U.S. patent application number 16/681209 was filed with the patent office on 2020-05-14 for method for controlling dwell time during processing to optical component.
The applicant listed for this patent is The Institute of Optics and Electronics, The Chinese Academy of Sciences. Invention is credited to Xiaochuan HU, Zhaohui LAI, Jinshan YANG, Xianyun ZHONG.
Application Number | 20200147753 16/681209 |
Document ID | / |
Family ID | 65077778 |
Filed Date | 2020-05-14 |
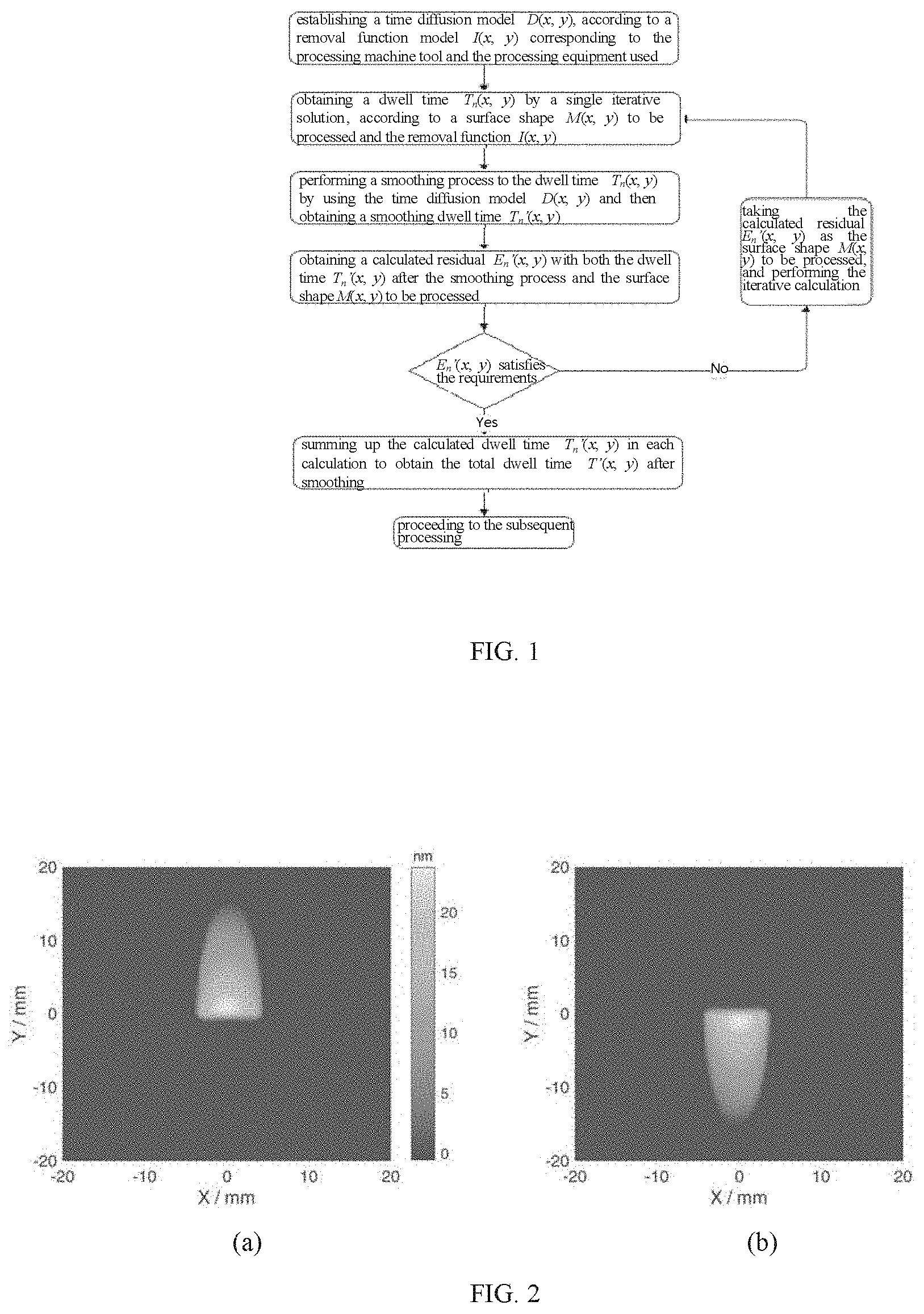
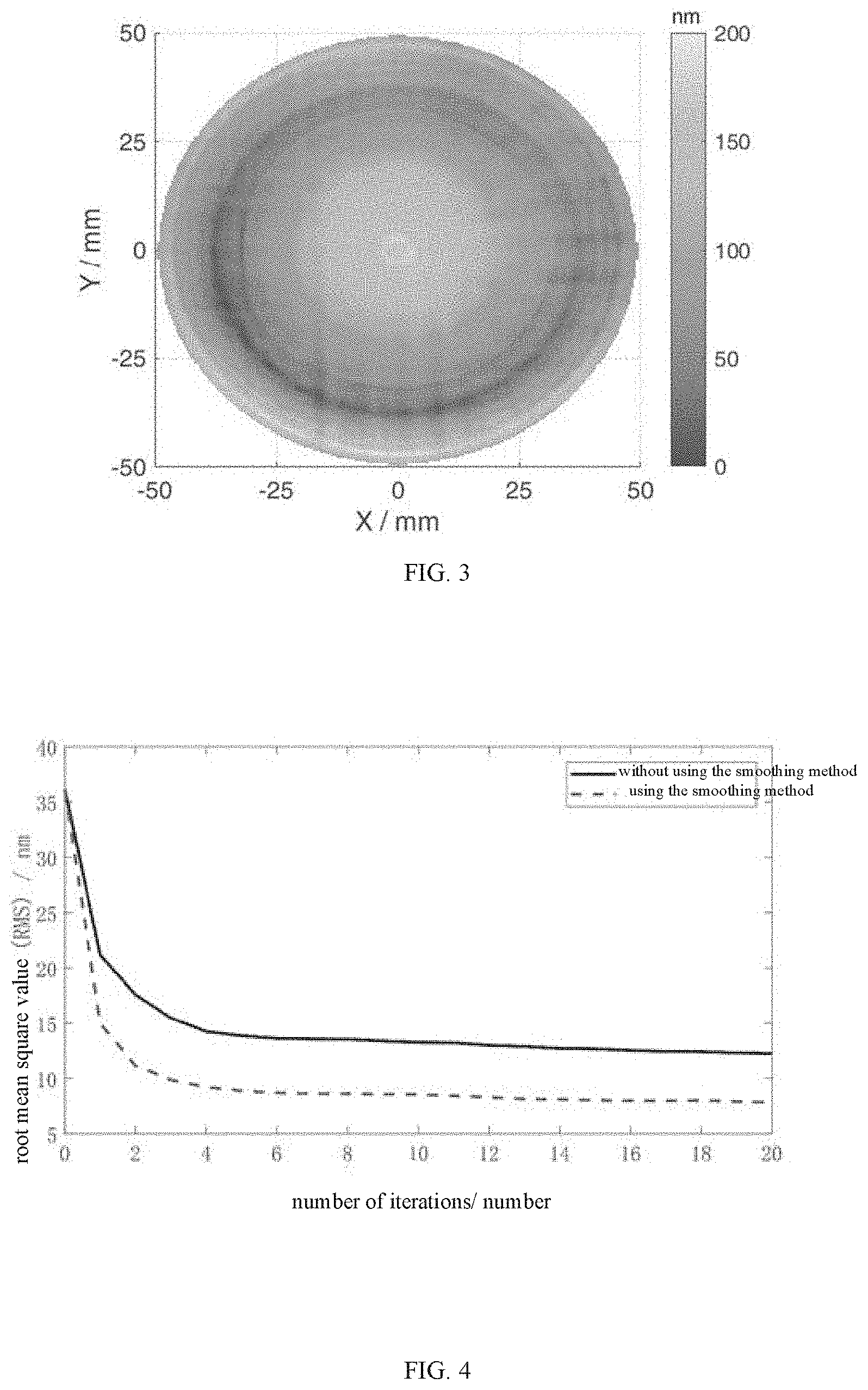

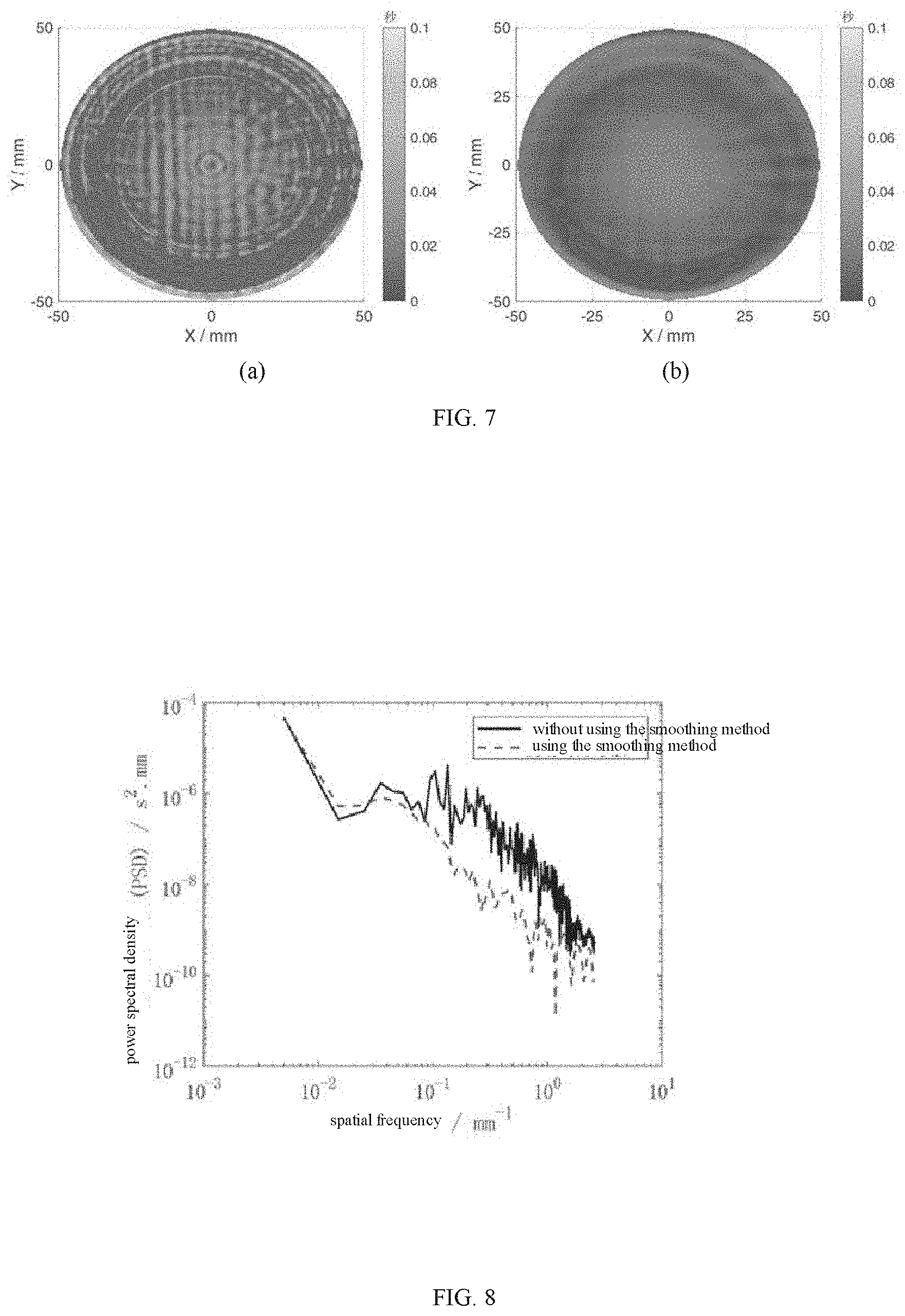

United States Patent
Application |
20200147753 |
Kind Code |
A1 |
HU; Xiaochuan ; et
al. |
May 14, 2020 |
METHOD FOR CONTROLLING DWELL TIME DURING PROCESSING TO OPTICAL
COMPONENT
Abstract
A method for smoothing a dwell time during a processing to an
optical component belongs to the field of processing optical
components, and solves a problem of an adverse effect of dwell time
jumps on a stability of the machine tool during processing. The
method achieves a smoothing treatment to the dwell time by a
diffusion transformation to the distribution of the conventionally
calculated dwell time using a time diffusion model. After the
smoothing treatment to the dwell time, the difference between times
at adjacent discrete points is relatively small, thereby achieving
a smooth transition between adjacent discrete points, and limiting
the effect of the polishing tool on machine stability due to its
frequent acceleration and deceleration during processing.
Inventors: |
HU; Xiaochuan; (Sichuan,
CN) ; ZHONG; Xianyun; (Sichuan, CN) ; LAI;
Zhaohui; (Sichuan, CN) ; YANG; Jinshan;
(Sichuan, CN) |
|
Applicant: |
Name |
City |
State |
Country |
Type |
The Institute of Optics and Electronics, The Chinese Academy of
Sciences |
Sichuan |
|
CN |
|
|
Family ID: |
65077778 |
Appl. No.: |
16/681209 |
Filed: |
November 12, 2019 |
Current U.S.
Class: |
1/1 |
Current CPC
Class: |
B24B 49/02 20130101 |
International
Class: |
B24B 49/02 20060101
B24B049/02 |
Foreign Application Data
Date |
Code |
Application Number |
Nov 12, 2018 |
CN |
201811336114.8 |
Claims
1. A method for smoothing a dwell time during a processing to an
optical component, wherein the dwell time of the polishing tool at
each discrete point on a surface of the optical component is
controlled such that a distribution of the dwell time on the
surface is smoothened, and a smoothing control to the dwell time is
achieved by a diffusion transformation to the distribution of the
dwell time using a time diffusion model, in which the method
comprises: (a) establishing a time diffusion model D(x, y) with a
center position D(x.sub.0, y.sub.0), and D(x, y) satisfies a
requirement for normalization to the total amount:
.SIGMA..sub.i,jD(x.sub.i,y.sub.j)=1 (1) (b) a surface shape error
of the component to be processed is M(x, y), and a removal function
of the polishing tool in a unit time is I(x, y), and in an
iterative calculation process, a dwell time obtained by a single
iteration solution is T.sub.1(x, y); in the dwell time T.sub.1(x,
y), a difference between a theoretical removal amount and the
surface shape error M(x, y) of the component to be processed is a
calculated residual E.sub.1(x, y), which can be expressed as:
E.sub.1(x,y)=M(x,y)-T.sub.1(x,y)**I(x,y) (2) where ** denotes a
convolution, T.sub.1(x, y)**I(x, y) denotes a removal amount of the
component to be processed by the polishing tool during the dwell
time T.sub.1(x, y); (c) for each discrete coordinate point
(x.sub.i, y.sub.j) in T.sub.1(x, y), the time diffusion model D(x,
y) is translated in both X and Y directions so that its center
position (x.sub.0, y.sub.0) is moved to (x.sub.i, y.sub.j) and is
expressed as D.sub.ij(x, y): D.sub.ij(x,y)=D(x-x.sub.i,y-y.sub.j)
(3) subsequently, performing a point-to-surface diffusion process
to the point T.sub.1(x.sub.i, y.sub.j) with the diffusion function
D.sub.ij(x, y), thereby obtaining a post-diffusion time
distribution K.sub.ij(x, y):
K.sub.ij(x,y)=D.sub.ij(x,y)T.sub.1(x.sub.i,y.sub.j) (4) since
D.sub.ij(x, y) also satisfies the requirement for normalization to
the total amount as in equation (1), so there are:
.SIGMA..sub.i,jK.sub.ij(x,y)=T.sub.1(x.sub.i,y.sub.j) (5)
k.sub.ij(x,y)**I(x,y).apprxeq.T.sub.1(x.sub.i,y.sub.j)I(x,y) (6)
(d) according to those described in said (c), obtaining a
post-diffusion time distribution K.sub.ij(x, y) for each discrete
point (x.sub.i, y.sub.j), and the dwell time distribution
T.sub.1'(x, y) after smoothing can be expressed as:
T.sub.1'(x,y)=.SIGMA..sub.i,jK.sub.ij(x,y) (7) and the removal
amount corresponding to the dwell time distribution T.sub.1'(x, y)
after smoothing should be approximately equal to the removal amount
corresponding to the dwell time distribution T.sub.1(x, y) before
smoothing: T.sub.1'(x,y)**I(x,y).apprxeq.T.sub.1(x,y)**I(x,y) (8)
(e) a difference between the surface shape error M(x, y) of the
component to be processed and the removal amount corresponding to
the dwell time T.sub.1'(x, y) after smoothing is a calculation
residual E.sub.1'(x, y) of the dwell time by a single iteration
solution after smoothing:
E.sub.1'(x,y)=M(x,y)-T.sub.1'(x,y)**I(x,y) (9) (f) selecting the
calculation residual E.sub.1' as the surface shape error M of the
component to be processed, and repeating said (b) to (e), and
performing iterative calculations, until the calculation of the
n.sub.th iteration is completed, and the corresponding calculated
residual E.sub.n' satisfies the requirement, thereby obtaining a
total dwell time distribution T'(x, y) after smoothing:
T'(x,y)=.SIGMA..sub.k=1.sup.nT.sub.k'(x,y) (10) where n denotes a
total number of iteration cycles; thereby achieving a smoothing
processing to the dwell time during a processing to the optical
component.
2. The method according to claim 1, wherein the performing of a
smoothing control to the dwell time using a time diffusion model,
includes adjusting the time diffusion model to improve the
smoothing effect of the dwell time, wherein a shape of the removal
function I(x, y) being normalized after rotating the removal
function I(x, y) by 180 degrees is normalized to be the time
diffusion model D(x, y).
Description
INCORPORATION BY REFERENCE TO ANY PRIORITY APPLICATIONS
[0001] Any and all applications for which a foreign or domestic
priority claim is identified in the Application Data Sheet as filed
with the present application are hereby incorporated by
reference.
BACKGROUND OF THE INVENTION
Field of the Invention
[0002] The embodiment of the present disclosure relates to a method
for smoothing a dwell time during a processing to an optical
component, which belongs to a field of processing the optical
component.
Description of the Related Art
[0003] With a rapid development of optical technology and a
continuous expansion of its application range, people have put
forward higher and higher requirements on technical indicators of
the optical components, such as the surface shape precision and
surface roughness. An aspherical surface, a relatively large
caliber, and a nanometer-order precision become development trends
of modern optical components. In order to effectively improve the
surface processing quality of optical components and to meet the
requirements of modern high-precision machining technology,
technicians have begun to use high-precision numerically controlled
machining tools to process optical components. In the numerically
controlled machining process, a polishing tool of a high-precision
numerically controlled machining tool applies a certain relative
movement speed and a certain pressure on the surface of the
components to be processed so as to remove excess material on the
surface of the components to be processed. Due to the introduction
of digital technology, a moving trajectory of the polishing tool on
the surface of the component to be processed can be approximated as
a continuous movement at various discrete points. In a unit time, a
removal amount of the components to be processed at a single
discrete point by the polishing tool is defined as a removal
function, while the time in which the polishing tool dwells at each
discrete point is defined as a dwell time. Therefore, how to plan a
distribution of the dwell time of the polishing tool on the surface
of the components to be processed is a key point to achieve a
high-precision numerical controlled machining.
[0004] In the relevant art, a method for solving the dwell time
mainly comprises a overall optimal solution and a local optimal
solution:
[0005] 1. Overall Optimal Solution
[0006] In a condition that the removal function and the removal
amount of the component to be processed are given, a set of optimal
dwell time distributions can be calculated by a classical algorithm
such as least square method and the like to minimize a surface
shape error of the surface of the component after processing, then
such a set of the optimal dwell time distributions is the overall
optimal solution. However, in an actual high-precision machining,
the amount of data and the amount of calculation involved in the
calculation process are very large, which makes it difficult to
obtain an overall optimal solution.
[0007] 2. Local Optimal Solution
[0008] In order to calculate a set of better dwell time
distributions in a limited time, which makes the surface shape
error of the surface of the component after processing to be as
small as possible, algorithms such as a proportional estimation
iteration method, a pulse iteration method and the like are usually
used to solve the dwell time, and such a set of dwell time
distributions is the local optimal solution. However, this method
is mainly applicable to the case where the removal function of the
polishing tool on the surface of the component is circularly
symmetric. In a condition of the polishing device, such as a
magnetorheological polishing machine and the like whose removal
function is non-circularly symmetric, a convergence effect in the
computation of the method is still to be improved.
[0009] However, neither of the above methods takes a smoothing
problem of the dwell time distribution into account; in a condition
that the dwell time variation between each two adjacent discrete
points is too large, that is, the dwell time distribution is not
smoothing enough, it is likely that the polishing tool accelerates
or decelerates frequently during the movement thereof, thereby
adversely affecting the stability of the machine tool, and thus
leaving a movement trail on the surface of the machined component.
Normally, the movement trail has a spatial size on the order of a
spacing between any two adjacent discrete points, i.e., the spatial
size corresponds to a medium frequency surface shape error and/or a
high frequency surface shape error. Since the surface shape error
is introduced during the processing to the processing equipment,
and a correction to the medium frequency surface shape error and
the high frequency surface shape error is a technical difficulty in
the current numerical control processing, then they are difficult
to be corrected by a secondary processing.
SUMMARY OF THE INVENTION
[0010] The object of the present disclosure is to overcome
deficiencies in relevant art and to provide a method for smoothing
the dwell time of an optical component during processing thereto.
In the method, the dwell time distribution obtained by calculation
in an iterative process through a local optimal solution is
diffused by introducing a time diffusion model, thereby achieve a
smoothing process to the dwell time, which inherits the advantages
of the local optimal solution, while the calculation amount is much
smaller than an overall optimal solution.
[0011] A method for smoothing a dwell time during a processing to
an optical component, which specifically comprises following
steps:
[0012] Step 1: establishing a time diffusion model D(x, y) with a
center position D(x.sub.0, y.sub.0), and D(x, y) satisfies a
requirement for normalization to the total amount:
.SIGMA..sub.i,jD(x.sub.i,y.sub.j)=1 (1)
[0013] Step 2: a surface shape error of the component to be
processed is M(x, y), and a removal function of the polishing tool
in a unit time is I(x, y), and in an iterative calculation process,
a dwell time obtained by a single iteration solution is T.sub.1(x,
y); in the dwell time T.sub.1(x, y), a difference between a
theoretical removal amount and the surface shape error M(x, y) of
the component to be processed is a calculated residual E.sub.1(x,
y), which can be expressed as:
E.sub.1(x,y)=M(x,y)-T.sub.1(x,y)**I(x,y) (2)
where ** denotes a convolution, T.sub.1(x, y)**I(x, y) denotes a
removal amount of the component to be processed by the polishing
tool during the dwell time T.sub.1(x, y);
[0014] Step 3: for each discrete coordinate point (x.sub.i,
y.sub.j) in T.sub.1(x, y), the time diffusion model D(x, y) is
translated in both X and Y directions so that its center position
(x.sub.0, y.sub.0) is moved to (x.sub.i, y.sub.j) and is expressed
as D.sub.ij(x, y):
D.sub.ij(x,y)=D(x-x.sub.i,y-y.sub.j) (3)
[0015] subsequently, performing a point-to-surface diffusion
process to the point T.sub.1(x.sub.i, y.sub.j) with the diffusion
function D.sub.ij(x, y), thereby obtaining a post-diffusion time
distribution K.sub.ij(x, y):
K.sub.ij(x,y)=D.sub.ij(x,y)T.sub.1(x.sub.i,y.sub.j) (4)
[0016] since D.sub.ij(x, y) also satisfies the requirement for
normalization to the total amount as in equation (1), so there
are:
.SIGMA..sub.i,jK.sub.ij(x,y)=T.sub.1(x.sub.i,y.sub.j) (5)
k.sub.ij(x,y)**I(x,y).apprxeq.T.sub.1(x.sub.i,y.sub.j)I(x,y)
(6)
[0017] Step 4: according to those described in Step 3, obtaining a
post-diffusion time distribution K.sub.ij(x, y) for each discrete
point (x.sub.i, y.sub.j), and the dwell time distribution
T.sub.1'(x, y) after smoothing can be expressed as:
T.sub.1'(x,y)=.SIGMA..sub.i,jK.sub.ij(x,y) (7)
and the removal amount corresponding to the dwell time distribution
T.sub.1'(x, y) after smoothing should be approximately equal to the
removal amount corresponding to the dwell time distribution
T.sub.1(x, y) before smoothing:
T.sub.1'(x,y)**I(x,y).apprxeq.T.sub.1(x,y)**I(x,y) (8)
[0018] Step 5: a difference between the surface shape error M(x, y)
of the component to be processed and the removal amount
corresponding to the dwell time T.sub.1'(x, y) after smoothing is a
calculation residual E.sub.1'(x, y) of the dwell time by a single
iteration solution after smoothing:
E.sub.1'(x,y)=M(x,y)-T.sub.1'(x,y)**I(x,y) (9)
[0019] Step 6: selecting the calculation residual E.sub.1' as the
surface shape error M of the component to be processed, and
repeating Step 2 to Step 5, and performing iterative calculations,
until the calculation of a n.sub.th iteration is completed, and the
corresponding calculated residual E.sub.n' satisfies the
requirement, thereby obtaining a total dwell time distribution
T'(x, y) after smoothing:
T'(x,y)=.SIGMA..sub.k=1.sup.nT.sub.k'(x,y) (10)
where n denotes a total number of iteration cycles; thereby
achieving a smoothing processing to the dwell time during a
processing to the optical component.
[0020] In an embodiment, the step of performing a smoothing control
to the dwell time using a time diffusion model, includes adjusting
the time diffusion model to improve the smoothing effect of the
dwell time, wherein a shape of the removal function I(x, y) after
rotating the removal function I(x, y) by 180 degrees is normalized
to be the time diffusion model D(x, y).
[0021] The advantages and beneficial technical effects of the
present disclosure over the prior art are as follows:
[0022] 1. The method for smoothing the dwell time during a
processing to an optical component according to the present
disclosure may achieve a compensate effect in case where the
removal function of the polishing tool on the surface of the
component is non-circularly symmetric, and improve the convergence
effect of the iterative calculation.
[0023] 2. The method for smoothing the dwell time during a
processing to an optical component according to the present
disclosure may reduce a degree of jump of the dwell time between
adjacent discrete points by smoothing the dwell time in the
iterative calculation process, thereby reducing the adverse effect
on the stability of the machine tool due to the frequent
acceleration or deceleration of the polishing tool during the
processing, thereby reducing the medium and high frequency surface
shape errors introduced by the equipment to the component to be
processed during the machining process.
BRIEF DESCRIPTION OF THE DRAWINGS
[0024] FIG. 1 is a flow chart for performing a method for smoothing
a dwell time during a processing to an optical component according
to the present disclosure;
[0025] FIG. 2(a) is the removal function distribution used in the
embodiment, and FIG. 2(b) is the time diffusion model used in the
embodiment;
[0026] FIG. 3 is an initial shape error to be processed in the
embodiment;
[0027] FIG. 4 is a graph showing a variation trend of the root mean
square value (RMS) of the calculated residual as a function of the
number of iterations in the embodiment, in which the solid line is
a variation trend of the root mean square value (RMS) of the
calculated residual as a function of the number of iterations
without using the method for smoothing a dwell time during a
processing to an optical component according to the present
disclosure, while the dashed line is a variation trend of the root
mean square value (RMS) of the calculated residual as a function of
the number of iterations using the method for smoothing a dwell
time during a processing to an optical component according to the
present disclosure.
[0028] FIG. 5 (a)(b) are comparison diagrams of the calculated
residuals in the embodiment, in which FIG. 5(a) is the calculated
residual without using the method for smoothing a dwell time during
a processing to an optical component according to the present
disclosure, and FIG. 5(b) is the calculated residual using the
method for smoothing a dwell time during a processing to an optical
component according to the present disclosure;
[0029] FIG. 6 is a power spectral density (PSD) distribution of the
calculated residual in the embodiment, in which the solid line is
the power spectral density (PSD) distribution of the calculated
residual without using the method for smoothing a dwell time during
a processing to an optical component according to the present
disclosure, and the dashed line is the power spectral density (PSD)
distribution of the calculated residual using the method for
smoothing a dwell time during a processing to an optical component
according to the present disclosure.
[0030] FIG. 7 (a)(b) are comparison diagrams of the dwell time
obtained by iterative calculation in the embodiment, in which FIG.
7 (a) is a dwell time distribution without using the method for
smoothing a dwell time during a processing to an optical component
according to the present disclosure, FIG. 7 (b) is a dwell time
distribution using the method for smoothing a dwell time during a
processing to an optical component according to the present
disclosure.
[0031] FIG. 8 is a power spectral density (PSD) distribution of the
dwell time in an embodiment, in which the solid line is the power
spectral density (PSD) distribution of the dwell time without using
the method for smoothing a dwell time during a processing to an
optical component according to the present disclosure, and the
dashed line is the power spectral density (PSD) distribution of
dwell time using the method for smoothing a dwell time during a
processing to an optical component according to the present
disclosure.
DETAILED DESCRIPTION OF THE PREFERRED EMBODIMENT
[0032] The present disclosure will be further described in detail
with reference to the accompanying drawings. It is to be understood
that the described embodiments are only intended to be a further
description of the disclosure, and are not intended to limit the
scope of the disclosure. The flow chart for implementing the method
for smoothing a dwell time during a processing to an optical
component proposed by the present disclosure is as shown in FIG.
1.
[0033] In the first step, establishing a time diffusion model D(x,
y) used in the method for smoothing a dwell time during a
processing to an optical component time in the processing of an
optical component of the present disclosure, according to a removal
function model I(x, y) corresponding to the processing machine tool
and the processing equipment used;
[0034] In the second step, obtaining a dwell time T.sub.n(x, y) by
a single iterative solution, according to a surface shape M(x, y)
to be processed and the removal function I(x, y);
[0035] In the third step, performing a smoothing process to the
dwell time T.sub.n(x, y) by using the time diffusion model D(x, y),
and then obtaining a smoothing dwell time T.sub.n'(x, y);
[0036] In the fourth step, obtaining a calculated residual
E.sub.n'(x, y) with both the dwell time T.sub.n'(x, y) after the
smoothing process and the surface shape M(x, y) to be
processed;
[0037] In the fifth step, taking the calculated residual
E.sub.n'(x, y) as the surface shape M(x, y) to be processed, and
repeating the second step to the fourth step, and performing the
iterative calculation, until the calculated residual E.sub.n'(x, y)
satisfies the requirements after finishing the nth iteration
calculation;
[0038] In the sixth step, summing up the calculated dwell time
T.sub.n'(x, y) in each calculation to obtain the total dwell time
T'(x, y) after smoothing, and in turn proceeding to the subsequent
processing.
EMBODIMENTS
[0039] In this embodiment, a magnetorheological numerical control
polishing machine is used as a processing device, and a circular
flat mirror having a diameter of 100 mm is used as a component to
be processed, and a specific embodiment of the present disclosure
is exemplified in conjunction with FIG. 2 to FIG. 7. In the
following description, the method for smoothing a dwell time during
a processing to an optical component according to the present
disclosure is simply referred to as a smoothing method. Under
normal circumstances, the removal function of the
magnetorheological polishing machine is non-circularly
symmetric.
[0040] FIG. 2(a) shows the removal function distribution I(x, y) of
the magnetorheological polishing head dwell at the coordinate point
of x=0, y=0 for 3 seconds. In this embodiment, the shape
distribution of the removal function distribution after being
rotated by 180 degrees with respect to a coordinate point of x=0,
y=0 may function as a time diffusion model D(x, y), and its
distribution pattern is shown in FIG. 2(b); and the total amount of
the time diffusion model is normalized to satisfy the equation
(1).
[0041] FIG. 3 is an initial shape error M(x, y) of the component to
be processed, whose peak-to-valley value (PV) of the surface shape
is 200.076 nm, and the root mean square value (RMS) is 36.115 nm.
By substituting both the surface shape error M(x, y) to be
processed and the removal function I(x, y) into the equation (2),
the dwell time distribution T.sub.1(x, y) and the corresponding
calculated residual E.sub.1(x, y) will be obtained without using
the smoothing method. For the above-mentioned dwell time T.sub.1(x,
y), using the time diffusion model D(x, y) shown in FIG. 2(b) to
perform smoothing process according to the equations (3).about.(8),
and then the dwell time distribution T.sub.1'(x, y) after using the
smoothing method can be obtained, and the calculated residual
E.sub.1'(x, y) after using the smoothing method is calculated by
the equation (9).
[0042] When the smoothing method is not used, the above-mentioned
calculated residual E.sub.1(x, y) is taken as the surface shape
error M(x, y) to be processed, and it is substituted into the cycle
for iterative calculation; when the smoothing method is used, the
above-mentioned calculated residual E.sub.1'(x, y) is taken as the
surface shape error M(x, y) to be processed, and it is substituted
into the cycle for iterative calculation.
[0043] FIG. 4 shows the variation trend of the root mean square
(RMS) of the calculated residual as a function of the number of
iterations in the 20 iterations calculation, in which the solid
line is a variation trend of the root mean square value (RMS) of
the calculated residual as a function of the number of iterations
without using the smoothing method, while the dashed line is a
variation trend of the root mean square value (RMS) of the
calculated residual as a function of the number of iterations using
the smoothing method. It can be seen from FIG. 4 that, the root
mean square value (RMS) of the calculated residuals tends to
decrease gradually with an increase in the number of iterations,
and after using the smoothing method, the convergence speed and
convergence effect of the root mean square value (RMS) of the
calculated residual are better than those without using the
smoothing method. When the smoothing method is not used, the
calculated residual E.sub.20(x, y) after the completion of the
20.sub.th iteration is shown in FIG. 5(a), and the corresponding
peak-to-valley (PV) value is 96.258 nm, and the root mean square
value is (RMS) is 12.263 nm; and after using the smoothing method,
the calculated residual E.sub.20'(x, y) after the completion of the
20.sub.th iteration is shown in FIG. 5(b), and the corresponding
peak-to-valley (PV) value is 86.432 nm, root mean square (RMS) is
7.835 nm. Compared with FIG. 5(a), the surface shape distribution
corresponding to FIG. 5(b) is more uniform and more gentle, and its
peak-to-valley (PV) value and root mean square (RMS) values are
also smaller, which indicates that the smoothing method can improve
the convergence effect of the iterative calculation, even if the
removal function of the polishing tool on the surface of the
component is a non-circular symmetric distribution, a better
convergence effect can be achieved after using the smoothing
method. As shown in FIG. 6, the power spectral density (PSD)
distribution of the calculated residual E.sub.20(x, y) without
using the smoothing method is compared with the power spectral
density (PSD) distribution of the calculated residual E.sub.20(x,
y) using the smoothing method. The power spectral density (PSD) is
well known in the art and will not be further described here. The
numerical equation is:
PSD = .DELTA. x n n = 0 N - 1 M ( n ) e - i 2 .pi. f m n .DELTA. x
( 11 ) ##EQU00001##
[0044] where .quadrature. .DELTA.x=L/N is a sampling interval, L is
a sampling length, N is an effective sampling point number, and
M(n) is an error function. It can be seen from FIG. 6 that,
compared with the case in which the smoothing method is not used,
after using the smoothing method, the portion of the calculated
residual surface shape with a spatial frequency less than 0.2
mm.sup.-1 (which usually corresponds to the medium frequency error
and/or low frequency error) is reduced, which in turn indicates
that the smoothing method can improve the processing effect of the
processing equipment in the middle and low frequency portions.
[0045] FIG. 7 shows a comparison of the dwell time distributions
solved without using the smoothing method and using the smoothing
method, in which the spatial size corresponding to each discrete
point is 0.0383 mm.sup.2, that is, 512.times.512 discrete points
are used to perform a discrete processing on a square area with a
side length of 100 mm; FIG. 7(a) is the total dwell time T(x, y)
distribution obtained after completion of the 20.sub.th iterative
calculation without using the smoothing method. T(x, y) satisfies
T(x, y)=.SIGMA..sub.k=1.sup.20 T.sub.k(x, y), the corresponding
peak-to-valley (PV) value is 0.107 seconds, and the root mean
square value (RMS) is 0.013 seconds; FIG. 7(b) is the total dwell
time T'(x, y) distribution obtained after completion of the
20.sub.th iterative calculation using the smoothing method. T'(x,
y) satisfies T'(x, y)=.SIGMA..sub.k=1.sup.20 T.sub.k'(x, y), the
corresponding peak-to-valley (PV) value is 0.038 seconds, and the
root mean square value (RMS) is 0.006 seconds. It can be seen that
the dwell time calculated using the smoothing method has a
peak-to-valley (PV) and root mean square (RMS) ratio which are
reduced when compared to those of the calculated dwell time without
using the smoothing method, and the time distribution is more
uniform and more gentle. FIG. 8 compares the distribution
characteristics of the dwell times T(x, y) and T'(x, y) at spatial
frequencies from the perspective of power spectral density. It can
be seen from FIG. 8 that the portions whose spatial frequency is
higher than 0.05 mm.sup.-1 (usually corresponding to the medium
frequency error and/or high frequency error) in the dwell time
distribution using the smoothing method are reduced compared to the
case where the smoothing method is not used, which shows that
utilization of smoothing method can reduce the level of the
frequent movement of the polishing tool in a small space, thereby
reducing the medium and high frequency errors introduced into the
components due to frequent shaking of the polishing tool during the
processing.
[0046] Through the above embodiments, it is shown that the method
for smoothing a dwell time during a processing to an optical
component according to the present disclosure can improve the
convergence effect of the iterative calculation in the process of
calculating the dwell time, and improve the capability of
correcting the medium and high frequency surface shape error of the
processing equipment to the surface of the component to be
processed. In addition, the method for smoothing the dwell time
during the processing to an optical component of the present
disclosure can limit the degree of jump of the dwell time between
adjacent discrete points by smoothing the dwell time, thereby
reducing the adverse effect on the stability of a numerical control
machining due to the frequent acceleration or deceleration of the
polishing tool during the processing, thereby reducing medium and
high frequency errors introduced into the components due to
frequent shaking of the polishing tool.
* * * * *