U.S. patent application number 16/551115 was filed with the patent office on 2020-03-05 for approach and mechanism for execution of critical system operations.
This patent application is currently assigned to Honeywell International Inc.. The applicant listed for this patent is Honeywell International Inc.. Invention is credited to Deenadayalan Karunakaran, Ankith Makam, Nagasree Poluri.
Application Number | 20200073351 16/551115 |
Document ID | / |
Family ID | 69640022 |
Filed Date | 2020-03-05 |

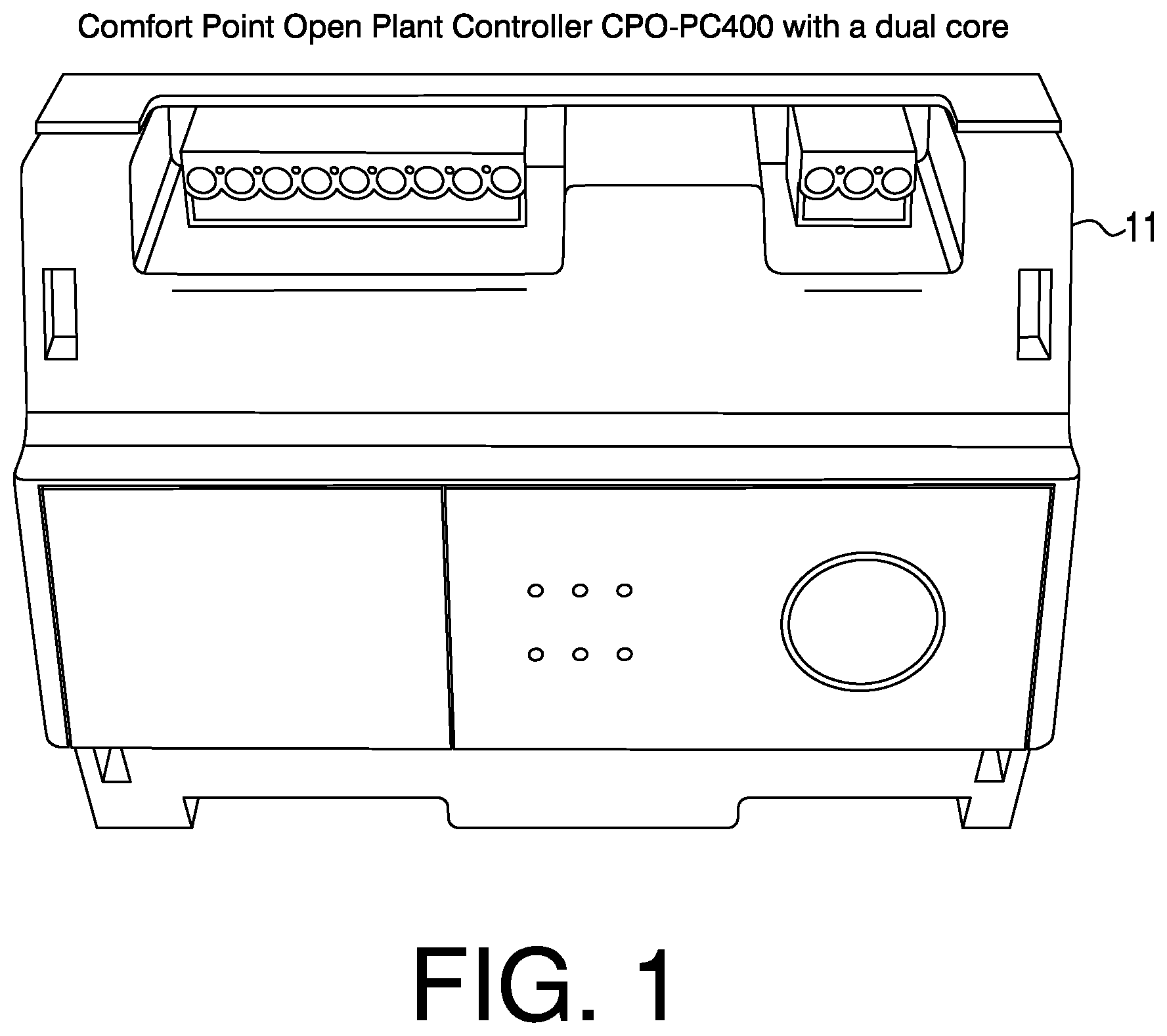

United States Patent
Application |
20200073351 |
Kind Code |
A1 |
Poluri; Nagasree ; et
al. |
March 5, 2020 |
APPROACH AND MECHANISM FOR EXECUTION OF CRITICAL SYSTEM
OPERATIONS
Abstract
An approach and mechanism for improving reliability, performance
and on time execution of critical operations of a system, such as
an HVAC. A controller may have two or more processing cores. One
core may be dedicated to execution of critical operations of a
system. Another core may be dedicated to less- or non-critical
operations of the system. For instance, if there are delays
relative to the less- or non-critical operations, these delays may
be ineffective relative to the processing of critical
operations.
Inventors: |
Poluri; Nagasree;
(Bangalore, IN) ; Makam; Ankith; (Bangalore,
IN) ; Karunakaran; Deenadayalan; (Bangalore,
IN) |
|
Applicant: |
Name |
City |
State |
Country |
Type |
Honeywell International Inc. |
Morris Plains |
NJ |
US |
|
|
Assignee: |
Honeywell International
Inc.
Morris Plains
NJ
|
Family ID: |
69640022 |
Appl. No.: |
16/551115 |
Filed: |
August 26, 2019 |
Related U.S. Patent Documents
|
|
|
|
|
|
Application
Number |
Filing Date |
Patent Number |
|
|
62725990 |
Aug 31, 2018 |
|
|
|
62726061 |
Aug 31, 2018 |
|
|
|
Current U.S.
Class: |
1/1 |
Current CPC
Class: |
G06F 7/462 20130101;
F24F 11/30 20180101; G06F 7/461 20130101; F24F 11/52 20180101; G05D
23/1934 20130101; G06F 11/3037 20130101; G05B 15/02 20130101; F24F
11/0001 20130101; G05B 2219/21105 20130101; G06F 12/0646 20130101;
G05B 2219/2642 20130101; G05B 2219/2614 20130101; G06F 9/5016
20130101; G06F 11/3476 20130101; F24F 2011/0006 20130101; F24F
11/63 20180101; G05B 19/0423 20130101; G05B 23/0264 20130101; G06F
12/0246 20130101 |
International
Class: |
G05B 19/042 20060101
G05B019/042; G05B 15/02 20060101 G05B015/02; G05D 23/19 20060101
G05D023/19; F24F 11/00 20060101 F24F011/00; F24F 11/30 20060101
F24F011/30 |
Claims
1. A multi-core processor comprising: at least two processor cores;
and wherein: a first core of the at least two processor cores is
dedicated to critical operations of a control system; a second core
of the at least two processor cores is dedicated to non-critical
operations of the control system; and the first core and the second
core are connected to each other for exchanging data.
2. The processor of claim 1, wherein the first core is dedicated
for providing on-time execution of critical operations.
3. The processor of claim 2, wherein the first core is dedicated to
achieve delay-free or interruption-free critical operations.
4. The processor of claim 3, wherein critical operations include
one or more items selected from a group comprising control logic
execution and operation of input/output devices.
5. The processor of claim 2, wherein the critical operations of the
first core M4 are made independent of a variable network load of
the second core A9.
6. The processor of claim 3, wherein: the control system is an HVAC
control system; and the HVAC control system has functionalities
segregated between the first core and the second core based on
priority levels of criticality of operation of the system.
7. The processor of claim 2, wherein the first core and the second
core are periodically synchronized with each other to avoid data
inconsistencies.
8. The processor of claim 2, wherein tasks outside of the tasks
handled by the first core comprise one or more tasks of a group
having schedules, BACnet Master Slave Token Passing (MSTP) routing,
BACnet communication, point sharing, trends, schedule updates, and
trend updates.
9. The processor of claim 2, wherein the first core and the second
core are a first processor and a second processor,
respectively.
10. The processor of claim 6, wherein: items that cause delay or
interruption are segregated to the second core; items that need to
be executed or commanded immediately are segregated to the first
core; and the items that cause delay or interruption are segregated
to the second core and do not cause delay or interruption of the
items that are segregated to the first core.
11. The processor of claim 1, wherein the first core and the second
core are part of a dual-core processor.
12. A method for utilizing a multi-core system, comprising:
segregating two or more processor cores according to operations of
a building component; and classifying the operations according to a
need of an operation to be executed or commanded within a
predetermined period of time; and wherein: the operations that need
to be executed or commanded within a predetermined period of time
are processed by a first processor core of the two or more
processor cores; and the operations that lack a need to be executed
or commanded within a predetermined period of time are processed by
a second, another or other processor core or cores of the two or
more processor cores.
13. The method of claim 12, wherein delays or interruptions of
operations processed by a second, another or other processor core
or cores, are ineffective upon a period of time for execution or
command of operations processed by the first processor core.
14. The method of claim 12, wherein the predetermined period of
time is adjustable.
15. The method of claim 13, wherein the building component is an
HVAC system.
16. The method of claim 15, wherein the operations to the first
processor core incorporate one or more items from a group
comprising execution of control logic and command of input/output
devices.
17. The method of claim 16, wherein a processor core is a
processor.
18. A processing mechanism comprising: a first processor core; and
a second processor core; and wherein: the first processor core is
dedicated to critical operations of an HVAC system; the second
processor core is dedicated to non-critical operations of the HVAC
system; and the critical operations are processed by the first
processor core within a predetermined period of time.
19. The mechanism of claim 18, wherein operations processed by the
first processor core are unaffected by operations processed by the
second processor core.
20. The mechanism of claim 18, further comprising: a hardware
device connected to the cloud and connected to the first and second
processor cores; and wherein the first and second processor cores
share data so that external communications can be handled with
updated data.
Description
[0001] This application claims the benefit of U.S. Provisional
Patent Application Ser. No. 62/725,990, filed Aug. 31, 2018. U.S.
Provisional Patent Application Ser. No. 62/725,990, filed Aug. 31,
2018, is hereby incorporated by reference.
[0002] This application claims the benefit of U.S. Provisional
Patent Application Ser. No. 62/726,061, filed Aug. 31, 2018. U.S.
Provisional Patent Application Ser. No. 62/726,061, filed Aug. 31,
2018, is hereby incorporated by reference.
BACKGROUND
[0003] This disclosure pertains to controllers and specifically to
various configurations of multi-core controllers.
SUMMARY
[0004] The disclosure reveals an approach and mechanism for
improving reliability, performance and on time execution of
critical operations of a system, such as an HVAC. A controller may
have two or more processing cores. One core may be dedicated to
execution of critical operations of a system. Another core may be
dedicated to less- or non-critical operations of the system. For
instance, if there are delays relative to the less- or non-critical
operations, these delays may be ineffective relative to the
processing of critical operations.
BRIEF DESCRIPTION OF THE DRAWING
[0005] FIG. 1 is a diagram of a controller relative to a system in
the present application; and
[0006] FIG. 2 is a diagram of plant controller firmware.
DESCRIPTION
[0007] The present system and approach may incorporate one or more
processors, computers, controllers, user interfaces, wireless
and/or wire connections, and/or the like, in an implementation
described and/or shown herein.
[0008] This description may provide one or more illustrative and
specific examples or ways of implementing the present system and
approach. There may be numerous other examples or ways of
implementing the system and approach.
[0009] Aspects of the system or approach may be described in terms
of symbols in the drawing. Symbols may have virtually any shape
(e.g., a block) and may designate hardware, objects, components,
activities, states, steps, procedures, and other items.
[0010] The present system may be about of how two CPU's/processors
can be segregating in terms of heating, ventilation and air
conditioning (HVAC) operations. One may just talk about an
in-general split of various HVAC components (not operations) and
sharing data between them but the present system may be about a
specific HVAC operations/activities and their segregation to
dedicated cores. One may also talk about single or multiple
processors executing instructions and computer programs.
Instructions may be executed by one or multiple processors. Thus,
such a system may appear more like an overall split system where
different components can run into one or more processors. However,
the present system may be about any specifics of which an HVAC
operation is dedicated to which core for a given device, how many
total cores/processors are available, and so on. The present system
may be specific to the way one segregates the most critical HVAC
operations (i.e., IO, control logic, and the like) to a single core
and other operations (e.g., BACnet communication, MSTP routing, and
so forth) to another core to achieve more reliability and
performance.
[0011] It appears troublesome that in the heating, ventilation and
air conditioning (HVAC) world today there may be a delay,
interruption and/or unreliability in executing the very critical
HVAC operations such as control logic execution and command of
input/output (TO) devices.
[0012] This situation appears to be a common issue with any HVAC
controller but it seems most prevalent in a supervisory or plant
controller due to a wide set of functionalities that it supports.
Possible causes of this situation may be that a controller is busy
handling other tasks like BACnet Master Slave Token Passing (MSTP)
routing, point sharing, schedule updates, trend updates, building
automation and control network (BACnet) communication, and so
forth.
[0013] The delay may be proportional to the network load, for
example, a larger number of MSTP devices may be connected to a
plant controller, and then more BACnet requests may need to be
handled at a given time, and so on. The delay or interruption seems
unacceptable in time-critical industries, like "Pharma", where even
a millisecond delay can incur a major loss.
[0014] There seems not to be any out of the box solutions through
which these critical HVAC operations can be handled with
reliability. It may be difficult to make such approach delay or
interruption free.
[0015] Also, some solutions may be limited in terms of resources
(e.g., processor power, memory availability, and so forth), and
thus prove to be ineffective in addressing a noted issue. The
present approach may be about segregating the most critical
operations of a HVAC controller to a dedicated core in HVAC
controller firmware, and improving the reliability, performance,
and on time execution of critical HVAC operations.
[0016] The present approach may achieve an improved and delay or
interruption-free performance on control logic execution and
input/output devices commanding a utilization of a dual core
capability to the fullest potential, thus providing a more
performant solution.
[0017] The present approach may be about reserving the highly
critical HVAC operations like control logic execution and
input/output devices commanding to a M4 core and other operations
to an A9 core.
[0018] Also, the present approach may be about making the core HVAC
functionality independent of network load, achieving more reliable
performant and timely HVAC core operations. It may be about
providing more priority to the critical HVAC operations, and
segregating the HVAC functionalities between the available two
cores based on priority levels. The approach may synchronize both
the cores periodically to avoid any data inconsistency.
[0019] Advantages may include the following features. This system
may help in a more reliable performant, and timely operation on
control logic execution and IO device command. Being a more or most
performant solution, it may be a best fit for time critical jobs
like "Pharma".
[0020] This approach or system may help in increasing revenues as a
reliable/delay-free core HVAC functionality is a key requirement
for some specific jobs (like those of Pharma, hospitals, and so
forth). This system may help in boosting the customer confidence
thus increasing a customer base. This system may help in a
reduction of the number of support calls or issues that may arise
due to a heavy network load. The reduction may help reduce travel
costs as many or most of the support calls related to core
functionality can only be investigated on the site.
[0021] The approach may help in bidding for more projects as it is
a unique, yet very important use case from a customer's stand
point, which many competitors might not have. The system may be a
key differentiator and USP for comfort point open controllers,
which may be targeted to be released as part of a program.
[0022] In a present solution, the comfort point open (CPO) plant
controller (PC), Honeywell International Inc. model number 400, for
example, i.e., CPO-PC400, may be built with a dual core processor,
for example, an M4 core and an A9 core. A diagram of a CPO-PC400
controller 11 is shown in FIG. 1.
[0023] In order to achieve more reliable performance and reduce the
delays in the most critical HVAC operations, one of the cores, such
as an M4 core, may be dedicated only for these operations in the
plant controller firmware. Thus, an M4 processor may take care of
executing the control logic and commanding the IO devices. Also,
the priority of these tasks could be set high when compared to any
other tasks that the controller has to handle. Thus, other
functionalities like schedules, MSTP routing, BACnet communication,
and so on, may be handled by another core, such as an A9 core.
[0024] By way of segregating the tasks in controller firmware by
utilizing the available two cores, RACL execution and IO handling
may have little or no impact even when there is a heavy load on the
network or in case of network failure. Since RACL execution and IO
handling may be the most critical tasks that a controller has to
handle without delay, the present robust design may help in
enabling the same.
[0025] The data between two cores may be shared periodically so
that BACnet communication can be handled with the updated data. In
sum, the present approach may be about segregating the most
critical operations of a HVAC controller to a dedicated core in
HVAC controller firmware.
[0026] Two CPUs or processors may be segregating in terms of HVAC
operations. The present approach may be a way to segregate the most
critical HVAC operations (TO, control logic, and the like) to
single core, and other operations to another core to achieve more
reliability and performance.
[0027] It may be particularly about specific HVAC
operations/activities and their segregation into dedicated cores.
The present system may be specific to the way one segregates the
most critical HVAC operations (TO, control logic, and the like) to
single core and other operations (BACnet communication, MSTP
routing, and so forth) to another core to achieve increased
reliability and performance.
[0028] A diagram in FIG. 2 shows CPO-PC400 plant controller
firmware 12. An M4 core and an A9 core have a bidirectional
connection with each other. An outward connection from the M4 core
may for command IO devices and execute control logic (RACL). An
outward connection from the A9 core may be for BACnet communication
and other HVAC functionaries such as MSTP routing, schedules, and
so forth.
[0029] The present system may have two or more CPUs or processors
that can be segregating in terms of HVAC operations. The system may
be about specific HVAC operations and/or activities and their
segregation into dedicated cores. The system may be also about any
specifics of which HVAC operation is dedicated to a core for a
given device, how many total cores and/or processors are available,
and so on. The system may be specific as to the way that one can
segregate the most critical HVAC operations (TO, control logic) to
a single core and other operations (BACnet communication, MSTP
routing, and so on) to another core to achieve more reliability and
performance.
[0030] FIG. 1 is a diagram of a controller 11 with a dual core. An
illustrative example may incorporate a Honeywell.TM. "Comfort Point
Open Plant Controller" model 400 (viz., CPO PC400). Controller 11
may have plant controller firmware 12 as shown in FIG. 2.
Controller firmware 12 may have an M4 core 13 and an A9 core 14,
which may be connected to each other with a two-way path 15. An
output 16 from M4 core 13 may provide for a command of I/O devices
and for execution of control logic (RACL). An output 17 from A9
core 14 may provide BACnet communication. For certain systems, such
as HVAC's, A9 core 14 may provide HVAC functions like MSTP routing,
schedules, and so on.
[0031] To recap, a multi-core processor may incorporate at least
two processor cores. A first core of the at least two processor
cores may be dedicated to critical operations of a control system.
A second core of the at least two processor cores may be dedicated
to non-critical operations of the control system. The first core
and the second core may be connected to each other for exchanging
data.
[0032] The first core is dedicated for providing on-time execution
of critical operations.
[0033] The first core may be dedicated to achieve delay-free or
interruption-free critical operations.
[0034] Critical operations may include one or more items selected
from a group comprising control logic execution and operation of
input/output devices.
[0035] The critical operations of the first core M4 may be made
independent of a variable network load of the second core A9.
[0036] The control system may be an HVAC control system. The HVAC
control system may have functionalities segregated between the
first core and the second core based on priority levels of
criticality of operation of the system.
[0037] The first core and the second core are periodically
synchronized with each other to avoid data inconsistencies.
[0038] Tasks outside of the tasks handled by the first core may
incorporate one or more tasks of a group having schedules, BACnet
Master Slave Token Passing (MSTP) routing, BACnet communication,
point sharing, trends, schedule updates, and trend updates.
[0039] The first core and the second core may be a first processor
and a second processor, respectively.
[0040] Items that cause delay or interruption may be segregated to
the second core. Items that need to be executed or commanded
immediately may be segregated to the first core. The items that
cause delay or interruption may be segregated to the second core
and do not necessarily cause delay or interruption of the items
that are segregated to the first core.
[0041] The first core and the second core may be part of a
dual-core processor.
[0042] An approach for utilizing a multi-core system, may
incorporate segregating two or more processor cores according to
operations of a building component, and classifying the operations
according to a need of an operation to be executed or commanded
within a predetermined period of time. The operations that need to
be executed or commanded within a predetermined period of time may
be processed by a first processor core of the two or more processor
cores. The operations that lack a need to be executed or commanded
within a predetermined period of time may be processed by a second,
another or other processor core or cores of the two or more
processor cores.
[0043] Delays or interruptions of operations processed by a second,
another or other processor core or cores, may be ineffective upon a
period of time for execution or command of operations processed by
the first processor core.
[0044] The predetermined period of time may be adjustable.
[0045] The building component is an HVAC system.
[0046] The operations to the first processor core may incorporate
one or more items from a group comprising execution of control
logic and command of input/output devices.
[0047] A processor core is a processor.
[0048] A processing mechanism may incorporate a first processor
core, and a second processor core. The first processor core may be
dedicated to critical operations of an HVAC system. The second
processor core may be dedicated to non-critical operations of the
HVAC system. The critical operations may be processed by the first
processor core within a predetermined period of time.
[0049] Operations processed by the first processor core may be
strictly unaffected by operations processed by the second processor
core.
[0050] The mechanism may further incorporate a hardware device
connected to the cloud and connected to the first and second
processor cores. The first and second processor cores may share
data so that external communications can be handled with updated
data.
[0051] Any publication or patent document noted herein is hereby
incorporated by reference to the same extent as if each publication
or patent document was specifically and individually indicated to
be incorporated by reference.
[0052] In the present specification, some of the matter may be of a
hypothetical or prophetic nature although stated in another manner
or tense.
[0053] Although the present system and/or approach has been
described with respect to at least one illustrative example, many
variations and modifications will become apparent to those skilled
in the art upon reading the specification. It is therefore the
intention that the appended claims be interpreted as broadly as
possible in view of the related art to include all such variations
and modifications.
* * * * *