U.S. patent application number 16/484970 was filed with the patent office on 2019-12-19 for pump apparatus.
The applicant listed for this patent is Nidec Tosok Corporation. Invention is credited to Koji HIGUCHI, Kazuhiro HOMMA, Yosuke ITO, Yoshiyuki KOBAYASHI.
Application Number | 20190383291 16/484970 |
Document ID | / |
Family ID | 63370487 |
Filed Date | 2019-12-19 |



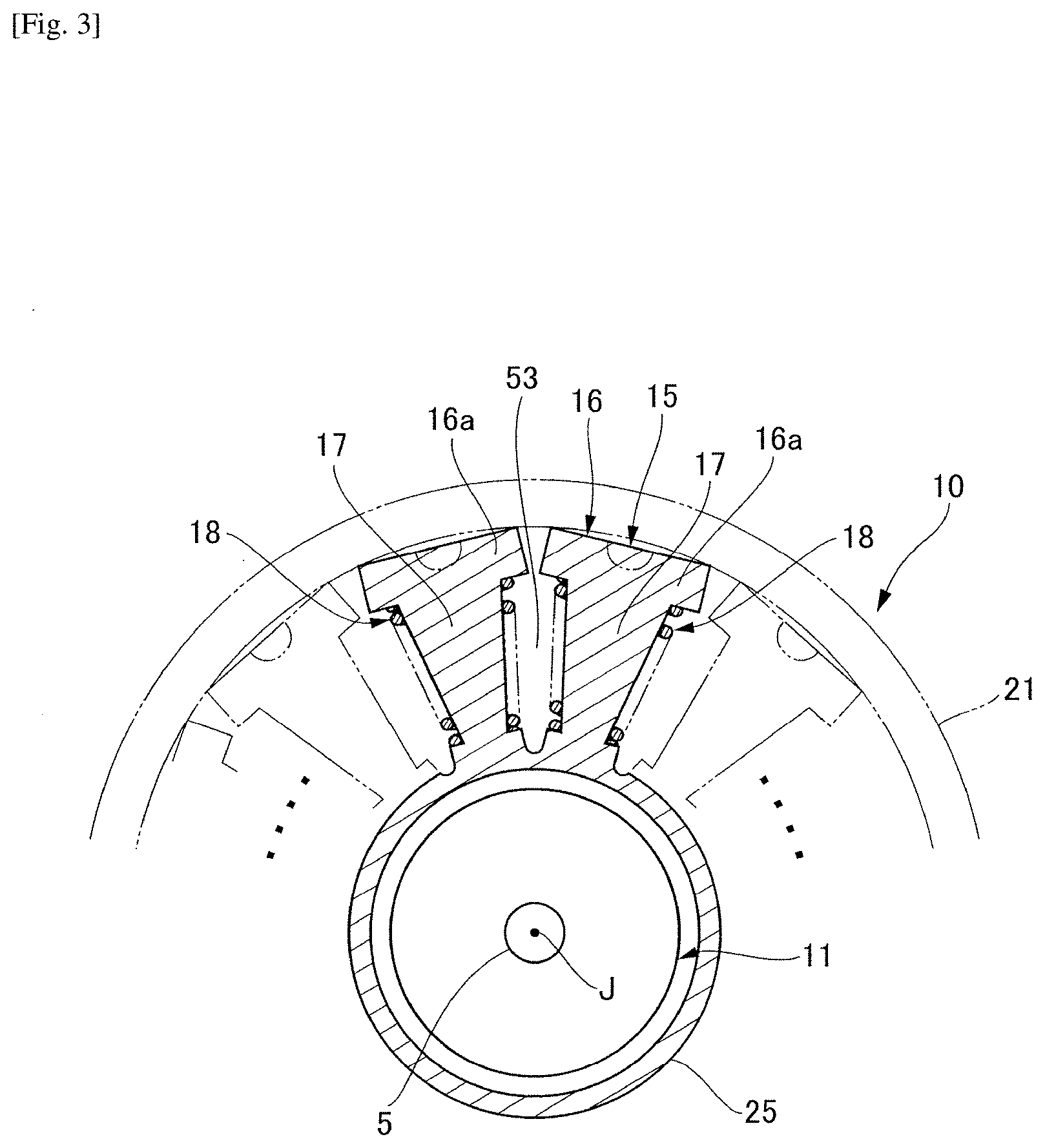
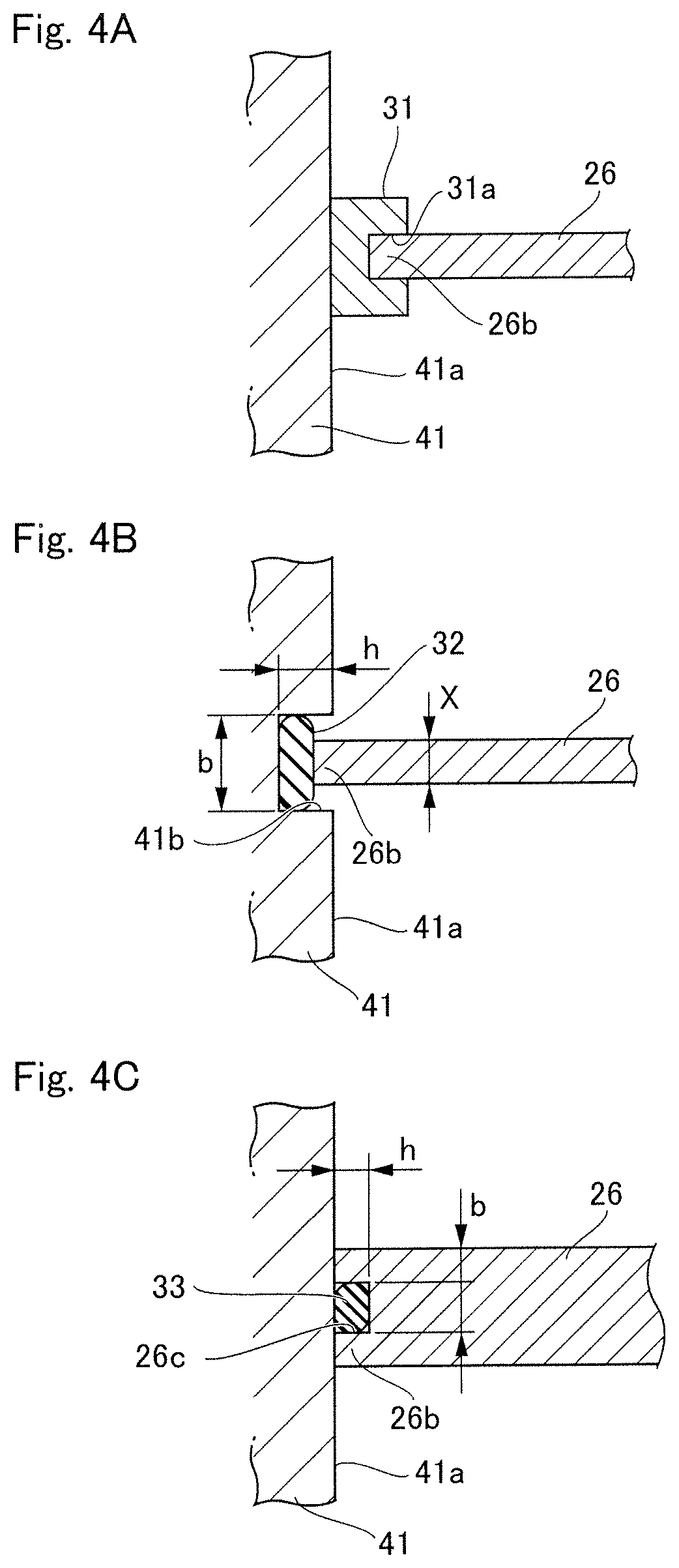
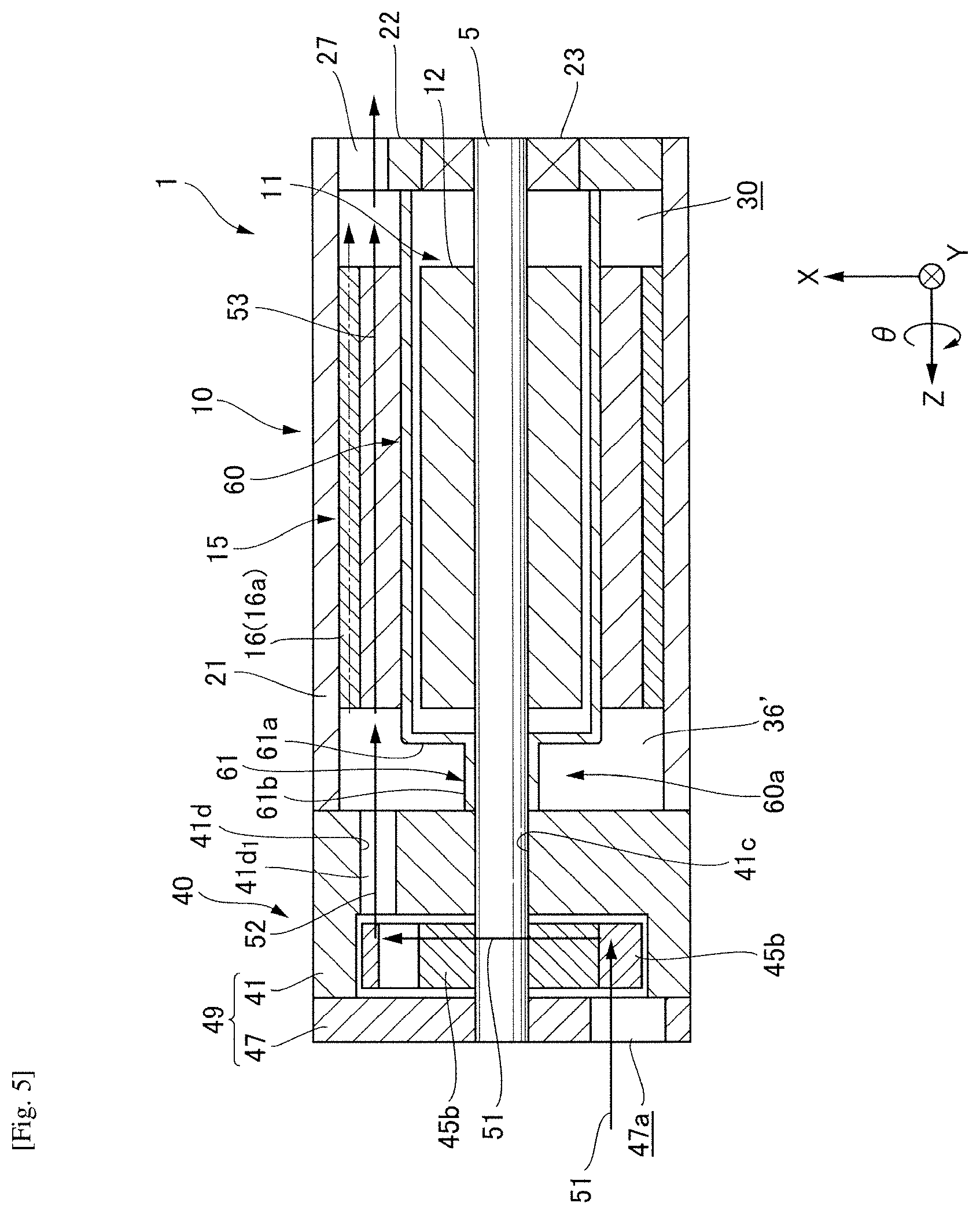
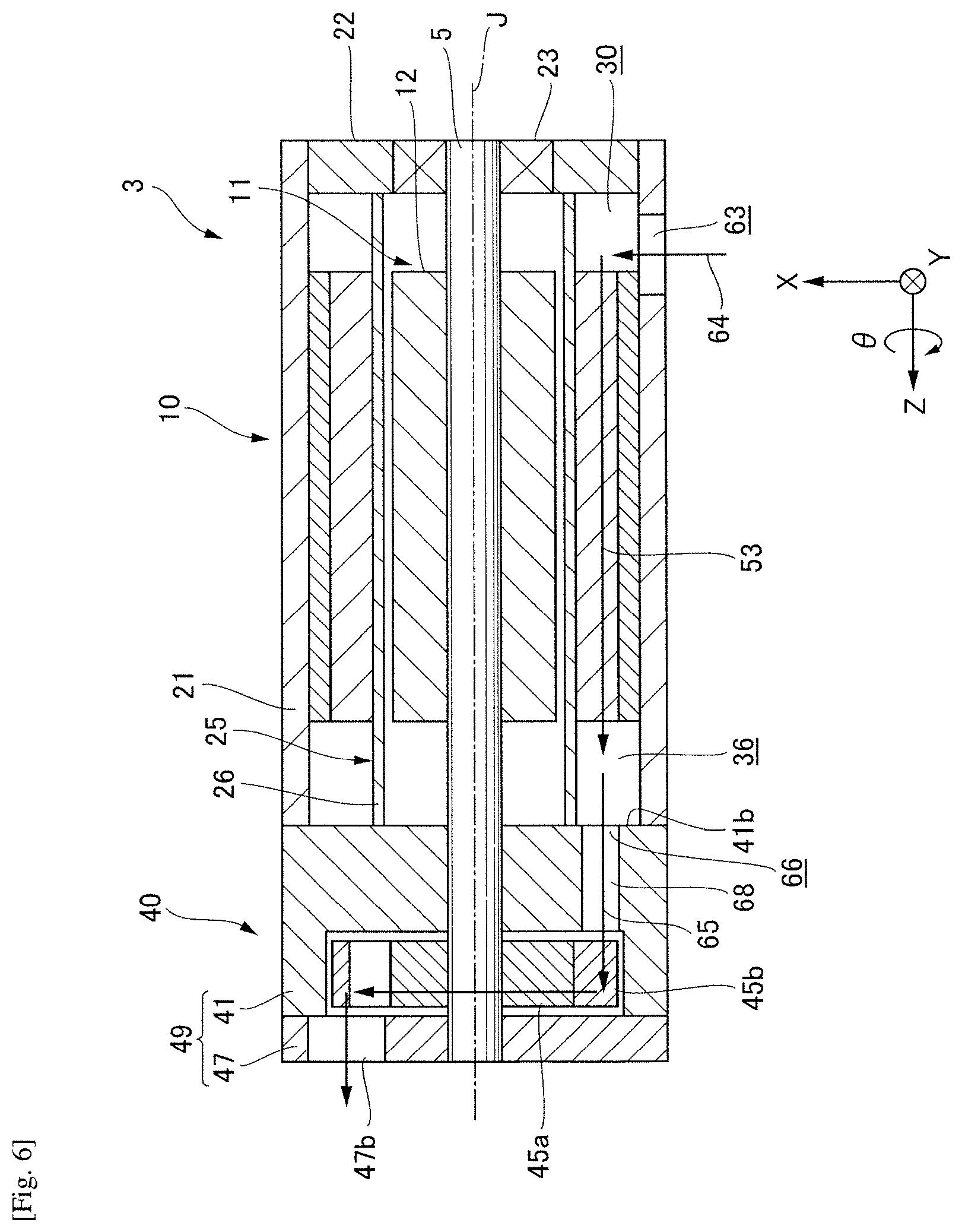
United States Patent
Application |
20190383291 |
Kind Code |
A1 |
KOBAYASHI; Yoshiyuki ; et
al. |
December 19, 2019 |
PUMP APPARATUS
Abstract
A pump apparatus includes a motor including a shaft rotatable
around a central axis, and a pump that is positioned on one side in
an axial direction thereof, is driven via the shaft, and discharges
an oil. The motor includes a rotor, a stator, a housing
accommodating the rotor and the stator, a wall partitioning the
stator and the rotor, and a motor side discharge port to discharge
an oil. The pump includes a pump rotor, a pump case accommodating
the pump rotor, a pump side suction port to suction an oil, and a
pump side delivery port to deliver an oil to the inside of the
motor. A pump apparatus includes a first flow channel to cause an
oil to flow into the pump through a pump side suction port, a
second flow channel to cause an oil to flow to a stator region
through the pump side delivery port, and a third flow channel to
cause an oil to flow into the stator.
Inventors: |
KOBAYASHI; Yoshiyuki;
(Zama-shi, JP) ; HOMMA; Kazuhiro; (Zama-shi,
JP) ; HIGUCHI; Koji; (Zama-shi, JP) ; ITO;
Yosuke; (Zama-shi, JP) |
|
Applicant: |
Name |
City |
State |
Country |
Type |
Nidec Tosok Corporation |
Zama-shi, Kanagawa |
|
JP |
|
|
Family ID: |
63370487 |
Appl. No.: |
16/484970 |
Filed: |
February 23, 2018 |
PCT Filed: |
February 23, 2018 |
PCT NO: |
PCT/JP2018/006641 |
371 Date: |
August 9, 2019 |
Current U.S.
Class: |
1/1 |
Current CPC
Class: |
F04C 2/18 20130101; H02K
7/14 20130101; F04C 15/0096 20130101; F04C 29/042 20130101; F04C
2210/206 20130101; F04C 11/008 20130101; F04C 2/102 20130101; F04C
2240/20 20130101; H02K 9/19 20130101; F04C 15/008 20130101; F04C
2240/30 20130101; F04C 2240/40 20130101; F04C 2240/60 20130101 |
International
Class: |
F04C 29/04 20060101
F04C029/04 |
Foreign Application Data
Date |
Code |
Application Number |
Mar 3, 2017 |
JP |
2017-040767 |
Claims
1-14. (canceled)
15. A pump apparatus comprising: a motor including a shaft
rotatably supported about a central axis extending in an axial
direction; and a pump that is positioned on one side of the motor
in the axial direction, is driven by the motor via the shaft, and
discharges an oil; wherein the motor includes: a rotor rotatable
around the shaft; a stator disposed on an outer side of the rotor
in a radial direction; a housing accommodating the rotor and the
stator; a wall provided between an inner circumference of the
stator and an outer circumference of the rotor to partition the
stator and the rotor from each other; and a motor side discharge
port to discharge the oil inside the motor; the pump includes: a
pump rotor attached to the shaft; a pump case accommodating the
pump rotor; a pump side suction port to suction the oil into the
pump using a negative pressure in the pump; and a pump side
delivery port to deliver the oil inside the pump to the inside of
the motor using pressurization of the pump; and the pump apparatus
further comprises: a first flow channel to cause the oil to flow
into the pump through the pump side suction port; a second flow
channel to cause the oil to flow to a region on a side which is
partitioned by the wall and on which the stator is present inside
the motor, through the pump side delivery port; and a third flow
channel provided inside the stator to cause the oil to flow into
the stator.
16. A pump apparatus comprising: a motor including a shaft
rotatably supported about a central axis extending in an axial
direction; and a pump that is positioned on one side of the motor
in the axial direction, is driven by the motor via the shaft, and
discharges an oil; wherein the motor includes: a rotor rotatable
around the shaft; a stator disposed on an outer side of the rotor
in a radial direction; a housing accommodating the rotor and the
stator; a wall provided between an inner circumference of the
stator and an outer circumference of the rotor to partition the
stator and the rotor from each other; and a motor side suction port
to suction the oil into the motor between the housing and the wall;
the pump includes: a pump rotor attached to the shaft; a pump case
accommodating the pump rotor; and a pump side introduction port to
introduce the oil inside the motor into the pump using a negative
pressure in the pump; and the pump apparatus includes: a fourth
flow channel to cause the oil to flow into the motor through the
motor side suction port; a third flow channel provided inside the
stator to cause the oil to flow into the stator; and a fifth flow
channel to introduce the oil inside the motor into the pump through
the pump side introduction port.
17. The pump apparatus according to claim 15, wherein the stator
includes: a cylindrical core back portion provided to surround the
central axis; a plurality of teeth portions provided at
predetermined intervals in a circumferential direction to protrude
to the rotor side from an inner surface of the core back portion;
and a coil wound around the teeth portion; wherein the third flow
channel is provided between the coils respectively wound around a
pair of teeth portions adjacent to each other in the
circumferential direction.
18. The pump apparatus according to claim 17, further comprising: a
sixth flow channel to cause the oil to flow between the core back
portion and the housing.
19. The pump apparatus according to claim 17, wherein the coil is
resin-molded.
20. The pump apparatus according to claim 15, wherein the wall
includes a cylinder portion covering an outer circumferential
surface of the rotor and extending in the axial direction of the
shaft.
21. The pump apparatus according to claim 20, wherein in the
cylinder portion, a first end portion of the cylinder portion in
the axial direction comes into contact with the pump case and a
second end portion of the cylinder portion in the axial direction
comes into contact with a second end portion of the housing in the
axial direction.
22. The pump apparatus according to claim 17, wherein the wall and
the stator are integrally molded structures made of a resin.
23. The pump apparatus according to claim 21, wherein the cylinder
portion comes into contact with the pump case via a seal.
24. The pump apparatus according to claim 23, wherein a recessed
portion is provided in any one of contact portions of the cylinder
portion and the pump case which come into contact with each other
via the seal, and the seal is inserted into the recessed
portion.
25. The pump apparatus according to claim 21, wherein the cylinder
portion comes into contact with the second end portion of the
housing of the motor in the axial direction via a seal.
26. The pump apparatus according to claim 25, wherein a recessed
portion is provided in any one of contact portions of the cylinder
portion and the second end portion of the housing in the axial
direction which come into contact with each other via the seal, and
the seal is inserted into the recessed portion.
27. The pump apparatus according to claim 15, wherein a space
surrounded by the stator, the wall, and the housing to be able to
be filled with the oil is provided between an end portion of the
stator in the axial direction and an end portion of the housing in
the axial direction inside the motor.
28. The pump apparatus according to claim 16, wherein a space
surrounded by the stator, the wall, and the housing to be able to
be filled with the oil is provided between an end portion of the
stator in the axial direction and an end portion of the housing in
the axial direction inside the motor.
Description
CROSS REFERENCE TO RELATED APPLICATIONS
[0001] This is a U.S. national stage of PCT Application No.
PCT/JP2018/006641, filed on Feb. 23, 2018, and priority under 35
U.S.C. .sctn. 119(a) and 35 U.S.C. .sctn. 365(b) is claimed from
Japanese Application No. 2017-040767, filed Mar. 3, 2017, the
entire disclosures of each application are hereby incorporated
herein by reference.
FIELD OF THE INVENTION
[0002] The present invention relates to a pump apparatus.
BACKGROUND
[0003] Recently, electric oil pumps used for transmissions and the
like have been required to have responsiveness. In order to realize
responsiveness in an electric oil pump, there is a need to increase
the output of a motor for an electric oil pump. When a motor for an
electric oil pump has a high output, a large current flows in a
coil of the motor, so that the temperature of the motor becomes
high, and a permanent magnet of the motor may be demagnetized, for
example. Therefore, in order to curb a temperature rise in the
motor, there is a need to provide a cooling structure in the motor.
Japanese Patent Laid-open No. 2008-125235 discloses an electric
motor including an oil supply mechanism in which a relative
positional relationship between a stator and a rotor in an axial
direction is displaced using an oil pressure of an oil according to
a rotation speed of the rotor and the rotor is cooled by the
oil.
[0004] However, the electric motor disclosed in Japanese Patent
Laid-open No. 2008-125235(which will hereinafter be referred to as
"the electric motor in the related art") has a structure in which a
cooling flow channel switches between a low speed and a high speed,
but this structure is complicated and it is difficult to be
realized. In addition, in the electric motor in the related art,
when an oil circulates inside a rotor, the inertia of the rotor
increases, so that there is concern that the rotational efficiency
of the rotor may be degraded. Moreover, in the electric motor in
the related art, when an oil circulates between a stator and the
rotor, there is concern that the rotational efficiency of the rotor
may be degraded due to the viscosity of the oil.
SUMMARY
[0005] Example embodiments of the present disclosure provide pump
apparatuses each of which has a structure that achieves a high
cooling effect on a motor without degrading the rotational
efficiency of a rotor.
[0006] According to an example embodiment of the present
disclosure, a pump apparatus includes a motor including a shaft
rotatably supported about a central axis extending in an axial
direction, and a pump that is located on one side of the motor in
the axial direction, is driven by the motor via the shaft, and
discharges an oil. The motor includes a rotor rotatable around the
shaft, a stator disposed on an outer side of the rotor in a radial
direction, a housing accommodating the rotor and the stator, a wall
provided between an inner circumference of the stator and an outer
circumference of the rotor to partition the stator and the rotor
from each other, and a motor side discharge port to discharge the
oil inside the motor. The pump includes a pump rotor attached to
the shaft, a pump case accommodating the pump rotor, a pump side
suction port to suction the oil into the pump using a negative
pressure in the pump, and a pump side delivery port to deliver the
oil inside the pump to the inside of the motor using pressurization
of the pump. The pump apparatus includes a first flow channel to
cause the oil to flow into the pump through the pump side suction
port, a second flow channel to cause the oil to flow to a region on
a side that is partitioned by the wall and on which the stator is
present inside the motor, through the pump side delivery port, and
a third flow channel provided inside the stator to cause the oil to
flow into the stator.
[0007] According to an example embodiment of the present
disclosure, it is possible to provide a pump apparatus including a
structure that achieves a high cooling effect on a motor without
degrading a rotational efficiency of a rotor.
[0008] The above and other elements, features, steps,
characteristics and advantages of the present disclosure will
become more apparent from the following detailed description of the
example embodiments with reference to the attached drawings.
BRIEF DESCRIPTION OF THE DRAWINGS
[0009] FIG. 1 is a cross-sectional view of a pump apparatus
according to a first example embodiment of the present
disclosure.
[0010] FIG. 2 is a cross-sectional view of a main portion of the
pump apparatus corresponding to an arrow view taken along I-I in
FIG. 1.
[0011] FIG. 3 is a cross-sectional view of the main portion of the
pump apparatus in which a stator and a wall portion are provided as
a portion of a single structure.
[0012] FIGS. 4A-4C are partially enlarged views illustrating a
state where an end portion of the wall portion comes into contact
with the pump apparatus via a seal.
[0013] FIG. 5 is a cross-sectional view of a pump apparatus
illustrating a modification example of the wall portion in the
first example embodiment of the present disclosure.
[0014] FIG. 6 is a cross-sectional view of a pump apparatus
according to a second example embodiment of the present
disclosure.
DETAILED DESCRIPTION
[0015] Hereinafter, with reference to the drawings, pump
apparatuses according to example embodiments of the present
disclosure will be described. However, it is intended that
dimensions, materials, shapes, relative dispositions, and the like
of constituent components disclosed as the example embodiments or
illustrated in the drawings are merely explanatory examples and do
not limit the scope of the present disclosure to the details
described above. For example, expressions expressing relative or
unique dispositions such as "in a certain direction", "along a
certain direction", "parallel", "orthogonal", "center",
"concentric", and "coaxial" express not only such dispositions in a
strict sense but also express states relatively displaced with a
tolerance, or at an angle or a distance to the extent that the same
functions can be achieved. For example, expressions expressing
states where subjects are equivalent to each other, such as "the
same", "equal", and "homogeneous" express not only equivalent
states in a strict sense but also express states having a tolerance
or a difference to the extent that the same functions can be
achieved is present. For example, expressions expressing shapes
such as a quadrangular shape and a cylindrical shape express not
only the shapes of a quadrangular shape and a cylindrical shape in
a geometrically strict sense but also express shapes including
uneven portions, chamfered portions, and the like within a range in
which the same effects can be achieved. On the other hand,
expressions such as "consisting of", "equipped with", "provided
with", "including", and "having" a constituent element are not
exclusive expressions excluding the presence of other constituent
elements.
[0016] In addition, in the drawings, an XYZ coordinate system is
suitably indicated as a three-dimensional orthogonal coordinate
system. In the XYZ coordinate system, a Z-axis direction is a
direction parallel to one direction in an axial direction of a
central axis J illustrated in FIG. 1. An X-axis direction is a
direction parallel to a width direction of a pump apparatus
illustrated in FIG. 1, that is, an up-down direction in FIG. 1. A
Y-axis direction is a direction orthogonal to both the X-axis
direction and the Z-axis direction.
[0017] In addition, in the following description, a positive side
in the Z-axis direction (positive Z-side) will be referred to as "a
front side", and a negative side in the Z-axis direction (negative
Z-side) will be referred to as "a rear side". The rear side and the
front side are names simply used for description and do not limit
actual positional relationships and directions. In addition, unless
otherwise specified, the direction (Z-axis direction) parallel to
the central axis J will be simply referred to as "an axial
direction". A radial direction about the central axis J will be
simply referred to as "a radial direction". A circumferential
direction about the central axis J, that is, a direction
(.theta.-direction) around the central axis J will be simply
referred to as "a circumferential direction".
[0018] In this specification, the expression "extending in the
axial direction" includes a case of extending in a direction
inclined within a range of less than 45.degree. with respect to the
axial direction, in addition to the case of strictly extending in
the axial direction (Z-axis direction). In addition, in this
specification, the expression "extending in the radial direction"
includes a case of extending in a direction inclined within a range
of less than 45.degree. with respect to the radial direction, in
addition to the case of strictly extending in the radial direction,
that is, a direction perpendicular to the axial direction (Z-axis
direction).
First Example Embodiment
[0019] FIG. 1 is a cross-sectional view of a pump apparatus of the
present example embodiment.
[0020] As illustrated in FIG. 1, a pump apparatus 1 of the present
example embodiment has a motor section 10 and a pump section 40.
The motor section 10 has a shaft 5 rotatably supported about the
central axis J extending in the axial direction. The shaft 5
rotates about the central axis J. The motor section 10 and the pump
section 40 are provided side by side along the axial direction.
<Motor Section 10>
[0021] The motor section 10 has a rotor 11, a stator 15, a housing
21, a wall portion 25, and a motor side discharge port 27.
[0022] The rotor 11 is fixed to an outer circumferential surface of
the shaft 5 and rotates around the shaft 5. The stator 15 is
positioned on an outer side of the rotor 11 in the radial
direction. Therefore, the motor section 10 is an inner rotor
motor.
[0023] The housing 21 accommodates the rotor 11 and the stator 15.
In the housing 21, the front side (positive Z-side) and the rear
side (negative Z-side) are open, and a bearing holding portion 22
is inserted into an opening portion of the housing 21 on the rear
side. The wall portion 25 is provided between an inner
circumferential surface 15a of the stator 15 and an outer
circumferential surface 11a of the rotor 11 and partitions the
stator 15 and the rotor 11. The motor side discharge port 27 is
provided in the bearing holding portion 22 and leads to a space
portion 30 surrounded by the housing 21, the wall portion 25, and a
rear end portion of the stator 15. Hereinafter, each component will
be described in detail.
(Housing 21)
[0024] As illustrated in FIG. 1, the housing 21 has a tubular
shape. In more detail, the housing 21 has a cylindrical shape in
which both ends about the central axis J are open. The material of
the housing 21 is a metal, for example. The housing 21 holds the
motor section 10.
[0025] The bearing holding portion 22 is fitted into and attached
to an opening portion 21a of the housing 21 on the other side in
the axial direction. The motor side discharge port 27 and a bearing
23 are provided in the bearing holding portion 22. The other end
portion of the shaft 5 in the axial direction is inserted into the
bearing 23 and is supported therein. An end portion of the housing
21 on one side in the axial direction is connected in a state of
being in contact with a bottom surface 41a of a pump body 41 of the
pump section 40 on the rear side in the axial direction.
[0026] An outer surface of the stator 15, that is, an outer surface
of a core back portion 16 (which will be described below) is fitted
onto an inner surface 21b of an intermediate portion of the housing
21 in the axial direction. Thus, the stator 15 is held in the
housing 21.
(Rotor 11)
[0027] The rotor 11 has a rotor core 12 and a rotor magnet. The
rotor core 12 surrounds the shaft 5 in the direction
(.theta.-direction) around the axis and is fixed to the shaft 5.
The rotor magnet is fixed to an outer circumferential portion of
the rotor core 12 along the direction around the axis. The rotor
core 12 and the rotor magnet rotate integrally with the shaft
5.
(Stator 15)
[0028] As illustrated in FIG. 2, the stator 15 surrounds the rotor
11 in the direction (.theta.-direction) around the axis and rotates
the rotor 11 around the central axis J. The stator 15 has the core
back portion 16, teeth portions 17, coils 18, and insulators
(bobbins) 20. The shape of the core back portion 16 is a
concentrically cylindrical shape with respect to the shaft 5. In
the illustrated example embodiment, the core back portion 16 is
made to have a cylindrical shape by disposing a plurality of split
cores 16a which are split close to each other in the
circumferential direction. That is, the core back portion 16 is a
core back for the plurality of split cores 16a. The core back
portion 16 may be a core back for a stator of a straight core made
by bending a belt-shaped stator core.
[0029] The teeth portions 17 extend toward the shaft 5 from the
inner surface of the core back portion 16. In the illustrated
example embodiment, the teeth portions 17 extend toward the shaft 5
from the inner surface of each of the plurality of split cores 16a
disposed in a cylindrical shape. A plurality of teeth portions are
provided to be disposed at equal intervals in the circumferential
direction of the inner surface of the core back portion 16. The
coil 18 is constituted of a wound conductive wire 19. The coil 18
is provided in the insulator (bobbin) 20. The insulator (bobbin) 20
is mounted in each teeth portion 17.
(Wall Portion 25)
[0030] As illustrated in FIGS. 1 and 2, the wall portion 25 is
provided between the inner circumferential surface 15a of the
stator 15 and the outer circumferential surface 11a of the rotor 11
and partitions the stator 15 and the rotor 11. The wall portion 25
has a cylinder portion 26 which covers the outer circumferential
surface 11a of the rotor 11 and extends in the axial direction of
the shaft 5. A gap 28 is provided between an inner circumferential
surface 26a of the cylinder portion 26 and the outer
circumferential surface 11a of the rotor 11. Therefore, there is no
concern that the rotor 11 will come into contact with the cylinder
portion 26 when the rotor 11 rotates. The cylinder portion 26 is
formed of a material (for example, a metal or a resin) transmitting
a magnetic force. In this manner, the wall portion 25 can be easily
provided by disposing the cylinder portion 26 in the gap 28 between
the stator 15 and the rotor 11.
[0031] In the cylinder portion 26, one end portion 26b of the
cylinder portion 26 in the axial direction comes into contact with
the pump body 41 of a pump case 49, and the other end portion 26d
of the cylinder portion 26 in the axial direction comes into
contact with the bearing holding portion 22 mounted in the housing
21 of the motor section 10. Therefore, it is possible to prevent
concern of an oil, which has been delivered to the inside of the
motor section 10 from the pump section 40, flowing to a rotor
region Ar where the rotor 11 is present. Therefore, degradation of
the rotational efficiency of the rotor 11 can be curbed.
[0032] As illustrated in FIG. 4A, the one end portion 26b of the
cylinder portion 26 in the axial direction may come into contact
with the bottom surface 41a of the pump body 41 via a seal member
31. In the illustrated example embodiment, for example, the seal
member 31 is made of an elastically deformable synthetic resin
material and has an annular shape. A recessed portion 31a extending
along the circumferential direction of the seal member 31 is
provided in the intermediate portion in the radial direction on a
surface of the seal member 31 on the other side in the axial
direction. In a state where the one end portion 26b of the cylinder
portion 26 in the axial direction is inserted into this recessed
portion 31a, the seal member 31 comes into contact with the bottom
surface 41a of the pump body 41 in an elastically deformed state.
Therefore, it is possible to curb concern of deviation of the
relative position between the one end portion 26b of the cylinder
portion 26 in the axial direction and the seal member 31, and it is
possible to prevent concern of a gap being generated between the
seal member 31 and the bottom surface 41a of the pump body 41.
[0033] In addition, as illustrated in FIG. 4B, a seal member 32 may
be disposed inside a recessed portion 41b provided on the bottom
surface 41a of the pump body 41. In the illustrated example
embodiment, the recessed portion 41b is provided on the bottom
surface 41a of the pump body 41 in an annular shape in the
circumferential direction. A cross-sectional shape of the recessed
portion 41b is a quadrangular shape. The cross-sectional shape of
the recessed portion 41b is not limited to a quadrangular shape and
may be an arc shape or a shape in which a rectangle and an arc are
combined. In addition, a width b of the recessed portion 41b is
larger than a thickness X of the cylinder portion 26 such that the
one end portion 26b of the cylinder portion 26 in the axial
direction can be inserted thereinto. Moreover, a depth h of the
recessed portion 41b has a size such that the seal member 32 and
the one end portion 26b of the cylinder portion 26 in the axial
direction can be inserted into the recessed portion 41b. In this
manner, when the seal member 32 is disposed inside the recessed
portion 41b and the one end portion 26b of the cylinder portion 26
in the axial direction is brought into contact with the seal member
32, the position of the seal member 32 can be set in a contact
state inside the recessed portion 41b. Therefore, when the one end
portion 26b of the cylinder portion 26 in the axial direction is
brought into contact with the seal member 32, in a state where the
seal member 32 is elastically deformed inside the recessed portion
41b, the cylinder portion 26 and the seal member 32 come into
contact with each other, and the seal member 32 and the recessed
portion 41b come into contact with each other. Therefore, it is
possible to curb generation of a gap between the seal member 32 and
the recessed portion 41b and a gap between the seal member 32 and
the cylinder portion 26.
[0034] In addition, as illustrated in FIG. 4C, a seal member 33 may
be disposed inside a recessed portion 26c provided in the one end
portion 26b of the cylinder portion 26 in the axial direction. In
this case, the recessed portion 26c is provided on a distal end
surface of the one end portion 26b of the cylinder portion 26 in
the axial direction in an annular shape in the circumferential
direction. A cross-sectional shape of the recessed portion 26c is a
quadrangular shape. The cross-sectional shape of the recessed
portion 26c is not limited to a quadrangular shape and may be an
arc shape or a shape in which a rectangle and an arc are combined.
In addition, the width b of the recessed portion 26c has a size
such that the seal member 33 can be inserted thereinto, for
example, a size approximately the same as or slightly smaller than
the width of the seal member 33 when the seal member 33 is in a
natural state. Moreover, the depth h of the recessed portion 26c
has a size such that a part of the seal member 33 can protrude from
the recessed portion 26c when the seal member 33 is inserted into
the recessed portion 26c. Therefore, when the one end portion 26b
of the cylinder portion 26 in the axial direction is brought into
contact with the bottom surface 41a of the pump body 41, the seal
member 33 comes into contact with the bottom surface 41a of the
pump body 41 in an elastically deformed state, and the seal member
33 adheres thereto inside the recessed portion 26c. Therefore, it
is possible to further curb generation of a gap between the seal
member 33 and the recessed portion 26c and a gap between the seal
member 33 and the bottom surface 41a.
(Motor Side Discharge Port 27)
[0035] As illustrated in FIG. 1, the motor side discharge port 27
is provided in the bearing holding portion 22. The motor side
discharge port 27 is provided in a circumferential edge portion of
the bearing holding portion 22. The motor side discharge port 27
communicates with the space portion 30 surrounded by the other side
end of the stator 15 in the axial direction, the housing 21, and
the wall portion 25.
<Pump Section 40>
[0036] As illustrated in FIG. 1, the pump section 40 is positioned
on one side of the motor section 10 in the axial direction, in
detail, the front side (positive Z-axis side). The pump section 40
is driven by the motor section 10 via the shaft 5. The pump section
40 has the pump body 41, a pump rotor 45, and a pump cover 47.
Hereinafter, the pump cover 47 and the pump body 41 will be
referred to as the pump case 49.
(Pump Body 41)
[0037] The pump body 41 is fixed to the end portion of the housing
21 on the front side of the motor section 10. The pump body 41 has
a pump chamber 42 which is depressed to the rear side (negative
Z-side) from the surface on the front side (positive Z-side) and
accommodates the pump rotor 45. The shape of the pump chamber 42
viewed in the axial direction is a circular shape.
[0038] The pump body 41 is open at both ends in the axial direction
to allow the shaft 5 to pass therethrough, and an opening on the
front side has a penetration hole 41c open in the pump chamber 42.
The opening of the penetration hole 41c on the rear side is open on
the motor section 10 side. The penetration hole 41c functions as a
bearing member rotatably supporting the shaft 5.
(Pump Rotor 45)
[0039] The pump rotor 45 is attached to the shaft 5. In more
detail, the pump rotor 45 is attached to the end portion of the
shaft 5 on the front side. The pump rotor 45 has an inner rotor 45a
which is attached to the shaft 5 and an outer rotor 45b which
surrounds the outer side of the inner rotor 45a in the radial
direction. The inner rotor 45a has a ring shape. The inner rotor
45a is a gear having teeth on the outer surface in the radial
direction.
[0040] The inner rotor 45a is fixed to the shaft 5. In more detail,
the end portion of the shaft 5 on the front side is press-fitted
into the inner rotor 45a. The inner rotor 45a rotates together with
the shaft 5 in the direction (.theta.-direction) around the axis.
The outer rotor 45b has a ring shape surrounding the outer side of
the inner rotor 45a in the radial direction. The outer rotor 45b is
a gear having teeth on the inner surface in the radial
direction.
[0041] The inner rotor 45a and the outer rotor 45b mesh with each
other, and the outer rotor 45b rotates when the inner rotor 45a
rotates. That is, the pump rotor 45 rotates due to rotation of the
shaft 5. In other words, the motor section 10 and the pump section
40 have the same rotation axis. Therefore, the electric oil pump
can be prevented from having an increased size in the axial
direction. In addition, when the inner rotor 45a and the outer
rotor 45b rotate, the volume of a space between meshed parts of the
inner rotor 45a and the outer rotor 45b changes. A region where the
volume decreases becomes a pressurization region Ap, and a region
where the volume increases becomes a negative pressure region Ad. A
pump side suction port 47a is disposed on one side of the negative
pressure region of the pump rotor 45 in the axial direction. Here,
an oil which has been suctioned into the pump chamber 42 through
the pump side suction port 47a is accommodated in a volume part
between the inner rotor 45a and the outer rotor 45b and is sent to
a delivery hole 41d side allowing the pump section 40 and the motor
section 10 to communicate with each other. Thereafter, the oil is
delivered to the inside of the motor section 10 through the
delivery hole 41d.
(Pump Body 41)
[0042] The delivery hole 41d connecting the pump chamber 42 and a
stator region As inside the motor section 10 to each other is
provided in the pump body 41. The opening of the delivery hole 41d
on the pump chamber 42 side leads to the pressurization region Ap
of the pump rotor 45. On the other hand, the opening of the
delivery hole 41d on the motor section 10 side, that is, a pump
side delivery port 41d1 leads to the stator region As inside the
motor section 10. Therefore, an oil inside the pump section 40 is
delivered to the inside of the stator region As through the pump
side delivery port 41d1 via the delivery hole 41d due to
pressurization of the pump section 40.
(Pump Cover 47)
[0043] The pump cover 47 is attached to the front side of the pump
body 41. The pump cover 47 has a disk shape extending in the radial
direction. The pump cover 47 blocks the opening of the pump chamber
42 on the front side.
[0044] The pump section 40 has the pump side suction port 47a. The
pump side suction port 47a is provided in the pump cover 47. The
pump side suction port 47a is open on the surface of the pump cover
47 on the front side. The pump side suction port 47a leads to the
pump chamber 42 and allows an oil to be suctioned into the pump
chamber 42.
[0045] When the shaft 5 rotates in one direction (negative
.theta.-direction) in the circumferential direction, an oil is
suctioned into the pump chamber 42 through the pump side suction
port 47a. The oil which has been suctioned into the pump chamber 42
is sent to the delivery hole 41d side by the pump rotor 45.
Thereafter, the oil is delivered to the inside of the motor section
10 via the delivery hole 41d by the pump rotor 45. The oil which
has been delivered to the inside of the motor section 10 passes
through the inside of the stator 15. Therefore, the motor section
10 can be cooled.
[0046] Next, a cooling structure of the pump apparatus 1 according
to the present example embodiment will be described. In the present
example embodiment, an oil which has been supplied from an external
apparatus flows inside the pump section 40 through the pump side
suction port 47a by the pump rotor 45, is delivered to the inside
of the motor section 10, and circulates inside the motor section
10, thereby realizing cooling of the stator 15.
[0047] The pump apparatus 1 has a first flow channel 51 for causing
an oil to flow into the pump section 40 through the pump side
suction port 47a; a second flow channel 52 for causing an oil to
flow to a region on a side which is partitioned by the wall portion
25 and on which the stator 15 is present inside the motor section
10, through the pump side delivery port 41d1; and a third flow
channel 53 provided inside the stator 15 to cause an oil to flow
into the stator 15. Hereinafter, details of each flow channel will
be described.
(First Flow Channel 51)
[0048] The first flow channel 51 is provided between the pump side
suction port 47a and the pressurization region Ap inside the pump
section 40. In the example illustrated in FIG. 1, the first flow
channel 51 is a flow channel for causing an oil delivered through
the pump side suction port 47a to move to the pressurization region
Ap from the negative pressure region Ad of the pump rotor 45.
(Second Flow Channel 52)
[0049] The second flow channel 52 is provided between the pump
chamber 42 of the pump section 40 and a space portion 36 inside the
motor section 10. In the example illustrated in FIG. 2, the second
flow channel 52 is a flow channel for connecting the pump chamber
42 and the space portion 36 surrounded by the housing 21 on the
pump section 40 side of the stator region As and the wall portion
25 to each other via the delivery hole 41d. An oil flowing in the
second flow channel 52 flows through the delivery hole 41d and is
delivered to the inside of the space portion 36 through the pump
side delivery port 41d1. An oil which has been delivered to the
inside of the space portion 36 is in a state of filling the inside
of the space portion 36.
(Third Flow Channel 53)
[0050] The third flow channel 53 is a flow channel leading to the
space portion 36 to cause an oil to flow into the stator 15. In the
example illustrated in FIG. 2, as illustrated in FIG. 2, the third
flow channel 53 is a flow channel which is provided between the
coils 18 respectively wound around a pair of teeth portions 17
adjacent to each other in the circumferential direction and leads
to the rear end from the front end of the stator 15. Regarding the
teeth portions 17, as described above, the core back portion 16 is
provided on a base end side of the teeth portions 17. A protrusion
portion 17a protruding in the circumferential direction of the
stator is provided on a distal end side of the teeth portion 17.
Moreover, the cylinder portion 26 is disposed close to the distal
end portions of a pair of teeth portions 17 adjacent to each other
in the circumferential direction. Therefore, a space which is
surrounded by the core back portion 16, the protrusion portion 17a,
and the wall portion 25 and extends in the axial direction is
further formed between the coils 18 of a pair of teeth portions 17
adjacent to each other in the circumferential direction. This space
is the third flow channel 53. Thus, an oil which has flowed into
the third flow channel 53 flows to the rear end from the front end
of the third flow channel 53 and is discharged via the space
portion 30 and the motor side discharge port 27.
[0051] In this manner, since an oil flows near the coils 18 in the
third flow channel 53, heat generated from the coils can be
effectively absorbed by the oil. Thus, the stator 15 can be
efficiently cooled, and the rotor magnet can be prevented from
being demagnetized due to heat radiation of the stator 15. In
addition, although an oil flowing into the motor section 10 flows
inside the stator 15, since the wall portion 25 prevents an oil
from flowing into the region where the rotor 11 is present, there
is no concern that the rotational efficiency of the rotor 11 will
be degraded.
[0052] A flow channel for causing an oil absorbing heat generated
from the coils 18 of the stator 15 to flow is not limited to the
inside of the stator 15 and may be provided between the stator 15
and the housing 21. In the example embodiment illustrated in FIG.
2, a groove portion 55 extending in the axial direction may be
provided on the outer surface of the split core 16a of the stator
15 to form a flow channel, that is, a sixth flow channel 56 in
which an oil can circulate by covering the opening of the groove
portion 55 with the inner surface of the housing 21. As illustrated
in FIG. 1, the front end portion of the sixth flow channel 56 leads
to the space portion 36, and the rear end portion of the sixth flow
channel 56 leads to the space portion 30. Therefore, an oil which
has been delivered to the inside of the space portion 36 through
the pump side delivery port 41d1 flows in the sixth flow channel 56
and is delivered to the space portion 30 on the rear side.
Therefore, heat generated from the coils 18 can be transferred to
and absorbed by the oil via the teeth portions 17 and the core back
portion 16 of the stator 15 and can cool the stator 15.
[0053] The sixth flow channel 56 is not limited to a linearly
extending flow channel. The sixth flow channel 56 may be spirally
provided such that the sixth flow channel 56 advances in the
circumferential direction of the stator 15 toward the axial
direction on the outer surface of the stator 15 or may be provided
in a wave shape such that the sixth flow channel 56 changes the
direction to the other side in the circumferential direction after
changing the direction to one side in the circumferential direction
of the stator 15 toward the axial direction on the outer surface of
the stator 15.
[0054] In addition, the coil 18 of the stator 15 may be
resin-molded. When the coil 18 is resin-molded, the coil 18 is
covered with a resin, and the resin also flows into a space between
the coils 18 adjacent to each other. Therefore, the contact area
between an oil and the coils 18 can be increased via the resin.
Therefore, when an oil flows on the surfaces of the resin-molded
coils 18, heat generated from the coils can be effectively cooled.
In addition, unevenness on the surface of the coil group can be
reduced by covering the coils exposed to the surface side of the
coil group wound around the teeth portions 17 in resin-molding with
a resin. Therefore, an oil can flow more smoothly.
[0055] In addition, the wall portion 25 and the stator 15 may be
integrally molded products formed of a resin. In the example
embodiment illustrated in FIG. 3, the wall portion 25 is integrally
connected to the stator 15 via the teeth portions 17 of the stator
15. That is, the stator 15 and the wall portion 25 are a part of a
single member. In this manner, when the wall portion 25 and the
stator 15 are integrally molded products formed of a resin, a gap
between the distal end portions of the teeth portions 17 and the
wall portion 25 can be eliminated. Therefore, the amount of an oil
leaking out from the third flow channel 53 can be reduced, and
cooling efficiency of the stator 15 can be improved.
[0056] In addition, as illustrated in FIG. 1, a space between the
other end portion of the stator 15 in the axial direction and the
bearing holding portion 22 attached to the housing 21 inside the
motor section 10, that is, the space portion 30 surrounded by the
stator 15, the wall portion 25, and the housing 21 is provided
inside the motor section 10. However, this space portion 30 can be
filled with an oil. When this space portion 30 is provided in the
motor section 10, an oil flowing out from the third flow channel 53
is in a state of filling the space portion 30 and is discharged
through the motor side discharge port 27. Therefore, an oil can be
efficiently discharged through the motor side discharge port
27.
[0057] In this manner, in the pump apparatus 1 according to the
first example embodiment, when the motor section 10 is driven, an
oil passes through the first flow channel 51 and flows into the
pump section 40. A part of the oil which has flowed into the pump
section 40 passes through the second flow channel 52 and is
delivered to the space portion 36 through the pump side delivery
port 41d1. The second flow channel 52 is present on the stator
region As side partitioned by the wall portion 25 inside the motor
section 10. Therefore, since the wall portion 25 prevents an oil
flowing in the second flow channel 52 from flowing to the rotor 11
side, most of the oil delivered through the pump side delivery port
41d1 can flow into the stator 15 via the third flow channel 53.
Thus, it is possible to realize the pump apparatus 1 in which the
stator 15 can be cooled using an oil circulating in the pump
section 40, without having the rotational efficiency of the rotor
11 being degraded.
Modification Example of First Example Embodiment
[0058] Next, a modification example of the pump apparatus 1
according to the first example embodiment will be described. FIG. 5
is a cross-sectional view of the pump apparatus 1 illustrating a
modification example of the wall portion 25 in the first example
embodiment. In the modification example of the first example
embodiment, only the points different from the first example
embodiment will be described. The same reference signs are applied
to parts having the same form as the first example embodiment, and
description thereof will be omitted.
[0059] As illustrated in FIG. 5, a wall portion 60 disposed inside
the motor section 10 has a step portion 61 in which a front side
portion 60a on the pump section 40 side of one end portion of the
rotor 11 in the axial direction is bent to the shaft 5 side and
extends to the pump section 40 side along the shaft 5. The step
portion 61 has a ring-shaped end wall portion 61a and a cylindrical
circumferential wall portion 61b. The circumferential wall portion
61b continues to the inner end of the end wall portion 61a in the
radial direction and extends to the front side in the axial
direction. The end wall portion 61a extends in the up-down
direction from the rear end of the circumferential wall portion 61b
in the axial direction. The shaft 5 internally penetrates the
circumferential wall portion 61b. A gap is provided between the
inner circumferential surface of the circumferential wall portion
61b and the outer circumferential surface of the shaft 5, and the
shaft 5 can rotate.
[0060] In this manner, when the step portion 61 is provided on the
front side of the wall portion 25 in the axial direction, a region
of a space portion 36' between one end of the stator 15 in the
axial direction and the pump section 40 can be increased.
Therefore, the amount of an oil delivered from the second flow
channel 52 to fill the inside of the space portion 36' can be
increased. Therefore, it is possible to efficiently supply an oil
flowing to the third flow channel 53 from the space portion
36'.
Second Example Embodiment
[0061] Next, a pump apparatus 3 according to a second example
embodiment of the present disclosure will be described. In the
second example embodiment, only the points different from the first
example embodiment will be described. The same reference signs are
applied to parts having the same form as the first example
embodiment, and description thereof will be omitted. FIG. 6 is a
cross-sectional view of the pump apparatus 3 according to the
second example embodiment.
[0062] A motor side suction port 63 for suctioning an oil into the
motor section 10 between the housing 21 and the wall portion 25 is
provided in the motor section 10. In the example embodiment
illustrated in FIG. 6, the motor side suction port 63 is provided
in the housing 21 on the rear side of the rear end portion of the
stator 15. In addition, a fourth flow channel 64 for causing an oil
which has passed through the motor side suction port 63 to flow
into the motor section is provided in the pump apparatus 3. In the
example embodiment illustrated in FIG. 6, an oil flowing out from a
speed change gear (not illustrated) flows into the motor section 10
through the fourth flow channel 64. That is, an oil passing through
the fourth flow channel 64 flows into the space portion 30 provided
on the rear side of the motor section 10 described above. The third
flow channel 53 illustrated in FIG. 1 as described above is
provided in the stator 15. However, the present example embodiment
differs in that the direction of a flow of an oil is a direction
toward the front side from the rear side of the stator 15.
[0063] A pump side introduction port 66 for introducing an oil
inside the motor section 10 into the pump section 40 using a
negative pressure of the pump section 40 is provided in the pump
body 41 of the pump section 40. In the example embodiment
illustrated in FIG. 6, the pump side introduction port 66 is open
in the space portion 36 provided on the front side of the motor
section 10.
[0064] In addition, a fifth flow channel 65 for introducing an oil
inside the motor section 10 into the pump section 40 through the
pump side introduction port 66 is provided in the pump body 41. In
the example embodiment illustrated in FIG. 6, an introduction hole
68, in which one end side is open in the negative pressure region
Ad of the pump section 40 and the other end side leads to the pump
side introduction port 66, is provided in the pump body 41. The
fifth flow channel 65 connects the space portion 36 and the
negative pressure region Ad of the pump section 40 to each other
via the introduction hole 68. A pump side discharge port 47b for
discharging an oil which has been suctioned into the pump section
40 is provided in the pump cover 47. The pump side discharge port
47b leads to the pressurization region Ap of the pump rotor 45. The
pump apparatus 1 of the second example embodiment does not have the
pump side delivery port 41d1, the motor side discharge port 27, and
the pump side suction port 47a illustrated in FIG. 1.
[0065] In the pump apparatus 1 according to the second example
embodiment, when the motor section 10 is driven, an oil flowing in
the fourth flow channel 64 flows into the space portion 30 via the
motor side suction port 63. The oil which has flowed into the space
portion 30 flows toward the front side from the rear side of the
motor section 10 via the third flow channel 53. The oil which has
flowed out from the third flow channel 53 is introduced into the
pump section 40 through the pump side introduction port 66. Here,
since an oil which has flowed into the motor section 10 is
prevented by the wall portion 25 from flowing to the rotor 11 side,
most of the oil which has been delivered to the inside of the motor
section 10 can flow into the stator 15 via the third flow channel
53. Thus, it is possible to realize the pump apparatus 1 in which
the stator 15 can be cooled using an oil flowing into the motor
section 10, without having the rotational efficiency of the rotor
11 being degraded.
[0066] In addition, as described above, the space portion 36
surrounded by the stator 15, the wall portion 25, and the housing
21 is provided between one end portion of the stator 15 in the
axial direction and one end portion of the housing 21 in the axial
direction inside the motor section 10. However, this space portion
36 may be able to be filled with an oil. In the illustrated example
embodiment, the space portion 36 surrounded by the stator 15, the
wall portion 25, and the housing 21 is provided between the front
end portion of the stator 15 in the axial direction and the bottom
surface 41a of the pump body 41 of the pump section 40 inside the
motor section 10. Since the space portion 36 can be filled with an
oil flowing out from the third flow channel 53 by providing this
space portion 36, an oil can be efficiently introduced into the
pump section 40 through the pump side introduction port 66.
[0067] Hereinabove, preferable example embodiments of the present
disclosure have been described. However, the present disclosure is
not limited to these example embodiments, and various modifications
and changes can be made within a range of the gist thereof.
[0068] While example embodiments of the present disclosure have
been described above, it is to be understood that variations and
modifications will be apparent to those skilled in the art without
departing from the scope and spirit of the present disclosure. The
scope of the present disclosure, therefore, is to be determined
solely by the following claims.
* * * * *