U.S. patent application number 16/343615 was filed with the patent office on 2020-02-13 for method for manufacturing pressure-sensitive adhesive film.
This patent application is currently assigned to LG Chem, Ltd.. The applicant listed for this patent is LG Chem, Ltd.. Invention is credited to Yoon Kyung KWON, Hui Je LEE, Byung Su PARK.
Application Number | 20200048505 16/343615 |
Document ID | / |
Family ID | 62187896 |
Filed Date | 2020-02-13 |

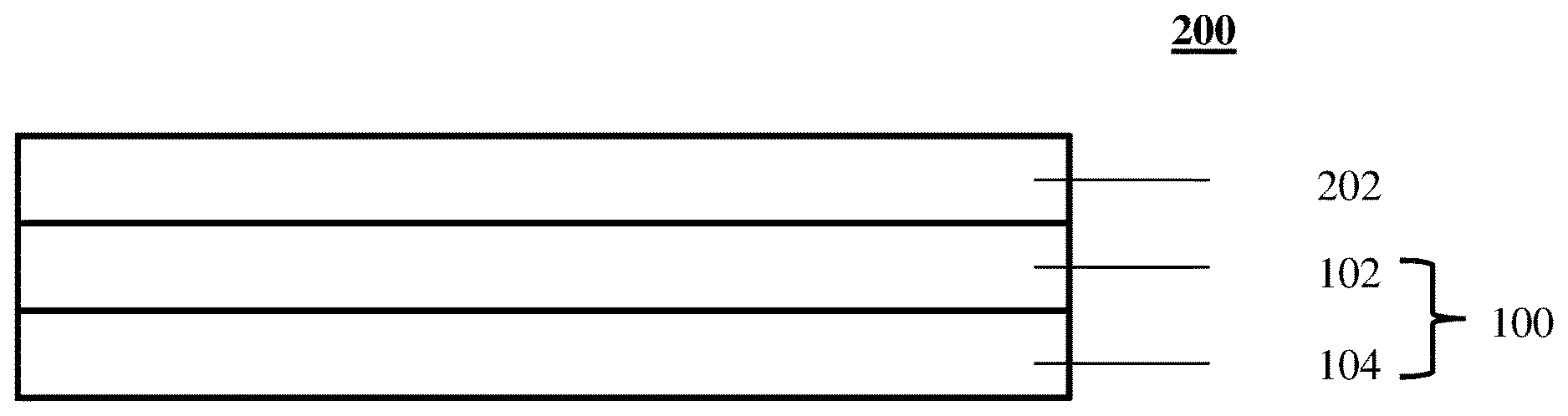

United States Patent
Application |
20200048505 |
Kind Code |
A1 |
LEE; Hui Je ; et
al. |
February 13, 2020 |
Method for Manufacturing Pressure-Sensitive Adhesive Film
Abstract
The present application relates to a method for manufacturing a
pressure-sensitive adhesive film. In an embodiment, a method for
manufacturing a pressure-sensitive adhesive film having a
pressure-sensitive adhesive layer and a base layer includes
applying a pressure-sensitive adhesive composition on at least one
side of a base layer, where the pressure-sensitive adhesive
composition comprises an isocyanate compound, a metal compound and
an acrylic polymer; and drying the pressure-sensitive adhesive
composition at a temperature of 100.degree. C. or higher to form a
pressure-sensitive adhesive layer on the base layer.
Inventors: |
LEE; Hui Je; (Daejeon,
KR) ; PARK; Byung Su; (Daejeon, KR) ; KWON;
Yoon Kyung; (Daejeon, KR) |
|
Applicant: |
Name |
City |
State |
Country |
Type |
LG Chem, Ltd. |
Seoul |
|
KR |
|
|
Assignee: |
LG Chem, Ltd.
Seoul
KR
|
Family ID: |
62187896 |
Appl. No.: |
16/343615 |
Filed: |
October 31, 2017 |
PCT Filed: |
October 31, 2017 |
PCT NO: |
PCT/KR2017/012145 |
371 Date: |
April 19, 2019 |
Current U.S.
Class: |
1/1 |
Current CPC
Class: |
C09J 11/06 20130101;
C09J 133/00 20130101; C09J 7/385 20180101; C09J 2205/102 20130101;
C09J 2433/00 20130101; C08K 5/0091 20130101; C08K 5/098 20130101;
C09J 2467/006 20130101; C09J 2203/318 20130101; C09J 2301/408
20200801; C09J 7/255 20180101 |
International
Class: |
C09J 7/38 20060101
C09J007/38; C09J 11/06 20060101 C09J011/06; C09J 7/25 20060101
C09J007/25 |
Foreign Application Data
Date |
Code |
Application Number |
Nov 4, 2016 |
KR |
10-2016-0146413 |
Oct 30, 2017 |
KR |
10-2017-0142311 |
Claims
1. A method for manufacturing a pressure-sensitive adhesive film,
the pressure-sensitive adhesive film having a pressure-sensitive
adhesive layer and a base layer, the method comprising: applying a
pressure-sensitive adhesive composition to at least one side of a
base layer, wherein the pressure-sensitive adhesive composition
comprises an isocyanate compound, a metal compound, and an acrylic
polymer; and drying the pressure-sensitive adhesive composition at
a temperature of 100.degree. C. or higher to form a
pressure-sensitive adhesive layer on the base layer.
2. The method for manufacturing a pressure-sensitive adhesive film
according to claim 1, wherein the metal compound comprises at least
one metal of iron (Fe), zinc (Zn), zirconium (Zr), tin (Sn) and
bismuth (Bi).
3. The method for manufacturing a pressure-sensitive adhesive film
according to claim 2, wherein the metal compound further comprises
diketonate or carboxylate as a ligand.
4. The method for manufacturing a pressure-sensitive adhesive film
according to claim 3, wherein the metal compound comprises an iron
(Fe) metal and a diketonate ligand.
5. The method for manufacturing a pressure-sensitive adhesive film
according to claim 1, wherein the acrylic polymer comprises a
(meth)acrylate monomer having a hydroxy group as a polymerized
unit.
8. The method for manufacturing a pressure-sensitive adhesive film
according to claim 1, wherein the isocyanate compound is a
bifunctional or multifunctional compound.
7. The method for manufacturing a pressure-sensitive adhesive film
according to claim 1, wherein the base layer comprises any one of a
polyester film, a polytetrafluoroethylene film, a polyethylene
film, a polypropylene film, a polybutene film, a polybutadiene
film, a vinyl chloride copolymer film, or a polyimide film.
8. The method for manufacturing a pressure-sensitive adhesive film
according to claim 1, wherein the pressure-sensitive adhesive
composition comprises 0.01 to 0.5 parts by weight of the metal
compound and 1 to 20 parts by weight of the isocyanate compound,
relative to 100 parts by weight of the acrylic polymer.
9. The method for manufacturing a pressure-sensitive adhesive film
according to claim 1, wherein the pressure-sensitive adhesive
composition further comprises a curing retardant.
10. The method for manufacturing a pressure-sensitive adhesive film
according to claim 9, wherein the curing retardant is one or more
of methyl acetoacetate, ethyl acetoacetate, octyl acetoacetate,
oleyl acetoacetate, lauryl acetoacetate, stearyl acetoacetate,
acetylacetone, 2,4-hexanedione or benzoylacetone.
11. The method for manufacturing a pressure-sensitive adhesive film
according to claim 1, further comprising: laminating a release film
on the pressure-sensitive adhesive layer after the drying step.
12. The method for manufacturing a pressure-sensitive adhesive film
according to claim 11, further comprising: curing, after the
lamination of the release film, at a temperature range of
30.degree. C. to 60.degree. C.
13. The method for manufacturing a pressure-sensitive adhesive film
according to claim 1, wherein craters are present in the
pressure-sensitive adhesive layer at a number of 5/m.sup.2 or
less.
14. The method for manufacturing a pressure-sensitive adhesive film
according to claim 13, wherein the craters have a diameter of 500
.mu.m or less.
15. An optical laminate comprising an optical film; and a
pressure-sensitive adhesive film, which is manufactured according
to claim 1, formed on one side or both sides of the optical film.
Description
CROSS-REFERENCE TO RELATED APPLICATIONS
[0001] This application claims the benefit of priority based on
Korean Patent Application No. 10-2016-0146413 filed on Nov. 4, 2016
and Korean Patent Application No. 10-2017-0142311 filed on Oct. 30,
2017, the disclosures of which are incorporated herein by reference
in their entirety.
TECHNICAL FIELD
[0002] The present application relates to a method for
manufacturing a pressure-sensitive adhesive film.
BACKGROUND ART
[0003] A liquid crystal display (LCD) is a device for displaying
images using liquid crystals, which has advantages such that it
consumes less power and can be made a low power consumption and can
be made thinner in a plane, and is a display device spotlighted in
various fields.
[0004] A polarizing plate, which is an optical member applied to
the liquid crystal display device or the like, usually has a
structure in which a film such as triacetyl cellulose, an acrylic
film, and a cycloolefin film is laminated on one side or both sides
of a polarizer, and thus a film for protecting the polarizing plate
from external impacts or friction and contamination by sticking on
the film is required from a manufacturing process to a process of
making an LCD module and thus To the process of making the LCD
module.
[0005] Since such a film can stick to the polarizing plate during
the process to accompany optical inspections in a sticking state,
it should have high transparency, and since it is peeled off as an
unnecessary material after completing the protection role, it
should be removed without leaving defects on the polarizing plate
or the like upon removal.
[0006] Particularly, when a crater is present on the surface of the
pressure-sensitive adhesive layer of the film, there is a risk that
the crater of the film attached to the polarizing plate is
recognized as a defect of the polarizing plate itself during the
process, whereby a situation such as process interruption occurs,
and there may be a risk that the crater will leave defects on the
polarizing plate upon removal of the film.
DISCLOSURE
Technical Problem
[0007] It is one object of the present application to provide a
pressure-sensitive adhesive film in which craters that may occur
upon producing the pressure-sensitive adhesive film are minimized
and an optical characteristic is improved.
[0008] The above object of the present application and other
objects can be all attained by the present application which is
described in detail below.
Technical Solution
[0009] In one example related to the present application, the
present application relates to a method for manufacturing a
pressure-sensitive adhesive film. The method of the present
application can produce a pressure-sensitive adhesive film capable
of protecting the polarizing plate from external impacts or
friction and contamination, from the manufacturing process of the
polarizing plate to the process of making the LCD module.
[0010] The method for manufacturing a pressure-sensitive adhesive
film may comprise a step of applying a pressure-sensitive adhesive
composition comprising an isocyanate compound, a metal compound and
an acrylic polymer to at least one side of a base layer.
[0011] In one example, the isocyanate compound may be a
bifunctional or multifunctional compound. The isocyanate compound
may react with the cross-linkable functional group of the acrylic
polymer to realize a cross-linked structure.
[0012] As the isocyanate compound, an isocyanate compound such as
tolylene diisocyanate, xylene diisocyanate, diphenylmethane
diisocyanate, hexamethylene diisocyanate, isophorone diisocyanate,
tetramethylxylene diisocyanate, naphthalene diisocyanate,
triphenylmethane triisocyanate or methylene bis(4-phenylmethane)
triisocyanate, or a compound that the isocyanate compound is
reacted with a polyol can be used, where as the polyol, for
example, trimethylolpropane and the like can be used. In the
pressure-sensitive adhesive composition, one or two or more
isocyanate compounds of the examples may be used, without being
limited thereto.
[0013] The isocyanate compound may be contained in an amount of 1
to 20 parts by weight relative to 100 parts by weight of the
acrylic polymer. The lower limit of the content of the isocyanate
compound may be, for example, 2 parts by weight or more, or 3 parts
by weight or more, and the upper limit may be, for example, 15
parts by weight or less, or 10 parts by weight or less. In this
range, a cross-linking degree of the pressure-sensitive adhesive
composition can be appropriately controlled, whereby all the
physical properties of the pressure-sensitive adhesive composition
such as cohesive force, pressure-sensitive adhesive force and
endurance reliability can be kept excellent.
[0014] In one example, the acrylic polymer may comprise a monomer
having a cross-linkable functional group as a polymerized unit. In
the present application, the inclusion of a monomer as a
polymerized unit may mean that the monomer undergoes a
polymerization reaction to form a skeleton of the polymer or block,
for example, a main chain or a side chain. The cross-linkable
functional group is variously known in the manufacturing field of a
pressure-sensitive adhesive, which is not particularly limited.
[0015] In one example, the monomer having a cross-linkable
functional group may be a (meth)acrylate monomer having a hydroxy
group, and specifically, hydroxyalkyl (meth)acrylate such as
2-hydroxyethyl (meth)acrylate, 2-hydroxypropyl (meth)acrylate,
4-hydroxybutyl (meth)acrylate, 6-hydroxyhexyl (meth)acrylate or
8-hydroxyoctyl (meth)acrylate, or hydroxyalkylene glycol
(meth)acrylate such as 2-hydroxyethylene glycol (meth)acrylate or
2-hydroxypropylene glycol (meth)acrylate, and the like can be used,
without being limited thereto. By using the monomer having a
cross-linkable functional group, the composition may exhibit an
appropriate cohesive force and stress relaxation property to form a
pressure-sensitive adhesive having excellent endurance reliability
and workability.
[0016] Also, the acrylic polymer may further comprise a
(meth)acrylic acid ester monomer as a polymerized unit. As the
(meth)acrylic acid ester monomer, for example, alkyl (meth)acrylate
having an alkyl group with 1 to 20 carbon atoms, 1 to 16 carbon
atoms, 1 to 12 carbon atoms, 1 to 8 carbon atoms or 1 to 4 carbon
atoms can be used. Here, the alkyl group may be linear, branched or
cyclic. An example of such a monomer may be methyl (meth)acrylate,
ethyl (meth)acrylate, n-propyl (meth)acrylate, isopropyl
(meth)acrylate, n-butyl (meth)acrylate, t-butyl (meth)acrylate,
sec-butyl (meth)acrylate, pentyl (meth)acrylate, 2-ethylhexyl
(meth)acrylate, 2-ethylbutyl (meth)acrylate, n-octyl
(meth)acrylate, isobornyl (meth)acrylate, isooctyl (meth)acrylate,
isononyl (meth)acrylate and lauryl (meth)acrylate, and the
like.
[0017] In one example, a metal compound may be included in the
pressure-sensitive adhesive composition. The metal compound can be
used as a catalyst for controlling the reaction rate of the
pressure-sensitive adhesive composition, and can accelerate the
cross-linking reaction to impart an appropriate cohesive force
thereto. In particular, it can selectively accelerate a urethane
reaction, which is a cross-linking reaction, and inhibit a urea
reaction, which is a side reaction.
##STR00001##
[0018] The urea reaction is a reaction which can occur by reacting
isocyanate with air or moisture contained in a solvent, where since
a crater may occur in the pressure-sensitive adhesive layer due to
carbon dioxide (CO.sub.2) gas generated in the urea reaction
process, the occurrence of craters can be suppressed by suppressing
the urea reaction.
[0019] The metal compound may comprise at least one metal of iron
(Fe), zinc (Zn), zirconium (Zr), tin (Sn) and bismuth (Bi), and
preferably, iron (Fe). In the case of aluminum (Al) conventionally
used mainly, there is a problem that the hardening promoting effect
is small, so that peel force is increased as well as the occurrence
of craters cannot be suppressed. On the other hand, by comprising
the metal, the urea reaction can be effectively suppressed to
inhibit the occurrence of craters, while maintaining proper peel
force, and even if craters are formed, only craters having a very
small size, for example, a diameter of 500 .mu.m or less can be
formed.
[0020] In one example, the metal compound may comprise diketonate
or carboxylate as a ligand, and preferably may comprise diketonate
as a ligand. The metal compound may be present in the form of a
complex compound in which the at least one metal and the ligand are
linked. By comprising the ligand, the urea reaction can be
effectively suppressed to inhibit the occurrence of craters, and
even if craters are formed, only craters having a very small size,
for example, a diameter of 500 .mu.m or less can be formed.
[0021] In one example, the metal compound may be included in an
amount of 0.01 to 0.5 parts by weight relative to 100 parts by
weight of the acrylic polymer. The lower limit of the content of
the metal compound may be, for example, 0.03 parts by weight or
more, or 0.05 parts by weight or more, and the upper limit may be,
for example, 0.4 parts by weight or less, or 0.3 parts by weight or
less. In this range, the reaction rate of the pressure-sensitive
adhesive composition can be suitably controlled, and appropriate
tackiness and endurance reliability can be imparted.
[0022] In the present application, the method of applying the
pressure-sensitive adhesive composition on the base layer is not
particularly limited, and for example, the composition can be
applied to the base layer by a conventional means such as a bar
coater.
[0023] In addition, the method for manufacturing a
pressure-sensitive adhesive film may comprise a step of drying the
pressure-sensitive adhesive composition to form a
pressure-sensitive adhesive layer after applying the composition.
The solvent or moisture contained in the pressure-sensitive
adhesive composition may be evaporated through the drying, and the
drying temperature is not particularly limited, which may be
appropriately adjusted depending on the components and content of
the solvent used.
[0024] In one example, the drying temperature may be at a
temperature of 100.degree. C. or higher, or 110.degree. C. or
higher. The upper limit of the temperature is not particularly
limited, but may be 150.degree. C. or lower. In the case of drying
in the above temperature range, the occurrence of craters can be
suppressed by evaporation of moisture or the like, the color index
of the pressure-sensitive adhesive film can be lowered, the
transparency can be improved by a low color index, and optical
characteristics can be improved.
[0025] The drying time is not particularly limited, and in one
example, it may be in a range of 20 seconds to 120 seconds, 40
seconds to 100 seconds, or 50 seconds to 80 seconds.
[0026] The thickness of the formed pressure-sensitive adhesive
layer is not particularly limited, and may be, for example, 6 .mu.m
to 100 .mu.m, and in another example, it may be 8 .mu.m or more, 10
.mu.m or more, or 15 .mu.m or more, and may be formed in a
thickness range of 90 .mu.m or less, 70 .mu.m or less, 60 .mu.m or
less, or 50 .mu.m or less. If the thickness of the
pressure-sensitive adhesive layer is out of the above-described
range, it is difficult to form a uniform pressure-sensitive
adhesive layer, which may result in uneven physical properties.
[0027] As the base layer, a general transparent film in this field
can be used without limitation, which may include, for example, a
plastic film, such as a polyester film such as polyethylene
terephthalate or polybutylene terephthalate, a
polytetrafluoroethylene film, a polyethylene film, a polypropylene
film, a polybutene film, a polybutadiene film, a vinyl chloride
copolymer film or a polyimide film. Such a base layer may be
composed of a single layer of the film, or may also be laminated by
two or more layers, and optionally, may also further comprise a
functional layer such as an antifouling layer or an antistatic
layer. In the present invention, a surface treatment such as a
primer treatment may also be performed on one side or both sides of
the base layer in terms of improving adhesiveness of the base
layer.
[0028] The thickness of the base layer is suitably selected
depending on applications, which is not particularly limited, and
may be, for example, 5 .mu.m to 500 .mu.m, and in another example,
it may be 10 .mu.m or more, 20 .mu.m or more, or 30 .mu.m or more,
and may be formed in a thickness range of 400 .mu.m or less, 300
.mu.m or less, 200 .mu.m or less, or 100 .mu.m or less.
[0029] In one example, the pressure-sensitive adhesive composition
may further comprise a curing retardant. The curing retardant may
comprise at least one of .beta.-keto ester such as methyl
acetoacetate, ethyl acetoacetate, octyl acetoacetate, oleyl
acetoacetate, lauryl acetoacetate and stearyl acetoacetate, or
.beta.-diketone such as acetylacetone, 2,4-hexanedione and
benzoylacetone.
[0030] The pressure-sensitive adhesive composition of the present
application may also suitably blend known additives such as a
silane coupling agent, an antioxidant, a surfactant, a curing
accelerator, a plasticizer, a filler, a processing aid and an
anti-aging agent as other components. These may be used alone or in
combination of two or more.
[0031] In one example, the method for manufacturing a
pressure-sensitive adhesive film may further comprise a step of
laminating a release film after the drying step. The release film
may be a film to which a releasing material for preventing fixation
of the pressure-sensitive adhesive is applied. The type of the
releasing material is not particularly limited, and for example, a
silicone release agent, a fluorine coating, a polyethylene coating,
or the like can be used.
[0032] In one example, the method for manufacturing a
pressure-sensitive adhesive film may further comprise a step of
curing after lamination of the release film. The method of curing
is not particularly limited and may be thermosetting or
photo-curing, and in one example, the curing may be performed at a
temperature of 30.degree. C. to 60.degree. C. Also, the curing time
may be for 24 hours to 72 hours. Outside the curing temperature
range, lifting of the laminated release film may occur.
[0033] According to another example related to the present
application, in a pressure-sensitive adhesive film comprising a
base layer and a pressure-sensitive adhesive layer cured by a
pressure-sensitive adhesive composition comprising an isocyanate
compound, a metal compound and an acrylic polymer, it may be a
method for manufacturing a pressure-sensitive adhesive film,
wherein the pressure-sensitive adhesive layer is formed so that
craters are present at a number of 5/m.sup.2 or less.
[0034] In one example, the crater may have a diameter of 500 .mu.m
or less, 400 .mu.m or less, or 300 .mu.m or less. The lower limit
of the diameter is not particularly limited and in one example, it
may be 10 .mu.m or more. The diameter of the crater may be measured
in a two-dimensional shape as viewed from above, and when the
two-dimensional shape of the crater is not circular, the diameter
may mean a length which is measured the greatest.
[0035] In another example, the depth of the crater is measured
below the thickness of the pressure-sensitive adhesive layer, which
may be 5 .mu.m or less, or 3 .mu.m or less. The lower limit of the
depth is not particularly limited and may be 0.1 .mu.m or more in
depth. The depth of the crater may mean a length, which is measured
the largest, of the depths formed by the craters, and the thicker
the thickness of the pressure-sensitive adhesive layer, the deeper
the crater may be.
[0036] When the craters formed in the pressure-sensitive adhesive
layer satisfy the number and size, a pressure-sensitive adhesive
film having excellent endurance reliability and workability can be
produced.
[0037] According to another example related to the present
application, it may be an optical laminate comprising an optical
film; and a pressure-sensitive adhesive film, which is manufactured
according to claim 1, formed on one side or both sides of the
optical film.
Advantageous Effects
[0038] According to the method for manufacturing a
pressure-sensitive adhesive film of the present application, the
pressure-sensitive adhesive film has a low color index to have high
transparency and the generation of craters is minimized, whereby a
pressure-sensitive adhesive film having excellent endurance
reliability and workability can be provided.
BEST MODE
[0039] Hereinafter, the present application will be described in
detail by way of examples. However, the scope of protection of the
present application is not limited by the examples described
below.
Method of Measuring Physical Properties
Experimental Example 1: Crater Occurrence Evaluation
[0040] For the pressure-sensitive adhesive films prepared in
Examples 1 to 6 and Comparative Examples 1 to 4 below, the number
of crater occurrences was measured by using a foreign matter
tester. As a result of measurements, X represents the case where a
crater having a diameter of 500 .mu.m or more and a depth of 7
.mu.m or more was generated, and A represents the case where a
crater having a diameter of 500 .mu.m or less and a depth of 7
.mu.m or less was not generated, B represents the case where 1 to 5
craters having a diameter of 500 .mu.m or less and a depth of 7
.mu.m or less are generated, C represents the case where 6 to 10
craters having a diameter of 500 .mu.m or less and a depth of 7
.mu.m or less are generated and D represents the case where over 10
craters having a diameter of 500 .mu.m or less and a depth of 7
.mu.m or less are generated. The results are as shown in Table
2.
Experimental Example 2: Color Index Evaluation
[0041] For the pressure-sensitive adhesive films prepared in
Examples 1 to 6 and Comparative Examples 1 to 4 below, the color
index was measured using a colorimeter (COH-400). The results are
as shown in Table 2, where the higher the value, yellowness more
increases to exhibit lower transparency.
Example 1
[0042] (1) Preparation of Pressure-Sensitive Adhesive
Composition
[0043] 2-ethylhexyl acrylate and 2-hydroxylethyl acrylate were
copolymerized in a weight ratio of 95:5 to prepare an acrylic
polymer solution having a solid content concentration of about 40%.
Ethyl acetate was used as the solvent.
[0044] Then, 5 parts by weight of an isocyanate compound (HDI
trimer, product name: DR750HD), 7.5 parts by weight of a curing
retardant (acetylacetone) and 0.05 part by weight of an iron
compound (Fe (III) acetylacetonate) having diketonate as a ligand,
relative to 100 parts by weight of the solid content of the acrylic
polymer solution, were uniformly blended to prepare a
pressure-sensitive adhesive composition.
[0045] (2) Manufacture of Pressure-Sensitive Adhesive Film
[0046] The pressure-sensitive adhesive composition prepared above
is bar-coated on one side of PET (poly(ethylene terephthalate)) and
dried at 120.degree. C. for 1 minute Immediately after drying, a
release film was laminated and cured at 40.degree. C. for 48 hours
to manufacture a pressure-sensitive adhesive film (1 m.times.100 m)
comprising a pressure-sensitive adhesive layer having a thickness
of 15 .mu.m.
Examples 2 to 6 and Comparative Examples 1 to 5
[0047] (1) Preparation of Pressure-Sensitive Adhesive
Composition
[0048] A pressure-sensitive adhesive composition was prepared in
the same manner as in Example 1, except that the metal compound was
changed as shown in Table 1 below.
[0049] (2) Manufacture of Pressure-Sensitive Adhesive Film
[0050] A pressure-sensitive adhesive film was prepared in the same
manner as in Example 1, except that the drying temperature in the
pressure-sensitive adhesive composition prepared above was changed
as in Table 1 below.
TABLE-US-00001 TABLE 1 Drying Metal compound temperature Type Part
by weight (.degree. C.) Example 1 Fe acetylacetonate 0.05 120 (Fe,
diketonate ligand) Example 2 Fe acetylacetonate 0.1 110 (Fe,
diketonate ligand) Example 3 Fe acetylacetonate 0.1 120 (Fe,
diketonate ligand) Example 4 Fe acetylacetonate 0.1 130 (Fe,
diketonate ligand) Example 5 Zn acetylacetonate 0.1 120 (Zn,
diketonate ligand) Example 6 Zr acetylacetonate 0.1 120 (Zr,
diketonate ligand) Comparative Dibutyltin dilaurate 0.01 90 Example
1 (Sn, carboxylate ligand) Comparative Zn ocotate 0.2 90 Example 2
(Zn, carboxylate ligand) Comparative Zr ocotate 0.2 90 Example 3
(Zr, carboxylate ligand) Comparative Fe acetylacetonate 0.1 90
Example 4 (Fe, diketonate ligand) Comparative Al acetylacetonate
0.1 120 Example 5 (Al, diketonate ligand)
TABLE-US-00002 TABLE 2 Crater occurrence Color index (b*) Example 1
A 0.35 Example 2 A 0.49 Example 3 A 0.41 Example 4 A 0.38 Example 5
B 0.36 Example 6 B 0.37 Comparative D 0.34 Example 1 Comparative D
0.36 Example 2 Comparative D 0.36 Example 3 Comparative A 1.1
Example 4 Comparative D 0.36 Example 5
* * * * *