U.S. patent application number 16/393105 was filed with the patent office on 2019-10-31 for interference monitoring device.
The applicant listed for this patent is FANUC CORPORATION. Invention is credited to Yasuhito ISHIKAWA.
Application Number | 20190332083 16/393105 |
Document ID | / |
Family ID | 68205714 |
Filed Date | 2019-10-31 |


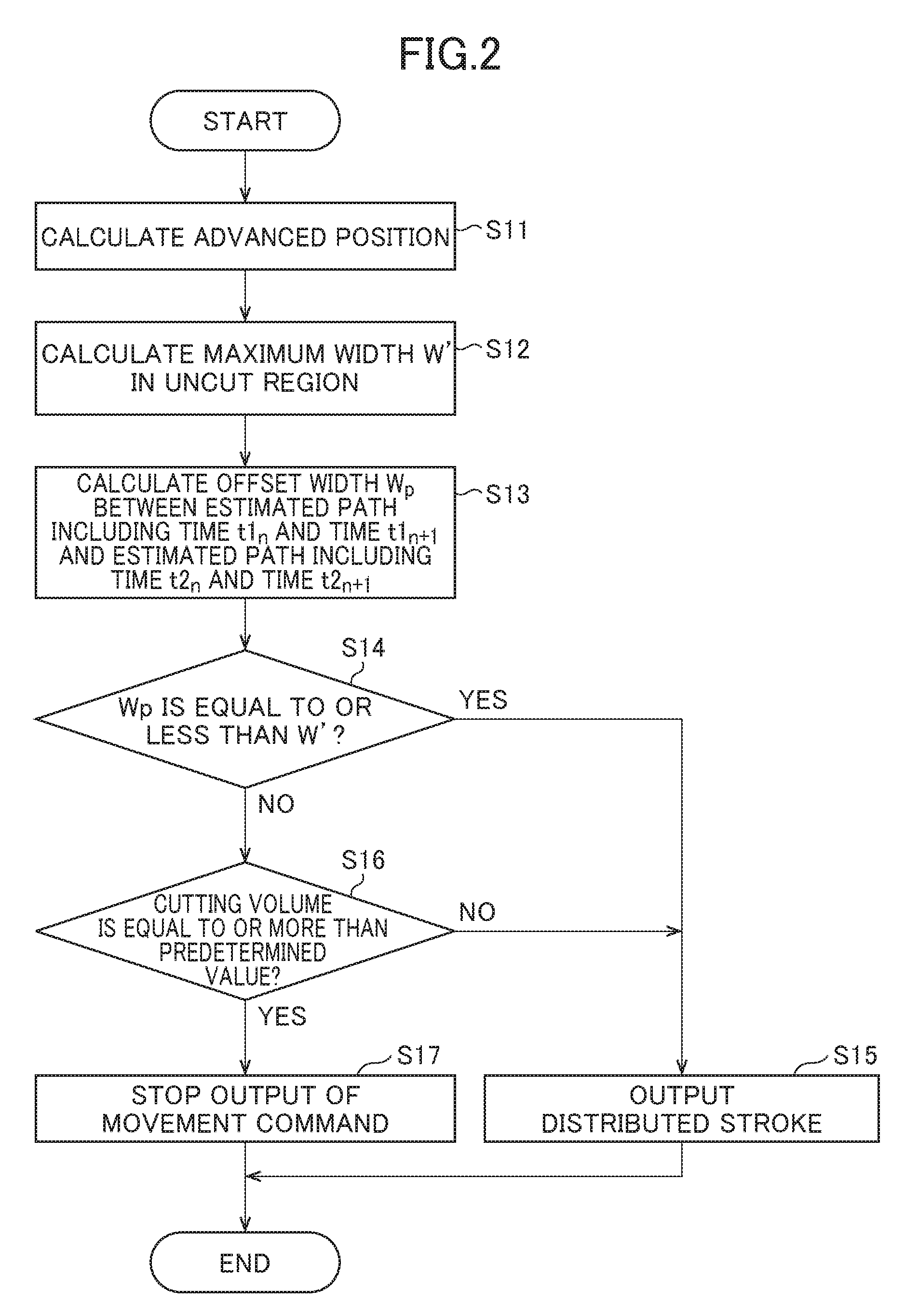

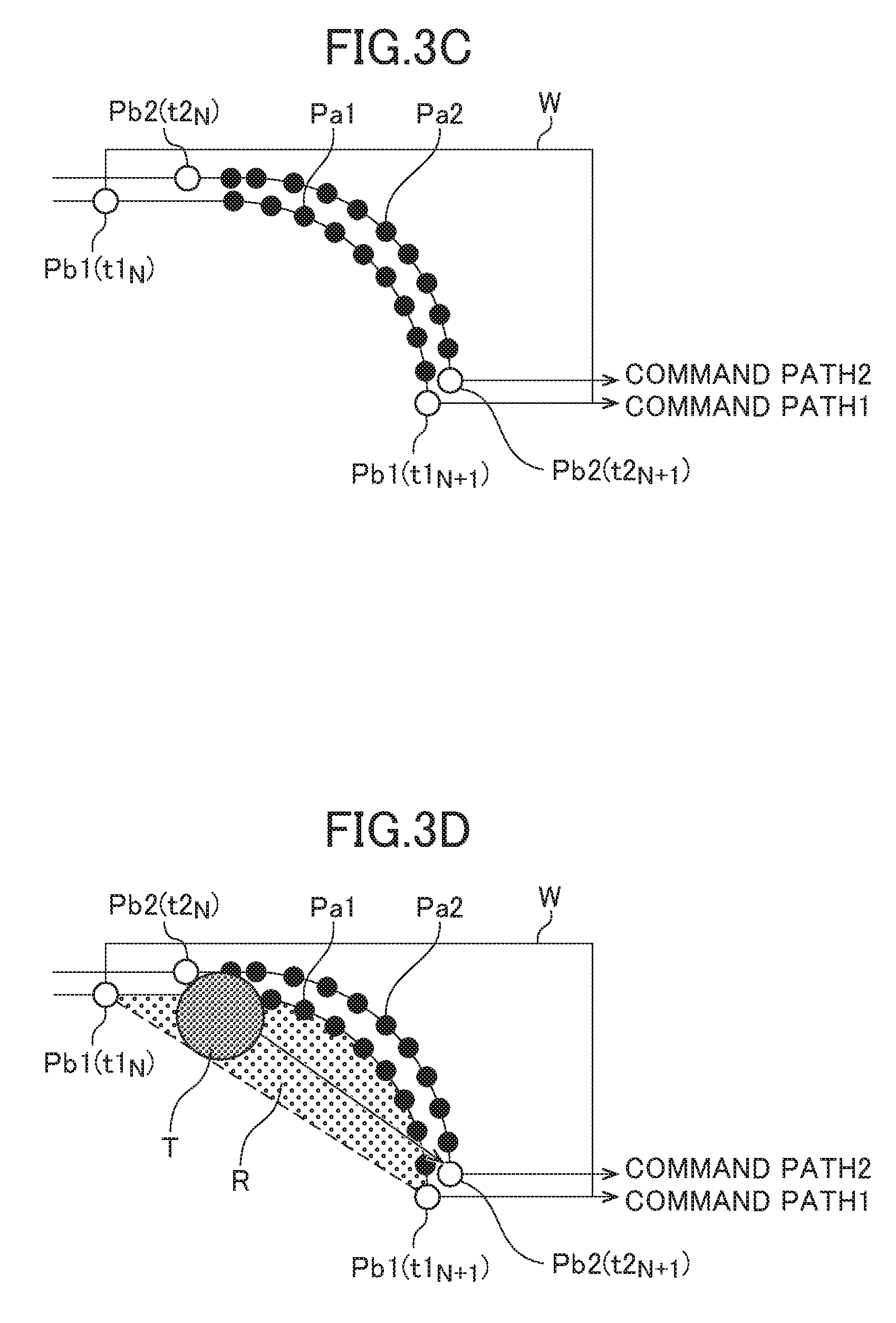


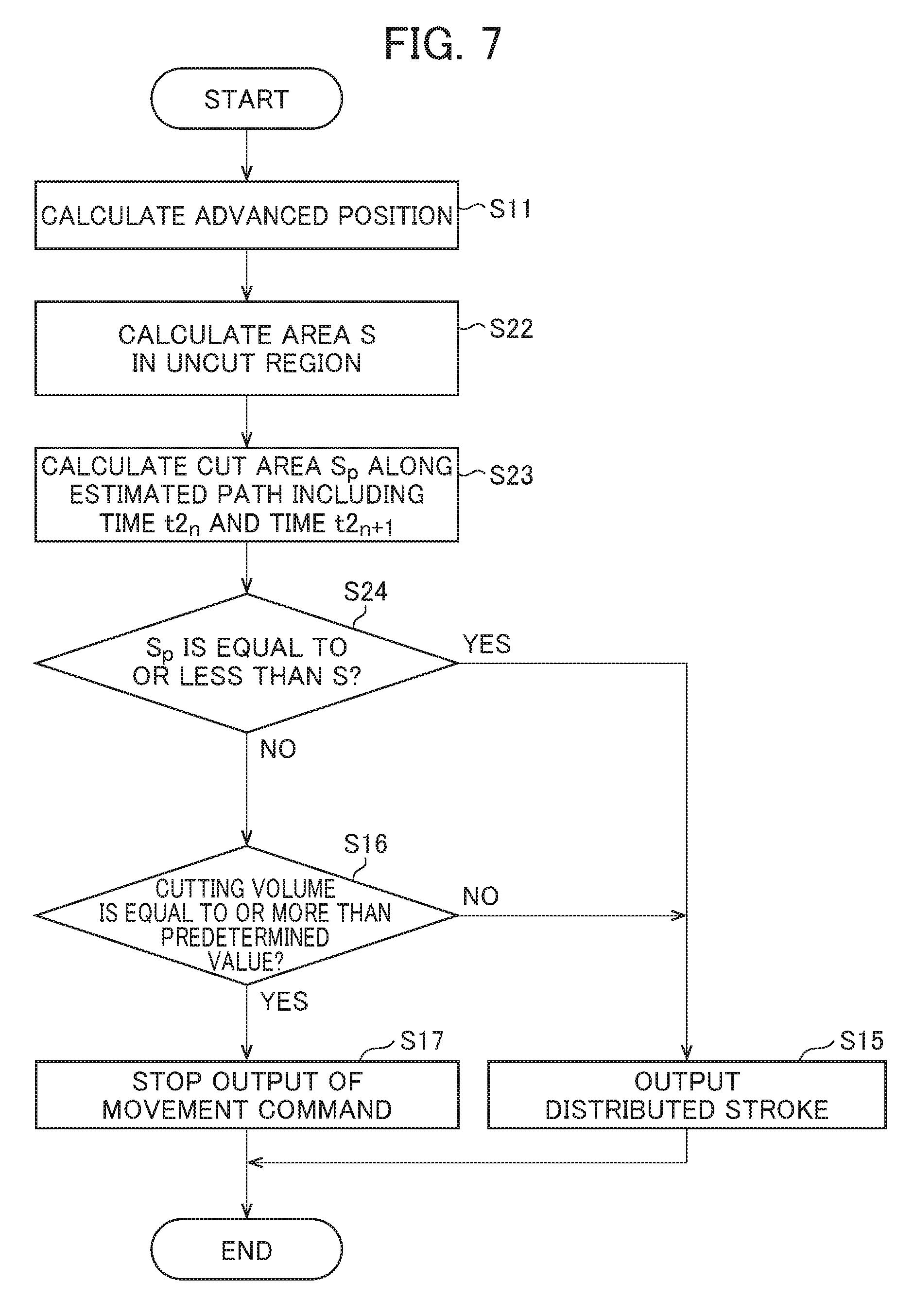
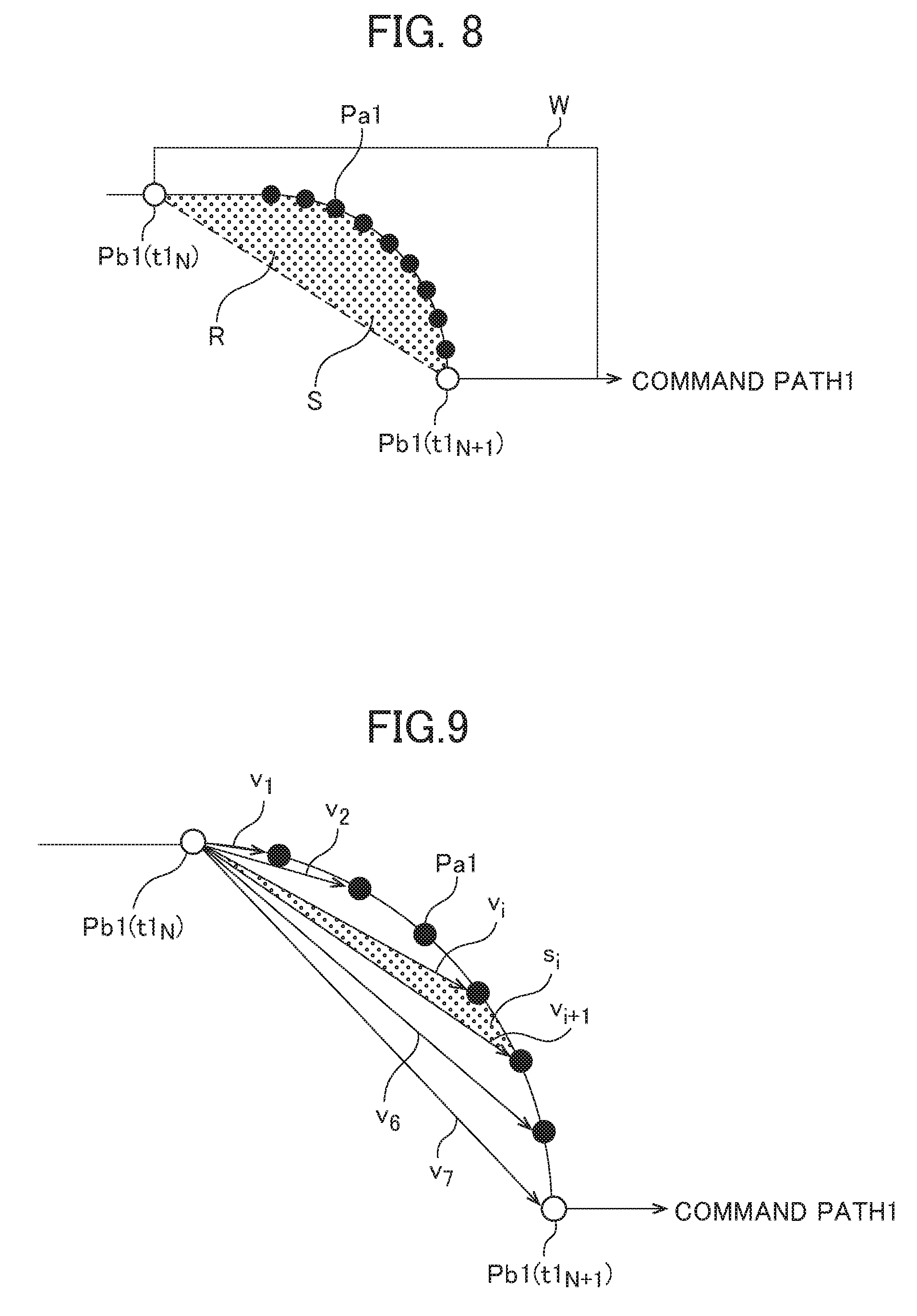

United States Patent
Application |
20190332083 |
Kind Code |
A1 |
ISHIKAWA; Yasuhito |
October 31, 2019 |
INTERFERENCE MONITORING DEVICE
Abstract
The interference monitoring device comprises: an advanced
position calculation unit that calculates an advanced position of
the tool or the workpiece ahead by a predetermined period of time
based on the program; an interference check unit that draws an
estimated shape of a machined part of the workpiece after machining
based on the advanced position, and makes the interference check
based on the estimated shape of the machined part of the workpiece
in the drawing; and an uncut region calculation unit that
calculates an error between the estimated shape of the machined
part of the workpiece in the drawing and an actual shape of the
machined part of the workpiece after machining as an uncut region
in the estimated shape of the machined part of the workpiece in the
drawing. The interference check unit does not make the interference
check in the uncut region.
Inventors: |
ISHIKAWA; Yasuhito;
(Yamanashi, JP) |
|
Applicant: |
Name |
City |
State |
Country |
Type |
FANUC CORPORATION |
Minamitsuru-gun |
|
JP |
|
|
Family ID: |
68205714 |
Appl. No.: |
16/393105 |
Filed: |
April 24, 2019 |
Current U.S.
Class: |
1/1 |
Current CPC
Class: |
G05B 19/404 20130101;
G05B 19/31 20130101; G05B 2219/49153 20130101; G05B 19/4097
20130101; G05B 19/4061 20130101 |
International
Class: |
G05B 19/31 20060101
G05B019/31; G05B 19/404 20060101 G05B019/404; G05B 19/4097 20060101
G05B019/4097 |
Foreign Application Data
Date |
Code |
Application Number |
Apr 27, 2018 |
JP |
2018-086741 |
Claims
1. An interference monitoring device that makes a check on
interference between a tool and a workpiece in a machine for
performing predetermined machining on the workpiece while moving
the tool and the workpiece relative to each other based on a
program, the interference monitoring device comprising: an advanced
position calculation unit that calculates an advanced position of
the tool or the workpiece ahead by a predetermined period of time
based on the program; an interference check unit that draws an
estimated shape of a machined part of the workpiece after machining
based on the advanced position, and makes the interference check
based on the estimated shape of the machined part of the workpiece
in the drawing; and an uncut region calculation unit that
calculates an error between the estimated shape of the machined
part of the workpiece in the drawing and an actual shape of the
machined part of the workpiece after machining as an uncut region
in the estimated shape of the machined part of the workpiece in the
drawing, wherein the interference check unit does not make the
interference check in the uncut region.
2. The interference monitoring device according to claim 1, wherein
the uncut region calculation unit calculates a maximum width in the
uncut region, and when an offset width between an estimated path
based on an advanced position on a last command path and an
estimated path based on an advanced position on a current command
path is equal to or less than the maximum width in the uncut
region, the interference check unit determines that the current
command path is to pass through the uncut region, and does not make
the interference check.
3. The interference monitoring device according to claim 2, wherein
the uncut region calculation unit calculates traveling direction
vectors via from a calculated advanced position corresponding to
time t.sub.N to a plurality of command positions, and calculates a
traveling direction vector vib from the calculated advanced
position corresponding to the time t.sub.N to a calculated advanced
position corresponding to time t.sub.N+1, the plurality of command
positions being command positions between the calculated advanced
position corresponding to the time t.sub.N and the calculated
advanced position corresponding to the time t.sub.N+1, the uncut
region calculation unit converts the traveling direction vector vib
to a unit vector, the uncut region calculation unit calculates the
absolute value of the outer product of the unit vector and each of
the traveling direction vectors via, thereby obtaining a normal
direction offset width of each of the traveling direction vectors
via to the traveling direction vector vib, and the uncut region
calculation unit defines a maximum of the offset widths as the
maximum width in the uncut region.
4. The interference monitoring device according to claim 1, wherein
the uncut region calculation unit calculates an area in the uncut
region, and when an area of current machining is equal to or less
than the area in the uncut region, the interference check unit
determines that the current machining is being performed in the
uncut region and does not make the interference check.
5. The interference monitoring device according to claim 4, wherein
the uncut region calculation unit calculates traveling direction
vectors vi from a calculated advanced position corresponding to
time t.sub.N to a plurality of command positions, and calculates a
traveling direction vector vi from the calculated advanced position
corresponding to the time t.sub.N to a calculated advanced position
corresponding to time t.sub.N+1, the plurality of command positions
being command positions between the calculated advanced position
corresponding to the time t.sub.N and the calculated advanced
position corresponding to the time t.sub.N+1, the uncut region
calculation unit obtains an area si in a region surrounded by the
traveling direction vector vi and a traveling direction vector vi+1
adjacent to each other, and the uncut region calculation unit
defines the total sum of the areas si from the time t.sub.N to the
time t.sub.N+1 as the area in the uncut region.
Description
[0001] This application is based on and claims the benefit of
priority from Japanese Patent Application No. 2018-086741, filed on
27 Apr. 2018, the content of which is incorporated herein by
reference.
BACKGROUND OF THE INVENTION
Field of the invention
[0002] The present invention relates to an interference monitoring
device that checks interference between a tool and a workpiece in a
machine for performing predetermined machining on the workpiece
while moving the tool and the workpiece relative to each other
based on a program.
Related Art
[0003] In a machine tool, for example, a tool and a workpiece are
moved relative to each other based on a program prepared in advance
to machine the workpiece. In the presence of a mistake in the
program or in the presence of a mistake in attachment of the
workpiece to the machine, for example, interference may occur such
as collision of the tool with the workpiece or with a jig for
attachment of the workpiece while the machine is running.
[0004] In this regard, an interference monitoring device has been
devised (Patent Document 1, for example). In this interference
monitoring device, an advanced position (advanced preview position)
of a tool or a workpiece ahead by a predetermined period of time is
calculated through look-ahead of a program, and interference
between the tool and the workpiece is checked based on the
calculated advanced position. If interference is expected to occur,
movement of the tool or the workpiece is decelerated and
stopped.
[0005] Patent Document 1: Japanese Patent No. 4221016
SUMMARY OF THE INVENTION
[0006] The present inventor has come up with an idea of making an
interference check using an interference monitoring device.
According to this check, while estimated cutting from a workpiece
is drawn, in other words, while an estimated shape of a machined
part of the workpiece after machining is drawn, an interference
check is made based on the estimated shape of the machined part of
the workpiece in the drawing. This idea has the following
problem.
[0007] As shown in FIG. 3A, for example, command end points (tiny
continuous blocks) Pa1 are given on a command path 1 in actual
control. Meanwhile, an interference monitoring device calculates an
advanced position Pb1 corresponding to each of time t1.sub.N and
time t1.sub.N+1 ahead by a predetermined period of time through
look-ahead of a program. This makes an interval between points in a
sequence of the advanced positions Pb1 larger than an interval
between the command end points Pa1, whereby an intermediate
coordinate corresponding to the command end point Pa1 cannot be
calculated.
[0008] When the interference monitoring device draws an estimated
shape of a machined part of a workpiece W after machining based on
the advanced positions Pb1, an error is caused between the
estimated shape of the machined part of the workpiece W in the
drawing (dashed line in a straight line between the advanced
positions Pb1, for example) and an actual shape of the machined
part of the workpiece W after machining (solid line along the
command end points Pa1, for example), as shown in FIG. 3B (this
error will also be called an uncut region R). The uncut region R is
a region cut from the actual shape of the machined part of the
workpiece W after machining but is erroneously recognized as an
uncut region in the estimated shape of the machined part of the
workpiece W in the drawing.
[0009] As shown in FIG. 3C, cutting along a command path 2 adjacent
to the last command path 1 may be commanded thereafter. As shown in
FIG. 3D, if the interference monitoring device calculates an
advanced position Pb2 on the command path 2 corresponding to each
of time t2.sub.N and time t2.sub.N+1 and makes an interference
check along a straight line connecting the advanced positions Pb2,
a cutting volume in the uncut region R is recognized erroneously as
being equal to or more than a predetermined value. Hence, the
interference monitoring device makes an erroneous detection that
interference between a tool T and the workpiece W has occurred as
shown in FIG. 3E. This unintentionally results in stopping of the
running of a machine tool, for example, despite the absence of
interference between the tool T and the workpiece W in
actuality.
[0010] The present invention is intended to provide an interference
monitoring device that avoids erroneous detection of interference
between a tool and a workpiece.
[0011] (1) An interference monitoring device according to the
present invention (interference monitoring device 100 described
later, for example) makes a check on interference between a tool
and a workpiece in a machine for performing predetermined machining
on the workpiece while moving the tool and the workpiece relative
to each other based on a program. The interference monitoring
device comprises: an advanced position calculation unit (advanced
position calculation unit 15 described later, for example) that
calculates an advanced position of the tool or the workpiece ahead
by a predetermined period of time based on the program; an
interference check unit (interference check device 2 described
later, for example) that draws an estimated shape of a machined
part of the workpiece after machining based on the advanced
position, and makes the interference check based on the estimated
shape of the machined part of the workpiece in the drawing; and an
uncut region calculation unit (uncut region calculation unit 16
described later, for example) that calculates an error between the
estimated shape of the machined part of the workpiece in the
drawing and an actual shape of the machined part of the workpiece
after machining as an uncut region in the estimated shape of the
machined part of the workpiece in the drawing. The interference
check unit does not make the interference check in the uncut
region.
[0012] (2) In the interference monitoring device described in (1),
the uncut region calculation unit may calculate a maximum width in
the uncut region. When an offset width between an estimated path
based on an advanced position on a last command path and an
estimated path based on an advanced position on a current command
path is equal to or less than the maximum width in the uncut
region, the interference check unit may determine that the current
command path is to pass through the uncut region, and may not make
the interference check.
[0013] (3) In the interference monitoring device described in (2),
the uncut region calculation unit may calculate traveling direction
vectors via from a calculated advanced position corresponding to
time t.sub.N to multiple command positions, and calculate a
traveling direction vector vib from the calculated advanced
position corresponding to the time t.sub.N to a calculated advanced
position corresponding to time t.sub.N+1. The multiple command
positions are command positions between the calculated advanced
position corresponding to the time t.sub.N and the calculated
advanced position corresponding to the time t.sub.N+1. The uncut
region calculation unit may convert the traveling direction vector
vib to a unit vector. The uncut region calculation unit may
calculate the absolute value of the outer product of the unit
vector and each of the traveling direction vectors via, thereby
obtaining a normal direction offset width of each of the traveling
direction vectors via to the traveling direction vector vib. The
uncut region calculation unit may define a maximum of the offset
widths as the maximum width in the uncut region.
[0014] (4) In the interference monitoring device described in (1),
the uncut region calculation unit may calculate an area in the
uncut region. When an area of current machining is equal to or less
than the area in the uncut region, the interference check unit may
determine that the current machining is being performed in the
uncut region and may not make the interference check.
[0015] (5) In the interference monitoring device described in (4),
the uncut region calculation unit may calculate traveling direction
vectors vi from a calculated advanced position corresponding to
time t.sub.N to multiple command positions, and calculate a
traveling direction vector vi from the calculated advanced position
corresponding to the time t.sub.N to a calculated advanced position
corresponding to time t.sub.N+1. The multiple command positions are
command positions between the calculated advanced position
corresponding to the time t.sub.N and the calculated advanced
position corresponding to the time t.sub.N+1. The uncut region
calculation unit may obtain an area si in a region surrounded by
the traveling direction vector vi and a traveling direction vector
vi+1 adjacent to each other. The uncut region calculation unit may
define the total sum of the areas si from the time t.sub.N to the
time t.sub.N+1 as the area in the uncut region.
[0016] According to the present invention, the interference
monitoring device can avoid erroneous detection of interference
between the tool and the workpiece.
BRIEF DESCRIPTION OF THE DRAWINGS
[0017] FIG. 1 shows the configuration of an interference monitoring
device according to an embodiment;
[0018] FIG. 2 is a flowchart showing interference check operation
by an interference monitoring device according to a first
embodiment;
[0019] FIG. 3A shows a problem about an interference monitoring
device;
[0020] FIG. 3B shows the problem about the interference monitoring
device;
[0021] FIG. 3C shows the problem about the interference monitoring
device;
[0022] FIG. 3D shows the problem about the interference monitoring
device;
[0023] FIG. 3E shows the problem about the interference monitoring
device;
[0024] FIG. 4 shows the function of an uncut region calculation
unit in the interference monitoring device according to the first
embodiment;
[0025] FIG. 5 shows the function of the uncut region calculation
unit in the interference monitoring device according to the first
embodiment;
[0026] FIG. 6 shows the function of an interference check device in
the interference monitoring device according to the first
embodiment;
[0027] FIG. 7 is a flowchart showing interference check operation
by an interference monitoring device according to a second
embodiment;
[0028] FIG. 8 shows the function of an uncut region calculation
unit in the interference monitoring device according to the second
embodiment;
[0029] FIG. 9 shows the function of the uncut region calculation
unit in the interference monitoring device according to the second
embodiment; and
[0030] FIG. 10 shows the function of an interference check device
in the interference monitoring device according to the second
embodiment.
DETAILED DESCRIPTION OF THE INVENTION
[0031] Examples of an embodiment of the present invention will be
described below by referring to the accompanying drawings. In the
drawings, corresponding or comparable parts are identified bv the
same sign.
First Embodiment
[0032] FIG. 1 shows the configuration of an interference monitoring
device according to a first embodiment. An interference monitoring
device 100 shown in FIG. 1 includes a numerical controller 1 and an
interference check device (interference check unit) 2. The
interference monitoring device 100 is not limited to such a
configuration with the two devices and can be configured as one
device. The numerical controller 1 moves a tool based on a program
to control a machine tool (a servo motor 3, for example) for
performing machining, such as cutting, on a workpiece. The
numerical controller 1 calculates an advanced position of the tool
based on the program. The interference check device 2 checks
interference between the tool and the workpiece based on the
calculated advanced position.
[0033] The numerical controller 1 includes a command analysis unit
10, a distribution processing unit 11, a movement command output
unit 12, an acceleration/deceleration processing unit 13, a servo
control unit 14, an advanced position calculation unit 15, and an
uncut region calculation unit 16.
[0034] The command analysis unit 10 reads a command corresponding
to one block from a program 20, converts the read command to data
in an execution format, and generates look-ahead block command data
21. The command analysis unit 10 stores the look-ahead block
command data 21 into a working memory (not shown), for example.
[0035] The distribution processing unit 11 reads pieces of the
look-ahead block command data 21 one by one corresponding to one
block. Based on the stroke and speed of each axis commanded in the
block, and an override value (%) commanded through a feed speed
override command unit 4, the distribution processing unit 11
determines a distributed stroke in each distribution cycle to be
given as a command to a movable part of each axis (a servo motor of
each axis). The distribution processing unit 11 adds the determined
distributed strokes to a current position register (not shown), for
example, thereby updating a current coordinate position (hereafter
called a current position).
[0036] The distribution processing unit 11 outputs the determined
distributed strokes to the acceleration/deceleration processing
unit 13 through the movement command output unit 12. As will be
described later, in response to input of an axis stop command from
the interference check device 2, the movement command output unit
12 stops output of the distributed strokes in a movement command,
having been output from the distribution processing unit 11, to the
acceleration/deceleration processing unit 13. Further, the movement
command output unit 12 outputs the movement command to the
acceleration/deceleration processing unit 13 in the absence of
input of an axis stop command from the interference check device
2.
[0037] The acceleration/deceleration processing unit 13 performs
acceleration/deceleration processing in response to receipt of the
movement command, and outputs a movement command containing a
stroke resulting from the acceleration/deceleration processing to
the servo control unit 14. The servo control unit 14 executes
position feedback control and speed feedback control based on the
output movement command, and a position feedback from a position
detector and a speed feedback from a speed detector attached to the
servo motor 3 (or a movable part to be driven by the servo motor
3). Further, the servo control unit 14 executes current feedback
control based on a current feedback from a current detector for
detection of a driving current, and controls drive of the servo
motor 3 through an amplifier. While only one servo motor 3 is shown
in FIG. 1, servo motors for all axes (all movable parts) belonging
to a machine tool are to be controlled in the same way to control
the respective positions and speeds of the movable parts.
[0038] The advanced position calculation unit 15 is functional
means that determines an advanced position showing a position to
which a movable part driven by the servo motor 3 is to move from a
current position after passage of an advanced period of time. The
advanced position is calculated based on the current position of
the movable part, the set advanced period of time, the look-ahead
block command data 21, and an override value (%) input through the
feed speed override command unit 4. The advanced position
calculation unit 15 outputs the advanced period of time and the
coordinate value of the advanced position to the interference check
device 2 for making an interference check.
[0039] The advanced period of time used by the advanced position
calculation unit 15 is a value determined by adding a predetermined
period of spare time a to a value (TP1+TP2+TP3) obtained by adding
a period of time TP1 required for the interference check device 2
to make an interference check, a period of time TP2 required for
communication between the advanced position calculation unit 15 and
the interference check device 2, and a period of time TP3 required
for decelerating and stopping a movable part being moved. Once this
system configuration is determined, the period of time TP2 for
communication between the advanced position calculation unit 15 and
the interference check device 2 generally takes a constant value
with substantially no change and can be obtained by measurement.
The period of time TP3 required for decelerating and stopping is a
constant value determined according to the configuration of the
acceleration/deceleration processing unit 13. By contrast, the
period of time TP1 required for the interference check device 2 to
make an interference check change according to the operating
positions of multiple movable parts. Meanwhile, giving attention to
the point that the position of a movable part intended to be
subjected to an interference check following the current time is
generally near the position of the movable part having been
subjected to the last interference check, a period of time required
for an interference check having been made immediately before by
the interference check device 2 may be fed back to the advanced
position calculation unit 15 to use the advanced period of time,
and this period of time can be used as the period of time TP1
required for an interference check. Alternatively, the interference
check device 2 or the advanced position calculation unit 15 to use
the advanced period of time may determine an average of periods of
time spent in interference checks in the past having been made
immediately before (an average of periods of time spent in the last
interference check, in the last but one interference check, in the
last but two interference check, . . . ). The determined average
may be used as the period of time TP1 required for an interference
check.
[0040] The interference check device 2 has stored the contour shape
of a tool or a workpiece, the contour shape of a machine, etc. when
the interference check device 2 receives the advanced period of
time and the coordinate value of the advanced position from the
advanced position of the calculation unit 15. The interference
check device 2 makes a check to determine whether interference is
to occur between the tool and the workpiece based on the position
of each movable part transmitted from the advanced position
calculation unit 15, and outputs an axis stop command to the
movement command output unit 12 based on a result of the check. The
interference check device 2 is configured using an information
processor such as a personal computer. Further details of the
processing performed by the advanced position calculation unit 15
and the interference check device 2 will not be described in this
specification as they are known publicly from a conventional
technique such as that described in Patent Document 1.
[0041] The interference check device 2 may be a device by which,
while estimated cutting from a workpiece is drawn, in other words,
while an estimated shape of a machined part of the workpiece after
machining is drawn, an interference check is made based on the
estimated shape of the machined part of the workpiece in the
drawing. In this case, the following problem arises. As shown in
FIG. 3A, for example, in actual control by the distribution
processing unit 11, the acceleration/deceleration processing unit
13, and the servo control unit 14, command end points (tiny
continuous blocks) Pa1 are given on a command path 1. Meanwhile,
the advanced position calculation unit 15 calculates an advanced
position Pb1 corresponding to each of time t1.sub.N and time
t1.sub.N+1 ahead by a predetermined period of time based on the
look-ahead block command data 21. This makes an interval between
points in a sequence of the advanced positions Pb1 larger than an
interval between the command end points Pa1, whereby an
intermediate coordinate corresponding to the command end point Pa1
cannot be calculated.
[0042] When the interference check device 2 draws an estimated
shape of a machined part of a workpiece W after machining based on
the advanced positions Pb1, an error is caused between the
estimated shape of the machined part of the workpiece W in the
drawing (dashed line in a straight line between the advanced
positions Pb1, for example) and an actual shape of the machined
part of the workpiece W after machining (solid line along the
command end points Pa1, for example), as shown in FIG. 3B (this
error will also be called an uncut region R). The uncut region R is
a region cut from the actual shape of the machined part of the
workpiece W after machining but is erroneously recognized as an
uncut region in the estimated shape of the machined part of the
workpiece W in the drawing.
[0043] As shown in FIG. 3C, cutting along a command path 2 adjacent
to the last command path 1 may be commanded thereafter. As shown in
FIG. 3D, if the advanced position calculation unit 15 calculates an
advanced position Pb2 on the command path 2 corresponding to each
of time t2.sub.N and time t2.sub.N+1 and the interference check
device 2 makes an interference check along a straight line
connecting the advanced positions Pb2, a cutting volume in the
uncut region R is recognized erroneously as being equal to or more
than a predetermined value. Hence, the interference check device 2
makes an erroneous detection that interference between a tool T and
the workpiece W has occurred as shown in FIG. 3E. This
unintentionally results in stopping of the running of a machine
tool, for example, despite the absence of interference between the
tool T and the workpiece W in actuality.
[0044] In this regard, as shown in FIG. 4, the uncut region
calculation unit 16 calculates an error between the estimated shape
of the machined part of the workpiece W in the drawing (dashed line
in a straight line between the advanced positions Pb1, for example)
and an actual shape of the machined part of the workpiece W after
machining (solid line along the command end points Pa1, for
example) as the uncut region R in the estimated shape of the
machined part of the workpiece W in the drawing. For example, the
uncut region calculation unit 16 calculates a maximum width W' in
the uncut region R.
[0045] More specifically, as shown in FIG. 5, the uncut region
calculation unit 16 calculates traveling direction vectors vi from
the calculated advanced position Pb1 corresponding to the time
t1.sub.N to multiple command end points Pa1 (for example, vi=via=v1
to v6) and a traveling direction vector vi from the calculated
advanced position Pb1 corresponding to the time t1.sub.N to the
calculated advanced position Pb1 corresponding to the time
t1.sub.N+1 (for example, vi=vib=v7). The command end points Pa1 on
the command path 1 can be acquired from the look-ahead block
command data 21 through the advanced position calculation unit 15.
The uncut region calculation unit 16 converts the traveling
direction vector v7 from the calculated advanced position Pb1
corresponding to the time t1.sub.N to the calculated advanced
position Pb1 corresponding to the time t1.sub.N+1 to a unit vector
e7, and calculates the absolute value of the outer product of the
unit vector e7 and each of the traveling direction vectors vi (for
example, v1 to v6) as shown in the following formula, thereby
obtaining a normal direction offset width wi of each of v1 to v6
from v7:
wi=|e7.times.vi|.
The uncut region calculation unit 16 defines a maximum of the
offset widths wi as the maximum width W' in the uncut region R, and
outputs the maximum width W' to the interference check device
2.
[0046] The interference check device 2 does not make an
interference check in the uncut region R. In other words, the
interference check device 2 handles the uncut region R as a region
not to be targeted for an interference check. This makes it
possible to avoid erroneous detection of interference between the
tool T and the workpiece W.
[0047] As shown in FIG. 6, when an offset width Wp between an
estimated path based on the calculated advanced positions Pb1 on
the last command path 1 corresponding to the time t1.sub.N and the
time t1.sub.N+1 (dashed line in a straight line between Pb1) and an
estimated path based on the calculated advanced positions Pb2 on
the current command path 2 corresponding to the time t2.sub.N and
the time t2.sub.N+1 (dashed line in a straight line between Pb2) is
equal to or less than the maximum width W' in the uncut region R
acquired from the uncut region calculation unit 16, for example,
the interference check device 2 determines that the current command
path 2 is to pass through the uncut region R. In this case, the
interference check device 2 does not check interference between the
tool T and the workpiece W. The offset width Wp may be a maximum
distance between the estimated path based on the advanced positions
Pb1 (dashed line in a straight line between Pb1) and the estimated
path based on the advanced positions Pb2 (dashed line in a straight
line between Pb2). The maximum width W' can also be compensated for
in consideration of a tool shape.
[0048] Interference check operation by the interference monitoring
device 100 according to the first embodiment will be described next
by referring to FIG. 2. FIG. 2 is a flowchart showing the
interference check operation by the interference monitoring device
100 according to the first embodiment.
Preliminary Processing
[0049] In preliminary processing, the command analysis unit 10
first reads a command corresponding to one block from the program
20, converts the read command to data in an execution format, and
generates the look-ahead block command data 21. The command
analysis unit 10 stores the look-ahead block command data 21 into
the working memory, for example.
Execution Processing
[0050] Next, in execution processing, the distribution processing
unit 11 reads pieces of the look-ahead block command data 21 one by
one corresponding to one block. Further, the distribution
processing unit 11 acquires an override value through the feed
speed override command unit 4. Based on a stroke and a speed of
each axis commanded in the read block and the acquired override
value, the distribution processing unit 11 calculates a distributed
stroke in each distribution cycle to be given as a command to a
movable part of each axis (a servo motor of each axis), and outputs
the calculated distributed strokes to the movement command output
unit 12. Further, the distribution processing unit 11 adds the
calculated distributed strokes to the current position register,
thereby updating a current coordinate position.
[0051] The advanced position calculation unit 15 calculates the
advanced position Pb1 on the command path 1 corresponding to each
of the time t1.sub.N and the time t1.sub.N+1 ahead by a
predetermined period of time based on the current position of the
movable part, a set advanced period of time, the look-ahead block
command data 21, and the override value (%) input through the feed
speed override command unit 4 (S11) (see FIG. 4). Next, as shown in
FIGS. 4 and 5, the uncut region calculation unit 16 calculates an
error between an estimated shape of a machined part of the
workpiece W in a drawing (dashed line in a straight line between
the advanced positions Pb1, for example) and an actual shape of the
machined part of the workpiece W after machining (solid line along
the command end points Pa1, for example) as the uncut region R in
the estimated shape of the machined part of the workpiece W in the
drawing, and calculates the maximum width W' in the uncut region R
(S12).
[0052] Next, as shown in FIG. 6, the interference check device 2
calculates the offset width Wp between an estimated path based on
the calculated advanced positions Pb1 on the last command path 1
corresponding to the time t1.sub.N and the time t1.sub.N+1 (dashed
line in a straight line between Pb1) and an estimated path based on
the calculated advanced positions Pb2 on the current command path 2
corresponding to the time t2.sub.N and the time t2.sub.N+1 (dashed
line in a straight line between Pb2) (S13). The interference check
device 2 determines whether the calculated offset width Wp is equal
to or less than the maximum width W' in the uncut region R acquired
from the uncut region calculation unit 16 (S14).
[0053] When the offset width Wp is equal to or less than the
maximum width W', the interference check device 2 determines that
the current command path 2 is to pass through the uncut region R,
and the interference check device 2 does not check interference
between the tool T and the workpiece W and does not output an axis
stop command to the movement command output unit 12. In this case,
the movement command output unit 12 outputs the distributed strokes
(S15), the acceleration/deceleration processing unit 13 performs
acceleration/deceleration processing, and the servo control unit 14
gives a command to drive the servo motor 3.
[0054] Meanwhile, when the offset width Wp is greater than the
maximum width W', the interference check device 2 determines that
current machining is being performed in a region other than the
uncut region R. Then, the interference check device 2 checks
interference between the tool T and the workpiece W at the advanced
positions Pb2. When a cutting volume is equal to or more than a
predetermined value (when YES in S16), the interference check
device 2 outputs an axis stop command to the movement command
output unit 12. In response to this, the movement command output
unit 12 stops output of a movement command (S17) to stop the
command to drive the servo motor 3. When the interference check
device 2 determines that the cutting volume is less than the
predetermined value (when NO in S16) as a result of making of a
check of interference between the tool T and the workpiece W at the
advanced positions Pb2, the interference check device 2 does not
output an axis stop command to the movement command output unit 12.
In response to this, the foregoing process in step S15 is
performed. The foregoing operation is repeated for every block in
the program and in every distribution cycle.
[0055] As described above, according to the interference monitoring
device 100 of the first embodiment, the uncut region calculation
unit 16 in the numerical controller 1 calculates an error between
the estimated shape of the machined part of the workpiece W in the
drawing and an actual shape of the machined part of the workpiece W
after machining as the uncut region R in the estimated shape of the
machined part of the workpiece W in the drawing. The interference
check device 2 does not make an interference check in the uncut
region R. This makes it possible to avoid erroneous detection of
interference between the tool T and the workpiece W despite the
absence of interference between the tool T and the workpiece W in
the uncut region R in actuality.
Second Embodiment
[0056] In the first embodiment, erroneous detection of interference
between the tool T and the workpiece W is avoided by calculating
the maximum width W in the uncut region R. In a second embodiment,
erroneous detection of interference between the tool T and the
workpiece W is avoided by calculating an area S in the uncut region
R.
[0057] In a numerical controller 1 according to the second
embodiment, the uncut region calculation unit 16 functions and
operates in different ways from that of the numerical controller 1
shown in FIG. 1. As shown in FIG. 8, the uncut region calculation
unit 16 calculates an error between an estimated shape of a
machined part of the workpiece W in a drawing (dashed line in a
straight line between the advanced positions Pb1, for example) and
an actual shape of the machined part of the workpiece W after
machining (solid line along the command end points Pa1, for
example) as the uncut region R in the estimated shape of the
machined part of the workpiece W in the drawing. For example, the
uncut region calculation unit 16 calculates the area S in the uncut
region R.
[0058] More specifically, as shown in FIG. 9, the uncut region
calculation unit 16 calculates traveling direction vectors vi from
the calculated advanced position Pb1 corresponding to the time
t1.sub.N to the multiple command end points Pa1 (for example, v1 to
v6) and a traveling direction vector vi from the calculated
advanced position Pb1 corresponding to the time t1.sub.N to the
calculated advanced position Pb1 corresponding to the time
t1.sub.N+1 (for example, v7). The command end points Pa1 on the
command path 1 can be acquired from the look-ahead block command
data 21 through the advanced position calculation unit 15. The
uncut region calculation unit 16 obtains an area si in a region
surrounded by a traveling direction vector vi and a traveling
direction vector vi+1 adjacent to each other as shown in the
following formula:
si=|vi.times.vi+1|/2.
The uncut region calculation unit 16 obtains the total sum of the
areas si from the time t1.sub.N to the time t1.sub.N+1 as the area
S in the uncut region R as shown in the following formula, and
outputs the obtained area S to the interference check device 2:
S=.SIGMA.si,
where .SIGMA.: sum for i=1 to 6.
[0059] The interference check device 2 does not make an
interference check in the uncut region R. In other words, the
interference check device 2 handles the uncut region R as a region
not to be targeted for an interference check. This makes it
possible to avoid erroneous detection of interference between the
tool T and the workpiece W. For example, when a cut area Sp
determined by passing through an estimated path based on the
calculated advanced positions Pb2 on the current command path 2
corresponding to the time t2.sub.N and the time t2.sub.N+1 is equal
to or less than the area S in the uncut region R acquired from the
uncut region calculation unit 16, the interference check device 2
determines that the current command path 2 is to pass through the
uncut region R. In this case, the interference check device 2 does
not check interference between the tool T and the workpiece W. As
shown in FIG. 10, the cut area Sp may be an area per unit length
determined by dividing a cutting volume V by a length L.
Alternatively, the cut area Sp may be an average of areas per unit
length. The area S may be compensated for in consideration of a
tool shape.
[0060] Interference check operation by an interference monitoring
device 100 according to the second embodiment will be described
next by referring to FIG. 7. FIG. 7 is a flowchart showing the
interference check operation by the interference monitoring device
100 according to the second embodiment.
[0061] Like in step S11 described above, the advanced position
calculation unit 15 calculates the advanced position Pb1 on the
command path 1 corresponding to each of the time t1.sub.N and the
time t1.sub.N+1 ahead by a predetermined period of time based on
the current position of a movable part, a set and calculated
advanced period of time, the look-ahead block command data 21, and
an override value (%) input through the feed speed override command
unit 4 (S11) (see FIG. 8). Next, as shown in FIGS. 8 and 9, the
uncut region calculation unit 16 calculates an error between the
estimated shape of the machined part of the workpiece W in the
drawing (dashed line in a straight line between the advanced
positions Pb1, for example) and an actual shape of the machined
part of the workpiece W after machining (solid line along the
command end points Pa1, for example) as the uncut region R in the
estimated shape of the machined part of the workpiece W in the
drawing, and calculates the area S in the uncut region R (S22).
[0062] Next, the interference check device 2 calculates the cut
area Sp taken along the estimated path based on the calculated
advanced positions Pb2 on the current command path 2 corresponding
to the time t2.sub.N and the time t2.sub.N+1 (S23). The
interference check device 2 determines whether the calculated cut
area Sp is equal to or less than the area S in the uncut region R
acquired from the uncut region calculation unit 16 (S24).
[0063] When the cut area Sp is equal to or less than the area S,
the interference check device 2 determines that current machining
is being performed in the uncut region R, and the interference
check device 2 does not check interference between the tool T and
the workpiece W and does not output an axis stop command to the
movement command output unit 12. In this case, the movement command
output unit 12 outputs a distributed strokes (S15), the
acceleration/deceleration processing unit 13 performs
acceleration/deceleration processing, and the servo control unit 14
gives a command to drive the servo motor 3.
[0064] When the cut area Sp is larger than the area S, the
interference check device 2 determines that the current machining
is being performed in a region other than the uncut region R. Then,
the interference check device 2 checks interference between the
tool T and the workpiece W at the advanced position Pb2. When a
cutting volume is equal to or more than a predetermined value (when
YES in S16), the interference check device 2 outputs an axis stop
command to the movement command output unit 12. In response to
this, the movement command output unit 12 stops output of a
movement command (S17) to stop the command to drive the servo motor
3. When the interference check device 2 determines that the cutting
volume is less than the predetermined value (when NO in S16) as a
result of making of a check of interference between the tool T and
the workpiece W at the advanced positions Pb2, the interference
check device 2 does not output an axis stop command to the movement
command output unit 12. In response to this, the foregoing process
in step S15 is performed. The foregoing operation is repeated for
every block in the program and in every distribution cycle.
[0065] As described above, the numerical controller 1 of the second
embodiment can achieve advantages comparable to those of the first
embodiment.
[0066] The present invention should not be limited to the
embodiments described above but various changes and modifications
are applicable to the present invention. For example, in the
foregoing embodiments, a machine tool that moves a tool has been
described. However, the features of the present invention should
not be limited to this machine tool but are further applicable to a
machine tool that moves a workpiece.
[0067] The interference monitoring device 100 described in the
foregoing embodiments checks interference between a tool and a
workpiece in a machine tool. However, the features of the present
invention should not be limited to this machine tool but are
further applicable to an interference monitoring device that checks
interference between tools and workpieces in various types of
machines such as industrial machines or industrial robots.
EXPLANATION OF REFERENCE NUMERALS
[0068] 1 Numerical controller [0069] 2 Interference check device
(interference check unit) [0070] 3 Servo motor [0071] 4 Feed speed
override command unit [0072] 10 Command analysis unit [0073] 11
Distribution processing unit [0074] 12 Movement command output unit
[0075] 13 Acceleration/deceleration processing unit [0076] 14 Servo
control unit [0077] 15 Advanced position calculation unit [0078] 16
Uncut region calculation unit [0079] 20 Program [0080] 21
Look-ahead block command data [0081] 100 Interference monitoring
device
* * * * *