U.S. patent application number 16/481195 was filed with the patent office on 2019-12-26 for method and formulation for preparing lignin fibres.
The applicant listed for this patent is FAURECIA SERVICES GROUPE, INSTITUT DE RECHERCHE TECHNOLOGIQUE JULES VERNE. Invention is credited to Maxence FACHE, Teddy FOURNIER, Ludivine JUNCA, Celia MERCADER.
Application Number | 20190390374 16/481195 |
Document ID | / |
Family ID | 58645211 |
Filed Date | 2019-12-26 |
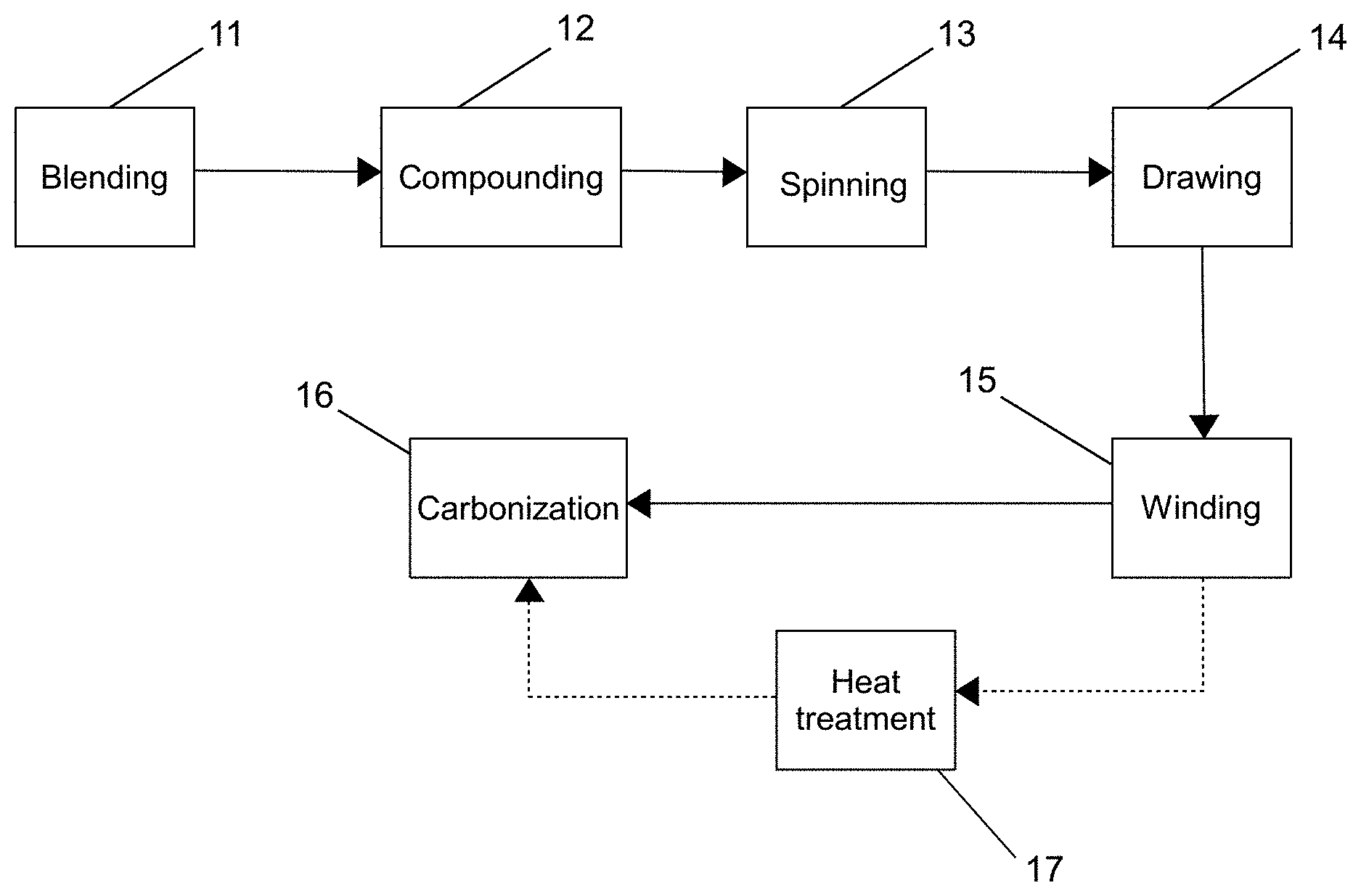

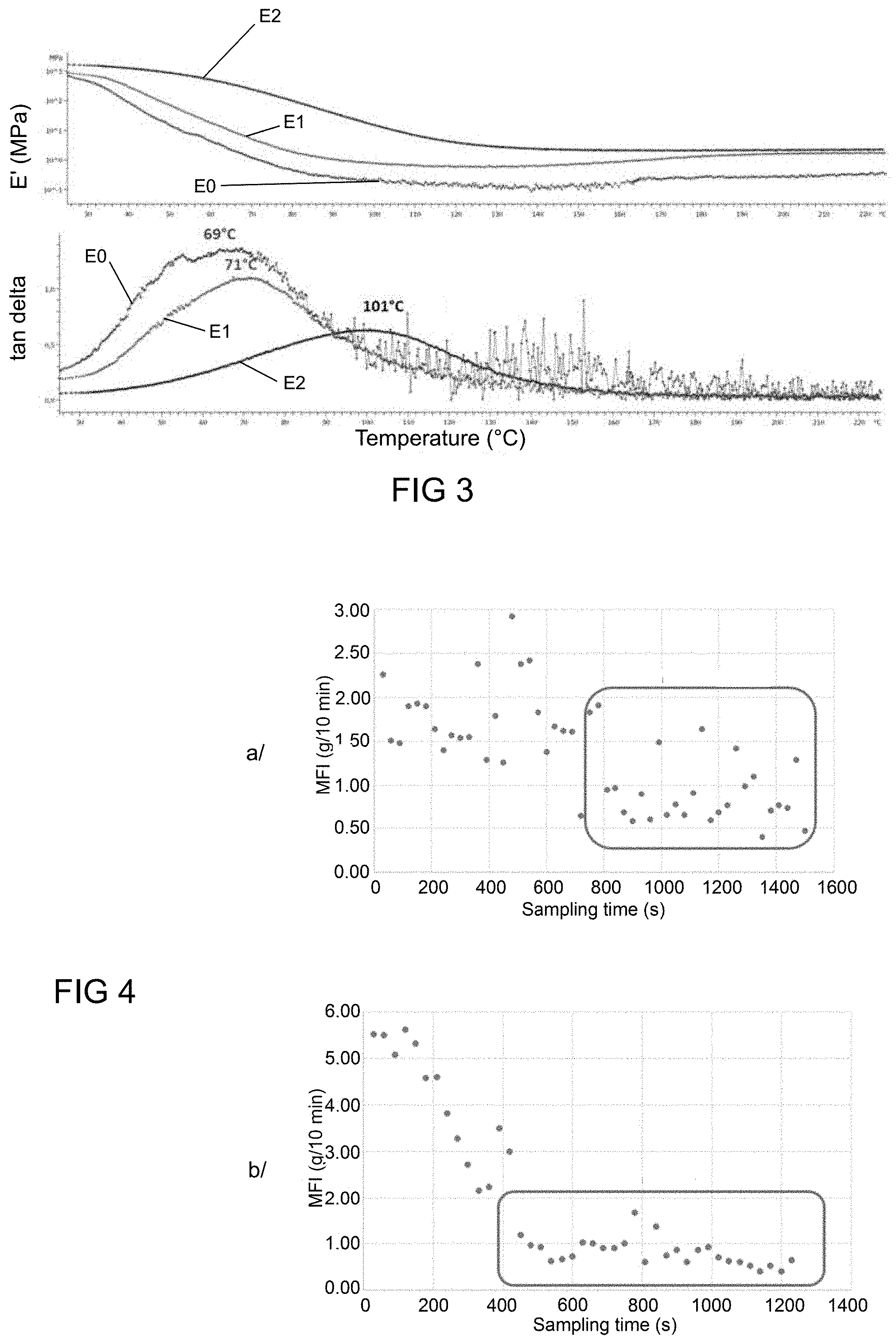
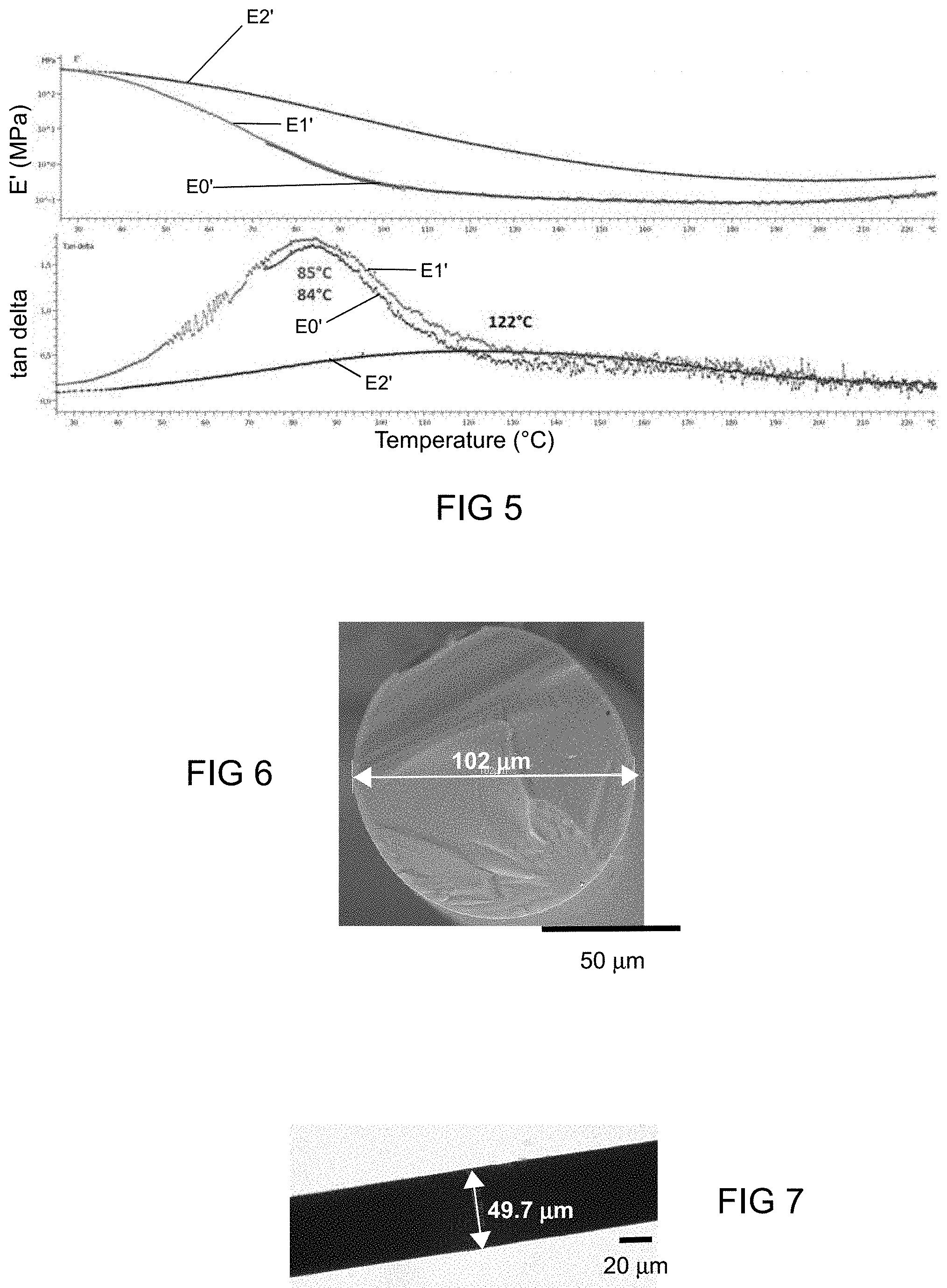

United States Patent
Application |
20190390374 |
Kind Code |
A1 |
FOURNIER; Teddy ; et
al. |
December 26, 2019 |
METHOD AND FORMULATION FOR PREPARING LIGNIN FIBRES
Abstract
A formulation for melt-preparation of lignin-based fibres, which
are precursors of carbon fibres. The formulation includes lignin, a
plasticiser and a cross-linking agent capable of cross-linking with
the lignin at a temperature at least 10.degree. C. higher than the
glass-transition temperature of the intimate blend of the lignin
and the plasticizer. A method for preparing lignin-based fibres
using this formulation includes the hot extrusion spinning of an
intimate blend of the components of the formulation, under adequate
conditions for cross-linking the cross-linking agent and the lignin
in the terminal area of the extrusion device used.
Inventors: |
FOURNIER; Teddy; (Maucor,
FR) ; JUNCA; Ludivine; (Billere, FR) ; FACHE;
Maxence; (Bordeaux, FR) ; MERCADER; Celia;
(Talence, FR) |
|
Applicant: |
Name |
City |
State |
Country |
Type |
INSTITUT DE RECHERCHE TECHNOLOGIQUE JULES VERNE
FAURECIA SERVICES GROUPE |
Bouguenais
Nanterre |
|
FR
FR |
|
|
Family ID: |
58645211 |
Appl. No.: |
16/481195 |
Filed: |
January 29, 2018 |
PCT Filed: |
January 29, 2018 |
PCT NO: |
PCT/FR2018/050191 |
371 Date: |
July 26, 2019 |
Current U.S.
Class: |
1/1 |
Current CPC
Class: |
D01D 5/38 20130101; D01F
9/00 20130101; D01F 9/17 20130101; C08L 97/005 20130101; D01F 6/54
20130101; D01F 8/18 20130101; D01F 1/10 20130101 |
International
Class: |
D01F 9/17 20060101
D01F009/17; D01D 5/38 20060101 D01D005/38; D01F 1/10 20060101
D01F001/10; D01F 8/18 20060101 D01F008/18 |
Foreign Application Data
Date |
Code |
Application Number |
Jan 27, 2017 |
FR |
1750688 |
Claims
1. A method for melt-preparation of lignin-based fibers,
comprising: a/ the intimate blending of the components of a
formulation comprising: lignin, a plasticizer miscible with said
lignin, and a cross-linking agent capable of cross-linking with
said lignin, in conditions in which no cross-linking of the
cross-linking agent and of the lignin occurs, b/ the spinning of
the intimate blend thus obtained in a hot extrusion device
comprising an extrusion head in a terminal part, in order to form
continuous threads, by application in said extrusion device of
conditions such that: the temperatures applied in said extrusion
device are higher than the glass-transition temperature of said
intimate blend, and the temperatures, the residence time of said
intimate blend in said extrusion device and the residence time of
said intimate blend in said extrusion head are such that the
cross-linking reaction of the cross-linking agent and lignin is
initiated only in the extrusion head, c/ when appropriate, the
drawing of the threads obtained in order to form lignin-based
fibers of great length, with the cross-linking agent being chosen
in such a way that the cross-linking reaction thereof with said
lignin is initiated in a time less than said residence time of said
intimate blend in said extrusion head at temperatures above a
temperature at least 10.degree. C. greater than the
glass-transition temperature of said intimate blend of said lignin
and of said plasticizer.
2. The method according to claim 1, wherein the step a/ of intimate
blending of the components of said formulation comprises the
following sub-steps: a1/ preparation of said formulation, by
blending of said lignin, said plasticizer and said cross-linking
agent, a2/ the blending by extrusion of the components of said
formulation, at a temperature greater than the glass-transition
temperature of the lignin and than a softening temperature of the
plasticizer, in order to form an extrudate in which the lignin, the
plasticizer and the cross-linking agent are in an intimate
blend.
3. The method according to claim 1, wherein the step b/ of spinning
of the intimate blend of the components of the formulation, it is
applied in the extrusion head a temperature that is greater than
the glass-transition temperature of said intimate blend by a value
of between 10 and 150.degree. C.
4. The method according to claim 1, wherein the lignin and the
plasticizer are such, and in proportions such, that the
glass-transition temperature of said intimate blend of said lignin
and of said plasticizer is between 0 and 180.degree. C.
5. Method according to claim 1, wherein the lignin has a weight
average molecular weight between 1,000 and 100,000 g/mol.
6. Method according to claim 1, wherein the plasticizer is a
polymer, or blend of polymers.
7. Method according to claim 1, wherein the plasticizer is a
fusible acrylonitrile polymer.
8. Method according to claim 1, wherein the plasticizer has a
glass-transition temperature, where applicable glass-transition
temperatures, of less than 150.degree. C.
9. Method according to claim 1, wherein the cross-linking agent is
chosen in the group consisting of: benzoxazines, epoxies,
oxazolines, polyoxymethylenes, aldehydes, hexamethylenetetramine
and hexamethylenemethoxymelamine; compounds that have a
functionality greater than or equal to two, of which the chemical
functions are chosen in the group consisting of the functions:
benzoxazine, epoxy (glycidyl ether in particular), isocyanate,
anhydride, carboxylic acid, methylol and ester, with these chemical
functions being identical or different, or any blend of such
compounds.
10. Method according to claim 1, wherein the cross-linking agent is
capable of initiating a cross-linking reaction with the lignin in
less than 10 minutes at a temperature between 30 and 190.degree.
C.
11. Method according to claim 1, wherein the cross-linking agent is
capable of cross-linking with the lignin at ambient
temperature.
12. Method according to claim 1, wherein said formulation comprises
the following percentages by weight, with respect to the total
weight of the formulation: 50 to 98% of lignin, and/or 1 to 49% of
plasticizer, and/or 1 to 25%, preferably 2 to 10%, preferentially
2.5 to 5%, of cross-linking agent.
13. Method according to claim 1, wherein said formulation comprises
one or several additives chosen in the group consisting of carbon
fillers of nanometric size, alone or in a mixture.
14. Method according to claim 1, wherein a final step of storage of
said lignin-based fiber at ambient temperature.
15. Formulation for the implementing of a method of
melt-preparation of lignin-based fibers according to claim 1,
comprising: lignin that is not chemically modified, a plasticizer
miscible with said lignin, and a cross-linking agent capable of
initiating a cross-linking reaction with said lignin in less than
10 minutes at temperatures above a temperature at least 10.degree.
C. greater than the glass-transition temperature of said intimate
blend of said lignin and of said plasticizer.
16. Formulation according to claim 15, wherein the plasticizer is a
fusible acrylonitrile polymer.
17. Lignin-based extrudate obtained at the end of the step a/ of
intimate blending of the components of the formulation of a method
according to claim 1.
18. Lignin-based fiber obtainable by a method according to claim 1,
having a length greater than or equal to 1 m.
19. A method for the manufacture of carbon fibers, comprising a
step of using a lignin-based fiber according to claim 18.
20. Method for the manufacture of a carbon fiber, comprising: 1/
the melt-preparation of lignin-based fiber, comprising: a/ the
intimate blending of the components of a formulation comprising:
lignin, a plasticizer miscible with said lignin, and a
cross-linking agent capable of cross-linking with said lignin, in
conditions in which no cross-linking of the cross-linking agent and
of the lignin occurs, b/ the spinning of the intimate blend thus
obtained in a hot extrusion device comprising an extrusion head in
a terminal part, in order to form continuous threads, by
application in said extrusion device of conditions such that: the
temperatures applied in said extrusion device are higher than the
glass-transition temperature of said intimate blend, and the
temperatures, the residence time of said intimate blend in said
extrusion device and the residence time of said intimate blend in
said extrusion head are such that the cross-linking reaction of the
cross-linking agent and lignin is initiated only in the extrusion
head, c/ when appropriate, the drawing of the threads obtained in
order to form lignin-based fibers of great length, with the
cross-linking agent being chosen in such a way that the
cross-linking reaction thereof with said lignin is initiated in a
time less than said residence time of said intimate blend in said
extrusion head at temperatures above a temperature at least
10.degree. C. greater than the glass-transition temperature of said
intimate blend of said lignin and of said plasticizer; and
2/subjecting the lignin-based fiber thus obtained to a
carbonization treatment.
21. Method for the manufacture of a carbon fiber according to claim
20, wherein said lignin-based fiber is not subjected to any heat
treatment step prior to the implementing of the carbonization
treatment.
22. Method for the manufacture of a carbon fiber according to claim
20, wherein prior to the treatment of said lignin-based fiber by
carbonization, a step of heat treating said lignin-based fiber
during a period between 10 and 60 minutes.
Description
CROSS REFERENCE TO RELATED APPLICATIONS
[0001] This application is a National Stage of International
Application No. PCT/FR2018/050191, having an International Filing
Date of 29 Jan. 2018, which designated the United States of
America, and which International Application was published under
PCT Article 21(2) as WO Publication No. 2018/138450 A1, which
claims priority from and the benefit of French Patent Application
No. 1750688, filed on 27 Jan. 2017, the disclosures of which are
incorporated herein by reference in their entireties.
BACKGROUND
1. Field
[0002] The present disclosure relates to the field of manufacturing
carbon fibers from biosourced materials.
[0003] More particularly, the present disclosure relates to a
method for preparing lignin-based fibers, via the melt technique,
as well as a formulation for the implementation of this method. The
present disclosure also relates to lignin-based fibers that can be
obtained by such a method, as well as an extrudate, in particular
in the form of granules, obtainable as an intermediate product
during the implementation of said method. The present disclosure
further relates to the use of a lignin-based fiber obtained by a
method according to the present disclosure for the manufacture of
carbon fibers, as well as, more generally, to a method of
manufacturing a carbon fiber using such a lignin-based fiber.
2. Brief Description of Related Developments
[0004] Carbon fibers are used in many fields, making use of their
particularly advantageous mechanical, electrical and thermal
properties and their low weight.
[0005] Manufacturing carbon fibers from renewable biosourced
materials, in order to overcome the problem of the programmed
depletion of fossil resources, has been the subject of much
research in the last few decades. It has in particular been
proposed by prior art to manufacture such fibers from lignin, a
macromolecule with a complex structure and a high carbon content
that forms one of the main components of wood, and which is present
in large quantities in nature.
[0006] Lignin offers in particular the advantage of being able to
be obtained by means of methods that are not toxic for the
environment and at a low cost. It can furthermore be formed by
spinning in order to form fibers, which can be used as precursors
of carbon fibers.
[0007] The methods for manufacturing carbon fibers from lignins
developed by the prior art globally implement the following
successive steps: the preparation of lignin-based fibers, by
spinning of a formulation containing lignin, the
stabilizing/structuring of the lignin-based fibers thus obtained by
an oxidative thermal treatment, and the carbonization of stabilized
fibers, in order to form the carbon fibers sought.
[0008] In particular, the stabilization of lignin-based fibers is
required to prevent these fibers from melting during the rise in
temperature to which they are subjected during the step of
carbonization. Conventionally, on the laboratory scale, this
stabilization is carried out by cross-linking of the lignin under
an oxidizing atmosphere, by exposure of the fibers to very slow
temperature increase gradients, of about 0.02.degree. C./min, for
very long periods of time, typically of about several hours and up
to several days, in order to reach temperatures as high as 300 to
400.degree. C. This method cannot however be transposed
industrially, in a continuous process, as it is too long and
expensive in terms of energy to be implemented.
[0009] There are today two main spinning techniques for preparing
lignin-based fibers: the so-called solvent or wet technique, and
the so-called melt technique.
[0010] The present inventors took more particular interest in the
melt technique for preparing fibers, wherein the fibers are formed
by melt spinning, typically by means of an extrusion device, this
technique having the advantages of great simplicity and quickness
to implement. Schematically, the lignin is subjected to a
temperature gradient that is high enough to provoke the creeping
thereof, which makes it possible to draw it in order to form a
thread.
[0011] In this particular field of preparing lignin-based fibers by
the melt spinning technique, it has been proposed by the prior art,
in order to improve the properties of aptitude for spinning and the
quality of the lignin, to modify it chemically and/or to add
various additives to it.
[0012] Document DE 102014004797 describes for example a method for
preparing lignin-based fibers using a formulation containing
chemically-modified lignin, more particularly esterified or
etherified, and additives with various functions, such as a
plasticizing function and/or a cross-linking function. Such a
method however makes it only possible to obtain lignin-based fibers
of short size, from 10 to about 20 cm. Furthermore, these fibers
must even so be subjected to a high-temperature heat stabilization
treatment before the final step of carbonization aiming at
obtaining the carbon fibers. As mentioned hereinabove, the carrying
out of this step of thermo-oxidative stabilization takes a lot of
time and uses a lot of energy.
[0013] In order to stabilize the lignin-based fibers obtained by
melt spinning, in order to overcome the problems related to the
implementation of the step of thermo-oxidative stabilization of the
fibers, it was otherwise proposed by the prior art, such as
illustrated by document EP 2 644 758, to incubate the lignin
fibers, obtained by melt spinning, with a cross-linking agent, at a
temperature at which no cross-linking occurs, then to subject the
fibers to a step of heat treating at a temperature that allows for
the cross-linking of the lignin of the fibers with the
cross-linking agent. Although this method can be implemented at
lower temperatures and more quickly than the methods of
thermo-oxidative stabilization heat treatment of fibers of the
prior art, it however requires even so a substantial heating of the
fibers, and a certain time for implementation. The step of soaking
fibers in a bath containing the cross-linking agent is in
particular long, expensive, technically complex and constraining to
implement.
SUMMARY
[0014] The present disclosure aims to overcome the disadvantages of
the methods for preparing lignin-based fibers proposed by the prior
art, in particular the disadvantages mentioned hereinabove, by
proposing a method for such a preparation, and a formulation for
the implementation thereof, which makes it possible to form
lignin-based fibers, including continuous fibers of a long size, in
particular of several hundred meters long, which are sufficiently
stable to be able to be directly subjected to a step of
carbonization, in order to form carbon fibers, without intermediate
oxidative heat stabilization treatment, or with an intermediate
heat treatment of a much shorter duration.
[0015] An additional objective of the present disclosure is that
such lignin-based fibers can be obtained quickly, easily, in few
steps and at a low cost.
[0016] The present disclosure also aims for this method to be able
to be applied to all forms of lignin, regardless of their origin
and their method of obtaining, and including unmodified forms of
lignin.
[0017] To this effect, according to a first aspect, it is proposed
by the present disclosure a method for the preparation of
lignin-based fibers, precursors of carbon fibers. This method
comprises the following steps:
[0018] a/ when necessary, the intimate blending of the components
of a formulation comprising: [0019] lignin, [0020] a plasticizer
that is miscible, in particular when hot, with the lignin, [0021]
and a cross-linking agent capable of cross-linking with the
lignin,
[0022] in conditions, in particular conditions of temperature and
of time, in which no cross-linking of the cross-linking agent and
of the lignin occurs,
[0023] b/ the spinning of this intimate blend in a melt extrusion
device comprising an extrusion head in a terminal part, in order to
form continuous threads, by application in the extrusion device of
conditions, in particular of temperature profiles and of residence
times in the device, which are such that: [0024] the temperatures
applied in the extrusion device are greater than the
glass-transition temperature of the intimate blend, [0025] and the
temperatures, the residence time of the intimate blend in the
extrusion device, and the residence time of the intimate blend in
the extrusion head are such that the cross-linking reaction of the
cross-linking agent and of the lignin is initiated in the extrusion
head, and only in the latter,
[0026] c/ when appropriate, the drawing, in particular the
continuous drawing, of the lignin-based threads obtained, in order
to form lignin-based fibers of great length.
[0027] The cross-linking agent is chosen in such a way that the
cross-linking reaction thereof with the lignin is initiated in a
time that is less than the residence time of the intimate blend in
the extrusion head at (and only at) temperatures above (including
equal to) a temperature at least 10.degree. C. greater than the
glass-transition temperature of the intimate blend of the lignin
and of the plasticizer.
[0028] The expression "operating cross-linking temperature", will
be used, by commodity in the rest of this description, to designate
the lowest temperature at which a cross-linking reaction of the
cross-linking agent and of the lignin is initiated in a time that
is less than the residence time of the intimate blend in the
extrusion head, which forms the terminal portion of the extrusion
device. According to the present disclosure, the cross-linking
agent is chosen in such a way that this operating cross-linking
temperature is at least 10.degree. C. higher than the
glass-transition temperature of the intimate blend of the lignin
and of the plasticizer.
[0029] According to the present disclosure, the choice of the
cross-linking agent, and of the conditions of temperature and of
residence time of the intimate blend in the various parts of the
extrusion device, is preferably carried out simultaneously, so as
to make it possible to achieve a softening of the intimate blend
that is sufficient for the spinning of the intimate blend and the
formation of lignin-based threads, while initiating the
cross-linking reaction of the cross-linking agent and of the lignin
in the terminal part of the extrusion device, and only in the
latter.
[0030] It is within the competences of those skilled in the art to
carry out such a joint choice, knowing that typically, the
residence time of the material in the terminal part of an extrusion
device is of a few tens of seconds to a few minutes, for example
between 30 seconds and 10 minutes, in particular between 30 seconds
and 5 minutes.
[0031] Those skilled in the art know perfectly how to determine,
according to the extrusion device that is used, which part forms
the extrusion head. Typically, this is the terminal part of the
device, located downstream of the parts for feeding the device with
material and of the parts for conveying this material, in the
direction of flow of the material, and in which is carried out the
forming of the material. The extrusion head is in particular
terminated by the spinning die.
[0032] According to the present disclosure the term lignin
encompasses a single lignin as well as a mixture of different
lignins.
[0033] Likewise, the expression "plasticizer" encompasses, in
addition to a single plasticizer, any blend of a plurality of
plasticizers, and the expression "cross-linking agent" encompasses,
in addition to a single cross-linking agent, any blend of a
plurality of cross-linking agents.
[0034] Moreover, also within the scope of the present disclosure
are the methods according to which the plasticizer and the
cross-linking agent are formed by a single and same compound, which
alone combines the plasticizing function and the cross-linking
function, and the characteristics of being miscible with the lignin
and of being capable of initiating a cross-linking reaction with
the latter in a time less than the residence time of the intimate
blend in the extrusion head of the extrusion device, at
temperatures above a temperature at least 10.degree. C. greater
than the glass-transition temperature of the intimate blend that it
forms with the lignin.
[0035] The phrase "intimate blend of the lignin and of the
plasticizer" means, conventionally in itself, a blend obtained by
mixing these components at a temperature that is greater than or
equal to the glass-transition temperature of the lignin and to the
softening temperature of the plasticizer, in particular to the
melting temperature of the plasticizer when the latter is a
crystalline or semi-crystalline material. Typically, the
glass-transition temperature of the intimate blend of the lignin
and of the plasticizer is less than that of the lignin alone.
[0036] In the present description, the terms "softening temperature
of the plasticizer" mean the temperature above which this
plasticizer becomes sufficiently fluid to be able to be mixed
intimately with the lignin and the cross-linking agent, by any
conventional means in itself for the formation of intimate blends
of compounds, in particular via extrusion.
[0037] The softening temperature can be determined by any method of
conventional thermal and/or thermomechanical analysis that makes it
possible to reveal the rheological and/or mechanical properties in
temperature of the plasticizer considered. This analysis can for
example be a measurement of the melt flow index (MFI) of the
plasticizer at different temperatures, as explained in detail
further on in the present description.
[0038] The glass-transition temperature, designated by the
abbreviation Tg, of the intimate blend of the lignin and of the
plasticizer depends on the particular characteristics of the lignin
and of the plasticizer used, in particular the molar mass of the
plasticizer, as well as their respective proportions in the blend.
It falls within the competences of those skilled in the art to
determine, for each given lignin--plasticizer blend, what is the
associated glass-transition temperature. To this effect, those
skilled in the art can in particular prepare an intimate blend of
these constituents, in the proportions of the formulation according
to the present disclosure, according to any conventional method,
then measure the glass-transition temperature thereof. Those
skilled in the art can for this use any conventional method in
itself, such as dynamic mechanical analysis (DMA).
[0039] In the context of the present disclosure, the
glass-transition temperature of the intimate blend of the lignin
and of the plasticizer is more preferably measured by dynamic
mechanical analysis, in particular according to the following
method: using parallelepiped samples of dimensions 5 mm.times.2
mm.times.0.8 mm of material, it is implemented a DMA 1 analyzer
from Mettler Toledo in solicitation in tension, operating at 1 Hz,
with a gradient of 2.degree. C./min and a displacement of 2
.quadrature.m.
[0040] According to the present disclosure, the cross-linking of
the cross-linking agent and of the lignin is advantageously carried
out, at least partially, in the extrusion device itself. The
cross-linking agent reacts therein with the lignin, in order to
create a three-dimensional network that stabilizes the fibers, and
which extends in all of the threads obtained, including in the core
of the fibers. This stabilization is advantageously sufficient to
allow for a direct carbonization of the lignin-based fibers thus
obtained, without it being in particular required to subject them
beforehand to thermo-oxidative stabilization treatment, or at least
to nothing other than a heat treatment of a very short duration. An
example of such subsequent heat treatment can for example consist
in a heating of the fibers in an oven, under oxygen or under
nitrogen for example, for a duration of a few tens of minutes, for
example of about 30 minutes, in such a way as to quickly complete
the cross-linking of the cross-linking agent and of the lignin that
had begun in the extrusion device.
[0041] The cross-linking is furthermore advantageously initiated
only in the terminal part of the extrusion device, in the extrusion
head itself, so that this cross-linking does not slow down, or
block, in any case, the step of spinning of the method according to
the present disclosure.
[0042] The introduction, in the formulation according to the
present disclosure, of the cross-linking agent, and its intimate
blend with the lignin, before proceeding with the melt spinning,
makes it possible to form, at the end of the spinning step, a fiber
containing the lignin and the plasticizer, which has a mechanical
resistance that is sufficient to support, without breaking, the
rise in temperature required for the later step of
carbonization.
[0043] Compared to the methods proposed by the prior art to carry
out the stabilization of the lignin fibers, in particular by
cross-linking of the lignin under an oxidizing atmosphere with very
slow temperature increase gradients, the method according to the
present disclosure thus makes it possible more easily and more
quickly to obtain fibers that are ready to be subjected to the step
of carbonization, and this at least cost.
[0044] The method according to the present disclosure
advantageously makes it possible to obtain continuous fibers of
great length, in particular of several hundred, even several
thousand meters.
[0045] Furthermore, it can be applied, with the same success, to
lignins of any origin and of any nature and regardless of the
method that made it possible to obtain them. It also applies, with
the same effectiveness, to any form of lignin, including to lignins
that are not chemically modified. It applies in particular to
lignins that have a low faculty to be thermo-oxidized.
[0046] It is easy and quick to implement, and comprises only a few
steps. The lignin-based fiber obtained at the output of the
extrusion device can furthermore advantageously be placed on a coil
directly, or when necessary after a simple step of drawing.
[0047] This method makes it possible to obtain at low cost
lignin-based fibers that are capable of being subjected to a step
of carbonization in order to form carbon fibers.
[0048] The method of melt preparation of lignin-based fibers
according to the present disclosure can respond to one or several
of the characteristics described hereinafter, implemented
separately or in each one of their technically operative
combination.
[0049] In particular aspects of the present disclosure, the
cross-linking agent is chosen to be capable of initiating a
cross-linking reaction with the lignin in less than 10 minutes,
preferably in less than 5 minutes, at a temperature between 30 and
190.degree. C., preferably between 80 and 170.degree. C.
[0050] Preferentially, it is furthermore chosen to be capable of
cross-linking with the lignin at a temperature between -15 and
25.degree. C., in particular at ambient temperature, i.e. at a
temperature of about 20.degree. C., and more largely between 15 and
25.degree. C., with the cross-linking at these temperatures then
being slow.
[0051] In particular aspects of the present disclosure, in the
formulation, the plasticizer makes it possible, conventionally, to
make the lignin more spinnable, at a lower temperature.
[0052] In the formulation according to the present disclosure, the
lignin and the plasticizer are preferably such, and in proportions
such, that the glass-transition temperature of said intimate blend
of said lignin and of said plasticizer is between and 180.degree.
C., in particular between 20 and 180.degree. C., preferably between
20 and 100.degree. C., in particular between 20 and 80.degree. C.,
and for example around 60.degree. C. Such a characteristics
advantageously makes it possible to operate, for the implementation
of the steps of the method for preparing lignin-based fibers
according to the present disclosure, at relatively low
temperatures, which do not provoke any degradation in the various
components of the formulation, and which can be achieved with a low
energy consumption.
[0053] The lignin entering into the composition of the formulation
according to the present disclosure can be of any type.
[0054] The term lignin means in particular, in the present
description, lignin that is substantially pure, not modified, as
well as the derivatives thereof. According to the present
disclosure the term derivatives encompasses the partially
fractionated products of the lignin, as well as the chemical
derivatives of the lignin, in particular esterified or etherified
lignins.
[0055] In particular aspects of the present disclosure, the lignin
used in the formulation is a non-chemically modified lignin. By
this it is meant that the lignin has not been subjected to any type
of chemical modification, in particular to no step of
esterification, etherification, and/or reaction introducing into
its formula one or several groups of sulfonate, phosphate,
phosphonate, phosphinate, phosphite, phosphonite, phosphinite,
etc.
[0056] The lignin can in particular be introduced into the
formulation in the form of a salt, or of a partially purified
extract, containing it in a blend with other components. Such an
extract can be obtained according to any conventional method in
itself for those skilled in the art. For example, the lignin can be
introduced into the formulation in a partially purified form, such
as the Kraft lignin or the Soda lignin, or in the form of
Organosolv lignin, or as any blend of such lignins.
[0057] The lignin that enters into the composition of the
formulation according to the present disclosure preferably has a
high molecular weight, in particular a weight average molecular
weight between 1000 and 100,000 g/mol, preferably between 1500 and
10,000 g/mol, for example between 3,000 and 10,000 g/mol, and in
particular between 5,000 and 10,000 g/mol; and/or a number average
molecular weight between 300 and 100,000 g/mol, preferably between
400 and 10,000 g/mol, and in particular between 500 and 10,000
g/mol.
[0058] The weight average molecular weight and the number average
molecular weight of the lignin can be determined by any
conventional method, in particular by gel permeation chromatography
(GPC). For the implementation of this technique, those skilled in
the art can for example chose as an eluent tetrahydrofurane,
conventionally per se. In this case, the lignin to be analyzed must
first be derivatized in order to be put into solution. This can be
accomplished by acetylating the lignin, for example by having it
react with acetic anhydride in the presence of pyridine. After
purification of the acetylated lignin, the latter can be put into
solution in the tetrahydrofurane, filtered and analyzed via GPC at
ambient temperature. The number and the weight average molecular
weights can then be determined using calibration curves, for
example obtained with polystyrene.
[0059] A particularly preferred lignin in the context of the
present disclosure is the lignin marketed under the name Protobind
2400 by the company GreenValue. This is a soda lignin without
sulfur, obtained from wheat straw, having a glass-transition
temperature between 100 and 120.degree. C., a number average
molecular weight of about 1000 g/mol and a weight average molecular
weight, measured by GPC as explained hereinabove, between 1,500 and
3,500 g/mol, more particularly equal to 2,000 g/mol. This lignin
further has in particular a carbon content between 55 and 65% of
the atoms, a content of --OH aliphatic functions between 1 and 2
mmol/g, a content of --OH aromatic functions between 2.5 and 3
mmol/g, and a content of --COOH functions between 0.5 and 1
mmol/g.
[0060] Another lignin that can be used in the context of the
present disclosure is in particular the lignin of the Kraft type
marketed under the name BioPiva.RTM. 100 (formerly BioChoice.RTM.)
by the company UPM. This lignin has in particular: a
glass-transition temperature between 130 and 160.degree. C.; a
weight average molecular weight between 8,000 and 10,000 g/mol; a
carbon content between 60 and 70% of the atoms; a content of --OH
aliphatic functions between 1.5 and 2 mmol/g; a content of --OH
aromatic functions between 3.5 and 4 mmol/g; and a content of
--COOH functions between 0 and 0.5 mmol/g.
[0061] The plasticizer entering into the composition of the
formulation according to the present disclosure is more preferably
of the polymer type. The term "polymers" here also encompasses the
copolymers and the blends of polymers and/or copolymers. The
plasticizer is preferably chosen from polyethers, polycarboxylates
and polyesters, such as for example poly(ethylene oxide) (PEO),
polyethylene terephthalate or polycaprolactone, or any blend of
such polymers. In particular aspects of the present disclosure, the
plasticizer is a fusible acrylonitrile polymer, commonly designated
by the expression "fusible PAN". Included in this definition is any
polymer or copolymer of acrylonitrile suitable for being
implemented in a method of melt extrusion.
[0062] The plasticizer according to the present disclosure can also
be chosen from all the copolymers of which at least one of the
monomer segments belongs to one of the polymers families
hereinabove. Examples of such copolymers are poly(ethylene
oxide)-co-poly(propylene oxide) (PEO-co-PPO) copolymers, such as
the copolymer marketed under the name Alkox.RTM. CP-A2H), and more
generally all copolymers that comprise a polyether block and/or a
polyacrylonitrile block.
[0063] For the plasticizer, it is in particular advantageously
possible to choose as a fusible PAN a copolymer of
polyacrylonitrile and of methylacrylate, in particular a
poly(acrylonitrile-co-methyl
acrylate)-block-poly(acrylonitrile-co-butadiene), such as the
copolymers marketed under the name Barex.RTM., in particular
Barex.RTM. 210 or known commercial derivatives.
[0064] The implementation of fusible PAN as a plasticizer is in
particular entirely advantageous in terms of mechanical properties
and stability over time of the fibers obtained. These fibers have
in particular great flexibility and a spinning resistance that is
particularly good.
[0065] The plasticizer used preferably has a weight average
molecular weight greater than 100 g/mol, preferentially greater
than or equal to 160 g/mol. Such a characteristic confers on the
formulation according to the present disclosure a hot viscosity
that is high enough to allow it to be handled easily during the
carrying out of the steps of the method according to the present
disclosure, and to ensure good mechanical resistance of the
lignin-based fiber obtained at the end of this method.
[0066] More particularly, when the plasticizer belongs to the
family of polyethers, its weight average molecular weight is
preferably between 500 and 10,000,000 g/mol, preferably between
100,000 and 1,000,000 g/mol, in particular between 300,000 and
600,000 g/mol and preferentially between 300,000 and 500,000
g/mol.
[0067] When the plasticizer belongs to the family of
polycarboxylates, its weight average molecular weight is preferably
between 10,000 and 500,000 g/mol, preferably between 50,000 and
300,000 g/mol and preferentially between 10,000 and 200,000 g/mol;
its number average molecular weight is preferably between 100 and
100,000 g/mol, preferably between 500 and 50,000 g/mol and
preferentially between 500 and 30,000 g/mol.
[0068] When the plasticizer belongs to the family of acrylonitrile
polymers, its number average molecular weight is preferably between
500 and 10,000,000 g/mol, preferably between 50,000 and 1,000,000
g/mol and preferentially between 50,000 and 500,000 g/mol.
[0069] According to its nature, the plasticizer entering into the
composition of the formulation according to the present disclosure
can have one glass-transition temperature, or several
glass-transition temperatures.
[0070] The plasticizer entering into the composition of the
formulation according to the present disclosure preferably has a
glass-transition temperature, where applicable glass-transition
temperatures, of less than 150.degree. C., preferably of less than
130.degree. C. Preferentially, at least one of the glass-transition
temperatures of the plasticizer is between -100 and 100.degree. C.,
preferably between -60 and 60.degree. C., or between -40 and
+70.degree. C. Such a characteristic advantageously makes it
possible to obtain a relatively low softening temperature for the
intimate blend of the lignin and of the plasticizer, so that it is
possible to transform this blend at a relatively low temperature,
at which no degradation of its constituents occurs.
[0071] Examples of plasticizers that can be implemented in the
formulation according to the present disclosure are in
particular:
[0072] the poly (ethylene oxide) marketed under the name Alkox.RTM.
E30 by the company Meisei Chemical Works LTD. This product has a
glass-transition temperature between -50 and -60.degree. C., a
melting temperature between 55 and 60.degree. C., a weight average
molecular weight between 400,000 and 550,000 g/mol and a number
average molecular weight between 300,000 and 400,000 g/mol;
[0073] the ether polycarboxylate marketed under the name
Ethacryl.RTM. HF by the company Coatex. This product has a
glass-transition temperature between -45 and -60.degree. C. and a
melting temperature between 35 and 45.degree. C.;
[0074] the copolymer poly(acrylonitrile-co-methyl
acrylate)-block-poly(acrylonitrile-co-butadiene) marketed under the
name Barex.RTM. 210. This product has two glass-transition
temperatures respectively between 60 and 70.degree. C. and between
125 and 135.degree. C.
[0075] The cross-linking agent entering into the composition of the
formulation according to the present disclosure is preferably of
the molecular type. Any cross-linking agent conventional in itself
for the cross-linking of the phenolic resins can be used according
to the present disclosure.
[0076] The cross-linking agent is preferably chosen from:
[0077] benzoxazines, epoxies, oxazolines, polyoxymethylenes, such
as paraformaldehyde, aldehydes, such as glutaraldehyde,
formaldehyde, furfural, etc., hexamethylenetetramine and
hexamethylenemethoxymelamine;
[0078] compounds that have a functionality greater than or equal to
two of which the chemical functions are chosen in the group
consisting of the functions: benzoxazine, epoxy, in particular
glycidyl ether, isocyanate, anhydride, carboxylic acid, methylol
and ester, with these chemical functions being identical or
different,
[0079] or any blend of such compounds.
[0080] The cross-linking agent used according to the present
disclosure preferably has an operating cross-linking temperature
with the lignin between 30 and 190.degree. C. and preferably
between 80 and 170.degree. C.
[0081] Examples of cross-linking agents that can be used in the
formulation according to the present disclosure are in
particular:
[0082] bisphenol bisbenzoxazine F marketed under the name
Araldite.RTM. MT 35700 by the company Huntsman. This product has a
glass-transition temperature of 73.6.degree. C., and an operating
cross-linking temperature with the lignin of 190.degree. C.;
[0083] bisphenol A diglycidylether marketed under the name
Epolam.RTM. 8056R by the company Axson. This product has a
glass-transition temperature of about -20.degree. C., an operating
cross-linking temperature with the lignin of 120.degree. C. and a
molecular weight of less than 700 g/mol;
[0084] 1,3-phenylene-bis-oxazoline marketed under the name
Nexamite.RTM. PBO by the company Nexamite. This product has a
melting temperature of 149.degree. C., a molecular weight of about
216 g/mol, and it is capable of initiating a cross-linking reaction
with the lignin in less than 10 minutes at a temperature greater
than or equal to 100.degree. C.
[0085] In particular aspects of the present disclosure, wherein the
plasticizer and the cross-linking agent are formed by a single and
same compound, this compound is in particular a polymer with a
plasticizing function, functionalized in such a way as to also have
a cross-linking function. As such compound, mention can be made in
particular of polyethers functionalized by epoxy functions.
[0086] The formulation according to the present disclosure can
contain the following percentages by weight, with respect to the
total weight of the formulation:
[0087] 50 to 98%, preferably 60 to 90%, and preferentially 65 to
80%, of lignin, [0088] and/or 1 to 49%, preferably 5 to 30%, and
preferentially 10 to 25%, of plasticizer, [0089] and/or 1 to 25%,
preferably 2 to 10%, and preferentially 2.5 to 5%, of cross-linking
agent.
[0090] Such proportions advantageously provide optimum properties,
in particular in terms of mechanical resistance and ease of
preparation, of the lignin-based fibers formed in accordance with
the present disclosure.
[0091] The formulation according to the present disclosure can
furthermore comprise one or several other additives, aiming to
better structure the material, improve the mechanical properties of
the fibers formed, etc.
[0092] Each one of these additives can in particular be present in
the formulation at a content between 1 ppm and 10% by weight, with
respect to the total weight of the formulation, preferably between
1 ppm and 5% by weight, for example between 100 ppm and 1% by
weight, with respect to the total weight of the formulation.
[0093] Examples of additives that can enter into the composition of
the formulation according to the present disclosure are
compatibilizing agents, such as maleic anhydride grafted polymers
or co-polymers. By way of example, mention can in particular be
made of Lotader.RTM. 3300 marketed by the company Arkema, or
Beiwa.RTM. 901 from DzBh.
[0094] The formulation according to the present disclosure can for
example include one or several additives chosen from carbon fillers
of nanometric size, in particular from nanotubes of carbon and
graphene, alone or in a mixture.
[0095] The term "carbon nanofiller" here means a filler comprising
an element from the group formed from carbon nanotubes, nanocarbon
fibers, graphene, fullerenes and carbon black, or any blend of such
elements. Preferably, the carbon nanofillers integrated in the
formulation according to the present disclosure are carbon
nanotubes, alone or in a mixture with graphene. Carbon nanotubes
are for example marketed by the company ARKEMA under the name
Graphistrength.RTM..
[0096] The carbon nanofillers according to the present disclosure
can have a smaller dimension between 0.1 to 200 nm, preferably
between 0.1 and 160 nm, and preferentially between 0.1 and 50 nm.
This dimension can for example be measured by light scattering.
[0097] The term "graphene" means, according to present disclosure,
a sheet of graphite that is flat, insulated and individualized, but
also, by extension, an assembly that comprises between one and a
few tens of sheets and having a planar or more or less undulated
structure. This definition thus encompasses FLG (Few Layer
Graphene), NGP (Nanosized Graphene Plates), CNS (Carbon
NanoSheets), GNR (Graphene NanoRibbons). It however excludes
nanotubes and nanocarbon fibers, which are respectively comprised
of the winding of one or several sheets of graphene coaxially and
of the turbostratic stacking of these sheets.
[0098] It is within the competences of those skilled in the art to
determine, according to the particular characteristics of the
compounds used, which conditions, in particular of temperature and
of time, must be applied for the carrying out of the step a/ of
intimate blending of the components of the formulation, so as to
carry out this intimate blend without causing the cross-linking of
the cross-linking agent and of the lignin.
[0099] In particular aspects of the present disclosure, the step a/
of intimate blending of the components of the formulation comprises
the following sub-steps--these sub-steps can be implemented
successively or simultaneously, at least partially:
[0100] a1/ the preparation of the formulation, by blending of its
components, in particular of the lignin, of the plasticizer and of
the cross-linking agent,
[0101] a2/ and the blending by extrusion, in particular by melting,
of said components of the formulation, at a temperature greater
than the glass-transition temperature of the lignin and than the
softening temperature, in particular melting temperature when it is
a crystalline or semi-crystalline material, of the plasticizer, in
order to form an extrudate in which the lignin, the plasticizer and
the cross-linking agent are in an intimate blend.
[0102] In particular, for the sub-step a1/ of blending components
of the formulation, the components in the solid state can first of
all be blended by mechanical action, for example by means of a
cement mixer, preferably at ambient temperature, in such a way as
to form a dry blend.
[0103] Any liquid components can be incorporated at that time into
this dry blend, or later during the step a2/ of blending via
extrusion, in particular by melting, the components of the
formulation, in the apparatus used for carrying out this step.
Thus, the formulation according to the present disclosure can be
formed either upstream of this apparatus, or in this apparatus
itself, extemporaneously, at the time of the preparation of the
intimate blend of the components of the formulation according to
the present disclosure.
[0104] It is in particular entirely advantageous in the context of
the present disclosure to integrate the cross-linking agent into
the formulation in the apparatus that makes it possible to form, in
particular by melting, the intimate blend of the constituents of
the formulation, so as to reduce as much as possible the exposure
of this cross-linking agent to high temperatures, and to prevent in
this way the risks of triggering the cross-linking reaction thereof
with the lignin.
[0105] The apparatus used for carrying out this sub-step a2/, of
blending via extrusion, in particular by melting, components of the
formulation according to the present disclosure, can be of any type
conventional in itself for such an operation, commonly designated
by the term of compounding. It can in particular be an extrusion
blending device conventional in itself, for example an extrusion
device of the twin-screw type, a co-blender, an internal blender,
etc.
[0106] The extrudate obtained at the end of the sub-step a2/, which
is formed from a material consisting in an intimate blend of the
components of the formulation, can then be subjected to the step b/
of spinning of the method according to the present disclosure,
preferably after having been cooled beforehand, for example by air
or by any other effluent that would not degrade the material, then
having been shaped in the form of granules.
[0107] In the particular aspects of the method according to the
present disclosure, in the step a/, the intimate blending of the
components of the formulation is preferentially carried out at the
lowest possible temperature, so as to prevent as much as possible
any degradation of the materials used, with the understanding that
it has to be carried out at a temperature greater than or equal to
the glass-transition temperature of the lignin, which is generally
between 100 to 160.degree. C., and to the softening temperature, in
particular to the melting temperature when it is a crystalline or
semi-crystalline material, of the plasticizer, which is generally
between 30 and 150.degree. C., and for example between 30 and
60.degree. C.
[0108] In particular, the sub-step a2/ of blending via extrusion,
in particular by melting, is preferably carried out at a
temperature between the glass-transition temperature of the
intimate blend of the lignin and of the plasticizer, and
100.degree. C. above this temperature.
[0109] By way of example, when the equipment used to carry out this
step is an extrusion device comprising a feeding hopper, a blending
tank, a means of conveying and an extrusion die, the temperatures
in these various areas can be chosen as follows:
[0110] temperature of the feeding area between 0 and 100.degree.
C., preferably 20 and 80.degree. C., and preferentially 40 and
60.degree. C.;
[0111] temperature of the blending area between 60 and 180.degree.
C., preferably 90 and 160.degree. C., and preferentially 100 and
130.degree. C. or 110 and 150.degree. C.;
[0112] temperature of the conveying area between 60 and 180.degree.
C., preferably 90 and 160.degree. C., and preferentially 100 and
130.degree. C. or 110 and 150.degree. C.;
[0113] temperature of the extrusion die between 60 and 180.degree.
C., preferably 90 and 160.degree. C., preferentially 110 and
150.degree. C. and for example 110 and 140.degree. C.
[0114] The advantage of such low temperature profiles is, on the
one hand, to prevent the degradation of the main material which is
the lignin; on the other hand, together with a very short residence
time of the material in the device, for example of less than 5
minutes, it makes it possible to prevent the cross-linking of the
components of the intimate blend so as to be able to consider
another extrusion of the granules obtained, for the step b/ of
spinning.
[0115] The residence time of the material in the extrusion device,
for carrying out the step a/ of intimate blending of the
components, is variable and chosen according to the particular
characteristics of the compounds used. It can for example be of
about 1 minute. At the end of this step a/, rings of a few
millimeters in diameter are recovered, which are subjected to the
following step of the method.
[0116] In particular aspects of the present disclosure, the method
comprises a prior step of baking the components of the formulation,
preferably at 80.degree. C. and for at least four hours.
[0117] In particular aspects of the present disclosure, in the step
b/ of spinning of the intimate blend of the components of the
formulation, a temperature is applied in the extrusion head which
is higher than the glass-transition temperature of said intimate
blend, of a value of between 10 and 150.degree. C., preferably of
between 30.degree. C. and 100.degree. C., and preferentially of
between 60.degree. C. and 90.degree. C.
[0118] This means that the temperature applied in the extrusion
head is equal to the glass-transition temperature of the intimate
blend of the components of the formulation, plus a value between
10.degree. C. and 150.degree. C., preferably a value between
30.degree. C. and 100.degree. C., and preferentially a value
between 60.degree. C. and 90.degree. C.
[0119] In this step b/ of spinning of the intimate blend of the
components of the formulation, it is furthermore applied in the
extrusion head a temperature that is greater than or equal to the
operating cross-linking temperature of the cross-linking agent with
the lignin.
[0120] The temperature of the extrusion head is preferably chosen,
in relation with the residence time of the blend in its interior,
in such a way that the cross-linking reaction of the cross-linking
agent and of the lignin begins and partially takes place in the
extrusion head, but that it is not complete therein.
[0121] Any conventional device in itself for those skilled in the
art can be used to carry out this step.
[0122] By way of example, when the equipment used for the carrying
out of this step b/ is an extrusion device that comprises a feeding
hopper, a means of conveying and an extrusion die, the temperatures
in these various areas can be chosen as follows:
[0123] temperature of the feeding area between 50 and 180.degree.
C., preferably 80 and 150.degree. C., and preferentially 100 and
130.degree. C.;
[0124] temperature of the conveying area between 60 and 180.degree.
C., preferably 90 and 160.degree. C., and preferentially 110 and
140.degree. C.;
[0125] and temperature of the extrusion head between 100 and
250.degree. C., preferably 150 and 200.degree. C.
[0126] The operating parameters are furthermore chosen in a
conventional way for those skilled in the art.
[0127] The rotation speed of the extrusion screw is in particular
between 10 and 300 rpm.
[0128] The residence time of the material in the extrusion device
is variable. It is preferably greater than 5 minutes.
[0129] During this step, the fluid blend is preferably directly
extruded through the extrusion head at the screw output. It is then
drawn during the cooling thereof, for example in the ambient air or
in a water bath.
[0130] It should be noted that during this step, the cross-linking
agent can react not only with the lignin, but also with the
plasticizer, according to the characteristics of these compounds
and of the operating conditions implemented.
[0131] The lignin-based threads thus obtained have
physical-chemical properties that make it possible to form, by
drawing of these threads, fibers of great length, of several
hundred, even several thousand, meters.
[0132] The step c/ of drawing threads can be carried out according
to any method and by means of any apparatus known to those skilled
in the art for carrying out such an operation. It can in particular
be carried out at a temperature that causes a softening of the
material forming the threads. To this effect, the threads scroll
successively in a set of so-called feeding rollers, through an oven
brought to said temperature, then in a set of so-called drawing
rollers. They undergo a drawing between the two sets of rollers,
according to the ratio of the rotating speeds of the feeding
rollers and of the drawing rollers. They can otherwise be drawn
over heated rollers rotating at different speeds.
[0133] Such a drawing advantageously makes it possible to align the
polymeric chains along the axis of the fibers.
[0134] The fibers can optionally be treated at the output of the
spinning, by radiation treatments, such as gamma rays, beta rays,
electron beams, UV rays.
[0135] In the last step, the lignin-based fiber obtained, which can
have a substantial length, can be wound, for example on a cardboard
tube.
[0136] All of these steps of the method according to the present
disclosure for preparing lignin-based fibers have been easy and
quick to implement, with a low consumption of energy.
[0137] The method for preparing a lignin-based fiber according to
the present disclosure can include a final step of storage of the
lignin-based fiber at ambient temperature, i.e. at a temperature of
about 20.degree. C., and more largely between 15 and 25.degree. C.
This storage is preferably done for a duration greater than 1
day.
[0138] Such a step is particularly advantageous in aspects of the
present disclosure in which the cross-linking agent is capable of
cross-linking with the lignin at ambient temperature. It indeed
makes it possible for the cross-linking reaction of the
cross-linking agent and of the lignin, which was initiated in the
extrusion device during the step b/ of spinning of the method
according to the present disclosure, to continue, even to be
completed. A storage duration of a few days at ambient temperature
is in particular particularly preferred for this purpose in the
context of the present disclosure.
[0139] The present disclosure does not however exclude a storage of
the lignin-based fiber at a lower temperature, for example at a
temperature between -15 and 15.degree. C., for example between 5
and 15.degree. C.
[0140] The method for preparing a lignin-based fiber according to
the present disclosure can further comprise, as a replacement for
this final step of storage, or as a supplement to the latter,
immediately before or after it, a step of heat treating the
lignin-based fiber for a short duration, for example of a few tens
of minutes, in particular between 10 and 60 minutes, for example
around 30 minutes, aiming at allowing the completion of the
cross-linking reaction of the cross-linking agent and of the
lignin, which had begun in the extrusion device during the step b/
of spinning according to the present disclosure. This heat
treatment can be carried out under an atmosphere which is oxidative
or not. It is preferentially carried out at a temperature less than
350.degree. C. In particular aspects of the present disclosure, it
is carried out at a temperature between 180 and 280.degree. C.
[0141] According to a second aspect, the present disclosure relates
to a formulation for the implementation of a method for
preparation, by the melt technique, of lignin-based fibers,
precursors of carbon fibers, according to present disclosure. This
formulation comprises:
[0142] lignin, preferably lignin that is not chemically
modified,
[0143] a plasticizer that is miscible, generally when hot, with the
lignin,
[0144] and a cross-linking agent capable of initiating a
cross-linking reaction with the lignin in less than 10 minutes at
temperatures above (including equal to) a temperature at least
10.degree. C. greater than the glass-transition temperature of the
intimate blend of the lignin and of the plasticizer. Preferably,
the cross-linking agent has an operating cross-linking temperature
at least 10.degree. C. higher than the glass-transition temperature
of said intimate blend of said lignin and of said plasticizer.
[0145] In particular aspects of the present disclosure, the
formulation comprises a cross-linking agent capable of initiating a
cross-linking reaction with the lignin in less than minutes, at
temperatures above a temperature at least 10.degree. C. greater
than the glass-transition temperature of the intimate blend of the
lignin and of the plasticizer.
[0146] The formulation according to the present disclosure, and the
various components thereof, can further respond to one or several
of the characteristics described hereinabove in reference to the
method for preparing lignin-based fibers according to the present
disclosure.
[0147] In particular, the plasticizer contained in the formulation
according to the present disclosure can be a fusible acrylonitrile
polymer, as described hereinabove.
[0148] According to a third aspect, the present disclosure relates
to a lignin-based extrudate able to be obtained at the end of the
step a/ of intimate blending of the components of the formulation,
and more particularly of the sub-step a2/, of a method for
preparing lignin-based fibers according to the present disclosure.
This extrudate has in particular the form of granules.
[0149] Another aspect of the present disclosure relates to a
lignin-based fiber that is able to be obtained by a method
according to the present disclosure, responding to one or several
of the characteristics hereinabove.
[0150] This fiber can be of the mono-filament type or of the
multi-filament type.
[0151] It is continuous, and it can have a diameter between 1 and
1000 .mu.m, preferably between 15 and 30 .mu.m, and a length
greater than or equal to 1 m, more precisely between one meter and
several kilometers.
[0152] The lignin that forms it is, at least partially, in a form
cross-linked with the cross-linking agent, and this as much in the
core itself of the fiber than on the surface thereof, so that it
has a mechanical resistance when submitted to a rise in
temperature, that is particularly good.
[0153] According to another aspect, the present disclosure relates
to the use of such a fiber according to the present disclosure, in
particular of a lignin-based fiber obtained, in particular
directly, by a method of preparation according to the present
disclosure, for the manufacture of carbon fibers.
[0154] More generally, the present disclosure also relates to a
method of manufacturing a carbon fiber, according to which a
lignin-based fiber according to the present disclosure, in
particular obtained, in particular directly, by a method of
preparation according to the present disclosure such as described
hereinabove, is subjected to a carbonization treatment, then when
required to a graphitization treatment.
[0155] The carbonization treatment can in particular be carried out
on the fiber obtained at the output of the step b/ or of the step
c/ of the method for preparing a lignin-based fiber according to
the present disclosure, without having subjected beforehand this
fiber to an intermediate thermo-oxidative treatment.
[0156] Thus, in particular aspects of the present disclosure, the
lignin-based fiber obtained by a method of preparation according to
the present disclosure is not subjected to any step of heat
treatment, in particular at high temperature, typically greater
than or equal to 150.degree. C., prior to the implementation of the
step of carbonization treatment.
[0157] The lignin-based fiber, obtained at the output of the step
b/ or of the step c/ of the method of preparing a lignin-based
fiber according to the present disclosure, can in particular be
subjected, prior to the step of carbonization treatment, to a
treatment via radiation of the UV, Gamma, Beta, electronic,
type.
[0158] The method of manufacturing of a carbon fiber according to
the present disclosure can furthermore include, prior to the step
of carbonization treatment, a step of heat treating the
lignin-based fiber for a short period, for example for a few tens
of minutes, in particular between 10 and 60 minutes, for example
around 30 minutes, aiming at allowing the completion of the
cross-linking reaction of the cross-linking agent and of the lignin
that had begun in the extrusion device during the step b/ of
spinning according to the present disclosure. This heat treatment,
which can advantageously be carried out in the oven implemented for
the carbonization treatment, can be carried out under an atmosphere
that can be oxidative or not. It is preferentially carried out at a
temperature less than 350.degree. C. In particular aspects of the
present disclosure, it is carried out at a temperature between 180
and 280.degree. C. The pressure applied in the oven is preferably
comprised between the atmospheric pressure, and 10 bars above the
atmospheric pressure.
[0159] In particular aspects of the present disclosure, the method
of manufacturing a carbon fiber comprises, before carrying out the
step of carbonization treatment, a step of storage of the
lignin-based fiber, for example in the form of a coil, at ambient
temperature, i.e. at a temperature of about 20.degree. C., or more
largely between 15 and 25.degree. C. If the cross-linking agent
used so allows, this step of storage is preferably carried out for
a duration that is sufficient to allow the cross-linking reaction
of the cross-linking agent and of the lignin, which was initiated
in the extrusion head of the extrusion device, to continue. The
stability of the lignin-based fibers is then advantageously even
higher. The step of storage of the lignin-based fiber can more
generally be carried out at a temperature between -15 and
25.degree. C.
[0160] The carbonization treatment of the lignin-based fiber can be
implemented according to any conventional method for those skilled
in the art.
[0161] It can be carried out continuously, with the fiber scrolling
in the carbonization oven, or discontinuously, i.e. in static mode,
with the fiber being more preferably maintained under tension in
the oven.
[0162] Prior to the carbonization, the fiber can be impregnated
with an agent that improves the carbonization, such as a
siloxane.
[0163] In particular aspects of the present disclosure, the
carbonization oven is hermetically sealed and placed under vacuum
to a value less than 1.104 Pa (0.1 bar). It is then filled with an
inert gas, such as nitrogen, argon, etc., and a gas leak is created
in such a way that the flow rate of gas is between 50 and 500
renewals in volume per hour. The pressure in the oven is more
preferably between 1.103 Pa and 5.104 Pa above atmospheric
pressure. The temperature applied in the carbonization oven is
preferably between 800.degree. C. and 1500.degree. C.
[0164] At the end of this carbonization treatment, a carbon fiber
is obtained.
[0165] This carbon fiber can then be subjected, if needed, to a
graphitization treatment, by heating up to a temperature of
2500.degree. C. under an inert gas, in such a way as to obtain a
better structuring of the carbon, and therefore more advantageous
mechanical properties.
[0166] The lignin-based fiber according to the present disclosure
can otherwise be carbonized continuously, by scrolling it
successively in different ovens, of which one carbonization oven
with an inert atmosphere at a temperature between 800.degree. C.
and 1500.degree. C., then a graphitization oven at a temperature
that can range up to 2500.degree. C. The scrolling speed of the
fiber in these ovens is then preferentially between 1 and 100
m/h.
BRIEF DESCRIPTION OF THE DRAWINGS
[0167] The characteristics and advantages of the present
disclosures shall appear more clearly in light of the examples of
implementation hereinafter, provided simply for the purposes of
illustration and in no way limiting of the present disclosure, with
the support of FIGS. 1 to 9, wherein:
[0168] FIG. 1 diagrammatically shows, in the form of a block
diagram, the various steps of a method for manufacturing a carbon
fiber according to the present disclosure;
[0169] FIG. 2 shows a bargraph that illustrates the melt flow index
(MFI) measured at different temperatures, for granules obtained in
the first step of a method according to the present disclosure
("with cross-linking agent") and for granules obtained by a similar
method, but which does not implement a cross-linking agent
("without cross-linking agent");
[0170] FIG. 3 shows a graph that represents, according to the
temperature, the loss factor (tan delta) and the storage modulus
(E') measured by dynamic mechanical analysis for a sample of
granules obtained in the first step of a method for preparing
lignin-based fibers according to the present disclosure: without
additional heat treatment (E0), with a heat treatment of
130.degree. C. for 5 min (E1) or a heat treatment of 130.degree. C.
for 5 min, then from 20.degree. C. up to 220.degree. C. for 100 min
(E2);
[0171] FIG. 4 shows graphs that illustrate the change in the melt
flow index (MFI) measured respectively at a/ 160.degree. C., b/
130.degree. C., according to the sampling time, for granules
obtained in the first step of a method according to the present
disclosure; on each one of these graphs the reference area for the
calculation of the MFI is indicated by a box;
[0172] FIG. 5 shows a graph that represents, according to the
temperature, the loss factor (tan delta) and the storage modulus
(E') measured by dynamic mechanical analysis for a sample of
granules obtained in the first step of a method according to the
present disclosure: without additional heat treatment (E0'), with a
heat treatment of 130.degree. C. for 5 min (E1') or a heat
treatment of 130.degree. C. for 5 min then of 20.degree. C. up to
220.degree. C. for 100 min (E2');
[0173] FIG. 6 shows a scanning electron microscope image of a
lignin-based fiber obtained by a method in accordance with the
present disclosure;
[0174] FIG. 7 shows an optical microscope image of a carbon fiber
obtained by direct carbonization of the lignin-based fiber of FIG.
5, by a method of manufacturing carbon fibers in accordance with
the present disclosure;
[0175] FIG. 8 shows graphs that illustrate the change in the melt
flow index (MFI) measured respectively at a/ 130.degree. C., b/
170.degree. C., according to the sampling time, for granules
obtained in the first step of a method similar to the method
according to the present disclosure that does not implement any
cross-linking agent; on each one of these graphs the reference area
for the calculation of the MFI is indicated by a box;
[0176] and FIG. 9 shows a graph that represents, according to the
temperature, the loss factor (tan delta) and the storage modulus
(E') measured by dynamic mechanical analysis for a sample of
granules obtained in the first step of a method similar to the
method according to the present disclosure that does not implement
any cross-linking agent, without additional heat treatment.
DETAILED DESCRIPTION
[0177] The various steps of a method for manufacturing a carbon
fiber according to an aspect of the present disclosure are shown
diagrammatically in FIG. 1, in the form of a block diagram.
[0178] This method first comprises the manufacturing of a
lignin-based fiber, in accordance with the present disclosure.
[0179] In the first step a1/, shown as 11 in the figure, it
comprises the blending of lignin, of a plasticizer that is hot
miscible with the lignin and of a cross-linking agent capable of
cross-linking with the lignin, more precisely to initiate a
cross-linking reaction with the lignin, in a few minutes at a
temperature which is at least 10.degree. C. greater than the
glass-transition temperature of the intimate blend of the lignin
and of the plasticizer.
[0180] The following step a2/ of the method, shown as 12 in the
figure, consists in carrying out the intimate blending of the
components hereinabove, via the so-called compounding technique, at
a temperature greater than the glass-transition temperature of the
lignin and than the softening temperature, in particular the
melting temperature when it is a crystalline or semi-crystalline
material, of the plasticizer. At the end of this step, an extrudate
is obtained, in particular in the form of granules, wherein the
lignin, the plasticizer and the cross-linking agent are in an
intimate blend. No cross-linking reaction has begun yet at this
stage of the method.
[0181] The step a1/ and the step a2/ can be carried out
successively or simultaneously, at least for some of the operations
that they require.
[0182] The following step of the method for preparation of a
lignin-based fiber according to a particular aspect of the present
disclosure, shown as 13 in the figure, consists in a step of
spinning b/ of the extrudate obtained, in an extrusion device
comprising an extrusion head in the terminal part, in order to form
continuous threads. To this effect, operating conditions of
temperature and of residence time are applied in the device, which
are such that the temperature applied in the extrusion device is
higher than the glass-transition temperature of the intimate blend
formed in the step a2/, so that this blend is in fluid form; and
the cross-linking of the cross-linking agent and of the lignin is
caused in the terminal part of the extrusion device, in the
extrusion head, and only in this terminal part.
[0183] At the output of the extrusion device, a lignin-based fiber
is obtained, which is subjected, if necessary, to a step c/ of
drawing, shown as 14 in the figure, which is conventional in
itself.
[0184] The lignin-based fiber obtained is then subjected to a step
of winding, shown as 15 in the figure.
[0185] The method for manufacturing a carbon fiber according to the
present disclosure then comprises a step of carbonization of the
lignin-based fiber, shown as 16 in the figure, and conventional in
itself.
[0186] Optionally, it can comprise an intermediate step, shown as
17 in FIG. 1, of heat treatment of the wound lignin-based fiber,
aiming to increase its stability by progression of the
cross-linking reaction of the cross-linking agent and of the
lignin, at a temperature less than 350.degree. C. and for a
duration that does not exceed a few tens of minutes.
Example 1
[0187] 1/ Formulation
[0188] The formulation in accordance with the present disclosure
implemented in this example contains the following contents of
constituents, expressed as a percentage by weight, with respect to
the total weight of the formulation:
[0189] 76% Protobind 2400 lignin marketed by the company
GreenValue,
[0190] 20% polyethylene oxide polymer marketed under the name
Alkox.RTM. E30 by the company Meisei Chemical Works, of a number
average molecular weight between 300,000 and 400,000 g/mol and of a
weight average molecular weight between 400,000 and 550,000 g/mol
(plasticizer),
[0191] and 4% bisphenol A diglycidylether, an epoxy compound
marketed under the name Epolam 8056 R by the company Axson
(cross-linking agent).
[0192] The properties of the plasticizer are as follows:
glass-transition temperature Tg=-50/-60.degree. C., melting
temperature Tf=55-60.degree. C., crystallization temperature
Tc=30-40.degree. C.
[0193] The properties of the cross-linking agent are as follows:
glass-transition temperature Tg=-20.degree. C., molecular weight
less than 700 g/mol.
[0194] The glass-transition temperature of this formulation,
measured by DMA according to the protocol mentioned hereinabove, is
62.degree. C. The operating cross-linking temperature thereof is
greater than 120.degree. C.
[0195] 2/ Method for Preparing Lignin Fibers
[0196] Using these ingredients, the following method for
manufacturing lignin fibers in accordance with the present
disclosure is implemented.
[0197] Compounding
[0198] The lignin and the plasticizer are blended in a prior step
via mechanical action. An auger dozer is used to pour this blend
into the feeding hopper of an extruder that is not heated.
[0199] The extruder used is a Eurolab twin-screw co-rotating screw
extruder from Thermo Scientific. The operating parameters are as
follows:
[0200] Screw diameter=16 mm
[0201] L/D ratio: 40
[0202] Screw speed=250 rpm
[0203] No degassing is implemented during the extrusion.
[0204] The temperatures of the various areas of the extruder are as
follows:
[0205] Temperature of the supply area: 60.degree. C.
[0206] Temperature of the blending areas: 100.degree. C. and
120.degree. C.
[0207] Temperature of the conveying areas: 120.degree. C. and
135.degree. C.
[0208] Temperature of the die: 130.degree. C.
[0209] The temperature of the extrusion die is 30.degree. C. less
than the operating cross-linking temperature of the cross-linking
agent with the lignin.
[0210] The cross-linking agent, which is in liquid form, is
injected using a syringe pump into the penultimate heating area
(i.e. at the level of the area at 135.degree. C.). It therefore
spends little time in the extruder, which makes it possible to
prevent activating the cross-linking reaction with the lignin.
[0211] A flexible and drawable ring is obtained at the die exit.
The total residence time of the lignin in the extruder was less
than 5 min.
[0212] This ring is air-cooled before being granulated.
[0213] Analysis of the Granules Obtained
[0214] The granules thus obtained are analyzed in order to
determine their melt flow index (MFI) at different temperatures.
This analysis consists in measuring the mass of material passing
through a given die under the action of a fixed pressure, during a
given time and at a fixed temperature. The more fluid the material
is, the more substantial the quantity of material exiting from the
die during this given time is.
[0215] The conditions of analysis are as follows. The temperatures
tested are 130, 140, 150, 160 and 170.degree. C. Once the oven is
at the desired temperature, 5 g of material are inserted into the
hopper of the MFI measuring device. So that this quantity is really
at the desired temperature, it is subjected to a preheating time of
5 min under a weight of 2.16 Kg, then a sample is taken every 10
seconds.
[0216] For the purposes of comparison, the same measuring protocol
is implemented, for granules obtained as indicated hereinabove, but
without the addition of a cross-linking agent.
[0217] The results obtained are shown in FIG. 2.
[0218] For the comparative granules without cross-linking agent
(hatched bars on the graph), it is observed that the higher the
temperature is, the higher the MFI index is.
[0219] For the granules obtained in accordance with the present
disclosure (white bars on the graph): at 130.degree. C., the MFI is
low, but higher than for the granules obtained without
cross-linking agent. At 130.degree. C., the non-reacted
cross-linking agent acts as a plasticizer and fluidizes the blend.
After 6 minutes of flow under heating, a caking due to the
cross-linking is observed (the cross-linking agent has played its
role well and entirely cross-linked the formulation: no more flow
is produced). A 140.degree. C., the MFI is a little higher. The
viscosity of the non-reacted blend is lower, because the
temperature is higher. A caking however takes place faster, after 3
minutes of flow under heating. The kinetics of the reaction is
accelerated as the temperature is higher. A 150.degree. C., it is
observed that the MFI has fallen, and the caking takes place after
only 2 minutes of flow under heating. This indicates that the
cross-linking started during the preheating time. Finally, at
160.degree. C., there is no flow after 5 minutes, the caking
therefore took place during the preheating time.
[0220] Thus, this demonstrates that the cross-linking agent reacts
after a certain period of time and cross-links the blend, causing
the viscosity to increase and the MFI to fall; furthermore, the
time required for the reaction decreases when the temperature
increases.
[0221] The granules are furthermore analyzed by dynamic mechanical
analysis (DMA) in order to measure their viscoelastic and
mechanical properties according to the temperature. To this effect,
at the end of the compounding step, they are subjected to
additional heat treatments that make it possible to simulate the
behavior of the material during the subsequent steps of the method
(spinning, then optional additional heat treatment): heat treatment
at 130.degree. C. for 5 min; heat treatment at 130.degree. C. for 5
min then a second passage from 20 to 220.degree. C. for 100 min.
For the purposes of comparison, a sample obtained directly at the
end of compounding is also analyzed.
[0222] A DMA device 1 from Mettler Toledo is implemented. The
operating parameters are as follows:
[0223] Type of solicitation: tension
[0224] Sample solicited: parallelepiped; L=5 mm; W=2 mm;
thickness=0.8 mm
[0225] Temperature gradient: 2.degree. C./min
[0226] Frequency: 1 Hz
[0227] Displacement: 2 .mu.m
[0228] The displacement is chosen in such a way as to obtain a
signal while still remaining in the linear viscoelastic domain.
[0229] The results obtained are shown in FIG. 3.
[0230] It is observed here that the sample such as obtained after
the compounding (E0) creeps after the glass transition, so that it
is suitable for a later spinning. The sample heated to 130.degree.
C. for 5 min (E1) has a slightly offset glass transition, and the
material does not creep after the latter; after the glass
transition, the storage modulus E' is from 5 to 10 times greater
than that of the sample E0. The material has started to cross-link.
The cross-linking is not completed, since a rise in E' is observed
between 130.degree. C. and 220.degree. C. This result confirms that
it will be possible to carry out the following step of the method
according to the present disclosure at a temperature greater than
or equal to 130.degree. C. to start the step of cross-linking. For
the sample that underwent the first temperature sweeping and a
subsequent temperature sweeping between 20 and 220.degree. C. (E2),
the glass transition is substantially offset towards the high
temperatures and after this transition, E' remains 10 times greater
than that of E0. The material is completely cross-linked and does
not creep. E' reached by E1 at 220.degree. C. is very close to E'
reached by E2. This result shows the importance of the temperature
of the die in the following step: an excessively hot die results in
a complete cross-linking and in an obstruction of the extrusion
head by the material.
[0231] Spinning
[0232] The granules obtained at the end of the step of compounding
are subjected to a step of hot extrusion spinning then drawing of
the fibers, in the following way.
[0233] A Scamex single-screw table horizontal extruder of the
Rheoscam type is implemented with a L/D ratio=11, with 3 heating
areas. The third heating area makes it possible to control the
temperature of the extrusion head, and is adjusted to initiate the
cross-linking.
[0234] The temperatures used are more precisely as follows:
[0235] Temperature of the supply area: 120.degree. C.
[0236] Temperature of the conveying area: 140.degree. C.
[0237] Temperature of the extrusion head: 180.degree. C.
[0238] The granules are introduced into the extruder, and the
melted blend is directly extruded through the extrusion head at the
screw output, to form a thread, which is drawn while being cooled
in the ambient air.
[0239] The thread then joins a set of feeding rollers, at a speed
of 20 m/min, passes through an oven at the temperature of
160.degree. C., the n over a set of drawing rollers, at a speed of
40 m/min. It undergoes a drawing between the two sets of rollers,
according to the ratio of the rotation speed of the feeding rollers
and of the drawing rollers. In the last step, the lignin fiber
obtained is wound on a cardboard tube.
[0240] This fiber has the form of a monofilament. It has a diameter
of about 20 .mu.m. Its length is about 1,000 meters.
[0241] This lignin fiber can be directly subjected to a step of
carbonization, in order to form a carbon fiber, without undergoing
any intermediate step of oxidative thermal treatment.
[0242] By way of example, it can to this effect be subjected to a
static carbonization under nitrogen and under tension with a
temperature gradient of 20 to 1200.degree. C. at 3.degree. C./min,
conventionally in itself. The carbon fiber then obtained has the
form of a monofilament, and has a diameter of about 10 .mu.m.
Example 2
[0243] 1/ Formulation
[0244] The formulation in accordance with the present disclosure
implemented in this example contains the following contents of
constituents, expressed as a percentage by weight, with respect to
the total weight of the formulation: [0245] 75% Protobind 2400
lignin, [0246] 20% polyethylene oxide polymer marketed under the
name Alkox.RTM. E30 (plasticizer), [0247] and 5% bisphenol F
bisbenzoxazine marketed under the name Araldite.RTM. MT 35700 by
the company Huntsman (cross-linking agent).
[0248] The properties of the plasticizer are as follows:
glass-transition temperature Tg=-50/-60.degree. C., melting
temperature Tf=55-60.degree. C., crystallization temperature
Tc=30-40.degree. C.
[0249] The properties of the cross-linking agent are as follows:
glass-transition temperature Tg=73.6.degree. C., melting
temperature Tf=240.degree. C.
[0250] The glass-transition temperature of this formulation,
measured by DMA according to the protocol mentioned hereinabove, is
65.degree. C. The operating cross-linking temperature thereof is
greater than 180.degree. C.
[0251] 2/ Method for Preparing Lignin Fibers
[0252] Using these ingredients, the method for manufacturing lignin
fibers in accordance with the present disclosure is implemented
such as described hereinabove in the example 1, except for the
following operating parameters.
[0253] Compounding
[0254] The temperatures of the various areas of the extruder are as
follows:
[0255] Temperature of the supply area: 60.degree. C.
[0256] Temperature of the blending areas: 100.degree. C. and
130.degree. C.
[0257] Temperature of the conveying areas: 130.degree. C. and
130.degree. C.
[0258] Temperature of the die: 130.degree. C.
[0259] The screw speed is 150 rpm.
[0260] The cross-linking agent used beings to cross-link with the
lignin around 200.degree. C. The extrusion temperatures being lower
than its activation temperature, it plays the role of a filler in
the formulation. The ring at the die output is flexible and can be
drawn. It is air cooled before it is granulated.
[0261] Analysis of the Granules Obtained
[0262] The granules thus obtained are analyzed in order to
determine their melt flow index MFI at different temperatures. The
protocol used is the same as the one disclosed in the Example 1
hereinabove.
[0263] The temperatures tested are 160 and 190.degree. C.
[0264] The results obtained are shown in FIG. 4.
[0265] For the sample treated at 160.degree. C. (graph a/), for the
reference area indicated by a box in the figure, a melt flow index
MFI=0.94.+-.0.41 g/10 min is calculated. For the sample treated at
130.degree. C. (graph b/), for the reference area indicated by a
box in the figure, a melt flow index MFI=0.82.+-.0.29 g/10 min.
[0266] These results obtained at 160 and 190.degree. C. are
explicit: the MFI decreases over time for each temperature. This
means that the cross-linking agent is starting to act. In the
following step of spinning, the cross-linking in the last area of
the extruder can be carried out, and this so as to obtain a
lignin-based fiber that does not require a later step of
thermo-oxidation.
[0267] The granules are furthermore analyzed by dynamic mechanical
analysis (DMA), according to the protocol indicated in the example
1 hereinabove.
[0268] The results obtained are shown in FIG. 5.
[0269] It is observed here that the sample such as obtained after
the compounding (E0') creeps after the glass transition, and is
therefore suitable for the next step of the method according to the
present disclosure. The sample treated at 130.degree. C. for 5 min
(E1') has exactly the same behavior: the cross-linking did not take
place. In both cases, a rise in E' towards 190.degree. C. is noted,
showing a starting of cross-linking. The result obtained for the
sample that was subjected to an additional heat treatment from
20.degree. C. to 220.degree. C. (E2') confirms that the
cross-linking has taken place: the glass transition takes place at
a higher temperature, and E' after this transition is 10 times
higher than in the preceding cases, there is still the signal: the
material has not crept.
[0270] This confirms that the cross-linking begins around
190.degree. C.
[0271] Spinning
[0272] The granules obtained at the end of the step of compounding
are subjected to a step of hot extrusion spinning then drawing of
the fibers, according to the protocol described in the example 1
hereinabove.
[0273] The temperatures of the various areas of the extruder are as
follows:
[0274] Temperature of the supply area: 130.degree. C.
[0275] Temperature of the conveying area: 180.degree. C.
[0276] Temperature of the extrusion head: 200.degree. C.
[0277] A lignin fiber with a length of about 500 m and a diameter
of about 100 .mu.m is obtained. A scanning electron microscope
image of this lignin-based fiber is shown in FIG. 6.
[0278] 3/ Method for Preparing Carbon Fibers
[0279] This lignin fiber is directly subjected to a step of
carbonization, in order to form a carbon fiber, without being
subjected beforehand to any step of oxidative heat treatment.
[0280] This step is carried out via static carbonization under
nitrogen and under tension, with a temperature gradient from 20 to
1200.degree. C. at 3.degree. C./min, conventionally in itself. The
carbon fiber obtained has the form of a continuous monofilament
with a length of about 20 cm, and has a diameter of about 50
.mu.m.
[0281] An optical microscope image of this carbon fiber is shown in
FIG. 7.
Example 3
[0282] 1/ Formulation
[0283] The formulation in accordance with the present disclosure
implemented in this example contains the following contents of
constituents, expressed as a percentage by weight, with respect to
the total weight of the formulation: [0284] 72% Protobind 2400
lignin marketed by the company GreenValue, [0285] 18% ether
polycarboxylate polymer marketed under the name Ethacryl.RTM. HF by
the company Coatex, with a weight average molecular weight between
100,000 and 150,000 g/mol (plasticizer), [0286] and 10% bisphenol A
diglycidylether, an epoxy compound marketed under the name Epolam
8056 R by the company Axson (cross-linking agent).
[0287] The properties of the plasticizer are as follows:
glass-transition temperature Tg=-45/-60.degree. C., melting
temperature Tf=35-45.degree. C., crystallization temperature
Tc=0-15.degree. C.
[0288] The glass-transition temperature of this formulation,
measured by DMA according to the protocol mentioned hereinabove, is
55.degree. C. The operating cross-linking temperature of the
cross-linking agent with the lignin is greater than 130.degree.
C.
[0289] 2/ Method for Preparing Lignin Fibers
[0290] Using these ingredients, the following method for
manufacturing lignin fibers in accordance with the present
disclosure is implemented.
[0291] Compounding
[0292] An auger dozer is used to pour the lignin into the feeding
hopper of an extruder that is not heated. The Ethacryl.RTM. HF is
injected into this same feeding hopper thanks to a peristaltic
pump, while the cross-linking agent is injected only into the
penultimate heating area before the die, using a syringe pump. It
therefore spends little time in the extruder, which makes it
possible to prevent activating the cross-linking reaction with the
lignin.
[0293] The extruder used is an LTE 26-40 twin-screw co-rotating
screw extruder from Labtech Engineering Company LTD. The operating
parameters are as follows:
[0294] Screw diameter=26 mm
[0295] L/D ratio: 40
[0296] Screw speed=190 rpm
[0297] Three degassing openings are implemented during the
extrusion.
[0298] The temperatures of the various areas of the extruder are as
follows:
[0299] Temperature of the supply area: 80.degree. C.
[0300] Temperature of the blending areas: 120.degree. C.
[0301] Temperature of the conveying areas: 120.degree. C.
[0302] Temperature of the die: 120.degree. C.
[0303] The temperature of the extrusion die is 10.degree. C. less
than the operating cross-linking temperature of the cross-linking
agent with the lignin.
[0304] A flexible and drawable ring is obtained at the die exit.
The total residence time of the lignin in the extruder was less
than 1 min.
[0305] This ring is air-cooled before being granulated.
[0306] Spinning
[0307] The granules obtained at the end of the step of compounding
are subjected to a step of hot extrusion spinning then drawing of
the fibers, in the following way. The operating protocol is such as
described in the example 1, except for temperatures of the
extruder, which are as follows:
[0308] Temperature of the supply area: 130.degree. C.
[0309] Temperature of the conveying area: 130.degree. C.
[0310] Temperature of the extrusion head: 140.degree. C.
[0311] The thread obtained at the end of the extrusion step then
join a set of feeding rollers, at a speed of 27 m/min, passes
through an oven at a temperature of 100.degree. C., then on a set
of drawing rollers, at a speed of 81 m/min.
[0312] In the last step, the lignin fiber obtained is wound on a
cardboard tube.
[0313] This fiber has the form of a monofilament. It has a diameter
of about 30 .mu.m. Its length is about 500 meters.
[0314] This lignin fiber can be subjected directly to a step of
carbonization, in order to form a carbon fiber, without undergoing
any intermediate step of oxidative thermal treatment.
[0315] By way of example, it can to this effect be subjected to a
static carbonization under nitrogen and under tension with a
temperature gradient of 20 to 1200.degree. C. to 3.degree. C./min,
conventionally in itself. The carbon fiber then obtained has the
form of a monofilament, and has a diameter of about 15 .mu.m.
Example 4
[0316] 1/ Formulation
[0317] The formulation in accordance with the present disclosure
implemented in this example contains the following contents of
constituents, expressed as a percentage by weight, with respect to
the total weight of the formulation: [0318] 63% Protobind 2400
lignin marketed by the company GreenValue, [0319] 27%
poly(acrylonitrile-co-methyl
acrylate)-block-poly(acrylonitrile-co-butadiene) copolymer marketed
under the name Barex.RTM. 210E. [0320] and 10% bisphenol F
bisbenzoxazine marketed under the name Araldite.RTM. MT 35700 by
the company Huntsman (cross-linking agent).
[0321] The properties of the plasticizer are as follows:
glass-transition temperature 1 Tg1=66.degree. C., glass-transition
temperature 2 Tg2=131.degree. C.
[0322] The glass-transition temperature of this formulation is
85.degree. C. The operating cross-linking temperature of the
cross-linking agent with the lignin is greater than 180.degree.
C.
[0323] 2/ Method for Preparing Lignin Fibers
[0324] Using these ingredients, the following method for
manufacturing lignin fibers in accordance with the present
disclosure is implemented.
[0325] Compounding
[0326] The lignin and the plasticizer are blended in a prior step
via mechanical action. An auger dozer is used to pour this blend
into the feeding hopper of an extruder that is not heated.
[0327] The extruder used is a Eurolab twin-screw co-rotating screw
extruder from Thermo Scientific. The operating parameters are as
follows:
[0328] Screw diameter=16 mm
[0329] L/D ratio: 40
[0330] Screw speed=150 rpm
[0331] No degassing is implemented during the extrusion.
[0332] The temperatures of the various areas of the extruder are as
follows:
[0333] Temperature of the supply area: 60.degree. C.
[0334] Temperature of the blending areas: 100.degree. C. and
150.degree. C.
[0335] Temperature of the conveying areas: 150.degree. C. and
150.degree. C.
[0336] Temperature of the die: 150.degree. C.
[0337] The temperature of the extrusion die is 30.degree. C. less
than the operating cross-linking temperature of the cross-linking
agent with the lignin.
[0338] A flexible and drawable ring is obtained at the die exit.
The total residence time of the lignin in the extruder was less
than 5 min.
[0339] This ring is air-cooled before being granulated.
[0340] Spinning
[0341] The granules obtained at the end of the step of compounding
are subjected to a step of hot extrusion spinning then drawing of
the fibers, in the following way. The operating protocol is such as
described in the example 1, except for temperatures of the
extruder, which are as follows:
[0342] Temperature of the supply area: 160.degree. C.
[0343] Temperature of the conveying area: 165.degree. C.
[0344] Temperature of the extrusion head: 170.degree. C.
[0345] The thread obtained is wound on a cardboard tube. This fiber
has the form of a monofilament. It has a diameter of about 30
.mu.m. Its length is greater than 1,200 m. The fiber obtained is
mechanically resistant and has increased drawability in relation to
the fibers obtained in the preceding examples 1, 2, and 3. Because
of that, it can advantageously be wound at a speed of 630
m/min.
[0346] This lignin fiber can be directly subjected to a step of
carbonization, in order to form a carbon fiber, without undergoing
any intermediate step of oxidative thermal treatment.
[0347] By way of example, it can to this effect be subjected to a
static carbonization under nitrogen and under tension with a
temperature gradient from 20 to 1200.degree. C. at 3.degree.
C./min, conventionally in itself. The carbon fiber then obtained
has the form of a monofilament, and has a diameter of about 20
.mu.m.
Example 5--Comparative Example
[0348] For the purposes of comparison, a method for preparing
lignin-based fibers similar to the method according to the present
disclosure is implemented, which however does not implement any
cross-linking agent.
[0349] 1/ Formulation
[0350] The formulation used in this example contains the following
content in constituents, expressed as a percentage by weight, with
respect to the total weight of the formulation: [0351] 80%
Protobind 2400 lignin, [0352] 20% polyethylene oxide polymer
marketed under the name Alkox.RTM. E30 (plasticizer),
[0353] The glass-transition temperature of this formulation,
measured by DMA according to the protocol disclosed hereinabove, is
74.degree. C.
[0354] 2/ Method for Preparing Lignin Fibers
[0355] Using these ingredients, a method for manufacturing lignin
fibers is implemented according to the operating conditions
described hereinabove in the example 1, except for the following
operating parameters.
[0356] Compounding
[0357] The temperatures of the various areas of the extruder are as
follows:
[0358] Temperature of the supply area: 60.degree. C.
[0359] Temperature of the blending areas: 100.degree. C. and
120.degree. C.
[0360] Temperature of the conveying areas: 120.degree. C. and
130.degree. C.
[0361] Temperature of the die: 130.degree. C.
[0362] The screw speed is 250 rpm.
[0363] Analysis of the Granules Obtained
[0364] The granules thus obtained are analyzed in order to
determine their melt flow index MFI at different temperatures. The
protocol used is the same as the one disclosed in the Example 1
hereinabove.
[0365] The temperatures tested are 130 and 170.degree. C. The
results obtained are shown in FIG. 8, respectively in a/ and in
b/.
[0366] The following is calculated: for the sample treated at
130.degree. C. (graph a/), for the reference area indicated by a
box in the figure, a melt flow index MFI=0.42.+-.0.22 g/10 min; for
the sample treated at 170.degree. C. (graph b/), for the reference
area indicated by a box in the figure, a melt flow index
MFI=4.40.+-.1.07 g/10 min.
[0367] These results obtained at 130 and 170.degree. C. are
explicit: the MFI is constant over time for a given temperature and
the MFI is increasingly higher when the temperature increases. This
means that the higher the temperature is, the more fluid the
lignin/plasticizer blend is.
[0368] The granules are furthermore analyzed by dynamic mechanical
analysis (DMA) according to the protocol indicated in the example 1
hereinabove, pour
[0369] The results obtained for the analysis of the sample coming
from the compounding, without any additional heat treatment, are
shown in FIG. 9.
[0370] It is observed here that the sample such as obtained after
the compounding creeps after the glass transition (loss of signal),
and is therefore suitable for the next step of the method.
[0371] The sample treated at 120.degree. C. for 5 min has exactly
the same behavior: the cross-linking did not take place. A second
passage at 220.degree. C. cannot be carried out, the sample having
crept in the apparatus.
[0372] Spinning
[0373] The granules obtained at the end of the step of compounding
are subjected to a step of hot extrusion spinning then drawing of
the fibers, according to the protocol described in the example 1
hereinabove, with the operating parameters:
[0374] Temperature of the supply area: 160.degree. C.
[0375] Temperature of the conveying area: 170.degree. C.
[0376] Temperature of the extrusion head: 180.degree. C.
[0377] A lignin-based fiber is obtained with a length of about 500
m and diameter about 100 .mu.m.
[0378] 3/ Method for Preparing Carbon Fibers
[0379] This lignin-based fiber is directly subjected to a step of
carbonization, without being subjected beforehand to any step of
oxidative heat treatment.
[0380] This step is carried out via static carbonization under
nitrogen and under tension, with a temperature gradient from 20 to
1200.degree. C. at 3.degree. C./min, conventionally in itself.
During this step, it is observed that the fiber melts and creeps at
a temperature less than 250.degree. C., and that it breaks in the
oven.
[0381] This demonstrates that it is not possible to directly
carbonize the lignin-based fiber obtained in the absence of a
cross-linking agent.
* * * * *