U.S. patent application number 16/587144 was filed with the patent office on 2020-04-23 for curvilinear circular-arc tooth gears for use in external gear pumps.
The applicant listed for this patent is The Government of the United States of America, as represented by the Secretary of the Navy. Invention is credited to Logan Williams.
Application Number | 20200124047 16/587144 |
Document ID | / |
Family ID | 70280596 |
Filed Date | 2020-04-23 |
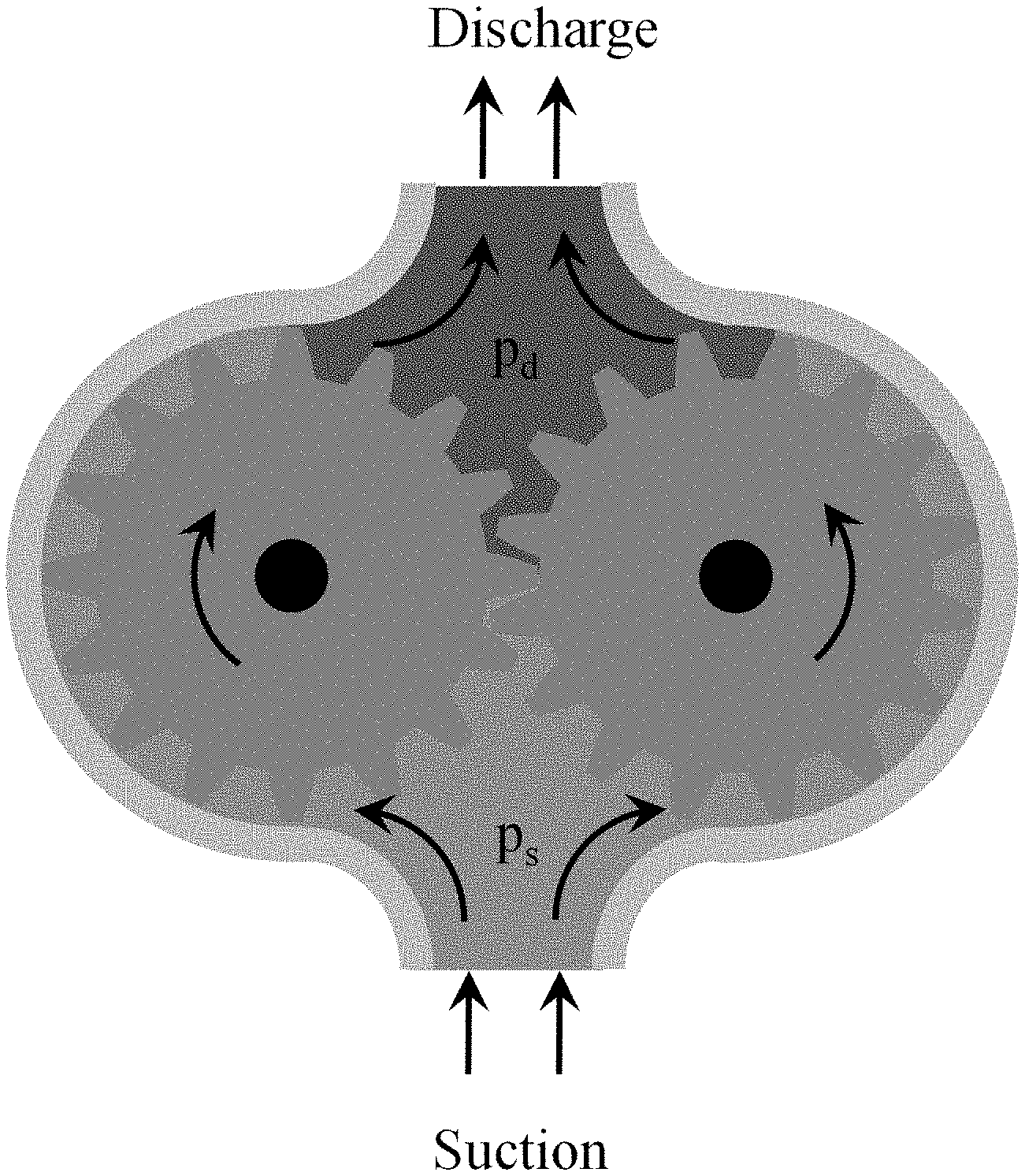






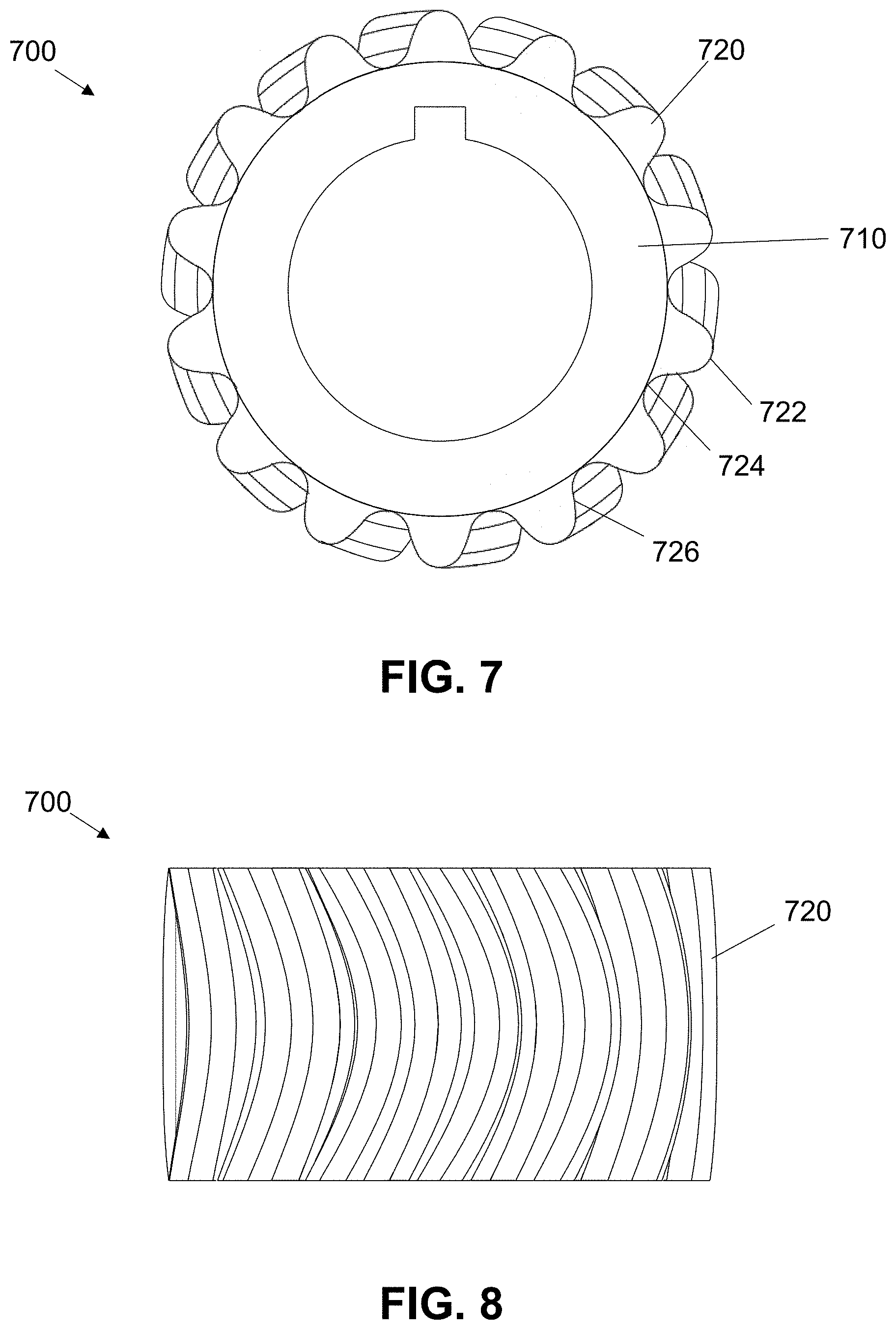
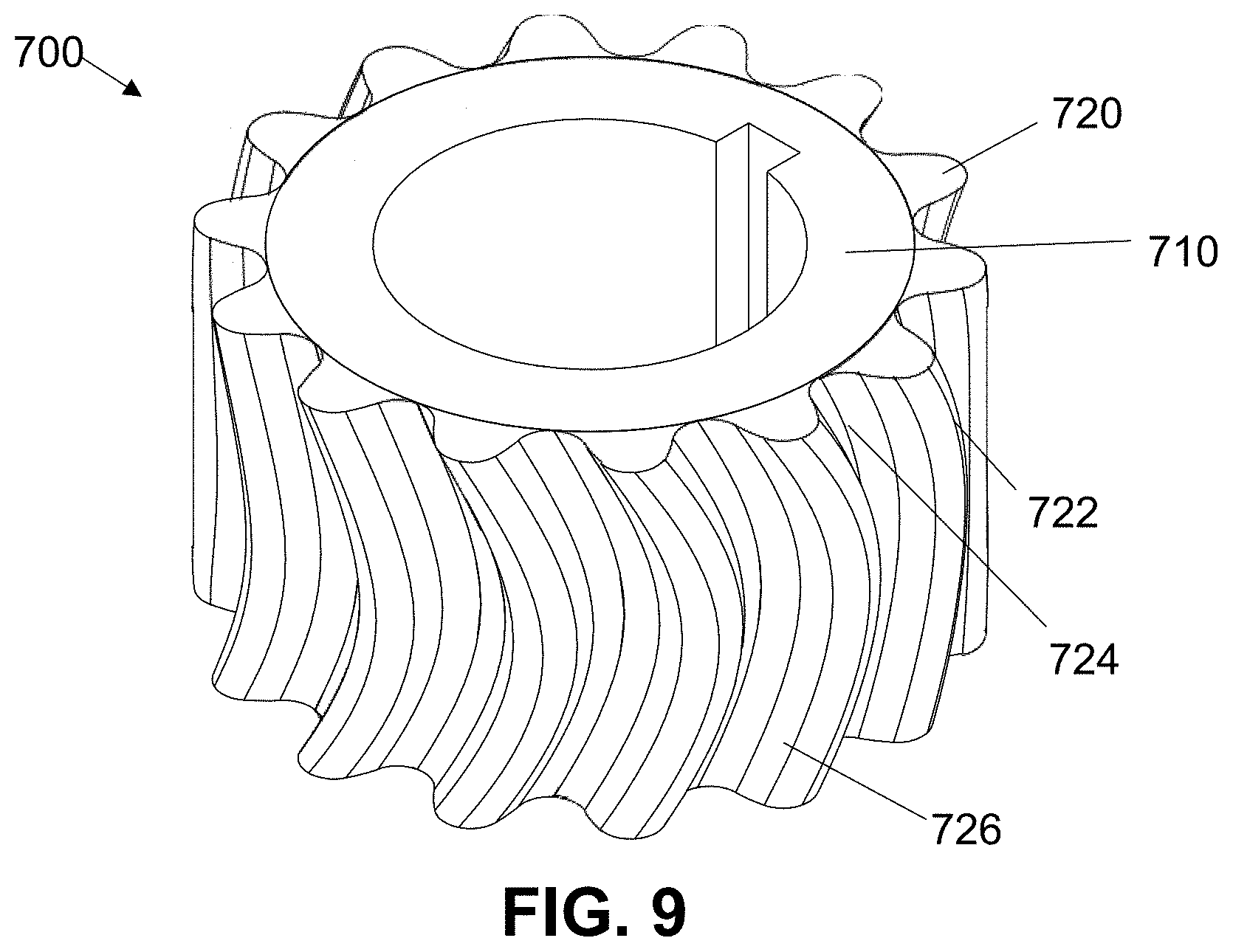


View All Diagrams
United States Patent
Application |
20200124047 |
Kind Code |
A1 |
Williams; Logan |
April 23, 2020 |
Curvilinear circular-arc tooth gears for use in external gear
pumps
Abstract
A curvilinear circular-arc-toothed (CCAT) gear for improving
gear performance and reducing noise while avoiding axial loads
common to helical gears includes an annular gear body; and a gear
tooth having a hybrid gear tooth profile comprising one or more
curves configured to provide a sweep of the gear tooth space by a
mating gear tooth while maintaining smooth contact during gear
mesh, and wherein the gear tooth extends along an axial length of
the gear body along an axial profile.
Inventors: |
Williams; Logan;
(Alexandria, VA) |
|
Applicant: |
Name |
City |
State |
Country |
Type |
The Government of the United States of America, as represented by
the Secretary of the Navy |
Arlington |
VA |
US |
|
|
Family ID: |
70280596 |
Appl. No.: |
16/587144 |
Filed: |
September 30, 2019 |
Related U.S. Patent Documents
|
|
|
|
|
|
Application
Number |
Filing Date |
Patent Number |
|
|
62749498 |
Oct 23, 2018 |
|
|
|
Current U.S.
Class: |
1/1 |
Current CPC
Class: |
F04C 2230/10 20130101;
F04C 2/084 20130101; F04C 2/18 20130101; F04C 15/0042 20130101 |
International
Class: |
F04C 15/00 20060101
F04C015/00; F04C 2/08 20060101 F04C002/08 |
Goverment Interests
FEDERALLY-SPONSORED RESEARCH AND DEVELOPMENT
[0002] The United States Government has ownership rights in this
invention. Licensing inquiries may be directed to Office of
Technology Transfer, US Naval Research Laboratory, Code 1004,
Washington, D.C. 20375, USA; +1.202.767.7230;
techtran@nrl.navy.mil, referencing NC 107458.
Claims
1. A curvilinear circular-arc-toothed (CCAT) gear for improving
gear performance and reducing noise while avoiding axial loads
common to helical gears, the CCAT gear comprising: an annular gear
body; and a set of gear teeth, with each tooth extending radially
away from the gear body and extending axially along the gear body,
and wherein the gear tooth has a cross-sectional profile transverse
to the rotational axis of the gear body, the cross-sectional
profile formed from a hybridization of two or more curves, the two
or more curves defining a tooth tip, a tooth flank, and a tooth
root, and wherein the gear tooth has an axial tooth profile
defining a circumferential positioning of the gear tooth on the
gear body relative to a respective axial positioning of the gear
tooth on the gear body, the axial tooth profile being generally
symmetric across the midplane of the gear to reduce axial loading
on gears induced by gear meshing.
2. The CCAT gear of claim 1, wherein the axial tooth profile is
continuously differentiable.
3. The CCAT gear of claim 1, wherein the axial tooth profile is
fully symmetric about an axial mid-plane of the gear to eliminate
axial loading from gear meshing.
4. The CCAT gear of claim 1, wherein the axial tooth profile has an
initial helix angle at each end of the gear.
5. The CCAT gear of claim 1, wherein the axial tooth profile is
curvilinear.
6. The CCAT gear of claim 5, wherein the axial tooth profile is a
half-period sinusoid function.
7. The CCAT gear of claim 1, wherein the gear tooth cross-sectional
profile is configured such that the tip fully sweeps along a tooth
root of a mating gear.
8. The CCAT gear of claim 7, wherein the tooth tip and root
profiles include a circular-arc.
9. The CCAT gear of claim 1, wherein the tooth flank is a curve
that allows smooth meshing of the gears.
10. The CCAT gear of claim 9, wherein the tooth flank is involute,
cycloidal, or circular arc.
11. The CCAT gear of claim 9, wherein the tooth flank is an
involute curve.
12. The CCAT gear of claim 1, wherein the tooth tip is circular,
the tooth flank is involute, and the tooth root is circular.
13. The CCAT gear of claim 1, wherein the two or more curves of the
hybrid tooth profile are combined such that the cross-sectional
profile of the tooth is continuously differentiable.
14. The CCAT gear of claim 1, wherein the gear teeth extend
radially outward from the annular body.
15. A curvilinear circular-arc-toothed (CCAT) gear for improving
gear performance and reducing noise while reducing axial loads
common to helical gears, the CCAT gear comprising: an annular gear
body; and a gear tooth having a hybrid gear tooth profile
comprising one or more curves configured to provide a sweep of the
gear tooth space by a mating gear tooth while maintaining smooth
contact during gear mesh, and wherein the gear tooth extends along
an axial length of the gear body along an axial profile.
16. The CCAT gear of claim 15, wherein the hybrid gear tooth
profile has a tip that conforms to a tooth root of the mating gear
to allow fully sweeping out the volume between gear teeth to
improve efficiency and reduce noise.
17. The CCAT gear of claim 16, wherein the hybrid gear tooth
profile has a circular arc at a tooth tip, a circular arc at a
tooth root, and the profile combines the two arcs with an involute
curve between the circular arcs to allow a full sweep of the volume
between gear teeth while maintaining a constant line of action of
the mesh.
18. The CCAT gear of claim 15, wherein a radius of a tooth tip arc
is equal to or less than a radius of a tooth root arc.
19. The CCAT gear of claim 15, wherein the hybrid profile is
continuously differentiable.
20. The CCAT gear of claim 15, wherein the axial profile is
configured to cause gradual contact between teeth to reduce shock
stress on the gear teeth and noise during meshing.
21. The CCAT gear of claim 15, wherein the axial profile is
configured to balance axial forces imparted on the gears from
meshing to reduce net axial load on the gear.
Description
RELATED APPLICATIONS
[0001] This application claims the benefit of U.S. Provisional
Application No. 62/749,498 filed Oct. 23, 2018, which is hereby
incorporated herein by reference.
FIELD OF INVENTION
[0003] The present invention relates generally to gears, and more
particularly to gears used in gear pumps.
BACKGROUND
[0004] The basic function of an external gear pump as shown in FIG.
1, is to drive the flow of a fluid through the rotary action of two
meshed gears. At one side of the meshing zone (termed the suction
side), the gear teeth unmesh, creating a void that draws fluid into
the tooth spaces of the gears. These fluid packets are then rotated
around the gear into the discharge region; at this side the teeth
mesh together, driving the fluid out of the inter-tooth spaces.
This pushes the fluid out the discharge of the pump through
whatever hydraulic load is connected to the pump. As a
fixed-displacement pump, a gear pump will pressurize the fluid to
whatever pressure is required to drive the flow rate created by the
meshing gears (a mechanical analog to a current-limited power
supply).
[0005] It is important to note that there are two main fluid
pathways: the intentional hydraulic load (i.e. a piston, actuator,
motor, etc.) and an internal leakage path where pressurized fluid
in the discharge leaks across the gears back into the suction side
of the pump. The internal leakage flow rate is dependent on the
size of the clearances between components, as well as the discharge
pressure (the higher the pressure, the more fluid that can be
forced through an opening). Thus, one of the limitations to the
maximum discharge pressure of a pump is the internal sealing to
prevent appreciable leakage. This results in gear pump designs
where there is minimal radial clearance between the tips of the
gear teeth and the pump casing. Additionally, the axial surfaces of
the gears are sealed with two wear plates that conform to the
pumping cavity shape. These wear plates ensure a tight seal and
minimize leakage, but can also contribute to frictional losses
during operation.
[0006] The most common gear tooth profile used in gear pumps is an
involute profile. The primary advantages of the involute profile is
that it provides smooth, consistent contact between two gears
during meshing, and that it is relatively cost-effective to machine
involute gears using basic cutting and hobbing techniques.
SUMMARY OF INVENTION
[0007] The key disadvantage of an involute profile is that during
the meshing action, the addendum of one tooth does not fully sweep
the dedendum of the corresponding tooth of the mating gear. This
results in a pocket of fluid being trapped between the teeth during
meshing. As the meshing action progresses, the fluid pocket
pressure rises significantly, contributing to noise and gear
wear.
[0008] According to one aspect of the invention, a curvilinear
circular-arc-toothed (CCAT) gear for improving gear performance and
reducing noise while avoiding axial loads common to helical gears
includes: an annular gear body; and a set of gear teeth, with each
tooth extending radially away from the gear body and extending
axially along the gear body. The gear tooth has a cross-sectional
profile transverse to the rotational axis of the gear body, the
cross-sectional profile formed from a hybridization of two or more
curves, the two or more curves defining a tooth tip, a tooth flank,
and a tooth root. The gear tooth has an axial tooth profile
defining a circumferential positioning of the gear tooth on the
gear body relative to a respective axial positioning of the gear
tooth on the gear body, the axial tooth profile being symmetric
across the midplane of the gear to reduce axial loading on gears
induced by gear meshing.
[0009] Optionally, the axial tooth profile is continuously
differentiable
[0010] Optionally, the axial tooth profile has an initial helix
angle at each end of the gear.
[0011] Optionally, the axial tooth profile is curvilinear.
[0012] Optionally, the axial tooth profile is a half-period
sinusoid function.
[0013] Optionally, the gear tooth cross-sectional profile is
configured such that the tip of one gear fully sweeps along the
tooth root of the mating gear.
[0014] Optionally, the tooth tip and root profiles include a
circular-arc.
[0015] Optionally, the tooth flank is a curve that allows smooth
meshing of the gears.
[0016] Optionally, the tooth flank is involute, cycloidal, or
circular arc.
[0017] Optionally, the tooth flank is an involute curve.
[0018] Optionally, the tooth tip is circular, the tooth flank is
involute, and the tooth root is circular.
[0019] Optionally, the two or more curves of the hybrid tooth
profile are combined such that the cross-sectional profile of the
tooth is continuously differentiable.
[0020] Optionally, the gear teeth extend radially outward from the
annular gear body.
[0021] According to another aspect of the invention, a curvilinear
circular-arc-toothed (CCAT) gear for improving gear performance and
reducing noise while reducing axial loads common to helical gears
includes: an annular gear body; and a gear tooth having a hybrid
gear tooth profile comprising one or more curves configured to
provide a sweep of the gear tooth space by a mating gear tooth
while maintaining smooth contact during gear mesh, and wherein the
gear tooth extends along an axial length of the gear body along an
axial profile.
[0022] Optionally, the hybrid gear tooth profile has a tip that
conforms to a tooth root of the mating gear to allow fully sweeping
out the volume between gear teeth to improve efficiency and reduce
noise.
[0023] Optionally, the hybrid gear tooth profile has a circular arc
at a tooth tip, a circular arc at a tooth root, and the profile
combines the two arcs with an involute curve between the circular
arcs to allow a full sweep of the volume between gear teeth while
maintaining a constant line of action of the mesh.
[0024] Optionally, a radius of a tooth tip arc is equal to or less
than a radius of a tooth root arc.
[0025] Optionally, the hybrid profile is continuously
differentiable.
[0026] Optionally, the axial profile is configured to cause gradual
contact between teeth to reduce shock stress on the gear teeth and
noise during meshing.
[0027] Optionally, the axial profile is configured to balance axial
forces imparted on the gears from meshing to reduce net axial load
on the gear.
[0028] The foregoing and other features of the invention are
hereinafter described in greater detail with reference to the
accompanying drawings.
BRIEF DESCRIPTION OF THE DRAWINGS
[0029] FIG. 1 schematically shows the function of conventional and
exemplary gear pumps.
[0030] FIG. 2 shows exemplary geometry of one half of a tooth
profile. Curve end points are identified A through D. Top and
bottom lines (A-B and C-D) denote circular curves, while the curved
line between(B-C) denote the involute curve. Pitch, base, and root
circles are denoted by the dot-dash lines and labeled as r.sub.p,
r.sub.b, and r.sub.r respectively.
[0031] FIG. 3 shows the origin of an exemplary involute curve
y.sub.f(x). The dashed line between points C and C.sub.0 denotes
the part of the involute curve that is not used in the actual tooth
profile.
[0032] FIG. 4 shows an exemplary post-splice tooth profile.
[0033] FIG. 5 shows a simplified block diagram of an exemplary
process for building a CAD model of an exemplary gear.
[0034] FIG. 6 shows a graphical depiction of the process of FIG.
5.
[0035] FIG. 7 shows a top view of an exemplary gear.
[0036] FIG. 8 shows a side view of an exemplary gear.
[0037] FIG. 9 shows an isometric view of an exemplary gear.
DETAILED DESCRIPTION
[0038] The primary drawback to involute tooth profiles in gear
pumps is that the tooth of one gear does not fully sweep the tooth
space of the mating gear. As the teeth progressively merge, a
pocket of fluid is trapped and increasingly compressed by the
continuing meshing action. The pressure of this fluid pocket is
continually increased to a level sufficient to force a fluid flow
rate between the gear teeth equal to the volume loss rate of the
pocket (minus the effect of fluid compressibility). For gears with
minimal backlash (and thus a tight mesh), as desired in gear pumps,
this can result in very high pressures within the fluid pocket that
can damage the tips of the gear teeth. The rapid pressurization of
the fluid also contributes to the noise level of the pump. Various
efforts have been done over time to model the meshing dynamics of
involute spur gears in this regard.
[0039] While there are multiple avenues to mitigate the pressure
oscillations, the most common is the relief groove. The primary
driver of these oscillations is that, for spur gears, once the
fluid pocket is trapped, the exit area of the pocket is very small
(the thickness of the fluid film between teeth multiplied by the
width of the gear). This increases the pressure within the pocket
required to drive the necessary fluid flow to allow continued gear
meshing, as the flow rate out of the pocket, Q.sub.p, is given
by
Q p = C d A e 2 ( p p - p d ) .rho. ( 1 ) ##EQU00001##
[0040] where C.sub.d is the discharge coefficient of the
tooth-to-tooth gap, A.sub.e is the exit area, p.sub.p is the
pressure within the pocket, pd is the discharge pressure, and p is
the density of the fluid. The required flow rate out of the pocket
is set by the geometry of the meshing gears and the shaft speed of
the pump; pp will rise to whatever is sufficient provide this flow
rate. Therefore, to reduce the maximum value of p.sub.p during
meshing process, the exit area of the pocket must be increased.
[0041] Enlarging the gap between the teeth during meshing is
problematic for two reasons. First, while widening the gap between
the teeth would allow fluid to escape the pocket, it would increase
fluid leakage through the mesh. Due to the dynamic nature of the
meshing zone, the only seal that separates the high pressure
discharge region from the low pressure suction region is close and
continual contact between the teeth at some point at all times. The
second issue is that if the tooth separation (backlash) is too
large, the gear mesh will lose a continuous line of action--at some
point in the meshing action the gears lose contact. This would
result in the idle gear slowing until the next meshing set of gears
make contact to drive the gear, essentially slamming together each
time. This would increase tooth wear and operational noise, and
thus should be avoidable.
[0042] Instead of enlarging the gap between the teeth, an opening
is made within the wear plate above and underneath the meshing
zone. As the gear teeth progress through the mesh, fluid can escape
through the groove into the discharge region. As long as the relief
groove does not extend beyond the meshing zone into the suction
region, leakage through the groove is limited. The exit area of the
pocket then becomes the depth of the relief groove multiplied by
the width.
[0043] While the addition of a relief groove can mitigate the
pressure rise within the trapped fluid pocket during meshing, it
does not entirely remove it. Once the teeth make contact, the
effective exit area reduces to the groove area on the two plates
which still necessitates a pressure rise--just a smaller one than
if there were not relief grooves. The width of the groove is
limited by the pump geometry, as it can only be as wide as the
meshing zone. Likewise, the depth of the groove is limited by the
design of the pump, as the bearing structure below competes for
space. Groove depth thus trades against pump size, which is
problematic for robotic applications where size and mass is at a
premium.
[0044] The limitation of the relief groove is that, for spur gears,
the tooth-to-tooth seal forms completely along the width of the
gear at the moment of contact. Thus the trapped fluid pocket can
only escape through the two ends of the pocket at the wear plate
relief grooves. That still requires fluid in the center of the
pocket between the two plates to travel the width of the gears in
the timescale of the meshing action, and for high pump speeds this
can result in large requisite pressures within the pocket. One
solution is to shift away from a spur gear architecture and utilize
one that enables gradual tooth meshing, such as a helical gear.
During meshing, one end of the gears engage first and the tooth
seal gradual engages as the gears rotate through the mesh. This has
two impacts: first, it allows gradual engagement of the mesh and
reduces tooth stress and noise at high speeds; second, as the
meshing teeth sweep out the tooth space volume, the tooth seal has
not fully engaged along the entire width, providing additional exit
area for the fluid pocket. In essence, rather than trapping a fluid
pocket and squeezing the fluid out through the ends, a helical gear
mesh compresses the volume at one end and progressively moves to
the other end, reducing exit area as the pocket volume reduces.
This larger exit area reduces the required pressure in the pocket
to vacate the volume and further attenuates pressure spikes.
Helical gears are often used in conjunction with wear plate relief
grooves, as otherwise there still exists a trapped fluid pocket at
the end of the meshing action, just greatly reduced.
[0045] The primary limitation with the helical gear approach is
that it introduces axial loads that must be compensated for. When
gears mesh, all force exchange is normal to the surface of the
tooth at the point of contact. For spur gears, this results in
primarily tangential loads with some small radial loads, as the
contact surface is aligned along the axial direction. For helical
gears, the teeth are at an angle to the axial direction, called the
helix angle; thus as the teeth mesh, force transfer occurs at a
vector that contains large tangential and axial loads, in addition
to minor radial loads. This axial load acts to force the helical
gears into the wear plate on one side.
[0046] Sufficient axial loading reduces the thickness of the fluid
film between the gears and the wear plates, which shifts the regime
from hydrodynamic lubrication to elastohydrodynamic lubrication and
potentially mixed lubrication, which is characterized by
dramatically increased wear and galling. Galling rapidly increases
frictional loads, increases motor loads, inhibits smooth operation,
and decreases pump lifetime. Beyond considering wear, excessive
compressive load on the film between the wear plate and the gear
increases frictional losses and decreases mechanical
efficiency.
[0047] Conventional pumps cut pressure compensation grooves in the
wear plates at the location of compression. These grooves are
connected to the discharge region and fill with high-pressure fluid
that supplies a hydrostatic force to counter the axial loading of
the gears. While this approach mitigates the risks of helical
gears, it does so by expanding the leakage path between the
discharge and suction regions, reducing volumetric efficiency.
Rather than try to compensate for a weakness of helical gears,
exemplary gears offer all the benefits mentioned thus far, but
without any of the drawbacks that come from helical gears.
[0048] In order to meet and exceed all of the benefits of
conventional gear pump technology, the gear should display the
following characteristics: [0049] A circular profile of the
addendum to match the dedendum, so that one tooth completely sweeps
the volume between tooth flanks of the mating gear [0050] Gradual
engagement of the teeth during meshing, enabling smoother operation
and lower pressure pulsations [0051] Balanced axial force transfer
during engagement to eliminate net axial loads on the gears
[0052] In order to achieve these goals, a new gear is described
herein. Exemplary tooth profiles hybridize the profiles of the
involute curve for smooth force transfer with the void-clearing
capability of a circular-arc tip. Likewise, the gradual engagement
of a helical gear may be made symmetrical to balance the axial
loading.
[0053] A primary drawback of a helical gear is the net axial
loading placed on the gears during meshing. Again, this axial load
is imparted on the gear during meshing, as there is an axial
component to the force exchange due to the orientation of the tooth
surface. One way to passively balance this axial load is to make
the gears symmetric about the central plane of the gear. For a
helical gear, this results in a herringbone gear. By using what is
essentially a gear made of two combined helical gears with opposite
helix angles, the axial load of one half of the gear is balanced
against the other, resulting in no net axial load. Herringbone
gears have been used in power transmission applications for over a
century, though not at such small scales.
[0054] The primary difficulty in fabricating a herringbone gear at
this size scale is the `V` junction along the centerline of the
gear; such sharp corners cannot be readily machined. An alternative
approach is to change the side profile from a `V` to a shape that
is continuously differentiable (i.e. smooth). Curvilinear gear
teeth nominally have side profiles that are circular arcs that are
both continuously differentiable and symmetric. This approach
offers the same benefits of herringbone hears, namely gradual mesh
contact and balanced axial loading, in a more readily
manufacturable shape.
[0055] An exemplary design process of the CCAT gear is as follows.
First, the overall gear geometry is selected, including the root
circle radius, maximum outer radius, gear height, and the number of
teeth. Second, the axial profile is formulated. Third, the hybrid
tooth profile is created to fit the needs of the specific
application, including any geometric or performance constraints.
Fourth, the gear is modeled in a CAD software package. Finally, the
generated CAD file is used in conjunction with a CNC milling
machine to fabricate the gear.
[0056] The first step is to select the overall geometric parameters
of the gear, such as root and outer radii, as well as height and
the number of teeth. These parameters are sometimes dictated by
external requirements, such as pump cavity dimensions, a desired
pump flow rate, or a required torque capacity. Other terms may be
selected arbitrarily and iterated on later in the process.
[0057] The second step is to create the axial profile
mathematically. For computer design applications such as NX 10, the
side profile curve may be defined parametrically in Cartesian
coordinates. Due to the nature of the geometry in question, this
may necessitate conversion from cylindrical to Cartesian
coordinates.
[0058] The surface of a cylinder of radius r is defined by
x=r cos t
y=r sin t
z .di-elect cons. [0, w] (1)
where t is the parametric parameter, and w is the height of the
cylinder. In this application, r is the root radius of the gear and
w is the width of the gear that was chosen in the first step. Next,
an axial profile is selected and defined in 2-d Cartesian
coordinates by some function f.
y=f(x) (2)
[0059] Equation (2) is mapped to the cylinder surface defined by
Equation set (1) by using the following parameter
transformation,
y=r(.theta.-.theta..sub.0)
x=z (3)
where .theta. is the angular position of an arbitrary point on the
axial profile, and .theta..sub.0 is the angular position of the
start of the curve when z=0. The profile angle is then described as
a function of axial position.
.theta. = f ( z ) r + .theta. 0 ( 4 ) ##EQU00002##
[0060] To express the profile in 3D Cartesian parametric form,
Equation (4) is substituted into Equation set (1) as the parametric
parameter. The axial profile is defined by convention as the locus
of points that is the reference point of the tooth profile as it is
propagated along the axis of the gear. The reference point of the
tooth profile is where the tooth profile contacts the root circle.
For an involute gear tooth, this where the involute curve crosses
the root circle or is a function of extra tooth root geometry where
applicable. For the example design of the CCAT gear, this reference
point is at the minimum of the circular dedendum profile (point D
FIG. 2). This makes .theta..sub.D the half-angle of the tooth
profile, which can be compared to the number of chosen teeth as a
design check to ensure that the selected number of teeth fit within
the circle.
[0061] The third step is to create the hybrid tooth profile. There
are multiple options for defining the tooth flank profile.
[0062] While the above discussions have focused on the limitations
of the involute curve, one of the chief advantages of it has been
the smooth transfer of force during meshing. Additionally, how a
tooth sweeps the flank of a mating tooth is primarily a function of
the design of the addendum and dedendum of the tooth. These curves
can be any function as long as it fits the constraint that one
conforms to the other during meshing of mating gears. The
functional goal is to increase the degree that one gear sweeps out
the volume between the teeth of the other gear. With these two
goals of smooth meshing and tooth conformity, the exemplary tooth
profile is a hybrid of circular and involute curves.
[0063] The process for defining the hybrid profile mathematically
is to divide the curve into the constituent parts, define any
required curve origins, and express each segment as a function of
geometric parameters. These parameters may be freely variable, such
as the base circle for involute curves, or may be dependent on
external constraints or previous assumptions, such as the outer
radius or the number of teeth. These expressions can then be used
in curve fitting calculations to refine parameter selection.
[0064] An exemplary hybrid tooth profile 200 consists of three
sections, as shown in FIG. 2: the addendum circular arc 210, the
involute flank curve 220, and the dedendum circular arc 230. The
two circular arcs have their separate origins located on the pitch
circle. The addendum arc origin, O.sub.1, is located at the 12
o'clock position and is where the azimuthal position, .theta., is
defined to be zero. The dedendum arc origin, O.sub.2, is defined to
be at the angle which defines the end of the half tooth profile.
The beginning and end points of the profile are labeled A and D,
respectively, while the transition points between circular arcs and
the involute curve are labeled B and C.
[0065] The arc length of the tooth in radians is determined by the
number of teeth, n.sub.t,
.theta. D = .pi. n t ( 5 ) ##EQU00003##
which also defines the angular position of O.sub.2.
[0066] In the exemplary tooth profile, the addendum and dedendum
curves are circular profiles, best expressed parametrically using a
reference angle, .gamma.. For example, the addendum curve can be
written as
x.sub.a=r.sub.a sin .gamma. (6)
y.sub.a=r.sub.p-r.sub.a cos .gamma. (7)
[0067] The flank curve, y.sub.f(x), must also be expressed in a
similar manner. For the exemplary curve, the Cartesian coordinates
of an involute curve can be expressed parametrically as
x.sub.f=r.sub.b(cos(t)+t sin(t)) (8)
y.sub.f=r.sub.b(sin(t)-t cos(t)) (9)
where t is the parametric parameter, and r.sub.b is the radius of
the base circle. Note that the flank curve may need to be
transformed using a variable rotation matrix to define the flank
curve origin on the base circle, shown in FIG. 3. Once defined, all
constituent curves must be defined with respect to the same
reference origin and in terms of a single reference parameter. For
the exemplary curve, this is the angular position, .theta..
[0068] In order to create a complete hybrid profile the component
curves must be combined. The criteria for merging the curves are
that the created hybrid curve is continuous and differentiable.
Most constituent curves satisfy that requirement internally, which
means that the solution criteria reduces solely to where the curves
meet--points B and C in the exemplary profile. Mathematically, this
means that at point B
y a ( x B ) = y f ( x B ) ( 10 ) dy a dx | x B = dy f dx | x B ( 11
) ##EQU00004##
and similarly so at point C.
[0069] Using these criteria is unlikely to result in an analytical
solution for the profile parameters, as the problem is likely
under-constrained due to the number of geometric parameters, shown
for the exemplary profile in Table 1. Instead, a numerical approach
is used where the termination parameters for all constituent curves
are calculated using the above equations. The squared differences
between the corresponding values may be calculated and summed, and
the remaining unknown parameters may be passed through a numerical
solving algorithm to minimize the sum error. The resulting curve
for the exemplary tooth profile is shown in FIG. 4. Once the smooth
hybrid profile is generated, it is reflected across the y-axis to
create a full tooth profile. A sampling of points along the profile
is collected to be used in creating a spline curve in CAD
software.
TABLE-US-00001 TABLE 1 Cuve splicing parameters and their range
restrictions. Parameter Range Restriction .gamma..sub.a 0 .ltoreq.
.gamma..sub.a .ltoreq. .pi./4 .gamma..sub.d 0.sub.D .ltoreq.
.gamma..sub.d .ltoreq. .pi./4 t.sub.B t.sub.C .ltoreq. t.sub.B
t.sub.C 0 .ltoreq. t.sub.C .theta..sub.C0 0 .ltoreq. .theta..sub.C0
.ltoreq. .theta..sub.D r.sub.b r.sub.r .ltoreq. r.sub.b .ltoreq.
r.sub.p b a .ltoreq. b
[0070] As shown in FIG. 5, once the tooth profile is complete, the
gear may be generated in a CAD software package, for example NX 10,
in process 500. The root cylinder may be created at block 520,
having a radius r.sub.r and height w. Next the bore for the shaft
may be cut, along with the keyway, at block 530. Then the tooth
side profile may be created as a 3D parametric curve at block 540.
The tooth profile may then be created at block 550 using 67 data
points calculated using the tooth profile parameters; these data
points may be imported into NX and used to generate the profile.
The circular arc sections may be created using the arc command,
while the involute section may be created using a fit spline to the
corresponding data points. The tooth profile is then closed with a
circular arc of radius r.sub.r and then swept along the side
profile, generating the first tooth 560. The component features of
this tooth are then grouped and propagated in a circular arc to
complete tooth formation at block 570. The process is illustrated
visually in FIG. 6.
[0071] Due to the complexity of the design and the small tolerances
required (less than 0.001 inches on the tooth profile), fabrication
may be performed using a high-quality mill such as a Kitamura
Mytrunnion 5-axis CNC mill. The Mytrunnion has a positional
repeatability of 0.00002 inches, which allows for component
tolerances less than 0.0005 inches.
[0072] An exemplary resulting gear is shown in FIGS. 7-9 at 700. As
depicted, the gear 700 includes an annular gear body 710. A set of
gear teeth 720 extend radially away from the gear body 710 and
extending axially along the gear body 710. As shown, the gear 700
is an exterior gear with the teeth 720 extending radially outward
from the annular body 710. However, an inner gear is also possible
with the gear teeth extending radially inwardly from the annular
body. Each tooth 720 has a cross-sectional profile taken transverse
to the rotational axis of the gear body 710. The cross-sectional
profile is shaped as described above, and is formed from a
hybridization of two or more curves. As described above, exemplary
embodiments include a profile having circular tips 722 and roots
724 with involute flanks 726. In preferred embodiments, the radius
of the tooth tip arc is equal to or less than a radius of a tooth
root arc. In other exemplary embodiments, however, the flank may be
circular or cycloidal, rather than involute.
[0073] In any case, the gear tooth cross-sectional profile may
configured such that the tip sweeps through the tooth root volume
of the mating gear and such that the gear smoothly meshes with a
complimentary gear. Preferably, the two or more curves of the
hybrid tooth profile are combined such that the cross-sectional
profile of the tooth is continuously differentiable.
[0074] Likewise, each tooth 720 has an axial tooth profile defining
a circumferential positioning of the gear tooth at any location
along the axis of the gear body 710. This profile is, as described
above, continuously differentiable or smooth along the axis of the
gear to reduce axial loading on gears induced by gear meshing. In
exemplary embodiments, the axial tooth profile is also symmetric
about an axial mid-plane of the gear to eliminate axial loading
from gear meshing. Also as described above, the axial tooth profile
may be
[0075] Although the invention has been shown and described with
respect to a certain embodiment or embodiments, it is obvious that
equivalent alterations and modifications will occur to others
skilled in the art upon the reading and understanding of this
specification and the annexed drawings. In particular regard to the
various functions performed by the above described elements
(components, assemblies, devices, compositions, etc.), the terms
(including a reference to a "means") used to describe such elements
are intended to correspond, unless otherwise indicated, to any
element which performs the specified function of the described
element (i.e., that is functionally equivalent), even though not
structurally equivalent to the disclosed structure which performs
the function in the herein illustrated exemplary embodiment or
embodiments of the invention. In addition, while a particular
feature of the invention may have been described above with respect
to only one or more of several illustrated embodiments, such
feature may be combined with one or more other features of the
other embodiments, as may be desired and advantageous for any given
or particular application.
* * * * *