U.S. patent application number 15/577448 was filed with the patent office on 2019-12-19 for lower temperature polycrystalline silicon thin film transistor and method of manufacture thereof and oled display device.
This patent application is currently assigned to WUHAN CHINA STAR OPTOELECTRONICS SEMICONDUCTOR DISPLAY TECHNOLOGY CO., LTD.. The applicant listed for this patent is WUHAN CHINA STAR OPTOELECTRONICS SEMICONDUCTOR DISPLAY TECHNOLOGY CO., LTD.. Invention is credited to Songshan LI.
Application Number | 20190386146 15/577448 |
Document ID | / |
Family ID | 60342199 |
Filed Date | 2019-12-19 |
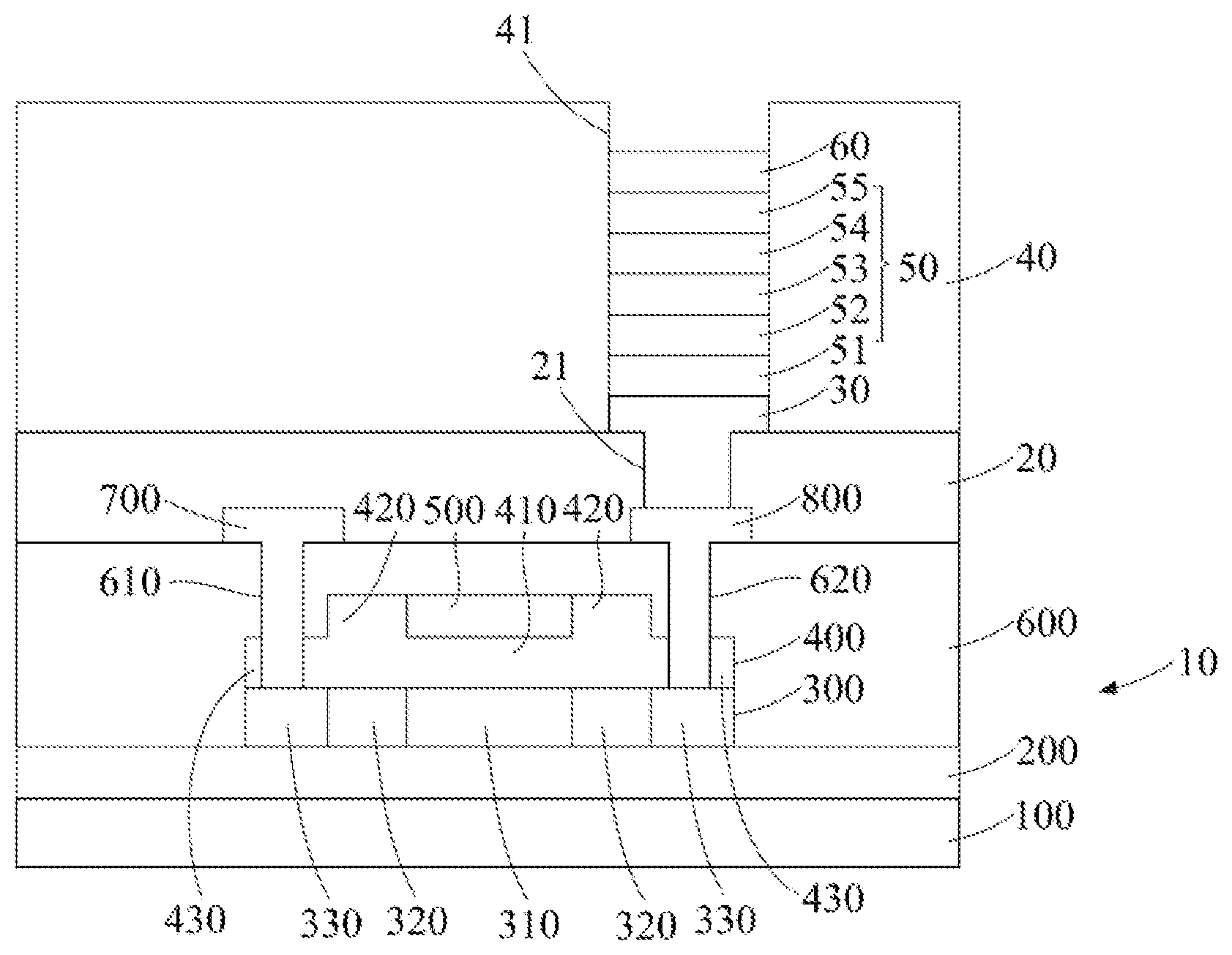
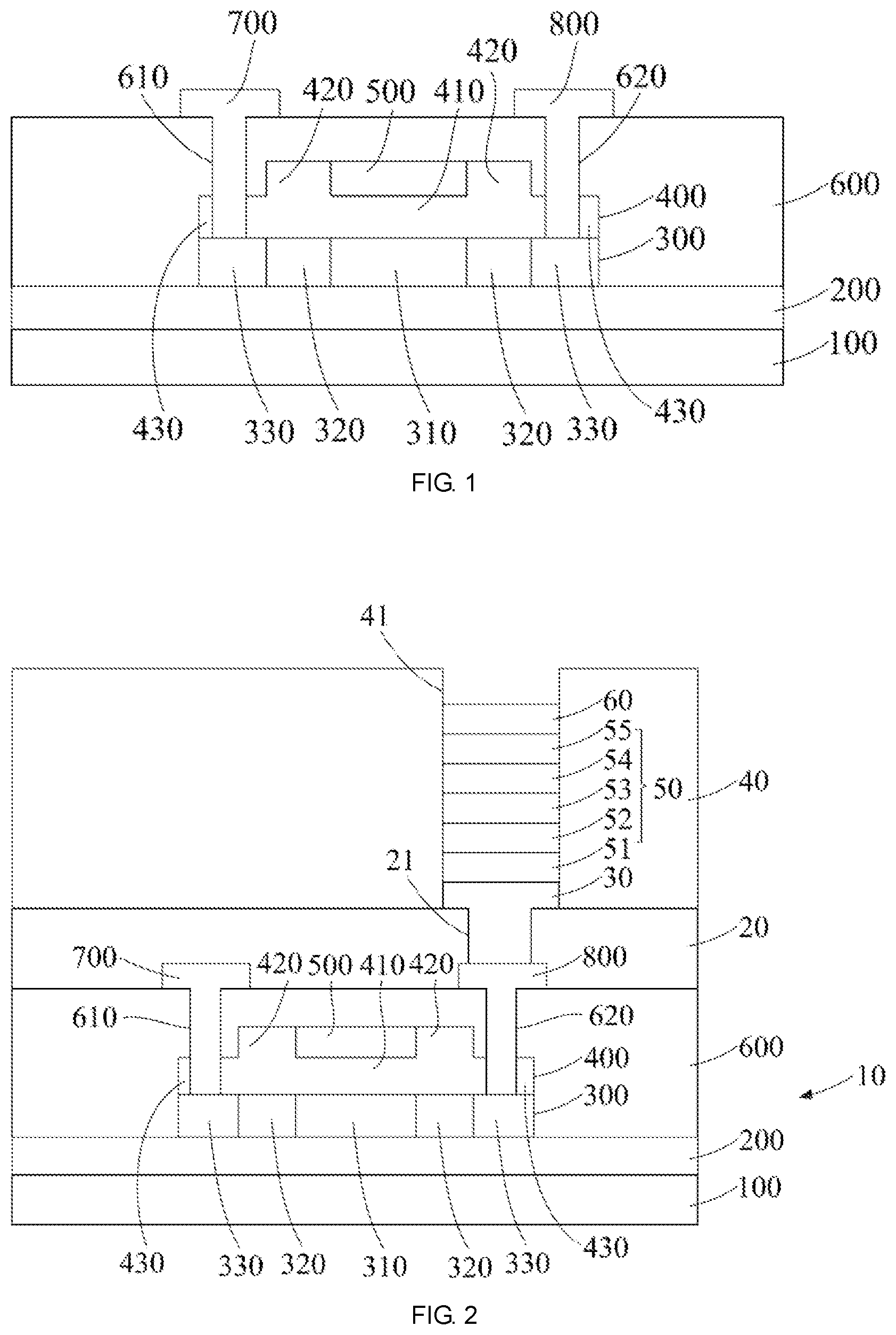
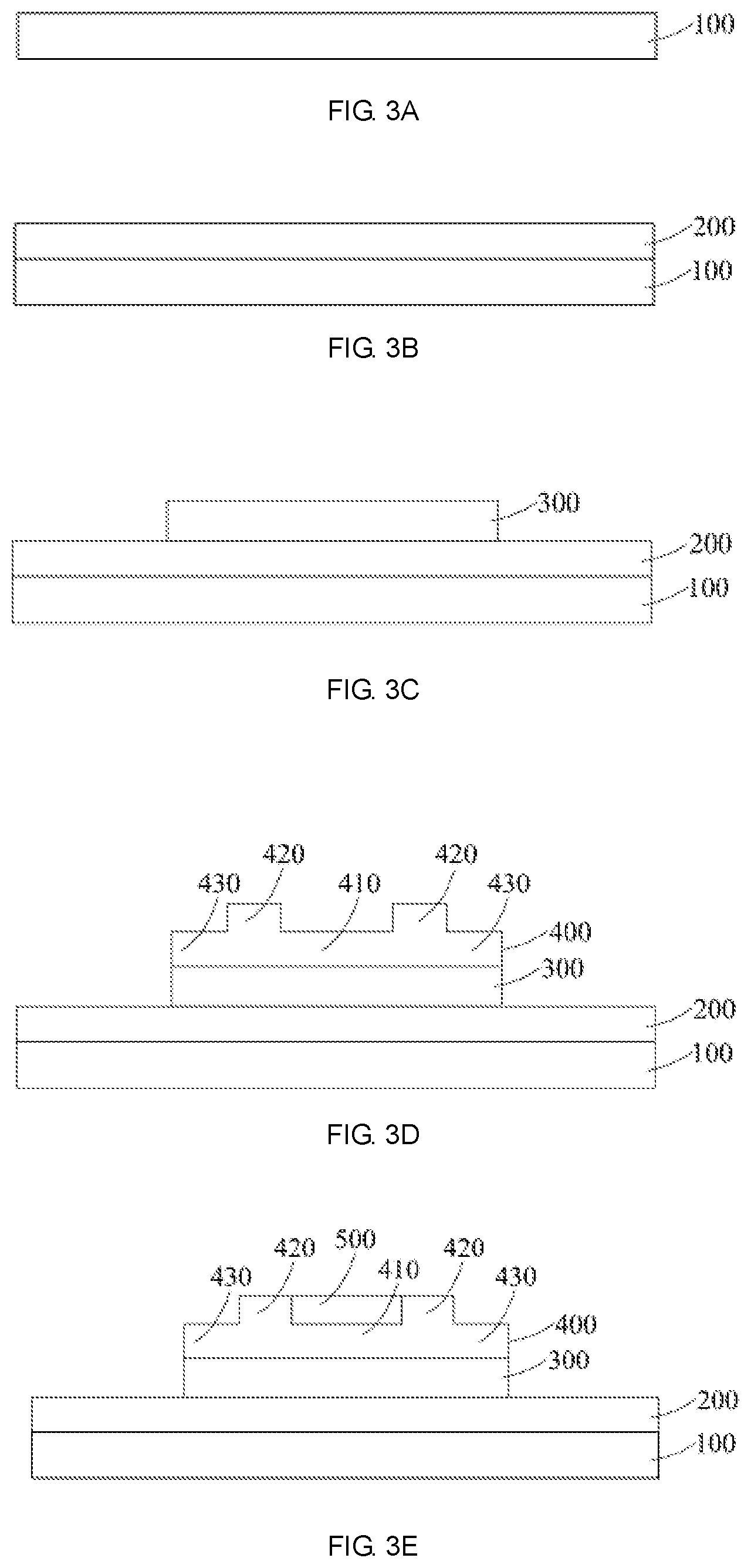
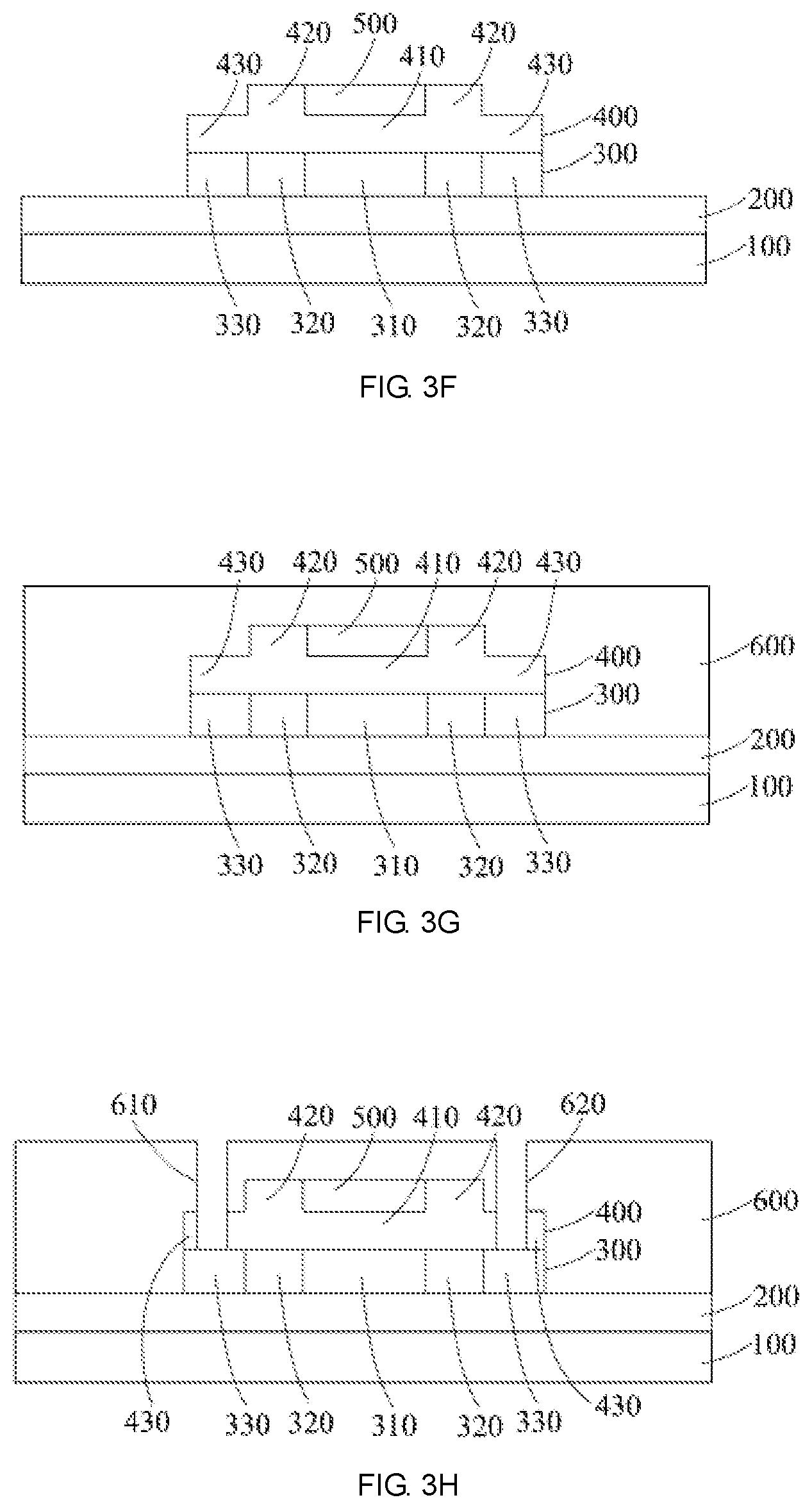


United States Patent
Application |
20190386146 |
Kind Code |
A1 |
LI; Songshan |
December 19, 2019 |
LOWER TEMPERATURE POLYCRYSTALLINE SILICON THIN FILM TRANSISTOR AND
METHOD OF MANUFACTURE THEREOF AND OLED DISPLAY DEVICE
Abstract
A LTPS TFT (Lower Temperature Polycrystal Silicon thin film
transistor) is provided. The LTPS TFT includes substrate, poly-Si
layer, gate insulation layer, grid, layer insulation layer, first
through hole, second through hole, source and drain. The poly-Si
layer includes an undoped layer, a heavily doped layers and a
lightly doped layer. The gate insulation layer includes a first
layer, a second layer and third layer respectively corresponding to
undoped layer, lightly doped layer and third layer. The thickness
of second layer is greater than sum of a thickness of first layer
and third layer. A manufacture method of LTPS TFT and OLED display
device are also provided in invention. The LTPS TFT of this
invention has simplify manufacture method and low cost.
Inventors: |
LI; Songshan; (Wuhan, Hubei,
CN) |
|
Applicant: |
Name |
City |
State |
Country |
Type |
WUHAN CHINA STAR OPTOELECTRONICS SEMICONDUCTOR DISPLAY TECHNOLOGY
CO., LTD. |
Wuhan, Hubei |
|
CN |
|
|
Assignee: |
WUHAN CHINA STAR OPTOELECTRONICS
SEMICONDUCTOR DISPLAY TECHNOLOGY CO., LTD.
Wuhan, Hubei
CN
|
Family ID: |
60342199 |
Appl. No.: |
15/577448 |
Filed: |
September 5, 2017 |
PCT Filed: |
September 5, 2017 |
PCT NO: |
PCT/CN2017/100585 |
371 Date: |
November 28, 2017 |
Current U.S.
Class: |
1/1 |
Current CPC
Class: |
H01L 29/78618 20130101;
H01L 21/02532 20130101; H01L 29/78675 20130101; H01L 27/1222
20130101; H01L 27/3246 20130101; H01L 21/02595 20130101; H01L
27/1218 20130101; H01L 27/3258 20130101; H01L 27/3248 20130101;
H01L 29/78621 20130101; H01L 21/26513 20130101; H01L 27/1248
20130101; H01L 29/0684 20130101; H01L 29/66757 20130101; H01L
27/1288 20130101; H01L 27/3262 20130101; H01L 2227/323
20130101 |
International
Class: |
H01L 29/786 20060101
H01L029/786; H01L 27/32 20060101 H01L027/32; H01L 21/02 20060101
H01L021/02; H01L 29/66 20060101 H01L029/66; H01L 21/265 20060101
H01L021/265 |
Foreign Application Data
Date |
Code |
Application Number |
Jul 27, 2017 |
CN |
201710625402.4 |
Claims
1. A LTPS TFT, comprising a substrate; a poly-Si layer at
positioned on the substrate, and the poly-Si layer includes an
undoped layer, heavily doped layers respectively positioned on two
sides of the undoped layer, and a lightly doped layer positioned
between the undoped layer and the heavily doped layer; a gate
insulation layer positioned on the poly-Si layer, the gate
insulation layer includes a first layer corresponding to undoped
layer, a second layer corresponding to the lightly doped layer and
a third layer corresponding to the heavily doped layer, a thickness
of the second layer is greater than sum of a thickness of the first
layer and a thickness of the third layer; a grid positioned on the
first layer; a layer insulation layer positioned on the grid, the
gate insulation layer and the substrate; a first through hole and a
second through hole, the first through hole passes through the
layer insulation layer and one part of the third layer, the second
through hole passes through the layer insulation layer and another
part of the third layer; and a source and a drain positioned on the
layer insulation layer, the source and the drain are respectively
pass through the first through hole and the second through hole and
correspondingly contact to the heavily doped layers.
2. The LTPS TFT according to claim 1, wherein the LTPS TFT further
comprises a buffer layer positioned between the poly-Si layer and
the layer insulation layer.
3. The LTPS TFT according to claim 1, wherein the lightly doped
layer is n-type lightly doped layer, and the heavily doped layer is
n-type heavily doped layer.
4. An OLED display device, comprising a substrate; a poly-Si layer
at positioned on the substrate, and the poly-Si layer includes an
undoped layer, heavily doped layers respectively positioned on two
sides of the undoped layer, and a lightly doped layer positioned
between the undoped layer and the heavily doped layers; a gate
insulation layer positioned on the poly-Si layer, the gate
insulation layer includes a first layer corresponding to undoped
layer, a second layer corresponding to the lightly doped layer and
a third layer corresponding to the heavily doped layer, a thickness
of the second layer is greater than sum of a thickness of the first
layer and a thickness of the third layer; a grid positioned on the
first layer; a layer insulation layer positioned on the grid, the
gate insulation layer and the substrate; a first through hole and a
second through hole, the first through hole passes through the
layer insulation layer and one part of the third layer, the second
through hole passes through the layer insulation layer and another
part of the third layer; a source and a drain positioned on the
layer insulation layer, the source and the drain are respectively
pass through the first through hole and the second through hole and
correspondingly contact to the heavily doped layers; a planar layer
positioned on the layer insulation layer, the source and the drain;
a third through hole passes through the planar layer for exposing
the drain; a bottom electrode positioned on the planar layer and
contacted to the drain by the third through hole; a pixel defining
layer positioned on the planar layer and the bottom electrode; a
fourth through hole passes through the pixel defining layer for
exposing the bottom electrode; an OLED (organic
light-emitting-diode) positioned on the bottom electrode; and a top
electrode positioned on the OLED.
5. The OLED display device according to claim 4, wherein the OLED
further includes a hole injection layer, a hole transport layer, an
organic emitting layer, an electron transport layer and a
electron-injection layer arranged in sequence from the bottom
electrode to the top electrode.
6. The OLED display device according to claim 4, wherein one of the
bottom electrode and the top electrode is transparent or
semi-transparent, another one is opaque and reflected.
7. The OLED display device according to claim 4, wherein the OLED
display device further comprises a buffer layer positioned between
the poly-Si layer and the layer insulation layer.
8. The OLED display device according to claim 4, wherein the
lightly doped layer is n-type lightly doped layer, and the heavily
doped layer is n-type heavily doped layer.
9. A manufacture method of LTPS TFT, comprising steps of: providing
a substrate; forming a poly-Si layer on the substrate; forming a
gate insulation layer on the poly-Si layer, the gate insulation
layer includes a first layer, third layers respectively positioned
on two sides of the first layer, and a second layer positioned
between the first layer and the third layer, a thickness of the
second layer is greater than sum of a thickness of the first layer
and a thickness of the third layer; forming a grid on the first
layer; injecting ion into the poly-Si layer and forming an undoped
layer corresponding to the first layer, a lightly doped layer
corresponding to the second layer and a heavily doped layer
corresponding to the third layer; forming a layer insulation layer
on the grid, the gate insulation layer and the substrate; forming a
first through hole and a second through holed on the layer
insulation layer, and the first through hole passes through the
layer insulation layer and one part of the third layer, and the
second through hole passes through the layer insulation layer and
other part of the third layer; and forming and filling the source
to the first through hole for contacting the correspondingly
heavily doped layer, and filing the drain to the second through
hole for contacting the correspondingly heavily doped layer.
10. The manufacture method of LTPS TFT according to claim 9,
wherein before the step of forming a poly-Si layer on the substrate
further comprises step of: forming a buffer layer on the substrate;
wherein the step of forming a poly-Si layer on the substrate is
substituted for the step of forming a poly-Si layer on the buffer
layer; wherein the step of forming a layer insulation layer on the
grid, the gate insulation layer and the substrate is substituted
for the step of forming a layer insulation layer on the grid, the
gate insulation layer and the buffer layer.
11. The manufacture method of LTPS TFT according to claim 9,
wherein specifically steps of forming a gate insulation layer on
the poly-Si layer comprising: forming an isolation material layer
on the poly-Si layer and the substrate; exposing the isolation
material layer by a half tone mask wherein the half tone mask
comprises a first portion corresponding to the first layer, a
second portion corresponding to the second layer, a third portion
corresponding to the third layer and a fourth portion corresponding
to the isolation material layer on the substrate, transmittance of
the fourth portion is greater than transmittance of the first
portion, the second portion and the third portion, and
transmittance of the first portion and the third portion are
greater than the second portion; and developing and etching the
exposed isolation material layer.
12. The manufacture method of LTPS TFT according to claim 10,
wherein specifically step of forming a gate insulation layer on the
poly-Si layer comprising: forming an isolation material layer on
the poly-Si layer and the substrate; exposing the isolation
material layer by a half tone mask wherein the half tone mask
comprises a first portion corresponding to the first layer, a
second portion corresponding to the second layer, a third portion
corresponding to the third layer and a fourth portion corresponding
to the isolation material layer on the substrate, transmittance of
the fourth portion is greater than transmittance of the first
portion, the second portion and the third portion, and
transmittance of the first portion and the third portion are
greater than the second portion; and developing and etching the
exposed isolation material layer.
13. The manufacture method of LTPS TFT according to claim 9,
wherein the lightly doped layer is n-type lightly doped layer, and
the heavily doped layer is n-type heavily doped layer.
Description
RELATED APPLICATIONS
[0001] The present application is a National Phase of International
Application Number PCT/CN2017/100585, filed on Sep. 5, 2017, and
claims the priority of China Application No. 201710625402.4, filed
on Jul. 27, 2017.
FIELD OF THE DISCLOSURE
[0002] The disclosure relates to manufacture of TFT (thin film
transistor) technical field, and more particularly to LTPS TFT
(Lower Temperature Polycrystalline Silicon thin film transistor)
and method of manufacture thereof and OLED (organic light-emitting
diodes) display device.
BACKGROUND
[0003] Flat panel display devices have been booming with the
evolution of optoelectronic and semiconductor technologies, and in
many types of flat panel display devices, liquid crystal display
(LCD) devices and organic light-emitting diode (OLED) display
devices have become the mainstream of market due to their many
superior characteristics such as high space utilization efficiency,
low power consumption, radiation-free and low electromagnetic
interference.
[0004] Currently, amorphous silicon thin film transistor (a-Si TFT)
is widely applied to switch element of the LCD display and OLED
display. But the a-Si TFT have limits of meeting the requirements
such as thin, light weight, high-finesse, high brightness, high
reliability and low power consumption. Compared with the a-Si TFT,
the LTPS TFT has significant advantages on the aspects of
satisfying the above requirements.
[0005] However, it needs two mask processes to poly-Si layer for
forming heavily doped region and lightly doped region, and then
injecting ions twice for forming heavily doped layer and lightly
doped layer in currently low temperature poly-Si TFT. Therefore,
the manufacture method is complications and high cost.
SUMMARY
[0006] A technical problem to be solved by the disclosure is to
provide LTPS TFT and method of manufacture thereof and OLED
(organic light-emitting diodes) display device by using only one
step for mask process, and forming heavily doped layer and light
doped layer by one step ion injection.
[0007] Furthermore, the disclosure further provides a LTPS TFT. The
LTPS TFT including a substrate, a poly-Si layer, a gate insulation
layer, a grid, a layer insulation layer, a first through hole, a
second through hole, a source and a drain. The poly-Si layer is
positioned on the substrate, and the poly-Si layer includes an
undoped layer, heavily doped layers respectively positioned on two
sides of the undoped layer, and a lightly doped layer positioned
between the undoped layer and the heavily doped layer. The gate
insulation layer is positioned on the poly-Si layer, the gate
insulation layer includes a first layer corresponding to undoped
layer, a second layer corresponding to the lightly doped layer and
a third layer corresponding to the heavily doped layer, a thickness
of the second layer is greater than sum of a thickness of the first
layer and a thickness of the third layer. The grid is positioned on
the first layer. The layer insulation layer is positioned on the
grid, the gate insulation layer and the substrate. The first
through hole and a second through hole, the first through hole
passes through the layer insulation layer and one part of the third
layer, the second through hole passes through the layer insulation
layer and another part of the third layer. The source and a drain
are positioned on the layer insulation layer, the source and the
drain are respectively pass through the first through hole and the
second through hole and correspondingly contact to the heavily
doped layers.
[0008] In an embodiment, the LTPS TFT further comprises a buffer
layer positioned between the poly-Si layer and the layer insulation
layer.
[0009] In an embodiment, the lightly doped layer is n-type lightly
doped layer, and the heavily doped layer is n-type heavily doped
layer.
[0010] According to another aspect of the disclosure, the
disclosure further provides an OLED display device. The OLED
display device includes a LTPS TFT as described above, a planar
layer, a third through hole, a bottom electrode, a pixel defining
layer, a fourth through hole, an OLED (organic
light-emitting-diode) and a top electrode. The planar layer is
positioned on the layer insulation layer, the source and the drain.
The third through hole passes through the planar layer for exposing
the drain. The bottom electrode is positioned on the planar layer
and contacted to the drain by the third through hole. The pixel
defining layer is positioned on the planar layer and the bottom
electrode. The fourth through hole passes through the pixel
defining layer for exposing the bottom electrode. The OLED (organic
light-emitting-diode) is positioned on the bottom electrode. The
top electrode is positioned on the OLED.
[0011] In an embodiment, the OLED further includes a hole injection
layer, a hole transport layer, an organic emitting layer, an
electron transport layer and a electron-injection layer arranged in
sequence from the bottom electrode to the top electrode.
[0012] In an embodiment, one of the bottom electrode and the top
electrode is transparent or semi-transparent, and another one is
opaque and reflected.
[0013] According to yet aspect of the disclosure, the disclosure
further provides a manufacture method of LTPS TFT, comprising the
following steps. Providing a substrate. Forming a poly-Si layer on
the substrate. Forming a gate insulation layer on the poly-Si
layer, the gate insulation layer includes a first layer, third
layers respectively positioned on two sides of the first layer and
a second layer at positioned between the first layer and the third
layer, a thickness of the second layer is greater than sum of a
thickness of the first layer and a thickness of the third layer.
Forming a grid on the first layer. Injecting ion into the poly-Si
layer and forming an undoped layer corresponding to the first
layer, a lightly doped layer corresponding to the second layer and
a heavily doped layer corresponding to the third layer. Forming a
layer insulation layer on the grid, the gate insulation layer and
the substrate. Forming a first through hole and a second through
holed on the layer insulation layer, and the first through hole
passes through the layer insulation layer and one part of the third
layer, and the second through hole passes through the layer
insulation layer and other part of the third layer. Forming and
filling the source to the first through hole for contacting the
correspondingly heavily doped layer, and filing the drain to the
second through hole for contacting the correspondingly heavily
doped layer.
[0014] In an embodiment, before the step of forming a poly-Si layer
on the substrate further comprises step of forming a buffer layer
on the substrate. So that the step of forming a poly-Si layer on
the substrate is substituted for the step of forming a poly-Si
layer on the buffer layer; the step of forming a layer insulation
layer on the grid, the gate insulation layer and the substrate is
substituted for the step of forming a layer insulation layer on the
grid, the gate insulation layer and the buffer layer.
[0015] In an embodiment, specifically steps of forming a gate
insulation layer on the poly-Si layer comprising following steps.
Forming an isolation material layer on the poly-Si layer and the
substrate. Exposing the isolation material layer by a half tone
mask. The half tone mask comprises a first portion corresponding to
the first layer, a second portion corresponding to the second
layer, a third portion corresponding to the third layer and a
fourth portion corresponding to the isolation material layer on the
substrate, transmittance of the fourth portion is greater than
transmittance of the first portion, the second portion and the
third portion, and transmittance of the first portion and the third
portion are greater than the second portion. Developing and etching
the exposed the isolation material layer.
[0016] In an embodiment, the lightly doped layer is n-type lightly
doped layer, and the heavily doped layer is n-type heavily doped
layer.
[0017] The advantages related to the present disclosure is that by
using only one step for mask process, and forming heavily doped
layer and light doped layer by one step ion injection which is
simplify manufacture method and decrease cost.
BRIEF DESCRIPTION OF THE DRAWINGS
[0018] Accompanying drawings are for providing further
understanding of embodiments of the disclosure. The drawings form a
part of the disclosure and are for illustrating the principle of
the embodiments of the disclosure along with the literal
description. Apparently, the drawings in the description below are
merely some embodiments of the disclosure, a person skilled in the
art can obtain other drawings according to these drawings without
creative efforts. In the figures:
[0019] FIG. 1 is a structural schematic view of a LTPS TFT
according to an embodiment of the disclosure;
[0020] FIG. 2 is a structural schematic view of an OLED display
device according to an embodiment of the disclosure;
[0021] FIG. 3A-3I is a process flow of manufacture method of LTPS
TFT according to an embodiment of the disclosure; and
[0022] FIG. 4A to 4C is a process flow of manufacture method of
gate insulation layer according to an embodiment of the
disclosure.
DETAILED DESCRIPTION OF PREFERRED EMBODIMENTS
[0023] Embodiments of the present invention will be described in
detail below by referring to the accompany drawings. However, the
present invention can be implemented in many different forms, and
the present invention should not be construed as being limited to
the specific embodiments set forth herein. Rather, these
embodiments are provided so as to explain the principle and actual
application of the present invention, thus other skilled in the art
can understand various embodiments and amendments which are
suitable for specific intended applications of the present
invention.
[0024] In the drawings, thicknesses of layers and regions are
exaggerated for the sake of clarity. The same reference numerals
refer to like elements in the entire description and drawings.
[0025] When it is said that any part, such as a layer, film,
region, or plate, is positioned on another part, it means the part
is directly on the other part, or intervening part may also be
present. In addition, it is said that any part is directly
positioned on another part, it means there is no intervening part
may also be present
[0026] The disclosure will be further described in detail with
reference to accompanying drawings and preferred embodiments as
follows.
[0027] FIG. 1 is a structural schematic view of a LTPS TFT
according to an embodiment of the disclosure;
[0028] Please refer to FIG.1. In this embodiment, a LTPS TFT 10
including a substrate 100, a buffer layer 200, a poly-Si layer 300,
a gate insulation layer 400, a grid 500, a layer insulation layer
600, a source 700 and a drain 800.
[0029] Specifically, the substrate 100 could be a transparent glass
substrate or a resin substrate, the present disclosure is not
limited thereto.
[0030] The buffer layer 200 is positioned on the substrate 100. The
buffer layer 200 could be SiNx/SiOx structure, but the present
disclosure is not limited thereto. For example the buffer layer 200
could be single layer of SiNx structure or SiOx structure. In
another embodiment, there can not having the buffer layer 200.
[0031] The poly-Si layer 300 is positioned on the buffer layer 200.
When there is no buffer layer 200 of the LTPS TFT, the poly-Si
layer 300 is directly positioned on the substrate 100. The poly-Si
layer 300 includes an undoped layer 310, heavily doped layers 330
and lightly doped layers 320. The heavily doped layers 330 are
respectively positioned on two sides of the undoped layer 310. The
lightly doped layer 320 is positioned between the undoped layer 310
and the heavily doped layer 330. In this embodiment, the lightly
doped layer 320 is n-type lightly doped layer, and the heavily
doped layer 330 is n-type heavily doped layer. It is not limited
thereto. For example the lightly doped layer 320 could be p-type
lightly doped layer, and the heavily doped layer 330 could be
p-type heavily doped layer.
[0032] The gate insulation layer 400 is positioned on the poly-Si
layer 300. The gate insulation layer 400 comprises a first layer
410, a second layer 420 and a third layer 430. The first layer is
corresponding to undoped layer 310. The second layer 420 is
corresponding to the lightly doped layer 320. The third layer 430
is corresponding to the heavily doped layer 330. The thickness of
the second layer 420 is greater than sum of a thickness of the
first layer 410 and a thickness of the third layer 430. In order to
simplify manufacture method and simplify structure of photo mask,
the first layer 410 and the third layer 430 have same thickness
preferably. In this embodiment, the gate insulation layer 400 could
be for example SiNx/SiOx structure, but it is not limited thereto.
In other embodiment, the gate insulation layer 400 also could be
single layer of SiNx structure or SiOx structure.
[0033] The grid 500 is positioned on the first layer 410. The grid
500 could be MoAkMo structure or TiAlTi structure, and also could
be single layer of Mo structure or single layer of Al structure. It
is not limited thereto.
[0034] The layer insulation layer 600 is poisoned on the grid 500,
the gate insulation layer 400 and the buffer layer 200. When there
is no buffer layer 200 of the LTPS TFT, the layer insulation layer
600 is directly positioned on the grid 500, the gate insulation
layer 400 and the substrate 100. The layer insulation layer 600
could be for example SiNx/SiOx structure, but it is not limited
thereto. In other embodiment, the layer insulation layer 600 also
could be single layer of SiNx structure or SiOx structure.
[0035] A first through hole 610 and a second through hole 620 are
located in the layer insulation layer 600. The first through hole
610 passes through one part of the third layer 430, the second
through hole 620 passes through other part of the third layer 430,
which for respectively exposing the heavily doped layer 330.
[0036] The source 700 and the drain 800 are positioned on the layer
insulation layer 600. The source 700 is filled to the first through
hole 610 for contacting the correspondingly heavily doped layer
330. The drain 800 is filled to the second through hole 620 for
contacting the correspondingly heavily doped layer 330. The source
700 and the drain 800 could be MoAlMo structure or TiAlTi
structure, and also could be single layer of Mo structure or single
layer of Al structure. It is not limited thereto.
[0037] The LTPS TFT 10 according to the embodiment of present
invention which can be applied to display device, for example
liquid crystal display or organic emitting display (Ex: OLED
display). In an embodiment, the LTPS TFT 10 of this invention is
applied to an OLED (organic light-emitting diodes) display device,
and the details of which are described below.
[0038] FIG. 2 is a structural schematic view of an OLED display
device according to an embodiment of the disclosure.
[0039] Please refer to FIG. 2. The OLED display device includes a
LTPS TFT 10 shown as FIG. 1, a planar layer 20, a bottom electrode
30, a pixel defining layer 40, an OLED (organic
light-emitting-diode) 50 and a top electrode 60.
[0040] The planar layer 20 is positioned on the layer insulation
layer 600, the source 700 and the drain 800. A third through hole
21 is located in the planar layer 20 for exposing the drain
800.
[0041] The bottom electrode 30 is positioned on the planar layer,
and the bottom electrode 30 is filled to the third through hole 31
for contacting to exposing the drain 800. The bottom electrode 30
is usually an anode. The bottom electrode 30 also could be a
reflecting mirror. When observing the emitting of the OLED 50 by
the substrate 100, the bottom electrode 30 is made by reflectively
metal, and thin enough for having partial transmittance under the
wave of emitting-light. It is called semi-transparent. Or the
bottom electrode 30 is made by transparent metal-oxide for example
Indium tin oxide (ITO) or zinc tin oxide (ZTO). When observing the
emitting of the OLED 50 by the top electrode 60, the bottom
electrode 30 could made by reflectively metal, and should be thick
enough for basically opaque and also be filly reflecting
mirror.
[0042] The pixel defining layer 40 is positioned on the planar
layer 20 and the bottom electrode 30. A fourth is located in the
pixel defining layer 40 for exposing the bottom electrode 30.
[0043] The OLED (organic light-emitting-diode) is positioned on the
exposing bottom electrode 30. In this embodiment, tacking layers of
the OLED are a hole injection layer (HIL) 51, a hole transport
layer (HTL) 52, an organic emitting layer (EML) 53, an electron
transport layer (ETL) 54 and a electron-injection layer (EIL) 55,
and there are arranged in sequence from the bottom electrode 30 to
the top electrode 60. The structure of OLED 50 in the present
disclosure is not limited thereto.
[0044] The top electrode 60 is positioned on the OLED 50. The top
electrode 60 is usually a cathode. The top electrode 60 also could
be a reflecting mirror. When observing the emitting of the OLED 50
by the top electrode 60, the top electrode 60is made by
reflectively metal and thin enough for having partial transmittance
under the wave of emitting-light. It is called semi-transparent. Or
the top electrode 60 is made by transparent metal-oxide for example
Indium tin oxide (ITO) or zinc tin oxide (ZTO). When observing the
emitting of the OLED 50 by the substrate 100, the top electrode 60
could made by reflectively metal, and should be thick enough for
basically opaque and also be filly reflecting mirror.
[0045] The detail of manufacture method of the LTPS TFT 10 of the
embodiment in present invention will be described below.
[0046] FIG. 3A-3I is a process flow of manufacture method of LTPS
TFT according to an embodiment of the disclosure.
[0047] The manufacture method of LTPS TFT, comprising following
steps.
[0048] Step 1, please refer to FIG. 3A. Providing the substrate
100, the substrate 100 could be a transparent glass substrate or a
resin substrate, the present disclosure is not limited thereto.
[0049] Step 2, please refer to FIG. 3B. Forming the buffer layer
200 on the substrate 100. The buffer layer 200 could be SiNx/SiOx
structure, but the present disclosure is not limited thereto. For
example the buffer layer 200 could be single layer of SiNx
structure or SiOx structure. In another embodiment, there is no
buffer layer 200. In addition, the step 2 can be omitted in another
embodiment.
[0050] Step 3, please refer to FIG. 3C. Forming the poly-Si layer
300 on the buffer layer 200. In another embodiment, the poly-Si
layer 300 is directly positioned on the substrate 100 when the step
2 is omitted. The specifically way to form the poly-Si layer 300 is
that forming an amorphous silicon layer on the buffer layer 200 by
PECVD (Plasma-enhanced chemical vapor deposition), and then forming
crystal to the amorphous silicon layer by excimer laser processing.
Therefore producing the poly-Si layer 300.
[0051] Step 4, please refer to FIG. 3D. Forming a gate insulation
layer 400 on the poly-Si layer 300. The gate insulation layer 400
includes a first layer 410, a second layer 420 and a third layer
430. The third layers 430 are respectively positioned on two sides
of the first layer 410. The second layer 420 is positioned between
the first layer 410 and the third layer 430. The thickness of the
second layer 420 is greater than sum of a thickness of the first
layer 410 and a thickness of the third layer 430. In order to
simplify manufacture method and simplify structure of photo mask,
the first layer 410 and the third layer 430 have same thickness
preferably. In this embodiment, the gate insulation layer 400 could
be for example SiNx/SiOx structure, but it is not limited thereto.
In other embodiment, the gate insulation layer 400 also could be
single layer of SiNx structure or SiOx structure.
[0052] FIG. 4A to 4C is a process flow of manufacture method of
gate insulation layer according to an embodiment of the
disclosure.
[0053] Firstly, please refer to FIG. 4A. Forming an isolation
material layer IL on the poly-Si layer 300 and the buffer layer.
The isolation material layer IL could be SiNx/SiOx structure, but
the present disclosure is not limited thereto. For example the
isolation material layer IL could be single layer of SiNx structure
or SiOx structure.
[0054] Then, please refer to FIG. 4B. Exposing the isolation
material layer IL by a half tone mask 70. The half tone mask 70
comprises a first portion 71, a second portion 72, a third portion
73 and a fourth portion 74. The first portion 71 is corresponding
to the first layer 410. The second portion 72 is corresponding to
the second layer 420. The third portion 73 is corresponding to the
third layer 430. The fourth portion 74 is corresponding to the
isolation material layer IL on the buffer layer 200. The
transmittance of the fourth portion 74 is greater than
transmittance of the first portion 71, the second portion 72 and
the third portion 73. The transmittance of the first portion 71 and
the third portion 73 are greater than the second portion 72.
Preferably, the first portion 71 and the third portion 73 have same
transmittance.
[0055] Then, please refer to FIG. 4C. Developing and etching the
exposed isolation material layer IL.
[0056] Step 5, please refer to FIG. 3E. Forming a grid 500 on the
first layer 410. The grid 500 could be MoAlMo structure or TiAlTi
structure, and also could be single layer of Mo structure or single
layer of Al structure. It is not limited thereto.
[0057] Step 6, please refer to FIG. 3F. Injecting ion into the
poly-Si layer 300 for forming an undoped layer 310, a lightly doped
layer 320 and a heavily doped layer 330. The undoped layer 310 is
corresponding to the first layer 410. The lightly doped layer 320
is corresponding to the second layer 420. The heavily doped layer
330 is corresponding to the third layer 430. The injecting ion
could be for example phosphorous ions, the present invention is not
limited thereto. It also could be boron ions.
[0058] Step 7, please refer to FIG. 3G. Forming a layer insulation
layer 600 on the grid 500, the gate insulation layer 400 and the
buffer layer 200. In another embodiment, the layer insulation layer
600 is directly formed on the grid 500, the gate insulation layer
400 and the substrate 100 when the step 2 is omitted. The layer
insulation layer 600 could be for example SiNx/SiOx structure, but
it is not limited thereto. In other embodiment, layer insulation
layer 600 also could be single layer of SiNx structure or SiOx
structure.
[0059] Step 8, please refer to FIG. 3H. Forming a first through
hole 610 and a second through holed 620. The first through hole 610
passes through the layer insulation layer 600 and one part of the
third layer 430, and the second through hole 620 passes through the
layer insulation layer 600 and another part of the third layer
430.
[0060] Step 8, please refer to FIG. 3I. Forming and filling the
source 700 to the first through hole 610 for contacting the
correspondingly heavily doped layer 330, and filing the drain 800
to the second through hole 620 for contacting the correspondingly
heavily doped layer 330. The source 700 and the drain 800 could be
MoAlMo structure or TiAlTi structure, and also could be single
layer of Mo structure or single layer of Al structure. It is not
limited thereto.
[0061] In summary, according to embodiments of the present
invention. The advantages related to the present disclosure is that
by using only one step for mask process, and forming heavily doped
layer and light doped layer by one step ion injection which is
simplify manufacture method and decreasing cost.
[0062] The foregoing contents are detailed description of the
disclosure in conjunction with specific preferred embodiments and
concrete embodiments of the disclosure are not limited to these
description. For the person skilled in the art of the disclosure,
without departing from the concept of the disclosure, simple
deductions or substitutions can be made and should be included in
the protection scope of the application.
* * * * *