U.S. patent application number 16/337653 was filed with the patent office on 2019-11-14 for heat pump apparatus.
The applicant listed for this patent is Mitsubishi Electric Corporation. Invention is credited to Taro HATTORI, Hirokazu MINAMISAKO, Kazutaka SUZUKI, Yasuhiro SUZUKI.
Application Number | 20190346191 16/337653 |
Document ID | / |
Family ID | 62491513 |
Filed Date | 2019-11-14 |





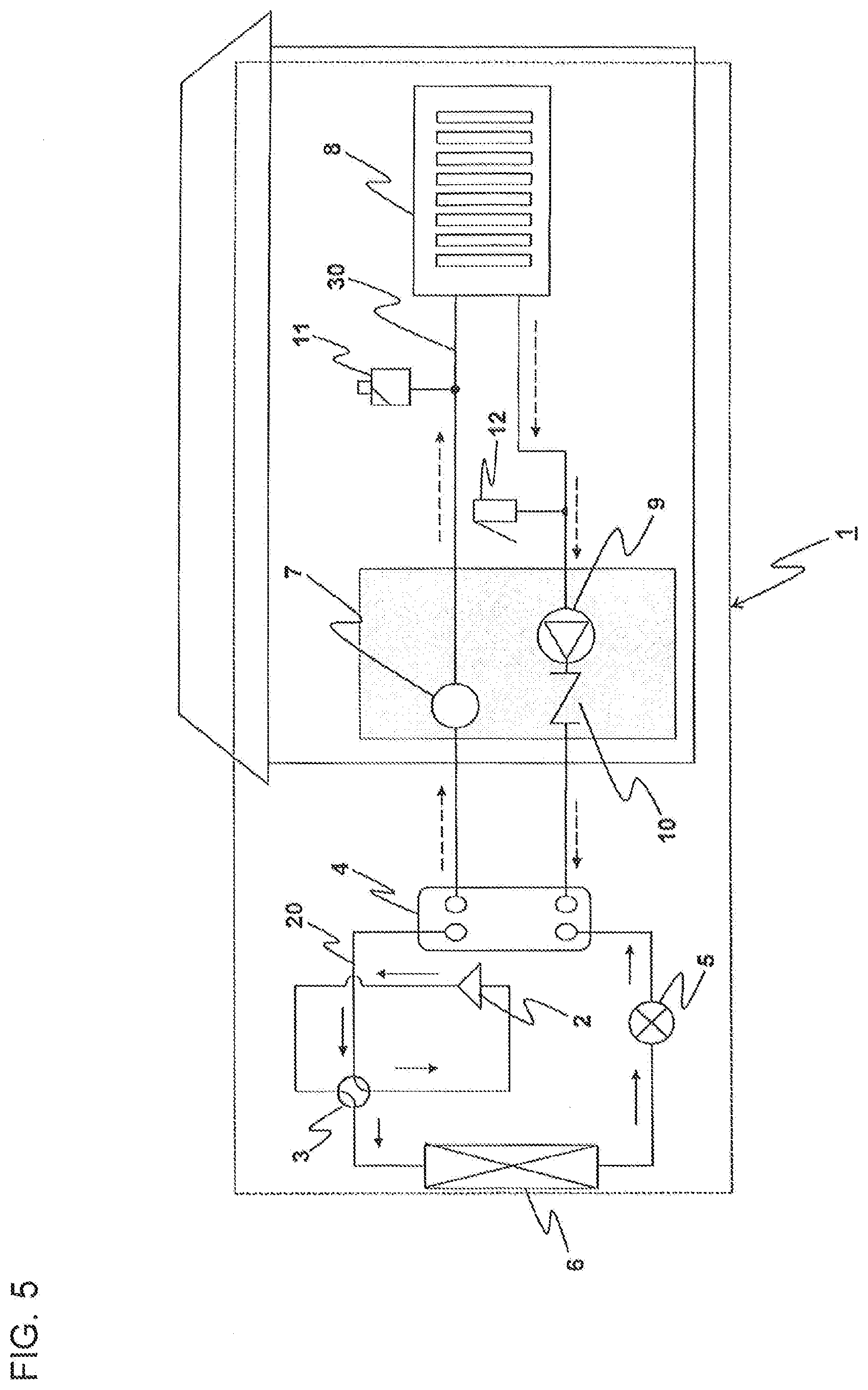



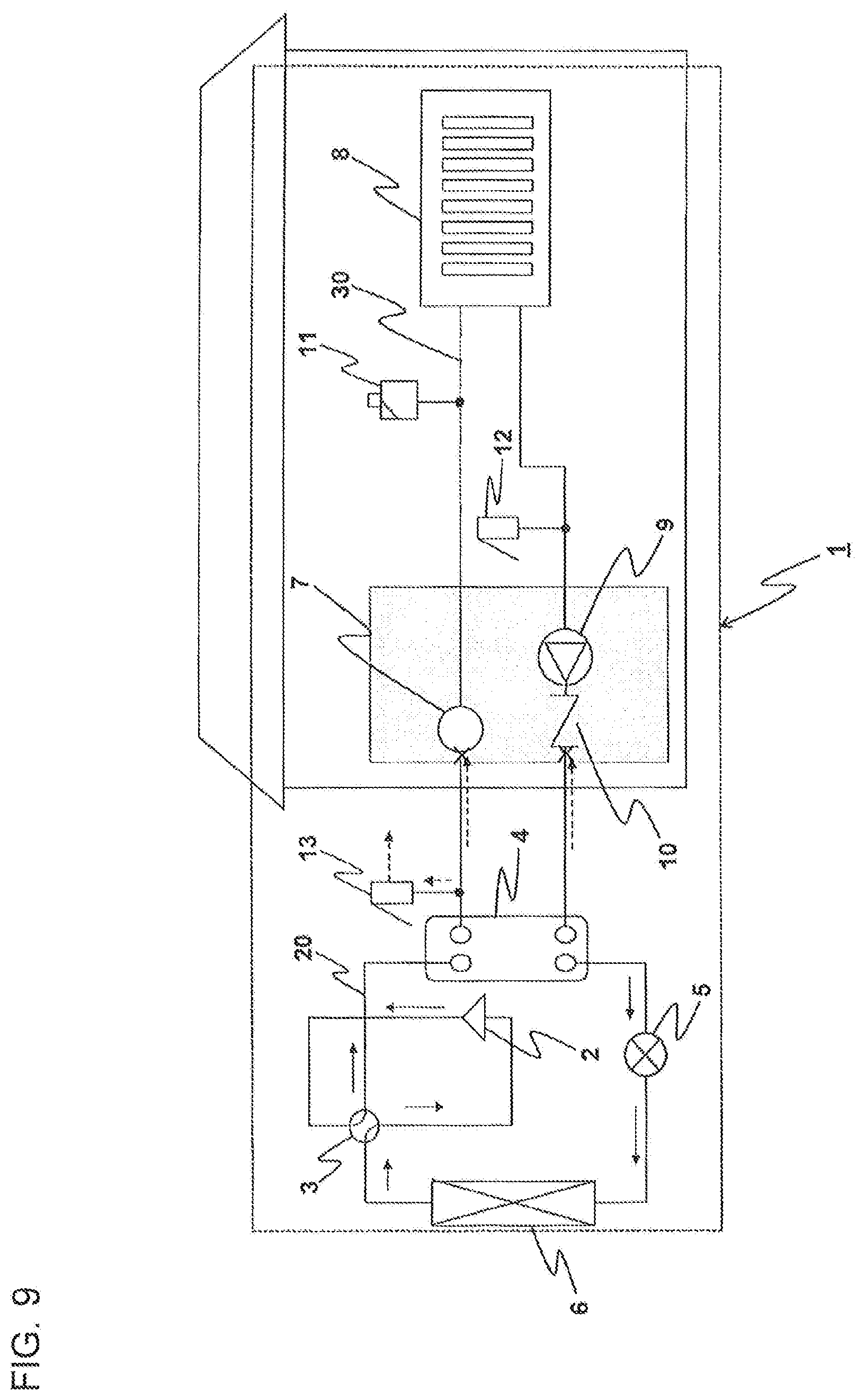
United States Patent
Application |
20190346191 |
Kind Code |
A1 |
MINAMISAKO; Hirokazu ; et
al. |
November 14, 2019 |
HEAT PUMP APPARATUS
Abstract
A heat pump apparatus includes: a refrigerant circuit, which is
configured to circulate refrigerant, and includes a compressor, a
heat source heat exchanger, an expansion mechanism, and an
intermediate heat exchanger which are sequentially connected
through a pipe; and a fluid circuit, which is configured to
circulate a fluid, and includes the intermediate heat exchanger, a
load heat exchanger, and a check valve which are sequentially
connected through a pipe. A pressure regulating valve is provided
to the heat pump apparatus. The pressure regulating valve is
connected to a pipe connecting an outlet of the intermediate heat
exchanger and an inlet of the load heat exchanger, and is
configured to interrupt a flow passage of the fluid when the
refrigerant leaks to the fluid, and pressure of the fluid is
increased.
Inventors: |
MINAMISAKO; Hirokazu;
(Tokyo, JP) ; SUZUKI; Yasuhiro; (Tokyo, JP)
; SUZUKI; Kazutaka; (Tokyo, JP) ; HATTORI;
Taro; (Tokyo, JP) |
|
Applicant: |
Name |
City |
State |
Country |
Type |
Mitsubishi Electric Corporation |
Tokyo |
|
JP |
|
|
Family ID: |
62491513 |
Appl. No.: |
16/337653 |
Filed: |
December 9, 2016 |
PCT Filed: |
December 9, 2016 |
PCT NO: |
PCT/JP2016/086735 |
371 Date: |
March 28, 2019 |
Current U.S.
Class: |
1/1 |
Current CPC
Class: |
F25B 41/04 20130101;
F25B 41/06 20130101; F25B 41/062 20130101; F25B 2500/22 20130101;
F24F 11/36 20180101; F25B 25/005 20130101; F25B 13/00 20130101;
F25B 2500/222 20130101; F25B 49/02 20130101 |
International
Class: |
F25B 49/02 20060101
F25B049/02; F25B 25/00 20060101 F25B025/00; F25B 41/04 20060101
F25B041/04 |
Claims
1. A heat pump apparatus comprising: a refrigerant circuit in which
refrigerant circulates, the refrigerant circuit being formed by
connecting in order, by pipes, a compressor, a heat source heat
exchanger, an expansion mechanism, and an intermediate heat
exchanger; a fluid circuit in which a fluid circulates, the fluid
circuit being formed by connecting in order, by pipes, the
intermediate heat exchanger, a load heat exchanger, and a check
valve; and a pressure regulating valve arranged in the fluid
circuit and connected to a pipe connecting an outlet of the
intermediate heat exchanger and an inlet of the load heat
exchanger, the pressure regulating valve being configured to
interrupt a flow passage of the fluid when the refrigerant leaks to
the fluid and pressure of the fluid is increased.
2. The heat pump apparatus of claim 1, wherein the pressure
regulating valve includes a flow part through which the fluid
flows, and a space that the fluid is prevented from flowing into,
an inner wall configured to partition an inflow side of the flow
part and an outflow side of the flow part, a diaphragm arranged on
the inflow side and configured to partition the space and the flow
passage, and to be deformed in accordance with the pressure, a
closing mechanism configured to be moved in association with the
deformation of the diaphragm to open and close an opening portion
formed in the inner wall; and a spring configured to deform the
diaphragm by applying a force to the diaphragm to move the closing
mechanism to a position at which the closing mechanism is prevented
from closing the opening portion, and wherein the spring is
configured to have a force set such that, under a state in which
the refrigerant is not leaking, the diaphragm is deformed against
the pressure of the fluid by the force, to prevent the opening
portion from being closed by the closing mechanism, and that, under
a state in which the refrigerant is leaking, the diaphragm is
deformed against the force, by the pressure of the fluid increased
due to leakage of the refrigerant so that the opening portion is
closed by the closing mechanism.
3. The heat pump apparatus of claim 2, wherein the closing
mechanism includes a shaft being a longitudinal member, inserted
through the opening portion while being supported by the diaphragm,
and arranged so that one distal end of the shaft is located on the
outflow side and an other distal end of the shaft is located in the
space; and a closing plate arranged on the one distal end of the
shaft, wherein the spring is wound around the shaft in the space,
wherein, under the state in which the refrigerant is not leaking,
the diaphragm is deformed in a direction toward the opening portion
by the force of the spring against the pressure of the fluid, and
the shaft is moved in association with the deformation of the
diaphragm so that the closing plate is located at a position away
from the opening portion, and wherein, under the state in which the
refrigerant is leaking, the diaphragm is deformed in a direction to
be away from the opening portion by the pressure of the fluid
increased due to the leakage of the refrigerant against the force
of the spring, and the shaft is moved in association with the
deformation of the diaphragm so that the closing plate is located
at a position at which the closing plate closes the opening
portion.
4. The heat pump apparatus of claim 1, further comprising an air
purge valve configured to exhaust air inside the fluid circuit to
an outside of the fluid circuit, and connected to a pipe branching
from the pipe connecting the outlet of the intermediate heat
exchanger and the inlet of the load heat exchanger, wherein the
pressure regulating valve is interposed between the outlet of the
intermediate heat exchanger and the air purge valve.
5. The heat pump apparatus of claim 1, further comprising a safety
valve configured to be opened when the pressure in the fluid
circuit is increased, and to exhaust the fluid to the outside of
the fluid circuit to prevent the increase of the pressure in the
fluid circuit, wherein the safety valve is connected to a pipe
branching from a portion between the check valve and the pressure
regulating valve in a circulating direction of the fluid which
flows from the check valve into an inlet of the intermediate heat
exchanger and reaches the pressure regulating valve through the
outlet of the intermediate heat exchanger, and wherein the safety
valve is configured to, when the refrigerant leaks to the fluid and
the pressure in the fluid circuit is increased, exhaust the fluid
including the refrigerant through the safety valve.
6. The heat pump apparatus of claim 5, wherein fluid interruption
pressure of the pressure regulating valve is set equal to or lower
than operating pressure of the safety valve.
7. The heat pump apparatus of claim 1, wherein the refrigerant
circulating through the refrigerant circuit is flammable, and the
fluid circulating through the fluid circuit is non-flammable.
Description
CROSS REFERENCE TO RELATED APPLICATION
[0001] This application is a U.S. national stage application of
International Application No. PCT/JP2016/086735, filed on Dec. 9,
2016, the contents of which are incorporated herein by
reference.
TECHNICAL FIELD
[0002] The present invention relates to a heat pump apparatus, and
more particularly, to leakage of refrigerant in the heat pump
apparatus.
BACKGROUND
[0003] Hitherto, there has been known a heat pump apparatus to be
used in an air-conditioning apparatus, a refrigeration apparatus,
or other similar apparatus. A heat pump apparatus described in
Patent Literature 1 includes a refrigerant circuit configured to
circulate refrigerant and a fluid circuit configured to circulate a
fluid. The refrigerant circuit includes a compressor, a heat source
heat exchanger, an expansion mechanism, and an intermediate heat
exchanger, which are sequentially connected through pipes to form a
circuit. The fluid circuit includes the intermediate heat
exchanger, a first valve, a load heat exchanger, and a second
valve, which are sequentially connected through pipes to form a
circuit. Further, in order to cope with leakage of the refrigerant,
the heat pump apparatus described in Patent Literature 1 includes a
leakage detection device configured to detect that the refrigerant
circulating through the refrigerant circuit is leaked from the
intermediate heat exchanger to the fluid, and a controller
configured to close the first valve and the second valve connected
to the fluid circuit when the leakage detection device detects the
leakage of the refrigerant. In the heat pump apparatus, when the
refrigerant is leaked from the refrigerant circuit to the fluid
circuit, the first valve and the second valve are closed by the
controller, thereby preventing the refrigerant thus leaked from
flowing beyond the first valve and the second valve.
PATENT LITERATURE
[0004] Patent Literature 1: International Patent WO 2013/038577
A1
[0005] In the heat pump apparatus in Patent Literature 1, both of
the leakage detection device and the controller configured to close
the first valve and the second valve use electric power as a power
source, and cannot be operated under a state in which the electric
power is not supplied. However, even under a state in which the
electric power is not supplied so that the leakage detection device
and the controller are shut down, there is a risk of causing
breakage of the intermediate heat exchanger due to corrosion and
breakage of the intermediate heat exchanger due to freezing caused
by temperature decrease. In such a case, the leakage of the
refrigerant cannot be detected, and further, there is a risk in
that the refrigerant thus leaked cannot be prevented from flowing
beyond the first valve and the second valve. As a result, there is
a risk in that the refrigerant may be leaked to an indoor space in
which the load heat exchanger of the fluid circuit is arranged.
SUMMARY
[0006] The present invention has been made to overcome the problem
described above, and an object of the present invention is to
provide a heat pump apparatus capable of preventing leakage of
refrigerant to an indoor space even when the refrigerant is leaked
under a state in which electric power is not supplied.
[0007] According to one embodiment of the present invention, there
is provided a heat pump apparatus, including: a refrigerant circuit
in which refrigerant circulates, the refrigerant circuit being
formed by connecting in order, by pipes, a compressor, a heat
source heat exchanger, an expansion mechanism, and an intermediate
heat exchanger; a fluid circuit in which a fluid circulates, the
fluid circuit being formed by connecting in order, by pipes, the
intermediate heat exchanger, a load heat exchanger, and a check
valve; and a pressure regulating valve arranged in the fluid
circuit and connected to a pipe connecting an outlet of the
intermediate heat exchanger and an inlet of the load heat
exchanger, the pressure regulating valve being configured to
interrupt a flow passage of the fluid when the refrigerant leaks to
the fluid and pressure of the fluid is increased.
[0008] In the heat pump apparatus according to one embodiment of
the present invention, the pressure regulating valve is configured
to interrupt the flow passage of the fluid when the refrigerant
leaks to the fluid circulating through the fluid circuit, and the
pressure of the fluid is increased. The pressure regulating valve
is connected to the pipe connecting the outlet of the intermediate
heat exchanger and the inlet of the load heat exchanger. Therefore,
even under a state in which the electric power is not supplied to
the heat pump apparatus, in the intermediate heat exchanger, the
refrigerant leaking to the fluid can be prevented from reaching the
load heat exchanger. As a result, the leakage of the refrigerant to
the indoor space can be prevented.
BRIEF DESCRIPTION OF DRAWINGS
[0009] FIG. 1 is a schematic diagram of configuration of an
air-conditioning apparatus of Embodiment 1 of the present
invention.
[0010] FIG. 2 is a schematic diagram of configuration of a pressure
regulating valve of Embodiment 1.
[0011] FIG. 3 is a diagram for illustrating flows of refrigerant
and water in the air-conditioning apparatus of Embodiment 1 during
a heating operation.
[0012] FIG. 4 is a diagram for illustrating an operation of the
pressure regulating valve of Embodiment 1 during the heating
operation.
[0013] FIG. 5 is a diagram for illustrating the flows of the
refrigerant and the water in the air-conditioning apparatus of
Embodiment 1 during a cooling operation.
[0014] FIG. 6 is a diagram for illustrating the flows of the
refrigerant and the water when the refrigerant is leaked in the
air-conditioning apparatus of Embodiment 1 during the heating
operation.
[0015] FIG. 7 is a diagram for illustrating an operation of the
pressure regulating valve of Embodiment 1 when the refrigerant is
leaked during the heating operation.
[0016] FIG. 8 is a schematic diagram of configuration of an
air-conditioning apparatus of Embodiment 2 of the present
invention.
[0017] FIG. 9 is a diagram for illustrating the flows of the
refrigerant and the water when the refrigerant is leaked in the
air-conditioning apparatus of Embodiment 2 during the heating
operation.
DETAILED DESCRIPTION
[0018] Now, heat pump apparatus according to embodiments of the
present invention are described in detail by referring to the
drawings. Note that, the present invention is not limited to the
embodiments described below. Moreover, in the drawings referred to
below, sizes of components may be different from the reality in
some cases.
Embodiment 1
[0019] FIG. 1 is a schematic diagram of configuration of an
air-conditioning apparatus of Embodiment 1 of the present
invention. An air-conditioning apparatus 1 includes a refrigerant
circuit 20 including a compressor 2, a four-way valve 3, a heat
source heat exchanger 6, an expansion valve 5, and an intermediate
heat exchanger 4, which are sequentially connected through pipes to
form a circuit. Further, the air-conditioning apparatus 1 includes
a water circuit 30 including the intermediate heat exchanger 4, a
pressure regulating valve 7, a load heat exchanger 8, a pump 9, and
a check valve 10, which are sequentially connected through pipes to
form a circuit. A flammable refrigerant such as the R32 refrigerant
or propane is circulating through the refrigerant circuit 20, and
water is circulating through the water circuit 30. In the water
circuit 30, an air purge valve 11 is connected to a pipe branching
from a pipe connecting the pressure regulating valve 7 and the load
heat exchanger 8, and a load safety valve 12 is connected to a pipe
branching from a pipe connecting the load heat exchanger 8 and the
pump 9.
[0020] The load heat exchanger 8 is installed in an indoor space
being a target to be air-conditioned. In the water circuit 30, the
pressure regulating valve 7 is connected to a pipe connecting an
outlet of the intermediate heat exchanger 4 and an inlet of the
load heat exchanger 8. The check valve 10 is a valve configured to
allow water to flow from the pump 9 to the intermediate heat
exchanger 4 in the water circuit 30, and to inhibit water from
flowing from the intermediate heat exchanger 4 to the pump 9 in the
water circuit 30.
[0021] The check valve 10 is connected in the water circuit 30 to a
pipe connecting an outlet of the load heat exchanger 8 and an inlet
of the intermediate heat exchanger 4. The air purge valve 11 is a
valve configured to exhaust air generated in or mixed into the
water circuit 30 to the outside, and to prevent idle running of the
pump 9. In order to exhaust the air efficiently, the air purge
valve 11 is connected to a pipe branching from a pipe located at an
upper most position in the water circuit 30. The load safety valve
12 is a valve configured to drain the water to suppress pressure
increase when pressure in the water circuit 30 is increased.
Therefore, the load safety valve 12 is connected to a pipe, which
is branched from the vicinity of an inflow side of the pump 9, so
as not to be operated by an influence of pressure increase in the
pump 9. That is, the air purge valve 11 and the load safety valve
12 are installed in the indoor space. In order to exchange heat
between the air and the refrigerant, the heat source heat exchanger
6 is accommodated in an outdoor unit installed in an outdoor
space.
(Configuration of Pressure Regulating Valve 7)
[0022] FIG. 2 is a schematic diagram of configuration of the
pressure regulating valve of Embodiment 1. Referring to FIG. 2, a
configuration of the pressure regulating valve 7 of Embodiment 1 is
described. The pressure regulating valve 7 is a valve which is
usable only in one direction, and has one inlet and one outlet. The
pressure regulating valve 7 has a machine space 7A being a space
that water does not flow into, and a water flow part 7B through
which water flows. Further, the pressure regulating valve 7
includes a diaphragm 71, a shaft 72, a coil spring 73, a closing
plate 74, and an inner wall 75.
[0023] The inner wall 75 is configured to partition an inlet-side
water flow part 7BA corresponding to an inflow side of the water
flow part 7B, and an outlet-side water flow part 7BB corresponding
to an outflow side of the water flow part 7B. An opening portion
75A is formed in the inner wall 75. The diaphragm 71 is arranged in
the inlet-side water flow part 7BA, and is configured to partition
the machine space 7A and the water flow part 7B. The diaphragm 71
is a member which is deformable in an up-and-down direction in FIG.
2 in accordance with pressure. The shaft 72 is a longitudinal
member inserted through the opening portion 75A of the inner wall
75 while being supported by the diaphragm 71. The shaft 72 is
arranged so that one distal end thereof is located in the
outlet-side water flow part 7BB and an other distal end thereof is
located in the machine space 7A. The closing plate 74 is arranged
on an end portion of the shaft 72, which is located in the
outlet-side water flow part 7BB. An end portion of the shaft 72,
which is located in the machine space 7A, is received in a
receiving portion 7C formed in the machine space 7A. The closing
plate 74 has an area larger than an opening area of the opening
portion 75A.
[0024] In the machine space 7A, the coil spring 73 being a spring
member is wound around the shaft 72. One end portion of the coil
spring 73 is fixed to an inner peripheral surface of the pressure
regulating valve 7, which forms the machine space 7A, and an other
end portion thereof is fixed to the diaphragm 71. The coil spring
73 urges the diaphragm 71 in a downward direction. The shaft 72 is
moved in an upward direction against the force of the coil spring
73. With this, the opening portion 75A of the inner wall 75 is
closed by the closing plate 74, and a flow passage connecting the
inlet-side water flow part 7BA and the outlet-side water flow part
7BB is interrupted. In Embodiment 1, the shaft 72 and the closing
plate 74 correspond to a closing mechanism.
[0025] When the water is circulating through the water circuit 30,
the water flows from an inlet of the pressure regulating valve 7
toward an outlet thereof. At this time, a force in the upward
direction is applied to the diaphragm 71 due to water pressure.
That is, when the water is circulating through the water circuit
30, the force of the coil spring 73 in the downward direction is
applied to the diaphragm 71, and the force in the upward direction
due to the water pressure is also applied to the diaphragm 71.
Therefore, the diaphragm 71 is deformed in an applying direction of
a force, which is greater of the force due to the water pressure
and the force of the coil spring 73. In Embodiment 1, as the coil
spring 73, there is selected a spring having a spring coefficient
large enough to push down the shaft 72 in the downward direction
against the water pressure to prevent the closing plate 74 from
closing the opening portion 75A of the inner wall 75 and
interrupting the flow passage of the water during a heating
operation, a cooling operation, and a defrosting operation at a
normal time during which the refrigerant is not leaked to the water
circuit 30. Therefore, as illustrated in FIG. 2, by the force of
the coil spring 73, the diaphragm 71 is deformed against the water
pressure in the downward direction, that is, in a direction toward
the opening portion 75A of the inner wall 75. In association with
the deformation of the diaphragm 71, the shaft 72 is moved in the
downward direction, and the closing plate 74 is located at a
position away from the opening portion 75A.
(Heating Operation)
[0026] Referring to FIG. 3, an operation during the heating
operation, which relates to Embodiment 1, is described. FIG. 3 is a
diagram for illustrating flows of refrigerant and water in the
air-conditioning apparatus of Embodiment 1 during the heating
operation. In FIG. 3, solid arrows indicate the flow of the
refrigerant, and broken arrows indicate the flow of the water.
During the heating operation of the air-conditioning apparatus 1,
in the refrigerant circuit 20, refrigerant compressed into a
high-temperature, high-pressure state by the compressor 2 passes
through the four-way valve 3 and flows into the intermediate heat
exchanger 4. The refrigerant flowing into the intermediate heat
exchanger 4 is subjected to heat exchange with water circulating
through the water circuit 30, and is condensed into liquid
refrigerant. At this time, the water circulating through the water
circuit 30 is heated. The liquid refrigerant passes through the
expansion valve 5 and is expanded into low-temperature and
low-pressure two-phase gas-liquid refrigerant. The two-phase
gas-liquid refrigerant flows into the heat source heat exchanger 6,
and is subjected to heat exchange with outdoor air to be evaporated
into gas refrigerant. The gas refrigerant passes through the
four-way valve 3, and is sucked into the compressor 2 again to be
compressed into a high-temperature, high-pressure state.
[0027] Meanwhile, in the water circuit 30, the high-temperature
water heated in the intermediate heat exchanger 4 passes through
the pressure regulating valve 7, and flows into the load heat
exchanger 8. The high-temperature water flowing into the load heat
exchanger 8 is subjected to heat exchange with indoor air to be
cooled. At this time, the indoor air is heated. The cooled water
sequentially passes through the pump 9 and the check valve 10 and
flows into the intermediate heat exchanger 4 again.
[0028] An operation of the pressure regulating valve 7 during the
heating operation is described. FIG. 4 is a diagram for
illustrating the operation of the pressure regulating valve of
Embodiment 1 during the heating operation. As described above, the
coil spring 73 of the pressure regulating valve 7 has a spring
coefficient large enough to push down the shaft 72 in the downward
direction against the water pressure to prevent the closing plate
74 from interrupting the flow passage of the water due to the
pressure of the water passing through the pressure regulating valve
7. Therefore, during the heating operation, the coil spring 73 of
the pressure regulating valve 7 pushes down the diaphragm 71, and
pushes down the shaft 72 and the closing plate 74. As a result, in
the pressure regulating valve 7, the flow passage is formed between
the inlet-side water flow part 7BA and the outlet-side water flow
part 7BB, and the high-temperature water flowing into the pressure
regulating valve 7 through the inlet flows out therefrom through
the outlet.
(Cooling Operation)
[0029] Referring to FIG. 5, an operation during the cooling
operation, which relates to Embodiment 1, is described. FIG. 5 is a
diagram for illustrating the flows of the refrigerant and the water
in the air-conditioning apparatus of Embodiment 1 during the
cooling operation. In FIG. 5, solid arrows indicate the flow of the
refrigerant, and broken arrows indicate the flow of the water.
During the cooling operation, in the refrigerant circuit 20,
refrigerant compressed into a high-temperature, high-pressure state
by the compressor 2 passes through the four-way valve 3 and flows
into the heat source heat exchanger 6. The refrigerant flowing into
the heat source heat exchanger 6 is subjected to heat exchange with
air to be turned into liquid refrigerant. The liquid refrigerant
passes through the expansion valve 5 and is expanded into
low-temperature and low-pressure two-phase gas-liquid refrigerant.
The two-phase gas-liquid refrigerant flows into the intermediate
heat exchanger 4, and is subjected to heat exchange with water to
be evaporated into gas refrigerant. At this time, the water
circulating through the water circuit 30 is cooled. The gas
refrigerant passes through the four-way valve 3, and is sucked into
the compressor 2 again to be compressed into a high-temperature,
high-pressure state.
[0030] Meanwhile, in the water circuit 30, the low-temperature
water cooled in the intermediate heat exchanger 4 passes through
the pressure regulating valve 7, and flows into the load heat
exchanger 8. The low-temperature water flowing into the load heat
exchanger 8 is subjected to heat exchange with the indoor air to be
heated. At this time, the indoor air is cooled. The heated water
sequentially passes through the pump 9 and the check valve 10 and
flows into the intermediate heat exchanger 4 again.
[0031] An operation of the pressure regulating valve 7 during the
cooling operation is described. Similarly to the case during the
heating operation, as illustrated in FIG. 4, in the pressure
regulating valve 7, the flow passage is formed between the machine
space 7A and the water flow part 7B, and the low-temperature water
flowing into the pressure regulating valve 7 through the inlet
flows out therefrom through the outlet.
(Defrosting Operation)
[0032] An operation of the air-conditioning apparatus 1 of
Embodiment 1 during the defrosting operation is described. The
defrosting operation is executed when frost is formed on the heat
source heat exchanger 6 by the heating operation. The operation
during the defrosting operation is similar to the operation during
the cooling operation. That is, as illustrated in FIG. 5, in the
refrigerant circuit 20, the refrigerant compressed into a
high-temperature, high-pressure state by the compressor 2 passes
through the four-way valve 3, and flows into the heat source heat
exchanger 6. The frost formed on the heat source heat exchanger 6
is melted and removed by the high-temperature and high-pressure
refrigerant flowing into the heat source heat exchanger 6. The
other operation is similar to the operation during the cooling
operation.
(When Refrigerant is Leaked)
[0033] As described above, during the cooling operation and the
defrosting operation, the low-temperature refrigerant flows into
the intermediate heat exchanger 4, and cools the water flowing
through the intermediate heat exchanger 4. Therefore, depending on
circumstances, the water flowing through the intermediate heat
exchanger 4 may be frozen, and there is a risk in that the
intermediate heat exchanger 4 may be broken due to cubical
expansion of the water caused by the freezing. Further, there is a
risk in that fatigue fracture caused by the pressure increase may
occur in the intermediate heat exchanger 4 due to the breakage
caused by abnormal increase of pressure of the refrigerant or as a
result of repetitive operations. Further, thinning of the
intermediate heat exchanger 4 caused by corrosion of components of
the intermediate heat exchanger 4 may lead to decrease in strength
of the intermediate heat exchanger 4, and there is also a risk in
that the breakage of the intermediate heat exchanger 4 may be
promoted.
[0034] When the intermediate heat exchanger 4 is broken, due to a
difference in pressure between the refrigerant flowing through the
refrigerant circuit 20 and the water flowing through the water
circuit 30, the refrigerant is mixed into the water circuit 30.
When the refrigerant is mixed into the water circuit 30, the
refrigerant is gasified due to an effect of pressure reduction,
thereby causing increase of the pressure in the water circuit 30.
When the pressure in the water circuit 30 is increased, the water
is drained through the load safety valve 12 mounted in the water
circuit 30. At this time, through the drainage of water, the
refrigerant mixed into the water inside the water circuit 30 is
exhausted to the indoor space. As a result, a flammable region is
formed, and when the flammable region reaches an ignition source,
there is a risk of causing ignition. Similarly, the gasified
refrigerant mixed into the water circuit 30 is exhausted through
the air purge valve 11 and forms the flammable region, with the
result that there is a risk of causing ignition. However, in
Embodiment 1, the pressure regulating valve 7 is provided. Thus,
the refrigerant is prevented from being exhausted to the indoor
space and forming the flammable region.
[0035] Now, an operation of the pressure regulating valve 7 of
Embodiment 1 when the refrigerant is leaked is described. FIG. 6 is
a diagram for illustrating the flows of the refrigerant and the
water when the refrigerant is leaked in the air-conditioning
apparatus of Embodiment 1 during the heating operation. FIG. 7 is a
diagram for illustrating an operation of the pressure regulating
valve of Embodiment 1 when the refrigerant is leaked during the
heating operation. When the refrigerant is leaked, the refrigerant
leaks to the water circulating through the water circuit 30. With
this, the water pressure of the water flowing into the pressure
regulating valve 7 through the inlet thereof is increased to be
greater than the force of the coil spring 73 of the pressure
regulating valve 7. As a result, the diaphragm 71 is deformed
upward, that is, in a direction to be away from the opening portion
75A of the inner wall 75 against the force of the coil spring 73.
The shaft 72 is moved in association with the deformation of the
diaphragm 71. With this, as illustrated in FIG. 7, the closing
plate 74 is located at a position at which the closing plate 74
closes the opening portion 75A. When the opening portion 75A of the
inner wall 75 is closed by the closing plate 74, in the pressure
regulating valve 7, the flow passage from the inlet-side water flow
part 7BA to the outlet-side water flow part 7BB is interrupted,
thereby preventing the water, which flows into the pressure
regulating valve 7 through the inlet thereof, from flowing out of
the pressure regulating valve 7 through the outlet thereof.
Further, the flow passage is interrupted so that the water pressure
applied to the inlet of the pressure regulating valve 7 is further
increased, thereby also increasing the pressure of pressing the
closing plate 74 against a peripheral edge of the opening portion
75A of the inner wall 75 by the diaphragm 71 and the shaft 72. As a
result, an amount of the refrigerant leaking to the water
circulating through the water circuit 30 is reduced.
[0036] As described above, in Embodiment 1, the pressure regulating
valve 7 is configured to be operated when the water pressure is
increased due to the leakage of the refrigerant to the water
circulating through the water circuit 30. Therefore, even under a
state in which electric power is not supplied to the
air-conditioning apparatus 1, when a situation of leakage of the
refrigerant occurs, the flow passage in the water circuit 30 is
interrupted by the pressure regulating valve 7, thereby preventing
the leakage of the refrigerant to the indoor space.
[0037] Further, in the air-conditioning apparatus described in
Patent Literature 1, a time period is required from detection by a
leakage detection device to interruption by a first valve and a
second valve. Therefore, there is a risk in that the refrigerant
thus leaked may flow further beyond the first valve and the second
valve. As a result, there is a risk in that the refrigerant may be
leaked to the indoor space in which a load heat exchanger of a
fluid circuit is arranged. On the other hand, according to
Embodiment 1, the pressure regulating valve 7 is operated in
response to the increase in water pressure caused by the leakage of
the refrigerant. Thus, the flow passage can be interrupted in a
short period of time. Therefore, the amount of the refrigerant
leaking to the water circuit 30 can be reduced.
[0038] The pressure regulating valve 7 is interposed at the pipe
connecting the outlet of the intermediate heat exchanger 4 and the
inlet of the load heat exchanger 8 at a portion between the outlet
of the intermediate heat exchanger 4 and the air purge valve 11.
Therefore, the refrigerant leaking to the water inside the water
circuit 30 is prevented from reaching the air purge valve 11. As a
result, the leakage of the refrigerant to the indoor space is
prevented.
[0039] Further, through interruption of the flow passage of the
water in the pressure regulating valve 7, the flow of the water in
the water circuit 30 is stopped, and the check valve 10 is set to a
closed state. As a result, the refrigerant leaked from the
intermediate heat exchanger 4 and flowing into the water circuit 30
is prevented from flowing from the pressure regulating valve 7 and
the check valve 10 to a side on which the load heat exchanger 8 is
located, thereby preventing the refrigerant from reaching the air
purge valve 11 and preventing the refrigerant from reaching the
load safety valve 12. Therefore, the leakage of the refrigerant to
the indoor space can be prevented. Further, the pressure increase
of the water flowing through the load heat exchanger 8, pipes
extending throughout the indoor space, and welding portions of the
pipes can be prevented. Therefore, the water including the
refrigerant can be prevented from leaking exceeding the pressure
resistance of the load heat exchanger 8, the pipes in the indoor
space, and the welding portions of the pipes.
Embodiment 2
[0040] FIG. 8 is a schematic diagram of configuration of an
air-conditioning apparatus of Embodiment 2 of the present
invention. Embodiment 2 is different from Embodiment 1 in that an
outdoor-space safety valve 13 is connected to a pipe branching from
a pipe connecting the intermediate heat exchanger 4 and the
pressure regulating valve 7. Operating pressure, that is, valve
opening pressure of the outdoor-space safety valve 13 is equal to
or higher than operating pressure of the closing plate 74 of the
pressure regulating valve 7, that is, fluid interruption pressure
of the pressure regulating valve 7. In other words, the fluid
interruption pressure of the pressure regulating valve 7 is equal
to or lower than the operating pressure of the outdoor-space safety
valve 13. It is desired that the valve opening pressure of the
outdoor-space safety valve 13 be higher than the operating pressure
of the closing plate 74. Further, it is desired that the
outdoor-space safety valve 13 and a drain outlet extending from the
outdoor-space safety valve 13 be installed in an open space such as
an open-air space or a room having a large floor area.
[0041] In Embodiment 2, a heating operation, a cooling operation,
and a defrosting operation are executed in a manner similar to
those in Embodiment 1 described above, and hence description
thereof is omitted. An operation of the air-conditioning apparatus
1 of Embodiment 2 when the refrigerant is leaked from the
intermediate heat exchanger 4 to the water circuit 30 is described.
FIG. 9 is a diagram for illustrating the flows of the refrigerant
and the water when the refrigerant is leaked in the
air-conditioning apparatus of Embodiment 2 during the heating
operation. In FIG. 9, solid arrows indicate the flow of the
refrigerant, and broken arrows indicate the flow of the water. When
the refrigerant is leaked from the intermediate heat exchanger 4 to
the water circuit 30, and the pressure of the water circulating
through the water circuit 30 is increased, the pressure regulating
valve 7 is operated to interrupt the flow passage of the water.
Such an operation is similar to the operation in Embodiment 1
described above. In Embodiment 2, after the leakage of the
refrigerant, when the pressure increase of the water inside the
water circuit 30 is continued so that the pressure of the water
inside the water circuit 30 exceeds the operating pressure of the
outdoor-space safety valve 13, the outdoor-space safety valve 13
releases the water and the refrigerant to the open space. Then, the
pressure in the water circuit 30 is gradually reduced. Through the
reduction of the pressure in the water circuit 30, the
outdoor-space safety valve 13 is closed, and the release of the
water and the refrigerant to the open space is stopped.
[0042] According to Embodiment 2, the outdoor-space safety valve 13
is provided on the pipe branching from the pipe connecting the
intermediate heat exchanger 4 and the pressure regulating valve 7.
Therefore, it is possible to prevent the refrigerant flowing into
the water circuit 30 through the broken part of the intermediate
heat exchanger 4 from reaching the indoor space, and to prevent the
increase of the pressure applied to the pipe connecting the check
valve 10 and the intermediate heat exchanger 4 and the pipe
connecting the intermediate heat exchanger 4 and the pressure
regulating valve 7. Further, when the refrigerant is leaked, the
increase of the pressure applied to those pipes is prevented. Thus,
components having low resistance to back pressure can be used for
the pressure regulating valve 7, the check valve 10, and the pipe
connecting each of the pressure regulating valve 7 and the check
valve 10 to the intermediate heat exchanger 4. That is, components
having special specification do not need to be prepared for the
pressure regulating valve 7, the check valve 10, and the pipe
connecting each of the pressure regulating valve 7 and the check
valve 10 to the heat exchanger 4. Thus, this configuration is
economical.
* * * * *