U.S. patent application number 16/552508 was filed with the patent office on 2020-01-09 for method for preparing microstructured laminating adhesive articles.
The applicant listed for this patent is 3M INNOVATIVE PROPERTIES COMPANY. Invention is credited to Henry Garcia, Mieczyslaw H. Mazurek, Audrey A. Sherman, Daniel Toro, Wendi J. Winkler.
Application Number | 20200009843 16/552508 |
Document ID | / |
Family ID | 38479293 |
Filed Date | 2020-01-09 |
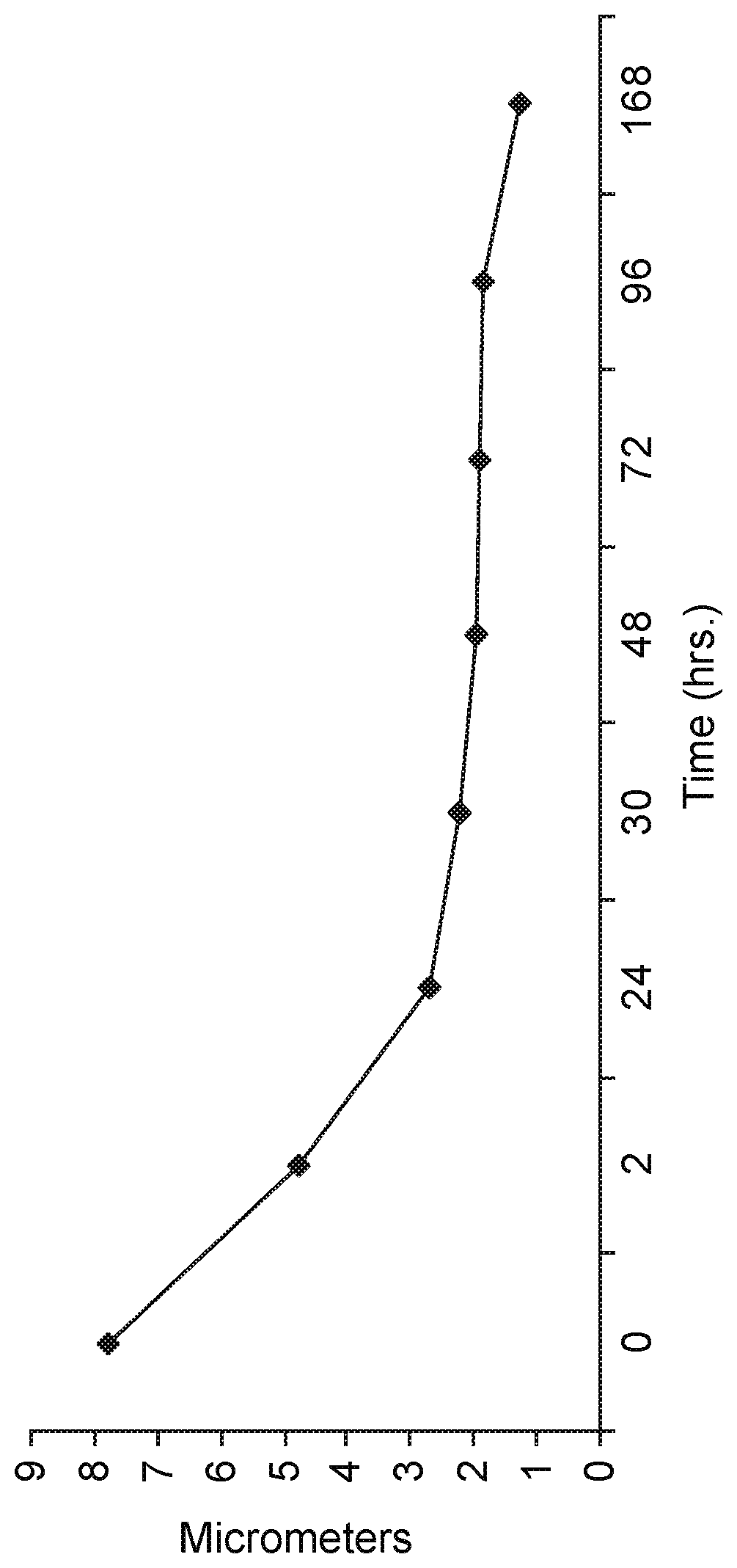
United States Patent
Application |
20200009843 |
Kind Code |
A1 |
Sherman; Audrey A. ; et
al. |
January 9, 2020 |
METHOD FOR PREPARING MICROSTRUCTURED LAMINATING ADHESIVE
ARTICLES
Abstract
A method of making a microstructured adhesive article that
includes (a) providing an article comprising a crosslinked pressure
sensitive adhesive layer disposed on a backing; and (b) embossing
the surface of the crosslinked pressure sensitive adhesive layer to
form a crosslinked pressure sensitive adhesive layer having a
microstructured adhesive surface.
Inventors: |
Sherman; Audrey A.;
(Woodbury, MN) ; Winkler; Wendi J.; (Minneapolis,
MN) ; Mazurek; Mieczyslaw H.; (Roseville, MN)
; Garcia; Henry; (Madrid, ES) ; Toro; Daniel;
(Madrid, ES) |
|
Applicant: |
Name |
City |
State |
Country |
Type |
3M INNOVATIVE PROPERTIES COMPANY |
St. Paul |
MN |
US |
|
|
Family ID: |
38479293 |
Appl. No.: |
16/552508 |
Filed: |
August 27, 2019 |
Related U.S. Patent Documents
|
|
|
|
|
|
Application
Number |
Filing Date |
Patent Number |
|
|
15347941 |
Nov 10, 2016 |
|
|
|
16552508 |
|
|
|
|
11372759 |
Mar 10, 2006 |
9555602 |
|
|
15347941 |
|
|
|
|
Current U.S.
Class: |
1/1 |
Current CPC
Class: |
B32B 27/08 20130101;
B32B 2037/268 20130101; B32B 2551/00 20130101; B32B 2605/006
20130101; B32B 37/26 20130101; C09J 2301/204 20200801; Y10T 428/28
20150115; B32B 17/10743 20130101; B32B 17/10036 20130101; B32B
37/003 20130101; B32B 37/12 20130101; B29K 2995/0026 20130101; B29C
2059/023 20130101; C09J 7/38 20180101; B32B 17/10697 20130101; B32B
38/06 20130101; B32B 2307/412 20130101; B32B 2405/00 20130101; C09J
7/403 20180101; B29C 59/022 20130101; B32B 17/10587 20130101; B32B
27/308 20130101 |
International
Class: |
B32B 37/00 20060101
B32B037/00; B32B 27/30 20060101 B32B027/30; B32B 27/08 20060101
B32B027/08; B32B 37/12 20060101 B32B037/12; B32B 38/06 20060101
B32B038/06; B32B 37/26 20060101 B32B037/26; B32B 17/10 20060101
B32B017/10; B29C 59/02 20060101 B29C059/02 |
Claims
1. A method of making a microstructured adhesive article
comprising: (a) providing an article comprising a crosslinked
pressure sensitive adhesive layer disposed on a backing, wherein
the crosslinked pressure sensitive adhesive layer has a thickness
of from about 10 micrometers to about 1500 micrometers; and (b)
embossing the surface of the crosslinked pressure sensitive
adhesive layer with a microstructured liner or a molding tool to
form a crosslinked pressure sensitive adhesive layer having a
microstructured adhesive surface structure, wherein the structure
consists of V-grooves or channels and wherein the surface structure
is unstable when not in contact with the microstructured liner or
molding tool, and the adhesive layer is able to wet out a substrate
surface by flattening of the microstructured surface structures and
displays complete wet out to a glass substrate after 48 hours.
2. The method of claim 1, wherein embossing comprises contacting
the surface of the crosslinked pressure sensitive adhesive layer
with a microstructured release liner.
3. The method of claim 1, wherein embossing comprises contacting
the surface of the crosslinked pressure sensitive adhesive layer
with a microstructured molding tool.
4. The method of claim 1, wherein the crosslinked pressure
sensitive adhesive layer comprises a covalently crosslinked
pressure sensitive adhesive layer.
5. The method of claim 1, wherein the crosslinked pressure
sensitive adhesive layer comprises a physically crosslinked
pressure sensitive adhesive layer.
6. The method of claim 1, wherein the crosslinked pressure
sensitive adhesive layer comprises a crosslinked acrylic adhesive
layer.
7. The method of claim 1, wherein the backing on which the
crosslinked pressure sensitive adhesive layer is disposed is
removable from the adhesive layer.
8. The method of claim 1, wherein the backing on which the
crosslinked pressure sensitive adhesive layer is disposed comprises
a microstructured release liner.
9. The method of claim 1, wherein the backing on which the
crosslinked pressure sensitive adhesive layer is disposed comprises
a polymeric film.
10. The method of claim 1, wherein the backing on which the
crosslinked pressure sensitive adhesive layer is disposed comprises
a rigid substrate.
11. The method of claim 1, wherein the backing on which the
crosslinked pressure sensitive adhesive layer is disposed comprises
a non-rigid substrate.
12. The method of claim 1, wherein the crosslinked pressure
sensitive adhesive layer having a microstructured adhesive surface
is capable of being dry laminated to a substrate to form a
laminate.
13. The method of claim 12, wherein during being dry laminated to a
substrate to form a laminate, air bleeds out through the
microstructural features to prevent the formation of bonding
defects.
14. A microstructured adhesive article prepared according to the
method of claim 1.
15. An article comprising a crosslinked pressure sensitive adhesive
layer disposed on a structured liner, wherein the crosslinked
pressure sensitive adhesive has a microstructured surface
structure, wherein the surface structure consists of V-grooves or
channels and wherein the surface structure is unstable when not in
contact with the structured liner, and the adhesive layer is able
to wet out a substrate surface by flattening of the microstructured
surface structures due to the minimization of the formation of
stresses within the adhesive upon removal of the structured liner,
and wherein the crosslinked pressure sensitive adhesive layer has a
thickness of from about 10 micrometers to about 1500 micrometers,
and wherein the crosslinked pressure sensitive adhesive having a
microstructured surface structure displays complete wet out to a
glass substrate after 48 hours.
16. The article of claim 15, wherein the article further comprises
a backing disposed on the crosslinked pressure sensitive adhesive
layer.
17. The article of claim 16, wherein the backing is removable from
the adhesive layer.
18. The article of claim 16, wherein the backing comprises a
microstructured release liner.
19. The article of claim 16, wherein the backing comprises a
polymeric film.
20. The article of claim 16, wherein the backing comprises a rigid
substrate.
21. The article of claim 16, wherein the backing comprises a
non-rigid substrate.
Description
TECHNICAL FIELD
[0001] This invention relates to methods for making microstructured
laminating adhesive articles.
BACKGROUND
[0002] Microstructured adhesive articles have been prepared by
applying a flowable pressure sensitive adhesive to the surface of a
microstructured release liner or the surface of a microstructured
molding tool. The process results in the creation of an adhesive
having a microstructured surface. When the resulting articles are
dry laminated under pressure to substrates such as glass or polymer
films, the microstructural features created in the adhesive surface
allow air to escape from the bonding interface, thereby minimizing
or preventing the formation of bubbles and pinholes.
[0003] During lamination, the microstructural features flatten out
and wet the substrate surface under the influence of applied
pressure. In the process, however, stresses are introduced into the
adhesive as the adhesive relaxes and tries to return to its initial
microstructured state. These stresses can create defects in the
adhesive that adversely affect its optical properties.
SUMMARY
[0004] A method of making a microstructured adhesive article is
described that includes (a) providing an article comprising a
crosslinked pressure sensitive adhesive layer disposed on a
backing; and (b) embossing the surface of the crosslinked pressure
sensitive adhesive layer to form a crosslinked pressure sensitive
adhesive layer having a microstructured adhesive surface. Emboss
means, for the purpose of the present application, deforming with
pressure. In some embodiments, the crosslinked adhesive surface is
embossed by contacting the surface with a microstructured release
liner. In other embodiments, the crosslinked adhesive surface is
embossed by contacting the surface with a microstructured molding
tool. The resulting articles may be dry laminated to a variety of
substrates, including rigid substrates such as glass, and are
particularly useful for optical applications where low haze, low
opacity, and high luminous transmittance are desirable.
[0005] Embossing the surface of a crosslinked pressure sensitive
adhesive to create a microstructured adhesive surface minimizes the
formation of stresses within the adhesive after lamination because
both the pre-structured and final states of the adhesive are
substantially planar. Therefore, the structure is unstable when not
in contact with the microstructured liner or molding tool. This is
in contrast to microstructured adhesives produced by coating a
flowable adhesive onto a microstructured release liner or a
microstructured molding tool, where the initial state of the
adhesive to which it tries to return is that of the microstructured
configuration, while the final state is substantially planar.
[0006] The details of one or more embodiments of the invention are
set forth in the accompanying drawings and the description below.
Other features, objects, and advantages of the invention will be
apparent from the detailed description, and from the claims.
BRIEF DESCRIPTION OF THE FIGURES
[0007] FIG. 1 is a graphical representation of the data shown in
Table 2.
DETAILED DESCRIPTION
[0008] Microstructured adhesive articles are prepared by embossing
the surface of a crosslinked pressure sensitive adhesive layer
disposed on a backing to create an adhesive having a
microstructured adhesive surface. The thickness of the adhesive
layer is selected based upon the application for which the articles
are intended. In general, the thickness ranges from about 10
micrometers (about 0.4 mils) to about 1500 micrometers (about 60
mils).
[0009] The microstructural features are generally three-dimensional
structures that are microscopic in at least two dimensions (i.e.,
the topical and/or cross-sectional view is microscopic). The term
"microscopic" as used herein refers to dimensions that are
difficult to resolve by the human eye without aid of a microscope.
One useful definition of microscopic is found in Smith, Modern
Optic Engineering, (1966), pages 104-105, wherein visual acuity is
defined and measured in terms of the angular size of the smallest
character that can be recognized. Normal visual acuity allows
detection of a character that subtends an angular height of 5
minutes of arc on the retina.
[0010] The microstructural features may assume a variety of shapes.
Representative examples include hemispheres, prisms (such as square
prisms, rectangular prisms, cylindrical prisms and other similar
polygonal features), pyramids, ellipses, grooves (e.g., V-grooves),
channels, and the like. In general, it is desirable to include
topographical features that promote air egress at the bonding
interface when the article is laminated to a substrate. In this
regard, V-grooves and channels that extend to the edge of the
article are particularly useful. The particular dimensions and
patterns characterizing the microstructural features are selected
based upon the specific application for which the article is
intended.
[0011] Embossing may be accomplished by contacting the crosslinked
adhesive surface with a microstructured molding tool, as described
in Mazurek et al., U.S. Pat. No. 5,650,215, which is incorporated
by reference in its entirety. The tool can be in form of a planar
stamping press, flexible or inflexible belts, or a roller. The
topography of the tool used to create the embossed microstructural
features can be prepared using techniques such as, for example,
chemical etching, mechanical etching, laser ablation,
photolithography, stereolithography, micromachining, knurling,
cutting, scoring, and the like.
[0012] Embossing may also be accomplished by contacting the
crosslinked adhesive surface with a microstructured release liner,
as described in the aforementioned Mazurek et al. patent. Suitable
liners are capable of being placed in intimate contact with the
crosslinked pressure sensitive adhesive and subsequently removed
without damaging the adhesive layer. Examples include polyethylene,
polypropylene, polyester, cellulose acetate, polyvinylchloride, and
polyvinylidene films, as well as paper. The liners may include
silicone release coatings. Commercially available examples include
liners available from 3M Company (St. Paul, Minn.), Rexam Corp.
(Iowa City, Iowa), Daubert Coated Products (Westchester, Ill.),
P.S. Substrates, Inc., Schoeller Technical Papers, Inc., Mondi
Inncoat GMBH, and P.W.A. Kunstoff GMBH.
[0013] The adhesive is disposed on a backing. The backing may be
removable (such as a release liner, including a microstructured
release liner such as described above or a carrier film) or
non-removable such as a polymeric film or a rigid or non-rigid
substrate.
[0014] Pressure sensitive adhesive (PSA) compositions are well
known to those of ordinary skill in the art to possess properties
including (1) aggressive and permanent tack, (2) adherence with no
more than finger pressure, (3) sufficient ability to hold onto an
adherend, and (4) sufficient cohesive strength. Materials that have
been found to function well as PSAs include polymers designed and
formulated to exhibit the requisite viscoelastic properties
resulting in a desired balance of tack, peel adhesion, and shear
holding power.
[0015] The pressure sensitive adhesives are crosslinked prior to
embossing. Examples of suitable adhesives include crosslinked
acrylics, rubbers, thermoplastic elastomers, silicones, and the
like.
[0016] In a preferred embodiment, the pressure sensitive adhesive
is based on at least one poly(meth)acrylate (i.e., a (meth)acrylic
pressure sensitive adhesive). Particularly preferred
poly(meth)acrylates are derived from: (A) at least one
monoethylenically unsaturated alkyl (meth) acrylate monomer (i.e.,
alkyl acrylate and alkyl methacrylate monomer); and (B) at least
one monoethylenically unsaturated free-radically copolymerizable
reinforcing monomer. The reinforcing monomer has a homopolymer
glass transition temperature (Tg) higher than that of the alkyl
(meth)acrylate monomer and is one that increases the glass
transition temperature and cohesive strength of the resultant
copolymer. Herein, "copolymer" refers to polymers containing two or
more different monomers, including terpolymers, tetrapolymers,
etc.
[0017] Monomer A, which is a monoethylenically unsaturated alkyl
acrylate or methacrylate (i.e., (meth)acrylic acid ester),
contributes to the flexibility and tack of the copolymer.
Preferably, monomer A has a homopolymer Tg of no greater than about
0.degree. C. Preferably, the alkyl group of the (meth)acrylate has
an average of about 4 to about 20 carbon atoms, and more
preferably, an average of about 4 to about 14 carbon atoms. The
alkyl group can optionally contain oxygen atoms in the chain
thereby forming ethers or alkoxy ethers, for example. Examples of
monomer A include, but are not limited to, 2-methylbutyl acrylate,
isooctyl acrylate, lauryl acrylate, 4-methyl-2-pentyl acrylate,
isoamyl acrylate, sec-butyl acrylate, n-butyl acrylate, n-hexyl
acrylate, 2-ethylhexyl acrylate, n-octyl acrylate, n-decyl
acrylate, isodecyl acrylate, isodecyl methacrylate, and isononyl
acrylate. Other examples include, but are not limited to,
poly-ethoxylated or -propoxylated methoxy (meth)acrylates such as
acrylates of CARBOWAX (commercially available from Union Carbide)
and NK ester AM90G (commercially available from Shin Nakamura
Chemical, Ltd., Japan). Preferred monoethylenically unsaturated
(meth)acrylates that can be used as monomer A include isooctyl
acrylate, 2-ethyl-hexyl acrylate, and n-butyl acrylate.
Combinations of various monomers categorized as an A monomer can be
used to make the copolymer.
[0018] Monomer B, which is a monoethylenically unsaturated
free-radically copolymerizable reinforcing monomer, increases the
glass transition temperature and cohesive strength of the
copolymer. Preferably, monomer B has a homopolymer Tg of at least
about 10.degree. C. More preferably, monomer B is a reinforcing
(meth)acrylic monomer, including an acrylic acid, a methacrylic
acid, an acrylamide, or a (meth)acrylate. Examples of monomer B
include, but are not limited to, acrylamides, such as acrylamide,
methacrylamide, N-methyl acrylamide, N-ethyl acrylamide,
N-hydroxyethyl acrylamide, diacetone acrylamide, N,N-dimethyl
acrylamide, N, N-diethyl acrylamide, N-ethyl-N-aminoethyl
acrylamide, N-ethyl-N-hydroxyethyl acrylamide, N,N-dihydroxyethyl
acrylamide, t-butyl acrylamide, N,N-dimethylaminoethyl acrylamide,
and N-octyl acrylamide. Other examples of monomer B include
itaconic acid, crotonic acid, maleic acid, fumaric acid,
2,2-(diethoxy)ethyl acrylate, 2-hydroxyethyl acrylate or
methacrylate, 3-hydroxypropyl acrylate or methacrylate, methyl
methacrylate, isobornyl acrylate, 2-(phenoxy)ethyl acrylate or
methacrylate, biphenylyl acrylate, t-butylphenyl acrylate,
cyclohexyl acrylate, dimethyladamantyl acrylate, 2-naphthyl
acrylate, phenyl acrylate, N-vinyl formamide, N-vinyl acetamide,
N-vinyl pyrrolidone, and N-vinyl caprolactam. Preferred reinforcing
acrylic monomers that can be used as monomer B include acrylic acid
and acrylamide. Combinations of various reinforcing
monoethylenically unsaturated monomers categorized as a B monomer
can be used to make the copolymer.
[0019] The preferred acrylate copolymer is formulated to have a
resultant Tg of less than about 0.degree. C. and more preferably,
less than about -10.degree. C. Such acrylate copolymers preferably
include about 60 parts to about 98 parts per hundred of at least
one monomer A and about 2 parts to about 40 parts per hundred of at
least one monomer B. Preferably, the acrylate copolymers have about
85 parts to about 98 parts per hundred or at least one monomer A
and about 2 parts to about 15 parts of at least one monomer B.
[0020] A crosslinking agent is used to build the molecular weight
and the strength of the copolymer. Preferably, the crosslinking
agent is one that is copolymerized with monomers A and B. The
crosslinking agent may produce chemical crosslinks (e.g., covalent
bonds or ionic bonds). Alternatively, it may produce thermally
reversible physical crosslinks that result, for example, from the
formation of reinforcing domains due to phase separation of hard
segments (i.e., those having a Tg higher than room temperature,
preferably higher than 70.degree. C.) such as the styrene macromers
of U.S. Pat. No. 4,554,324 (Husman) and/or acid/base interactions
(i.e., those involving functional groups within the same polymer or
between polymers or between a polymer and an additive) such
polymeric ionic crosslinking as described in WO 99/42536. Suitable
crosslinking agents are also disclosed in U.S. Pat. No. 4,737,559
(Kellen), U.S. Pat. No. 5,506,279 (Babu et al.), and U.S. Pat. No.
6,083,856 (Joseph et al.). The crosslinking agent can be a
photocrosslinking agent, which, upon exposure to ultraviolet
radiation (e. g., radiation having a wavelength of about 250
nanometers to about 400 nanometers), causes the copolymer to
crosslink.
[0021] The crosslinking agent is used in an effective amount, by
which is meant an amount that is sufficient to cause crosslinking
of the pressure sensitive adhesive to provide adequate cohesive
strength to produce the desired final adhesion properties to the
substrate of interest. Preferably, the crosslinking agent is used
in an amount of about 0.1 part to about 10 parts, based on the
total amount of monomers.
[0022] Rubber-based pressure sensitive adhesives are generally of 2
classes, natural rubber-based or synthetic rubber-based.
[0023] Useful natural rubber pressure sensitive adhesives generally
contain masticated natural rubber, from 25 parts to 300 parts of
one or more tackifying resins to 100 parts of natural rubber, and
typically from 0.5 to 2.0 parts of one or more antioxidants.
Natural rubber may range in grade from a light pale crepe grade to
a darker ribbed smoked sheet and includes such examples as CV-60, a
controlled viscosity rubber grade and SMR-5, a ribbed smoked sheet
rubber grade. Tackifying resins used with natural rubbers generally
include but are not limited to wood rosin and its hydrogenated
derivatives; terpene resins of various softening points, and
petroleum-based resins, such as, the ESCOREZ 1300 series of C5
aliphatic olefin-derived resins from Exxon. Antioxidants are used
to retard the oxidative attack on natural rubber, which can result
in loss of the cohesive strength of the natural rubber adhesive.
Useful antioxidants include but are not limited to amines, such as
N--N' di-beta-naphthyl-1,4-phenylenediamine, available as AgeRite
D; phenolics, such as 2,5-di-(t-amyl) hydroquinone, available as
Santovar A, available from Monsanto Chemical Co.,
tetrakis[methylene
3-(3',5'-di-tert-butyl-4'-hydroxyphenyl)propianate]methane,
available as IRGANOX 1010 from Ciba-Geigy Corp., and
2,2'-methylenebis(4-methyl-6-tert butyl phenol), available as
Antioxidant 2246; and dithiocarbamates, such as zinc dithiodibutyl
carbamate. Curing agents are used to partially vulcanize
(crosslink) the pressure sensitive adhesive.
[0024] Another useful class of pressure sensitive adhesives are
those comprising synthetic rubber. Such adhesives are generally
rubbery elastomers, which are either self-tacky or non-tacky and
require tackifiers.
[0025] Self-tacky synthetic rubber pressure sensitive adhesives
include, for example, butyl rubber, a copolymer of isobutylene with
less than 3 percent isoprene, polyisobutylene, a homopolymer of
isoprene, polybutadiene, or styrene/butadiene rubber. Butyl rubber
pressure sensitive adhesives often contain an antioxidant such as
zinc dibutyl dithiocarbamate. Polyisobutylene pressure sensitive
adhesives do not usually contain antioxidants. Synthetic rubber
pressure sensitive adhesives, which generally require tackifiers,
are also generally easier to melt process. They comprise
polybutadiene or styrene/butadiene rubber, from 10 parts to 200
parts of a tackifier, and generally from 0.5 to 2.0 parts per 100
parts rubber of an antioxidant such as IRGANOX 1010. An example of
a synthetic rubber is AMERIPOL 101 1A, a styrene/butadiene rubber
available from BF Goodrich. Tackifiers that are useful include
derivatives of rosins such as FORAL 85, a stabilized rosin ester
from Hercules, Inc., the SNOWTACK series of gum rosins from
Tenneco, and the AQUATAC series of tall oil rosins from Sylvachem;
and synthetic hydrocarbon resins such as the PICCOLYTE A series,
polyterpenes from Hercules, Inc., the ESCOREZ 1300 series of C5
aliphatic olefin-derived resins and the ESCOREZ 2000 Series of C9
aromatic/aliphatic olefin-derived resins. Curing agents are added
to vulcanize (crosslink) the adhesive partially.
[0026] Thermoplastic elastomer pressure sensitive adhesives include
styrene block copolymer pressure sensitive adhesives which
generally comprise elastomers of the A-B or A-B-A type, where A
represents a thermoplastic polystyrene block and B represents a
rubbery block of polyisoprene, polybutadiene, or
poly(ethylene/butylene), and resins. Examples of the various block
copolymers useful in block copolymer pressure sensitive adhesives
include linear, radial, star and tapered styrene-isoprene block
copolymers such as KRATON D1107P, available from Shell Chemical
Co., and EUROPRENE SOL TE 9110, available from EniChem Elastomers
Americas, Inc.; linear styrene-(ethylene-butylene) block copolymers
such as KRATON G1657, available from Shell Chemical Co.; linear
styrene-(ethylene-propylene) block copolymers such as KRATON
G1750X, available from Shell Chemical Co.; and linear, radial, and
star styrene-butadiene block copolymers such as KRATON D1118X,
available from Shell Chemical Co., and EUROPRENE SOL TE 6205,
available from EniChem Elastomers Americas, Inc. The polystyrene
blocks tend to form domains in the shape of spheroids, cylinders,
or plates that causes the block copolymer pressure sensitive
adhesives to have two phase structures. Resins that associate with
the rubber phase generally develop tack in the pressure sensitive
adhesive. Examples of rubber phase associating resins include
aliphatic olefin-derived resins, such as the ESCOREZ 1300 series
and the WINGTACK series, available from Goodyear; rosin esters,
such as the FORAL series and the STAYBELITE Ester 10, both
available from Hercules, Inc.; hydrogenated hydrocarbons, such as
the ESCOREZ 5000 series, available from Exxon; polyterpenes, such
as the PICCOLYTE A series; and terpene phenolic resins derived from
petroleum or terpentine sources, such as PICCOFYN A100, available
from Hercules, Inc. Resins that associate with the thermoplastic
phase tend to stiffen the pressure sensitive adhesive.
Thermoplastic phase associating resins include polyaromatics, such
as the PICCO 6000 series of aromatic hydrocarbon resins, available
from Hercules, Inc.; coumarone-indene resins, such as the CUMAR
series, available from Neville; and other high-solubility parameter
resins derived from coal tar or petroleum and having softening
points above about 85.degree. C., such as the AMOCO 18 series of
alphamethyl styrene resins, available from Amoco, PICCOVAR 130
alkyl aromatic polyindene resin, available from Hercules, Inc., and
the PICCOTEX series of alphamethyl styrene/vinyl toluene resins,
available from Hercules.
[0027] Silicone pressure sensitive adhesives comprise two major
components, a polymer or gum, and a tackifying resin. The polymer
is typically a high molecular weight polydimethylsiloxane or
polydimethyldiphenylsiloxane, that contains residual silanol
functionality (SiOH) on the ends of the polymer chain, or a block
copolymer comprising polydiorganosiloxane soft segments and urea
terminated hard segments. The tackifying resin is generally a
three-dimensional silicate structure that is endcapped with
trimethylsiloxy groups (OSiMe3) and also contains some residual
silanol functionality. Examples of tackifying resins include SR
545, from General Electric Co., Silicone Resins Division,
Waterford, N.Y., and MQD-32-2 from Shin-Etsu Silicones of America,
Inc., Torrance, Calif. Manufacture of typical silicone pressure
sensitive adhesives is described in U.S. Pat. No. 2,736,721
(Dexter). Manufacture of silicone urea block copolymer pressure
sensitive adhesive is described in U.S. Pat. No. 5,214,119 (Leir,
et al).
[0028] As discussed above, the pressure sensitive adhesive is
crosslinked prior to embossing using methods known in the art
depending on the adhesive used. Crosslinking may be effected prior
to embossing by means of covalent crosslinks, physical crosslinks
or a combination thereof. The degree of crosslinking may be
selected based upon the application for which the article is
intended. Covalent crosslinks may be formed by incorporating a
multi-functional monomer in the polymerization process, followed by
curing using, e.g., ultraviolet thermal energy, radiation, ionizing
radiation, moisture, or a combination thereof. Examples of physical
crosslinks include high Tg polymer segments included, for example,
in thermoplastic elastomer block copolymers. Such segments
aggregate to form physical crosslinks that dissipate upon heating.
If a physically crosslinked PSA is used such as a thermoplastic
elastomer, the embossing typically is carried out at temperature
below, or even substantially below, the temperature at which the
adhesive flows.
[0029] The crosslinked pressure sensitive adhesive can optionally
include one or more additives such as initiators, filler,
plasticizers, tackifiers, chain transfer agents, fibrous
reinforcing agents, woven and non-woven fabrics, foaming agents,
antioxidants, stabilizers, fire retardants, viscosity modifying
agents, coloring agents, and mixtures thereof.
[0030] One class of useful crosslinked pressure sensitive adhesives
includes adhesives having properties that make them suitable for
optical applications. Examples of optical applications includes
windows, vehicle windshields, displays, and the like. Useful
adhesives are selected such that upon dry lamination to a
substrate, the adhesive layer has a haze after lamination, measured
according to ASTM D 1003-95, of less than about 50% (e.g., less
than about 10%, preferably less than about 3%, and more preferably
less than about 1%) of the haze of the adhesive layer before
lamination. Such adhesives also preferably do not interfere with
light transmission over the wavelength region of interest (e.g.,
the visible region). For example, after dry lamination, the
adhesive layer may have a luminous transmittance of at least about
85%, preferably about 95% to about 99.9%, and a haze of less than
about 25%, more preferably less than about 5% or even less than
about 2%, as measured according to ASTM D 1003-95. In addition, the
adhesive layer may have an opacity of less than about 3% (e.g.,
less than about 1% or 0.5%), as measured by a spectrophotometer
using well-known analysis techniques.
[0031] In use, the microstructured release liner is removed and the
microstructured adhesive surface is laminated to a substrate.
During lamination, the microstructural features flatten out,
thereby wetting the substrate surface, thereby forming a bond to
the substrate surface. In the course of lamination, air bleeds out
through the microstructural features to minimize or prevent the
formation of bonding defects.
[0032] The air bleed feature is particularly important when dealing
with lamination to rigid substrates, especially rigid-to-rigid
lamination or where the object to be laminated is relatively large.
Currently used methods to prevent defects in such laminations
include techniques such as coating the adhesive layer with water or
a water-detergent solution to prevent bubble formation during
lamination. These techniques require removal of the water by
evaporation. Bubble formation is particularly unacceptable in
optical applications.
[0033] The substrate may be rigid or flexible. Examples of suitable
substrates include glass, metal, plastic, wood, and ceramic
substrates, painted surfaces of these substrates, and the like.
Representative plastic substrates include polyester, polyvinyl
chloride, ethylene-propylene-diene monomer rubber, polyurethanes,
polymethyl methacrylate, engineering thermoplastics (e.g.,
polyphenylene oxide, polyetheretherketone, polycarbonate), and
thermoplastic elastomers. The substrate may also be a woven fabric
formed form threads of synthetic or natural materials such as, for
example, cotton, nylon, rayon, glass, or ceramic material. The
substrate may also be made of a nonwoven fabric such as air laid
webs of natural or synthetic fibers or blends thereof.
[0034] Particularly useful substrates for optical applications
include substrates that are substantially specular such as glass,
clear polymeric materials, and the like. The adhesive forms a
substantially specular adhesive layer when permanently bonded to
such a substrate. The term "substantially specular" as used herein
refers to a material that absorbs substantially no light over a
wavelength region of interest, i.e., substantially all light over
the wavelength region of interest that falls on the surface of the
substantially specular material is reflected or transmitted.
[0035] It is also possible to form a structure whereby the adhesive
is sandwiched between two substrates. A specific example of such a
structure is a window. In such applications, one or both adhesive
surfaces has a microstructured topography. The second substrate may
be selected from the examples of substrates set forth above.
EXAMPLES
[0036] These examples are merely for illustrative purposes only and
are not meant to be limiting on the scope of the appended claims.
All parts, percentages, ratios, etc. in the examples and the rest
of the specification are by weight, unless noted otherwise.
Solvents and other reagents used were obtained from Sigma-Aldrich
Chemical Company; Milwaukee, Wis. unless otherwise noted.
TABLE-US-00001 Table of Abbreviations Abbreviation or Trade
Designation Description Adhesive 3M Optically Clear Adhesive 8141,
adhesive thickness Laminate-1 25 micrometers (1 mil) between 2
release liners, used as obtained. Commercially available from 3M
Company, St. Paul, MN. Adhesive 3M Optically Clear Adhesive 8142,
adhesive thickness Laminate-2 51 micrometers (2 mils) between 2
release liners, used as obtained. Commercially available from 3M
Company, St. Paul, MN. Adhesive 3M Paint Protection Film 84824,
adhesive thickness Laminate-3 51 micrometers (2 mils) between a
paper release liner and a urethane film, used as obtained.
Commercially available from 3M Company, St. Paul, MN. Adhesive A
modified version of 3M Paint Protection Film Laminate-4 84824
(commercially available from 3M Company, St. Paul, MN) was prepared
with the paper release liner replaced with polyethylene
terephthalate release liner, adhesive thickness 51 micrometers (2
mils) between a polyethylene terephthalate liner and a urethane
film. Adhesive 3M Window Film CS35, adhesive thickness 10
Laminate-5 micrometers (0.4 mils) between a polyethylene
terephthalate release liner and a polyethylene terephthalate film.
Commercially available from 3M Company, St. Paul, MN. Adhesive 3M
SCLAR 150 Window Film, adhesive thickness 51 Laminate-6 micrometers
(2.0 mils) between a polyethylene terephthalate release liner and a
polyethylene terephthalate film. Commercially available from 3M
Company, St. Paul, MN. Adhesive VHB 4915 tape 1.5 millimeter thick
and 25 Laminate-7 millimeters wide commercially available from 3M
Company, St. Paul, MN. Liner-1 Flat liners present with the
commercial products sold under the tradenames 3M Optically Clear
Adhesive 8141 and 3M Optically Clear Adhesive 8142. Liner-2 A
polyethylene coated polyethylene terephthalate release liner with
square pyramidal structures, pitch of 200 micrometers and a depth
of 12 micrometers, sidewalls have an angle of about 8.degree..
Glass Glass plate of 4 millimeter thickness. substrate PMMA
Polymethyl methacrylate plate of 3 millimeter substrate
thickness.
Test Methods
180.degree. Peel Adhesion
[0037] Adhesive laminates of backing, pressure sensitive adhesive
and release liner were cut into 1.27 centimeter by 15 centimeter
strips. The release liner was removed and the strip adhered to a 10
centimeter by 20 centimeter clean, solvent washed glass coupon
using a 2 kilogram roller passed once over the strip. The bonded
assembly dwelled at room temperature for about one minute and was
tested for 180.degree. peel adhesion using an IMASS slip/peel
tester (Model 3M90, commercially available from Instrumentors Inc.,
Strongsville, Ohio) at a rate of 2.3 meters/minute (90
inches/minute) over a 5 second data collection time. Two samples
were tested; the reported adhesion value is an average of the two
samples.
% Wet Out
[0038] Adhesive laminates of backing, pressure sensitive adhesive,
and release liner were cut into 5.0 centimeter by 7.5 centimeter
pieces. After the release liner was removed, the exposed adhesive
face was placed carefully on to a clean glass slide with a minimal
amount of pressure. After application an image was captured with a
digital camera, and again at regular time intervals in the same
spot on the sample. ImageJ (a shareware software package) was used
to determine the area that was wetted by the adhesive, which was
reported as % wet out.
Rebound Testing
[0039] This test measures whether an adhesive structure is unstable
after removal from a microstructured liner or molding tool.
Adhesive laminates of the backing, pressure sensitive adhesive, and
microstructured liner were prepared by post-embossing the PSA of a
sample with a microstructured release liner. The microstructured
liner was removed from a sample of the post-embossed adhesive and
the depth of the microstructured adhesive was measured in open air
using a laser imaging interferometer (Zygo Corporation Middlefield,
Conn. 06455). The depth of the microstructured adhesive was
measured over time to observe how long it takes for the adhesive to
lose the microstructured embossing and regain its pre-embossed
state of flatness. An adhesive is unstable if it regains at least
50% of its pre-embossed state within 24 hours.
Visual Inspection Test
[0040] Three layer laminates of either glass/adhesive/glass or
PMMA/adhesive/PMMA were prepared. These laminates were visually
inspected for the presence of bubbles and rated on a 1 to 5 scale
based upon the aesthetic appearance with 1 being lowest aesthetic
appearance (or most bubbles) and 5 being the highest aesthetic
appearance (or least bubbles).
Comparative Example C1
[0041] For Comparative Example C1 a sample of Adhesive Laminate-2
as obtained was tested for 180.degree. Peel Adhesion as described
in the Test Method above. The results are shown in Table 1.
Example 1
[0042] For Example 1 a sample of Adhesive Laminate-2 was obtained
and one liner was removed and Liner-2 was laminated to the PSA
using a laminator. Liner-2 was removed to determine whether the
structure had embossed into PSA-1 surface. The embossed surface was
placed in contact with a glass plate and pressure was applied with
a simple finger rub-down to one half of the sample and the other
half of the sample was left untouched. The rubbed portion showed
complete wet out as viewed by the eye.
Example 2
[0043] The same procedure described for Example 1 was followed
except that Adhesive Laminate-2 was used. Tape samples were
prepared from the sample of Adhesive Laminate-1 by removing one
liner, laminating to a 127 micrometer (5 mil) polyethylene
terephthalate film and then removing the other liner and laminating
Liner-2 to this construction. 180.degree. Peel Adhesion was
measured as described in the Test Method above, immediately after
adhesion to the glass plate or after a 24 hour dwell on the glass
plate. The results are shown in Table 1. Rebound Testing of a tape
sample was made. The results are shown in Table 2 and graphically
in FIG. 1.
TABLE-US-00002 TABLE 1 180.degree. Peel Adhesion 180.degree. Peel
Adhesion After Example Initial (N/dm) 24 Hour Dwell (N/dm) C1 60 60
2 48 62
TABLE-US-00003 TABLE 2 Elapsed Time Feature Depth (hours)
(Micrometers) 0 7.8 2 4.8 24 2.7 30 2.2 48 2.0 72 1.9 96 1.8 168
1.3
Comparative Example C2
[0044] For Comparative Example C2 a sample of Adhesive Laminate-3
as obtained was tested for 180.degree. Peel Adhesion as described
in the Test Method above. Peel Adhesion samples were tested at 5
minutes dwell, 15 minutes dwell, 30 minutes dwell, 60 minutes
dwell, 120 minutes dwell, 180 minutes dwell, 24 hour dwell and 48
hour dwell. The results are shown in Table 2. Over the same time
range as the Peel Adhesion testing, Percent Wet Out was also
measured using the Test method above. The results are in Table
3.
Example 3
[0045] For Example 3 a sample of Adhesive Laminate-3 was obtained
and the release liner was removed and Liner-2 was laminated to the
PSA using a laminator. The thus formed tape samples were tested for
180.degree. Peel Adhesion as described in the Test Method above.
Peel Adhesion samples were tested at 5 minutes dwell, 15 minutes
dwell, 30 minutes dwell, 60 minutes dwell, 120 minutes dwell, 180
minutes dwell, 24 hour dwell and 48 hour dwell. The results are
shown in Table 3. Over the same time range as the Peel Adhesion
testing, Percent Wet Out was also measured using the Test method
above. The results are in Table 4.
TABLE-US-00004 TABLE 3 180.degree. Peel 180.degree. Peel
180.degree. Peel 180.degree. Peel 180.degree. Peel 180.degree. Peel
180.degree. Peel 180.degree. Peel after 5 after 15 after 30 after
60 after 120 after 180 after 24 after 48 minutes minutes minutes
minutes minutes minutes hours hours Example (N/dm) (N/dm) (N/dm)
(N/dm) (N/dm) (N/dm) (N/dm) (N/dm) C2 40 43 46 48 48 46 49 52 3 30
37 45 48 49 51 50 50
TABLE-US-00005 TABLE 4 Wet Out Wet Out Wet Out Wet Out Wet Out Wet
Out Wet Out Wet Out Wet Out after 5 after 15 after 30 after 60
after 120 after 180 after 24 after 48 Initial minutes minutes
minutes minutes minutes minutes hours hours Example (%) (%) (%) (%)
(%) (%) (%) (%) (%) C2 85.6 90.0 95.0 95.3 96.4 95.4 95.4 98.6 100
3 70.3 76.0 84.8 82.0 82.0 88.3 94.6 99.8 100
Comparative Example C3
[0046] For Comparative Example C3 the same procedure was followed
as for Comparative Example C2 except that Adhesive Laminate-4 was
used in place of Adhesive Laminate-3. Peel Adhesion results are
shown in Table 5. Over the same time range as the Peel Adhesion
testing, Percent Wet Out was also measured using the Test method
above. The results are in Table 6.
Example 4
[0047] For Example 4 the same procedure was followed as for Example
3 except that Adhesive Laminate-4 was used in place of Adhesive
Laminate-3. Peel Adhesion results are shown in Table 5. Over the
same time range as the Peel Adhesion testing, Percent Wet Out was
also measured using the Test method above. The results are in Table
6.
TABLE-US-00006 TABLE 5 180.degree. Peel 180.degree. Peel
180.degree. Peel 180.degree. Peel 180.degree. Peel 180.degree. Peel
180.degree. Peel 180.degree. Peel after 5 after 15 after 30 after
60 after 120 after 180 after 24 after 48 minutes minutes minutes
minutes minutes minutes hours hours Example (N/dm) (N/dm) (N/dm)
(N/dm) (N/dm) (N/dm) (N/dm) (N/dm) C3 35 40 43 43 51 51 48 51 4 42
40 43 46 49 49 51 53
TABLE-US-00007 TABLE 6 Wet Out Wet Out Wet Out Wet Out Wet Out Wet
Out Wet Out Wet Out Wet Out after 5 after 15 after 30 after 60
after 120 after 180 after 24 after 48 Initial minutes minutes
minutes minutes minutes minutes hours hours Example (%) (%) (%) (%)
(%) (%) (%) (%) (%) C3 100 100 100 100 100 100 100 100 100 4 79.5
88.9 91.8 92.0 91.8 96.6 98.3 100 100
Comparative Example C4
[0048] For Comparative Example C4 a sample of Adhesive Laminate-5
as obtained was tested for 180.degree. Peel Adhesion as described
in the Test Method above. Peel Adhesion samples were tested at 5
minutes dwell, 15 minutes dwell, 30 minutes dwell, 60 minutes
dwell, 120 minutes dwell, 180 minutes dwell, 24 hour dwell and 48
hour dwell. The results are shown in Table 7.
Example 5
[0049] For Example 5 a sample of Adhesive Laminate-5 was obtained
and the release liner was removed and Liner-2 was laminated to the
PSA using a laminator. The thus formed tape samples were tested for
180.degree. Peel Adhesion as described in the Test Method above.
Peel Adhesion samples were tested at 5 minutes dwell, 15 minutes
dwell, 30 minutes dwell, 60 minutes dwell, 120 minutes dwell, 180
minutes dwell, 24 hour dwell and 48 hour dwell. The results are
shown in Table 7.
TABLE-US-00008 TABLE 7 180.degree. Peel 180.degree. Peel
180.degree. Peel 180.degree. Peel 180.degree. Peel 180.degree. Peel
180.degree. Peel 180.degree. Peel after 5 after 15 after 30 after
60 after 120 after 180 after 24 after 48 minutes minutes minutes
minutes minutes minutes hours hours Example (N/dm) (N/dm) (N/dm)
(N/dm) (N/dm) (N/dm) (N/dm) (N/dm) C4 6.2 NM 18.4 20.1 NM 20.6 30.4
32.1 5 8.3 7.9 8.3 9.8 10.5 12.8 20.9 27.5 NM = Not Measured
Comparative Example C5
[0050] For Comparative Example C5 a sample of Adhesive Laminate-6
as obtained was tested for 180.degree. Peel Adhesion as described
in the Test Method above. Peel Adhesion samples were tested at 5
minutes dwell, 15 minutes dwell, 30 minutes dwell, 60 minutes
dwell, 120 minutes dwell, 180 minutes dwell, 24 hour dwell and 48
hour dwell. The results are shown in Table 8.
Example 6
[0051] For Example 6 a sample of Adhesive Laminate-6 was obtained
and the release liner was removed and Liner-2 was laminated to the
PSA using a laminator. The thus formed tape samples were tested for
180.degree. Peel Adhesion as described in the Test Method above.
Peel Adhesion samples were tested at 5 minutes dwell, 15 minutes
dwell, 30 minutes dwell, 60 minutes dwell, 120 minutes dwell, 180
minutes dwell, 24 hour dwell and 48 hour dwell. The results are
shown in Table 8.
TABLE-US-00009 TABLE 8 180.degree. Peel 180.degree. Peel
180.degree. Peel 180.degree. Peel 180.degree. Peel 180.degree. Peel
180.degree. Peel 180.degree. Peel after 5 after 15 after 30 after
60 after 120 after 180 after 24 after 48 minutes minutes minutes
minutes minutes minutes hours hours Example (N/dm) (N/dm) (N/dm)
(N/dm) (N/dm) (N/dm) (N/dm) (N/dm) C5 49.3 41.2 55.9 54.0 56.0 52.0
50.2 52.6 6 32.8 28.1 38.4 42.2 41.9 50.2 34.6 40.9
Comparative Example C6
[0052] For Comparative Example C6 a sample of Adhesive Laminate-7
as obtained was tested by preparing laminates between 2 glass
plates or 2 PMMA plates. The laminates were prepared by removing
the bottom liner, applying to the substrate, and rolling over the
laminate with a hand roller. The top liner was then removed and the
second substrate was laminated to it using a hand roller. The
laminate was inspected using the Visual Inspection Test Method
above, both initially and after 24 hour dwell. The results are
shown in Table 9.
Example 7
[0053] For Example 7 a sample of Adhesive Laminate-7 was obtained
and the top and bottom release liners were removed and 2 pieces of
Liner-2 were laminated to the PSA with the microstructured face of
the liner into the adhesive. The thus formed tape samples were
tested by preparing laminates between 2 glass substrates or 2 PMMA
substrates. The laminates were prepared by removing the bottom
liner, applying the tape to the substrate and rolling a hand roller
over the laminate. The top liner was then removed and the second
substrate was laminated to it using a hand roller. The laminate was
inspected using the Visual Inspection Test Method above, both
initially and after 24 hour dwell. The results are shown in Table
9.
Example 8
[0054] For Example 8 a sample of Adhesive Laminate-7 was obtained
and the top and bottom release liners were removed and 2 pieces of
Liner-2 were laminated to the PSA. In this instance the top piece
of Liner-2 was laminated with the microstructured face of Liner-2
into the adhesive and the bottom piece of Liner-2 was laminated
with flat side of Liner-2 against the adhesive. The thus formed
tape samples were tested by preparing laminates between 2 glass
substrates or 2 PMMA substrates. The laminates were prepared by
removing the bottom liner, applying the tape to the substrate and
rolling a hand roller over the laminate. The top liner was then
removed and the second substrate was laminated to it using a hand
roller. The laminate was inspected using the Visual Inspection Test
Method above, both initially and after 24 hour dwell. The results
are shown in Table 9.
TABLE-US-00010 TABLE 9 Glass Substrates PMMA Substrates Visual
Visual Visual Inspection Visual Inspection Inspection Rating After
Inspection Rating After Example Rating Initial 24 hours Rating
Initial 24 hours C6 2 2 2 2 7 5 5 5 5 8 5 5 5 5
[0055] A number of embodiments of the invention have been
described. Nevertheless, it will be understood that various
modifications may be made without departing from the spirit and
scope of the invention. Accordingly, other embodiments are within
the scope of the following claims.
* * * * *