U.S. patent application number 16/505890 was filed with the patent office on 2020-01-09 for polishing protocol for zirconium diboride based ceramics to be implemented into optical systems.
The applicant listed for this patent is Arizona Board of Regents on Behalf of the University of Arizona. Invention is credited to Michael Hart, Dae Wook Kim, Joseph Rice.
Application Number | 20200009701 16/505890 |
Document ID | / |
Family ID | 69101314 |
Filed Date | 2020-01-09 |






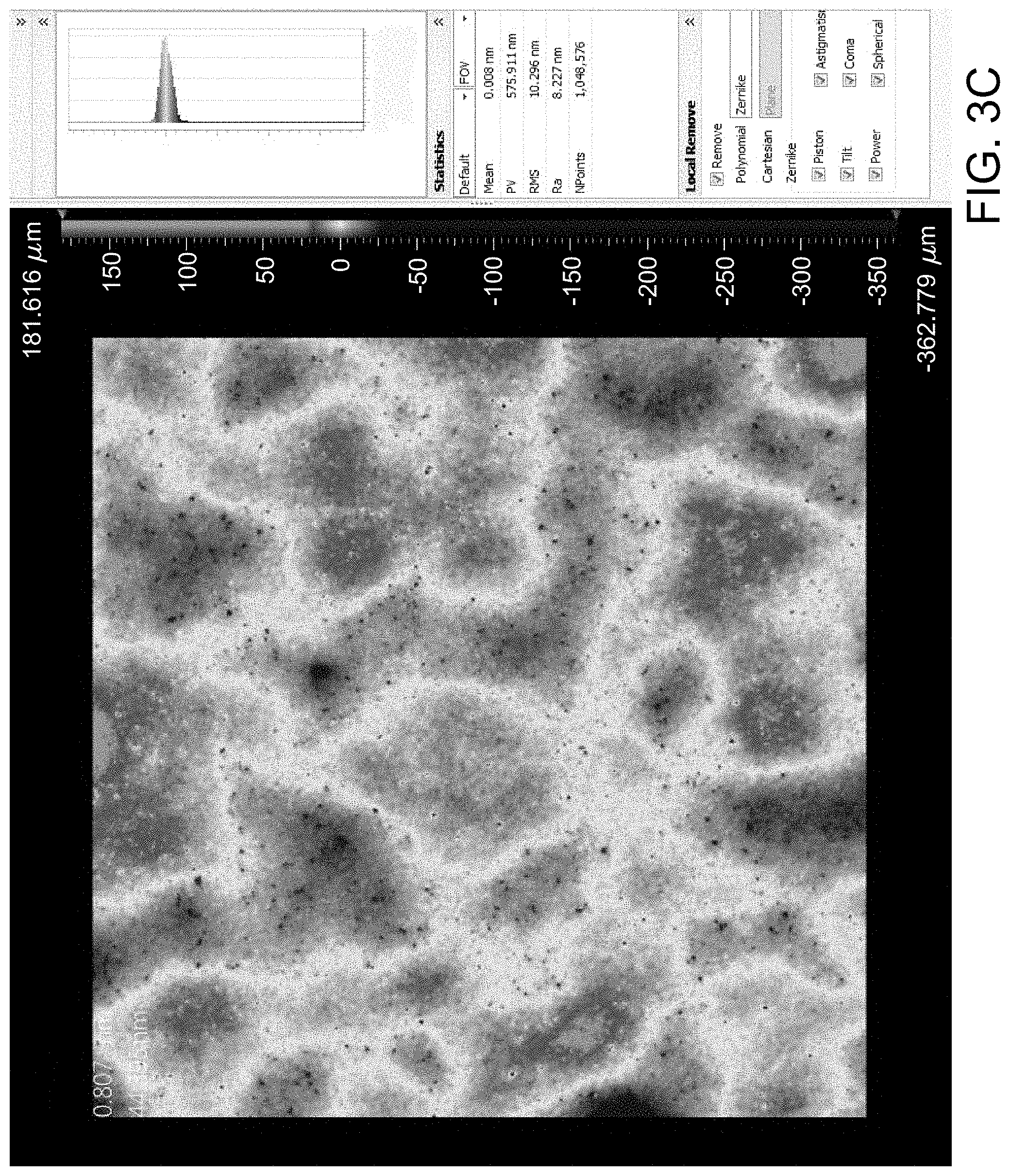
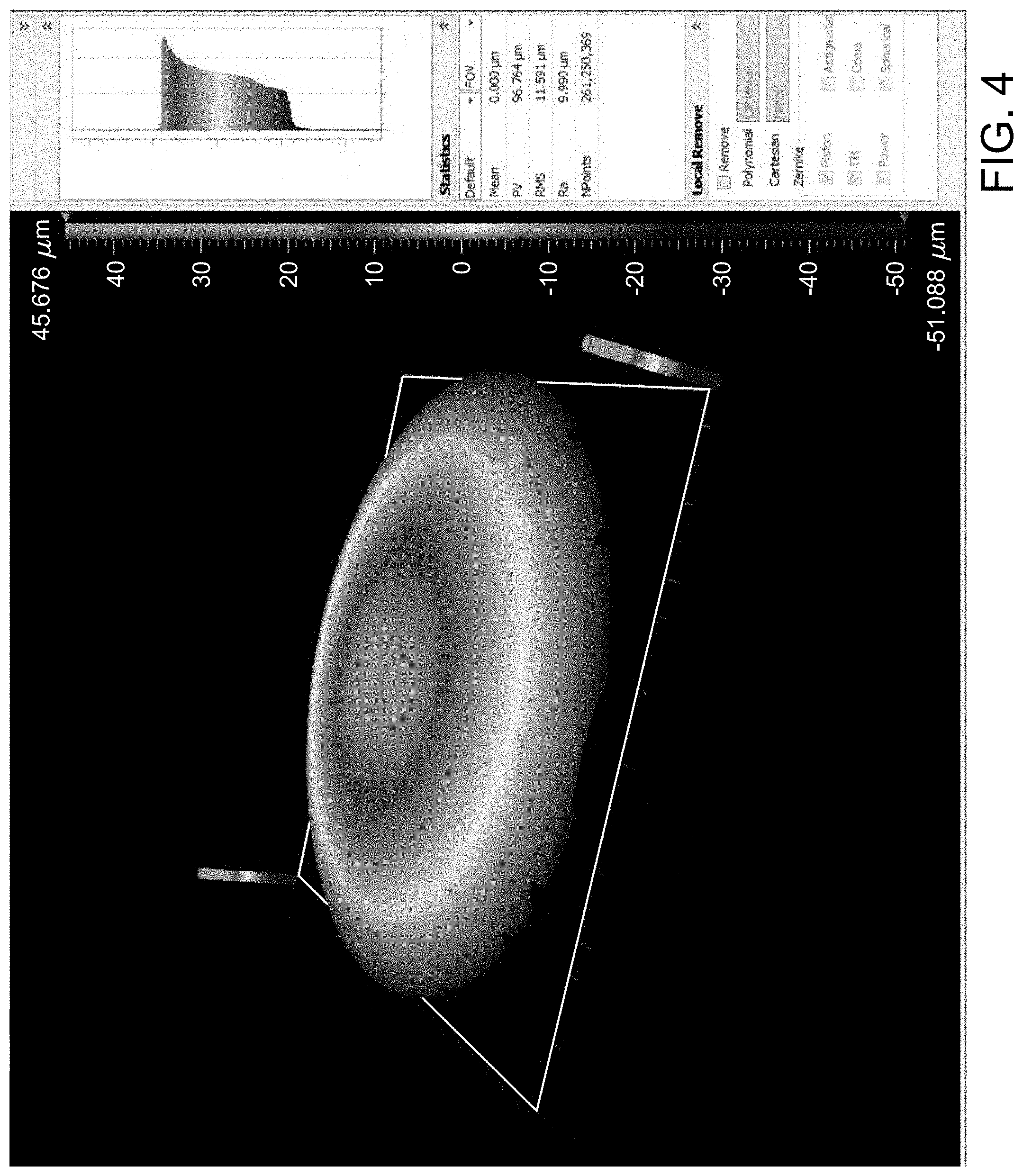

United States Patent
Application |
20200009701 |
Kind Code |
A1 |
Rice; Joseph ; et
al. |
January 9, 2020 |
POLISHING PROTOCOL FOR ZIRCONIUM DIBORIDE BASED CERAMICS TO BE
IMPLEMENTED INTO OPTICAL SYSTEMS
Abstract
The present disclosure relates to a polishing protocol for ZrB2
ceramics.
Inventors: |
Rice; Joseph; (Tucson,
AZ) ; Hart; Michael; (Tucson, AZ) ; Kim; Dae
Wook; (Tucson, AZ) |
|
Applicant: |
Name |
City |
State |
Country |
Type |
Arizona Board of Regents on Behalf of the University of
Arizona |
Tucson |
AZ |
US |
|
|
Family ID: |
69101314 |
Appl. No.: |
16/505890 |
Filed: |
July 9, 2019 |
Related U.S. Patent Documents
|
|
|
|
|
|
Application
Number |
Filing Date |
Patent Number |
|
|
62695598 |
Jul 9, 2018 |
|
|
|
Current U.S.
Class: |
1/1 |
Current CPC
Class: |
B24B 13/0031 20130101;
B24B 13/0018 20130101 |
International
Class: |
B24B 13/00 20060101
B24B013/00 |
Claims
1. A method comprising: polishing, using at least a first machine,
a ceramic material comprising zirconium diboride to a surface
roughness of less than 150 nm root mean square (RMS); and
polishing, using at least a second machine different from the first
machine, the ceramic material having a surface roughness of less
than 150 nm RMS to a surface roughness of less than 40 nm RMS.
2. The method of claim 1, wherein the ceramic material comprises at
least 75 wt % zirconium diboride as measured from a total of 100 wt
%.
3. The method of claim 1, wherein the ceramic material comprises
silicon carbide.
4. The method of claim 3, wherein the ceramic material comprises 25
wt % or less of silicon carbide as measured from a total of 100 wt
%.
5. The method of claim 1, wherein the ceramic material is polished
to a surface roughness of less than 10 nm RMS.
6. The method of claim 1, wherein the polishing, using a least a
first machine further comprises: using a first polishing
compound.
7. The method of claim 6, wherein the first polishing compound
comprises: a diamond disc, an aluminum oxide, and a coolant.
8. The method of claim 1, wherein the polishing, using a least a
second machine further comprises: using a second polishing
compound.
9. The method of claim 8, wherein the second polishing compound
comprises: diamond powder, vegetable oil, and deionized water.
10. The method of claim 1, wherein the polishing, using a least a
first machine further comprises: polishing the ceramic material at
a first speed.
11. The method of claim 1, wherein the polishing, using a least a
second machine further comprises: polishing the ceramic material at
a second speed.
12. The method of claim 1, wherein the first machine is a computer
numerical control (CNC) machine.
13. The method of claim 1, wherein the second machine is a
Strasbaugh machine.
14. An optical system comprising one or more optical components
formed from a method comprising: polishing, using at least a first
machine, a ceramic material comprising zirconium diboride to a
surface roughness of less than 150 nm root mean square (RMS); and
polishing, using at least a second machine different from the first
machine, the ceramic material having a surface roughness of less
than 150 nm RMS to a surface roughness of less than 40 nm RMS.
15. The system of claim 14, wherein the ceramic material comprises
at least 75 wt % zirconium diboride as measured from a total of 100
wt %.
16. The system of claim 14, wherein the ceramic material comprises
silicon carbide.
17. The system of claim 16, wherein the ceramic material comprises
25 wt % or less of silicon carbide as measured from a total of 100
wt %.
18. The system of claim 14, wherein the first machine is a computer
numerical control (CNC) machine.
19. The system of claim 14, wherein the second machine is a
Strasbaugh machine.
20. An optical apparatus formed from a method comprising:
polishing, using at least a first machine, a ceramic material
comprising zirconium diboride to a surface roughness of less than
150 nm root mean square (RMS); and polishing, using at least a
second machine different from the first machine, the ceramic
material having a surface roughness of less than 150 nm RMS to a
surface roughness of less than 40 nm RMS.
Description
CROSS-REFERENCE TO RELATED APPLICATIONS
[0001] This application claims the benefit of U.S. Provisional
Application No. 62/695,598, filed Jul. 9, 2018, which is hereby
incorporated herein in its entirety.
TECHNICAL FIELD
[0002] The technical field generally relates to methods for
polishing. More specifically, the technical field relates to
methods for polishing ceramics for optical systems.
BACKGROUND
[0003] One key component of adaptive optical systems is a
deformable mirror (DM). Through the use of actuators, a DM may
correct aberrations present in a wavefront being examined.
Generally, a DM and the components used to hold it in place are
comprised of different materials having different properties,
including, for example, thermal properties. The differences in the
materials and respective material properties can create engineering
challenges to these systems. For instance, thermally induced
aberrations, or in some instances, failure of one more components,
can occur, as the parts will generally have different coefficients
of thermal expansion. Thus, improvements are needed.
SUMMARY
[0004] A polishing method and corresponding system are contemplated
in the present disclosure. In various example embodiments, the
disclosure provides a method comprising polishing a ceramic
material comprising zirconium diboride to a surface roughness of
less than 40 nm root mean square (RMS). The method may include:
polishing, using at least a first machine, a ceramic material
comprising zirconium diboride to a surface roughness of less than
150 nm RMS; and polishing, using at least a second machine
different from the first machine, the ceramic material having a
surface roughness of less than 150 nm RMS to a surface roughness of
less than 40 nm RMS.
[0005] In various example embodiments, an optical system comprising
one or more optical components formed from the methods described
herein is also provided.
BRIEF DESCRIPTION OF THE DRAWINGS
[0006] FIG. 1 illustrates an example method flow in accordance with
an aspect of the present disclosure.
[0007] FIGS. 2A-2B illustrate machinery that may be used in one or
more of the disclosed methods.
[0008] FIGS. 3A-3C illustrate surface maps of a small portion of
the ceramic sample at various steps of the one or more disclosed
methods.
[0009] FIG. 4 illustrates an example 3-D full surface map after
polishing in accordance with an aspect of the present
disclosure.
[0010] FIG. 5 illustrates a polished ceramic sample.
DETAILED DESCRIPTION
[0011] The present disclosure describes systems and methods for
polishing ceramic materials or components of adaptive optical
systems, such as ceramics comprising zirconium diboride machined
for optical grade applications (e.g., facesheets for a DM having a
surface roughness error of 20 nm RMS or less). Systems and methods
for polishing according to the present disclosure may provide one
or more polished components to be integrated into an adaptive
optical system. As a non-limiting example, and in accordance with
aspects of the present disclosure, a ceramic material (e.g.,
zirconium diboride ceramics, ceramics comprising about 75%
ZrB.sub.2 and about 25% SiC, etc.), may be used in the adaptive
optics system. Such polished components, if comprised of the same
material, may be utilized in the adaptive optical system to reduce
or substantially eliminate thermally induced aberrations by
preventing certain causes of thermal expansion.
[0012] FIG. 1 illustrates a process flow chart of a method 100 in
accordance with the present disclosure. Prior to a first step of
method 100, a sample (e.g., an optical component) may be
manufactured in a sintering furnace. As an example, a sample disk
(e.g., 3 inch diameter flat disk with 0.8 mm thickness) may be
polished using the methods described herein. An initial shape of
the sample (e.g., a flat disc) may be defined by coarse grinding.
After sample fabrication, method 100 may move to a first step of
measuring a sample thickness 110. Method 100 may reduce surface
roughness through a plurality of polishing steps as disclosed
herein to achieve an adaptive optical system component (e.g., a
mirror) having surface deformations of less than about 2 nm RMS on
spatial scales below about a millimeter.
[0013] If the sample has a thickness within an acceptable range for
use in an adaptive optical system, method 100 may move to a step of
fine grinding 120. Method 100 may include, for instance, fine
grinding of the sample on a first machine. In some instances of the
disclosure, first machine comprises a CNC machine. FIG. 2A
illustrates a CNC machine that may be used in one or more of the
disclosed methods. The CNC machine may be driven by a custom code
written in Matlab. Multiple different parameters of the machine,
such as the polishing compound, speed, and pressure may be adjusted
to accomplish fine grinding to a target roughness. In exemplary
embodiments, the surface roughness of a sample may be decreased
from a starting roughness of about 0.265 .mu.m to and end roughness
of about 0.1330 .mu.m RMS. A diamond disc system (e.g., a Trizact
diamond disc system) may be utilized to accomplish a first fine
grinding step. For instance, a 9 .mu.m Trizact disc and a slurry of
Al.sub.2O.sub.3 and coolant may be utilized. In some embodiments,
the slurry may be comprised of a slurry of 5 .mu.m Al.sub.2O.sub.3
and Sabre coolant. However, it is understood that other
configurations and slurries may be used. In embodiments, diamond
grit sizes of 20, 9, and 3 .mu.m at 2.552 PSI and a speed of 500
mm/min may be selected at various grinding and/or polishing steps
of the method 100. If the sample is outside of an acceptable
thickness range, method 100 may proceed to interim step 115 of
grinding the sample, and the sample may then be remeasured (e.g.,
step 110) until a target thickness is achieved. Step 115 may be
accomplished using one or more diamond discs (e.g., 90 .mu.m
diamond discs).
[0014] Method 100 may then move to a step of measuring a surface
roughness error (e.g., RMS) of the sample 130. As described herein,
the surface roughness may be measured at one or more intervals
during the method 100. In some instance, RMS may be measured using
a Zygo white-light interferometer. However, other means of
measuring the surface roughness may be used, as would be
appreciated by one of skill in the art. If the RMS is around 185
nm, method may move to a second step of fine grinding 140. In some
embodiments, a 3 .mu.m Trizact and a slurry of 5 .mu.m
Al.sub.2O.sub.3 and coolant may be utilized. If the RMS is outside
of the range of about 185 nm, then previous method steps may be
repeated until the RMS is around 185 nm.
[0015] After the second fine grinding step 140, the RMS of the
sample may be measured 150, and, if the RMS is about 135 nm or
less, method 100 may move to a step of fine polishing the sample
160. Following the CNC machining, a Strasbaugh machine may be
utilized for finer polishing. FIG. 2B illustrates a Strasbaugh
machine that may be used in one or more of the disclosed methods. A
Strasbaugh machine may provide faster polishing times but allows
for easy deterioration of the shape of the material being polished.
In some embodiments, a first step of fine polishing the sample 160
may be accomplished using a diamond powder and a slurry of olive
oil and deionized water. For instance, a 1.5 .mu.m diamond powder
may be mixed with olive oil and deionized water. This slurry may be
applied, for instance, to a pellon pad to accomplish the fine
polishing. In embodiments, successive particle sizes of 1.5 and 0.5
.mu.m may be utilized in this or other fine polishing steps. In
embodiments, this step may lower the surface roughness to about 7
nm RMS.
[0016] After the first fine polishing step 160, the RMS of the
sample may be measured 170, and, if the RMS is around 20 nm, method
100 may move to a second step of fine polishing the sample 180.
Second fine polishing step 180 may be accomplished with 0.5 .mu.m
diamond powder and a slurry of olive oil and deionized water.
[0017] After the second fine polishing step 180, the RMS of the
sample may be measured 190, and, if the RMS is around 10 nm, method
100 may move to a third step of fine polishing 200. In some
embodiments, third fine polishing step 200 may be accomplished with
0.1 .mu.m diamond powder and a slurry of olive oil and deionized
water.
[0018] After the third fine polishing step 200, the RMS of the
sample may be measured 210, and, if the RMS is around 2 nm, method
100 may conclude 220 and a resultant polished sample may be ready
for use in an adaptive optical system. If the RMS is greater than
around 2 nm, the third step of fine polishing 200 may be repeated
until the sample reaches an RMS of around 2 nm.
[0019] Examples of the specifications for each of the grinding and
polishing steps are listed below in Table 1.
TABLE-US-00001 Polishing Pressure Polishing Resulting Machine
Compound (PSI) Speed Radius (mm) RMS (nm) CNC Trizact (20 .mu.m),
2.552 500 mm/min 3 328 Al.sub.2O.sub.3 (5 .mu.m), Sabre Coolant CNC
Trizact (9 .mu.m), 2.552 500 mm/min 3 184 Al.sub.2O.sub.3 (5
.mu.m), Sabre Coolant CNC Trizact (3 .mu.m), 2.552 500 mm/min 3 133
Al.sub.2O.sub.3 (5 .mu.m), Sabre Coolant Strasbaugh Diamond (1.5
.mu.m), 2.552 Eccentric: 35 RPM 30 20 Olive Oil, Spindle: 50 RPM
Deionized Water Strasbaugh Diamond (0.5 .mu.m), 2.552 Eccentric: 30
RPM 30 7 Olive Oil, Spindle: 50 RPM Deionized Water
However, it is understood that the decision points based on
satisfying a particular surface roughness may be example thresholds
and such process includes other thresholds within +/-20% of the
enumerated thresholds. Other tolerances may be used without
departing from the invention. It is further understood that
throughout the polishing process, other forms of polishing
compound, such as SiC and Al.sub.2O.sub.3, may be used.
[0020] FIGS. 3A-3C illustrate surface maps of a small portion of
the ceramic sample, approximately 0.8 mm on a side generated at one
or more key intervals in the polishing process. FIG. 3A shows a
surface map at the beginning of the polishing process with the RMS
surface error at about 265 nm. FIG. 3B shows a surface map
following Trizact polishing, with the RMS surface error reduced to
about 110 nm. FIG. 3C shows a surface map towards the end of
polishing, with the surface quality at about 10 nm RMS.
[0021] In FIG. 4, a map of a whole sample surface is illustrated.
The map is comprised of hundreds of successive measurements across
the entirety of the sample taken using the white-light
interferometer and stitched together to form the map. In the
illustrated map, the sample (e.g., a ceramic component comprising
zirconium diboride) has been polished to a low surface roughness
(e.g., less than 40 nm, 30 nm, 20 nm, 10 nm, 2 nm RMS). Significant
power is shown in the surface of the sample, caused by edge
roll-down from the Strasbaugh machine. In embodiments of the
disclosed method, the CNC machine may provide improved control of
the shape of sample during one or more steps of the polishing
method. To maintain the flat figure, controlled polishing can
accomplished with the CNC machine. The finer control possible with
the CNC machine may limit this error and the shape may be held to a
higher standard.
[0022] FIG. 5 illustrates a polished ceramic sample. The polished
sample may be, for instance, a ceramic disk having a diameter of
about 30 mm and a thickness of about 6 mm. Once polished down to a
surface roughness of between about 40 nm-2 nm RMS, including 40 nm,
30 nm, 20 nm, 10 nm, and 2 nm or less (and including intervening
end points), the sample (e.g., mirror) may be optically and
mechanically tested.
[0023] As described herein, methods for preparing a ceramic
material may provide for the manufacture of aspheric ceramic
facesheets for a DM that may be incorporated as the primary or
secondary mirrors of adaptively corrected telescopes. It is
understood that other components may be prepared using the same or
similar methods. A facesheet according to embodiments of the
disclosure may be lightweight and robust, with a thickness of about
0.8 mm, for example, and may be capable of handling high power
density. In some embodiments, a ceramic comprising zirconium
diboride may be utilized to polish to an optical finish (e.g., less
than 40 nm, 30 nm, 20 nm, 10 nm, 2 nm RMS). The material may be
durable having, for instance, a bulk modulus of about 5 times that
of conventional glass. Thus, a complete optical system may be built
that is robust and substantially lighter than a conventional glass
and metal system.
[0024] As described herein, the ZrB.sub.2 materials are of interest
for more than their athermal properties. They are also relatively
light-weight, durable, and very strong. This allows for adaptation
to many different optical systems.
* * * * *