U.S. patent application number 16/614001 was filed with the patent office on 2020-03-12 for loader working device.
The applicant listed for this patent is Guangxi LiuGong Machinery Co., Ltd.. Invention is credited to Mingzhi Lin, Edward Wagner, Xuan Xiao, Jinxia Yang.
Application Number | 20200080279 16/614001 |
Document ID | / |
Family ID | 62866543 |
Filed Date | 2020-03-12 |
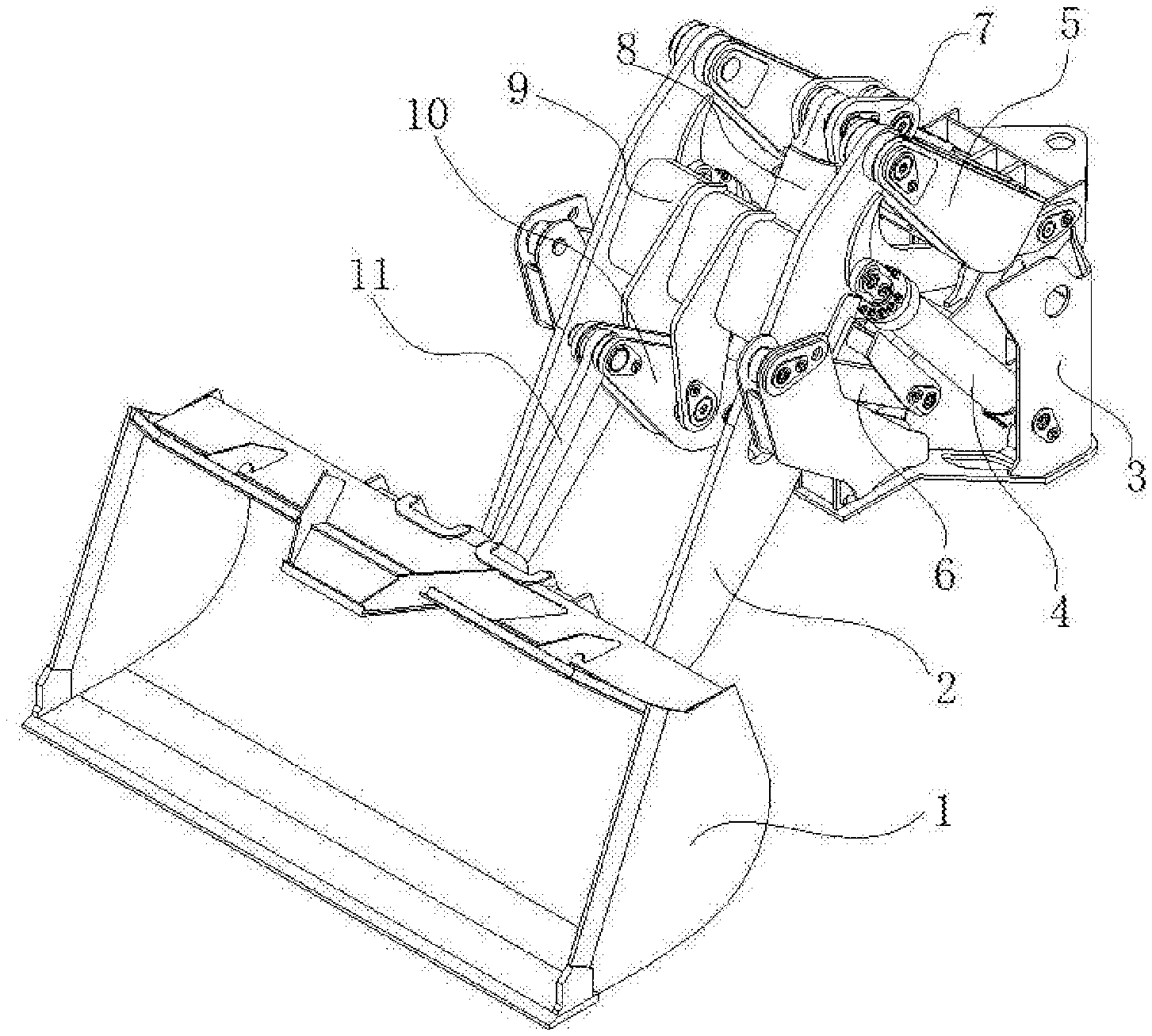
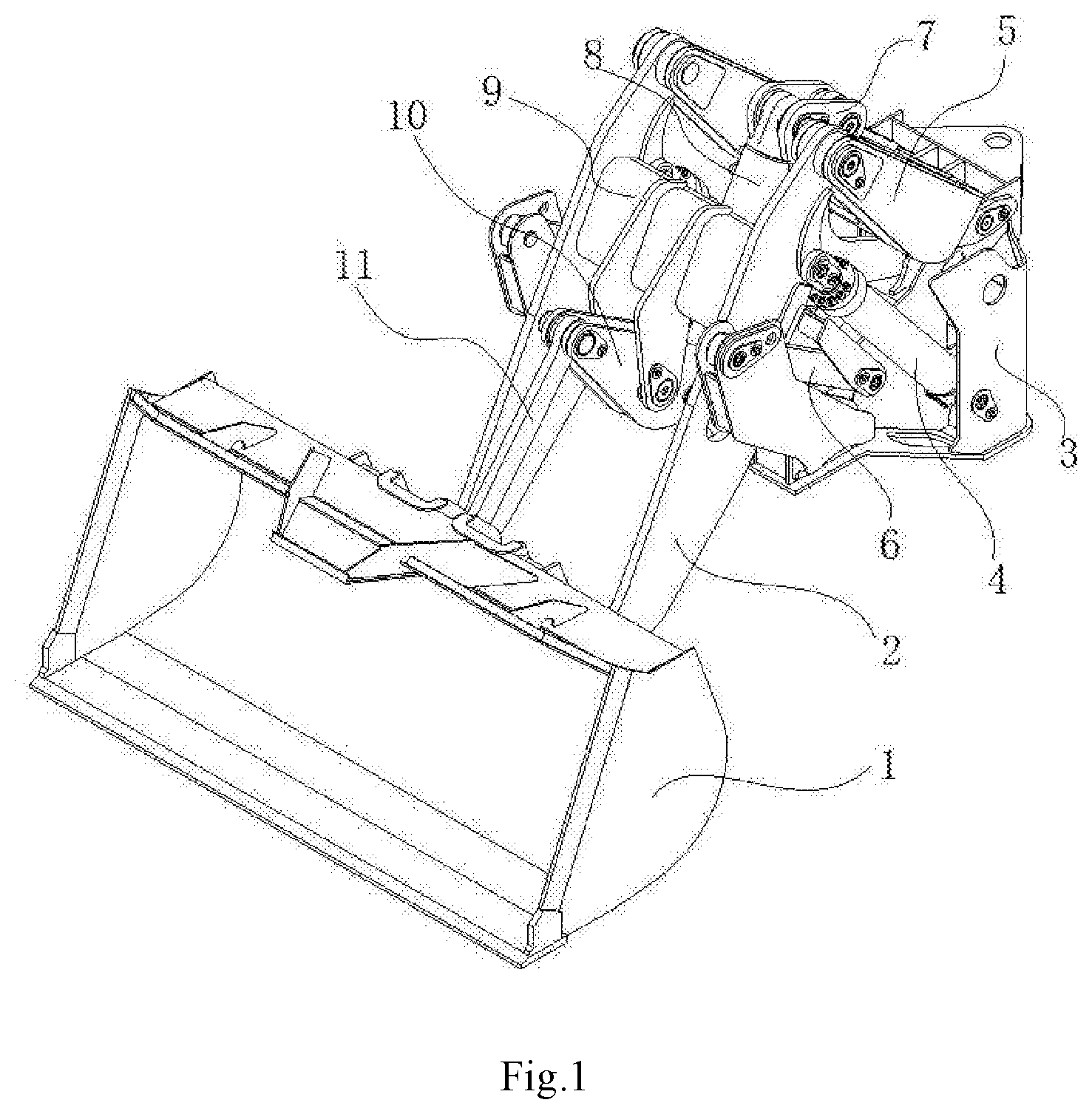
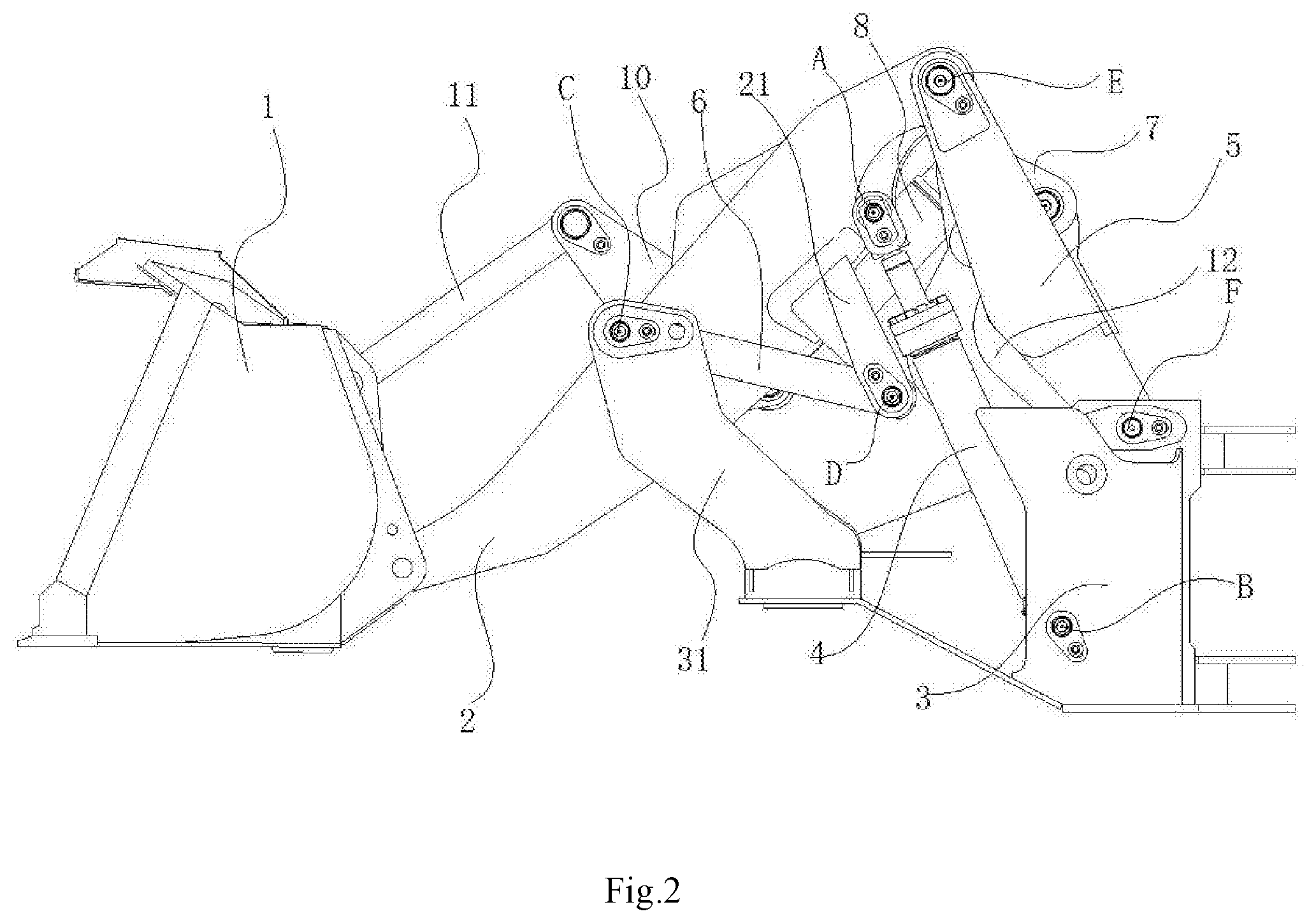
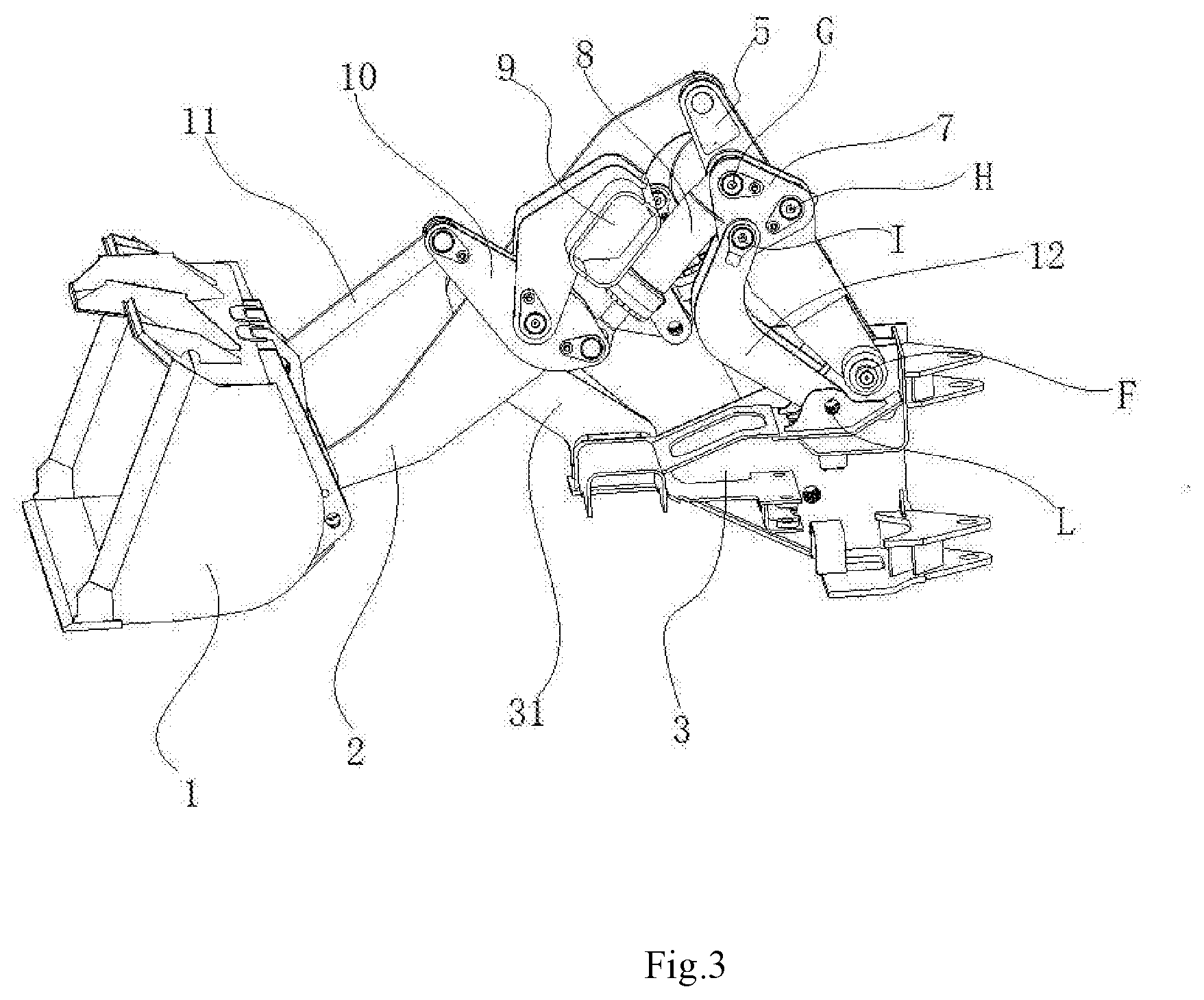
United States Patent
Application |
20200080279 |
Kind Code |
A1 |
Yang; Jinxia ; et
al. |
March 12, 2020 |
Loader Working Device
Abstract
The disclosure relates to a loader working device for solving
the problem of arranging the parts used in a vertical lifting
mechanism of an existing loader. The loader working device
comprises an accessory, an accessory overturning mechanism, and an
accessory lifting mechanism including a movable arm, a movable arm
oil cylinder, a front link rod and a rear link rod. The accessory
lifting mechanism does not cause the accessory to interfere with a
rocker arm and a front axle package of the loader working device. A
connecting and mounting point of the movable arm and the accessory
can be moved backwardly, thus improving a digging force and a
tilting load at a low position of the loader working device.
Inventors: |
Yang; Jinxia; (Liuzhou,
Guangxi, CN) ; Lin; Mingzhi; (Liuzhou, Guangxi,
CN) ; Xiao; Xuan; (Liuzhou, Guangxi, CN) ;
Wagner; Edward; (Liuzhou, Guangxi, CN) |
|
Applicant: |
Name |
City |
State |
Country |
Type |
Guangxi LiuGong Machinery Co., Ltd. |
Liuzhou Guangxi |
|
CN |
|
|
Family ID: |
62866543 |
Appl. No.: |
16/614001 |
Filed: |
January 25, 2019 |
PCT Filed: |
January 25, 2019 |
PCT NO: |
PCT/CN2019/073111 |
371 Date: |
November 15, 2019 |
Current U.S.
Class: |
1/1 |
Current CPC
Class: |
E02F 3/283 20130101;
E02F 3/3408 20130101; E02F 3/38 20130101; E02F 3/342 20130101; E02F
3/422 20130101; E02F 3/431 20130101; E02F 9/0841 20130101; E02F
3/42 20130101; E02F 3/3405 20130101 |
International
Class: |
E02F 3/42 20060101
E02F003/42; E02F 3/34 20060101 E02F003/34 |
Foreign Application Data
Date |
Code |
Application Number |
Jan 26, 2018 |
CN |
201810076343.4 |
Claims
1. A loader working device, comprising: a front frame, wherein a
front end of the front frame is provided with a support; an
accessory; an accessory lifting mechanism connected between the
accessory and the front frame, wherein the accessory lifting
mechanism is symmetrical left and right about a central plane, and
wherein the accessory lifting mechanism comprises: a movable arm on
each of a left side and a right side of the accessory lifting
mechanism, wherein a movable arm beam is fixedly connected between
the movable arms; and a movable arm oil cylinder on each of the
left side and the right side of the accessory lifting mechanism,
wherein one end of the movable arm oil cylinder is hinged to a
point A on one of the movable arms, and wherein another end of the
movable arm oil cylinder is hinged to a point B on the front frame;
an accessory overturning mechanism connected between the accessory
and the front frame; a front link rod, wherein a front end of the
front link rod is hinged to a point C on the support, and wherein a
rear end of the front link rod is hinged to a point D on one of the
movable arms; and a rear link rod, wherein an upper end of the rear
link rod is hinged to a point E at the rear end of one of the
movable arms, and wherein a lower end of the rear link rod is
hinged to a point F on the front frame; wherein: a convex
quadrilateral is formed by connecting lines between projection
points of the points A, E, F, and D on the central plane; the
connecting lines between projection points of the points C, E, and
D on the central plane form a triangle; and a projection point of
the point D is located below a connecting line of the projection
points of the point C and the point E.
2. The loader working device according to claim 1, wherein the
movable arm is provided with a front link rod hinge arm extending
downwardly, wherein the rear end of the front link rod is hinged to
a lower end of the front link rod hinge arm, and wherein the front
link rod hinge arm is located between the movable arm oil cylinder
and the support at the front end of the front frame.
3. The loader working device according to claim 1, wherein: the
accessory overturning mechanism comprises a pulling rod, a rocker
arm, an overturning oil cylinder, a three-hinge point holder, and a
self-leveling link rod; rear link rods at the left side and the
right side are connected into an H shape by a middle beam; a middle
portion of the rocker arm is hinged to the movable arm beam; an
upper end of the rocker arm is hinged to a rear end of the pulling
rod; a front end of the pulling rod is hinged to the accessory; a
lower end of the rocker arm is hinged to a front end of the
overturning oil cylinder; a rear end of the overturning oil
cylinder is hinged to a point G of the three-hinge point holder; a
point H of the three-hinge point holder is hinged to the middle
beam; a point I of the three-hinge point holder is hinged to an
upper end of the self-leveling link rod; a lower end of the
self-leveling link rod is hinged to a point L on the front frame;
the point G is located above the point I; and the point H is
located at a rear side of a connecting line between the point G and
the point I.
4. The loader working device according to claim 2, wherein: the
accessory overturning mechanism comprises a pulling rod, a rocker
arm, an overturning oil cylinder, a three-hinge point holder and a
self-leveling link rod; rear link rods at the left side and the
right side are connected into an H shape by a middle beam; a middle
portion of the rocker arm is hinged to the movable arm beam; an
upper end of the rocker arm is hinged to a rear end of the pulling
rod; a front end of the pulling rod is hinged to the accessory; a
lower end of the rocker arm is hinged to a front end of the
overturning oil cylinder; a rear end of the overturning oil
cylinder is hinged to a point G of the three-hinge point holder; a
point H of the three-hinge point holder is hinged to the middle
beam; a point I of the three-hinge point holder is hinged to an
upper end of the self-leveling link rod; a lower end of the
self-leveling link rod is hinged to a point L on the front frame;
the point G is located above the point I; and the point H is
located at a rear side of a connecting line between the point G and
the point I.
5. The loader working device according to claim 3, wherein
connecting lines of the point G, the point H, and the point I of
the three-hinge point holder form an equilateral triangle.
6. The loader working device according to claim 3, wherein
connecting lines between projection points of the point I, the
point H, the point F, and the point L on the central plane form a
parallelogram.
7. The loader working device according to claim 5, wherein the
self-leveling link rod is L-shaped, and wherein an upper section
thereof is bent backwardly.
8. The loader working device according to claim 3, wherein the
overturning oil cylinder is located below the movable arm beam.
Description
TECHNICAL FIELD
[0001] The present disclosure relates to a working device, and more
particularly, to a vertically lifted loader working device.
BACKGROUND
[0002] A working device is one of important components on a
construction machinery loader, and different functions of a whole
machine can be realized through different working device
mechanisms. At present, a common working device mechanism of the
loader includes a six-link rod mechanism and an eight-link rod
mechanism. The biggest market share is the six-link rod mechanism,
but this type of working device mechanism has the problem that a
tilting ability of the whole machine is insufficient, the increase
of tilting will lead to an increase in the weight of the whole
machine, the insufficient ease of operation and an increase in oil
consumption of the whole machine. With the improvement of technical
ability of the loader, the vertical lifting mechanism solves this
problem well, the vertical lifting mechanism has a short load
moment arm in a lifting process, which can realize a larger tilting
load with smaller weight of the whole machine and make the
operation process of the whole machine more stable. At the same
time, due to the short load moment arm, useless work in the lifting
process of the working device is reduced, and the lifting ability
of the working device is stronger. The currently used vertical
lifting mechanism realizes all operation functions of the loader
through three sets of four-link rod mechanisms, compared with other
link mechanisms, the vertical lifting mechanism uses more parts,
which are arranged in the middle of the working device with limited
arrangement space. At present, an inverted bucket mechanism used in
vertical lifting, an overturning oil cylinder is connected to an
upper hinge point of a rocker arm and a short link rod, with a high
mounting position, which affects the visual field before operation.
At the same time, the arrangement structure of the bucket mechanism
is compact, at present, the arrangement requirements of the rocker
arm are met through compressing a stroke of the overturning oil
cylinder and changing an external structure of a bucket, for
example, an opening angle of the bucket and a receiving angle of
the bucket of the working device are reduced to meet the mechanism
requirements, which affects the bucket performance and the
operation performance of the working device to a certain extent,
thus resulting in poor bucket filling rate, and the bucket needs to
avoid the front hinge point of the rocker arm, making the bucket
structure complicated.
SUMMARY
[0003] The technical problem to be solved by the present disclosure
is to provide a loader working device for vertical lifting aiming
at the problem that a vertical lifting mechanism of existing loader
uses more parts, which are arranged in the middle of the working
device and have limited arrangement space.
[0004] The technical solution of the present disclosure to achieve
the purpose thereof is as follows: a loader device is arranged,
which comprises an accessory, an accessory lifting mechanism
connected between the accessory and a front frame of the loader,
and an accessory overturning mechanism, wherein the accessory
lifting mechanism is symmetrical left and right about a central
plane, and comprises a movable arm and a movable arm oil cylinder
on left and right sides; one end of the movable arm oil cylinder is
hinged to a point A on the movable arm, the other end is hinged to
a point B on the front frame, and a movable arm beam is fixedly
connected between the two movable arms; the loader working device
further comprises a front link rod and a rear link rod; a front end
of the front frame is provided with a support;
[0005] a front end of the front link rod is hinged to a point C on
the support, and a rear end of the front link rod is hinged to a
point D on the movable arm;
[0006] an upper end of the rear link rod is hinged to a point E at
the rear end of the movable arm, and a lower end is hinged to a
point F on the front frame; and
[0007] a convex quadrilateral is formed by connecting lines between
projection points of the hinge points A, E, F and D on a central
plane; the connecting lines between projection points of the hinge
points C, E and D on the central plane form a triangle, and a
projection point of the point D is located below the connecting
line of the projection points of the point C and the point E. In
the present disclosure, the accessory lifting mechanism is formed
by superposing two four-link rods to realize vertical lifting, and
a first four-link rod mechanism consisting of the movable arm, the
rear link rod, the front frame and the movable arm oil cylinder
realizes a lifting movement of the movable arm; and a second
four-link rod consisting of the movable arm, the front link rod,
the front frame and the movable arm oil cylinder realizes
horizontal restraint in a lifting process, so that a distance
between the accessory and a front wheel is basically kept unchanged
in the lifting process, so as to realize vertical lifting. In the
present disclosure, the accessory can be a loader bucket, a pallet
fork or a holding fork, etc.
[0008] Preferably, in the loader working device above, the movable
arm is provided with a front link rod hinge arm extending
downwardly, the rear end of the front link rod is hinged to a lower
end of the front link rod hinge arm, and the front link rod hinge
arm is located between the movable arm oil cylinder and the support
at the front end of the front frame.
[0009] Preferably, in the loader working device above, the
accessory overturning mechanism comprises a pulling rod, a rocker
arm, a overturning oil cylinder, a three-hinge point holder and a
self-leveling link rod; the rear link rods at left and right sides
are connected into an H shape by a middle beam, a middle portion of
the rocker arm is hinged to the movable arm beam, an upper end of
the rocker arm is hinged to a rear end of the pulling rod, a front
end of the pulling rod is hinged to the accessory, a lower end of
the rocker arm is hinged to a front end of the overturning oil
cylinder, a rear end of the overturning oil cylinder is hinged to a
G hinge point of the three-hinge point holder, an H hinge point of
the three-hinge point holder is hinged to the middle beam, an I
hinge point of the three-hinge point holder is hinged to an upper
end of the self-leveling link rod, a lower end of the self-leveling
link rod is hinged to an L hinge point on the front frame, the G
hinge point is located above the I hinge point, and the H hinge
point is located at a rear side of a connecting line between the G
hinge point and the I hinge point. Preferably, a forward Z-shaped
six-link rod consisting of the accessory, the pulling rod, the
rocker arm, the movable arm, the overturning oil cylinder and the
three-hinge point holder at the front end of the accessory
overturning mechanism realizes an overturning action of the
accessory, and controls an overturning angle of the accessory and a
digging force of the accessory. The overturning oil cylinder can be
mounted at the lower end of the rocker arm, and the pulling rod can
be mounted at the upper end of the rocker arm, thus reducing a
mounting height of the overturning oil cylinder and improving a
front visual field. Meanwhile, an overturning movement direction of
the accessory is consistent with a movement direction of the rocker
arm, which is beneficial to increasing the overturning angle of the
accessory. Preferably, a four-link rod mechanism consisting of the
three-hinge point holder, the self-leveling link rod, the rear link
rod and the front frame at the rear end of the accessory
overturning mechanism realizes automatic leveling in an accessory
overturning process, which is intended to solve the problem of
asynchronous angle turnover of the lifting mechanism and the
accessory overturning mechanism, and the four-link rod structure at
the rear end controls the change of the accessory overturning angle
in the lifting process of the lifting mechanism, so that the change
of the accessory angle relative to the ground is smaller. The
three-hinge point holder skillfully solves the connection problem
of the overturning oil cylinder, the rear link rod and the
self-leveling link rod, and reduces the assembly difficulty.
[0010] Preferably, in the loader working device above, connecting
lines of the G hinge point, the H hinge point and the I hinge point
of the three-hinge point holder form an equilateral triangle.
[0011] Preferably, in the loader working device above, connecting
lines between projection points of the I hinge point, the H hinge
point, the F hinge point and the L hinge point on a central plane
form a parallelogram.
[0012] Preferably, in the loader working device above, the
self-leveling link rod is L-shaped, and an upper section thereof is
bent backwardly.
[0013] Preferably, in the loader working device above, the
overturning oil cylinder is located below a movable arm beam.
[0014] Compared with the prior art, the forward overturning
mechanism is used in the vertical lifting mechanism according to
the present disclosure, the overturning movement direction of the
rocker arm is consistent with that of the accessory, the
overturning oil cylinder can be arranged at the lower end of the
rocker arm, and the pulling rod can be connected to the upper end
of the rocker arm, so that the overturning oil cylinder moves
downwardly, the working field at the front end of the working
device is improved, and better operation performance is provided
for the user. According to the present disclosure, the forward
accessory overturning mechanism used in the vertical lifting
mechanism does not cause the accessory to interfere with the rocker
arm and the front axle package, and the connecting and mounting
point of the movable arm and the accessory can be moved backwardly,
thus being beneficial to improving the digging force and the
tilting load at the low position of the working device. The
mechanism has the self-leveling link rod to ensure little change in
the angle of the accessory during lifting. The rear link rod, the
overturning oil cylinder and the self-leveling link rod can be
connected and mounted by adopting the three-hinge point holder,
thus greatly reducing the assembly difficulty and improving the
assembly efficiency.
BRIEF DESCRIPTION OF THE DRAWINGS
[0015] FIG. 1 is a structural diagram of a loader working device
according to the present disclosure.
[0016] FIG. 2 is a side view of the loader working device according
to the present disclosure.
[0017] FIG. 3 is a sectional view of the loader working device
according to the present disclosure.
DETAILED DESCRIPTION
[0018] The detailed embodiment is described with reference to the
drawings.
[0019] As shown in FIG. 1 and FIG. 2, a loader working device in
the embodiment is a loader bucket working device, which comprises
an accessory bucket, a bucket lifting mechanism connected between
the bucket and a front frame of the loader, and a bucket
overturning mechanism, wherein the bucket lifting mechanism is
symmetrical left and right about a vertical central plane, and
comprises a movable arm 2, a movable arm oil cylinder 4, a front
link rod 6 and a rear link rod 5 on left and right sides; and the
two movable arms 2 are fixedly connected by a movable arm beam 9. A
front end of the front frame 3 is provided with a support 31. One
end of the movable arm oil cylinder 4 is hinged to a point A on the
movable arm 2, and the other end is hinged to a point B on the
front frame 3; a front end of the front link rod 6 is hinged to a
point C on the support 31, the movable arm 2 is provided with a
front link rod hinge arm 21 extending downwardly, a rear end of the
front link rod 6 is hinged to a lower end of the front link rod
hinge arm 21, and the hinge point is a point D. An upper end of the
rear link rod 5 is hinged to a point E at the rear end of the
movable arm, and a lower end is hinged to a point F on the front
frame. A convex quadrilateral is formed by connecting lines between
projection points of the hinge points A, E, F and D on a central
plane; the connecting lines between projection points of the hinge
points C, E and D on the central plane form a triangle, a
projection point of the point D is located below the connecting
line of the projection points of the point C and the point E, and
the hinge point D is located between the movable arm oil cylinder 4
and the support 31 of the front frame at the front end.
[0020] As shown in FIG. 3, a bucket overturning mechanism comprises
a pulling rod 11, a rocker arm 10, an overturning oil cylinder 8, a
three-hinge point holder 7 and a self-leveling link rod 12; the
rear link rods at left and right sides are connected into an H
shape by a middle beam, a middle portion of the rocker arm 10 is
hinged to the movable arm beam 9, an upper end of the rocker arm 10
is hinged to a rear end of the pulling rod 11, a front end of the
pulling rod 11 is hinged to the bucket 1, a lower end of the rocker
arm 10 is hinged to a front end of the overturning oil cylinder 8,
a rear end of the overturning oil cylinder 8 is hinged to a G hinge
point of the three-hinge point holder 7, an H hinge point of the
three-hinge point holder 7 is hinged to the middle beam, an I hinge
point of the three-hinge point holder 7 is hinged to an upper end
of the self-leveling link rod 12, a lower end of the self-leveling
link rod 12 is hinged to an L hinge point on the front frame 3, the
G hinge point is located above the I hinge point, and the H hinge
point is located at a rear side of a connecting line between the G
hinge point and the I hinge point. Connecting lines of the G hinge
point, the H hinge point and the I hinge point of the three-hinge
point holder form an equilateral triangle. Connecting lines between
projection points of the I hinge point, the H hinge point, the F
hinge point and the L hinge point on a central plane form a
parallelogram. The self-leveling link rod is L-shaped, and an upper
section thereof is bent backwardly, thus avoiding interference
between the self-leveling link rod and the middle beam connecting
the two rear link rods. The overturning oil cylinder is located
below the movable arm beam.
[0021] In the present disclosure, the bucket lifting mechanism is
formed by superposing two four-link rods to realize vertical
lifting, and a first four-link rod mechanism consisting of the
movable arm 2, the rear link rod 5, the front frame 3 and the
movable arm oil cylinder 4 realizes a lifting movement of the
movable arm 2; and a second four-link rod consisting of the movable
arm 2, the front link rod 6, the front frame 3 and the movable arm
oil cylinder 4 realizes horizontal restraint in a lifting process,
and controls a load moment arm to swing in a small range, so that a
distance between the bucket 1 and a front wheel is basically kept
unchanged in the lifting process, so as to realize vertical
lifting.
[0022] A forward Z-shaped six-link rod consisting of the bucket 1,
the pulling rod 11, the rocker arm 10, the movable arm 2, the
overturning oil cylinder 8 and the three-hinge point holder 7 at
the front end of the accessory overturning mechanism realizes an
overturning action, and controls an overturning angle of the bucket
and a digging force of the bucket. The overturning oil cylinder 8
is mounted at the lower end of the rocker arm 10, and the pulling
rod 11 is mounted at the upper end of the rocker arm 10, thus
reducing a mounting height of the overturning oil cylinder 8 and
improving a front visual field. Meanwhile, an overturning movement
direction of the bucket is consistent with a movement direction of
the rocker arm 10, which is beneficial to increasing the
overturning angle of the bucket. A four-link rod mechanism
consisting of the three-hinge point holder 7, the self-leveling
link rod 12, the rear link rod 5 and the front frame 3 at the rear
end of the bucket overturning mechanism realizes automatic leveling
in an overturning process, which solves the problem of asynchronous
angle turnover of the bucket lifting mechanism and the bucket
overturning mechanism, and the four-link rod structure at the rear
end controls the change of the bucket overturning angle in the
lifting process of the bucket lifting mechanism, so that the change
of the bucket angle relative to the ground is smaller. The
three-hinge point holder 7 skillfully solves the connection problem
of the overturning oil cylinder 8, the rear link rod 5 and the
self-leveling link rod 12, and reduces the assembly difficulty.
* * * * *