U.S. patent application number 16/523327 was filed with the patent office on 2019-11-14 for reactive sintering of ceramic lithium-ion solid electrolytes.
The applicant listed for this patent is CORNING INCORPORATED. Invention is credited to Bruce Gardiner Aitken, Michael Edward Badding, George Halsey Beall, Curtis Robert Fekety, Lanrik Wayne Kester, Robert Michael Morena, Zhen Song.
Application Number | 20190348706 16/523327 |
Document ID | / |
Family ID | 47352007 |
Filed Date | 2019-11-14 |



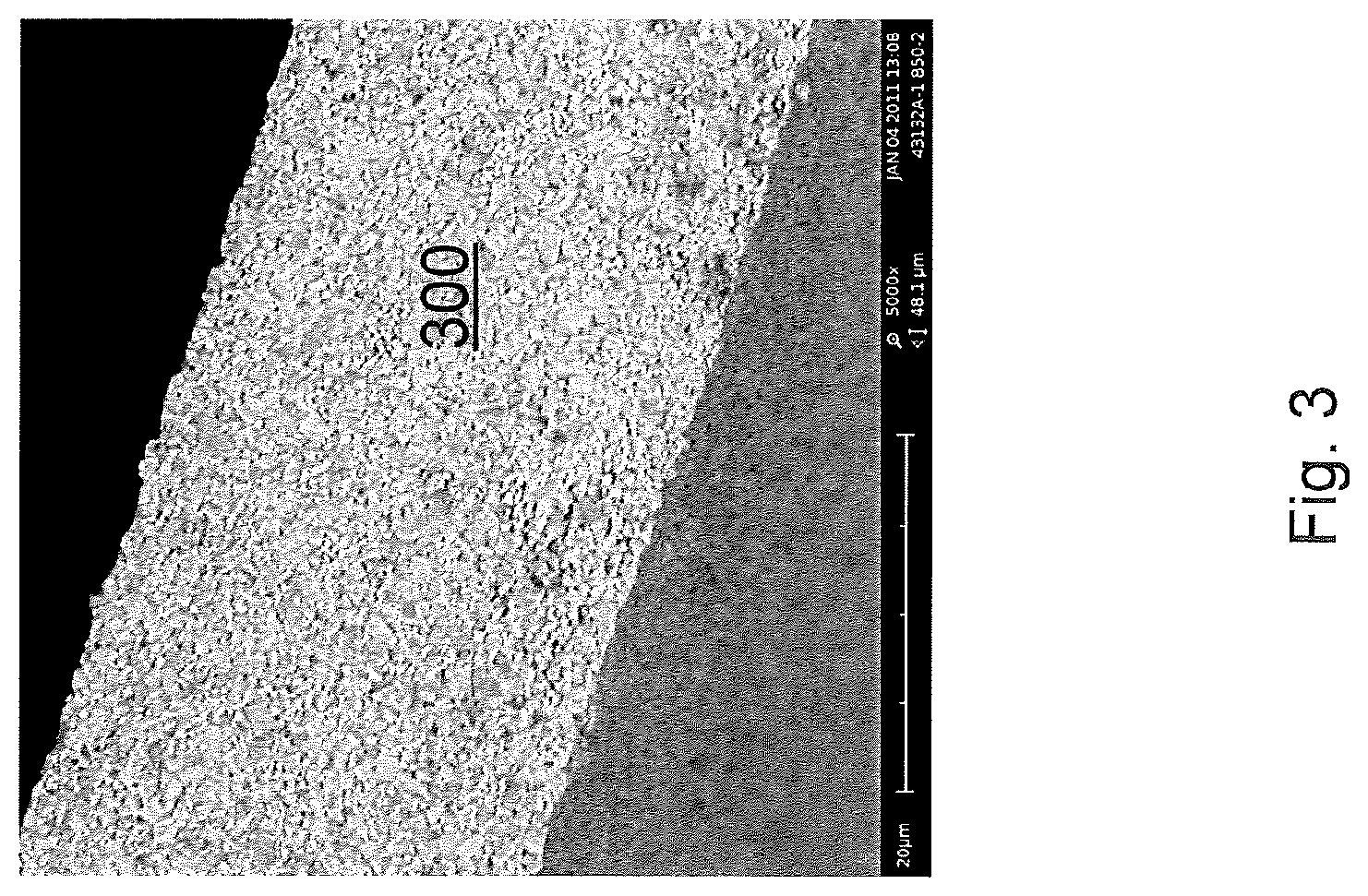


United States Patent
Application |
20190348706 |
Kind Code |
A1 |
Aitken; Bruce Gardiner ; et
al. |
November 14, 2019 |
REACTIVE SINTERING OF CERAMIC LITHIUM-ION SOLID ELECTROLYTES
Abstract
A method of forming a solid, dense, hermetic lithium-ion
electrolyte membrane comprises combing an amorphous, glassy, or low
melting temperature solid reactant with a refractory oxide reactant
to form a mixture, casting the mixture to form a green body, and
sintering the green body to form a solid membrane. The resulting
electrolyte membranes can be incorporated into lithium-ion
batteries.
Inventors: |
Aitken; Bruce Gardiner;
(Corning, NY) ; Badding; Michael Edward;
(Campbell, NY) ; Beall; George Halsey; (Big Flats,
NY) ; Fekety; Curtis Robert; (Corning, NY) ;
Kester; Lanrik Wayne; (Savona, NY) ; Morena; Robert
Michael; (Lindley, NY) ; Song; Zhen; (Painted
Post, NY) |
|
Applicant: |
Name |
City |
State |
Country |
Type |
CORNING INCORPORATED |
Corning |
NY |
US |
|
|
Family ID: |
47352007 |
Appl. No.: |
16/523327 |
Filed: |
July 26, 2019 |
Related U.S. Patent Documents
|
|
|
|
|
|
Application
Number |
Filing Date |
Patent Number |
|
|
13306011 |
Nov 29, 2011 |
10411288 |
|
|
16523327 |
|
|
|
|
Current U.S.
Class: |
1/1 |
Current CPC
Class: |
C04B 35/447 20130101;
C04B 2235/77 20130101; C04B 2235/3287 20130101; C03C 8/14 20130101;
C04B 2235/5454 20130101; C03C 3/253 20130101; C03C 3/16 20130101;
H01M 10/0562 20130101; C04B 2235/3201 20130101; C04B 2235/3293
20130101; B82Y 30/00 20130101; C04B 2235/5445 20130101; C03C 8/20
20130101; C04B 2235/3244 20130101; C04B 2235/3203 20130101; C03B
19/06 20130101; C04B 2235/36 20130101; C04B 2235/3217 20130101;
C04B 2235/785 20130101; H01M 10/0525 20130101; C04B 2235/3232
20130101 |
International
Class: |
H01M 10/0525 20060101
H01M010/0525; C03C 8/20 20060101 C03C008/20; H01M 10/0562 20060101
H01M010/0562; C03C 3/253 20060101 C03C003/253; B82Y 30/00 20060101
B82Y030/00; C03C 8/14 20060101 C03C008/14; C03C 3/16 20060101
C03C003/16; C03B 19/06 20060101 C03B019/06; C04B 35/447 20060101
C04B035/447 |
Claims
1. A solid lithium-ion electrolyte membrane having a composition
represented by the formula
Li.sub.1+x-yM.sub.xM'.sub.2-x-yM''.sub.y(PO.sub.4).sub.3, wherein M
is a 3.sup.+ ion, M' is a 4.sup.+ ion, M'' is a 5.sup.+ ion,
0.ltoreq.x.ltoreq.2 and 0.ltoreq.y.ltoreq.2.
2. The electrolyte membrane according to claim 1, wherein M is Al
or Fe, M' is selected from the group consisting of Ti, Sn, Nb and
Ge, and M'' is Nb.
3. The electrolyte membrane according to claim 1, wherein a
thickness of the membrane is less than 200 microns.
4. The electrolyte membrane according to claim 1, wherein a
conductivity of the membrane is greater than 10.sup.-4 S/cm.
5. The electrolyte membrane according to claim 1, wherein a density
of the membrane is at least 95% of its theoretical density.
6. A solid electrolyte membrane comprising a sintered reaction
product of a first powder and a second powder, wherein the first
powder comprises a first inorganic, non-lithium-ion-conductive
glass or ceramic, and the second powder comprises a second
inorganic, non-lithium-ion-conductive glass or ceramic.
7. The solid electrolyte membrane according to claim 6, wherein the
first powder comprises a material selected from the group
consisting of lithium phosphate glasses, germanium phosphate
glasses, lithium aluminum phosphate glasses and crystallized
lithium aluminum phosphate ceramics and the second powder comprises
a material selected from the group consisting of titanium oxide,
tin oxide and germanium oxide.
Description
CROSS-REFERENCE TO RELATED APPLICATIONS
[0001] This application is a divisional application of U.S.
application Ser. No. 13/306,011, filed Nov. 29, 2011 and claims the
benefit of priority thereto under 35 U.S.C. .sctn. 120, the content
of which is relied upon and incorporated herein by reference in its
entirety.
BACKGROUND
[0002] The present disclosure relates generally to the formation of
ceramic lithium-ion solid electrolytes, and more specifically to a
reactive sintering process for forming dense, hermetic electrolyte
membranes.
[0003] Solid electrolytes, also known as fast ion conductors, are
materials that can function as solid state ion conductors and can
be used, for example, in solid oxide fuel cells and lithium-ion
batteries. In a lithium-ion battery, for example, lithium ions move
from a negative electrode to a positive electrode during discharge
(and back when charging) via the solid electrolyte. The solid
electrolyte, such as lithium aluminum titanium phosphate (LATP),
can conduct lithium ion through vacancies in the LATP crystal
lattice. In Li-ion batteries, the solid electrolyte membrane can
provide a hermetic barrier between the anode and the cathode in
order to prevent the anode and cathode from sharing a common
electrolyte solution.
[0004] Thus, important to the development of Li-ion batteries is
the availability of dense, conductive lithium-ion electrolyte
membranes. A major challenge for such membranes is the desire to
sinter suitable materials to sufficient density such that the
membrane is hermetic while providing sufficient conductivity and
economy. Conventional hermetic membranes, for example, which are
commonly made using a glass-ceramic process, can be made dense and
hermetic, but typically at the expense of other attributes such as
conductivity and cost. A challenge facing the conventional
glass-ceramic process is the requirement that the desired
composition form a stable glass.
[0005] In view of the foregoing, it would be desirable to develop a
process for forming dense, hermetic, Li-ion conductive ceramic
electrolyte membranes without such a limitation to stable glass
formation. As used herein, a hermetic membrane is substantially
impervious to the diffusion of liquids or gasses.
[0006] Additional features and advantages will be set forth in the
detailed description which follows, and in part will be readily
apparent to those skilled in the art from that description or
recognized by practicing the invention as described herein,
including the detailed description which follows, the claims, as
well as the appended drawings.
[0007] It is to be understood that both the foregoing general
description and the following detailed description present
embodiments of the invention, and are intended to provide an
overview or framework for understanding the nature and character of
the invention as it is claimed. The accompanying drawings are
included to provide a further understanding of the invention, and
are incorporated into and constitute a part of this specification.
The drawings illustrate various embodiments of the invention and
together with the description serve to explain the principles and
operations of the invention.
SUMMARY
[0008] Disclosed herein is a reactive sintering method for forming
a Li-ion conductive ceramic electrolyte membrane. The process
involves reactive sintering of at least two solid state reactants.
In embodiments, the reactive components are powders that are
combined, and heated to simultaneously react the components and
densify the reaction product. The heating step can be used to form
the reaction product into a membrane using a process such as tape
casting.
[0009] A method of forming a solid lithium-ion electrolyte membrane
comprises combining an amorphous, glassy, or low melting
temperature solid reactant with a refractory oxide reactant to form
a mixture, casting the mixture to form a green body, and sintering
the green body to form a solid membrane. As used herein, a glassy
material has a softening point of less than 850.degree. C., a low
melting temperature solid reactant has a melting temperature less
than or equal to 850.degree. C., and a refractory oxide has a
melting temperature of greater than 850.degree. C. Thus, in various
embodiments the reactants include a glassy material and a ceramic
material. The refractory oxide may be an amorphous material,
including a glass. In a complementary embodiment, the reactants
include at least one amorphous material, at least one glassy
material, at least one low melting temperature material that are
combined with at least one refractory oxide. In each of the
embodiments, at least one of the reactants is an amorphous, glassy
or low melting temperature solid reactant and at least one of the
reactants is a refractory oxide.
[0010] Each of the reactants can comprise a powder material having,
for example, a submicron particle size distribution. In an example
method, the reactive sintering temperature is less than
1100.degree. C., e.g., less than 1000.degree. C.
[0011] Disclosed also are solid lithium-ion electrolyte membranes
having a composition represented by the formula
Li.sub.1+x-yM.sub.xM'.sub.2-x-yM''.sub.y(PO.sub.4).sub.3, wherein M
is a 3.sup.+ ion, M' is a 4.sup.+ ion, and M'' is a 5.sup.+ ion. In
the foregoing, 0.ltoreq.x.ltoreq.2 and 0.ltoreq.y.ltoreq.2. In an
example embodiment the product composition is a lithium metal
phosphate having the NaZr.sub.2(PO.sub.4).sub.3 ("NZP") crystal
structure. For example, embodiments relate to dense, hermetic
Li.sub.1.4Al.sub.0.4Sn.sub.1.6(PO.sub.4).sub.3 lithium-ion
electrolyte membranes.
[0012] The resulting membrane can have an average thickness of less
than 200 microns, e.g., less than 150 microns, where the
constituent electrolyte material can have an average grain size of
less than 10 um, e.g., less than 1 um. For certain compositions,
self-supporting ceramic membranes as thin as 30 microns can be
formed.
[0013] According to a further embodiment, a solid electrolyte
membrane comprises a sintered reaction product of a first powder
and a second powder. The first powder comprises a first inorganic,
non-lithium-ion-conductive glass or ceramic, and the second powder
comprising a second inorganic, non-lithium-ion-conductive glass or
ceramic. Thus, at least one of the first and second inorganic glass
or ceramic powders contains lithium in composition, but is not a
lithium ion conductor. In further embodiments, none of the
reactants are lithium ion conductors. As defined herein, a lithium
ion conductor has a conductivity of at least 10.sup.-6 S/cm.
BRIEF DESCRIPTION OF THE DRAWINGS
[0014] FIG. 1 is a is a schematic representation of one embodiment
comprising the reaction of a lithium phosphate glass (A) with
titanium dioxide to produce a water stable membrane with
LiTi.sub.2(PO).sub.3 as the major phase;
[0015] FIG. 2 is an illustration of the glass-forming regions in
the Li.sub.2O--Al.sub.2O.sub.3--P.sub.2O.sub.5 composition
space;
[0016] FIG. 3 is an SEM cross-sectional micrograph of an LATP
membrane made according to an embodiment;
[0017] FIG. 4 is a family of XRD scans for example titanium
phosphate powders; and
[0018] FIG. 5 is a family of XRD scans for example aluminum
titanium phosphate powders.
DETAILED DESCRIPTION
[0019] A conventional glass-ceramic approach can be used to form
certain lithium metal phosphate electrolyte compositions. However,
the glass-ceramic approach is inherently limited to starting
compositions that can form a homogeneous glass, typically at
temperatures in excess of 1000.degree. C. Further, the sintering of
ceramic Li-ion electrolyte materials to a density sufficient to
produce hermetic membranes can be difficult due to the vaporization
of volatile lithium and/or phosphate species at temperatures above
about 1000.degree. C. These limitations, in addition to restricting
control of the process conditions, restrict the compositional space
available for the optimization of important properties like
conductivity and environmental stability.
[0020] According to a disclosed method of forming a solid
lithium-ion electrolyte membrane, an amorphous, glassy, or low
melting temperature solid reactant is combined with a refractory
oxide reactant to form a mixture. The mixture is then cast to form
a green body, which is sintered to form a solid membrane. Reaction
of the amorphous, glassy, or low melting temperature solid with the
refractory oxide to produce the final membrane composition and
densification of the structure occur simultaneously, i.e., the acts
of reacting and densifying at least partially overlap with one
another during the heating.
[0021] In the disclosed approach, the amorphous, glassy, or low
melting temperature reactant mobilizes the diffusion of reactant
components, which promotes sintering, and is entirely or
substantially entirely reacted and converted to the target Li-ion
ceramic electrolyte composition. In this way, the advantage of a
mobilizing glass or low melting temperature liquid phase is
provided without the issue of environmental instability because the
amorphous, glassy, or low melting temperature component is
substantially consumed during the formation reaction that yields
the product phase.
[0022] The amorphous, glassy, or low melting temperature
reactant(s) can comprise, for example, lithium phosphate glasses or
lithium aluminum phosphate glasses (e.g., 39% Li.sub.2O+11%
Al.sub.2O.sub.3+50% P.sub.2O.sub.5). Additional example glasses
include germanium phosphates (e.g., 75% GeO.sub.2+25%
P.sub.2O.sub.5) and amorphous aluminum titanium phosphates. Further
example reactants include crystallized lithium aluminum phosphate
ceramics. The refractory oxides can include various oxide ceramics
such as, for example, titanium oxide, tin oxide and germanium oxide
(i.e., MO.sub.2 oxides and ceramics).
[0023] The amorphous, glassy, or low melting temperature
reactant(s) may further comprise an oxide modifier such as
TiO.sub.2, GeO.sub.2, SiO.sub.2, B.sub.2O.sub.3, Fe.sub.2O.sub.3,
Nb.sub.2O.sub.5 and SnO.sub.2. An oxide modifier, if used, is
limited to at most 30 mol. % of the amorphous, glassy, or low
melting temperature reactant. For example, the concentration of the
oxide modifier can be 1, 2, 5, 10, 20, 25 or 30 mol. % of the
amorphous, glassy, or low melting temperature reactant.
[0024] In embodiments, an average particle size of the respective
reactants can be less than 0.5 micron (e.g., d50<0.5 micron). An
average particle size of one or all of the reactants can be less
than 0.5, 0.1, 0.05 or 0.01 microns.
[0025] The reactive sintering can be performed at a sintering
temperature of less than 1100.degree. C. (e.g., less than 1100,
1050, 1000, 950, 900 or 850.degree. C.), and result in a solid
membrane having a thickness of less than 200 microns (e.g., less
than 200, 150, 100 or 50 microns). In embodiments, the maximum
processing temperature (e.g., melting temperature of the glass) is
less than 1300.degree. C. (e.g., less than 1300, 1250, 1200, 1150,
1100, 1050, 1000, 950, 900 or 850.degree. C.). By minimizing the
sintering (processing) temperature, the loss of lithium or
phosphate constituents can be minimized. In embodiments, a
conductivity of the electrolyte membrane is greater than 10.sup.-4
S/cm (e.g., greater than 1.times.10.sup.-4, 2.times.10.sup.-4,
5.times.10.sup.-4 or 1.times.10.sup.-5/cm). The electrolyte
membrane can be fully dense or have a density that is at least 95%
(e.g., at least 95, 96, 97, 98, 99, 99.9 or 99.99%) of its
theoretical density.
[0026] The invention may be better understood through the following
examples.
Example 1--LTP Via LP Glass and TiO.sub.2
[0027] One approach to promoting sintering is to add excess
lithium, which can result in the formation of low melting point
lithium phosphate liquid phases. This approach may also result,
however, in residual lithium phosphate phase that leaches in
aqueous environments from the final membrane, resulting in
mechanical weakness and/or membrane failure. According to
embodiments, a water-stable membrane can be formed using a low
melting point reactant that forms a liquid phase during sintering,
but where the low melting point reactant is consumed during
sintering.
[0028] Referring to the Li.sub.2O--TiO.sub.2--P.sub.2O.sub.5
composition diagram shown in FIG. 1, the water stability of the
various phases indicated in this figure has been evaluated. Phases
indicated with a filled circle are stable whereas phases indicated
by an unfilled circle are unstable in water. Stability was
determined by exposing each phase to distilled water and measuring
the conductivity of the leachate. If a substantial increase in
leachate conductivity was observed, the phase is considered
unstable in water.
[0029] According to the present example, and still referring to
FIG. 1, a lithium phosphate glass of composition "A" (25%
Li.sub.2O:75% P.sub.2O.sub.5) is made by melting and quenching the
appropriate composition. The glass of composition "A" is located
within a glass-forming region. The glass is milled and added to
milled TiO.sub.2 to yield a composition nominally equivalent to
LiTi.sub.2(PO.sub.4).sub.3 with slight TiO.sub.2 excess. The milled
powders are incorporated into a tape casting slip with suitable
binders and rheological modifiers, cast to a green tape, dried,
cut, released and sintered to make a ceramic electrolyte membrane.
This process forms a water stable phase after the lithium phosphate
is consumed in making the LiTi.sub.2(PO.sub.4).sub.3. Prior to
completion of the reaction, the lithium phosphate glass provides
for enhanced mobility of the reactant components, facilitating
sintering and densification.
Example 2--LATP Via LAP Glass and TiO.sub.2
[0030] A lithium-ion ceramic electrolyte with the composition
Li.sub.1+xAl.sub.xTi.sub.2-x(PO.sub.4).sub.3 is formed. This
material, which is aluminum doped, has been shown to have a high
lithium ion-conductivity exceeding 10.sup.-4 S/cm.
[0031] Compared with the lithium phosphate glasses,
Li.sub.2O--Al.sub.2O.sub.3--P.sub.2O.sub.5 glasses are less
hygroscopic and can be milled to submicron particle size. FIG. 2
shows the glass-forming region within the
Li.sub.2O--Al.sub.2O.sub.3--P.sub.2O.sub.5 "LAP" composition space.
The region "1" corresponds to a compositional range that forms a
clear glass upon melting, while the compositions within regions "2"
form a partially crystallized glass.
[0032] In this example, an LAP glass of composition (mol. %) 29.2%
Li.sub.2O, 8.3% Al.sub.2O.sub.3 and 62.5% P.sub.2O.sub.5
(composition "B") was made by melting a mixture of lithium
carbonate, aluminum metaphosphate and phosphoric acid in the
appropriate quantities. The components were mixed in a platinum
crucible, dried overnight at 250.degree. C., and melted at
1000.degree. C. In one case, the liquid melt was poured onto a
steel plate to quench, yielding a partially-crystallized glass.
Partial crystallization was identified by powder x-ray diffraction,
which confirmed the formation of crystalline Al(PO.sub.3).sub.3) in
the otherwise glassy matrix. In a separate case, in addition to
pouring the liquid melt onto the steel plate, the poured glass was
roller quenched, which increased the quench rate and resulted in a
clear glass.
[0033] The formed glass was broken up and dry milled to form a
free-flowing powder. The powdered glass was mixed in a solvent
mixture containing ethanol, butanol, propylene glycol and Emphos
dispersant. The powder was wet-milled in a high-energy attrition
mill to a particle size with d50<0.5 micron. Separately,
nano-particle TiO.sub.2 (Aldrich, 15 nm primary particle size) was
prepared by mixing nano-TiO.sub.2 in a similar solvent system and
attrition milling to an agglomerate size d50<0.5 micron.
[0034] Without wishing to be bound by theory, by providing
reactants having a small particle size, the particle size within
the final membrane can be controlled (i.e., minimized).
[0035] Solids from the two mill batches (LAP glass, nano-TiO.sub.2)
were mixed to resultant composition of
Li.sub.1.4Al.sub.0.4Ti.sub.1.6(PO.sub.4).sub.3 and further milled
to promote good mixing of the two reactant materials.
Polyvinylbutyral binder and a plastisizer were dissolved into the
mill batch to make a tape casting slip. In embodiments, a tape
casting slip can optionally include one or both of a binder and a
plastisizer. The slip was tape cast, dried, released and fired at
850.degree. C. for two hours to make a sample electrolyte
membrane.
[0036] Samples from the sample membrane were cut into 1'' diameter
disks and characterized by SEM analysis for microstructure, XRD for
phase composition and impedance spectroscopy for conductivity. A
cross-section SEM image is shown in FIG. 3. The membrane 300 is
free-standing (i.e., unsupported by a substrate), dense, hermetic
and has an average grain size of less than 1 micron and a thickness
of about 30 microns. Impedance spectroscopy shows a conductivity of
3.times.10.sup.-4 S/cm. XRD shows reflections consistent with
nearly pure Li.sub.1.4Al.sub.0.4Ti.sub.1.6(PO.sub.4).sub.3.
[0037] Compared with the glass-ceramic method, which can involve
processing temperatures greater than 1300.degree. C., the
relatively low processing temperatures associated with the present
example minimize lithium and phosphorus loss, which results in a
more reproducible, lower cost process.
Example 3--LAGP
[0038] The LAP glass described in example 2 was mixed with a mill
batch containing GeO.sub.2 milled to a d50 of less than 0.5
microns. A tape cast green tape was prepared in a manner similar to
that used in Example 2. The tape was dried, cut, released and
sintered at 900.degree. C. for 2 hours to make a membrane sample.
Samples were cut into 1'' diameter disks and characterized by SEM,
XRD and impedance spectroscopy. The resulting membrane is dense,
hermetic and has an average grain size of less than 1 micron. XRD
shows near pure Li.sub.1.4Al.sub.0.4Ge.sub.1.6(PO.sub.4).sub.3. A
conductivity of 1.8.times.10.sup.-4 S/cm was measured by impedance
spectroscopy.
Example 4--LASnP
[0039] The LAP glass described in Example 2 was mixed with a mill
batch containing SnO.sub.2 milled to a d50 of less than 0.5
microns. A tape cast green tape was prepared in a manner similar to
that used in Example 2. The tape was dried, cut, released and
sintered at 900.degree. C. for 2 hours to make a membrane sample.
Samples were cut into 1'' diameter disks and characterized by SEM,
XRD and impedance spectroscopy. The resulting membrane is dense,
hermetic and has an average grain size of less than 1 micron. XRD
shows near pure Li.sub.1.4Al.sub.0.4Sn.sub.1.6(PO.sub.4).sub.3. A
conductivity of 2.1.times.10.sup.-4 S/cm was measured by impedance
spectroscopy.
[0040] Due to the limited solubility of tin oxide in glass phases,
Applicants believe that the LASnP composition of the present
example cannot be produced by a glass-ceramic method.
Example 5--Modified LAP Glass
[0041] To reduce the hygroscopicity of the starting LAP glass, and
to reduce milling time by increasing the glass transition
temperature of the glass, the starting LAP glass may be modified by
including a fraction of a transition metal desired in the final
NASICON material. The table below compares hygroscopic behavior and
milling times required to achieve a d50 of less than 0.5 microns
for a variety of "LAP+M" melts. In Table 1, the designation "a" in
the ID column represents the amount of Al substitution, i.e.,
Li.sub.1+aAl.sub.aM.sub.2-a(PO.sub.4).sub.3. The Li.sub.2O,
Al.sub.2O.sub.3, P.sub.2O.sub.5, TiO.sub.2 and GeO.sub.2
compositions are reported in mol. %. The melting temperature
T.sub.m is given in degrees Celsius. Column 9 of the Table
indicates whether the glass was hygroscopic or not. In column 10,
the mill time is given in hours. As seen with reference to samples
5-8, the addition of TiO.sub.2 and/or GeO.sub.2 can reduce the
hygroscopic behavior and reduce milling time.
TABLE-US-00001 TABLE 1 Modified LAP glass compositions ID Li.sub.2O
Al.sub.2O.sub.3 P.sub.2O5 TiO.sub.2 GeO.sub.2 T.sub.m Hyg. mill 1
LATP 0.175 0.050 0.375 0.400 0.000 -- 2 LP, a = 0 0.250 0.000 0.750
0.000 0.000 1100 Yes 3 LP + G, a = 0 0.225 0.000 0.675 0.000 0.100
1200 Yes 4 LAP, a = 0.2 0.273 0.045 0.682 0.000 0.000 1100 Yes 5
LAP + T, a = 0.2 0.245 0.041 0.614 0.100 0.000 1200 No 6 LAP, a =
0.4 0.292 0.083 0.625 0.000 0.000 1000 No 240 7 LAP + T, a = 0.4
0.263 0.075 0.563 0.100 0.000 1300 No 96 8 LAP + G, a = 0.4 0.263
0.075 0.563 0.000 0.100 1200 No 96
[0042] In Table 1, the primary phases identified by XRD for samples
5-7 were TiP.sub.2O.sub.7, Al(PO.sub.3).sub.3, and
TiP.sub.2O.sub.7, respectively. The XRD scan from sample 8 was
amorphous.
Example 6--Amorphous Flame Spray Powder
[0043] In a further embodiment, hermetic LATP membranes can be made
via reactive sintering from an amorphous titanium phosphate (TP)
and/or aluminum titanium phosphate (ATP) material. A flame spray
pyrolysis (FSP) method was used to generate amorphous TP and ATP
nanopowders. In the FSP process, Ti, Al and P precursors, such as
Ti-isopropoxide, Al tri-sec butoxide, AlCl.sub.3,
trimethylphosphate, etc. are dissolved in an organic solvent such
as ethanol, isopropanol, 2-methoxyethanol, etc. Due to the high
volatility of certain precursors, the precursor concentration in
solution can be at least 30% (e.g., at least 40%) in order to
minimize loss of the precursor material during combustion. In an
example process, the solution is sprayed through a nozzle, which is
surrounded by CH.sub.4/O.sub.2 flame, to combust the sprayed
droplets. In the flame, the precursor materials react to form the
nanopowder product.
TABLE-US-00002 TABLE 2 Precursor and powder compositions for TP and
ATP materials Solution Powder LATP Target Sample P/Ti P/Ti P/Ti TP1
2.4 1.24 1.857 TP2 2.2 1.48 TP3 1.8 1.48 P/(Al + Ti) P/(Al + Ti)
P/(Al + Ti) ATP1 1.95 1.03 1.5 ATP2 1.08 1.02 ATP3 1.27 1.44
[0044] Table 2 lists example precursor (solution) compositions
together with the corresponding powder compositions for example TP
and ATP materials. XRD diffraction scans for the resulting powders
are shown in FIG. 4 (TP) and FIG. 5 (ATP).
[0045] In an example synthesis, a substantially amorphous ATP
powder was fabricated by the flame spray pyrolysis technique. The
ATP powder composition (in mol. %) was 0.1065
Al.sub.2O.sub.3--0.518 TiO.sub.2--0.376 P.sub.2O.sub.5. The
amorphous ATP nanopowder was wet mill mixed with crystalline
powders of TiP.sub.2O.sub.7, Li.sub.3PO.sub.4 and Li.sub.2CO.sub.3
and the mixture was attrition wet milled to a particle size of less
than 0.5 micron. The powder mixture was tape cast and heated at
850.degree. C. for 2 hr to form a hermetic LATP membrane with a
submicron average grain size. The composition of the LATP membrane
(in mol. %) was 0.175 Li.sub.2O--0.05 Al.sub.2O.sub.3--0.4
TiO.sub.2--0.375 P.sub.2O.sub.5.
[0046] Disclosed herein is a method for making dense, hermetic,
Li-ion conductive ceramic electrolyte membranes. Since a
homogeneous glass starting phase is not required, the method may be
applied to a much broader compositional space than is accessible
using conventional glass-ceramic processes. In addition, because
the reactant materials used typically have lower processing
temperatures compared to those used in the glass-ceramics route, a
lower cost process exhibiting better process control is achievable,
especially when volatile lithium phosphate species are present.
[0047] As used herein, the singular forms "a," "an" and "the"
include plural referents unless the context clearly dictates
otherwise. Thus, for example, reference to a "reactant" includes
examples having two or more such "reactants" unless the context
clearly indicates otherwise.
[0048] Ranges can be expressed herein as from "about" one
particular value, and/or to "about" another particular value. When
such a range is expressed, examples include from the one particular
value and/or to the other particular value. Similarly, when values
are expressed as approximations, by use of the antecedent "about,"
it will be understood that the particular value forms another
aspect. It will be further understood that the endpoints of each of
the ranges are significant both in relation to the other endpoint,
and independently of the other endpoint.
[0049] Unless otherwise expressly stated, it is in no way intended
that any method set forth herein be construed as requiring that its
steps be performed in a specific order. Accordingly, where a method
claim does not actually recite an order to be followed by its steps
or it is not otherwise specifically stated in the claims or
descriptions that the steps are to be limited to a specific order,
it is no way intended that any particular order be inferred.
[0050] It is also noted that recitations herein refer to a
component of the present invention being "configured" or "adapted
to" function in a particular way. In this respect, such a component
is "configured" or "adapted to" embody a particular property, or
function in a particular manner, where such recitations are
structural recitations as opposed to recitations of intended use.
More specifically, the references herein to the manner in which a
component is "configured" or "adapted to" denotes an existing
physical condition of the component and, as such, is to be taken as
a definite recitation of the structural characteristics of the
component.
[0051] It will be apparent to those skilled in the art that various
modifications and variations can be made to the present invention
without departing from the spirit and scope of the invention. Since
modifications combinations, sub-combinations and variations of the
disclosed embodiments incorporating the spirit and substance of the
invention may occur to persons skilled in the art, the invention
should be construed to include everything within the scope of the
appended claims and their equivalents.
* * * * *