U.S. patent application number 16/515120 was filed with the patent office on 2020-01-23 for liquid discharge device.
The applicant listed for this patent is Seiko Epson Corporation. Invention is credited to Shunya FUKUDA, Hiroki MIYAJIMA.
Application Number | 20200023644 16/515120 |
Document ID | / |
Family ID | 67402825 |
Filed Date | 2020-01-23 |
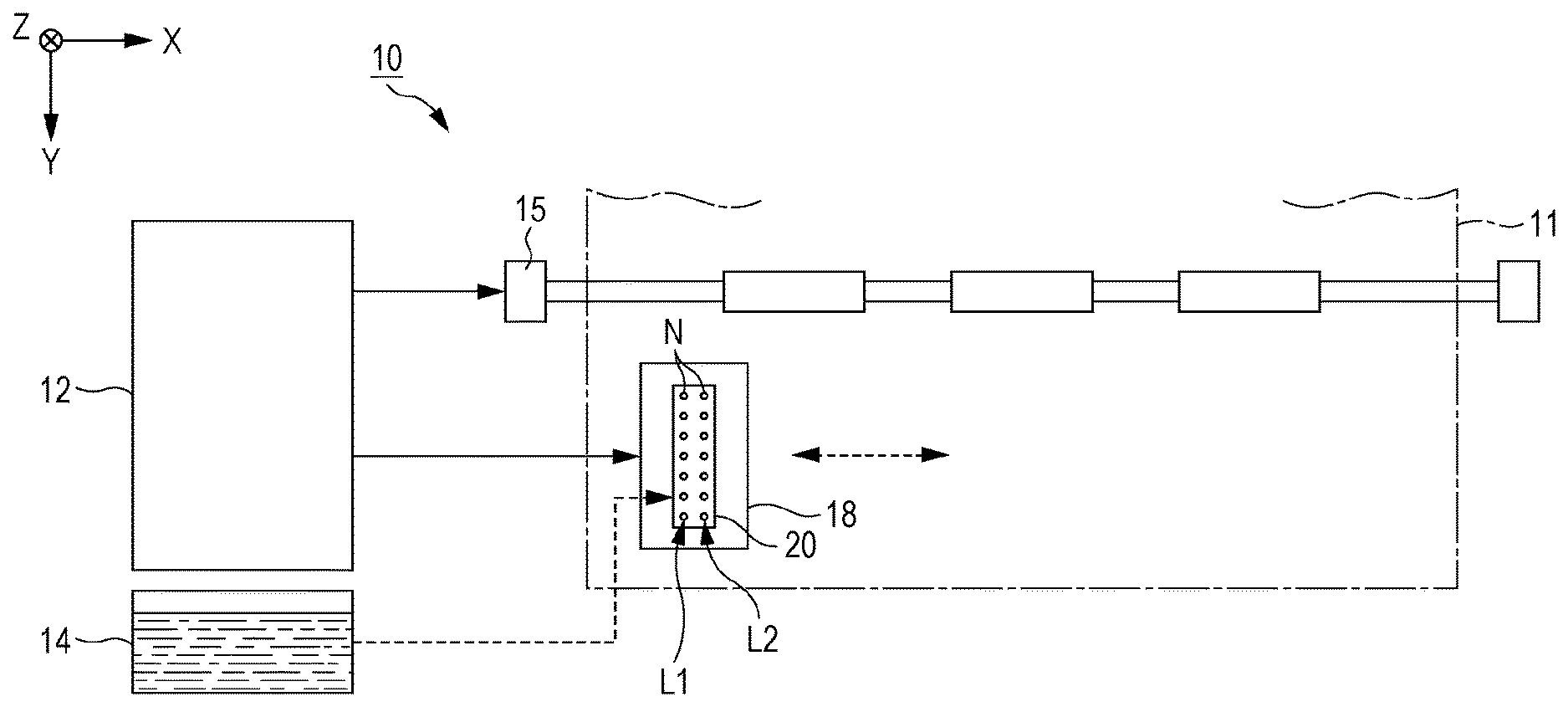



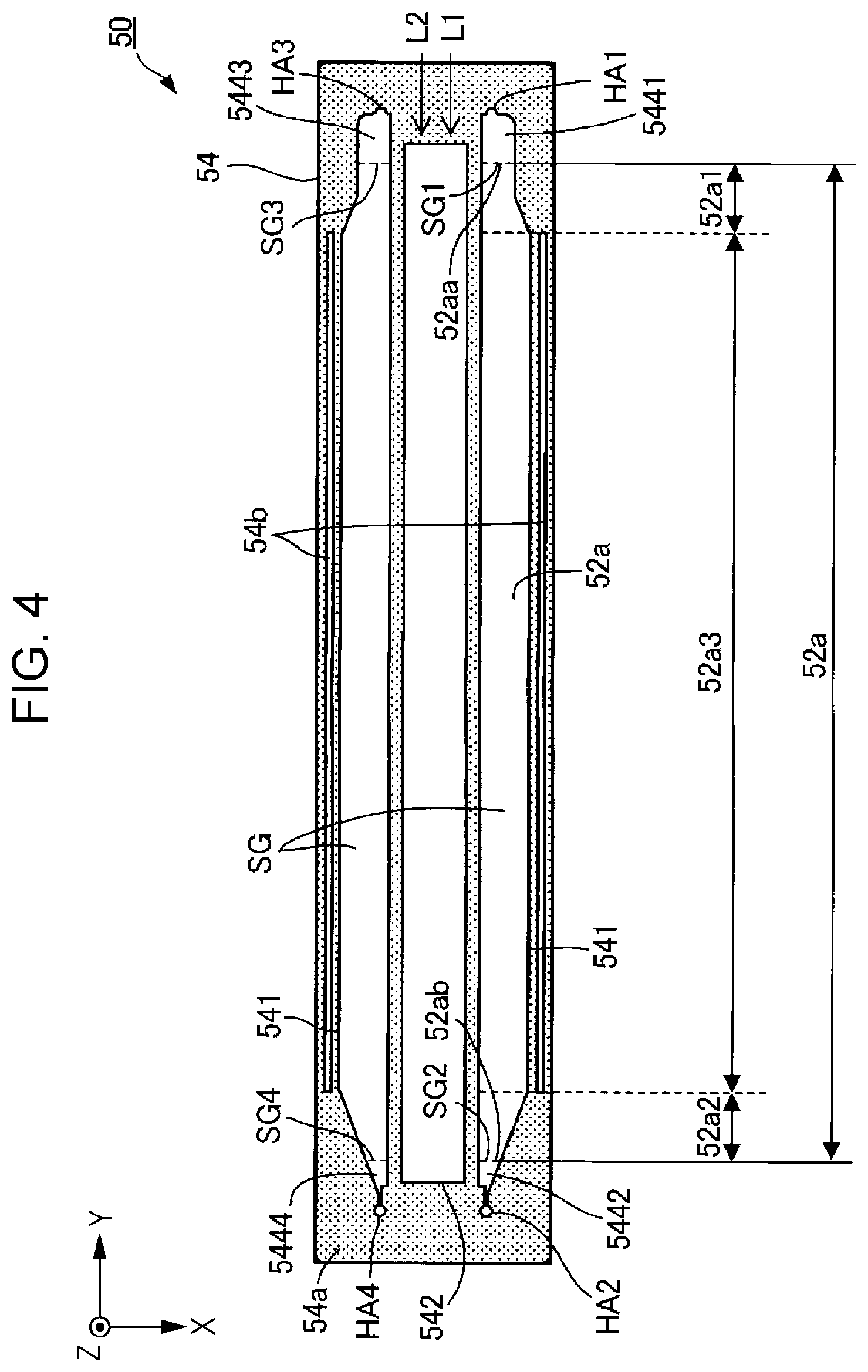

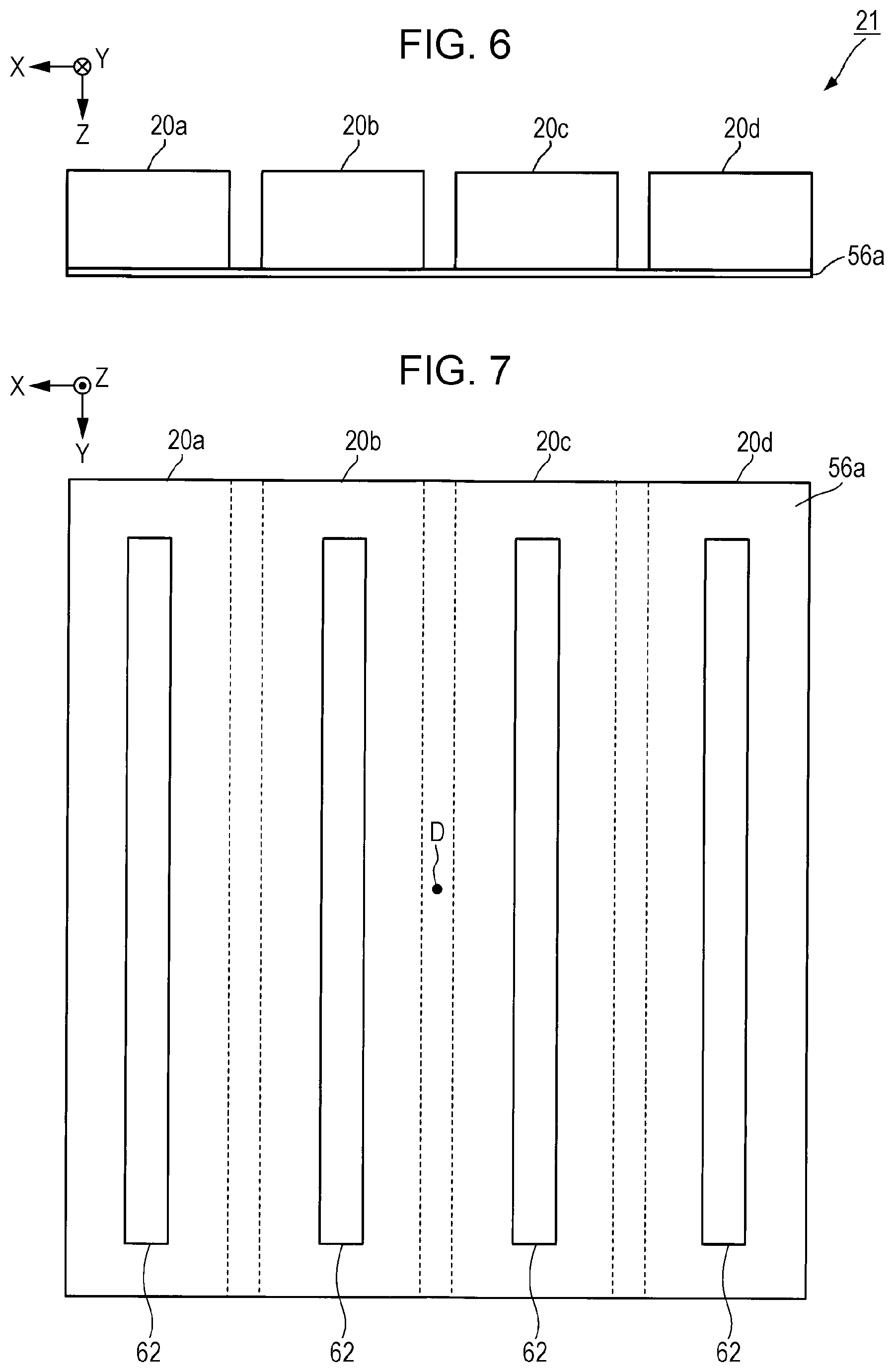

United States Patent
Application |
20200023644 |
Kind Code |
A1 |
FUKUDA; Shunya ; et
al. |
January 23, 2020 |
LIQUID DISCHARGE DEVICE
Abstract
A liquid discharge device includes a channel member, a nozzle
plate, a flexible film, a support, and a lid. The channel member
has a storage chamber that stores liquid. The nozzle plate has a
nozzle through which the liquid stored in the storage chamber is
discharged. The flexible film forms part of walling of the storage
chamber. The support has an opening that surrounds a space where
the flexible film is exposed at a side of the flexible film
opposite the storage chamber. The lid is configured to cover the
flexible film across the space, and is bonded, by an adhesive, to a
surface of the support. The support has a groove provided in the
surface bonded to the lid. The adhesive is also disposed in the
groove.
Inventors: |
FUKUDA; Shunya; (Azumino,
JP) ; MIYAJIMA; Hiroki; (Matsumoto, JP) |
|
Applicant: |
Name |
City |
State |
Country |
Type |
Seiko Epson Corporation |
Tokyo |
|
JP |
|
|
Family ID: |
67402825 |
Appl. No.: |
16/515120 |
Filed: |
July 18, 2019 |
Current U.S.
Class: |
1/1 |
Current CPC
Class: |
B41J 2/1623 20130101;
Y10T 29/49401 20150115; B41J 2/14233 20130101; B41J 2202/20
20130101; B41J 2202/11 20130101; B41J 2002/14419 20130101; B41J
2002/14491 20130101; B41J 2/161 20130101; B41J 2002/14241 20130101;
B41J 2/16505 20130101; B41J 2202/19 20130101 |
International
Class: |
B41J 2/165 20060101
B41J002/165; B41J 2/14 20060101 B41J002/14 |
Foreign Application Data
Date |
Code |
Application Number |
Jul 19, 2018 |
JP |
2018-135435 |
Claims
1. A liquid discharge device comprising: a channel member having a
storage chamber that stores liquid; a nozzle plate having a nozzle
through which the liquid stored in the storage chamber is
discharged; a flexible film configured to form part of walling of
the storage chamber; a support having an opening configured to
surround a space where the flexible film is exposed at a side of
the flexible film opposite the storage chamber; and a lid
configured to cover the flexible film across the space, the lid
being bonded, by an adhesive, to a surface of the support, wherein,
the support has a groove provided in the surface bonded to the lid,
and wherein the adhesive is also disposed in the groove.
2. The liquid discharge device according to claim 1, wherein a
liquid discharge head that discharges the liquid includes the
channel member, the nozzle plate, the flexible film, the support,
and the lid, wherein the space and the flexible film extend along a
first axis, wherein one end of the space along the first axis
communicates with a first communication passage that communicates
with outside of the liquid discharge head, wherein another end of
the space along the first axis communicates with a second
communication passage that communicates with the outside, wherein
the flexible film includes a first flexible region including one
end of the flexible film along the first axis and a second flexible
region including another end of the flexible film along the first
axis, and wherein, along a second axis that intersects both the
first axis and a thickness axis of the flexible film, a smallest
width of the second flexible region is smaller than a smallest
width of the first flexible region.
3. The liquid discharge device according to claim 1, wherein the
space extends along a first axis, and wherein the groove extends
along the first axis without being separated.
4. The liquid discharge device according to claim 1, further
comprising: a regulating member located between the flexible film
and the lid in the space so as to regulate contact between the
flexible film and the lid, wherein the regulating member is
provided separately from the support plate.
5. The liquid discharge device according to claim 2, wherein the
storage chamber is a first storage chamber, wherein the channel
member is a first channel member, wherein the flexible film is a
first flexible film, wherein the space is a first space, wherein
the opening is a first opening, wherein the support is a first
support, wherein the liquid discharge device further includes a
second channel member having a second storage chamber that is
disposed beside the first storage chamber along the second axis, a
second flexible film that forms part of walling of the second
storage chamber, and a second support having a second opening that
surrounds a second space where the second flexible film is exposed
at a side of the second flexible film opposite the second storage
chamber, wherein the lid is configured to cover the second flexible
film across the second space, the lid being bonded, by the
adhesive, to a surface of the second support, wherein the liquid
discharge head further includes the second channel member, the
second flexible film, and the second support, wherein the second
space and the second flexible film extend along the first axis,
wherein one end of the second space along the first axis
communicates with a third communication passage that communicates
with the outside, wherein another end of the second space along the
first axis communicates with a fourth communication passage that
communicates with the outside, wherein the second flexible film
includes a third flexible region including one end of the second
flexible film along the first axis and a fourth flexible region
including another end of the second flexible film along the first
axis, wherein, along the second axis, a smallest width of the
fourth flexible region is smaller than a smallest width of the
third flexible region, and wherein, when seen along the second
axis, at least part of the first flexible region and at least part
of the third flexible region overlap, and at least part of the
second flexible region and at least part of the fourth flexible
region overlap.
6. The liquid discharge device according to claim 1, wherein a
liquid discharge head that discharges the liquid includes the
channel member, the nozzle plate, the flexible film, the support,
and the lid, wherein the space and the flexible film extend along a
first axis, wherein one end of the space along the first axis
communicates with a first communication passage that communicates
with outside of the liquid discharge head, wherein another end of
the space along the first axis communicates with a second
communication passage that communicates with the outside, wherein
the flexible film includes a first flexible region including one
end of the flexible film along the first axis and a second flexible
region including another end of the flexible film along the first
axis, and wherein a shape of the first flexible region is different
from a shape of the second flexible region.
Description
[0001] The present application is based on, and claims priority
from, JP Application Serial Number 2018-135435, filed Jul. 19,
2018, the disclosure of which is hereby incorporated by reference
herein in its entirety.
BACKGROUND
1. Technical Field
[0002] The present disclosure relates to a liquid discharge
device.
2. Related Art
[0003] A liquid discharge device discharges from a nozzle liquid
such as ink stored in a storage chamber. In the liquid discharge
device, pressure variation in the storage chamber may affect
discharge of the liquid from the nozzle. A liquid discharge device
described in JP-A-2015-057315 has a storage chamber having walling
partially formed by a flexible film. The pressure variation in the
storage chamber is absorbed by deformation of the flexible film.
This liquid discharge device has a space that accommodates the
deformation of the flexible film on a side of the flexible film
opposite the storage chamber. The space is defined by a support
having an opening and a lid bonded to the support by an adhesive so
as to cover the opening.
[0004] In order to more firmly bond the lid and the support to each
other, there is contemplated a structure in which the sizes of
surfaces of the lid and the support that face each other are
increased, more specifically, the sizes of the surfaces where the
adhesive is applied are increased. However, when the sizes of the
surfaces of the lid and the support facing each other are
increased, for example, a gap is likely to be formed between the
lid and the support due to, for example, distortion of the facing
surfaces or the like. When such a gap is formed, there is a problem
in that clogging of the nozzle or other troubles are likely to
occur because of an increase in viscosity of the liquid resulting
from evaporation of water in the storage chamber through this gap
and the flexible film.
SUMMARY
[0005] To address the above-described problem, according to an
aspect of the present disclosure, a liquid discharge device
includes a channel member, a nozzle plate, a flexible film, a
support, and a lid. The channel member has a storage chamber that
stores liquid. The nozzle plate has a nozzle through which the
liquid stored in the storage chamber is discharged. The flexible
film forms part of walling of the storage chamber. The support has
an opening that surrounds a space where the flexible film is
exposed at a side of the flexible film opposite the storage
chamber. The lid is bonded, by an adhesive, to a surface of the
support on a side of the support opposite the flexible film so as
to cover the opening. In the surface of the support, a groove is
provided at a position opposite the nozzle with the space
interposed therebetween. The adhesive is also disposed in the
groove.
BRIEF DESCRIPTION OF THE DRAWINGS
[0006] FIG. 1 illustrates the structure of a liquid discharge
device according to a first embodiment.
[0007] FIG. 2 is an exploded perspective view of a liquid discharge
head.
[0008] FIG. 3 is a sectional view of the liquid discharge head
illustrated in FIG. 2 taken along line III-III.
[0009] FIG. 4 is a plan view of a compliance plate.
[0010] FIG. 5 is a plan view of a compliance plate according to a
second embodiment.
[0011] FIG. 6 illustrates a head unit used for a third
embodiment.
[0012] FIG. 7 illustrates arrangement of a first liquid discharge
head, a second liquid discharge head, a third liquid discharge
head, and a fourth liquid discharge head in the X-Y plane.
[0013] FIG. 8 illustrates the arrangement of the first liquid
discharge head, the second liquid discharge head, the third liquid
discharge head, and the fourth liquid discharge head in the X-Y
plane of the respective compliance plates.
DESCRIPTION OF EXEMPLARY EMBODIMENTS
First Embodiment
[0014] FIG. 1 illustrates a structure that exemplifies a liquid
discharge device 10 according to a first embodiment. The liquid
discharge device 10 is an ink jet printer that discharges ink
exemplifying liquid to a medium 11. Typically, the medium 11 is a
printing paper. However, as the medium 11, a printing target formed
of any material such as a resin film or cloth may be used. A liquid
container 14 in which the ink is stored is provided in the liquid
discharge device 10. As the liquid container 14, for example, a
cartridge removably mountable to the liquid discharge device 10, a
bag-shaped ink pack formed of a flexible film, or an ink tank able
to be replenished with the ink is used. The ink stored in the
liquid container 14 may be a black ink or a color ink.
[0015] The liquid discharge device 10 includes a controller 12, a
transport mechanism 15, a carriage 18, and a liquid discharge head
20. The controller 12 includes, for example, a processing circuit
such as a central processing unit (CPU) or a field programmable
gate array (FPGA) and a storage circuit such as semiconductor
memory. The controller 12 controls the elements of the liquid
discharge device 10 in a centralized manner. The transport
mechanism 15 transports the medium 11 in the Y direction under the
control of the controller 12. The Y direction is an example of a
first axis.
[0016] The liquid discharge head 20 is mounted in the carriage 18.
Although a single liquid discharge head 20 is mounted in the
carriage 18 in the example illustrated in FIG. 1, a plurality of
liquid discharge heads 20 may be mounted in the carriage 18. The
carriage 18 causes the liquid discharge head 20 to reciprocate
between the positive side and the negative side in the X direction
under the control of the controller 12. The X direction is
perpendicular to the Y direction in which the medium 11 is
transported. The X direction is an example of a second axis. The
liquid container 14 may be mounted in the carriage 18 together with
the liquid discharge head 20.
[0017] The liquid discharge head 20 discharges the ink supplied
from the liquid container 14 from a plurality of nozzles N to the
medium 11 under the control of the controller 12. When the liquid
discharge head 20 discharges the ink to the medium 11 in parallel
with transportation of the medium 11 performed by the transport
mechanism 15 and repetitive reciprocation of the carriage 18, a
desired image is formed on the surface of the medium 11. A
direction perpendicular to the X-Y plane is represented as the Z
direction. A direction in which the ink is discharged by the liquid
discharge head 20 corresponds to the Z direction. The X-Y plane is
parallel to, for example, the surface of the medium 11.
[0018] FIG. 2 is an exploded perspective view of the liquid
discharge head 20. FIG. 3 is a sectional view taken along line
III-III illustrated in FIG. 2. As exemplified in FIG. 2, the liquid
discharge head 20 includes the plurality of nozzles N arranged in
the Y direction. The plurality of nozzles N are grouped into a
first row L1 and a second row L2. The second row L2 and the first
row L1 are arranged in the X direction with a space therebetween.
Each of the first row L1 and the second row L2 is a corresponding
one of sets of a plurality of the nozzles N arranged linearly in
the Y direction. The positions of the nozzles N of the first row L1
in the Y direction can be different from the positions of the
nozzles N of the second row L2 in the Y direction. However, in the
following example structure, for convenience of description, the
positions of the nozzles N of the first row L1 in the Y direction
are coincident with the positions of the nozzles N of the second
row L2 in the Y direction. As can be understood from FIG. 3, the
liquid discharge head 20 has a structure in which elements
associated with the nozzles N of the first row L1 and elements
associated with the nozzles N of the second row L2 are
substantially symmetrically arranged about line O-O.
[0019] As exemplified in FIGS. 2 and 3, the liquid discharge head
20 includes a channel forming unit 30. The channel forming unit 30
is a structure that defines channels for supplying the ink to the
plurality of nozzles N. The channel forming unit 30 is formed by
stacking a channel member 32 and a laminate 38. The laminate 38
includes a pressure chamber substrate 382, a vibrating plate 384,
and a protecting plate 386. The channel member 32, the pressure
chamber substrate 382, the vibrating plate 384, and the protecting
plate 386 are plate-shaped members elongated in the Y direction.
The pressure chamber substrate 382 is secured by, for example, an
adhesive, to the surface of the channel member 32 on the negative
side in the Z direction. The vibrating plate 384 is formed on the
surface on the side of the pressure chamber substrate 382 opposite
the channel member 32. The protecting plate 386 is secured to the
surface on the side of the pressure chamber substrate 382 where no
pressure chamber C, which will be described later, is formed. The
protecting plate 386 may be omitted.
[0020] As exemplified in FIG. 2, a case member 40 is provided on
the negative side of the channel forming unit 30 in the Z
direction. A nozzle plate 62, a compliance plate 50, and a lid 56
are provided on the positive side of the channel forming unit 30 in
the Z direction. The compliance plate 50 includes a flexible film
52 and a support plate 54. The support plate 54 is an example of a
support. In general, the elements of the liquid discharge head 20
are, as is the case with the channel member 32 and the like,
plate-shaped members elongated in the Y direction and bonded to one
another by using, for example, an adhesive.
[0021] The nozzle plate 62 is a plate-shaped member in which the
plurality of nozzles N are provided. The nozzle plate 62 is
provided on the surface of the channel member 32 on the positive
side in the Z direction. Each of the plurality of nozzles N is a
circular through hole that allows the ink passing therethrough. The
plurality of nozzles N included in the first row L1 and the
plurality of nozzles N included in the second row L2 are provided
in the nozzle plate 62. The nozzle plate 62 is manufactured by
processing a silicon (Si) monocrystalline substrate, utilizing, for
example, a semiconductor manufacturing technique, examples of which
include processing techniques such as dry etching and a wet
etching. For the manufacture of the nozzle plate 62, any known
material and manufacturing method can be used.
[0022] As exemplified in FIGS. 2 and 3, for each of the first row
L1 and the second row L2, an inlet 342, a plurality of supply
channels 344, a plurality of communication channels 326, and a
storage chamber 34 are provided in the channel member 32. The inlet
342 is a through hole having an elongated shape extending in the Y
direction in a plan view seen in the Z direction. The supply
channels 344 and the communication channels 326 are through holes.
The supply channels 344 are formed for the respective nozzles N,
and the communication channels 326 are formed for the respective
nozzles N. The storage chamber 34 is a space having an elongated
shape extending in the Y direction in a plan view seen in the Z
direction. The storage chamber 34 allows the inlet 342 and the
plurality of supply channels 344 to communicate with one another.
The ink is stored in the storage chamber 34. Part of walling
defining the storage chamber 34 on the positive side in the Z
direction is formed by the flexible film 52 instead of the channel
member 32. Each of the plurality of communication channels 326 and
a corresponding one of the nozzles N overlap in a plan view seen in
the Z direction.
[0023] The pressure chamber substrate 382 illustrated in FIGS. 2
and 3 is a plate-shaped member having a plurality of the pressure
chambers C for each of the first row L1 and the second row L2. The
pressure chambers C are also referred to as cavities. The plurality
of pressure chambers C are arranged in the Y direction. Each of the
pressure chambers C is formed for a corresponding one of the
nozzles N. Each of the pressure chambers C is a space having an
elongated shape extending in the X direction in a plan view seen in
the Z direction. As is the case with the nozzle plate 62, the
channel member 32 and the pressure chamber substrate 382 are
manufactured by processing a silicon monocrystalline substrate,
utilizing, for example, a semiconductor manufacturing technique.
For the manufacture of the channel member 32 and the pressure
chamber substrate 382, any known material and manufacturing method
can be used.
[0024] The vibrating plate 384 is a plate-shaped member that can
elastically vibrate. The vibrating plate 384 is formed by, for
example, stacking an elastic film formed of an elastic material
such as silicon dioxide (SiO.sub.2) and an insulating film formed
of an insulating material such as zirconium dioxide (ZrO.sub.2).
Part or the entirety of the vibrating plate 384 may be integrally
formed with the pressure chamber substrate 382 by selectively
removing part of a plate-shaped member, along the thickness axis,
having a predetermined thickness in regions corresponding to the
pressure chambers C.
[0025] As can be understood from FIG. 3, the pressure chambers C
are spaces positioned between the channel member 32 and the
vibrating plate 384. The plurality of pressure chambers C are
arranged in the Y direction for each of the first row L1 and the
second row L2. As exemplified in FIG. 3, the pressure chambers C
communicate with the communication channels 326 and the supply
channels 344. Accordingly, the pressure chambers C communicate with
the nozzles N through the communication channels 326 and
communicate with the inlet 342 through the supply channels 344 and
the storage chamber 34.
[0026] A plurality of piezoelectric elements 385 are formed for
each of the first row L1 and the second row L2 on the surface of
the side of the vibrating plate 384 opposite the pressure chambers
C so as to correspond to the different nozzles N. Each of the
piezoelectric elements 385 is a driver element that is deformed
when a drive signal is supplied thereto.
[0027] Each of the piezoelectric elements 385 is a laminate in
which a piezoelectric layer is interposed between two electrodes
facing each other. One of the two electrodes facing each other is a
common electrode that is formed on the surface of the side of the
vibrating plate 384 opposite the pressure chambers C and associated
with the plurality of continuously arranged piezoelectric elements
385. A predetermined reference voltage is supplied to the common
electrode. The other of the two electrodes facing each other is an
individual electrode formed for each of the piezoelectric elements
385. A drive signal that deforms the piezoelectric element 385 is
supplied to each of a plurality of the individual electrodes.
[0028] A part where the two electrodes facing each other and the
piezoelectric layer overlap in a plan view seen in the Z direction
functions as the piezoelectric element 385. When the vibrating
plate 384 vibrates in accordance with deformation of the
piezoelectric element 385, the pressure of the ink in the pressure
chamber C varies. This causes the ink filled in the pressure
chamber C to be discharged to the outside through the communication
channel 326 and the nozzle N. It is noted that the positional
relationship between the two electrodes facing each other may be
reversed, or both of the two electrodes included in the
piezoelectric element 385 may be individual electrodes.
[0029] Similarly to the storage chambers 34 of the channel member
32, the case member 40 stores the ink supplied to the plurality of
pressure chamber C. As exemplified in FIG. 3, the case member 40
has ink openings 42. The ink openings 42 are each provided for a
corresponding one of the first row L1 and the second row L2. In
each of the first row L1 and the second row L2, the ink opening 42
and the inlet 342 communicate with each other. The ink is supplied
to the storage chamber 34 and a space formed by the inlet 342 and
the ink opening 42 through a corresponding one of introduction
openings 43 formed in the case member 40.
[0030] As exemplified in FIGS. 2 and 3, the compliance plate 50 is
provided on the surface of the channel member 32 on the positive
side in the Z direction. The compliance plate 50 is an element that
suppresses variation of the pressure of the ink in the storage
chamber 34. As described above, the compliance plate 50 includes
the flexible film 52 and the support plate 54.
[0031] The flexible film 52 is a film-shaped flexible member. The
flexible film 52 is formed of, for example, polyphenylenesulfide
(PPS), aromatic polyamide (aramid), or the like. The flexible film
52 is thick in the Z direction. The flexible film 52 has a
flexible-film opening 522 for exposing the nozzle plate 62. The
flexible film 52 is disposed on the surface of the side of the
channel member 32 opposite the case member 40 such that the nozzle
plate 62 is exposed from the flexible-film opening 522. The
flexible film 52 forms the part of the walling of the storage
chamber 34 for each of the first row L1 and the second row L2.
[0032] In the example illustrated in FIGS. 2 and 3, the flexible
film 52 forms the bottom of the storage chamber 34 as the part of
the walling of the storage chamber 34. Since the flexible film 52
forms the part of the walling of the storage chamber 34, the
pressure variation of the ink in the storage chamber 34 is likely
to be absorbed by variation of the flexible film 52 compared to the
case where the part of the walling of the storage chamber 34 is not
formed by the flexible film 52. Referring to FIG. 3, the part of
the walling of the storage chamber 34 of the first row L1 and the
part of the walling of the storage chamber 34 of the second row L2
are formed by a single flexible film 52. However, the part of the
walling of each of the storage chambers 34 may be formed of a
corresponding one of separate flexible films 52.
[0033] The support plate 54 is formed of, for example, a metal such
as stainless steel (SUS). The support plate 54 has flexible-film
exposure openings 541 for exposing walling flexible films 52a. The
walling flexible films 52a are portions of the flexible film 52
that each form the part of the walling of the storage chamber 34.
The support plate 54 also has a nozzle-plate exposure opening 542
for exposing the nozzle plate 62. The support plate 54 is provided
on the surface of the side of the flexible film 52 opposite the
storage chambers 34 such that the walling flexible films 52a are
exposed from the flexible-film exposure openings 541 and the nozzle
plate 62 is exposed from the nozzle-plate exposure opening 542.
[0034] As exemplified in FIGS. 2 and 3, the flexible-film exposure
openings 541 at least surround respective spaces SG where the
walling flexible films 52a are exposed. As exemplified in FIG. 2,
the spaces SG and the walling flexible films 52a extend in the Y
direction. According to the present embodiment, no part of the
support plate 54 overlaps the storage chambers 34 in a plan view
seen in the Z direction.
[0035] As exemplified in FIGS. 2 and 3, the lid 56 is provided on
the positive side of the support plate 54 in the Z direction. The
lid 56 is formed of, for example, a metal such as stainless steel
(SUS). The lid 56 has a nozzle-plate opening 622 for exposing the
nozzle plate 62. As exemplified in FIG. 3, the lid 56 is bonded by
an adhesive 57 to a surface 54a of the side of the support plate 54
opposite the flexible film 52 so as to cover the spaces SG such
that the nozzle plate 62 is exposed from the nozzle-plate opening
622. In other words, the lid 56 is bonded by the adhesive 57 to the
surface 54a of the support plate 54 so that the lid 56 covers,
across the spaces SG, the flexible film 52 exposed from the
flexible-film exposure openings 541 that is the walling flexible
films 52a.
[0036] Since the spaces SG are provided, the walling flexible films
52a are likely to vary in accordance with the pressure variation of
the ink in the storage chambers 34 compared to a structure where
the spaces SG are not provided. Furthermore, covering the spaces SG
by the lid 56 can prevent damage to walling flexible films 52a,
which are exposed in the spaces SG, caused by contact of the
walling flexible films 52a with another member.
[0037] The spaces SG each communicate with at least two of first to
fourth external communication openings HA1 to HA4 that communicate
with the outside of the liquid discharge head 20. Thus, air can
move between the spaces SG and the outside of the liquid discharge
head 20 in accordance with the variation of the walling flexible
films 52a, and accordingly, movement of the walling flexible films
52a is facilitated.
[0038] As exemplified in FIG. 3, grooves 54b are provided in the
surface 54a of the support plate 54 bonded to the lid 56, and the
grooves 54b are each provided at a position opposite the nozzles N
with a corresponding one of the spaces SG interposed therebetween.
The adhesive 57 is also disposed in the grooves 54b. FIG. 4
illustrates the surface of the compliance plate 50, which includes
the support plate 54 having the grooves 54b, on the positive side
in the Z direction.
[0039] Since the adhesive 57 flows into the grooves 54b, compared
to a structure in which grooves 54b are not provided, the area by
which the adhesive 57 and the support plate 54 are in contact with
each other increases, and further, an anchor effect is produced by
the adhesive 57 flowing into the grooves 54b. Thus, the strength of
bonding between the lid 56 and the support plate 54 can be
increased. Accordingly, it is not required, for increasing the
strength of bonding between the lid 56 and the support plate 54, to
increase the sizes of a facing surface of the lid 56 and a facing
surface of the support plate 54 where the lid 56 and the support
plate 54 face each other. This can suppress formation of a gap
between the lid 56 and the support plate 54 due to distortion or
the like of the facing surfaces caused by the increase the sizes of
the facing surfaces of the lid 56 and the support plate 54. Thus,
the occurrences of clogging of the nozzles N or other troubles due
to an increase in viscosity of the ink resulting from evaporation
of water in the storage chambers 34 through the gap as described
above and the flexible film 52 can be suppressed.
[0040] In the support plate 54, each of the grooves 54b is provided
at a position opposite the nozzles N with a corresponding one of
the space SG interposed therebetween. Thus, for example, even when
the adhesive 57 flows into only part of one or each of the grooves
54b and part of the adhesive 57 spills from a space between the
support plate 54 and the lid 56, the adhesive 57 having spilled is
unlikely to reach the nozzles N. Thus, clogging of the nozzles N or
other troubles caused by the adhesive 57 can be suppressed.
[0041] Although the grooves 54b penetrate through the support plate
54 in the example illustrated in FIGS. 2 to 4, the grooves 54b do
not necessarily penetrate through the support plate 54. When the
grooves 54b do not penetrate through the support plate 54, the
stiffness of the support plate 54 can be improved compared to the
structure where the grooves 54b penetrate through the support plate
54. With the support plate 54 having improved stiffness, bending of
the support plate 54, and further, bending of the liquid discharge
head 20 can be suppressed. Thus, reduction of accuracy of landing
positions of the ink due to such bending can be suppressed.
[0042] As exemplified in FIGS. 2 and 4, when the grooves 54b
penetrate through the support plate 54, compared to the structure
in which the grooves 54b do not penetrate through the support plate
54, the contact area between the adhesive 57 and the grooves 54b
can be increased, and accordingly, the strength of bonding between
the lid 56 and the support plate 54 can be increased.
[0043] The shape of the grooves 54b is not limited to the shape
illustrated in FIGS. 2 to 4 and can be appropriately changed. For
example, the grooves 54b may have a shape the width of which
reduces toward the bottoms of the grooves 54b.
[0044] As exemplified in FIGS. 2 and 4, the spaces SG extend in the
Y direction. Each of the grooves 54b extends in the Y direction
without being separated. For example, when the groove 54b is
separated into a plurality of groove portions, the plurality of
groove portions are independently of one another. Thus, the
adhesive 57 flowing into one of the groove portions cannot move to
another of the groove portions. Thus, the bonding strength with the
adhesive 57 is likely to vary among the plurality of groove
portions.
[0045] In contrast, as exemplified in FIGS. 2 and 4, when the
groove 54b extends without being separated, the adhesive 57 flowing
into part of the groove 54b can move to another part of the groove
54b. Thus, variation of the bonding strength with the adhesive 57
can be reduced over the entirety of the groove 54b. Accordingly,
compared to the structure in which the groove 54b is separated into
the plurality of groove portions, the strength of the bonding
between the lid 56 and the support plate 54 can be increased.
[0046] As exemplified in FIG. 2, the first to fourth external
communication openings HA1 to HA4 are provided in the case member
40, the channel member 32, the flexible film 52, and the support
plate 54.
[0047] In a plan view seen in the Z direction, the first external
communication opening HA' is located on the positive side in the Y
direction relative to one end SG1, which is an end of one of the
spaces SG corresponding to the first row L1, on the positive side
in the Y direction. As exemplified in FIGS. 2 and 4, the one end
SG1 of the space SG corresponding to the first row L1 communicates
with a first communication passage 5441 that communicates with the
first external communication opening HA'.
[0048] In a plan view seen in the Z direction, the second external
communication opening HA2 is located on the negative side in the Y
direction relative to another end SG2, which is an end of the space
SG corresponding to the first row L1, on the negative side in the Y
direction. As exemplified in FIGS. 2 and 4, the other end SG2 of
the space SG corresponding to the first row L1 communicates with a
second communication passage 5442 that communicates with the second
external communication opening HA2.
[0049] The first communication passage 5441, the second
communication passage 5442, and the first and second external
communication openings HA', HA2 in the support plate 54 are,
together with the space SG corresponding to the first row L1,
surrounded by one of the flexible-film exposure openings 541
corresponding to the first row L1.
[0050] In a plan view seen in the Z direction, the third external
communication opening HA3 is located on the positive side in the Y
direction relative to one end SG3, which is an end of one of the
spaces SG corresponding to the second row L2, on the positive side
in the Y direction. As exemplified in FIGS. 2 and 4, the one end
SG3 of the space SG corresponding to the second row L2 communicates
with a first passage 5443 that communicates with the third external
communication opening HA3.
[0051] In a plan view seen in the Z direction, the fourth external
communication opening HA4 is located on the negative side in the Y
direction relative to another end SG4, which is an end of the space
SG corresponding to the second row L2, on the negative side in the
Y direction. As exemplified in FIGS. 2 and 4, the other end SG4 of
the space SG corresponding to the second row L2 communicates with a
second passage 5444 that communicates with the fourth external
communication opening HA4.
[0052] The first passage 5443, the second passage 5444, and the
third and fourth external communication openings HA3, HA4 in the
support plate 54 are, together with the space SG corresponding to
the second row L2, surrounded by one of the flexible-film exposure
openings 541 corresponding to the second row L2.
[0053] As exemplified in FIG. 4, the walling flexible film 52a
corresponding to the first row L1 has a first region 52a1, a second
region 52a2, and a third region 52a3. The first region 52a1 is an
example of a first flexible region. The second region 52a2 is an
example of a second flexible region. The first region 52a1 includes
one end 52aa of one of the walling flexible films 52a corresponding
to the first row L1 on the positive side in the Y direction. The
second region 52a2 includes another end 52ab of the walling
flexible film 52a corresponding to the first row L1 on the negative
side in the Y direction. The third region 52a3 is a region between
the first region 52a1 and the second region 52a2. The width of the
third region 52a3 in the X direction is uniform. The largest width
of the first region 52a1 in the X direction is smaller than the
width of the third region 52a3 in the X direction. The largest
width of the second region 52a2 in the X direction is smaller than
the width of the third region 52a3 in the X direction.
[0054] As exemplified in FIGS. 2 and 4, in the X direction, the
smallest width of the second region 52a2 is smaller than the
smallest width of the first region 52a1.
[0055] When both of the smallest width of the first region 52a1 and
the smallest width of the second region 52a2 are excessively small,
a smallest width portion of each of the first region 52a1 and the
second region 52a2 is unlikely to be bent. This causes a first
problem in that the pressure variation in the storage chamber 34 is
unlikely to be absorbed by variation of the walling flexible film
52a.
[0056] In contrast, when both of the smallest width of the first
region 52a1 and the smallest width of the second region 52a2 are
excessively large, the walling flexible film 52a is largely bent.
This causes a second problem in that the flexible film 52 is easily
removed from the channel member 32.
[0057] According to the present embodiment, the occurrences of a
situation in which both of the smallest width of the first region
52a1 and the smallest width of the second region 52a2 are
excessively small or excessively large can be suppressed.
Accordingly, the occurrences of the first and second problems can
be avoided.
[0058] Furthermore, the smallest width of the first region 52a1 is
larger than the smallest width of the second region 52a2. Thus, the
water in the ink evaporates more easily in the smallest width
portion of the first region 52a1 than in the smallest width portion
of the second region 52a2. In addition, the air easily moves
between the outside of the liquid discharge head 20 and the space
SG. Thus, the water evaporating from the first region 52a1 is
easily discharged to the outside of the liquid discharge head
20.
[0059] As exemplified in FIGS. 2 and 4, the shape of the first
region 52a1 is different from the shape of the second region 52a2.
This can reduce the likelihood of each of the first region 52a1 and
the second region 52a2 having a shape that is excessively easily to
be bent or a shape that is excessively difficult to be bent.
Second Embodiment
[0060] Next, a second embodiment is described. In exemplifications
described below, elements having similar functions to those of the
first embodiment are denoted by the reference signs used for the
first embodiment, thereby appropriately omitting detailed
description.
[0061] FIG. 5 illustrates the compliance plate 50 according to the
second embodiment. In the spaces SG exemplified in FIG. 5,
regulating members 545 are provided between the walling flexible
films 52a and the lid 56 so as to regulate contact between the
walling flexible films 52a and the lid 56.
[0062] According to the present embodiment, a plurality of
projections projecting from the walling flexible films 52a toward
the lid 56 are used as the regulating members 545. The regulating
members 545 are secured to the walling flexible films 52a by an
adhesive. As exemplified in FIG. 5, the regulating members 545 are
provided separately from the support plate 54 and independently of
the support plate 54.
[0063] According to the second embodiment, the regulating members
545 are provided. This can suppress the occurrences of failure in
which the walling flexible films 52a are bent toward the lid 56
more largely than required, resulting in removal of the flexible
film 52 from the channel member 32.
[0064] When dust or the like is attracted to the regulating members
545, there occurs a problem in that flow of the air in the spaces
SG becomes poor, and the walling flexible films 52a are unlikely to
be bent. However, since the regulating members 545 are provided at
positions separated from the support plate 54, the air can pass
through both sides of the regulating members 545. Accordingly,
attraction of dust or the like to the regulating members 545 can be
reduced, and a situation in which the walling flexible films 52a
are unlikely to be bent can be suppressed.
[0065] The regulating members 545 may be secured by an adhesive to
the lid 56 instead of being secured to the walling flexible films
52a. Furthermore, the number, positions, and shape of the
regulating members 545 can be appropriately changed. For example,
the length of the regulating members 545 in the Z direction may be
smaller than the length of the support plate 54 in the Z direction,
that is, the thickness of the support plate 54.
Third Embodiment
[0066] Next, a third embodiment is described. FIG. 6 illustrates a
head unit 21 used for the third embodiment. As exemplified in FIG.
6, the head unit 21 includes a first liquid discharge head 20a, a
second liquid discharge head 20b, a third liquid discharge head
20c, and a fourth liquid discharge head 20d. The head unit 21 is
mounted on the carriage 18 illustrated in FIG. 1 and discharges the
ink.
[0067] Hereinafter, in the case where it is not required to
distinguish the first liquid discharge head 20a, the second liquid
discharge head 20b, the third liquid discharge head 20c, and the
fourth liquid discharge head 20d from one another, each of the
first to fourth liquid discharge heads 20a to 20d is referred to as
"liquid discharge head 20e".
[0068] The structure of the liquid discharge heads 20e is the same
as the structure of the liquid discharge head 20 according to the
second embodiment with the lid 56 removed. The liquid discharge
heads 20e discharge, for example, inks of different colors. The
flexible-film exposure openings 541 of the liquid discharge heads
20e are covered with a common lid 56a used in common for the liquid
discharge heads 20e. The common lid 56a is an example of a lid.
[0069] FIG. 7 illustrates arrangement of the first liquid discharge
head 20a, the second liquid discharge head 20b, the third liquid
discharge head 20c, and the fourth liquid discharge head 20d in the
X-Y plane. The fourth liquid discharge head 20d, the third liquid
discharge head 20c, the second liquid discharge head 20b, and the
first liquid discharge head 20a are equally spaced from one another
in the X direction.
[0070] The first liquid discharge head 20a and the fourth liquid
discharge head 20d are in such a positional relationship that the
first liquid discharge head 20a and the fourth liquid discharge
head 20d are arranged point symmetrically with each other.
Specifically, in a plan view seen in the Z direction, the first
liquid discharge head 20a and the fourth liquid discharge head 20d
are arranged point symmetrically with each other about a center D
of a circumscribed circle that circumscribes the common lid 56a.
Furthermore, the second liquid discharge head 20b and the third
liquid discharge head 20c are arranged point symmetrically with
each other about the center D.
[0071] FIG. 8 illustrates the arrangement of the first liquid
discharge head 20a, the second liquid discharge head 20b, the third
liquid discharge head 20c, and the fourth liquid discharge head 20d
in the X-Y plane of the respective compliance plates 50. In FIG. 8,
the compliance plates 50 of the first liquid discharge head 20a,
the second liquid discharge head 20b, the third liquid discharge
head 20c, and the fourth liquid discharge head 20d are, for
convenience, respectively represented as a compliance plate 50a, a
compliance plate 50b, a compliance plate 50c, and a compliance
plate 50d.
[0072] As exemplified in FIG. 8, the compliance plate 50 of the
first liquid discharge head 20a and the compliance plate 50 of the
fourth liquid discharge head 20d are arranged point symmetrically
with each other about the center D. Accordingly, when seen in the X
direction, the entirety of the first region 52a1 of the first
liquid discharge head 20a and the entirety of the second region
52a2 of the fourth liquid discharge head 20d overlap, and the
entirety the second region 52a2 of the first liquid discharge head
20a and the entirety of the first region 52a1 of the fourth liquid
discharge head 20d overlap.
[0073] Instead, when seen in the X direction, the first region 52a1
of the first liquid discharge head 20a and the second region 52a2
of the fourth liquid discharge head 20d may partially overlap, and
the second region 52a2 of the first liquid discharge head 20a and
the first region 52a1 of the fourth liquid discharge head 20d may
partially overlap. For example, the first liquid discharge head 20a
and the second liquid discharge head 20b may be offset in the Y
direction from the third liquid discharge head 20c and the fourth
liquid discharge head 20d.
[0074] As exemplified in FIGS. 2 and 4, as the width of the walling
flexible films 52a in the X direction increases, the width of the
flexible-film exposure openings 541 in the X direction increases
and the stiffness of the support plate 54 reduces. Also according
to the present embodiment, in the X direction, the smallest width
of the second region 52a2 is smaller than the smallest width of the
first region 52a1. Accordingly, in the support plate 54, the
stiffness of a portion around the first region 52a1 is different
from the stiffness of a portion around the second region 52a2.
[0075] According to the present embodiment, when seen in the X
direction, at least part of the first region 52a1 of the first
liquid discharge head 20a and at least part of the second region
52a2 of the fourth liquid discharge head 20d overlap, and at least
part of the second region 52a2 of the first liquid discharge head
20a and at least part of the first region 52a1 of the fourth liquid
discharge head 20d overlap.
[0076] Thus, portions having low stiffness can be varied in the Y
direction among the support plates 54, and accordingly,
nonuniformity of the head unit 21 in stiffness can be reduced. This
can suppress bending of the head unit 21 caused by nonuniformity in
stiffness of the head unit 21, and further, suppress bending of the
nozzle plate 62. Thus, reduction of accuracy of landing positions
of the ink due to such bending can be suppressed.
[0077] Here, the following elements that correspond to the first
row L1 of the first liquid discharge head 20a respectively
exemplify a first storage chamber, a first flexible film, a first
flexible region, a second flexible region, a first space, and a
first opening: the storage chamber 34, the walling flexible film
52a, the first region 52a1, the second region 52a2, the space SG,
and the flexible-film exposure opening 541. The channel member 32
and the support plate 54 of the first liquid discharge head 20a
respectively exemplify a first channel member and a first support.
The following elements that correspond to the first row L1 of the
fourth liquid discharge head 20d respectively exemplify a second
storage chamber beside the first storage chamber along the second
axis, a second flexible film, a second space, a second opening, a
third communication passage, a fourth communication passage, a
third flexible region, and a fourth flexible region: the storage
chamber 34, the walling flexible film 52a, the space SG, the
flexible-film exposure opening 541, the first communication passage
5441 with which the space SG communicates, the second communication
passage 5442 with which the space SG communicates, the first region
52a1, and the second region 52a2. The channel member 32 and the
support plate 54 of the fourth liquid discharge head 20d
respectively exemplify a second channel member and a second
support. It is sufficient that two or more liquid discharge heads
20e be mounted on the head unit 21.
VARIATIONS
[0078] The above-described embodiments can be varied in a variety
of manners. Specific forms applicable to the embodiments are
exemplified as follows. Two or more of the forms arbitrarily
selected from among the following exemplifications can be
appropriately combined as long as no conflict occurs between the
selected two or more forms.
[0079] 1. The driver element that discharges the liquid contained
in the pressure chamber C from the nozzle N is not limited to the
piezoelectric element 385 exemplified for the embodiments. For
example, a heating element that generates heat so as to generate
bubbles in the pressure chamber C for variation of the pressure may
be used as the driver element. As can be understood from the
above-described exemplifications, the driver element is generally
represented as an element that ejects the liquid contained in the
pressure chamber C from the nozzle N, and typically, as an element
that applies pressure to the inside of the pressure chamber C.
Here, the driver element may be operated in any method, for
example, a piezoelectric method or a heating method and may have
any specific structure.
[0080] 2. Although a serial scan liquid discharge device 10 in
which the carriage 18 on which the liquid discharge head 20 is
mounted reciprocates has been described according to the
above-described embodiments, the present disclosure can be applied
also to a line scan liquid discharge device in which the plurality
of nozzles N are distributed throughout the width of the medium
11.
[0081] 3. The liquid discharge device 10 exemplified according to
the above-described embodiments can be used for any of a variety of
apparatuses such as facsimile machines and copiers other than
apparatuses dedicated to printing. Furthermore, application of the
liquid discharge device 10 is not limited to printing. For example,
a liquid discharge device that discharges a solution of colorant is
used as any of manufacturing devices that form color filters of
liquid crystal displays. Furthermore, a liquid discharge device
that discharges a solution of a conductive material is used as any
of manufacturing devices that form wiring or electrodes of wiring
substrates. Furthermore, a liquid discharge device that discharges
a solution of biological organic matter is used as, for example,
any of manufacturing devices that fabricate biochips.
* * * * *