U.S. patent application number 16/747126 was filed with the patent office on 2020-05-14 for moisture wicking and cooling capsules having an outer shell comprising a siloxane and methods for making same.
This patent application is currently assigned to MICROTEK LABORATORIES, INC.. The applicant listed for this patent is MICROTEK LABORATORIES, INC.. Invention is credited to Carl M. Lentz, Kayla L. M. Ryan.
Application Number | 20200146378 16/747126 |
Document ID | / |
Family ID | 63245484 |
Filed Date | 2020-05-14 |




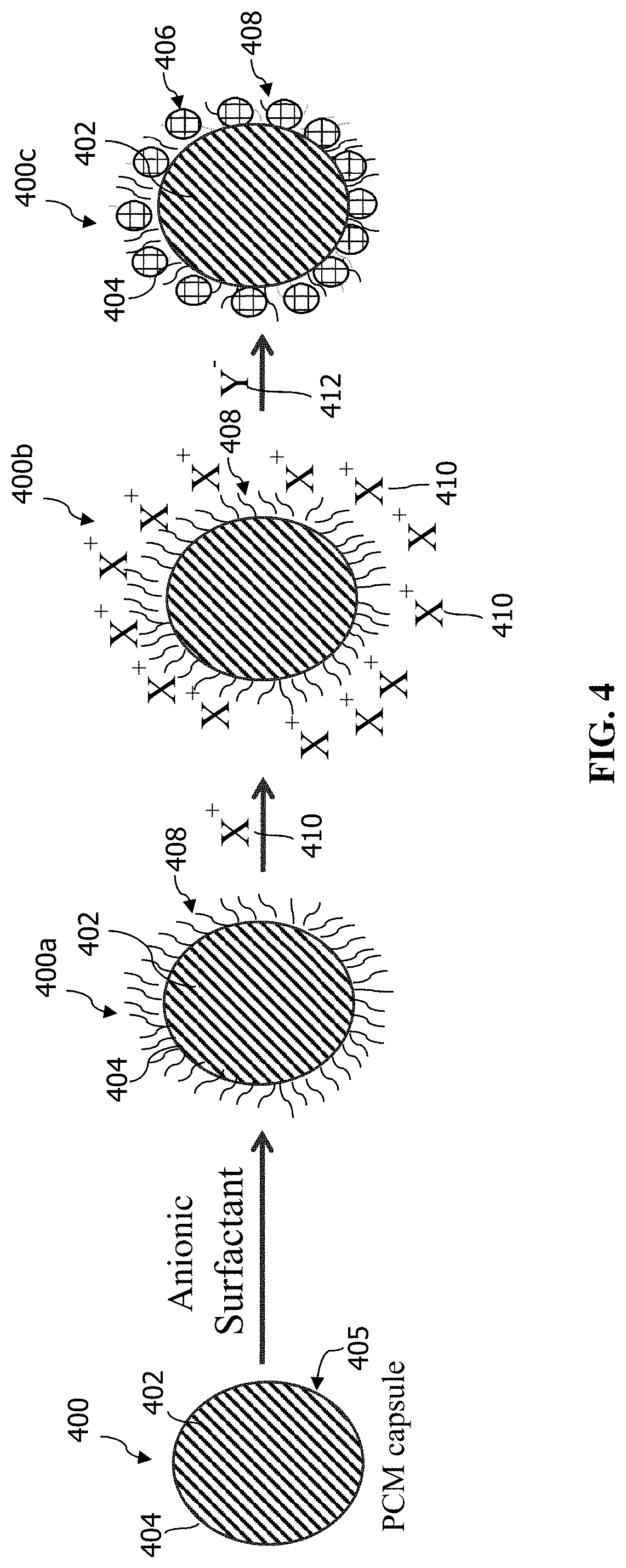

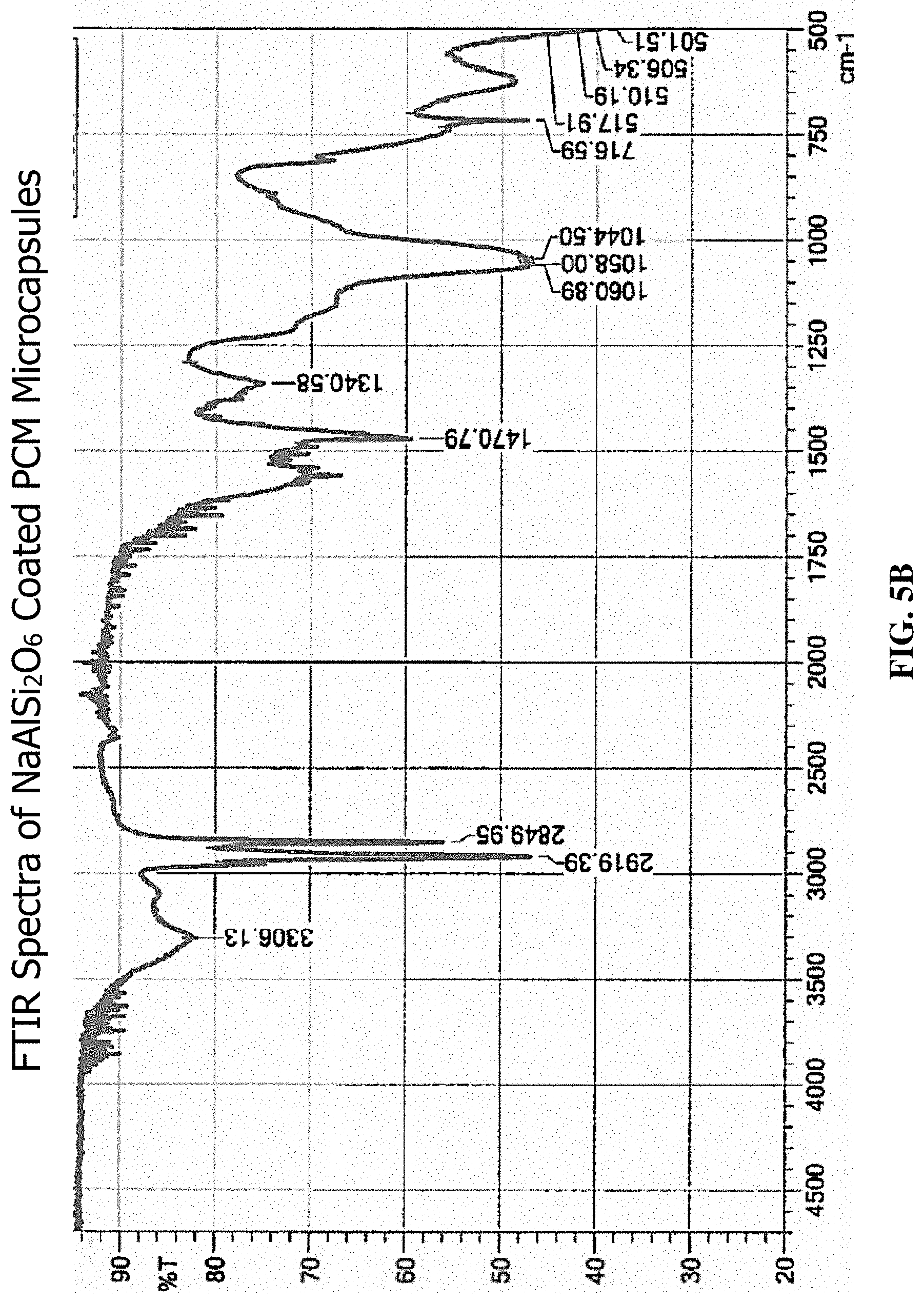

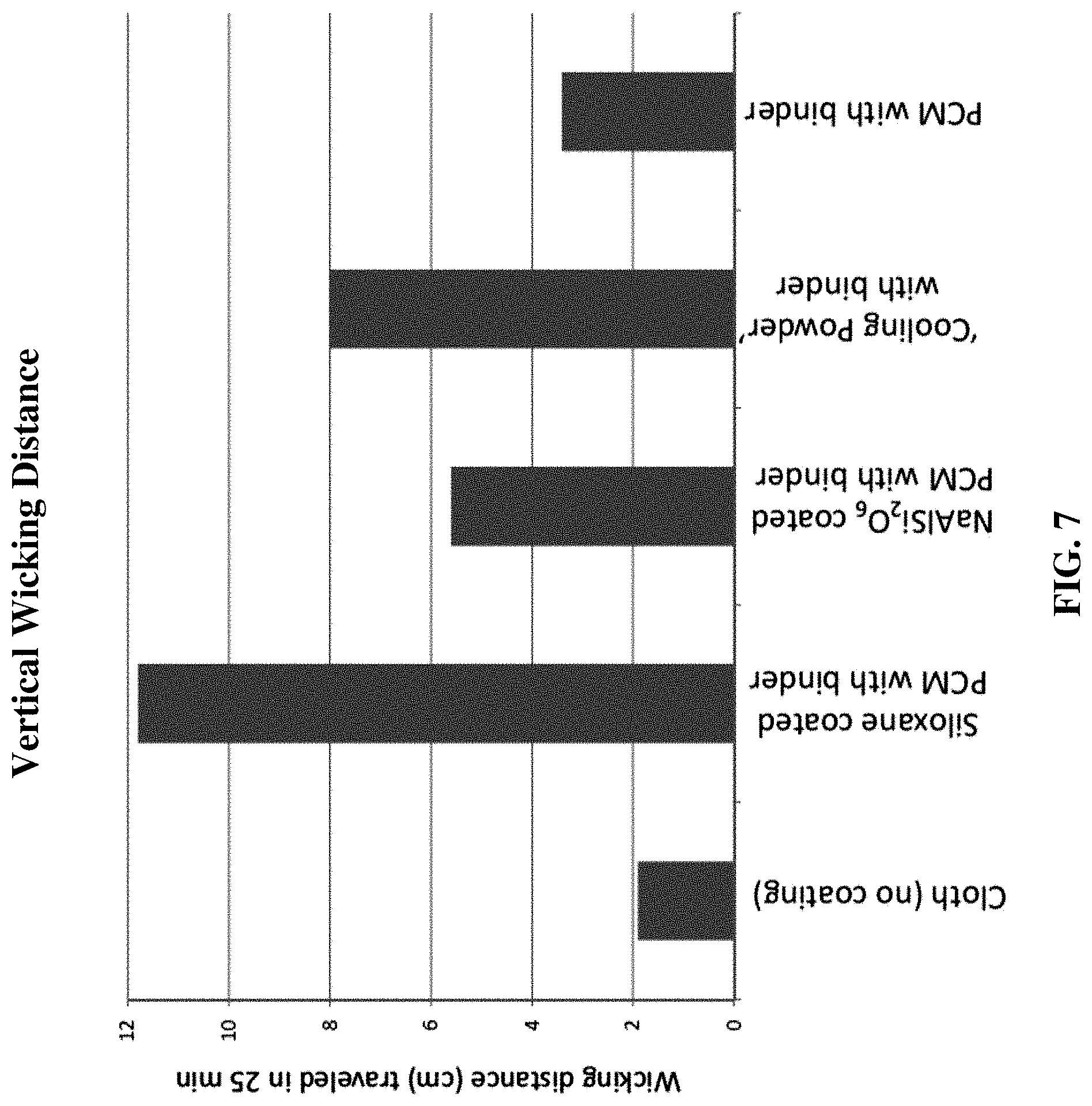

United States Patent
Application |
20200146378 |
Kind Code |
A1 |
Ryan; Kayla L. M. ; et
al. |
May 14, 2020 |
MOISTURE WICKING AND COOLING CAPSULES HAVING AN OUTER SHELL
COMPRISING A SILOXANE AND METHODS FOR MAKING SAME
Abstract
Microcapsules or macrocapsules have a core composition that
includes a phase change material (PCM) encapsulated within a
polymer wall with an outer shell having a siloxane tethered to an
exterior surface of the polymer wall by a surfactant. The siloxane
may form a crystalline or a sol-gel outer shell. Methods of making
such capsules and textile fabrics and clothing incorporating such
capsules include treating pre-formed capsules with a surfactant
solution followed by treating with a compound containing a siloxane
functional group. The surfactant connects or tethers the siloxane
to the exterior surface of the polymer wall and the siloxane forms
an outer shell of the capsules.
Inventors: |
Ryan; Kayla L. M.;
(Alamogordo, NM) ; Lentz; Carl M.; (Waynesville,
OH) |
|
Applicant: |
Name |
City |
State |
Country |
Type |
MICROTEK LABORATORIES, INC. |
Dayton |
OH |
US |
|
|
Assignee: |
MICROTEK LABORATORIES, INC.
Dayton
OH
|
Family ID: |
63245484 |
Appl. No.: |
16/747126 |
Filed: |
January 20, 2020 |
Related U.S. Patent Documents
|
|
|
|
|
|
Application
Number |
Filing Date |
Patent Number |
|
|
15906015 |
Feb 27, 2018 |
10561182 |
|
|
16747126 |
|
|
|
|
62464733 |
Feb 28, 2017 |
|
|
|
Current U.S.
Class: |
1/1 |
Current CPC
Class: |
A42B 3/125 20130101;
A63B 21/4037 20151001; B01J 20/265 20130101; C09K 5/066 20130101;
B01J 20/3217 20130101; A41D 2600/10 20130101; A41D 27/02 20130101;
A63B 2209/00 20130101; B01J 20/28004 20130101; B01J 20/3246
20130101; B01J 20/3293 20130101; B01J 20/3208 20130101; A41D 31/02
20130101; A42B 3/066 20130101; B01J 20/28019 20130101 |
International
Class: |
A41D 31/02 20060101
A41D031/02; C09K 5/06 20060101 C09K005/06; A42B 3/12 20060101
A42B003/12; A41D 27/02 20060101 A41D027/02; B01J 20/32 20060101
B01J020/32; B01J 20/28 20060101 B01J020/28; B01J 20/26 20060101
B01J020/26 |
Claims
1. A capsule comprising: a core composition comprising a phase
change material (PCM); a polymer wall encapsulating the core
composition; and an outer shell comprising a reaction product of a
silicate and a metal-oxygen containing compound or a reaction
product of a metal-oxygen containing compound and a compound
containing a siloxane functional group chemically bonded to an
exterior surface of the polymer wall by a surfactant; wherein the
capsules wick moisture.
2. The capsule of claim 1, wherein the surfactant comprises one or
more of a cationic surfactant, an anionic surfactant, and a
non-ionic surfactant.
3. The capsule of claim 1, wherein the PCM comprises a
C.sub.10-C.sub.40 hydrocarbyl.
4. The capsule of claim 1, wherein the metal complex containing
oxygen comprises NaAlSi.sub.2O.sub.6.
5. The capsule of claim 1, wherein the reaction product forms a
crystalline outer shell and the outer shell is a discontinuous
shell.
6. The capsule of claim 1, wherein the surfactant solution is in an
organic solvent and the siloxane forms a sol-gel outer shell.
7. The capsule claim 1, wherein the capsule is a microcapsule or a
macrocapsule.
8. The capsule of claim 1, wherein the capsule is a microcapsule
having a diameter of about 15 .mu.m to about 25 .mu.m.
9. The capsule of claim 1, wherein the polymer wall comprises one
or more of a melamine formaldehyde, a crosslinked melamine
formaldehyde, a resorcinol urea formaldehyde, a poly-urea
formaldehyde, an acrylic polymer, and a gelatin.
10. The capsule of claim 9, wherein the polymer wall comprises a
crosslinked melamine formaldehyde and the cross-linked melamine
comprises melamine formaldehyde polymerized with a crosslinking
agent comprising: (a) a reaction product of a cyclic urea (U) and a
multifunctional aldehyde (A), and (b) at least one crosslinker
selected from the group consisting of (b1) reaction products of an
aminotriazine and at least one aldehyde selected from the group
consisting of aliphatic monoaldehydes and multifunctional aliphatic
aldehydes having the structure Y(CHO).sub.n, where Y is an
n-functional aliphatic residue, and n is greater than 1, where U is
not dihydroxyethylene urea if the crosslinker (b) is (b1), (b2)
reaction products of urea and/or cyclic ureas and formaldehyde,
(b3) alkoxycarbonylaminotriazines, (b4) multifunctional isocyanates
which may be partially or completely blocked, (b5) reaction
products of phenols and aliphatic monoaldehydes, (b6)
multifunctional epoxides, (b7) multifunctional aziridines, (b8)
multifunctional carbodiimides, wherein any of the crosslinkers (a)
and (b) which have hydroxyl groups may be etherified with one or
more linear, branched, or cyclic aliphatic alcohols.
11. The capsule of claim 10, wherein the capsule has a free
formaldehyde level of less than 100 pm.
12. The capsule of claim 1, wherein the capsule has an enthalpy of
greater than 75 J/g as measured by differential scanning
calorimetry.
13. A textile fabric comprising a plurality of capsules according
to claim 1.
14. The textile fabric of claim 13, wherein the textile fabric is
an article of clothing.
15. The textile fabric of claim 13, wherein each capsule of the
plurality of capsules has an enthalpy of greater than 75 J/g as
measured by differential scanning calorimetry.
16. The textile fabric of claim 13, wherein the plurality of
capsules forms a layer having a thickness of about 1 mm to about 50
mm on a surface of the textile fabric.
Description
RELATED APPLICATIONS
[0001] This application is a continuation of U.S. application Ser.
No. 15/906,015, filed Feb. 27, 2018, which claims the benefit of
U.S. Provisional Application No. 62/464,733, filed Feb. 28, 2017,
which is incorporated herein in its entirety.
TECHNICAL FIELD
[0002] The present disclosure relates to capsules having a polymer
wall encapsulating a core composition including a phase change
material (PCM) and an outer shell comprising a siloxane tethered to
the polymer wall by a surfactant.
BACKGROUND
[0003] Articles made from cotton fabric and other natural material
fabrics (such as linen, wool, etc.) are generally absorbent, and
may feel comfortable under conditions of very light perspiration.
However, under conditions of heavier perspiration, these fabrics
feel wet, heavy and clingy, restricting movement and becoming
uncomfortable to wear.
[0004] Wicking technology for apparel has been developed to address
this problem. Generally, wicking aims to pull moisture away from
the skin of the wearer and make the wearer more comfortable while
being active. In the early to mid-nineties, patent applications
were filed for moisture-managing clothing, where a fabric would
pull moisture away from the skin via a dual-layered fabric, where
the layer closest to the skin would be hydrophobic, and the outer
layer would be hydrophilic. In some cases, these two components
were woven into the same layer of clothing, in order to make the
material thinner. The hydrophobic layer would wick moisture, so as
to pull it away from the wearer, then force the moisture into
contact with the hydrophilic layer, which would then absorb the
moisture and spread it out along the surface of an article of
clothing. The thinning of the moisture would allow evaporation from
the clothing at a quicker rate than normal fabric. The hydrophobic
layer would typically consist of a polyester or cotton fiber,
whereas the hydrophilic layer would typically consist of a nylon or
polypropylene fiber. One main issue with this is that the wicking
and evaporating of the moisture is not noticeable to the
wearer.
[0005] Accordingly, there is a need for better wicking and overall
moisture control in clothing articles.
SUMMARY
[0006] In one aspect, capsules, such as microcapsules or
macrocapsules, are disclosed that have a core composition
comprising a phase changing material encapsulated in a polymer wall
and having an outer shell formed of a siloxane chemically bonded to
an exterior surface of the polymer wall by a surfactant. The
surfactant is one or more of a cationic surfactant, an anionic
surfactant, and a non-ionic surfactant, and the polymer wall
comprises one or more of a melamine formaldehyde, a crosslinked
melamine formaldehyde, a resorcinol urea formaldehyde, a poly-urea
formaldehyde, an acrylic polymer, and a gelatin. The siloxane can
form a crystalline outer shell or a sol-gel outer shell. When the
capsules are microcapsules, the microcapsules may have a diameter
of about 15 .mu.m to about 25 .mu.m. The capsules have an enthalpy
of greater than 75 J/g as measured by differential scanning
calorimetry.
[0007] In all embodiments, the PCM can be a C.sub.10-C.sub.40
hydrocarbyl and in some embodiments, the siloxane is
NaAlSi.sub.2O.sub.6. The siloxane can form a crystalline outer
shell or a sol-gel outer shell.
[0008] In one embodiment, the polymer wall is a crosslinked
melamine formaldehyde and the cross-linked melamine comprises
melamine formaldehyde polymerized with a crosslinking agent
comprising:
[0009] (a) a reaction product of a cyclic urea (U) and a
multifunctional aldehyde (A), and
[0010] (b) at least one crosslinker selected from the group
consisting of [0011] (b1) reaction products of an aminotriazine and
at least one aldehyde selected from the group consisting of
aliphatic monoaldehydes and multifunctional aliphatic aldehydes
having the structure Y(CHO).sub.n, where Y is an n-functional
aliphatic residue, and n is greater than 1, where U is not
dihydroxyethylene urea if the crosslinker (b) is (b1), [0012] (b2)
reaction products of urea and/or cyclic ureas and formaldehyde,
[0013] (b3) alkoxycarbonylaminotriazines, [0014] (b4)
multifunctional isocyanates which may be partially or completely
blocked, [0015] (b5) reaction products of phenols and aliphatic
monoaldehydes, [0016] (b6) multifunctional epoxides, [0017] (b7)
multifunctional aziridines, [0018] (b8) multifunctional
carbodiimides, wherein any of the crosslinkers (a) and (b) which
have hydroxyl groups may be etherified with one or more linear,
branched, or cyclic aliphatic alcohols. The crosslinked melamine
formaldehyde capsules have a free formaldehyde level of less than
100 pm.
[0019] In another aspect, textile fabrics are disclosed that have a
plurality of the capsules disclosed herein incorporated therein,
which may be present as a layer on a surface of the textile fabric
at a thickness of about 1 mm to about 50 mm. The textile fabric may
be bedding or an article of clothing. The plurality of capsules has
an enthalpy that is greater than 75 J/g as measured by differential
scanning calorimetry.
[0020] In another aspect, methods for producing an outer shell of a
capsule, such as a microcapsule or macrocapsule, are disclosed. The
method includes the provision of pre-formed capsules that have a
core composition comprising a phase changing material encapsulated
by a polymer wall, treating pre-formed capsules with a surfactant
solution to form a surfactant-coated capsule (the surfactant is
tethered to the exterior surface of the capsule), and treating the
surfactant-coated capsule with a compound containing a siloxane
functional group. The surfactant connects the compound containing
the siloxane functional group to the exterior surface of the
polymer wall and the compound containing the siloxane functional
group forms an outer shell of the capsule. The compound containing
a siloxane functional group may be one or more of sodium silicate,
tetramethyl orthosilicate, and tetraethyl orthosilicate. In one
embodiment, the surfactant solution is in an organic solvent and
the outer shell is a sol-gel reaction product.
[0021] The surfactant solution is an aqueous solution, and the
method further comprises, subsequent to treating with the compound
containing the siloxane functional group, treating the
surfactant-coated capsules with a metal-oxygen containing compound
to form a crystalline outer shell. The metal-oxygen containing
compound comprises one or more of sodium, aluminum, calcium,
potassium, iron, manganese, or magnesium as an acetate, phosphate,
sulfate, ethoxide, silicate, hydroxide, oxide hydroxide, nitrate,
thiocyanate, chlorate, and/or nitrite.
BRIEF DESCRIPTION OF THE DRAWINGS
[0022] FIG. 1 is an SEM image, 0.10 mm scale, of capsules having a
melamine-formaldehyde polymer wall encapsulating a phase change
material before addition of a sodium aluminum silicate crystalline
shell.
[0023] FIG. 2 is an SEM image, 10 .mu.m scale, of the capsules of
FIG. 1 after the addition of a sodium aluminum silicate
(NaAlSi.sub.2O.sub.6) crystalline shell, which is tethered to the
melamine-formaldehyde polymer wall.
[0024] FIG. 3 is a flow diagram of addition of the
NaAlSi.sub.2O.sub.6 shell to pre-formed capsules, represented as a
cross-sectional view.
[0025] FIG. 4 is a flow diagram of an alternate embodiment of
addition of a crystalline silicate compound as an outer shell,
represented as a cross-sectional view, to pre-formed capsules.
[0026] FIG. 5A is a FTIR spectra of the pre-formed PCM
microcapsules (no tethered outer shell).
[0027] FIG. 5B is a FTIR spectra of NaAlSi.sub.2O.sub.6 coated PCM
microcapsules.
[0028] FIG. 6 is an FTIR spectra of siloxane coated
microcapsules.
[0029] FIG. 7 is a bar graph comparing the vertical wicking
distance of a cloth comprising inventive examples compared to
existing wicking "cooling powder."
[0030] FIG. 8 is a bar graph comparing the heat absorbance (J/g) of
inventive examples compared to existing wicking "cooling
powder."
DETAILED DESCRIPTION
[0031] The following detailed description will illustrate the
general principles of the invention, examples of which are
additionally illustrated in the accompanying drawings. In the
drawings, like reference numbers indicate identical or functionally
similar elements.
[0032] Provided in this disclosure are capsules including a core
encapsulated by a polymer wall, and an outer shell having a
siloxane tethered to the exterior surface of the polymer wall,
which renders the capsule capable of wicking moisture, such as
water and/or sweat. The core of such capsules comprises a phase
changing material, which enables the capsules to have a high heat
of absorption. As such, the capsules are suitable for inclusion in
a textile material or fabric to cool a wearer of an article of
clothing made therefrom and to pull moisture away from the wearer's
body. To attach the siloxane to the exterior of the pre-formed
capsules, a surfactant acts as a tether to connect the crystalline
silicate compound to the exterior surface of the polymer wall,
typically through electrostatic interactions, i.e., a chemical
bond. For example, a hydrophobic portion of a surfactant can
interact with the polymer wall via hydrophobic association.
[0033] As used herein, the term "about" allows a degree of
variability in a value or range, for example, within 10% of a
stated value or of a stated limit of a range for all embodiments,
but within 5% of a stated value or of a stated limit of a range in
more preferred embodiments.
[0034] As used herein, the term "hydrocarbon" refers to a
functional group or molecule that includes carbon and hydrogen
atoms. The term can also refer to a functional group or molecule
that normally includes both carbon and hydrogen atoms but wherein
some or all the hydrogen atoms are substituted with other
functional groups.
[0035] As used herein, the term "substituted" refers to an organic
group as defined in which one or more hydrogen atoms contained
therein are replaced by one or more substituents. The term
"functional group" or "substituent" as used herein refers to a
group that can be or is substituted onto a molecule or onto an
organic group. Examples of substituents or functional groups
include, but are not limited to, a halogen (e.g., F, Cl, Br, and
I); an oxygen atom in groups such as hydroxy groups, alkoxy groups,
aryloxy groups, aralkyloxy groups, oxo(carbonyl) groups, carboxyl
groups including carboxylic acids, carboxylates, and carboxylate
esters; a sulfur atom in groups such as thiol groups, alkyl and
aryl sulfide groups, sulfoxide groups, sulfone groups, sulfonyl
groups, and sulfonamide groups; a nitrogen atom in groups such as
amines, hydroxyamines, nitriles, nitro groups, N-oxides,
hydrazides, azides, and enamines; and other heteroatoms in various
other groups.
[0036] Referring to FIGS. 1 and 2, SEM image of capsules are shown.
FIG. 1 comprises capsules having a melamine-formaldehyde polymer
wall encapsulating a phase change material before addition of a
sodium aluminum silicate (NaAlSi.sub.2O.sub.6) crystalline shell.
FIG. 2 comprises the same capsules after addition of the
NaAlSi.sub.2O.sub.6 crystalline shell.
[0037] Referring to FIG. 3, capsule 200c has an outer
NaAlSi.sub.2O.sub.6 shell 206 surrounding a polymer wall 204
encapsulating a PCM 202 as the core. The NaAlSi.sub.2O.sub.6 shell
206 is typically an outermost shell or coating, but in some
embodiments another coating can be applied thereto. For example, an
adhesive coating (e.g., a discontinuous adhesive coating) can be
applied to allow the capsules to adhere to a surface. The capsule
200c having the NaAlSi.sub.2O.sub.6 shell 206 is formed from a
preformed capsule 200 that has one or more PCMs 202 as the core
encapsulated within the polymer wall 204. Polymer wall 204 is used
as a scaffold on which a surfactant 208 is tethered, in FIG. 3 a
cationic surfactant, and the surfactant 208 tethers the
NaAlSi.sub.2O.sub.6 shell 206 to the exterior surface 205 of the
polymer wall 204.
[0038] As shown in FIG. 3, capsule 200 is treated with a cationic
surfactant to form surfactant-coated capsule 200a. The
surfactant-coated capsule 200a is then treated with a sodium
silicate 213 to form sodium silicate-coated capsule 200b. The
silicate-coated capsule 200b is then treated with an aluminum
complex 214 containing oxygen, specifically nano-boehmite in this
example, to form a NaAlSi.sub.2O.sub.6 shell 206. The nano-boehmite
is dissolved in water, such as deionized water, and the
NaAlSi.sub.2O.sub.6 shell 206 formed may be a continuous (i.e., a
full, endless coating) or a discontinuous (partial) shell. The
polymer wall 204, PCM 202, and surfactant 208 can be any polymer
wall, PCM, or cationic surfactant described herein.
[0039] Referring to FIG. 4, in another embodiment, the outer shell,
here 406, may be formed on the exterior surface 405 of the polymer
wall 404 of a pre-formed capsule 400 containing a core composition
402 by introducing an anionic surfactant 408 to form the
surfactant-containing intermediate capsule 400a. The surfactant 408
is introduced as an aqueous solution. The pre-formed capsule 400
can be added to the surfactant solution (or vice versa) with
stirring and heating (if desired) for sufficient time to allow the
surfactant 408 to tether to the polymer wall 404 thereof. After the
surfactant 408 is applied to the polymer wall 404, the
surfactant-containing intermediate capsule 400a is treated with a
metal-oxygen containing compound to form a secondary intermediate
capsule 400b. For example, the metal-oxygen containing compound
(such as boehmite) can be added to an aqueous solution of
surfactant-containing intermediate capsule 400a and stirred for a
sufficient time to allow the compound to chemically bond to the
surfactant 408. The secondary intermediate capsule 400b is then
treated with a compound containing a siloxane functional group 412
to form a crystalline, silicate outer shell 406. The compound
containing a siloxane functional group 412 is dissolved in water,
such as deionized water, and the crystalline outer shell 406 formed
may be a continuous (i.e., a full, endless coating) or a
discontinuous (partial) shell.
[0040] While FIGS. 3 and 4 are described as starting with
pre-formed capsules, the methods herein may further include forming
the capsules. The capsules can be formed by encapsulating a PCM in
a polymer shell using known methods of encapsulations such as
coacervation, polymer-polymer phase separation, interfacial and
dispersion polymerization, in-situ polymerization, solvent phase
separation, desolvation, solvent evaporation, spray drying, spray
chilling, matrix encapsulation, various types of fluid bed,
extrusion, and various hybrid systems. The PCM and polymer shell
can be any PCM and polymer shell described herein.
[0041] As discussed above with respect to the example set forth in
FIG. 3, the outer shell comprising the siloxane may form a
crystalline outer shell; see resultant capsules 200c in FIG. 3 and
the SEM image in FIG. 2. When the method of making the capsules
includes aqueous solutions for the surfactant and the compound
containing a siloxane functional group and a metal-oxygen
containing compound is used to precipitate the siloxane as a
silicate (or vice versa), the outer shell will be crystalline. In
other embodiments, as demonstrated in working example 5, the outer
shell comprising the siloxane may form a sol-gel product, which is
not crystalline. Here, the solutions have organic solvents and,
after the surfactant has been tethered to the exterior surface of
the polymer wall, a silicate is added, and adequate time is
provided for the silicate to be chemically bonded to the
surfactant. Then, a strong base is added to catalyze the reaction
of the silicate to form the outer shell.
[0042] Each PCM in the core can include a substituted or
unsubstituted, saturated or unsaturated C.sub.10-C.sub.40
hydrocarbon, particularly a C.sub.10-C.sub.40 hydrocarbon having a
melting point of about -30.degree. C. to about 70.degree. C., and
mixtures thereof. In some embodiments, the PCM can be an ester, an
alcohol, a carboxylic acid, a salt hydrate, an ether, or a mixture
thereof. The PCM of the core can be selected for the purpose having
a melting point that would be comfortable to the wearer. Some
preferred embodiments include a C.sub.15-C.sub.25 hydrocarbon or
mixtures thereof, since these hydrocarbons have melting points in a
range that is comfortable to a wearer of an article of clothing
having the capsules disclosed herein incorporated therein.
[0043] Examples of saturated or unsaturated C.sub.10-C.sub.40
hydrocarbons, which are branched or linear, include, but are not
limited to, n-tetradecane, n-pentadecane, n-hexadecane,
n-heptadecane, n-octadecane, n-nonadecane, n-eicosane,
n-heneicosane, n-docosane, n-tricosane, n-tetracosane,
n-pentacosane, n-hexacosane, n-heptacosane, and n-octacosane.
Examples of cyclic hydrocarbons include, but are not limited to,
cyclohexane, cyclooctane, and cyclodecane. Examples of aromatic
hydrocarbyl compounds include, but are not limited to, benzene,
naphthalene, biphenyl, and o- or n-terphenyl. Examples of
C.sub.10-C.sub.40-alkyl-substituted aromatic hydrocarbons include,
but are not limited to, dodecylbenzene, tetradecylbenzene,
hexadecylbenzene, hexylnaphthalene or decyinaphthalene. Examples of
saturated or unsaturated C.sub.10-C.sub.30-fatty acids include, but
are not limited to, lauric, stearic, oleic or behenic acid, and
eutectic mixtures of decanoic acid with myristic, palmitic or
lauric acid. Examples of fatty alcohols include, but are not
limited to, lauryl, stearyl, oleyl, myristyl, cetyl alcohol,
mixtures such as coconut fatty alcohol, and the so-called oxo
alcohols which are obtained by hydroformylation of .alpha.-olefins
and further reactions. Examples of C.sub.a-alkyl esters include,
but are not limited to, C.sub.1-C.sub.10-alkyl esters of fatty
acids, such as propyl palmitate, methyl stearate or methyl
palmitate, and their eutectic mixtures or methyl cinnamate.
Examples of natural and synthetic waxes include, but are not
limited to, montan acid waxes, montan ester waxes, polyethylene
wax, oxidized waxes, polyvinyl ether wax, and ethylene vinyl
acetate wax. In some embodiments, the PCM is a paraffin wax.
[0044] In all embodiments, the PCM can include one or more of
docosane, docosene, eicosane, heneicosane, heptadecane, hexadecane,
nonadecane, octadecane, tetracosane, and tricosane. In some
embodiments, the core composition includes octadecane or is
octadecane.
[0045] The core composition can have a melting point of about
-30.degree. C. to about 70.degree. C. For textile materials
suitable for articles of clothing a melting point in a range that
is comfortable to the wearer is preferred. Accordingly, a core
composition with a melting point of 15.degree. C. to about
40.degree. C. or more particularly about 25.degree. C. to about
35.degree. C. is useful. If the capsules are intended to be
incorporated in a material or fabric to be used in cold
environments, a PCM, or mixture of PCMs, with a lower melting point
can be selected, for example about -20.degree. C. to about
5.degree. C. If the capsules are intended to be incorporated in a
fabric to be used in hot environments, a PCM, or mixture of PCMs,
with a higher melting point can be selected, for example about
25.degree. C. to about 45.degree. C.
[0046] In all embodiments, the capsules typically have a relatively
high payload of a core composition relative to the amount of
material forming the polymer wall and the outer shell. The core in
the capsules can be about 10% to about 90% by weight of the
capsule. In some embodiments, the PCM is about 70% to about 80% by
weight, more particularly about 75% to about 85%, and even more
particularly about 77% to about 81% by weight of the capsule. In
some embodiments, the PCM is at least 50% by weight of capsule,
more particularly at least 70%, and even more particularly at least
80% by weight of the capsule.
[0047] The polymer wall can include a melamine formaldehyde, a
crosslinked melamine formaldehyde, a resorcinol urea formaldehyde,
a poly-urea formaldehyde, an acrylic polymer, a gelatin, or a
mixture thereof, or another known wall material made using known
methods such as in-situ polymerization, interfacial
polycondensation, interfacial cross-linking, or any other known
method. In some embodiments, the polymer wall includes crosslinked
melamine formaldehyde.
[0048] The polymer wall and capsule can have low levels of
formaldehyde. For example, melamine formaldehyde walled
microcapsules can have levels of free formaldehyde around 200 ppm,
however, a crosslinked melamine formaldehyde walled microcapsule
(as discussed in detail below) can have free formaldehyde levels of
less than about 100 pm, less than about 50 ppm, less than about 20
ppm, or less than about 10 ppm.
[0049] The in-situ polymerization process of polycondensation can
prepare capsules having a melamine formaldehyde polymer wall and a
PCM core. The process can include a melamine formaldehyde
prepolymer, soluble in a continuous water phase, and a hydrophobic
PCM, as dispersed core droplets. As the polymerization reaction
starts in the aqueous solution, the formed oligomers start to
collapse on the surface of the core droplets. On the surface,
polymerization continues, and crosslinking occurs that results in
the formation of a solid melamine formaldehyde wall.
[0050] Capsules having a gelatin wall encapsulating a core material
are known, as taught in Onder et al. Encapsulation of Phase Change
Materials by Complex Coacervation to Improve Thermal Performances
of Woven Fabrics, Thermochimica Acta. 2008, 467, 63-72, and in
Patrick et al. Optimization Process by Complex Coacervation of Fish
Oil Using Gelatin/SDS/NaCMC and Secondary Coating Application with
Sodium Polyphosphate, IJSBAR. 2014, 17, 74-94.
[0051] For a crosslinked melamine microcapsule, reference is made
to co-pending U.S. Provisional Application No. 62/206,367 for
methods of making the microcapsule, which is incorporated herein by
reference. These microcapsules are made from a melamine
formaldehyde prepolymer comprising a crosslinking agent, the
crosslinking agent being a mixture of:
[0052] (a) a reaction product of a cyclic urea (U) and a
multifunctional aldehyde (A), and
[0053] (b) at least one crosslinker selected from the group
consisting of [0054] (b1) reaction products of an aminotriazine and
at least one aldehyde selected from the group consisting of
aliphatic monoaldehydes and multifunctional aliphatic aldehydes
having the structure Y(CHO).sub.n, where Y is an n-functional
aliphatic residue, and n is greater than 1, where U is not
dihydroxyethylene urea if the crosslinker (b) is (b1), [0055] (b2)
reaction products of urea and/or cyclic ureas and formaldehyde,
[0056] (b3) alkoxycarbonylaminotriazines, [0057] (b4)
multifunctional isocyanates which may be partially or completely
blocked, [0058] (b5) reaction products of phenols and aliphatic
monoaldehydes, [0059] (b6) multifunctional epoxides, [0060] (b7)
multifunctional aziridines, [0061] (b8) multifunctional
carbodiimides, wherein any of the crosslinkers (a) and (b) which
have hydroxyl groups may be etherified with one or more linear,
branched, or cyclic aliphatic alcohols, polymerized by adjusting
the pH and/or addition of urea. The crosslinking agent (b) is
preferably at least one crosslinker selected from the group
consisting of (b1), (b2), (b3), and (b5). These cross-linked
melamine microcapsules have MF prepolymer present in a ratio by
weight percent to the crosslinking agent of 1:1 to 4:1, more
preferably 1.5:1 to 3.75:1. These capsules have an initial free
formaldehyde level of less than 100 ppm, more preferably less than
80 ppm, less than 60 ppm, and even more preferably less than 40
ppm. Such a crosslinking agent is available from Allnex USA
Inc.
[0062] In one embodiment, the crosslinking agent has the reaction
product of a cyclic urea U and a multifunctional aliphatic aldehyde
A, portion (a), in a mixture with one or more of (b1), (b2), (b3)
and (b5). Mixtures of the reaction product of a cyclic urea (U) and
a multifunctional aldehyde (A) and one or more of the crosslinkers
(b) have a ratio of the mass of the reaction product to the mass of
the crosslinker (b) (or to the sum of the masses of all
crosslinkers (b)) from 1/99 to 99/1, preferably from 10/90 to
90/10, and more preferably from 30/70 to 70/30.
[0063] The multifunctional aldehyde A has the formula OHC--R'--CHO
where R' may be a direct bond or a divalent radical which may
preferably be a linear, branched or cyclic aliphatic radical and
may have from one to twenty carbon atoms, both these options for R'
leading to a divalent aldehyde having exactly two --CHO groups, or
an aliphatic divalent radical which may be linear, branched or
cyclic and may have from one to twenty carbon atoms, which radical
carries at least one additional aldehyde group --CHO, which latter
option leads to trivalent or polyvalent aldehydes having at least
three aldehyde groups. Preferred aldehydes are divalent aliphatic
aldehydes, particularly glyoxal, malonic dialdehyde, succinic
dialdehyde, and glutaric dialdehyde. Especially preferred is
glyoxal in an aqueous solution, as anhydrous solid which has to be
cooled as its melting temperature is 15.degree. C., or in the form
of its dimer or trimer, optionally in solid hydrated form as
dihydrates, or in the form of its addition products with sulphites
or hydrogen sulphites which decompose under acidic conditions.
[0064] The cyclic ureas U which may be used according to the
present invention have at least one unsubstituted amidic --NH
group. These cyclic ureas are cycloaliphatic or bicycloaliphatic
compounds having an element of the structure --NH--CO--NH-- within
a ring structure, the total number of ring atoms preferably being
from 5 to 7 (ethylene urea, 1,2-propylene urea, 1,3-propylene urea,
1,4-butylene urea or tetramethylene urea). Particularly preferred
is ethylene urea or a mixture comprising ethylene urea, especially
a mixture comprising at least a mass fraction of 50% of ethylene
urea. In the case of a bicyclic compound, the simplest structure is
glycoluril or acetylene diurea. Hydroxy functional ureas are not
useful for the present invention. The cyclic ureas may be
substituted, preferably by alkyl groups on the N-- or C-atoms, or
both, the alkyl residues preferably having from one to four carbon
atoms. At least one of the nitrogen atoms must remain unsubstituted
to enable reaction with the aldehyde functional molecule.
Preferably, at least one cyclic urea is selected from the group
consis