U.S. patent application number 16/492375 was filed with the patent office on 2020-02-06 for bearing structure and electric compressor.
This patent application is currently assigned to IHI Corporation. The applicant listed for this patent is IHI Corporation. Invention is credited to Kuniaki IIZUKA, Tatsumi INOMATA, Kai llJIMA, Takashi MORI, Takuya OZASA, Yuji SASAKI, Takashi YOSHIDA, Ryosuke YUMOTO.
Application Number | 20200040903 16/492375 |
Document ID | / |
Family ID | 63676107 |
Filed Date | 2020-02-06 |
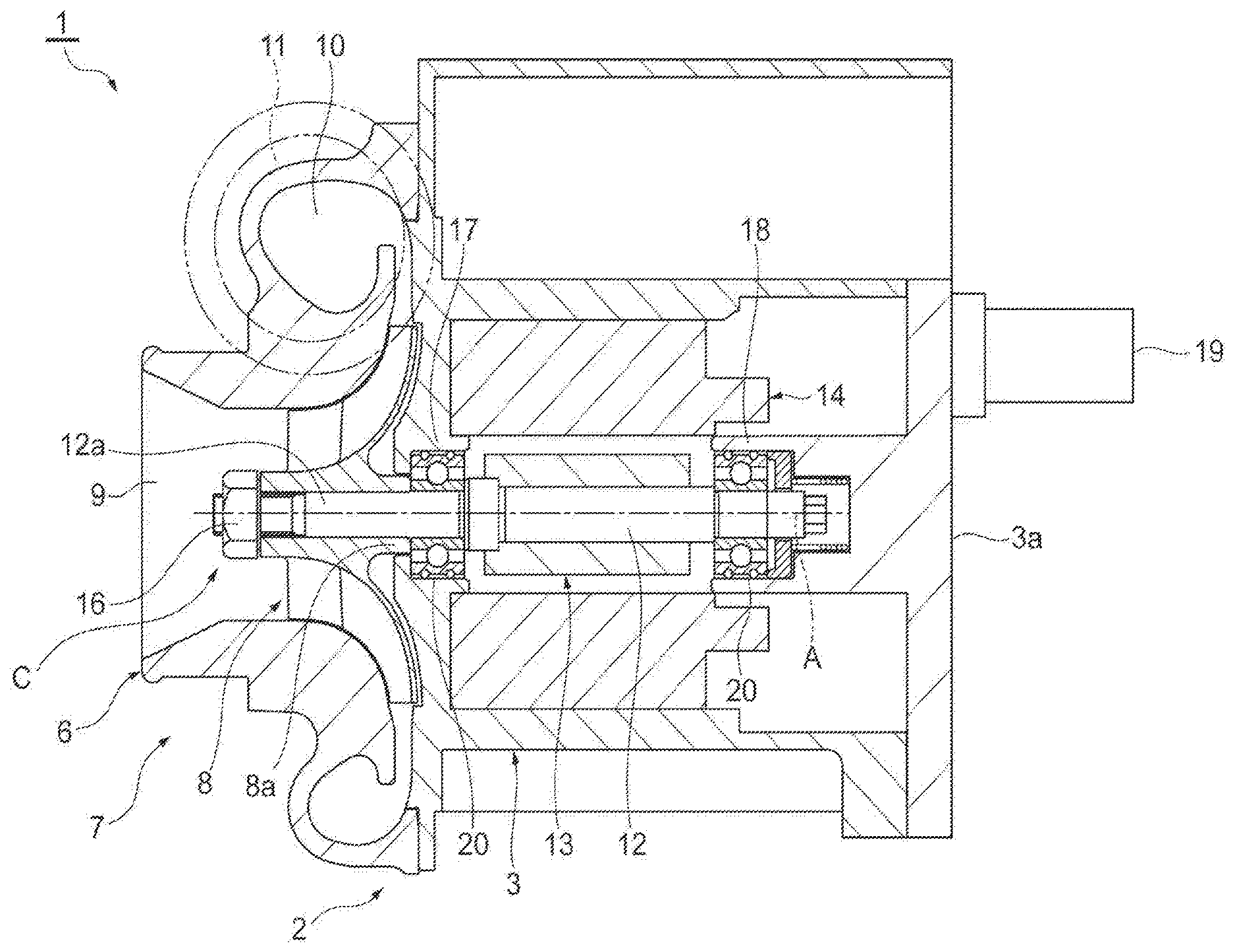
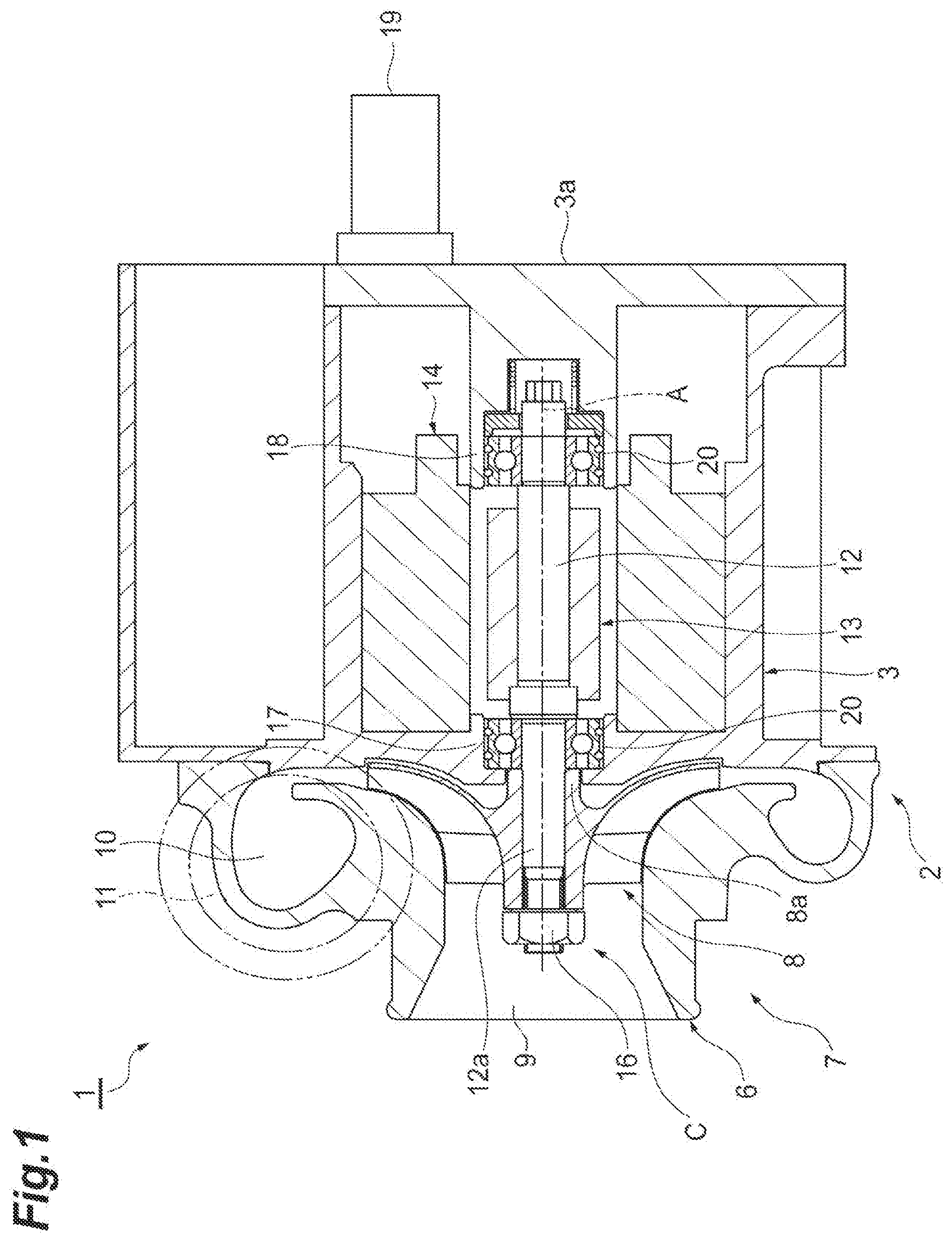

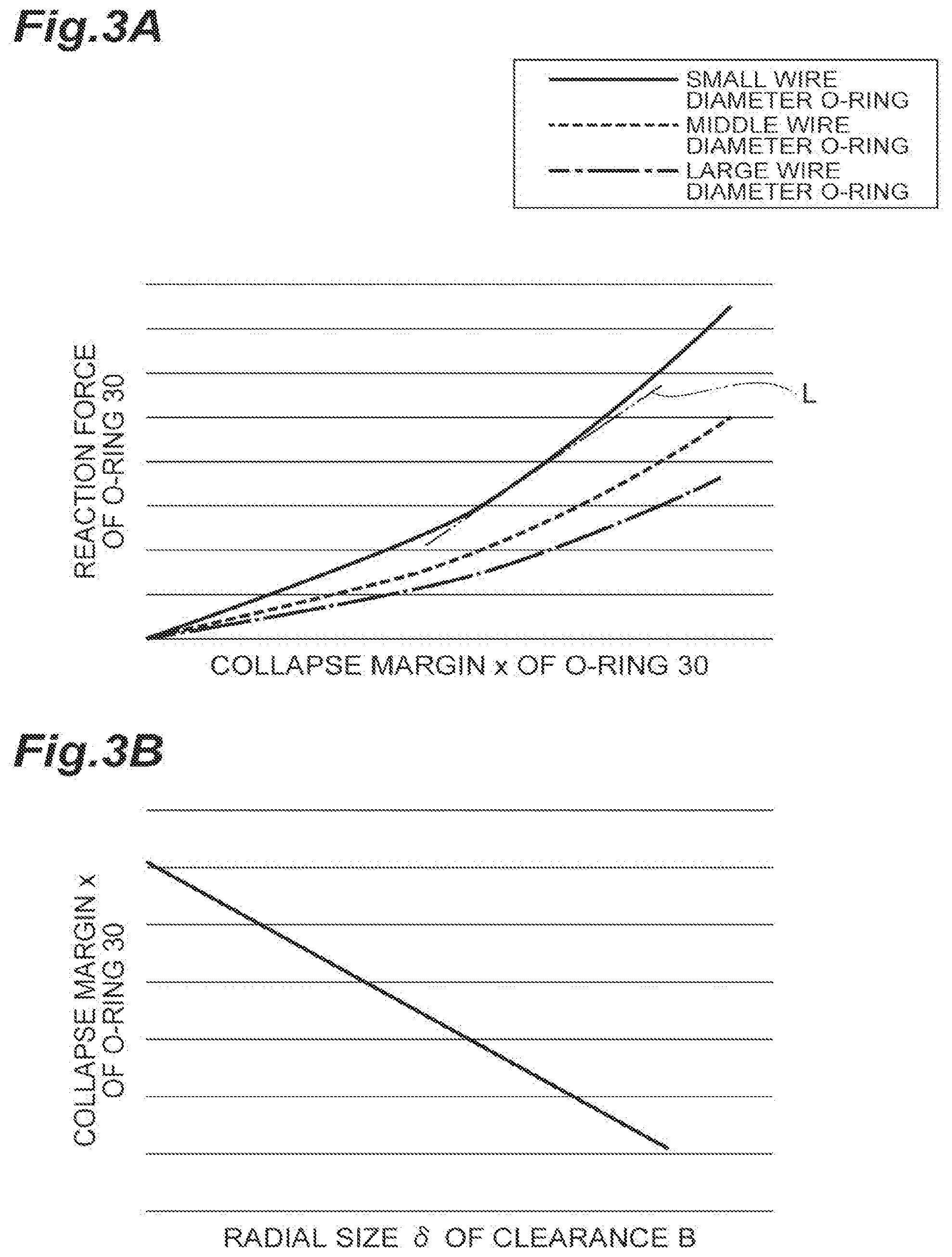
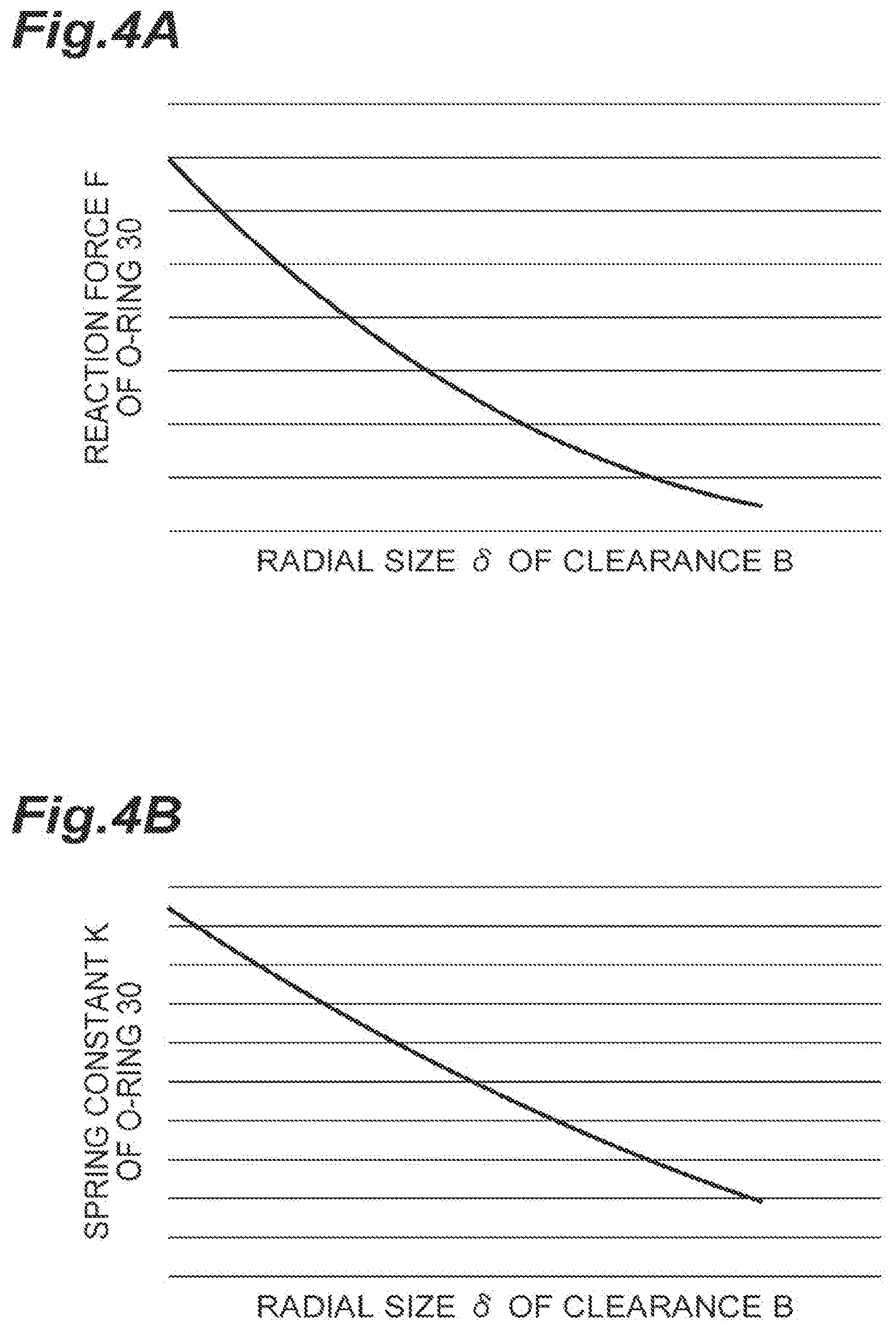






View All Diagrams
United States Patent
Application |
20200040903 |
Kind Code |
A1 |
IIZUKA; Kuniaki ; et
al. |
February 6, 2020 |
BEARING STRUCTURE AND ELECTRIC COMPRESSOR
Abstract
A bearing structure of the present disclosure includes a
rotation shaft, a bearing that is attached in a housing to support
the rotation shaft with respect to the housing and includes an
inner race through which the rotation shaft is inserted and an
outer race which includes an annular groove portion formed on an
outer peripheral surface facing an inner wall surface of the
housing, and an O-ring which is disposed on the groove portion of
the outer race of the bearing, protrudes outward in a radial
direction in relation to the outer peripheral surface, and comes
into contact with the inner wall surface of the housing. A
clearance is formed between the inner wall surface of the housing
and the outer peripheral surface of the bearing. The clearance is
larger than a radial displacement amount of the O-ring.
Inventors: |
IIZUKA; Kuniaki; (Koto-ku,
JP) ; YOSHIDA; Takashi; (Koto-ku, JP) ;
INOMATA; Tatsumi; (Koto-ku, JP) ; OZASA; Takuya;
(Koto-ku, JP) ; llJIMA; Kai; (Koto-ku, JP)
; YUMOTO; Ryosuke; (Koto-ku, JP) ; MORI;
Takashi; (Koto-ku, JP) ; SASAKI; Yuji;
(Koto-ku, JP) |
|
Applicant: |
Name |
City |
State |
Country |
Type |
IHI Corporation |
Koto-ku |
|
JP |
|
|
Assignee: |
IHI Corporation
Koto-ku
JP
|
Family ID: |
63676107 |
Appl. No.: |
16/492375 |
Filed: |
March 26, 2018 |
PCT Filed: |
March 26, 2018 |
PCT NO: |
PCT/JP2018/012150 |
371 Date: |
September 9, 2019 |
Current U.S.
Class: |
1/1 |
Current CPC
Class: |
F04D 29/668 20130101;
F04D 25/06 20130101; F16C 35/077 20130101; F04D 29/056 20130101;
F02B 39/00 20130101; F04D 29/058 20130101 |
International
Class: |
F04D 29/056 20060101
F04D029/056; F04D 25/06 20060101 F04D025/06 |
Foreign Application Data
Date |
Code |
Application Number |
Mar 31, 2017 |
JP |
2017-071204 |
Claims
1.-3. (canceled)
4. A bearing structure for supporting a rotation shaft of a
rotation body accommodated in a housing with respect to the
housing, comprising: the rotation shaft; a bearing that is attached
in the housing to support the rotation shaft with respect to the
housing and includes an inner race through which the rotation shaft
is inserted and an outer race which includes an annular groove
portion formed on an outer peripheral surface facing an inner wall
surface of the housing; and an O-ring which is disposed on the
groove portion of the outer race of the bearing, protrudes outward
in a radial direction in relation to the outer peripheral surface,
and comes into contact with the inner wall surface of the housing,
wherein a clearance is formed between the inner wall surface of the
housing and the outer peripheral surface of the bearing and the
clearance is larger than a radial displacement amount of the
O-ring.
5. The bearing structure according to claim 4, wherein the inner
wall surface of the housing, the bearing, and the O-ring are
configured such that a frictional force between the inner wall
surface of the housing and the O-ring becomes larger than a
rotational force of the rotation body.
6. An electric compressor comprising: the housing; a compressor
impeller which is attached to an end portion of the rotation shaft
and constitutes a part of the rotation body; and the bearing
structure according to claim 4 for supporting the rotation shaft
with respect to the housing.
7. An electric compressor comprising: the housing; a compressor
impeller which is attached to an end portion of the rotation shaft
and constitutes a part of the rotation body; and the bearing
structure according to claim 2 for supporting the rotation shaft
with respect to the housing.
Description
TECHNICAL FIELD
[0001] The present disclosure relates to a bearing structure and an
electric compressor.
BACKGROUND ART
[0002] Conventionally, a bearing structure described in Patent
Documents 1 and 2 is known. The bearing structure described in
Patent Document 1 includes a bearing which supports a shaft of a
fan motor. An O-ring is attached to a groove of an outer race of
the bearing. The O-ring is in contact with a housing. A viscous
fluid is filled between two O-rings. The bearing structure
described in Patent Document 2 includes a bearing which supports a
drive shaft. An O-ring is attached to a groove of an outer race of
the bearing. Highly viscous oil is applied to an outer diameter
surface of the outer race.
CITATION LIST
Patent Literature
[0003] Patent Document 1: Japanese Unexamined Patent Publication
No. 2000-120669
[0004] Patent Document 2: Japanese Unexamined Patent Publication
No. 2007-211865
SUMMARY OF INVENTION
Technical Problem
[0005] In the bearing structure described in Patent Document 1, a
collapse margin of the O-ring is set so that an insertion force of
the bearing at the time of incorporating the bearing attached with
the O-ring into the housing decreases. The insertion force is
defined by a frictional coefficient and a radial force generated by
the collapse margin of the O-ring. That is, the insertion force
deceases when the radial force is decreased. As a result, it is
possible to improve workability when incorporating the bearing. In
the bearing structure described in Patent Document 2, since a
frictional coefficient between the inner diameter surface of the
housing and the outer diameter surface of the outer race decreases,
it is possible to prevent creeping in which the outer race rolls
along the inner diameter surface of the housing.
[0006] In the above-described related art, there is concern that
the transmission of the vibration of the rotation body to the
housing through the bearing cannot be reliably prevented. For
example, when the outer race of the bearing comes into contact with
the housing due to a vibration, the vibration will be transmitted
much more. The present disclosure will describe a bearing structure
capable of reliably preventing a vibration from being transmitted
to a housing through a bearing.
Solution to Problem
[0007] An aspect of the present disclosure provides a bearing
structure for supporting a rotation shaft of a rotation body
accommodated in a housing with respect to the housing, including:
the rotation shaft; a bearing that is attached in the housing to
support the rotation shaft with respect to the housing and includes
an inner race through which the rotation shaft is inserted and an
outer race which includes an annular groove portion formed on an
outer peripheral surface facing an inner wall surface of the
housing; and an O-ring which is disposed on the groove portion of
the outer race of the bearing, protrudes outward in a radial
direction in relation to the outer peripheral surface, and comes
into contact with the inner wall surface of the housing, in which a
clearance is formed between the inner wall surface of the housing
and the outer peripheral surface of the bearing and the clearance
is larger than a radial displacement amount of the O-ring.
Effects of Invention
[0008] According to an aspect of the present disclosure, it is
possible to reliably prevent a vibration from being transmitted to
a housing through a bearing.
BRIEF DESCRIPTION OF DRAWINGS
[0009] FIG. 1 is a cross-sectional view illustrating an electric
compressor according to an embodiment of the present
disclosure.
[0010] FIG. 2 is a partially enlarged cross-sectional view
illustrating a bearing structure of FIG. 1.
[0011] FIG. 3A is a diagram showing a relationship between a
collapse margin of an O-ring and a reaction force of the O-ring and
FIG. 3B is a diagram showing a relationship between a clearance and
the collapse margin of the O-ring.
[0012] FIG. 4A is a diagram showing a relationship between a
clearance and a reaction force of the O-ring and FIG. 4B is a
diagram showing a relationship between the clearance and a spring
constant of the O-ring.
[0013] FIG. 5 is a diagram showing a relationship between a
clearance and a load displacement amount.
[0014] FIG. 6A is a diagram showing a range of a clearance allowing
the O-ring to prevent the rotation of the outer race and FIG. 6B is
a diagram showing a range of a clearance capable of reliably
preventing the transmission of the vibration.
[0015] FIG. 7 is a diagram in which FIGS. 6A and 6B overlap each
other and is a diagram showing a range of a clearance preventing
both of the transmission of the vibration and the rotation of the
outer race.
DESCRIPTION OF EMBODIMENTS
[0016] An aspect of the present disclosure is a bearing structure
for supporting a rotation shaft of a rotation body accommodated in
a housing with respect to the housing, including: the rotation
shaft; a bearing that is attached in the housing to support the
rotation shaft with respect to the housing and includes an inner
race through which the rotation shaft is inserted and an outer race
which includes an annular groove portion formed on an outer
peripheral surface facing an inner wall surface of the housing; and
an O-ring which is disposed on the groove portion of the outer race
of the bearing, protrudes outward in a radial direction in relation
to the outer peripheral surface; and comes into contact with the
inner wall surface of the housing, in which a clearance is formed
between the inner wall surface of the housing and the outer
peripheral surface of the bearing and the clearance is larger than
a radial displacement amount of the O-ring.
[0017] According to the bearing structure, the rotation shaft of
the rotation body is supported by the bearing structure. The O-ring
provided between the outer race of the bearing and the inner wall
surface of the housing exhibits the same function as that of a
spring. When the rotation body rotates, the radial displacement
amount is defined on the basis of the mass of the rotation body and
the spring constant of the O-ring. Since the clearance formed
between the inner wall surface of the housing and the outer
peripheral surface of the bearing is larger than the radial
displacement amount of the O-ring, the contact of the outer race of
the bearing with respect to the housing is prevented. According to
the bearing structure, it is possible to reliably prevent the
transmission of the vibration to the housing through the
bearing.
[0018] In some aspects, the inner wall surface of the housing, the
bearing, and the O-ring are configured such that a frictional force
between the inner wall surface of the housing and the O-ring
becomes larger than a rotational force of the rotation body. In
this case, it is possible to suppress the rotation of the outer
race of the bearing when the rotation body rotates.
[0019] An electric compressor according to another aspect of the
present disclosure includes a housing, a compressor impeller which
is attached to an end portion of the rotation shaft and constitutes
a part of the rotation body; and the bearing structure according to
claim 1 or 2 for supporting the rotation shaft with respect to the
housing. According to the electric compressor, it is possible to
prevent the outer race of the bearing from contacting the housing
when the rotation body including the compressor impeller rotates.
Thus, since it is possible to reliably prevent the transmission of
the vibration to the housing through the bearing, it is possible to
suppress an occurrence of a vibration or noise in the electric
compressor.
[0020] Hereinafter, an embodiment of the present disclosure will be
described with reference to the drawings. Additionally, in the
description of the drawings, the same reference numerals will be
given to the same components and a repetitive description thereof
will be omitted. In the description below, a rotation shaft 12 is
set as a reference in the case of the "axial direction" or the
"radial direction".
[0021] An electric compressor according to an embodiment will be
described with reference to FIG. 1. An electric compressor 1 is
applied to, for example, an internal combustion engine of a vehicle
or a ship. The electric compressor 1 includes a compressor 7. The
electric compressor 1 rotates a compressor impeller 8 by an
interaction of a rotor portion 13 and a stator portion 14 and
compresses a fluid such as air to generate compressed air.
[0022] The electric compressor 1 may be connected to, for example,
a turbocharger (not illustrated) applied to an internal combustion
engine of a vehicle or a ship. In that case, the electric
compressor 1 sends a compressed fluid such as compressed air to a
compressor of the turbocharger. By the combination of the electric
compressor 1 and the turbocharger, the electric compressor 1
assists the startup of the turbocharger.
[0023] The electric compressor 1 includes the rotation shaft 12
which is rotatably supported inside a housing 2 and the compressor
impeller 8 which is fastened to a front end portion 12a of the
rotation shaft 12. The housing 2 includes a motor housing 3 which
accommodates the rotor portion 13 and the stator portion 14 and an
end wall 3a which closes an opening at a second end side (which is
the right side of the drawing and is the side opposite to the
compressor impeller 8) of the motor housing 3. A compressor housing
6 which accommodates the compressor impeller 8 is provided at a
first end side (which is the left side of the drawing and is the
side of the compressor impeller 8) of the motor housing 3. The
compressor housing 6 includes a suction port 9, a scroll portion
10, and a discharge port 11. For example, an inverter 19 for
supplying a current to the stator portion 14 may be provided at the
outside of the end wall 3a.
[0024] The rotor portion 13 is attached to a center portion of the
rotation shaft 12 in the axial direction and includes one or plural
permanent magnets (not illustrated) attached to the rotation shaft
12. The stator portion 14 is attached to an inner surface of the
motor housing 3 to surround the rotor portion 13 and includes a
coil portion (not illustrated). When an AC current flows to the
coil portion of the stator portion 14, the rotation shaft 12 and
the compressor impeller 8 rotate together about a rotation axis A
by the interaction of the rotor portion 13 and the stator portion
14. When the compressor impeller 8 rotates, the compressor 7 sucks
external air through the suction port 9, compresses air through the
scroll portion 10, and sends compressed air from the discharge port
11. The compressed air discharged from the discharge port 11 is
supplied to the above-described internal combustion engine.
[0025] The electric compressor 1 includes two bearings 20 which
rotatably support the rotation shaft 12 with respect to the housing
2. The bearing 20 is attached in the motor housing 3 of the housing
2. The bearing 20 supports the rotation shaft 12 to the motor
housing 3 at both ends thereof. The first bearing 20 is provided in
a sleeve portion 17 formed at the side of the compressor impeller 8
of the motor housing 3. The second bearing 20 is provided in a
sleeve portion 18 protruding from the end wall 3a in the axial
direction (toward the compressor impeller 8). For example, the
compressor impeller 8 is attached to the rotation shaft 12 by a
shaft end nut 16 provided in the front end portion 12a of the
rotation shaft 12.
[0026] The rotation shaft 12, the compressor impeller 8 fixed to
the rotation shaft 12, the rotor portion 13, and the bearing 20 are
integrated with one another inside the housing 2 to constitute a
rotation body C. Each of the rotation shaft 12, the compressor
impeller 8, the rotor portion 13, and the bearing 20 constitutes a
part of the rotation body C. The rotation body C is biased to one
side in the axial direction while being accommodated in the motor
housing 3. An annular wall surface 17b (see FIG. 2) of the sleeve
portion 17 faces and contacts an end surface of the bearing 20 in
the axial direction, so that the rotation body C is positioned in
the axial direction.
[0027] In the electric compressor 1 of the embodiment, the
vibration caused by the rotation of the rotation body C is
suppressed. More specifically, the transmission of the vibration of
the rotation body C to the housing 2 is prevented, so that the
vibration of the electric compressor 1 is suppressed. In order to
prevent the transmission of the vibration, the electric compressor
1 has a bearing structure including the bearing 20. The bearing
structures provided at two positions of the rotation shaft 12 in
the axial direction have the same configuration. Each bearing
structure supports the rotation shaft 12 of the rotation body C to
the motor housing 3.
[0028] Hereinafter, the first bearing 20 and the bearing structure
provided at the first end side will be described. A description of
the second bearing 20 and the bearing structure provided at the
second end side will be omitted. The arrangement of the second
bearing 20 with respect to the sleeve portion 18 may be the same as
the arrangement of the first bearing 20 with respect to the sleeve
portion 17.
[0029] The bearing 20 is, for example, a ball bearing. More
specifically, the bearing 20 is, for example, a grease lubricating
type radial bearing. The bearing 20 may be a deep groove bearing or
an angular bearing.
[0030] As illustrated in FIG. 2, the bearing 20 includes an inner
race 21 through which the rotation shaft 12 is inserted and an
outer race 22 which is relatively rotatable with respect to the
inner race 21 through a plurality of balls 23. The inner race 21 is
press-fitted to, for example, the rotation shaft 12. An inner
peripheral surface 21a of the inner race 21 is in contact with an
outer peripheral surface 12b of the rotation shaft 12. An end
surface at the side of the compressor impeller 8 of the inner race
21 may be in contact with an end surface perpendicular to the
rotation axis A of a boss portion 8a of the compressor impeller
8.
[0031] The sleeve portion 17 of the motor housing 3 includes a
cylindrical inner peripheral surface (inner wall surface) 17a which
faces inwardly in the radial direction. The sleeve portion 17
supports the outer race 22. The outer race 22 includes an outer
peripheral surface 22a which faces the inner peripheral surface 17a
of the sleeve portion 17 and two annular groove portions 22c which
are formed in the outer peripheral surface 22a. The diameter of the
outer peripheral surface 22a of the outer race 22 is smaller than
that of the inner peripheral surface 17a of the sleeve portion 17.
For example, a cylindrical clearance B is formed between the inner
peripheral surface 17a of the sleeve portion 17 and the outer
peripheral surface 22a of the outer race 22. The end surface at the
side of the compressor impeller 8 of the outer race 22 may be in
contact with the wall surface 17b perpendicular to the rotation
axis A in the annular portion disposed at the outer peripheral side
of the boss portion 8a of the compressor impeller 8. Additionally,
the shape of the clearance B can be changed in response to the
displacement of the rotation body C during the operation of the
electric compressor 1.
[0032] Two groove portions 22c are formed to be separated from each
other in the axial direction. Each groove portion 22c is continuous
to the outer peripheral surface 22a and opens outwardly in the
radial direction. An annular O-ring 30 is disposed in each groove
portion 22c. The O-ring 30 is directly fitted to the outer race 22.
The O-ring 30 is formed of an elastic material. The O-ring 30 is
formed of, for example, rubber. The inner peripheral surface of the
O-ring 30 fitted to the groove portion 22c is in contact with the
bottom surface of the groove portion 22c. A part of the outer
peripheral side of the O-ring 30 protrudes outwardly in the radial
direction in relation to the outer peripheral surface 22a. An
annular outer peripheral end surface which is most distant from the
rotation axis A in the O-ring 30 is in contact with the inner
peripheral surface 17a of the sleeve portion 17.
[0033] The O-ring 30 has, for example, a circular cross-section in
a natural state (a state not receiving any external force) before
the O-ring is disposed between the hearing 20 and the sleeve
portion 17. The O-ring 30 which is fitted between the groove
portion 22c of the bearing 20 and the inner peripheral surface 17a
of the sleeve portion 17 is compressed (collapsed). The compressed
O-ring 30 has, for example, a non-circular cross-section. The size
of the clearance B is set in consideration of the diameter (the
wire diameter) of the cross-section of the O-ring 30, the collapse
margin of the O-ring 30, and the spring characteristics of the
collapsed O-ring 30. The size of the clearance B is not limited to
these components and may be set in consideration of, for example,
the hardness of the O-ring 30. Additionally, the term of the
"collapse margin" is the same concept as the "collapse amount" or
the "collapse rate". The term of the "collapse" is the same concept
as the "compression".
[0034] Referring to FIGS. 3 to 7, a concept of the size of the
clearance B will be described. First, when the O-ring 30 has three
kinds of wire diameters as shown in FIG. 3A, a reaction force
becomes different in accordance with the wire diameter, the inner
diameter, and the hardness even in the same collapse margin. The
inclination of the tangent line L of each curve shown in FIG. 3A
indicates the spring constant of the O-ring 30.
[0035] This relationship is expressed by the following Equation
(1).
[Equation 1]
F=.lamda.*.kappa./D*d0*(ax.sup.2+bx+c) (1)
[0036] Here, F indicates the reaction force of the O-ring 30, x
indicates the collapse margin of the O-ring 30, a, b, and c
indicate coefficients when the wire diameter of the O-ring 30 is 1
mm (here, the coefficient is different according to the material
and/or hardness), D indicates the wire diameter of the O-ring 30,
d0 indicates the diameter of the O-ring 30, and k indicates a
coefficient.
[0037] Here, the collapse margin x of the O-ring 30 is expressed by
the following Equation (2) from the dimensional relationship shown
in FIG. 2.
[ Equation 2 ] x = D - Y - X 2 ( 2 ) ##EQU00001##
[0038] Here, X indicates the diameter of the bottom surface of the
groove portion 22c and Y indicates the inner diameter of the sleeve
portion 17.
[0039] The radial size .delta. of the clearance B is also expressed
by the following Equation (3) from the dimensional relationship
shown in FIG. 2.
[ Equation 3 ] .delta. = Y - Z 2 ( 3 ) ##EQU00002##
[0040] Here, Z indicates the outer diameter of the outer race 22
(the diameter of the outer peripheral surface 22a).
[0041] From Equations (2) and (3), a relationship between the
radial size .delta. of the clearance B and the collapse margin x of
the O-ring 30 is expressed by the following Equation (4).
[Equation 4]
x=D-(Y-X)/2=D-(2*.delta.+Z-X)/2 (4)
[0042] Here, when the diameter X of the seat surface of the groove
portion 22c, the wire diameter D of the O-ring 30, and the outer
diameter Z of the outer race 22 are given values, Equation (4) is
expressed as shown in FIG. 3B. Additionally, FIG. 2 illustrates the
wire diameter D of the O-ring 30 in a compressed state in order to
easily understand the structure with reference to the drawings, but
this is not precisely accurate. The wire diameter D is a diameter
of the wire portion of the O-ring 30 in a natural state. Further,
each of the dimensions X, Y, and Z is a diameter based on the
rotation axis A.
[0043] As shown in FIG. 3B, the collapse margin x of the O-ring 30
decreases when the radial size .delta. of the clearance B
increases. Further, the spring force of the O-ring 30 decreases
when the radial size .delta. of the clearance B increases as shown
in FIG. 4A on the basis of the relationship of FIG. 3A and the
relationship of FIG. 3B. Furthermore, the frictional force Fr
between the O-ring 30 and the inner peripheral surface 17a of the
sleeve portion 17 is the product of the frictional coefficient .mu.
of the O-ring 30 and the drag force of the spring force F of the
O-ring 30 of the rotation shaft 12. Thus, the frictional force Fr
also decreases when the spring force F decreases.
[0044] Meanwhile, a value obtained by dividing the frictional
torque T.sub.f in the rotation direction generated in the boundary
portion between the outer race 22 and the inner race 21 of the
bearing 20 in accordance with the rotation of the rotation shaft 12
by the radius R based on the rotation axis A of the outer
peripheral surface 22a of the outer race 22 is set as the
rotational force Ft. The frictional torque T.sub.f can be changed
in accordance with the viscosity v of the grease, the rolling
contact friction of the rolling elements, and the like in addition
to the rotation speed of the rotation shaft 12.
[0045] Here, a condition that prevents the rotation of the outer
race 22 (and the O-ring 30) is that the frictional force Fr is
larger than the rotational force Ft. That is, the establishment of
the following Equation (5) becomes a first condition.
[Equation 5]
Fr/Ft>1 (5)
[0046] The inner peripheral surface 17a of the sleeve portion 17 of
the motor housing 3, the bearing 20, and the O-ring 30 are set such
that the frictional force Fr between the inner peripheral surface
17a and the O-ring 30 becomes larger than the rotational force Ft
of the rotation body C. In FIG. 6A, the rotation of the outer race
22 is prevented when the clearance is 1.0 or more.
[0047] Meanwhile, since the spring constant K is the inclination of
Equation (1) (that is, the differentiation of Equation (1)), the
following Equation (6) is established.
[Equation 6]
K=.pi.*.kappa./D*d0*(2ax+b) (6)
[0048] Here, the collapse margin x of the O-ring 30 decreases when
the radial size .delta. of the clearance B increases from the
relationship (Equation (4)) of FIG. 3B. Further, the spring
constant K decreases when the collapse margin x of the O-ring 30
decreases according to Equation (6). Thus, as shown in FIG. 4B, the
spring constant K decreases when the clearance B (size .delta.)
increases.
[0049] The displacement amount r is expressed by the following
Equation (7) from the relationship of M*g*r=1/2*K*r.sup.2.
[ Equation 7 ] r = 2 M g K ( 7 ) ##EQU00003##
[0050] Here, K indicates the spring constant of the O-ring 30, Mg
indicates a load applied to the bearing 20 (rotor mass
load+eccentric load+vibration load received by the bearing 20), and
g indicates gravity acceleration.
[0051] By applying Equations (2) and (6) to Equation (7), the
following Equation (8) is established.
[ Equation 8 ] r = 2 M g .pi. .kappa. / D d 0 ( a ( D - ( Y - X ) +
b ) ) ( 8 ) ##EQU00004##
[0052] A condition that prevents the outer race 22 from contacting
the sleeve portion 17 is that the radial size .delta. of the
clearance B is larger than the displacement amount r. Thus, the
establishment of the following Equation (9) from Equations (3) and
(8) becomes a second condition.
[ Equation 9 ] Y - Z 2 > 2 M g .pi. .kappa. / D d 0 ( a ( D - (
Y - X ) + b ) ) ( 9 ) ##EQU00005##
[0053] The following equation needs to be established according
to
[0054] Equation (9).
[ Equation 10 ] .delta. / r = ( ( Y - Z ) / 2 ) / 2 M g .pi.
.kappa. / D d 0 ( a ( D - ( Y - X ) + b ) ) > 1 ( 10 )
##EQU00006##
[0055] This corresponds to a range indicated by the arrow in FIG.
6B.
[0056] As shown in FIG. 4A, when the clearance B increases even in
the case of the same load, the spring force decreases and hence the
load displacement amount increases. As shown in FIG. 5, in a case
in which the displacement amount r (the load displacement amount)
becomes larger than the size .delta. of the clearance B, the outer
peripheral surface 22a of the outer race 22 of the bearing 20 comes
into contact with the inner peripheral surface 17a of the sleeve
portion 17 when the load displacement occurs. This may cause a
vibration or noise.
[0057] Here, when the relationship (the second condition) shown in
Equation (10) is established, the outer peripheral surface 22a of
the outer race 22 does not come into contact with the inner
peripheral surface 17a of the sleeve portion 17.
[0058] Then, as shown in FIG. 6A, in order to cause the O-ring 30
to stop the rotation of the outer race 22 from the first condition,
the range of the clearance needs to be in the range indicated by
the arrow of the drawing. Further, as shown in. FIG. 6B, in order
to effectively suppress the vibration from the second condition,
the range of the clearance needs to be in the range indicated by
the arrow of the drawing.
[0059] From FIGS. 6A and 6B, the clearance B of the range indicated
by the arrow of FIG. 7 is set in order to realize both of the first
condition, that is, the condition of stopping the rotation of the
outer race 22 and the second condition, that is, the condition of
suppressing the vibration. In the embodiment, the size .delta. of
the clearance B is set in the range of realizing both of the
rotation stop and the vibration suppression in consideration of the
rotation load and the load applied to the O-ring 30 in this way.
The point of realizing both of these is the characteristic of the
embodiment.
[0060] According to the embodiment, the rotation shaft 12 of the
rotation body C is supported by the bearing structure. The O-ring
30 provided between the outer race 22 of the bearing 20 and the
inner peripheral surface 17a of the motor housing 3 has the same
function as that of the spring with respect to the radial load.
When the rotation body C rotates, the radial displacement amount is
defined on the basis of the mass, the eccentric load, and the
vibration of the rotation body C and the spring constant of the
O-ring 30. Since the clearance B formed between the inner
peripheral surface 17a of the housing 2 and the outer peripheral
surface 22a of the bearing 20 is larger than the radial
displacement amount of the O-ring 30, it is possible to prevent the
outer race 22 of the bearing 20 from contacting the sleeve portion
17. According to the bearing structure, it is possible to reliably
prevent the transmission of the vibration to the housing 2 through
the hearing 20. No impact load is applied to the sleeve portion 17
and a damped load is applied thereto.
[0061] In the above-described patent document, there is a document
in which the spring force and the rotational friction force of the
O-ring are considered. However, regarding the vibration
suppression, there is no disclosure on the point of setting the
collapse margin of the O-ring by focusing on the relationship
between the load displacement amount and the clearance. In the
embodiment, since the collision margin of the O-ring 30 is set by
focusing on these two points, there is an advantageous effect of
compatibility between the vibration reduction and the rotation stop
function.
[0062] Since the frictional force between the inner peripheral
surface 17a of the housing 2 and the O-ring 30 is larger than the
rotational force of the rotation body C, it is possible to suppress
the rotation of the outer race 22 of the bearing 20 when the
rotation body C rotates. Particularly, in the electric compressor 1
of which the rotation speed can be abruptly increased, it is
important to stop the rotation of the outer race 22.
[0063] According to the electric compressor 1, it is possible to
prevent the outer race 22 of the bearing 20 from contacting the
housing 2 when the rotation body C including the compressor
impeller 8 rotates. Thus, since it is possible to reliably prevent
the transmission of the vibration to the housing 2 through the
bearing 20, it is possible to suppress an occurrence of a vibration
or noise in the electric compressor 1.
[0064] Although the embodiment of the present disclosure has been
described above, the invention is not limited to the
above-described embodiment. For example, two bearings 20 may be
provided and one of them may not be provided with the bearing
structure. One of two bearings 20 may be omitted. When the bearing
structure is provided only at one position, the bearing structure
may be provided only at the first end side of the rotation shaft 12
or the second end side of the rotation shaft 12.
[0065] A relationship between the frictional force between the
inner peripheral surface 17a and the O-ring 30 and the rotational
force of the rotation body C may not satisfy a relationship shown
in the above-described embodiment. That is, the bearing structure
which satisfies the second condition but does not satisfy the first
condition may be employed. Also in this case, it is possible to
obtain an effect that the transmission of the vibration to the
housing 2 is reliably prevented.
[0066] The cross-sectional shape of the O-ring 30 is not limited to
the circular shape.
INDUSTRIAL APPLICABILITY
[0067] According to some aspects of the present disclosure, it is
possible to reliably prevent the transmission of the vibration to
the housing through the bearing.
REFERENCE SIGNS LIST
[0068] 1: electric compressor, 2: housing, 3: motor housing, 6:
compressor housing, 7: compressor, 8: compressor impeller, 12:
rotation shaft, 13: rotor portion, 14: stator portion, 17a: inner
peripheral surface (inner wall surface), 20: bearing, 21: inner
race, 21a: inner peripheral surface, 22: outer race, 22a: outer
peripheral surface, 22c: groove portion, 23: ball, 30: O-ring, A:
rotation axis, B: clearance, C: rotation body.
* * * * *