U.S. patent application number 16/516435 was filed with the patent office on 2020-03-19 for track system for traction of a vehicle.
The applicant listed for this patent is CAMSO INC.. Invention is credited to Jules DANDURAND, Jason DAVIS, Pascal LABBE, Daniel LOCHNIKAR.
Application Number | 20200086935 16/516435 |
Document ID | / |
Family ID | 59270795 |
Filed Date | 2020-03-19 |





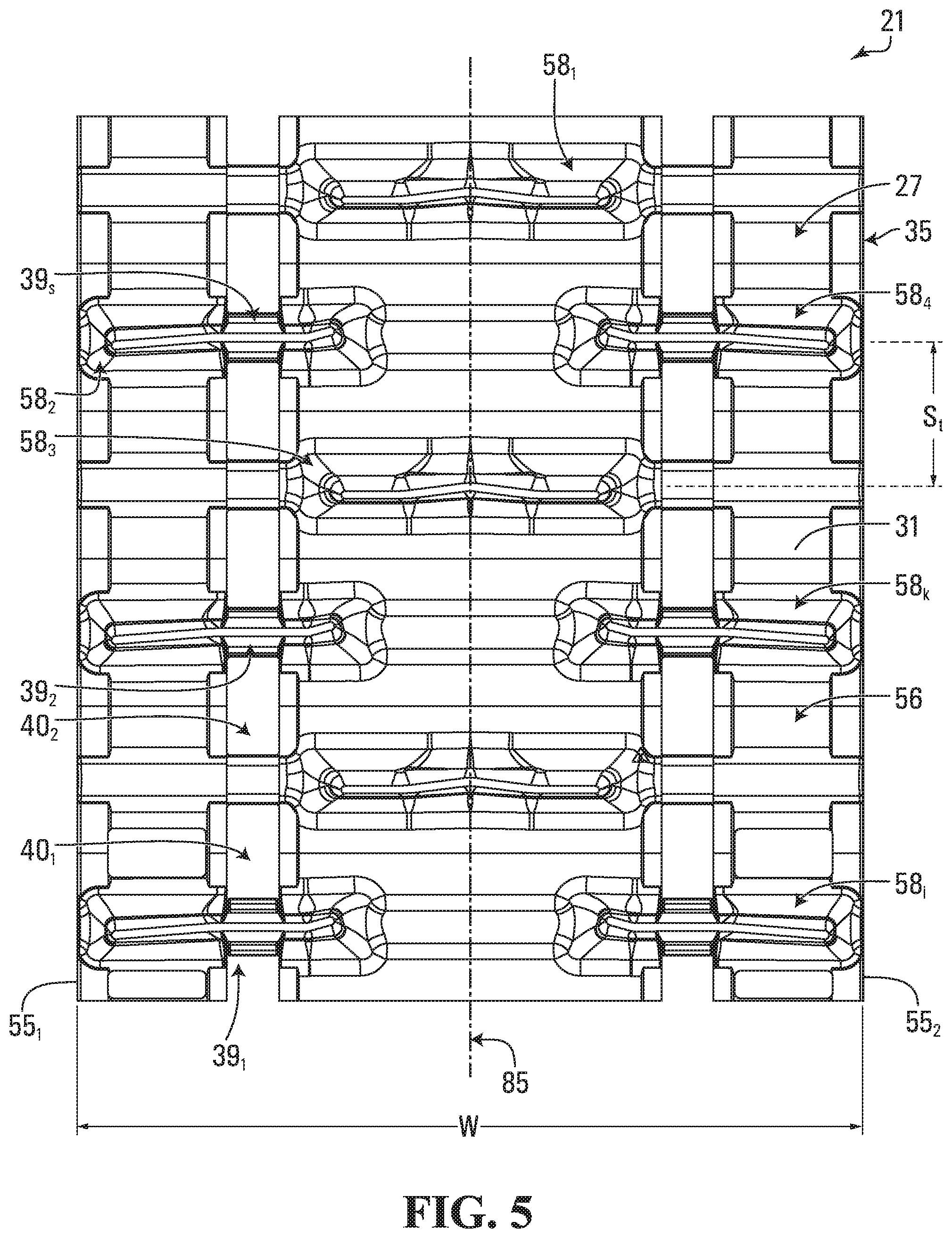





View All Diagrams
United States Patent
Application |
20200086935 |
Kind Code |
A1 |
DANDURAND; Jules ; et
al. |
March 19, 2020 |
TRACK SYSTEM FOR TRACTION OF A VEHICLE
Abstract
A track system for traction of a vehicle (e.g., a snowmobile, an
all-terrain vehicle (ATV) etc.). The track system comprises a track
and a track-engaging assembly for driving and guiding the track
around the track-engaging assembly. The track system may have
various features to enhance its traction, floatation, and/or other
aspects of its performance, including, for example, a lightweight
design, enhanced tractive effects, an enhanced heat management
capability, an enhanced resistance to lateral skidding (e.g., on a
side hill), an adaptive capability to adapt itself to different
conditions (e.g., ground conditions, such as different types of
snow, soil, etc.; and/or other conditions), an adjustability of a
contact area of its track with the ground, and/or other
features.
Inventors: |
DANDURAND; Jules;
(SHERBROOKE, CA) ; LABBE; Pascal; (Sherbrooke,
CA) ; DAVIS; Jason; (Cadyville, NY) ;
LOCHNIKAR; Daniel; (Gunnison, CO) |
|
Applicant: |
Name |
City |
State |
Country |
Type |
CAMSO INC. |
Magog |
|
CA |
|
|
Family ID: |
59270795 |
Appl. No.: |
16/516435 |
Filed: |
July 19, 2019 |
Related U.S. Patent Documents
|
|
|
|
|
|
Application
Number |
Filing Date |
Patent Number |
|
|
15400692 |
Jan 6, 2017 |
10392060 |
|
|
16516435 |
|
|
|
|
62275944 |
Jan 7, 2016 |
|
|
|
62337101 |
May 16, 2016 |
|
|
|
Current U.S.
Class: |
1/1 |
Current CPC
Class: |
B62M 27/02 20130101;
B62D 55/07 20130101; B62D 55/14 20130101; B62D 55/10 20130101; B62D
55/27 20130101; B62M 2027/027 20130101; B62D 55/244 20130101; B62D
55/104 20130101 |
International
Class: |
B62D 55/24 20060101
B62D055/24; B62M 27/02 20060101 B62M027/02; B62D 55/27 20060101
B62D055/27; B62D 55/14 20060101 B62D055/14; B62D 55/104 20060101
B62D055/104; B62D 55/10 20060101 B62D055/10; B62D 55/07 20060101
B62D055/07 |
Claims
1. A track for traction of a vehicle, the track being movable
around a track-engaging assembly comprising a drive wheel to drive
the track, the track comprising: a carcass comprising a
ground-engaging outer surface for engaging the ground and an inner
surface opposite to the ground-engaging outer surface; and a
plurality of traction projections projecting from the
ground-engaging outer surface; wherein: a thickness of the carcass
from the ground-engaging outer surface to the inner surface is no
more than 0.20 inches; and a ratio of a widthwise rigidity of the
carcass over a longitudinal rigidity of the carcass is at least
1.5.
2. The track of claim 1, wherein the thickness of the carcass is no
more than 0.18 inches.
3. The track of claim 1, wherein the thickness of the carcass is no
more than 0.16 inches.
4. The track of claim 1, wherein the ratio of the widthwise
rigidity of the carcass over the longitudinal rigidity of the
carcass is at least 2.
5. (canceled)
6. The track of claim 1, wherein the ratio of the widthwise
rigidity of the carcass over the longitudinal rigidity of the
carcass is at least 3.
7. The track of claim 1, wherein: the carcass comprises elastomeric
material and a reinforcement disposed within the elastomeric
material; and a ratio of a bending stiffness of the reinforcement
in a widthwise direction of the track over a bending stiffness of
the reinforcement in a longitudinal direction of the track is at
least 2.
8. The track of claim 7, wherein the ratio of the bending stiffness
of the reinforcement in the widthwise direction of the track over
the bending stiffness of the reinforcement in the longitudinal
direction of the track is at least 3.
9. The track of claim 7, wherein the ratio of the bending stiffness
of the reinforcement in the widthwise direction of the track over
the bending stiffness of the reinforcement in the longitudinal
direction of the track is at least 4.
10. The track of claim 7, wherein the ratio of the bending
stiffness of the reinforcement in the widthwise direction of the
track over the bending stiffness of the reinforcement in the
longitudinal direction of the track is at least 5.
11. The track of claim 7, wherein the reinforcement comprises a
layer of reinforcing cables.
12. The track of claim 7, wherein the reinforcement comprises a
layer of reinforcing fabric.
13. The track of claim 1, wherein: the carcass comprises
elastomeric material and a reinforcement disposed within the
elastomeric material; a ratio of a modulus of elasticity of the
reinforcement in a longitudinal direction of the track over the
thickness of the track is at least 1 GPa/in; and a ratio of a
modulus of elasticity of the reinforcement in a widthwise direction
of the track over the thickness of the track is at least 5
GPa/in.
14.-40. (canceled)
41. A track for traction of a vehicle, the track being movable
around a track-engaging assembly comprising a drive wheel to drive
the track, the track comprising: a ground-engaging outer surface
for engaging the ground and an inner surface opposite to the
ground-engaging outer surface; a plurality of traction projections
projecting from the ground-engaging outer surface; and a plurality
of slide members for sliding against the track-engaging assembly;
wherein a spacing of longitudinally-adjacent ones of the slide
members in a longitudinal direction of the track is at least
one-fifth of a length of the track.
42. The track of claim 41, wherein the spacing of
longitudinally-adjacent ones of the slide members in the
longitudinal direction of the track is at least one-quarter of the
length of the track.
43. The track of claim 41, wherein the spacing of
longitudinally-adjacent ones of the slide members in the
longitudinal direction of the track is at least one-third of the
length of the track.
44. The track of claim 41, wherein the spacing of
longitudinally-adjacent ones of the slide members in the
longitudinal direction of the track is at least half of the length
of the track.
45. The track of claim 41, wherein the slide members are arranged
such that no more than three of the slide members can contact the
track-engaging assembly at any given instant.
46. The track of claim 41, wherein the slide members are arranged
such that no more than two of the slide members can contact the
track-engaging assembly at any given instant.
47. The track of claim 41, wherein the slide members are arranged
such that no more than one of the slide members can contact the
track-engaging assembly at any given instant.
48.-59. (canceled)
60. A track for traction of a vehicle, the track being movable
around a track-engaging assembly comprising a drive wheel to drive
the track, the track comprising: a ground-engaging outer surface
for engaging the ground and an inner surface opposite to the
ground-engaging outer surface; a plurality of traction projections
projecting from the ground-engaging outer surface; and a plurality
of drive/guide projections projecting from the inner surface;
wherein a spacing of adjacent ones of traction projections in a
longitudinal direction of the track is greater than a spacing of
adjacent ones of the drive/guide projections in the longitudinal
direction of the track.
61.-188. (canceled)
Description
CROSS-REFERENCE TO RELATED APPLICATION
[0001] This application claims priority from U.S. Provisional
Patent Application 62/275,944 filed on Jan. 7, 2016 and
incorporated by reference herein and from U.S. Provisional Patent
Application 62/337,101 filed on May 5, 2016 and incorporated by
reference herein.
FIELD
[0002] The invention relates generally to track systems for
traction of vehicles such as snowmobiles, all-terrain vehicles
(ATVs), and other off-road vehicles.
BACKGROUND
[0003] Certain vehicles may be equipped with track systems which
enhance their traction and floatation on soft, slippery and/or
irregular grounds (e.g., snow, ice, soil, mud, sand, etc.) on which
they operate.
[0004] For example, snowmobiles allow efficient travel on snowy and
in some cases icy grounds. A snowmobile comprises a track system
which engages the ground to provide traction. The track system
comprises a track-engaging assembly and a track that moves around
the track-engaging assembly and engages the ground to generate
traction. The track typically comprises an elastomeric body in
which are embedded certain reinforcements, such as transversal
stiffening rods providing transversal rigidity to the track,
longitudinal cables providing tensional strength, and/or fabric
layers. The track-engaging assembly comprises wheels and in some
cases slide rails around which the track is driven.
[0005] A snowmobile, including its track system, may face a number
of challenges while riding. For example, the snowmobile's track may
perform very differently on different ground conditions. For
instance, the track may perform properly on a given type of snow
condition (e.g., deep powder snow) but may not perform as well on
another type of snow (e.g., packed snow). This inconsistent
performance of the track in different ground conditions can be
inconvenient and/or make it difficult to travel efficiently over
different types of terrain. Also, the snowmobile may have an
undesirable tendency to skid sideways when travelling in a given
direction on a slope terrain like a side hill or other inclined
ground area. A weight of the track system may also affect the
snowmobile's power consumption and/or ride. Excessive heat
generated within the snowmobile's track may cause deterioration
and/or failure of the track.
[0006] Similar considerations may arise for track systems of other
types of off-road vehicles (e.g., all-terrain vehicles (ATVs),
agricultural vehicles, or other vehicles that travel on uneven
grounds) in certain situations.
[0007] For these and other reasons, there is a need to improve
track systems for traction of vehicles.
SUMMARY
[0008] In accordance with various aspects of the invention, there
is provided a track system for traction of a vehicle. The track
system comprises a track and a track-engaging assembly for driving
and guiding the track around the track-engaging assembly. The track
system may have various features to enhance its traction,
floatation, and/or other aspects of its performance, including, for
example, a lightweight design, enhanced tractive effects, an
enhanced heat management capability, an enhanced resistance to
lateral skidding (e.g., on a side hill), an adaptive capability to
adapt itself to different conditions (e.g., ground conditions, such
as different types of snow, soil, etc.; and/or other conditions),
an adjustability of a contact area of its track with the ground,
and/or other features.
[0009] For example, in accordance with an aspect of the invention,
there is provided a track for traction of a vehicle. The track is
movable around a track-engaging assembly comprising a drive wheel
to drive the track. The track comprises: a carcass comprising a
ground-engaging outer surface for engaging the ground and an inner
surface opposite to the ground-engaging outer surface; and a
plurality of traction projections projecting from the
ground-engaging outer surface. A thickness of the carcass from the
ground-engaging outer surface to the inner surface is no more than
0.20 inches, and a ratio of a widthwise rigidity of the carcass
over a longitudinal rigidity of the carcass is at least 1.5.
[0010] In accordance with another aspect of the invention, there is
provided a track for traction of a vehicle. The track is movable
around a track-engaging assembly comprising a drive wheel to drive
the track. The track comprises: a carcass comprising a
ground-engaging outer surface for engaging the ground and an inner
surface opposite to the ground-engaging outer surface; and a
plurality of traction projections projecting from the
ground-engaging outer surface. The track comprises first
elastomeric material and second elastomeric material less dense
than the first elastomeric material.
[0011] In accordance with another aspect of the invention, there is
provided a track for traction of a vehicle. The track is movable
around a track-engaging assembly comprising a drive wheel to drive
the track. The track comprises: a ground-engaging outer surface for
engaging the ground and an inner surface opposite to the
ground-engaging outer surface; a plurality of traction projections
projecting from the ground-engaging outer surface; and a plurality
of slide members for sliding against the track-engaging assembly. A
spacing of longitudinally-adjacent ones of the slide members in a
longitudinal direction of the track is at least one-fifth of a
length of the track.
[0012] In accordance with another aspect of the invention, there is
provided a track for traction of a vehicle. The track is movable
around a track-engaging assembly comprising a drive wheel to drive
the track. The track comprises a ground-engaging outer surface for
engaging the ground and an inner surface opposite to the
ground-engaging outer surface; and a plurality of traction
projections projecting from the ground-engaging outer surface.
Longitudinally-successive ones of the traction projections that
succeed one another in a longitudinal direction of the track differ
in height.
[0013] In accordance with another aspect of the invention, there is
provided a track for traction of a vehicle. The track is movable
around a track-engaging assembly comprising a drive wheel to drive
the track. The track comprises a ground-engaging outer surface for
engaging the ground and an inner surface opposite to the
ground-engaging outer surface; and a plurality of traction
projections projecting from the ground-engaging outer surface. Each
traction projection comprises a recess defining a recessed area at
a base of the traction projection.
[0014] In accordance with another aspect of the invention, there is
provided a track for traction of a vehicle. The track is movable
around a track-engaging assembly comprising a drive wheel to drive
the track. The track comprises: a ground-engaging outer surface for
engaging the ground and an inner surface opposite to the
ground-engaging outer surface; a plurality of traction projections
projecting from the ground-engaging outer surface; and a plurality
of drive/guide projections projecting from the inner surface. A
spacing of adjacent ones of traction projections in a longitudinal
direction of the track is greater than a spacing of adjacent ones
of the drive/guide projections in the longitudinal direction of the
track.
[0015] In accordance with another aspect of the invention, there is
provided a track for traction of a vehicle. The track is movable
around a track-engaging assembly comprising a drive wheel to drive
the track. The track comprises: a ground-engaging outer surface for
engaging the ground and an inner surface opposite to the
ground-engaging outer surface; a plurality of traction projections
projecting from the ground-engaging outer surface; and a plurality
of lateral stabilizers projecting from the ground-engaging outer
surface to oppose a tendency of the track to skid transversely to a
direction of motion of the vehicle.
[0016] In accordance with another aspect of the invention, there is
provided a track for traction of a vehicle. The track is movable
around a track-engaging assembly comprising a drive wheel to drive
the track. The track comprises a ground-engaging outer surface for
engaging the ground and an inner surface opposite to the
ground-engaging outer surface; and a plurality of traction
projections projecting from the ground-engaging outer surface. The
track comprises uneven surfaces projecting from the ground-engaging
outer surface and having a texture to oppose a tendency of the
track to skid transversely to a direction of motion of the
vehicle.
[0017] In accordance with another aspect of the invention, there is
provided a track for traction of a vehicle. The track is movable
around a track-engaging assembly comprising a drive wheel to drive
the track. The track comprises: a ground-engaging outer surface for
engaging the ground and an inner surface opposite to the
ground-engaging outer surface; and a plurality of traction
projections projecting from the ground-engaging outer surface. Each
traction projection comprises a containment space to contain ground
matter when the traction projection engages the ground.
[0018] In accordance with another aspect of the invention, there is
provided a track for traction of a vehicle. The track is movable
around a track-engaging assembly comprising a drive wheel to drive
the track. The track comprises: a ground-engaging outer surface for
engaging the ground and an inner surface opposite to the
ground-engaging outer surface; and a plurality of traction
projections projecting from the ground-engaging outer surface. Each
traction projection comprises a containment space to contain ground
matter when the traction projection engages the ground. The
containment space of the traction projection comprises a plurality
of containment voids to contain respective portions of the ground
matter.
[0019] In accordance with another aspect of the invention, there is
provided a track for traction of a vehicle. The track is movable
around a track-engaging assembly comprising a drive wheel to drive
the track. The track comprises: a ground-engaging outer surface for
engaging the ground and an inner surface opposite to the
ground-engaging outer surface; and a plurality of traction
projections projecting from the ground-engaging outer surface. Each
traction projection is configured to scoop and compact ground
matter when the traction projection engages the ground.
[0020] In accordance with another aspect of the invention, there is
provided a track for traction of a vehicle. The track is movable
around a track-engaging assembly comprising a drive wheel to drive
the track. The track comprises: a ground-engaging outer surface for
engaging the ground and an inner surface opposite to the
ground-engaging outer surface; and a plurality of traction
projections projecting from the ground-engaging outer surface. A
component of the track is adaptable in response to a stimulus such
that a state of the component of the track is variable in different
conditions.
[0021] In accordance with another aspect of the invention, there is
provided a track for traction of a vehicle. The track is movable
around a track-engaging assembly comprising a drive wheel to drive
the track. The track comprises: a ground-engaging outer surface for
engaging the ground and an inner surface opposite to the
ground-engaging outer surface; and a plurality of traction
projections projecting from the ground-engaging outer surface. Each
traction projection is adaptable in response to a stimulus such
that a state of the traction projection is variable in different
conditions.
[0022] In accordance with another aspect of the invention, there is
provided a track for traction of a vehicle. The track system
comprises: a track comprising a ground-engaging outer surface for
engaging the ground and an inner surface opposite to the
ground-engaging outer surface; and a track-engaging assembly for
driving and guiding the track around the track-engaging assembly.
The track-engaging assembly comprises: a drive wheel configured to
drive the track; and an adjustment mechanism configured to change a
configuration of the track-engaging assembly in order to vary a
size of a contact patch of the track with the ground.
[0023] These and other aspects of the invention will now become
apparent to those of ordinary skill in the art upon review of the
following description of embodiments of the invention in
conjunction with the accompanying drawings.
BRIEF DESCRIPTION OF THE DRAWINGS
[0024] A detailed description of embodiments of the invention is
provided below, by way of example only, with reference to the
accompanying drawings, in which:
[0025] FIG. 1 shows an example of a snowmobile comprising a track
system in accordance with an embodiment of the invention;
[0026] FIG. 2 shows a side view of the track system;
[0027] FIG. 3 shows a perspective view of a track-engaging assembly
of the track system;
[0028] FIGS. 4 to 7 respectively show a perspective view, a plan
view, an elevation view, and a longitudinal cross-sectional view of
part of a track of the track system;
[0029] FIG. 8A shows a widthwise cross-sectional view of part of
the track;
[0030] FIG. 8B shows a widthwise cross-sectional view of part of
the track in accordance to another embodiment;
[0031] FIG. 9 shows a three-point bending test being performed on a
carcass of the track along a widthwise direction of the track and
along a longitudinal direction of the track;
[0032] FIG. 10 shows a widthwise cross-sectional view of part of
the track in which reinforcements are spaced apart significantly in
a height direction of the track;
[0033] FIG. 11 shows a longitudinal cross-sectional view of part of
the track in which reinforcements are spaced apart significantly in
the height direction of the track;
[0034] FIG. 12 shows an example of an embodiment in which the track
comprises a low-density elastomeric material and a high-density
elastomeric material;
[0035] FIG. 13A shows a longitudinal cross-sectional view of the
track of FIG. 12 and FIG. 13B shows a close-up view of part of the
carcass of the track of FIG. 13A;
[0036] FIG. 14 shows a widthwise cross-sectional view of the track
of FIG. 12;
[0037] FIG. 15 shows a plurality of higher-density elastomeric
materials of the track in accordance with another embodiment;
[0038] FIG. 16 shows the lower-density elastomeric material forming
part of a periphery of the track in accordance with another
embodiment;
[0039] FIG. 17 shows a longitudinal cross-sectional view of part of
the track including a slide member of a plurality of slide
members;
[0040] FIG. 18 shows a longitudinal cross-sectional view of part of
the track in accordance with an embodiment in which the track
comprises a reduced number of slide members;
[0041] FIG. 19 shows a longitudinal cross-sectional view of part of
the track of FIG. 18 illustrating a spacing between
longitudinally-adjacent ones of the slide members;
[0042] FIG. 20 shows a longitudinal cross-sectional view of part of
the track in accordance with another embodiment in which traction
projections of the track have different characteristics to generate
different tractive effects on the ground;
[0043] FIGS. 21 and 22 show a perspective view and a top view of a
cross-section of the traction projections of the track in
accordance with another embodiment;
[0044] FIG. 23 shows a longitudinal cross-sectional view of part of
the track in accordance with another embodiment in which a pitch of
traction projections is greater than a pitch of drive/guide lugs of
the track;
[0045] FIG. 24 shows a longitudinal cross-sectional view of part of
the track in accordance with another embodiment in which the pitch
of adjacent traction projections is variable;
[0046] FIG. 25 shows an embodiment of the track in which the track
opposes a tendency of the track to skid sideways when the
snowmobile is travelling in a given direction;
[0047] FIG. 26 shows a plan view of the ground-engaging outer side
of the track of FIG. 25, including a plurality of lateral
stabilizers of the track;
[0048] FIG. 27 shows a perspective view of a lateral stabilizer of
the plurality of lateral stabilizers of FIG. 26;
[0049] FIGS. 28 to 32 show plan views of the ground-engaging side
of the track in accordance with different embodiments in which the
lateral stabilizers are configured differently on the track;
[0050] FIG. 33 shows an elevation view of the track in accordance
with an embodiment in which the ground-engaging outer side of the
track comprises uneven surfaces;
[0051] FIG. 34 shows an elevation view of the track in accordance
with an embodiment in which the lateral stabilizers of the track
comprise the uneven surfaces;
[0052] FIGS. 35A to 35D show different examples of formations of a
texture of the uneven surfaces of FIGS. 33 and 34;
[0053] FIG. 36 shows a perspective view of part of a traction
projection comprising an uneven lateral surface;
[0054] FIG. 37 shows a top portion of a traction projection
comprising an uneven lateral surface;
[0055] FIG. 38 shows the uneven lateral surface of the traction
projection bending;
[0056] FIG. 39 shows a functional block diagram of an adaptable
function of the track in accordance to an embodiment where one or
more components of the track are adaptable in response to a
stimulus;
[0057] FIG. 40 shows the traction projections of the track of FIG.
39, the traction projections assuming a first state corresponding
to a first condition and a second state corresponding to a second
condition;
[0058] FIG. 41 shows an embodiment where a stiffness of a traction
projection is adaptable in response to the stimulus;
[0059] FIG. 42 shows a material of the traction projections of FIG.
41 in accordance with an embodiment;
[0060] FIG. 43 shows an adaptable member of a traction projection
in accordance with another embodiment;
[0061] FIG. 44 shows the adaptable member at an outer surface of
the traction projection;
[0062] FIG. 45 shows an embodiment where a shape of the traction
projections is adaptable to the stimulus;
[0063] FIGS. 46 and 47 show a portion of a traction projection
having an angular orientation that is different in powder snow than
in wet/spring snow;
[0064] FIG. 48 shows a traction projection in accordance with
another embodiment where the traction projection comprises a
shape-changing member to change the shape of the traction
projection in response to the stimulus;
[0065] FIG. 49 shows an embodiment where the shape-changing member
comprises an actuator to change a shape of the shape-changing
member in response to a signal;
[0066] FIG. 50 shows an example of an embodiment of a device within
the track that transmits the signal to the shape-changing
member;
[0067] FIG. 51 shows an example of an embodiment in which the track
system comprises an adjustment mechanism for changing a
configuration of the track-engaging assembly of the track
system;
[0068] FIG. 52 shows the adjustment mechanism according to an
embodiment in which the adjustment mechanism can change the
configuration of the track-engaging assembly while a length of the
track remains constant;
[0069] FIGS. 53 to 57 show an example of an embodiment of the track
in which the track comprises an adjustment mechanism to adjust the
length of the track;
[0070] FIGS. 58 and 59 show an example of a connection member of a
connector of the adjustment mechanism of FIGS. 53 to 57;
[0071] FIG. 60 shows a diagram depicting an adjustment command
inputted the adjustment mechanism in order to adjust the
configuration of the track-engaging assembly;
[0072] FIG. 61 shows a diagram depicting a user interface of the
adjustment mechanism with which the user interacts to input the
adjustment command;
[0073] FIG. 62 shows the user interface of the adjustment
mechanism;
[0074] FIGS. 63 to 66 show an example of an embodiment of the
adjustment mechanism in which the adjustment mechanism is manually
operated;
[0075] FIGS. 67 and 68 show examples of an actuator of the
adjustment mechanism of FIG. 63;
[0076] FIG. 69 shows a diagram depicting a controller of the
adjustment mechanism for automatically generating the adjustment
command;
[0077] FIG. 70 shows an example of an embodiment in which the
adjustment mechanism comprises the controller and an automatic
adjustment system for automatically adjusting the configuration of
the track-engaging assembly;
[0078] FIG. 71 shows an example of an embodiment of the controller
of the adjustment mechanism, including a sensor and a processing
apparatus;
[0079] FIG. 72 shows an example of an embodiment of the sensor of
the controller;
[0080] FIG. 73 shows an example of an embodiment of the processing
apparatus of the controller;
[0081] FIG. 74 shows a diagram depicting interactions between the
sensor, the processing apparatus and an actuator of the adjustment
mechanism;
[0082] FIG. 75 shows an example of an embodiment of the actuator of
the automatic adjustment system;
[0083] FIG. 76 shows an example of an embodiment in which the
controller is part of a communication device;
[0084] FIGS. 77 and 78 show an example of an embodiment in which
the adjustment mechanism is configured to change the configuration
of the track-engaging assembly using one or more tools;
[0085] FIGS. 79 and 80 show perspective and plan views of the track
in accordance with an embodiment in which the traction projections
of the track comprise lateral stabilizers and a containment space;
and
[0086] FIG. 81 shows a perspective view of a traction projection in
accordance with the embodiment of FIGS. 79 and 80;
[0087] FIG. 82 shows a top view of a traction projection in
accordance with the variant of FIGS. 79 and 80;
[0088] FIG. 83 shows a volume of a containment space of the
traction projection of FIG. 81;
[0089] FIGS. 84 and 85 show side and top views of the traction
projection of FIG. 81;
[0090] FIGS. 86 and 87 show perspective and plan views of the track
in accordance with another embodiment in which the traction
projections of the track comprise lateral stabilizers and a
containment space; and
[0091] FIGS. 88 and 89 show front and rear perspective views of a
traction projection in accordance with the embodiment of FIGS. 86
and 87.
[0092] It is to be expressly understood that the description and
drawings are only for the purpose of illustrating certain
embodiments of the invention and are an aid for understanding. They
are not intended to be a definition of the limits of the
invention.
DETAILED DESCRIPTION OF EMBODIMENTS
[0093] FIG. 1 shows an example of a tracked vehicle 10 in
accordance with an embodiment of the invention. In this embodiment,
the vehicle 10 is a snowmobile. The snowmobile 10 is designed for
travelling on snow and in some cases ice. The snowmobile 10
comprises a frame 11, a powertrain 12, a track system 14, a ski
system 17, a seat 18, and a user interface 20, which enables a user
to ride, steer and otherwise control the snowmobile 10.
[0094] As further discussed below, in this embodiment, the track
system 14 may have various features to enhance its traction,
floatation, and/or other aspects of its performance, including, for
example, a lightweight design, enhanced tractive effects, an
enhanced heat management capability, an enhanced resistance to
lateral skidding (e.g., on a side hill), an adaptive capability to
adapt itself to different conditions (e.g., ground conditions, such
as different types of snow, soil, etc.; and/or other conditions),
an adjustability of its contact area with the ground, and/or other
features.
[0095] The powertrain 12 is configured for generating motive power
and transmitting motive power to the track system 14 to propel the
snowmobile 10 on the ground. To that end, the powertrain 12
comprises a prime mover 15, which is a source of motive power that
comprises one or more motors (e.g., an internal combustion engine,
an electric motor, etc.). For example, in this embodiment, the
prime mover 15 comprises an internal combustion engine. In other
embodiments, the prime mover 15 may comprise another type of motor
(e.g., an electric motor) or a combination of different types of
motor (e.g., an internal combustion engine and an electric motor).
The prime mover 15 is in a driving relationship with the track
system 14. That is, the powertrain 12 transmits motive power from
the prime mover 15 to the track system 14 in order to drive (i.e.,
impart motion to) the track system 14.
[0096] The ski system 17 is turnable to allow steering of the
snowmobile 10. In this embodiment, the ski system 17 comprises a
pair of skis 191, 192 connected to the frame 11 via a
ski-supporting assembly 13.
[0097] The seat 18 accommodates the user of the snowmobile 10. In
this case, the seat 18 is a straddle seat and the snowmobile 10 is
usable by a single person such that the seat 18 accommodates only
that person driving the snowmobile 10. In other cases, the seat 18
may be another type of seat, and/or the snowmobile 10 may be usable
by two individuals, namely one person driving the snowmobile 10 and
a passenger, such that the seat 18 may accommodate both of these
individuals (e.g., behind one another) or the snowmobile 10 may
comprise an additional seat for the passenger.
[0098] The user interface 20 allows the user to interact with the
snowmobile 10 to control the snowmobile 10. More particularly, the
user interface 20 comprises an accelerator, a brake control, and a
steering device that are operated by the user to control motion of
the snowmobile 10 on the ground. In this case, the steering device
comprises handlebars, although it may comprise a steering wheel or
other type of steering element in other cases. The user interface
20 also comprises an instrument panel (e.g., a dashboard) which
provides indicators (e.g., a speedometer indicator, a tachometer
indicator, etc.) to convey information to the user.
[0099] The track system 14 engages the ground to generate traction
for the snowmobile 10. With additional reference to FIGS. 2 and 3,
the track system 14 comprises a track 21 and a track-engaging
assembly 24 for driving and guiding the track 21 around the
track-engaging assembly 24. More particularly, in this embodiment,
the track-engaging assembly 24 comprises a frame 23 and a plurality
of track-contacting wheels which includes a plurality of drive
wheels 22.sub.1, 22.sub.2 and a plurality of idler wheels that
includes rear idler wheels 26.sub.1, 26.sub.2, lower roller wheels
28.sub.1-28.sub.6, and upper roller wheels 30.sub.1, 30.sub.2. As
it is disposed between the track 21 and the frame 11 of the
snowmobile 10, the track-engaging assembly 24 can be viewed as
implementing a suspension for the snowmobile 10. The track system
14 has a longitudinal direction and a first longitudinal end and a
second longitudinal end that define a length of the track system
14, a widthwise direction and a width that is defined by a width of
the track 21, and a height direction that is normal to its
longitudinal direction and its widthwise direction.
[0100] The track 21 engages the ground to provide traction to the
snowmobile 10. A length of the track 21 allows the track 21 to be
mounted around the track-engaging assembly 24. In view of its
closed configuration without ends that allows it to be disposed and
moved around the track-engaging assembly 24, the track 21 can be
referred to as an "endless" track. With additional reference to
FIGS. 4 to 7, the track 21 comprises an inner side 25 for facing
the track-engaging assembly 24 and a ground-engaging outer side 27
for engaging the ground. A top run 65 of the track 21 extends
between the longitudinal ends of the track system 14 and over the
track-engaging assembly 24 (including over the wheels 22.sub.1,
22.sub.2, 26.sub.1, 26.sub.2, 28.sub.1-28.sub.6, 30.sub.1,
30.sub.2), and a bottom run 66 of the track 21 extends between the
longitudinal ends of the track system 14 and under the
track-engaging assembly 24 (including under the wheels 22.sub.1,
22.sub.2, 26.sub.1, 26.sub.2, 28.sub.1-28.sub.6, 30.sub.1,
30.sub.2). The bottom run 66 of the track 11 defines an area of
contact 59 of the track 21 with the ground which generates traction
and bears a majority of a load on the track system 14, and which
will be referred to as a "contact patch" of the track 21 with the
ground. The track 21 has a longitudinal axis which defines a
longitudinal direction of the track 21 (i.e., a direction generally
parallel to its longitudinal axis) and transversal directions of
the track (i.e., directions transverse to its longitudinal axis),
including a widthwise direction of the track (i.e., a lateral
direction generally perpendicular to its longitudinal axis). The
track 21 has a thickness direction normal to its longitudinal and
widthwise directions.
[0101] The track 21 is elastomeric, i.e., comprises elastomeric
material, to be flexible around the track-engaging assembly 24. The
elastomeric material of the track 21 can include any polymeric
material with suitable elasticity. In this embodiment, the
elastomeric material of the track 21 includes rubber. Various
rubber compounds may be used and, in some cases, different rubber
compounds may be present in different areas of the track 21. In
other embodiments, the elastomeric material of the track 21 may
include another elastomer in addition to or instead of rubber
(e.g., polyurethane elastomer).
[0102] More particularly, the track 21 comprises an endless body 35
underlying its inner side 25 and ground-engaging outer side 27. In
view of its underlying nature, the body 35 will be referred to as a
"carcass". The carcass 35 is elastomeric in that it comprises
elastomeric material 38 which allows the carcass 35 to elastically
change in shape and thus the track 21 to flex as it is in motion
around the track-engaging assembly 24. The elastomeric material 38
can be any polymeric material with suitable elasticity. In this
embodiment, the elastomeric material 38 includes rubber. Various
rubber compounds may be used and, in some cases, different rubber
compounds may be present in different areas of the carcass 35. In
other embodiments, the elastomeric material 38 may include another
elastomer in addition to or instead of rubber (e.g., polyurethane
elastomer).
[0103] In this embodiment, as shown in FIGS. 8A and 8B, the carcass
35 comprises a plurality of reinforcements 45.sub.1-45.sub.P
embedded in its rubber 38. These reinforcements 45.sub.1-45.sub.P
can take on various forms.
[0104] For example, in this embodiment, a subset of the
reinforcements 45.sub.1-45.sub.P is a plurality of transversal
stiffening rods 36.sub.1-36.sub.N that extend transversally to the
longitudinal direction of the track 21 to provide transversal
rigidity to the track 21. More particularly, in this embodiment,
the transversal stiffening rods 36.sub.1-36.sub.N extend in the
widthwise direction of the track 21. Each of the transversal
stiffening rods 36.sub.1-36.sub.N may have various shapes and be
made of any suitably rigid material (e.g., metal, polymer or
composite material).
[0105] As another example, in this embodiment, the reinforcements
45.sub.i, 45.sub.j are layers of reinforcing material that is
flexible in the longitudinal direction of the track 21.
[0106] For instance, in this embodiment, the reinforcement 45.sub.i
is a layer of reinforcing cables 37.sub.1-37.sub.M that are
adjacent to one another and extend generally in the longitudinal
direction of the track 21 to enhance strength in tension of the
track 21 along its longitudinal direction. In this case, each of
the reinforcing cables 37.sub.1-37.sub.M is a cord including a
plurality of strands (e.g., textile fibers or metallic wires). In
other cases, each of the reinforcing cables 37.sub.1-37.sub.M may
be another type of cable and may be made of any material suitably
flexible longitudinally (e.g., fibers or wires of metal, plastic or
composite material). In some examples of implementation, respective
ones of the reinforcing cables 37.sub.1-37.sub.M may be constituted
by a single continuous cable length wound helically around the
track 21. In other examples of implementation, respective ones of
the transversal cables 37.sub.1-37.sub.M may be separate and
independent from one another (i.e., unconnected other than by
rubber of the track 21).
[0107] Also, in this embodiment, the reinforcement 45.sub.j is a
layer of reinforcing fabric 43. The reinforcing fabric 43 comprises
thin pliable material made usually by weaving, felting, knitting,
interlacing, or otherwise crossing natural or synthetic elongated
fabric elements, such as fibers, filaments, strands and/or others,
such that some elongated fabric elements extend transversally to
the longitudinal direction of the track 21 to have a reinforcing
effect in a transversal direction of the track 21. For instance,
the reinforcing fabric 43 may comprise a ply of reinforcing woven
fibers (e.g., nylon fibers or other synthetic fibers). For example,
the reinforcing fabric 43 may protect the transversal stiffening
rods 36.sub.1-36.sub.N, improve cohesion of the track 21, and
counter its elongation.
[0108] In some embodiments, as shown in FIG. 8B, the carcass 35 may
comprise only one type of reinforcement (e.g., the reinforcing
cables 37.sub.1-37.sub.M) or any other selected combination of the
above-mentioned reinforcements 45.sub.1-45.sub.P.
[0109] The carcass 35 may be molded into shape in a molding process
during which the rubber 38 is cured. For example, in this
embodiment, a mold may be used to consolidate layers of rubber
providing the rubber 38 of the carcass 35, the reinforcing cables
37.sub.1-37.sub.M and the layer of reinforcing fabric 43.
[0110] In this embodiment, the track 21 is a one-piece "jointless"
track such that the carcass 35 is a one-piece jointless carcass. In
other embodiments, the track 21 may be a "jointed" track (i.e.,
having at least one joint connecting adjacent parts of the track
21) such that the carcass 35 is a jointed carcass (i.e., which has
adjacent parts connected by the at least one joint). For example,
in some embodiments, the track 21 may comprise a plurality of track
sections interconnected to one another at a plurality of joints, in
which case each of these track sections includes a respective part
of the carcass 35. In other embodiments, the track 21 may be a
one-piece track that can be closed like a belt with connectors at
both of its longitudinal ends to form a joint.
[0111] The ground-engaging outer side 27 of the track 21 comprises
a ground-engaging outer surface 31 of the carcass 35 and a
plurality of traction projections 58.sub.1-58.sub.T that project
from the ground-engaging outer surface 31 to enhance traction on
the ground. The traction projections 58.sub.1-58.sub.T, which can
be referred to as "traction lugs" or "traction profiles", may have
any suitable shape (e.g., straight shapes, curved shapes, shapes
with straight parts and curved parts, etc.).
[0112] A height H of a traction projection 58.sub.x may have any
suitable value. For example, in some embodiments, the height of the
traction projection 58.sub.x may be at least 2 inches, in some
cases at least 3 inches, in some cases at least 4 inches, in some
cases at least 5 inches, and in some cases even more. The height of
the traction projection 58.sub.x may have any other suitable value
in other embodiments. The traction projection 58.sub.x also has a
longitudinal axis 75 and a first longitudinal end 308.sub.1 and a
second longitudinal end 308.sub.2 that define a length L of the
traction projection 58.sub.x. The longitudinal axis 75 of the
traction projection 58.sub.x extends transversally to the
longitudinal direction of the track 21, in this example in the
widthwise direction of the track 21.
[0113] In this embodiment, each of the traction projections
58.sub.1-58.sub.T is an elastomeric traction projection in that it
comprises elastomeric material 41. The elastomeric material 41 can
be any polymeric material with suitable elasticity. More
particularly, in this embodiment, the elastomeric material 41
includes rubber. Various rubber compounds may be used and, in some
cases, different rubber compounds may be present in different areas
of each of the traction projections 58.sub.1-58.sub.T. In other
embodiments, the elastomeric material 41 may include another
elastomer in addition to or instead of rubber (e.g., polyurethane
elastomer).
[0114] The traction projections 58.sub.1-58.sub.T may be provided
on the ground-engaging outer side 27 in various ways. For example,
in this embodiment, the traction projections 58.sub.1-58.sub.T are
provided on the ground-engaging outer side 27 by being molded with
the carcass 35.
[0115] The inner side 25 of the track 21 comprises an inner surface
32 of the carcass 35 and a plurality of inner projections
34.sub.1-34.sub.D that project from the inner surface 32 and are
positioned to contact the track-engaging assembly 24 (e.g., at
least some of the wheels 22.sub.1, 22.sub.2, 26.sub.1, 26.sub.2,
28.sub.1-28.sub.6, 30.sub.1, 30.sub.2) to do at least one of
driving (i.e., imparting motion to) the track 21 and guiding the
track 21. Since each of them is used to do at least one of driving
the track 21 and guiding the track 21, the inner projections
34.sub.1-34.sub.D can be referred to as "drive/guide projections"
or "drive/guide lugs". In some cases, a drive/guide lug 34i may
interact with a given one of the drive wheels 22.sub.1, 22.sub.2 to
drive the track 21, in which case the drive/guide lug 34.sub.i is a
drive lug. In other cases, a drive/guide lug 34.sub.i may interact
with a given one of the idler wheels 26.sub.1, 26.sub.2,
28.sub.1-28.sub.2, 30.sub.1, 30.sub.2 and/or another part of the
track-engaging assembly 24 to guide the track 21 to maintain proper
track alignment and prevent de-tracking without being used to drive
the track 21, in which case the drive/guide lug 34.sub.i is a guide
lug. In yet other cases, a drive/guide lug 34.sub.i may both (i)
interact with a given one of the drive wheels 22.sub.1, 22.sub.3 to
drive the track 21 and (ii) interact with a given one of the idler
wheels 26.sub.1, 26.sub.2, 28.sub.1-28.sub.6, 30.sub.1, 30.sub.2
and/or another part of the track-engaging assembly 24 to guide the
track 21, in which case the drive/guide lug 34.sub.i is both a
drive lug and a guide lug.
[0116] In this embodiment, each of the drive/guide lugs
34.sub.1-34.sub.D is an elastomeric drive/guide lug in that it
comprises elastomeric material 42. The elastomeric material 42 can
be any polymeric material with suitable elasticity. More
particularly, in this embodiment, the elastomeric material 42
includes rubber. Various rubber compounds may be used and, in some
cases, different rubber compounds may be present in different areas
of each of the drive/guide lugs 34.sub.1-34.sub.D. In other
embodiments, the elastomeric material 42 may include another
elastomer in addition to or instead of rubber (e.g., polyurethane
elastomer).
[0117] The drive/guide lugs 34.sub.1-34.sub.D may be provided on
the inner side 25 in various ways. For example, in this embodiment,
the drive/guide lugs 34.sub.1-34.sub.D are provided on the inner
side 25 by being molded with the carcass 35.
[0118] In this embodiment, the carcass 35 has a thickness T.sub.c
which is relatively small. The thickness T.sub.c of the carcass 35
is measured from the inner surface 32 to the ground-engaging outer
surface 31 of the carcass 35 between longitudinally-adjacent ones
of the traction projections 58.sub.1-58.sub.T. For example, in some
embodiments, the thickness T.sub.c of the carcass 35 may be no more
than 0.25 inches, in some cases no more than 0.22 inches, in some
cases no more than 0.20 inches, and in some cases even less (e.g.,
no more than 0.18 or 0.16 inches). The thickness T.sub.c of the
carcass 35 may have any other suitable value in other
embodiments.
[0119] Elastomeric material of a given portion of the endless track
21, including the elastomeric material 38 of the carcass 35, the
elastomeric material 41 of one of the traction projection
58.sub.1-58.sub.T, and the elastomeric material 42 of one of the
drive/guide lugs 34.sub.1-34.sub.D, has various material
properties, including a hardness (e.g., durometers in a Shore A
hardness scale) and a modulus of elasticity, which can have any
suitable value.
[0120] If the elastomeric material of the given portion of the
track 21 is constituted of a single elastomer, the hardness of the
elastomeric material of the given portion of the track 21 is the
hardness of this single elastomer. Alternatively, if the
elastomeric material of the given portion of the track 21 is
constituted of two or more different elastomers, the hardness of
the elastomeric material of the given portion of the track 21 is
taken as an average hardness, which is obtained by multiplying a
proportion of each elastomer in the elastomeric material of the
given portion of the track 21 by that elastomer's hardness and then
summing the results. That is, if the elastomeric material of the
given portion of the track 21 is constituted of N elastomers, the
average hardness is
A avg = i = 1 N P i A i ##EQU00001##
where A.sub.i is the hardness of elastomer "i" and P.sub.i is the
proportion (%) of elastomer "i" in the elastomeric material of the
given portion of the track 21. In situations where this calculated
value is not an integer and the hardness scale is only in integers,
this calculated value rounded to the nearest integer gives the
average hardness. An elastomer's hardness can be obtained from a
standard ASTM D-2240 test (or equivalent test).
[0121] Similarly, if the elastomeric material of the given portion
of the track 21 is constituted of a single elastomer, the modulus
of elasticity of the elastomeric material of the given portion of
the track 21 is the modulus of elasticity of this single elastomer.
Alternatively, if the elastomeric material of the given portion of
the track 21 is constituted of two or more different elastomers,
the modulus of elasticity of the elastomeric material of the given
portion of the track 21 is taken as an average modulus of
elasticity, which is obtained by multiplying a proportion (%) of
each elastomer in the elastomeric material of the given portion of
the track 21 by that elastomer's modulus of elasticity and then
summing the results. That is, if the elastomeric material of the
given portion of the track 21 is constituted of N elastomers, the
average modulus of elasticity is
.lamda. avg = i = 1 N P i .lamda. i ##EQU00002##
where .lamda..sub.i is the modulus of elasticity of elastomer "i"
and P.sub.i is the proportion (%) of elastomer "i" in the
elastomeric material of the given portion of the track 21. For
instance, in an embodiment in which the elastomeric material of the
given portion of the track 21 is constituted of two types of
rubbers, say rubber "A" having a modulus of elasticity of 1.9 MPa
and being present in a proportion of 15% and rubber "B" having a
modulus of elasticity of 6.3 MPa and being present in a proportion
of 85%, the average modulus of elasticity of the elastomeric
material of the given portion of the track 21 is 5.64 MPa. An
elastomer's modulus of elasticity can be obtained from a standard
ASTM D-412-A test (or equivalent test) based on a measurement at
100% elongation of the elastomer.
[0122] The track-engaging assembly 24 is configured to drive and
guide the track 21 around the track-engaging assembly 24.
[0123] Each of the drive wheels 22.sub.1, 22.sub.2 is rotatable by
an axle for driving the track 21. That is, power generated by the
prime mover 15 and delivered over the powertrain 12 of the
snowmobile 10 rotates the axle, which rotates the drive wheels
22.sub.1, 22.sub.2, which impart motion of the track 21. In this
embodiment, each drive wheel 22.sub.i comprises a drive sprocket
engaging some of the drive/guide lugs 34.sub.1-34.sub.D of the
inner side 25 of the track 21 in order to drive the track 21. In
other embodiments, the drive wheel 22.sub.i may be configured in
various other ways. For example, in embodiments where the track 21
comprises drive holes, the drive wheel 22.sub.i may have teeth that
enter these holes in order to drive the track 21. As yet another
example, in some embodiments, the drive wheel 22.sub.i may
frictionally engage the inner side 25 of the track 21 in order to
frictionally drive the track 21. The drive wheels 22.sub.1,
22.sub.2 may be arranged in other configurations and/or the track
system 14 may comprise more or less drive wheels (e.g., a single
drive wheel, more than two drive wheels, etc.) in other
embodiments.
[0124] The idler wheels 26.sub.1, 26.sub.2, 28.sub.1-28.sub.6,
30.sub.1, 30.sub.2 are not driven by power supplied by the prime
mover 15, but are rather used to do at least one of guiding the
track 21 as it is driven by the drive wheels 22.sub.1, 22.sub.2,
tensioning the track 21, and supporting part of the weight of the
snowmobile 10 on the ground via the track 21. More particularly, in
this embodiment, the rear idler wheels 26.sub.1, 26.sub.2 are
trailing idler wheels that maintain the track 21 in tension, guide
the track 21 as it wraps around them, and can help to support part
of the weight of the snowmobile 10 on the ground via the track 21.
The lower roller wheels 28.sub.1-28.sub.6 roll on the inner side 25
of the track 21 along the bottom run 66 of the track 21 to apply
the bottom run 66 on the ground. The upper roller wheels 30.sub.1,
30.sub.2 roll on the inner side 25 of the track 21 along the top
run 65 of the track 21 to support and guide the top run 65 as the
track 21 moves. The idler wheels 26.sub.1, 26.sub.2,
28.sub.1-28.sub.6, 30.sub.1, 30.sub.2 may be arranged in other
configurations and/or the track assembly 14 may comprise more or
less idler wheels in other embodiments.
[0125] The frame 23 of the track system 14 supports various
components of the track-engaging assembly 24, including, in this
embodiment, the idler wheels 26.sub.1, 26.sub.2, 28.sub.1-28.sub.6,
30.sub.1, 30.sub.2. More particularly, in this embodiment, the
frame 23 comprises an elongate support 62 extending in the
longitudinal direction of the track system 14 along the bottom run
66 of the track 21 and frame members 49.sub.1-49.sub.F extending
upwardly from the elongate support 62.
[0126] The elongate support 62 comprises rails 44.sub.1, 44.sub.2
extending in the longitudinal direction of the track system 14
along the bottom run 66 of the track 21. In this example, the idler
wheels 26.sub.1, 26.sub.2, 28.sub.1-28.sub.6 are mounted to the
rails 44.sub.1, 44.sub.2. In this embodiment, the elongate support
62 comprises sliding surfaces 77.sub.1, 77.sub.2 for sliding on the
inner side 25 of the track 21 along the bottom run 66 of the track
21. Thus, in this embodiment, the idler wheels 26.sub.1, 26.sub.2,
28.sub.1-28.sub.6 and the sliding surfaces 77.sub.1, 77.sub.2 of
the elongate support 62 can contact the bottom run 66 of the track
21 to guide the track 21 and apply it onto the ground for traction.
In this example, the sliding surfaces 77.sub.1, 77.sub.2 can slide
against the inner surface 32 of the carcass 35 and can contact
respective ones of the drive/guide lugs 34.sub.1-34.sub.D to guide
the track 21 in motion. Also, in this example, the sliding surfaces
77.sub.1, 77.sub.2 are curved upwardly in a front region of the
track system 14 to guide the track 21 towards the drive wheels
22.sub.1, 22.sub.2. In some cases, as shown in FIG. 17, the track
21 may comprise slide members 39.sub.1-39.sub.S that slide against
the sliding surfaces 77.sub.1, 77.sub.2 to reduce friction. The
slide members 39.sub.1-39.sub.S, which can sometimes be referred to
as "clips", may be mounted via holes (i.e., windows)
40.sub.1-40.sub.H of the track 21. In other cases, the track 21 may
be free of such slide members.
[0127] In this embodiment, the elongate support 62 comprises
sliders 33.sub.1, 33.sub.2 mounted to respective ones of the rails
44.sub.1, 44.sub.2 and comprising respective ones of the sliding
surfaces 77.sub.1, 77.sub.2. In this embodiment, the sliders
33.sub.1, 33.sub.2 are mechanically interlocked with the rails
44.sub.1, 44.sub.2. In other embodiments, instead of or in addition
to being mechanically interlocked with the rails 44.sub.1,
44.sub.2, the sliders 33.sub.1, 33.sub.2 may be fastened to the
rails 44.sub.1, 44.sub.2. For example, in some embodiments, the
sliders 33.sub.1, 33.sub.2 may be fastened to the rails 44.sub.1,
44.sub.2 by one or more mechanical fasteners (e.g., bolts, screws,
etc.), by an adhesive, and/or by any other suitable fastener.
[0128] In some examples, each slider 33.sub.i may comprise a
low-friction material which may reduce friction between its sliding
surface 77.sub.i and the inner side 25 of the track 21. For
instance, the slider 33.sub.i may comprise a polymeric material
having a low coefficient of friction with the rubber of the track
21. For example, in some embodiments, the slider 33.sub.i may
comprise a thermoplastic material (e.g., a Hifax.RTM.
polypropylene). The slider 33.sub.i may comprise any other suitable
material in other embodiments. For instance, in some embodiments,
the sliding surface 77.sub.i of the slider 33.sub.i may comprise a
coating (e.g., a polytetrafluoroethylene (PTFE) coating) that
reduces friction between it and the inner side 25 of the track 21,
while a remainder of the slider 33.sub.i may comprise any suitable
material (e.g., a metallic material, another polymeric material,
etc.).
[0129] While in embodiments considered above the sliding surface
77.sub.i is part of the slider 33.sub.i which is separate from and
mounted to each rail 44.sub.i, in other embodiments, the sliding
surface 77.sub.i may be part of the rail 44.sub.i. That is, the
sliding surface 77.sub.i may be integrally formed (e.g., molded,
cast, or machined) as part of the rail 44.sub.i.
[0130] The frame members 49.sub.1-49.sub.F extend upwardly from the
elongate support 62 to hold the upper roller wheels 30.sub.1,
30.sub.2 such that the upper roller wheels 30.sub.1, 30.sub.2 roll
on the inner side 25 of the track 21 along the top run 65 of the
track 21.
[0131] The track-engaging assembly 24 may be implemented in any
other suitable way in other embodiments.
[0132] The track system 14, including the track 21, may have
various features to enhance its traction, floatation, and/or other
aspects of its performance, including, for example, a lightweight
design, enhanced tractive effects, an enhanced heat management
capability, an enhanced resistance to lateral skidding (e.g., on a
side hill), an adaptive capability to adapt itself to different
conditions (e.g., ground conditions, such as different types of
snow, soil, etc.; and/or other conditions), an adjustability of its
contact patch 59, and/or other features. This may be achieved in
various ways in various embodiments, examples of which will now be
discussed.
1. Lightweight Track
[0133] In some embodiments, the track 21 may be designed to reduce
a weight of the track 21 while maintaining performance of the track
21. This may help to reduce power consumption, improve riding of
the snowmobile 10, and/or enhance other aspects of performance of
the snowmobile 10.
1.1 Thin Carcass
[0134] In some embodiments, as shown in FIG. 7, the carcass 35 may
be very thin yet remain sufficiently rigid for proper traction and
floatation.
[0135] For example, in some embodiments, the thickness T.sub.c of
the carcass 35 may be no more than 0.20 inches, in some cases no
more than 0.18 inches, in some cases no more than 0.16 inches, and
in some cases even less (e.g., no more than 0.14 inches). For
instance, in some examples of implementation, the thickness T.sub.c
of the carcass 35 may be 0.165 inches or less.
[0136] Meanwhile, in such embodiments, rigidity characteristics of
the carcass 35 allow proper performance of the track 21. For
instance, the rigidity characteristics of the carcass 35 may relate
to (1) a longitudinal rigidity of the carcass 35, i.e., a rigidity
of the carcass 35 in the longitudinal direction of the track 21
which refers to the carcass's resistance to bending about an axis
parallel to the widthwise direction of the track 21, and/or (2) a
widthwise rigidity of the carcass 35, i.e., a rigidity of the
carcass 35 in the widthwise direction of the track 21 which refers
to the carcass's resistance to bending about an axis parallel to
the longitudinal direction of the track 21.
[0137] To observe the longitudinal rigidity and the widthwise
rigidity of the carcass 35 without influence from a remainder of
the track 21, as shown in FIG. 9, the carcass 35 can be isolated
from the remainder of the track 21 (e.g., by scraping, cutting, or
otherwise removing the traction projections 58.sub.1-58.sub.T and
the drive/guide lugs 34.sub.1-34.sub.D, or by producing the carcass
35 without the traction projections 58.sub.1-58.sub.T, the carcass
35, the drive/guide lugs 34.sub.1-34.sub.D) and a three-point
bending test can be performed on a sample of the carcass 35 to
subject the carcass 35 to loading tending to bend the carcass 35 in
specified ways (i.e., bend the carcass 35 longitudinally to observe
the longitudinal rigidity of the carcass 35 and bend the carcass 35
laterally to observe the widthwise rigidity of the carcass 35) and
measure parameters indicative of the longitudinal rigidity and the
widthwise rigidity of the carcass 35. For instance in some
embodiments, the three-point bending test may be based on
conditions defined in a standard test (e.g., ISO 178(2010) but
using elastomeric material). For example: [0138] To observe the
longitudinal rigidity of the carcass 35, the three-point bending
test may be performed to subject the carcass 35 to loading tending
to longitudinally bend the carcass 35 until a predetermined
deflection of the carcass 35 is reached and measure a bending load
at that predetermined deflection of the carcass 35. The
predetermined deflection of the carcass 35 may be selected such as
to correspond to a predetermined strain of the carcass 35 at a
specified point of the carcass 35 (e.g., a point of the inner
surface 32 of the carcass 35). For instance, in some embodiments,
the predetermined strain of the carcass 35 may between 3% and 5%.
The bending load at the predetermined deflection of the carcass 35
may be used to calculate a bending stress at the specified point of
the carcass 35. The bending stress at the specified point of the
carcass 35 may be calculated as .sigma.=My/I, where M is the moment
about a longitudinal-bending neutral axis 63 of the carcass 35
caused by the bending load, y is the perpendicular distance from
the specified point of the carcass 35 to the neutral axis of the
carcass 35, and I is the second moment of area about the neutral
axis of the carcass 35. The longitudinal rigidity of the carcass 35
can be taken as the bending stress at the predetermined strain
(i.e., at the predetermined deflection) of the carcass 35.
Alternatively, the longitudinal rigidity of the carcass 35 may be
taken as the bending load at the predetermined deflection of the
carcass 35; [0139] To observe the widthwise rigidity of the carcass
35, the three-point bending test may be performed to subject the
carcass 35 to loading tending to laterally bend the carcass 35
until a predetermined deflection of the carcass 35 is reached and
measure a bending load at that predetermined deflection of the
carcass 35. The predetermined deflection of the carcass 35 may be
selected such as to correspond to a predetermined strain of the
carcass 35 at a specified point of the carcass 35 (e.g., a point of
the inner surface 32 of the carcass 35). For instance, in some
embodiments, the predetermined strain of the carcass 35 may between
3% and 5%. The bending load at the predetermined deflection of the
carcass 35 may be used to calculate a bending stress at the
specified point of the carcass 35. The bending stress at the
specified point of the carcass 35 may be calculated as
.sigma.=My/I, where M is the moment about a lateral-bending neutral
axis 57 of the carcass 35 caused by the bending load, y is the
perpendicular distance from the specified point of the carcass 35
to the neutral axis of the carcass 35, and I is the second moment
of area about the neutral axis of the carcass 35. The widthwise
rigidity of the carcass 35 can be taken as the bending stress at
the predetermined strain (i.e., at the predetermined deflection) of
the carcass 35. Alternatively, the widthwise rigidity of the
carcass 35 may be taken as the bending load at the predetermined
deflection of the carcass 35.
[0140] Thus, in such embodiments where the carcass 35 is very thin,
the widthwise rigidity of the carcass 35 may be significantly
greater than the longitudinal rigidity of the carcass 35. For
instance, a ratio of the widthwise rigidity of the carcass 35 over
the longitudinal rigidity of the carcass 35 may be at least 1.5, in
some cases at least 2, in some cases at least 2.5, in some cases at
least 3, and in some cases even more (e.g., 4, 5, etc.).
[0141] As another example, in some embodiments, the carcass 35
being very thin while sufficiently rigid may be such that a ratio
of the longitudinal rigidity of the carcass 35 over the thickness
T.sub.c of the carcass 35 is relatively high and/or a ratio of the
widthwise rigidity of the carcass 35 over the thickness T.sub.c of
the carcass 35 is relatively high.
[0142] The carcass 35 may be maintained sufficiently rigid in any
suitable way in various embodiments. Examples of this are discussed
below.
1.1.1 Stiffer Reinforcement
[0143] In some embodiments, as shown in FIG. 8A, a reinforcement
45.sub.x embedded in the rubber 38 of the carcass 35 may be
stiffer. That is, a bending stiffness of the reinforcement 45.sub.x
in the longitudinal direction of the track 21 and/or a bending
stiffness of the reinforcement 45.sub.x in the widthwise direction
of the track 21 may be relatively high. As shown in FIG. 8A, the
reinforcement 45.sub.x may be, for example, a layer of reinforcing
material flexible in the longitudinal direction of the track 21,
such as a layer of reinforcing cables 37.sub.1-37.sub.M or a layer
of reinforcing fabric 43.
[0144] The bending stiffness of the reinforcement 45.sub.x in the
longitudinal direction of the track 21 may be measured using a
three-point bending test performed on a sample of the reinforcement
45.sub.x to subject the reinforcement 45.sub.x to loading tending
to bend the reinforcement 45.sub.x in the longitudinal direction of
the track 21 until a predetermined deflection of the reinforcement
45.sub.x is reached and measure a bending load at that
predetermined deflection of the reinforcement 45.sub.x, and
calculating the bending stiffness of the reinforcement 45.sub.x in
the longitudinal direction of the track 21 as a ratio of that
bending load over that predetermined deflection.
[0145] The bending stiffness of the reinforcement 45.sub.x in the
longitudinal direction of the track 21 depends on a product of an
area moment of inertia (i.e., a second moment of area) of a
cross-section of the reinforcement 45.sub.x normal to the
longitudinal direction of the track 21 and a modulus of elasticity
(i.e., Young's modulus) of a material of the reinforcement
45.sub.x. As such, the bending stiffness of the reinforcement
45.sub.x in the longitudinal direction of the track 21 may be
increased by increasing the area moment of inertia of the
cross-section of the reinforcement 45.sub.x normal to the
longitudinal direction of the track 21 and/or the modulus of
elasticity of the material of the reinforcement 45.sub.x.
[0146] Similarly, the bending stiffness of the reinforcement
45.sub.x in the widthwise direction of the track 21 may be measured
using a three-point bending test performed on a sample of the
reinforcement 45.sub.x to subject the reinforcement 45.sub.x to
loading tending to bend the reinforcement 45.sub.x in the widthwise
direction of the track 21 until a predetermined deflection of the
reinforcement 45.sub.x is reached and measure a bending load at
that predetermined deflection of the reinforcement 45.sub.x, and
calculating the bending stiffness of the reinforcement 45.sub.x in
the widthwise direction of the track 21 as a ratio of that bending
load over that predetermined deflection.
[0147] The bending stiffness of the reinforcement 45.sub.x in the
widthwise direction of the track 21 depends on a product of an area
moment of inertia (i.e., a second moment of area) of a
cross-section of the reinforcement 45.sub.x normal to the widthwise
direction of the track 21 and the modulus of elasticity (i.e.,
Young's modulus) of the material of the reinforcement 45.sub.x. As
such, the bending stiffness of the reinforcement 45.sub.x in the
widthwise direction of the track 21 may be increased by increasing
the area moment of inertia of the cross-section of the
reinforcement 45.sub.x normal to the widthwise direction of the
track 21 and/or the modulus of elasticity of the material of the
reinforcement 45.sub.x.
[0148] For example, in some embodiments, the bending stiffness of
the reinforcement 45.sub.x in the longitudinal direction of the
track 21 may be at least a certain value, and/or the bending
stiffness of the reinforcement 45.sub.x in the widthwise direction
of the track 21 may be at least a certain value.
[0149] In some embodiments, a ratio of the bending stiffness of the
reinforcement 45.sub.x in the longitudinal direction of the track
21 over the bending stiffness of the reinforcement 45.sub.x in the
widthwise direction of the track 21 may be at least 2, in some
cases at least 3, in some cases at least 4, in some cases at least
5, and in some cases even more (e.g., 6, 7, 8 or more).
[0150] As another example, in some embodiments, the carcass 35
being very thin while sufficiently rigid may be such that a ratio
of the bending stiffness of the reinforcement 45.sub.x in the
longitudinal direction of the track 21 over the thickness T.sub.c
of the carcass 35 is relatively high and/or a ratio of the bending
stiffness of the reinforcement 45.sub.x in the widthwise direction
of the track 21 over the thickness T.sub.c of the carcass 35 is
relatively high. For instance, in some embodiments, the ratio of
the bending stiffness of the reinforcement 45.sub.x in the
longitudinal direction of the track 21 over the thickness T.sub.c
of the carcass 35 may be at least a certain value, and/or the ratio
of the bending stiffness of the reinforcement 45.sub.x in the
widthwise direction of the track 21 over the thickness T.sub.c of
the carcass 35 may be at least a certain value.
[0151] As another example, in some embodiments, a ratio of the
modulus of elasticity of the reinforcement 45.sub.x in the
longitudinal direction of the track 21 over the modulus of
elasticity of the reinforcement 45.sub.x in the widthwise direction
of the track 21 may be at least 2, in some cases at least 3, in
some cases at least 4, in some cases at least 5, and in some cases
even more (e.g., 6, 7, 8 or more). For instance, in some
embodiments, the modulus of elasticity of the reinforcement
45.sub.x in the longitudinal direction of the track 21 may be at
least 200 MPa, in some cases at least 300 MPa, in some cases at
least 400 MPa, and in some cases even more, while the modulus of
elasticity of the reinforcement 45.sub.x in the widthwise direction
of the track 21 may be at least 1 GPa, in some cases at least 1.5
GPa, in some cases at least 2.0 GPa, in some cases at least 2.5
GPa, and in some cases even more. Alternatively or additionally,
the area moment of inertia of the cross-section of the
reinforcement 45.sub.x normal to the longitudinal direction of the
track 21 and/or the area moment of inertia of the cross-section of
the reinforcement 45.sub.x normal to the widthwise direction of the
track 21 may be at least a certain value. The modulus of elasticity
of the reinforcement 45.sub.x, the area moment of inertia of the
cross-section of the reinforcement 45.sub.x normal to the
longitudinal direction of the track 21, and/or the area moment of
inertia of the cross-section of the reinforcement 45.sub.x normal
to the widthwise direction of the track 21 may have any other
suitable values in other embodiments.
[0152] As another example, in some embodiments, the carcass 35
being very thin while sufficiently rigid may be such that a ratio
of the modulus of elasticity of the reinforcement 45.sub.x over the
thickness T.sub.c of the carcass 35 is relatively high, a ratio of
the area moment of inertia of the cross-section of the
reinforcement 45.sub.x normal to the longitudinal direction of the
track 21 over the thickness T.sub.c of the carcass 35 is relatively
high, and/or a ratio of the area moment of inertia of the
cross-section of the reinforcement 45.sub.x normal to the widthwise
direction of the track 21 over the thickness T.sub.c of the carcass
35 is relatively high. For instance, in some embodiments, the ratio
of the modulus of elasticity of the reinforcement 45.sub.x in the
longitudinal direction of the track 21 over the thickness T.sub.c
of the carcass 35 may be at least 1 GPa/in, in some cases at least
1.5 GPa/in, in some cases at least 2 GPa/in, and in some cases even
more, and the ratio of the modulus of elasticity of the
reinforcement 45.sub.x in the widthwise direction of the track 21
over the thickness T.sub.c of the carcass 35 may be at least 5
GPa/in, in some cases at least 7 GPa/in, in some cases at least 9
GPa/in, in some cases at least 12 GPa/in, and in some cases even
more. Moreover, the ratio of the area moment of inertia of the
cross-section of the reinforcement 45.sub.x normal to the
longitudinal direction of the track 21 over the thickness T.sub.c
of the carcass 35 may be at least a certain value, and/or the ratio
of the area moment of inertia of the cross-section of the
reinforcement 45.sub.x normal to the widthwise direction of the
track 21 over the thickness T.sub.c of the carcass 35 may be at
least a certain value. These ratios may have any other suitable
values in other embodiments.
1.1.2 Stiffer Elastomeric Material
[0153] In some embodiments, the elastomeric material 38 of the
carcass 35 may be stiffer. For example, in some embodiments, the
300% modulus of the elastomeric material 38 of the carcass 35
(i.e., the Young's modulus of the elastomeric material 38 at 300%
elongation) may be at least 15 MPa, in some cases at least 20 MPa,
in some cases at least 25 MPa, and in some cases even more (e.g.,
30 MPa). The modulus of elasticity of the elastomeric material 38
of the carcass 35 may have any other suitable value in other
embodiments.
1.1.3 Increased Spacing of Reinforcements
[0154] In some embodiments, respective ones of the reinforcements
45.sub.1-45.sub.P embedded in the elastomeric material 38 of the
carcass 35 may be spaced apart from one another significantly in
order to increase the longitudinal rigidity and/or the widthwise
rigidity of the carcass 35.
[0155] For example, in some embodiments, as shown in FIG. 10, a
reinforcement 45.sub.i and a reinforcement 45.sub.j that mainly
stiffen the track 21 laterally and that are adjacent to one another
in the thickness direction of the track 21 (i.e., there is no
reinforcement mainly stiffening the track 21 laterally between the
reinforcements 45.sub.i, 45.sub.j) may be spaced apart
significantly in order to increase the track's widthwise rigidity.
Each of the reinforcements 45.sub.i, 45.sub.j may thus be spaced
apart significantly from the lateral-bending neutral axis 57 of the
carcass 35.
[0156] For instance, in some embodiments, a ratio of a spacing
S.sub.r-w of the reinforcements 45.sub.i, 45.sub.j in the thickness
direction of the track 21 over the thickness T.sub.c of the carcass
35 may be at least 0.4, in some cases at least 0.5, in some cases
at least 0.6, and in some cases even more. As an example, in some
embodiments, where the thickness T.sub.c of the carcass 35 is 5 mm,
the spacing S.sub.r-w of the reinforcements 45.sub.i, 45.sub.j may
be at least 2 mm, in some cases at least 2.5 mm, in some cases at
least 3 mm, and in some cases even more. The ratio of the spacing
S.sub.r-w of the reinforcements 45.sub.i, 45.sub.j over the
thickness T.sub.c of the carcass 35, the spacing S.sub.r-w of the
reinforcements 45.sub.i, 45.sub.j, and/or the thickness T.sub.c of
the carcass 35 may have any other suitable value in other
embodiments.
[0157] In some embodiments, a stiffness of the reinforcement
45.sub.i in the widthwise direction of the track 21 and a stiffness
of the reinforcement 45.sub.j in the widthwise direction of the
track 21 may be substantially identical. For instance, in some
cases, the reinforcements 45.sub.i, 45.sub.j may be of a common
type or structure. For example, the reinforcements 45.sub.i,
45.sub.j may be substantially identical layers of reinforcing
cables or of reinforcing fabric.
[0158] Alternatively, in some embodiments, the stiffness of the
reinforcement 45.sub.i in the widthwise direction of the track 21
and the stiffness of the reinforcement 45.sub.j in the widthwise
direction of the track 21 may be substantially different. For
example, in some cases, the reinforcements 45.sub.i, 45.sub.j may
be layers of reinforcing cables that differ from one another (e.g.,
in terms of cable material, diameter, pitch, etc.). As another
example, in some cases, the reinforcements 45.sub.i, 45.sub.j may
be layers of reinforcing fabric that differ from one another (e.g.,
in terms of fabric material, configuration (e.g., weft, warp, bias,
etc.), etc.). As yet another example, in some cases, the
reinforcements 45.sub.i, 45.sub.j may be respective ones of a layer
of reinforcing cable and a layer of reinforcing fabric.
[0159] In a similar manner, in some embodiments, as shown in FIG.
11, a reinforcement 45.sub.m and a reinforcement 45.sub.n that
mainly stiffen the track 21 longitudinally and that are adjacent to
one another in the thickness direction of the track 21 (i.e., there
is no reinforcement mainly stiffening the track 21 longitudinally
between the reinforcements 45.sub.m, 45.sub.n) may be spaced apart
significantly in order to increase the track's longitudinal
rigidity. Each of the reinforcements 45.sub.m, 45.sub.n may thus be
spaced apart significantly from a longitudinal-bending neutral axis
63 of the carcass 35.
[0160] For instance, in some embodiments, a ratio of a spacing
S.sub.r-l of the reinforcements 45.sub.m, 45.sub.n in the thickness
direction of the track 21 over the thickness T.sub.c of the carcass
35 may be at least 0.4, in some cases at least 0.5, in some cases
at least 0.6, and in some cases even more. As an example, in some
embodiments, where the thickness T.sub.c of the carcass 35 is 5 mm,
the spacing S.sub.r-l of the reinforcements 45.sub.m, 45.sub.n may
be at least 2 mm, in some cases at least 2.5 mm, in some cases at
least 3 mm, and in some cases even more. The ratio of the spacing
S.sub.r-l of the reinforcements 45.sub.m, 45.sub.n over the
thickness T.sub.c of the carcass 35, the spacing S.sub.r-l of the
reinforcements 45.sub.m, 45.sub.n, and/or the thickness T.sub.c of
the carcass 35 may have any other suitable value in other
embodiments.
[0161] In some embodiments, a stiffness of the reinforcement
45.sub.m in the longitudinal direction of the track 21 and a
stiffness of the reinforcement 45.sub.n in the longitudinal
direction of the track 21 may be substantially identical. For
instance, in some cases, the reinforcements 45.sub.m, 45.sub.n may
be of a common type or structure. For example, the reinforcements
45.sub.m, 45.sub.n may be substantially identical layers of
reinforcing cables or of reinforcing fabric.
[0162] Alternatively, in some embodiments, the stiffness of the
reinforcement 45.sub.m in the longitudinal direction of the track
21 and the stiffness of the reinforcement 45.sub.n in the
longitudinal direction of the track 21 may be substantially
different. For example, in some cases, the reinforcements 45.sub.m,
45.sub.n may be layers of reinforcing cables that differ from one
another (e.g., in terms of cable material, diameter, pitch, etc.).
As another example, in some cases, the reinforcements 45.sub.m,
45.sub.n may be layers of reinforcing fabric that differ from one
another (e.g., in terms of fabric material, configuration (e.g.,
weft, warp, bias, etc.), etc.). As yet another example, in some
cases, the reinforcements 45.sub.m, 45.sub.n may be respective ones
of a layer of reinforcing cable and a layer of reinforcing
fabric.
1.2 Low-Density Elastomeric Material
[0163] In some embodiments, as shown in FIG. 12, the elastomeric
material of the track 21 may comprise elastomeric material 50
having a density that is relatively low. This "lower-density"
elastomeric material 50 may help to reduce the weight of the track
21.
[0164] For example, in this embodiment, in addition to the
lower-density elastomeric material 50, the elastomeric material of
the track 21 comprises elastomeric material 52 having a density
that is relatively higher such that the lower-density elastomeric
material 50 is less dense than this "higher-density" elastomeric
material 52. For instance, in some embodiments, a ratio of the
density of the lower-density elastomeric material 50 over the
density of the higher-density elastomeric material 52 may be no
more than 0.9, in some cases no more than 0.8, in some cases no
more than 0.7, in some cases no more than 0.6, and in some cases
even less (e.g., no more than 0.5). This ratio may have any other
suitable value in other embodiments.
[0165] For instance, in some embodiments, the density of the
lower-density elastomeric material 50 may be no more than 1.4
g/cm.sup.3, in some cases no more than 1.2 g/cm.sup.3, in some
cases no more than 1.0 g/cm.sup.3, in some cases no more than 0.8
g/cm.sup.3 and in some cases even less, and/or the density of the
higher-density elastomeric material 52 may be at least 1.4
g/cm.sup.3, in some cases at least 1.6 g/cm.sup.3, in some cases at
least 1.8, in some cases at least 2.0 g/cm.sup.3 and in some cases
even more. The density of the lower-density elastomeric material 50
and/or the density of the higher-density elastomeric material 52
may have any other suitable value in other embodiments.
[0166] More particularly, in this embodiment, the lower-density
elastomeric material 50 is internal elastomeric material 54 of the
track 21 that is located away from a periphery 56 of the track 21
(i.e., the inner side 25, the ground-engaging outer side 27, and
lateral edges 55.sub.1, 55.sub.2 of the track 21), such as
elastomeric material 38 inside the carcass 35, elastomeric material
41 inside the traction projections 58.sub.1-58.sub.T, and/or
elastomeric material 42 inside the drive/guide lugs
34.sub.1-34.sub.D, while the higher-density elastomeric material 52
is peripheral elastomeric material 60 forming at least part of the
periphery 56 of the track 21, such as elastomeric material 62 of
the inner side 25 of the track 21, elastomeric material 64 of the
ground-engaging outer side 27 of the track 21, and/or elastomeric
material 68 of the lateral edges 55.sub.1, 55.sub.2 of the track
21. This may help to reduce the weight of the track 21 while
providing suitable wear resistance and/or other useful properties
in external regions of the track 21 that may be expected to wear
faster and/or be subject to other particular effects during
use.
[0167] In this embodiment, the elastomeric material 62 of the inner
side 25 of the track 21 comprises an elastomeric material of the
inner surface 32 of the carcass 35 and an elastomeric material of
an outer surface of the drive/guide lugs 34.sub.1-34.sub.D; the
elastomeric material 64 of the ground-engaging outer side 27 of the
track 21 comprises an elastomeric material of the ground-engaging
outer surface 31 of the carcass 35 and an elastomeric material 41
of an outer surface of the traction projections 58.sub.1-58.sub.T;
and the elastomeric material 38 inside the carcass 35 is part of
the internal elastomeric material 54 spaced from the inner surface
32 and the ground-engaging outer surface 31 of the carcass 35. In
this example, the internal elastomeric material 54 is thus
encapsulated in the elastomeric material 62, 64, 68 of the inner
side 25, the ground-engaging outer side 27 and the lateral edges
55.sub.1, 55.sub.2 of the track 21.
[0168] In this embodiment, a quantity of the internal elastomeric
material 54 is significant to allow this elastomeric material to
occupy more space within the track 21. For example, in some
embodiments, as shown in FIGS. 13A, 13B and 14, a thickness T.sub.q
of the internal elastomeric material 54 inside the carcass 35 may
occupy at least 20% of the thickness T.sub.c of the carcass 35, in
some cases at least 30% of the thickness T.sub.c of the carcass 35,
in some cases at least 40% of the thickness T.sub.c of the carcass
35, in some cases at least 50% of the thickness T.sub.c of the
carcass 35, and in some cases even more (e.g., 60%, 70% or more).
In this example of implementation, the thickness T.sub.q of the
internal elastomeric material 54 inside the carcass 35 occupies at
least a majority, in this case at least three-quarters, of the
thickness T.sub.c of the carcass 35. The thickness T.sub.q of the
internal elastomeric material 54 inside the carcass 35 may have any
other suitable value in other embodiments. As another example, in
some embodiments, a width W.sub.q of the internal elastomeric
material 54 inside the carcass 35 may occupy at least 20% of a
width W of the track 21 (measured between the lateral edges
55.sub.1, 55.sub.2 of the track 21), in some cases at least 30% of
the width W of the track 21, in some cases at least 40% of the
width W of the track 22, in some cases at least 50% of the width W
of the track 21, and in some cases even more (e.g., 60%, 70% or
more). In this example of implementation, the width W.sub.q of the
internal elastomeric material 54 inside the carcass 35 occupies at
least a majority, in this case at least three-quarters, of the
width W of the track 21. In this example, the internal elastomeric
material 54 inside the carcass 35 is constituted of a single
segment. In other embodiments, the internal elastomeric material 54
inside the carcass 35 may be constituted of separate segments
(e.g., two segments) such that its width W.sub.q corresponds to a
sum of a width of each of these separate segments. The width
W.sub.q of the internal elastomeric material 54 inside the carcass
35 may have any other suitable value in other embodiments. As yet
another example, in some embodiments, a weight of the internal
elastomeric material 54 inside the carcass 35 may constitute at
least 25% of a total weight of elastomeric material of the track
21, in some cases at least 30% of the total weight of elastomeric
material of the track 21, in some cases at least 35% of the total
weight of elastomeric material of the track 21, in some cases at
least 40% of the total weight of elastomeric material of the track
21, and in some cases even more.
[0169] This arrangement of the internal elastomeric material 54
inside the carcass 35 and the elastomeric material 62, 64, 68 of
the inner side 25, the ground-engaging outer side 27 and the
lateral edges 55.sub.1, 55.sub.2 of the track 21 may be achieved by
placing elastomeric components (e.g., sheets or other layers of
elastomeric material and/or blocks of elastomeric material
previously produced using any suitable process such as calendering,
molding, etc.) in a mold and consolidating them. Different
elastomeric compounds may be used in the inner side 25, the
ground-engaging outer side 27 and/or the lateral edges 55.sub.1,
55.sub.2 of the track 21 than inside the carcass 35 (e.g., rubber
compounds having different base polymers, different concentrations
and/or types of carbon black, and/or different contents of sulfur
or other vulcanizing agent).
[0170] The lower-density elastomeric material 50 may be implemented
in any suitable way in various embodiments.
[0171] For example, in some embodiments, the lower-density
elastomeric material 50 may be cellular elastomeric material (e.g.,
cellular rubber, a.k.a foam rubber or expanded rubber). The
cellular elastomeric material 50 is elastomeric material which
contains cells (e.g., bubbles) created by a foaming agent (e.g., a
gas (e.g., air) or a gas-producing agent (e.g., sodium
bicarbonate)) during manufacturing of the cellular elastomeric
material 50. The cells of the cellular elastomeric material 50 may
include closed cells and/or open cells.
[0172] For instance, the cellular elastomeric material 50 may be
expanded rubber (a.k.a. foam rubber).
[0173] The cellular elastomeric material 50 may be manufactured in
any suitable way. For instance, a foaming agent may be sprayed,
poured or molded with an elastomeric material (e.g., rubber) to
react with the elastomeric material in order to produce the
cellular elastomeric material 50. The foaming agent may be
azodicarbonamide (ADC), sulfonylhydrazides (OBSH, TSH and/or BSH),
silica, a suitable ceramic material or any other suitable foaming
agent.
[0174] The cellular elastomeric material 50 may be molded with the
higher-density elastomeric material 52 in any suitable way. For
instance, the cellular elastomeric material 50 may be molded in a
first mold and then inserted into a second mold where it is
overmolded by the higher-density elastomeric material 52.
[0175] In other embodiments, the cellular elastomeric material 50
may be molded together with the higher-density elastomeric material
52 via compression molding.
[0176] In this embodiment, the higher-density elastomeric material
52 is not cellular elastomeric material, i.e., it substantially
does not contain cells created by a foaming agent during its
manufacturing.
[0177] In other embodiments, both the lower-density elastomeric
material 50 and the higher-density elastomeric material 52 may be
cellular.
[0178] The lower-density elastomeric material 50 may constitute
other parts of the track 21 and/or may otherwise be provided in
different ways in the track 21 in other embodiments.
[0179] For example, in some embodiments, as shown in FIG. 15, in
addition to the lower-density elastomeric material 50, the track 21
may comprise a plurality of higher-density elastomeric materials
70.sub.1, 70.sub.2 that have different densities and that are
denser than the lower-density elastomeric material 50. For
instance, the higher-density elastomeric material 70.sub.1 may be
denser than the higher-density elastomeric material 70.sub.2 such
that the lower-density elastomeric material 50 and the
higher-density elastomeric material 70.sub.1 have a lowest and a
highest density respectively while the higher-density elastomeric
material 70.sub.2 has a medium density. The lower-density and the
higher density elastomeric materials 50, 70.sub.1, 70.sub.2 may be
arranged in any suitable way. For example, the lower-density and
the higher-density elastomeric materials 50, 70.sub.1, 70.sub.2 may
be arranged to form a density gradient. For instance, the
lower-density elastomeric material 50 may be an innermost
elastomeric material, the higher-density elastomeric material
70.sub.1 may be an outermost elastomeric material, and the
higher-density elastomeric material 70.sub.1 may be a middle
elastomeric material.
[0180] In some embodiments, as shown in FIG. 16, the lower-density
elastomeric material 50 may form part of the periphery 56 of the
track 21. For instance, in some cases, the lower-density
elastomeric material 50 may form part of the periphery 56 at the
inner side 25 of the track 21 since the inner side 25 of the track
21 is less exposed to wear than the outer side 27 of the track 21.
In some embodiments, the lower-density elastomeric material 50 may
form part of the periphery 56 of the track 21 at the outer side 27
of the track 21.
[0181] The lower-density elastomeric material 50 may constitute at
least a bulk of the elastomeric material of the track 21. For
instance, the lower-density elastomeric material 50 may constitute
at least a majority of the elastomeric material of the track 21. In
some embodiments, the lower-density elastomeric material 50 may
constitute an entirety of the elastomeric material of the track 21
(e.g., there is no higher-density elastomeric material).
[0182] In some embodiments, the lower-density elastomeric material
50 may comprise other types of material rather than cellular
elastomeric material. For instance, the lower-density elastomeric
material 50 may comprise any suitable low-density polymeric
material. For example, the lower-density elastomeric material 50
may comprise polypropylene, polyethylene or any other suitable
material.
1.3 Track with Few or No Slide Members (e.g., "Clips")
[0183] In some embodiments, as shown in FIG. 18, the track 21 may
have fewer or no slide member (e.g., "clips") such as the slide
members 39.sub.1-39.sub.S to slide against the sliding surfaces
77.sub.1, 77.sub.2 of the rails 44.sub.1, 44.sub.2 of the
track-engaging assembly 24.
[0184] For instance, in some embodiments, the track 21 may comprise
the slide members 39.sub.1-39.sub.S in a reduced number. In such
embodiments, longitudinally-adjacent ones of the slide members
39.sub.1-39.sub.S may be significantly spaced apart from one
another. More specifically, as shown in FIG. 19, a longitudinal
spacing J defined between longitudinally-adjacent ones of the slide
members 39.sub.1-39.sub.S may be large. For example, in some cases
the longitudinal spacing J may be at least one-fifth of the length
of the track 21, in some cases at least one-quarter of the length
of the track 21, in some cases at least one-third of the length of
the track 21, in some cases at least half of the length of the
track 21, and in some cases even more.
[0185] In some embodiments, the longitudinal spacing J defined
between longitudinally-adjacent ones of the slide members
39.sub.1-39.sub.S may be such that no more than a certain number of
slide members 39.sub.1-39.sub.S can contact a rail 44.sub.i at any
given instant. For example, in some cases, no more than three slide
members 39.sub.1-39.sub.S may contact the rail 44.sub.i at any
given instant, in some cases no more than two slide members
39.sub.1-39.sub.S may contact the rail 44.sub.i at any given
instant, and in some cases no more than one slide member
39.sub.1-39.sub.S may contact the rail 44.sub.i at any given
instant.
[0186] In other embodiments, the track 21 may be free of slide
members and thus may be referred to as a "clipless" track.
2. Different Traction Projections with Different Tractive
Effects
[0187] In some embodiments, as shown in FIG. 20, respective ones of
the traction projections 58.sub.1-58.sub.T may have different
characteristics (e.g., different shapes and/or different rigidity
characteristics) to generate different tractive effects on the
ground. For instance, this may allow the track 21 to perform well
in different ground conditions, such as different types of snow,
soil, etc.
[0188] For example, in this embodiment, longitudinally-successive
traction projections 58.sub.i-58.sub.k that succeed one another in
the longitudinal direction of the track 21 differ in height. In
this example, the height of the traction projection 58.sub.i (i.e.,
H.sub.1) is greater than the height of the traction projections
58.sub.j (i.e., H.sub.2), which is greater than the height of the
traction projection 58.sub.k (i.e., H.sub.3). This pattern may be
repeated over other longitudinally-successive ones of the traction
projections 58.sub.1-58.sub.T. For instance, this may allow the
traction projections 58.sub.1-58.sub.T to have different degrees of
engagement with the ground in different ground conditions.
[0189] In this embodiment, the longitudinally-successive traction
projections 58.sub.i-58.sub.k may have different rigidity
characteristics.
[0190] For instance, a taller one of the longitudinally-successive
traction projections 58.sub.i-58.sub.k (e.g., 58.sub.i) may
comprise an upper portion 72 that is more flexible than an upper
portion 74 of a lower one of the longitudinally-successive traction
projections 58.sub.i-58.sub.k (e.g., 58.sub.i). For example, a
modulus of elasticity of a material 76 of the upper portion 72 of
the traction projection 58.sub.i may be lower than a modulus of
elasticity of a material 78 of the upper portion 74 of the traction
projection 58.sub.i.
[0191] For instance, in some embodiments, a ratio of the modulus of
elasticity of the material 76 of the upper portion 72 of the
traction projection 58.sub.i over the modulus of elasticity of the
material 78 of the upper portion 74 of the traction projection
58.sub.i may be at least 1.5, in some cases at least 2, in some
cases at least 2.5, in some cases at least 3, and in some cases
even more.
3. Traction Projections Providing Enhanced Heat Management
[0192] In some embodiments, as shown in FIGS. 21 and 22, respective
ones of the traction projections 58.sub.1-58.sub.T may be
configured to allow the track 21 to better manage heat generated
within its elastomeric material as it moves around the
track-engaging assembly 24. Notably, this may reduce heat buildup
within the track 21 by allowing more heat to be transferred to the
track's environment.
[0193] For example, in some embodiments, a traction projection
58.sub.x may be designed such that a base 80 of the traction
projection 58.sub.x from which it projects from the carcass 35
leaves more of the ground-engaging outer surface 31 of the carcass
35 exposed to facilitate transfer of heat from the carcass 35 to
the track's environment. This may thus reduce heat buildup within
the carcass 35.
[0194] In this embodiment, the traction projection 58.sub.x
comprises a recessed space 82 that defines a recessed area 84 at
the base 80 of the traction projection 58.sub.x which leaves an
open area 86 of the ground-engaging outer surface 31 of the carcass
35 exposed. The recessed area 84 at the base 80 of the traction
projection 58.sub.x is delimited by an imaginary boundary 88 made
up of the base 80 of the traction projection 58.sub.x and straight
lines circumscribing the base 80 of the traction projection
58.sub.x.
[0195] The recessed area 84 at the base 80 of the traction
projection 58.sub.x may be significant in relation to a
cross-sectional area of the base 80 of the traction projection
58.sub.x. For example, in some embodiments, a ratio of the recessed
area 84 at the base 80 of the traction projection 58.sub.x over the
cross-sectional area of the base 80 of the traction projection
58.sub.x may be at least 30%, in some cases at least 40%, in some
cases at least 50%, in some cases at least 60%, in some cases at
least 70%, in some cases at least 80%, and in some cases even more.
This ratio may have any other suitable value in other
embodiments.
[0196] In this embodiment, the traction projection 58.sub.x
comprises narrow portions 90 and enlarged portions 92 that are
larger than the narrow portions 90 in the longitudinal direction of
the track 21. For instance, the narrow portions 90 may be walls
forming "paddles" and the enlarged portions 92 may be blocks
forming "columns".
[0197] In some embodiments, a ratio of a dimension of a narrow
portion 90 over a dimension of an enlarged portion 92 in the
longitudinal direction of the track 21 may be at least 0.05, in
some cases at least 0.1, in some cases at least 0.15, in some cases
at least 0.2 and in some cases even more (e.g., 0.25, 0.3, etc.).
Moreover, in some embodiments, a ratio of a dimension of a narrow
portion 90 over a dimension of an enlarged portion 92 in the
widthwise direction of the track 21 may be at least 1, in some
cases at least 1.5, in some cases at least 2, in some cases at
least 2.5 and in some cases even more (e.g., 3).
[0198] The recessed space 82 and the recessed area 84 at the base
80 of the traction projection 58.sub.x may be configured in any
other suitable way in other embodiments.
4. Enhancement Based on Spacing of Traction Projections
[0199] In some embodiments, as shown in FIG. 5, a longitudinal
spacing S.sub.t of adjacent traction projections 58.sub.i, 58.sub.j
(i.e., a spacing of the adjacent traction projections 58.sub.i,
58.sub.j in the longitudinal direction of the track 21), which can
be referred to as a "pitch" of the adjacent traction projections
58.sub.i, 58.sub.j, may be used to improve a performance of the
track 21.
[0200] For example, in some embodiments, as shown in FIG. 23, the
pitch S.sub.t of the adjacent traction projections 58.sub.i,
58.sub.j may be greater than a longitudinal spacing S.sub.i of
adjacent drive/guide lugs 34.sub.i, 34.sub.j (i.e., a spacing of
the adjacent drive/guide lugs 34.sub.i, 34.sub.j in the
longitudinal direction of the track 21), which can be referred to
as a "pitch" of the adjacent drive/guide lugs 34.sub.i, 34.sub.j.
For instance, in some embodiments, a ratio of the pitch S.sub.t of
the adjacent traction projections 58.sub.i, 58.sub.j over the pitch
S.sub.i of the adjacent drive/guide lugs 34.sub.i, 34.sub.j may be
at least 1.2, in some cases at least 1.5, in some cases at least 2,
in some cases at least 3, and in some cases even more. This ration
may have any other suitable value in other embodiments.
[0201] In some examples of implementation, the pitch S.sub.t of the
adjacent traction projections 58.sub.i, 58.sub.j may be such that
at least two of the holes (i.e., windows) 40.sub.1-40.sub.H of the
track 21 that succeed one another in the longitudinal direction of
the track 21 are disposed between the adjacent traction projections
58.sub.i, 58.sub.j.
[0202] Moreover, in some examples of implementation, the pitch
S.sub.t of the adjacent traction projections 58.sub.i, 58.sub.j may
be such that at least two of the reinforcements 45.sub.x of the
track 21 that succeed one another in the longitudinal direction of
the track 21 are disposed between the traction projections
58.sub.i, 58.sub.j.
[0203] In some embodiments, as shown in FIG. 24, the pitch S.sub.t
of adjacent ones of the traction projections 58.sub.1-58.sub.T may
vary in the longitudinal direction of the track 21 such that the
pitch S.sub.t of the adjacent traction projections 58.sub.i,
58.sub.j is different from the pitch S.sub.t of adjacent traction
projections 58.sub.m, 58.sub.n.
[0204] For instance, in some embodiments, a ratio of the pitch
S.sub.t of the adjacent traction projections 58.sub.i, 58.sub.j
over the pitch S.sub.t of adjacent traction projections 58.sub.m,
58.sub.n may be at least 1, in some cases at least 1.5, in some
cases at least 2, and in some cases even more.
[0205] In some embodiments, certain ones of the traction
projections 58.sub.1-58.sub.T may be misaligned with respect to one
another in the widthwise direction of the track 21. For instance,
certain ones of the traction projections 58.sub.1-58.sub.T may not
overlap with one another in the widthwise direction of the track
21. For example, certain traction projections 58.sub.1-58.sub.T may
be "side" traction projections 58.sub.1-58.sub.T that are disposed
substantially to a side of the track 21 in the widthwise direction
of the track 21 while other ones of the traction projections
58.sub.1-58.sub.T may be "center" traction projections
58.sub.1-58.sub.T that are disposed substantially centrally of the
track 21 in the widthwise direction of the track 21. A pitch of the
side traction projections may be different from a pitch of the
center traction projections. For example, a ratio of the pith of
the side traction projections over the pitch of the center traction
projections may be no more than 0.9, in some cases no more than
0.8, in some cases no more than 0.7, and in some cases even less.
This ratio may have any suitable value in other embodiments.
5. Enhanced Resistance to Lateral Skidding
[0206] In some embodiments, as shown in FIGS. 25 and 26, the
ground-engaging outer side 27 of the track 21 may be configured to
oppose a tendency of the track 21 to skid sideways (i.e.,
laterally) when the snowmobile 10 is travelling in a given
direction, such as, for example, when the snowmobile 10 is
travelling on (e.g., crossing) a slope terrain 94 like a side hill
or other inclined ground area.
[0207] For example, in some embodiments, the ground-engaging outer
side 27 of the track 21 may comprise lateral stabilizers
96.sub.1-96.sub.n projecting from the ground-engaging outer surface
31 to oppose a tendency of the track 21 to skid transversely to a
direction of motion of the snowmobile 10. In this embodiment, each
of the lateral stabilizers 96.sub.1-96.sub.n comprises elastomeric
material 98. The lateral stabilizers 96.sub.1-96.sub.n can be
provided and connected to the carcass 35 in the mold during the
track's molding process.
[0208] Where the snowmobile 10 travels such that there is a
tendency of the track 21 to skid sideways to the snowmobile's
direction of motion, such as on the slope terrain 94, the lateral
stabilizers 96.sub.1-96.sub.n generate lateral forces that oppose
the tendency of the track 21 to skid sideways. This may facilitate
keeping the snowmobile 10 in its direction of motion on the slope
terrain 94.
[0209] In this embodiment, the lateral stabilizers
96.sub.1-96.sub.n are located adjacent to the lateral edges
55.sub.1, 55.sub.2 of the track 21. In this example, the lateral
stabilizers 96.sub.1-96.sub.n are located at longitudinal ends of
respective ones of the traction projections 58.sub.1-58.sub.T.
[0210] In this embodiment, as shown in FIG. 27, each lateral
stabilizer 96.sub.i is elongated transversally to the widthwise
direction of the track 21. More particularly, the lateral
stabilizer 96.sub.i has a longitudinal axis 67 that is transversal
to the widthwise direction of the track 21 and defines its length
L.sub.S, a width W.sub.L normal to its longitudinal axis 67, and a
height H.sub.S in the thickness direction of the track 21. In this
example, the longitudinal axis 67 of the lateral stabilizer
96.sub.i is substantially normal to the widthwise direction of the
track 21, i.e., substantially parallel to the longitudinal
direction of the track 21.
[0211] In this embodiment, the lateral stabilizer 96.sub.i
protrudes, in the longitudinal direction, beyond a traction
projection 58.sub.x at the end of which it is located. As such, the
length L.sub.S of the lateral stabilizer 96.sub.i is greater than a
front-to-rear dimension L.sub.L of the traction projection
58.sub.x. For example, in some cases a ratio L.sub.S/L.sub.L of the
length of the lateral stabilizer 96.sub.i to the front-to-rear
dimension L.sub.L of the traction projection 58.sub.x may be at
least 1.2, in some cases at least 1.3, in some cases at least 1.4,
in some cases at least 1.5, and in some cases even more (e.g., 2 or
more).
[0212] The lateral stabilizers 96.sub.1-96.sub.n are arranged to
occupy a significant part of a gap G.sub.T in the longitudinal
direction of the track 21 between adjacent ones of the traction
projections 58.sub.1-58.sub.T. For instance, in this embodiment,
adjacent lateral stabilizers 96.sub.i, 96.sub.j occupy a
significant part of the gap G.sub.T between adjacent traction
projections 58.sub.i, 58.sub.j. For example, the lateral
stabilizers 96.sub.i, 96.sub.j occupy at least a majority of the
gap G.sub.T between the traction projections 58.sub.i, 58.sub.j, in
some cases at least two-thirds the gap G.sub.T between the traction
projections 58.sub.i, 58.sub.j, in some cases at least
three-quarters of the gap G.sub.T between the traction projections
58.sub.i, 58.sub.j, and in some cases even more (e.g., up to an
entirety of the gap G.sub.T between the traction projections
58.sub.i, 58.sub.j).
[0213] In a variant, with additional reference to FIG. 28, a single
lateral stabilizer 96.sub.i may occupy at least majority of the gap
G.sub.T between the traction projections 58.sub.i, 58.sub.j, in
some cases at least two-thirds the gap G.sub.T between the traction
projections 58.sub.i, 58.sub.j, in some cases at least
three-quarters of the gap G.sub.T between the traction projections
61.sub.i, 61.sub.j, and in some cases even more (e.g., up to an
entirety of the gap G.sub.T between the traction projections
61.sub.i, 61.sub.j).
[0214] In a variant, with additional reference to FIG. 29, the
lateral stabilizers 96.sub.1-96.sub.n may be disposed at the
longitudinal ends of selected ones of the traction projections
58.sub.1-58.sub.T, i.e., the lateral stabilizers 96.sub.1-96.sub.n
may not be disposed at the longitudinal ends of each traction
projection 58.sub.i. For instance, the lateral stabilizers may be
distributed in the longitudinal direction of the track 21 such that
a pitch of the lateral stabilizers (i.e., a spacing between
adjacent lateral stabilizers 96.sub.i, 96.sub.j is different than
the pitch S.sub.t of the traction projections 58.sub.1-58.sub.T. In
this example, the lateral stabilizers 96.sub.1-96.sub.n are
disposed at longitudinal ends of every second traction projection
58.sub.i in the longitudinal direction of the track 21. In other
words, the pitch of the lateral stabilizers is twice the pitch
S.sub.t of the traction projections 58.sub.1-58.sub.T. In other
words, a ratio of the pitch of the lateral stabilizers
96.sub.1-96.sub.n over the pitch S.sub.t of the traction
projections 58.sub.1-58.sub.T may be at least 1, in some cases at
least 2, in some cases at least 3, in some cases at least 4, and in
some cases even more.
[0215] In another variant, with additional reference to FIG. 30, a
lateral stabilizer 96.sub.i may be located away from the lateral
edges 55.sub.1, 55.sub.2 of the track 21. For instance, the lateral
stabilizer 96.sub.i may be located remote from the longitudinal
ends of the traction projections 58.sub.1-58.sub.T. For example,
the lateral stabilizer 96.sub.i may be located in a center region
of the track 21 (i.e., a center region in the widthwise direction
of the track 21). More particularly, in this example, the lateral
stabilizer 96.sub.i is located in a center third of the width W of
the track 21.
[0216] In another variant, with additional reference to FIG. 31,
the track 21 may comprise any number of lateral stabilizers
96.sub.1-96.sub.n that are spaced apart in the widthwise direction
of the track 21 but overlapping in the longitudinal direction of
the track 21. For instance, while the embodiment of FIG. 26 shows
two lateral stabilizers 96.sub.i, 96.sub.j that are spaced apart in
the widthwise direction of the track 21 and overlapping in the
longitudinal direction of the track 21, in this variant, the track
21 may comprise at least three lateral stabilizers
96.sub.1-96.sub.n that are spaced apart in the widthwise direction
of the track 21 and overlapping in the longitudinal direction of
the track 21. In some cases, the track 21 may comprise more lateral
stabilizers 96.sub.1-96.sub.n (e.g., four) that are spaced apart in
the widthwise direction of the track 21 and overlapping in the
longitudinal direction of the track 21.
[0217] In yet another variant, a lateral stabilizer 96.sub.i may be
located between successive ones of the traction projections
58.sub.1-58.sub.T in the longitudinal direction of the track 21.
For example, as shown in FIG. 32, each lateral stabilizer 96.sub.i
may be located between successive ones of the traction projections
58.sub.1-58.sub.T in the longitudinal direction of the track 21
such that lateral stabilizers 96.sub.i, 96.sub.j that are spaced
apart in the widthwise direction of the track 21 and overlapping in
the longitudinal direction of the track 21 do not overlap with a
traction projection 58.sub.i in the longitudinal direction of the
track 21.
[0218] In some embodiments, as shown in FIG. 33, the
ground-engaging outer side 27 of the track 21 may comprise uneven
surfaces 102.sub.1-102.sub.U that project from the ground-engaging
outer surface 31 and have a texture 104 to oppose a tendency of the
track 21 to skid transversely to the direction of motion of the
snowmobile 10. The uneven surfaces 102.sub.1-102.sub.U of the
ground-engaging outer side 27 of the track 21 may be part of the
traction projections 58.sub.1-58.sub.T and/or the lateral
stabilizers 96.sub.1-96.sub.n, if present. For instance, the uneven
surfaces 102.sub.1-102.sub.U may be part of a lateral surface
(i.e., a surface facing transversally of the longitudinal direction
of the track system 14) of the traction projections
58.sub.1-58.sub.T and/or the lateral stabilizers 96.sub.1-96.sub.n.
For example, the uneven surfaces 102.sub.1-102.sub.U may be part of
an outer lateral surface of a traction projections 58.sub.i (i.e.,
a lateral surface of a traction projections 58.sub.i that is
closest to a lateral edge 55.sub.i of the track 21). Moreover, in
some examples, as shown in FIG. 34, the uneven surfaces
102.sub.1-102.sub.U may be part of an outer lateral surface of a
lateral stabilizer 96.sub.i (i.e., a lateral surface of a lateral
stabilizer 96.sub.i that is closest to a lateral edge 55.sub.i of
the track 21).
[0219] The texture 104 comprises a plurality of formations
106.sub.1-106.sub.F that increase friction to oppose a tendency of
the track 21 to skid transversely to the direction of motion of the
snowmobile 10. More particularly, the formations
106.sub.1-106.sub.F provide an increased number of ground-engaging
faces on the lateral surfaces of the traction projections
58.sub.1-58.sub.T and/or the lateral stabilizers 96.sub.1-96.sub.n
such that the traction projections 58.sub.1-58.sub.T and/or the
lateral stabilizers 96.sub.1-96.sub.n have an increased frictional
engagement with the ground to oppose a tendency of the track 21 to
skid transversely to the direction of motion of the snowmobile
10.
[0220] The formations 106.sub.1-106.sub.F may be configured in
various ways in various embodiments.
[0221] For instance, in some embodiments, as shown in FIG. 35A, the
formations 106.sub.1-106.sub.F may be configured in a step-like
manner such that the formations form steps 108.sub.1-108.sub.S in
an ascending manner from a bottom portion to a top portion of the
traction projection 58.sub.i. In other embodiments, as shown in
FIGS. 35B and 35C, the formations 106.sub.1-106.sub.F may be
configured to form projections 110.sub.1-110.sub.P. The projections
110.sub.1-110.sub.F may have any suitable shape. For instance, the
projections 110.sub.1-110.sub.F may have a rectangular shape (as
shown in FIG. 35B), a rounded shape, a triangular shape (as shown
in FIG. 35C) or any other suitable shape. In yet other embodiments,
as shown in FIG. 35D, the formations 106.sub.1-106.sub.F may be
configured to form recesses 112.sub.1-112.sub.M.
[0222] The formations 106.sub.1-106.sub.F may be configured
differently in other embodiments. For instance, the formations
106.sub.1-106.sub.F may be spaced evenly from one another as shown
in FIGS. 35A to 35D or, alternatively, the formations
106.sub.1-106.sub.F may be unevenly spaced from one another such
that a pitch defined between successive ones of the formations
106.sub.1-106.sub.F varies. Moreover, the formations
106.sub.1-106.sub.F may extend along only a portion of the height
of the traction projection 58.sub.i and/or a height of the lateral
stabilizer 96.sub.i. For example, as shown in FIG. 37, the
formations 106.sub.1-106.sub.F may extend along a top portion 107
of the traction projection 58.sub.i while a bottom portion 109 of
the traction projection 58.sub.i may not comprise any of the
formations 106.sub.1-106.sub.F. The top portion 107 of the traction
projection 58.sub.i may correspond to at least 10% of a height H of
the traction projection 58.sub.i, in some cases at least 30%, in
some cases at least 50%, in some cases at least 60%, and in some
cases even more (e.g., 70%). In a similar manner, the formations
106.sub.1-106.sub.F may extend along a top portion of the lateral
stabilizer 96.sub.i.
[0223] In a variant, the uneven surfaces 102.sub.1-102.sub.U may be
able to bend. More specifically, as shown in FIG. 38, an uneven
surface 102.sub.i extending along the top portion 107 of the
traction projection 58.sub.i may bend relative to the bottom
portion 109 of the traction projection 58.sub.i. This may be useful
to further oppose the tendency of the track 21 to skid due to a
sloped terrain. For instance, this may enhance a grabbing action of
the uneven surface 102.sub.i with the ground.
[0224] In another variant, with additional reference to FIGS. 79 to
81, a traction projection 58i may comprise a plurality of lateral
stabilizers 296.sub.1-296.sub.S configured to increase a lateral
restrictive force exerted by the traction projection 58.sub.i. The
traction projections 58.sub.1-58.sub.T comprising the lateral
stabilizers 296.sub.1-296.sub.S may be disposed in a staggered
arrangement on the ground-engaging outer side 27 of the track 21.
In other words, at least a majority of (i.e., a majority or an
entirety of) a given traction projection 58.sub.i may be offset
from an adjacent traction projection 58.sub.j (i.e., may not
overlap the adjacent traction projection 58.sub.j) in the widthwise
direction of the track 21.
[0225] Considering a cross-section of the traction projection
58.sub.i normal to the thickness direction of the track 21, a
dimension D.sub.1 of each lateral stabilizer 296.sub.i in the
longitudinal direction of the track 21 is greater than a dimension
D.sub.2 of the lateral stabilizer 296.sub.i in the widthwise
direction of the track 21. For instance, in some embodiments, a
ratio of the dimension D.sub.1 of the lateral stabilizer 296.sub.i
over the dimension D.sub.2 of the lateral stabilizer 296.sub.i may
be at least 3, in some cases at least 4, in some cases at least 5,
and in some cases even more (e.g., 6).
[0226] The number of lateral stabilizers 296.sub.1-296.sub.S per
traction projection 58.sub.i may be significant. For instance, in
some embodiments, the traction projection 58.sub.i may comprise at
least three lateral stabilizers 296.sub.1-296.sub.S, in some cases
at least four lateral stabilizers 296.sub.1-296.sub.S, in some
cases at least five lateral stabilizers 296.sub.1-296.sub.S, and in
some cases even more (e.g., six or more).
[0227] In this example, the traction projection 58.sub.i also
comprises a plurality of propulsive protrusions 298.sub.1-298.sub.P
configured to propel the snowmobile 10 and disposed between
adjacent ones of the lateral stabilizers 296.sub.1-296.sub.S. The
propulsive protrusions 298.sub.1-298.sub.P are longer in the
widthwise direction of the track 21 than the lateral stabilizers
296.sub.1-296.sub.S. That is, a dimension D.sub.3 of a propulsive
protrusion 298.sub.i in the widthwise direction of the track 21 is
greater than the dimension D.sub.2 of a lateral stabilizer
296.sub.i.
[0228] The propulsive protrusions 298.sub.1-298.sub.P may be shaped
to improve traction by causing the traction projection 58i to
contain snow or other ground matter on which the track 21 travels,
as will be further discussed later. For instance, the propulsive
protrusions 298.sub.1-298.sub.P may be shaped to create a
"scooping" effect of the traction projection 58.sub.i on the snow
or other ground matter on which the track 21 travels. To that end,
in this embodiment, the propulsive protrusions 298.sub.1-298.sub.P
are curved or otherwise shaped to respectively form a plurality of
recesses 300.sub.1-300.sub.P in which snow or other ground matter
may be more easily accumulated by the traction projection 58i. For
instance, in some examples, a recess 300.sub.i of a propulsive
protrusion 298.sub.i may be shaped such that propulsive protrusion
298.sub.i implements a "scoop" or "cup" to scoop or cup the snow or
other ground matter. In particular, in this example, the propulsive
protrusions 298.sub.1-298.sub.P are curved along a plane that is
normal to the height direction of the track 21. For example, each
of the propulsive protrusions 298.sub.1-298.sub.P may be U-shaped,
V-shaped or shaped in any other suitable manner such as to form the
recesses 300.sub.1-300.sub.P.
[0229] In some embodiments, selected ones of the propulsive
protrusions 298.sub.1-298.sub.P may be curved or otherwise shaped
to form the recesses 300.sub.1-300.sub.P, while other ones of the
propulsive protrusions 298.sub.1-298.sub.P may not be curved (e.g.,
flat). In other embodiments, all of the propulsive protrusions
298.sub.1-298.sub.P may not be curved (e.g., flat).
[0230] The traction projection 58.sub.i comprising the lateral
stabilizers 296.sub.1-296.sub.S and the propulsive protrusions
298.sub.1-298.sub.P may have a significant height HT. For instance,
in some embodiments, the height HT of the traction projection
58.sub.i may be at least 1.5 inches, in some cases at least 1.75
inches, in some cases at least 2 inches, and in some cases even
more (e.g., 2.5 or 3 inches). Such a configuration of the traction
projection 58.sub.i may be particularly useful in a mountainous
environment as lateral forces exerted on the track 21 may be more
significant.
[0231] Furthermore, in this example of implementation, as shown in
FIG. 81, the traction projection 58.sub.i comprises a flap 302 that
can deflect (e.g., bend) in response to a lateral force to increase
a surface area of the traction projection 58.sub.i that is
transversal to the widthwise direction of the track 21.
[0232] The flap 302 has a deflected state and an undeflected state.
In its undeflected state, the flap 302 is positioned transversally
to the longitudinal direction of the track 21 while in its
deflected state, the flap 302 is positioned transversally to the
widthwise direction of the track 21. In its undeflected state, a
surface area of the flap 302 transversal to the widthwise direction
of the track 21 is smaller than in the deflected state of the flap
302.
[0233] The flap 302 protrudes from a given lateral stabilizer
296.sub.i in a direction transverse to the longitudinal direction
of the track 21. The flap 302 may be disposed on an inner side of
the traction projection 58.sub.i (i.e., a side of the traction
projection 58.sub.i that is closest to a center of the track 21) or
on an outer side of the traction projection 58.sub.i (i.e., a side
of the traction projection 58.sub.i that is closest to a given one
of the lateral edges 55.sub.1, 55.sub.2 of the track 21).
[0234] In this example, the flap 302 tapers in the height direction
of the track 21. More specifically, a top portion of the flap 302
has a greater extent in a direction transverse to the longitudinal
direction of the track 21 than a bottom portion of the flap 302
such that an extent of the flap 302 in a direction transverse to
the longitudinal direction of the track 21 decreases downwardly
from the top portion of the flap 302. Moreover, in this example,
the flap 302 is in contact with the ground-engaging outer surface
31 of the track 21. In other examples, the flap 302 may not be in
contact with the ground-engaging outer surface 31 and may instead
be solely in contact with the lateral stabilizer 296.sub.i. The
flap 302 may be configured differently in other examples.
6. Traction Projections Configured to Contain Snow or Other Ground
Matter
[0235] In some embodiments, as shown in FIGS. 79 to 85, a traction
projection 58.sub.i may be configured to contain snow or other
ground matter from the ground to enhance traction. That is, the
traction projection 58.sub.i comprises a containment space 304 to
contain an amount of snow or other ground matter when the traction
projection 58.sub.i engages the ground. This may help to compact
the amount of snow or other ground matter contained in the traction
projection 58.sub.i and thus allow the traction projection 58.sub.i
to press more on the compacted snow or other ground matter, thereby
generating greater tractive forces. For instance, the containment
space 304 of the traction projection 58.sub.i may create a
"scooping" or "cupping" action to scoop or cup the snow or other
ground matter. The scooping or cupping action may further be
amplified when the traction projection 58i deforms as it engages
the snow or other ground matter and causes the containment space
304 to expand.
[0236] The containment space 304 of the traction projection
58.sub.i may be sized such that the amount of snow or other ground
matter it can contain may be relatively significant, as this may
further improve traction.
[0237] In this embodiment, the containment space 304 of the
traction projection 58.sub.i comprises a plurality of containment
voids 306.sub.1-306.sub.4 to contain respective portions of the
amount of snow or other ground matter contained by the traction
projection 58.sub.i. More particularly, in this embodiment, the
traction projection 58.sub.i comprises the propulsive protrusions
298.sub.1-298.sub.P and each of the containment voids
306.sub.1-306.sub.4 is implemented by a respective one of the
recesses 300.sub.1-300.sub.P defined by the propulsive protrusions
298.sub.1-298.sub.P.
[0238] In this example, the recesses 300.sub.1-300.sub.P
implementing the containment voids 306.sub.1-306.sub.4 are
distributed in a longitudinal direction of the traction projection
58.sub.i, which in this case corresponds to the widthwise direction
of the track 21. This allows the traction projection 58.sub.i to
contain the snow or other ground matter over a significant part of
the length L of the traction projection 58.sub.i.
[0239] For instance, in some embodiments, the containment space 304
of the traction projection 58.sub.i may occupy at least a majority
(e.g., a majority or an entirety) of the length L of the traction
projection 58.sub.i. For example, in some embodiments, the
containment space 304 of the traction projection 58.sub.i may
occupy at least 60%, in some cases at least 70%, in some cases at
least 80%, in some cases at least 90%, and in some cases an
entirety of the length L of the traction projection 58.sub.i.
[0240] In this regard, in this embodiment, each of the recesses
300.sub.1-300.sub.P of the containment space 304 of the traction
projection 58.sub.i may occupy a significant part of the length L
of the traction projection 58.sub.i. For example, in some
embodiments, a recess 300.sub.i of the containment space 304 of the
traction projection 58.sub.i may occupy at least 10%, in some cases
at least 15%, in some cases at least 20%, in some cases at least
25%, and in some cases an even larger part of the length L of the
traction projection 58.sub.i.
[0241] The containment space 304 of the traction projection
58.sub.i may therefore be viewed as imparting an "effective" length
L.sub.eff of the traction projection 58.sub.i that exceeds the
(actual) length L of the traction projection 58.sub.i. Basically,
the traction projection 58.sub.i may be viewed as generating more
traction as if it was effectively longer. The effective length
L.sub.eff of the traction projection 58.sub.i can be measured by
measuring a line that follows a shape of the traction projection
58.sub.i from the first longitudinal end 308.sub.1 of the traction
projection 58.sub.i to the second longitudinal end 308.sub.2 of the
traction projection 58.sub.i. Conceptually, this can be viewed as
that length the traction projection 58.sub.i would have if it was
straightened by straightening segments that are non-straight in the
longitudinal direction of the traction projection 58.sub.i (which
in this case corresponds to the widthwise direction of the track
21), i.e., the propulsive protrusions 298.sub.1-298.sub.P defining
the recesses 300.sub.1-300.sub.P in this example, such that they
are straight in the longitudinal direction of the traction
projection 58.sub.i.
[0242] For instance, in some embodiments, a ratio L.sub.eff/L of
the effective length L.sub.eff of the traction projection 58.sub.i
over the length L of the traction projection 58.sub.i may be at
least 1.1, in some cases at least 1.2, in some cases at least 1.3,
in some cases at least 1.4, and in some cases even more.
[0243] Also, in this embodiment, the containment space 304 of the
traction projection 58.sub.i may occupy at least a majority (e.g.,
a majority or an entirety) of the height H of the traction
projection 58.sub.i. For example, in some embodiments, the
containment space 304 of the traction projection 58.sub.i may
occupy at least 60%, in some cases at least 70%, in some cases at
least 80%, in some cases at least 90%, and in some cases an
entirety of the height H of the traction projection 58.sub.i.
[0244] In this example of implementation, this may be particularly
useful as the height H of traction projection 58.sub.i is
relatively significant. For instance, in some embodiments, the
height H of the traction projection 58.sub.i may be at least 1.5
inches, in some cases at least 1.75 inches, in some cases at least
2 inches, and in some cases even more (e.g., 2.5 or 3 inches).
[0245] In this regard, in this embodiment, each of the recesses
300.sub.1-300.sub.P of the containment space 304 of the traction
projection 58.sub.i may occupy at least a majority of the height H
of the traction projection 58.sub.i. For example, in some
embodiments, a recess 300.sub.i of the containment space 304 of the
traction projection 58.sub.i may occupy at least 60%, in some cases
at least 70%, in some cases at least 80%, in some cases at least
90%, and in some cases an entirety of the height H of the traction
projection 58.sub.i.
[0246] The amount of snow or other ground matter that can be
contained in the containment space 304 of the traction projection
58.sub.i may thus be significant. This can be measured as a volume
V of the containment space 304 of the traction projection 58.sub.i
in which the amount of snow or other ground matter can be
contained. For instance, in some embodiments, the volume V of the
containment space 304 of the traction projection 58.sub.i may be at
least 0.8 in.sup.3, in some cases at least 1 in.sup.3, in some
cases at least 1.2 in.sup.3, in some cases at least 1.4 in.sup.3
and in some cases even more. For instance, in some cases, a ratio
V/L of the volume V of the containment space 304 over the length L
of the traction projection 58.sub.i may be at least 0.3
in.sup.3/in, in some cases at least 0.5 in.sup.3/in, in some cases
at least 0.8 in.sup.3/in, and in some cases even more.
[0247] In this embodiment, as shown in FIG. 83, the volume V of the
containment space 304 of the traction projection 58.sub.i
corresponds to a sum of volumes v.sub.1-v.sub.4 of the recesses
300.sub.1-300.sub.P that can contain the snow or other ground
matter. In this example, a volume v.sub.i of a recess 300.sub.i may
be relatively significant. For instance, in some embodiments, the
volume v.sub.i of the recess 300.sub.i may be at least at least
10%, in some cases at least 15%, in some cases at least 20%, in
some cases at least 25%, and in some cases an even larger part of
the volume V of the containment space 304 of the traction
projection 58.sub.i.
[0248] The propulsive protrusions 298.sub.1-298.sub.P defining the
recesses 300.sub.1-300.sub.P of the containment space 304 of the
traction projection 58.sub.i may be shaped in any suitable way. In
this embodiment, each propulsive protrusion 298.sub.i is curved to
define its recess 300.sub.i. More particularly, in this embodiment,
the propulsive protrusion 298.sub.i is generally U-shaped such that
its recess 300.sub.i is also U-shaped. The recess 300.sub.i is open
facing the ground as the traction projection 58.sub.i approaches
the ground while the track 21 moves around the track-engaging
assembly 24 when the snowmobile 10 travels forward.
[0249] In this example of implementation, the traction projection
58.sub.i, including the propulsive protrusions 298.sub.1-298.sub.P
and the lateral stabilizers 296.sub.1-296.sub.S, tapers in the
thickness direction of the track 21. That is, a top portion 310 of
the traction projection 58.sub.i has a smaller cross-sectional area
than a bottom portion 312 of the traction projection 58.sub.i
adjacent to the outer surface 31 of the carcass 35. This may help
to strengthen the traction projection 58.sub.i given its height and
its containment space 304 which are relatively significant.
[0250] More particularly, in this example of implementation, the
top portion 310 of the traction projection 58.sub.i is smaller in
the longitudinal direction of the track 21 than the bottom portion
312 of the traction projection 58.sub.i. In this case, a top
portion 314 of each lateral stabilizer 296.sub.i is smaller in the
longitudinal direction of the track 21 than a bottom portion 316 of
the lateral stabilizer 296.sub.i, while a top portion 318 of each
propulsive protrusion 298.sub.i is smaller in the longitudinal
direction of the track 21 than a bottom portion 320 of the
propulsive protrusion 298.sub.i.
[0251] For instance, in some embodiments, a ratio of a dimension
D.sub.1-b of the bottom portion 316 of the lateral stabilizer
296.sub.i in the longitudinal direction of the track 21 over a
dimension D.sub.1-t of the top portion 314 of the lateral
stabilizer 296.sub.i in the longitudinal direction of the track 21
may be at least 1.1, in some cases at least 1.2, in some cases at
least 1.5, and in some cases even more (e.g., 2), and/or a ratio of
a dimension D.sub.4-b of the bottom portion 320 of the propulsive
protrusion 298.sub.i in the longitudinal direction of the track 21
over a dimension D.sub.4-t of the top portion 318 of the propulsive
protrusion 298.sub.i in the longitudinal direction of the track 21
may be at least 1.1, in some cases at least 1.2, in some cases at
least 1.5, and in some cases even more (e.g., 2).
[0252] Also, in some embodiments, the dimension D.sub.1-t of the
top portion 314 of the lateral stabilizer 296.sub.i may be
significantly greater than the dimension D.sub.4-t of the top
portion 318 of the propulsive protrusion 298.sub.i. For instance,
in some cases, a ratio D.sub.1-t/D.sub.4-t of the dimension
D.sub.1-t of the top portion 314 of the lateral stabilizer
296.sub.i over the dimension D.sub.4-t of the top portion 318 of
the propulsive protrusion 298.sub.i may be at least 2, in some
cases at least 3, in some cases at least 4 and in some cases even
more. This significant difference between the dimensions D.sub.1-t
and D.sub.4-t may allow the containment space 304 of the traction
projection 58.sub.i to be bigger and thus compact more snow or
other ground matter.
[0253] FIGS. 86 to 89 show a similar embodiment in which at least
one of the traction projections 58.sub.1-58.sub.T of the track 21
is configured to contain snow or other ground matter from the
ground to enhance traction. The containment space 304 in this
embodiment is reduced due to a smaller size of the propulsive
protrusions 298.sub.1-298.sub.P.
[0254] Furthermore, as shown in FIG. 89, in some embodiments, a
traction projection 58.sub.i may comprise a strengthener 315 for
reinforcing a given one of the propulsive protrusions
298.sub.1-298.sub.P. The strengthener 315 is positioned such as to
face away from the ground as the traction projection 58.sub.i
approaches the ground while the track 21 moves around the
track-engaging assembly 24 when the snowmobile 10 travels forward.
In other words, the strengthener 315 is disposed on a side of the
traction projection 58.sub.i that is opposite to the recesses
300.sub.1-300.sub.P of the containment space 304 of the traction
projection 58.sub.i. The strengthener 315 is disposed adjacent to a
propulsive protrusion 298.sub.i in the longitudinal direction of
the track 21 such as to reinforce the propulsive protrusion
298.sub.i when the propulsive protrusion 298.sub.i engages the
ground. This may help minimize wear of the traction projection
58.sub.i. In this embodiment, the strengthener 315 comprises an
elongated rib that extends in the height direction of the track 21.
A height of the strengthener 315 may be significant. For instance,
the height of the strengthener 315 may be equal to a majority or an
entirety of the height H of the traction projection 58.sub.i. In
this embodiment, the strengthener 315 is integral with the
remainder of the traction projection 58.sub.i such that it is
formed together with the traction projection 58.sub.i.
[0255] The strengthener 315 may be configured in other ways in
other embodiments. For instance, the strengthener 315 may be shaped
differently or its height may be less than a majority of the height
H of the traction projection 58.sub.i.
[0256] Furthermore, a given traction projection 58.sub.i may
comprise more than one strengthener 315. Notably, in this example
of implementation, the traction projection 58.sub.i comprises two
strengtheners 315, each strengthener 315 being configured to
reinforce a respective propulsive protrusion 298.sub.i. Thus, in
some embodiments, each propulsive protrusion 298.sub.i may be
associated with a corresponding strengthener 315, or one or more of
the propulsive protrusions 298.sub.1-298.sub.P may be free of a
strengthener 315.
7. Adaptable Track
[0257] In some embodiments, as shown in FIG. 39, one or more
components of the track 21 (e.g., the traction projections
58.sub.1-58.sub.T, the carcass 35, the drive/guide lugs
34.sub.1-34.sub.D) may be adaptable in response to a stimulus
(e.g., temperature, humidity, loading, a signal, etc.) such that a
state of a given component of the track 21 (e.g., a stiffness or
other property; a shape; and/or any other characteristic of the
given component of the track) is variable in different conditions
(e.g., weather conditions; ground conditions, such as different
types of snow, soil, etc.; and/or other conditions) in order to
better perform in specified conditions.
7.1 Adaptable Traction Projections
[0258] In some embodiments, as shown in FIG. 40, respective ones of
the traction projections 58.sub.1-58.sub.T may be adaptable in
response to a stimulus (e.g., temperature, humidity, loading, a
signal, etc.) such that a state of a traction projection 58.sub.i
(e.g., a stiffness, hardness, or other property; a shape; and/or
any other characteristic of the traction projection 58.sub.i) is
variable in different conditions (e.g., weather conditions; ground
conditions, such as different types of snow, soil, etc.; and/or
other conditions) in order to better perform in specified
conditions. For example, in some embodiments, the traction
projection 58.sub.i may be less stiff (e.g., softer) and/or less
straight (e.g., bent) in powder snow (or other looser matter on the
ground) than in wet snow (or other denser matter on the
ground).
7.1.1 Adaptable Stiffness
[0259] In some embodiments, as shown in FIG. 41, a stiffness of a
traction projection 58.sub.i may be adaptable in response to a
stimulus such that the traction projection 58.sub.i is stiffer in a
first condition than in a second condition. That is, the stiffness
of the traction projection 58.sub.i changes based on the
stimulus.
[0260] For instance, in some embodiments, the stiffness of the
traction projection 58.sub.i may change based on a stimulus
associated with an environmental parameter of an environment of the
traction projection 58.sub.i.
[0261] For example, the stiffness of the traction projection
58.sub.i may be lower when the traction projection 58.sub.i is in
powder snow (or other looser matter on the ground) than when the
traction projection 58.sub.i is in wet/spring snow (or other denser
matter on the ground). Wet/spring snow is defined here as snow with
a humidity of more than 3%.
[0262] More specifically, a ratio of the stiffness of the traction
projection 58.sub.i in powder snow over the stiffness of the
traction projection 58.sub.i in wet/spring snow may be at least
1.1, in some cases at least 1.2, in some cases at least 1.3, in
some cases at least 1.5, in some cases at least 2, and in some
cases even more (e.g., 3 or more).
[0263] In some embodiments, the stiffness of the traction
projection 58.sub.i may be lower when the humidity of the
environment of the traction projection 58.sub.i is lower. For
example, the stiffness of the traction projection 58.sub.i may be
lower when the humidity of the snow that the traction projection
58.sub.i engages is lower.
[0264] For instance, a ratio of the stiffness of the traction
projection 58.sub.i when the humidity has a given value over the
stiffness of the traction projection 58.sub.i when the humidity has
a lower value than the given value may be at least 1.1, in some
cases at least 1.2, in some cases at least 1.3, in some cases at
least 1.5, in some cases at least 2, and in some cases even more
(e.g., 3 or more).
[0265] In some embodiments, the stiffness of the traction
projection 58.sub.i may be lower when a temperature of the
environment of the traction projection 58.sub.i is lower.
[0266] For instance, a ratio of the stiffness of the traction
projection 58.sub.i when the temperature has a given value over the
stiffness of the traction projection 58.sub.i when the temperature
has a lower value than the given value may be at least 1.1, in some
cases at least 1.2, in some cases at least 1.3, in some cases at
least 1.5, in some cases at least 2, and in some cases even more
(e.g., 3 or more).
[0267] In some cases, the stiffness of the traction projection
58.sub.i may be lower when snow (or other matter on the ground)
that the traction projection 58.sub.i engages is softer. For
instance, the stiffness of the traction projection 58.sub.i may be
lower when loading (e.g., impacts) on the traction projection
58.sub.i is lower.
[0268] For instance, a ratio of the stiffness of the traction
projection 58.sub.i when the snow (or other matter on the ground)
that the traction projection 58.sub.i engages has a given hardness
over the stiffness of the traction projection 58.sub.i when the
snow (or other matter on the ground) that the traction projection
58.sub.i engages has a lower hardness may be at least 1.1, in some
cases at least 1.2, in some cases at least 1.3, in some cases at
least 1.5, in some cases at least 2, and in some cases even more
(e.g., 3 or more). The difference in hardness of the snow (or other
matter on the ground) that the traction projection 58.sub.i engages
over which this ratio may apply may be no more than a certain
value.
[0269] The stiffness of the traction projection 58.sub.i may be
observed in any suitable way in various embodiments.
[0270] For example, a material 114 of the traction projection
58.sub.i may vary in stiffness. For instance, a modulus of
elasticity of the material 114 of the traction projection 58.sub.i
may vary based on the stimulus.
[0271] More particularly, a ratio of the modulus of elasticity of
the material 114 of the traction projection 58.sub.i in the first
condition over the modulus of elasticity of the material 114 of the
traction projection 58.sub.i in the second condition may be at
least 2, in some cases at least 3, in some cases at least 4, and in
some cases even more (e.g., 4.5 or more). For instance, the modulus
of elasticity may be Young's modulus or the 100% modulus for the
material 114 of the traction projection 58.sub.i.
[0272] In some embodiments, a hardness of the material 114 of the
traction projection 58.sub.i may vary based on the stimulus.
[0273] For instance, a ratio of the hardness of the material 114 of
the traction projection 58.sub.i in the first condition over the
hardness of the material 114 of the traction projection 58.sub.i in
the second condition may be at least 1.1, in some cases at least
1.2, in some cases at least 1.3, in some cases at least 1.5, in
some cases at least 2, and in some cases even more (e.g., 3 or
more).
[0274] The material 114 of the traction projection 58.sub.i may be
any suitable material. For example, in some embodiments, as shown
in FIG. 42, the material 114 may be the rubber 41 of the traction
projection 58.sub.i. In other embodiments, as shown in FIG. 43 the
material 114 may interface with the rubber 41 of the traction
projection 58.sub.i. That is, the traction projection 58.sub.i may
comprise an adaptable member 116 that includes the material 114 and
that interfaces with the rubber 41 of the traction projection
58.sub.i. The adaptable member 116 may be at least partially
embedded in the rubber 41 of the traction projection 58.sub.i. For
example, the adaptable member 116 may be a core within the rubber
41 of the traction projection 58.sub.i.
[0275] In some embodiments, as shown in FIG. 44, the adaptable
member 116 may be at an outer surface of the rubber 41 of the
traction projection 58.sub.i. For example, the adaptable member 116
may be a cover of the traction projection 58.sub.i that covers the
rubber 41 of the traction projection 58.sub.i.
[0276] The adaptable member 116 and its material 114 may be
provided in the traction projection 58.sub.i in any suitable way.
For instance, in embodiments in which the adaptable 116 is at least
partially embedded within the rubber 41 of the traction projection
58.sub.i, the adaptable member 116 may be formed in a first molding
operation and then overmolded by the rubber 41 of the traction
projection 58.sub.i in a subsequent molding operation. Conversely,
in embodiments in which the adaptable member 116 at the outer
surface of the rubber 41 of the traction projection 58.sub.i, the
rubber 41 may be formed in a first molding operation and then
overmolded by the material 114 to form the adaptable member that
covers the rubber 41 in a subsequent molding operation.
[0277] The adaptability of the stiffness of the traction projection
58.sub.i may be implemented in any suitable way.
[0278] In some embodiments, the material 114 may have a property
related to the stiffness, such as its modulus of elasticity and/or
hardness, that varies considerably over a range of values of the
stimulus to which the traction projection 58.sub.i is expected to
be exposed during use.
[0279] For instance, in some embodiments, the property related to
the stiffness of the material 114 may vary considerably over a
range of temperatures to which the traction projection 58.sub.i is
expected to be exposed during use. For example, the property
related to the stiffness of the material 114 may vary between 0 and
-30.degree. C., in some cases between 0 and -20.degree. C., and in
some cases between 0 and -10.degree. C.
[0280] In some embodiments, the property related to the stiffness
of the material 114 may vary considerably over a range of humidity
to which the traction projection 58.sub.i is expected to be exposed
during use. For example, the property related to the stiffness of
the material 114 may vary between 0% and 1% humidity, in some cases
between 0% and 2% humidity, in some cases between 0% and 3%
humidity, in some cases between 0% and 4% humidity, and in some
cases between 0% and 5% humidity.
[0281] In some embodiments, the material 114 may be a
rate-dependent material. That is, the property related to the
stiffness of the material 114 (e.g., modulus of elasticity and/or
hardness of the material 114) may vary based on a rate of change of
a force applied on the traction projection 58.sub.i. For example,
the material 114 may comprise a rate-dependent foam that is
characterized as possessing a load-response behavior that resists
sudden-movement rapid compression, yet is less resistive to
slow-movement compression.
[0282] Furthermore, in some embodiments, the material 114 may be a
non-Newtonian material (i.e., a non-Newtonian fluid) having a
viscosity that is dependent on shear rate or shear rate
history.
7.1.2 Adaptable Shape
[0283] In some embodiments, as shown in FIG. 45, a shape of a
traction projection 58.sub.i may be adaptable in response to a
stimulus such that the shape of the traction projection 58.sub.i is
different in a first condition than in a second condition. That is,
the shape of the traction projection 58.sub.i changes based on the
stimulus. This change in shape of the traction projection 58.sub.i
is distinct from any change in shape of the traction projection
58.sub.i that may occur when the traction projection 58.sub.i
contacts the ground and ceases to contact the ground.
[0284] For instance, the shape of the traction projection 58.sub.i
may have a greater "packing" effect and/or "scooping" effect in
powder snow than in wet/spring snow. For example, the shape of the
traction projection 58.sub.i may be less straight (e.g., bent) in
powder snow (or other looser matter on the ground) than in
wet/spring snow (or other denser matter on the ground). This may
allow an improved floatation of the track 21 on powder snow.
[0285] More particularly, as shown in FIG. 46, an angle
.theta..sub.1 between a portion 118 of the traction projection
58.sub.i and the height direction of the track 21 may be different
in powder snow than in wet/spring snow. For instance, the angle
.theta..sub.1 may be greater in powder snow than wet/spring snow.
For example, a ratio of .theta..sub.1 in powder snow over
.theta..sub.1 in wet/spring snow may be at least 1.1, in some cases
at least 1.2, in some cases at least 1.3, in some cases at least
1.5, in some cases at least 2, and in some cases even more (e.g., 3
or more).
[0286] In some cases, the portion 118 of the traction projection
58.sub.i may be substantially vertical or nearly vertical (i.e.,
the angle .theta..sub.1 may be or be close to 0.degree.) in
wet/spring snow. In other cases, the portion 118 of the traction
projection 58.sub.i may be inclined in wet/spring snow, but may be
more inclined in powder snow.
[0287] For example, in wet/spring snow, the angle .theta..sub.1 may
be no more than 30.degree., in some cases no more than 20.degree.,
in some cases no more than 10.degree., and in some cases 0.degree.,
while, in powder snow, the angle .theta..sub.1 may be at least
30.degree., in some case at least 40.degree., in some cases at
least 50.degree., and in some cases even more.
[0288] In some embodiments, as shown in FIG. 47, an angle .