotate in opposite directions about the pipe and have coating
removal tools for removing the coating material from the pipe.
[0020] U.S. Pat. No. 4,333,277, issued Jun. 8, 1982 to Tasedan,
entitled Combination sand-blasting and vacuum apparatus, which
teaches providing a sand blasting gun having an air inlet passage
and a sand inlet passage and a vacuum chamber coupled to the end of
the sand blasting gun therein to thereby suck the sand out of the
vacuum chamber and through a sand outlet passage to a sand storage
container.
[0021] U.S. Pat. No. 5,531,634, issued Jul. 2, 1996 to Schott,
Method of using an abrasive material for blast cleaning of solid
surfaces, which teaches providing a blasting pot, a blasting hose
and spray nozzle connected to the blasting pot, an air compressor
and compressor air lines connected to the blasting pot.
[0022] U.S. Pat. No. 4,771,579, issued Sep. 20, 1988 to Giese,
entitled Abrasive blast media recovery and cleaning for reuse,
which teaches providing a first vacuum system vacuums up spent
contaminated blast media from a work site and entrains it in an
airstream.
[0023] Many methods and systems are currently utilized to clean and
prep pipes, but none of them teach by themselves or in combination
thereof the key elements of the currently disclosed pipeline
cleaning and surface preparation machine enabling environmental and
safe working conditions and other features taught in the subsequent
specification.
SUMMARY
[0024] In view of the foregoing disadvantages inherent in the known
types of apparatus like in the prior art, the present invention
provides an improved apparatus. As such, the general purpose of the
present invention, which will be described subsequently in greater
detail, is to provide a new and improved apparatus with all the
advantages of the prior art and none of the disadvantages.
[0025] In one embodiment of the invention, there may be a pipeline
exterior blasting system 10, movably mounted to a pipeline 20, to
blast only uncoated end sections of a first and second pipe 20A and
20B at a weld site where the first and second pipes were welded
together, comprising: a blasting containment device 12 having: a
fixed portion 22, having: a releasable holder 66 that releasably
attaches to the first pipe 20A, to hold the fixed portion 22 in
position during blasting operation; a motor 40, coupled to the
fixed portion 22; a linkage system 42, 44, 46, 50, with one end
coupled to the motor 40; a rotating containment portion 24
rotatably mounted to the fixed portion 22, and releasably and
rotatively coupled to the second pipe 20B; having: a linkage
engagement portion 48, coupled to a second end of the linkage
system 42, 44, 46, 50; a blasting nozzle 27, directed at the weld
site; a vacuum hose 38, oriented to suck out airborne dust; a
support device 68, abutting to the second pipe 20B, positioned to
rotatively move around the second pipe as the rotating containment
portion 24 circumferentially moves around the second pipe; a
support devices system 106, coupled to the blasting containment
device 12 via connections 107, including: a blasting device 16,
coupled to the blasting containment portion 22 via a blasting
material delivery hose 36 and the material blasting nozzle 27, to
enable delivery of blasting material 72 to the material blasting
nozzle 27 at high air pressure and speed, and thereby impacting the
weld site 11 with the blasting material 72; a vacuum device 18,
coupled to the blasting containment device 12, via a vacuum port
37, to enable resulting dust 62 to be vacuumed out of the blasting
containment device after impacting the weld site 11 with the
blasting material 72; and an electrical power generator 14,
electrically coupled via electrical cord 34 to the grit blasting
containment device 12, the grit blasting device 16, and the grit
vacuum device 18 to enable electrical power to be provided thereto;
and a first position that holds the grit blasting containment
device 12 in a fixed position as the grit blasting containment
device blasts particles circumferentially around the two pipes; a
second position that moving the grit blasting containment device
off of the two pipes; and a third position that provides movement
of the grit blasting containment device along the two pipes.
[0026] In another embodiment, wherein the lateral movement system
is a remote control system 170, coupled to the grit blasting
containment device 12, having a remote control movement system 170.
Also, the lateral movement system includes a first and second
releasable holder devices 35, mounted to the fixed portion 22 and
rotating containment portion 24 respectively; a connector 33,
inserted through the releasably first and second holder devices 35;
and a vehicle 100 with a lifting device 101 that is releasably
couplable to the connector 35.
[0027] In another embodiment the lateral movement device includes a
friction reduction device that reduces friction between the grit
blasting containment device and the pipeline 20, wherein the
lateral movement device remains in contact with a length of the
pipeline 20 during lateral movement towards a subsequent work site
of the grit blasting containment device 12 while being positioned
atop the pipeline 20.
[0028] In an additional embodiment there may be a friction
reduction device that includes a remote controlled vehicle 170,
coupled to the grit blasting containment device 12, and positioned
on a top portion of the pipeline 20 during movement thereof, having
a carriage 175, movable into a first position that moves the grit
blasting containment device 12 along the pipeline 20.
[0029] In yet another potential embodiment of the invention that
could be a camera 133, mounted to the rotatable containment portion
24 oriented to send real time images of the pipeline 20 relative
positioning thereto, and to enable proper alignment of the blasting
nozzle 27 with the welding site 11; and a remote viewing system
200, in controlling communication with the remote controlled
vehicle 170, sending controlling signals to the remote controlled
vehicle 170 to move the grit blasting containment device 12 forward
and backward along the pipeline 20.
[0030] There is disclosed one embodiment of a method 150 of
progressive welding, cleaning and coating a pipeline, comprising
the steps of:
[0031] a) providing at least a first, second, third, and forth
pipe, each progressively lined up end to end, wherein the site of
the first and second abutting pipe ends 111 are not welded, the
site of the second and third abutting pipe ends 11 are welded, and
the site of the third and forth abutting pipe ends 122 are welded
and cleaned;
[0032] b) providing a welding system 110 at the site of the first
and second abutting pipe ends 111;
[0033] c) providing a blasting containment device 12 at the site of
the second and third abutting pipe ends 11, that is removably
coupled around the second and third pipe ends 11;
[0034] d) providing a pipe protective coating application system
120 at the site of the third and forth abutting pipe ends 122;
[0035] d) providing a blasting containment device moving
system;
[0036] e) welding the first and second abutting pipe ends with the
welding system 110;
[0037] f) blasting the second and third abutting pipe ends 11 with
the blasting containment device 12 without allowing dust from the
blasting to escape from the blasting containment device 12;
[0038] g) coating the third and forth abutting pipe ends 122 using
the pipe protective coating application system 120; and
[0039] h) after completing the welding, blasting and coating steps,
performing the following steps: [0040] i) releasing the blasting
containment device 12 from being coupled around the second and
third pipe ends 11; [0041] ii) moving the welding system 110 to a
subsequent site where two subsequent pipe ends are not welding
together; [0042] iii) moving the blasting containment device 12,
via the blasting containment device moving system, to a subsequent
site where two subsequent pipe ends are welded together but not
coated by the pipe protective coating application system 120; and
[0043] iv) moving the pipe protective coating application system
120 to a subsequent site where two subsequent pipe ends were
previously welded together and previously blasted by the blasting
containment device 12.
[0044] In another potential embodiment of the method of operation,
the blasting containment device moving system includes a vehicle
with a boom arm coupled to a cable attached to the blasting
containment device 12.
[0045] In another potential embodiment of the method of operation,
the blasting containment device moving system includes a remote
control vehicle mounted above the pipeline 20 and coupled to the
blasting containment device 12.
[0046] In another potential embodiment of the method of operation,
the blasting containment device 12 is coupled to a support system
106 having: a power system 14, a blasting material delivery system
16, and a vacuum system 18.
[0047] There has thus been outlined, rather broadly, the more
important features of the invention in order that the detailed
description thereof that follows may be better understood and in
order that the present contribution to the art may be better
appreciated.
[0048] Numerous objects, features and advantages of the present
invention will be readily apparent to those of ordinary skill in
the art upon a reading of the following detailed description of
presently preferred, but nonetheless illustrative, embodiments of
the present invention when taken in conjunction with the
accompanying drawings. The invention is capable of other
embodiments and of being practiced and carried out in various ways.
Also, it is to be understood that the phraseology and terminology
employed herein are for the purpose of descriptions and should not
be regarded as limiting.
BRIEF DESCRIPTION OF THE DRAWINGS
[0049] To further clarify various aspects of some example
embodiments of the present invention, a more particular description
of the invention will be rendered by reference to specific
embodiments thereof that are illustrated in the appended drawing.
It is appreciated that the drawing depicts only illustrated
embodiments of the invention and are therefore not to be considered
limiting of its scope. The invention will be described and
explained with additional specificity and detail through the use of
the accompanying drawing in which:
[0050] FIG. 1 is a representative view of various devices used in
the present invention.
[0051] FIG. 2 is a representative view of a cross section in the
present invention.
[0052] FIG. 3 is a representative end view of the present
invention.
[0053] FIG. 4 is a schematic view of an inventive pipeline welding,
cleaning, and coating process.
DETAILED DESCRIPTION OF THE INVENTION
[0054] The embodiments of the present disclosure described below
are not intended to be exhaustive or to limit the disclosure to the
precise forms disclosed in the following detailed description.
Rather, the embodiments are chosen and described so that others
skilled in the art may appreciate and understand the principles and
practices of the present disclosure.
[0055] The following embodiments and the accompanying drawings,
which are incorporated into and form part of this disclosure,
illustrate embodiments of the invention and together with the
description, serve to explain the principles of the invention. To
the accomplishment of the foregoing and related ends, certain
illustrative aspects of the invention are described herein in
connection with the following description and the annexed drawings.
These aspects are indicative, however, of but a few of the various
ways in which the principles of the invention can be employed and
the subject invention is intended to include all such aspects and
their equivalents. Other advantages and novel features of the
invention will become apparent from the following detailed
description of the invention when considered in conjunction with
the drawings.
[0056] This section, requiring all discussions of every Figure
taken together and the prior incorporated art presented in the
Background section herein, summarizes some aspects of the present
disclosure and briefly introduces some preferred embodiments.
Simplifications or omissions in this section as well as in the
abstract or the title of this description may be made to avoid
obscuring the purpose of this section, the abstract and the title.
Such simplifications or omissions are not intended to limit the
scope of the present disclosure nor imply any limitations.
[0057] Turning now to all of the figures and specifically to FIG.
1, which presents a representative view of some of the various
parts used in the present invention 10. Specifically, the pipeline
grit blasting system 10 is releasably mounted to a pipeline welded
section 11, and includes a grit blasting containment device 12, a
electrical power generator 14, a grit blasting device 16, and a
grit vacuum device 18. Specifically, the grit blasting containment
device 12 includes fixed portion 22, and a rotating containment
portion 24, a heavy grit capture portion 26, a single grit blasting
nozzle portion 27, a fixed attachment portion 28, and a hinged
device 30. Additionally, there is illustrated electrical power
lines 34 coupled as illustrated to all of the associated parts
needed power for operation as is well known in the industry.
Moreover, there is illustrated a grit blasting material hose 36 to
deliver blasting material to the nozzle portion 27. Additionally,
there is illustrated a vacuum hose 38 coupled between the vacuum
device 16 and the grit blasting containment device 12. Taken
together, the electrical power generator 14, the grit blasting
device 16, and the grit vacuum device 18 along with their
respective connections 107, (comprising 34, 36 and 38), form a
support devices system 106. There is also a catch device 26 for
catching heavy blast material when the grit blasting containment
device 12 is opened.
[0058] In another embodiment, there are several releasably holder
devices 35, illustrated in the form of rings, that are mounted to
the fixed portion 22 and rotating containment portion 24, whereby a
connector 33, illustrated in the form of a rod, may be inserted
through some or all of the releasably holder devices 35. Wherein,
if the connector 33 is pulled out from the releasably holder
devices 35 that are attached only to the rotating containment
portion 24, then rotation of the rotating containment portion 24 is
enabled relative to the fixed portion 22. Likewise, if the
connector 33 is inserted through all of the releasably holder
devices 35, a releasable gripper 31 may be attached thereto, and
thus allowing a connected lifting device 32, in the form of a
cable, to lift, remove, elevate, and relocate the entire robotic
grit blaster 10 from its current location on the pipeline 20 and
move it to a subsequent selected operational work site. In summary,
there are two positions for the connector 33 to allow for two
different operations of the entire robotic grit blaster 10; namely,
rotation of the rotating containment portion 24, and the
transporting of the entire robotic grit blaster 10.
[0059] In an alternative embodiment, there is illustrated in the
figures, a propulsion system 170, which will be further detailed in
subsequent figures. If such a propulsion system 170 is employed,
then there may not be required to have the connector 33 the holder
devices 35, a the releasable gripper 31. The propulsion system will
be able to lift up the grit blasting containment device 12 from off
of the pipe 20 and self propel it down the length of the pipe 20 to
a next work site. One skilled in the art will easily contemplate
this propelling operation upon review of the subsequent figures and
related elements presented therein.
[0060] Referring to all of the figures and specifically to FIG. 2,
which presents a representative view of a cross section in the
present invention. In addition to the previously introduced
elements in discussion regarding FIG. 1, there is illustrated the
following elements forming one embodiment of the presently
presented invention. Specifically, within the fixed portion 22 and
fixed portion wall 22A of the grit blasting containment device 12,
there may be a motor 40 coupled to the electric power line 34 with
a typical rotor shaft 42 extending therefrom. There may be a first
coupling device 46 (which may be a gear) mounted on the rotor shaft
42, and being designed to positively engage a linkage device 44
(which may be a bicycle like chain) that may be positively engaged
to a second coupling device 50 (which may be a second gear) that is
fixedly mounted to a first portion 48 that may be coupled to the
rotating containment portion wall 24A. It is noted that the entire
system may be referred to as a linkage system 43 collectively,
which would include all of the needed parts (42, 44, 46, 48, 50) to
cause the rotation of the rotating containment portion 24.
[0061] In an alternative embodiment regarding the propulsion system
170 discussed previously, there is further illustrated in FIG. 2 an
operating unit 171, an extendible linkage unit 173, and a moving
carriage unit 175. Wherein, the operating control unit 171 contains
mechanical and electrical elements to engage and augment the
extending and contracting of the linkage unit 173 toward and away
from the pipe 20 in a controlled and directed fashion. The
operating control unit 171 may use any known radio, Wi-Fi, blue
tooth, direct circuitry, controls and sensors to move the carriage
unit 175 into and away from contact with the pipe 20, much like a
remote control vehicle, which are well known in the art. The
carriage unit 175 may contain any form of wheels and gears or
linkages sufficient to enable the operating control unit 171 to
enable the carriage unit 175 to extend from a retracted position,
to then engage the pipe 20, then to keep extending and thereby
pushing against the pipe 20 with sufficient force to lift the grit
blasting containment device 12, and the two halves 23A and 23B off
of the pipe, much like butter fly wings or a clam shelf opening and
closing. Thereafter, the carriage unit 175 could be activated like
a remote control vehicle to forcibly move the grit blasting
containment device 12 along the pipe 20 to a subsequent position.
The following US patents are herein incorporated by reference for
their supportive teaching on automated pipeline moving systems and
remote control vehicles to illustrate the well known art of moving
objects along a pipeline, and other features needed for the
functioning of the presently described invention 10, including:
U.S. Pat. Nos. 4,092,950, 4,563,841, 5,022,812, 5,337,846,
6,461,231, 5,046,289, 5,136,969 5, 5,205,058, 5,596,319, 5,644,113,
6,030,169, 6,439,956, and U.S. Pat. Nos. 6,746,304, 8,396,611.
[0062] It is noted that the propulsion system 170 illustrated in
FIG. 1, shows the two different positions that may be employed.
Namely, the left side is retracted away from the pipe 20 and would
be the position when the blasting operation is underway, and the
right side is in an extended to be in contact with the pipe 20,
which is the position requisite for opening the two wall halves 23A
and 23B and thus lifting the entire blasting device 12 off of the
pipe 20. It is noted that these two left and right side depictions
only illustrate the two positions that will simultaneously be
undertaken by the right and left sides when engaging in the
rotation and lateral movement processes.
[0063] In operation of the rotation of the rotating containment
portion 24, and in reference to all of the figures, as the motor 40
is activated, the rotor shaft 42 will rotate accordingly, thereby
causing the first coupling device 46 to also rotate, which will
engage the linkage device 44 and thereby cause the first portion 48
to rotate since the second coupling device 50 is fixed thereto and
coupled to the linkage device 44. Therefore, the entire rotating
containment portion 24 will be caused to rotate about and relative
to the pipe 20 just as one skilled in the art would easily
understand in light of this explanation and the additionally
provided disclosure. Also, it is noted that rotational
stabilization devices or wheel mechanisms 68 will aid in the smooth
rotation 90 of the entire rotating containment portion 24.
[0064] Whereby, it is noted that in the described embodiments, the
linkage device 44 would be wrapped completely around the first and
second coupling devices if there is a bike-like chain and gearing
arrangement to enable the rotation of the first portion 48 and thus
the couple rotating containment portion 24. Although, it is noted
that there are many other mechanical systems that may enable the
desired described rotation thereof. For example, there could be
employed a screw-type gear to replace the typical tooth gears 46
and 50, and a rod with matching screw-type teeth system to engage
in known fashion. Additionally, there could be a simple belt drive
like used on a car cooling fan belt system. Moreover, it is noted
that the linkage device 44 could be altogether eliminated in
another embodiment that would arrange the rotatable shaft 42 to
come into direct contact with the first portion 48 and have the
first and second couple devices 46 and 50 positively engaging
theretogether. In such an embodiment, the motor 40 may be
repositioned in a closer orientation to enable the requisite
positive engagement between as commonly known by one skilled in the
art of gearing mechanisms
[0065] Additionally, continuing the discussion of elements
represented in FIG. 2, there may also be a curtain device 52, in
the form of a brush, coupled to the first circular wall portion 48
to separate atmospheric conditions within and between the fixed
portion 22 and the rotating containment portion 24. Thus,
preventing most air born elements in the rotating containment
portion 24 from entering the fixed portion 22. There may also be a
releasably fixing device 66, which may be in the form of clamps,
designed to temporally and releasably hold the position of the
fixed portion 22 relative to the pipe section 22A and thus prevent
relative motion therebetween when the motor 40 is activated. It is
noted that the fixing device 66 may be in any physical design,
form, or arrangement that would allow for the function of securing
the fixed positioning of the fixed portion 22 relative to the pipe
20 during the rotational operation of the rotating containment
portion 24.
[0066] In another embodiment of the illustrated invention, there
are illustrated elements located within and about the rotating
containment portion 24 illustrated in both FIGS. 1 and 2.
Specifically, there is a containment cavity 60 defined by the
containment wall 23. There is illustrated a vacuum hose mounting
device 37, designed to releasably mount the vacuum hose 38 through
the containment wall 23B. There is illustrated rotational
stabilization devices or support device 68, which may be in the
form of wheels or a wheel mechanism, that abut to the pipeline 20,
that allow for smooth rotation of the rotating containment portion
24 as one skilled in the art would anticipate. Positioned between
the containment wall 23B and the pipeline 20 there may be another
curtain device 64, like a circular brush, fitted around the
periphery of the pipe 20, and designed in any form to prevent dust
contamination created within the containment cavity 60 from gaining
access to the outside ambient atmosphere where the workers are
located.
[0067] Regarding elements shown on the pipeline 20, there are such
elements such as a first pipe 20A, and a second pipe 20B, each
having a protective covering 58 thereon that does not cover the
exposed end section 56 of each pipe 20A and 20B. There is a weld
bead 54 that circumvents the entire circumference of the two
uncovered pipe end sections 56. These exposed end sections 56 and
weld bead 54 forms the work area 11 for the robotic grit blasting
device 12.
[0068] In operation, and in reference to all of the figures, the
material blasting nozzle portion 27 will project at high speeds a
blast material 72 toward the work area 11 and impinge thereon at
impact zone 73 as is commonly understood by one skilled in the
blasting art. Whereby, the blast material 72 will clean and pit the
pipe sections 56 in the work zone 11, thus preparing the pipe for
subsequent environmental protection coating process 122 material
being much like the pipe coating 58.
[0069] Subsequently, the blast material 72 upon high impact
generally will be pulverized into smaller particles and create a
dust 62 and larger less pulverized particles 84, which will fill
the containment cavity 60. Simultaneously, the grit vacuum device
18 will be activated and suction out the dust particles 62
therethrough the vacuum hose 38 in known vacuum process and
operation. Additionally, since the blasting nozzle portion 27 is
fixed into the container wall 23B, the entire rotating containment
portion 24 will be rotated via the motor 40, linkage device 44,
contacting first circular wall portion 48, and other associated
parts described therein. Thus, as the motor 40 actuates, the
rotating containment portion 24 will rotate completely 360 degrees
around the circumference of the pipe work site 11 during the
activation of the blasting material 72 impacting the blast zone 73,
while the pulverized blasting dust material 62 will be suctioned
out of the containment cavity 60 through the vacuum hose 38, and
the heavy less pulverized material 84 is collected toward a bottom
portion of the cavity 60 in a known fashion. Whereby, upon
completion of the entire 360 degrees of rotation the entire system
will reverse direction and eventually return to the original
starting position of the blasting nozzle 27, and thus the blasting
operation is completed. It is noted that during the rotation
thereof, the exterior associated hoses and cords 107 will have
sufficient excess length to thereby be wrap therearound the
rotational containment portion 24 before becoming unwrapped in well
understood operation. Also, it is noted that the wheels 68 will
assist in the rotation and hold the relative positioning for all
associated elements in a known fashion. It is also noted that there
are many methods of controlling the rotation herein described,
including using stoppers, position sensors, switches, all of which
would be obvious to one skilled in the art of rotational movement
of mechanical systems.
[0070] Referring now to all the figures and especially referring to
FIG. 3, which illustrates an end representative view of the grit
blasting containment device 12 that shows previous discussed
elements, and additional elements. Specifically, there is a
separation, interface, or cut 43 extending down the center of the
entire grit blasting containment device 12, and thus has a top cut
position starting at the hinge device 30 and extends down to a
bottom section located proximate a mounted catch device 26; thus
the cut 43 separating the grit blasting containment device 12 into
a first half wall 23A and a second half wall 23B. There is also a
coupling device 80 designed to hold together the two halves of the
robotic grit blasting device 12 and specifically the walls 23A and
23B during operation thereof. Upon closure of the robotic grit
blasting device 12, the wheels 68 will come in contact with the
pipe 20 and all for friction reduced rotation thereof. Obvious to
one skilled in the art, the hinge 30 facilitates the smooth opening
and closing of the two half walls 23A and B. Dashed lines 41
illustrate a possible open position of the cut 43, wherein the
opening will need to be a sufficient distance to allow for the
lifting of the entire grit blasting containment device 12 to be
lifted off of the pipe 20 during some moving operations thereof. It
is noted that the two half walls 23A and 23B will open in an
arcuate motion 83 and be repositioned to an open position 41 of the
cut 43. Also, it is noted that as the motor 40 is activated, the
associated linkage system 42,44, 46, 50 will cause the entire
containment portion 24 to rotate in a rotational direction 90
relative to the pipe 20 and to the fixed portion 22 that is
releasably coupled to the pipe 20A via holder 66.
[0071] Also, it is noted that there may be a mounted camera system
133, having radio, internet, Wi-Fi, bluetooth, or other known
connection 135, and a rotatable protective cover 131. Wherein, the
camera system 135 is positioned to view inside cavity 60 to aid in
positioning the grit blasting nozzle 27 in line with the work site
11. The cover 131 may be opened for viewing, and closed during
blasting operation via any known remote control method and
associated mechanical mechanisms. The following patents are
incorporated by reference for their supportive and enabling
teaching on how a potential camera embodiment may be implemented
with remote viewing capabilities in real time: 2005/0057502, U.S.
Pat. Nos. 6,903,724, 8,810,718, 8,994,800, 8,995,945, 9,196,133,
9,237,318, 9,769,368, and U.S. Pat. No. 9,781,565.
[0072] It is additionally noted; the illustrated lifting system of
cable 32 and clip 31 is shown in two separate steps. Specifically,
the right side shows the clamp 31 being unattached, and the left
side shows an attached view where claim 31 is not viewable from
that position. Further, it is illustrated that as the cable 32 is
lifted or lowered 82 that the cable 32 would exert pressure on
attachments 35 and thus cause the two halves 23A and 23B to
rotatively open 83 to reach a desired opening position 41 of the
divide 43. Thus, enabling the repositioning of the entire blasting
system 12 to a subsequent welding site 11.
[0073] In an alternative design, the cable 32, attachments 35, and
clamp 31 may or may not be needed in regular operation if moving
system 170 is employed and added thereto.
[0074] Referring now to all of the previous figures, and
specifically FIG. 4 where there is illustrated a representation of
the broad method 150 of implementing the robotic grit blasting
system 10. Specifically, in one embodiment, there may be
illustrated a pipeline 20 coupling process site 150, which includes
the grit blasting containment device 12, the support devices system
106, a pipe welding system 110, a pipe protective coating
application system 120, a robotic grit blasting system transporter
100 and its working arm 101. Uniquely, The welding system 110 may
include typical pipeline welding operations, including typical
workers, welding equipment, all located at a welding site 111 where
two unconnected pipe section will be welding together in any known
fashion. Moreover, the support devices system 106 in one embodiment
may additionally include a vehicle and driver 109. Additionally,
the protective coating application system will include known
workers and pipeline coating devices, like spray guns, spray
material containers, and associated power systems.
[0075] There is also illustrated a remote viewing system 200,
having a communication device 201, which may be in the form of a
cell phone using any known remote camera monitoring software
system. Wherein, the remote viewing system 200 receives real time
viewing images using any known data transfer system (blue tooth,
Wi-Fi, radio, etc.) from the camera 133 when the protective flap
131 is opened accordingly. Additionally, there is shown a typical
viewing screen 202 that will display the camera generated data,
which is used by a user to perform accurate positioning of the grit
blasting containment device 12 so that the blasting nozzle 27 is
properly oriented and lined up and pointing toward the two pipe
ends 56 intended to be blasted at the welding site 11.
Additionally, there is also illustrated a known remote control
device 210 used to communicate and control the operation of the
propulsion system 170 by controlling the forward and backward
propulsion movement thereof to properly align the grit blasting
containment device 12. Again, if the alternative propulsion system
170 is used, the robotic grit blasting system transporter 100, in
the form of a vehicle like a truck, will not be needed for each
relocation process of the entire system to the subsequent blasting
work site 11. The following patents are herein incorporate by
reference for their supportive teachings, and illustrating that the
remote control and camera technology is well known in the art,
regarding remote control system design: U.S. Pat. Nos. 8,568,238,
6,557,041, 7,043,524, 7,633,521, 2019/0297847, 7,218,994, and
2014/0172,197.
[0076] In operations, and in reference to all figures, the entire
process site 150 is designed to generally move from a first work
site 102 and move to a second work site 104 and continue such along
an entire gas pipeline 20 construction project amounting often to
dozens and even hundred of miles entailing thousands of weld sites
11. Specifically, pipe 20 is laid out in a linear orientation as
shown, and the welding system 110 will weld together two pipe ends
56 theretogether in know fashion and move on to a subsequent
un-welded dual pipe interface work site 111. Simultaneously, the
welded pipe section 11 will be cleaned by the robotic grit blasting
container 12. Where, in moving the blasting device 12, the two
halves 23A and 23B are opened in an arcuate direction 83 like a
clam shell along hinge 30 and resulting position illustrated by
opened position dividing cut 41 and transferred along the pipe to a
subsequent work site 11, and after arriving thereat, it will be
proper orientated and thereby closed via releasably fixing device
66 and the wall-coupling device 80, removably anchoring the
blasting container 12 to the pipe 20 thereat. Thereby, all of the
connections 107 may be reattached, if decoupled before hand, to the
grit blasting device 12. Thereby, the connector 33 will be
uncoupled from holding device 35 that would be mounted to the
rotating containment portion 24. Whereby, upon activation of the
motor 40 and associated linkages (44, 48 and 50), the robotic grit
blasting device 12 is now able to enable the rotating containment
portion 24 to rotate completely 360 degrees therearound. Therein,
the welded pipe section 11 will be blasted and cleaned by the grit
material 72 expelled from grit blasting nozzle 27 in known fashion.
Meanwhile, the vacuum system 18, via hose 38, removes the particle
dust 62 from the containment cavity 60. After the 360 degree
cleaning of the pipe section 11, the rotating containment portion
24 will reverse rotate back into its previous starting position via
the motor 40 reversing operation. Thereafter, all of the
connections 107 may be disconnected therefrom the robotic grit
blasting device 12. Whereby, releasably fixing device 66 and the
wall-coupling device 80 will be disengaged, the rod connector 33
will be reinserted into the holding device 35, and the releasable
gripper 31 will be reattached thereto as illustrated and the
transporter 100 will lift the connected lifting device 32 via arm
101, which will open the two halves of robotic grit blasting device
12 along cut 43 and around hinges 30 in a known fashion a
sufficient amount to enable the two halves to clear the diameter of
the pipe 20, thus simultaneously allowing heavy materials 84 that
were not captured by the vacuum system 18 to fall into the catch
tray 26. Thereby, the current work site 102 would be ready to be
moved to a subsequent work site 104, where the robotic grit
blasting device 12 will be lowered onto the pipe 20 causing the two
halves to close around the pipe 20, then recoupling the releasably
fixing device 66 to the pipe 20 and enabling the rotational
stabilization devices 68 to contact the pipe 20 and the curtain
devices 52 and 64 also contact proximate to the pipe 20. Whereby,
the wall-coupling device 80 is engaged to releasably hold the two
halves of the robotic grit blasting device 12 together while
performing the next blasting operation. Finally, the pipe
protective coating application system 120 is moved along after the
blasting operation is performed, and thus perform coating
operations at coating site 122 to protect the remaining exposed and
now clean pipe ends 56.
[0077] In the alternative method where the robotic grit blasting
system transporter 100 may not be used every step of the subsequent
cleaning operations and movement thereof, and may not consistently
use the connector 33 and holding device 35; wherein the alternative
propulsion system 170 is optionally mounted thereto as illustrated
and used in all subsequent operations. Obviously, there will be
modifications to the operation thereof in using the alternative
propulsion system 170. Specifically, the reconnection and
disconnection of the connections 107 may preferably not be
required. Additionally, to prep for movement, there would be the
added step of engaging the alternative propulsion system 170 to be
activated to first extend their carriage device wheels 175 to
contact the pipe 20 and thereby force open the two halves of the
robotic grit blasting device 12 to position 41. Thereafter, the
carriage device 175 may be remotely activated via camera
visualization device 200 and moved along the pipe 20 via motion
control system 210 until the appropriate position is reached
allowing the blasting nozzle 27 be properly positioned for accurate
blasting operations. Thereby, the carriage device wheels 175 will
be retracted enabling the two halves of the robotic grit blasting
device 12 to close around the pipe 20, and are thereby positioned
in a retracted non-engaging position as illustrated in FIG. 3. All
other previously described operational steps may operate as
previously presented.
[0078] It is noted that there are many variation to the presented
invention that are well within the scope and understanding of one
skilled in the various arts required to design the subject
invention. For example, although the description discusses using
"grit", this term is a term of art, and is no way limited to "grit"
type material. In fact, there are many known materials that are
well known, such as glass beads, coal material, sand, etc.
Additionally, the linkage engagement portion 43 that is illustrated
is only one of hundreds of systems that may enable the motor 40 to
couple to the rotating containment portion 24 to rotate 90 during
blasting operations.
[0079] It is further noted, the number of illustrated items is
merely for illustrative purposes. For example, the there may be
more than one blasting nozzles, there may be more than one holding
device 66, there may be more than two wheels 68, and etc.
[0080] Also, although the lateral movement system 170 is purely
illustrative and not definitive, in that there may only be a single
side mounted system on the leading or trailing side relative to the
lateral movement discussed in FIG. 4, instead of the illustrated
two sided system (one on the leading side and the other on the
trailing side). The actual teaching is that most any system will
work if it enables the lateral movement of the grit blasting system
12 down the pipeline to subsequent weld sites. There may even be a
separate opening system that would widely open the two wall halves
23A and 23B in preparation of the subsequent lateral movement of
the entire blasting system 12 to a subsequent weld site 11.
[0081] It should be noted that the steps described in the method of
use may be carried out in many different orders according to user
preference. The use of "step of" should not be interpreted as "step
for", in the claims herein and is not intended to invoke the
provisions of 35 U.S.C. .sctn. 112, II 6. Upon reading this
specification, it should be appreciated that, under appropriate
circumstances, considering such issues as design preference, user
preferences, marketing preferences, cost, structural requirements,
available materials, technological advances, etc., other methods of
use arrangements such as, for example, different orders within
above-mentioned list, elimination or addition of certain steps,
including or excluding certain maintenance steps, etc., may be
sufficient.
[0082] Although specific embodiments have been illustrated and
described herein, it will be appreciated by those of ordinary skill
in the various arts that any mechanical or electrical arrangement,
which is calculated to achieve the same purpose, may be substituted
for the specific embodiments shown. This application is intended to
cover any adaptations or variations of the present invention.
Further, although the invention has been explained in relation to
its preferred embodiment, it is to be understood that many other
possible modifications and variations can be made without departing
from the spirit and scope of the invention.
* * * * *