U.S. patent application number 16/034655 was filed with the patent office on 2020-01-16 for metal extrusion quenching method and system with variable length entry zone.
The applicant listed for this patent is Granco Clark, Inc.. Invention is credited to Drew Thompson Griffioen, David Rolston Jenista.
Application Number | 20200017944 16/034655 |
Document ID | / |
Family ID | 69138179 |
Filed Date | 2020-01-16 |



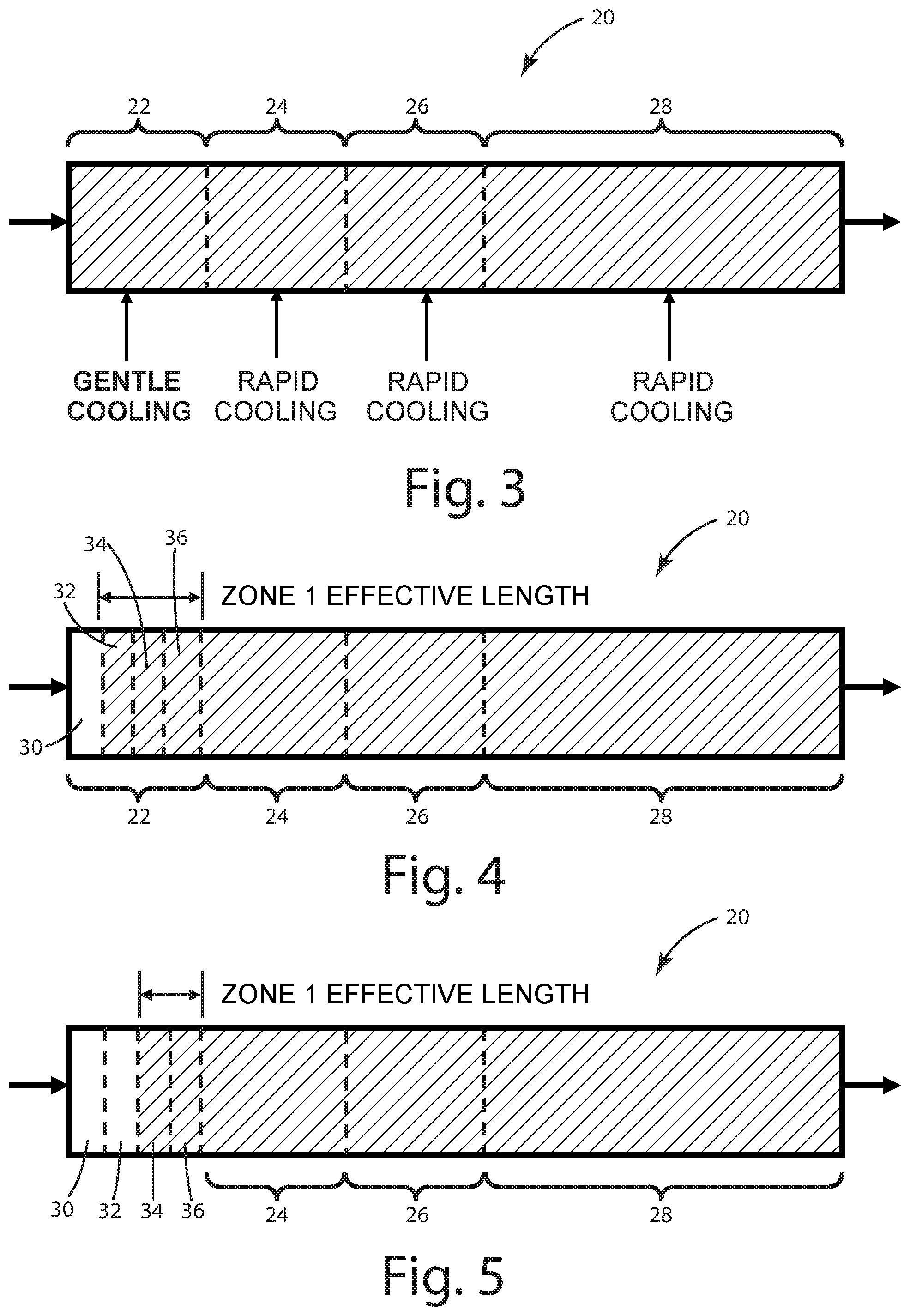
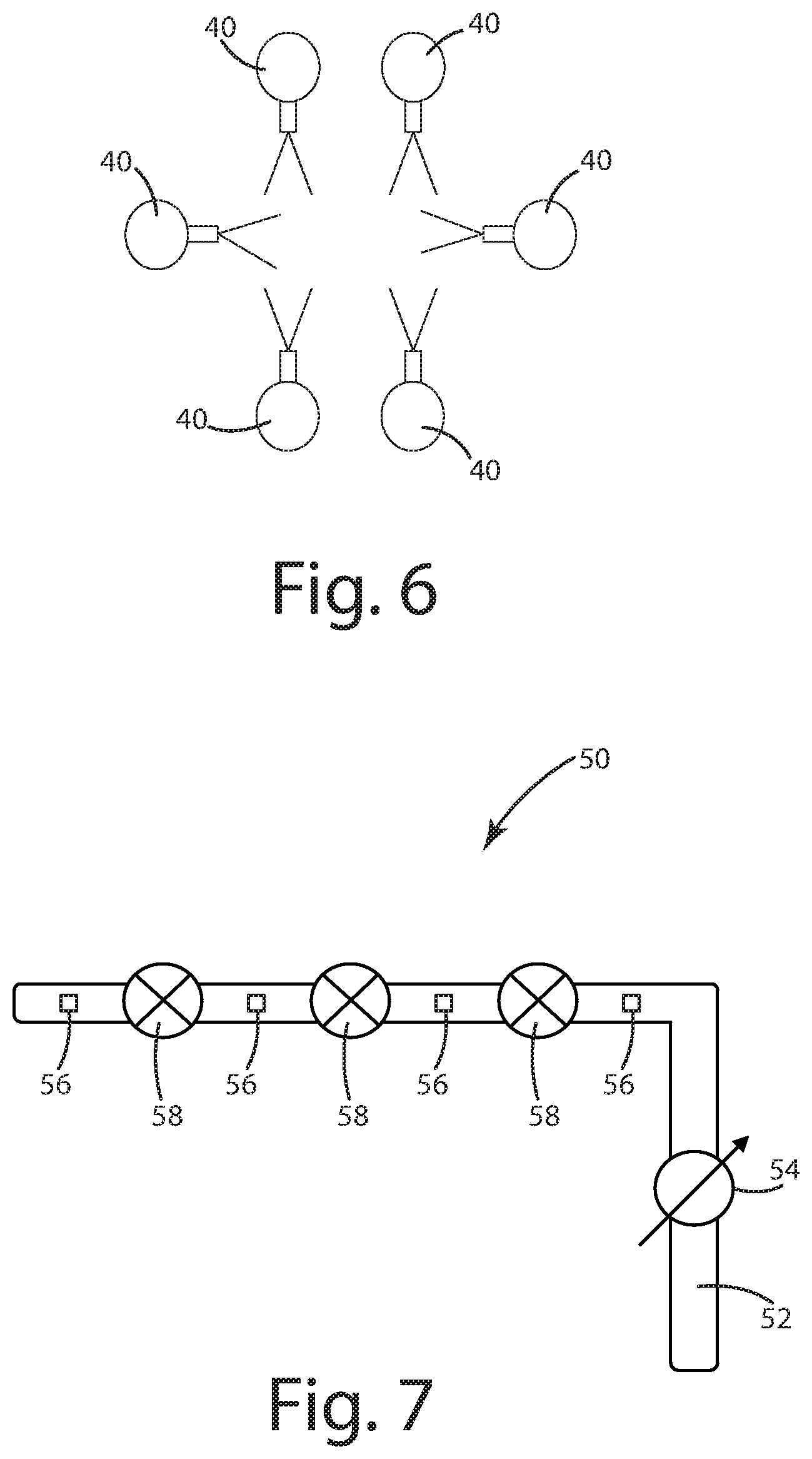
United States Patent
Application |
20200017944 |
Kind Code |
A1 |
Jenista; David Rolston ; et
al. |
January 16, 2020 |
METAL EXTRUSION QUENCHING METHOD AND SYSTEM WITH VARIABLE LENGTH
ENTRY ZONE
Abstract
The specification discloses a metal extrusion quenching method
and system in which multiple quenching steps are accomplished in
multiple quenching zones. In a first zone, the extrusion is cooled
relatively gently while the extrusion is in the pre-critical
temperature range of the alloy of which the metal extrusion is
fabricated. In a second zone, the extrusion is cooled relatively
aggressively while the extrusion is in the critical temperature
range. The first quenching zone includes a plurality of subzones
each of which can be controlled independently. Consequently, the
effective length of the first zone may be controlled by controlling
the quenching provided in each subzone.
Inventors: |
Jenista; David Rolston;
(Belmont, MI) ; Griffioen; Drew Thompson;
(Portland, MI) |
|
Applicant: |
Name |
City |
State |
Country |
Type |
Granco Clark, Inc. |
Belding |
MI |
US |
|
|
Family ID: |
69138179 |
Appl. No.: |
16/034655 |
Filed: |
July 13, 2018 |
Current U.S.
Class: |
1/1 |
Current CPC
Class: |
C22C 21/08 20130101;
B21C 29/003 20130101; C22F 1/047 20130101; C22F 1/002 20130101;
C21D 1/667 20130101 |
International
Class: |
C22F 1/00 20060101
C22F001/00; C21D 1/667 20060101 C21D001/667; C22F 1/047 20060101
C22F001/047 |
Claims
1. A method of quenching a metal extrusion comprising: first
quenching the metal extrusion in a first zone relatively gently
when the temperature of the metal extrusion is approximately within
the pre-critical temperature range of the alloy of which the metal
extrusion is fabricated; and second and subsequently quenching the
metal extrusion in a second zone relatively aggressively and
relatively quickly while the temperature of the metal extrusion is
approximately within the critical temperature range of the alloy of
which the metal extrusion is fabricated.
2. A method as defined in claim 1 wherein: the first zone comprises
a plurality of subzones; and the first quenching step includes
selectively applying quenching in the subzones.
3. A method as defined in claim 2 wherein the selectively applying
quenching step within each subzone includes turning quenching on or
off.
4. A method as defined in claim 3 wherein the selectively applying
quenching step within each subzone includes quenching with
mist.
5. A method as defined in claim 1 wherein the first quenching step
comprises quenching with mist.
6. A quenching system for a metal extrusion comprising: a first
quenching zone in which the metal extrusion is quenched relatively
gently while the temperature of the metal extrusion is
approximately within the pre-critical temperature range of the
alloy of which the metal extrusion is fabricated; and a second
quenching zone in which the metal extrusion is quenched relatively
quickly while the temperature of the metal extrusion passes is
approximately within the critical temperature range of the alloy of
which the metal extrusion is fabricated.
7. A system as defined in claim 6 wherein the first quenching zone
comprises a plurality of subzones in which the metal extrusion is
selectively quenched or not quenched in each of the subzones.
8. A system as defined in claim 7 wherein quenching can be turned
on or off within each subzone.
9. A system as defined in claim 8 wherein any quenching within each
subzone includes quenching with mist.
10. A system as defined in claim 6 wherein the metal extrusion
within the first quenching zone is quenched with mist.
Description
BACKGROUND OF THE INVENTION
[0001] The present invention relates to metal extrusion quenching
methods and systems, and more particularly to such methods and
systems in which quenching occurs differently at different and
locations in the quenching process.
[0002] Methods and systems for quenching metal extrusion profiles
are well known. Examples of such methods and systems are
illustrated in U.S. Pat. No. 5,425,386 to Gentry et al; U.S. Pat.
No. 5,337,768 to Gentry; U.S. Pat. No. 5,325,694 to Jenista; U.S.
Pat. No. 5,027,634 to Visser et al; and other references identified
in the Information Disclosure Statement filed with the present
application. The disclosures of the noted patents are incorporated
by reference.
[0003] The properties of high-performance extruded profiles are
affected by the quench rates used in cooling the profiles. The
classic, published quench rates of the past were typically
specified to meet the minimum specification for ultimate strength
of standard aluminum alloys such as 6061. The more complex
requirements of automotive and other applications have pushed the
limits of what were previously accepted industry standards.
[0004] To illustrate this change in specified quench rates, the
recommendations from a major ingot supplier have changed over the
years. In 2002, the ingot supplier recommended a cooling rate for
6082 alloy of 5.5-11.degree. C. (10-20.degree. F.) per second--a
cooling rate that can easily be reached using simple quenching
methods. However, in 2014, the same aluminum ingot supplier
recommended a cooling rate of 42.degree. C. (75.degree. F.) per
second for a specific, specialized 6082 alloy variant.
[0005] High-impact spray quenching provides the highest performance
water quench systems available. Spray quench performance is
typically limited by the formation of the steam barrier around the
profile at elevated temperatures. The period of maximum temperature
differential between the profile and the water is where the steam
barrier interferes with the heat transfer. The nominal breakdown of
the steam barrier (called the Leidenfrost temperature) is about
250.degree. C. (480.degree. F.). At breakdown, the heat transfer
coefficient increases dramatically, but the temperature
differential drops so low that the average heat transfer rate
remains low. Increasing the impact velocity of the water droplets
can increase the Leidenfrost temperature to as high as 600.degree.
C. (1100.degree. F.).
[0006] Desired quench rates have increased for high-performance
sectors of the extrusion market. However, increased quench rates
create higher temperature differentials within the profile, which
induce mechanical stresses that can exceed the yield strength of
the metal extrusion at the extrusion temperature. This can result
in distortion of the profile that is undesirable or even
unacceptable. Consequently, known quenching technologies do not
provide desired quench rates without affecting the quality of the
extrusion.
SUMMARY OF THE INVENTION
[0007] The present invention provides a method and system for
improving the overall quench rate of a metal extrusion quench
system.
[0008] The method includes first and second quenching steps. The
first quenching step includes quenching the metal extrusion
relatively gently until the temperature of the metal extrusion
approaches the critical temperature range of the alloy. The second
quenching step includes quenching the metal extrusion relatively
aggressively and relatively quickly as the temperature of the metal
extrusion passes through the critical temperature range.
[0009] The corresponding system includes first and second zones in
which the first and second quenching steps are performed.
[0010] In the disclosed embodiment, the effective length of the
first step or zone may be changed. This entry zone may be
physically divided into subzones, each of which may be selectively
controlled (e.g. to be turned on or off). The number of activated
subzones controls the effective length of the entry zone.
[0011] The present method and system provide 1) relatively gentle,
relatively slow quenching where needed to avoid distortion and to
increase the yield strength of the extrusion and 2) relatively
aggressive, relatively fast quenching after the yield strength of
the extrusion has increased sufficiently to withstand such
quenching. The overall result is an increase in the quenching rate
provided by the method and the system.
[0012] These and other advantages and features of the invention
will be more fully understood and appreciated by reference to the
description of the current embodiment and the drawings.
BRIEF DESCRIPTION OF THE DRAWINGS
[0013] FIG. 1 is a C-curve for aluminum alloy 6061 showing the
temperatures at which the first quenching step of the present
invention is performed.
[0014] FIG. 2 is the same C-curve illustrated in FIG. 1, showing
the temperatures at which the second quenching step of the present
invention is performed.
[0015] FIG. 3 is a schematic illustration of the metal extrusion
quench system of the present invention.
[0016] FIG. 4 is a schematic illustration of the quench system in
which three subzones of the entry zone is activated.
[0017] FIG. 5 is a schematic illustration of the quench system in
which two subzones of the entry zone are activated.
[0018] FIG. 6 is a schematic illustration of the quench heads
within a single subzone of the entry zone.
[0019] FIG. 7 is a schematic illustration of a water supply
arrangement for controlling water flow to the quench heads within
the subzones of the entry zone.
DESCRIPTION OF THE CURRENT EMBODIMENT
[0020] Before the embodiments of the invention are explained, it is
to be understood that the invention is not limited to the details
of operation or to the details of construction; and the arrangement
of the components set forth in the following description or
illustrated in the drawings. The invention may be implemented in
various other embodiments and may be practiced or carried out in
alternative ways not expressly disclosed herein.
[0021] In addition, it is to be understood that the phraseology and
terminology used herein are for the purpose of description and
should not be regarded as limiting. The use of "including" and
"comprising" and variations thereof encompasses the items listed
thereafter and equivalents thereof as well as additional items and
equivalents thereof. Further, enumeration may be used in the
description of various embodiments. Unless otherwise expressly
stated, the use of enumeration should not be construed as limiting
the invention to any specific order or number of components. Nor
should the use of enumeration be construed as excluding from the
scope of the invention any additional steps or components that
might be combined with or into the enumerated steps or components.
Any reference to claim elements as "at least one of X, Y and Z" is
meant to include any one of X, Y or Z individually, and any
combination of X, Y and Z, for example, X, Y, Z; X, Y; X, Z; and Y,
Z.
[0022] Directional terms, such as "vertical," "horizontal," "top,"
"bottom," "upper," "lower," "inner," "inwardly," "outer" and
"outwardly," are used to assist in describing the invention based
on the orientation of the embodiments shown in the illustrations.
The use of directional terms should not be interpreted to limit the
invention to any specific orientation(s).
[0023] A C-curve for aluminum alloy 6061 is illustrated in FIGS. 1
and 2 and generally designated 10. The C-curve 10 is generally well
known to those skilled in the art. C-curves, also known as
time-temperature-property (TTP) curves, are published by aluminum
suppliers. Each alloy has a unique C-curve. A C-curve graphically
depicts the correlation between the temperature of the alloy and
the precipitation of magnesium silicide (Mg2Si and also known as
Mag-silicide).
[0024] The pre-critical temperature range is illustrated by the
single-headed arrow 12 in FIG. 1. The pre-critical temperature
range includes all temperatures down to approximately 820.degree.
F. Magnesium silicide precipitation within the alloy develops
relatively slowly in this range. Accordingly, the quenching rate
within this range is relatively unimportant to the development of
corrosion.
[0025] When in the pre-critical temperature range 12, the metal
extrusion may be relatively easily distorted, for example, by
high-impact quenching water. Distortion may be reduced in one of
two ways. First, distortion may be reduced by reducing the quench
rate. Second, distortion may be reduced by increasing the yield
strength of the profile by reducing the temperature of the
extrusion.
[0026] The critical temperature range is illustrated by the
double-headed arrow 14 in FIG. 2. This range includes the
temperatures between approximately 680.degree. F. and approximately
820.degree. F. As noted above, Mag-silicide precipitation within
the alloy develops relatively quickly in this range. Accordingly,
the quenching rate within this range preferably is relatively
aggressive to move the extrusion temperature through this range
relatively quickly.
[0027] The present invention discovers, and takes advantage of, the
reality that the rate at which the temperature of the extrusion is
reduced (i.e. quenched) should depend on the temperature of the
extrusion as it moves through the quenching process. The cooling
rate of the extrusion will vary according to the extrusion speed
and the extrusion geometry, and there can be no single location in
the quench at which the critical temperature is reached for all
shapes and speeds. The present invention therefore provide a
balance of 1) preventing shock cooling in the pre-critical
temperature range and 2) cooling as rapidly as possible across the
critical temperature range. For example, one aluminum ingot
supplier suggests quench rates of 80.degree. F. per second through
the critical temperature range.
[0028] The C-curve illustrated in FIGS. 1 and 2 is illustrative for
a particular aluminum alloy. However, the present invention is not
dependent on any particular metal, any particular alloy, or any
particular C-curve.
[0029] FIG. 3 schematically illustrates a quench system constructed
in accordance with a current embodiment of the invention. The
aluminum extrusion profile (not shown) moves through the quench
system 20 from left to right as viewed in the Figures. The quench
system 20 includes a first zone or an entry zone 22, a second zone
24, a third zone 26, and a fourth zone 28. Different quenching may
be implemented in each of the zones 22-28 to achieve different
quenching rates. For example, the quench system 20 implements
relatively gentle quenching in the entry zone 22 and relatively
aggressive and/or rapid quenching in zones 24-28.
[0030] FIG. 4 shows the entry zone 22 as a sequence of four
sequential subzones 30, 32, 34, and 36. The physical length of the
entry zone 22 is the combined length of the subzones 30-36. Each of
the subzones 30-36 is adapted to provide mist quenching within the
subzone. In addition, the mist quenching in each of the subzones
30-36 may be independently controlled and, specifically, may be
turned on or off. As is known to those skilled in the art, mist
quenching provides relatively gentle and/or slow quenching.
Additionally, this type of quenching reduces or even eliminates
distortion of the metal extrusion.
[0031] As configured in FIG. 4, the system 20 provides mist
quenching in subzones 32-36 but not in subzone 30. Consequently,
the effective quench length of the entry zone 22 in this
configuration is the combined lengths of the subzones 32-36.
[0032] As configured in FIG. 5, the system 20 provides mist
quenching in subzones 34 and 36 but not in subzones 30 and 32.
Consequently, the effective quench length of the entry zone 22 in
this configuration is the combined lengths of the subzones 34 and
36.
[0033] By extension (although not specifically illustrated), the
system 20 may be configured to provide quenching in subzone 36 but
not in subzones 30, 32, and 34. In such a configuration, the
effective quenching length of the entry zone 22 is the length of
the subzone 36.
[0034] By further extension, the system 20 may be configured to
provide quenching in all four subzones 30-36. In such a
configuration, the effective quenching length of the entry zone 22
is the combined lengths of all four subzones 30-36.
[0035] By yet further extension, the system 20 may be configured
not to provide quenching in any of the four subzones 30-36. In such
a configuration, the effective quenching length of the entry zone
22 is zero.
[0036] The configuration of the system 20, and particularly the
activation of quenching within the subzones 30-36, is selected to
relatively slowly reduce the temperature of the metal extrusion
through, or approximately through, the pre-critical temperature
range of the alloy of which the metal extrusion is fabricated.
Because the quenching within the entry zone 22 is relatively
gentle, distortion of the metal extrusion is insignificant or even
nonexistent. This enables the metal extrusion to be cooled to a
condition where its yield strength is sufficient to withstand more
aggressive quenching in subsequent zones 24, 26, and 28.
[0037] Relatively aggressive and/or relatively rapid cooling is
provided in quenching zones 24, 26, and 28. Such cooling may be
provided using techniques well known to those skilled in the art.
These techniques may include the use of high-pressure and/or
high-volume water as the quenching medium. Such quenching provides
relatively high rates of cooling as the temperature of the metal
extrusion moves through the critical temperature range, which is
desired for the reasons noted above.
[0038] FIG. 6 schematically illustrates the misting heads 40 for
each of the subzones 30-36. The illustration includes six misting
heads 40. This number is arbitrary, and different numbers of
misting heads 40 in different configurations and orientations may
be provided. The misting heads 40 are arranged around the
circumference of the metal extrusion to direct mist onto the
extrusion. An enclosure (not shown) contains the mist within the
quenching system 20.
[0039] FIG. 7 schematically illustrates a water supply arrangement
50 suitable for providing quenching water to the subzones 30-36.
The arrangement 50 includes a supply pipe 52 having a master valve
54. The arrangement 50 further includes a plurality of connection
points 56 and individual valves 58. Each connection point 56 may be
connected to the misting heads 40 within one of the subzones 30-36.
Each of the valves 54 and 58 may be controlled to allow water to
flow from the supply pipe 52 to the subzones 30-36. As disclosed,
water may be provided (a) to none of the subzones, (b) to subzone
36 alone, (c) to subzones 34 and 36 (see FIG. 5), (d) to subzones
32, 34, and 36 (see FIG. 3), or (e) to all of subzones 30-36. This
enables quenching water to be selectively applied to the subzones
30-36 to control the effective length (or quenching length) of the
entry zone 22 so as to be extendable or extensible.
[0040] The supply of quenching water to the subzones may be
controlled in other ways not currently illustrated in the drawings.
For example, quenching water could be supplied to each zone
independently of whether or not quenching water is supplied to the
other zones.
[0041] The two-step quenching provided by the present invention
includes 1) a first step in which the quenching is relatively
gentle and/or relatively slow in order to provide relatively slow
cooling of the metal extrusion in the pre-critical temperature
range and 2) a second step in which the quenching is relatively
aggressive and/or relatively fast cooling through the critical
temperature range. Consequently, the invention provides slow
quenching where appropriate and fast quenching where appropriate
depending on the temperature of the metal extrusion at any location
through the quench system 20.
[0042] The above description is that of current embodiments of the
invention. Various alterations and changes can be made without
departing from the spirit and broader aspects of the invention as
defined in the appended claims, which are to be interpreted in
accordance with the principles of patent law including the doctrine
of equivalents.
[0043] This disclosure is illustrative and should not be
interpreted as an exhaustive description of all embodiments of the
invention or to limit the scope of the claims to the specific
elements illustrated or described in connection with these
embodiments. For example, and without limitation, any individual
element(s) of the described invention may be replaced by
alternative elements that provide substantially similar
functionality or otherwise provide adequate operation. This
includes, for example, presently known alternative elements, such
as those that might be currently known to one skilled in the art,
and alternative elements that may be developed in the future, such
as those that one skilled in the art might, upon development,
recognize as alternatives.
[0044] Further, the disclosed embodiments include a plurality of
features that are described in concert and that might cooperatively
provide a collection of benefits. The present invention is not
limited to only those embodiments that include all of these
features or that provide all of the stated benefits, except to the
extent otherwise expressly set forth in the issued claims. Any
reference to claim elements in the singular, for example, using the
articles "a," "an," "the" or "said," is not to be construed as
limiting the element to the singular.
* * * * *